Werkzeug zum abrichten von schleifsteinen
(10) RK 413,669 B 2006-04-15 (12) patent specification (21) registration number: A 53/2003 (22) registration day: 2003-01-16 (42) beginning of the patent duration: 2005-09-15 (45) expenditure day: 2006-04-15 (51) Int. Cl/: B24B 53/12 (30) priority: 31.01.2002 US 062935 stresses. (56) Holding out: US3608536A GB605146A GB175555A (of 73) patentees: PUT KARL-HEINZ D-98522 HEIDENHEIM (DE). (54) TOOL FOR STRAIGHTENING WHET-STONES o COo oCd o>CD CDCOI-< (57) it is intended a sharp (60, 100) for straightening a Schleifwerkzeugs, like a sharpening surface of a whet-stone sharpening tool (20) for the mechanical production of cellulose. At least the sharp (60, 100) covers a cylindrical body, a majority by at its lateral surface (62) arranged and of this teeth (64) and one which are away outward ring channel (110), intended in its lateral surface (62). The sharp can plan a more uniform straightening sample on a sharpening surface of a whet-stone sharpening tool, in order to ensure an improved firmness and quality of the cellulose produced thereby. FIG. SA DVR 0078018 2 RKs 413,669 B the available invention concerns generally a device and a procedure for straightening Schleifwerkzeugen. More exactly said the available invention concerns a tool (i.e. a sharp) and a procedure for straightening (also sharpnesses called) whet-stone sharpening tools, which are used for the mechanical production of cellulose. The quality of cellulose can improve 5 the tool according to invention and extend the life span of whet-stone sharpening tools on favourable way both. The use from whet-stone sharpening tools to sharpening wood (e.g. in the form of trunks or alternatively in the form of splinters or shreds) to groundwood for the Pa jetty industry is well-known. A typical whet-stone sharpening tool is cylindric and relatively largely and complex for example with a diameter from approximately 120 to approximately 190 cm or more and a length from approximately 70 to approximately 230 cm or more. A conventional whet-stone sharpening tool exhibits typically a majority by Schleifsegmenten, those around a cylindrical concrete core is in line (see for example to the USA 5,243,789, Bacic). The segments contain generally a mixture out sharpen kömern and of bonding agents (e.g. ceramic(s), sinter or cement binder), which are injected to the desired form. For the improvement of the sharpening achievement of conventional whet-stone sharpening tools 20 the sharpening surface the same is typically straightened (or also sharpened). When straightening the sharpening surface of the whet-stone is treated generally with a tool, which is called herein sharp. For example a sharp with sufficient pressure can be rolled over the surface of the whet-stone sharpening tool, in order to stamp a sample on the surface. More commercial standard more spiralsharply (e.g. that one the company Norton Cana-25 there, Inc. Hamilton, Ontario, Canada with dimensions of 6x28) can be used for applying a sample by grooves and fields on the surface of the whet-stone sharpening tool, as is described still more exactly below. A conventional sharp for straightening a sharpening surface is for example from 30 US 3.608.536 admits become. The sharp has a rounded off edge, which comes with the whet-stone into contact, so that the Schleifer can be positioned and on the necessary rotating speed be brought can before it begins over the whet-stone surface to drive and these cut. From the GB 605,146 is a puller for the surface of a Schleifrades admits become. The GB 175,555 reveals a Abrichtewerk-35 things with circling cutters, that are connected with a spindle connected with the grinding machine. The handling takes place in such a manner that the cutters basic case will proceed, in order to employ the cutters against the surface of the Schleifrades. The characteristics of a typical Schärfers affect the sample on a sharpening surface 40 of a whet-stone sharpening tool and thus the characteristics of the cellulose produced thereby. For example the Faserlänge of cellulose bends to stand in reverse relationship with the angle of incidence of a Spiralschärfers, which is used for straightening the whet-stone sharpening tool. Further the characteristics of the Schärfers can affect themselves on the life span of a whet-stone sharpening tool and affect in the consequence final costs the 45 of the cellulose clearly. An improved wheel dresser and/or an improved procedure for straightening the surface of a whet-stone sharpening tool can lead from there to an improved quality and/or to smaller costs of the cellulose and from there for the paper industry and other cellulose processing industries be most worthwhile. such an aspect of the available invention refers to a sharp for straightening a sharpening surface of a Schleifwerkzeugs. The sharp covers a cylindrical body with a lateral surface, a majority of at the lateral surface radially outward distant teeth and at least a ring channel planned in the lateral surface. With a variant of this aspect the sharp is suitable for straightening the sharpening surface of a whet-stone 55 of Schleifwerkzeugs for the mechanical production of cellulose. The available invention refers 3 RK 413,669 B in accordance with another aspect to a sharp for straightening a sharpening surface of a whet-stone sharpening tool for the mechanical production of cellulose. The sharp covers a cylindrical body with a lateral surface, a length (axial dimension) and a longitudinal axis. The sharp contains further a majority 5 teeth extending radially outward from itself at the lateral surface and at least a ring channel planned in the lateral surface. The sharp is suitable for straightening a sharpening surface of a whet-stone sharpening tool for the mechanical production of cellulose. In accordance with a further aspect the available invention covers a procedure for straightening 10 of a sharpening surface of a whet-stone sharpening tool for the mechanical production of cellulose. The procedure covers a planning of a Schärfers, which exhibits a cylindrical body with a lateral surface, a majority of at the lateral surface planned and of this distant teeth and at least a ring channel planned in the lateral surface. The procedure covers further the swivelling arranging of the Schärfers on a Ein-15 direction to the procedure along the length of the whet-stone sharpening tool, pressing the Schärfers in slightly to the sharpening surface of the whet-stone sharpening tool, rotating the whet-stone sharpening tool in such a manner that the sharp rolls a shifting of the Schärfers over the sharpening surface of the same, and along the length of the whet-stone sharpening tool. In the attached designs is Fig. 1 a perspective opinion of an execution form of a whet-stone sharpening tool provided with segments; Fig. 2 a schematic cross section opinion of a sharpening surface of a whet-stone sharpening tool after an exemplary surface straightening procedure; Fig. 3 a schematic cross section opinion of a generally desirable sharpening surface of a whet-stone sharpening tool after an exemplary surface straightening procedure; Fig. 4A a perspective opinion of an execution form of a spiral sharp wheel dresser for straightening the surface of a whet-stone sharpening tool as in Fig. 1 shown, Fig. 4B a schematic cross section opinion of the exterior surface of the Spiralschärfers in accordance with Fig. 4A; Fig. 5 a schematic opinion, those the employment of a Spiralschärfers as in Fig. 4A shown when straightening a Schleifflä che of a whet-stone sharpening tool as in Fig. 1 shown illustrates; Fig. 6A a perspective opinion of an execution form of the wheel dresser according to invention; and Fig. 6B a side view of the wheel dresser of the Fig. 6A. The available invention covers a sharp (also wheel dresser called), which when 35 straightening and/or sharpening Schleifwerkzeugen (e.g. grinding wheels) and in particular whet-stone sharpening tools like it with the mechanical production of cellulose is used, to be useful can. With reference to the Fig. 6A and 6B covers a sharp according to invention 100 a cylindrical body 63, which is typically designed as cylinder ring or Zylinderrad and exhibits at its lateral surface of 62 teeth 64 '. The sharp 40,100 contains further one or more channels 110, which extend over the extent of the body 63 and for the partitioning of the lateral surface 62 in two or more surface ranges 120 serve. With an execution form the sharp contains 100 two channels 110, which divide the lateral surface 62 effectively into three surface ranges 120, which are with special execution forms from approximately same axial dimension. The sharp according to invention is useful for straightening a sharpening surface of a whet-stone sharpening tool, which is used for sharpening cellulose. The teeth of the Schärfers proved in favourable way less wear-susceptibly than those of a conventional Schärfers. In the consequence the sharp according to invention stamps a rather even in such a way sample in the sharpening surface of the whet-stone sharpening tool and facilitates thus the production of relatively firm, uniform and high-quality cellulose. The sharp according to invention can be of advantage further in as much as its employment extends the life span of whet-stone sharpening tools. Further advantages of the available invention come out more in detail from the following description of several execution forms of the same 55. 4 RKs 413,669 B with reference to the Fig. 1-6B are described now the state of the art as well as the device according to invention and the procedure according to invention. Described like briefly before and in Fig. 1 shown, covers a conventional whet-stone sharpening tool 20 typically a majority of Schleifsegmenten 22, which are in line around any other cylindrical carrier structure around a cylindrical Betonkem 23 or. A typical segment 22 contains a mixture of Schleifkörnern from silicon carbide or alumina, which are arranged in a bonding agent matrix (e.g. sinter, ceramic(s) or cement binder). The Schleifkorn has typically a granulation size of approximately 24 US-Mesh (standard filter) for relatively rough applications of sharpening to approximately 80 US-Mesh for relatively fine applications of sharpening (i.e. granulation sizes of approximately 170 to approximately 750 pm diameters). A typical segment 22 contains further a majority of pores. Depending upon special application of wood explanations segments with a relatively far porenvolumen and pore diameter range can be used. The sharpening surface 27 of a whet-stone tool 20 can be straightened for various reasons, as also for occupying with fresh Schleifkörnern, cleaning or releasing of the pores of dirt, improving the water movement into the sharpening zone and the Ausschlämmens the same and, as before briefly descriptive, affecting the characteristics cellulose. In an exemplary procedure becomes (in Fig. 4A more represented and below more near more schriebener) more spiralsharply 60 over the surface segments of an exhibiting whet-stone tool 20 rolled. With nunmehriger reference in particular to Fig. originates in to 2 with straightening a whet-stone sharpening tool with the help of a Spiralschärfers 60 (Fig. 4A) an alternating sample from grooves 32 and fields 34 on the sharpening surface 27 " the same. During the wood explanation procedure the grooves 32 and fields 34 run typically rapidly over the surface of the wood, which leads to a rapid compression and decompression of the same, whereby it to local heating and separating from wood fibers from the surface of the wood come. With a whet-stone sharpening surface 27 ' with relatively narrow fields 34 (i.e. a so relatively small surface portion at fields) easily a increased local pressure and thus a heating develop, whereby cellulose with relatively long wood fibers is produced. However a sharpening surface produces 27 ' with relatively broad fields 34 (i.e. a relatively large surface portion at fields) rather mechanical pulp with relatively short wood fibers. Regrinding the fibers after the separation of the wood affects likewise the length the same. For example whet-stone sharpening tools with relatively well defined and deep grooves 32 supply with to rather long-fibrous cellulose. One believes that such deep grooves 32 in the enterprise carry the fibers from the sharpening zone, in order to prevent important regrinding effectively. The Faserlänge can do further by the angle of the grooves relative to the longitudinal axis 25 the 40 of the whet-stone sharpening tool 20 (Fig. 1) to be affected. With a larger angle the sharpening zone extends, whereby regrinding is promoted and thus the Faserlänge is reduced. It was also observed that straightening parameters affect the life span of a Schleifstein-45 of Schleifwerkzeugs. For example can with reference to Fig. 3 a generally desirable whet-stone sharpening surface by the fact 27 " characterized its that it exhibits a field width at the basis 36, which is at least five times as large as the average sharpening grain diameters 38. A whet-stone sharpening surface with a field width at the basis 36, which is smaller than five times as large as the sharpening grain diameters 38, is inclined to more rapidly in such a way wear (i.e. the fields become easily defective by the sharpening procedure with relatively high pressure). An excessive wear requires for relatively frequent straightening, whereby the production of cellulose is retarded and the life span of the whet-stone sharpening tool is reduced. 55 with nunmehriger reference to the Fig. 4A and 4B is an exemplary sharp 60 (also RK 413,669 B more spiralsharply called) for use when straightening the sharpening surface of a whet-stone sharpening tool (like the tool 20 in Fig. 1) illustrated. The sharp 60 exhibits a cylindrical body 63, which is typically in form of a cylindrical ring with a majority by teeth 64 trained, which at an outside lateral surface 62 des-5 of same (also work surface called) are arranged and/or are away from this. The teeth 64 are typically oblong and extend continuous over the length 68 of the Schärfers 60. The teeth 64 are typically in even distances arranged and in an angle of incidence 65 relative to the longitudinal axis of the Schärfers 60 aligned. The sharp 60 can exhibit teeth 64 with essentially each distance, but is the teeth 64 IO typically in an even distance 69, which is enough from approximately 0.5 to approximately 6.0 mm. Further the angle of incidence 65 can essentially be each angle in a range from 0 to 90oC, typically however in a range from approximately 5 to for instance 75°. With nunmehriger reference to Fig. 5 is spiralsharper as a sharp 60 (Fig. 4A 15 and 4B) on a putting arrangement 80 installs, whereby in the cylindrical sharp 60 (not represented) a hydraulic tight fit for the plug-in to contain and the putting arrangement can be attached swivelling on a putting spindle 82, for its part is stored which on the fork 84 of a centre lathe. In an example of a straightening procedure the sharp 60 is pressed over a controlled penetration depth (typically a depth within the range of approximately 0.5 to approximately 20,2.5 mm) into the whet-stone sharpening tool. Then the sharp 60 will proceed along the length of the whet-stone sharpening tool 20 axially (i.e. parallel to the longitudinal axis 25), while the tool 20 around the axle 25 (Fig. 1) one turns. Thus the sharp is moved effectively over the sharpening surface 27 of the whet-stone 20 with a pre-determined shift speed, which permits a relatively small overlap (e.g. 2 to 3 cm) of the course 25 Schärfers with each revolution of the tool 20. In a typical straightening procedure the above procedure in or is several times repeated, whereby each recent repetition plans a larger radial penetration of the Schärfers 60 into the whet-stone sharpening tool 20. so above with reference to Fig. typically a sample of grooves 32 and fields 34 (Fig supplies 5 descriptive straightening procedures. 2) in the sharpening surface 27, 27 ', etc. of the whet-stone sharpening tool 20. Ideal way supplies this procedure an essentially uniform sample over (axial) the length of the whet-stone sharpening tool 20. An aspect of the available invention consists of the fact that the teeth of the Schärfers, in particular that one at the employment edge 85 the same, while the shift becomes ever blunter (i.e. the cross section of the teeth becomes round or sinusoidal). In the consequence the sample at an end can the whet-stone sharpening tool 20 relatively sharp and deep triangle förmige grooves 32 and relatively flat of fields 34 contain, while at the end relatively round opposite 40 and flatten grooves of 32 and somewhat rounded off fields 34 find. Since the sample from grooves 32 and fields 34 affects the quality of the cellulose as well known (implemented as above), became the available invention the production of a relatively uniform sample over the entire sharpening surface of the tool 20 conceived. 45 with nunmehriger reference to the Fig. is illustrated 6A and 6B an execution form of a generally worthwhile Schärfers 100. The sharp 100 is similar to the sharp 60 with the exception that he exhibits at least a ring channel 110 arranged in its lateral surface 62. The ring channel and/or the ring channels 110/separates the sharpening surface 62 separates separate surface ranges 120 in at least two, preferably three or more. so the surface ranges 120 have typically, but not necessarily approximately the same axial (i.e. spreading) dimensions 122 (i.e. they vary within approximately 10%). The ring channels 110 exhibit typically in each case an axial dimension 112 in the order of magnitude from approximately 1 to approximately 10% (preferably about 4 to approximately 7%) of the entire axial dimension 102 of the Schärfers 100. In an execution form the depth 116 is the Ringkanä 55 le 110 more largely or equivalent about (not represented) the height of the teeth 64 '. In the depth 116 of the ring channels 110 between approximately 20 and about 50% constitutes another 6 RKs 413,669 B execution form the wall thickness 104 of the cylindrical ring 63. The ring channels can exhibit further tapered edges 114, which facilitate an interference of the teeth 64 ' into the whet-stone sharpening tool 20. In the represented and descriptive execution forms the channels 110 extend extent-moderately in a direction, which essentially runs orthogonal to the axle 67 (i.e. in an angle of incidence 65 of 90°). The angle of incidence 65 of the channels 110 can be varied however e.g. in such a manner that the channels 110 run sprialförmig along the lateral surface 62 of the Schärfers IO, without going off thereby the thought and range of the available invention. The sharp 100 knows teeth 64 ' of essentially everyone the specialist admitted geometry to exhibit, so for example diamantförmige extensions. In different execution forms the teeth 64 are however similar ' before with reference to the sharp 60 to the 15 (Fig. 4A and 4B) represented and descriptive teeth. For example the teeth 64 have ' typically dreieckförmigen cross section (as in Fig. 4B shown) and are oblong, so that they extend over the full axial dimension of the surface range 120, over which them are arranged. The sharp 100 can in a similar way as the sharp 60 for straightening the sharpening surface 27, 27 ', etc. of a whet-stone sharpening tool 20 (like before with reference to Fig. 5 described) to be used. The sharp 100 has the advantage that he becomes less easily blunt than the sharp 60. In certain sense one would not expect the increased resistance against, since the channels 110 in the sharp 100 62 che actually reduce the extent of the Schneidflä (e.g. over about 12% in an execution form with two channels 110, of which everyone exhibits an axial dimension 112 of approximately 6% of the entire axial dimension 102 of the Schärfers). Nothing the defiance produces a more uniform sample of grooves 32 and fields 34 (Fig for the sharp 110. 2) along the sharpening surface 27 of a whet-stone sharpening tool 20 (Fig. 1 and 5) and can supply from there cellulose with improved quality, as is more near described later still with reference to example 3. Without wanting, become to limit itself to a certain theory the teeth 64, 64 ' probably first of all at the employment edge 85 of the Schärfers blunt (see Fig. 5). With the training of one or more channels 110 in the surface 62 of the Schärfers the latter is divided into two or more surface ranges 120 (described like before), from which everyone edges an employment as it were exhibits. It is conceivable from there that the sharp possesses 100 two or more employment edges, whereby the teeth of 64 ' blunt making forces are distributed on favourable way. From there of the Schärfers 100 seems to be improved, in order to produce a more uniform sample of grooves 32 and fields 34 along the length of a whet-stone sharpening tool 20. EXAMPLE 1 in accordance with the principles of the available invention were manufactured more attempt-sharply, in order to evaluate their achievement. More attempt-sharply were to that extent similar to the commercial 45 6x28-Spiralschärfern (the company Norton Canada, Inc., Hamilton, Ontario, Canada), when they exhibited a cylindrical ring with an axial dimension of approximately 73 mm and an outside diameter of approximately 111 mm. The teeth were aligned in an angle of incidence of for instance 28° and were in a distance of approximately 4.2 mm. More attempt-sharply of the available example differed from the commercial 6x28-Spiralschärfer, by it two as circular channels 110 essentially as in Fig. 6A represented and descriptive contained before, of which everyone exhibited an axial dimension (width) of approximately 4 mm and a depth of approximately 2.2 mm. The distances of the channels were so dimensioned that three surface ranges developed, of which everyone an axial dimension of approximately 22 mm exhibited. 55 EXAMPLE 2 7 RKs 413,669 B more attempt-sharply (herein than sharp 2-A designated), which in accordance with the parameters by example 1 was made, for straightening a sharpening surface of a whet-stone sharpening tool (model No. AZOINZVG with an axial dimension of approximately 2290 mm of the company Norton Canada, Inc., Hamilton, Ontario, Canada) were used. For comparison purposes 5 commercial 6x28-Spiralschärfer were venvendet for straightening a sharpening surface of another whet-stone sharpening tool (likewise model No. A701N7VG). Before straightening the whet-stones were straightened in each case in conventional way using one diamond schärfers No. 12 (the company Norton Canada, Inc.). IO the straightening procedure used in this example was similarly before with reference to Fig. 5 descriptive procedures. A first sharp was pressed into the sharpening surface of the whet-stone sharpening tool into a penetration depth by 0.5 mm beyond the point of spark and shifted then along the length of the same axially. Subsequently, the first sharp was rejected and a second sharp was pressed into a penetration depth by 0.76 mm and shifted in the same way. Then the second sharp was rejected and a third sharp was pressed into a penetration depth by 1.0 mm and shifted in the same way. Then the third sharp was rejected and a fourth sharp was pressed into a penetration depth by 1.1 mm and shifted in the same way. Before beginning of the straightening procedure the shift speed was computed using the following formula: BT = (60 x WG) x 0.90/(Ss x stock) BT = shift speed of the Schärfers in seconds of WG = axial one length of the whet-stone 25 Ss = rotation speed of the whet-stone in rpm stock = length of the Schärfers the computed shift speed permits an overlap of the Schärfers per revolution of the whet-stone of approximately 25 mm. The special straightening conditions were as follows: It brought 8 RKs to 413,669 B a visual examination of the sharpening surfaces of the whet-stone sharpening tools to light that under Venwendung the more attempt-sharply straightened tool a more uniform sample of grooves and fields exhibited over its length than under employment the more comparison-sharply straightened tool. In particular the grooves and fields at both ends of 5 of the tool straightened with the Versuchsschärfern were relatively sharply and well defined. In contrast to it straightened the tool with the Vergleichsschärfern pointed relatively sharp and defined grooves and fields at to an end (where the shift began) and relatively rounded off and seichtere grooves at the other end (where the shift ended) up. IO EXAMPLE of 3 in accordance with example 2 manufactured whet-stone sharpening tools were used for the production of cellulose. The sharpening test conditions were as follows: 9AT 413,669 B TABLE 1 characteristics of the cellulose sharpening temperature high-stably moderately stably fiber firmness (TEA test) 4100 m 3900 m brightness of the cellulose (ISO standard test) characteristics of the cellulose sharpening temperature high-stably moderately stably fiber firmness (TEA test) 4100 m 3900 m brightness of the cellulose (ISO standard test) the preceding examples and the description serve more attempt-sharply more comparison-sharply more attempt-sharply more comparison-sharply primarily for the illustration. Even if the invention were described on the basis an exemplary execution form, 15 it is naturally clear for the specialist that alterations can be accomplished to deviate without of the spirit of the invention. The range of the invention is to be understood in such a way that it is defined by the attached requirements by the description of the invention in the Besehreibungsteil or in the examples reduced, but rather. The modifications at the different criteria of the available invention, described before, are purely exemplary. Of course other modifications with the illustration examples can be made by the specialist. All these modifications and alterations fall in the framework and spirit of the available invention, as them are defined in the attached requirements. Patent claims: 1.Schärfer (60, 100) to straightening a sharpening surface of a Schleifwerkzeugs, comprehensively 30 a cylindrical body 11AT 413,669 B 19. Procedure for straightening a sharpening surface of a whet-stone sharpening tool suitable for the mechanical production of cellulose, comprehensively: making a Schärfers available according to requirement 1, swivelling installing of the Schärfers on a mechanism to the procedure along the axial dimension of the whet-stone sharpening tool, pressing the Schärfers in slightly to the sharpening surface of the whet-stone sharpening tool, rotating the whet-stone sharpening tool in such a manner that the sharp rolls over the sharpening surface of the tool, and shifting the Schärfers along the axial dimension of the whet-stone IO of Schleifwerkzeugs. 20. Procedure for the production of cellulose, comprehensively: making a Schärfers available according to requirement 1, swivelling installing of the Schärfers on a mechanism to the procedure along the 15 axial dimension of the whet-stone sharpening tool, pressing the Schärfers in slightly to the sharpening surface of the whet-stone sharpening tool, rotating the whet-stone sharpening tool, whereby the sharp rolls over the sharpening surface of the same, shifting the Schärfers along the axial dimension of the Schleifstein-20 of Schleifwerkzeugs, and using the whet-stone sharpening tool for mechanical sharpening from wood to cellulose. 25 Hiezu 5 sheets designs Austrian patent office RK 413,669 B 2006-04-15Blatt: 1IntCI.7: B24B 53/12FIG. 1 27 ' Austrian patent office RK 413,669 B 2006-04-15Blatt: 2IntCI.7: B24B 53/12^38 FIG. 3 Austrian patent office RK 413,669 B 2006-04-15Blatt: 3Int. Cl.7: B24B 53/12 FIG. 4A FIG.4B Austrian patent office RK 413,669 B 2006-04-15Blatt: 4InLCI/: B24B 53/12 84 - 60.100 FIG. 5 Austrian patent office RK 413,669 B 2006-04-15 sheets: 5 IntCI.7: B24B 53/12 FIG. 6AN \ 64 ' A burr is provided for dressing a grinding tool, such as the grinding surface of a pulpstone grinding tool used for mechanical preparation of wood pulp. The burr includes a cylindrical body portion, a plurality of teeth disposed on and protruding outward from the outer surface thereof, and at least one annular channel formed in the outer surface thereof. The burr may provide for a more uniform dress pattern in a grinding surface of a pulpstone grinding tool to provide improved consistency and quality of wood pulp produced thereby. 1. A burr adapted for dressing a grinding surface of a grinding tool, said burr comprising:
a cylindrical body portion having an outer surface; a plurality of teeth protruding radially outward from said outer surface; and at least one annular channel disposed in said outer surface. 2. The burr of claim 1 wherein said burr configured for dressing a grinding surface of a pulpstone grinding tool and said pulpstone grinding tool is adapted for mechanical preparation of wood pulp. 3. A burr for dressing a grinding surface of a pulpstone grinding tool adapted for mechanical preparation of wood pulp, said burr comprising:
a cylindrical body portion having an outer surface, a longitudinal axis, and an axial dimension; a plurality of teeth protruding radially outward from said outer surface; at least one annular channel disposed in said outer surface; and said burr being configured for dressing a grinding surface of apulpstone grinding tool adapted for mechanical preparation of wood pulp. 4. The burr of claim 3 wherein said outer surface comprises at least two grinding surface regions separated from one another by said at least one annular channel. 5. The burr of claim 4 wherein said at least two grinding surface regions include substantially equal axial dimensions. 6. The burr of claim 4 comprising three grinding surface regions. 7. The burr of claim 3 comprising two annular channels. 8. The burr of claim 3 wherein said at least one annular channel has an axial dimension ranging from about 1 to about 10 percent of the axial dimension of said cylindrical body portion. 9. The burr of claim 8 wherein said at least one annular channel has an axial dimension ranging from about 4 to about 7 percent of the axial dimension of said cylindrical body portion. 10. The burr of claim 3 wherein said at least one annular channel includes a radial depth dimension greater than or about equal to a radial height dimension of said teeth, said depth dimension and said height dimension being substantially perpendicular to said longitudinal axis. 11. The burr of claim 3 wherein said cylindrical body portion comprises a cylindrical ring having a radial thickness dimension, wherein said at least one annular channel includes a redial depth ranging from about 20 to about 50 percent of said radial thickness of said cylindrical ring. 12. The burr of claim 3 wherein said plurality of teeth are elongated. 13. The burr of claim 12 wherein said plurality of teeth comprise a substantially triangular cross section. 14. The burr of claim 12 wherein said plurality of teeth extend continuously along the axial dimension of a surface region upon which they are disposed. 15. The burr of claim 12 wherein said plurality of teeth extend in a direction offset from the longitudinal axis by a lead angle ranging from about 5 to about 75 degrees. 16. The burr of claim 15 wherein the lead angle ranges from about 20 to about degrees. 17. The burr of claim 12 wherein said teeth have a spacing ranging from about 0.5 to about 6.0 millimeters. 18. The burr of claim 3 wherein said plurality of teeth have a substantially pyramidal shape. 19. A burr for dressing a grinding surface of a pulpstone grinding tool, said burr comprising:
a cylindrical ring having an outer surface, a longitudinal axis, and an axial dimension; two annular channels disposed in said outer surface, said two annular channels dividing said outer surface into at three surface regions having approximately equal axial dimensions, each of said two annular channels including an axial dimension ranging from about 1 to about 10 percent of the axial dimension of the cylindrical ring; a plurality of elongated teeth protruding radially outward from said outer surface, said plurality of elongated teeth including substantially triangular cross sections and extending in a direction offset from said longitudinal axis by a lead angle ranging from about 5 to about 75 degrees; and said burr being useful for dressing a grinding surface of a pulpstone grinding tool. 20. A method of fabricating a burr useful for dressing a grinding surface of a pulpstone grinding tool adapted for mechanical preparation of wood pulp, said method comprising:
providing a cylindrical body portion having an outer surface; forming a plurality of teeth in the outer surface of the cylindrical body portion; and forming at least one annular channel in the outer surface of the cylindrical body portion. 21. A method of dressing a grinding surface of a pulpstone grinding tool adapted for mechanical preparation of wood pulp, said method comprising:
providing a burr including:
a cylindrical body portion having an outer surface; a plurality of teeth disposed on and protruding from the outer surface; at least one annular channel disposed in the outer surface; rotatably mounting the burr on an assembly adapted to traverse the axial dimension of the pulpstone grinding tool ; pressing the burr into contact with the grinding surface of the pulpstone grinding tool; rotating the pulpstone grinding tool, wherein the burr rolls over the grinding surface of the tool; and traversing the burr along the axial dimension of the pulpstone grinding tool. 22. A method of preparing wood pulp comprising:
providing a burr including:
a cylindrical body portion having an outer surface; a plurality of teeth extending from the outer surface; at least one annular channel disposed in the outer surface; rotatably mounting the burr on an assembly adapted to traverse the axial dimension of the pulpstone grinding tool; pressing the burr into contact with the grinding surface of the pulpstone grinding tool; rotating the pulpstone grinding tool, wherein the burr rolls over the grinding surface thereof; traversing the burr along the axial dimension of the pulpstone grinding tool; and using the pulpstone grinding tool to mechanically grind wood into wood pulp.
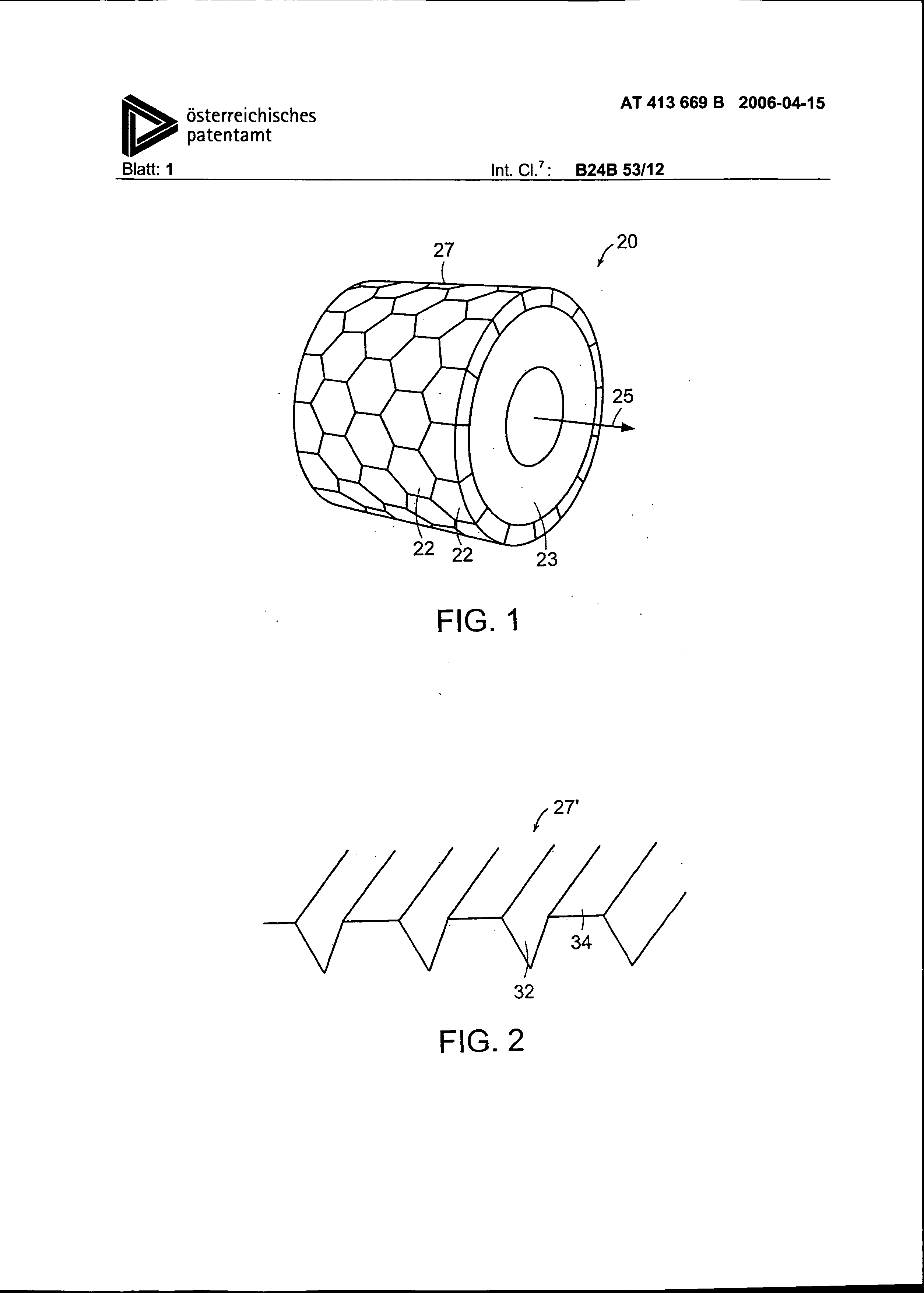
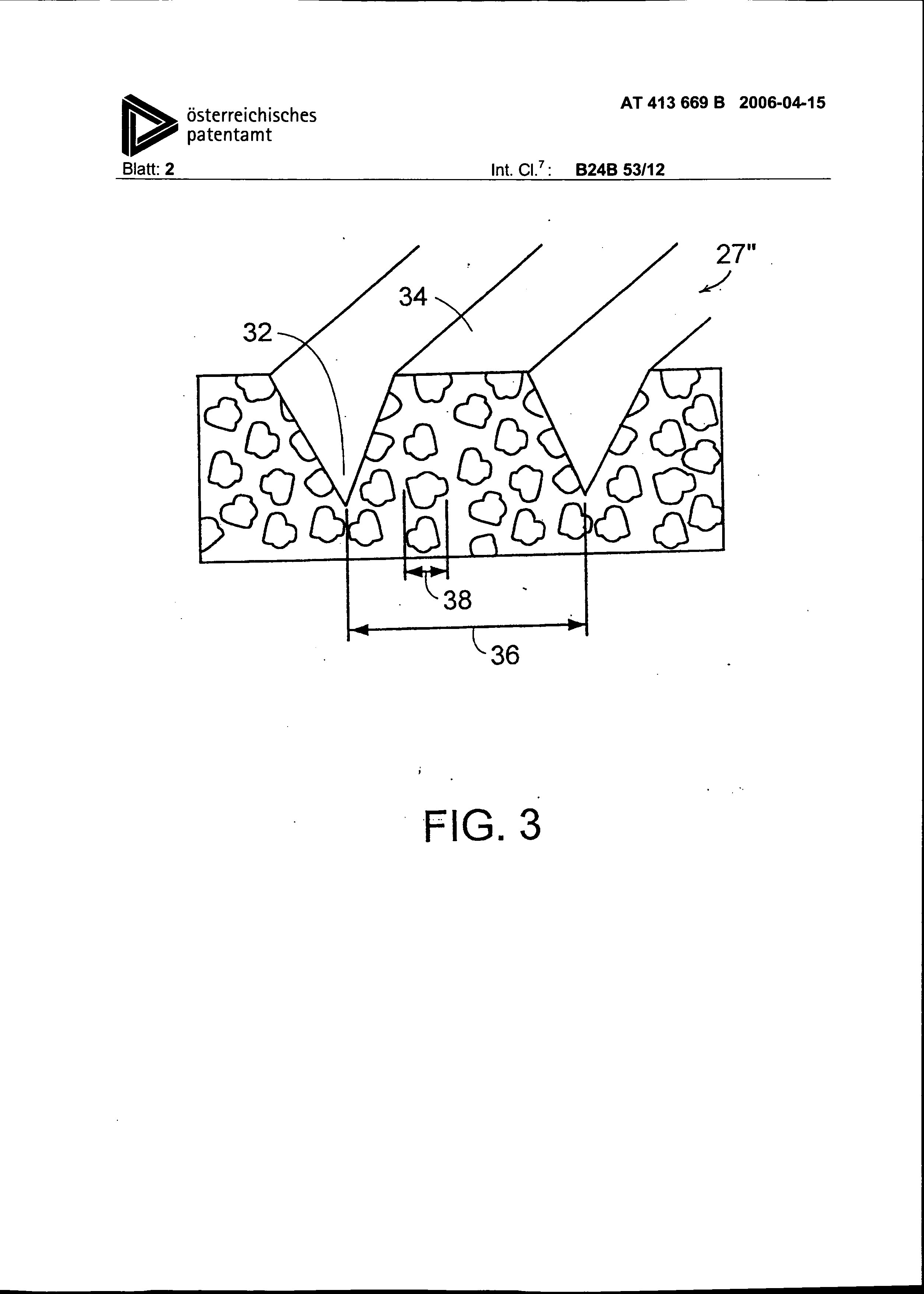


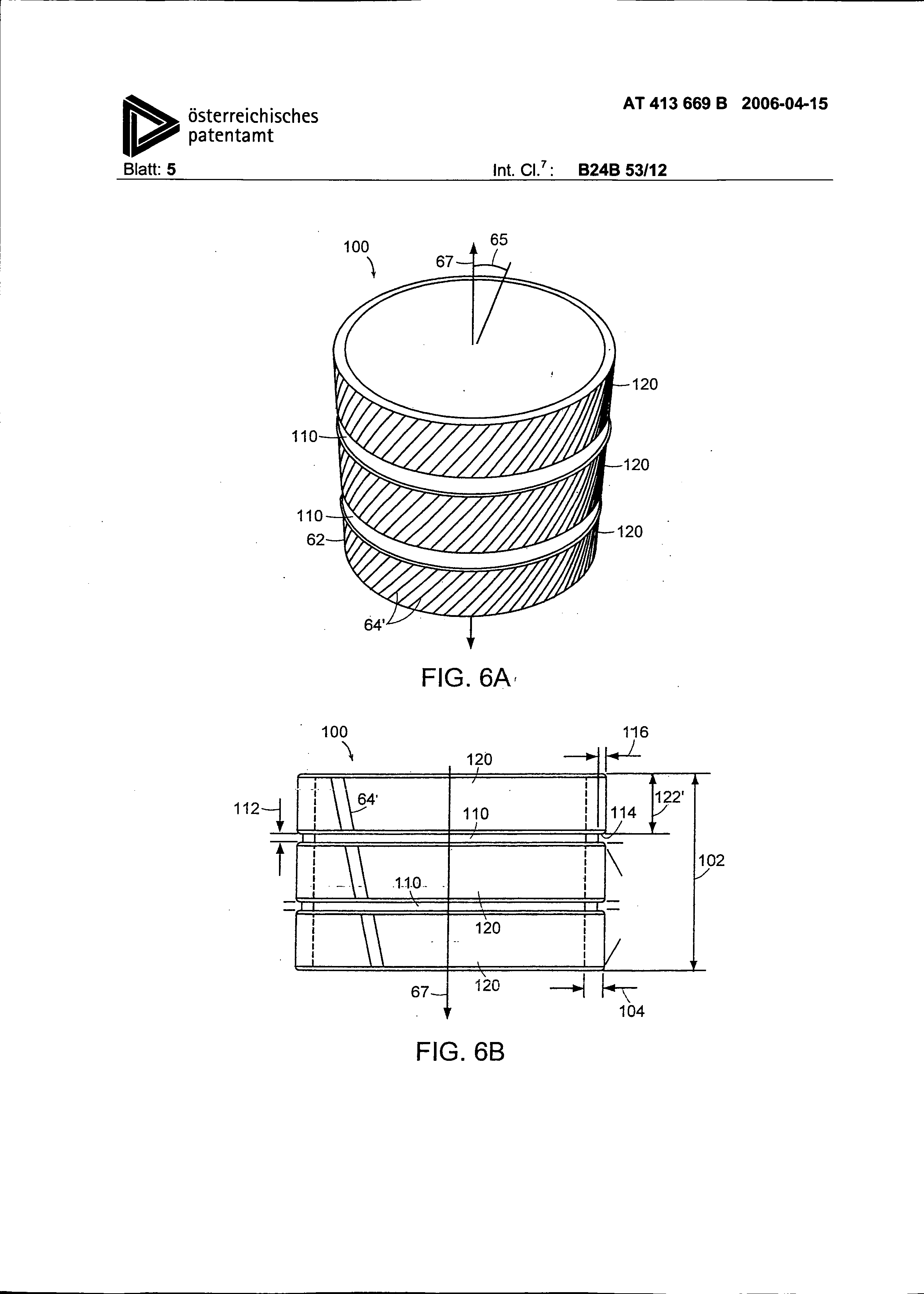