DOUBLE-BOTTOM SIDE-WELDED BAG
The present invention relates generally to flexible bags designed to hold food products such as bread. It is known to construct a plastic bag by folding a continuous sheet of a flexible material, such as thermoplastic, over on itself, then making an in-fold at the folded edge, to form a gusset, and then simultaneously cutting and heat sealing the folded sheet along spaced apart transverse lines that are perpendicular to the fold. Each individual bag formed in this manner has an “W” shaped cross section at the gusset. This type of bag is commonly referred to as a “bread bag” and is often used for packaging loaves of bread. The bread loaf is inserted into the bag through an open end that is opposite the gusset. The open end is then tied shut in an appropriate manner to often present what is called the “pony-tail” end of the bag. When fresh warm bread and similar bakery products are packaged in plastic bags, the moisture from the bread is retained and often condenses on the inside of the package. This is a particular problem when bread is stored in bags formed from polyethylene where the bread contacts the bottom gusset of the bag. Typically, the bottom gusset faces the consumer and contains the product identifying information and the supplier's trade-marks and logos. Product information and logos are often printed directly on the bag or affixed using a label at this location. Because bread bags are usually transparent or translucent, any moisture that condenses on the inside of the polyethylene bottom gusset causes the package to have an unsightly appearance and decreases the visual quality of the food. There is therefore a need for improved flexible bags which solves the above problems and can be efficiently manufactured. The present invention is directed to a double-bottom bag comprising an outer web and an inner web having an open mouth and an opposing bottom, where the outer web has a first side edge, an opposing second side and is folded upon itself thereby defining a front panel having a length and a back panel having a length. The outer web further includes an inward-facing cross-sectional gusset opposite the open mouth of the bag and centered along the width of the bag which joins the front panel to the back panel and forms an outer bottom portion of the bag. The inner web has a first side edge, an opposing second side and is folded upon itself thereby defining a front panel having a length which is less than the length of the front panel of the outer web and a back panel having length which is less than the length of the back panel of the outer web. The inner web further includes an inward-facing cross-sectional gusset opposite the open mouth of the bag and centered along the width of the bag which joins the front panel to the back panel and forms an inner bottom portion of the bag. The bag further comprises a first side-seam affixing the first side edge of both the inner and outer webs together and affixing the front and back panels of the outer web together along the first side edge. The bag still further includes an opposing second side-seam affixing the opposing second side edge of both the inner and outer webs together and affixing the front and back panels of the outer web together along the second side edge. The bag of the present invention is designed such that the inward-facing cross-sectional gussets of both the inner and outer webs expand to form a square cross-sectional portion upon receiving a material to be packaged. One advantage of the present invention provides is a separate surface of an inner web where moisture from the bread or other bakery products may condense without affecting the appearance of product identifying information printed on an outer web of the bag. The present invention also provides the convenience of a square or rectangular bottom gusset cross sectional area where product information can be printed and viewed by the consumer. Further features and advantages of the present invention will become apparent from the following detailed description, taken in combination with the appended drawings, in which: In accordance with the practice of the present invention, a representative double-bottom bag as described herein is shown in In accordance with the present invention, the front panel 33 of inner web 30 has a length which is less than the length of the front panel 23 of outer web 20. Front panel 33 may have a length which is about 75%, 70%, 65%, 60%, 55%, 50%, 45%, 40%, 35%, 30%, 25%, 20%, 15%, 10% or 5% of the length of front panel 23 of outer web 20. Preferably, as illustrated in Optionally, the back panel 25 of outer web 20 may have a length which is greater than the length of the front panel 23 of outer web 20. Back panel 25 may have a length which is 5%, 10%, 15%, 20% greater than the length of front panel 23 of outer web 20. As illustrated in Any suitable packaging material may be used to formed outer and inner webs 20 and 30. Preferably, outer web 20 is formed from a heat-fusible material. In one embodiment, it is desirable to form outer web 20 from a flexible thermoplastic film which is heat-fusible. In another embodiment, it is desirable to from outer 20 from a flexible thermoplastic film which is heat-fusible and substantially transparent. Preferably, outer web 20 is fabricated from a polyolefin thermoplastic material, which may include, but not limited to polyethylene homopolymer and copolymers, polyethylene blends, polypropylene homopolymer and copolymers, and blends of polyethylene and other thermoplastic materials. Preferably, outer web 20 comprises a blend of low density polyethylene (LDPE) and linear low density polyethylene (LLDPE), a blend of 10% by weight of low density polyethylene (LDPE) and 90% by weight of linear low density polyethylene (LLDPE), a blend of 40% by weight of low density polyethylene (LDPE) and 60% by weight of linear low density polyethylene (LLDPE), or a blend of 60% by weight of low density polyethylene (LDPE) and 40% by weight of linear low density polyethylene (LLDPE). Outer web 20 may comprise a monolayer or multilayer structure. Referring now the Inner web 30 may be formed from the same material as outer web 20 or a different material. Preferably, inner web 30 is formed from a heat-fusible material. In one embodiment, it is desirable to from inner web 30 from a flexible thermoplastic film which is heat-fusible. In another embodiment, it is desirable to form inner 30 from a flexible thermoplastic film which is heat-fusible and substantially transparent. It may also be desirable to emboss at least one surface of inner web 30. Embossing reduces the total surface area of inner web 30 that comes into contact with the moistened surface of a bread product. In another embodiment, inner web 30 is embossed and formed from a flexible thermoplastic film which is substantially opaque. Preferably, inner web 30 is fabricated from a polyolefin thermoplastic material, which may include, but not limited to polyethylene homopolymer and copolymers, polyethylene blends, polypropylene homopolymer and copolymers, and blends of polyethylene and other thermoplastic materials. Inner web 30 may comprise a monolayer or multilayer structure. Referring now the The above description and the following examples illustrate certain embodiments of the present invention and are not to be interpreted as limiting. Selection of particular embodiments, combinations thereof, modifications, and adaptations of the various embodiments, conditions and parameters normally encountered in the art will be apparent to those skilled in the art and are deemed to be within the spirit and scope of the present invention. In all the following examples, the outer web 20 structures were produced using a blown film coextrusion apparatus and methods which are well known to those skilled in the art. The inner web 30 structures were produced using cast coextrusion film apparatus and methods which are well known to those skilled in the art. Inner web 30 was embossed by pressing and simultaneously cooling a melt-plastified film against an engraving cylinder. Example 1 is one embodiment of an outer web 20 as illustrated in Layer 201 is a blend of 43% by weight of low density polyethylene (LDPE) having density of 0.922 g/cm3, 54% by weight of linear low density polyethylene (LLDPE) having density of 0.918 g/cm3, and about 3% by weight of processing additives. Exemplary of a commercially available LDPE is ExxonMobil™ LDPE LD 123.LN supplied by Exxon Mobil Chemical Company (Houston, Tex., USA). Exemplary of a commercially available LLDPE is ExxonMobil™ LLDPE LL 1002YB supplied by Exxon Mobil Chemical Company (Houston, Tex., USA). Layer 202 is a blend of 60% by weight of linear low density polyethylene (LLDPE) having density of 0.919 g/cm3, 10% by weight of polyethylene regrind, 27.5% by weight of low density polyethylene (LDPE) having density of 0.922 g/cm3, and about 2.5% by weight processing additives. Exemplary of a commercially available LLDPE is DOWLEX™ TG 2085B supplied by Dow Chemical Company (Midland, Mich., USA). Layer 203 has the same composition as Layer 201. Layer 301 is a blend of 29.5% by weight of linear low density polyethylene (LLDPE) having a density of 0.941 g/cm3, 25% by weight of high density polyethylene (HDPE) having a density of 0.96 g/cm3, 23% by weight of low density polyethylene (LDPE) having density of 0.918 g/cm3. 21% by weight of linear low density polyethylene (LLDPE) having a density of 0.918 g/cm3, and about 1.5% by weight processing additives. Exemplary of a commercially available LLDPE having a density of 0.941 g/cm3is ExxonMobil™ LLDPE LL 3404.48 supplied by Exxon Mobil Chemical Company (Houston, Tex., USA). Layer 302 is a blend of 25% by weight of high density polyethylene (HDPE) having a density of 0.96 g/cm3, 22% by weight of linear low density polyethylene (LLDPE) having a density of 0.918 g/cm3, 18% by weight of linear low density polyethylene (LLDPE) having a density of 0.941 g/cm3, 18% by weight of low density polyethylene (LDPE) having density of 0.918 g/cm3, 12% by weight of a white pigmented low density polyethylene masterbatch, 2% by weight of polyethylene regrind, and about 2% by weight processing additives. Exemplary of a commercially available white pigment masterbatch is POLYBATCH® 8000 AP supplied by A. Schulman, Inc. (Akron, Ohio, USA). Layer 303 has the same composition as Layer 301. Webs 20 and 30 of Example 1 were then evaluated for their physical and optical properties. The results are shown in TABLES 1 and 2 as follows: To produce a bag as illustrated in The present invention relates to flexible double-bottom bags having an outer web which is folded upon itself to form a front panel and a back panel The outer web includes an inward-facing cross-sectional gusset opposite the open mouth of the bag and centered along the width of the bag joining the front panel to the back panel and creating an outer bottom portion of the bag. The bags also have an inner web which is folded upon itself to form a front panel and a back panel. 1. A double-bottom bag having an open mouth, an opposing bottom and a width, comprising:
a. an outer web having a first side edge, an opposing second side edge and folded upon itself thereby defining:
i. a front panel having a length; ii. a back panel having a length; iii. an inward-facing cross-sectional gusset opposite the open mouth and centered along the width of the bag which joins the front panel to the back panel and forms an outer bottom portion of the bag; b. an inner web having a first side edge, an opposing second side and folded upon itself thereby defining:
i. a front panel having a length which is less than the length of the front panel of the outer web; ii. a back panel having length which is less than the length of the back panel of the outer web; iii. an inward-facing cross-sectional gusset opposite the open mouth and centered along the width of the bag which joins the front panel to the back panel and forms an inner bottom portion of the bag; c. a first side-seam affixing the first side edge of both the inner and outer webs together, and affixing the front and back panels of the outer web together along the first side edge; d. an opposing second side-seam affixing the opposing second side edge of both the inner and outer webs together, and affixing the front and back panels of the outer web together along the opposing second side edge; and e. wherein the inward-facing cross-sectional gussets of both the inner and outer webs expand to form a square or rectangular cross-sectional bag bottom upon receiving a material to be packaged. 2. A bag according to 3. A bag according to 4. A bag according to 5. A bag according to 6. A bag according to 7. A bag according to 8. A bag according to 9. A bag according to 10. A bag according to 11. A bag according to 12. A bag according to 13. A bag according to 14. A bag according to 15. A bag according to 16. A bag according to 17. A bag according to 18. A bag according to 19. A bag according to 20. A bag according to BACKGROUND OF THE INVENTION
SUMMARY OF THE INVENTION
BRIEF DESCRIPTION OF THE DRAWINGS
DETAILED DESCRIPTION OF THE INVENTION
WORKING EXAMPLES
Example 1
Thickness (microns) 31 Elmendorf Tear Strength MD/TD (gram- 114/763 force) Secant Modulus MD/TD (Psi) 22000/27000 Elongation to Break (%) 400/550 Peak Stress MD/TD (Psi) 3300/2200 Haze 7.5 Gloss at 60° 100 Puncture to Break (Pound-force) 4.9 Seal Strength @ 140° C., 60 psi (grams/inch) 1600 Coefficient of Friction Kinetic/Static 0.16/0.14 Thickness (microns) 20-30 Elmendorf Tear Strength MD/TD 10/140 (gram-force) Elongation to Break (%) MD 160-600 Elongation to Break (%) MD 300-800 Opacity 50

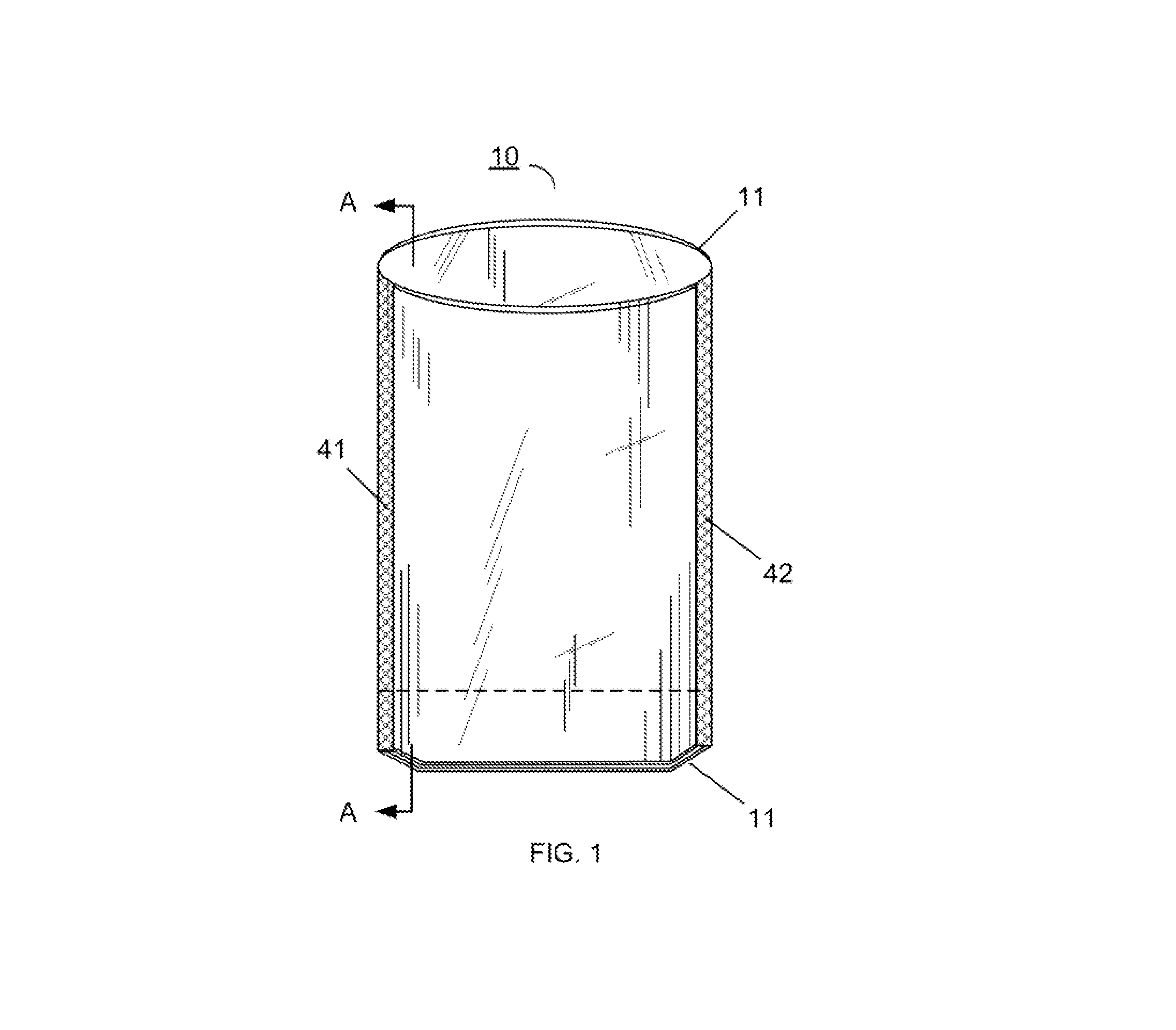
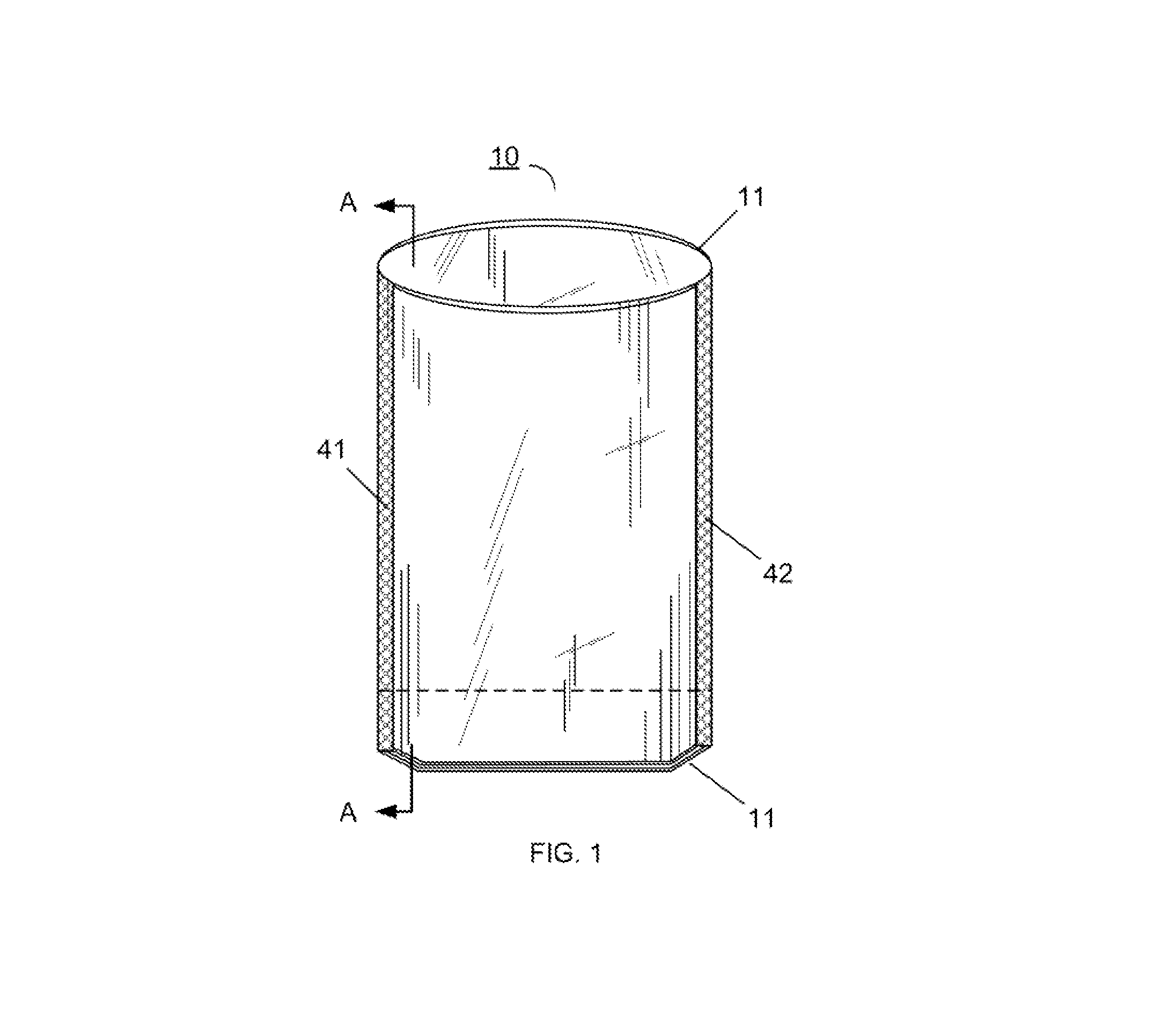
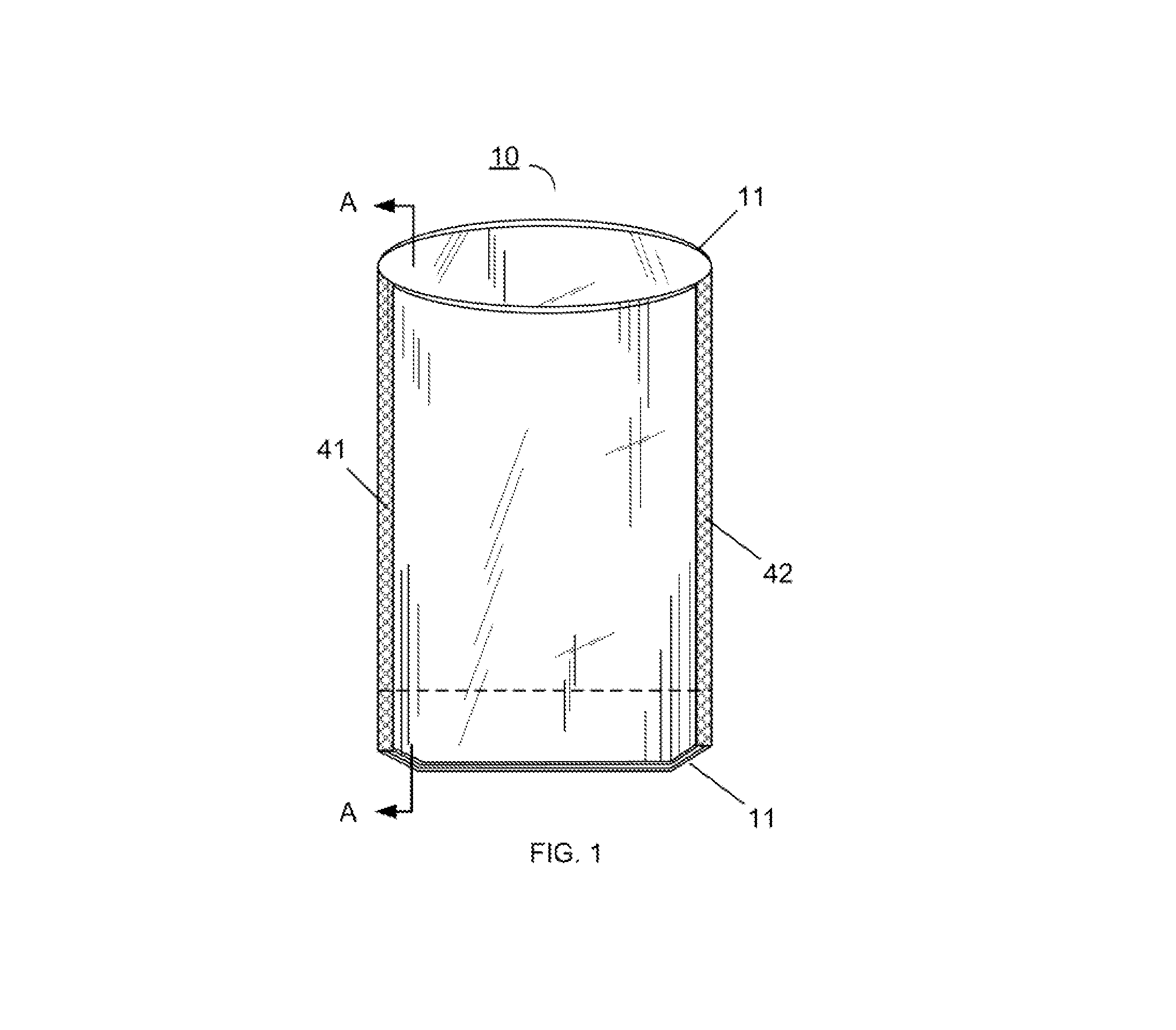
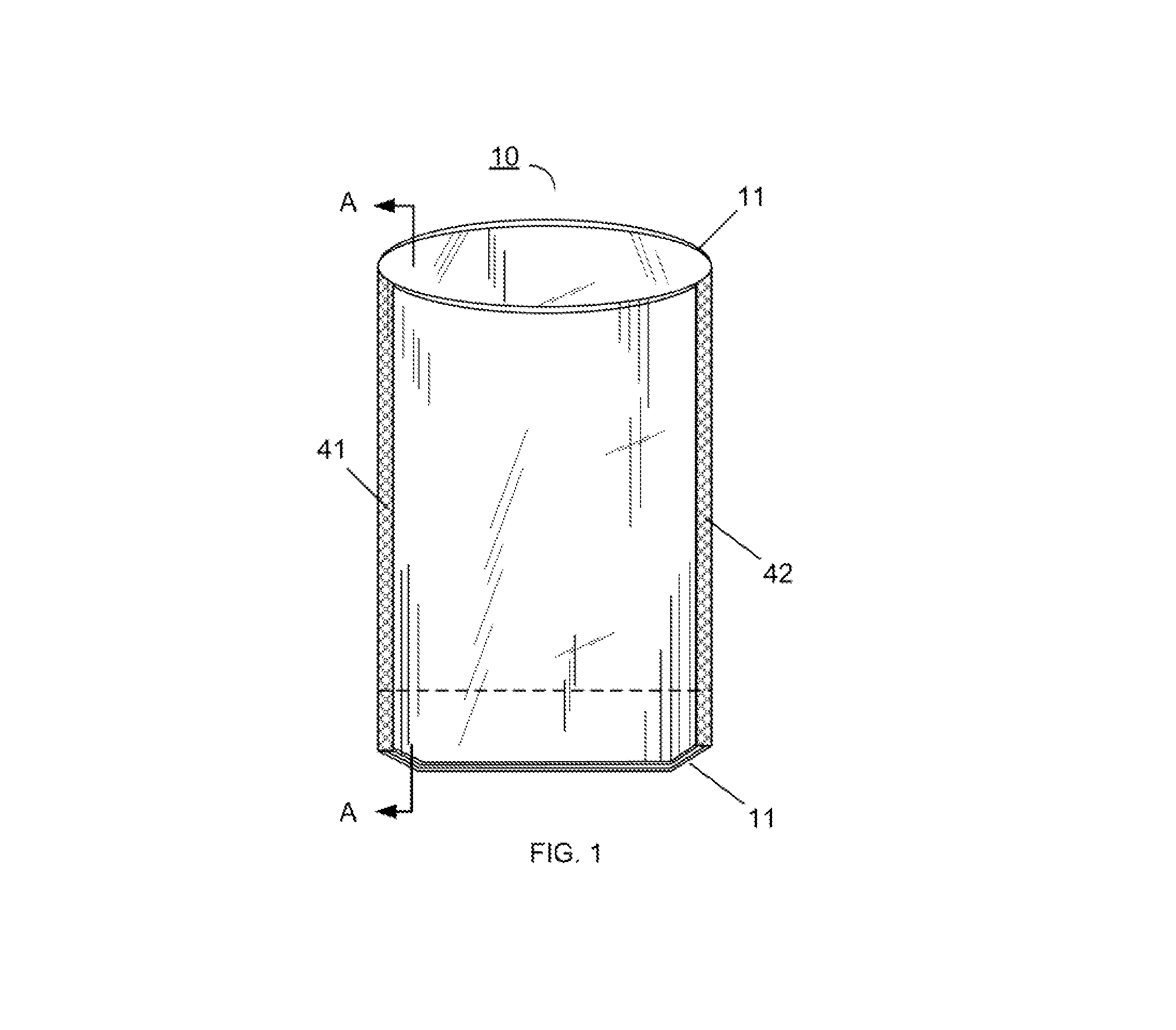