BRAKE SYSTEM AND METHOD FOR BRAKING A MOTOR VEHICLE
The present application claims the benefit under 35 U.S.C. § 119 of German Patent Application No. DE 102019210271.9 filed on Jul. 11, 2019, which is expressly incorporated herein by reference in its entirety. The present invention relates to a brake system for braking a motor vehicle and to a method for braking a motor vehicle. Motor vehicles having dual circuit-type braking systems have two mutually independent line circuits for actuating the brakes of the individual wheels. Even if one of the line circuits fails, this allows for a controlled deceleration of the motor vehicle using the remaining line circuit. The two line circuits share a common master brake cylinder. There are basically five different systems with regard to the actuation of the wheels of the different axles, i.e. a II-split, an X-split, an LL-split, an HT-split, and an HH split. The line circuits in different systems differ in the number and placement of the wheels that are braked by the respective line circuits. For a better emergency running strategy in a failure of components, an electronic brake system is described in EP Patent No. EP 0728086 B1. This electronic brake system has a central module and brake modules allocated to the brake circuits or wheel groups, which are able to communicate with one another. The present invention provides a brake system for a motor vehicle and a method for braking a motor vehicle. According to a first aspect, the present invention thus pertains to a brake system for a motor vehicle having a first hydraulic brake device and a second hydraulic brake device. The first hydraulic brake device brakes the wheels on a first axle of the motor vehicle, but not on a second axle of the motor vehicle, and has a first control unit which controls the braking operation of the wheels on the first axle of the motor vehicle. The second hydraulic brake device brakes the wheels on the second axle of the motor vehicle, but not on the first axle of the motor vehicle, and has a second control unit, which controls the braking operation of the wheels on the second axle of the motor vehicle. The first control unit is coupled with the second control unit via a communication channel. The first control unit and the second control unit are configured to receive data that are relevant for the control of the braking operation. Based on the received data, the first control unit transmits a data signal via the communication channel to the second control unit. According to a second aspect, the present invention relates to a method for braking a motor vehicle in which a braking operation of wheels on a first axle of the motor vehicle is controlled by a first control unit, and a braking operation of wheels on a second axle of the motor vehicle is controlled by a second control unit. The first control unit is coupled with the second control unit via a communication channel. The first control unit receives first data that are relevant for the control of the braking operation. The second control unit receives second data that are relevant for the control of the braking operation. On the basis of the first data received by the first control unit, the first control unit generates a data signal and transmits it via the communication channel to the second control unit. Given an intact communication channel, the second control unit controls the braking operation of the wheels of the second axle using the received data signal. In an interruption of the communication channel, the second control unit controls the braking operation of the wheels of the second axle of the motor vehicle based on the second data received by the second control unit. Preferred embodiments of the present invention are described herein. In accordance with an example embodiment of the present invention, a brake system is described which is designed in an axle-wise fashion, which means that the first hydraulic brake device and the second hydraulic brake device are designed to carry out braking operations of the wheels of the corresponding axles independently of one another. In particular, the brake system preferably has no common master brake cylinder. The first hydraulic brake device and the second hydraulic brake device are preferably capable of building up pressure on their own in order to brake the wheels of the corresponding axle. In addition, the first control unit and the second control unit may be configured to model the pressure, in particular in order to implement ABS and/or ESP functionalities. Preferably, the first hydraulic brake device and the second hydraulic brake device are coupled only electronically via the communication channel between the first control unit and the second control unit but have no hydraulic connection. This makes it possible to dispense with long hydraulic lines between the front axle and the rear axle, which is advantageous in terms of the space requirement. The axle-wise brake system builds on conventional components used in brake systems that are not based on axles and thus in essence does not require new technology. In particular, the first hydraulic brake device and the second hydraulic brake device may have an essentially identical development, which simplifies a series production. With regard to the output power, the drives of the first hydraulic brake device and the second hydraulic brake device are able to be selected in accordance with the axle volume. On the front axle, for example, approximately twice the power may be required than on the rear axle. The first control unit forms a master unit, which provides the received data via the communication channel to the second control unit acting as a slave unit. However, in order to enable the second control unit to continue the control of the braking operation even if the communications link between the first control unit and the second control unit has failed, the present invention provides that the second control unit also receive data that are relevant for the control of the braking operation. However, most of the data typically required for the control of the braking operation are preferably acquired with the aid of sensors which are linked only with the first control unit, so that additional direct data lines between the individual sensors and the second control unit are not required. Preferably, the second control unit is coupled only with sensors that are situated in the region of the second axle, in particular closer to the second axle than to the first axle, such as acceleration sensors or wheel-speed sensors for measuring a wheel speed of the wheels of the second axle. As a result, an ABS functionality and/or an electronic brake force distribution (EBD) is still able to be made available even in a failure of the communications link between the first control unit and the second control unit. The first axle is preferably a front axle of the motor vehicle, and the second axle is a rear axle of the motor vehicle. The data relevant for the control of the braking operation in particular include the acquired sensor data from different sensors of the motor vehicle, some of which in particular could be wheel-speed sensors measuring the wheel speeds of the wheels of the first axle, wheel-speed sensors measuring the wheel speeds of the wheels of the second axle, a yaw rate sensor, a transverse acceleration sensor, a steering angle sensor, and a sensor for determining the inlet pressure of a hydraulic brake unit. The data relevant for the control of the braking operation may particularly include a driver brake input, which, for example, is able to be ascertained on the basis of sensor data of a travel sensor and/or a pressure sensor on the brake pedal of the motor vehicle, for instance. According to one preferred embodiment of the brake system according to the present invention, the first hydraulic brake device includes a sensor device for detecting a driver brake input. In particular, the first hydraulic brake device may include a travel sensor and/or a pressure sensor on the brake pedal of the motor vehicle, which output(s) sensor signals for outputting the driver brake input. According to one preferred embodiment of the brake system according to the present invention, the first hydraulic brake device includes an hydraulic fallback level, which makes it possible for a driver of the motor vehicle to build up brake pressure even without support. According to one preferred further development of the brake system according to the present invention, the first and the second control unit are coupled with different devices in order to receive the data that are relevant for the control of the braking operation. For example, the second control unit is able to be coupled with a wheel-speed sensor on the second axle and to receive the measured wheel speed of the wheels of the second axle. The first control unit is able to be coupled with further sensors and to receive further data relevant for the control of the braking operation. The first control unit is able to convey these received further data relevant for the control of the braking operation to the second control unit or transmit a control signal based on these data to the second control unit, while the second control unit transmits the measured wheel speed of the wheels of the second axle to the first control unit. According to one preferred further development of the brake system in accordance with the present invention, given an intact communication channel, the second control unit is configured to carry out the braking operation of the wheels of the second axle of the motor vehicle using the received data signal. The data received by the second control unit itself may be utilized as supplementation. According to one preferred further development of the brake system in accordance with the present invention, in the event of an interruption of the communication channel, the second control unit is configured to control the braking operation of the wheels of the second axle of the motor vehicle on the basis of the data received by the second control unit. While the second control unit may no longer be able to access the data acquired by the first control unit because the communications link has been severed, it is still able to carry out the braking operation on the basis of the data it received itself. According to one preferred further development of the brake system in accordance with the present invention, the second control unit is configured to transmit a further data signal on the basis of the received data via the communication channel to the first control unit. Given an intact communication channel, the first control unit is configured to carry out the braking operation of the wheels of the first axle using the further data signal. The communication channel thus allows for a bidirectional communication between the first control unit and the second control unit. In a normal operation, both control units are able to access all data, whereas in an interruption in the communication channel, the control units utilize only the data they received themselves for the control of the braking operation. According to one preferred further development of the present invention, the brake system has at least one sensor device, which is configured to generate the data that are relevant for the control of the braking operation and to transmit the data to the first control unit and/or the second control unit. In this case, the devices that generate the data relevant for the braking are therefore themselves part of the brake system. According to one preferred further development of the brake system in accordance with the present invention, the at least one sensor device includes a wheel-speed sensor which ascertains the rotational speed of a wheel of the second axle of the motor vehicle and transmits a sensor signal to the second control unit on the basis of the ascertained rotational speed. According to one preferred further development of the brake system in accordance with the present invention, the at least one sensor device includes an acceleration sensor, which ascertains an acceleration of the motor vehicle and transmits a sensor signal to the second control unit on the basis of the ascertained acceleration. According to one preferred further development of the brake system in accordance with the present invention, the acceleration sensor and/or the second control unit is/are configured to ascertain a deceleration of the motor vehicle in the longitudinal direction on the basis of the ascertained acceleration of the motor vehicle. When calculating the deceleration of the motor vehicle in the longitudinal direction, in particular the gradient of the surface on which the vehicle is traveling is able to be taken into account. According to one preferred further development of the brake system in accordance with the present invention, the wheel-speed sensor and/or the second control unit is/are configured to calculate a deceleration of the motor vehicle in the longitudinal direction on the basis of the ascertained rotational speed of a wheel of the second axle of the motor vehicle. Identical or functionally equivalent elements and devices in all of the figures have been provided with the same reference numerals. The numbering of method steps is used for the sake of clarity and in general is not meant to imply a certain time sequence. It is particularly also possible to carry out a plurality of method steps simultaneously. First control unit 22 First control unit 22 During a normal operation, that is to say, with an operative data link via communication channel 7, first control unit 22 If the data connection via communication channel 7 is interrupted due to a fault, then first control unit 22 Via a simulator valve 83, cylinder 82 is hydraulically connected to a simulator unit 84 for the generation of a brake pressure. According to further embodiments, however, instead of simulator unit 84, it is also possible to provide an electromechanical brake booster, in particular an iBooster developed by the Bosch company. As a result, the brake pressure is able to be completely generated by simulator unit 84, but the driver is also able to contribute to the buildup of the brake pressure. Via an isolation valve 85, cylinder 82 is furthermore hydraulically connected to a first brake unit 21 A second hydraulic brake device 3 First hydraulic brake device 2 Second control unit 32 Based on the sensor data received from first device 61 Based on the sensor data received from second device 62 First control unit 22 According to one variant, it may be provided that brake system 1 Furthermore, shorten the braking distance, first control unit 22 If one of the hydraulic circuits of first hydraulic brake device 2 In the event of a failure of a pump 213, 313, the driver displaces the volume of the fluid via isolation valve 85 into first brake unit 21 In the event of a power failure, simulator valve 83 remains closed and isolation valve 85 is open. In this case, the driver is able to build up pressure directly in the wheel cylinders. In an interruption in communication channel 7, second hydraulic brake device 2 In addition, it may be provided that second control unit 32 Second control unit 32 In addition, second control unit 22 In this context, As an alternative, it may be provided to determine the position of the motor vehicle by measuring the direction of the magnetic field lines of a magnetic field of the earth, for which a periodic calibration may be provided due to the local deviations. It may additionally be provided to determine the position information of the motor vehicle from the comparison of the deceleration which is ascertained from the wheel speeds, and the deceleration which is ascertained from the acceleration a_x of the motor vehicle in the longitudinal direction. In the equation a_x=a+g·sin(a), the acceleration a_x in the x-direction is able to be obtained directly from the sensor data of acceleration sensor 622, while deceleration a is calculated from the change in the wheel speed. The position information, i.e. gradient α, follows therefrom. In addition, it may be provided that second control unit 32 In a first step S1, data that are relevant for the control of the braking operation are received by first control unit 22 In a second step S2, second control unit 32 The first two method steps S1, S2 are able to be carried out simultaneously or in any desired sequence. In a further method step S3, first control unit 22 If it is determined in a further method step S4 that the data transmission was successful, then first control unit 22 However, if it is determined, S4, that the data transmission was faulty or the transmission via communication channel 7 is impossible, then first control unit 22 A brake system for a motor vehicle, having a first hydraulic brake device configured to brake wheels on a first axle of the motor vehicle, a first control unit configured to control the braking operation of the wheels on the first axle; and a second hydraulic brake device configured to brake the wheels on a second axle of the motor vehicle, and a second control unit configured to control the braking operation of the wheels on the second axle. The first control unit is coupled with the second control unit via a communication channel. The first control unit and the second control unit are each configured to receive data that are relevant for the control of the braking operation, the first control unit furthermore being configured to transmit a data signal on the basis of the received data via the communication channel to the second control unit. 1. A brake system for a motor vehicle, comprising:
a first hydraulic brake device which is configured to brake wheels on a first axle of the motor vehicle, the first hydraulic brake device including a first control unit which is configured to control a braking operation of the wheels on the first axle of the motor vehicle; and a second hydraulic brake device which is configured to brake wheels on a second axle of the motor vehicle, the second hydraulic brake device including a second control unit configured to control a braking operation of the wheels on the second axle of the motor vehicle, the first control unit being coupled with the second control unit via a communication channel; wherein the first control unit and the second control unit are each configured to receive data that are relevant for the control of the braking operation, and the first control unit is further configured to transmit a data signal, based on the received data, via the communication channel to the second control unit. 2. The brake system as recited in 3. The brake system as recited in 4. The brake system as recited in 5. The brake system as recited in 6. The brake system as recited in at least one sensor device configured to generate the data that are relevant for the control of the braking operation and to transmit the data to the first control unit and/or to the second control unit. 7. The brake system as recited in 8. The brake system as recited in 9. The brake system as recited in 10. The brake system as recited in 11. A method for braking a motor vehicle, a braking operation of wheels on a first axle of the motor vehicle being controlled by a first control unit, and a braking operation of wheels on a second axle of the motor vehicle being controlled by a second control unit, the first control unit being coupled with the second control unit via a communication channel, the method comprising the following steps:
receiving first data that are relevant for the control of the braking operation by the first control unit; receiving second data that are relevant for the control of the braking operation by the second control unit; and transmitting a data signal generated based on the received first data from the first control unit via the communication channel to the second control unit; wherein when communication channel is intact, the second control unit controlling the braking operation of the wheels of the second axle using the received data signal; and wherein in the event of an interruption in the communication channel, the second control unit controlling the braking operation of the wheels of the second axle of the motor vehicle based on the second data received by the second control unit.CROSS REFERENCE
FIELD
BACKGROUND INFORMATION
SUMMARY
BRIEF DESCRIPTION OF THE DRAWINGS
DETAILED DESCRIPTION OF EXAMPLE EMBODIMENTS


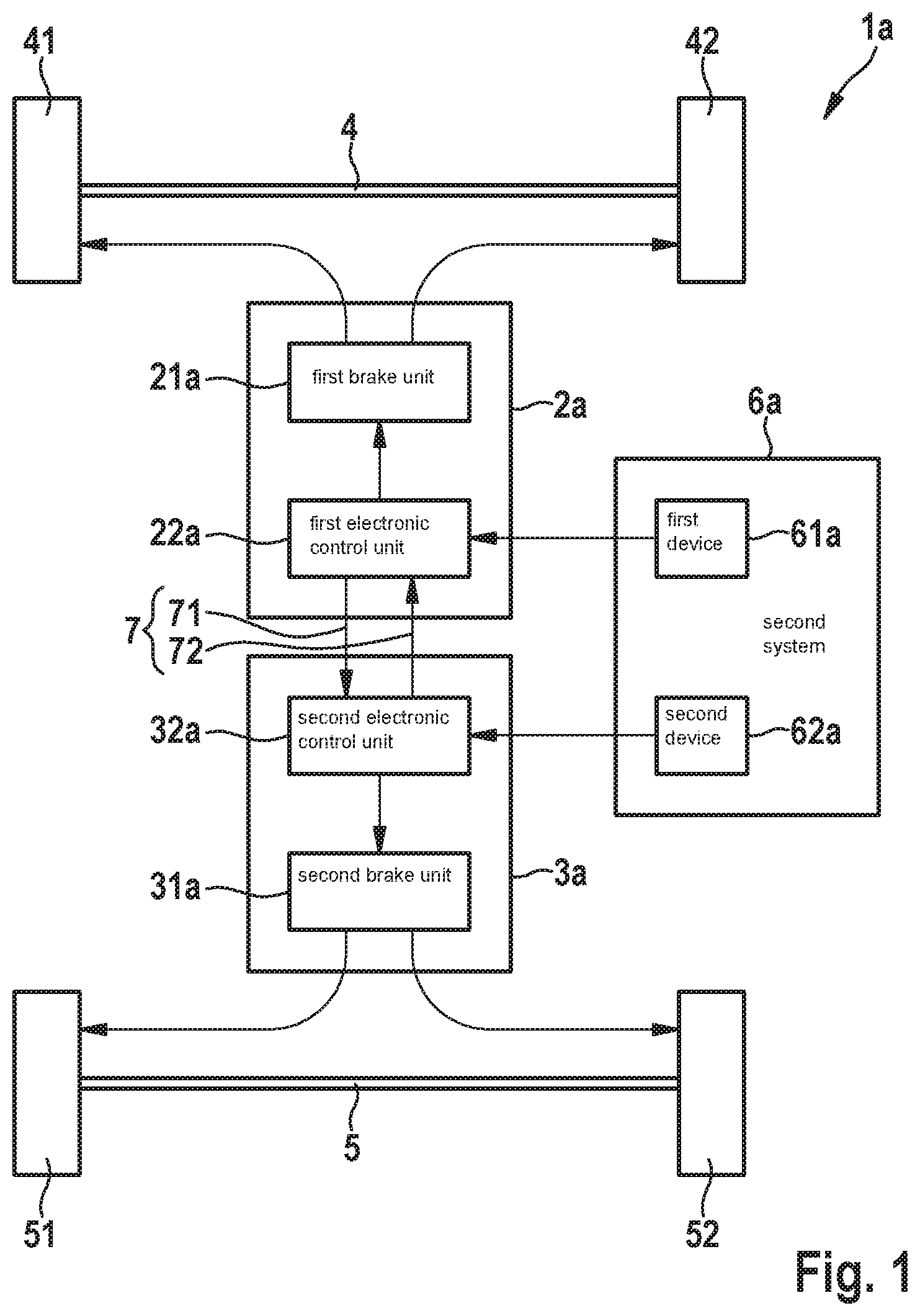