Medical device with a medical-optical device and a holding device and method of operating the medical device.
[0001] the invention relates to a medical device, the apparatus comprises a holder and a medical-optical. The retaining device comprises at least two retaining arms, a hinge connected to at least one degree of freedom of movement are movable together. The holding device has a further actuator, with the two holding arms connected such. a force that can be exerted between the two holding arms above the actuator in the direction of the movement freedom degree. The medico-optical device is held on the holding device. A control unit for outputting a first control signal comprises a first controller via an actuator to the actuator. [0002] in many medical procedures are medical-optical devices used for investigation or treatment of a patient. These devices are often mounted on an articulated support, so that they can be positioned at different positions in the work area and oriented in a desired direction where they may. It is often necessary in operation, the position and orientation of the medical-optical device optionally vary, for instance of a perspective on the surgical field of a surgical microscope or a laser beam direction to change a treatment. It is therefore often change standstill phase, in which the medical-optical device is maintained in a given position in space, with movement phase, in which the medical-optical devices from one layer to another layer is transferred, from. [0003] in a movement phase should the medical-optical apparatus by a user smoothly as possible, i.e. less physical forces under mobilization, from an initial position into an end position can be transferred. It is known from the state of the technology, the holding device to the links provided to actuators, the support stand or allow movement of the first place. [0004] in DE 10 2004, 063, 606 a1 disclosed is a medical device, the medical-optical apparatus in the form of a surgical microscope comprises a, which is supported on a holding device. For free movement of the surgical microscope the medical device via electric motors has forces to the links of said holding device. On position sensor are detected angular positions in the pivot joints. Current control curves are stored in an electronic memory, from which current values are determined as a function of the sensed angular pitches can. From the detected angular positions is determined using the current control curves a current value, with the electric motors may be energized, so that a defined torque is generated in the electric motors. In this way a static load torque can be widened by the resistant torque created by compensating electric motors, so that the surgical microscope of a user apparently forces can be moved freely. The medical device according to the de 10 2004, 063, 606 a1 but has disadvantages in the unpiloted state, when a user moves the medical device not active or holds at a position in space. In this case it come to a drift, therefore a creeping movement of the medico-optical device from a set to out position. Another disadvantage of the medical device is, that a shock (unintentional) against the holding device or the operation microscope may have a lead to uncontrolled movement, in order to avoid what is an operation position. [0005] it is known from the state of the technique to avoid uncontrolled movements, holding devices to provided with brakes, the user can be activated, or the fixture to suppress all individual degrees of freedom of movement, such that a position and/or orientation of the medico-optical device in space is maintained. Retaining devices with brakes are for example in the publications DE 10,144,033 a1. The de 20,218,693 u1 and de 20 2007, 003, 822 u1 disclosed. The disadvantage of the use of brakes will increase the complexity of the overall system that they must, due to a tendency of the elasticities support and opened and closed several times during an operation usually active, which impedes the surgical drain is however, . [0006] a task of the present invention consists, a medical device with a medical-optical device and a movement assisted develop holding device, so that a safe stop is ensured. Another challenge is the provision of a suitable operating method for such a medical device. [0007] the tasks by a medical device having the features of claim 1 and are by a method having the features of claim 6 dissolved. [0008] invention comprises the control unit of the medical device on the hinge and a second means for measuring a kinematic state controller for outputting a second control signal to the actuator via the actuator. The control unit is arranged, in a first mode of operation and in a second operating state that is displaceable, wherein in the first operating state of the actuator via the first regulator and the actuator in dependence on the measured kinematic state regulated in position on the joint is driven such, that a relative position between the two holding arms at least largely independent of external or internal shocks on the holding device or the medical-optical apparatus is maintained, and wherein in the second operating state of the actuator and the actuator is controlled in such force via the second regulator, that a relative movement between the two holding arms is permitted. [0009] the term "force" is in the context of the present invention to understand, that both a directed longitudinal force and a torque acting about an axis of rotation should be comprises. The terms "force control * 1 or" also are similarly regulated not to limit longitudinal forces directed force "" arrangements, but also include rules of torques. [0010] under a "measuring a kinematic state" in the sense of the present invention is a measurement of one or more kinematic variables to understand. In particular including measurements fall, of angles of rotation or translational displacements. Translational velocities and angular accelerations or translational accelerations or angular velocities or combinations of these variables. The means for measuring a kinematic state being formed, determine a kinematic condition at the joint, for example by direct measurement of one or more kinematic variables on the joint or a device for tracking the position of the medical-optical indirectly by device in space and a back bill on kinematic variables on the joint. [0011] during operation of the medical device, in which the control unit is offset in the second operating state, the actuator is controlled in force. Relative movement between the two holding arms is characterized by exerting an external force on the holding device or the medical-optical apparatus allows. Depending on interpretation of scheme can also be very small the outer force, the medical-optical apparatus so that a user can move freely almost forces. After a change in the first operating state by the control unit of the actuator can be controlled in location. Then preferably the change takes place, when the medical-optical device should be kept at a particular location in space, for example at the site, wherein the change in operating conditions is on the an initiation. By the position control is ensured, that the medico-optical device to the set location remains, especially upon exposure to external or internal forces to the medical-optical device or the holding device. A further advantage is, that at a medical device on an insert of the invention brakes be eliminated came, the medical-optical device at a desired position in the work space to hold, or that existing brakes, for example may be present for safety reasons, can be of smaller dimensions. [0012] in one embodiment of the invention the control unit is configured, in the second operating condition the actuator via the second regulator as a function of a measured kinematic drive on the joint state. It is possible in particular, the same sensors, the control unit in the first operating state during the driving of the actuator are used for measuring a position controlled kinematic state, for measuring a condition in the second operating state the control unit - optionally different type kinematic of force-controlled or force-controlled to control the actuator during use. In this way a small number of sensors is for the operation of the medical device with the control unit in the first operating state and in the second operating state sufficiently. [0013] in another embodiment of the invention the control unit comprises means for determining a force generated by the actuator, and the control unit is arranged, in the second operating condition that the actuator via the second regulator is controlled in dependence on the measured force. In this way a force regulator for the second operating state can be realized, a particularly precise setting of the characterized by the force. [0014] in another embodiment of the invention the medical device comprises a user operable release unit a, which is arranged such, that actuation of the release unit a change of control unit from the first mode to the second mode or vice versa causes. The medical device can be the de release unit from a user as required with hats in a state thus enable, in which a movement of the medico-optical device under a defined force (second operating state of the control unit) is permitting mobilization, or in the medical-optical apparatus in a defined position and/or orientation in space sure is held (first operating state of the control unit). [0015] in another embodiment of the invention the medical device has means for blocking relative movement between the two holding arms on, and the control unit is configured, upon exceeding a limit for the force generated from the actuator to cause a blocking relative movement. The activation of the means for blocking the de relative movement represents a safety mechanism is, for example with the risk of overload of the actuators, the retaining arms or other parts of the external forces acting due to unusually strong medical device, erroneous operation or control error can be reduced. In the control unit can alternatively or additionally also limits for individual kinematic variables, one or more or all of the holding device or the medical-optical apparatus for retaining arms in a suitable, for example space defined be fixed coordinate system. The limit values can also be adapted, that critical positions of the holding device in the work area are avoided, for example by a minimum distance of the medico-optical device from a patient to ensure. [0016] a method for operating a medical device comprising the steps according to the invention SE: Displacing the control unit in the first operating state -, in which a kinematic condition at the joint and the actuator via the first regulator and the measured actuator location adjusted depending on the measured kinematic state is controlled, so that a relative position between the two holding arms at least largely is maintained; and - Change the operating state of the control unit in the second operating state, in which the actuator is driven via the second regulator and the inclined member force regulated, so that relative movement between the two holding arms is permitted. [0017] alternatively or additionally to the method can also be carried out in reverse order, starting with a displacement of the control unit in the second operating state and therefore a subsequent change of the operating state of the control unit in the first operating state. The operating conditions of the control unit are further also change between multiple possible. Without the scope of the invention to leave the control unit between a can changing of said first mode to the second mode or vice versa also assume further operating conditions, in which the medical-optical instrument on the holding device is guided by means of the actuator control for example without user or one or more actuators at several joints defined by a situation in a different location in the working space is moved. In this case preferably to configure such a release unit, the various operating conditions that can be selected by a user. [0018] to the method is distinguished by, on the one hand that the medico-optical apparatus in the regulated operating state of the control unit of a user defined force while exerting a force or even almost free from a situation in another position can be moved forces and secondly a secure positioning of the medical-optical device in position controlled operating state under the action of external or internal forces on the device or working space also ensure the holding device. [0019] in one embodiment of the process is the change between the operating conditions by actuating a release unit initiated. The scope of the invention to leave it without a change from the first to the second operating state can both singly or multiply initiated one behind the other or vice versa. [0020] in a further configuration of the method are the first controller and the second controller adapted to one another such, that external forces without the action in the second operating state immediately after a change of the actuator force delivered by less than 10%, preferably less than 5%, more preferably less than 1% ., in the first operating state immediately before the change of the actuator from a different force delivered. In this way a force - or torque can jump in the force applied from the actuator at a transition between the operating conditions at the moment or reduce or avoid. This aspect is particularly important at a transition from the position regulated in the force controlled operating state, a sudden movement of the medico-optical device (for example a sagging due to gravity) to avoid. [0021] in another embodiment of the process is a measured force generated from the actuator, and means for preventing a relative movement between the two exceeding a limit be activated holding arms, the relative movement and/or suppressed by the braked. Thus realized is a safety mechanism, the risk of overload of the medical device with the for example can be avoided. [0022] the invention is described in more detail below with reference to Figures. This show in detail Figure. 1: a first embodiment of a medical device according to the invention; Figure. 2: a pivotal connection of the medical device with an actuator; Figure. 3: a first embodiment for a method according to the invention SE; Figure. 4: a second embodiment for a method according to the invention SE; and Figure. 5: a second embodiment of a medical device according to the invention. [0023] in Figure. 1 is a first embodiment of a medical device according to the invention represented. The medical device comprises a medical-optical apparatus in the form of a surgical microscope 2 on, on a holding device in the form of a stand is supported the 1. [0024] it is often necessary during surgery, the position of the surgical microscope in space to vary. Depending on the application the variations in the position and changes can both changes the angular orientation of the surgical microscope in space changes comprise or combinations of these. In order to accomplish, the stand 1 comprises a plurality of retaining arms 3, 4, 5, 6, 8 via articulations, 9, 10, 11, 12 are connected to each other. [0025] the stand has a vertically disposed first support arm 3 on, via a first fulcrum 7, via a vertically disposed axis of rotation has, connected to said floor. The first support arm attached to a base plate 3 can alternatively also be, may be equipped with rollers, the medical device in the operating room to transporting. Via the first hinge 7 can be the stand as a whole with attached surgical microscope 2 pivoting about the vertical rotation axis. The first support arm 3 is via a second pivot 8, which has a horizontally disposed rotational axis, with a second support arm 4 connected, in this embodiment is designed as a parallelogram structure. The parallelogram structure comprises a third rotary joint 9, a fourth pivot 10 and a fifth hinge 11, their axes parallel to the rotation axis of the second pivot joint 8 are arranged. The upper arm of the parallelogram construction is carried out as a third support arm 5 and extending over the fifth rotary joint beyond 11. At the other end of the third support arm 5 via a sixth hinge 12 is arranged a front link 6, turn on the the operation microscope 2 is supported on a seventh joint 13. The fifth and the sixth articulation joint 12 13 with more degrees of freedom can, for example with more degrees of freedom and/or translational movement axes, be configured. [0026] at one, several or all joints of the tripod are provided actuators 1, which movement of the support stand or can be carried out. The actuators are in this embodiment based on a first and a second actuator 15 explained an example actuator 14. The first actuator arm between the first and the second support arm 4 3 14 is arranged, such that operation of the first actuator and the rotation of the second support arm 14 4 arranged thereon as a whole about the axis of rotation causes further stand elements 8. The second actuator 15 is arranged within the parallelogram construction of the second retaining arm 4, such that operation of the second actuator causes a displacement within the parallelogram construction, by the third support arm 5 is tilted around the fifth joint 11. Without limiting the generality can alternatively or additionally be provided at other joints of the tripod further actuators. [0027] in Figure basis. 2 between the first arm and the second support arm 4 3 compound represented is, following the establishment of a swivel joint for a medical device in the invention described in detail below. Between the holding arms 3, 4 is the first actuator 14 arranged, the electric motor is carried out as in this embodiment. The electric motor 14 comprises a stator 20, is supported on the first support arm 3, and a rotor 19 with a shaft 16, is attached to the second support arm 4. A torque by the electric motor 16 between the first and the second support arm can support arm 3 4 generating. [0028] the shaft 16 via a first bearing unit 17 and a second bearing unit 18 is on the first support arm 3 supported. Shaft 16, 17 and 18 together form the first pivot bearing unit first second bearing unit 8 between the two holding arms. The second support arm relative to the first support arm about the longitudinal axis of the shaft 4 is rotatably 3 16, so that the first hinge 8 has a degree of freedom of rotational movement. [0029] the medical device further includes a control unit, the means for measuring a kinematic state in the form of a angle sensor 21, a first controller 22, a second controller comprises an actuator 23 and 24. [0030] the angle sensor 21 is arranged between the first support arm 3 and the shaft 16 and is therefore suitable, 3 and the second support arm 4 an angle between said first support arm to measure. The measured angle is via a signal line 22 and/or the second controller to the first controller 25 23 supplyable. [0031] the control unit means for determining one of the first actuator can optionally generated force of the first actuator torque generated relationship-wise 14 14 comprise, in this embodiment are configured as the torque sensor 28. The output signal of the torque sensor 28 is the first controller 22 and/or 23 via a third signal line 29 can be fed your second regulator. for the rule so that it as input variable of the first regulator or the second regulator 23/22 and algorithms can be used. [0032] the first controller 22 as position control is carried out. The terms "position control" or "regulated in position" mean in this context, that the regulator is arranged. by a comparison of one or more measured parameters with a desired value using a kinematic variables or more deduced therefrom from the state of the technique known control algorithm to generate an output signal, which in the actuator to a controlled variable for the actuator is converted (usually a current), so that the actuator a defined position or at least largely maintains a defined motion, under the action of external or internal forces even. [0033] the first controller 22 preferably includes a control algorithm for active vibration damping, more preferably comprises the control algorithm of the first regulator adjustable parameter, a damping and/or stiffness in the regulated system which is adjustable. In a supplementary embodiment comprises the medical device tracking system for determining and tracking a state of the medical-optical device and/or the fixture kinematic in space. The determined kinematic state is fed to the control unit via a control line and acts as a further input signal for the control algorithms and/or the second controller from the first controller 22 23. The use of a further input size allows, with an improved control accuracy and/or speed control algorithms - use. [0034] the second controller 23 includes a force control. The terms "force control" or "regulated force" mean in this context, that the regulator is arranged. by a comparison of one or more measured forces or torques more deduced therefrom with a desired value using a size or from the state of the technique known control algorithm to generate an output signal, which in the actuator to a controlled variable for the actuator is converted (usually a current), so that the actuator a defined force or a defined torque on said elements, between which it is disposed, exerts. Alternatively the output signal as a function of a measured cam can also deposited from kinematic state (translational or rotational position for example, speed and/or acceleration), as in de 10 2004, 063, 606 disclosed, are determined. [0035] the controller 22, 23 in a conventional manner than classical linear regulators can, for example as PID controller, or as a state controller, fuzzy controller, adaptive controller, or otherwise self-learning controller with a central, decentralized or cascaded controller architecture be constructed. [0036] in the present embodiment are the first controller and the second controller via a further signal line 22 23 26 27 connected with a release unit, on which a user as hereinafter explained more precise relative movement between said first and said second support arm optionally support arm 3 or 4 can suppress release. The release unit can for example as manual switch, mouth switch, foot switch, touch-screen, voice control or control be performed gestures. [0037] the actuator 24 includes a power electronics, with the aid of which the output signals of the first regulator and the output signals of the second regulator 22 into a first controlled variable 23 into a second adjusting parameter, respective flows in this embodiment, for the first actuator are converted to 14. The first actuator 14 via a power line 29 the variables are supplied. The actuator 24 may without restriction of the public for the first controller and the second controller 22 different leistungselektroniken also comprise 23. [0038] a method of operating the medical device on the basis of Figure is subsequently. 3 described. In operation is continuously examined, whether the release unit 27 has been activated by a user. Wherein the second controller is activated release unit 27 23 for regulated to control the actuator force used. In this mode of operation can be the operation microscope 2 by a user under a defined force moving in space mobilization. The second controller can be adapted 23, in some moments that load at standstill, several or all positions of the holding device 1 in the work area at least approximately completely through the actuator 14, 15 or the actuators of the holding device are compensated. In this way the operation microscope 2 by a user can be almost free from one position to another position in the working space forces spend. Here is the sum of the positions under the working space to understand, the operation microscope 2 to take account of the holding device 1 predetermined kinematic constraints can occupy. [0039] 27 while the first controller is deactivated release unit 22 to control the actuator position controlled for 14, 15 for use. In this operating mode is the operation microscope 2 of the actuator 14, 15 at a position and/or at least virtually constant held in an orientation in the work area, an external or internal force even under the action. External or internal forces can arise in operation for example, that a user (unintentionally) to the device or at the apparatus supports pushes, or by transmission of vibrations by vibrations or bottom auxiliary devices (pump, fan or the like) more mounted. [0040] the first controller and the second controller are particularly preferably 22 23 so adapted to one another, using the first actuator 14 or a moment force generated when changing between the two regulators at least almost free hopping is maintained. In other words should be followed by a from the first actuator 14 immediately before the change as a result of the driving force generated by less than 10% with one of the two regulators, preferably less than 5%, more preferably less than 1% from the from the first actuator 14 immediately after the change as a result of the driving force generated by the other controller distinguish. In order to ensure, that serve to unwanted, sudden movement of the holding device 1 and the surgical microscope 2 when changing is disposed thereon. [0041] in Figure. 4 is a variation of the method for operating the medical device represented. The method differs from the according to Figure. 3 substantially characterized, when changing from a force control in a position that a transitional control is activated. The transitional regime is particularly important, if the releasing unit 27 during movement of the surgical microscope 2 is deactivated, so if during movement of the second controller and the first controller 22 and 23 deactivated activated from a force control is switched to a position control. In this case the transitional controls the braking of the holding device 1 to a standstill. In a embodiment is the transitional adapted therefor, in that the holding device 1 and the surgical microscope 2 attached thereto without overshoot to a halt as soon as possible. Although this result, that the system is not in the position to a stop, at which the release unit 27 has been deactivated, but also are not or hardly vibrations during deceleration procedure on. In an alternative or supplementary embodiment is adapted the transitional, 1 that the holding device and/or the operation microscope 2 shipped into the position, in which it in the deactivation of the release unit were 27. In this embodiment an overshoot of the position is accepted. After the change to a position control the release unit 27 is then monitored continuously and upon re-activation of the first actuator 14 to a controlled driving force again switched. [0042] in Figure. 5 another embodiment of the invention is a medical device represented. Acting with same reference symbols as in Figure components are equal. 1 provided. From the embodiment according to Figure. 1 differs according to the embodiment Figure. 5 characterized in, that means for compensating static load torque are provided on the holding device 1, the counterweights are designed as 30 in this embodiment. It is possible with the counterweights, a ' manual file or all of the load to compensate for static moments occurring, so that a balance of the holding device is supported at standstill. The first actuator and the second actuator are characterized 14 15 relieved, since at best only a portion of the torques necessary for holding the fixture in a position of equilibrium of the actuators must be applied. The actuators can therefore be dimensioned smaller 14.15. [0043] in an alternative or supplementary embodiment the means for equalizing a static load torque can also force elements, for example springs, pneumatic devices or further comprise actuators, which forces or moments between the holding arms can be applied, so that a steady state of the medical device is supported. [0044] can optionally the medical device as in Figure. 2 represented a brake 31 comprise, between the shaft 16 and the first support arm 3 is arranged the. The brake is connected to the control unit via a control line 32 drift 31. In a memory of the control unit of the actuator or actuators are limits for the 14, 15 applied forces or moments or forces or moments for measured deposited. A limit value is exceeded the brake 31 activated, so that a relative movement between the first support and the second support arm at least 3 4 braked, even preferably is suppressed. A safety mechanism is thus available, by means of which the risk of overload of the actuators 14, 15, of the holding arms 3, 4 or other portions of the medical device due to unusually strong external forces acting for example. Erroneous operation or control error is reduced. [0045] the brake 31 is preferably dimensioned, that a relative movement between the holding arms 3, 4 present at maximum torque also, which can be generated by the first actuator 14, can be suppressed effectively. [0046] the invention was in the embodiments based on the first actuator between the first holding arm 14 substantially the second holding arm 3 and 4 described. Without limiting the general public and/or between the holding arms can further actuators between other cab over 6 and the operation microscope 2 be provided, with which forces or moments in the direction of one or more of predetermined degrees of freedom of movement by the corresponding articulation can generate, and extending across corresponding to driving control units. [0047] the invention is not limited to the illustrated configurations of the holders but also on different devices with different numbers of degrees of freedom built applicable. Holding devices of the invention can both translational and a rotational medical device generally a - or polyvalent pivot joints between the holding arms comprise, adapted for generating a longitudinal force and/or on which actuators are arranged a torque. For example DC motors as actuators can electrically, dCBL motors, stepper motors, piezoelectric actuator or traveling wave motors be performed. As actuators pneumatic cylinder drives also alternatively, membrane drives or so-called pneumatic muscles " are used. It is also conceivable in turn alternatively or additionally, hydraulic cylinder drives, gear machines, machines or piston machines to use as actuators wing. [0048] the medical device and method for operating the invention invention are characterised by the fact, that it is possible, on the one hand a medical-optical device under a defined force or forces almost free from a location in the mobilization workspace to another location in the working space to spend, and on the other hand the medical-optical apparatus when required and controlled in a certain position and/or orientation in securely hold space. Providing the control unit with a position controller and a force controller further allows, during operation of the medical device on to give up the use of brakes. The use of brakes for fixing the medical-optical device with a multitude of disadvantages. Brakes, are dimensioned sufficient, the holding device in different positions in the work area to be able to retain sure, are usually large, heavy and expensive. The brake lining and/or the connection of the brake at the holding device often has a certain degree of flexibility on, by the oscillations of the tripod are promoted, optionally by additional damper must be damped. Wherein when braking friction brakes can also arise from a movement of the holding device abrasion, the braking effect can reduce contamination of the system and the operation panel and at worst can lead. All these disadvantages can be overcome with the invention medical device. The invention relates to a medical apparatus having a medical optical appliance and a holding device with at least two holding arms which are connected movably to one another with at least one degree of freedom of movement via a joint and with an actuator which is connected to the two holding arms in such a way that a force can be exerted via the actuator between the two holding arms in the direction of the degree of freedom of movement. A control unit comprises a first regulator for outputting a first control signal to the actuator via an adjusting element. The medical optical appliance is mounted on the holding device. 1. a medical device, comprising - a medical-optical apparatus (2), - a holding device (1) with at least two holding arms (3, 4, 5, 6), the via a joint (8, 9, 10, 11, 12) with at least one degree of freedom of movement are movably connected with one another, and an actuator (14, 15). with the two holding arms such (3, 4, 5, 6) is connected, via the actuator that (14, 15) a force between the two holding arms (3, 4, 5, 6) is exerted in the direction of the movement freedom degree, and - a control unit, a first regulator (22) for outputting a first control signal via an actuator (24) to the actuator (14, 15) comprises, wherein the medical-optical apparatus (2) on the holding device (1) is supported, characterized in that the control unit means (21) for measuring a kinematic state at the joint and a second regulator (23) for outputting a second control signal via the actuator (24) to the actuator (14, 15) comprises, and that the control unit is arranged, in a first mode of operation and in a second operating state that is displaceable, wherein in the first operating state of the actuator (14, 15) via the first regulator (22) and the actuator (24) in dependence on the on the joint (8, 9, 10, 11, 12) is regulated in position measured kinematic state so driven. that a relative position between the two holding arms (3, 4, 5, 6) at least largely independent of external or internal shocks on the holding device (1) or the medical-optical apparatus (2) is maintained, and wherein in the second operating state of the actuator (14, 15) via the second regulator (23) and the actuator (24) is controlled in such force, that a relative movement between the two holding arms (3, 4, 5, 6) is permitted. 2. medical device according to claim 1, characterized in that the control unit is adapted to, in the second operating condition the actuator (14, 15) via the second regulator (23) on the joint in response to a (8, 9, 10, 11, 12) measured kinematic drive state. 3. medical device according to one of claims 1 or 2, characterized in that the control unit means (28) for determining a from the actuator (14.15) generated force comprises, and that the control unit is arranged, that in the second operating condition the actuator (14, 15) via the second regulator (23) as a function of the measured force is controlled. 4. a medical device according to any of the preceding claims, characterized in that the medical device a of a user operable release unit (27) comprises, is so set up, that actuation of the release unit (27) a change in the control unit from the first mode to the second mode or vice versa causes. 5. a medical device according to claim 3 or according to claim 4, dependent on claim 3, characterized in that the medical device means (31) for blocking relative movement between the two holding arms (3, 4, 5, 6) comprises, and that the control unit is adapted. of the actuator exceeds a limit for the (14, 15) to cause a blocking relative movement force generated. 6. method for operating a medical device according to any of claims 1 to 3, comprising the steps of: Displacing the control unit in the first operating state -, in which a kinematic state is measured and the actuator on the joint (14, 15) via the first regulator (22) and the actuator (24) is controlled in dependence on the measured kinematic state regulated in position, so that a relative position between the two holding arms (3, 4, 5, 6) is maintained at least largely; and - Change the operating state of the control unit in the second operating state, in which the actuator (14.15) Conventionon second regulator (23) and the actuator (24) is controlled in force, so that relative movement between the two holding arms (3, 4, 5, 6) is permitted. 7. method according to claim 6, characterized in that the change between the operating conditions by actuating a release unit (27) is initiated. 8. method according to one of claims 6 or 7, characterized in that the first regulator (22) and the second regulator (23) are adapted to one another such, without external action that forces in the second operating state immediately after a change of the actuator (14, 15) is less than 10% of a force delivered in the first operating state immediately before the change of the actuator (14, 15) different force delivered. 9. method according to any of claims 6 to 8, characterized in that one of said actuator (14, 15) is measured force generated, and wherein exceeding a limit means (31) for blocking relative movement between the two holding arms (3, 4, 5, 6) are activated, the braked by the relative movement and/or suppressed.Description
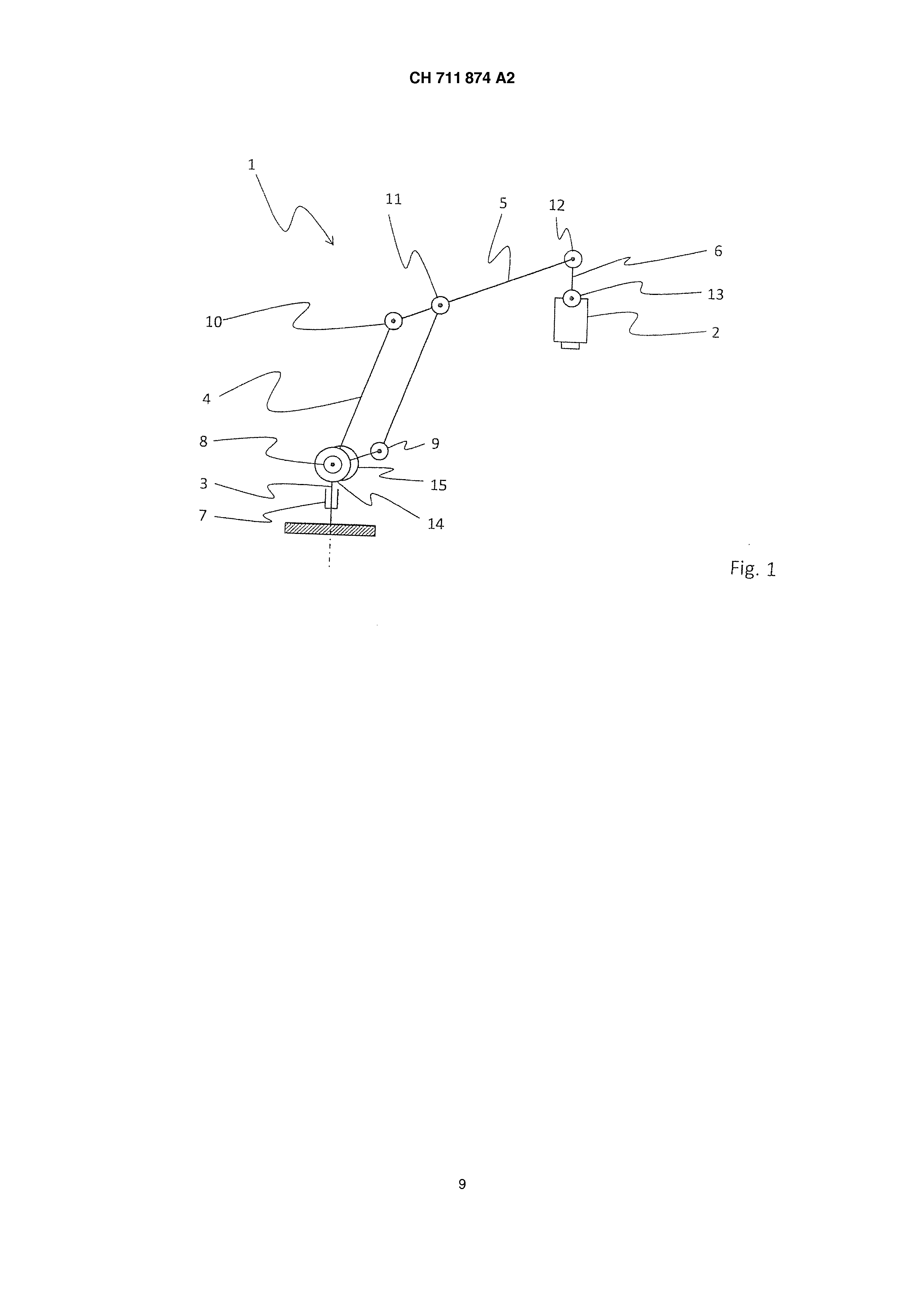
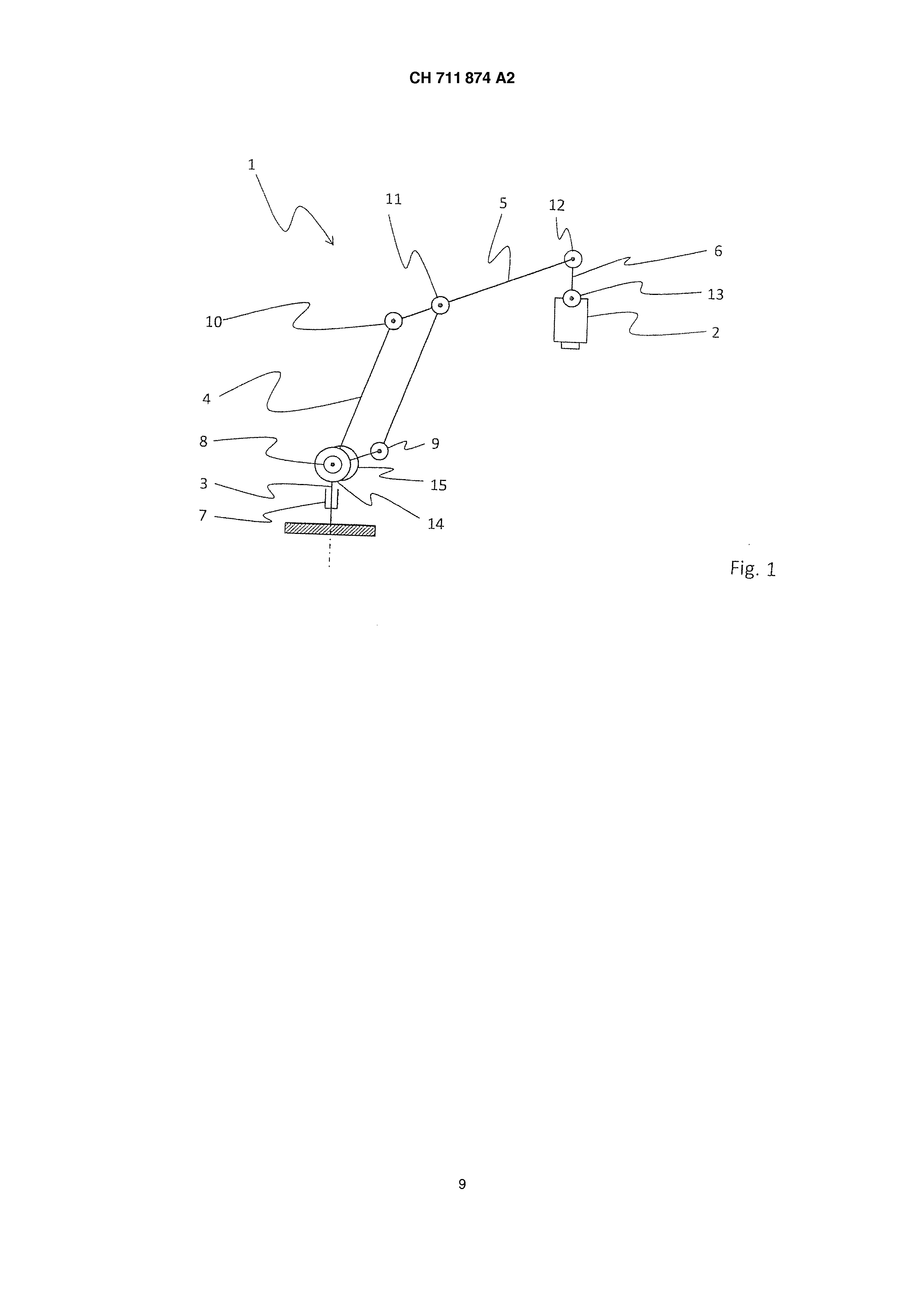
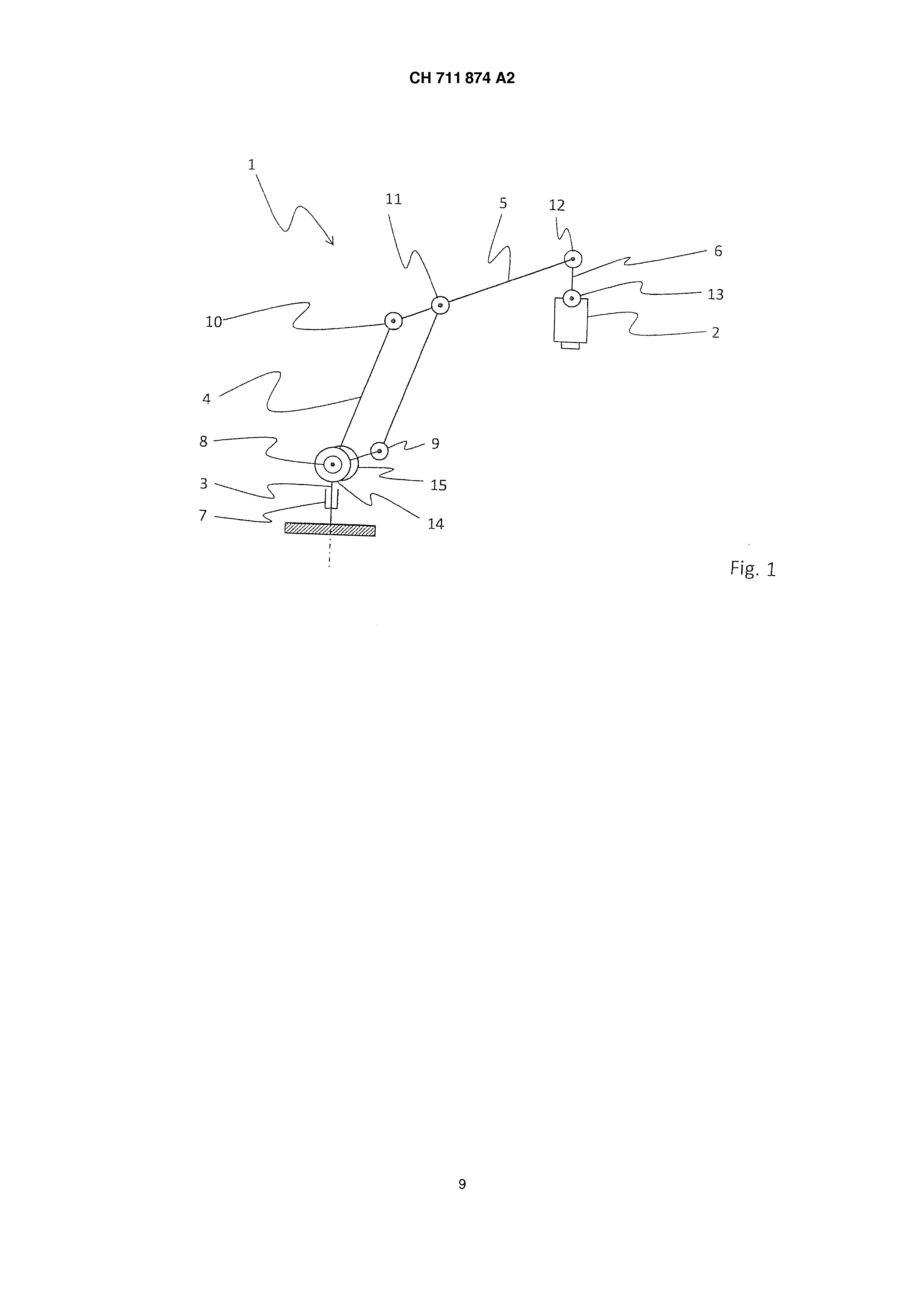
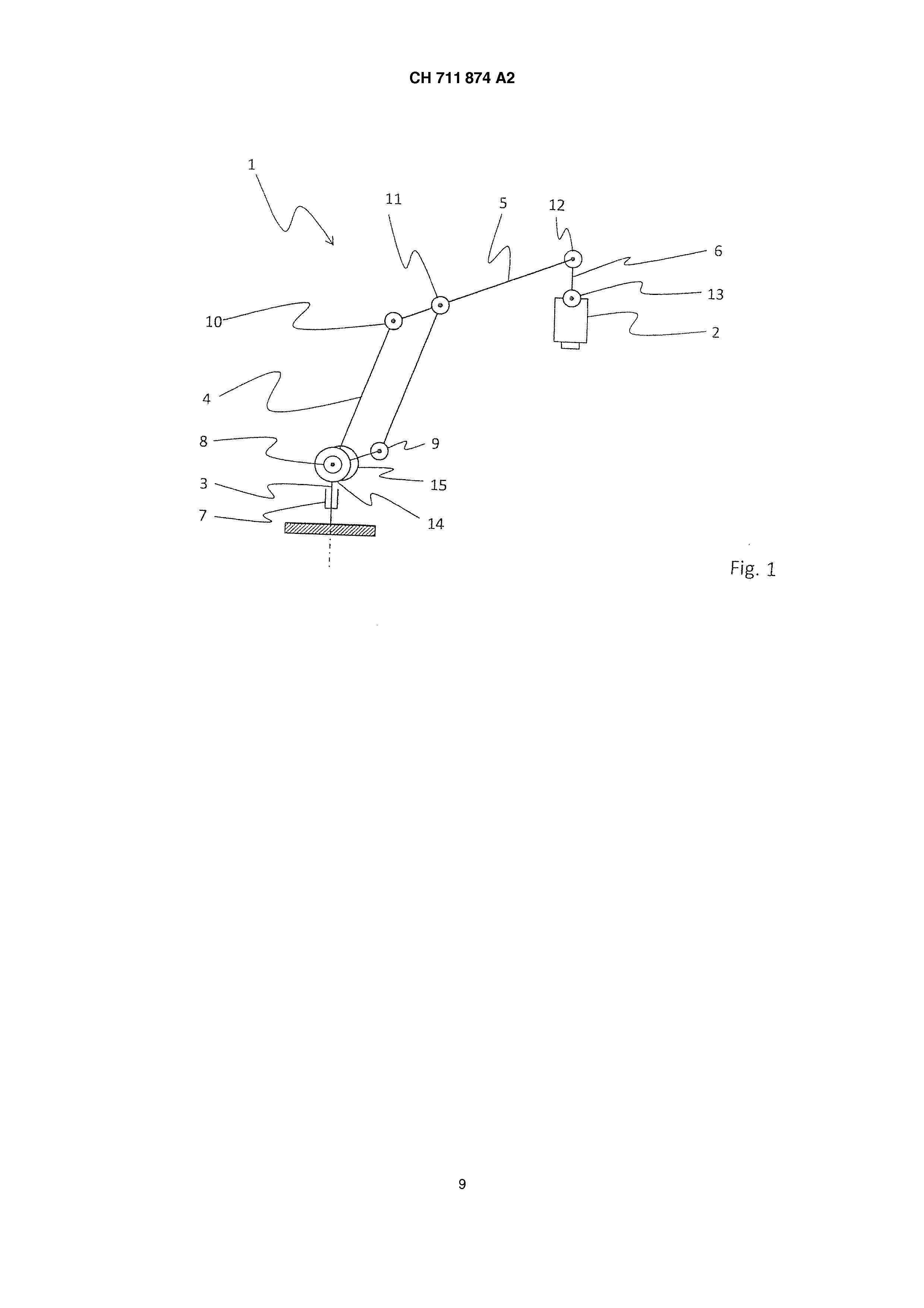
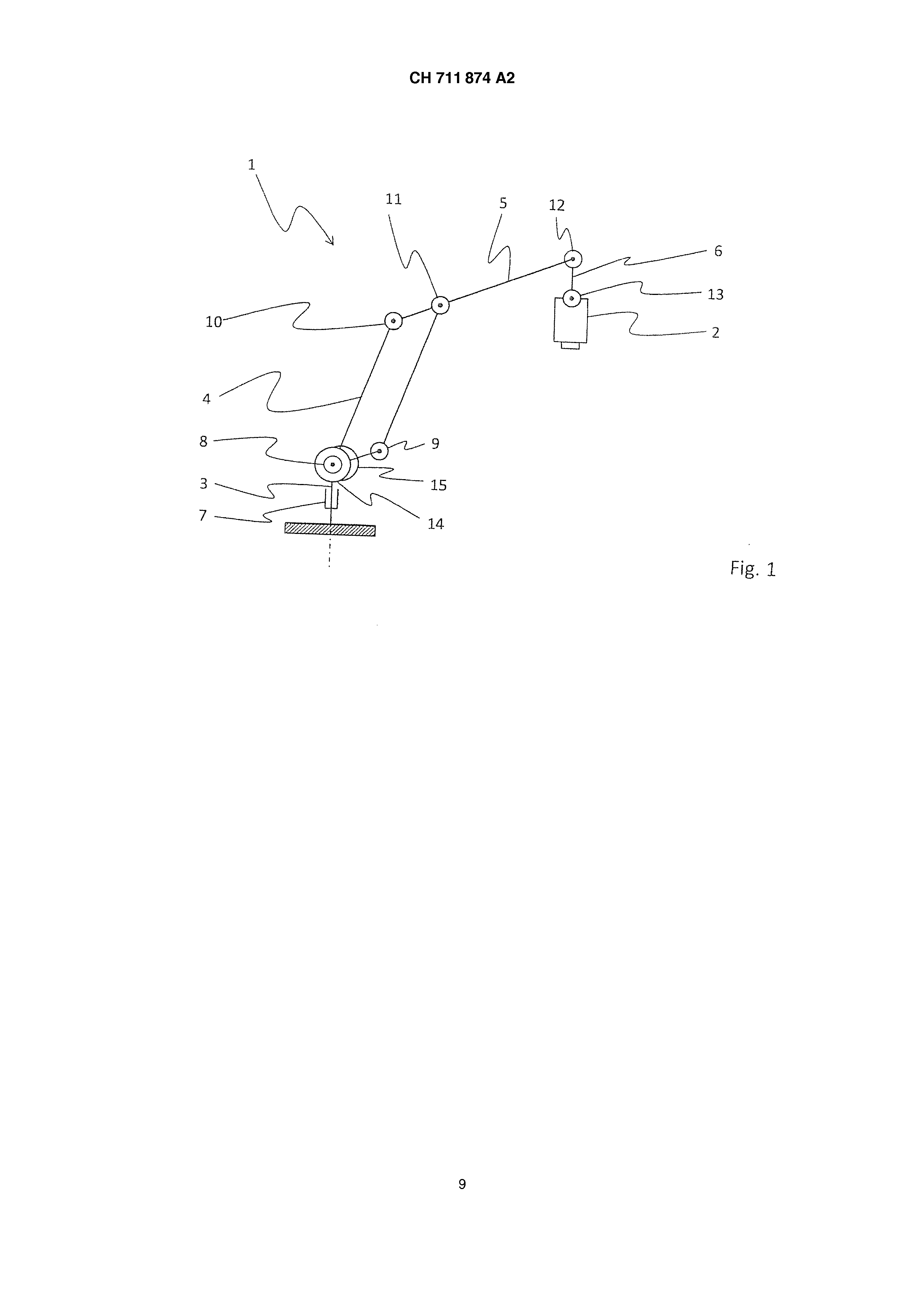