Unit making drinking straws corrugated at appropriate intervals, avoiding marks on intermediate smooth sections, includes series of recirculated suction molds in liquid-filled vacuum tank
The molding unit is built into a closed vacuum chamber (30) containing cooling medium flowing around it. It follows precalibration (40) directly.
Die Erfindung betrifft eine Vorrichtung sowie das Verfahren entsprechend dem Oberbegriff desAnspruchs 1, damit dünnwandige, glatte Kunststoffrohre mit gewellten Sektionen, bei hohen Ausstoßleistungen, rationell und endlos im Extrusionsverfahren hergestellt werden können.
Es ist hinreichend bekannt, daß die Hersteller von biegsamen Trinkhalmen diese weltweit größ-tenteils in mehreren Arbeitsschritten, sehr personalintensiv herstellen. So wird z. B. zuerstdas Glattrohr (Fig. 1/50 ) bei einer Lineargeschwindigkeit von >70 m/min hergestellt, danach indie gewünschte Stücklänge gebracht und dann auf speziellen Rollmaschinen oder Warmformanla-gen das Wellprofil eingewalzt. Speziell dieser Arbeitsschritt ist sehr personal- und kostenintensiv.So werden pro Extrusionslinie zirka drei Rollautomaten benötigt, um die angelieferte bzw. gefer-tigte Menge Kunststoffrohre zeitlich und ohne große Zwischenlager verarbeiten zu können.
Die Extrusionslinien zur Herstellung von Glattrohren, bestehend aus Extruder, Düse und Vaku-umkalibriertank, sind hinreichend bekannt und technisch auf sehr hohem Niveau. Ebenso Anla-gen mit Durckkalibrierung lassen sich zur Herstellung solcher Glattrohre (Fig. 1/50 ) einsetzen.Der Fachwelt sind auch Extrusionsanlagen mit unterschiedlichen Kühlsystemen und Herstel-lungsverfahren (Druck, Vakuum) bekannt, um einfache Wellrohre oder Wellrohre mit angeform-ten glatten Stutzen endlos herzustellen (Fig. 2, 3).
Diese Vorrichtungen sind durch eine Vielzahl von derzeit noch bestehenden Patenten abgesi-chert, die zum Einen deshalb für die neue Erfindung nicht verfügbar sind und zum Anderen technisch auch nicht dafür eingesetzbar sind.
Wir verweisen auf folgende Patentschriften:EP 65 729, US 5,494,430 etc.
Alle Wellrohranlagen haben einen großen Nachteil, daß pro Dimension und Produkt eine Vielzahlvon Formblöcken eingesetzt und die Produktlänge immer nur ein Vielfaches der Formblocklängebetragen kann. Selbst gleicher Produktdurchmesser aber unterschiedliche Abstände zwischen den Wellsektionen erfordern neue, zusätzliche Formketten.
Durch die bekannten Herstellungsverfahren (Druck- bzw. Vakuumkalibrierung) gibt es auch ent-sprechende Weiterentwicklungen, um Wellrohre auch abschnittsweise mit längeren, glatten Stut-zen herzustellen. Bekannt sind Produkte mit Wellsektionen mit mindestens einer Wellung auf einem Glattrohr, bei einer Stücklänge von zirka 2 Metern.
Bei dieser Art der Herstellung und unter Verwendung von herkömmlichen Wellrohranlagen, istes unerläßlich, Vakuum sowohl zur Ausformung der Wellung als auch zur Ausformung des Glattroh-res einzusetzen. Dabei zeichnen sich teilweise die Schließkanten und auch die Vakuumschlitzeder Formblöcke in regelmäßigen Abständen der Formblocklänge ab (Fig. 4).
Solch eine ungleichmäßig geformte "glatte" Oberfläche als Trinkhalm in den Handel zubringen,ein unvorstellbarer Gedanke.
Die OS DE 34 27 732 A1, bzw. die OS 28 04 012 zeigt Trinkhalme, die durch verschiedenartige,radial verlaufende Rillen eine teleskopartige Verbindung zweier ineinandergesteckter Trinkhalmeermöglicht, bzw. ein Herstellungsverfahren beschreibt, bei dem jede Wellung einzeln gefertigtwird.
Diese neue Erfindung unterscheidet sich von v.g. OS DE 34 27 732 und berührt nicht die darinerwähnten und nachfolgend kurz zitierten Schutzrechte:
- Die Trinkhalme sind verlängerbar und weisen diverse Kopplungsmöglichkeiten auf
- Der Trinkhalm steht während der Warmverformung still oder dreht sich um die eigene Achse.
- Ein Dorn wird während der Warmverformung in den Trinkhalm eingeschoben.
Aufgabe und Ziel dieser neuen Erfindung ist es, eine möglichst einfache und kostengünstigeKonstruktion zu bauen, sowie die Möglichkeit zu schaffen, bestehende Glattrohranlagen auf die-ses neue Verfahren umzurüsten und die Herstellung sektional gewellter Trinkhalme im Extrusions-verfahren mit folgenden Hauptmerkmalen zu garantieren:
- Die Herstellung der wellförmigen Sektion durch wenige Formkörper.
- Die Abstände x1-x2 (Fig. 5) zwischen den wellförmigen Sektionen sind frei definierbar.
- Die Rohre in der glatten, ungewellten Sektion weisen keine störenden Oberflächenmarkierun-gen auf (Fig. 5/x1+x2)
- Die Trinkhalme werden nicht auf einer herkömmlichen Wellrohrformmaschine hergestellt.
- Die Produktionsgeschwindigkeit wird nicht durch langwierige Stauch- oder Rollverfahrenge-drosselt.
- Die Herstellung der Trinkhalme ist auf handelsüblichen bzw. modifizierten Glattrohr-Extrusionsanlagen möglich.
- Die Vorrichtung (Fig. 7/20 ) zur Herstellung solcher Trinkhalme ist im Vakuumbad (Fig.7/30 ) einsetzbar.
- Bestehende Extrusionsanlagen können umgerüstet werden.
- Der sektional gewellte Trinkhalm wird nach dem Verfassen oder im Anschluß an die Kühl-bzw. Formstrecke auf die gewünschte Länge gebracht und liegt verpackungsgerecht vor.
- Der sektional gewellte Trinkhalm ist U-förmig biegbar.
- Die Wellform bzw. die Faltenausbildung (Fig. 3+5/10 ) ist durch entsprechende Formkörperfrei gestaltbar.
Diese vorgenannten Aufgaben und die Erfüllung der speziellen Kriterien des Endproduktes wer-den durch die nachfolgend beschriebene Vorrichtung und die nachfolgend beschriebenen An-sprüche gelöst.
Die Formmaschine (Fig. 7/20 ) ist ideal zur Herstellung von sektional gewellten Trinkhalmenge-mäß (Fig. 5), die üblicherweise auf einer Glattrohr Extrusionsanlage hergestellt werden undmit mindestens einer Vakuumkammer (Fig. 7/30 ) und einer Kurzkalibrierung (Fig. 7/40 ) ausgestattetist.
Die Außenabmessungen dieser Vorrichtung (Fig. 7/20 ) sind so gehalten, daß sie in die Vakuum-kammer (Fig. 7/30 ) integriert werden kann und gleich im direkten Anschluß an die Kalibrierung(Fig. 7/40 ) positioniert wird. Dies ist notwendig, damit das extrudierte und vorkalibrierteRohr (Fig. 7/50 ) noch soviel Restwärme besitzt, um eine ausreichende Ausformung der Wellung zu garantieren (Pos. 10 ).
Die zur Ausformung der Wellsektion benötigten Formkörper (Pos. 80) besitzen die negative Ausdrehung der Weltform und sind als Halbschalen ausgebildet. Beim Durchlaufen der Form-strecke (Pos. 60 ) bilden die spiegelbildlich angeordneten Halbschalen einen geschlossenen kon-zentrischen Kreis. Die Formkörper (Pos. 80 ) können auch so ausgeführt sein, daß eine Mehr-
fach-Extrusion möglich ist und die Ausdrehungen für die Wellgeometrie in gleichen Abständen,parallel nebeneinander angeordnet sind.
Die Trägerelemente (Pos. 70 ) der Formblöcke (Pos. 80 ) sind in einer Führungsnut geführtund können sich auf dieser Bahn (Pos. 90 ) frei bewegen. Diese Bahn besitzt in ihrer Umlenkung halbkreisförmig angeordnete Nuten, in denen die Trägerelemente paternosterähnlich bewegt werden. Dies wird durch unterschiedliche Nuttiefen, durch entsprechenden Achsversatz und Gestaltung dieser Achsen (Pos. 100 ) erreicht.
Diese Art und Konstruktion solcher Führungen ist hinreichend bekannt und ist als allgemeinerStand der Technik einzustufen.
Die Trägerelemente (Fig. 8/70 ) sind so ausgeführt, daß jedes Element seine eigene Einrichtungzur Unterdruckerzeugung (Fig. 8/110 ) trägt.
Diese zusätzliche Unterdruckbeaufschlagung zur Ausformung der Wellform ist deshalb notwendig,da der in der Vakuumkammer (Fig. 7/30 ) vorherrschende Unterdruck nicht in der Lage ist, dieAus-formung ordnungsgemäß zu garantieren. Diese Unterdruckeinrichtung (Fig. 7/110 ) wird währenddes Einfahrens in den Einlaufbereich (Fig. 7/120 ) mechanisch vorgespannt und expandiert beim Durch-laufen der Formstrecke (Fig. 7/60 ). Im Bereich der hinteren Umlenkung (Fig. 7/130 ) erreichtdiese Unterdruckeinrichtung (Fig. 8/110 ) ihre völlige Entspannung und die Druckverhältnisse im Vaku-umtank (Fig. 7/30 ) und in der Unterdruckeinrichtung (Fig. 8/110 ) haben sich ausgeglichen.
Die Trägerelemente (Fig. 8/70 ) werden mechanisch, durch die hintere Umlenkung (Fig. 8/130 )in eine Parkposition geschoben, bzw. schieben sich gegenseitig, und stehen aneinandergereiht undabrufbereit für kurze Zeit in dieser Position. In dieser Parkposition sind die Abstände (Fig.8/L1) zwi-schen den einzelnen Formblöcken (Fig. 8/80 ) annähernd gleich und werden nach Verlassen dieserParkposition erst in den gewünschten größeren Abstand (Fig. 8/L2) gebracht.
Diese Vergrößerung der Abstände wird durch eine motorisch angetriebenen Fördereinrichtung(Fig. 8/150 ) bewirkt, die sich in der gewünschten Abzugsgeschwindigkeit bewegt. Zeittaktgesteuertwer-den die Trägerelemente (Fig. 8/70 ) mit den Formblöcken (Fig. 8/80 ) durch eine entsprechendkon-struierte Einheit auf diese Fördereinrichtung (Fig. 8/150 ) befördert, von dieser erfaßt undmitgenom-men. Kürzere Zeittakte bedeuten kürzere Abstände zwischen den Trägerelementen bzw. längere Zeittakte äquivalent längere Abstände. Somit ist gewährleistet, daß verschiedene Produkte mitun-terschiedlich langen glatten Zonen innerhalb einer Produktgröße gefertigt werden können.
Nach Verlassen der Formstrecke (Fig. 7/60 ) durchläuft das Rohr (Fig. 7/180 ) noch eine Zeitlang die geflutete Vakuumkammer (Fig. 7/30 ), an deren Ende eine Dichtmanschette (Fig. 7/170 ) angebrachtist, um die Vakuumkammer (Fig. 7/30 ) gegen evtl. eintretende Leckluft abzudichten und um dasmit-gerissene Wasser von der Rohroberfläche (Fig. 7/180 ) abzustreifen.
Das in der Vakuumkammer befindliche und unter Druck stehende Wasser kann das frei durch-laufende Rohr nicht zusammendrücken und gewährleistet so eine gute bis sehr gute Abkühlung des Rohres. Auch wird die entstandene Wellform nicht durch den Wasserdruck beeinflußt, da der atmosphärische Druck gegen die Innenwand des Rohres drückt.
Im Anschluß an die Vakuumkammer ist ein herkömmlicher Raupenabzug (Pos. 160 ) installiert,dessen Abzugsgeschwindigkeit mit der Geschwindigkeit der Fördereinrichtung (Pos. 150 ) syn-chronisiert ist.
Die Ausführungen dieser Erfindung sind in beiliegenden Zeichnungen bzw. Skizzen und ohne große Details dargestellt, denn es soll nur die Funktion herausgestellt werden.
Fig. 1 zeigt ein herkömmliches, dünnwan-diges Glattrohr
Fig. 2 zeigt ein herkömmliches, endlos gefertigtes Wellrohr
Fig. 3 zeigt ein Wellrohr mit angeformten Stutzen
Fig. 4 zeigt ein auf einem Corrugator her gestelltes Glattrohr mit den bekannten Markierungen, verursacht durch die Schließkanten unddie Vakuumschlitze
Fig. 5 zeigt ein Glattrohr mit unterschiedli-chen Abständen zwischen den gewellten Sektionen, frei von irgendwelchen Oberflächenmarkie-rungen
Fig. 6 zeigt einen Profilausschnitt (10.1 ) der Formblöcke (Fig. 8/80 ) mit den Vakuumschlitzen (10.2 )
Fig. 7 zeigt skizzenhaft die Vakuumkam-mer (30 ) mit der integrierten Formeinheit (20 ), sowie Düse (50 ), Kalibrierung (40 ), Dichtung(170 ) und Raupenabzug (160 )
Fig. 8 zeigt skizzenhaft die Formeinheit (20 ) mit Trägerelementen (70 ), Formblöcken (80 ) und Unterdruckeinheit (110 ), sowie Förderein-heit (150 ) und weitere Bauteile
Fig. 9 zeigt ein Glattrohr mit unterschied-lichen Abständen zwischen den gewellten Sektionen und mit gestauchtem Wellprofil
1. Vorrichtung zum Herstellen von glatten Kunststoffrohren vornehmlich Trinkhalme aus teilkri-stallinen Kunststoffmaterialien und zur Ausformung von sektionalen Wellungen in definierbarenAbständen ohne störende Oberflächenmarkierungen im glatten Bereich zwischen den gewell-ten Sektionen, dadurch gekennzeichnet , daß die Formeinheit in eine in sich geschlossene und mit einem Kühlmedium gefluteten Vakuumkammer (Fig. 7/30 ) eingebaut ist, vom Kühlme-dium völlig umspült wird und direkt nach der Vorkalibrierung (Fig. 7/40 ) positioniert wird.
2. Vorrichtung nach Anspruch 1, dadurch gekennzeichnet, daß der sektional gewellte Trinkhalm(Fig. 7/180 ) endlos hergestellt wird.
3. Vorrichtung nach Anspruch 1 oder 2, dadurch gekennzeichnet, daß sich die Trägerelemente(Fig. 8/70 )auf einer vordefinierten Bahn (Fig. 8/90 ) bewegen und zueinander spiegelbildlichan-geordnet sind.
4. Vorrichtung nach Anspruch 1 bis 3, dadurch gekennzeichnet, daß die Bewegung der Trä-gerelemente (Fig. 8/70 ) paternosterartig verläuft.
5. Vorrichtung nach Anspruch 1 bis 4, dadurch gekennzeichnet, daß die Tägerelemente (Fig.8/70 ) zur Aufnahme von verschiedenen Formkörpern (Fig. 8/80 ) vorbereitet sind und diese kraft- und formschlüssig mit den Trägerelementen (Fig. 8/70 ) verbunden werden können.
6. Vorrichtung nach Anspruch 1 bis 5, dadurch gekennzeichnet, daß die Trägerelemente (Fig.8/70 ) mit Unterdruckeinheiten (Fig. 8/110 ) ausgestattet sind, entsprechende Kanäle in dieFormkörper (Fig. 8/80 ) führen und in den Vakuumschlitzen (Fig. 6/10.2 ) über der Negativformdes Wellprofils (Fig. 6/10.1 ) enden.
7. Vorrichtung nach Anspruch 1 bis 6, dadurch gekennzeichnet, daß die Unterdruckeinheiten
(Fig. 8/110 ) blasebalgähnlich ausgeführt sind und durch mechanische Bauteile wie Druckfe-dern (Fig. 8/141 ) oder Kolben bewegt werden.
8. Vorrichtung nach Anspruch 1 bis 7, dadurch gekennzeichnet, daß die Trägerelemente (Fig.8/70 ) mit längenversetzten Achsen (Fig. 8/100 ) ausgestattet sind.
9. Vorrichtung nach Anspruch 1 bis 8, dadurch gekennzeichnet, daß die versetzt angeordnetenAchsen (Fig. 8/100 ) mit entsprechenden Rollen in den Umlenkzonen (Fig. 8/120 +130 ) in unter-schiedlich tiefen Nuten (Fig. 8/90 ) laufen.
10. Vorrichtung nach Anspruch 1 bis 9, dadurch gekennzeichnet, daß die am Rücken der Trä-gerelemente (Fig. 8/70 ) angeordneten Unterdruckeinheiten (Fig. 8/110 ) während der Zufüh-rung in den Einlaufbereich durch eine nicht dargestellte Einheit gespannt werden, d. h., daßalle innerhalb des Blasebalges (Fig. 8/140 ) befindlichen Medien (Wasser, Luft) herausgepreßt werden.
11. Vorrichtung nach Anspruch 1 bis 10, dadurch gekennzeichnet, daß durch die Entspannungbzw. durch das mechanische Aufziehen des Blasebalges (Fig. 8/140 ) ein Unterdruck an den Vakuumschlitzen (Fig. 6/10.2 ) entsteht, welche das negativ eingearbeitete Wellprofil (Fig.6/10.1 ) in den Formkörpern (Fig. 8/80 ) radial umgeben und somit das plastische Kunststoffma-terial in die Wellung (Fig. 7/10.1 ) gesaugt wird.
12. Vorrichtung nach Anspruch 1 bis 11, dadurch gekennzeichnet, daß die kompletten Träger-elemente (Fig. 8/70 ) aneinandergereiht oder mit einem geringen Abstand in eine Parkpositionbefördert werden und dort abrufbereit verharren.
13. Vorrichtung nach Anspruch 1 bis 12, dadurch gekennzeichnet, daß mindestens eine nichtdargestellte, mechanische Vorrichtung diese kompletten Trägerelemente (Fig. 8/70 ) in variier-baren Zeittakten auf die Fördereinrichtung (Fig. 8/150 ) bewegt.
14. Vorrichtung nach Anspruch 1 bis 13, dadurch gekennzeichnet, daß die Trägerelemente, (Fig.8/70 ) die von der Fördereinrichtung (Fig. 8/150 ) erfaßt, auf die gewünschte Extrusionsge-schwindigkeit beschleunigt und synchronisiert werden und zusammen mit den spiegelbildlich an-geordneten, mechanisch gekoppelt Trägerelementen (Fig. 8/70 ) eine geschlossene Form bilden.
15. Vorrichtung nach Anspruch 1 bis 14, dadurch gekennzeichnet, daß die Fördereinheit (Fig.8/150 ) aus mindestens einem abriebfesten Band besteht und als Reibantrieb ausgelegt ist odermit entsprechendem, nicht dargestelltem Mitnehmer ausgestattet ist.
16. Vorrichtung nach Anspruch 1 bis 15, dadurch gekennzeichnet, daß die Fördereinheit (Fig.8/150 ) motorisch angetrieben wird und mit dem im Anschluß an das Vakuumbad angebrachten Raupenabzug (Fig. 7/160 ) elektrisch oder mechanisch gekoppelt bzw., synchronisiert ist.
17. Vorrichtung nach Anspruch 1 bis 16, dadurch gekennzeichnet, daß die Geschwindigkeit derFördereinrichtung (Fig. 8/150 ) und des Raupenabzuges (Fig. 7/160 ) so aufeinander abgestimmt(synchronisiert) sind, daß das offene Wellprofil gestaucht wird (Fig. 9).
18. Vorrichtung nach Anspruch 1 bis 17, dadurch gekennzeichnet, daß die Formblöcke (Fig.8/80 ) für Mehrfachextrusion ausgelegt werden können und mehr als eine Kavität aufweisen (Fig. 8/10.1 ).

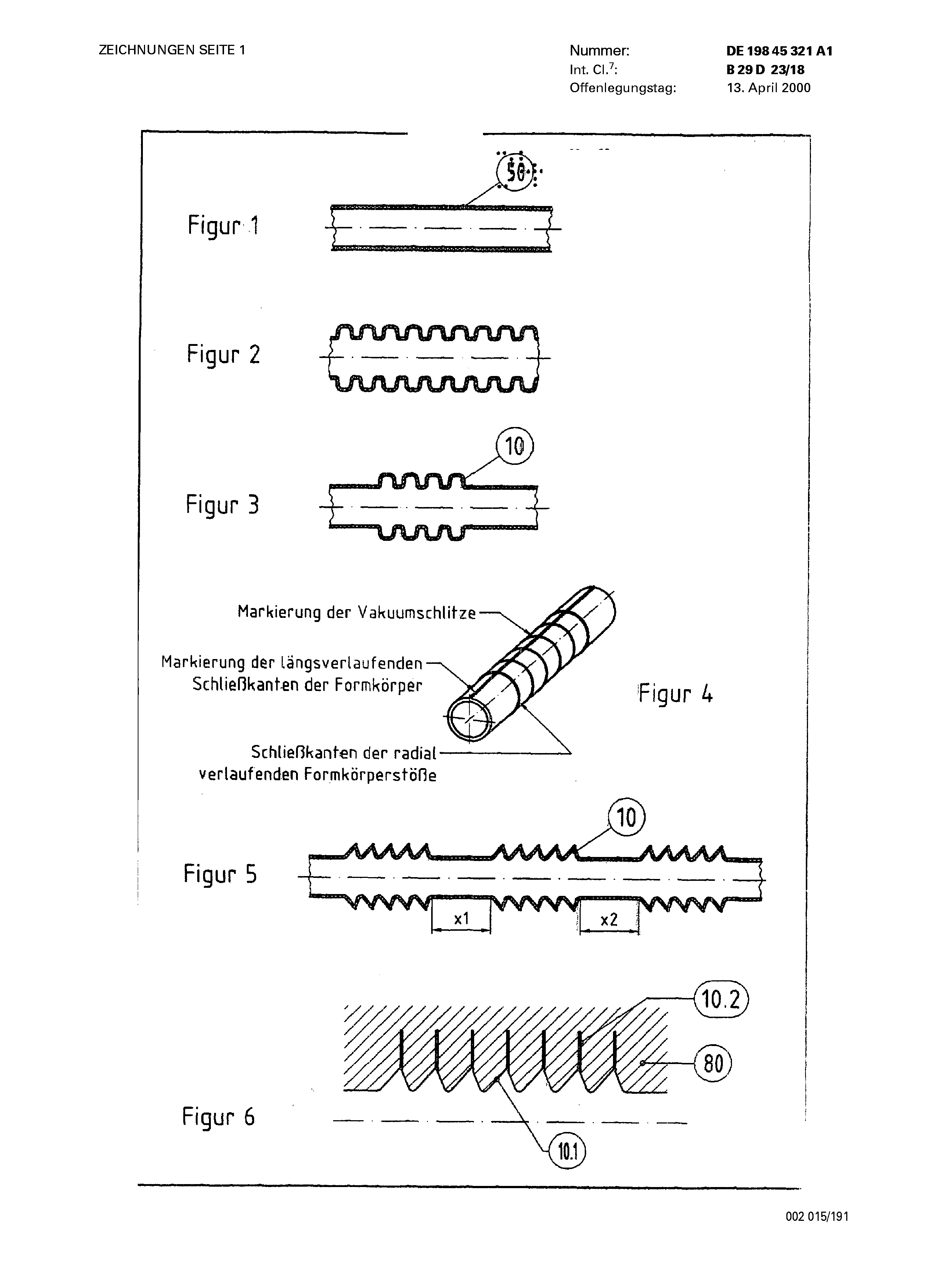
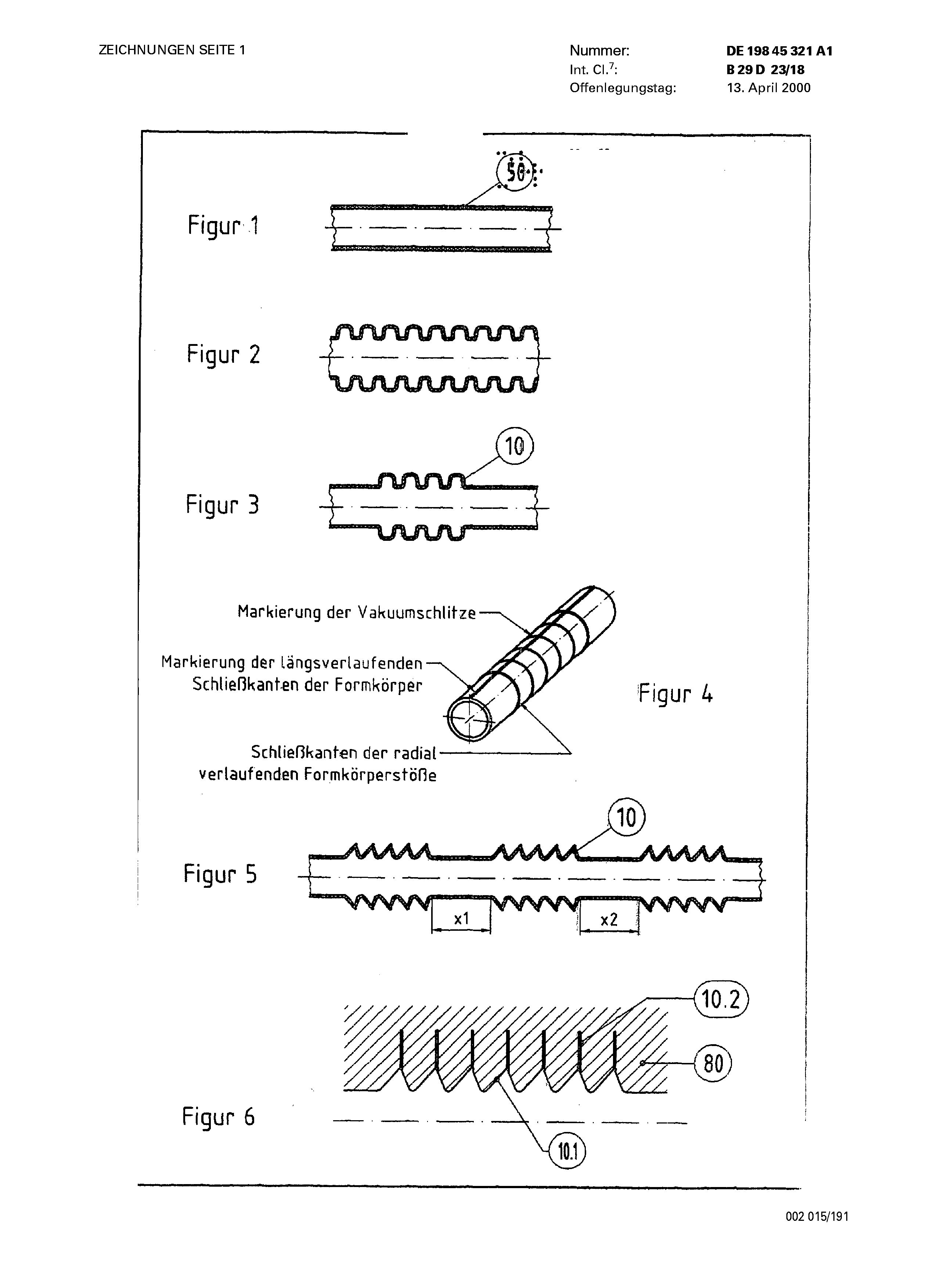
