Method for separation of diamond particle clusters
Method for the separation of diamond particle clustets A method for the separation of diamond particle clusters into discrete diamond particles and/or into smaller diamond particle clusters comprising fewer diamond particles is disclosed. The diamond particle clusters are combined with at least one liquid phase organic or inorganic compound, or with a solution of at least one organic or inorganic compound in at least one solvent to form a reaction mixture. Mechanical means (e.g. shaking, stirring, milling with beads or sonication) are then used to separate the diamond particle clusters into discrete diamond particles and/or into smaller clusters within the reaction mixture producing diamond particles with free bonding sites on the surface of the diamond particles. The at least one organic or inorganic compound (e.g. an alkene such as undecene) then reacts with these free carbon bonding sites present on the diamond particle surface. The surfaces of the diamond particles are functionalised by the reaction with the organic or inorganic compounds and the diamond particles and/or smaller clusters produced are well dispersed in dry powder form, as well as in solution. Claims 1. A method for the separation of diamond particle clusters having a diameter of less than or equal to l.Onnn into discrete diamond particles and/or into smaller dusters comprising fewer diamond particles, the method comprising the steps oft c) combining the diamond particle clusters with at least one liquid phase organic or inorganic compound, or with a solution of at least one organic or inorganic compound at least one solvent to form a reaction mixture, wherein theat least one organic or inorganic compound reacts with unsaturated bonds of carbon atoms present on the diamond particle surface; and d) using mechanical means to break up the diamond particle clusters into discrete diamond particles and/or into smaller clusters comprising fewer diamond particles within the reaction mixture; wherein step h) produces diamond particles with free bonding sites on the surface of the diamond particles and wherein the at least one organic or inorganic compound reacts with at least some of the free bonding sites on rile diamond particles. 2. A method according to claim 1, wherein step b) includes shaking or stirring the reaction mixture or applying ultt-asomcation to the reaction mixture. 3.Aniethod according to claim 2, wherein step h) isa mechanical milling step and includes the introduction of milling beads to the reaction mixture. 4. A method according to Claim 3, wherein the milling beads are ceramic mil ng heads. 5. A method according to Claim 4, wherein the milling beads are selected from the group comprising 2ircona beads and silica heads and mixtures thereoft 6. A method according to any of claims 3 to 5, wherein the milling beads are larger than the diamond particles by a factor of between 111)11) and 1 00(160.7. A mci-hod according to any preceding claim, wherein the diamond particles have a diameter of 0.5mm or less.8. A method according to any prcceding claim, wherein the diamond particles arc nanodiamond particles and have a diameter in the range I to l000nm.9. A method according to any preceding claim, wherein thc at least one organic compound is an unsaturated organic compound.10. A method according to any preceding claim, wherein the at least one organic compound is a straight chain allcene.11. A method according to any preceding claim, wherein the organic compound is unsaturated at the first position.12. A method according to any preceding claim, wherein the at least one organic compound comprises a number of carbon atoms in tIle range 6 to 12.13. A method according to any of claims 2 to 12, wherein the reaction mixture is shaken at a frequency of at least 10 liz.14. A method according to any of claims 2 to 12, wherein ultrasonicarion is applied to the reaction mixture at a frequency of not more than 8OkHa.15. A method according to any preceding claim, wherein cooling is applied during step h) to cool the liquid phase organic compound to a temperature of not more than the boiling po-of the reaction mixture.16. A method according to any of claims 3 to 15, further comprising: step c) separating the discrete diamond particles from the milling beads.17. A method according to Claim 16, wherein in step c the diamond particles are separated from the milling heads using a method selected from the group comprising: filtration, centrifugation, extraction, precipitation, decantation and combinations thereoF.18. A method according to any preceding claim, further comprising the step of isolating the discrete diamond particles in solid form.
Field of the Invention
The invention relates to a process for separating clusters of cliantond particles, and in particular to clusters of micron anti nano-sized diamond particles. The invention also relates to a process for the functionalization of separated diamond particles, and in particular to the functionalization of separated micron and nano-sized diamond particles.
Background to the Invention
Diamond particles, including diamond nanoparticles or nanodiamonels, have potential uses in a wide variety of applications includmg platrng, lubricating oils, polishing, coating agents for metal surfaces, abrasives, and biomedical devices Nanodiamonds may he produced by the detonation of explosives with a negative oxygen halance in hermetic tanks. These detonation nanodiasnonds have particle siaes typically in the range 1-SOntn and ate particularly prone to agglomeration, forming tightly aggregated secondary particles or clusters.
Nanodiasnonds and micron-siaed diamond particles may also he synthesised by high tenpetatLLre-and high pressure (HTIHP) methods. These diamond particles typically have particle sizes in the range mm-I 000 micron. Alternative sources of nano-or niieron-siaed diamond particles include diamond particles formed by HTHP methods and natural micron diamond powder. These diamond particles are also prone to aggregation forming aggregated secondary particles or clusters. Sizes of aggregated diamond particles vary widely but can he up to several lOGs of microns in size.
A known method for separating these tightly aggregated nanodiamond clusters is via wer-stirred-media-mffling in water using micrometer-sized heads to break up the aggregates and simultaneously dispersing them in water. This method has been used to form clear colloidal solutions of nanodiamonds (Adv Mater. 2007, 19, 1201-1206). This method is only suitable for the formation of nanodiamond dispersions in solvents since the nanodianronds tend to re-agglomerate after drying.
T_1S2i111 0/0298601) describes a method for i-lie chemical functionalization of i-he surface of nanodiamonds in a liquid phase. The method uses a wet milling process similar to that described above, prior to treatment with acid. Tilie method attemprs to dc-aggregate particles using an acid treatmenr step, which leads to formation of carhoxvlic acid groups on the surface of the nanodiamonds. Tihere is no step in i-he process which actually breaks apart the clusters of nanodiamonds. In addition, the presence of carhoxyhc acid groups on the surface of the nanodiamonds will actually promote aggregation of the nanodiamonds after drying.
it would be desirable to provide an improved method for the separation of secondary diamond particle clusters into discrete particles, providing diamond particles that are well dispersed in dry powder form, as well as in soluuon.
Summary of the Invention
According to a first aspect of the present invention, a method for the separation of diamond particle clusters having a diameter of less than or equal to 1.0mm into discrete diamond particles and/or into smaller clusters comprising fewer diamond particles, comprises the steps oft a) combining the diamond particle clusters with at least one liquid phase organic or inorganic compound, or with a soltition of at least one organic or inorganic compound in at least one solvent to fhrm a reaction mixture, wherein the at least one organic or inorganic compound reacts with unsaturared bonds of carbon atoms presenr on the diamond particle surface; and b) using mechanical means to break up the diamond particle clusters into discrete diamond particles and/or into smaller clusters comprising fewer diamond particles within the reaction mixture; wherein step b) produces diamond particles with free bonding sites on the surface of the diamond particles and wherein the--at least one organic or inorganic compound reacts with at least some of the free bonding sites on the diamond particles.
Step h) of the method involves imparting kinetic energy to the diamond particle clusters, causing the clusters or aregates to break apart into individual diamond partides and/or into smaller diamond particle dusters containing Fewer diamond particles. Preferably, step b) includes sinking or stirring or ulnasonication of the reaction mixture. Dangling bonds of carbon atoms are formed in places where i-he diamond clusters break S apart. The at kast one organic or inorganic compound(s) added in step a) reacts with these dangling bonds of carbon atoms, saturating the bonds. This prevents re-aggregation of the individual diamond partides or re-aggregation of i-he smaller diamotid particle clusters since the active sites on the surface of the diamond particles are occupied through reacflon with the organic or inorganic compound(s) added in step a). The nature of the chemical groups added to the surface of the diamond lDtice5 is governed by the organic or morganic compound(s)_used in step a) of the method.
Preferably, the method produces discrete diamond particles. Tflic product may include smaller diamond particle clii sters comprising fewer diamond particles.
Preferably, the reaction mixture formed in step a) is in the form of a slurry.
The at kast ()flC ()rgarnc or inorganic compound(s) may he dissAvcd in at kast one s(ilvcnt to form a S(JUtli)fl prior to combining with the diamond particle clusters. Preferabhr the solvent is inert. Preferably the at east one solvent is an organic solvent. The at least one organic or inorganic compound(s) may he dissolved in a mixture of sokents. Solvent mixtures may he used to Iidp improe soiubthty of the organic or inorganic compound(s).
A mixture of more titan one organic or inorganic compounds may be used in step a) of the method.
The at kast one organic or inorganic compound may be any compound that reacts with free radica's.
The at kast one organic or inorganic compound may be a compound which generates free radicals within the reaction mixture. Suitabk compounds inducle halogen molecules, azo compounds and organic peroxmdes.
Preferably, step b) is a mechanica' milling step and further includes the introduction of milling beads to the reaction mixture. When milling beads are present shaking or stirring the reaction mixture or by applying ultrasonication i-u the mixture causes the milling he>tds to collide with the diamond particle clusters. Tihis causes the clusters to break apart into individual diamond particles and/or smaller diamond particle dusters containing fewer diamond particles.
Preferably, the milling beads are ceramic milling beads. More preferably, the milling beads are selected from the group comprising zirconia beads and silica beads and mixtures thereof.
Alternatively, the milling beads may be diamond particles which are larger in size compared to the eiamond particles to he separated.
Prefei-ahly the milling heads ate latger in size than thc diamond patticles by a factot of between 100 and 100000.
When the diamond particles are nanodiamond particles the milling heads preferably have an average diameter of less than 1mm. More preferably the milling heads have an average diameter of less than 0.5mm. Still more preferably the milling heads have an average diameter of less than or equal to 0.linni.
Preferably the diamond particles have a diameter of less than 0.5mm.
More ptefetahlv the diamond pai-ticles ate nanodiamord particles with a diametet in the tange I to I 0(IOnm.
TIhe diamond particle clusters used in the method may be from any commercial source. For example the diamond particle clusters may he nanodmamond aggregates from a detonation nanodiamond source, known as detonation nanodiamonds or DND. Alternatively, the diamond particle clusters may originate front a high temperature and high pressure (HTIHP) method of diamond particle synthesis or may originate from natural micron diamond powder. Diamond particle clusters from HTHP methods may he further ground to reduce the size of the particles before being treated to separate the clusters using the method of the invention.
Where raw, untreated, detonation nanodmamond powder is used in the method of the invention, die method may include the initial step of treatment of the nanodiamonds with an oxidising mineral acid. The mineral acid may he selected from the group comprising 11C104, 112504 and 11N03. Treatment with oxidising mineral acid purifies the detonation nanodiamond powder by removing any non-diamond fornis of carbon.
Alternately the iniHal step may involve a treatment of raw nanodianionds with oxygen or air or nitrogen oxides at elevated temperatures LL) tO 700 C. The at least one organic or inorganic compound may be any compound that reacts with free radicals and/or that reacts with unsaturated (danglin bonds of carbon atoms present on the diamond particle surface. This includes any unsaturated organic compounds, and particularly includes alkenes, unsarurated fatty acids, and free radical inhibitors. An unsaturated organic compound contains at least one unsaturated CC double bond. The organic compound may be a liquid phase compound, alternatively, or additionally, it may be dissolved in at least one inert solvent prior to reaction with the diamond particle clusters. Preferably the inert solvent is an organic solvent. The organic compound maybe dissolved in a mixture of solvents.
Preferably, the alkenes from which tlL-*at least one organic compound may be selected comprisc Cs to (x alkenes, more preferably C0 to C13 ailcenes, and mixtures thereof Preferably the alkenes are straight chain alkenes. Use of straight chain organic compounds avoids steric hindrance for reactions to occur. Preferably the alkene double bond is located at the first position. Location of the double bond at the tirst position also avoids stetic hindrance.
In a particularly preferred embodiment, the alkene is selected from the group comprising i-undecene or dodecene.
Preferably, the unsaturated fatty acids from which the liquid phase organic compound may be selected conipnse C2 to Cu unsaturated fatty acids, more preferably C6 to C12 unsaturated fatty acids.
In a particularly preferred embodiment, the unsaturated fatty acid is hnoleic acid.
When the reacixin mixture is shaken itis preferably shaken at a frequency of at least 10 lIz. More preferably the reaction mixture is shaken at a frequency in the range 10-40000 lIa.
When ultrasonication is applied to the reaction mixture the frequency of ultrasonication is preferably less than 80kHz.
Shaking and/or ultrasonication is preferably perfoi-med iii closed vessels. Valves may be used on reaction vessels to release any build tip of pressure.
Shaking and/or ultrasomcauon is preferably performed under an atmosphere of inert gas. The inert gas may be selected from the group comprising nitrogen and argon.
Shaking and/or ultrasonicatli)n is preferably perf'I)rmed at atmospheric pressure. Shaking and/or ulirasonicadon may be performed at elevated pressure in order to increase the reac don rate of the at least one organic or inorganic compound(s) with the diamond particles. Shaking and/or ultrasonicarion may he performed at elevated pressure in order to increase the boiling temperature of the at least one solvent or the reaction mixture.
Shaking and/or ultrasonication is performed ar temperatures below the boiling point of the at least one organic or inorganic compound(s), or the boiling point of the reaction mixture.
Preferably, the reaction mixture is shaken continuously, or idtrasonication applied continuously, provided that continuous cooling of the reaction mixture is applied. Preferably the reaction mixture is continuously cooled to a temperature of not more than the boiling temperature of tle-at least one solvent(s) and/or the at least one organic or inorganic compound(s) of thc reaction mixture at the pressure at which i-lie process is conducted. The coohng temperature depends on the erganic/inorganic compound(s) and/or solvent(s) being used in the reaction mixture and should he maintained below the boiling temperature of the reaction mixture at the pressure at which the process is conducted.
Alternatively, the reaction mixture is shaken, or ultrasonication is applied, in cycles, and preferably the duration of each cycle is not more than lO minutes.
Mechanical shaking or tdtrasonication of the reaction mixtutv can eaLise a rise in temperature through the flThDact of diamond particle clusters with other clusters or ehamonel particles and through chentical reactions occiarring in the mixture. When milling heads are used heat can also he generated when the heads coffide with diamond parlicle clusters or diamond paitcles. Excessive healing can cause polymensation of the at least one organic compound(s), which is not desirable for the method of the invention.
Preferably the reaction mixture is cooled between shaking or ultrasonication cycles to avoid excessive hearing.
Preferably the reaction naixture is cooled to a temperature of not more than 60CC between cycles. The cooling temperature depends on the organic compound and/or solvent being used in the reaction mixture.
Preferably, the maximum temperature of thc mixture is he maintained below the boiling teniperature of the at least one organic or inorganic compound and/or the at least one solvent and/or the reaction mixture.
When miffing beads are used, the method of the invention preferably includes a further step, c) of separating the separated diamond particles and/or smaller clusters from the milling beads. Preferably the diamond particles and/or smaller clusters arc separated from the niluing beads using a method selected from the group comprising: filtration, centrifugation, extraction, precipitation, decantation and combinations thereof.
The milling beads are much greater in sue compared to the separated diamond particles so filtration may be used to separate the milling beads from the rest of the mixture.
Alternatively, the milling beads may be separated from the test of the mixture using a centrifuge or simply by mixing. illie slurry from step h) may he diluted with an organic solvent, or a mixture of organic solvents, prior to separation in a cenrrifuge or by mixing. The milUng beads are much larger in siae compared to the separated diamond p>trticles, so these fall to the bottom of the mixture quickly in >t centrifuge or shortly after mixing. The supernatant containing the suspended diamond particles can then he separated from the milling beads by decanting. This process can be repeated several times if necessary.
Alternatively, or additionally, the separation step may be carried out using a soxhlet extractor and an organic solvent, or mixture of solvents, in which the diamond particles are at least partially soluble. Milling beads are insoluble in organic solvents and therefore are not extracted into the organic solvent or solvents.
The organic solvent may he a non polar solvent ora polar solvent or a mixture of several s'I)lvents.
The reacHon mixture from step h) may he Erst suhected to a centrifugarion step or a liiixitig step or a filftation step to remove the majority of milling heads. The restdtant filftate or supernatant Imay then he subjected to a further separation step, for example using a soxhiet extractor.
Preferably, the method of the invention further comprises the step of isolating the diamond particles in solid form. Separated diamond particles can be isolated by evaporation of excess organic or inorganic compound(s) or excess solvent(s) . AlternaHvely, the diamond particles li-lay be extracted itito all organic solvent (or a mixture of solvents) and the diamond particles are isolated by evaporation of the organic solve tit(s).
The method of the invention provides a simple method for the separation of diamond particle clusters into discrete diamond particles and/or smaller diamond particle clusters comprising fewer diamond panicles hy functionalising the surface of the diamond particles with various chemical groups. The nature of these chemical groups is governed by the organic or inorganic compound(s) used in step a) of the process. There are very few steps to the method, resulting in increased yields, and tile diamond particles produced are well dispersed in dry powder form, as well as in solution.
Brief Description of the Drawings
In the drawings, which illustrate preferred emhodiments of the invention: Figure 1 is an ET1R spectrum of nanodianionds alkylated with 1 -undecene; Figure 2 is a Cls X-ray photoeniission spectrum of nanodiamonds alkylated with 1-undence; Figure 3 illustrates Super STEM images of nanodiamond powder functionallsed with 1-undecene that has been re-suspended in solution and deposited by a drop cast method onto a carbon lacey TEM grid; Figure 3a illustrates a bright-field (BE) image of separated nanodiamond particles; Figure 31) is a BF image of twinned particles; Figures 3c and 3d illustrate a I IAADF image ot nanodiamotid ci-ystallinii-y; Figure 4 illustrates HRTFIM images and an associated fast Fourier transform (FFT) of evaporated nanoehamond powder evaporated at -200[deg.]C for 15 minutes, Oil a lacey carbon TEv1 grid.
Figure 4a is a BE image of sparsely distributed nanodiamonds; Figure 4h is a magniEcarion of a box-selected area in Figure 4a; Figure 4c is a RF image of an isolated nanodiamond; and Figure 4d is an FF11 analysis of the nanodiamond crystalline structure from Figure 4c.
Detailed Description of the Preferred Embodiments
Nanodiamonds used in the examples were produced by the detonation of explosives with a negative oxygen balance in hermetic tanks.
Examples
Example 1: alkylation with 1-undecene The detonation nanodiamond powder was boiled in a mixture of concentrated sulphuric and perchloric acids (1:1) fir a period of two hours in order to remove any non-thamond fi)rms of carbon. After this purification step the powder was dried in air at 50[deg.]C to produce dr nanodianiond powder containing clusters of nanodiam onds.
2IiOmg of the dry nanodiamond powder was mixed with Ig of zircoma/silica heads with an average diameter of approximately 0.1mm. The mixure was placed in a plastic vial (2in1 and filled with 1-undecene (CttHn).
the vial containing the in ixture was shaken in a \tiniBeaelhearer 31 I 0T3X (Stratech ScientiFic Ttel) at a frequency of 4500 Hz. Shaking was performed in cycles lasting 5 minutes. After each cscle the sample was cooled to avoid excessive heating by immersing the vial in water with a temperature of approxmiately 15[deg.]C.
Shaking and cooling was repeated twelve times to give a total shaking time oft hour.
After shaking, the slurry containing the beads, the nanodiamonds and the 1 -undecene was transferred to a \Xhatman cellulose extraction thimble and placed inside a Quickfit Sohxhlet exctrator to recover the nanodiarnond material. Extraction of the nanodiamond particles was performed with undecane at 174[deg.]C for I 5 hours.
After the extraction, the solunon was centrifuged at lti000g for 1 hout-.
The solution was left to evapot-ate completely to leave the alkylated nanodiamonds as a pale white powder residue.
(:onfkmatioii of 1-undecene attachment to die nanodiamonds was performed by Foutier transform infrared specrroscopy (FIITR). Figure 1 shows the FTITR spectrum of the alkylated nanodiamonds. The peak at 2955 cnr' indicates the presence of die -CH3 asymmetric stretch mode, while bands at 2924 cm-1 and 2854 cnr' confirm die presence of -CH1 asymmetric and symmettic stretch modes The appearance of a terminal methyl group can be demonstrated by vibrational absorption at 1463 and 1375 cln' corresponding to C-CT Iiasvnimetric and symmetric bending vibration, respectively. The complete absence of CC groups which would appear at 1610-1680 cm confirms that the 1-undecene is involved directly in bonding to the surface.
Tt is suested that the x bond of the alkene is broken, transforming into a a bond linking the alkene to the nanodianiond surface.
A sample of the alkylated nanodiamond powder was dissolved in pentane and several drops were deposited and allowed to dry upon a pre-cleaned, and Argon ion sputter tantalum foil for X-ray photoentission spectroscopy XPS) characterisadon.
Figure 2 illustrates the Cis X-ray photoemission spectrum of the nanodiamonds treated with 1-undecene. A single peak at a binding energy of 285.8 eVis observed, with a full width at half maximum (FWIIM) of 1.7eV indicating the presence of C-C sp3 bonding within the material. This confirms that tile 52 component present in pristine nanodiamond powder has been removed.
The SuperSTLM niicrographs shown in Figure 3 demonstrate that a sohiuon of the alkyt-coated nanocliarnonds with cianteters of approxintatelv Snrn can be sparsdy dispersed onto the surface of a acey carbon TlFi\'{ grid wand subsequently allowed to dry at ambient temperature (see Figure 3a. Figures 3a and 3h conrm that the diamond particles are largely spherical in shape with an average diameter of 5nm. TIilese restilts confirm that the diamond particles remain as discrete paffices after drying.
Figure 4 illustrates HRTEM images and an associated fast Fourier transform FFT) of evaporated nanodiamond powder. Figure 4a iii particular illustrates that tile diamond nanoparticles are well-separated and deposited successfully onto a lacey carbon grid by evaporation at 2OO0C for 15 minutes. Enlargement of the micrograph, Figure 4b, shows that separated nanodiamond particles have chameters ranging from 2- 4nm. Figure Se shows an isolated particle with a diameter of 4nm, which was subsequently used to determine the crystalline structure on-he evaporated nanodiamonds. Determination of the crystal structure was carried out by FFT analysis which can be seen in Figure 3d.
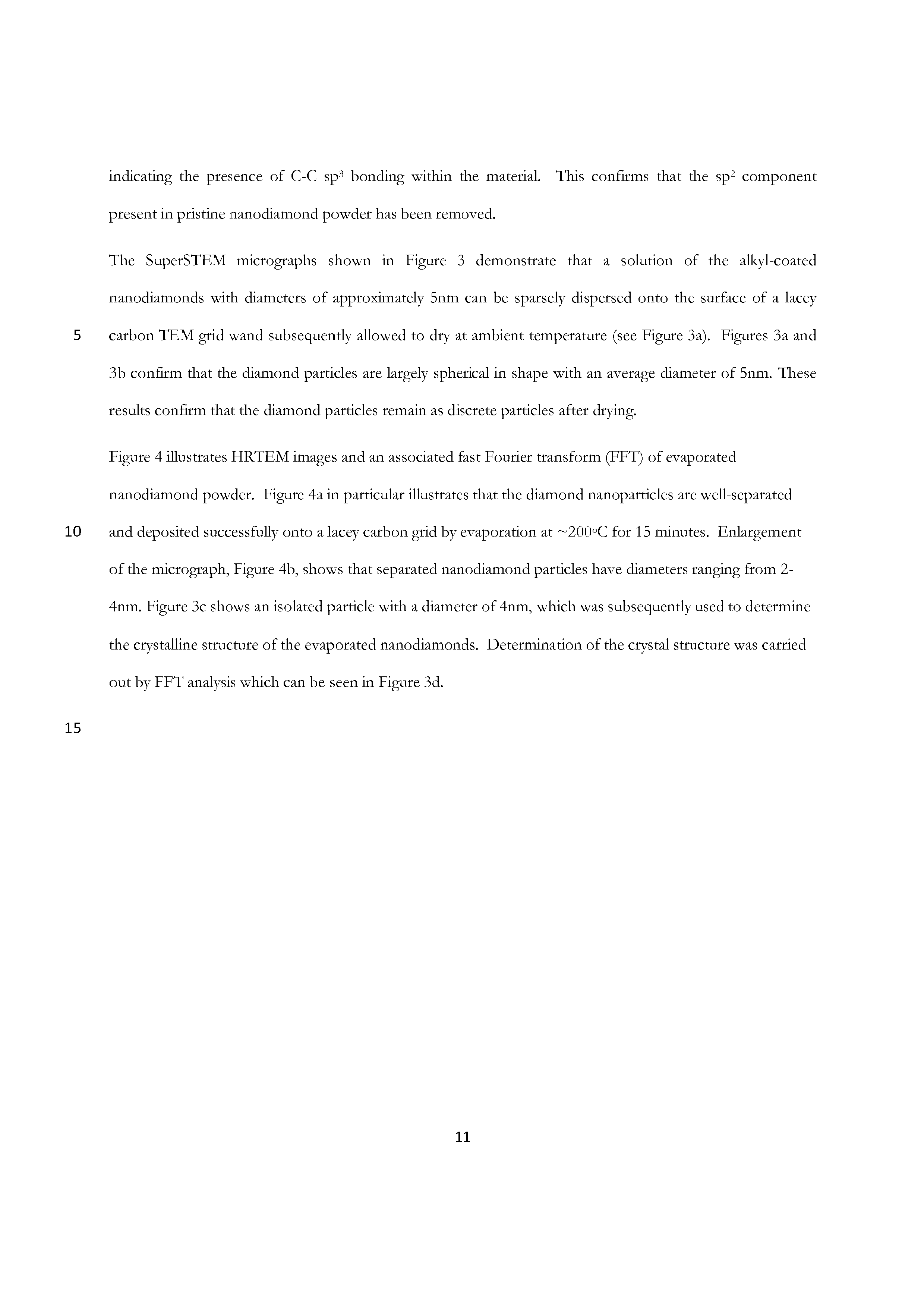
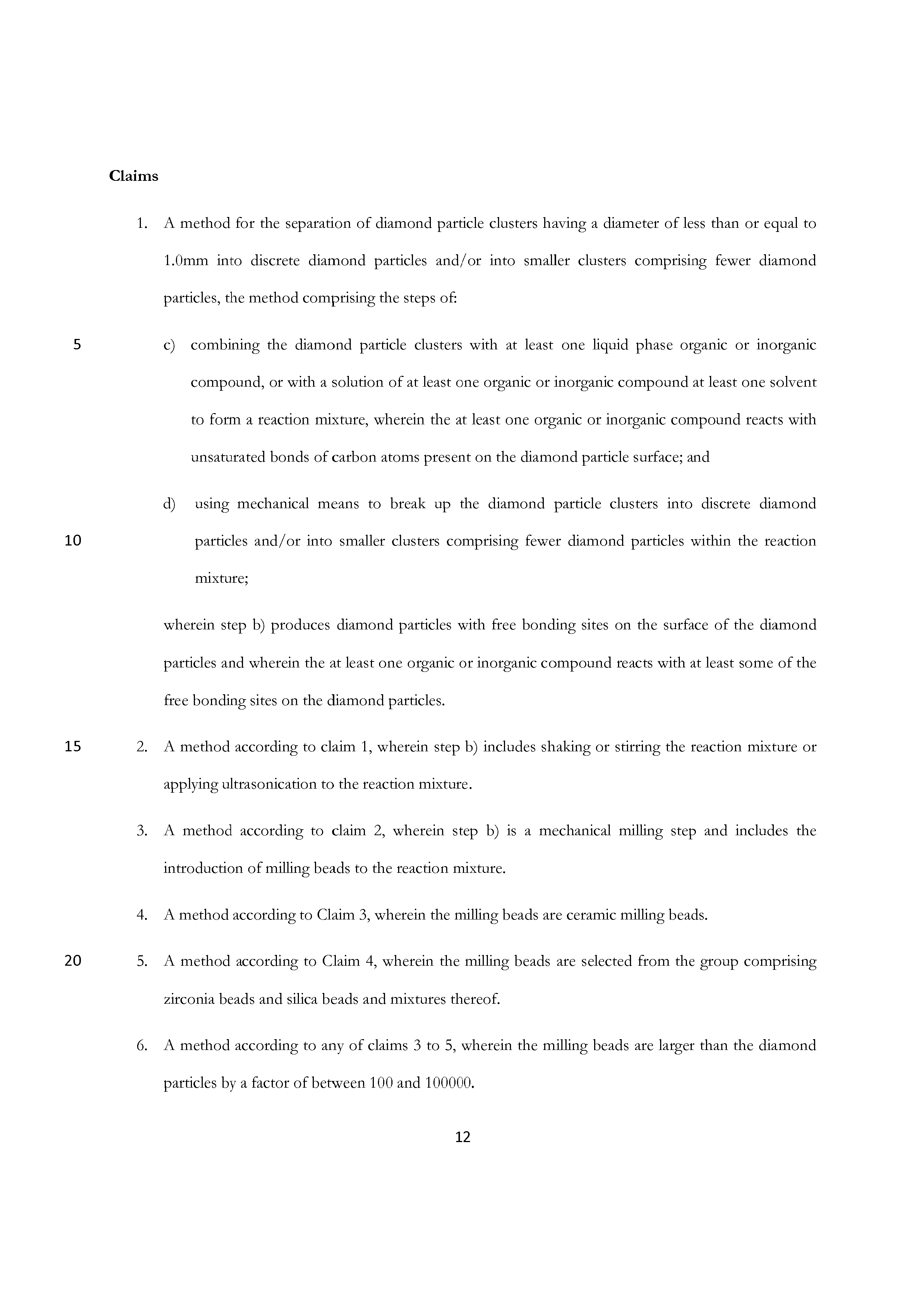
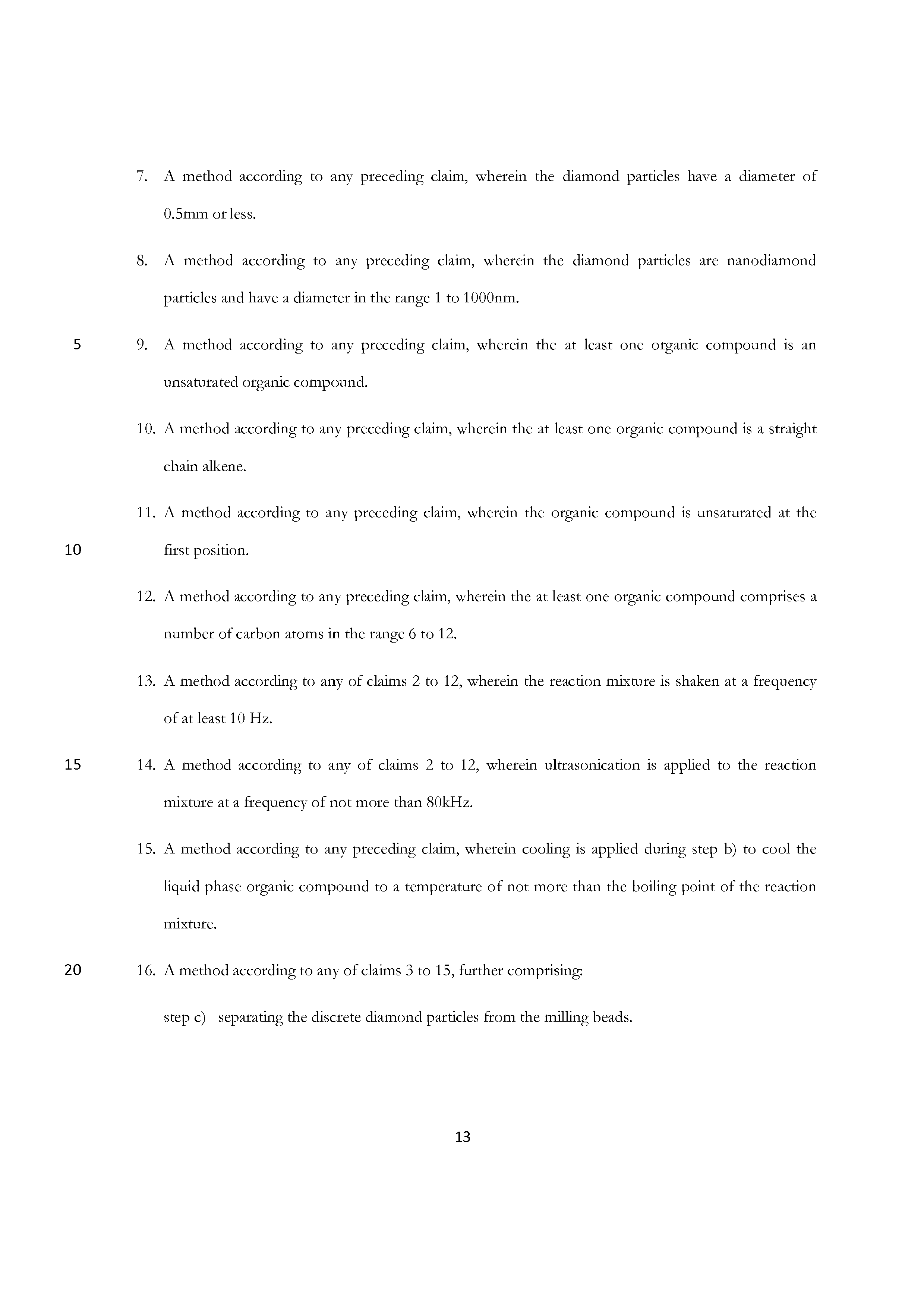
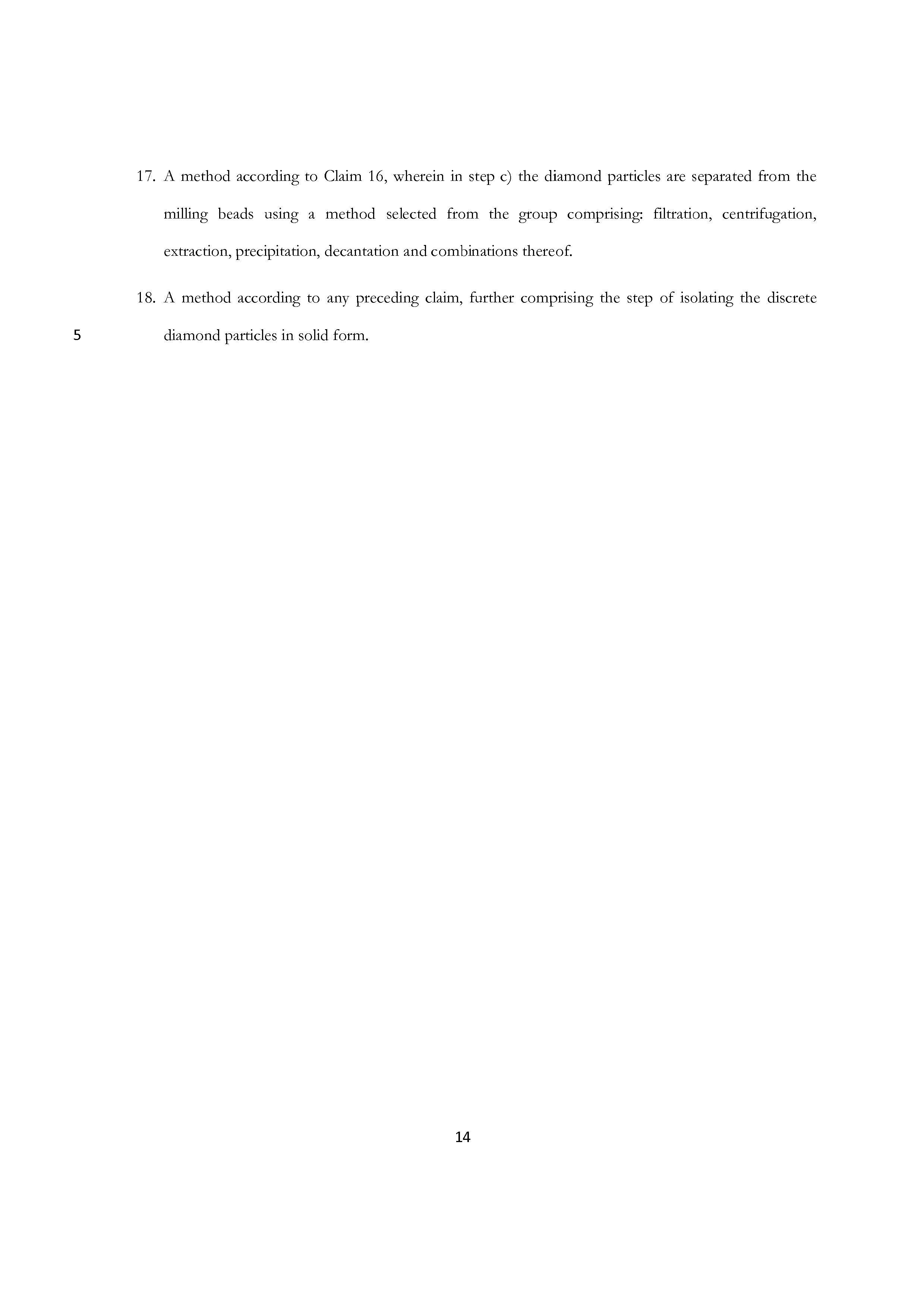
CPC - классификация
BB8B82B82BB82B3B82B3/B82B3/0B82B3/00B82B3/000B82B3/0009B82B3/006B82B3/0061CC0C01C01BC01B3C01B32C01B32/C01B32/2C01B32/25C01B32/28C07C07CC07C2C07C2/C07C2/8C07C2/86C07C9C07C9/C07C9/2C07C9/22IPC - классификация
BB8B82B82BB82B3B82B3/B82B3/0B82B3/00CC0C01C01BC01B3C01B31C01B31/C01B31/0C01B31/06Цитирование НПИ
KR 1KR 1