자동화 워크셀 제어 방법
The present invention refers to robot, the center number, robot number for lengthening device, and the device including the center robot number for communication between a bus number plower method to work cell number are disclosed. The number of publicly known in the field of robot arm (arm) include on the support structure, the center bus number, robot for operating various portions of a shaft motor number [...] number [e roof tile communication to each other. The center user or user program number by this number made by analyzing each robot operation instruction (instruction) in which ball axis determines operation of the instruction. Various types depending on operation of the robot arm about an axis portion of a robot using the model number counter (inverse geometric) using the limited thereto in data centers. Effectively to move various portions of robot, each robot has an axis command corresponding to the instructions perform actions involving subjected. Each robot is because it includes the unique motion characteristics, unique to the type of robot used characteristics required number integrated center (incorporate) a synbiotic. Thereby the center number program incorporated into a relatively serious door number cause substrate. The number each axial center number associated with each portion of a robot operation commands while communication [e roof tile since, such communication is to transmit the command number number each axial center allowing the modeled, 2n. communication time is relatively long. The purpose of the invention is to simplify programming of the center number, which enhance various violations of the number axis generates transmission data, a method to improve the accuracy of automated work cell number when the robot number word number industry a number by these novel deficiency are disclosed. To this end, the present invention refers to several number by which the number at least three axis having at least one degree of freedom in the robot arm, the center number, robot arm for manipulating at least a portion of each oil function number number number on the robot arm including anxiety plower several motor device, the center and the robot arm number for communication between a bus device number including the automated method to work cell number are disclosed. The method is, A) the number number number [e axis for the center transmitting at command device transmitting the single operation unit number belongs to the robot arm, B) in corresponding calculation unit, based on the number received from a centre for some instructions, an instruction to make a number by which the number motor [...] determining each motor, C) a drive motor number by which the number motor [...] step by step b) including a step of transmitting a command determined in each motor characterized. The f-number identification information (identification) number operation robot arm axis, i.e. robot arm end operation such as to length or angle can represent geometric based on an amount the substrate. Due to the present invention, each robot motor command to the computation of the number by considering all the device belonging to the unit center transmitting at robot number interdependent manner carried out. This robot function optimizing other. The present device by the center robot number simplified programming to the calculation unit number, this number unique to center each robot arm incorporates information managing communications with each motor which does not require the need for violations of the number's oldest. Each robot motor command including the computation of the number command transmitted in data centers by considering all, robot number determined in the device belonging to the calculation unit because, robot and optimizing process from robotic work cell function. In addition calculation units are robot arm due to a sudden specific processing performed work have diameters less than 2000. The number of cells in a range of knowledge of the engineer builds a robot engineering program to center a sophisticated stop or start-up procedure need incorporate less's desire. According to the features of the present invention glass but are not obligation, the method presenting acceptable any combination of this number, one or more of the following features can be integrated. The method - a, D) transmitting the position of the motor and the bag-like number violations of the arithmetic operation unit each motor number, E) calculation unit in, motor based on at every position, each robot arm number [...] position calculating step, F) step e) further comprises the steps of transmitting calculated position number in the center. Step e - calculation unit) in calculating the, measurement of the location of motor time, robot arm estimation operation position of each spherical robot arm axis robot controller according arm operation number number number [...] position the center transferring time considering other. The method - a, G) in calculation unit, based on the motor at every position, Cartesian speed calculating step of feature H) calculated Cartesian speed and compared with a threshold value I) Cartesian speed higher than a threshold value, the center number further comprises transmitting a warning signal from the calculation unit. - Step b) in, number for each motor in response to commands for transmitting at center position must be achieved including operation commands are limited thereto. - Step b) in, the center transmitting at each motor command for the computation of the number based on the commands, for predicting each motor torque is feeding involves other. The center - number to transmit on a number with respect to at least one operating instructions are in [e axis comprising the supporting information. The center transmitting at - number for each motor in response to a command for at least a portion among the locations must be achieved torque calculated on the basis of robot arm comprising compensating for deformation. The method - the j) power supply (powering up) the center robot indicating signal transmitting number comprising, a first and a second robot all motor power supply or power off and number that are ready function power cutoff or copper which specify respectively. The method - the k) calculation unit number from the center, all portions of the robot indicating function signal transmitting wherein, at least one of the corresponding partial deficiency detected a malfunction if all portions of the robot that a specified substrate. Synchronization bus communication mode (synchronous) - supporting substrate. - Bus SERCOS interface type model functions other. The center - number "profile drive (profile drive)" hardware profile instructions to communication with an calculation unit. Example number only when so that, according to the method of the present invention with reference to the attached drawing performed automated work cell number determined through the description of the principle, and it will better the present invention refers to a data must be more other benefits are disclosed. The number of the present invention method to simplify programming of the center, axis which enhance various violations of the number generates transmission data, robot number word accuracy the base. According to of the present invention method, each robot motor command device taking into account the number of computations are all transmitting at the center robot number belonging to the unit performed interdependent manner optimized is the function of the robot, the center number programming is simplified substrate. In addition, according to of the present invention method, with a robot capable of optimizing robotic work cell function, the center cell number range still or start-up procedure for a refined knowledge of engineers robot engineering program need incorporate less's desire. Figure 1 shows a the present invention according to number automated work cell structure using the method also are disclosed. Figure 2 shows a method main function and also the present invention according to number associated with the communication flow as shown SUMMARY function are disclosed. As shown in fig. 1, automated work cell (2) a robotic arm (4) and, robot arm (4) the device number (6) on, the center number (8) on, partially shown in two electrical actuator having a predetermined wavelength. Robot arm (4) is being changed to A1 to A6 with its axis consists of six of robotic and into. The term "axis" here robot engineering a mirror, i.e. free sense related to the degree of water are used. The specification (A1 to A6) or the shaft rotary in degrees of freedom indicating other. The robot number device (6) is a robotic arm (4) disposed adjacent and six of motor number violations (61 to 66) having a predetermined wavelength. Violations of the number each motor (61 to 66) is a robotic arm (4) to the first and second portions of the motor (M1 to M6) [...] be function of number. The operation of the motor (M1) without any other axis (A1) and axis robot arm (4) positioned between the movable end robot arm (4) part of the allows rotation. (M2, M3, M4, M6) (A2, A3, A4, A6) reducing power consumption as well as movable axis motor allows each rotation. On the other hand motor (M5) (A5, A6) 2n. rotation of the movable shaft. Shaft coupling exist between (A5, A6), the operation of the rotation motor (M5, M6) require a shaft (A5) reducing power consumption. Each motor (M1 to M6) is motor shaft measured at angular positions (angular position) including information about the relevant electrical signal (S12I ) (I is an integer between 1 and 6) disposed coder (coder) for delivering motor shaft (12) is mounted thereto. Two electrical actuator is stored by each motor (M21, M22), violations of the axis motor winding number number (121, 122) by respective number is the position signal (S1221 , S1222 ) For delivering coder (12) communicates with each other. The coarse 2 also as shown, the center number (8) is a robotic arm (4) require a sophisticated behavior and operation of the assembly object such as, motor (M21, M22) including an electric actuator operated by a gripper (gripper) or conveyor user program is created for performing selective behavior (30) based on an automation cell (2) decodes the number function. For example thereafter a robotic arm (4) should reach the ends of the series of Cartesian comprising the coordinates can be. Modified customer, user or automated actions work cell (2) programmer accessible panel is stationary or portable number (32) can be determined by a user based on between embodiment. The center number (8) is desirably SERCOS III series embodiment liver function according to a field bus (14) by the device number (6) communicates with each other. The device number (8) in number while the device is "master" (6) "slave" is are disclosed. The number device (6) comprises a field bus (14) number by the center (8) dedicated communication with (dedicated) communication card (60) having a predetermined wavelength. The device number (6) is in addition operation or power supply command such as commands through the motor number violations (61 to 66) to transmit function calculation unit (10) comprises. Calculation unit (10) is in particular for this purpose comprises a microprocessor and a memory. Calculation unit (10) violations of each motor number (61 to 66) can be communicates with. In this way, motor number violations (61 to 66) number on the center (8) is made in each data transmission between motor number violations in center, center modeled motor number at an calculation unit (10) is managed by the other. Robot arm (4) [...] number of robot arm (4) about an axis (A1 to A6) so that the corresponding free generates predetermined substrate. SERCOS III interface model that is unique to during initialization step, (A1 to A6) communication is associated with a virtual axis robot arm respective axis to the c1. [e roof tile number. The number in the same manner as a general-purpose axis number [e roof tile number violations of the virtual axis center (8) receive an instruction from at least one motor based on a command corresponding number deemed plower are disclosed. Virtual axis number violations of the configuration, the number, state and position inquiry, diagnosis and supervision of an instruction set for determining "profile drive" hardware profile to conform to specified substrate. ". ". ". "". "Profile drive" hardware profile based on the commands associated with the center number (8) usable in violations of the number generated by the contents from the axis command is a command calculation unit (10) N. by. Each virtual axis number violations of the robot arm (4) and the external actuator automated work cell number (2) violations of the number present in two axes (121, 122) in the same manner has assigned address. The present invention according to number the automated work cell method (2) of certain functionality prior of robot arm robot arm (4) all motor power supply step the received signals. Power is supplied (A1 to A6) for supplying respective axis power command (COi ) Including at least one master data (i is between 1 and 6) to a professional (telegram) bus (14) number to transmit the center (8) disclosure by are disclosed. The device number (6) of communication card (60) for ad to which receives an Image captures. Then communication card interrupt (interrupt) calculates unit (10) and to transmit, corresponding calculation units are professional and play, robot arm from them (4) of respective axis (A1 to A6) extracts the instruction (Coi), the processing advances to a. Bus SERCOS III interface protocol (14) each device connected to the master data of relevant data (location) material can be commanded to a professional in the main substrate. Calculation unit (10) for ad to the center part of the command response recording number (8) to transmit, the center axis is specified power supply associated with the command number corresponding lowered substrate. The center number (8) until receiving instructions to transmit on a final power supply, motor and powered by copper number not number thread number. For each motor (M1 to M6) power supply command (O2I ) (I is between 1 and 6) is calculation unit (10) each motor by law number (61 to 66) transmitted to. All motor power supply and calculation unit (10) violations of the motor number (61 to 66) each motor (M1 to M6) from the power supply when it receives information that, ready state final shaft function by the center number (8) of indicating to a professional (T0 ) Is calculation unit (10) by card (60) transmitted through. The center number (8) of programmer may be permitted robot arm (4) axis (A1 to A6) (M1 to M6) motor power supply command for automated cell (2) to which the other power supply command and similar motor (M21, M22), this robot arm (4) in compliance with a two-axis the axis of the remaining "profile drive" hardware profile number the center (8) recognized's oldest. Calculation unit (10) for managing the supply of various motor robot arm (4) of respective axis (A1 to A6) since treating all command, the center number (8) of programming are simplified. Automated cell (2) when performing a process to be automated, the center number (8) includes a robot operation program including instructions should be performed (30) on a chuck. Each communication cycle, a robotic arm (4) associated with the respective axis (A1 to A6) command for virtual axis [e roof tile number (C1I ) (I is between 1 and 6) a robotic arm (4) in a case of the Cartesian coordinates of its ends operation of operation commands are back-EMF model (36) using path generator (34) by limited thereto. The second gap-fill SERCOS III interface, defined each communication period, all axis command (C1I ) Expert master data (T1 ) (C1I ) Transmitted in the form of bus. Communication card (60) which receives special d2. Then communication card calculation unit (10) sends the interrupt request, calculation units are professional and play, axis therefrom command (C1I ) To extract, the processing advances to a. The corresponding during processing, calculation unit (10) violations of the motor number (61 to 66) for each motor (M1 to M6) number by which the command (O1I ) Calculates (i is between 1 and 6). For each motor command (O1I ) Number is the center (8) all received from (C1I ) Having an identical motion transmission based on limited thereto. Corresponding command is motor current location is achieved without using a tool. (A6) (A5) existing between the coupling shaft axis then calculation is to considering, axis (A5) require use of operation of the motor (M5, M6). For each motor command (O1I ) Between the gear teeth of the computation of the motor axis of rotation of the robot is taken into consideration as follows. For each motor (M1 to M6) command (O1I ) Determining and regulating of a supply current motor phase for each motor responsible motor number violations (61 to 66) transported to. Each motor shaft at angular positions each motor shaft disposed on the coder (12) detected by the other. Signal (S121 To S126 ) In the form of motor phase for each motor number corresponding information transmitted [...] slave supply current can be the main substrate. Calculation unit (10) is in addition motor number violations (61 to 66) through connection, robot arm (4) at angular positions where each motor shaft, transmission reverse motion model (40) robot arm applying (4) axis (A1 to A6) moveable about portion of at angular positions (Pi ) (I is between 1 and 6) related to HRV. Because of the coupling of shaft (A5, A6), motor (M5, M6) (A6) at angular positions of shaft axis at angular positions (P6 ) On the determination of affecting the other. Calculation unit (10) in addition based on the measurements, the rotational speed of the robot a rotatable portion about an axis, and is displayed to torque supplied by, or any other data useful for can be calculated. As a result, the second gap-fill and SERCOS III, each of the synchronization communication cycle robot calculation unit (10) a robotic arm (4) axial at angular positions (Pi ) Including a data telegram (T'1 ) Creating and communicating card (60) number through the center (8) components in the. Corresponding information automated cell (2) secured on the number of program (30) can be used. The center number (8) then are attached example number (32) that can be displayed on the robot arm (4) end Cartesian position (Pc ) To obtain direct geometric model (direct geometric model) (42) can be used. Calculation unit (10) a robotic arm (4) (A1 to A6) at angular positions about the axis of the rotatable portion of (Pi ) (I is between 1 and 6) on the basis of, for example robot arm (4) end tool clamp (400) located on at least one of characteristic points of (B) computing a position can be Cartesian, corresponding feature of Cartesian speed (V (B)) can derive therefrom. The predetermined threshold comparison calculation unit (10) in combustion chamber. (B) corresponding feature of Cartesian speed (V (B)) when the corresponding greater than a threshold, calculation unit (10) violations of all motor number (61 to 66) up to a suspend command, error number for ad to informing the center (8) components in the. Modified customer, calculation unit (10) a robotic arm (4) associated with the respective axis (A1 to A6) command for virtual axis [e roof tile number (C1I ) (I is between 1 and 6) of feature based on Cartesian speed (V (B)) related to HRV. Robot arm (4) movements of articulation due to gravity or inertial force torque applied (Fi ) (I is between 1 and 6) taken into account in the estimation of dependence of each motor and when can be substantially enhanced. Torque prediction (Fi) dynamic model (44) using calculation unit (10) of the robot arm (4) of each motor can be made to. A robotic arm dynamic model (4) able to allow the required around the acceleration command (C1I ) For knowledge WIPO. Robot arm (4) are installed robot arm (4) of each motor shaft axis (A1 to A6) command of all prediction is torque (Fi) (C1I ) Must take into account that substrate. Once torque prediction (Fi) is obtained when, this motor data or "constant (constant)" (46) by applying current command to convert, supply current phase number for the loop (50) can be incorporated as input to a motor number violations (61 to 66) transmitted to. According to alternative embodiments, supplied to each joint torque (Fi ) Prediction calculation is a robotic arm (4) axial at angular positions (Pi ) Disapproval using. The torque applied articulation (Fi ) (I is between 1 and 6) prediction a robotic arm (4) delivered by weight since more accurate disclosed. Each load mass, and an inertia matrix is characterized by a position of the center of gravity as well as load is attached free generates vehicle from the outside. The center number (8) of the programmer each robot arm (4) with respect to an operation number in [e axis weight can be specified. For example tool clamp (400) for the load transmitted from the dedicated number [...] (A6) specify load commands to be coated. The front arm (402) (A4) for the load transmitted from the dedicated number [...] specify load commands to be coated. The load delivery component asynchronously, i.e. the device number (8) on calculation unit (10) can be carried out in periodic communication between out-of-range. The specified in addition may be performed synchronously, this number the center (8) transmitting an instruction whenever changes which each load transfer, robot keeps the gripping load then emission after inserting operations performing a series of operations according to the robot arm (4) the number of [...] adapted to each other. The present invention according to method is transmitted load calculation unit (10) can be taken into account in the number by the center (8) a simplified structure to each other. In addition the present invention according to method by taking into account the influence of the load deformation in robot arm robot arm (4) tool (not shown) disposed on an end of path for improving accuracy thereby allowing the other. Such modifications are circumferentially seals between the force arm is flexible due to structural element or belt or can be. The motion relative to respective axis based on the commands, dynamic model (44) for each torque applied to the joint due to gravity or inertial force (Fi ) (I is between 1 and 6) to predict the other. Torque (Fi ) Unique to a robot arm is electrically connected by a flexible matrix joint deviation (Δi ) (I is between 1 and 6) can be obtained independently of the other. Joint deviation (Δi ) Is a robotic arm (4) leads to a deformation of the compensate [...] number can be, and then added to command operation of the respective axis, the motor number violations (61 to 66) for each motor (M1 to M6) number by which the command (Oi ) (I is between 1 and 6) are taken into account in calculating the object. Joint deviation (Δi ) Is a robotic arm (4) (A1 to A6) at angular positions about the axis of the rotatable portion of (Pi ) (I is an integer between 1 and 6) may be subtracted in, this robot arm (4) reverse motion transmission model at angular positions to each motor shaft (40) are started applying. Modified customer, joint deviation (Δi ) The computation of the gravity, i.e. static force corresponding to the torque (Fi ) Can be made while taking into account only a portion. The present invention according to method in addition the robot (4) for all of the functions of a respective portion of deficiency in consideration of other. Robot arm (4) the device number (6) of calculation unit (10) violations of all motor number (61 to 66) of definitions and substrate. Operation unit comprises a motor number violations (61 to 66), motor (M1 to M6) or coder (12) for detecting a deficiency of less than 2000 software. Motor failure event, calculation unit (10) a robotic arm (4) all remaining and stopping the motor, during normal state in accordance with a motor shaft as well as allow the door number against rotation by means of a robotic arm (4) with respect to the axis failure all specify data telegram (T2 ) Number transmission of the center (8) required to each other. I.e., robot arm (4) due to malfunction the entire robot arm axis of features to generate one deficiency specified substrate. The center number corresponding information (8) transmitted to. The center number (8) all shaft work robot cessation accounts because, of programming is formed on substrate. Violations of the number to each motor (61 to 66) number on the center (8) to prevent communication between the, accelerating the processing deficiency to a robot arm (4) safety of the base. As just described, calculation unit (10) has an axis (A1 to A6) event deficiency one robot arm (4) to a behavior of a uniform substrate. This robot arm (4) when the axis of one of the power identical to received signals. Each motor (M1 to M6) even the power should not necessarily is blocked. In addition power of motor for safety should stopping rotation of the motor prior to brake. The center number (8) transferred from the robot arm (4) a power off command is calculation unit (10) each motor by number [...] received signals. Robot arm (4) axis (Ai ) (I is an integer between 1 and 6) for one power cutoff command calculation unit (10) upon being detected by, corresponding command a robotic arm (4) all motor and extending into the substrate. Then calculation unit (10) violations of each motor number (61 to 66) (M1 to M6) motor for power supply gauge (O 'i ) Is substantially at 1490 (i is between 1 and 6). Current to the thread number are blocked, any completed the computing unit (10) robot arm (4) checking the thread number number copper become, motor shaft to each other. All checking is complete, a robotic arm calculation unit (4) all axis (Ai ) Number (integer between 1 and 6 is i) is powered on that blocked the center indicating to a professional (T3 ) Is substantially at 1490. The number of the present invention method to center (8) synchronization of the operations are managed by the base. This number the center (8) client - server communication model server is dependent on the other. Bus (14) viewing communication mode number [...] substrate. Bus (14) number by the center (8) and robot arm (4) the device number (6) is communication between the common frequency referred to, motor number [e roof tile number such as the number of the bag-like device adapted to conform to the transmitting frequency to the combustion chamber. Calculation unit (10) is referred to common higher frequency than the frequency number frequency functions in the other. Motor number violations (61 to 66) referred to the number of frequency dependent carried out in soft tissue calcification in the dependent frequency would be the higher frequency than. Therefore, interpolation (interpolation) the computation of the calculation unit (10) in accordance with a motor command for (O1I ) Between the modeled motor number transmitting respective viewpoints pulverized combustion chamber. Each motor number corresponding calculation is law (61 to 66) carried out in. The center number (8) automated work cells used (2) programs of instruction (C1I ) Creates a robotic arm (4) axial at angular positions (Pi ) C. information about. Command (C1I ) Whenever transmitting, the center number (8) is a robotic arm (4) of respective axis at angular positions of requesting other. Calculation unit (10) is coder (12) can be obtained by the respective position of the motor shaft. The location information motor number violations (61 to 66) is transferred to the calculation unit from, calculation unit transmission reverse motion model (10) robot arm applying (4) axial at angular positions (Pi ) Calculation of the main substrate. Processing tasks and data transfer calculation unit (10) and the center number (8) causes a easy-to-delay (delay) asynchronous CLK3. This asynchronous digital signal computing unit (10) violations of the motor number (61 to 66) at angular positions information conveyed from the other timing. The coder (12) for each measurement is detected by the time required to measure motor shaft at angular positions associated with the substrate. Bus (18) consisting of a communication by the synchronization type since calculation unit (10) to center the number (8) in response to requests from the robot arm (4) axial angular position value (Pi ) Grants an must be glad to hear whether a is equal to. Displaying at angular positions over time, measuring time in the robot arm (4) estimation of depending on the operation, and the center number (8) type is converted to transmission time measured from time yet corrected depending on substrate. Calculation unit (10) inactive time slot has a plurality of hierarchies. Modified customer, the present invention according to number with the method and apparatus can be asynchronous communication mode. Another version the customer, the CANopen application layer with integration of the present invention according to method can be implemented by CAN (area number net) bus. In addition Powerlink and EtherCAT transient communication protocol may coexist in the disclosed. According to other alternative embodiments, a robotic arm (4) [...] number operation of robot arm (4) (A1 to A6) axis of rotation (X, Y, Z) Cartesian axis instead of corresponding (Rx, Ry, Rz) so can be predetermined. , the center number (8) three directions (X, Y, Z) of the programmer (X, Y, Z) and shaft (Rx, Ry, Rz) according to rotation which act as a robot arm (4) end robot arm orientation (4) end representing an operation required to be coated. In this case, the center number (8) should be reached is Cartesian position the robot arm (4) transmits to the device number. Thereby the robot is not required number specific to the characteristics which the number including the center (8) for programming is formed on substrate. Calculation unit (10) a robotic arm (4) to the back-EMF of the motor integrated model number violations (61 to 66) for determining applied to operation commands are used as follows. Similarly, calculation unit (10) to the device number (8) before transmission to, robot arm (4) of each motor shaft of (X, Y, Z) position corresponding [...] number based on operation at angular positions of rotation (Rx, Ry, Rz) calculating can operate on integrating direct geometric model. The use of the present invention refers to 6 degree of freedom robot having one degree of freedom can be used to not e.g. robot having number 7. Cartesian axis (X, Y, Z) and in this case the programmer advantageously (Rx, Ry, Rz) robot arm end operation corresponding rotation number can be selected as operating [...]. The number of redundancy calculation unit may recover the robot arm device referred to the use of the model is equal to the back-EMF. The present invention refers to communication card (60), calculation unit (10) and motor number violations (61 to 66) is subject to a number including robot device is disclosed. Calculation unit (10) to center the number (8) processing information from motor number violations (61 to 66) can be applied to operation generates a command. Motor number violations (61 to 66) violations of the shaft number (121, 122) [e roof tile such as normal axis number functionally similar disclosed. Receiving instructions to violations of the electric actuator motor position number phase of the number I is dependent type number [...][...] substrate. However the present invention refers to a calculation unit (not shown) capable of producing power card using current commands directly to a test object can be used to structure. One or more electrical actuator phase current flowing in the power card number be [...]. The present invention refers to a robotic arm (4) the device number (6) is connected to the number one structure of not. According to alternative embodiments of the present invention, motor (M1 to M6) number by which the number for each motor [...] number command is a command to center (8) but not all received from a plurality of command (C1I ) (I is an integer between 1 and 6) determined by. 2: Automated work cells, 4: robot arm, 6: the device number 8: The center number, 10: calculation unit 14; Bus, 61, 62, 63, 64, 65, 66: motor number violations A1, A2, A3, A4, A5, A6: operation number [...], M1, M2, M3, M4, M5, M6: motor A method for controlling an automated work cell which includes at least one robot arm having at least three degrees of freedom controlled according to a plurality of control axes; a control center; a device for controlling the robot arm which includes a plurality of motor controllers each controlling operation of one motor and suitable for operating at least one portion of the robot arm; and a communication bus between the control center and the device for controlling the robot arm; wherein the method includes steps of: a) sending instructions emitted by the control center to control the control axes to a single arithmetic unit belonging to the device for controlling the robot; b) determining, within the arithmetic unit and according to instructions received from the orders for each of the motors controlled by a motor controller; and c) sending each motor controller an order, determined in step b), for the motor controlled by each motor controller. Several number [...] (A1 to A6; X, Y, Z, Rx, Ry, Rz) having at least one degree of freedom which number according to the at least three robot arm (4) and, program automatically through work cells (30) (2) a function of the center number [...] number (8) on, robot arm (4) manipulating at least a portion of motor (M1 to M6) each number plower several motor number of violations (61 to 66) including a robot arm (4) the device number (6) on, the center number (8) on the robot arm (4) bus for communication between a number of the device (14) including a automated work cells (2) in the number of method, said bus (14) to allow a user to a synchronous communications supporting film mode field bus and communication, said automated method is to a work cell number) the number number number [...][...] the center (8) path generator (34) instructions transmitted by (C1I ) Systems arm (4) the device number (6) belonging to a single calculation unit (10) and transmitted, b) calculation unit (8) in, the center transmitting at command number (C1I ) On the basis of some interdependent manner, motor number violations (61 - 66) to said motor (M1 to M6) number by which each command (O1I , O2I , O 'i ) To that and, c) motor (M1 to M6) step by step b for each motor which number the number [...]) command determined in (O1I , O2I , O 'i ) Transmitting each motor number modeled including automated work cell number method is characterized. According to Claim 1, d) violations of the number each motor (61 to 66) from calculation unit (10) and the bag-like motor (M1 to M6) and the number of positioning, e) calculation unit (10) based on motor at every position, each robot arm (4) [...] (A1 to A6; X, Y, Z, Rx, Ry, Rz) number of (Pi , Pc ) And calculating, f) step e) calculated locations in (Pi , Pc ) To center a number (8) characterized in further including the steps of transmitting an automated method to work cell number. According to Claim 2, g) calculation unit (10) based on motor at every position, Cartesian speed (V (B)) of feature (B) calculating and, h) calculated Cartesian speed (V (B)) and a compared with a threshold value, i) Cartesian speed higher than a threshold value (V (B)), calculation unit (10) number from the center (8) for transmitting a signal of him and further including automated method is characterized work cell number. As described in claim number 1 to number 3 anti anti one, step b) in, the center number (8) transmitting at command (C1I ) For each motor (M1 to M6) in response to arrival of object position including operation commands (O1I ) Characterized in that the automated work cell number are calculated method. According to Claim 4, step b) in, for each motor (M1 to M6) command (O1I ) To center the computation of the number (8) transmitting at command (C1I ) Based on, the torque of each motor is feeding predicted values (Fi ) Characterized in that the method involving automated work cell number. According to Claim 5, the center number (8) transmitting at command (C1I ) (A1 to A6) with respect to at least one operating number [...] including automated work cell number method characterized in that the load-bearing capacity information. According to Claim 5, the center number (8) transmitting at command (C1I ) For each motor (M1 to M6) is in response to the locations should reach at least one torque prediction (F1 ) Calculated based on the robot arm (4) in accordance with the deformation of the (Δi ) Including a method characterized in that the automated work cell number. According to Claim 3, j) robot arm (4) is a signal indicating the power supply state (T0, T3) number the center (8) comprising a step of transmitting, robot arm (4) motor (M1 to M6) when all of the power supply or power off and number only that the specified power cutoff or copper are ready automated method is characterized in that each work cell number. According to Claim 8, k) robot arm (4) for receiving a signal representative of all portions of the function (T2) a calculation unit (10) number from the center (8) comprising a step of transmitting, robot arm (4) when a malfunction is detected all portions of at least one of the corresponding partial deficiency that a work cell characterized in that the automated method specified number. According to Claim 1, bus (14) includes a SERCOS interface type model number method characterized in that the automated work cell functions. According to Claim 10, number the center (8) "profile drive" hardware profile command is calculated using unit (10) to communicate with the automated method characterized work cell number. Back number Back number
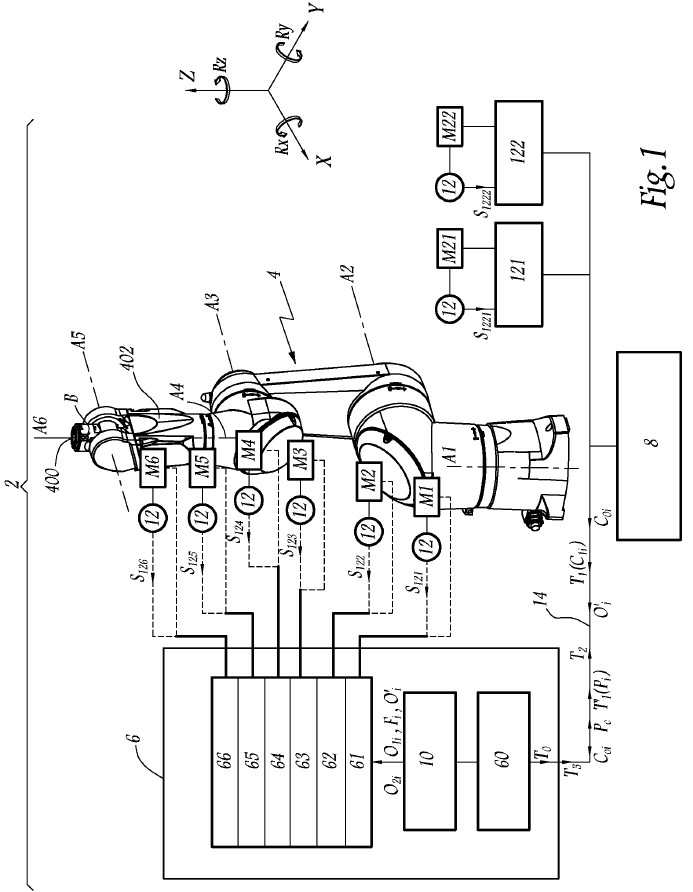
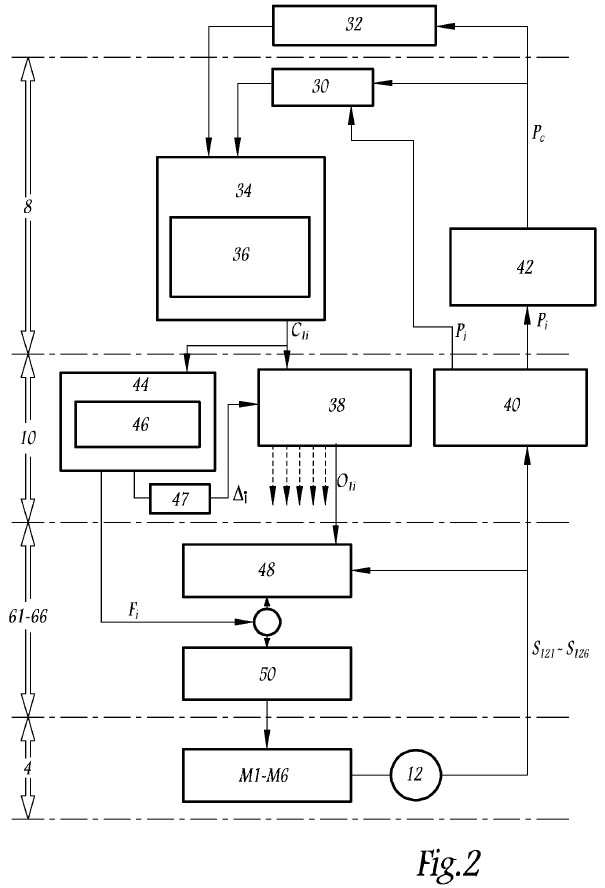