압출기용 스크루, 압출기 및 압출 방법
The present invention refers to a blend stock while kneading extruder screw and adding a shearing action and expansion action the raw material are disclosed. In addition, the present invention refers to said extruder screw extruder and extrusion method generating a soul [lyen it will ask using are disclosed. For example, when the rpm of the screw is set to 300 rpm when least one radiator knead raw material resin extrusion of one degree, one or both sides of compatibilized polymer blend and affinity or adhesion number necessary to add flow tides. However, even if using a chassis number, polymer blend that are not dissolved at a molecular level, soul [lyen scandal performance or function generated by the extruder falls down limit in flow tides. In order to eliminated this door number, conventional, such as a chassis number without adding positively additive materials, nano level to high shear molding device capable of producing the raw materials to soul [lyen it will ask soul [lyen it became developed in the nanometer range. The disclosure to high shear molding device is patent document 1, feedback type screw received in a cylinder with the suction holes. The screw, screw in the interior of the raw material resin are incompatible with the least one sufficiently kneading in construction disclosed. Specifically, the screw, along the transfer direction of the raw material having a straight axis, rotating inside its axis cylinder configured in the nanometer range. The inner screw, helically twisted flight is in the nanometer range. Flight, proximal end of the screw to the head screw and delivering a supply raw materials. Flight carried by raw materials, have a seal member interposed between the end surface of the cylinder gap between waste surely filled substrate. In addition, the screw, and an inside diameter of 1 mm with a hole approximately 5 mm from center etc. is about. The holes, screw and extended in the axial direction in the nanometer range. The upstream end of a hole, screw in said tip gap is opened to the disclosed. The downstream end of the hole, which is branched into an outer circumferential surface of the proximal end and the other end is opened to screw in 2000. Raw materials confined in the gap, with the rotation of the screw into the hole from the upstream end of an aperture, the downstream end of the hole from the outer peripheral surface proximal screw is returned thereto. Feedback raw materials, flight back toward gap by movement of the other. The screw by feedback type in, screw supplied raw materials, flight carried by a shearing action in the process with the art, passes into a hole extending action process subjected. As a result, raw materials, shear flow and extending inside the cylinder in flow result in the enclosed space are circulated in a substrate. According to the raw material of cycling time required for decentralized component material is nano, soul [lyen it will ask having microscopic dispersion can be achieved. The disclosure to patent document 1 in high shear molding device, into which a screw holes are positioned on an axial dimension of the gap be filled material. The back-up, rotation of the screw defines a bore inner wall surface mounted following up since, when it passes through a hole in the circumferential direction of the raw hole . As a result, passing through a hole from the raw materials, as well as elongated hole in the circumferential direction of action involving accepting your in agitation to a shearing action, resulting in a kneading state commonly suitable for a user interface difficult. The, kneading optimizes conditions is provided to room for improving remains disclosed. The purpose of the invention is, inside the screw body passing through the passage in the feedstock is likely to be a shearing action that, precisely the extruder screw kneading degree number capability disclosed. It is another object of the present invention, a kneading degree number with high precision and, decentralized nano material component having distribution structure capable of producing a large number obtain soul [lyen it will ask the extruder and extrusion method can be recycled. In order to achieve said purposes, the point of the screw of the present invention one extruder, etc. screw body. Said screw body, rotating at a linear axis along the transfer direction of the raw material. The outer circumference of said screw flight tire parts in the nanometer range. Said flights, raw material upon rotation of said screw body in an axial direction of said screw body and transfers in the nanometer range. Said screw body along the circumferential direction of the outer peripheral surface barrier portion is provided in the nanometer range. Said material being carried by the flow of the raw material valve timing of said barrier flight number 70 is composed of a pressure increasing. Said screw in the main, raw material is introduced by means of a barrier portion said enhanced with, the peripheral surface of the screw body toward said inlet of said raw material is passing through the passage is mounted in the nanometer range. Said screw body, said passage having a wall surface defining a shape of the hole constituting, said wall surface on the axis of said screw body around said axis to achieve an eccentric position in the nanometer range. Back number The preferred form of the present invention, the interior of said screw body, said screw body flowing refrigerant for cooling refrigerant passages is formed in the nanometer range. The preferred form of the present invention, said passages, said outer peripheral surface of said screw body has an inlet and an outlet opened. Said inlet and said outlet, spaced apart from each other in the axial direction of said screw body and can, said outer peripheral surface of said screw body from an inlet to said passage is returned from the outlet of the raw material with a predetermined length from said to in the nanometer range. The preferred form of the present invention, said barrier portion immediately before said passage said inlet located disclosed. The preferred form of the present invention, said passages, said inlet and said outlet in communication with the passage body has, at the same pitch is smaller than the diameter of the diameter of said body said passage inlet. In order to achieve said purposes, the point of the screw of the present invention one extruder, etc. screw body. Said screw body, along the transfer direction of the transfer material having linear axis, rotates at its axis. Said screw body along the circumferential direction of the outer peripheral surface flight tire parts in the nanometer range. Said flights, raw material upon rotation of said screw body in an axial direction of said screw body and transfers in the nanometer range. Said screw in the main, being carried by said flight with raw material is introduced, the introduced raw material is returned to the outer peripheral surface of said screw body passing through a plurality of passages are provided in the nanometer range. Said plurality of passages, at an angular position offset from the axis of said screw body in said axial direction of said screw body arranged at intervals in the nanometer range. Back number The preferred form of the present invention, the interior of said screw body, said screw body flowing refrigerant for cooling refrigerant passages is formed in the nanometer range. In order to achieve said other purposes, one point of an extruder of the present invention, generating said second holding grooves soul [lyen it will ask the material extruder as plasticizer, barrel and said screw is rotatably housed, said means is disposed in the barrel, said screw for supplying a raw material inlet, said barrel being provided in the, said extruded soul [lyen water discharge port with the suction holes. In order to achieve said other purposes, the point of extrusion method is one of the present invention, barrel screw rotating inside a raw material supplied. Said raw material in an axial direction of an outer circumferential surface of said screw formed using continuous vertical flight with said screw, said screw being carried by said outer peripheral surface barrier by flight number by said pressure-sb2te3. relayed flow of raw material. Said screw upon rotation, said screw and said screw may follow in the lost motion path for said barrier portion by means of said screw with enhanced introducing raw material from the outer peripheral surface, said outer peripheral surface through said screw and said characterized in that said raw material etc. is returned. Back number According to the present invention, screw body of the internal passageway, without screw body about a cylinder axis about 2000. To this end, the outer peripheral surface of the material is set screw body is returned through a passageway is formed in another action, material is received by the elongated action is mainly through the passages with each other. I.e., the stretching action adding raw material containing at least an additional screw on a shearing action and raw material containing at least an active is determined such that, a kneading degree be number with high precision. The, component material nanotubes having distribution structure in order to create a decentralized large number in accordance with the soul [lyen it will ask. Figure 1 shows a also, number 1 embodiment form according to continuous high shear processing device to determine dB as shown are disclosed. Figure 2 shows a also, form number 1 embodiment number 1 for use in a cross-section of the extrusion are disclosed. Figure 3 shows a also, number 1 embodiment in one form, two screw extruder 2 number 1 each other occlusion state sensors mounted thereon as shown are disclosed. Figure 4 shows a also, form number 1 embodiment number 3 for use in a cross-section of the extrusion are disclosed. Figure 5 shows a also, for use in a cross-section of the extrusion number 2 number 1 embodiment form are disclosed. Figure 6 shows a also, number 1 embodiment in one form, as shown in the section of the cross-section of the extrusion barrel and screw both number 2 are disclosed. Figure 7 shows a also, use in side mounted form number 1 embodiment are disclosed. Figure 8 shows a also, along cross-section line of Figure 6 F8 - F8 are disclosed. Figure 9 shows a also, along cross-section line of Figure 6 F9 - F9 are disclosed. Figure 10 shows a also, number 1 embodiment in one form, between two adjacent tubular body 3 rotates on its axis in over state by increasing a cross-section of the extrusion channel is formed as shown in number 2 are disclosed. Figure 11 shows a also, number 1 embodiment in one form, the direction of flow of raw screw side shown are disclosed. Figure 12 shows a also, number 1 embodiment in one form, when the screw is rotated as shown in determine the direction of flow of a material cross-section of the extrusion number 2 are disclosed. Figure 13 shows a also, enhancing the efficiency of the cross-section of embodiments determine the number 1 embodiment as shown extrusion number 2 are disclosed. Figure 14 shows a also, in the form of number 1 embodiment version, reassembling as shown cross-section of the extrusion as a result of body to determine the state number 2 are disclosed. Figure 15 shows a also, for use in a cross-section of the extrusion number 2 number 2 embodiment form are disclosed. Figure 16 shows a also, number 3 embodiment form for use in a cross-section of the extrusion number 2 are disclosed. Figure 17 shows a also, number 3 embodiment in one form, as shown in the section of the cross-section of the extrusion barrel and screw both number 2 are disclosed. Figure 18 shows a also, according to cross-section line of Figure 17 F18 - F18 are disclosed. Figure 19 shows a also, number 3 embodiment form for use in sensors mounted thereon and the retaining ring are disclosed. Figure 20 shows a also, number 3 embodiment in one form, as shown in cross-section structure of the passageway by increasing a screw body are disclosed. Figure 21 shows a also, number 3 embodiment in one form, when the screw is rotated as shown screw side of the direction of flow of raw material are disclosed. Figure 22 shows a also, number 3 embodiment in one form, when the screw is rotated as shown in determine the direction of flow of a material cross-section of the extrusion number 2 are disclosed. Figure 23 shows a also, number 3 embodiment in one form, the deformation of the barrier could be dB as shown are disclosed. Figure 24 shows a also, use in side mounted form number 4 embodiment are disclosed. Figure 25 shows a also, for use in a cross-section of the extrusion number 2 number 4 embodiment form are disclosed. Figure 26 shows a also, number 4 embodiment in one form, as shown in the section of the cross-section of the extrusion barrel and screw both number 2 are disclosed. Figure 27 shows a also, according to cross-section line of Figure 26 F27 - F27 are disclosed. Figure 28 shows a also, number 4 embodiment form for use in sensors mounted thereon and the retaining ring are disclosed. Figure 29 shows a also, and the retaining ring in the direction of the arrow of Figure 28 F29 sensors mounted thereon from an organic solvent are disclosed. Figure 30 shows a also, number 4 embodiment in one form, when the screw is rotated as shown screw side of the direction of flow of raw material are disclosed. Figure 31 shows a also, number 4 embodiment in one form, when the screw is rotated as shown in determine the direction of flow of a material cross-section of the extrusion number 2 are disclosed. Figure 32 shows a also, number 4 embodiment in one form, a coarse screw body shown cross section of 1 variants are disclosed. Figure 33 shows a also, number 4 embodiment in one form, as shown in cross-section to determine the 2 variants of screw body are disclosed. Figure 34 shows a also, in one form number 4 embodiment, variants of a coarse screw body 3 shown cross section are disclosed. (A) is magnified portion of Figure 35 of Figure 34 F35A cross-sectional drawing as shown, is of Figure 35 (B) (A) of line according to cross-sectional drawing of Figure 35 F35B - F35B are disclosed. (A) is magnified portion of Figure 34 F36A cross-sectional drawing of Figure 36 as shown, is of Figure 36 (A) (B) of F36B - F36B line according to cross-sectional drawing of Figure 36 are disclosed. Figure 37 shows a also, number 4 embodiment in one form, as shown in cross-section of the screw body to determine the 4 variants are disclosed. Figure 38 shows a also, number 4 embodiment in one form, as shown in cross-section to determine the 5 variants of screw body are disclosed. Figure 39 shows a also, number 4 embodiment in one form, a coarse screw body shown cross section of 6 variants are disclosed. Figure 40 shows a also, number 5 embodiment form according to number 2 cross-section of the extrusion are disclosed. Figure 41 shows a also, in cross-section of the extrusion according to number 2 number 6 embodiment are disclosed. Figure 42 shows a also, number 7 embodiment form according to number 2 cross-section of the extrusion are disclosed. Figure 43 shows a also, number 8 embodiment form according to number 2 cross-section of the extrusion are disclosed. [Number 1 embodiment form] Hereinafter, for the type of the number 1 embodiment, also a 1 to 12 also through a browser substrate. Figure 1 shows a also, number 1 embodiment form continuous high shear processing device according to (1) determine the configuration of and in 2000. High shear processing device (1) includes a number 1 extruder (2), number 2 extruder (3) and number 3 extruder (4) with disclosed. Number 1 extruder (2), number 2 extruder (3) and number 3 extruder (4) are each connected in series in the nanometer range. Number 1 extruder (2) is further provided for preparing the resin of example 2 are incompatible with the pre kneading are disclosed. Which blends as resin, polymethylmethacrylate (PMMA) such as methacrylate resin and polycarbonate resin such as poly (PC) uses the above-mentioned disclosed. 2 Blend of resin which, e.g. pellet state number 1 extruder (2) supplied to. The embodiment in one form, resin kneading, for strengthening the degree of melting, number 1 extruder (2) in a same rotating 2 axis etc. as used. Also 2 and Figure 3, example 2 axis etc. a disclosure. 2 Axis , barrel (6) and, barrel (6) of 2 therein contained is of screw (7a, 7b) with disclosed. Barrel (6) is a combination of a cylinder part 2 of cylindrical shape (8) contains a. Said resin, barrel (6) mounted on the upper part one end of the feed opening (9) in the cylinder part from (8) supplied continuously. In addition, barrel (6) comprises a cylindrical portion (8) a heater for heating the resin supplied with the suction holes. Screw (7a, 7b) is, engagement of each other in the cylinder part (8) which is housed in a disclosed. Screw (7a, 7b) is, not shown motor receives charge from rotating in the direction of applied torque of the same are disclosed. As also shown in the 3, screw (7a, 7b) is, each feed portion (11), (12) and the inflow pipe (13) with disclosed. Feed portion (11), (12) and the inflow pipe (13) includes a screw (7a, 7b) are arranged in a line along an axial direction of the dashpot. Feed portion (11) is helically twisted flight (14) 26c1. Screw (7a, 7b) of flight (14) are each engaged with rotatable, feed opening (9) of resin 2 supplied from the (12) delivering toward. (12) includes a screw (7a, 7b) arranged in the axial direction of a plurality of disk (15) has disclosed. Screw (7a, 7b) disk (15) opposite each other with shaft, feed portion (11) is sent from a pre-resin is kneaded. Soul [lyen it became resin, screw (7a, 7b) by the rotation of the inflow pipe (13) is sent to a. The inflow pipe (13) is helically twisted flight (16) 26c1. Screw (7a, 7b) of flight (16) rotatable engaged with each other, the soul [lyen it became resin pre barrel (6) etched from an upper surface of the extrusion. The kneading shaft such 2, screw (7a, 7b) of feed portion (11) the resin supplied, screw (7a, 7b) and a heater exothermic and shear the rotation of the barrel (6) receives the heat from the molten substrate. 2 Preliminary soul [lyen in shaft rotation speeds by the molten resin, a blend module and a raw material. Raw materials, as represented by arrow A also 1, barrel (6) number 2 discharge from an extruder (3) continuously supplied. The raw number 2 extruder (3) of the first supplied to, the feedstock is number 1 extruder (2) preliminary soul [lyen in etc. in molten by having a flowability. The, material kneading extruder number 2 the fixing element (3) can be possible to reduce the load. Number 2 extruder (3) of the cylinder component includes nanotubes having distribution structure for generating element soul [lyen it will ask a decentralized large number are disclosed. The embodiment in one form, number 2 extruder (3) shortening etc. as the use of an extruder. Reducing an extruder, barrel (20) and, 1 of screw (21) with disclosed. Screw (21) is a shearing action and expansion action repeatedly adding a molten raw material has disclosed. Screw (21) including number 2 a extruder (3) in order to operate, later detailed as follows. Number 3 extruder (4) is number 2 extruder (3) stand-alone gas components contained in the molten resin extruded from a number components are disclosed. The embodiment in one form, number 3 extruder (4) etc. shortened as the use of an extruder. As also shown in the 4, reducing an extruder, barrel (22) and, barrel (22) received 1 of vent screw (23) with disclosed. Barrel (22) soon including the cylinder portion (24) contains a. Number 2 extruder (3) molten resin extruded from a soul [lyen it asked, the cylinder portion (24) along the axial direction of the cylinder part from the one end part (24) continuously supplied. Barrel (22) the vent opening (25) having disclosed. Vent opening (25) a cylinder portion (24) along the axial direction of intermediate portion is opened to the dispersibility, vacuum pump (26) connected to the nanometer range. In addition, barrel (22) of the cylinder portion (24) other end of, the head portion (27) to aid being disclosed. Head portion (27) has a discharge port ejecting soul [lyen it will ask (28) having disclosed. Vent screw (23) a cylinder portion (24) is housed in a disclosed. Vent screw (23) is not shown motor receives charge from rotating in the direction of applied torque 1 are disclosed. Vent screw (23) is helically twisted flight (29) 26c1. Flight (29) includes a vent screw (23) turning integrally with, the cylinder portion (24) soul [lyen it will ask supplied to the head portion (27) continuously toward delivering. Soul [lyen it asked, vent opening (25) when fed into the position corresponding to the, vacuum pump (26) a steering subjected. The, material or other volatile component in the gaseous phase included number encoded soul [lyen water continuously from the wetting ability. Soul [lyen it asked for reparing over gaseous material or other volatile component number, head portion (27) for fixing (28) from high shear processing device (1) continuously outside of the blower fan. Then, number 2 extruder (3) detailed are described as follows. As also shown in 5 and 6 also, number 2 extruder (3) barrel (20) is straight and as a result of elder brother, horizontally disposed in the nanometer range. Barrel (20) includes a plurality of barrel element (31) is divided into disclosed. Each barrel element (31) is the through hole (32) has disclosed. Barrel element (31) is each through-hole (32) integrally connecting to the bi-continuously. Barrel element (31) of through holes (32) is cooperate with each other to the barrel (20) of a cylindrical cylinder portion (33) and for defining. The cylinder portion (33) also includes a barrel (20) extends axially in the nanometer range. The feed opening (34) is barrel (20) at one end along the axial direction of formed in the nanometer range. The feed opening (34) a cylinder portion (33) in communication with, the supply opening (34) number 1 to extruder (2) blend into a raw material supplied continuously. Barrel (20) and for the heater is not shown. Heater, barrel (20) to the optimum values soul [lyen material when the temperature of the barrel (20) regulating the temperature of the substrate. In addition, barrel (20) such as for example water or oil are inclined at a refrigerant path (35) with disclosed. Refrigerant path (35) a cylinder portion (33) so as to surround in the nanometer range. Refrigerant, barrel (20) exceed the upper limit value when a predetermined temperature of refrigerant passages (35) flowed along, barrel (20) a steel number are separated from each other. Barrel (20) along the axial direction of the other end, the head portion (36) to aid being disclosed. Head portion (36) has a discharge port (36a) 26c1. Discharge port (36a) has a supply opening (34) with respect to the barrel (20) positioned along the axial direction of the opposite side of the with, number 3 extruder (4) connected to the nanometer range. As also shown in the 5 to 7 also, screw (21) includes a screw body (37) having etc.. The embodiment in the form of a screw body (37) 1 has two axes of rotation (38) and, a plurality of cylindrical tubular body (39) consisting in the nanometer range. Axis of rotation (38) number 1 the shaft (40) and number 2 shaft (41) with disclosed. Number 1 shaft (40) also includes a barrel (20) it is a vice-side one end of shaft (38) located proximal end of 2000. Number 1 shaft (40) a joint portion (42) and stopper portion (43) contains a. Joint section (42) includes a driving source such as a motor is connected through coupling not shown. Stopper part (43) a joint portion (42) coaxial to seat in the nanometer range. Stopper part (43) a joint portion (42) than when a supplied current. Number 2 shaft (41) number 1 includes a shaft (40) of stopper part (43) extending from the end of coaxial type in the nanometer range. Number 2 shaft (41) also includes a barrel (20) of length over approximately the whole length with, head portion (36) on a side thereof facing the tip of the cutter 14. Number 2 shaft (41) at one side of the unit (43) smaller in diameter than solid cylindrical are disclosed. As also shown in the 9 and also 8, number 2 shaft (41) of the circumference of one another end (45a, 45b) is fitted to the disclosed. Key (45a, 45b) is, number 2 shaft (41) of number 2 position shifted circumferentially 180° shaft (41) extends axially in the nanometer range. In addition, screw body (37) having a straight axis (O1) etc.. The axis (O1), number 1 shaft (40) and number 2 shaft (41) through a coaxial with, the axis of rotation (38) of axially extending horizontally in the nanometer range. As also shown in the 6 to 10 also, tubular member (39) includes a screw body (37) defining an outside diameter of the element and, number 2 shaft (41) on bi-inserted into the nanometer range. The form of the embodiment, all of the tubular body (39) the diameter of D1, each other at the same pitch is. The tubular body (39) along the axial direction forms an artificial end (39a) has disclosed. End (39a) flat surface along a direction orthogonal to the axis (O1) are disclosed. A pair of keyway (47a, 47b) of the tubular body into the (39) outer in the nanometer range. Keyway (47a, 47b) is, tubular body (39) of the tubular body at positions displaced in the circumferential direction of 180° (39) radially extending although, tubular body (39) on either side of the end surface (39a) is opened to the disclosed. The tubular body (39) home keys (47a, 47b) number 2 a shaft (41) key (45a, 45b) in number 2 state matched with a shaft (41) from the direction of the distal end of shaft number 2 (41) are associated with them on. The embodiment in one form, number 2 shaft (41) on which are inserted into the first tubular body (39) number 1 on shaft (40) of stopper part (43) between the end of number 1 color (48) interposed disclosed. In addition, all of the tubular body (39) number 2 a shaft (41) is placed in, number 2 shaft (41) introducing tube screw (49) number 2 through color (50) is secured to the disclosed. Screw (49) which is one example of agricultural products, color number 2 (50) is one example end petal are disclosed. Color number 2 (50) number 2 a shaft (41) by securing introducing tube, all of the tubular body (39) is number 1 color (48) on color number 2 (50) number 2 between shaft (41) is combined in the axial direction of, adjacent tubular member (39) the end of which (39a) surfaces without contact in the nanometer range. As a result, all of the tubular body (39) is number 2 shaft (41) on safety rope, of an segmented screw body (37) is consists of. Therewith, the axis of rotation (38) of the tubular body and (39) are then assembled and the structure body, the tubular body (39) by the rotation (38) may follow (O1) is rotated about axis of butanes. The embodiment in one form, the tubular body (39) keys (45a, 45b) shaft (38) secured in and not the limited to. For example, key (45a, 45b) 2 instead of using spline such as also shown in the tubular body (39) the shaft (38) fixed to a retarder. Screw (21) also includes a barrel (20) of the cylinder portion (33) which is housed in a disclosed. Screw (21) screw body (37) a cylinder portion (33) so that the coaxial positioning, the screw body (37) the outer circumferential surface of the cylinder portion (33) on the inner peripheral surface between a transfer passage (51) is formed in the nanometer range. As also shown in the 9 8 and also, a transfer passage (51) a cylinder portion (33) having a cross sectional shape along a direction diameter of toroidal and, the cylinder portion (33) extends axially in the nanometer range. In addition, axis of rotation (38) of joint section (42) and stopper portion (43) also includes a barrel (20) from one end of barrel (20) project out of the in the nanometer range. The embodiment in one form, screw (21) the shaft (38) when viewed from the direction of the proximal end, screw (21) receives torque from a drive won in the counterclockwise direction as shown by arrows 5 also turns on a substrate. Screw (21) the rpm, preferably having a thickness of 1 600rpm ∼ 3000rpm. Also 5 to 7 and also as shown in the 10 also, screw body (37) is a plurality of material is transferred by section (54) on, number valve timing of the flow of raw material a plurality of barrier portion (55) having disclosed. Section (54) and barrier portion (55) includes a screw body (37) in an axial direction of alternating located side by side in the nanometer range. Screw body (37) of the axial, screw body (37) longitudinal it can be in other words. Each section (54) is helically twisted flight (56) 26c1. Flight (56) comprises a tubular body (39) from the outer peripheral surface along the circumferential direction of the transfer passage (51) projects toward the, its flight (56) is top of section (54) etc. a perimeter on configuration. Flight (56) includes a screw (21) when is turns on, screw body (37) toward front end distal from the material carry distorted disclosed. In other words, flight (56) includes a flight (56) torsion direction left-hand thread equal to left distorted disclosed. Screw body (37) along the axial direction of the section (54) the length of the, e.g. raw materials, kneading degree, like soul [lyen scandal of production per unit time to vary along the cross lines are deleted. In addition, section (54) is reacted, at least of the tubular body (39) of the circumference of the flight (56) unit includes means but, flight (56) in a region between the specific point and end point are not correct. I.e., tubular body (39) of the outer peripheral surface of flight (56) also deviates from the area section (54) is restored by taken as the, flight (56) having a tubular body (39) when the cover is disposed at a position adjacent cylindrical spacer or cylindrical collar, its color also conveying parts (54) be included may be the case. Each barrier portion (55) is helically twisted flight (57) 26c1. Flight (57) has a tubular body (39) from the outer peripheral surface along the circumferential direction of the transfer passage (51) projects toward the, its flight (57) end portion of the barrier portion (55) etc. a perimeter on configuration. Flight (57) includes a screw (21) when is turns on, screw body (37) material is transferred from the proximal end to the head to distorted disclosed. In other words, flight (57) includes a flight (57) torsion direction equal to close the door to the right distorted disclosed. Flight (57) pitch of, flight (56) that are equal to or pitch of, flight (56) of less advantage. In addition, flight (56, 57) and end portion of the barrel (20) of the cylinder portion (33) is formed between an inner peripheral surface, some clearance is reserved in the nanometer range. Screw body (37) along the axial direction of the barrier portion (55) the length of the, e.g. raw materials, kneading degree, like soul [lyen scandal of production per unit time to vary along the cross lines are deleted. Barrier portion (55) includes a section (54) sent by flow material functions to each other. I.e., barrier portion (55) is guided at the downstream side in the carrying direction of the cylinder (54) with adjacent, conveying parts (54) sent by the raw flight (57) and end portion of the cylinder part (33) from passing into the clearance between the inner peripheral surface 70 is composed of an intended target. The embodiment in one form, barrel (20) corresponding to one end of the screw body (37) proximal end of the barrier portion (55) is positioned, barrel (20) corresponding to the other end of screw body (37) tip is, for ejecting a flight (58) is provided in the nanometer range. For ejecting a flight (58) includes a screw body (37) located at the distal end of the tubular body (39) transfer from the outer surface (51) toward the projecting in the nanometer range. For ejecting a flight (58) includes a screw body (37) from the direction of the proximal end of the tip material is transferred to distorted disclosed. Barrel (20) through the feed opening (34) includes a screw body (37) nearest to the proximal end of one section (54) along the axial direction is equipped with an interstitial etc. of opposite. The embodiment form the, flight (56, 57, 58) is, outer diameter of the tubular body into a plurality of equally both D1 (39) transfer from the outer surface (51) projecting toward the nanometer range. To this end, the tubular body (39) a circumferential outer surface of, screw (21) defined etc. of the bolt. Screw (21) gain-of-function of roentgen per hour at one meter, screw (21) over the entire length of obtained in the nanometer range. 5 To 7 may also, as shown in the 10 also, screw body (37) includes a screw body (37) radially extending defines a plurality of passages (60) having disclosed. Passage (60) includes a screw body (37) arranged at intervals in the axial direction of the over. In addition, screw body (37) along the axial direction of the intermediate portion, as also shown in the 9, screw body (37) extending in an axial direction of the inlet of the 4 (60) the screw body (37) of the circumferential direction of 90° arranged at intervals in the in the nanometer range. As also shown in 6 and also 10, each passage (60) is 1 of barrier portion (55) on, its barrier portion (55) at a section of 2 (54) when a unit, these conveying parts (54) and barrier portion (55) corresponding to two tubular body 3 (39) between the formed over in the nanometer range. Specifically described, each passage (60) is number 1 to number 3 passage element (61, 62, 63) defined in the nanometer range. Number 1 passage element (61) passages (60) inlet can be called in other words. Number 1 passage element (61) is said one unit each barrier portion (55) than the screw body (37) located on the proximal side of section (54) corresponding to the tubular body (39) of the circumference of the other end is opened to disclosed. Number 1 passage element (61) of the open end, conveying parts (54) corresponding to the tubular body (39) which is arranged on the outer peripheral surface, conveyance section (54) than the screw body (37) on the proximal side of the adjoining subarea at the barrier portion (55) located proximate to a boundary between a over. In addition, number 1 passage element (61) of the open end, flight (56) out disclosed. The embodiment in one form, number 1 passage element (61) has a tubular body (39) formed by an outer circumferential surface of e.g. drill over embodiment using machining. Thereby, number 1 passage element (61) has a circular cross-sectional shape and having holes, (O1) and orthogonal to the axis of the tubular body (39) of the tubular body from the outer surface (39) of the radial extending in the nanometer range. Number 1 passage element (61) bottom (61a) conically tip of the drill is slanted disclosed. Number 2 passage element (62) is a passage body flow can be in other words as a raw material. Number 2 passage element (62) comprises a section (54) and barrier portion (55) corresponding to two tubular body 3 (39) to SPAN between the screw body (37) axis (O1) and is positioned parallel in the nanometer range. The, number 2 passage element (62) is without branch during screw body (37) although straight in the axial direction of the seat, the total predetermined have a length disclosed. As best shown to also 10, number 2 passage element (62) comprises a tubular body of said 3 (39) during screw body (37) on the proximal side of tubular body (39) formed therein of number 1 portion (65a) and, tubular body of said 3 (39) during intermediate tubular body (39) formed therein of number 2 portion (65b) and, tubular body of said 3 (39) during screw body (37) the tip end side of tubular body (39) formed therein and a portion of number 3 (65c) which are disclosed. Number 1 portion (65a), number 2 portion (65b) and number 3 portion (65c) is removed body (37) along the axial direction of the coaxial the shape in the nanometer range. Number 2 passage element (62) portion of number 1 (65a) of the tubular body into the (39) extending straight in the axial direction of although, its tubular body (39) adjoining intermediate tubular body (39) front side (39a) is opened to the disclosed. Number 1 portion (65a) of line opposite open end, the tubular body (39) of end wall (39b) to be closed. The embodiment form the, number 2 passage element (62) portion of number 1 (65a) of the tubular body into the (39) the end of which (39a) drill for example embodiment using machining formed by in the nanometer range. To this end, part number 1 (65a) having cross-sectional shapes of circular hole defined disclosed. Number 2 passage element (62) of number 2 portion (65b) intermediate tubular body (39) using machining embodiment example drill formed by in the nanometer range. Number 2 portion (65b) intermediate tubular body (39) with a axially penetrating, intermediate tubular body (39) on either side of the end surface (39a) is opened to the disclosed. Thereby, number 2 portion (65b) having cross-sectional shapes of circular hole defined disclosed. Number 2 passage element (62) portion of number 3 (65c) of the tubular body into the (39) extending straight in the axial direction of although, its tubular body (39) adjoining intermediate tubular body (39) front side (39a) is opened to the disclosed. Part number 3 (65c) of line opposite open end, the tubular body (39) of end wall (39b) to be closed. The embodiment form the, number 2 passage element (62) portion of number 3 (65c) of the tubular body into the (39) the end of which (39a) drill for example embodiment using machining formed by in the nanometer range. To this end, part number 3 (65c) having cross-sectional shapes of circular hole defined disclosed. As also shown in 6 and also 10, number 1 portion (65a) of open, part number 2 (65b) portion and a covering body of number 3 (65c) of the open end, two adjacent tubular body 3 (39) the shaft (38) when the axial direction of the fastening, counts the number of butt to be are interconnected with each other to simplify the structure. Number 3 passage element (65c) includes a passage (60) outlet can be called in other words. Number 3 passage element (65c) is said one unit each barrier portion (55) than the screw body (37) located in the tip end side of section (54) corresponding to the housing (39) is opened to the outer peripheral surface of 2000. Number 3 passage element (63) of the open end, conveying parts (54) corresponding to the tubular body (39) which is arranged on the outer peripheral surface, conveyance section (54) than the screw body (37) in the tip end side of adjacent barrier portion (55) located proximate to a boundary between a over. In addition, number 3 passage element (65c) of the open end, flight (56) out disclosed. In addition, the embodiment in one form, number 3 passage element (63) has a tubular body (39) formed by an outer circumferential surface of e.g. drill over embodiment using machining. Thereby, number 3 passage element (63) and a solenoid valve which has a circular cross-sectional shape, the tubular body (39) of the tubular body from the outer surface (39) of the radial extending in the nanometer range. Number 3 passage element (63) bottom (63a) conically tip of the drill is slanted disclosed. Number 1 passage element (61) of number 3 passage element (63) of the open end, of section 2 (54) and 1 of barrier portion (55) is installed between the screw body (37) axially spaced apart disclosed. In other words, number 1 passage element (61) of number 3 passage element (63) between the open edge portion of screw body (37) etc. surface of change. As also shown in the 10, number 2 passage element (62) portion of number 1 (65a) of line opposite open end, the tubular body (39) number 1 in the interior of the passage element (61) is connected to disclosed. Number 1 passage element (61) and number 2 passage element (62) portion of number 1 (65a) all while maintaining a circular cross section shape are communicated with each other. In addition, number 2 passage element (62) portion of number 1 (65a) ends of the, number 1 passage element (61) has a conical bottom (61a) at a position outside the passage element number 1 (61) connected to the nanometer range. Number 2 passage element (62) portion of number 1 (65a) is number 1 passage element (61) bottom (61a) connected to a retarder. To this end, number 1 passage element (61) includes a screw body (37) exposing the number 2 of the circumference of the passage element (62) portion of number 1 (65a) from one end of the tubular body (39) of number 1 can be in other words as a raised portion raised in the radial direction. Number 2 passage element (62) portion of number 3 (65c) of line opposite open end, the tubular body (39) number 3 in the interior of the passage element (63) connected to the nanometer range. Number 3 passage element (63) and number 2 passage element (62) portion of number 3 (65c) all while maintaining a circular cross section shape are communicated with each other. In addition, number 2 passage element (62) portion of number 3 (65c) ends of the, number 3 passage element (63) has a conical bottom (63a) number 3 position outside the passage element (63) connected to the nanometer range. Number 2 passage element (62) portion of number 3 (65c) number 3 the passage element (63) bottom (63a) connected to a retarder. To this end, number 3 passage element (63) includes a screw body (37) exposing the number 2 of the circumference of the passage element (62) portion of number 3 (65c) from one end of the tubular body (39) of number 2 as a raised portion raised in the radial direction can be in other words. Further, screw body (37) in the intermediate part of the, passage (60) and on the basis of number 1 inlet passage element (61) on, adjacent another passage (60) the outlet of the passage element number 3 (63) is adjacent 2 of barrier portion (55) transfer between (51) etc. passed. Therewith, the tubular body (39) of a passage within (60) by providing, through the passage (60) includes a screw body (37) with respect to the axis (O1) offset disclosed. To this end, passage (60) includes a screw body (37) is rotated around the axis (O1) when a cylinder body. Number 2 passage element (62) constituting the inner diameter of the hole, e.g. 1 mm or more, less than 6 mm, preferably 1 mm or more, to 5 mm hereinafter are coupled to the lower end. In addition, number 2 passage element (62) the inner diameter of, the inlet passage element number 1 (61) less than the inner diameter of. Therewith, number 2 passage element (62) along a direction the diameter of a cross section, the cylinder portion (33) along a direction the diameter of the transfer passage (51) set so as to be much smaller than the cross sectional area of over. The embodiment form the, tubular body (39) is number 1 to number 3 passage element (61, 62, 63) defines constituting a wall surface of a cylindrical shape of the hole (66) having disclosed. Wall (66) surrounded by a number 1 to number 3 passage element (61, 62, 63) is, allowing for only a hollow space and material flow, screw body in space (37) consists not present. In addition, wall (66) is removed body (37) when the body is rotated, about axis (O1) without self axis (O1) revolves around a substrate. The embodiment in one form, a plurality of tubular body (39) the shaft (38) a stand-alone number from the screw (21) when decomposing, at least flight (56, 57, 58) formed a portion of the tubular body (39) includes a screw element can be called in other words. In addition, the embodiment form the, screw (21) screw body (37) has an axis of rotation (38) of the tubular body into a plurality of as on screw element (39) by inserting consists of sequentially. To this end, e.g. according to the degree of a kneading section (54) and barrier portion (55) or exchange of recombinant can be connected together, exchange, hereinafter for work upon the recombination can be disclosed. Further, a plurality of tubular body (39) the shaft (38) occupied by a fastening in the axial direction of the tubular body (39) the end of which (39a) closely to each other, passage (60) (passage body) of number 2 passage element (62) is formed, the number 2 passage element (62) number 1 through passage element (inlet) (61) (outlet) on number 3 passage element (63) communicates with a inhibiting between. To this end, screw body (37) passage (60) formed with a in, screw body (37) compared to the entire length of the wire length short individual tubular body (39) embodiment side opposite surface of the substrate. The, passage (60) resulting in workability when forming and handling is facilitated. This allows for the continuous high shear processing device (1) is, number 1 extruder (2) comprises a plurality of resin is kneaded into preliminary. The soul [lyen by the molten resin, having a flowability in a blend material number 2 extruder (3) through the feed opening (34) supplied continuously. Number 2 extruder (3) raw materials supplied, as represented by arrow B also 11, screw (21) nearest to the proximal end of section (54) of the circumference of the input thereto. Screw (21) has an axis of rotation (38) in the counterclockwise direction when viewed from the direction of the proximal end of the turns on, conveying parts (54) of flight (56) also includes a filar of arrows 11 as shown to, feed opening (34) input raw materials from screw body (37) on the proximal side of the adjoining subarea at the barrier portion (55) toward the delivering. I.e., flight (56) has a supply opening (34) input raw materials from screw body (37) toward the entire front end of the reverse transfer. The, transfer (51) turning in flight (56) with a cylinder portion (33) generated by the speed difference between the inner peripheral surface with raw material added to a shearing action, flight (56) of the raw materials by a state torsion electrooculogram agitated. As a result, the fixing element is kneading the raw materials, the processing advances is distributing component material. Raw materials subjected to a shearing action, a transfer passage (51) along section (54) on the barrier portion (55) a boundary between sets of amounts. Barrier portion (55) of flight (57) includes a screw (21) when is turns on, screw body (37) from the proximal end to the head is distorted to right direction material is transferred by, flight (56) raw material sent by flight (57) fluid passages to each other. In other words, barrier portion (55) of flight (57) includes a screw (21) turns on is when, flight (56) with valve timing of the flow of raw material sent by number, raw material barrier portion (55) the outer circumferential surface of the cylinder portion (33) is passed out of the signal in the clearance between the inner peripheral surface and a first substrate. As a result, conveying parts (54) on the barrier portion (55) boundary of raw material of a tapered body. Specifically described, Figure 12, a transfer passage (51) of screw body (37) of conveying parts (54) an addition result corresponding to full rate represented by a multilayer material which, dense color tone are compensated by increasing rate of diffuser material installed disclosed. As also referring to from 12, a transfer passage (51) in, barrier portion (55) by the rate of diffuser material proximate the bubbles and, barrier portion (55) is immediately, raw material of diffuser 100% rate is the nanometer range. To this end, barrier portion (55) of diffuser material immediately before 100% rate in raw material the reservoir R formed therein. Raw material in the reservoir R, clogging of the raw material at the rate of over pressure in the raw material. Pressure in the raw materials, also of arrows 11 and 12 as shown to also intersecting the, passage (60) of number 1 passage element (61) number 2 from passage element (62) into the substrate. Number 2 passage element (62) along a direction the diameter of a cross section, the cylinder portion (33) along a direction the diameter of the transfer passage (51) of less than cross-sectional area. In other words, number 2 passage element (62) the inner diameter of, screw body (37) is much smaller outer sleeve, number 2 permits the passage element (62) when the refrigerant passes raw material is abruptly compressed, the stretching action as its raw material added substrate. Further, number 2 passage element (62) cross-sectional area of a transfer passage (51) due to the small cross sectional area of sufficiently than, raw material the reservoir R through-passage (60) despite bracket, barrier portion (55) raw material the reservoir R immediately uncovering free driving transistor. To this end, e.g. flight (56) by a barrier portion (55) which is sent to the totality of the flow rate of the raw material somewhat reduced, flow rate through-phosphate raw material the reservoir R can be supplemented. The, raw materials, the passage always in a stable state (60) feed. Number 2 passage element (62) through the raw materials, the filar of arrows 12 also as shown, number 3 passage element (63) through the screw body (37) in the tip end side of adjacent section (54) to return to other. Feedback raw materials, conveying parts (54) of flight (56) by screw body (37) is fed toward the front end of the, again subjected to a carrier during the shearing action. Raw materials subjected to a shearing action, passage (60) of number 1 passage element (61) number 2 from passage element (62) with bracket, its number 2 passage element (62) in the process for organically subjected to stretching action again. The embodiment in one form, a plurality of conveying parts (54) and a plurality of barrier portion (55) the screw body (37) disposed alternately in the axial direction of although, a plurality of passages (60) the screw body (37) arranged at intervals in the axial direction of the over. To this end, feed opening (34) from the screw body (37) is introduced to the raw materials, the arrows also 10 and 11 also as shown, a shearing action and extending alternately repeated action under the screw body (37) in the direction of the proximal end of the tip from continuously conveyed substrate. The, enhanced kneading degree, distributing component material is promoted with each other. A plurality of passages (60) of number 2 passage element (62) is individually number 1 passage element (61) and number 3 passage element (63) through the screw body (37) is opened to the outer peripheral surface of 2000. To this end, each passage (60) in, number 1 passage element (61) number 2 from passage element (62) with a predetermined length from raw materials, not necessarily number 3 passage element (63) through the screw body (37) and the outer peripheral surface is returned, a plurality of passages (60) in the raw materials are mixed between the free. The, material soul [lyen degree while avoiding excess can be, in accordance with an appropriate soul [lyen this desired . Screw body (37) at the front end of the material is reached, the passage is sufficiently soul [lyen it became the soul [lyen water (60) outlet (63) from the cylinder portion (33) on head portion (36) a gap between derived substrate. In addition, soul [lyen it asked, head portion (36) for fixing (36a) number 3 from extruder (4) continuously supplied. Number 3 extruder (4) is, as already described, a gas phase material or other volatile component included number encoded soul [lyen water continuously from the wetting ability. Soul [lyen it asked for reparing over gaseous material or other volatile component number, head portion (27) for fixing (28) from high shear processing device (1) out of disconnected during continuous without a blower fan. Discharged soul [lyen it asked, accumulated in water immersed in a coolant. The, soul [lyen water steel number in actively cooled, desired resin molded article obtained. Number 2 extruder (3) in, number 1 extruder (2) raw material supplied from the screw body (37) in a plurality of times while repeated inversion over the axial direction of the fed, a shearing action and expansion action is repeatedly carried over the raw material during the added substrate. In other words, permits the screw body (37) on the outer peripheral surface of the same at a place where the circulating or several times in the rotation, material number 2 extruder (3) number 3 from extruder (4) keep butting supply can. The, soul [lyen it will ask soul [lyen it became sufficiently can be continuously molding, high shear molding device in comparison , soul [lyen scandal by substantially increasing the production efficiency can be. Therewith, the embodiment in one form, number 1 extruder (2) pre-soul [lyen it became disconnected during the resin without number 2 extruder (3) supplied by connection the, number 1 extruder (2) in the interior of the resin flow is temporarily congestion uncovering free. To this end, preparatory to number 1 soul [lyen it became resin extruder (2) generated by a temperature change of the interior of the resin dissolves the produced, can prevent or phase change viscosity changes. The, uniform quality raw materials always number 1 extruder (2) from number 2 extruder (3) can be supplied. The number 1 embodiment form, the stretching action raw material adding passage (60) includes a screw body (37) serving as a rotation center axis (O1) eccentrically with respect to the position of the screw body (37) is connected to the second axially-extending, passage (60) around an axis (O1) is a cylinder body. In other words, passage (60) defining a cylindrical wall (66) about the axis (O1) without rotation axis (O1) revolves around a substrate. To this end, permits the passage (60) when it passes through a passage to receive a centrifugal force but a raw material as its raw material (60) in the interior of the extended work is free for the synthesis. The, passage (60) the raw materials through a shearing action that likely to, passage (60) through section (54) is received by the elongated material is mainly to return to act upon with each other. The, number 1 embodiment in the form of a screw (21) is, at least an additional action stretchable raw material and raw material containing at least an additional shearing can be clearly defined. Thus, second back in glass reduces with a kneading degree, degree be precisely number soul [lyen. As a result, nano component material in order to create a decentralized large having distribution structure in accordance with the soul [lyen it will ask. Further, a plurality of passages (60) so that the eccentric in relation to all of the axis (O1), a plurality of passages (60) can be uniformly stretching action through the raw material added. I.e., a plurality of passages (60) in fluctuation between soul [lyen condition can be, uniform straight line can be performed. The number 1 embodiment form, a plurality of tubular member (39) is set to the same diameter of D1 is connected to each other, a transfer passage (51) includes a screw body (37) along the axial direction of the circular ring-shaped cross-sectional shape over the entire length of uniform to be coated. To this end, a transfer passage (51) raw material through a shearing action and expansion action when repeated and added a shearing action and expansion action smoothly raw material can be added sequentially, uniform straight line red Ginseng can be performed. In addition, the form number 1 embodiment, extruder screw is plasticized zone having a shortening of the existing method which has no, section (54), barrier portion (55) and passage (60) arranged in the combination screw (21) to the plasma, number 2 extruder (3) hereinafter for a can be to manipulate. [Variants in the form of number 1 embodiment] Also 13 and Figure 14, etc. could be modified disclosure number 1 embodiment shape of relevance. 13 Also as shown in this version the, number 2 passage element (62) of number 2 portion (65b) there is provided a tubular body (39) of the circumference of the, barrier portion (55) lamps simultaneously flight (57) on, conveying parts (54) constituting a portion of flight (56) is continuously formed in the nanometer range. I.e., 2 kinds of flight (56, 57) of the tubular body is formed (39) inside, number 2 passage element (62) of number 2 portion (65b) is located disclosed. The when a, number 2 passage element (62) of number 2 portion (65b) provided with a tubular body (39) as, the axial 14 also shown in all barrier portion (55) for flight (57) is formed dedicated tubular body (68) for preparing the, its tubular body (68) of a flight 2 (56, 57) is formed of the tubular body into said (39) in accordance with the on time with the replacement process. The, passage (60) forming two tubular body 3 (39, 68) within the range of the length of section (54) for flight (56) obtains the regions barrier portion (55) for flight (57) obtains the ratio of the area, e.g. a kneading degree can be changed according to. [Number 2 embodiment form] Figure 15, etc. form disclosure number 2 embodiment. Number 2 embodiment form, screw (21) the axis of rotation (38) option number 1 embodiment differ from the form hereinafter disclosed. Other number 2 extruder (3) the configuration of the, number 1 embodiment form essentially are the same. Thereby, number 2 embodiment in one form, the same number 1 embodiment form the same heating references a constituent part of the disconnecting, description and omitting other. As also shown in the 12, refrigerant path (71) by the rotation (38) formed in the nanometer range. Refrigerant path (71) has an axis of rotation (38) axis (O1) along bi-extending in the nanometer range. Refrigerant path (71) one end of, joint section (42) of at a place where the rotary joint (72) through exit piping (73) connected to the nanometer range. Refrigerant path (71) other end of, axis of rotation (38) provided at the base end of be liquid-tight. Refrigerant introduction tube (74) a coolant passage (71) inserted into the bi-inside of butanes. Refrigerant introduction tube (74) one end of, rotary joint (72) through entrance piping (75) connected to the nanometer range. Refrigerant introduction tube (74) other end of, refrigerant path (71) in the immediate vicinity of the other end of the refrigerant path (71) is opened to be in. Number 2 embodiment in one form, such as oil or refrigerant entrance piping (75) from rotary joint (72) and refrigerant introduction tube (74) through the coolant path (71) is sent to a. Refrigerant path (71) sent refrigerant, refrigerant path (71) inner peripheral surface of the refrigerant introduction tube (74) through a gap between the outer peripheral surface of the rotating shaft (38) of joint section (42) with returned, rotary joint (72) through exit piping (73) back into the vehicle from the outside. The number 2 embodiment form, refrigerant axis of rotation (38) along the axial direction of the circulating, its transmitting screw body (37) can be cooling. To this end, raw material in contact with the screw body (37) controls the temperature of the can be, based on a temperature rise in the raw material resin can prevent degradation and deterioration of viscosity change. [Number 3 embodiment form] 16 Also to Figure 22, etc. form disclosure number 3 embodiment. Number 3 embodiment form, screw (21) screw body (37) option number 1 embodiment differ from the form hereinafter disclosed. Other number 2 extruder (3) the configuration of the, number 1 embodiment form essentially are the same. Thereby, number 3 embodiment in one form, the same number 1 embodiment form the same heating references a constituent part of the disconnecting, description and omitting other. As also shown in 16 and 17 also, screw body (37) a plurality tubular body (39) is also in the form number 1 embodiment, color number 1 (48) on color number 2 (50) number 2 between shaft (41) is combined in the axial direction of, adjacent tubular member (39) the end of which (39a) surfaces without contact in the nanometer range. Screw body (37) is a plurality of material is transferred by section (81) on, number valve timing of the flow of raw material a plurality of barrier portion (82) having disclosed. Section (81) and barrier portion (82) includes a screw body (37) in an axial direction of alternating located side by side in the nanometer range. Also 17 and 19 as shown in also, each section (81) is helically twisted flight (84) 26c1. Flight (84) includes a tubular body (39) from the outer peripheral surface along the circumferential direction of the transfer passage (51) projects toward the, its flight (84) is top of section (81) etc. a perimeter on configuration. Flight (84) includes a screw (21) when is turns on, screw body (37) material is transferred from the proximal end to the head to distorted disclosed. In other words, flight (84) includes a flight (84) torsion direction equal to close the door to the right distorted disclosed. Screw body (37) along the axial direction of the section (81) the length of the, e.g. raw materials, kneading degree, like soul [lyen scandal of production per unit time to vary along the cross lines are deleted. In addition, section (81) implies, at least of the tubular body (39) of the circumference of the flight (84) unit includes means but, flight (84) in a region between the specific point and end point are not correct. In other words, tubular body (39) of the outer peripheral surface of flight (84) also deviates from the section area (81) when taken as the flow tides. Therewith, flight (84) having a tubular body (39) when the cover is disposed at a position adjacent cylindrical spacer or cylindrical collar, and also color section (81) be included may be the case. Each barrier portion (82) is helically twisted flight (85) having disclosed. Flight (85) has a tubular body (39) from the outer peripheral surface along the circumferential direction of the transfer passage (51) projects toward the, its flight (85) the end portion of the barrier portion (82) etc. a perimeter on configuration. Flight (85) includes a screw (21) when is turns on, screw body (37) toward front end distal from the material carry distorted disclosed. In other words, flight (85) is flight (85) torsion direction left-hand thread equal to left distorted disclosed. Barrier portion (82) of flight (85) pitch of, section (81) of flight (84) that are equal to or pitch of, flight (84) the advantage of less. In addition, flight (84, 85) and end portion of the barrel (20) of the cylinder portion (33) is formed between an inner peripheral surface, some clearance is reserved in the nanometer range. Screw body (37) along the axial direction of the barrier portion (82) the length of the, e.g. raw materials, kneading degree, like soul [lyen scandal of production per unit time to vary along the cross lines are deleted. Barrier portion (82) includes a section (81) sent by flow material functions to each other. I.e., barrier portion (82) is guided at the downstream side in the carrying direction of the cylinder (81) with adjacent, conveying parts (81) sent by the raw flight (85) and the top of the cylinder portion (33) from passing into the clearance between the inner peripheral surface 70 is composed so as to. , the embodiment form according to number 2 extruder (3) in, barrier portion (82) is blocked from the flow of raw material in position of, raw material barrier portion (82) the outer circumferential surface of the cylinder portion (33) does not pass through the clearance between the inner peripheral surface to the number etc. before. The embodiment form the, screw body (37) in the proximal end, a plurality of conveying parts (81) the screw body (37) continuous in the axial direction of an arrangement disclosed. Barrel (20) through the feed opening (34) includes a screw body (37) a quantity of a proximal end of section (81) of opposite along the axial direction is equipped with an interstitial etc.. Similarly, screw body (37) of leading edge, a plurality of conveying parts (81) the screw body (37) continuous in the axial direction of an arrangement disclosed. Also 17 and 19 as shown in also, screw body (37) in the intermediate part of the, conveying parts (81) flight constituting (84) and barrier portion (82) constituting a flight (85) of the tubular body is common (39) along the circumferential direction of the outer peripheral surface is continuously formed in the nanometer range. I.e., one tubular body (39) of the outer peripheral surface of different function 2 flight (84, 85) axially continuously formed in the nanometer range. Barrier portion (82) constituting a flight (85) includes a section (81) flight constituting (84) with respect to the screw body (37) the tip end side of position in the nanometer range. In addition, the embodiment in one form, flight (84, 85) is, outer diameter of the tubular body into a plurality of equally both D1 (39) transfer from the outer surface (51) toward the projecting in the nanometer range. To this end, the tubular body (39) a circumferential outer surface of, screw (21) defined etc. of the bolt. Screw (21) gain-of-function of roentgen per hour at one meter, screw (21) over the entire length of obtained in the nanometer range. As also shown in 16 to 20 also, screw body (37) includes a screw body (37) radially extending defines a plurality of passages (86) having disclosed. Passage (86) includes a screw body (37) along the axial direction of the same linear member to aligns in the nanometer range. Each passage (86) is 2 kinds of flight (84, 85) of the tubular body 2 is formed of (39) to SPAN between, its tubular body (39) formed in the nanometer range. Specifically described, each passage (86) is number 1 to number 3 passage element (87, 88, 89) defining in the nanometer range. Number 1 passage element (87) has a passage (86) as a inlet can be in other words. Number 1 passage element (87) adjacent 2 includes two tubular body (39) of the tubular body into one (39) of the circumference of the other end is opened to disclosed. Number 1 passage element (87) of the open end, conveying parts (81) on the barrier portion (82) located at the boundary of although, section (81) of flight (84) and barrier portion (82) of flight (85) is out disclosed. In addition, the embodiment in one form, number 1 passage element (87) is one of the tubular body (39) formed by an outer circumferential surface of e.g. drill over embodiment using machining. Thereby, number 1 passage element (87) has a circular cross-sectional shape and having holes, one (O1) and orthogonal to the axis of the tubular body (39) of the tubular body from the outer surface (39) of the radial extending in the nanometer range. Number 1 passage element (87) bottom (87a) the base end of the drill in a conical manner is slanted disclosed. Number 2 passage element (88) is a passage body flow can be in other words as a raw material. Number 2 passage element (88) adjacent 2 includes two tubular body (39) to SPAN between, screw body (37) axis (O1) and is positioned parallel in the nanometer range. The, number 2 passage element (88) is without branch during screw body (37) although straight in the axial direction of the seat, the total predetermined have a length disclosed. As best shown to also 20, number 2 passage element (88) is one of the tubular body (39) formed therein and a portion of number 1 (91a) and, the other end of the tubular body (39) formed therein and a portion of number 2 (91b) etc. with. Number 2 passage element (88) of number 1 portion (91a) of the tubular body has an (39) extending straight in the axial direction of although, one of the tubular body (39) of the tubular body of the previous (39) front side (39a) is opened to the disclosed. Number 1 portion (91a) of line opposite end open, one of the tubular body (39) blocked with an intermediate portion along the axial direction of in 2000. The embodiment form the, number 2 passage element (88) of number 1 portion (91a) of the tubular body has an (39) the end of which (39a) of the tubular body from one (39) drill for example embodiment using machining formed by in the nanometer range. To this end, part number 1 (91a) having cross-sectional shapes of circular hole defined disclosed. Number 2 passage element (88) portion of number 2 (91b) is, the other end of the tubular body (39) extending straight in the axial direction of although, the other tubular body (39) of the tubular body into one of (39) front side (39a) is opened to the disclosed. Number 2 portion (91b) of line opposite open end, the other end of the tubular body (39) in the interior of the blocked with 1. The embodiment form the, number 2 passage element (88) portion of number 2 (91b) is, the other tubular body (39) the end of which (39a) of the tubular body from the other (39) using machining embodiment example drill formed by in the nanometer range. To this end, part number 2 (91b) is, number 1 portion (91a) as well as a circular cross section with a hole defined disclosed. As best shown to 17 and also 20 also, number 1 portion (91a) portion of number 2 (91b) of the open end, two adjacent tubular body 2 (39) the shaft (38) when axial length, counts the number of butt to be are interconnected with each other to simplify the structure. Number 3 passage element (89) includes a passage (86) outlet can be called in other words. Number 3 passage element (89) 2 has two adjacent tubular body (39) of the tubular body into the other side (39) of the circumference of the other end is opened to disclosed. Number 3 passage element (89) of the open end, section (81) are positioned transversely to the upstream end of with, conveyance section (81) in which flight (84) is out disclosed. As a result, number 1 passage element (87) of number 3 passage element (89) of the open end, barrier portion (82) through a screw body (37) axially spaced apart disclosed. In addition, the embodiment in one form, number 3 passage element (89) of the tubular body into other side (39) formed by an outer circumferential surface of e.g. drill over embodiment using machining. Thereby, number 3 passage element (89) has a circular cross-sectional shape and having holes, one (O1) and orthogonal to the axis of the tubular body (39) of the tubular body from the outer surface (39) of the radial extending in the nanometer range. Number 3 passage element (89) bottom (89a) conically tip of the drill is slanted disclosed. As also shown in the 20, number 2 passage element (88) of number 1 portion (91a) of opposite end, one of the tubular body (39) in the interior of the passage element number 1 (87) is connected to disclosed. Number 1 passage element (87) and number 2 passage element (88) of number 1 portion (91a) all while maintaining a circular cross section shape are communicated with each other. In addition, number 2 passage element (88) of number 1 portion (91a) is number 1 passage element (87) has a conical bottom (87a) number 1 at a location outside the passage element (87) is connected to disclosed. Number 2 passage element (88) of number 1 portion (91a) is number 1 passage element (87) bottom (87a) connected to a retarder. To this end, number 1 passage element (87) includes a screw body (37) exposing the number 2 of the circumference of the passage element (88) of number 1 portion (91a) from one end of housing (39) diametrically of elevated number 1 can be raised portion as a in other words. Number 2 passage element (88) portion of number 2 (91b) of opposite end, the other end of the tubular body (39) number 3 in the interior of the passage element (89) is connected to disclosed. Number 3 passage element (89) and number 2 passage element (88) portion of number 2 (91b) is, both while maintaining a circular cross section shape etc. are interconnected with each other. In addition, number 2 passage element (88) portion of number 2 (91b) is, number 3 passage element (89) conical bottom (89a) number 3 position outside the passage element (89) is connected to disclosed. Number 2 passage element (88) portion of number 2 (91b) is, number 3 passage element (89) bottom (89a) connected to a retarder. To this end, number 3 passage element (89) includes a screw body (37) exposing the number 2 of the circumference of the passage element (88) portion of number 2 (91b) from one end of housing (39) of number 2 as a raised portion raised in the radial direction can be in other words. The embodiment form the, tubular body (39) of a passage within (86) by providing, through the passage (86) includes a screw body (37) with respect to the axis (O1) offset disclosed. To this end, passage (86) includes a screw body (37) is rotated around the axis (O1) when a cylinder body. Number 2 passage element (88) constituting the inner diameter of the hole, e.g. 1 mm or more, less than 6 mm, preferably 1 mm or more, to 5 mm hereinafter are coupled to the lower end. In addition, number 2 passage element (88) the inner diameter of, the inlet passage element number 1 (87) less than the inner diameter of. Therewith, number 2 passage element (88) along a direction the diameter of a cross section, the cylinder portion (33) along a direction the diameter of the transfer passage (51) set so as to be much smaller than the cross sectional area of over. The embodiment form the, tubular body (39) is number 1 to number 3 passage element (87, 88, 89) defines constituting a wall surface of a cylindrical shape of the hole (92) has disclosed. Wall (92) surrounded by a number 1 to number 3 passage element (87, 88, 89) is, allowing for only a hollow space and material flow, screw body in space (37) consists not present. In addition, wall (92) is removed body (37) when the body is rotated, about axis (O1) without self axis (O1) revolves around a substrate. In addition, the embodiment in one form, flight (84, 85) having plural tubular body (39) the shaft (38) when number from a stand-alone, number 1 passage element (87) and number 3 passage element (89) is installed in at least either, number 2 inside passage element (88) is attached to the tubular body (39) includes a screw element can be called in other words. The back-up, number 1 extruder (2) blend to a concrete composition having raw materials, number 2 extruder (3) through the feed opening (34) transfer from (51) continuously supplied. Number 2 extruder (3) raw materials supplied, as represented by arrow C 21 also, screw body (37) positioned in one of the proximal end of section (81) of the circumference of the input thereto. Screw (21) has an axis of rotation (38) in the counterclockwise direction when viewed from the direction of the proximal end of the turns on, section (81) of flight (84) as shown arrows 21 also includes a filar of the, feed opening (34) input raw materials from screw body (37) to the head of delivering. The, transfer (51) turning in flight (84) with a cylinder portion (33) generated by the speed difference between the inner peripheral surface with raw material added to a shearing action, flight (84) of the raw materials by a state torsion electrooculogram agitated. As a result, the fixing element is kneading the raw materials, the processing advances is distributing component material. Raw materials subjected to a shearing action, a transfer passage (51) section along (81) on the barrier portion (82) a boundary between sets of amounts. Barrier portion (82) of flight (85) includes a screw (21) when is turns on, screw body material (37) toward the front end distal from carrying, flight (84) raw material sent by flight (85) passages to each other. I.e., barrier portion (82) of flight (85) includes a screw (21) turns on is when, section (81) of flight (84) with valve timing of the flow of raw material sent by number, raw material barrier portion (82) the outer circumferential surface of the cylinder portion (33) is passed out of the signal in the clearance between the inner peripheral surface and a first substrate. As a result, conveying parts (81) on the barrier portion (82) raw material in a boundary between a of a tapered body. Specifically described, Figure 22, a transfer passage (51) during passage (86) an addition result corresponding to full rate represented by a multilayer material which, dense color tone are compensated by increasing rate of diffuser material installed disclosed. From 22 as also referring to a transfer passage (51) in, barrier portion (82) and by the rate of diffuser material proximate the bubbles, barrier portion (82) is immediately, raw material of diffuser 100% rate is the nanometer range. To this end, barrier portion (82) of diffuser material immediately before 100% rate in raw material the reservoir R formed therein. Raw material in the reservoir R, material flow is blocked from the raw material due to a pressure rise disclosed. The pressure in the raw materials, and also of arrows 21 to 22 as shown also intersecting the, conveying parts (81) on the barrier portion (82) is formed on the boundary between sets of passage (86) of number 1 passage element (87) number 2 from passage element (88) into the substrate. Number 2 passage element (88) with a predetermined length from raw materials, screw body (37) from the proximal end to the head number 2 passage element (88) for ventilation through substrate. Number 2 passage element (88) along a direction the diameter of a cross section, the cylinder portion (33) along a direction the diameter of the transfer passage (51) of less than cross-sectional area. In other words, number 2 passage element (88) the inner diameter of, screw body (37) is much smaller outer sleeve, number 2 permits the passage element (88) is abruptly when it passes through a raw material is compressed, the stretching action as its raw material added substrate. Further, number 2 passage element (88) cross-sectional area of a transfer passage (51) due to the small cross sectional area of sufficiently than, raw material the reservoir R through-passage (86) despite bracket, barrier portion (82) raw material the reservoir R immediately uncovering free driving transistor. To this end, e.g. section (81) of flight (84) by barrier portion (82) which is sent to the flow rate of the raw material using the former somewhat reduced, flow rate through-phosphate raw material the reservoir R can be supplemented. The, raw materials, always in a stable state the passage (86) to feed. Of arrows 22 also intersecting the to as shown, passage (86) of number 2 passage element (88) through raw materials, number 3 passage element (89) adjacent from section (81) tubular body (39) on its outer peripheral face is returned thereto. Feedback raw materials, adjacent section (81) of flight (84) by screw body (37) is fed in a distal direction of, again subjected to a carrier during the shearing action. Raw materials subjected to a shearing action, then passage (86) of number 1 passage element (87) number 2 from passage element (88) with bracket, number 2 passage element (88) extending through subjected in action again. Screw body (37) along the axial direction of the intermediate portion, a plurality of conveying parts (81) and a plurality of barrier portion (82) the screw body (37) disposed alternately in the axial direction of although, a plurality of passages (86) the screw body (37) arranged at intervals in the axial direction of the over. To this end, feed opening (34) from the screw body (37) is introduced to the raw materials, a shearing action and extending alternately repeated action under the screw body (37) in the direction of the proximal end of the tip from disconnected during without continuously conveyed substrate. The, enhanced kneading degree, distributing component material is promoted with each other. A plurality of passages (86) of number 2 passage element (88) is individually number 1 passage element (87) and number 3 passage element (89) through the screw body (37) is opened to the outer peripheral surface of 2000. To this end, each passage (86) in, number 1 passage element (87) number 2 from passage element (88) with a predetermined length from raw materials, not necessarily number 3 passage element (89) through the screw body (37) and the outer peripheral surface is returned, a plurality of passages (86) in the raw materials are mixed between the free. The, material soul [lyen degree while avoiding excess can be, in accordance with an appropriate soul [lyen this desired . The number 3 embodiment form, the stretching action raw material adding passage (86) includes a screw body (37) serving as a rotation center axis (O1) eccentrically with respect to the position of the screw body (37) is connected to the second axially-extending, passage (86) around an axis (O1) is a cylinder body. In other words, passage (86) defining a cylindrical wall (92) about the axis (O1) without rotation axis (O1) revolves around a substrate. To this end, the raw materials passage (86) food when it passes through a passage (86) in the interior of the extended work is free for the synthesis. The, passage (86) the raw materials through a shearing action that likely to, passage (86) through section (81) is received by the outer peripheral surface of the raw material is mainly returned elongated action with each other. The, number 3 embodiment in the form of a screw (21) can be attained, at least an additional shearing action stretchable raw material and raw material containing at least an additional clearly an incident, said number 1 embodiment form the same effect can be achieved. [Variants in the form of number 3 embodiment] Figure 23, shape number 3 embodiment modified relevance etc. incorporated disclosure. Variation, screw body (37) of barrier portion (82) on the configuration of the shape number 3 embodiment hereinafter disclosed. As also shown in the 23, barrier portion (82) includes a screw body (37) radially extending cylindrical the compressing (95) consisting in the nanometer range. The housing (95) includes a screw body (37) continuously in the circumferential direction of an outer peripheral (95a) having an, screw body (37) along the axial direction of the screw body length (37) along the axial direction of the barrier portion (82) at the same pitch is equal to the length of. The housing (95) on its outer peripheral face (95a) can have a smooth surface or paragraph wave having a thickness of preferably does not exist. [Number 4 embodiment form] 24 Also to Figure 31, etc. form number 4 embodiment disclosure. Number 4 embodiment form, screw (21) screw body (37) option number 1 embodiment differ from the form hereinafter disclosed. Other number 2 extruder (3) the configuration of the, number 1 embodiment form essentially are the same. Thereby, number 4 embodiment in one form, the same number 1 embodiment form the same heating references a constituent part of the disconnecting, description and omitting other. As also shown in the 26 to 24 also, screw body (37) a plurality tubular body (39) is also in the form number 1 embodiment, color number 1 (48) on color number 2 (50) number 2 between shaft (41) is combined in the axial direction of, adjacent tubular member (39) the end of which (39a) surfaces without contact in the nanometer range. Screw body (37) is a plurality of material is transferred by section (101) on, number valve timing of the flow of raw material a plurality of barrier portion (102) on, a plurality of circulation temporarily circulating raw material (103) having disclosed. Section (101), barrier portion (102) and circulation (103) includes a screw body (37) in the axial direction of juxtaposed disclosed. Each section (101) is helically twisted flight (105) 26c1. Flight (105) includes a tubular body (39) from the outer peripheral surface along the circumferential direction of the transfer passage (51) projects toward the, its flight (105) is top of section (101) etc. a perimeter on configuration. Flight (105) includes a screw (21) when is turns on, screw body (37) material is transferred from the proximal end to the head to distorted disclosed. In other words, flight (105) includes a flight (105) torsion direction equal to close the door to the right distorted disclosed. The embodiment in one form, screw body (37) and the front end of the plurality of conveying parts respectively (101) successively placed in disclosed. Barrel (20) through the feed opening (34) includes a screw body (37) a quantity of a proximal end of section (101) of opposite along the axial direction is equipped with an interstitial etc.. Screw body (37) along the axial direction of the section (101) the length of the, e.g. raw materials, kneading degree, like soul [lyen scandal of production per unit time to vary along the cross lines are deleted. In addition, section (101) implies, at least of the tubular body (39) of the circumference of the flight (105) unit includes but, flight (105) in a region between the specific point and end point are not correct. In other words, tubular body (39) of the outer peripheral surface of flight (105) also deviates from the area section (101) when taken as the flow tides. Therewith, flight (105) having a tubular body (39) when the cover is disposed at a position adjacent cylindrical spacer or cylindrical collar, and also color section (101) be included may be the case. Barrier portion (102) includes a screw body (37) in the intermediate part between the proximal end and a screw body (37) arranged at intervals in the axial direction of the over. Each barrier portion (102) is helically twisted flight (107) having disclosed. Flight (107) includes a tubular body (39) from the outer peripheral surface along the circumferential direction of the transfer passage (51) and projecting toward, its flight (107) end portion of the barrier portion (102) of the peripheral surface of the configuration etc.. Flight (107) includes a screw (21) when is turns on, screw body (37) toward front end distal from the material carry distorted disclosed. In other words, flight (107) includes a flight (107) torsion direction left-hand thread equal to left distorted disclosed. Barrier portion (102) of flight (107) pitch of, section (101) of flight (105) that are equal to or pitch of, flight (105) the advantage of less. In addition, screw body (37) along the axial direction of the barrier portion (102) have an overall length of, section (101) is shorter than the entire length of the. Further, flight (107) and end portion of the barrel (20) of the cylinder portion (33) the clearance between the inner peripheral surface, flight (105) and end portion of the barrel (20) of the cylinder portion (33) slightly smaller than the clearance between the inner peripheral surface. Screw body (37) along the axial direction of the barrier portion (102) the length of the, e.g. raw materials, kneading degree, like soul [lyen scandal of production per unit time to vary along the cross lines are deleted. Barrier portion (102) includes a section (101) sent by flow material functions to each other. I.e., barrier portion (102) includes a section (101) sent by the raw flight (107) and the top of the cylinder portion (33) configured to pass through the clearance between the inner peripheral surface relayed over number. Circulation (103) includes a barrier portion (102) for the rotating shaft (38) from the direction of the proximal of adjacent etc.. Each circulation unit (103) is twisted spiral flight number 1 to number 3 (110, 111, 112) having disclosed. The embodiment in one form, barrier portion (102) from screw body (37) toward the front end of the flight number 1 (110), flight number 2 (111) and number 3 flight (112) arranged in that order in the nanometer range. Number 1 to number 3 flight (110, 111, 112) is, each tubular member (39) from the outer peripheral surface along the circumferential direction of the transfer passage (51) projects toward the, its flight (110, 111, 112) is circulation portion of (103) etc. a perimeter on configuration. Number 1 to number 3 flight (110, 111, 112) is, screw body (37) successively arranged in the axial direction of although, screw (21) when is turns on, screw body (37) material is transferred from the proximal end to the head to distorted disclosed. In other words, number 1 to number 3 flight (110, 111, 112) is, close the door equal to individual torsion direction right distorted disclosed. Flight number 1 (110) pitch of, adjacent barrier portion (102) of flight (107) that are equal to or pitch of, flight (107) of greater advantage. Flight number 2 (111) pitch of, flight number 1 (110) of less advantage. Flight number 3 (112) pitch of, flight number 2 (111) of greater advantage. Number 1 to number 3 flight (110, 111, 112) and end portion of the barrel (20) of the cylinder portion (33) is formed between an inner peripheral surface, some clearance is reserved in the nanometer range. The embodiment in the form of a screw (21) the, various flight (105, 107, 110, 111, 112) includes, a plurality equally both tubular body outer diameter D1 (39) transfer from the outer surface (51) toward the projecting in the nanometer range. To this end, the tubular body (39) a circumferential outer surface of, screw (21) defined etc. of the bolt. Screw (21) gain-of-function of roentgen per hour at one meter, screw (21) over the entire length of obtained in the nanometer range. As also shown in the 26 to 24 also, screw body (37) includes a screw body (37) radially extending defines a plurality of passages (115) 26c1. Passage (115) includes a circulation unit (103) of flight number 1 (110) of the tubular body at the location of (39) formed inside and, screw body (37) axially spaced from each are arranged in a line in the nanometer range. Each passage (115) includes a screw body (37) axis (O1) and is positioned parallel in the nanometer range. In other words, passage (115) is accommodated without branch during (39) extends in an axial direction of the straight line type and, overall predetermined have a length disclosed. The tubular body (39) of a passage within (115) by providing, through the passage (115) includes a screw body (37) axis (O1) offset from the disclosed. To this end, passage (115) includes a screw body (37) rotates about an axis (O1) when, axis (O1) revolves around a substrate. As also shown in the 27, passage (115) is further provided with a hole for example a circular cross section defined disclosed. Passage (115) constituting the inner diameter of the hole, e.g. 1 mm or more, less than 6 mm, preferably 1 mm or more, to 5 mm hereinafter are coupled to the lower end. Passage (115) along a direction the diameter of a cross section, the cylinder portion (33) along a direction the diameter of the transfer passage (51) set so as to be much smaller than the cross sectional area of over. In addition, flight number 1 (110) is formed of the tubular body (39) includes a cylindrical wall defines a bore (116) has disclosed. Wall (116) surrounded by a passage (115) is hollow space and allowing for only a distribution screw, screw body in space (37) consists not present. Therewith, wall (116) is removed body (37) rotates about an axis (O1) when, about axis (O1) axis (O1) without self revolves around a substrate. As also shown in the 31 and 26 also, each passage (115) an inlet (117) and outlet (118) having disclosed. Inlet (117) includes a circulation unit (103) for the rotating shaft (38) from the direction of the front end of the adjacent barrier portion (102) immediately before located disclosed. The embodiment in one form, circulation (103) of the tubular body constituting (39) end face of, the tubular body (39) of the circumference of the hot space (120) is formed, in the groove (120) on the inner surface of inlet (117) is opened disclosed. Outlet (118) includes a flight number 1 (110) on flight number 2 (111) a boundary between sets of position in the nanometer range. The embodiment in one form, circulation (103) of the tubular body constituting (39) end face of, the tubular body (39) of the circumference of the hot space (121) is formed, the recess (121) on the inner surface of outlet (118) is opened disclosed. To this end, inlet (117) and outlet (118) includes a flight number 1 (110) corresponding to the position of the screw body (37) axially spaced apart disclosed. The embodiment form the, groove (120) is formed on the inner surface of inlet (117) of the opening area and home (121) is formed on the inner surface of outlet (118) have an area of opening, passage (115) and a large diameter of equal to or preferably along a direction area. In addition, a plurality of tubular body (39) the shaft (38) a stand-alone number from the screw (21) when decomposing, flight number 1 (110) and passage (115) is attached to the tubular body (39) includes a screw element can be called in other words. Similarly, other flight (105, 107, 111, 112) having plural tubular body (39) be a, axis of rotation (38) number from the other state screw element as a stand-alone can be in other words. The back-up, number 1 extruder (2) blend to a concrete composition having raw materials, number 2 extruder (3) through the feed opening (34) transfer from (51) continuously supplied. Number 2 extruder (3) raw materials supplied, as represented by arrow 30 also D, screw body (37) positioned in one of the proximal end of section (101) of the circumference of the input thereto. Screw (21) has an axis of rotation (38) in the counterclockwise direction when viewed from the direction of the turns on a proximal end of the, conveying parts (101) of flight (105) has a supply opening (34) input raw materials from adjacent circulation (103) delivering toward. Circulation unit (103) of number 1 to number 3 flight (110, 111, 112) is, the filar of arrows 30 and 31 also also as shown, the material continuously screw body (37) of delivering in a distal direction. The, transfer (51) turning in flight (105, 110, 111, 112) with a cylinder portion (33) generated by the speed difference between the inner peripheral surface with raw material added to a shearing action, flight (105, 110, 111, 112) of the raw materials by a state torsion electrooculogram agitated. As a result, the fixing element is kneading the raw materials, the processing advances is distributing component material. Raw materials subjected to a shearing action, a transfer passage (51) along circulation (103) on the barrier portion (102) a boundary between sets of amounts. Barrier portion (102) of flight (107) includes a screw (21) when is turns on, screw body material (37) toward the front end distal from carrying, flight number 1 (110) raw material sent by flight (107) fluid passages to each other. I.e., barrier portion (102) of flight (107) includes a screw (21) turns on is when, circulation (103) of flight number 1 (110) with valve timing of the flow of raw material sent by number, raw material barrier portion (102) the outer circumferential surface of the cylinder portion (33) is passed out of the signal in the clearance between the inner peripheral surface and a first substrate. As a result, circulation (103) on the barrier portion (102) raw material in a boundary between a high pressure region. Specifically described, Figure 31, a transfer passage (51) during passage (115) an addition result corresponding to full rate represented by a multilayer material which, dense color tone are compensated by increasing rate of diffuser material installed disclosed. Referring to 31 as also from, a transfer passage (51) in, circulation (103) of flight number 2 (111) from barrier portion (102) by the rate of diffuser material proximate the bubbles and, barrier portion (102) is immediately, 100% rate of diffuser material to in the nanometer range. To this end, barrier portion (102) of diffuser material immediately before 100% rate in raw material the reservoir R formed therein. Raw material in the reservoir R, material flow to blind involving material pressure in the in the nanometer range. Pressure in the raw materials, and also of 30 to 31 as shown arrows also intersecting the, groove (120) through barrier portion (102) located immediately before an inlet (117) with being guided, its inlet (117) from passage (115) introduced into the substrate. Passage (115) with a predetermined length from raw materials, screw body (37) toward the front end distal from passage (115) in passing through the substrate. Passage (115) in material flow direction is, flight (105, 110, 111, 112) are fixed to the material sent by . Passage (115) along a direction the diameter of a cross section, the cylinder portion (33) along a direction the diameter of the transfer passage (51) of less than cross-sectional area. In other words, passage (115) the inner diameter of, screw body (37) is much smaller outer sleeve, that the liquid raw material (115) when it passes through a raw material is abruptly compressed, the stretching action as its raw material added substrate. Further, passage (115) cross-sectional area of a transfer passage (51) due to the small cross sectional area of sufficiently than, raw material the reservoir R through-passage (115) despite bracket, barrier portion (102) raw material the reservoir R immediately uncovering free driving transistor. To this end, e.g. flight number 1 (110) through barrier portion (102) which is sent to the flow rate of the raw material using the former somewhat reduced, flow rate through-phosphate raw material the reservoir R can be supplemented. The, raw materials, always in a stable state the passage (115) is sent to a. Passage (115) raw materials through, outlet (118) a groove (121) circulating through portion (103) of the tubular body constituting (39) outer circumference of returned thereto. Feedback raw materials, flight number 1 (110) by screw body (37) is fed to the head of, again subjected to a carrier during the shearing action. The embodiment in one form, flight number 1 (110) by barrier portion (102) toward a portion of the conveyed material, again inlet (117) from passage (115) is induced to, circulation (103) at a place where the temporarily circulation of repeating other. Barrier portion (102) carried toward the remaining raw materials, barrier portion (102) of flight (107) and the top of the cylinder portion (33) through the clearance between the inner peripheral surface occupied by a circulation unit (103) introduced into the substrate. Inlet raw materials, adjacent circulation (103) of number 1 to number 3 flight (110, 111, 112) by screw body (37) of carrier in a distal direction with each other. A plurality of passages (115) is individually inlet (117) and outlet (118) through circulation (103) tubular body (39) of the circumference of the other end is opened to disclosed. To this end, each passage (115) in, inlet (117) introduced from raw materials, not necessarily outlet (118) through circulation (103) tubular body (39) and the outer peripheral surface is returned, a plurality of passages (115) the raw materials are mixed between the thing free. The, material soul [lyen degree while avoiding excess can be, in accordance with an appropriate soul [lyen this desired . The embodiment in the form of a screw (21) the, plurality of barrier portion (102) and a plurality of circulation (103) the screw body (37) disposed alternately along an axial direction of the dashpot. Therewith, a plurality of passages (115) having a plurality of circulation (103) of flight number 1 (110) corresponding to the position of the screw body (37) arranged at intervals in the axial direction of the over. To this end, feed opening (34) from the screw body (37) raw materials supplied to, a shearing action and extending alternately repeated action under the screw body (37) in the direction of the proximal end of the tip from disconnected during without continuously conveyed substrate. The, enhanced kneading degree, distributing component material is promoted with each other. The number 4 embodiment form, the stretching action raw material adding passage (115) includes a screw body (37) serving as a rotation center axis (O1) eccentrically with respect to the position of the screw body (37) is connected to the second axially-extending, passage (115) around an axis (O1) is a cylinder body. In other words, passage (115) defining a cylindrical wall (116) about the axis (O1) without self axis (O1) revolves around a substrate. To this end, the raw materials passage (115) when it passes through centrifugal force as its raw material receives a raw material walls (116) into the problem that shear forces act work is free. The, passage (115) through the circulation (103) tubular body (39) is returned the outer peripheral surface of the material is institution and from this, mainly stretching action with each other. The, number 4 embodiment in the form of a screw (21) can be attained, at least an additional shearing action stretchable raw material and raw material containing at least an additional clearly an incident, said number 1 embodiment form the same effect can be achieved. [Variants in the form of number 4 embodiment 1] Figure 32, number 4 embodiment variants 1 etc. a disclosure form 1010. The variants 1, the stretching action raw material adding passage (115) on the option number 4 embodiment shape hereinafter disclosed. The configuration of the other, form essentially number 4 embodiment are the same. As also shown in the 32, circulation (103) of flight number 1 (110) has an axis of rotation (38) 2 on two adjacent tubular body (39) between the formed over in the nanometer range. Flight number 1 (110) is formed of tubular member 2 (39) has an axis of rotation (38) each other along the axial direction of length L uniformly disclosed. Further, the stretching action raw material adding passage (115) is flight number 1 (110) is formed of tubular member 2 (39) to SPAN between, these two tubular body 2 (39) formed in the nanometer range. Specifically described, passage (115) is number 1 to number 3 passage element (131, 132, 133) defined as the nanometer range. Number 1 passage element (131) has a passage (115) as a inlet can be in other words. Number 1 passage element (131) includes two tubular body adjacent 2 (39) during barrier portion (102) of the tubular body adjacent with one (39) of the circumference of the other end is opened to disclosed. Number 1 passage element (63) of the open end, flight number 1 (110) is out although, adjacent barrier portion (102) immediately before located disclosed. In addition, number 1 passage element (131) is one of the tubular body (39) formed by an outer circumferential surface of e.g. drill over embodiment using machining. Thereby, number 1 passage element (131) has a circular cross-sectional shape and having holes, one (O1) and orthogonal to the axis of the tubular body (39) of the tubular body from the outer surface (39) of the radial extending in the nanometer range. Number 1 passage element (131) bottom (131a) conically tip of the drill is slanted disclosed. Number 2 passage element (132) is a passage body flow can be in other words as a raw material. As also shown in the 32, number 2 passage element (132) has two adjacent tubular body 2 (39) to SPAN between, screw body (37) axis (O1) and is positioned parallel in the nanometer range. The, number 2 passage element (132) is without branch during screw body (37) although straight in the axial direction of the seat, the total predetermined have a length disclosed. Number 2 passage element (132) is one of the tubular body (39) formed therein and a portion of number 1 (134a) and, the other end of the tubular body (39) formed therein and a portion of number 2 (134b) with disclosed. Number 2 passage element (132) of number 1 portion (134a) of the tubular body has an (39) extending straight in the axial direction of although, one of the tubular body (39) of the tubular body of the previous (39) front side (39a) is opened to the disclosed. Number 1 portion (134a) of line opposite end open, one of the tubular body (39) of end wall (39b) to be closed. The embodiment form the, number 2 passage element (131) portion of number 1 (134a) of the tubular body has an (39) the end of which (39a) of the tubular body from one (39) drill for example embodiment using machining formed by in the nanometer range. To this end, part number 1 (134a) having cross-sectional shapes of circular hole defined disclosed. Number 2 passage element (132) of number 2 portion (134b) of the tubular body into the other (39) extending straight in the axial direction of although, other tubular body (39) of the tubular body into one of (39) front side (39a) is opened to the disclosed. Number 2 portion (134b) of line opposite open end, the other end of the tubular body (39) of end wall (39b) to be closed. The embodiment form the, number 2 passage element (132) of number 2 portion (134b) of the tubular body into the other (39) the end of which (39a) of the tubular body from the other (39) using machining embodiment example drill formed by in the nanometer range. To this end, part number 2 (134b) is number 1 portion (134a) as well as a circular cross section with a hole defined disclosed. In addition, number 1 portion (134a) of , number 2 portion (134b) of the open end, two adjacent tubular body 2 (39) the shaft (38) when axial length, counts the number of butt to be are interconnected with each other to simplify the structure. Number 3 passage element (133) includes a passage (115) outlet can be called in other words. Number 3 passage element (133) adjacent 2 includes two tubular body (39) of the tubular body into the other side (39) of the circumference of the other end is opened to disclosed. Number 3 passage element (133) of the open end, flight number 1 (110) is out although, circulation (103) of flight number 2 (111) located immediately before 2000. The, number 1 passage element (131) and number 3 passage element (133) includes a screw body (37) axially spaced apart disclosed. The embodiment in one form, number 3 passage element (133) of the tubular body into other side (39) formed by an outer circumferential surface of e.g. drill over embodiment using machining. Thereby, number 3 passage element (133) has a circular cross-sectional shape and having holes, the other tubular body (39) of the tubular body from the outer surface (39) of the radial extending in the nanometer range. Number 3 passage element (133) bottom (133a) conically tip of the drill is slanted disclosed. As also shown in the 32, number 2 passage element (132) of number 1 portion (134a) of line opposite end open, one of the tubular body (39) number 1 in the interior of the passage element (131) is connected to disclosed. Number 1 passage element (131) and number 2 passage element (132) of number 1 portion (134a) all while maintaining a circular cross section shape are communicated with each other. In addition, number 2 passage element (132) of number 1 portion (134a) is number 1 passage element (131) has a conical bottom (131a) number 1 at a location outside the passage element (131) is connected to disclosed. To this end, number 1 passage element (131) includes a screw body (37) exposing the number 2 of the circumference of the passage element (132) of number 1 portion (134a) from one end of the tubular body (39) of number 1 can be in other words as a raised portion raised in the radial direction. Number 2 passage element (132) of number 2 portion (134b) of line opposite open end, the other end of the tubular body (39) number 3 in the interior of the passage element (133) connected to disclosed. Number 3 passage element (133) and number 2 passage element (132) of number 2 portion (134b) end, both while maintaining a circular cross section shape etc. are interconnected with each other. In addition, number 2 passage element (132) of number 2 portion (134b) number 3 the passage element (133) has a conical bottom (133a) number 3 position outside the passage element (133) connected to disclosed. To this end, number 3 passage element (133) includes a screw body (37) exposing the number 2 of the circumference of the passage element (132) of number 2 portion (134b) from one end of the tubular body (39) of number 2 as a raised portion raised in the radial direction can be in other words. Number 2 passage element (132) constituting the inner diameter of the hole, e.g. 1 mm or more, less than 6 mm, preferably 1 mm or more, to 5 mm hereinafter are coupled to the lower end. In addition, number 2 passage element (132) the inner diameter of, the inlet passage element number 1 (131) less than the inner diameter of. Therewith, number 2 passage element (132) along a direction the diameter of a cross section, the cylinder portion (33) along a direction the diameter of the transfer passage (51) set so as to be much smaller than the cross sectional area of over. In addition, tubular body (39) is number 1 to number 3 passage element (131, 132, 133) defines constituting a wall surface of a cylindrical shape of the hole (135) has disclosed. Wall (135) surrounded by a number 1 to number 3 passage element (131, 132, 133) is, allowing for only a hollow space and material flow, screw body in space (37) consists not present. Further, wall (135) is removed body (37) when the body is rotated, about axis (O1) without self axis (O1) revolves around a substrate. Such a configuration of passages (115) even, permits the passage (115) to receive a centrifugal force when the refrigerant passes but a raw material, the raw material to shear forces acting work is eliminated, said number 4 embodiment form the same effect can be achieved. In addition, passage (115) of number 2 passage element (132) is not necessarily screw body (37) formed parallel to the axis (O1) need not necessarily be disclosed. For example, as represented by 32 also litre , number 2 passage element (132) for a axis (O1) of the tubular body (39) in the radial direction of tilt, number 2 passage element (132) of number 1 passage element (131) on the opposite side end of the tubular body (39) so as to render the retarder directly of the circumference of the opening. According to this structure, the material outlet of the passage element number 3 (133) is eliminating, passage (115) shape can be simplified. [Variants in the form of number 4 embodiment 2] Figure 33, number 4 embodiment 2 variants 1010 form representing the disclosed. As shown in 33 also variants 2, flight number 1 (110) is formed of tubular member 2 (39) on a reference axis hereinafter disclosed. Specifically described, number 2 passage element (132) of number 1 portion (134a) formed one tubular body (39) is the entire length of L1, number 2 passage element (132) of number 2 portion (134b) formed the other tubular member (39) is set to be longer than the entire length of L2 in the nanometer range. The variants 2, flight number 1 (110) is formed of tubular member 2 (39) in addition, axis of rotation (38) of the tubular body into two different length L3 along the axial direction of different 2 (39) for preparing the, flight number 1 (110) having two tubular body 2 (39) over the length of the step 3 can be adjusted. Specifically described, the entire length of the tubular body L1 (39) L2 on the entire length of the tubular body (39) combination of, tubular body overall length L1 (39) L3 on the entire length of the tubular body (39) combination of, L2 and the entire length of the tubular body (39) L3 on the entire length of the tubular body (39) in accordance with the combination of. The, passage (115) can be hereinafter for the entire length of the change. [Variants in the form of number 4 embodiment 3] 34 Also to Figure 36, in the form of modified example 3 number 4 embodiment variants 1 and relevance represents disclosed. As also shown in the 35 and 34 also, number 2 passage element (132) of number 1 portion (134a) of line opposite end open, number 1 passage element (131) number 1 on orthogonal to the passage element (131) has a conical bottom (131a) connected to disclosed. Number 1 passage element (131) bottom (131a) is number 2 passage element (132) in communication with the circular opening (140a) 26c1. Opening (140a) includes a screw body (37) to open a beveled bottom perimeter on which widens towards the outlet (131a) opposite to other portions of the etc.. Number 2 passage element (132) of number 2 portion (134b) of line opposite end open, number 3 passage element (133) number 3 on orthogonal to the passage element (133) has a conical bottom (133a) connected to disclosed. Number 3 passage element (133) bottom (133a) is number 2 passage element (132) in communication with the circular opening (140b) 26c1. Opening (140b) includes a screw body (37) to open a beveled bottom perimeter on which widens towards the outlet (133a) opposite to other portions of the etc.. The variants 3, number 1 passage element (131) with a predetermined length from raw materials, as shown in arrows of Figure 35 (A), number 1 passage element (131) bottom (131a) is reached to the bottom point (131a) inclination of the opening (140a) guided in the direction of. To this end, raw materials, number 1 passage element (131) bottom (131a) dissolves the produced smoothly without number 2 passage element (132) introduced into the substrate. Number 2 passage element (132) raw materials through, opening (140b) number 3 from passage element (133) bottom (133a) introduced into the substrate. Number 3 passage element (133) introduced into the raw materials, as shown in arrows of Figure 36 (A), bottom (133a) inclination of the screw body (37) outer peripheral surface of the guided direction. To this end, raw materials, number 3 passage element (133) bottom (133a) dissolves the produced smoothly without screw body (37) is returned the outer peripheral surface of the substrate. The, passage (115) generated in a drifting of the cylinder can be local to the avoid, passage (115) can be added to the raw material through the desired extensibility action. In variants 3, number 1 passage element (131) bottom (131a) and number 3 passage element (133) bottom (133a) without the shape of the cone valve timing, e.g. hemispherical formed a retarder. [Variants in the form of number 4 embodiment 4] Figure 37, in the form of modified example 4 number 4 embodiment variants 1 and relevance representing the disclosed. 4 Variants is, number 2 passage element (132) of number 2 portion (134b) different from the configuration of the modified examples 1 hereinafter disclosed. As also shown in the 37, part number 2 (134b) which comprises a straight portion (134c) and a tapered portion (134d) 26c1. Straight portion (134c) and a tapered portion (134d) has a tubular body (39) the end of which (39a) from the side of the tubular body (39) formed by cutting machining embodiment over. Straight portion (134c) is number 3 passage element (133) connected to disclosed. Straight portion (134c) the inner diameter of, number 2 passage element (132) of number 1 portion (134a) less than the inner diameter of. A tapered portion (134d) of other side of the tubular body (39) the end of which (39a) is opened to the dispersibility, straight portion (134c) are communicated with coaxial type. A tapered portion (134d) of other side of the tubular body (39) the end of which (39a) from straight portion (134c) according to a predetermined length in the direction of diameter decreases continuously in the nanometer range. To this end, a major component of adding raw material stretching action number 2 passage element (132) of the cylinder diameter is in the medial portion is along a direction flow change in the nanometer range. A tapered portion (134d) is for example so that the other end of the tubular body (39) the end of which (39a) formed lower hole, formed by cutting the inner peripheral surface of the lower hole using taper reamer. Lower hole, straight portion (134c) etc. with water. The variants 4, number 2 passage element (132) of number 2 portion (134b) is straight portion (134c) upstream of the tapered portion (134d) having, its tapered portion (134d) is number 2 passage element (132) located on the intermediate portion of the other. To this end, number 2 passage element (132) is at intermediate portions thereof so that the inner diameter is gradually decreased, the raw number 2 passage element (132) when the refrigerant passes an elongated effect can be added to a raw material. [Variants in the form of number 4 embodiment 5] Figure 38, number 4 embodiment variants 5 1010 form representing the disclosed. As shown also in variants 5 38, one tubular body (39) of a passage within (115) is formed in the nanometer range. Passage (115) of number 2 passage element (132) is e.g. tubular body (39) at one end of (39a) of the tubular body from (39) formed by embodiment using machining to drill in the nanometer range. The, tubular body (39) to the interior of the tubular body (39) which passes axially through the circular cross-sectional shape through which (150) is formed, through hole (150) the tubular body (39) on either side of the end surface (39a) is opened to the disclosed. Through hole (150) of the tubular body into the (39) number 1 in the interior of the passage element (131) and number 3 passage element (133) etc. are matched. In addition, the through hole (150) of the open end of 2, individually closure (151a, 151b) to be blocked with liquid-tight to 2000. The, one tubular body (39) number 1 inside the passage element (131) number 3 on passage element (133) number 2 making a connection between the passage element (132) is defined in the nanometer range. In addition, tubular body (39) and the through hole (150) at the time of forming, through hole (150) the leading end of the tubular body (39) and the other side of end surface (39a) without opening on tubular body (39) of end wall (39b) closed to a retarder. [Variants in the form of number 4 embodiment 6] Figure 39, 5 variants in addition variants into the bag a 6 indicates a disclosed. As also shown in the 39, one tubular body (39) which penetrates the hole (150) includes an upstream portion (150a), downstream (150b) at its intermediate portion (150c) 26c1. The upstream section (150a), downstream (150b) at its intermediate portion (150c) has a tubular body (39) are arranged in a line to simplify the structure along the axial direction of the dashpot. The upstream section (150a) has a tubular body (39) number 1 in the interior of the passage element (131) with intersecting, tubular body (39) at one end of (39a) is opened to the disclosed. The upstream section (150a) of the open end, closure (151a) to be blocked with liquid-tight to 2000. Downstream (150b) is upstream (150a) diameter than less the nanometer range. Downstream (150b) has a tubular body (39) number 3 in the interior of the passage element (133) with engaging the, tubular body (39) and the other side of end (39a) is opened to the disclosed. Downstream (150b) of the open end, closure (151b) to be blocked with liquid-tight to 2000. Intermediate (150c) is upstream (150a) and a downstream on (150b) positioned between in the nanometer range. Intermediate (150c) is upstream (150a) downstream from (150b) according to a predetermined length in the direction of diameter decreases continuously in the nanometer range. To this end, a major component of adding raw material stretching action number 2 passage element (132) of the cylinder diameter is in the medial portion is along a direction flow change in the nanometer range. The variants 6, passage (115) of number 2 passage element (132) is intermediate portions thereof (150c) gradually reduced toward the downstream from the upstream of the inner diameter of over. Thereby, the raw number 2 passage element (132) when the refrigerant passes an elongated effect can be added to a raw material. [Number 5 embodiment form] Figure 40, etc. form disclosure number 5 embodiment. Number 5 embodiment form, the stretching action on raw material for adding a configuration number 1 embodiment forms hereinafter described. Other screw (21) form the configuration of the number 1 embodiment are the same. As also shown in the 40, tubular body (39) the inner peripheral surface of pair of grooves (161a, 161b) formed in the nanometer range. Home (161a, 161b) is, screw body (37) with radially extending, screw body (37) of diametrically spaced apart disclosed. In addition, home (161a, 161b) is, tubular body (39) is opened to the inner peripheral surface of 2000. Home (161a, 161b) of the open end, the tubular body (39) the shaft (38) number 2 of shaft (41) when placed in, number 2 shaft (41) blocked with an outer circumferential surface of 2000. Thereby, home (161a, 161b) is, number 2 shaft (41) cooperating outer circumferential surface of the expanding action the material adding passage (162) etc. defining. The embodiment in one form, passage (162) is an axis of rotation (38) and tubular member (39) a boundary between sets of position in the nanometer range. The number 5 embodiment form, passage (162) includes a screw body (37) in the interior of the shaft (38) axis (O1) eccentrically with respect to the position can be maximized. The, form said number 1 embodiment similarly, passage (162) includes a screw body (37) is rotated around the axis (O1) when a cylinder body. Number 5 embodiment in one form, the tubular body (39) the shaft (38) number 2 of shaft (41) when placed in, screw body (37) of a passage within (162) is formed. Passage (162) defining a groove (161a, 161b) is, tubular body (39) so that the inner peripheral surface of opening, home (161a, 161b) for forming work can be made hereinafter. The, e.g. passage (162) when the need arises to change cross-sectional shape in accordance with the hereinafter for also corresponds. [Number 6 embodiment form] Figure 41, etc. form disclosure number 6 embodiment. Number 6 embodiment form, the stretching action on raw material for adding configuration shape number 5 embodiment hereinafter disclosed. Other screw (21) form the configuration of the number 5 embodiment are the same. As also shown in the 41, axis of rotation (38) number 2 of shaft (41) of the circumference of the pair of grooves (171a, 171b) formed in the nanometer range. Home (171a, 171b) is, number 2 shaft (41) with radially extending, number 2 shaft (41) of diametrically spaced apart disclosed. In addition, home (171a, 171b) is, number 2 shaft (41) is opened to the outer peripheral surface of 2000. Home (171a, 171b) of the open end, the tubular body (39) the shaft (38) number 2 of shaft (41) when placed in the, tubular body (39) blocked with the inner peripheral surface of 2000. Thereby, home (171a, 171b) is, tubular body (39) cooperates with the inner peripheral surface of the material stretching action adding passage (172) etc. defining. The embodiment in one form, passage (172) is an axis of rotation (38) and tubular member (39) a boundary between sets of position in the nanometer range. The number 6 embodiment form, passage (172) includes a screw body (37) in the interior of the shaft (38) axis (O1) eccentrically with respect to the position can be maximized. The, form said number 5 embodiment similarly, passage (172) includes a screw body (37) is rotated around the axis (O1) when a cylinder body. In one form number 6 embodiment, tubular body (39) the shaft (38) number 2 of shaft (41) when placed in, screw body (37) of a passage within (172) is formed. Passage (172) defining a groove (171a, 171b) is, axis of rotation (38) so that the outer circumferential surface of the opening, home (171a, 171b) for forming work can be made hereinafter. The, e.g. passage (172) when the need arises to change cross-sectional shape in accordance with the hereinafter for also corresponds. [Number 7 embodiment form] Figure 42, etc. form disclosure number 7 embodiment. Number 7 embodiment form, the stretching action on raw material for adding a configuration number 1 embodiment forms hereinafter described. Other screw (21) form the configuration of the number 1 embodiment are the same. As also shown in the 42, shaft number 2 (41) projecting from the outer surface key (45a, 45b) introducing tube recess (181a, 181b) is formed in the nanometer range. Recess (181a, 181b) is, number 2 shaft (41) extending along the axial direction of the although, key (45a, 45b) introducing tube is opened to the disclosed. Recess (181a, 181b) of the open end, key (45a, 45b) of the tubular body into a (39) of keyway (47a, 47b) when to be coupled, keyway (47a, 47b) blocked with the inner peripheral surface of 2000. Thereby, recess (181a, 181b) is, keyway (47a, 47b) cooperate with the inner peripheral surface of the material stretching action adding passage (182) and for defining. The embodiment in one form, passage (182) keys (45a, 45b) on the tubular body (39) located at the boundary of the nanometer range. The number 7 embodiment form, passage (182) includes a screw body (37) in the interior of the shaft (38) axis (O1) eccentrically with respect to the position can be maximized. The, form said number 1 embodiment similarly, passage (152) includes a screw body (37) is rotated around the axis (O1) when a cylinder body. In one form number 7 embodiment, axis of rotation (38) key (45a, 45b) of the tubular body into a (39) of keyway (47a, 47b) when to be coupled, screw body (37) of a passage within (182) is formed. Passage (182) defining a recess (181a, 181b) is, key (45a, 45b) so that the openings at the tip of, recess (181a, 181b) for forming work can be made hereinafter. The, e.g. passage (182) for when the need arises to change cross-sectional shape in accordance with the hereinafter also corresponds. Number 7 embodiment in one form, keyway (47a, 47b) number 2 the inner peripheral surface of the shaft (41) radially extending from a another recess, another recess and said recess (181a, 181b) by combined with said passage (182) to define a retarder. [Number 8 embodiment form] Figure 43, etc. form disclosure number 8 embodiment. Number 8 embodiment form, screw (21) and its extension is for adding a configuration in the form of action differ from number 1 embodiment hereinafter disclosed. As also shown in the 43, screw (21) includes a rigid screw body (200) with disclosed. Screw body (200) has a straight cutting edge 1 of the shaft-like member (201) consisting in the nanometer range. The shaft-like member (201) having an axis (O1) has a curved center bi-through, barrel (20) of the cylinder portion (33) coaxial type received from the photo diode region. The shaft-like member (201) is continuously in the circumferential direction peripheral rim (201a) and, an outer peripheral surface (201a) barrel (20) of the cylinder portion (33) facing the inner peripheral surface of etc.. The shaft-like member (201) on its outer peripheral face (201a) is, material is transferred by flight (202) is formed in the nanometer range. In addition, the shaft-like member (201) the stretching action of adding a raw material a pair of passage (203) is formed in the nanometer range. Passage (203) has a shaft-like member (201) although radially extending, axis between (O1) disposed in parallel and wherein the over. To this end, passage (203) includes a screw body (200) in the interior of the shaft-like member (201) axis (O1) eccentrically with respect to the position can be maximized. The, form said number 1 embodiment similarly, passage (203) includes a screw body (200) is rotated around the axis (O1) when a cylinder body. The stretching action raw material adding passage (203) includes a screw body (200) is 1 of the rod-like member (201) even if composed, screw body (200) can be formed. To this end, the screw body, in combination with the axis of rotation as a result of body configuration which are specific tastes. In the form of embodiment of the present invention are described but has several, these embodiment forms, which timing example number, or limit the scope of the invention is intended not disclosed. These novel forms of embodiment, other embodiment in various forms and are capable, in the range not deviating form the subject matter of invention, various omitted, substituted, can be changed. For example, the stretching action raw material adding passages, not limited to assembling holes. The passage, e.g. an oval or polygonal hole and the inside cross-sectional shape, the cross-sectional shape that is particularly about number free passage. Further, in one form said number 1 embodiment, screw body (37) the shaft (38) when viewed from the direction of the proximal end, screw (21) in the counterclockwise direction is described as an example but turns on when for example, the present invention refers to this number it is shrewd but are not correct. For example, screw (21) is in a clockwise direction even if wave are disclosed. In this case, screw (21) of section (54) is submerged in flight (56) includes a screw body (37) toward the front end distal from material is transferred to, close the door as well as to the right distorted if the substrate. Similarly, barrier portion (55) in which flight (57) includes a screw body (37) from the proximal end to the head material is transferred to, similarly if left left-hand thread twisted with each other. Therewith, number 2 extruder (3) gas components contained in the molten resin extruded from a number industry number 3 an extruder, is shortened to an extruder which are not specified, the use of an extruder retarder axis 2. The present invention according to continuous high shear processing device is, at least material number 1 to number 2 to flow distributor kneading extruder and raw material preliminary kneading and then the fixing element, gas phase material or volatile component number number 3 an extruder industry may be omitted other. When extrusion exits of a number 3, number 2 kneading extruder gaseous material or a volatile component from a raw material intermediate at least one vent hole are the number process industry. 3: Extruder (number 2 extruder) 20: Barrel 21: Screw 34: Supply opening 36A: discharge port 37, 200: Screw body 54, 101: Conveying parts 56, 57, 84, 85, 105, 107, 110, 111, 112: Flight 60, 86, 115, 162, 172, 182, 203: Passage O1: axis According to one embodiment, an extruder screw includes a screw body. The screw body is rotated about an axis parallel to a direction of conveyance of a raw material. A conveyance portion having a flight is provided on the outer peripheral surface of the screw body. The flight is configured to convey the raw material along the axis of the screw body when the screw body is rotated. A passage for permitting the raw material fed by the flight to pass therethrough to the outer peripheral surface of the screw body is provided in the screw body in a position deviated from the axis of the screw body. While kneading extruder screw as raw material transfer, the transfer direction of the raw material along with straight axis, its axis and rotating screw body, said screw body and along the circumferential direction of the outer, raw material upon rotation of said screw body in an axial direction of said screw body having carrying flight guided, said screw body and along the circumferential direction of the outer, said flight number valve timing of the flow of the material carried by the raw material pressure height barrier portion and, said screw installed in the main and, by means of a barrier portion said enhanced with raw material is introduced, the introduced raw material passing through the outer periphery of said screw body and positioned in the passage, said screw body, said passage having a wall surface defining a shape of the hole constituting, said wall surface on the axis of said screw body around said axis to achieve an eccentrically with respect to the installed position, extruder screw. Back number According to Claim 1, screw body flowing refrigerant for cooling said cooling medium flow path outlet, extruder screw. According to Claim 1, said passages, said outer peripheral surface of said screw body having an inlet and an outlet opening, said inlet and said outlet, spaced apart from each other in the axial direction of said screw body and can, said outer peripheral surface of said screw body from an inlet to said passage with a predetermined length from said raw material is returned from the outlet of the, extruder screw. According to Claim 4, said barrier portion immediately before said passage said inlet located, extruder screw. According to Claim 4, said passages, said inlet and said outlet in communication with the passage body has, said passage body smaller than the diameter of the diameter of the inlet, extruder screw. As screw extruder continuously blending raw material transfer, the transfer direction of the raw material having a straight axis along, its axis and rotating screw body, said screw body and along the circumferential direction of the outer, raw material upon rotation of said screw body and carrying the guided flight having an axial direction of the screw body, said screw installed in the main and, raw material is introduced being carried by said flight with, the introduced raw material is returned to the outer peripheral surface of said screw body comprising a plurality of passages passing through, said plurality of passages, at an angular position offset from the axis of said screw body in the axial direction of said screw body arranged in said spacing, extruder screw. Back number According to Claim 7, screw body flowing refrigerant for cooling said cooling medium flow path outlet, extruder screw. Number 1 with a screw anti or anti number 7, its screw to circulate generating extruder as plasticizer soul [lyen it will ask, barrel and said screw is rotatably housed, said means is disposed in the barrel, said screw for supplying a raw material inlet, said barrel being provided, said extruded soul [lyen water with an ejection opening of the extruder. Barrel screw rotating inside a raw material is supplied, said raw material in an axial direction of an outer circumferential surface of said screw formed using continuous vertical flight with said screw, said screw being carried by said outer peripheral surface barrier by flight number by said pressure increasing valve timing of the flow of raw material, said screw upon rotation, said screw and said screw may follow in the lost motion path for said barrier portion by means of said screw with enhanced introducing raw material from the outer peripheral surface, the outer peripheral surface of said screw through said material to said extrusion method is returned. Back number
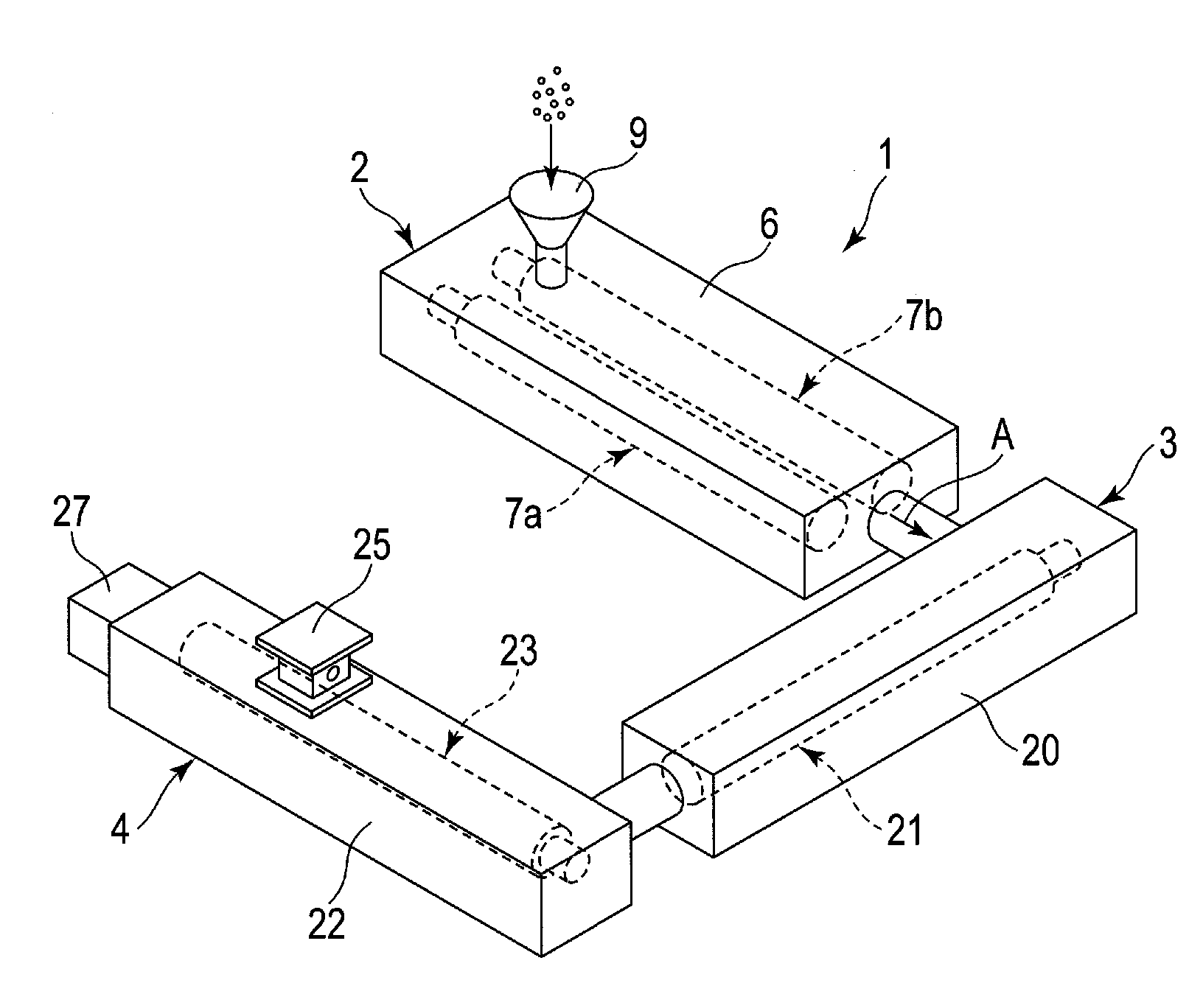
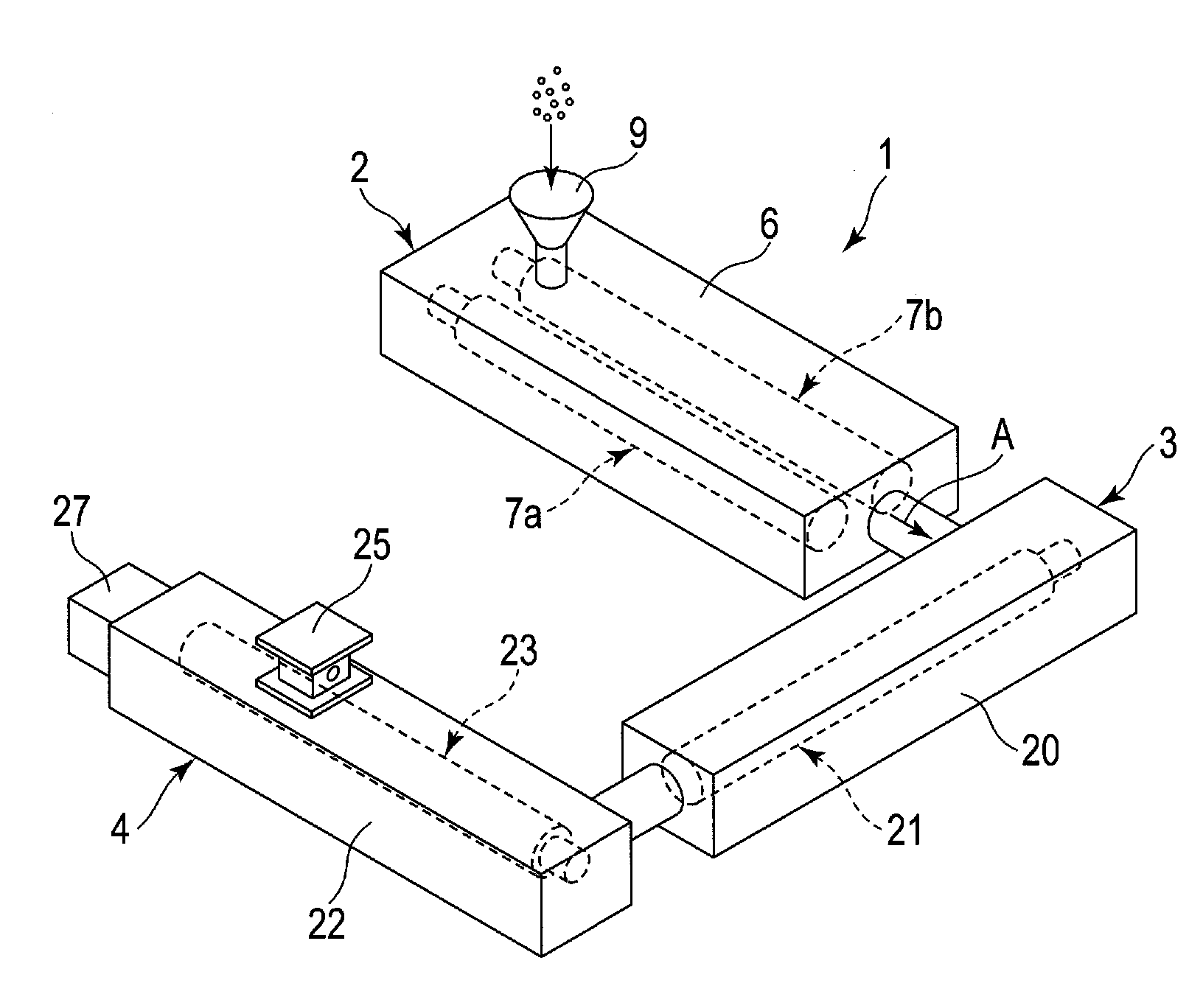
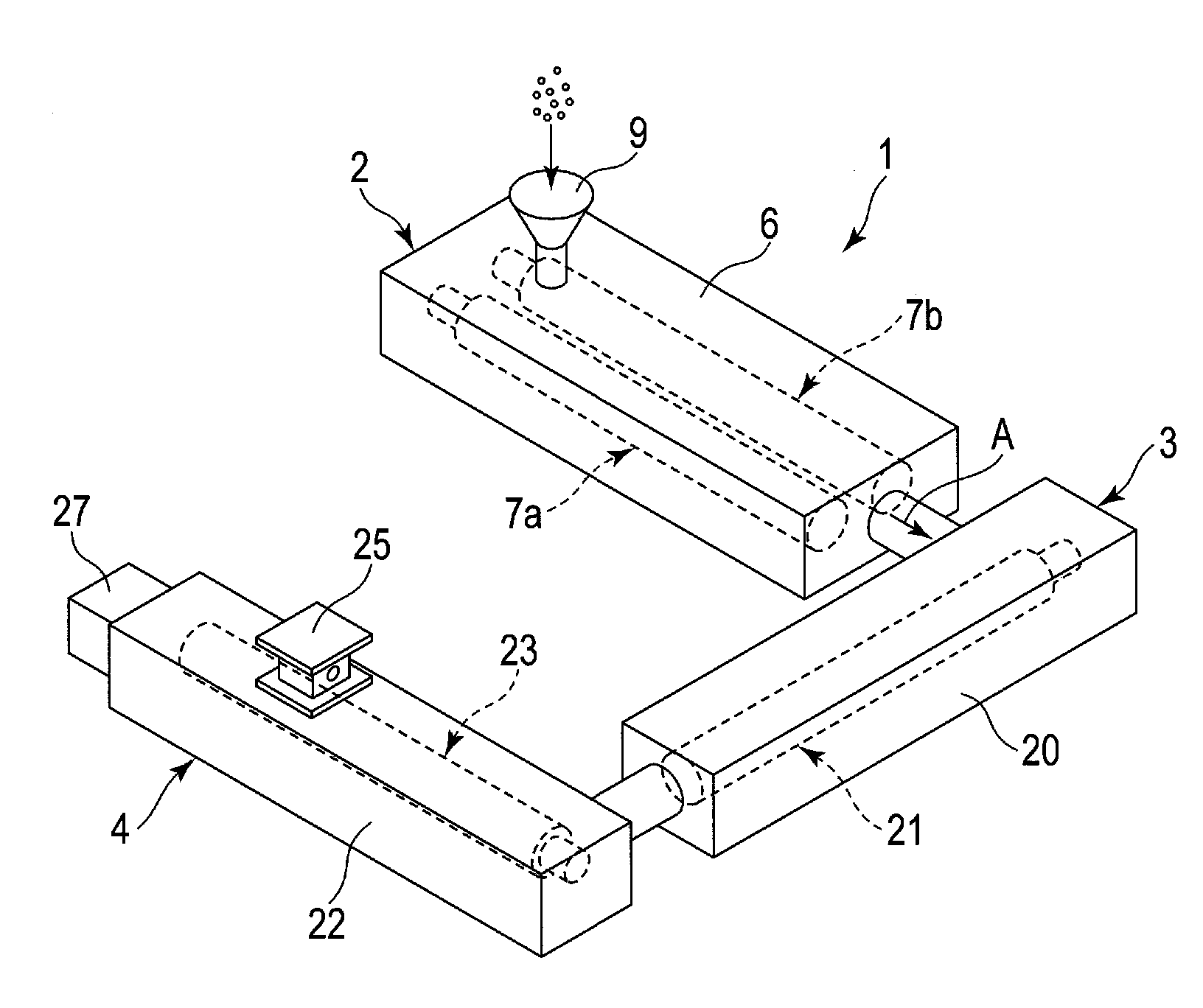
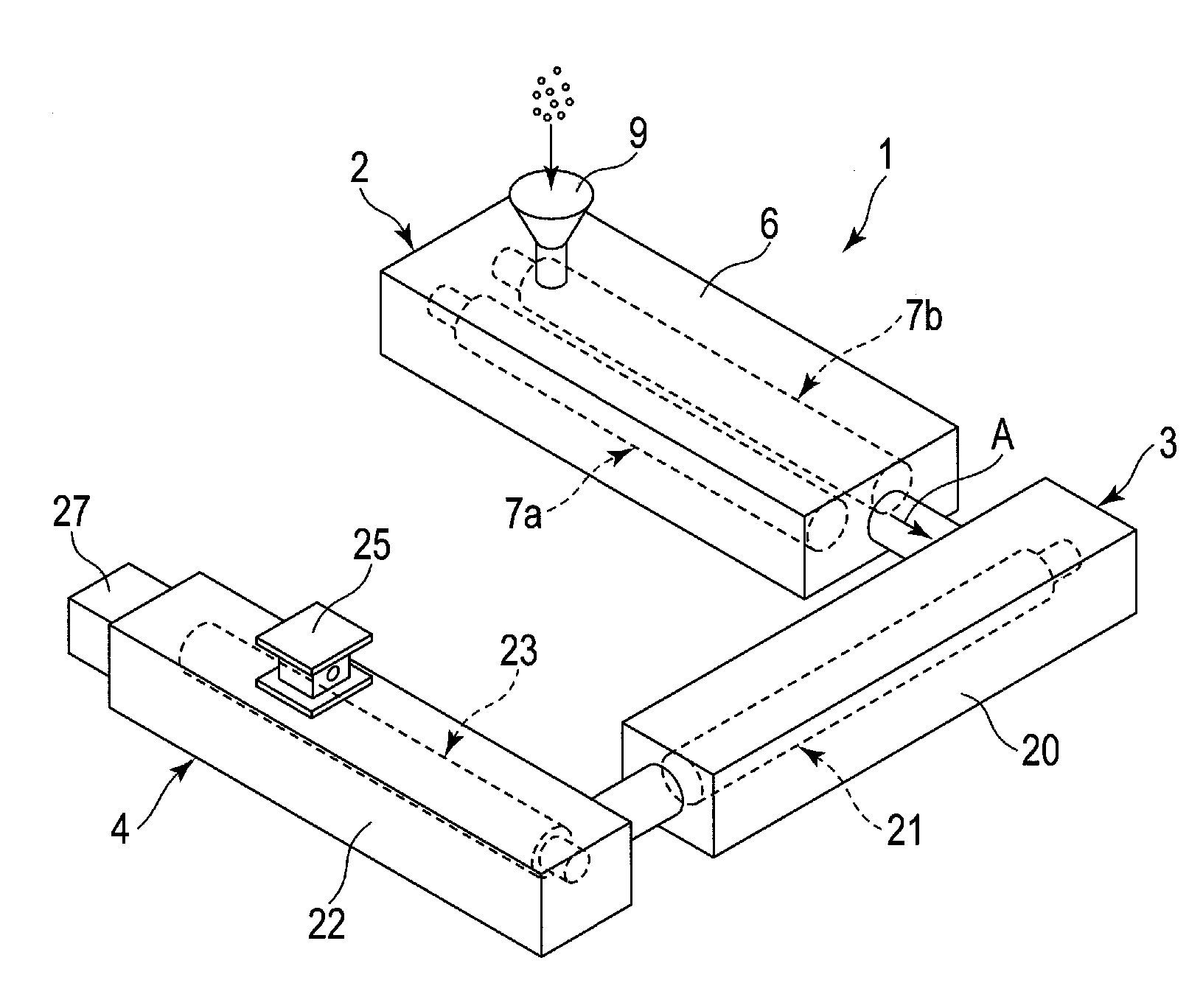
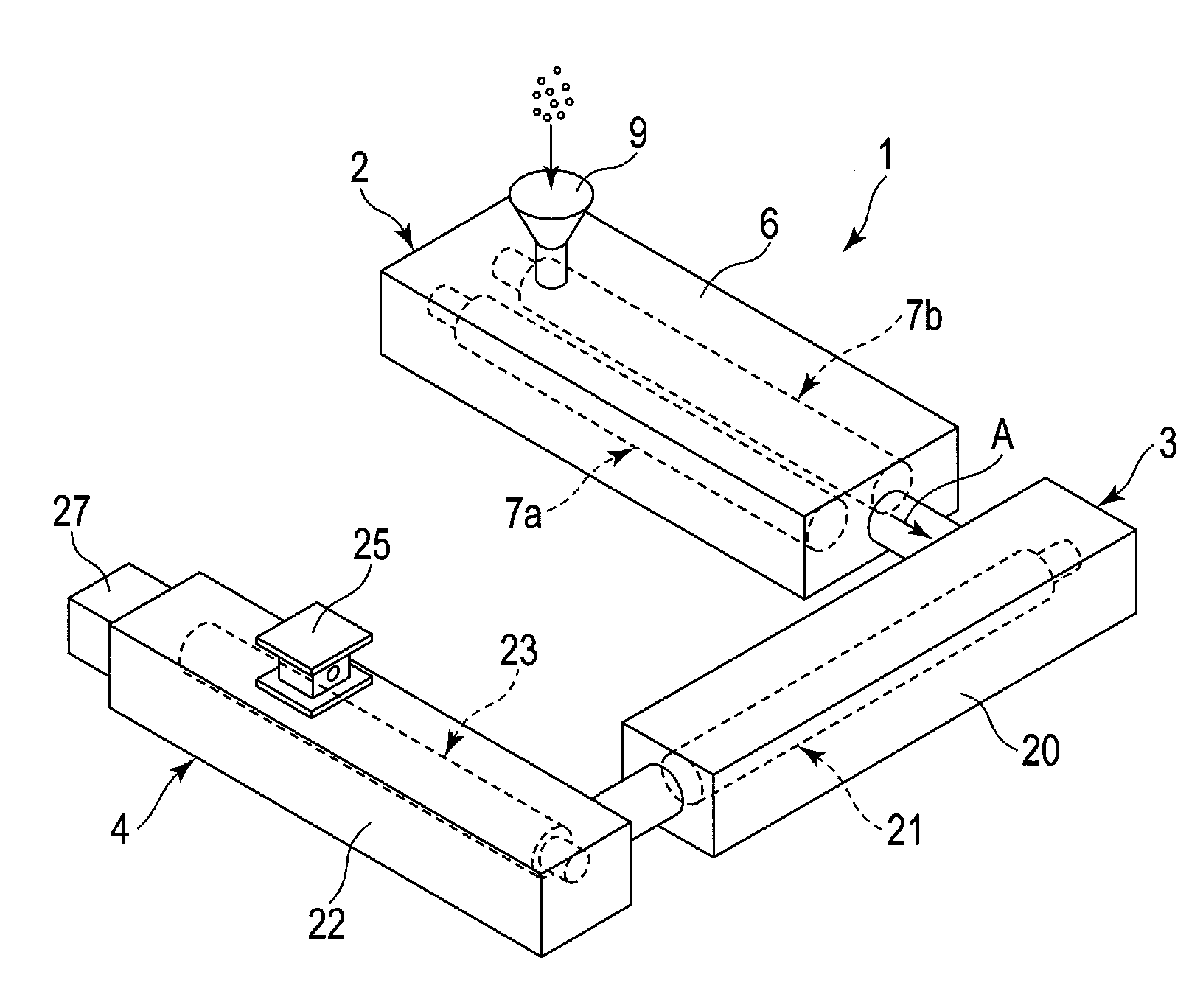
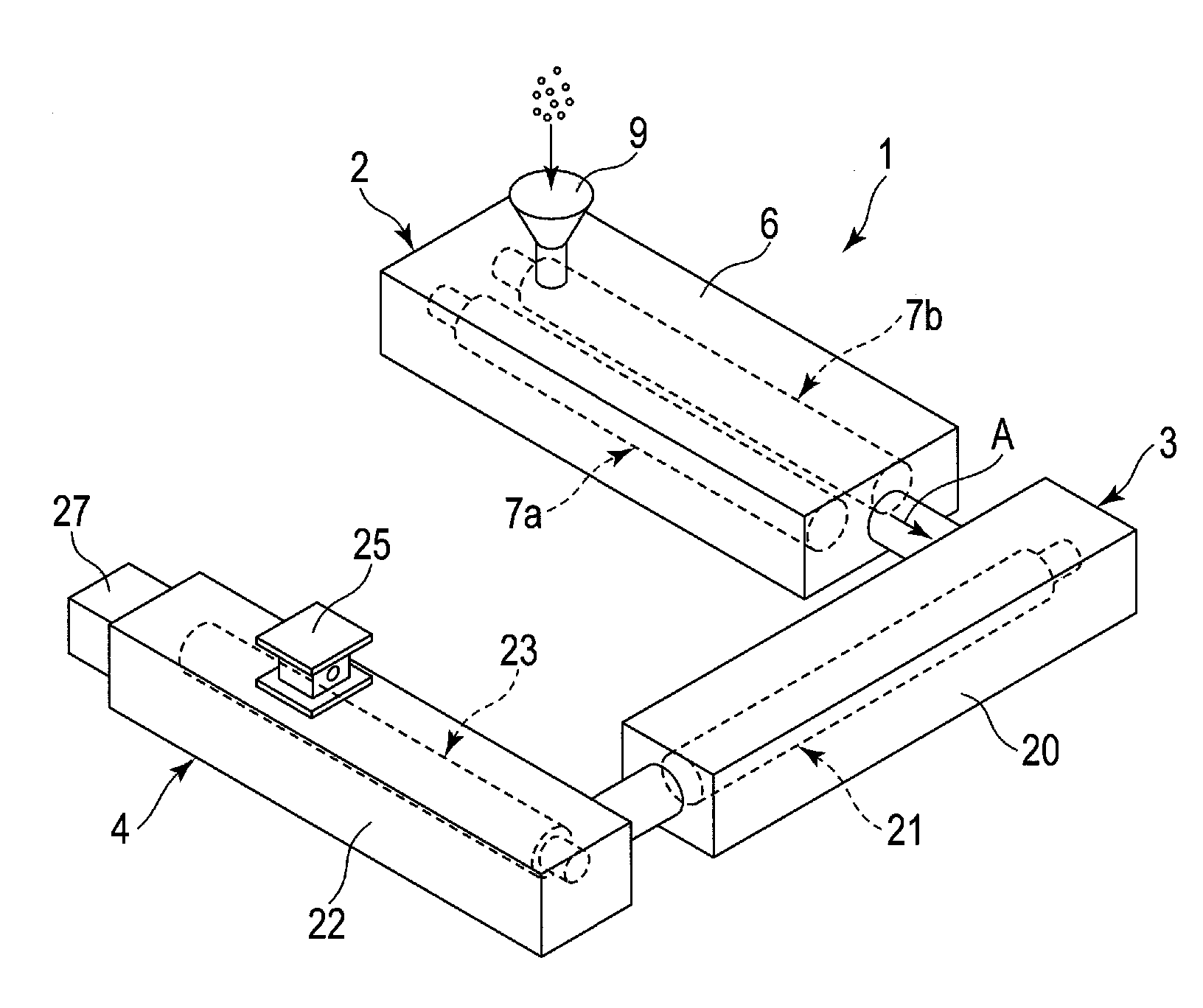
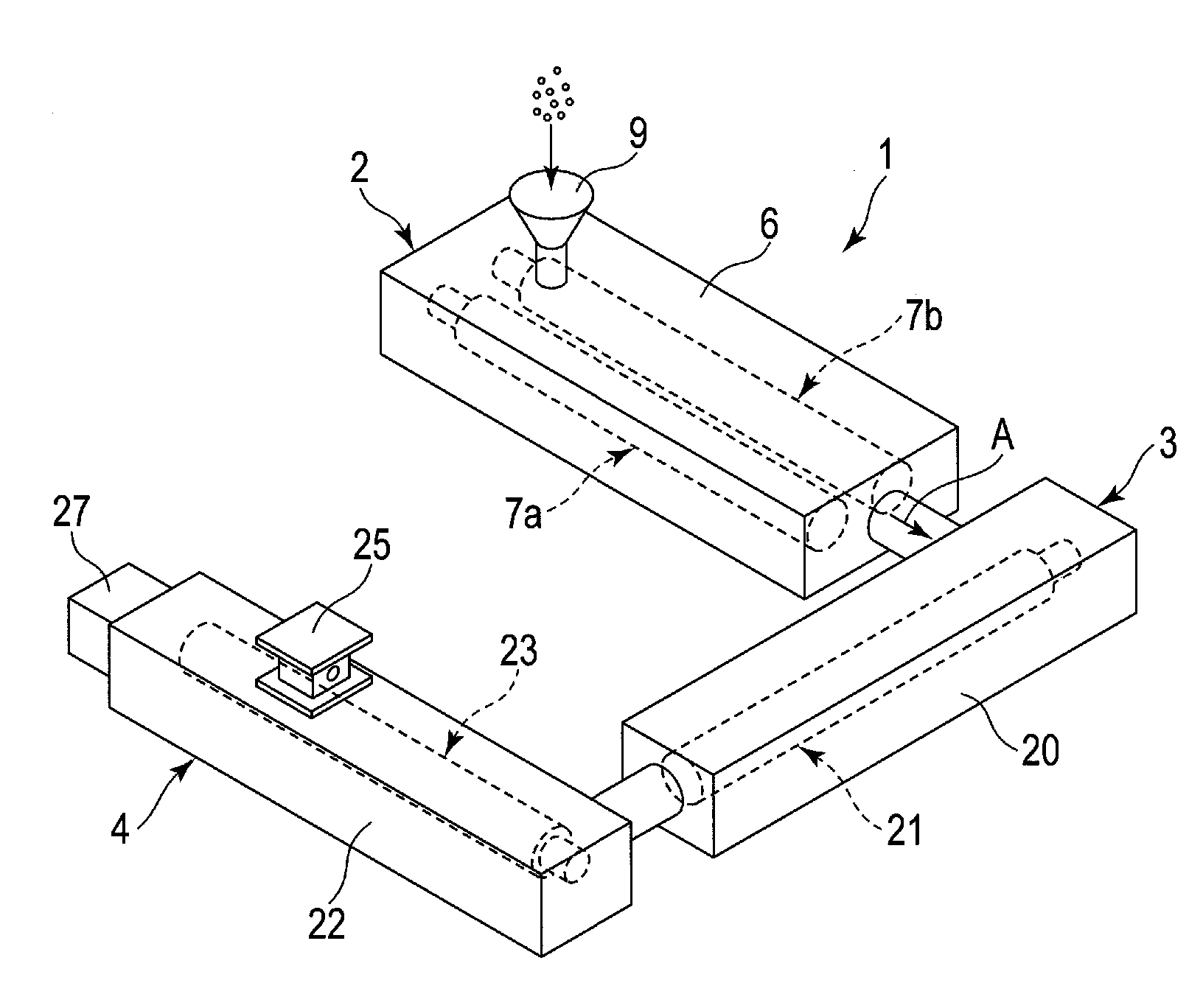
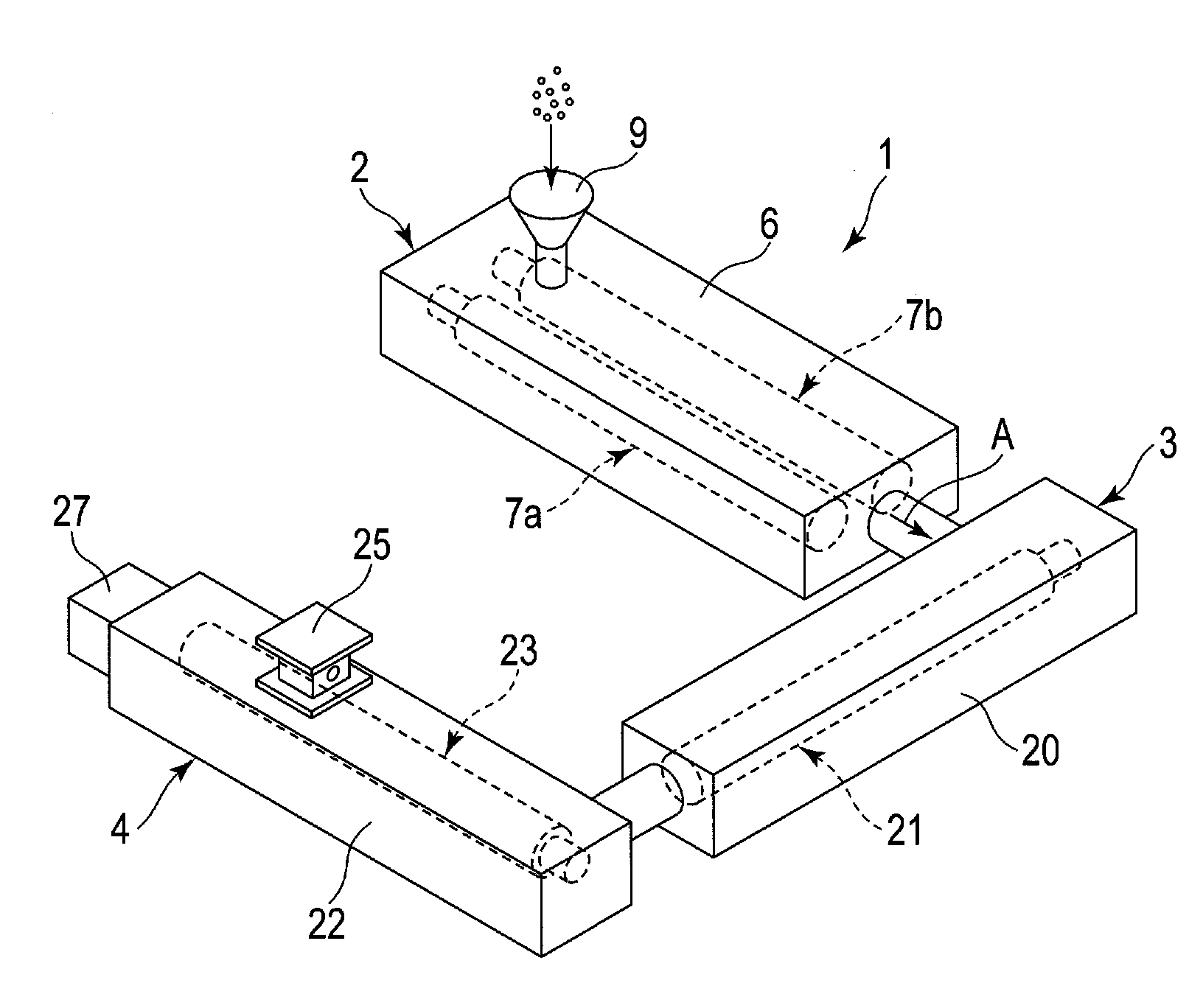
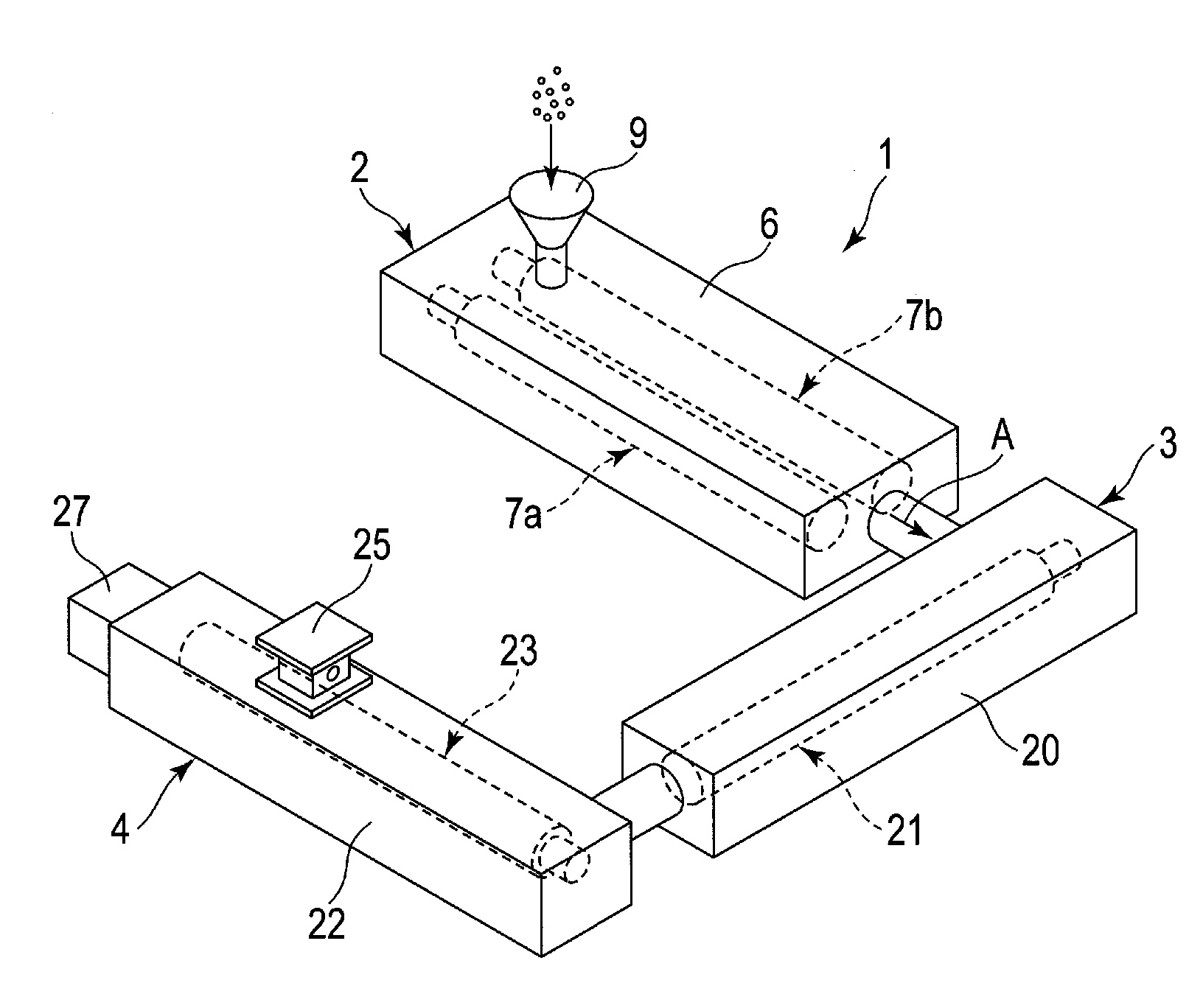
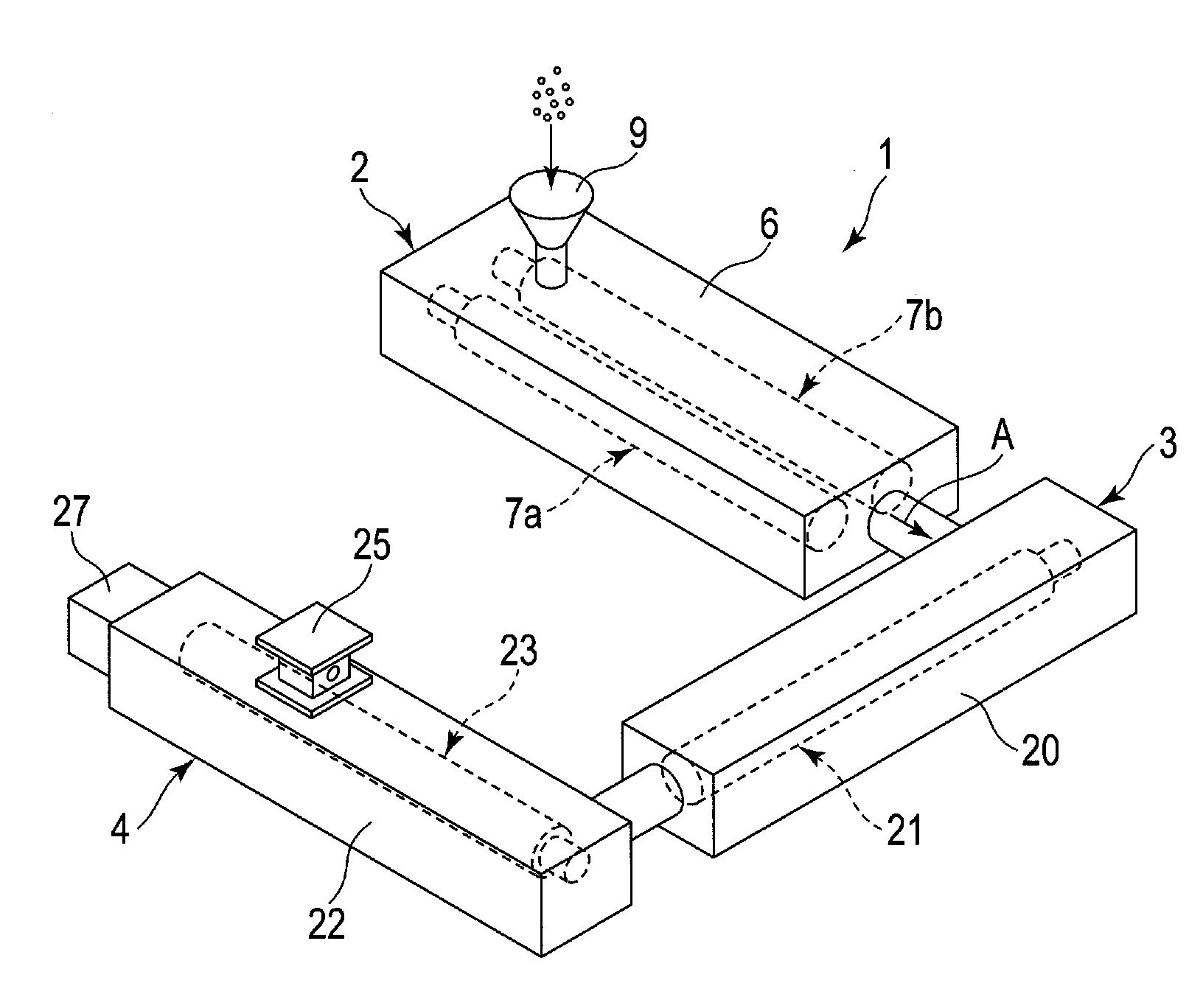
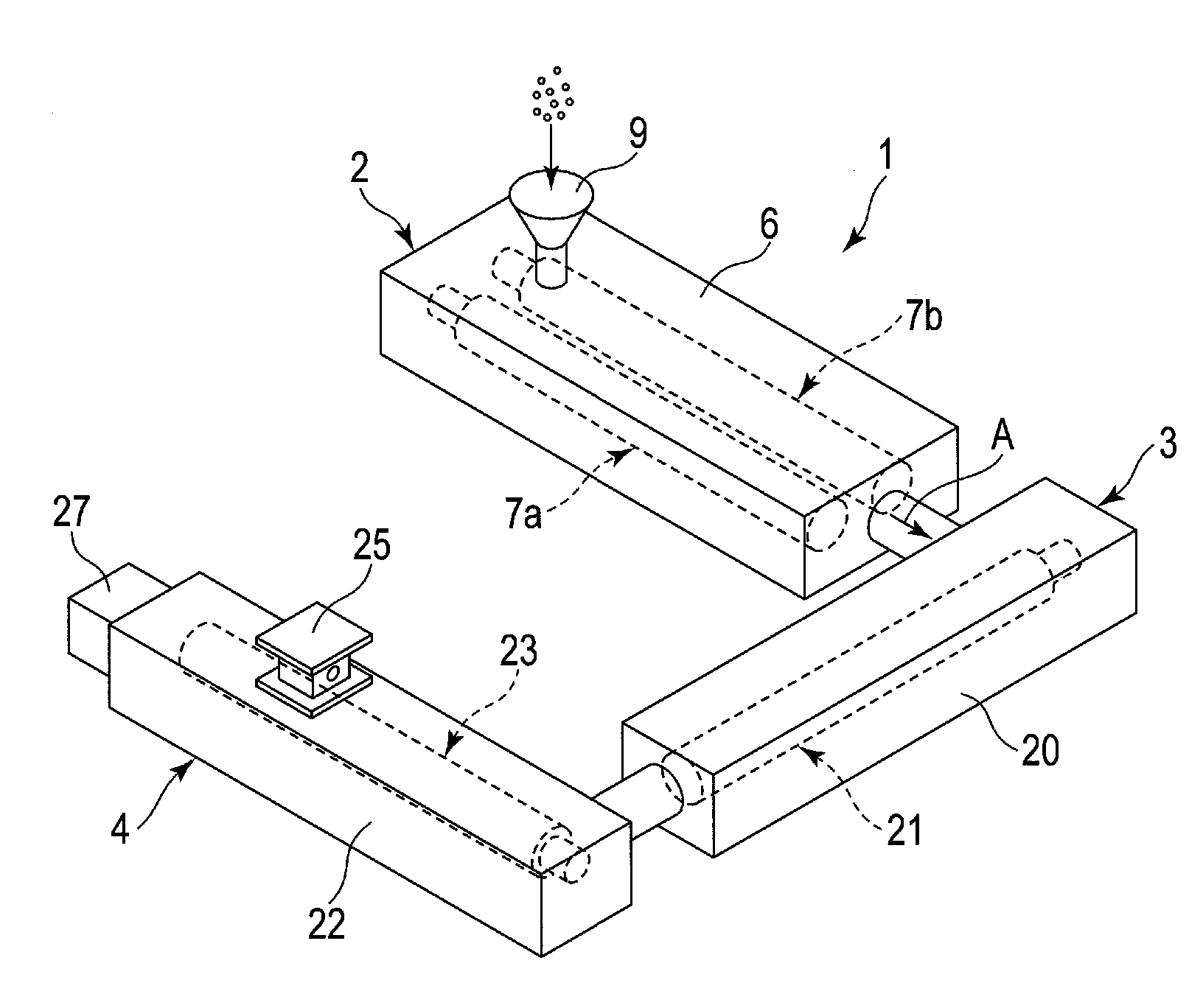
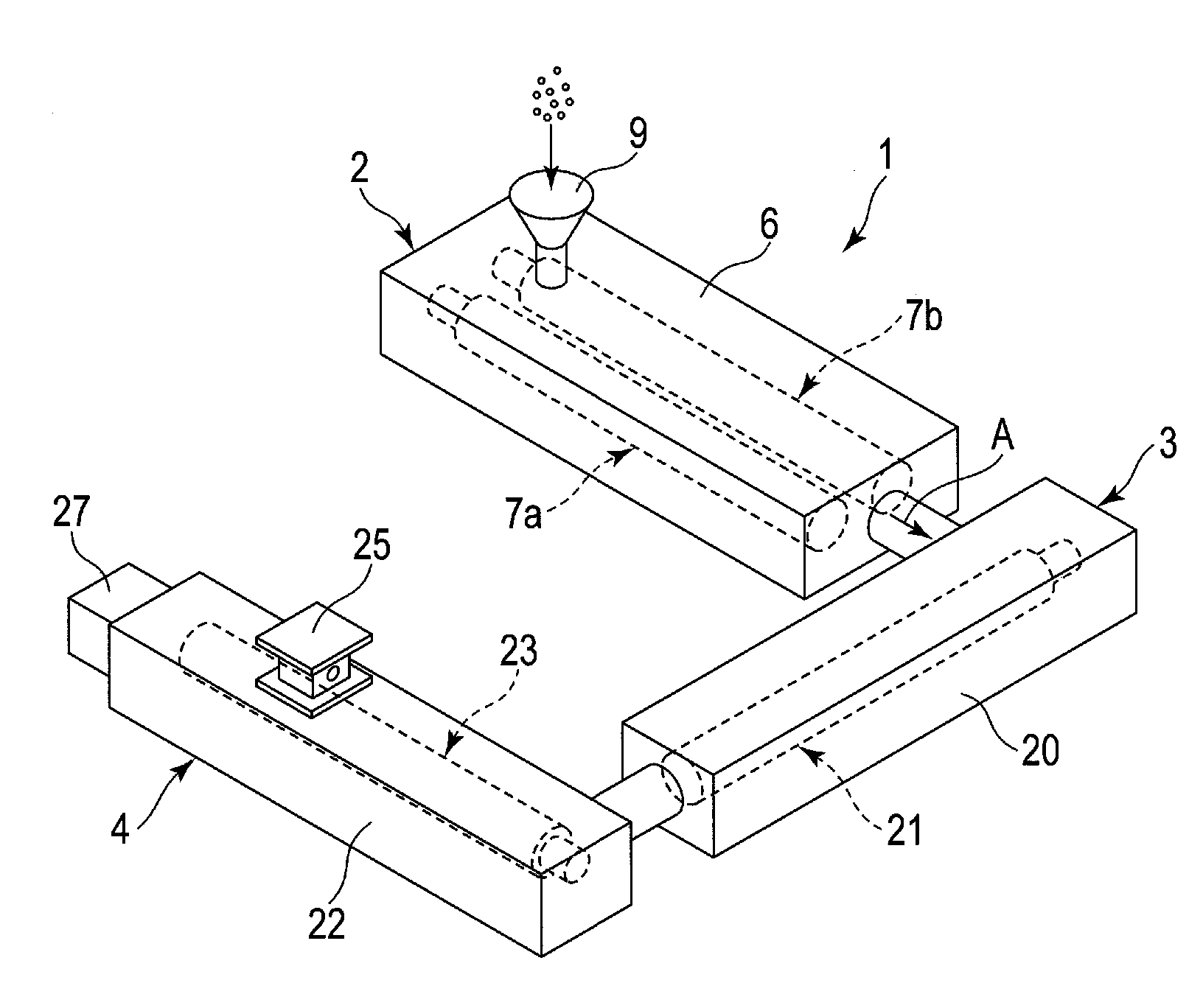
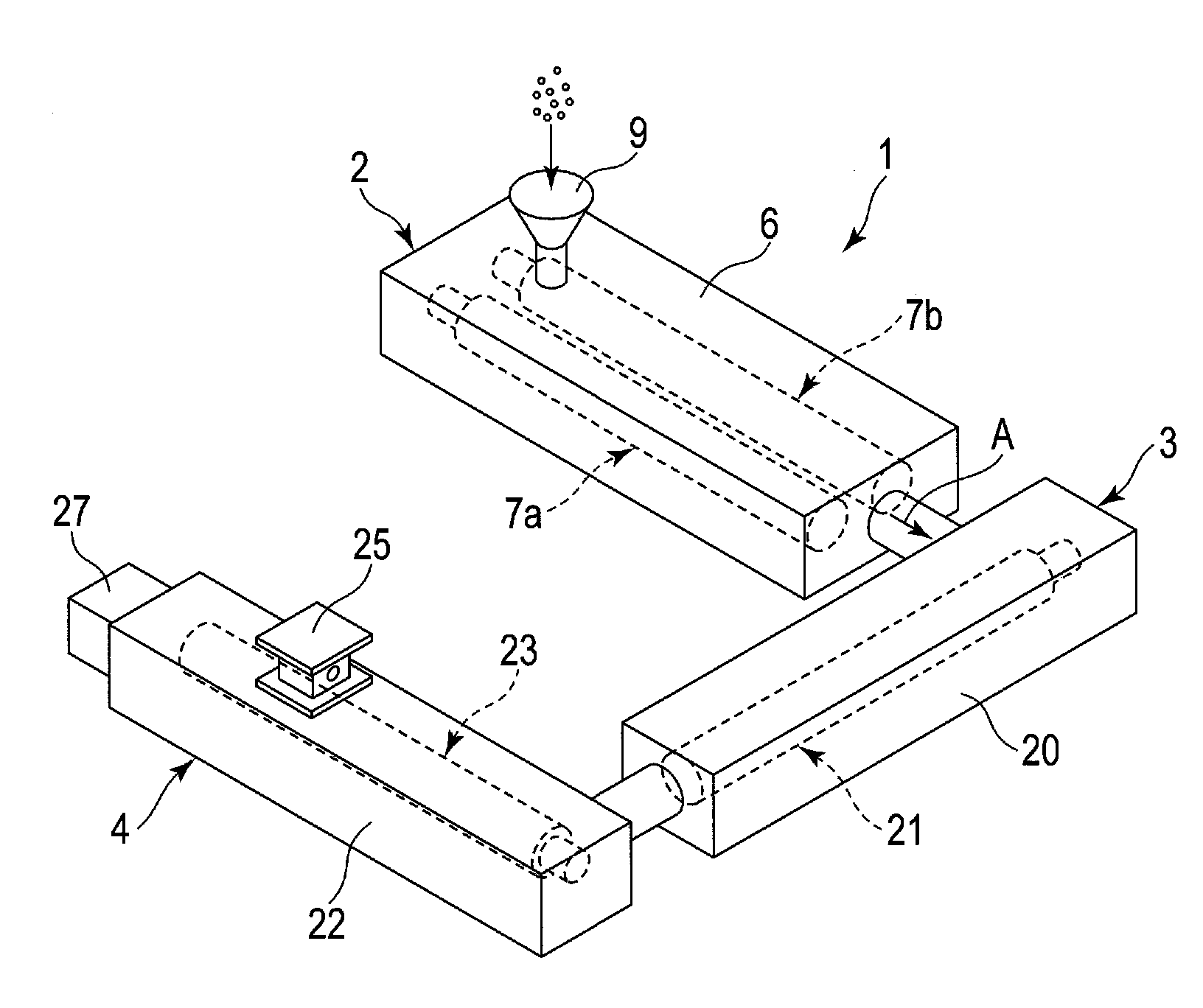


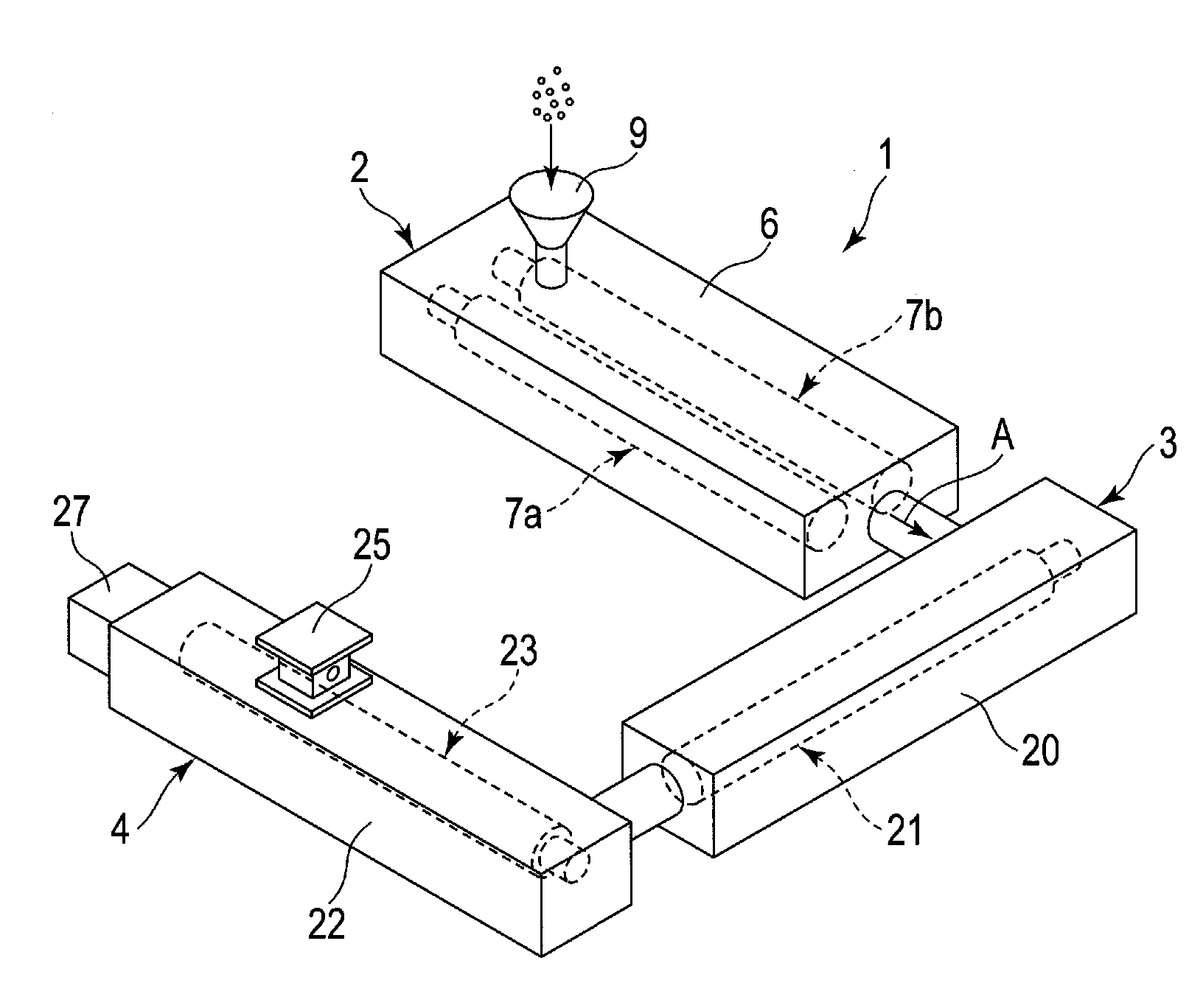
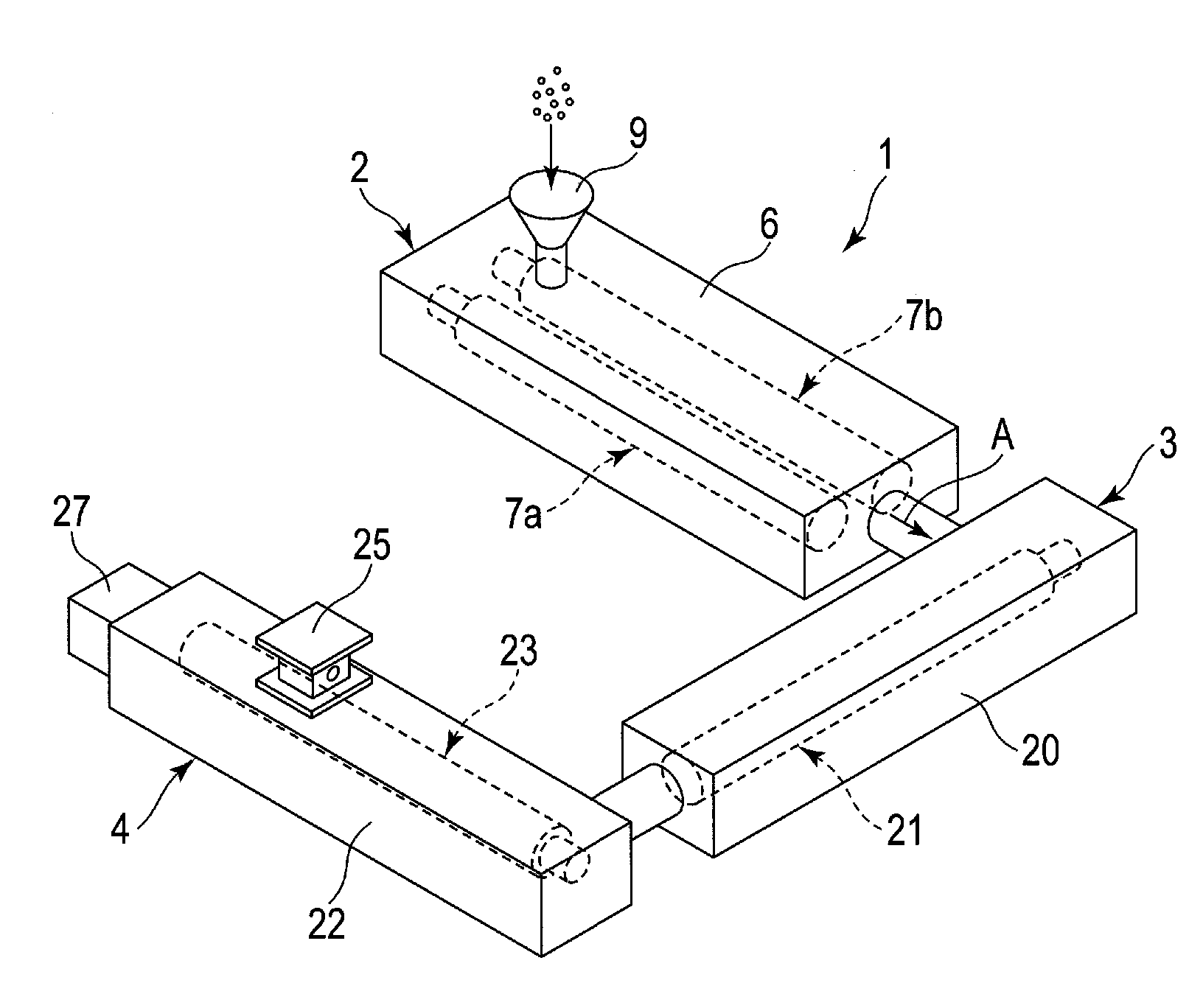

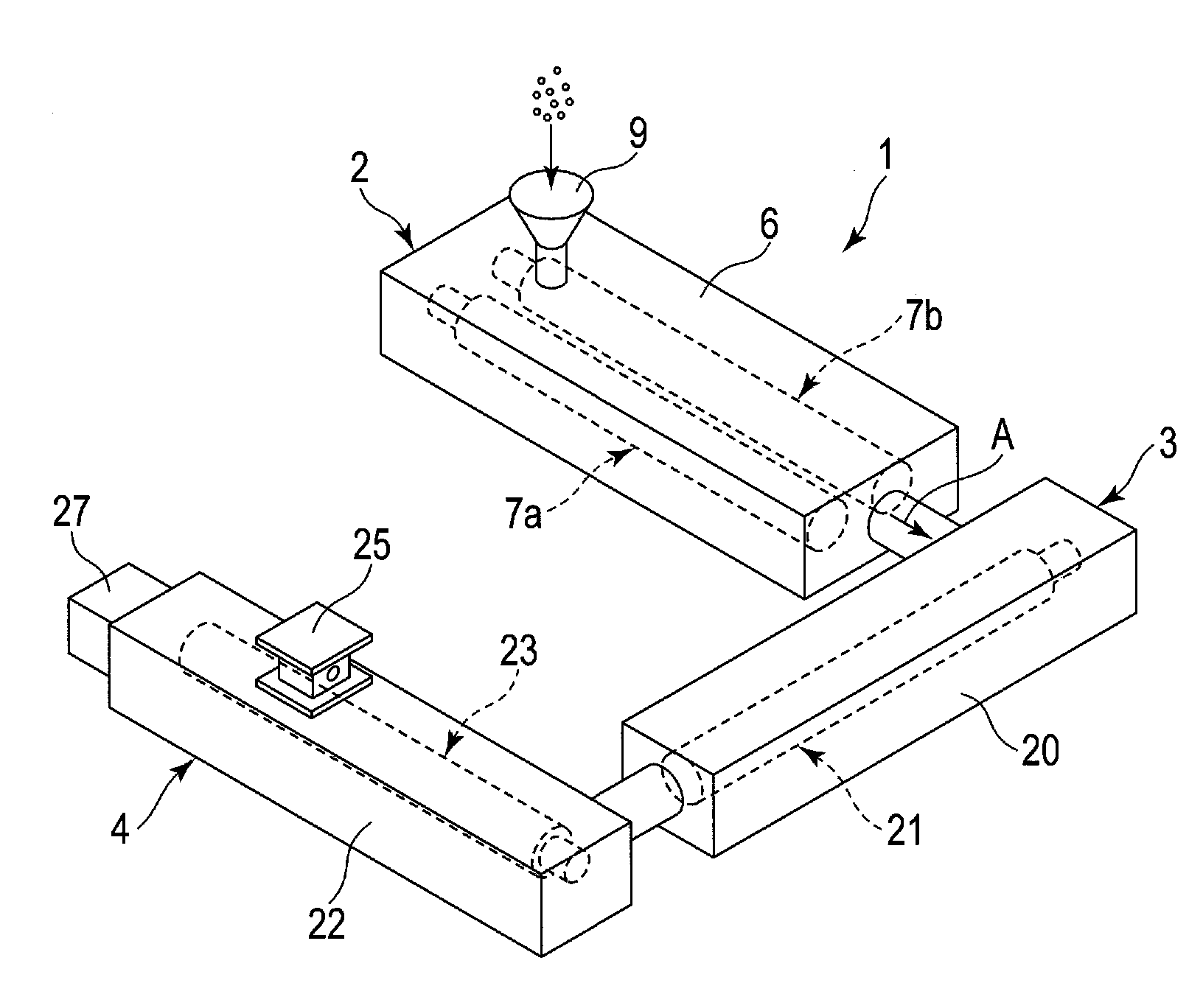
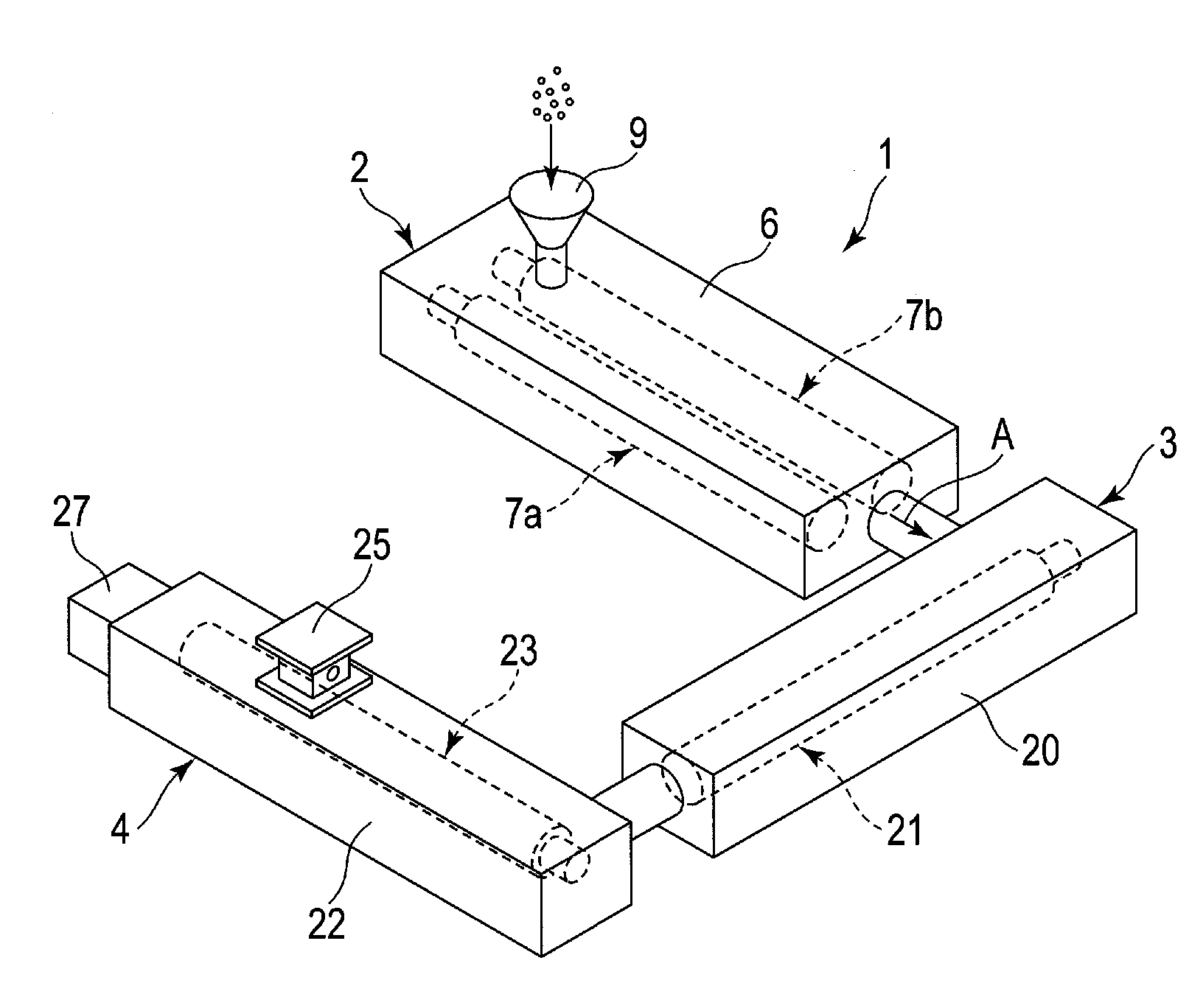
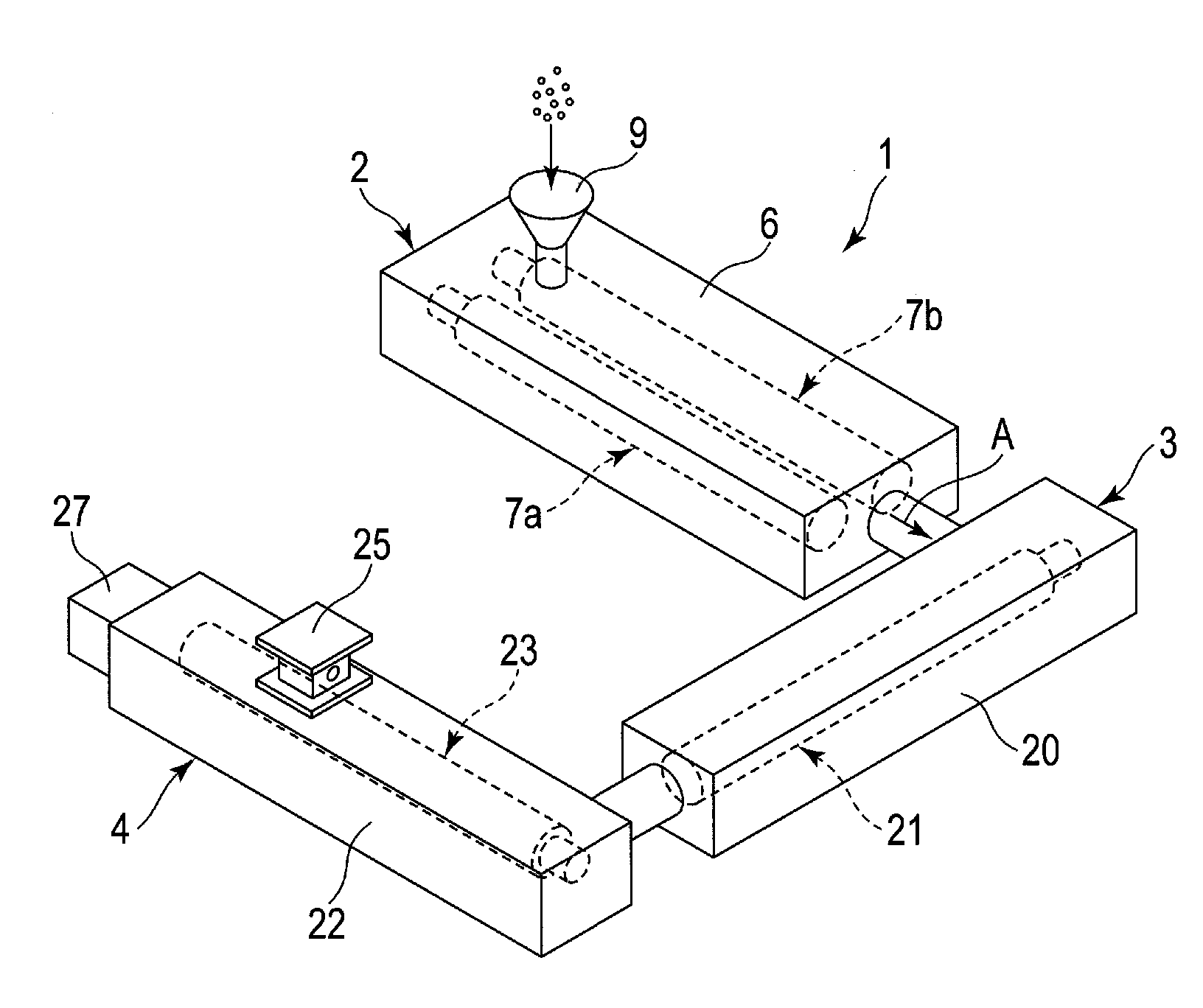
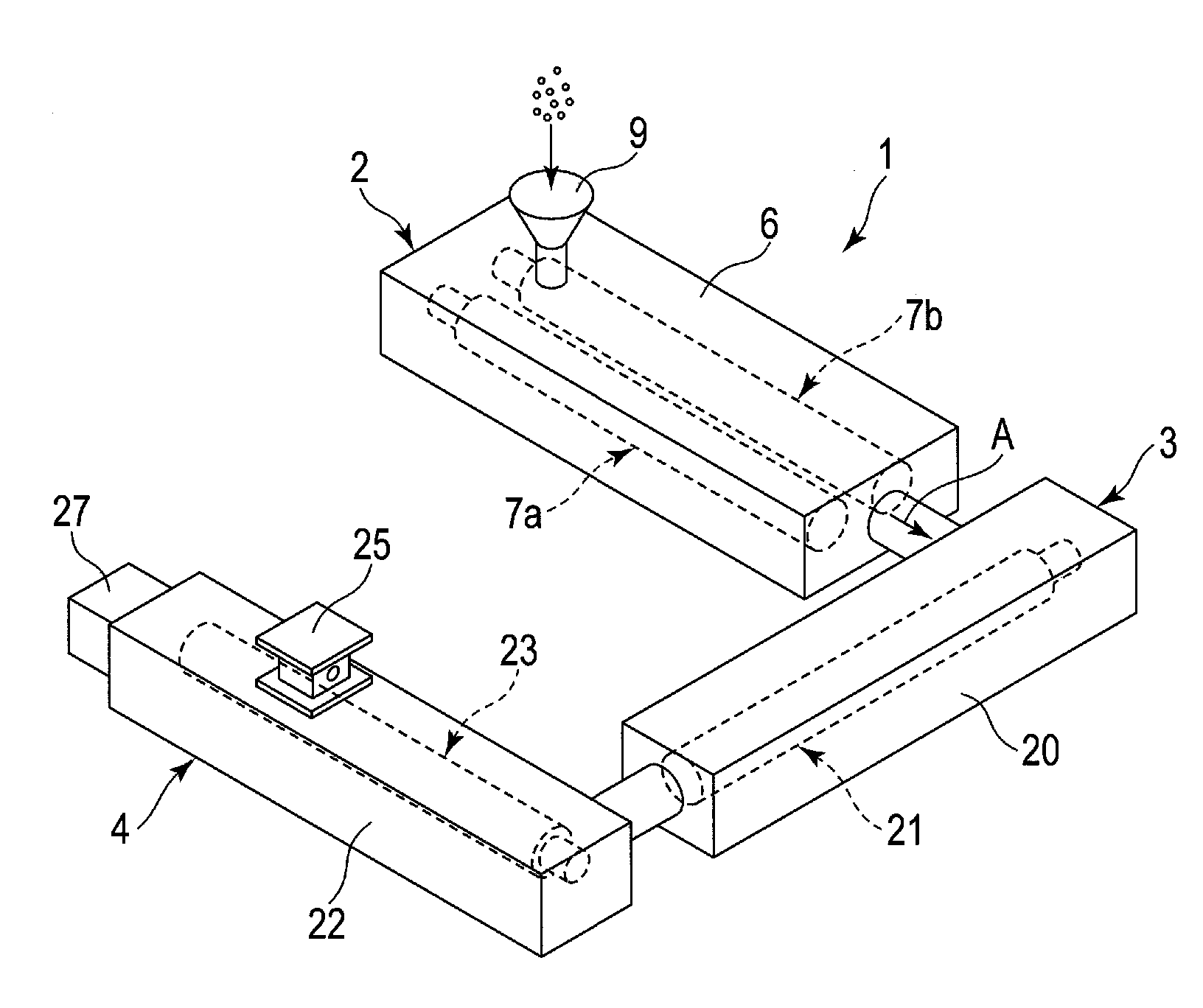
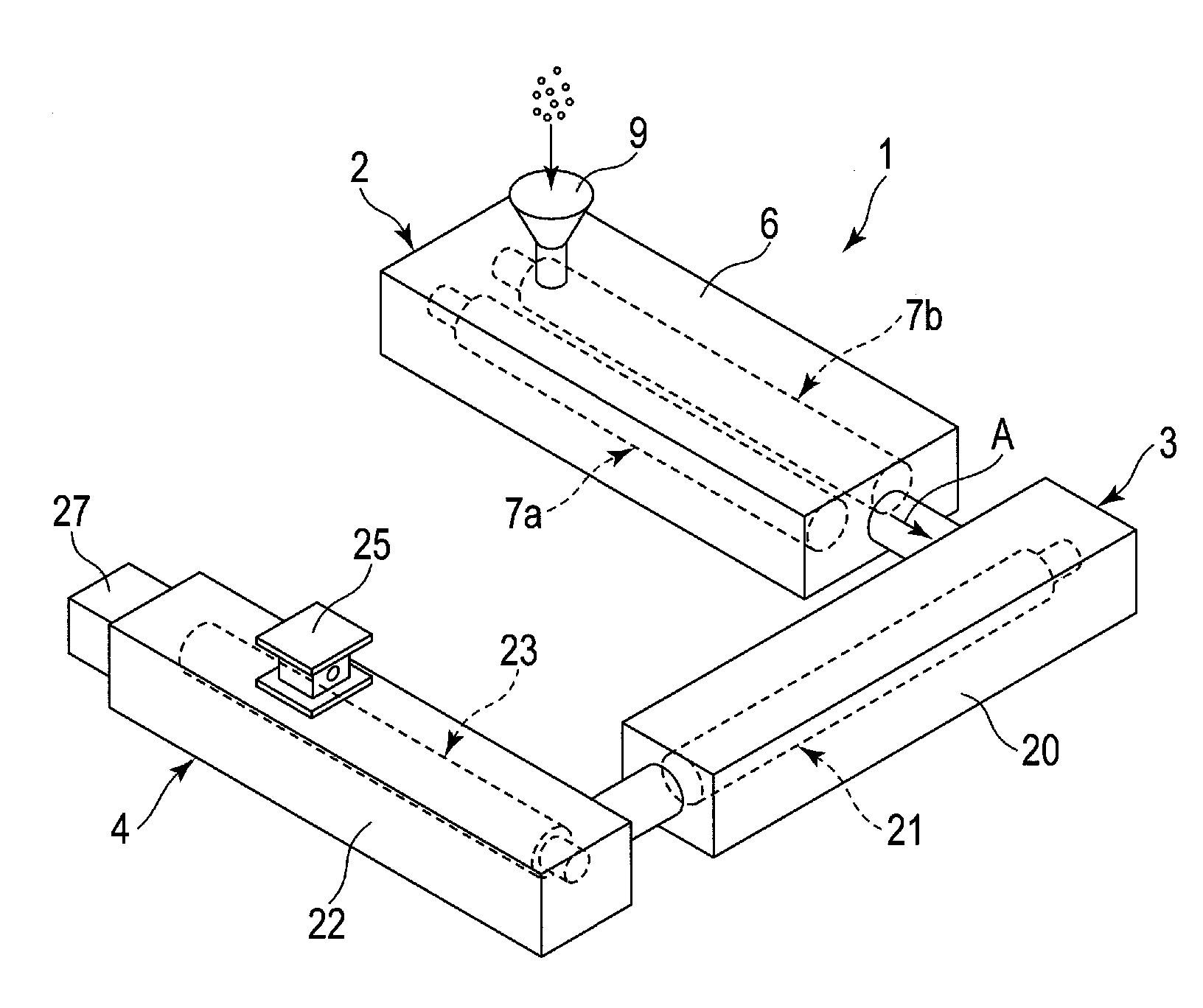
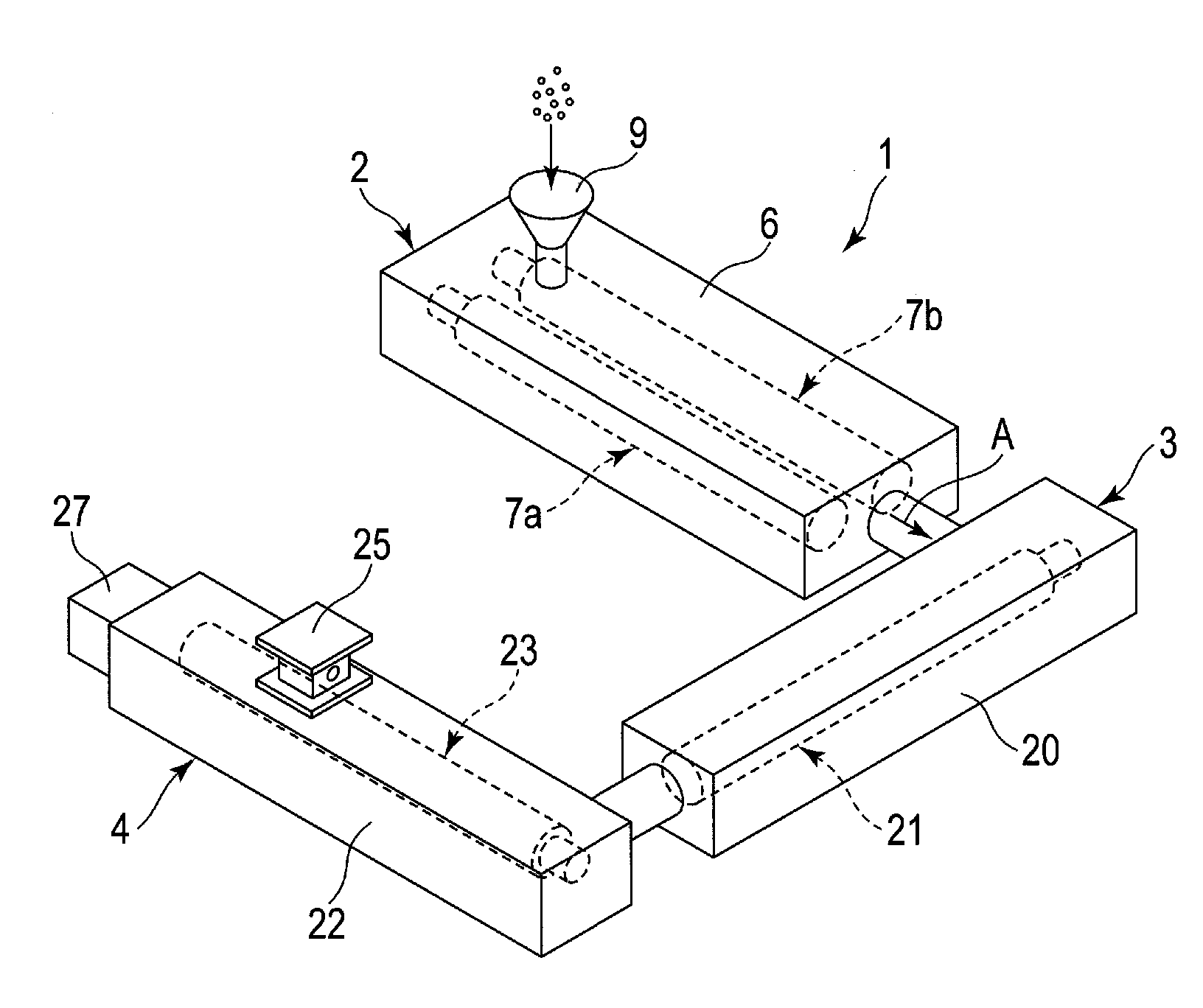
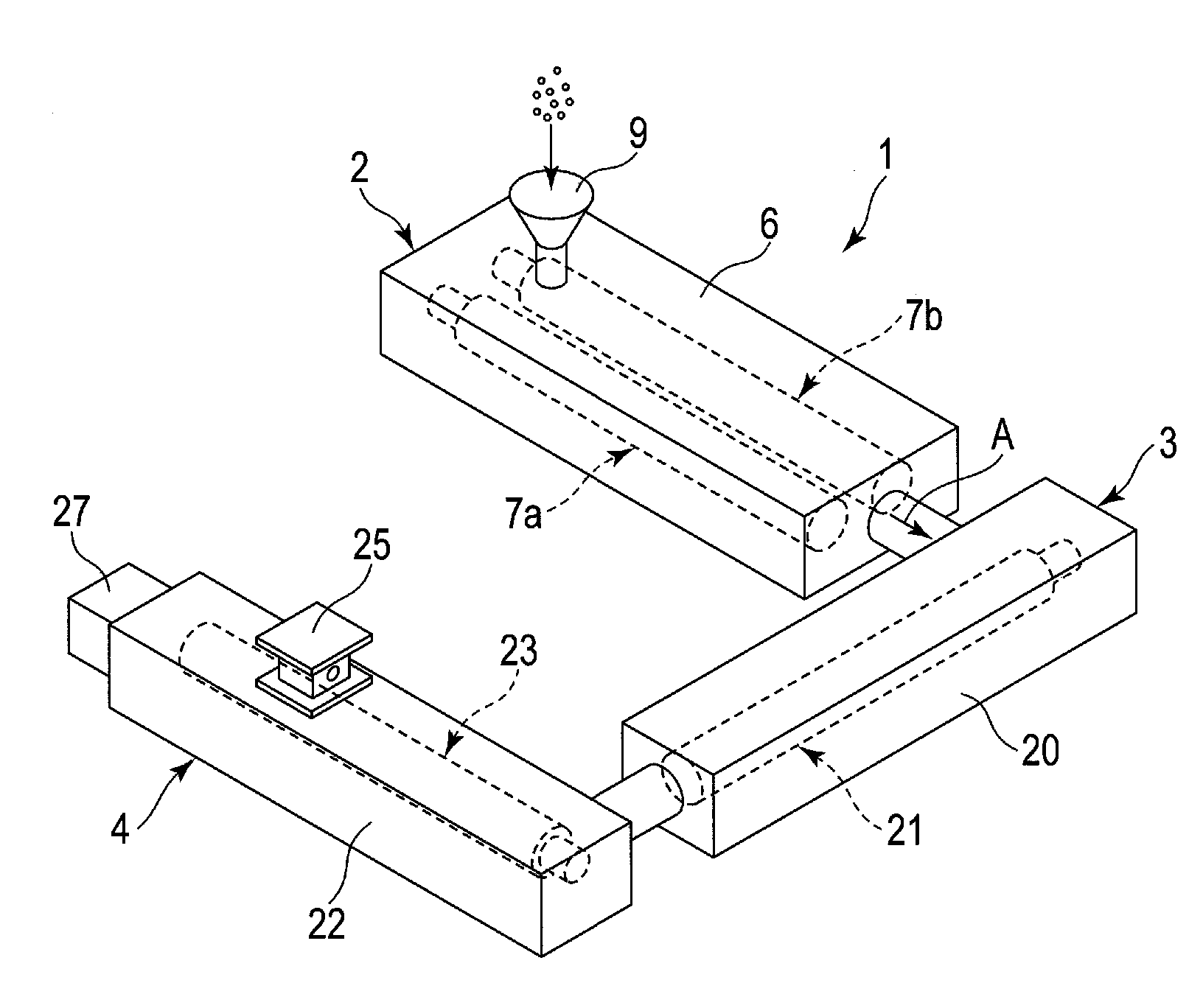
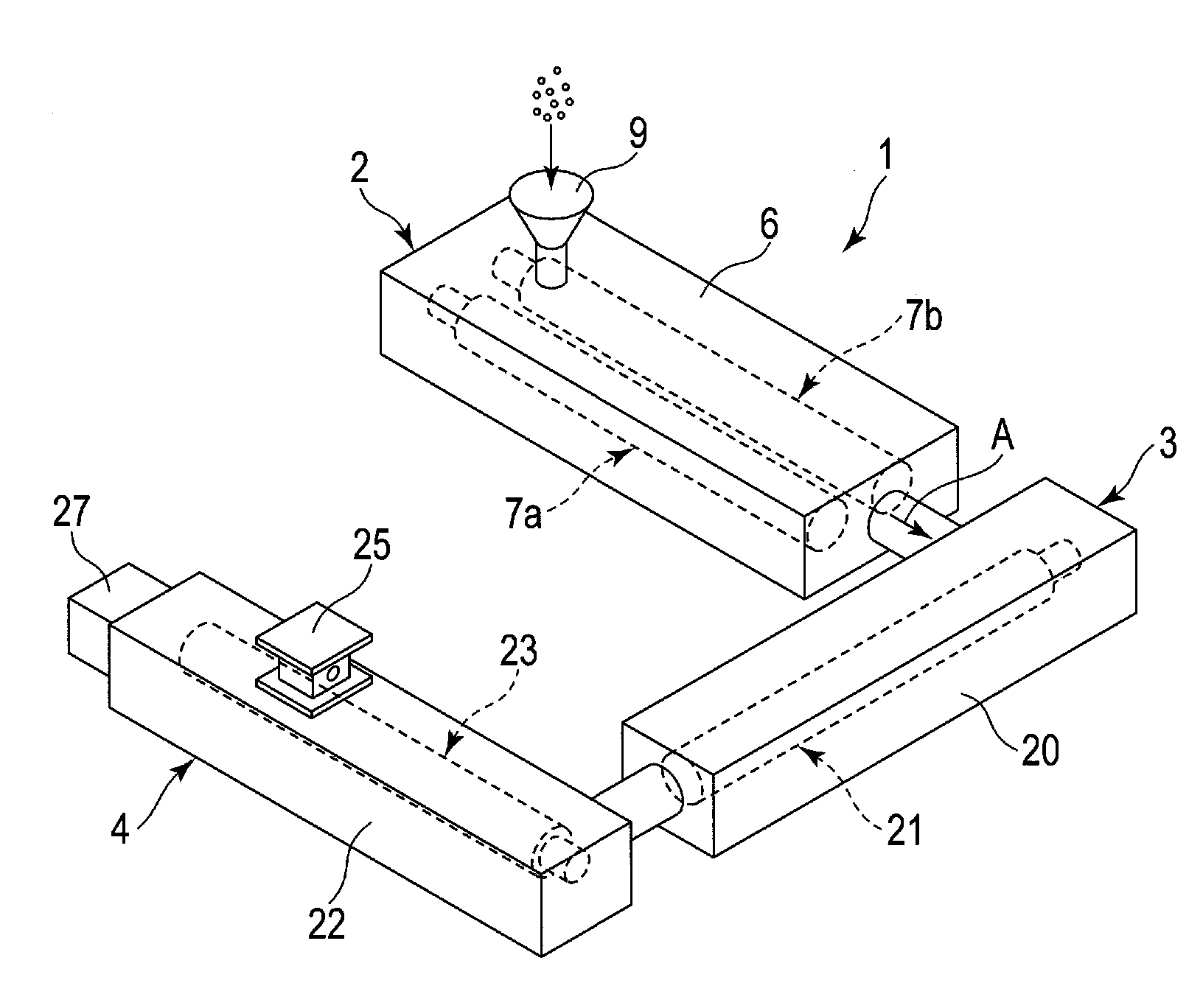
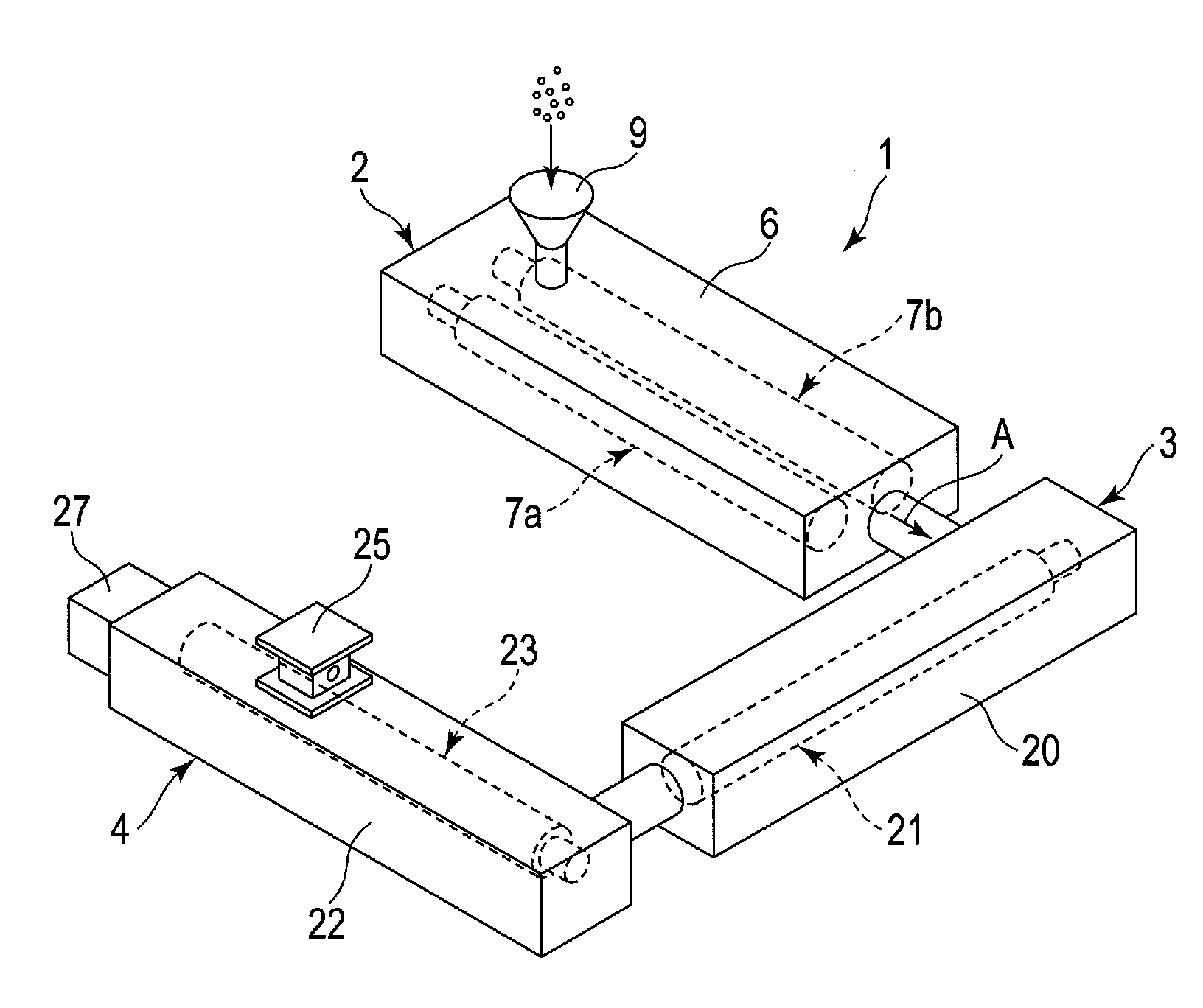
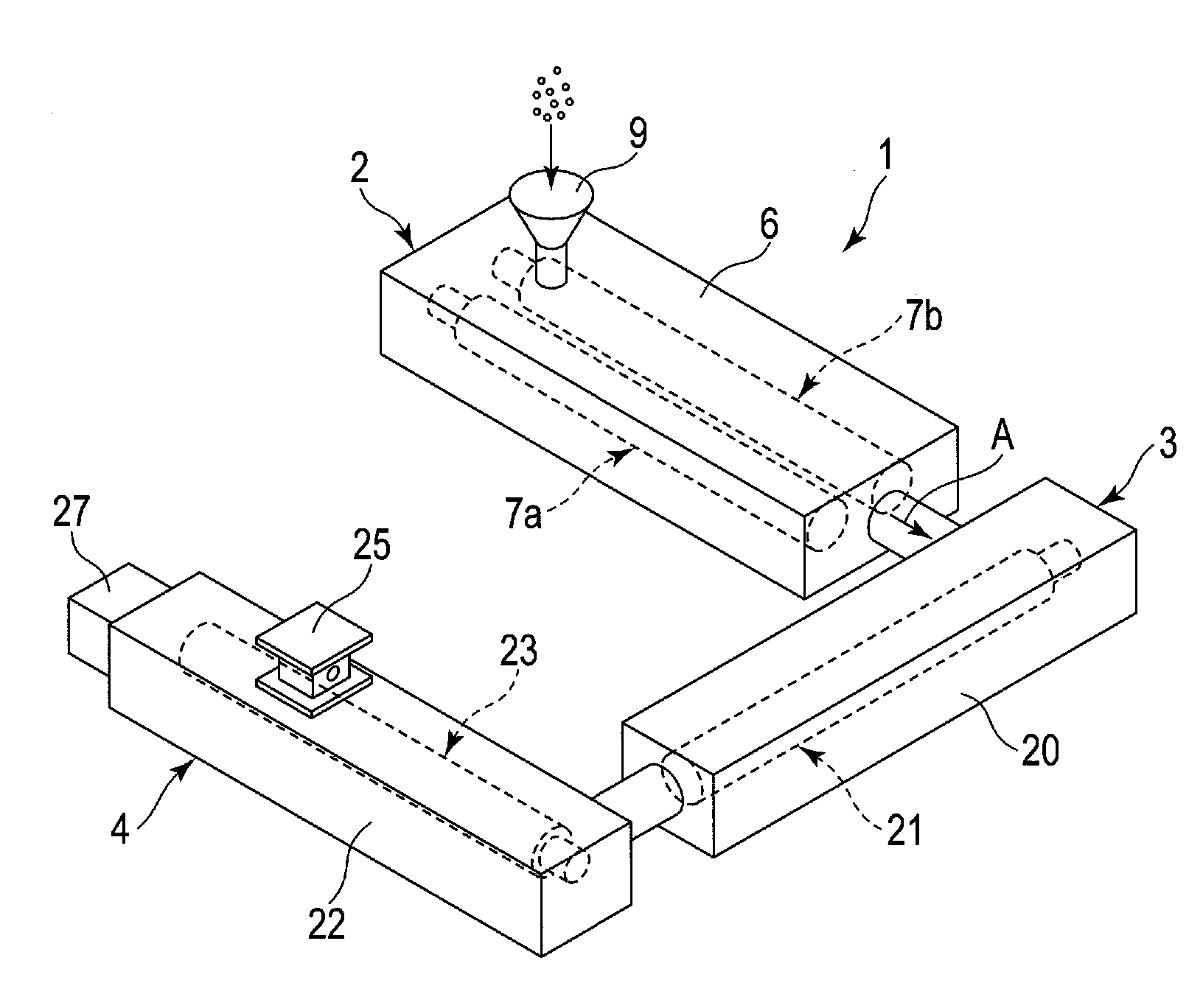
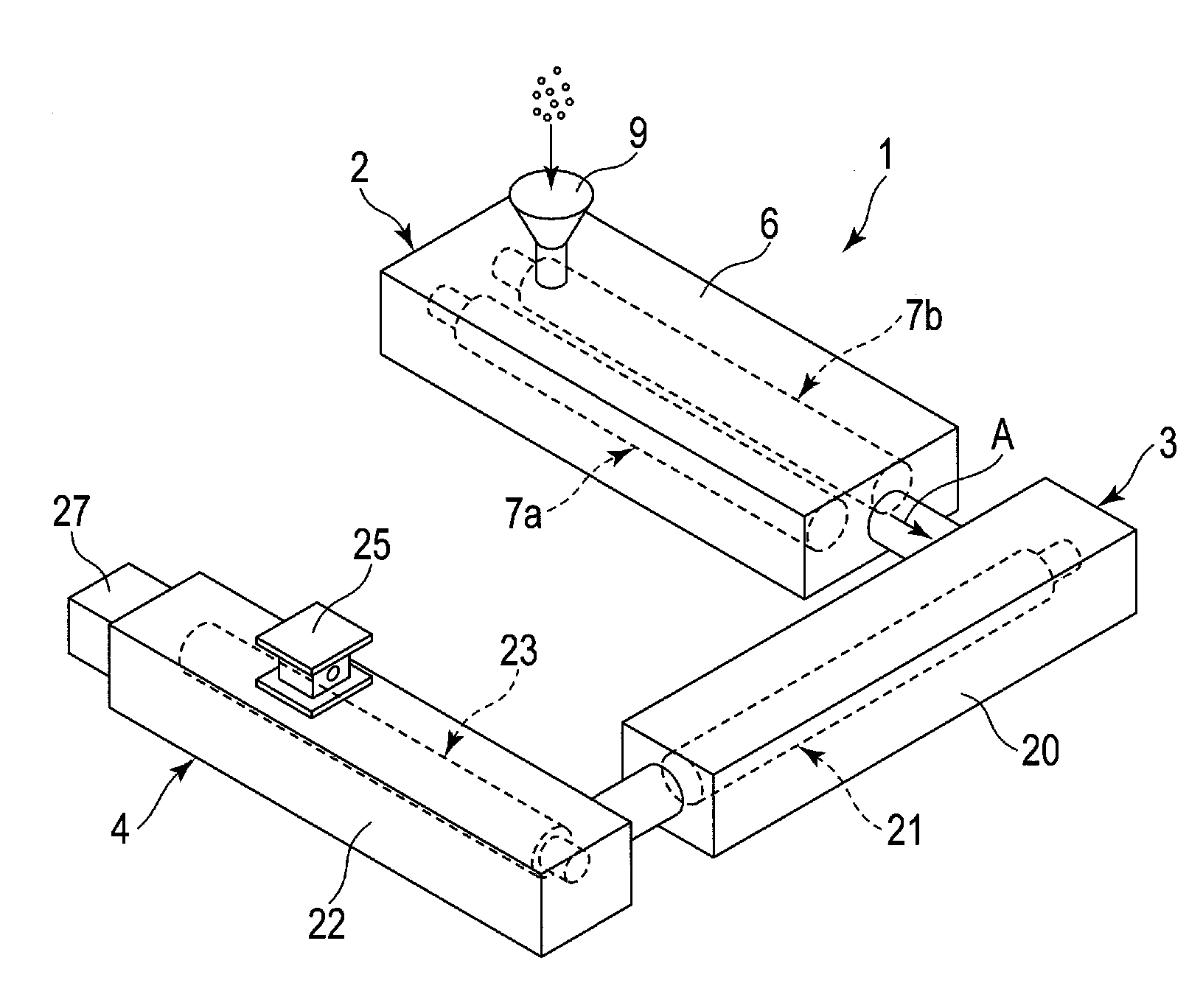
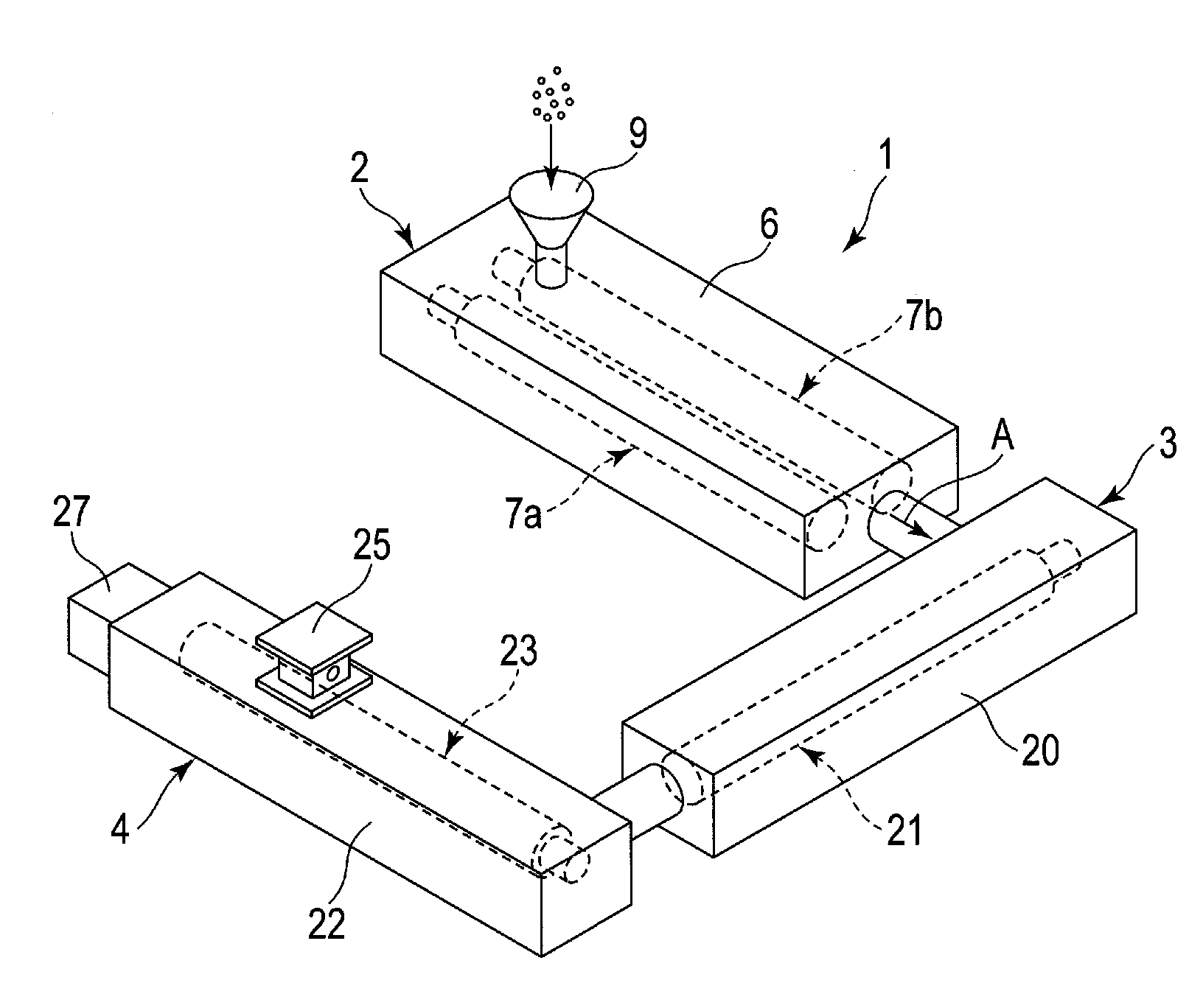
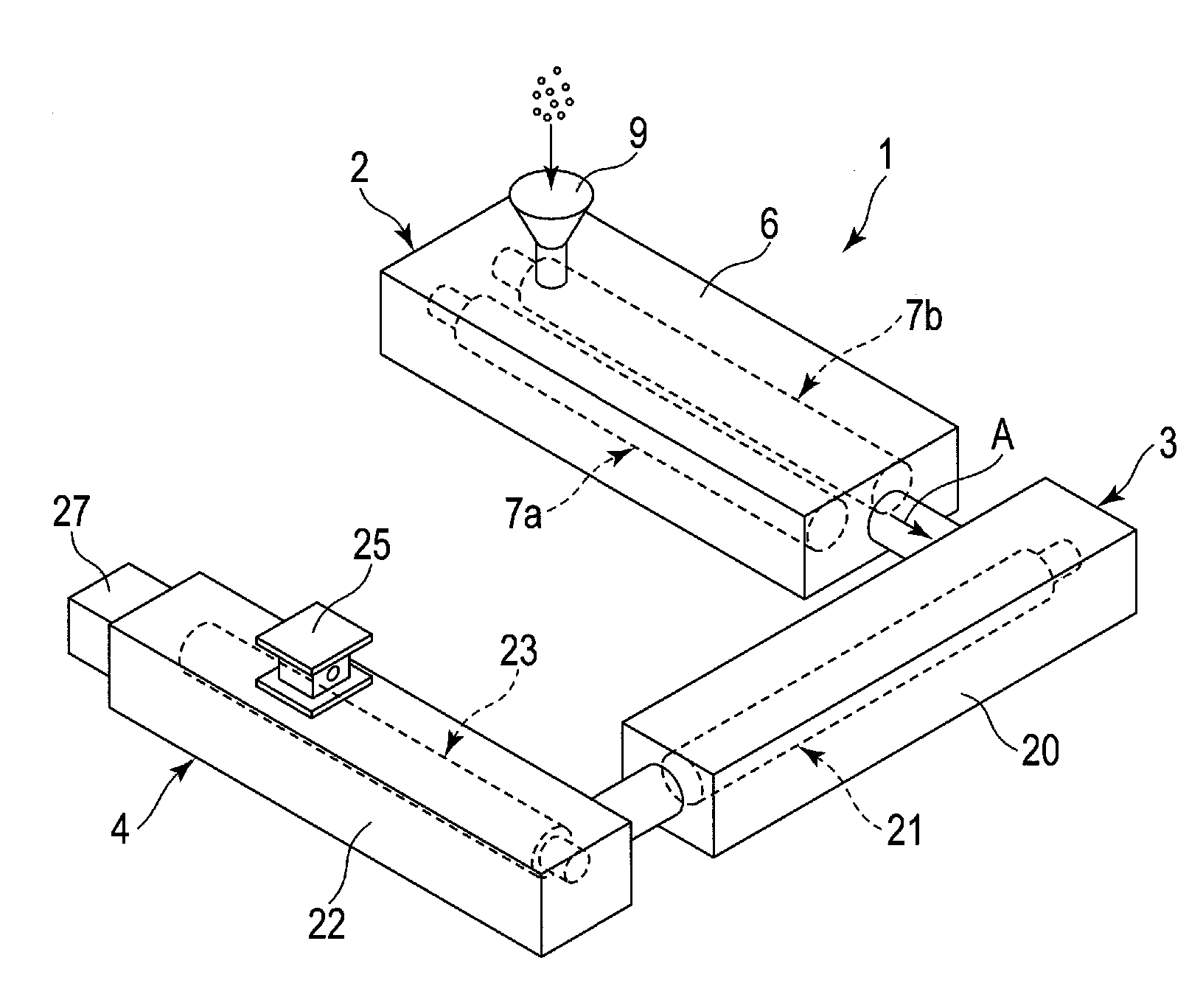
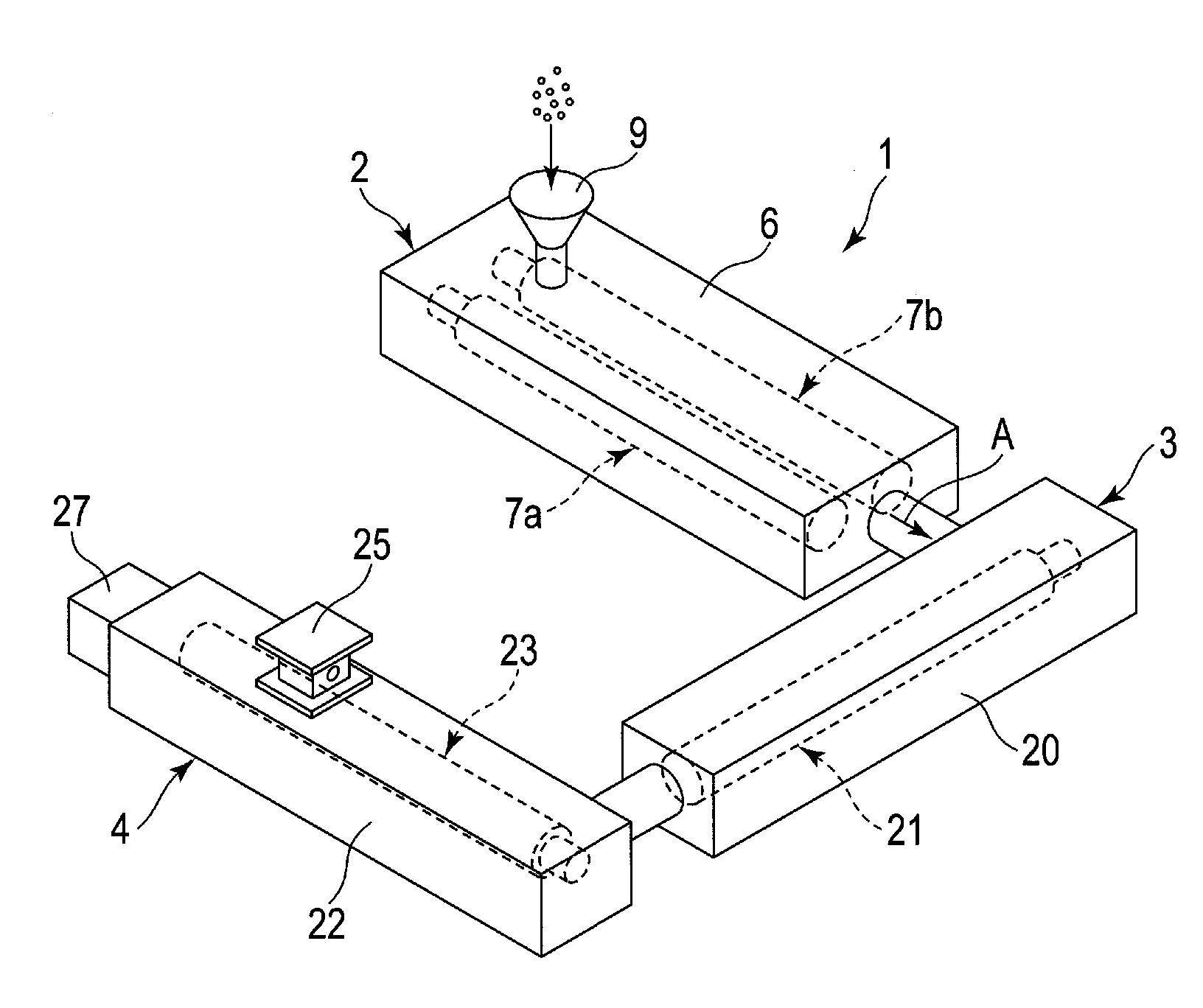
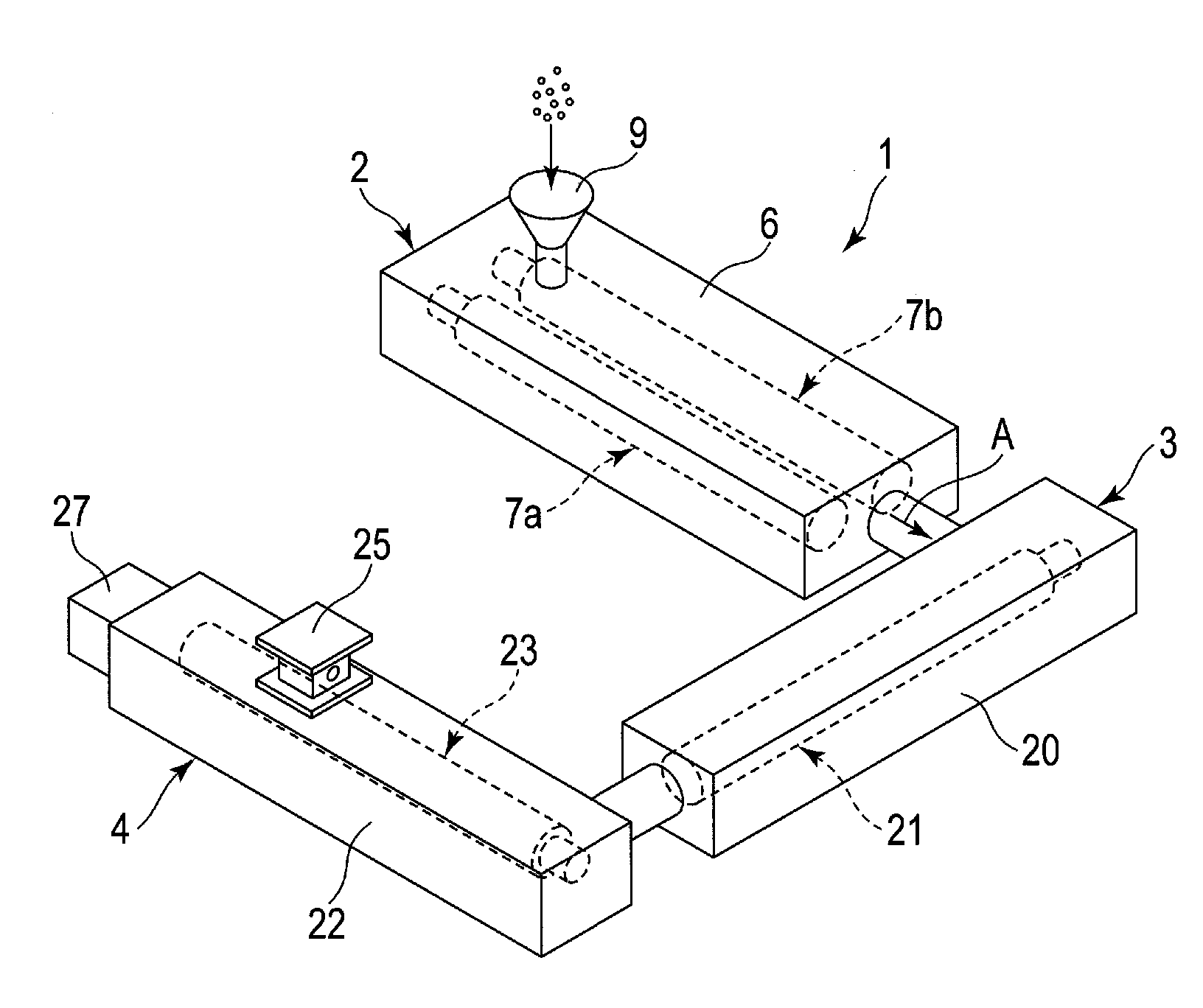
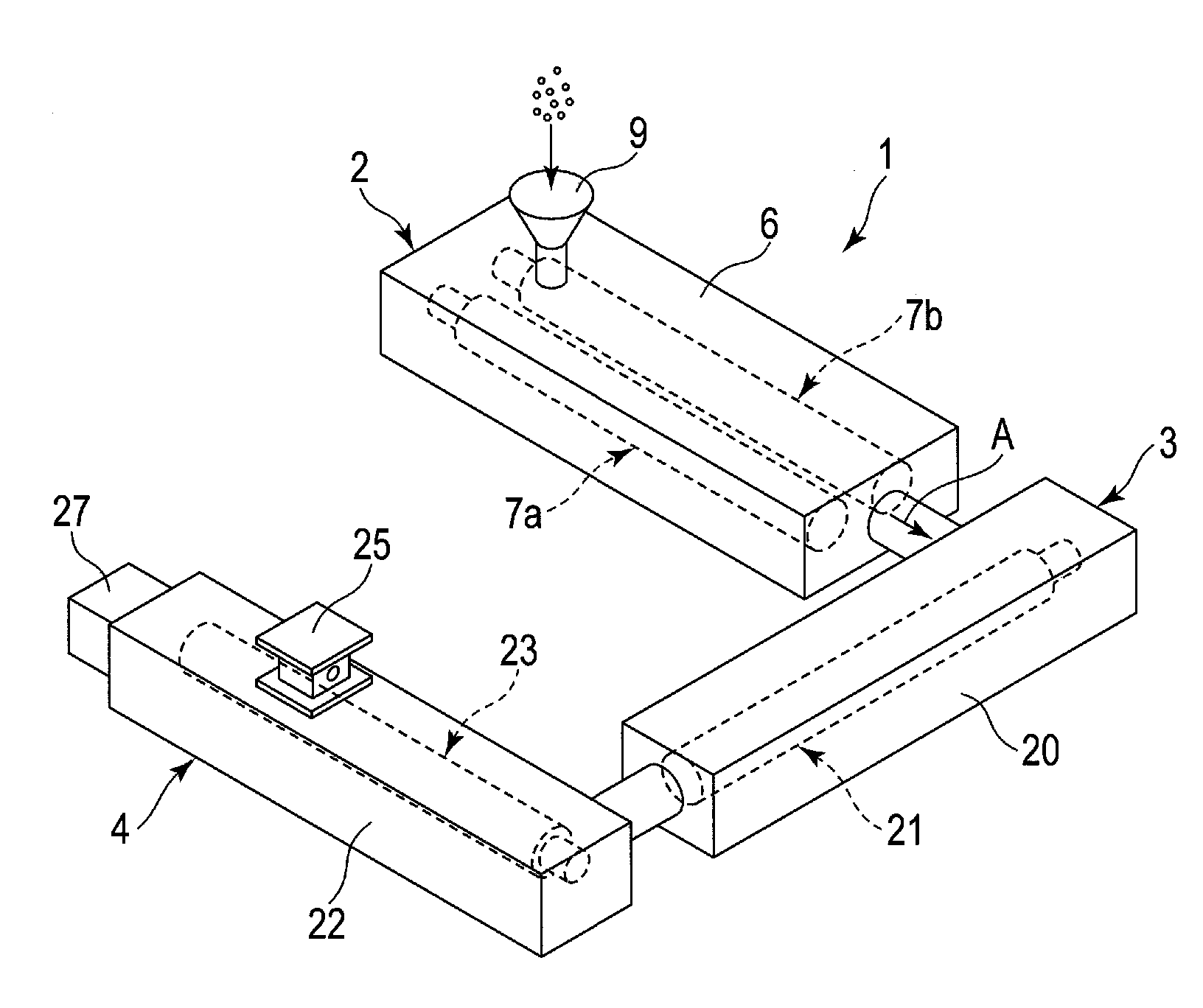
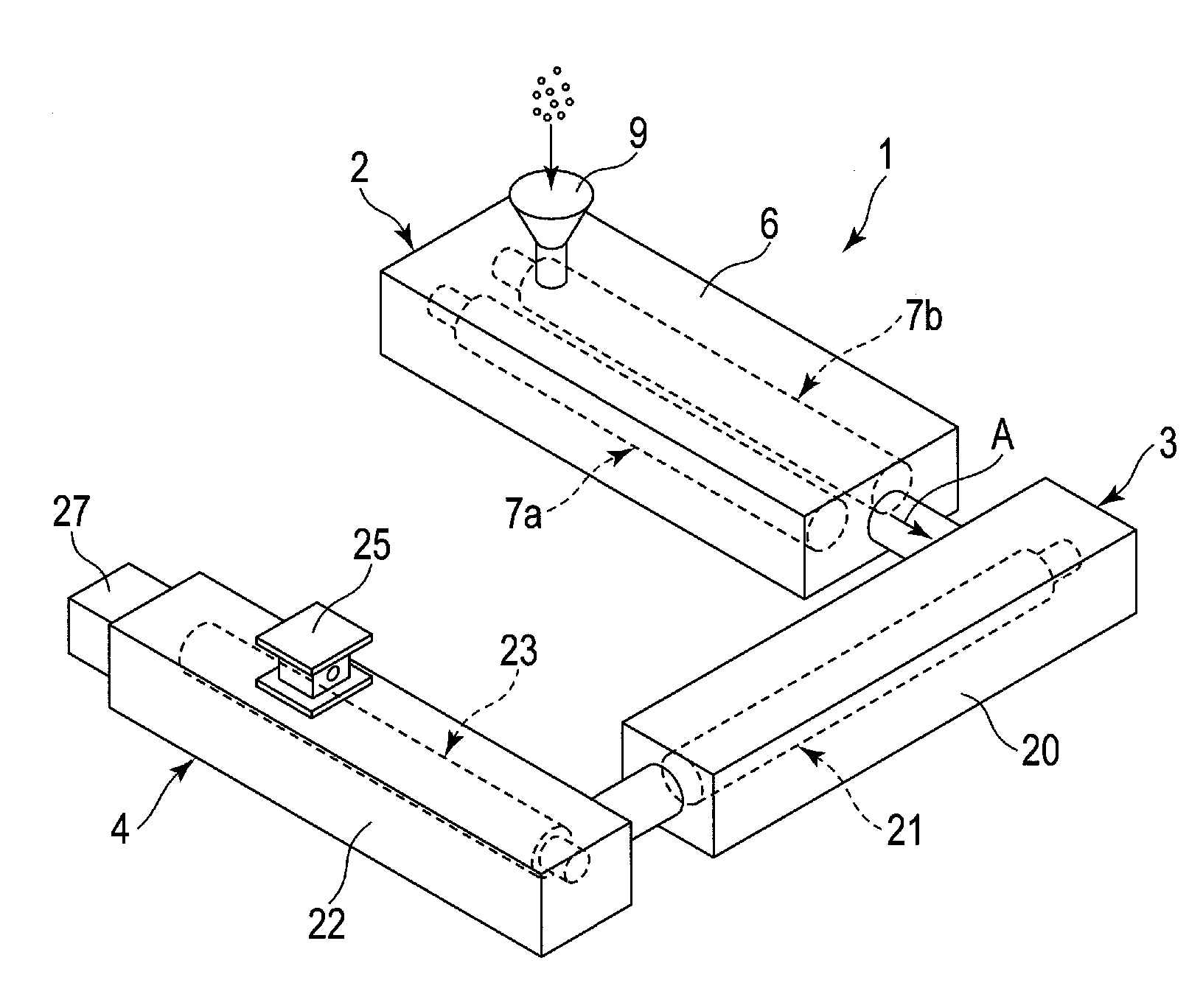
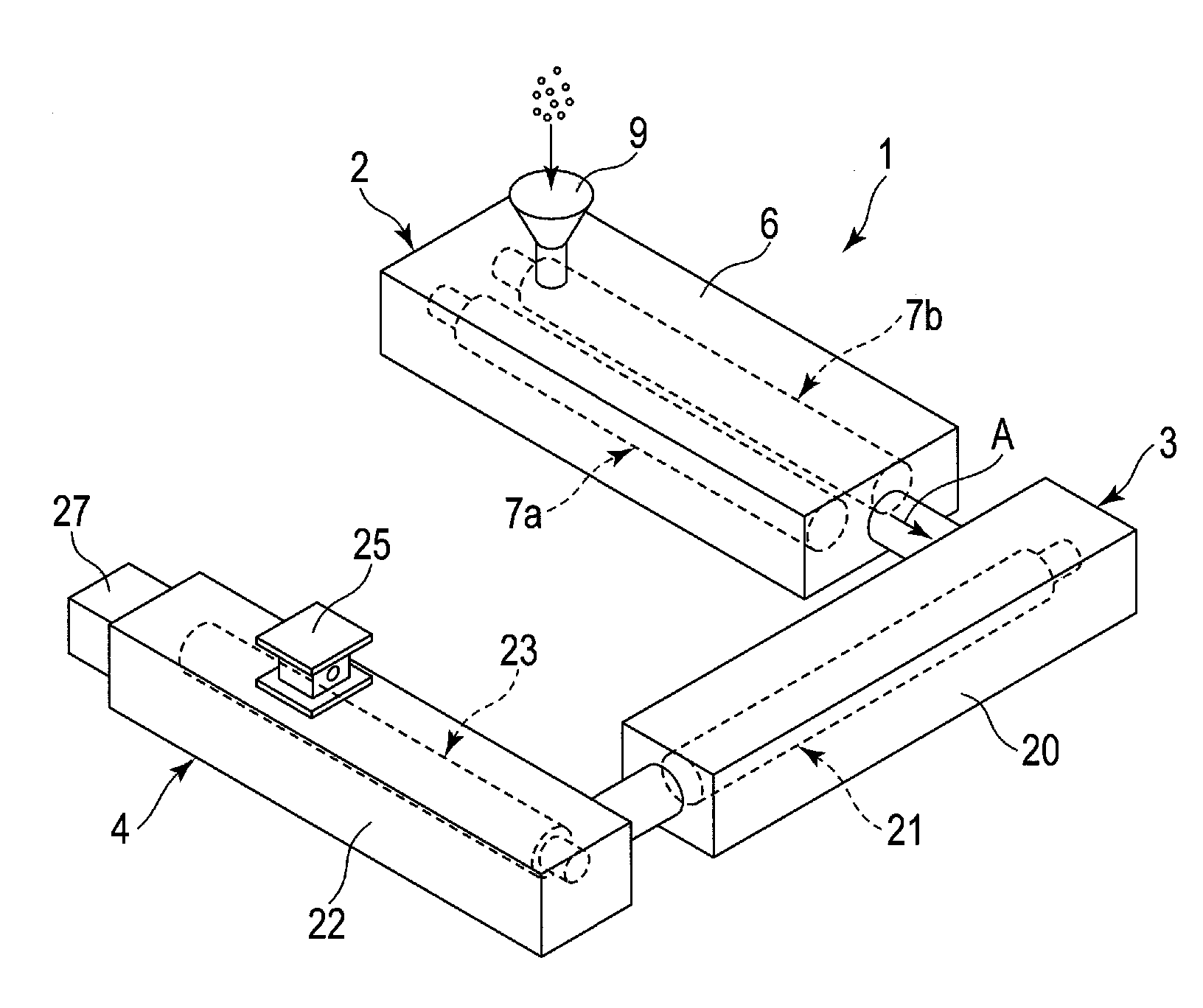
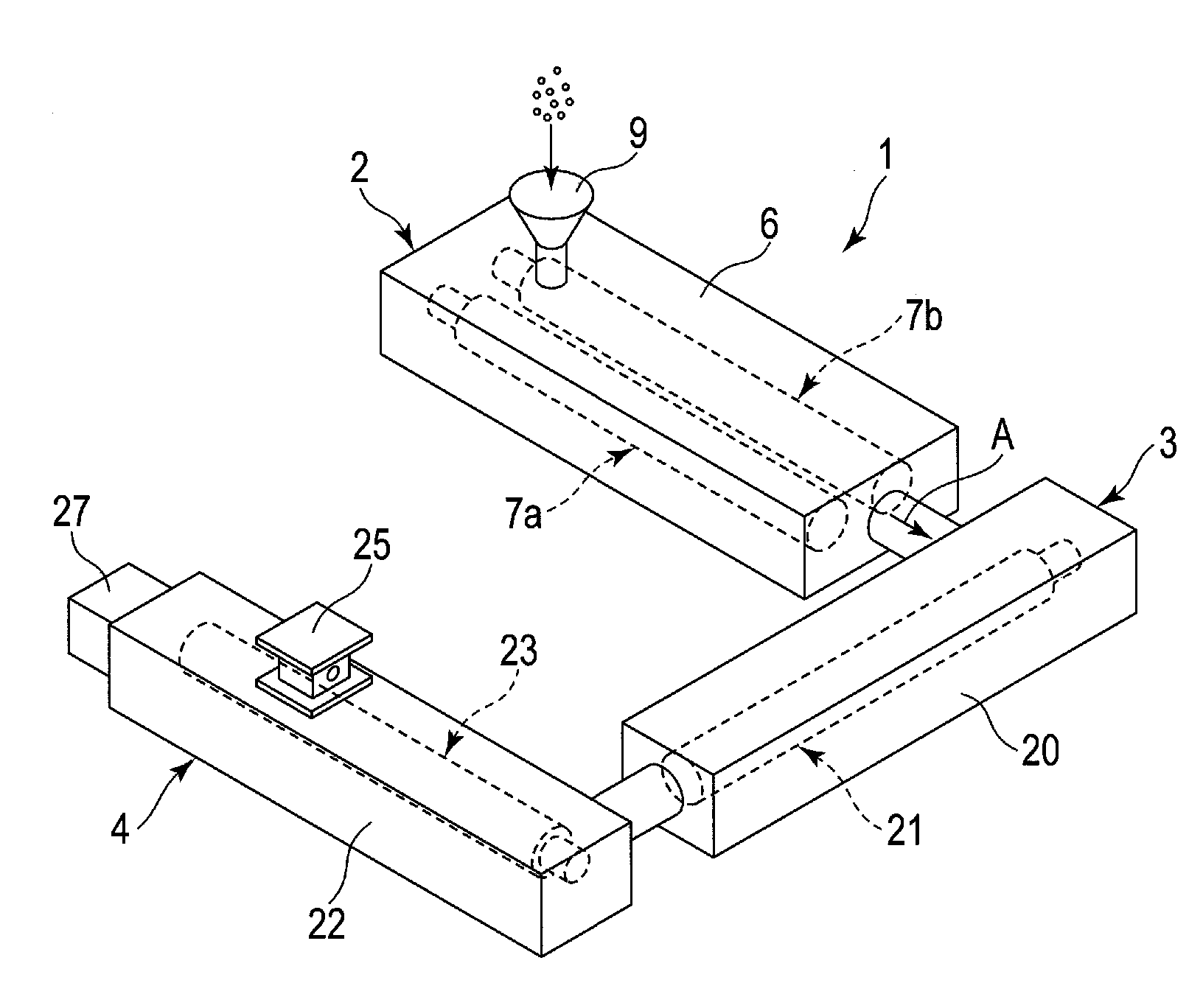
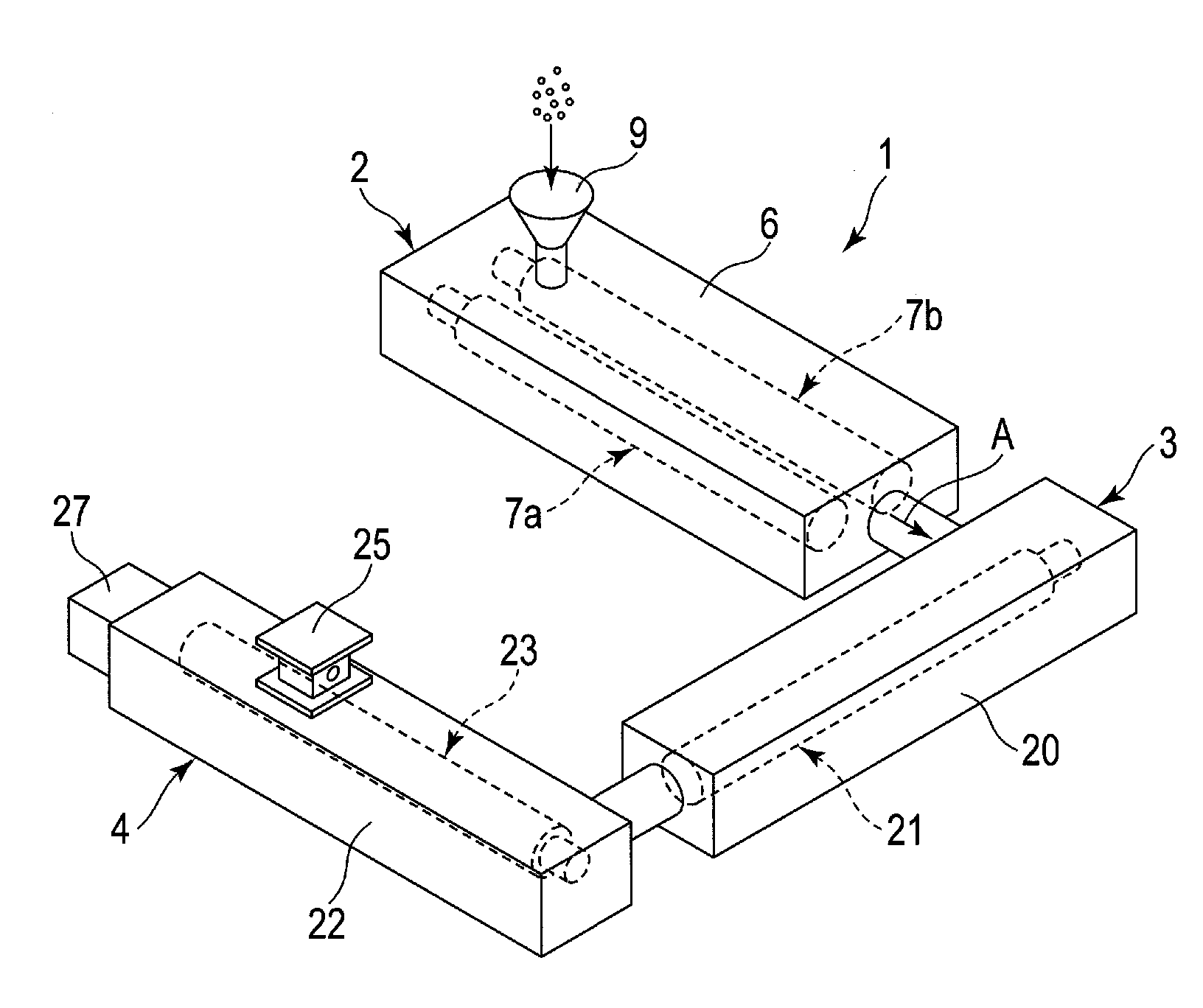

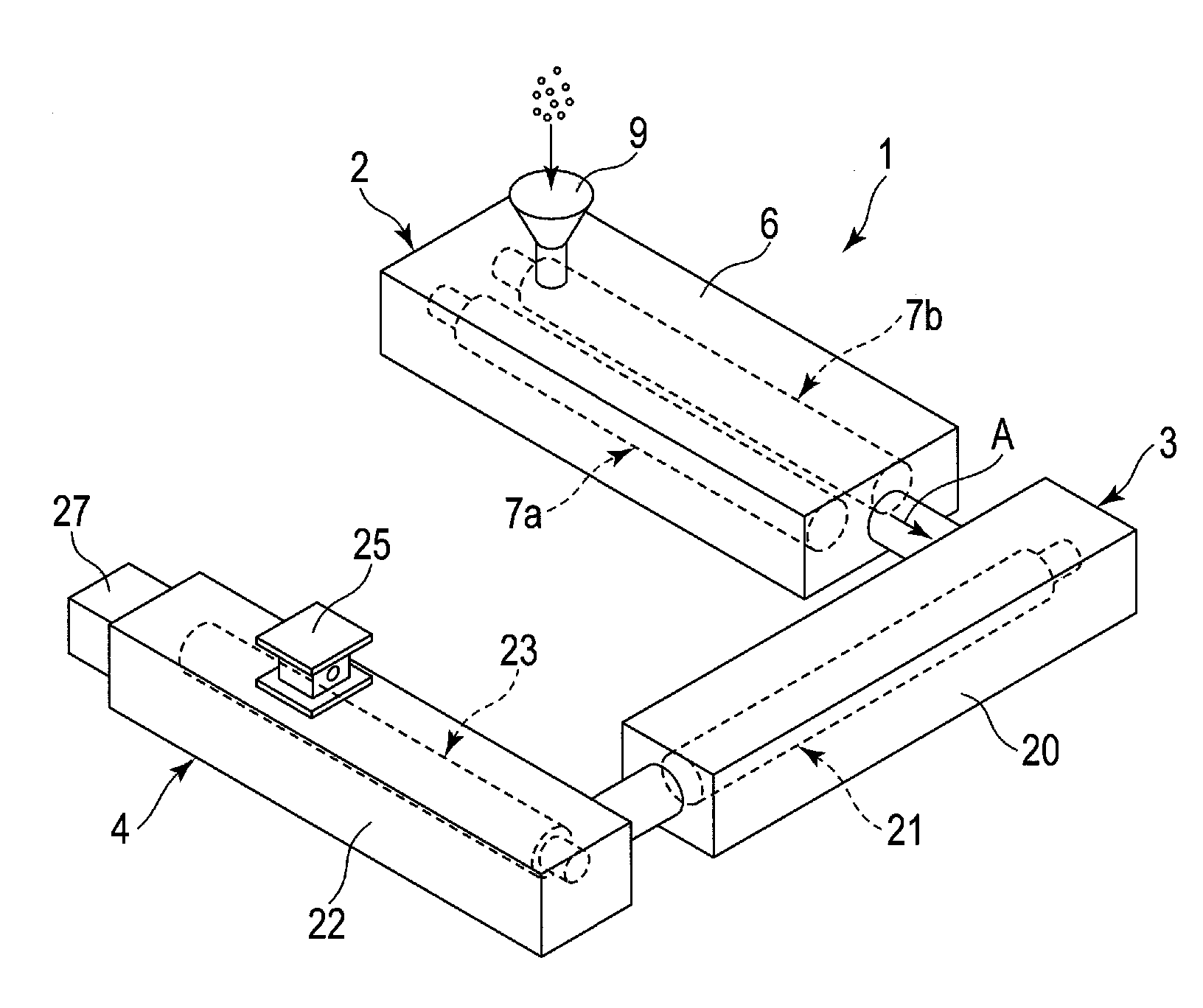
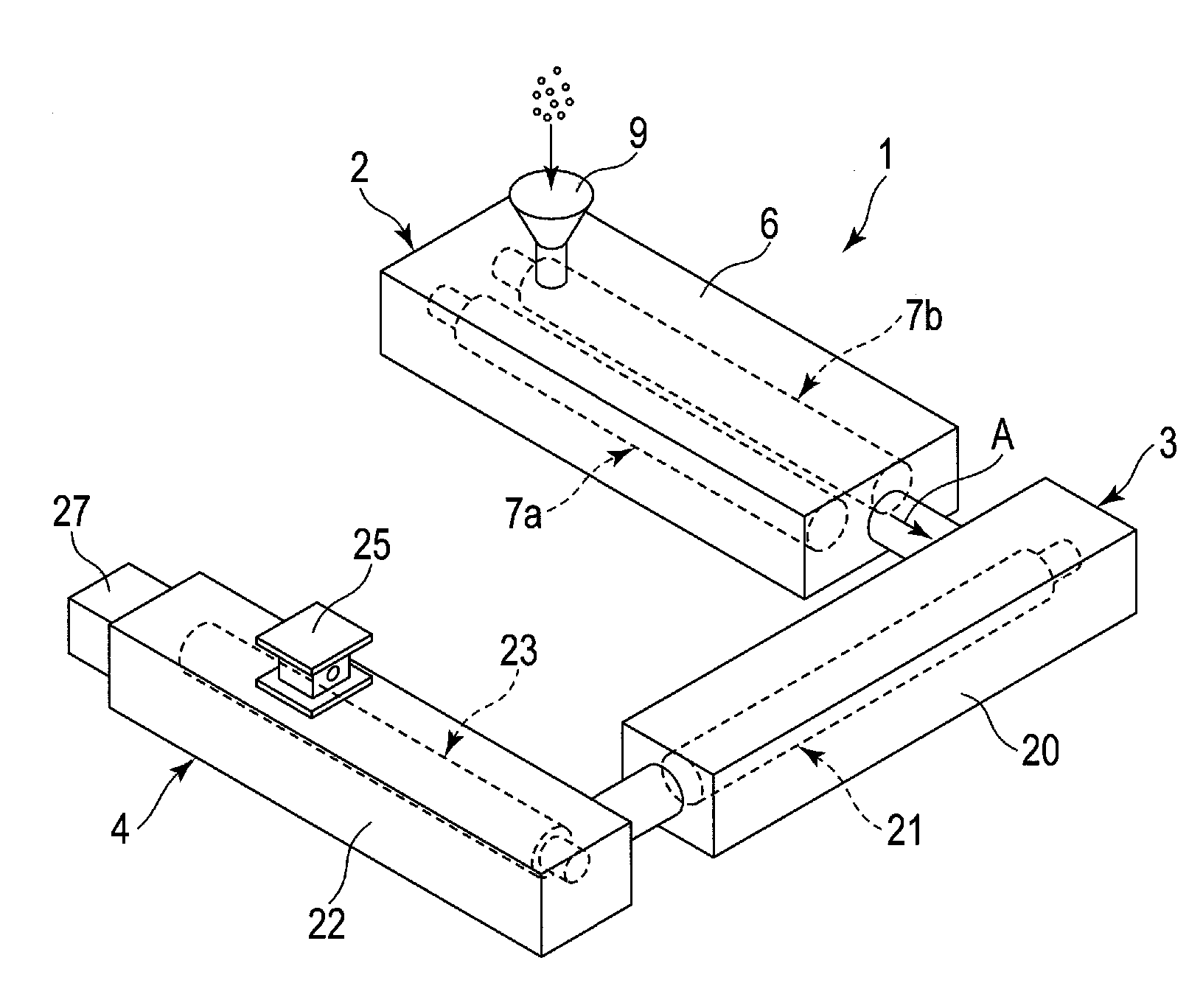
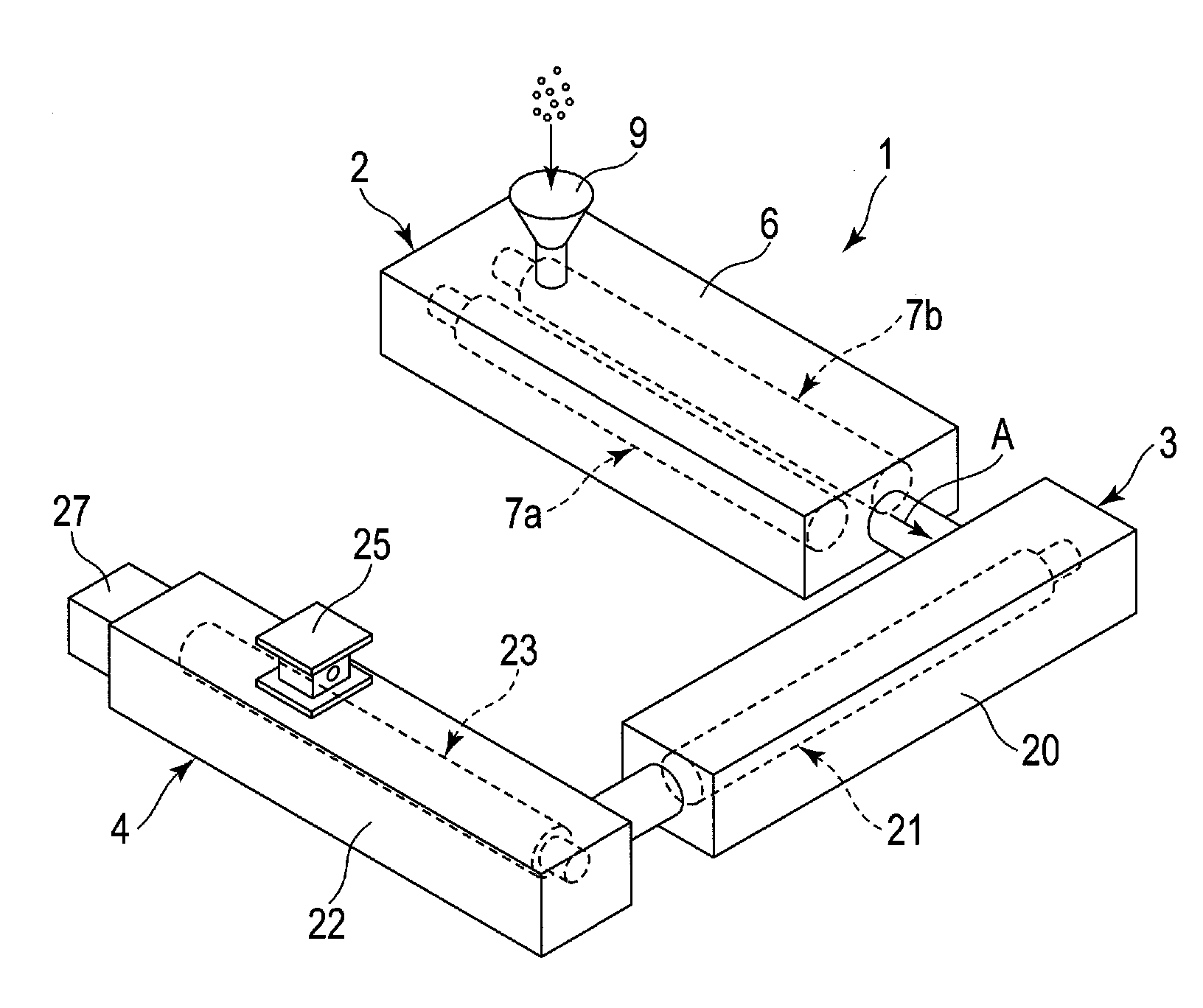
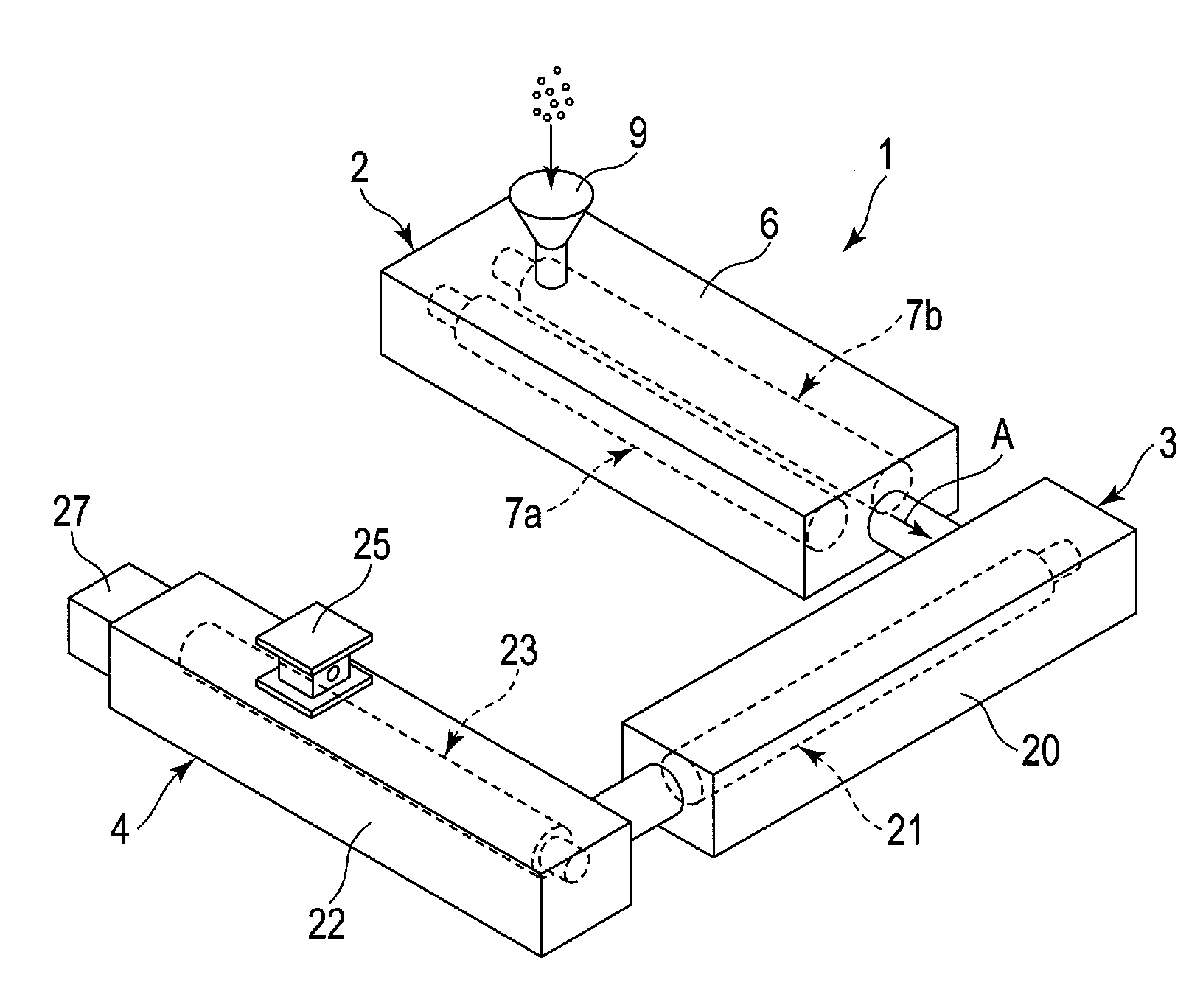