METHOD FOR OPTIMALLY DESIGNING HUB AND DRUM OF VEHICLE BRAKE SYSTEM USING FINITE ELEMENT ANALYSIS
The present invention refers to using finite element analysis method relates to search optimum-designed hub and drum of vehicle brake system, an axle for the specific of construction drum, hub, tie rod, spindle arm of each of the key components for selecting employing a sensor for detecting beam converter, generating driving conditions during operation, load conditions, b constraint applied to the drum and hub of each stress and stress value determines the position finite element analysis method using the optimum-designed hub and drum of vehicle brake system are disclosed. In attaching the device number of copper drum comprises a brake system, hub, tie rod, spindle arm being the key components for detecting beam coated, small pilot bolt number encoded manner. This bolt pilot scheme is also 1 as shown in drum (2) on the outside of the hub (1) and thereby an assembly configuration, drum (2) but the main part is completely after it escaped, according to structure attached increases and energy by an ordinary maintenance of brake, to reuse it escaped bolt cannot be further pin is of a fixed cost. In addition, coupled to the hub at a working efficiency of 0 generation taper bearings assembly, preload management withdrawing disapproval drainage holes shorten the service life. This structure as a prior art Korean publicized patent number 10 - 2014 - 0078907 call "drum brake case prevention structure" bottoms in number, wheel center coupled to the outer surface of the hub by a bolt mounted drum pilot of driving gate of construction according to the disk is maintenance cost, increased time etc. the cap having door number point. In order to solve the present invention refers to said door number point such as battery is provided, the purpose of the invention is, 1 generation taper bearings receiving satellit broadcasting on the outside of the drum brake system and the small composite number scheme coupled hub pilot manner it became work car number various wire hub and drum in various conditions which are optimum design value can be a number of hub and drum of vehicle brake system using finite element analysis or a reversed F. optimum design method. Of the present invention another object is to provide, in various conditions generated during operation applied to analyzing various hub and drum and driver's load conditions through the finite element analysis (Finite element analysis, FEA) Image and the highest stress and stress can be finite element analysis using a number of hub and drum of vehicle brake system or a reversed F. optimum design method. Of the present invention another object is to provide, through finite element analysis and highest stress occurrence position detection, hub and drum can be most suitable design for performing finite element analysis using a number of hub and drum of vehicle brake system or a reversed F. optimum design method. Of the present invention another object is to provide, the outer surface of the hub 1 generation taper bearings is applied can be used combining drum hub pilot scheme only after stripping the drum maintenance can be conveniently installed at a display part, when a driver bolt may be reused to finite element analysis using a number of hub and drum of vehicle brake system or a reversed F. optimum design method. In order to achieve said purposes such as drum assembled outside of the hub as well as taper bearings the present invention refers to brake system for optimum design method as applied to pilot devices by hub, brake system components by selecting, applying predetermined of each mesh properties after modeling design phase; said each designated in a design phase for accommodating components driving conditions, load conditions, constraint and material properties of the set value; setting said set information using finite element analysis (FEM) calculating wire hub and drum set or more stress and strain generation is checked the highest stresses generated position analysis step; and from the characterized. Brake system component of hub, drum, tie rod, preferably isobutylene and spindle arm selected from the beam. Applying said driving condition number 1 and number 2 applying hub and drum brake system to the operating state is the operating state is made, the same fixed time stored in both axial tire operating state said number 1 number 1 situation, one tire pressure of the tire is the same time stored in fixed axial situation number 2, number 3 and leading the 10 front tire detects contact with the curb situation, said concave section facing a vehicle tire in contact through the curb number 4 stores and number 5 is composed of a situation, the operating state is said number 2 simple fall, turning, lateral load is special in that it consists in situation 3 preferably. the constraint, said drum inner surface axis by restricting screwed position, said hub bearing coupled within the lower direction preferably is located outside of the load restraining the [tu which is a gun. The present invention 1 through generation taper bearings receiving satellit broadcasting outside of drum hub pilot manner it became work operation of small combined composite number scheme number generated at various conditions wire hub and drum brake system by analyzing value can optimum design. According to the present invention, operation is set to various conditions and driver's load conditions applied to the hub and the drum there is a finite element analysis (Finite element analysis, FEA) highest stresses generated through the changed position of the most suitable design may be made disclosed. According to the present invention, the outer surface of the hub 1 generation taper bearings is applied only after stripping the drum hub pilot scheme combining drum can be used by maintenance can be conveniently installed at the maintenance, maintenance may be reused upon bolt...copyright 2001. Figure 1 shows a combined hub and drum of bolts also pilot type engagement of the existing method 0 generation taper bearings shown cross section, Figure 2 shows a hub and drum of vehicle brake system using the present invention according to finite element analysis also shown optimum-designed method block, Figure 3 shows a general outline of the present invention according to brake system shown also key components, Figure 4 shows a cross-section of the present invention according to 1 combined with taper bearings generation also illustrates the engagement pilot hub, Figure 5 shows a hub also shown in the present invention according to sensors mounted thereon, The present invention according to Figure 6 shows a drum sensors mounted thereon also shown are disclosed. In the present invention according to hereinafter using finite element analysis system of brake hub and drum on the attached drawing with optimum-designed method with detailed the on-sensors other. Figure 2 shows a hub and drum of vehicle brake system using the present invention according to finite element analysis also optimum-designed method block shown also, brake system shown in Figure 3 the present invention according to a general outline the key components also, combined with a pilot hub of engagement shown in Figure 4 the present invention according to 1 generation taper bearings cross-sectional drawing, Figure 5 the present invention according to hub is shown in perspective view, shown in Figure 6 the present invention according to drum sensors mounted thereon are disclosed. As also shown in the present invention refers to the present invention refers to using finite element analysis and also 2 6 hub and drum of vehicle brake system the optimum-designed method, of construction for vehicle axle drum, hub, tie rod, spindle arm of each of the key components for selecting employing a sensor for detecting beam converter, generating driving conditions during operation, load conditions, b constraint applied to the drum and hub of each stress and stress value determines the position finite element analysis using method etc. deal with optimum-designed hub and drum of vehicle brake system. The present invention refers to such essentially 1 generation taper bearings (11) on the outside of the drum brake system as well as hub coupled hub pilot scheme travel to a dye by stress applied to the hub and drum simultaneously at the impact and load through finite element analysis value of each step (S10) is made of a red designed and stress analysis, established (S20) and analyzing step (S30) consisting of an. The, said 1 generation taper bearings (11) connecting it into the structure referred to as the rim bearing two rounded, cylindrical recuperative structure to fit the rim hub first and drive shaft fitting having lever handles shift prevention and lubrication of the bearing holes for injecting a grease sealing both big thread form. To the W-CDMA, bind to the drive shaft of the existing method 0 amount hub bearing in the case of taper bearings generation was rounded inner fitting bearing between the bearing and the data consisting of an outer tub. Ionomer such as structural difference working efficiency, life of bearings which cleaves the determined and as the other. In addition, one complex number of small hub pilot scheme is referred, only stripping manner after which maintenance is to inner drum hub drum, drum hub bolt pilot scheme is completely it escaped at an outside drum assembled after the collision disclosed. The present invention refers to 1 about the generation taper bearings (11) as well as hub (10) assembled on the outside of the drum brake system for hub pilot devices by applying the weld can be made corresponding to the optimal design for a metallization layer disclosed. First, said design phase (S10) in brake system (100) for selecting each component modeling mesh characteristics is equal to applying the key components. The brake system (100) being the key components drum (20), hub (10), tie rod (30), spindle arm (40), isobutylene and beam (50) a seal number selecting brake system (100) in accordance with the is designed each 3D modeling of 100. After designed 3D modeling using finite element analysis (Finite element analysis, FEA) after assembling said hub (10) on said drum (20) that the set properties of the mesh, the mesh characteristic is available consists of the finite element analysis. (S10) design phase (S20) designated in said setting in said each for accommodating components driving conditions, load conditions, constraint and material property value as follows. The material property value is brake system (100) according to a manner of interfacing resources demanded defined value input lines are deleted. In addition, the mesh characteristic is set for said constraint is said hub (10) on said drum (20) respectively the set, said drum (20) in the inner surface fixed axis (RA) by restricting, said hub (10) is arranged on the bearing by restricting rod lower end for positioning in order to provide restraint for every (LP) 2000. In addition, said drum (20) is combined by fixing the each screw groove centerline axis (RA) on rotating through all restraint, said hub (10) inner coupled to 1 generation taper bearings (11) after the lower end of the hub portions located outside load point (LP) toward on restraining substrate. Said, operation conditions brake system (100) number 1 and number 2 applying the operating state is the operating state is applying the entire hub and drum connected to the chamber. The operating state of a vehicle tire and moving said number 1 depending on the direction and impact forces exerted on the various steering in a direction brake system 5 to by analysis and calculated based on the conditions, specifically the same fixed time stored in both axial tire number 1 situation, one tire pressure of the tire is the same time stored in fixed axial situation number 2, number 3 detects the curb and leading the 10 front tire contact with the situation, said lateral concave section number 4 stores and vehicle tire in contact through the curb into a consists of number 5. In addition, the operating state is said number 2 simple fall, turning, into a special transverse load is consists of 3. The operating state is said number 2 the hub (10) and said drum (20) support and impact force applied in a direction various analyzing 3 calculated based on the conditions and, specifically simple fall, turning, special cross load 3 consists of the conditions. Wherein only the chin upon movement of simple dropped due, vertically load status generated by the burner head, by the rotation of the tire upon movement of a motor vehicle turning a status generated on the load, load application of an alkali-soluble novolak use special cross load force is greater than each situation thus set to the combustion chamber. The load applied to the axis from being dropped due in simple (WL) analyze, lateral load force is applied to the axis of turning and special (WL) and horizontal-(BL) in composite load is equal to analyzing. The, said axis corresponding to a center of the vehicle (WL) upwards as the axis of rotation of a vehicle tire, vehicle left-right direction of the vehicle toward the center of the axis of rotation transverse (BL) corresponding substrate. Through and mobile of vehicle brake system (100), said hub (10) and said drum (20) amd and impact force applied respectively can be within the range taking into account the situation. In addition, the load conditions said drum (20) gravity acceleration applied to 0. 6G, 0. 8G 1. 0G 3 conditions of a new substrate. In said analysis step (S30) (S20) finite element analysis (FEM) set in said setting information using said hub (10) on said drum (20) determined its position calculating stress applied to the highest stresses and excessive stress strain generation is checked as follows. Thus, when the operating state is in wide variety of environments and conditions by the impact and load said hub (10) and said drum (20) and determining a location highest stress applied to an optimum design can be. In addition, said hub (10) on said drum (20) can be judges its position to the highest stresses, in terms of the finite element analysis as follows. I.e., said hub (10) on said drum (20) is brake system (100) each binding site and structure in different load and impact applied by the main, constraint and load conditions made individually by finite element analysis to be coated. Through said hub (10) through the interpretation of number 1 number 2 by 3 by 5 the operating state is the operating state and server is context and, constraint and materials properties of highest stress and its position number 1 and number 2 caused by the operating state which is rotated excessive stress and strain oil, can be decided or absent. In addition, said drum (20) number 1 through 5 by interpretation of the operating state is context and load conditions, constraint and material properties of the highest stresses caused by its location number 1 which is rotated excessive stress and strain oil, can be decided or absent. The, safety rate disclosure formula by determining tensile strength/stress caused through said 1 generation taper bearings (11) as well as a hub drum hub pilot manner most suitable design to allowable stress range can be made. In addition, said lower face of the pilot to the hub by optimum design such as, simple maintenance, attached as well, reducing maintenance expense to reuse the bolt can be, 1 generation taper bearings (11) to the first and the size of concave grooves are formed, pivotably . In the embodiment described above of the present invention laser diode rights not limited range defined by described and claimed, in the field of the present invention is therefore a person with skill in the art in various angular positions in the object transfer rights range deformation can be nontrivial disclosed. 10: Hub 11:1 generation taper bearings 20: Drum 30: tie rod 40: Spindle arm 50: eye beam 100: Brake system WL: axis BL: transverse LP: every rod RA: axis The present invention relates to a method for optimally designing a hub and a drum of a vehicle brake system using finite element analysis. More specifically, the present invention relates to a method for optimally designing a hub and a drum of a vehicle brake system using finite element analysis, wherein main components such as a drum, a hub, a tie rod, a spindle arm, and an I-beam constituting a structure of a vehicle axle are selected so as to enable a physical property value of each of the components to be applied, and a stress value applied to the drum and the hub is calculated by substituting a driving condition, a load condition, and a restraint condition generated during driving so as to calculate the highest stress and a position thereof. COPYRIGHT KIPO 2018 Taper bearings as well as on the outside of the drum brake system for hub assembled hub pilot devices by optimum design method as applied to the, brake system (100) by selecting components, each of modeling design phase (S10) after applying a predetermined mesh characteristics; said designated in a design phase (S10) each for accommodating components driving conditions, load conditions, constraint and material properties of the set value (S20); setting said set information using finite element analysis (FEM) (S20) hub (10) in which the drum (20) stress applied to calculating position generated the highest stresses set or more stress and strain generation step (S30) analysis is checked; replaced and, said applying operation condition number 1 and number 2 hub and drum brake system to which certainly just applying operation on the operating state, the operating state is said number 1 number 1 the same time stored in both axial tire well situation, one tire pressure of the tire is the same time stored in fixed axial situation number 2, number 3 and leading the 10 front tire detects contact with the curb situation, said lateral concave section number 4 stores and vehicle tire in contact through the curb number 5 is composed of a situation, the operating state is said number 2 simple fall, turning, 3 transverse load is characterized in that it consists in special situations using finite element analysis system of brake hub and drum whose optimum-designed method. According to Claim 1, brake system (100) component of hub (10), drum (20), tie rod (30), spindle arm (40) for detecting beam (50) characterized selected optimum-designed hub and drum of vehicle brake system using finite element analysis method. Back number According to Claim 1, the constraint, said drum (20) in position when threaded inner surface axis (RA) by restricting, said hub (10) bearing coupled within the lower direction (LP) for every load is located outside of the apparat US using the characterized using optimum-designed method of finite element analysis system of brake hub and drum.

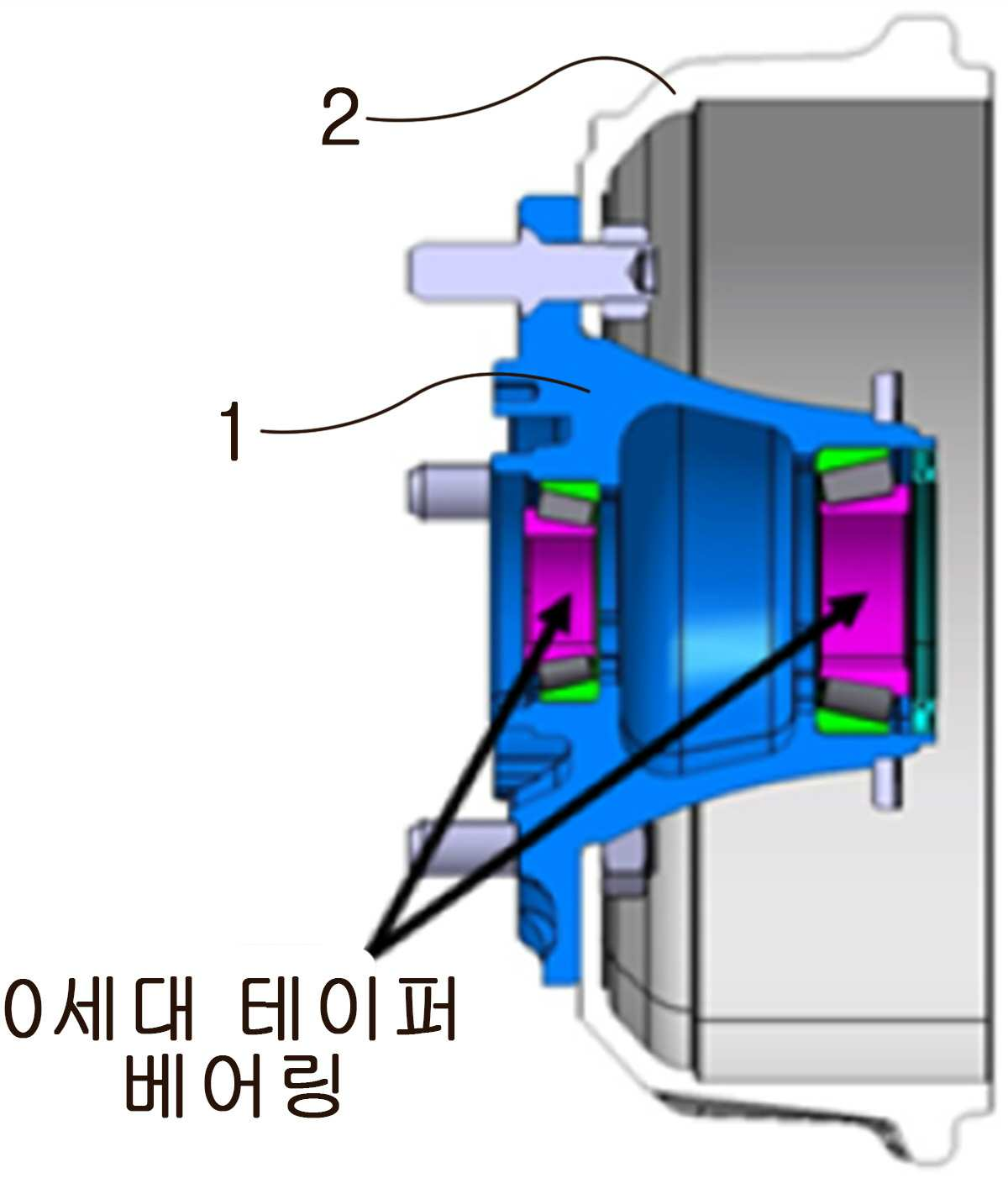
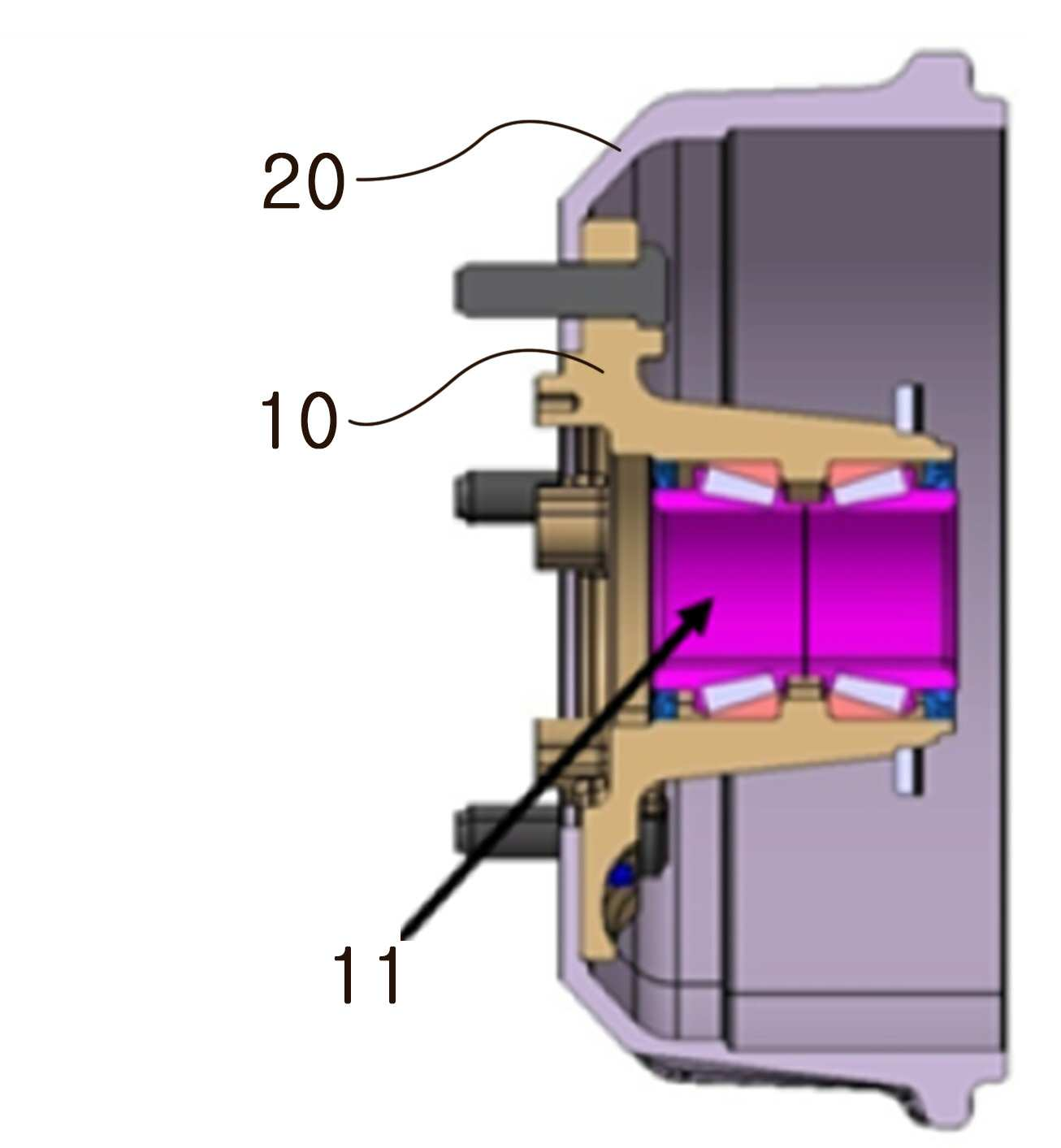

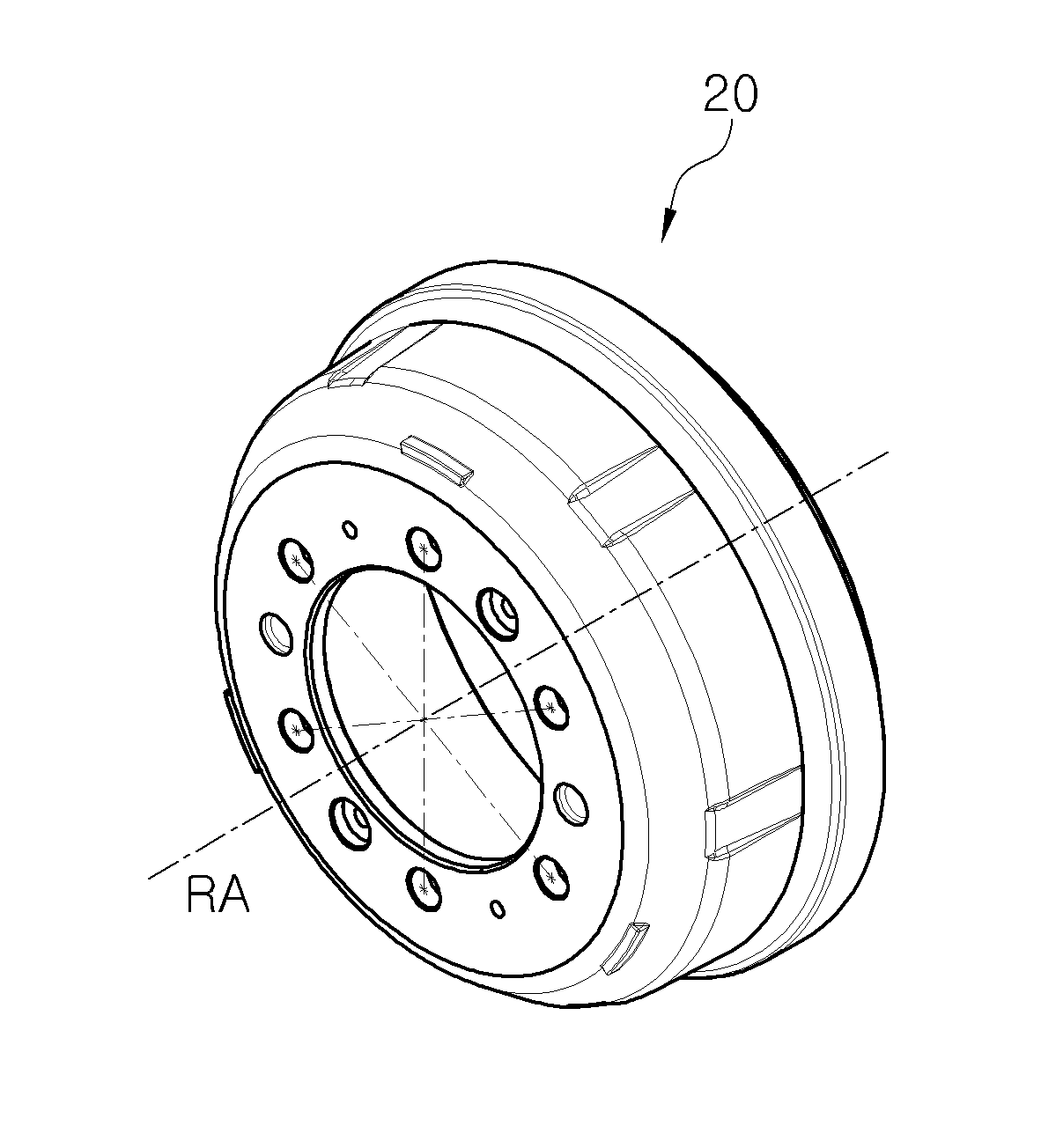
