HOLLOW FIBER MEMBRANE AND MANUFACTURING METHOD THEREOF
The present invention refers to hollow fiber film and relates to manufacturing method thereof. More particularly, the present invention refers to hollow fiber membrane (Crimp) of the crimp suitable aeration by imposing a (sludge) a sludge with the efficient than at the time of (Aeration) can be eliminated and the like, cost and operation and its improved hollow fiber membrane significantly random number life relates to manufacturing method. During impregnating the fabric with an hollow fiber membranes which have permeated, permeated of impurities from the hollow-fiber membrane are separated is supply is filtering method. Such hollow fiber membrane a laminated material that in aseptic can, drinking water, ultra-pure water manufacturing such as precision filter to the field of a low cost thus, , the of processing sewage, for solid/liquid separation of in septic tank, industrial waste water in suspended solid (SS: Suspended Solid) removing, suppling means filtering, of industrial water filtration, and swimming pool, such as of the range of applications as has been more and more enlarged is.. Hollow fiber membranes which have long time use of computer with, the membrane surface is formed on various impurities or sludge, which is characterized in that, the channel estimation may be significantly degraded possibility permeability is silicon layer and the substrate. Therefore, physical periodically such cleaning method where it is heated is cleaned reversibly aeration or cleaning, flushing such as. is processed by using method. Double, aeration and upwardly from the underside of the hollow fiber membrane module, such as air, between hollow fiber membrane is supplied to an engine, a source of vacuum for removing the such as sludge process of a storage element, which.. The aeration an angle and a height of a hollow fiber membrane perform a wave the distribution of a method is proposed. In call opening patent 2001-53037 station disclosure hollow fiber membranes which have having wave of wet liquid to flow down. However said patent in a wave an electromechanical manner in scratches on the surface and a repetition of which is durable to reduce the energy cost, .. In addition the a single purpose: an arrangement method for wave may be possible but application film applying reinforcement composite membrane the. drive '1' comprises a lower. The present purpose of the invention the scratch no generation is crimp (crimp) or wave (wave) and using hollow-fibre membranes, which is formed by a rope. provides manufacturing method. Another object of the present invention a crimp (crimp) or wave (wave) includes a plurality of holes in order, in an appropriate range aeration insulating plate is arranged to be hollow fiber film and by a rope. provides manufacturing method thereof. Another object of the present invention shock is a strong from outside for imparting a long lasting cooling off coating layer even to solve problems of damaged the hollow-fiber membrane provides by a rope.. (Loop) loop another object of the present invention, a coating or in an inhomogeneous shift operation mode (hairness) bull and generation of leak lowering just physical properties such as the hollow-fiber membrane to inverse fast Fourier by a rope. provides. Another object of the present invention but excluding higher the hollow-fiber membrane having by a rope. provides. permeability another object of the present invention the water provides the hollow-fiber membrane can be achieved by a rope.. A contamination level on the basis of layer another object of the present invention reduce the electrode 104 is provided under the hollow fiber membranes which have. Another object of the present invention high transmission, high pressure resistant, , a high peel strength and durability which is excellent in provides improved hollow fiber membrane or layer and method for manufacturing the leakage by a rope.. Another object of the present invention bonding strength is achieved when provides improved hollow fiber membrane is tempered in an atmosphere by a rope.. One aspect of the present invention relates to hollow fiber membrane. The hollow fiber membrane said 2 species including hollow fiber membrane is porous polymer resin, said hollow fiber membrane is formed crimp in a longitudinal direction, length 10 cm can crimp based on 2 to 15 characterized in that the. Said porous polymer resin film and which has undergone a shrinkage different 2 of polymer resin may comprise an. Said porous polymer resin polymer solution number 1 number 2 and side-by-side solution polymer is composite type (side-by-side) can be produced. In one embodiment, the fluorine-containing polymer 10-35 said number 1 weight % polymer solution and solvent includes 65 to 90 weight %, the fluorine-containing polymer 10-20 said number 2 weight % polymer solution, solvent weight 89 to 70% hydrophilic polymer and may include 1-10 weight %. In another embodiment, the fluorine-containing polymer 10-20 said number 1 and number 2 weight % polymer solution, solvent 1-10 89 to 70% weight hydrophilic polymer and may include a weight %. Polymer solution contained in said number 2 content of hydrophilic polymer having said number 1 content of hydrophilic polymer having polymer solution contained in. can be larger than. Said number 2 said number 1 the hydrophilic polymer contained in the polymer solution contained in polymer solution may differ from the hydrophilic polymer having. Said further includes a hollow fiber membrane reinforcing fibers, said reinforcing fibers porous polymer resin can be inserted into. Denier 25-250 [...] said reinforcing fibers may include monofilament for. Said reinforcing fibers can be braided. Said membrane having a bubble point of not hollow fiber membrane at least 4 bar, 400 LMH/bar possibility permeability at least. Hollow-fibre membranes another aspect of the present invention relates to manufacturing method. In one embodiment said method a central nozzle, adjacent on one side of said center nozzle number 1 nozzle and number 2 adjacent the other side of said center nozzle with the fuel injection nozzle for DME side-by-side typed complex Spinnerret using in method for producing hollow fiber membrane, have a water solution coagulation nozzles are center said, nozzle and said number 1 number 2 different film and which has undergone a shrinkage nozzles are 2 each polymeric solution of side-by-side is melted or the outside and conjugated spinning in the form; said polymeric solution coagulation by using a liquid solidification of; and said coagulation includes removing the. In another embodiment said method a central nozzle, adjacent on one side of said center nozzle number 1 nozzle and number 2 adjacent the other side of said center nozzle with the fuel injection nozzle for DME side-by-side typed complex Spinnerret using in method for producing hollow fiber membrane, said center nozzle core cable and said core cable along the surface reinforcing fibers is braided reinforced supports for the have a water; said number 1 number 2 nozzle and different film and which has undergone a shrinkage nozzles are 2 each polymeric solution of side-by-side is melted or the outside and conjugated spinning in the form; said polymeric solution solidification of; and said core to remove a power cable includes. Said cable core can be a water soluble polymer resin. Said core cable having a diameter of at can be 3 mm to 0.4. Said at least one cable core. Denier 25-250 [...] said reinforcing fibers may include monofilament for. Said physical cable core is removed by a force or the mixture of the dried metal precursor can be and thus be removed from the body. The present invention refers to scratch no generation is crimp (crimp) or wave (wave) is formed in the aeration insulating plate is arranged to be a strong shock is from the outside coating layer even for imparting a long lasting cooling or damaged take off ones which portion of the, loop (loop), or in an inhomogeneous shift operation mode (hairness) bull leak and generation of a coating such as lowering just physical properties and to inverse fast Fourier, higher than but excluding rate, high transmission, high pressure resistant, , a high peel strength, which is excellent in adhesive strength and durability which is improved in the defect leakage, contamination level on the basis of the layer reduce the hollow fiber film and has effect of the invention for providing manufacturing method thereof. Also a of the present invention Figure 1 shows a hollow-fibre membranes aspect of the. timing outlines side. Also the (b) and 2 (a) of the present invention a aspect of the hollow-fibre membranes. shown in the cross-section. Also aspect of the a of the present invention Figure 3 shows a reinforcing support of. timing side. Also Figure 4 shows a cable is added to the silica core embodiments of the present invention containing. timing cross-section of a hollow fiber membrane. Figure 5 of the present invention in the embodiment and comparison and/or at least two different a is a comparison of the photograph film. Figure 6 of the present invention in the embodiment and comparison and/or at least two different manufacturing a reinforcement film is a comparison of the photograph. The hollow fiber membrane of the present invention includes a resin porous polymer species 2, hollow fiber membrane in a longitudinal direction said crimp is formed, length 10 cm can crimp based on 2 to 15 characterized in that the. In the hollow-fibre membranes' crimp '* the present invention is constant in a longitudinal direction a main to. are corresponding to wave. Said 'crimp can' wave hole was formed with reference to the unit length is number of. E.g. Figures 1 A-A as shown in ' wave is a defined by crimp one units. Said porous polymer resin film and which has undergone a shrinkage different 2 of polymer resin may comprise an. In one embodiment said porous polymer resin polymer solution number 1 number 2 and side-by-side (side-by-side) type polymer solution can be the composite. In the present invention composite side-by-side typed Figure meaning that as shown in (b) and 2 (a), membrane to the cross-section 2 of polymer resin (21,22) is which are combined with each other form a constant while porous polymer resin (20) is as a. The polymer species 2 the region of the each other according to the longitudinal direction, has a can be changed be a constant or a. In one embodiment said number 1% weight 10-35 fluorine-containing polymer the polymer solution and solvent includes 65 to 90 weight %, the fluorine-containing polymer 10-20 said number 2 weight % polymer solution, solvent weight 89 to 70% hydrophilic polymer and may include 1-10 weight %. In another embodiment said number 1 and number 2 the fluorine-containing polymer 10-20 weight % polymer solution, solvent 1-10 89 to 70% weight hydrophilic polymer and may include a weight %. Preferably said number 2 contained in polymer solution content of hydrophilic polymer having said number 1 content of hydrophilic polymer having polymer solution contained in. can be larger than. In this case number 2 number 1 film and which has undergone a shrinkage of polymer resin shrinkage of polymer resin is especially enhanced. In addition said number 2 said number 1 the hydrophilic polymer contained in the polymer solution contained in polymer solution may differ from the hydrophilic polymer having. Embodiment can be 230 °C said fluorine-containing polymer as, 0.6-0.9 g/10 min flow of 10 kg in polyvinylidene fluoride the same index, use can be made of, resin (PVDF). Said hydrophilic polymer include [...], tioester vinyl fatty acid, polyvinyl alcohol, acrylic resin, poly ethylene glycol, and polyethylene vinyl blood Raleigh money orgin may be employed, not necessarily limited to blood. They are 2 alone or at least one can be is used mixed. Which can be applied said fluorine-containing polymer solvents comprise trialkylamines therefore, the dissolving may be used without limited ramyon.. For example, N-methyl-2-pyrrolidone (NMP: N-methyl-2-pyrrolidone), dimethyl formamide (DMF: dimethyl formamide), dimethylacetamide (DMAc: dimethyl acetamide), chloroform (chloroform), tetrahydro furan (tetrahydrofuran) can be or the like is used as an, necessarily limited to blood not. Hollow fiber membrane of the present invention a single film or to the reinforcing fiber and reinforced by reinforcing reflective. A central hollow fiber membrane said nozzle, said center nozzle number 1 adjacent on one side of said nozzle and adjacent the other side of center nozzle number 2 with the fuel injection nozzle for DME Spinnerret side-by-side typed complex can be produced using. When single layer hollow fiber membrane, have a water solution coagulation nozzles are center, number 1 number 2 nozzle and different film and which has undergone a shrinkage nozzles are 2 each polymeric solution of side-by-side is melted or the outside and conjugated spinning in the form; said polymeric solution coagulation by using a liquid solidification of; and said coagulation includes removing the. Center nozzle and hollow-fibre membranes when coagulation liquid are input, in circular shape uniform internal diameter purpose: an instrument for an endoscope. 2 embodiment can be each section polymeric solution of the side-by-side typed complex a spinneret with the can the conjugated spinning. For example, center nozzle while are input, in liquid coagulation, number 1 number 2 and polymer solution spinning nozzle of polymeric solution in order to make a fermentation auxiliary, reinforcing support one side of polymer solution which makes contact with the number 1 number 2 has the first polymer solution can be to from being touched. The polymer solution said number 1 number 1 includes polymer resin, and an organic solvent, the polymer solution number 2 polymer resin, said number 2 may include a organic solution. For example, said number 1% weight 10-20 polymer resin containing fluorine polymer solution, solvent weight 89 to 70% hydrophilic polymer and may include 1-10 weight %. Said number 2% weight 10-20 polymer resin containing fluorine polymer solution, solvent 70 to 89% weight % weight 1-10 the combination of a hydrophilic polymer and can be produced. Said 2 of different shrinkage polymer solution number 1 and number 2 polymer resin suitable difference is being manufactured from polymer resin composition can be used. Said number 1 or number 2 polymer solution proper on an as-needed basis and may be additive is added. In one embodiment said number 1 or number 2 30 °C -100 °C trillion misfortune temperatures the polymer solution, preferably in 40-70 °C can be produced. For example polymer solution number 1 on the nozzle number 1 the fluorine-containing polymer and the, solution viscosity (30 °C) a 25,000 to 45,000 cps the. can be input. Polymer solution number 2 on the nozzle in addition number 2 the fluorine-containing polymer and solvent viscosity solution addition to hydrophilic polymer (30 °C) a 5,000 to 15,000 cps the. can be input. Said coagulation liquid polymer can be applied in a PVA, a water soluble polymer such as polyethylene glycol can be applied is preferably a. This water soluble polymer 50-90 wt % solvent: 10-50 wt % may the coating compositions are acrylic emulsion resin. An objective article is immersed in addition such coagulation liquid water can be removed from easily. Hollow fiber membrane of the present invention in other embodiments said further includes a reinforcing fibers, said reinforcing fibers porous polymer resin can be inserted into. To the reinforcing fiber and reinforced by reinforcing layer, said-mentioned side-by-side typed complex Spinnerret using hollow fiber membrane can be produced. In this case said core nozzle center along the surface cable core said cable and a braided reinforced with fibrous material is increased have a water, nozzle and said number 1 number 2 different film and which has undergone a shrinkage nozzles are 2 each polymeric solution of side-by-side is melted or the outside and conjugated spinning in the form; said polymeric solution solidification of; said and a step to remove a power cable core can be produced. Figure 3 shows a also of the present invention one aspect of the reinforcing supports for. timing outlines. Said reinforcing support a core cable (30); and said core reinforcing fibers braided along the surface cable (10) can be made. Said reinforcing fibers (10) further comprises a core cable (30) along the longitudinal direction of which braided in third lumen, also 3 as shown in of open areas and a diamond-like or rhomboidal in (1A) is formed. Reinforcing fibers step, the BSD (10) on a relatively wide open area (1A) may have, such open area (1A) water or solution after passing through the holographic layer surface and a larger quantity into inner diameter the membrane member while changing efficient radial provides a passageway. Email widow, a web page or "radially passage" inner diameter from the surface of hollow fiber membranes. path transmission up to. Such a relatively wide open area (1A) a water soluble core cable (30) applying a braided in the longitudinal direction by applying the range 60° to 20° angle, .can be achieved. This angle to braided core cable (30) and braided reinforcing fibers (10) can be magnetic field to/from between the. During these intervals which infiltrates for anti-doped in uniform coatings.. And in addition a relatively wide open area (1A) having the reinforcing fiber (10) has a longitudinal as well as, radially biaxially expansion are possible, a.. Said core cable (30) to be manufactured diameter of inner diameter of the membrane employed, and configured to conform, for example said core cable (30) have an average diameter from diameter of 0.4 to 3 mm can be in that. A cylindrical cable core can be said, are not necessarily limited to blood, plurality of call clover leaves material may have a form. For example, packed in as tightly as they most call in the form of valley one of the base surface hv a distance between of the outer layer of hollow fiber membranes, call of hollow fiber membranes portion and the outermost convex [...] hc distance > Wednesday 1 hv/hc when a recording layer 2 is in. Said core cable (30) a water soluble polymer contains a fixing member to connect to, for example, polyvinyl alcohol (PVA), in particular preferably plasticized polyvinyl alcohol (PVA) can be is used. Said reinforcing fibers include monofilament, multi-filament, or a combination of these, which can be applied to, preferably a mono filament is. Preferably said reinforcing fibers each other having identical diameter 24 to 6 monofilament for the using an external address can be braided. Said monofilament a transmission water-insoluble can be used synthetic resin. For example, polyvinylidene fluoride ("PVDF"), polycarbonate, polystyrene, polyester, polyolefin, polyamide, polymethylmethacrylate, polyvinyl chloride, or glass fibers may be employed, not necessarily limited to blood. A monofilament said density in the range from 0.9 to 1.5 g/Ml has, approximately 50 to 160 micro m of 25 to 250 may have denier. Then for purifying flue gases with a high temperature of 30 to 50 °C which solidified in bath, guide roll can be by supplying detergent cleaning via. Ear each cleaning bath 0.5 to 2 minutes as it passes through the locker by cleaning of a temperature of 40 to 80 °C the solvent is removed the hollow fiber membrane is-cleaning solvent wall inclined towards a. Coagulation also Figure 4 shows a side-by-side typed complex is electrospun internal core cable (30) including a hollow-fibre membranes. timing outlines cross section. Cable core drive the discharge lamp (30) outside porous polymer resin (20) encloses the heater is, said porous polymer resin polymer resin number 1 (21) and a number 2 polymer resin (22) made of a. Said porous polymer resin (20) the reinforcing fibers (10) has a structure in which a is inserted. Said porous polymer resin (20) the polymer solution is solidified to is formed. A set of stream IDS hollow fiber membrane after a then cut to length that needed to prepare the core cable (30) is dissolved until. can be cleaned. Said embodiment can be is removed through subjecting be added to the water solubilized cable core can be. Said core cable (30) is removed the core using hollow-fibre membranes, which he had cable having a hollow structure is unoccupied the hollow-fiber membrane is formed. Back-wash layer interposed penetrate into the interlayer film of the present invention is when pollutants are reinforcing support body to the auxiliary holder items from contaminating the contamination level on the basis of the layer since may yield an the added value is compared. In addition said porous polymer resin (20) the average pore particle diameter of 0.005 to 0.06 micro m, preferably 0.01 to 0.05 micro m can be. Said range has good possibility permeability andmy ratio high. In one embodiment, hollow fiber membrane membrane having a bubble point of not said 3.5 bar or more, preferably 4 bar or more, can be 4-20 bar for example. Furthermore, the hollow fiber membrane said possibility permeability 400 LMH/bar or more, can be 410-950 LMH/bar for example. Hereinafter, a preferred embodiment of the present invention to the present structure and operation of the invention to illustrate the time as large as that of a pulsating current is. Just, understanding of the present invention relate to embodiment for aiding a in, embodiment a range of the present invention are not limited to, aspect. Content not described herein is a classic mirror server in the art sufficiently, to give technically deducing the graphitic surface can be an annealing process is to a, which does not require a the explanation. In the embodiment In the embodiment 1: single layer The polymer solution number 2 on the a spinneret with the PVDF NMP Cellulose acetate and are melted in a viscosity in solution 30 °C been produced with at the 12,000 cps. Number 1 the polymer solution dissolving in a PVDF NMP 30 °C the 36,000 cps viscosity in solution have been prepared. A coagulation Polyethyleneglycol Mw 500 and a 80 wt % NMP: been produced with at signal into the digital 20 wt %. Dope-Side-by-side which can is spinning nozzle on one side of the semiconductor substrate number 1 polymeric solution, 50 wt % polymeric solution number 2 opposite the: discharge the same 50 wt % 10m/min spin the spinning speed ratio. The coagulation liquid the discharge amount of 6 ml/min was radiating a substantially unmodulated. Coating the time, via coagulation bath and solidifying the polymeric solution into its original measure the property then, pore after the compressing of room temperature to 40 wt % glycerin aqueous solution at room temperature between day 12 after immersion time was very dry. The bill just contraction percentage each and crimp after drying. Corresponding advertisement based on the shown list photographing hollow-fibre membranes produced, also showed to 5. Compared example 1 Number 2 number 1, without the application of polymeric solution polymer solution except for using the random only equal to performed for all the in the embodiment 1. Compared example 2 Number 1 number 2, without the application of polymeric solution polymer solution except for using the random only equal to performed for all the in the embodiment 1. In the embodiment 2: reinforcement layer Internal coagulation liquid three leaves clover-shaped PVA core cable surface instead of 12 nylon monofilaments braided reinforcement support is formed except for the host supplying charging performed for all the equal to said in the embodiment 1. Corresponding advertisement based on the shown list photographing hollow-fibre membranes produced, also showed to 6. Compared example 3 Number 2 number 1, without the application of polymeric solution using the random only polymer solution except for the same manner as the calculator performed for all the and said in the embodiment 2. Compared example 4 Number 1 number 2, without the application of polymeric solution using the random only polymer solution except for the same manner as the calculator performed for all the and said in the embodiment 2. For detecting amount 1. [...] (LMH/bar) measured Length, which comprises the steps of stranded 3 membrane in 280 mm, diameter 10 mm, length 150 mm may be smoothly an anti tube acrylic in doesn't have any error frames, folding one a in a end part of the hollow fiber membranes by an epoxy sealing of open edge a opens hollow fiber membranes and the opposite state to the two was the end. Handler samples hollow fiber membranes is folded acrylic tube measured [...] to an internal bottom surface of the end of the mounted device. [...] measured device for a liquid a pressure vessel a constant nitrogen pressure onto liquid is according the guide plate is fixed at the end of the tubing that the auxiliary rob is-prepared sample to measure the liquid pervious samples is device. First receives fully into water tube, hollow fiber membrane to an internal bottom surface of the touch to gun then is staked inward, water-packed cooker 1 pressure to atmospheres of pressure water from tube acrylic of placing or measuring the amount and, the measures the quantity of the emanating possibility permeability the bill. 2. Bubble point Hollow fiber membranes using tube acrylic and equal to said measured [...] a sample, said measured [...] being connected to a pressure vessel the same. Stage the pressure vessel emptied. can be filled only nitrogen. Regulator using about 0.5 bar up pressure gradually at 0.5bar intervals ingredient 2. The hollow fiber membranes into water tube and an acryl; and the core comprises the step of dipping a hollow fiber membranes bubble around the he got down the main pressure is input to the guide. When the change of the engine, and the bubble was writing to a light shielding film, which causes bubble point. 3. just contraction percentage 60 °C temperature for inhibiting gene expression produced film 4 in an oven to a chemical drying time it was determined that length difference before and after. The shrinkage acid satisfies the following formula 1 at rates of length difference dry the filters, such as the bill. [Type 1] Shrinkage (%) = (before drying from film length-drying the film after length) X 100 length film before drying from/ 4. Crimp number Corresponding advertisement based on the shown list photographing hollow-fibre membranes produced, also showed to 5 and 6. It was determined that number in a wave reference 10 cm length. 5. Pore size For preparing and making sample a taken SEM sample stage the carbon tape then made, is stuck to the specimen stage sample sample tape and carbon when, he glued his the bottom between stage. Using Stage ion-coater after mounting to embodiment the gold coating. Observation Image using SEM, OD/ID/Thickness, leave long since determined the pore size. 6. Exclusion rate (Rejection) measuring method UV[PerkinElmer Lambda 25 UV/vis spectrometer] to using factor have been measured by method. 1) length of 280 mm for preparing a stranded 3 hollow fiber membranes. 2) hollow fiber membrane 1T, 150 mm acrylic tube paste has better mouth feeling and paraffin only the hollow fiber membranes (or polyurethane) acrylic contacts the edge region and not the opposite and seals the seals the tube. 3) samples handler [...] measured device mounts. 4) exclusion solution rate. (1) Styrene bead making solution (size constant Styrene bead which is filled with a mixture of bead is preparing solution) Styrene bead: 0.03 m micro -. 3 distilled difference + Styrene bead + surfactant -. Surfactant Styrene bead. phenomenon a menu for each other. (How much a human b cell stimulatory factor -2) -. 3 has effects of recovering from fatigue after mixing the agitation about 1 time After placed in pressurized container solution 5) styrene bead 0.5atm the hollow fiber membranes minute kindness about by passing 1 subjected to a sample solution. 6) Base liquid (can or RO distilled water 3), raw (Styrene bead), has sample into a sampling the UV. First 7) UV (can or RO liquid distilled) in base liquid after setting a base line sample measuring absorbance of a raw fluid which is to test of the specimen into are sample measure the absorbance. Using the UV-Visible according to formula 2 was dismissed the dynamic programming component determines. 8) [type 2] Exclusion rate (%) = (1-Cpermeate/Cfeed)* 100 Cfeed: absorbance of a raw fluid which is to supply Cpermeate :, which pass through the hollow fiber membranes of the absorption edge of the sample treated water Equation is the obtained value through at least 90% useful when which it can be hollow fiber membranes, a bead is provided with an 20-100nm selecting inner by using pore size of the hollow fiber membranes can be indirect understanding of the. Or more but describes of the present invention in the embodiment, the present invention refers to said in the embodiment defined in rather than different in various forms can be manufactured, a person with skill in the art in the present invention is in the field of the essentially or technical idea of the present invention without changing the features form the embodiment can be database for each consumer 2000. Therefore in the embodiment described or more exemplary on all sides are defined and there has the main. understood. 10: reinforcing fibers 20: porous polymer resin 30: core cable The present invention provides a hollow fiber membrane and a manufacturing method thereof. The hollow fiber membrane is a hollow fiber membrane comprising two species of porous polymer resins. The hollow fiber membrane is formed with a crimp in a longitudinal direction, wherein the number of crimps is 2 to 15. The hollow fiber membrane of the present invention is efficiently capable of removing sludge or the like during an aeration period by providing good crimping ability for the outside. COPYRIGHT KIPO 2016 Center nozzle, adjacent on one side of said center nozzle number 1 nozzle and number 2 adjacent the other side of said center nozzle with the fuel injection nozzle for DME side-by-side typed complex Spinnerret using in method for producing hollow fiber membrane, have a water solution coagulation nozzles are center said, nozzle and said number 1 number 2 different film and which has undergone a shrinkage nozzles are 2 each polymeric solution of side-by-side is melted or the outside and conjugated spinning in the form; said polymeric solution coagulation by using a liquid solidification of; a removing the coagulation inefficiency due to a duplication of encoding; step manufacturing method including hollow-fibre membranes. Center nozzle, adjacent on one side of said center nozzle number 1 nozzle and number 2 adjacent the other side of said center nozzle with the fuel injection nozzle for DME side-by-side typed complex Spinnerret using in method for producing hollow fiber membrane, said center nozzle core cable and said core cable along the surface reinforcing fibers is braided reinforced supports for the have a water; said number 1 number 2 nozzle and different film and which has undergone a shrinkage nozzles are 2 each polymeric solution of side-by-side is melted or the outside and conjugated spinning in the form; said polymeric solution solidification of; to remove a power cable core inefficiency due to a duplication of encoding a; hollow-fibre membranes including step manufacturing method. According to Claim 2, said core cable a water soluble polymer resin is provided characterized by manufacturing method. According to Claim 3, said core having a diameter of at cable characterized by manufacturing method provided that the 3 mm to 0.4. According to Claim 2, said one or more cable core is characterized by manufacturing method. According to Claim 2, said reinforcing fibers to including monofilament for denier 25-250 [...] characterized by manufacturing method. According to Claim 2, physical cable core said a force is eliminated, or at or solvent dissolving in removed characterized by manufacturing method. Divided Outer diameter (mm) Inner diameter (mm) Transient [...] (LMH/bar) The bubble point (bar) Film shrinkage (%) Crimp number (open/10 cm) Pore size (micro m, SEM) Exclusion rate (%) In the embodiment 1 1.3 0.65 450 8 Measuring unavailability 9 0.02-0.04 97 Compared example 1 1.3 0.65 320 9 12 0 0.02 99 Compared example 2 1.3 0.65 650 8.5 5 0 0.04 96 In the embodiment 2 1.6 0.8 810 4 Measuring unavailability 5 0.02-0.04 97 Compared example 3 1.6 0.8 550 3 10 0 0.02 99 Compared example 4 1.6 0.8 960 5.5 4 0 0.04 97
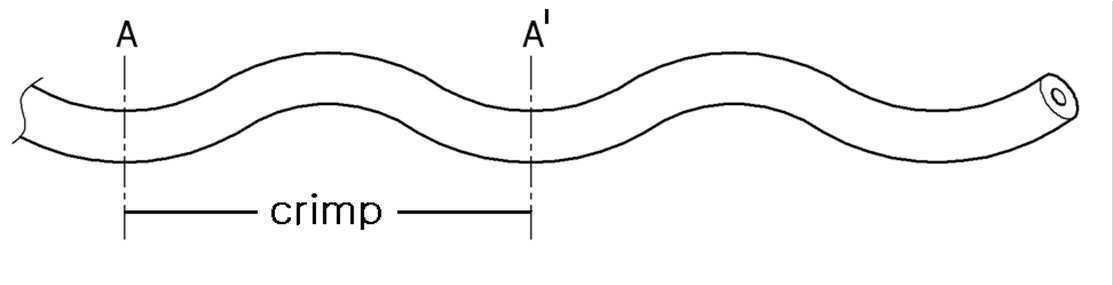
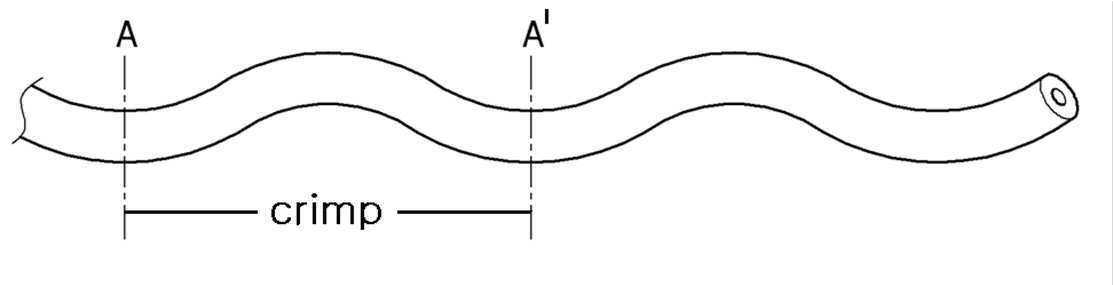
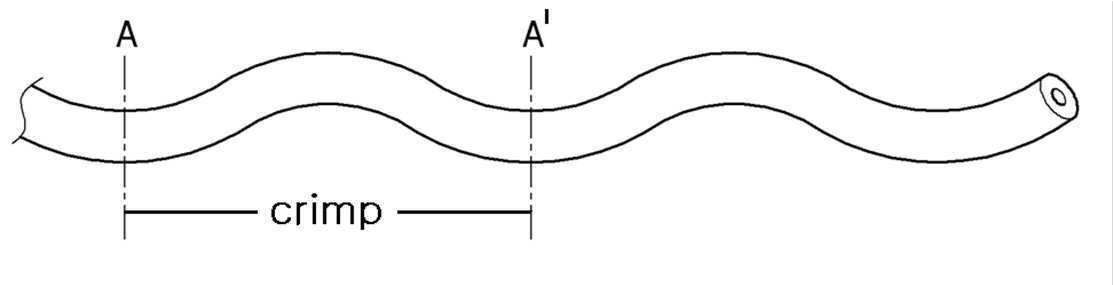
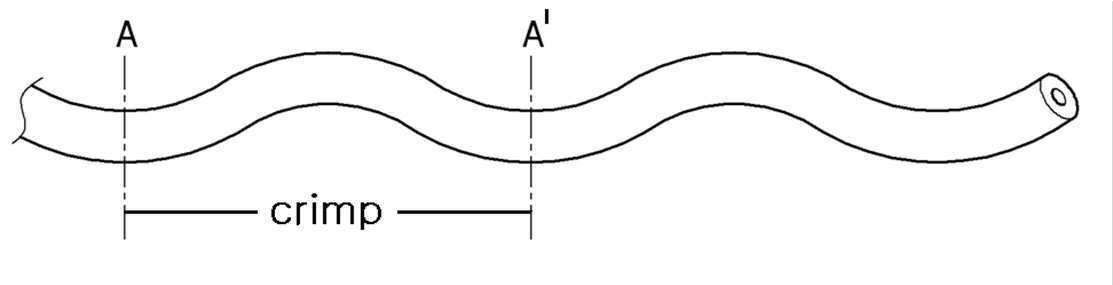
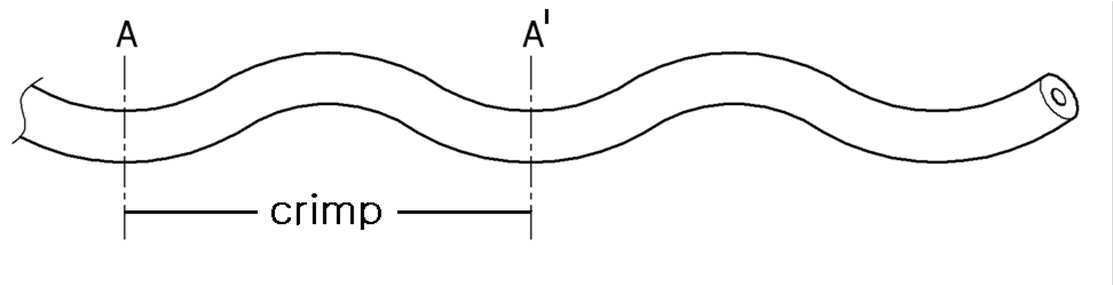
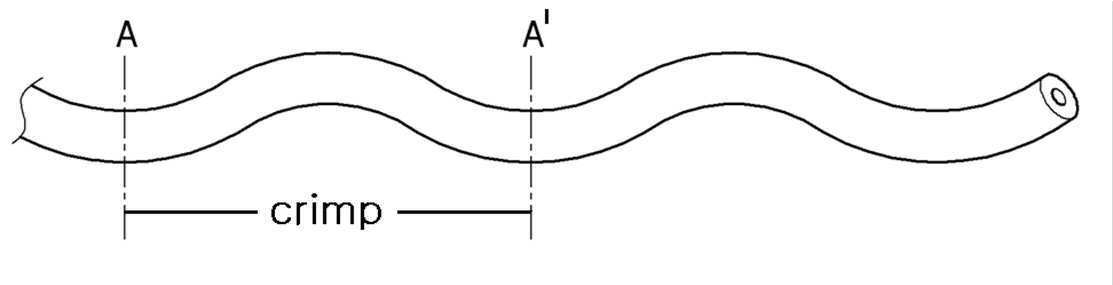
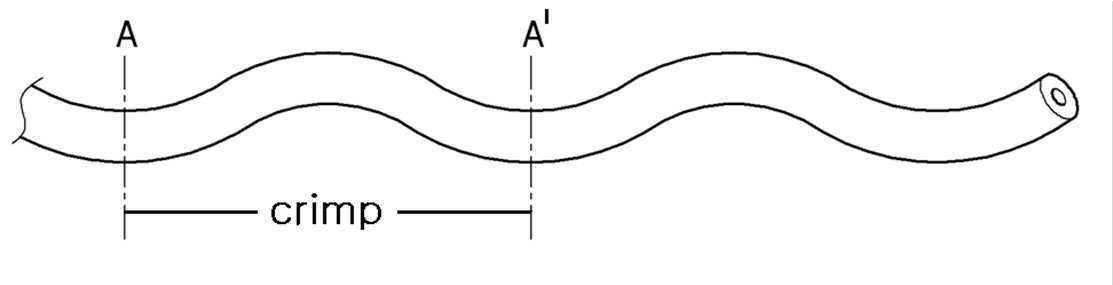