NONAQUEOUS ELECTROLYTE SECONDARY BATTERY AND METHOD OF MANUFACTURING THE SAME
1. Field of the Invention The present invention relates to a nonaqueous electrolyte secondary battery and a method of manufacturing the same. 2. Description of Related Art The importance of nonaqueous electrolyte secondary batteries such as a lithium ion secondary battery has increased as a power supply, for example, a vehicle-mounted power supply or a power supply for a PC, a portable device, or the like. In particular, a lithium ion secondary battery is preferably used as a vehicle-mounted power supply with high output because it is light-weight and has high energy density. As a structure of such a battery, a battery structure is known including a wound electrode body in which a sheet-shaped positive electrode and a sheet-shaped negative electrode are laminated and wound together with a separator. In addition, a metal case is mainly used as a battery case from the viewpoint of obtaining high physical strength. When a metal case is used, typically, an electrode body is covered with an insulating film to insulate the battery case and the electrode body from each other. For example, Japanese Patent Application Publication No. 2010-287456 (JP 2010-287456 A) discloses a battery including an electrode body and a battery case, in which an insulating film is disposed between the electrode body and the battery case. In a typical example of one of the nonaqueous electrolyte secondary batteries, the battery is charged and discharged by charge carriers (for example, lithium ions) moving between a positive electrode and a negative electrode of an electrode body, in which the electrode body is impregnated with a nonaqueous electrolytic solution, and the charge carriers are contained in the nonaqueous electrolytic solution. However, depending on charging-discharging conditions, the electrode body may generate heat. When the electrode body generates heat, the nonaqueous electrolytic solution is heated and expands and thus may flow out of the electrode body. Particularly in a nonaqueous electrolyte secondary battery used as a drive power supply for a vehicle, high-rate charging and discharging is performed. Therefore, the expanded nonaqueous electrolytic solution is likely to flow out of the electrode body. It is difficult to impregnate the nonaqueous electrolytic solution, which has been flown out of the electrode body, into the electrode body again even after the volume thereof returns to the original state due to a decrease in the temperature of the electrode body. Therefore, the amount of the nonaqueous electrolytic solution in the electrode body may decrease, or the concentration of the nonaqueous electrolytic solution may become uneven. Such a decrease in the amount of the nonaqueous electrolytic solution in the electrode body, unevenness in concentration, and the like may cause an increase in the internal resistance of a secondary battery including the electrode body and a decrease in the capacity retention thereof (that is, a decrease in the cycle characteristics). In order to solve the above-described problems, Japanese Patent Application Publication No. 2013-235795 (JP 2013-235795 A) discloses a technique of increasing the swelling degrees of active material layers of a positive electrode and a negative electrode at opposite end portions of a wound electrode body in a winding axial direction, in which the opposite end portions may form an impregnation port and an outflow port for a nonaqueous electrolytic solution. According to the technique disclosed in JP 2013-235795 A, since the active material layers at the opposite end portions are swollen by being impregnated with the nonaqueous electrolytic solution, the nonaqueous electrolytic solution is prevented from flowing out of the wound electrode body. However, in the wound electrode body having such a configuration, the active material layers at the opposite end portions start to become swollen from the start of the impregnation of the nonaqueous electrolytic solution, which may block the impregnation of the nonaqueous electrolytic solution into the wound electrode body. The invention has been made to provide a nonaqueous electrolyte secondary battery and a method of manufacturing the same, in which a nonaqueous electrolytic solution is prevented from flowing out of an electrode body while being impregnated into the electrode body. According to a first aspect of the invention, there is provided a nonaqueous electrolyte secondary battery including: an electrode body; a nonaqueous electrolytic solution; a battery case; and a bag-shaped film. The electrode body has a laminate structure in which a positive electrode and a negative electrode are laminated. The battery case accommodates the electrode body and the nonaqueous electrolytic solution. The bag-shaped film covers the electrode body to insulate the electrode body and an inner wall of the battery case from each other. An inner pressure of the battery case is adjusted to be 0.14 MPa to 0.23 MPa. According to the first aspect of the invention, the inner pressure of the battery case is appropriately adjusted. As a result, a decrease in the amount of the electrolytic solution in the electrode body after high-rate charging and discharging can be prevented. In addition, since the inside of the battery case is in the appropriate pressure state, the electrolytic solution discharged from the electrode body due to high-rate charging and discharging is promoted to be impregnated into the electrode body again. As a result, an increase in reaction resistance after high-rate charging and discharging can be suppressed, and high-rate cycle characteristics can be improved. In the first aspect of the invention, an internal space of the battery case may contain carbon monoxide. According to the above-described configuration, since gas is present in the internal space of the battery, the above-described pressure state can be suitably realized. Since the gas is carbon monoxide, the carbon monoxide is not likely to be dissolved in the nonaqueous electrolytic solution, and thus the above-described pressure state can be suitably maintained. In the first aspect of the invention, the battery case may have a flat square shape. The positive electrode and the negative electrode may have an elongated shape. The positive electrode and the negative electrode may be laminated with a separator interposed between the positive electrode and the negative electrode. The electrode body may be a flat wound electrode body in which the positive electrode, the negative electrode, and the separator are wound in a flat shape. The battery case may have a wide side surface and a narrow side surface. The electrode body may be disposed such that a winding axial direction of the electrode body is a horizontal direction of the wide side surface. A ratio of a dimension of the electrode body in a vertical direction of the wide side surface to a dimension of the electrode body in the horizontal direction may be 0.5 or less. According to the above-described configuration, the nonaqueous electrolytic solution is not likely to be discharged from the wound electrode body during high-rate charging and discharging and the like. As a result, an increase in the reaction resistance after high-rate charging and discharging can be further suppressed. In the first aspect of the invention, the bag-shaped film may have an opening that is positioned on an upper side of the battery case and may be formed of one sheet-shaped insulating film. The insulating film has at least a bag bottom portion, a first wide side surface portion, a second wide side surface portion, a first narrow side surface portion, a second narrow side surface portion, a third narrow side surface portion, a fourth narrow side surface portion, and a movement blocking mechanism, the first wide side surface portion and the second wide side surface portion may be folded centering on the bag bottom portion. The first narrow side surface portion and the second narrow side surface portion may extend from the first wide side surface portion to the second wide side surface portion. The third narrow side surface portion and the fourth narrow side surface portion may extend from the second wide side surface portion to the first wide side surface portion. The first narrow side surface portion and the second narrow side surface portion may be joined to the third narrow side surface portion and the fourth narrow side surface portion, respectively. The movement blocking mechanism may be surrounded by the bag bottom portion, the first narrow side surface portion, and the third narrow side surface portion in a state where the insulating film is unfolded as a sheet. The movement blocking mechanism may be configured to block at least a portion of a gap of the bag-shaped film through which an inside and an outside of the bag-shaped film are communicated with each other. According to the above-described configuration, even when the nonaqueous electrolytic solution is discharged from the electrode body due to high-rate charging and discharging, the nonaqueous electrolytic solution is prevented from flowing out of the bag-shaped film and can be held in the bag-shaped film. As a result, the reimpregnation of the electrolytic solution discharged from the electrode body due to high-rate charging and discharging can be further promoted. In the above-described configuration, the movement blocking mechanism may include an extending portion. The extending portion may extend from the bag bottom portion and may be folded to overlap lower ends of the first narrow side surface portion and the third narrow side surface portion. According to the above-described configuration, the bag-shaped film can loosely block the gap, which is formed among the bag bottom portion, the first narrow side surface portion and the third narrow side surface portion, with the extending portion extending from the bag bottom portion. As a result, the electrolytic solution can be suitably prevented from flowing out of the bag-shaped film. Further, the reimpregnation of the electrolytic solution discharged from the electrode body due to high-rate charging and discharging can be suitably promoted. In the above-described configuration, the extending portion may be joined to at least one of the first narrow side surface portion and the third narrow side surface portion. According to the above-described configuration, the bag-shaped film can completely block the gap among the bag bottom portion, the first narrow side surface portion and the third narrow side surface portion. As a result, the electrolytic solution can be completely prevented from flowing out of the bag-shaped film. Further, the reimpregnation of the electrolytic solution discharged from the electrode body due to high-rate charging and discharging can be more reliably promoted. In the first aspect of the invention, the nonaqueous electrolytic solution may contain a carbon monoxide producing agent. The carbon monoxide producing agent may be an oxalato complex compound containing at least one of phosphorus and boron as a constituent element. The oxalato complex compound contains an oxalate ion (C2O42−) in the molecular structure thereof. When this oxalate ion is reduced and degraded, gas (CO and CO2) are produced. The oxalato complex can be degraded when the battery is charged and discharged. Accordingly, according to the above-described configuration, the inside of the battery case after being blocked can be easily made to be in the above-described pressure state. The oxalato complex compound is reduced and degraded on the surface of the positive electrode, and a coating film containing at least one of phosphorus and boron is formed on the surface of the negative electrode. Accordingly, in the first aspect of the invention, it is preferable that the above-described coating film is formed on the surface of the negative electrode. According to a second aspect of the invention, there is provided a method of manufacturing a nonaqueous electrolyte secondary battery. This method includes allowing an insulating bag-shaped film to accommodate an electrode body having a laminate structure where a positive electrode and a negative electrode are laminated; allowing a battery case to accommodate the electrode body, which electrode body is accommodated in the bag-shaped film, and a nonaqueous electrolytic solution; and adjusting an inner pressure of the battery case to be 0.14 MPa to 0.23 MPa. According to the nonaqueous electrolyte secondary battery manufactured using the above-described method, a decrease in the amount of the electrolytic solution in the electrode body after high-rate charging and discharging is prevented, and an increase in the reaction resistance after high-rate charging and discharging is suppressed. In addition, since the inside of the battery case is in the appropriate pressure state, the electrolytic solution discharged from the electrode body due to high-rate charging and discharging is promoted to be impregnated into the electrode body again. The method according to the second aspect of the invention may further include: forming the battery case in a flat square shape having a wide side surface and a narrow side surface; forming each of the positive electrode and the negative electrode into an elongated shape; laminating the elongated positive electrode and the elongated negative electrode with a separator interposed between the positive electrode and the negative electrode; winding the electrode body in a flat shape; forming the electrode body such that a ratio of a dimension of the electrode body in a vertical direction of the wide side surface to a dimension of the electrode body in a horizontal direction of the wide side surface is 0.5 or less; and disposing the electrode body such that a winding axial direction of the electrode body is the horizontal direction. According to the nonaqueous electrolyte secondary battery manufactured using the above-described method, the nonaqueous electrolytic solution is not likely to be discharged from the electrode body during high-rate charging and discharging and the like. That is, a nonaqueous electrolyte secondary battery can be manufactured in which an increase in the resistance due to outflow of the electrolytic solution is suppressed. The method according to the second aspect of the invention may further include: disposing an opening of the bag-shaped film on an upper side of the battery case; and forming one sheet-shaped insulating film that has at least a bag bottom portion, a first wide side surface portion, a second wide side surface portion, a first narrow side surface portion, a second narrow side surface portion, a third narrow side surface portion, a fourth narrow side surface portion, and a movement blocking mechanism. In this step, the first narrow side surface portion and the second narrow side surface portion extend from the first wide side surface portion in a width direction of the first wide side surface portion. The third narrow side surface portion and the fourth narrow side surface portion extend from the second wide side surface portion in a width direction of the second wide side surface portion. The movement blocking mechanism is surrounded by the bag bottom portion, the first narrow side surface portion, and the third narrow side surface portion in a state where the insulating film is unfolded as a sheet. In addition to the above steps, the method may further include forming the bag-shaped film of the insulating film; folding the first wide side surface portion and the second wide side surface portion centering on the bag bottom portion; folding back the first narrow side surface portion and the second narrow side surface portion toward the first wide side surface portion; folding back the third narrow side surface portion and the fourth narrow side surface portion toward the second wide side surface portion; joining the first narrow side surface portion and the second narrow side surface portion to the third narrow side surface portion and the fourth narrow side surface portion, respectively; and disposing the movement blocking mechanism so as to block at least a portion of a gap of the bag-shaped film through which an inside and an outside of the bag-shaped film are communicated with each other. According to the nonaqueous electrolyte secondary battery manufactured using the above-described method, even when the nonaqueous electrolytic solution is discharged from the electrode body due to high-rate charging and discharging, the nonaqueous electrolytic solution can be held in the bag-shaped film. Accordingly, the electrolytic solution can be prevented from flowing out of the bag-shaped film while maintaining the inner pressure of the battery to be appropriately high. As a result, the reimpregnation of the electrolytic solution discharged from the electrode body due to high-rate charging and discharging can be further promoted. The method according to the second aspect of the invention may further include: introducing a carbon monoxide producing agent into the battery case, the carbon monoxide producing agent containing at least one of oxalato phosphate and oxalato borate. In addition, the inner pressure of the battery case may be adjusted by carbon monoxide which is produced by the carbon monoxide producing agent being degraded when the nonaqueous electrolyte secondary battery is charged. According to the nonaqueous electrolyte secondary battery manufactured using the above-described method, the inside of the battery case after being blocked can be easily made to be in the above-described pressure state. Features, advantages, and technical and industrial significance of exemplary embodiments of the invention will be described below with reference to the accompanying drawings, in which like numerals denote like elements, and wherein: Hereinafter, embodiments of the invention will be described with reference to the drawings. Matters (for example, general configurations of a battery and a method of manufacturing the same which are not characteristics of the invention) necessary to practice this invention other than those specifically referred to in this description may be understood as design matters based on the related art in the pertinent field for a person of ordinary skills in the art. The invention can be practiced based on the contents disclosed in this description and common technical knowledge in the subject field. In addition, parts or portions having the same function are represented by the same reference numerals. In each drawing, a dimensional relationship (for example, length, width, or thickness) does not reflect the actual dimensional relationship. “Secondary battery” described in this description refers to general storage devices which can be repeatedly charged and discharged and is a collective term for storage elements including so-called storage batteries such as a lithium ion secondary battery and electric double layer capacitors. In addition, “nonaqueous electrolyte secondary battery” refers to batteries including a nonaqueous electrolytic solution (typically, an electrolytic solution containing a supporting electrolyte in a nonaqueous solvent). In addition, “lithium ion secondary battery” refers to a secondary battery in which lithium ions are used as electrolyte ions, and charging and discharging are performed by electrons moving between positive and negative electrodes along with the lithium ions. In addition, an electrode active material refers to a material which can reversibly store and release chemical species (lithium ions in a lithium ion secondary battery) as charge carriers. Hereinafter, the invention will be described in detail using a flat square lithium ion secondary battery and a method of manufacturing the same as an example. The invention is not intended to be limited to the embodiments. <Lithium Ion Secondary Battery> Basically, this lithium ion secondary battery can be suitably manufactured using a method including the following steps (1) to (3): (1) allowing the insulating bag-shaped film 10 to accommodate the electrode body 20 having the laminate structure where the positive electrode 30 and the negative electrode 40 are laminated; (2) allowing the battery case 80 to accommodate the electrode body 20, which is accommodated in the bag-shaped film 10, and the nonaqueous electrolytic solution; and (3) adjusting an inner pressure of the battery case 80 to be 0.14 MPa to 0.23 MPa. 1. Accommodation of Electrode Body in Bag-Shaped Film Typically, the electrode body 20 includes the positive electrode 30 and the negative electrode 40. The positive electrode 30 and the negative electrode 40 are insulated from each other by a separator 50 being interposed therebetween. The positive and negative electrodes 30, 40 include active material layers 34, 44 on respective surfaces (respective single surfaces or both surfaces) of current collectors 32, 42. In the positive and negative electrodes 30, 40, belt-shaped current collector portions 36,46 are set in at least one of the end portions of the current collectors 32, 42 along a longitudinal direction thereof. Each of the active material layers 34, 44 is disposed on a single surface or both surfaces of each of the current collectors 32, 42 excluding the current collector portions 36, 46 set in the current collectors 32, 42. Here, “current collector portions 36, 46” may be portions of the current collectors 32, 42 where the active material layers 34, 44 are not formed. In general, the wound electrode body 20 is formed by laminating a first separator 50, the positive electrode 30, a second separator 50, and the negative electrode 40 in this order and winding this laminate around the winding axis WL. During the lamination, the negative electrode active material layer 44 is disposed so as to cover the positive electrode active material layer 34 in the width direction perpendicular to the longitudinal direction. In addition, the first and second separators 50 are arranged so as to cover the negative electrode active material layer 44 and the positive electrode active material layer 34 in the width direction. The current collector portion 36 of the positive electrode 30 and the current collector portion 46 of the negative electrode 40 are disposed so as to protrude to the opposite side of the separator 50 in the width direction. In this example, the current collector portions 36, 46 of the positive and negative electrodes protrude from opposite ends of the separator 50 in the winding axial direction in a spiral shape when seen from the winding axial direction. In addition, in this example, the current collector portions 36, 46 have a flat shape (elongated circle-like shape in cross-section) which is compressed in a direction perpendicular to the winding axis so as to correspond to the shape of the battery case 80. The shape of the wound electrode body 20 is not particularly limited as long as it corresponds to the shape of the battery case 80 to be used, and for example, may be a cylindrical shape. The positive and negative electrode current collector portions 36, 46 protruding from the separator 50 are gathered in the above-described direction perpendicular to the winding axis and are connected by welding or the like to tip end portions 64, 74 of positive and negative electrode internal terminals 62, 72 which are provided on a sealing plate 84 to face the inside of the battery case 80. Through the internal terminals 62, 72, the positive and negative electrode current collector portions 36, 46 are electrically connected to a positive electrode external connection terminal 60 and a negative electrode external connection terminal 70, respectively, which are provided on the sealing plate 84. With such a configuration, the electrode body 20 is stably disposed such that the winding axial direction faces a horizontal direction of a wide side surface of the battery case 80. According to the observation by the present inventors, even in the flat laminated electrode body, the same problems as in the wound electrode body such as insufficient impregnation of a nonaqueous electrolytic solution occur. Accordingly, the electrode body 20 may, be a so-called flat laminated electrode body having a laminate structure in which plural plate-shaped positive electrodes 30 and plural plate-shaped negative electrodes 40 (typically, as well as the separator 50) are laminated. However, the insufficient impregnation of an electrolytic solution is more likely to occur in a wound electrode body including end portions only at opposite ends of a winding axis of an electrode body, rather than in a flat laminated electrode body including end portions (that is, impregnation ports of a nonaqueous electrolytic solution) at four corners of an electrode body. That is, the effects of the invention are more significant in the wound electrode body. Accordingly, the invention disclosed herein will be described using a nonaqueous electrolyte secondary battery including the wound electrode body 20 as an example. [Positive Electrode] The positive electrode (positive electrode sheet) 30 includes a positive electrode current collector 32 and a positive electrode active material layer 34. As the positive electrode current collector 32, for example, a metal foil suitable for the positive electrode 30 may be suitably used. As the positive electrode current collector 32, for example, a belt-shaped aluminum foil having a predetermined width and a thickness of about 15 μm may be used. In the positive electrode current collector 32, as described above, the positive electrode current collector portion 36 is set along one end portion in the width direction. The positive electrode active material layer 34 is disposed on a single surface or both surfaces of the positive electrode current collector 32 excluding the positive electrode current collector portion 36 set in the positive electrode current collector 32. The positive electrode active material layer 34 is bonded onto the positive electrode current collector 32, in which particles of a positive electrode active material bind to each other through a binder. As the positive electrode active material, various materials which are used as a positive electrode active material of a lithium ion battery in the related art may be used without any particular limitation. The positive electrode active material layer 34 may further contain a conductive material. A ratio of the mass of the positive electrode active material to the total mass of the positive electrode active material layer 34 is suitably about 50 mass % or more (typically, 50 mass % to 95 mass %) and is usually preferably about 70 mass % to 95 mass %. [Negative Electrode] The negative electrode (negative electrode sheet) 40 includes a negative electrode current collector 42 and a negative electrode active material layer 44. As the negative electrode current collector 42, for example, a metal foil suitable for the negative electrode 40 may be suitably used. As the negative electrode current collector 42, for example, a belt-shaped copper foil having a predetermined width and a thickness of about 10 μm may be used. In the negative electrode current collector 42, as described above, the negative electrode current collector portion 46 is set along one end portion in the width direction. The negative electrode active material layer 44 is disposed on a single surface or both surfaces of the negative electrode current collectors 42 excluding the negative electrode current collector portion 46 set in the negative electrode current collectors 42. The negative electrode active material layer 44 is bonded onto the negative electrode current collector 42, in which particles of a negative electrode active material bind to each other through a binder. As the negative electrode active material, various materials which are used as a negative electrode active material of a lithium ion battery in the related art may be used without any particular limitation. A ratio of the mass of the negative electrode active material to the total mass of the negative electrode active material layer 44 is not particularly limited, but is suitably about 50 mass % or more and is preferably about 90 mass % to 99 mass % (for example, 95 mass % to 99 mass %). <Binder> In addition, the binder allows particles of the electrode active materials and the conductive material contained in the active material layers 34, 44 to bind to each other, or allows these particles and the positive and negative electrode current collectors 32, 42 to bind to each other. This binder is not particularly limited as long as it can exhibit the above-described functions according to the method of manufacturing the positive electrode 30 or the negative electrode 40 and the use thereof. Representatively, various resin materials can be used. Preferable examples of the binder include polyvinylidene fluoride (PVdF), polytetrafluoroethylene (PTFE), a tetrafluoroethylene-hexafluoropropylene copolymer (FEP), polyvinyl alcohol (PVA), a vinyl acetate copolymer, styrene-butadiene rubber (SBR), polyethylene oxide (PEO), and an acrylic polymer. [Separator] As shown in [Bag-Shaped Film] The wound electrode body 20, to which the positive and negative electrode current collector portions 36 and 46 are attached, including the internal terminals 62, 72 is covered with the bag-shaped film 10. Due to this bag-shaped film 10, direct contact between the wound electrode body 20 (and the internal terminals 62, 72), which is a power generating element, and the battery case 80 can be avoided, and insulation between the electrode body 20 and an inner wall of the battery case 80 can be secured. In this embodiment, the bag-shaped film 10 is formed in a bag shape having an opening on the upper side of the battery case and a closed bottom. Although described below in detail, the bag-shaped film 10 has a configuration shown in Here, the material of the bag-shaped film 10 is not particularly limited as long as it has insulating properties, which are required for this type of battery, and can function as an insulating member. For example, a synthetic resin material which has high insulating properties and high heat resistance and is not likely to be corrugated is preferably used. Specifically, for example, a polyolefin resin material such as polyethylene (PE) or polypropylene (PP) can be suitably used. The thickness of the resin material is 1 mm or less (typically 10 μm to 1000 μm) and is preferably about 100 μm to 200 μm. The material, dimension, and the like of the bag-shaped film 10 can be appropriately changed depending on the configuration conditions of battery 100 and the like. 2. Accommodation of Electrode Body in Battery Case Next, the battery case 80 accommodates the electrode body 20, which is accommodated in the bag-shaped film 10, and the nonaqueous electrolytic solution. <Battery Case> Typically, as shown in In the example shown in The material of the battery case 80 is not particularly limited, but for example, it is preferable that the battery case 80 contains a metal material as a major component because the metal material is light-weight and has high strength and superior thermal conductivity. Examples of the metal material include aluminum, iron, copper, and alloys thereof. As shown in [Nonaqueous Electrolytic Solution] As the nonaqueous electrolytic solution, a solution containing an electrolyte in an appropriate nonaqueous solvent may be used. As the electrolyte, various electrolytes or equivalents thereof which are used in a lithium ion battery in the related art may be used without any particular limitation. As the nonaqueous solvent, organic solvents such as ethylene carbonate, propylene carbonate, dimethyl carbonate, diethyl carbonate, ethyl methyl carbonate, 1,2-dimethoxyethane, 1,2-diethoxyethane, tetrahydrofuran, and 1,3-dioxolane may be used. Among these organic solvents, one kind may be used alone, or two or more kinds may be used in combination as the nonaqueous solvent. In addition, as the electrolyte (also referred to as “supporting electrolyte”), for example, a lithium salt such as LiPF6, LiBF4, LiAsF6, LiCF3SO3, LiC4F9SO3, LiN(CF3SO2)2, or LiC(CF3SO2)3may be used. For example, a nonaqueous electrolytic solution in which a mixed solvent of ethylene carbonate and diethyl carbonate (for example, mass ratio=1:1) contains LiPF6in a concentration of about 1 mol/L may be used. As the electrolyte, a gel or solid electrolyte having high ion conductivity may be used instead of the nonaqueous electrolyte. Various additives may be appropriately added to the nonaqueous electrolytic solution according to the purpose, and examples of the additives include a film forming agent such as vinylene carbonate (VC) or fluoroethylene carbonate (FEC); and an overcharge additive such as biphenyl (BP) or cyclohexylbenzene (CHB). 3. Adjustment of Inner Pressure of Battery Case In the nonaqueous electrolyte secondary battery 100 disclosed herein, the inner pressure of the battery case is adjusted to be an appropriate pressure. As long as being performed after the injection of the nonaqueous electrolytic solution, the adjustment of the inner pressure of the battery case may be performed during the sealing of the battery case 80 or may be performed using initial charging after the sealing of the battery case 80. For example, typically, the adjustment of the inner pressure may be realized using at least one of the following methods (1) and (2). Alternatively, methods other than (1) and (2) may be used. (1) Injecting appropriate gas into the battery case 80 for pressurization (2) Producing appropriate gas in the case after the sealing of the battery case 80 It is preferable that the gas realizing the above pressure state has low solubility in the nonaqueous electrolytic solution. For example, in a commonly-used nonaqueous electrolytic solution, carbon monoxide (CO) may be preferably used as a gas having low solubility. When the adjustment of the inner pressure is performed by the injection of the gas for pressurization, the following procedure may be adopted including: introducing the nonaqueous electrolytic solution into the battery case 80 through the injection port 88 in “2. Accommodation of Electrode Body in Battery Case”; injecting the gas into the battery case 80 through the injection port 88 for pressurization; and then sealing the injection port 88 with a lid. When the appropriate gas is produced in the case after the sealing of the battery case 80, the following procedure may be preferably adopted. That is, a gas producing agent is introduced into the battery case 80 in advance. The gas producing agent is reduced and degraded due to the initial charging (which may be conditioning) of the battery 100 after the sealing of the battery case 80. As a result, desired gas can be produced in the case. The gas producing agent may be introduced into the battery case 80 as it is, or may be introduced thereinto after being contained in the nonaqueous electrolytic solution or as a part of another component such as the positive electrode 30, the negative electrode 40, or the separator 50. In order to degrade the gas producing agent in an appropriate amount, it is preferable that the gas producing agent is introduced into the battery case 80 after being contained in the nonaqueous electrolytic solution or the positive electrode 30. It is preferable that the gas producing agent is a CO producing agent that produces CO having low solubility in the nonaqueous electrolytic solution as described above. Preferable examples of the CO producing agent include an oxalato complex compound having an oxalate ion (C2O42−) in the molecular structure thereof. The oxalato complex compound suitably produces gas (CO and CO2) in the battery case 80 after sealing by the oxalate ion being reduced and degraded due to initial charging. The oxalato complex compound may be used without any particular limitation, but an oxalato complex compound containing at least one of phosphorus (P) and boron (B) as a constituent element is more preferably used. Typical examples of an oxalato complex compound containing P include lithium difluorobis(oxalato)phosphate (LPFO) and lithium tris(oxalato)phosphate. Typical examples of an oxalato complex compound containing B include lithium bis(oxalato)borate and lithium difluoro(oxalato)borate. When the gas producing agent is added (used) to the nonaqueous electrolyte secondary battery, the gas producing agent remains as it is without being degraded or is degraded into a degradation product in the battery case. Accordingly, the addition of the gas producing agent can be verified by detecting the gas producing agent and/or the degradation product. The degradation product may be coating film formed on a surface of an electrode (typically, the negative electrode). Specifically, when the oxalato complex compound containing at least one of phosphorus and boron as a constituent element is used as the gas producing agent, a coating film containing at least one of phosphorus and boron may be formed on the surface of the negative electrode. The coating film can be verified by detecting phosphorus and/or boron derived from the oxalato complex compound. For example, these characteristic elements can be detected and the contents thereof can be measured based on a well-known appropriate detection method such as inductively coupled plasma atomic emission spectroscopy or X-ray absorption fine structure spectroscopy. By adjusting the inner pressure of the battery case to be in the appropriate pressure state as described above, the impregnation force is improved during the impregnation of the nonaqueous electrolytic solution into the electrode body 20, and thus the impregnation of the nonaqueous electrolytic solution into the electrode body 20 is promoted. Accordingly, the number of manufacturing steps can be reduced, the ability of the electrode body 20 to hold the nonaqueous electrolytic solution is improved, the battery can be charged and discharged due to a sufficient amount of electrolyte, and further a battery reaction can be realized with low resistance. In addition, when the battery 100 constructed as described above is charged and discharged at a high rate, the wound electrode body 20 may generate heat. When the electrode body 20 generates heat, the nonaqueous electrolytic solution impregnated into the electrode body is heated and expands and thus may flow out of the electrode body. In the battery 100 disclosed herein, the inner pressure of the battery case is adjusted to be the appropriate pressure. Therefore, during the heat generation of the electrode body 20, the nonaqueous electrolytic solution can be prevented from flowing out of the electrode body. Further, when the temperature of the electrode body 20 decreases after the high-rate charging and discharging, the volume of the nonaqueous electrolytic solution returns to the original state. In the battery 100 disclosed herein, the inner pressure of the battery case is adjusted to be the appropriate pressure. Therefore, the electrolytic solution flowing out of the electrode body 20 after high-rate charging and discharging can be promoted to be impregnated into the electrode body 20 again. As a result, a resistance increase during and after high-rate charging and discharging can be suppressed to be low, and battery performance can be maintained to be high for a long period of time. The impregnation of the nonaqueous electrolytic solution can be promoted as long as the inner pressure of the battery case is a little higher than the pressure of an atmosphere (typically, the atmospheric pressure; about 0.1 MPa) during the impregnation. When the pressure of the atmosphere is as described above, the inner pressure is preferably about 0.12 MPa or higher and more preferably 0.13 MPa or higher (for example, 0.14 MPa or higher). The upper limit of the inner pressure is not particularly limited, but for example, when the inner pressure is excessively high, the battery resistance may increase. In addition, it is necessary to consider battery designs such as the strength and safety of the battery case and the opening pressure of the safety valve. Accordingly, the upper limit of the inner pressure is 0.25 MPa or lower and is, for example, preferably 0.23 MPa or lower. [Form of Bag-Shaped Film] The form (structure) of the bag-shaped film 10 may greatly affect the effect of promoting the impregnation of the nonaqueous electrolytic solution and the effect of suppressing the resistance increase due to high-rate charging and discharging. Hereinafter, these effects and the form of the bag-shaped film 10 will be described. In regard to the insulating film 10 in the unfolded state shown in In the bag-shaped film 10 shown in In addition, the movement blocking mechanism may be configured of the extending portion 18 shown in The extending dimension of the extending portion 18 is not limited to be h/2 as described above and can be appropriate adjusted, for example, in a range from more than 0 to h. As the extending dimension decreases from h/2, the dimension of a portion where the extending portion 18 and the narrow side surface portions 16 On the other hand, the movement blocking mechanism may be formed, for example, by joining the bag bottom portion 12 and the narrow side surface portions 16 As described above, the movement blocking mechanism is provided between the bag bottom portion 12 and the narrow side surface portions 16 The insulating film 10 in the unfolded state can be easily folded (assembled) into the bag-shaped film 10, for example, using a film folding tool 200. Specifically, for example, as shown in [Aspect Ratio of Electrode Body] The impregnating ability of the nonaqueous electrolytic solution into the flat wound electrode body 20 can be improved by appropriately adjusting the inner pressure of the battery case 80 as described above, but can be further improved by controlling the form of the flat wound electrode body 20. That is, in the wound electrode body, the impregnation of the nonaqueous electrolytic solution progresses along the winding axial direction. Accordingly, when the dimension of the wound electrode body in the vertical direction perpendicular to the winding axial direction, which also functions as the impregnation port of the nonaqueous electrolytic solution, is greater than the dimension of the wound electrode body in the horizontal direction (winding axial direction), the impregnation of the nonaqueous electrolytic solution is likely to be promoted. However, the impregnation port may function as a discharge port during the swelling of the nonaqueous electrolytic solution. Accordingly, in order to prevent the nonaqueous electrolytic solution from being discharged during the swelling of the nonaqueous electrolytic solution, a ratio of the dimension of the wound electrode body 20 in the vertical direction to the dimension of the wound electrode body 20 in the horizontal direction, that is, an aspect ratio (vertical/horizontal) is preferably 0.5 or less. The aspect ratio is preferably 0.48 or less (for example, 0.45 or less). However, as the aspect ratio decreases, the time required for the impregnation of the nonaqueous electrolytic solution during the construction of the battery increases, which decreases the manufacturing efficiency. In addition, when nonaqueous electrolytic solution is discharged from the wound electrode body 20 during the construction of the battery, it is difficult to impregnate the nonaqueous electrolytic solution into the wound electrode body 20 again. Therefore, the lower limit of the aspect ratio is preferably 0.2 or more and more preferably 0.23 or more (for example, 0.25 or more). Hereinafter, several examples relating to the invention will be described, but the examples are not intended to limit the invention. LiNi1/3Co1/3Mn1/3O2(average particle size: 10 μm) as a positive electrode active material; acetylene black (AB) as a conductive material; polyvinylidene fluoride (PVdF) as a binder were weighed at a weight ratio of 90:8:2. These materials were dispersed in NMP to prepare a positive electrode paste. This paste was supplied onto both surfaces of an elongated sheet-shaped positive electrode current collector (aluminum foil) having a thickness of 15 μm such that the coating weight was 20 mg/cm2(in terms of solid content), followed by drying. As a result, a positive electrode sheet was prepared. By rolling this positive electrode sheet, the thickness thereof was adjusted to 130 μm, and the active material layer density was adjusted to 2.8 g/cm3. A negative electrode active material (natural graphite: C, average particle size: 5 μm); styrene-butadiene rubber (SBR) as a binder; and carboxymethyl cellulose (CMC) as a thickener were weighed at a weight ratio of 98:1:1, and were dispersed in ion exchange water. As a result, a negative electrode paste was prepared. This paste was supplied onto both surfaces of an elongated sheet-shaped negative electrode current collector (copper foil) having a thickness of 10 μm such that the coating weight was 14 mg/cm2(in terms of solid content), followed by drying. As a result, a negative electrode sheet was prepared. By rolling this negative electrode sheet, the thickness thereof was adjusted to 100 um, and the active material layer density was adjusted to 1.4 g/cm3. A separator was interposed between the positive electrode and the negative electrode prepared as described above, and this laminate was wound to have a cross-section having an elongated circle-like shape. As a result, a flat wound electrode body was prepared. The separator had a three-layer structure in which a porous polypropylene layer having a thickness of 20 μm was laminated on both surfaces of a porous polyethylene layer. Positive and negative current collector portions integrated into a lid of a battery case were welded to the positive electrode current collector and the negative electrode current collector of the flat wound electrode body, respectively. Next, the flat wound electrode body was accommodated in an insulating bag-shaped film. The bag-shaped film was constructed by folding an insulating film having an unfolded shape of A case body of the battery case accommodated the flat wound electrode body which was accommodated in the bag-shaped film, and the lid and the case body were welded to seal the case. As the battery case, a flat square battery case formed of an aluminum alloy having a length of 75 mm, a width of 120 mm, a thickness of 15 mm, and a case thickness of 1 mm was used. A nonaqueous electrolytic solution was injected through an electrolytic solution injection port provided on the lid. Here, in the nonaqueous electrolytic solution, 1 mol/L of LiPF6as a supporting electrolyte was dissolved in a mixed solvent containing EC, DMC, and EMC at a volume ratio of 3:4:3. After the injection of the nonaqueous electrolytic solution, CO gas was blown into the battery case to change the inner pressure of the battery to 12 values in a range of 0.12 MPa to 0.375 MPa. Then, the liquid injection port was sealed. As a result, batteries (nonaqueous electrolyte secondary batteries for evaluation) having 12 different values of the inner pressure of the case were prepared. The theoretical capacity of the battery was 4 Ah. After performing conditioning on the batteries under the following conditions, the initial resistance and the resistance ratio after a high-rate cycle test were measured. The following charging-discharging operations (1) and (2) were repeatedly performed on the batteries in 3 cycles at a temperature of 25° C. to perform a conditioning treatment. (1) The batteries were charged to 4.2 V at a constant current (CC) at a rate of 1/3 C, and then the operation was stopped for 10 minutes. (2) The batteries were discharged to 3.0 V at a constant current (CC) at a rate of 1/3 C, and then the operation was stopped for 10 minutes. (Measurement of Initial Resistance) The batteries were charged to SOC 20% at a constant current (CC) at a temperature of 25° C. The batteries whose SOC was adjusted to 20% were discharged to 3 V at a constant current (CC) at a discharge rate of 10 C, and the voltage drop amount after 10 seconds from discharging was measured. The IV resistance was calculated by dividing the measured voltage drop amount by the corresponding the current value and was set as the initial resistance. (High-Rate Cycle Test) The SOC of the batteries after the initial resistance measurement was adjusted to 100% at a temperature of 25° C., and then the following charging-discharging operations (1) and (2) were repeatedly performed thereon in 1200 cycles to perform the high-rate cycle test. The electrolytic solution was promoted to be discharged from the electrode body by swelling the electrolytic solution. (1) The batteries were charged at a constant current (CC) of 75 A for 40 seconds, and the operation was stopped for 5 seconds. (2) The batteries were charged to SOC 100% at a constant current (CC) of 10 A, and the operation was stopped for 5 seconds. After the high-rate cycle test, the IV resistance was measured using the same method as in the measurement of the initial resistance. The reaction resistance ratio was calculated based on the following equation. As shown in 1: The impregnation of the electrolytic solution into the electrode body was promoted. 2: The electrolytic solution impregnated into the electrode body was prevented from being discharged from the electrode body. 3: The reimpregnation of the electrolytic solution, discharged from the electrode body, into the electrode body was promoted. The reason why the above-described effects were decreased along with an increase in the inner pressure is considered to be that the initial resistance and the reaction resistance ratio were increased by gas clogging or the like in the electrode body. It was verified from the above result that the initial resistance was reliably suppressed when the inner pressure was in a range of about 0.12 MPa to 0.25 MPa. In addition, it was verified that the resistance ratio after the high-rate cycle test tended to be suppressed when the inner pressure was in a range of about 0.12 MPa or higher. It was found that these effects were more efficiently obtained at the same time when the inner pressure of the battery was about 0.14 MPa to 0.23 MPa. In this test example, the shape of the flat wound electrode body and the form of the insulating bag-shaped film were changed, and LiPF2(C2O4)2having a concentration of 0.04 mol/L was added to the nonaqueous electrolytic solution. Under the same conditions as those of Test Example 1 other than the above-described conditions, nonaqueous electrolyte secondary batteries having 28 forms in total were prepared. That is, when the winding axial direction was the horizontal direction, and the long diameter direction of the elongated circle-like cross-section is the vertical direction, the width of the winding axis was adjusted such that the aspect ratio (vertical/horizontal) was changed to seven different values in a range of 0.3 to 0.8. As a result, wound electrode bodies were prepared. In addition, insulating films having four unfolded shapes shown in (High-Rate Cycle Test) A conditioning treatment was performed on the prepared 28 batteries under the same conditions as those of Test Example 1. All the inner pressures of the batteries after the conditioning treatment were about 0.18 MPa when measured using an inner pressure measuring gauge. The reason is considered to be as follows: LPFO contained in the batteries was degraded due to the conditioning treatment (initial charging), and CO gas was produced in the battery cases. Next, the initial resistances of these batteries were measured and were provided for the high-rate cycle test, and then the resistance ratio was measured. The results were shown in As shown in In addition, it was verified from Hereinabove, the lithium ion secondary battery according to the embodiment of the invention has been described. However, the nonaqueous electrolyte secondary battery according to the invention is not limited to the above-described embodiment, and various modifications can be made. For example, the electrolytic solution movement blocking mechanism that is provided among the bottom surface portion and the narrow side surface portions of the bag-shaped film is not limited to the above-described examples as long as it prevents the movement of the electrolytic solution between the inside and outside of the bag-shaped film, and various modifications can be made. In addition, as described above, the invention may contribute to the improvement of the performance of nonaqueous electrolyte secondary batteries (for example, a lithium ion secondary battery). The invention is suitably applicable to a lithium ion secondary battery as a drive power supply for a vehicle such as a hybrid vehicle or an electric vehicle. The drive power supply for a vehicle may be a battery pack in which plural secondary batteries are combined. A nonaqueous electrolyte secondary battery includes an electrode body (20), a nonaqueous electrolytic solution, a battery case (80), and a bag-shaped film (10). The electrode body has a laminate structure in which a positive electrode (30) and a negative electrode (40) are laminated. The battery case accommodates the electrode body and the nonaqueous electrolytic solution. The bag-shaped film covers the electrode body to insulate the electrode body and an inner wall of the battery case from each other. An inner pressure of the battery case is adjusted to be 0.14 MPa to 0.23 MPa. 1. A nonaqueous electrolyte secondary battery comprising:
an electrode body having a laminate structure in which a positive electrode and a negative electrode are laminated; a nonaqueous electrolytic solution; a battery case that accommodates the electrode body and the nonaqueous electrolytic solution; and a bag-shaped film that covers the electrode body to insulate the electrode body and an inner wall of the battery case from each other, wherein an inner pressure of the battery case is adjusted to be 0.14 MPa to 0.23 MPa wherein the bag-shaped film has an opening that is positioned on an upper side of the battery case and is formed of one sheet-shaped insulating film, the insulating film has at least a bag bottom portion, a first wide side surface portion, a second wide side surface portion, a first narrow side surface portion, a second narrow side surface portion, a third narrow side surface portion, a fourth narrow side surface portion, and a movement blocking mechanism, the first wide side surface portion and the second wide side surface portion are folded centering on the bag bottom portion, the first narrow side surface portion and the second narrow side surface portion extend from the first wide side surface portion to the second wide side surface portion, the third narrow side surface portion and the fourth narrow side surface portion extend from the second wide side surface portion to the first wide side surface portion, the first narrow side surface portion and the second narrow side surface portion are joined to the third narrow side surface portion and the fourth narrow side surface portion, respectively, the movement blocking mechanism is surrounded by the bag bottom portion, the first narrow side surface portion, and the third narrow side surface portion in a state where the insulating film is unfolded as a sheet, and the movement blocking mechanism is configured to block at least a portion of a gap of the bag-shaped film through which an inside and an outside of the bag-shaped film are communicated with each other. 2. The nonaqueous electrolyte secondary battery according to an internal space of the battery case contains carbon monoxide. 3. The nonaqueous electrolyte secondary battery according to the battery case has a flat square shape, the positive electrode and the negative electrode have an elongated shape, the positive electrode and the negative electrode are laminated with a separator interposed between the positive electrode and the negative electrode, the electrode body is a flat wound electrode body in which the positive electrode, the negative electrode, and the separator are wound in a flat shape, the battery case has a wide side surface and a narrow side surface, the electrode body is disposed such that a winding axial direction of the electrode body is a horizontal direction of the wide side surface, and a ratio of a dimension of the electrode body in a vertical direction of the wide side surface to a dimension of the electrode body in the horizontal direction is 0.5 or less. 4. The nonaqueous electrolyte secondary battery according to the wide side surface and the narrow side surface are connected to a side of the battery case, the horizontal direction is perpendicular to the side of the battery case and is parallel to the wide side surface, and the vertical direction is perpendicular to the horizontal direction and is parallel to the wide side surface. 5. (canceled) 6. The nonaqueous electrolyte secondary battery according to the movement blocking mechanism includes an extending portion, and the extending portion extends from the bag bottom portion and is folded to overlap lower ends of the first narrow side surface portion and the third narrow side surface portion. 7. The nonaqueous electrolyte secondary battery according to the extending portion is joined to at least one of the first narrow side surface portion and the third narrow side surface portion. 8. The nonaqueous electrolyte secondary battery according to the nonaqueous electrolytic solution contains a carbon monoxide producing agent, and the carbon monoxide producing agent is an oxalato complex compound containing at least one of phosphorus and boron as a constituent element. 9. The nonaqueous electrolyte secondary battery according to a coating film containing at least one of phosphorus and boron is formed on a surface of the negative electrode. 10. A method of manufacturing a nonaqueous electrolyte secondary battery, the method comprising:
allowing an insulating bag-shaped film to accommodate an electrode body having a laminate structure where a positive electrode and a negative electrode are laminated; allowing a battery case to accommodate the electrode body, which electrode body is accommodated in the bag-shaped film, and a nonaqueous electrolytic solution; and adjusting an inner pressure of the battery case to be 0.14 MPa to 0.23 MPa; disposing an opening of the bag-shaped film on an upper side of the battery case; and forming one sheet-shaped insulating film that has at least a bag bottom portion, a first wide side surface portion, a second wide side surface portion, a first narrow side surface portion, a second narrow side surface portion, a third narrow side surface portion, a fourth narrow side surface portion, and a movement blocking mechanism, wherein
the first narrow side surface portion and the second narrow side surface portion extend from the first wide side surface portion in a width direction of the first wide side surface portion, the third narrow side surface portion and the fourth narrow side surface portion extend from the second wide side surface portion in a width direction of the second wide side surface portion, and the movement blocking mechanism is surrounded by the bag bottom portion, the first narrow side surface portion, and the third narrow side surface portion in a state where the insulating film is unfolded as a sheet; forming the bag-shaped film of the insulating film; folding the first wide side surface portion and the second wide side surface portion centering on the bag bottom portion; folding back the first narrow side surface portion and the second narrow side surface portion toward the first wide side surface portion; folding back the third narrow side surface portion and the fourth narrow side surface portion toward the second wide side surface portion; joining the first narrow side surface portion and the second narrow side surface portion to the third narrow side surface portion and the fourth narrow side surface portion, respectively; and disposing the movement blocking mechanism so as to block at least a portion of a gap of the bag-shaped film through which an inside and an outside of the bag-shaped film are communicated with each other. 11. The method according to forming the battery case in a flat square shape having a wide side surface and a narrow side surface; forming each of the positive electrode and the negative electrode into an elongated shape; laminating the elongated positive electrode and the elongated negative electrode with a separator interposed between the positive electrode and the negative electrode; winding the electrode body in a flat shape; forming the electrode body such that a ratio of a dimension of the electrode body in a vertical direction of the wide side surface to a dimension of the electrode body in a horizontal direction of the wide side surface is 0.5 or less; and disposing the electrode body such that a winding axial direction of the electrode body is the horizontal direction. 12. (canceled) 13. The method according to introducing a carbon monoxide producing agent into the battery case, the carbon monoxide producing agent containing at least one of oxalato phosphate and oxalato borate, wherein the inner pressure of the battery case is adjusted by carbon monoxide which is produced by the carbon monoxide producing agent being degraded when the nonaqueous electrolyte secondary battery is charged.BACKGROUND OF THE INVENTION
SUMMARY OF THE INVENTION
BRIEF DESCRIPTION OF THE DRAWINGS
DETAILED DESCRIPTION OF EMBODIMENTS
[Electrode Body]
Test Example 1
Inner Pressure of Battery
(Conditioning)
Reaction Resistance ratio (%)=(Resistance after High-Rate Cycle Test)÷(Initial Resistance)×100Test Example 2
Shape of Electrode Body and Electrolytic Solution Movement Blocking Mechanism
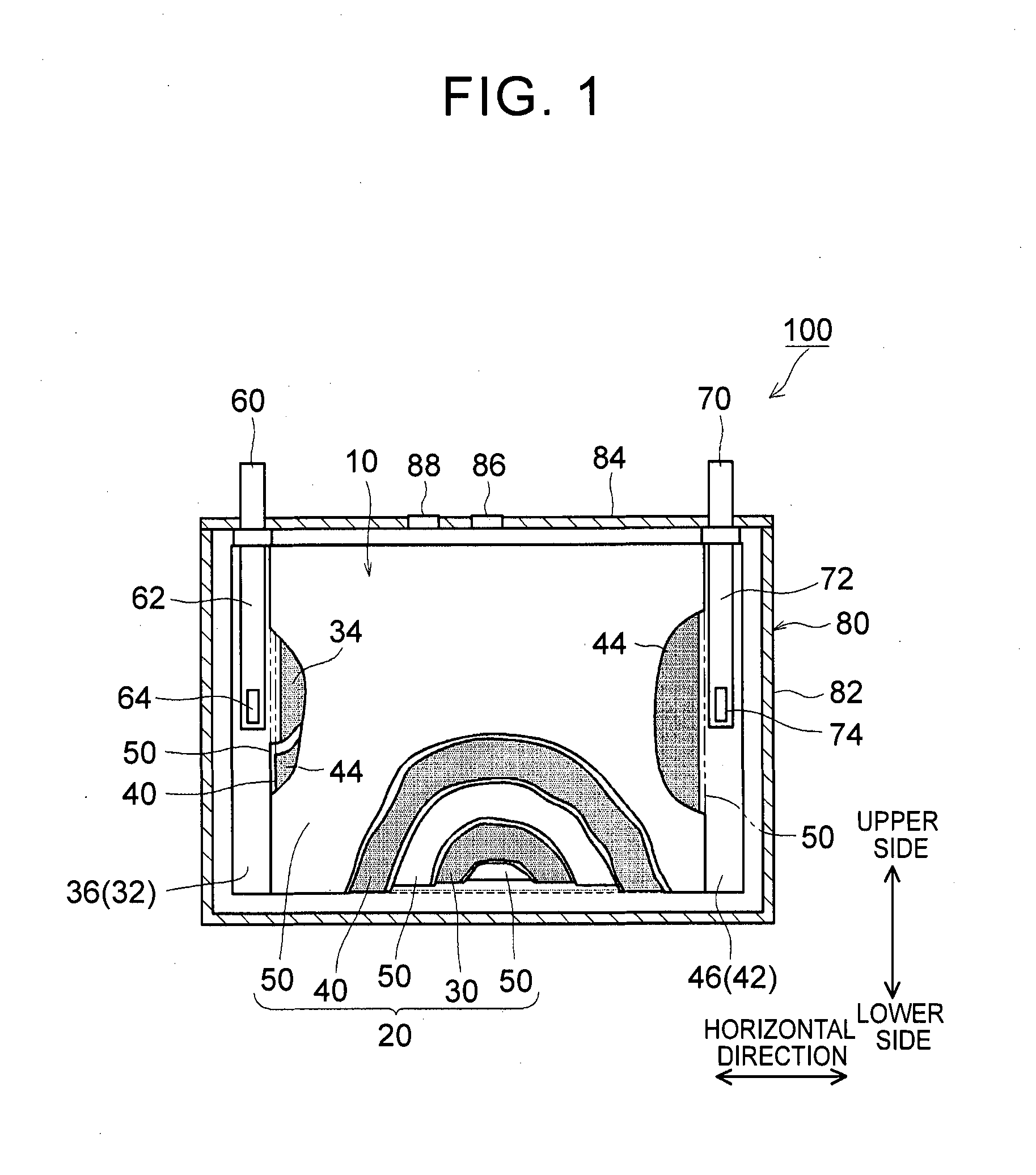
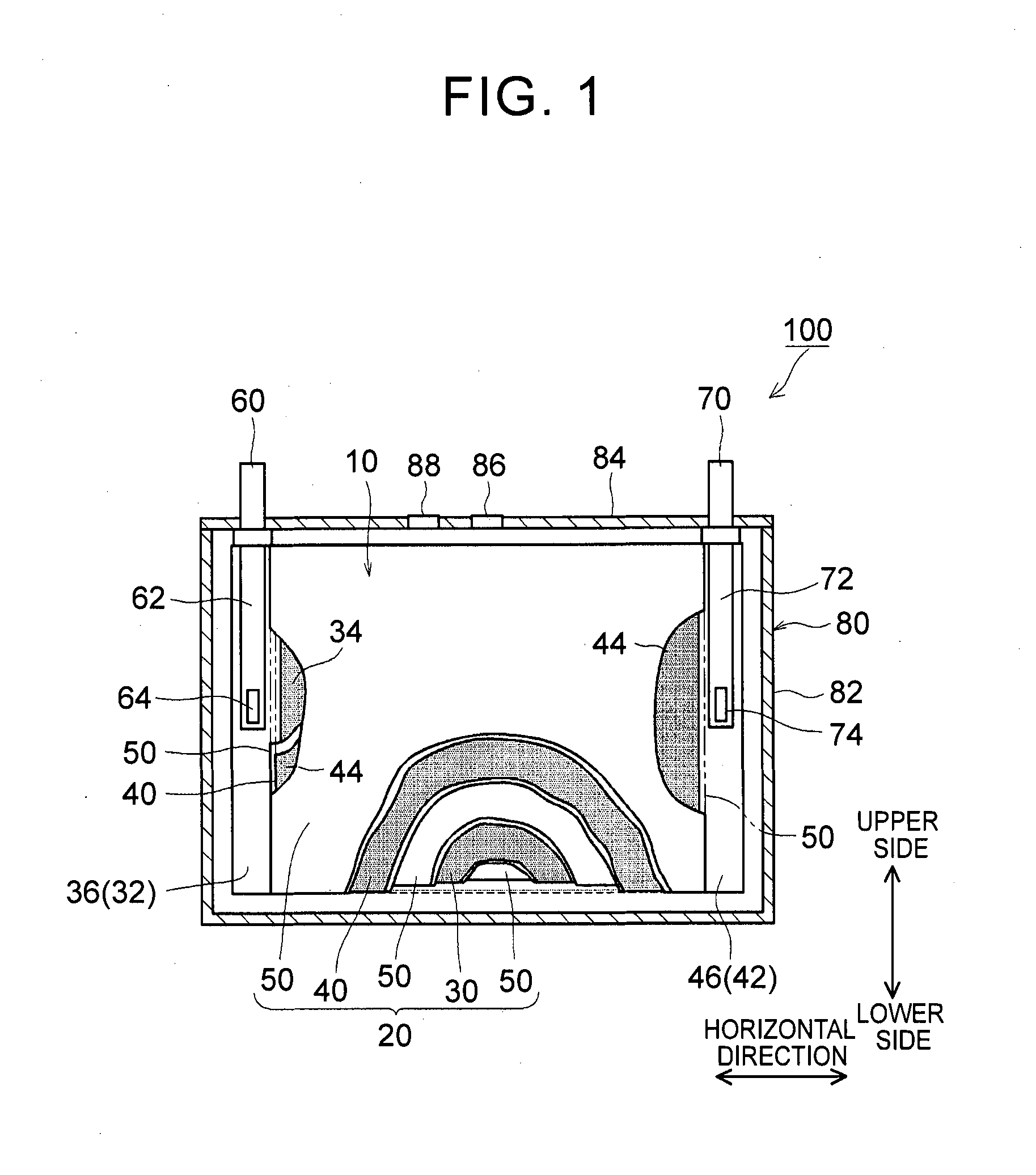
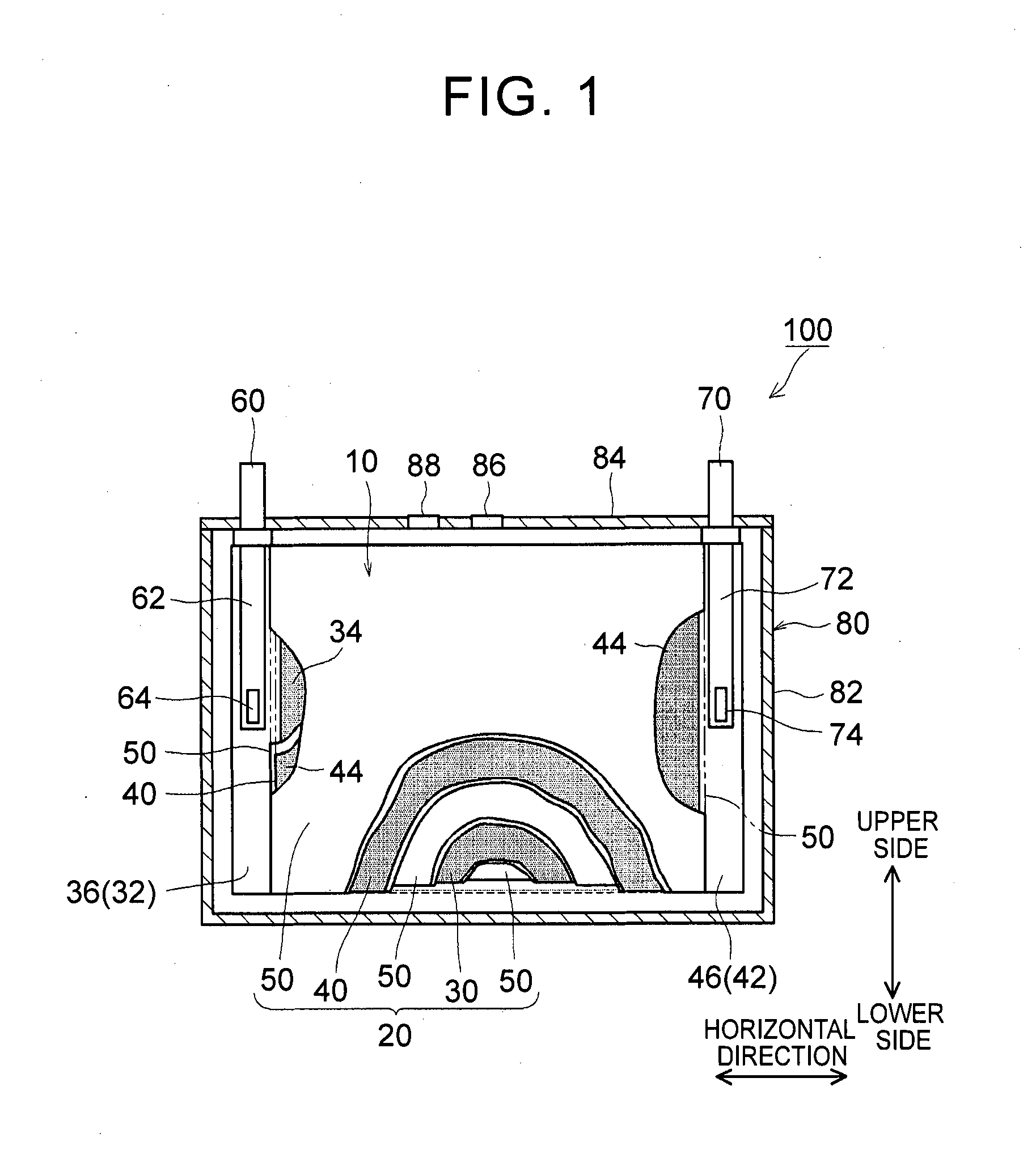
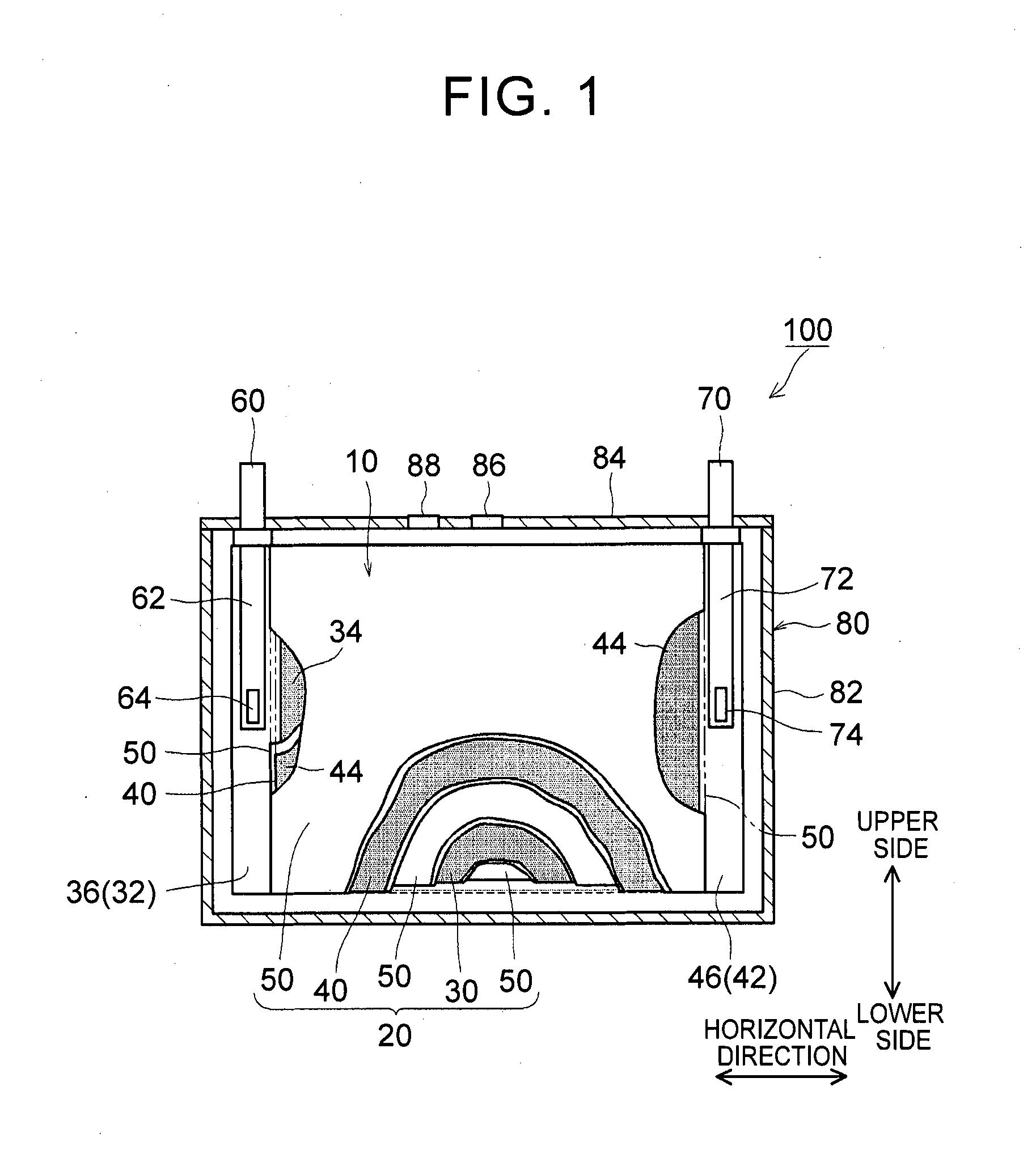
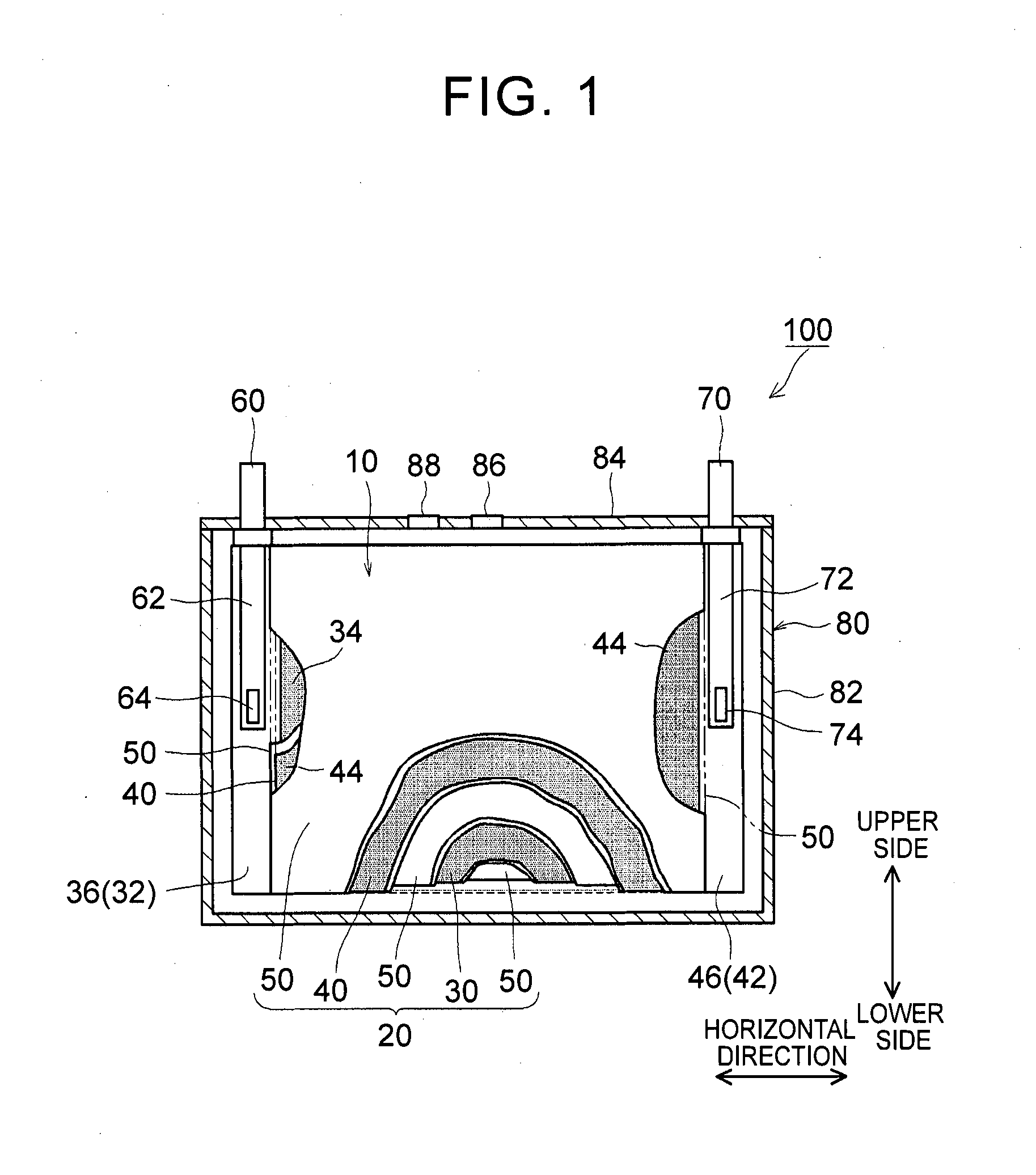
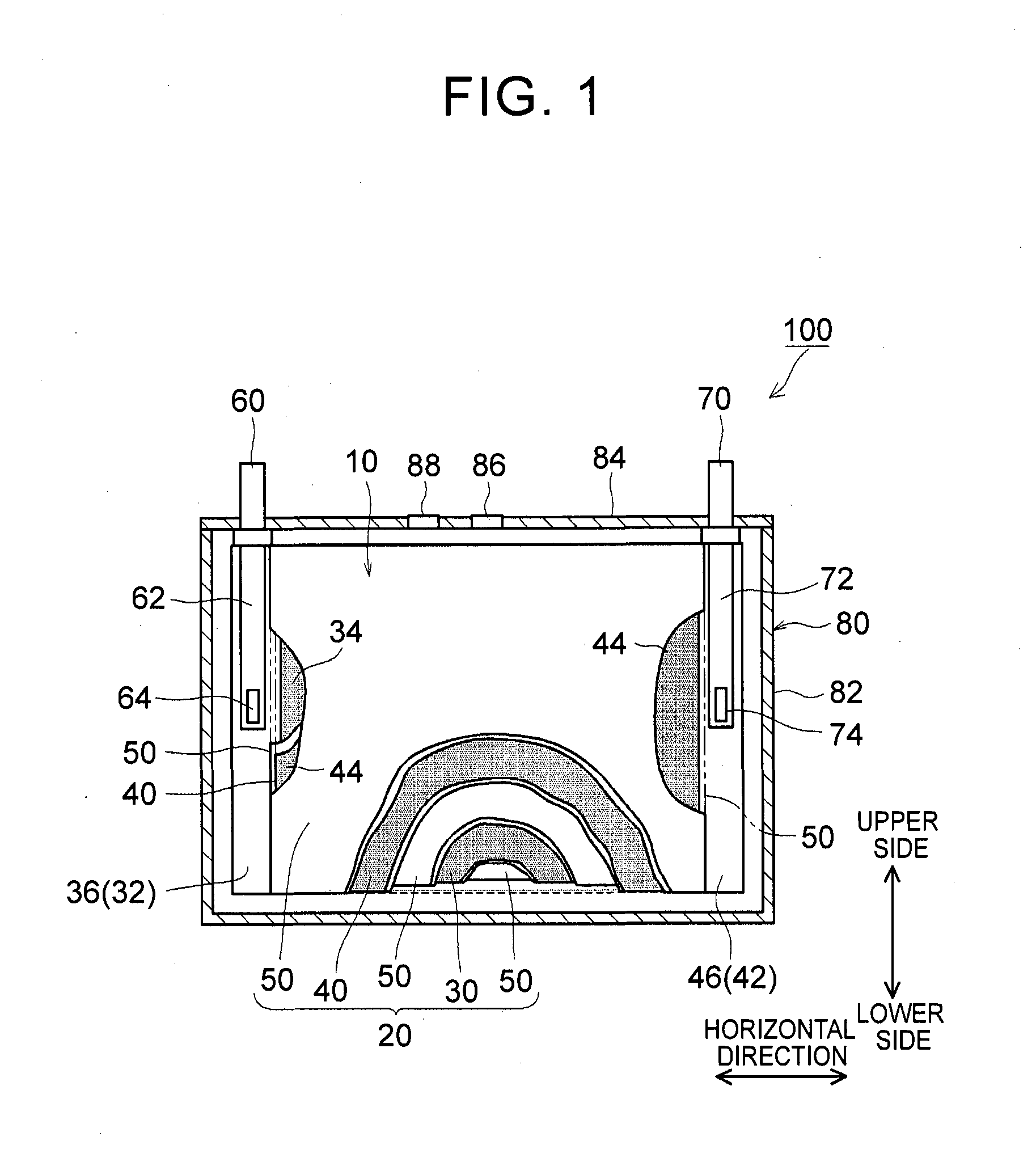
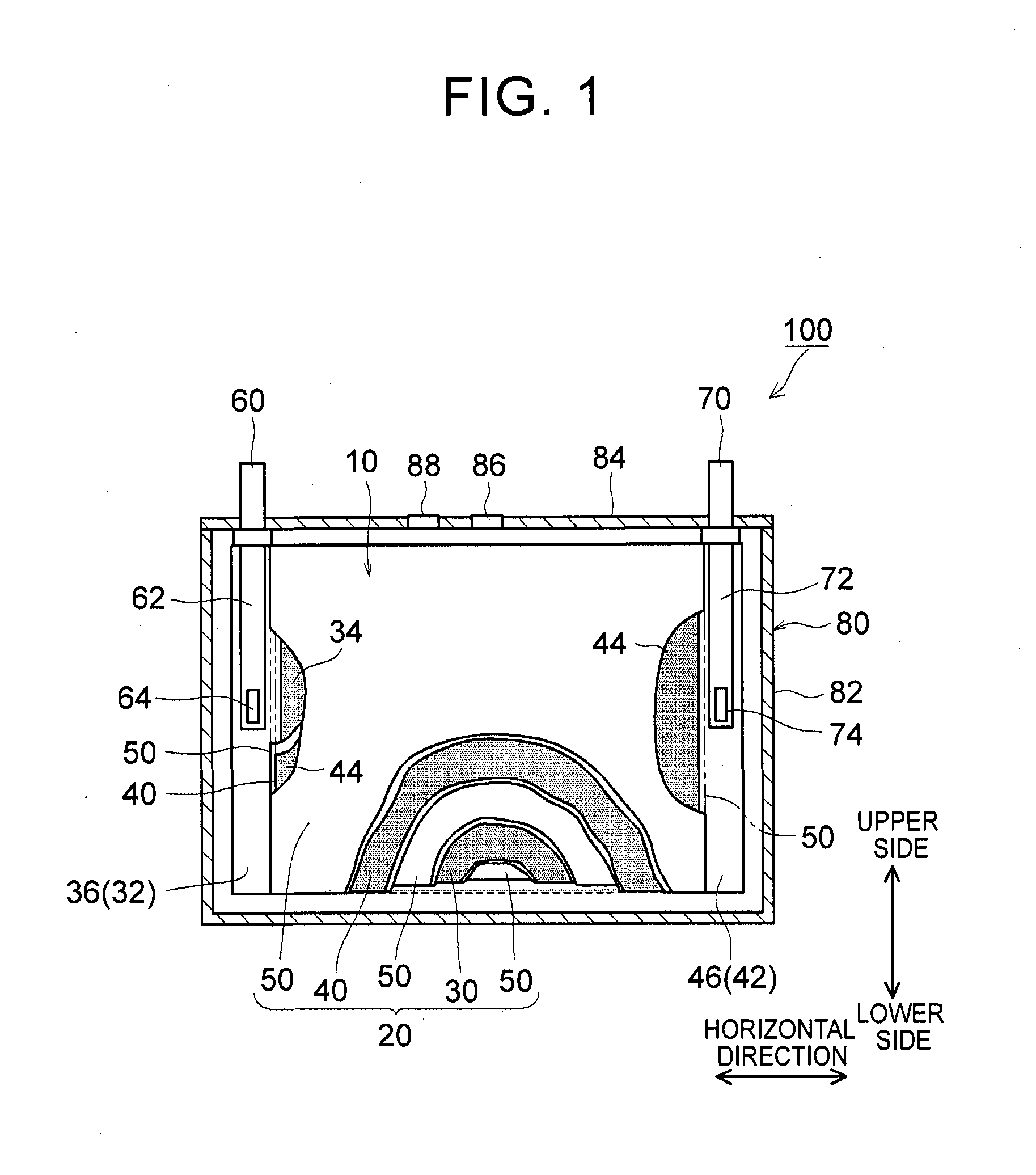