PETROLEUM RESIDUUM BURNING BOILER AND COMBUSTION METHOD THEREOF
The present invention relates to a petroleum residuum burning boiler which uses, as fuel, a flame-retardant petroleum residuum, such as asphalt pitch or petroleum coke. Conventionally known are petroleum residuum burning boilers which use, as fuel, a flame-retardant petroleum residuum, such as asphalt pitch or petroleum coke. PTL 1 discloses this type of boiler. The boiler described in PTL 1 includes a high-temperature reduction combustion chamber and a low-temperature oxidation combustion chamber located under the high-temperature reduction combustion chamber and connected to the high-temperature reduction combustion chamber through a throat. A primary burner that supplies petroleum residuum fuel and primary combustion air is provided at the high-temperature reduction combustion chamber, and a two-stage combustion air supply nozzle is provided at the low-temperature oxidation combustion chamber. In the high-temperature reduction combustion chamber, the fuel is combusted at a high temperature of about 1,450° C. to 1,550° C. in a fuel ultra-rich and reduction atmosphere. A combustion gas generated in the high-temperature reduction combustion chamber flows through the throat into the low-temperature oxidation combustion chamber. In the low-temperature oxidation combustion chamber, the combustion is completed at a low temperature of about 1,100° C. in an oxidizing atmosphere. In the flame-retardant petroleum residuum, such as asphalt pitch or petroleum coke, the content of nitrogen and the content of sulfur are large since nitrogen and sulfur are concentrated in a petroleum refining process. Therefore, a flue gas of the flame-retardant petroleum residuum contains a large amount of NOx. Moreover, in the flame-retardant petroleum residuum, the content of vanadium is large since vanadium is concentrated in the petroleum refining process. Therefore, combustion ash of the flame-retardant petroleum residuum contains vanadium oxide having a low melting point. If the combustion ash adheres to a furnace wall or a heat exchanger tube, blocking of heat transfer, blocking of ventilation, and high-temperature corrosion by influence of the high sulfur content may be caused. Therefore, when using the flame-retardant petroleum residuum as the fuel, reductions in the amount of NOx generated and the amount of soot generated are problems to be solved. According to the boiler of PTL 1, the amount of NOx generated is reduced by combusting the flame-retardant petroleum residuum fuel through two stages that are high-temperature reduction combustion and low-temperature oxidation combustion. Moreover, according to the boiler of PTL 1, the amount of soot generated is reduced in such a manner that: steam is added to the primary combustion air; and a water gas reaction is caused between carbon and the steam to promote gasification of the carbon. PTL 1: Japanese Laid-Open Patent Application Publication No. 2012-107825 The water gas reaction that is an endothermic reaction is advantageous at higher temperatures from the viewpoint of the equilibrium theory. When steam that is significantly lower in temperature than a furnace internal temperature is supplied as a gasifying agent to the inside of a furnace, the furnace internal temperature decreases. The effects of the water gas reaction are limited by the decrease in the furnace internal temperature. The present invention was made under these circumstances, and an object of the present invention is to propose a petroleum residuum burning boiler and a combustion method of the petroleum residuum burning boiler, each of which promotes a water gas reaction more effectively than when steam is directly supplied as a gasifying agent to the inside of a furnace, and with this, realizes low soot combustion. A petroleum residuum burning boiler according to one aspect of the present invention includes: a furnace body including a high-temperature reduction combustion chamber in which combustion is performed at a temperature of 1,300° C. or more and an air ratio of less than one and a low-temperature oxidation combustion chamber which is connected to the high-temperature reduction combustion chamber and in which combustion is performed at a temperature of less than 1,300° C. and an air ratio of one or more; a burner that supplies petroleum residuum fuel and primary combustion air to the high-temperature reduction combustion chamber; a two-stage combustion air supply nozzle that supplies two-stage combustion air to the low-temperature oxidation combustion chamber; and an assist gas supply nozzle through which an assist gas is supplied to the high-temperature reduction combustion chamber, the assist gas containing a component which generates steam by combustion, the steam being used as a gasifying agent for unburned carbon of a combustion gas of the petroleum residuum fuel. A combustion method of a petroleum residuum burning boiler according to another aspect of the present invention is a combustion method of a petroleum residuum burning boiler, the petroleum residuum burning boiler including: a high-temperature reduction combustion chamber to which petroleum residuum fuel and primary combustion air are supplied and in which combustion is performed at a temperature of 1,300° C. or more and an air ratio of less than one; and a low-temperature oxidation combustion chamber which is connected to the high-temperature reduction combustion chamber and in which combustion is performed at a temperature of less than 1,300° C. and an air ratio of one or more, the combustion method including: supplying an assist gas to the high-temperature reduction combustion chamber; and gasifying unburned carbon of a combustion gas of the petroleum residuum fuel by a water gas reaction by using steam, generated by combustion of the assist gas, as a gasifying agent. According to the petroleum residuum burning boiler and the combustion method of the petroleum residuum burning boiler, the steam (H2O gas) is generated by the combustion of the assist gas supplied to the high-temperature reduction combustion chamber, and the unburned carbon of the combustion gas of the petroleum residuum fuel can be gasified by the water gas reaction by using the steam as the gasifying agent. In addition, since the decrease in the furnace internal temperature can be suppressed more than when the steam is directly supplied as the gasifying agent to the inside of the furnace, the inside of the furnace is maintained at a high temperature that is advantageous for the progress of the water gas reaction. As above, since the gasification of the unburned carbon is promoted, the amount of soot generated by the combustion can be reduced. The present invention can propose the petroleum residuum burning boiler and the combustion method of the petroleum residuum burning boiler, each of which promotes the water gas reaction more effectively than when steam is directly supplied as the gasifying agent to the inside of the furnace, and with this, realizes low soot combustion. Hereinafter, the present invention will be described based on an embodiment with reference to the drawings. The petroleum residuum burning boiler 1 shown in Walls of the high-temperature reduction combustion chamber 2 are covered with a fire-resistant material 6 that withstands a high temperature of 1,550° C. or more. Burners 5 are provided on each of a pair of opposing furnace walls of the high-temperature reduction combustion chamber 2. The burners 5 are lined up in a horizontal direction to form burner rows, and the burner rows are provided in an upper-lower direction. The burners 5 are opposed to each other and arranged in a zigzag manner such that axes of flames from the opposing burners 5 do not intersect with each other. A first air supply device 53 that supplies combustion air (primary combustion air) by pressure is connected to the main fuel supply nozzle 51. A second air supply device 57 that supplies combustion air (secondary combustion air) is connected to the secondary combustion air nozzle 56. The second air supply device 57 can adjust the amount of combustion air supplied. Moreover, a petroleum residuum fuel supply device 54 that supplies petroleum residuum fuel to the primary combustion air supplied by pressure is connected to the main fuel supply nozzle 51. The petroleum residuum fuel supply device 54 can quantitatively supply the petroleum residuum fuel. The petroleum residuum fuel is flame-retardant solid fuel prepared by, for example, finely crushing asphalt pitch or petroleum coke. An assist gas supply device 55 that supplies an assist gas by pressure is connected to the assist gas supply nozzle 52. The assist gas supply device 55 can adjust the amount of assist gas supplied. The assist gas is a gas containing components which generate steam (H2O gas) by combustion. The assist gas is, for example, a by-product gas in a petroleum refining step. The by-product gas in the petroleum refining step contains components, such as hydrogen (H2), methane (CH4), ethane (C2H6), and propane (C3H8), which generate steam by combustion. Table 1 below shows compositions of the by-product gases in the petroleum refining step which gases may be used as the assist gas. The assist gas used in the present invention is not limited to the by-product gases having the compositions shown in Table 1. The petroleum residuum fuel supplied to the combustion air supplied by pressure to the main fuel supply nozzle 51 is conveyed by the flow of the combustion air. The primary combustion air and the petroleum residuum fuel flowing together with the primary combustion air are ejected from the main fuel supply nozzle 51 to the high-temperature reduction combustion chamber 2. Moreover, the assist gas is ejected from the assist gas supply nozzle 52. To be specific, the assist gas and the mixture of the primary combustion air and the petroleum residuum fuel are coaxially ejected from the burner 5. A calorie ratio R (R=B/A) [%] that is a ratio of a calorie B [Kcal/h] of the assist gas to a calorie A [Kcal/h] of the petroleum residuum fuel is not limited but is preferably 10 or more and 30 or less. The amount of combustion air supplied by the second air supply device 57, the amount of fuel supplied by the petroleum residuum fuel supply device 54, and the amount of assist gas supplied by the assist gas supply device 55 are adjusted such that the calorie ratio R is maintained. A known swirling flow generator (not shown) including a swirler is provided at the burner 5. The secondary combustion air swirls by the action of the swirling flow generator, and therefore, the combustion gas forms swirling flow. By the swirling flow generated by each burner 5, the fuel and the combustion gas in the high-temperature reduction combustion chamber 2 are collected at a middle portion of a ceiling, and this brings about an extension effect of a residence time of the fuel and the combustion gas in the high-temperature reduction combustion chamber 2. Referring back to In the low-temperature oxidation combustion chamber 3, the cooler 9 is located between the throat 4 and the two-stage combustion air supply nozzles 7 in the upper-lower direction. The cooler 9 cools the high-temperature combustion gas flowing downward from the high-temperature reduction combustion chamber 2 through the throat 4. Heat exchanger tubes (not shown) for steam generation extend at a furnace wall of the cooler 9. In the low-temperature oxidation combustion chamber 3, the two-stage combustor 10 is located under the two-stage combustion air supply nozzles 7. Heat exchanger tubes (not shown) for steam generation extend at a furnace wall of the two-stage combustor 10. The two-stage combustor 10 is maintained at a low temperature by a cooling medium flowing through the heat exchanger tubes. The two-stage combustion air supply nozzles 7 are provided at each of a pair of opposing furnace walls of the low-temperature oxidation combustion chamber 3. The two-stage combustion air supply nozzles 7 are lined up in a horizontal direction to form nozzle rows, and the nozzle rows are provided in the upper-lower direction. By the air supplied from the two-stage combustion air supply nozzles 7, an unburned gas in the combustion gas cooled by the cooler 9 is subjected to two-stage combustion in a low-temperature oxidizing atmosphere in the two-stage combustor 10. The ash discharger 8 is formed at a bottom portion of the low-temperature oxidation combustion chamber 3. An ash discharging mechanism (not shown) is provided under the ash discharger 8. Combustion ash accumulated at a bottom of the furnace is discharged from the ash discharger 8 to an outside of the furnace. A gas outflow port 11 communicating with a gas duct 12 is provided at a lower side surface of the two-stage combustor 10. A flue gas generated in the two-stage combustor 10 flows in a U shape to flow into the gas duct 12. Steam superheater tubes 13 and an economizer 14 are provided at the gas duct 12. An ash outlet port 15 through which the combustion ash flowing together with the combustion gas is discharged after being precipitated is provided at a bottom portion of the gas duct 12 where the steam superheater tubes 13 and the economizer 14 are provided. A combustion method of the petroleum residuum burning boiler 1 configured as above will be described. The fuel and the primary combustion air are supplied from the burners 5 to the high-temperature reduction combustion chamber 2, and the combustion of the fuel is started. Introduction of air to the high-temperature reduction combustion chamber 2 is suppressed, and the high-temperature reduction combustion chamber 2 is maintained in a reduction atmosphere in which an air ratio is less than one (for example, about 0.6 to 0.8). The high-temperature reduction combustion chamber 2 is maintained at a high temperature of 1,300° C. or more, desirably 1,450° C. or more and 1,550° C. or less by the combustion of the fuel and, according to need, the combustion of auxiliary fuel. When the fuel combusts in the high-temperature reduction atmosphere in the high-temperature reduction combustion chamber 2, a high-temperature combustion gas is generated. The combustion gas is pushed out from the high-temperature reduction combustion chamber 2 by the combustion gas generated continuously, to flow downward through the throat 4 to the low-temperature oxidation combustion chamber 3. The combustion gas is cooled to less than 1,300° C., desirably 1,200° C. or more and less than 1,300° C. while flowing through the cooler 9. Then, the combustion gas flows downward to the two-stage combustor 10. The two-stage combustion air having a relatively low temperature is supplied from the two-stage combustion air supply nozzles 7 to the two-stage combustor 10. With this, the two-stage combustor 10 is maintained in an oxidizing atmosphere in which the air ratio is one or more (for example, about 1.1). An unburned portion of the combustion gas is completely combusted in the oxidizing atmosphere of the two-stage combustor 10. The flue gas is cooled to about 1,000° C. to 1,100° C. by the two-stage combustor 10 and then flows out to the gas duct 12. The flue gas flowing through the gas duct 12 is subjected to heat exchange with boiler feedwater at the steam superheater tubes 13 and the economizer 14 and then flows out to a post-process step connected to the gas duct 12. Typically, the amount of NOx generated in the combustion of the petroleum residuum fuel strongly depends on a combustion temperature and the air ratio. To be specific, in the reduction atmosphere, the amount of NOx generated decreases as the temperature of the combustion increases. Moreover, in the oxidizing atmosphere, the amount of NOx generated decreases as the temperature of the combustion decreases. In the petroleum residuum burning boiler 1 according to the present embodiment, the generation of fuel NOx is suppressed by combusting the fuel in the high-temperature reduction atmosphere in the high-temperature reduction combustion chamber 2, and the generation of thermal NOx is suppressed by completely combusting the unburned portion of the combustion gas in the low-temperature oxidizing atmosphere in the low-temperature oxidation combustion chamber 3. In the petroleum residuum burning boiler 1 according to the present embodiment, the amount of NOx generated can be effectively reduced by adopting the above two-stage combustion system. Typically, when petroleum residuum fuel is combusted in a high-temperature reduction combustion atmosphere, part of carbon is not gasified and remains as unburned carbon. This increases the amount of soot. However, in the petroleum residuum burning boiler 1 according to the present embodiment, the assist gas is supplied to the high-temperature reduction combustion chamber 2, and the high-temperature reduction combustion chamber 2 is maintained at a high temperature of 1,300° C. or more (desirably, 1,450° C. or more). With this, a water gas reaction is caused in the high-temperature reduction combustion chamber 2, and this promotes the gasification of carbide. The amount of soot generated by the combustion of the petroleum residuum fuel can be reduced by the gasification of the carbide. The petroleum residuum fuel, the assist gas, and the combustion air are ejected from the burners 5 in the high-temperature reduction combustion chamber 2. Since the petroleum residuum fuel is flame-retardant, the assist gas starts combusting prior to the petroleum residuum fuel. When the assist gas combusts by the combustion air, steam is generated. The generated H2O gas serves as a gasifying agent, and the unburned carbon of the combustion gas is subjected to the water gas reaction to be converted into a CO gas and an H2gas. When the temperature of the combustion gas is less than 1,300° C., and the percentage of the assist gas in mixed combustion of the petroleum residuum fuel and the assist gas increases, the amount of oxygen becomes inadequate, and therefore, the water gas reaction is not caused. As a result, the amount of soot may increase. When the assist gas is supplied to the high-temperature reduction combustion chamber 2, and the steam is generated by the combustion of the assist gas, a decrease in the furnace internal temperature can be suppressed more than when the steam lower in temperature than the furnace internal temperature is directly supplied as the gasifying agent to the inside of the furnace. To be specific, the inside of the furnace is maintained at a high temperature that is advantageous for the progress of the water gas reaction. As shown in the graph of As described above, the petroleum residuum burning boiler 1 according to the present embodiment includes: the furnace body 20 including the high-temperature reduction combustion chamber 2 in which combustion is performed at 1,300° C. or more and the air ratio of less than one and the low-temperature oxidation combustion chamber 3 which is connected to the high-temperature reduction combustion chamber 2 and in which combustion is performed at a temperature of less than 1,300° C. and the air ratio of one or more; the burner 5 that supplies the petroleum residuum fuel and the primary combustion air to the high-temperature reduction combustion chamber 2; the two-stage combustion air supply nozzle 7 that supplies the two-stage combustion air to the low-temperature oxidation combustion chamber 3; and the assist gas supply nozzle 52 that supplies the assist gas to the high-temperature reduction combustion chamber 2. The assist gas contains a component which generates steam by combustion, and the steam serves as the gasifying agent for the unburned carbon of the combustion gas of the petroleum residuum fuel. Moreover, the combustion method of the petroleum residuum burning boiler 1 according to the present embodiment includes, in the petroleum residuum burning boiler 1 including the high-temperature reduction combustion chamber 2 to which the petroleum residuum fuel and the primary combustion air are supplied and in which combustion is performed at a temperature of 1,300° C. or more and the air ratio of less than one and the low-temperature oxidation combustion chamber 3 which is connected to the high-temperature reduction combustion chamber 2 and in which combustion is performed at a temperature of less than 1,300° C. and the air ratio of one or more, supplying the assist gas to the high-temperature reduction combustion chamber 2 and gasifying the unburned carbon of the combustion gas of the petroleum residuum fuel by the water gas reaction by using the steam, generated by the combustion of the assist gas, as the gasifying agent. According to the petroleum residuum burning boiler 1 and the combustion method of the petroleum residuum burning boiler 1, the steam (H2O gas) is generated by the combustion of the assist gas supplied to the high-temperature reduction combustion chamber 2, and the unburned carbon of the combustion gas of the petroleum residuum fuel can be gasified by the water gas reaction by using the steam as the gasifying agent. In addition, since the decrease in the furnace internal temperature can be suppressed more than when the steam is directly supplied as the gasifying agent to the inside of the furnace, the inside of the furnace is maintained at a high temperature that is advantageous for the progress of the water gas reaction. As above, since the gasification of the unburned carbon is promoted, the amount of soot generated by the combustion can be reduced. To be specific, the water gas reaction is promoted more effectively than when the steam is directly supplied as the gasifying agent to the inside of the furnace, and with this, the petroleum residuum burning boiler 1 and the combustion method of the petroleum residuum burning boiler 1, both of which can realize the low soot combustion, can be provided. In the petroleum residuum burning boiler 1 according to the present embodiment, the burner 5 is a coaxial mixed combustion burner including the assist gas supply nozzle 52 and the main fuel supply nozzle 51 through which the petroleum residuum fuel and the primary combustion air are supplied. Similarly, in the combustion method of the petroleum residuum burning boiler 1 according to the present embodiment, the assist gas and the mixture of the petroleum residuum fuel and the primary combustion air are coaxially supplied to the high-temperature reduction combustion chamber 2. As above, since the assist gas and the mixture of the petroleum residuum fuel and the primary combustion air are coaxially supplied (ejected) to the high-temperature reduction combustion chamber 2, the primary combustion air and the assist gas can be made to react with each other prior to the flame-retardant petroleum residuum fuel. Then, the steam generated by the combustion reaction between the primary combustion air and the assist gas can be made to react with the unburned carbon contained in the combustion gas generated by the combustion of the petroleum residuum fuel. In the petroleum residuum burning boiler 1 and the combustion method of the petroleum residuum burning boiler 1 according to the present embodiment, the assist gas may be the by-product gas generated in the petroleum refining step. Since the petroleum residuum burning boiler 1 uses, as the fuel, the petroleum residuum generated in the petroleum refining step, the petroleum residuum burning boiler 1 may be provided at or adjacent to a petroleum refinery. In such a case, when the assist gas is the by-product gas generated in the petroleum refining step, both the petroleum residuum fuel and the by-product gas which are generated in the petroleum refining step can be effectively utilized, which is preferable. The foregoing has described a preferred embodiment of the present invention. Modifications of specific structures and/or functional details of the above embodiment may be included in the present invention as long as they are within the scope of the present invention. The above configuration may be changed as below, for example. For example, in the above embodiment, the burner 5 is a coaxial mixed combustion burner which uses the petroleum residuum fuel and the assist gas. However, the burner 5 may be a single-fuel burner which uses petroleum residuum fuel. In this case, the assist gas supply nozzle 52 that ejects the assist gas such that the assist gas is mixed with the petroleum residuum fuel and the primary combustion air ejected from the single-fuel burner which uses the petroleum residuum fuel may be provided independently from the burner 5. In a petroleum residuum burning boiler including: a high-temperature reduction combustion chamber to which petroleum residuum fuel and primary combustion air are supplied and in which combustion is performed at a temperature of 1,300° C. or more and an air ratio of less than one; and a low-temperature oxidation combustion chamber which is connected to the high-temperature reduction combustion chamber and in which combustion is performed at a temperature of less than 1,300° C. and an air ratio of one or more, an assist gas is supplied to the high-temperature reduction combustion chamber, and unburned carbon of a combustion gas of the petroleum residuum fuel is gasified by a water gas reaction by using steam, generated by combustion of the assist gas, as a gasifying agent. 1. A petroleum residuum burning boiler comprising:
a furnace body including
a high-temperature reduction combustion chamber in which combustion is performed at a temperature of 1,300° C. or more and an air ratio of less than one and a low-temperature oxidation combustion chamber which is connected to the high-temperature reduction combustion chamber and in which combustion is performed at a temperature of less than 1,300° C. and an air ratio of one or more; a burner that supplies petroleum residuum fuel and primary combustion air to the high-temperature reduction combustion chamber; a two-stage combustion air supply nozzle that supplies two-stage combustion air to the low-temperature oxidation combustion chamber; and an assist gas supply nozzle through which an assist gas is supplied to the high-temperature reduction combustion chamber, the assist gas containing a component which generates steam by combustion, the steam being used as a gasifying agent for unburned carbon of a combustion gas of the petroleum residuum fuel. 2. The petroleum residuum burning boiler according to 3. The petroleum residuum burning boiler according to 4. A combustion method of a petroleum residuum burning boiler,
the petroleum residuum burning boiler including: a high-temperature reduction combustion chamber to which petroleum residuum fuel and primary combustion air are supplied and in which combustion is performed at a temperature of 1,300° C. or more and an air ratio of less than one; and a low-temperature oxidation combustion chamber which is connected to the high-temperature reduction combustion chamber and in which combustion is performed at a temperature of less than 1,300° C. and an air ratio of one or more, the combustion method comprising: supplying an assist gas to the high-temperature reduction combustion chamber; and gasifying unburned carbon of a combustion gas of the petroleum residuum fuel by a water gas reaction by using steam, generated by combustion of the assist gas, as a gasifying agent. 5. The combustion method according to 6. The combustion method according to TECHNICAL FIELD
BACKGROUND ART
CITATION LIST
Patent Literature
SUMMARY OF INVENTION
Technical Problem
Solution to Problem
Advantageous Effects of Invention
BRIEF DESCRIPTION OF DRAWINGS
DESCRIPTION OF EMBODIMENTS
H2 33.3 39.7 23.6 83.3 H2S 0 0.01 0.0005 0 CO 0.5 0.1 0.05 0.1 CO2 0.3 0.09 0 0 N2 6.0 0 0 0 CH4 19.0 36.8 45.4 16.1 C2H6 11.5 11.5 19.1 0.04 C2H4 11.0 0.1 1.1 0.4 C3H8 8.8 4.8 5.6 0 C3H6 0.9 0.2 1.2 0 C4-total 6.0 5.9 3.6 0 C5-total 2.6 0.6 0.3 0 C6 or more 0 0.2 0.1 0 [The unit is mol. %]
2H2+O2→H2O, CH4+O2→CO2+2H2O, . . .
C+H2O→CO+H2REFERENCE SIGNS LIST
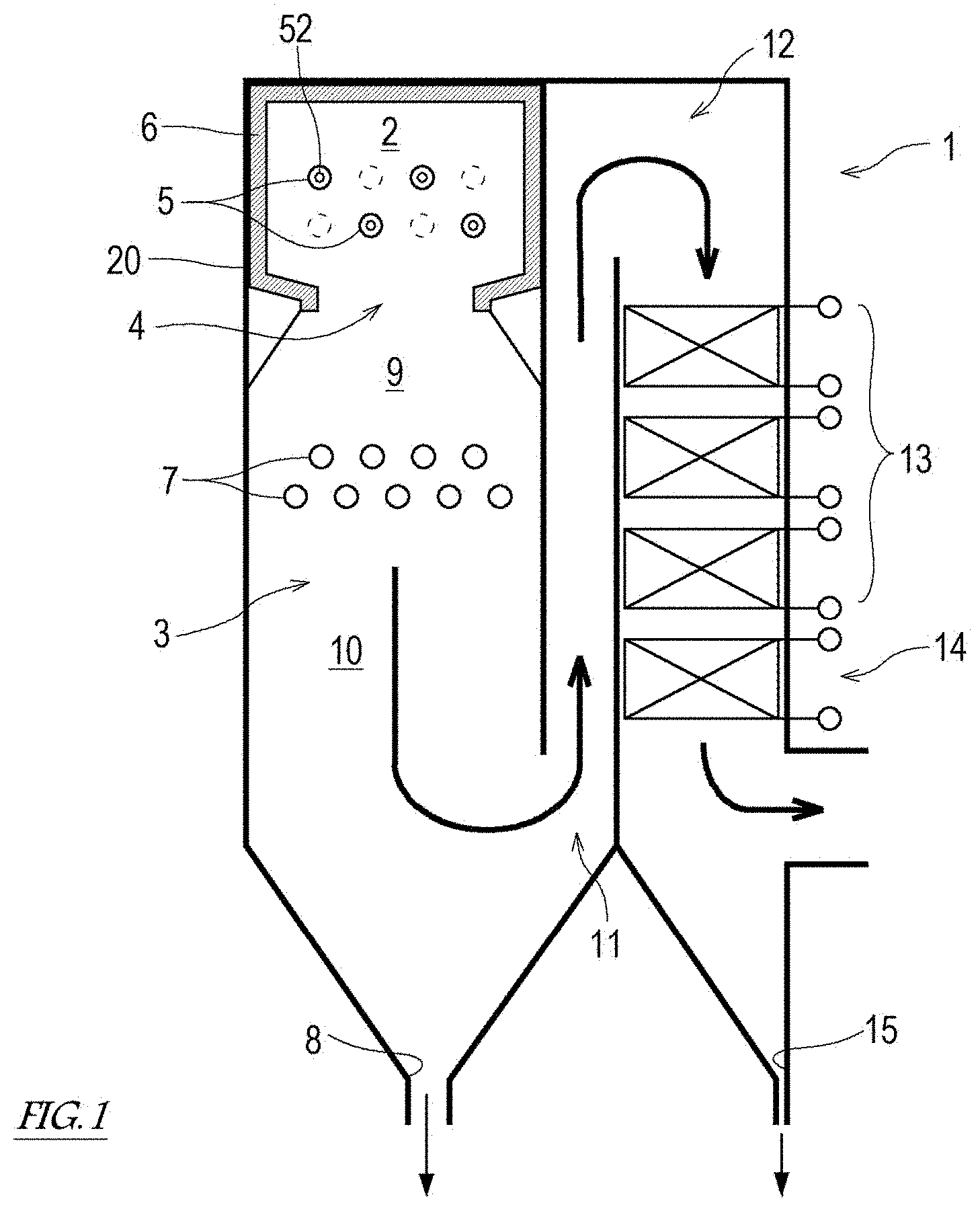
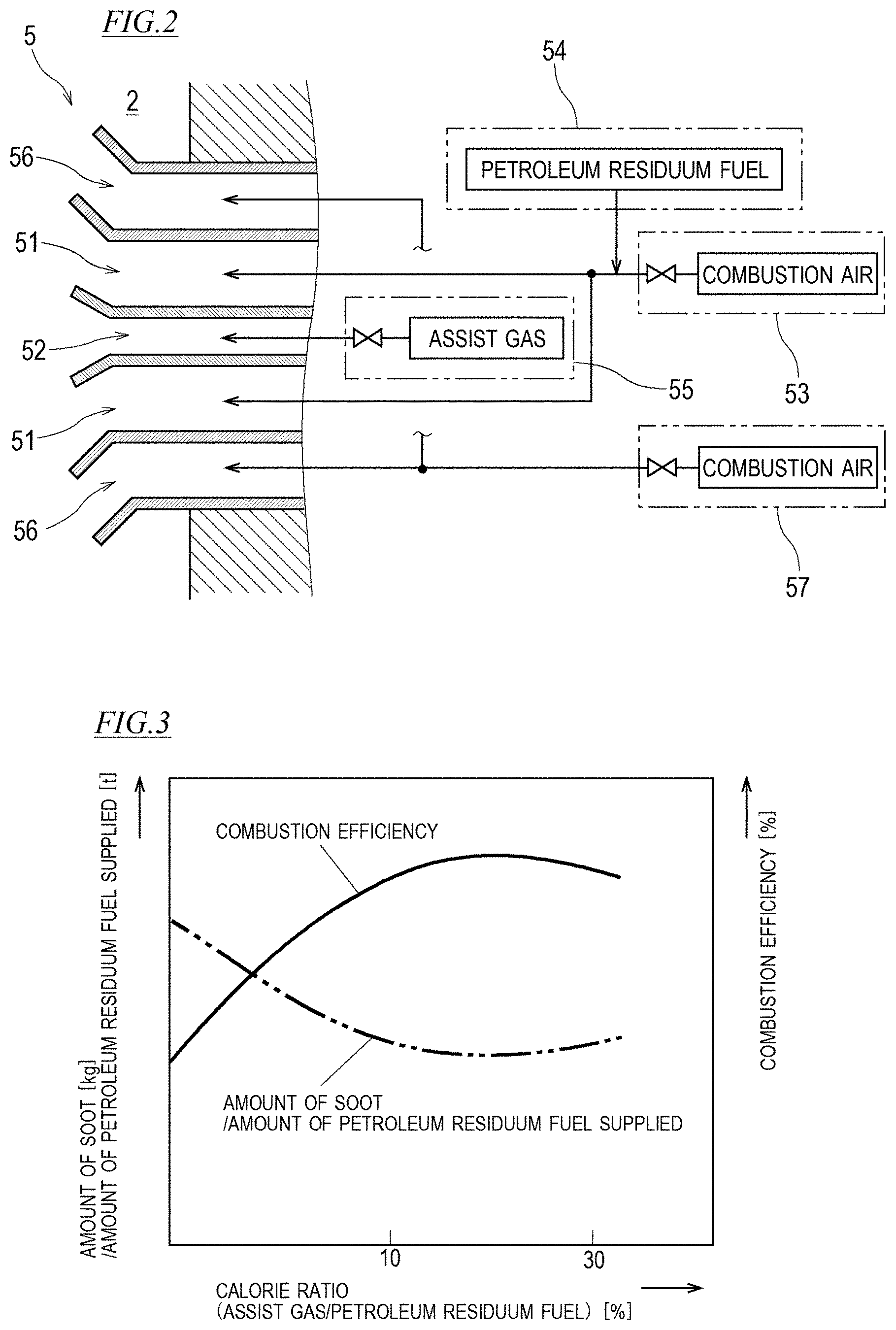