Computer-generiertes Hologramm (CGH), sowie Verfahren zur Charakterisierung der Oberflächenform eines optischen Elements
Die Erfindung betrifft ein Computer-generiertes Hologramm (CGH) sowie ein Verfahren zur Charakterisierung der Oberflächenform eines optischen Elements. Mikrolithographie wird zur Herstellung mikrostrukturierter Bauelemente, wie beispielsweise integrierter Schaltkreise oder LCD's, angewendet. Der Mikrolithographieprozess wird in einer sogenannten Projektionsbelichtungsanlage durchgeführt, welche eine Beleuchtungseinrichtung und ein Projektionsobjektiv aufweist. Das Bild einer mittels der Beleuchtungseinrichtung beleuchteten Maske (= Retikel) wird hierbei mittels des Projektionsobjektivs auf ein mit einer lichtempfindlichen Schicht (Photoresist) beschichtetes und in der Bildebene des Projektionsobjektivs angeordnetes Substrat (z.B. ein Siliziumwafer) projiziert, um die Maskenstruktur auf die lichtempfindliche Beschichtung des Substrats zu übertragen. In für den EUV-Bereich ausgelegten Projektionsobjektiven, d.h. bei Wellenlängen von z.B. etwa 13 nm oder etwa 7 nm, werden mangels Verfügbarkeit geeigneter lichtdurchlässiger refraktiver Materialien Spiegel als optische Komponenten für den Abbildungsprozess verwendet. Typische für EUV ausgelegte Projektionsobjektive, wie z.B. aus Mit der Erhöhung der bildseitigen numerischen Apertur (NA) geht typischerweise eine Vergrößerung der erforderlichen Spiegelflächen der in der Projektionsbelichtungsanlage eingesetzten Spiegel einher. Dies hat wiederum zur Folge, dass neben der Fertigung auch die Prüfung der Oberflächenform der Spiegel eine anspruchsvolle Herausforderung darstellt. Hierbei kommen zur hochgenauen Prüfung der Spiegel insbesondere interferometrische Messverfahren unter Verwendung Computer-generierter Hologramme (CGH) zum Einsatz. Dabei ist es u.a. auch bekannt, in ein- und dasselbe CGH zusätzlich zu der für die eigentliche Prüfung benötigten Funktionalität (d.h. der entsprechend der Spiegelform ausgelegten CGH-Struktur zur Formung der mathematisch der Prüflingsform entsprechenden Wellenfront) wenigstens eine weitere „Kalibrierfunktionalität“ zur Bereitstellung einer zur Kalibrierung bzw. Fehlerkorrektur dienenden Referenzwellenfront einzukodieren. Gemäß Dabei ist eine Kenntnis des Gitterprofils des bei der interferometrischen Messung eingesetzten CGH sowie die Vorhersage etwaiger Änderungen dieses Gitterprofils erforderlich, um bei Feststellung einer Phasenabweichung in dem interferometrischen Messaufbau eindeutig unterscheiden zu können, ob diese Phasenabweichung auf vorhandene Fehler auf dem CGH oder auf der zu messenden Fläche zurückzuführen ist. Hierbei tritt in der Praxis das Problem auf, dass Änderungen des Gitterprofils auch durch Kontamination mit z.B. Kohlenwasserstoffen hervorgerufen werden können, wobei etwa in Vakuumanlagen Kontaminationen beispielsweise durch Fette vorhanden sein können. Bei Messungen in Atmosphäre kann sich an der Oberfläche des CGH z.B. ein Wasserfilm mit variierender Dicke ausbilden. Die hochgenaue Ermittlung des Gitterprofils des CGH stellt eine zunehmend anspruchsvolle Herausforderung dar, da in gegenwärtigen und künftigen Messanordnungen eine Reproduzierbarkeit in der Größenordnung von 0.1nm über einen Zeitraum von 1 Jahr (entsprechend der maximal zulässigen Änderung des Messergebnisses bei identischem Prüfling) gefordert sein kann. Das Problem einer hochgenauen Charakterisierung des CGH-Gitterprofils wird dadurch erschwert, dass eine vorübergehende Entnahme des CGH aus der interferometrischen Prüfanordnung im Hinblick auf die zu gewährleistende hohe Reproduzierbarkeit sowie auch aus Zeitgründen nicht wünschenswert ist. Zum Stand der Technik wird lediglich beispielhaft auf Vor dem obigen Hintergrund ist es eine Aufgabe der vorliegenden Erfindung, ein Computer-generiertes Hologramm (CGH) sowie ein Verfahren zur Charakterisierung der Oberflächenform eines optischen Elements bereitzustellen, welche in einer interferometrischen Prüfanordnung eine erhöhte Messgenauigkeit unter zumindest teilweiser Vermeidung der vorstehend beschriebenen Probleme ermöglichen. Diese Aufgabe wird durch das Computer-generierte Hologramm (CGH) gemäß den Merkmalen des unabhängigen Patentanspruchs 1 bzw. das Verfahren gemäß den Merkmalen des nebengeordneten Patentanspruchs 11 gelöst. Gemäß einem Aspekt der Erfindung weist ein Computer-generiertes Hologramm (CGH), insbesondere zur Verwendung in einer interferometrischen Prüfanordnung zum Prüfen eines optischen Elements einer mikrolithographischen Projektionsbelichtungsanlage auf:
Gemäß einer Ausführungsform weist der zweite Bereich zwei räumlich voneinander separierte Substrukturen auf, wobei sich diese Substrukturen hinsichtlich der Kontaminationsabhängigkeit ihrer Phasenwirkung auf im Betrieb auf das CGH auftreffendes Licht voneinander unterscheiden. Gemäß einer Ausführungsform unterscheiden sich diese Substrukturen hinsichtlich des Flankenanteils, welcher für jede der Substrukturen jeweils als Quotient aus der mit einem Flankenwinkel von wenigstens 80° strukturbelegten Fläche und der gesamten strukturbelegten Fläche definiert ist, um wenigstens 30%, bezogen auf den jeweils größeren Wert, voneinander. Die Erfindung betrifft weiter ein computer-generiertes Hologramm (CGH), insbesondere zur Verwendung in einer interferometrischen Prüfanordnung zum Prüfen eines optischen Elements einer mikrolithographischen Projektionsbelichtungsanlage, mit
Der Erfindung liegt insbesondere das Konzept zugrunde, zur Detektion und Überwachung einer auf einem CGH befindlichen Kontamination einen von der eigentlichen Nutzstruktur räumlich separierten Kontrollbereich bereitzustellen, welcher seinerseits über die in der interferometrischen Prüfanordnung durchgeführte Wellenfrontmessung einen Rückschluss auf die besagte Kontamination erlaubt. Hierbei geht die Erfindung von der Überlegung aus, dass eine Sensitivität des CGH bzw. der durch das CGH in der Prüfanordnung gelieferten Messergebnisse im Hinblick auf Kontaminationen dadurch variiert werden kann, dass ausgehend von der vorstehend diskutierten schematischen Darstellung von Konkret macht sich die Erfindung den Umstand zu Nutze, dass ein im Kontrollbereich befindlicher Bereich in Form einer vergleichsweise feineren Substruktur mit insgesamt größerer Gesamtfläche der zwischen Bergen und Tälern befindlichen Flankenbereiche aufgrund der effektiv größeren Angriffsfläche für Kontamination eine vergleichsweise stärkere Sensitivität der Phasenwirkung auf Kontamination besitzt als ein zweiter Bereich mit vergleichsweise gröberer Substruktur. Hierbei ist zu beachten, dass ungeachtet der im Kontrollbereich des erfindungsgemäßen CGH vorhandenen unterschiedlichen Substrukturen insofern eine „übereinstimmende Grundfunktionalität“ für den Kontrollbereich bzw. die unterschiedlichen Substrukturen vorliegt, als gewährleistet bleibt, dass auch die von dem Kontrollbereich bzw. besagten Substrukturen ausgehenden Wellen im Interferometeraufbau erfasst und vermessen werden. Diese „übereinstimmende Grundfunktionalität“ kann in Ausführungsformen der Erfindung insbesondere dadurch erreicht werden, dass eine Übereinstimmung in der Gitterperiode oder in einer der mehrfach kodierten Gitterperioden vorliegt. In weiteren Ausführungsformen kann besagte „übereinstimmende Grundfunktionalität“ auch dadurch erreicht werden, dass die im Kontrollbereich vorhandene, die Substrukturen umfassende Struktur so ausgelegt ist, dass zumindest ein Teil des einfallenden Lichts (entsprechend der Littrow-Bedingung) in die Einfallsrichtung zurückgebeugt wird. Mit anderen Worten bleibt auch für die erfindungsgemäß in einem separaten Kontrollbereich vorhandenen, unterschiedlich kontaminationssensitiven Substrukturen die prinzipielle Hauptfunktionalität des CGH bestehen, da diese Substrukturen lediglich den Zweck haben, unterschiedlich auf Kontamination zu reagieren und eine diesbezügliche Berücksichtigung in den letztlich in der interferometrischen Prüfanordnung erhaltenen Messergebnissen zu ermöglichen. Infolge der Existenz von wenigstens zwei unterschiedlich kontaminationssensitiven Bereichen auf dem erfindungsgemäßen CGH ist es dabei auch möglich, kontaminationsbedingte Änderungen des Messsignals von Signaländerungen, welche z.B. aus Lagetoleranzen der unterschiedlichen optischen Elemente resultieren können, zuverlässig zu unterscheiden. Gemäß einer Ausführungsform gehen die Substrukturen hinsichtlich des Flankenanteils sukzessive ineinander über. Gemäß einer Ausführungsform ist das Computer-generierte Hologramm (CGH) dazu ausgelegt, zusätzlich zu einer Prüfwelle eine Referenzwelle zur interferometrischen Überlagerung mit der Prüfwelle nach Reflexion der Referenzwelle an einem Referenzspiegel zu erzeugen. Gemäß einer Ausführungsform weist das Computer-generierte Hologramm (CGH) zur Bereitstellung der Referenzwelle eine komplexe Kodierung auf. Gemäß einer Ausführungsform weist der zweite Bereich eine in ihrer Gitterperiode mit der Nutzstruktur übereinstimmende Grundstruktur auf. Gemäß einer Ausführungsform weist der zweite Bereich eine als Littrow-Gitter ausgestaltete Grundstruktur auf. Die Erfindung betrifft weiter eine interferometrische Prüfanordnung zum Prüfen eines optischen Elements, insbesondere eines optischen Elements einer mikrolithographischen Projektionsbelichtungsanlage, wobei die Prüfanordnung ein Computer-generiertes Hologramm aufweist und wobei eine Prüfung zumindest einer Teilfläche des optischen Elements durch interferometrische Überlagerung einer von diesem Computer-generierten Hologramm auf das optische Element gelenkten Prüfwelle und einer Referenzwelle durchführbar ist, wobei das Computer-generiertes Hologramm gemäß den vorstehend beschriebenen Merkmalen ausgelegt ist. Die Erfindung betrifft weiter ein Verfahren zur Charakterisierung der Oberflächenform eines optischen Elements, unter Verwendung einer interferometrischen Prüfanordnung, wobei diese Prüfanordnung ein Computer-generiertes Hologramm mit den vorstehend beschriebenen Merkmalen aufweist. Gemäß einer Ausführungsform weist das Verfahren die Schritte auf:
Gemäß einer Ausführungsform erfolgt das Ermitteln des Modellparameters auf Basis eines Vergleichs einer für den Kontrollbereich des CGH modellbasiert berechneten Wellenfront mit bei interferometrischer Messung anhand des Kontrollbereichs des CGH in der Prüfanordnung erhaltenen Messergebnissen. Weitere Ausgestaltungen der Erfindung sind der Beschreibung sowie den Unteransprüchen zu entnehmen. Die Erfindung wird nachstehend anhand von in den beigefügten Abbildungen dargestellten Ausführungsbeispielen näher erläutert. Es zeigen:
Gemäß Bei dem in einer interferometrischen Prüfanordnung (z.B. mit dem anhand von Im Weiteren werden Ausführungsformen der Erfindung unter Bezugnahme auf die schematischen Abbildungen in Das CGH 120 weist, wie in Um die von dem Kontrollbereich 122 in der interferometrischen Prüfanordnung ausgehenden Wellen ebenfalls bei der interferometrischen Messung erfassen zu können, stimmt die Gitterperiode der im Kontrollbereich 122 befindlichen Gitterstruktur (Grundstruktur B) mit derjenigen der Nutzstruktur A überein. Um jedoch erfindungsgemäß innerhalb des Kontrollbereichs 122 eine kontaminationssensitive Funktionalität bereitzustellen, sind in besagtem Kontrollbereich 122 wie im Weiteren beschrieben wenigstens zwei voneinander verschiedene Substrukturen B1 und B2 vorhanden. Die erfindungswesentliche Wirkung dieser Substrukturen B1 und B2 ist dabei, dass infolge der voneinander verschiedenen Sensitivitäten der Substrukturen B1 und B2 gegenüber einer sich auf dem CGH 120 bzw. dem Kontrollbereich 122 ausbildenden Kontamination eine eindeutige (z.B. von Lagetoleranzen der optischen Elemente unterscheidbare) Detektion der betreffenden Kontamination ermöglicht wird. Mit anderen Worten reagieren die Bereiche B1 und B2 unterschiedlich auf Kontamination, was sich im schematisch dargestellten Ausführungsbeispiel von Als quantitatives Kriterium zur Beschreibung der vorstehend genannten Oberflächenvariation zwischen den Substrukturen B1 und B2 kann insbesondere die für die betreffenden Bereiche gebildete effektive Flankenfläche herangezogen werden, wobei wiederum als „Flanke“ diejenigen Wandungsbereiche mit einer Steigung größer als 80° angesehen werden können. Dabei ändert sich die so definierte Flankenfläche zwischen den Substrukturen B1 und B2 vorzugsweise um wenigstens 30% (bezogen auf den jeweils größeren Wert). Gemäß Anhand der Substrukturen B1, B2 wird wiederum wie vorstehend unter Bezugnahme auf Im Unterschied zu Eine quantitative Betrachtung ausgehend von der schematischen Darstellung in Eine kontaminationsbedingte Füllfaktoränderung um den Faktor 0.005 entspricht somit einer Kontaminationsschichtdicke von 3nm bei Annahme einer mittleren Gitterperiode von p = 1.2µm, welches einem Signal in der Größe von 6nm in der interferometrischen Prüfanordnung entspricht. Wenn die Erfindung auch anhand spezieller Ausführungsformen beschrieben wurde, erschließen sich für den Fachmann zahlreiche Variationen und alternative Ausführungsformen, z.B. durch Kombination und/oder Austausch von Merkmalen einzelner Ausführungsformen. Dementsprechend versteht es sich für den Fachmann, dass derartige Variationen und alternative Ausführungsformen von der vorliegenden Erfindung mit umfasst sind und die Reichweite der Erfindung nur im Sinne der beigefügten Patentansprüche und deren Äquivalente beschränkt ist. Diese Liste der vom Anmelder aufgeführten Dokumente wurde automatisiert erzeugt und ist ausschließlich zur besseren Information des Lesers aufgenommen. Die Liste ist nicht Bestandteil der deutschen Patent- bzw. Gebrauchsmusteranmeldung. Das DPMA übernimmt keinerlei Haftung für etwaige Fehler oder Auslassungen. Die Erfindung betrifft ein Computer-generiertes Hologramm (CGH) sowie ein Verfahren zur Charakterisierung der Oberflächenform eines optischen Elements. Gemäß einem Aspekt weist ein CGH einen wenigstens eine Nutzstruktur (A) aufweisenden ersten Bereich (121, 321, 421) und einen von diesem ersten Bereich (121, 321, 421) räumlich separierten zweiten Bereich (122, 322, 422) auf, wobei dieser zweite Bereich einen Kontrollbereich zur Detektion einer sich auf dem CGH (120, 320, 420, 520) ausbildenden Kontamination bildet. Computer-generiertes Hologramm (CGH), insbesondere zur Verwendung in einer interferometrischen Prüfanordnung zum Prüfen eines optischen Elements einer mikrolithographischen Projektionsbelichtungsanlage, mit
Computer-generiertes Hologramm (CGH) nach Computer-generiertes Hologramm (CGH) nach Computer-generiertes Hologramm (CGH), insbesondere zur Verwendung in einer interferometrischen Prüfanordnung zum Prüfen eines optischen Elements einer mikrolithographischen Projektionsbelichtungsanlage, mit
Computer-generiertes Hologramm (CGH) nach Computer-generiertes Hologramm (CGH) nach einem der vorhergehenden Ansprüche, dadurch gekennzeichnet, dass dieses dazu ausgelegt ist, zusätzlich zu einer Prüfwelle eine Referenzwelle zur interferometrischen Überlagerung mit der Prüfwelle nach Reflexion der Referenzwelle an einem Referenzspiegel (431, 531) zu erzeugen. Computer-generiertes Hologramm (CGH) nach Computer-generiertes Hologramm (CGH) nach einem der Computer-generiertes Hologramm (CGH) nach einem der Interferometrische Prüfanordnung zum Prüfen eines optischen Elements, insbesondere eines optischen Elements einer mikrolithographischen Projektionsbelichtungsanlage, wobei die Prüfanordnung ein Computer-generiertes Hologramm (CGH) aufweist und wobei eine Prüfung zumindest einer Teilfläche des optischen Elements durch interferometrische Überlagerung einer von diesem Computer-generierten Hologramm auf das optische Element gelenkten Prüfwelle und einer Referenzwelle durchführbar ist, wobei das Computer-generiertes Hologramm (CGH) nach einem der Verfahren zur Charakterisierung der Oberflächenform eines optischen Elements, unter Verwendung einer interferometrischen Prüfanordnung nach Verfahren nach Verfahren nach HINTERGRUND DER ERFINDUNG
Gebiet der Erfindung
Stand der Technik
ZUSAMMENFASSUNG DER ERFINDUNG
Figurenliste
DETAILLIERTE BESCHREIBUNG BEVORZUGTER AUSFÜHRUNGSFORMEN
ZITATE ENTHALTEN IN DER BESCHREIBUNG
Zitierte Patentliteratur
• einem wenigstens eine Nutzstruktur (A) aufweisenden ersten Bereich (121, 321, 421); und
• einem von diesem ersten Bereich (121, 321, 421) räumlich separierten zweiten Bereich (122, 322, 422), wobei dieser zweite Bereich einen Kontrollbereich zur Detektion einer sich auf dem CGH (120, 320, 420, 520) ausbildenden Kontamination bildet.
• einem wenigstens eine Nutzstruktur (A) aufweisenden ersten Bereich (121, 321, 421); und
• einem von diesem ersten Bereich (121, 321, 421) räumlich separierten zweiten Bereich (122, 322, 422);
• wobei der zweite Bereich (122, 322, 422) zwei räumlich voneinander separierte Substrukturen (B1, B2) aufweist, wobei sich diese Substrukturen (B1, B2) hinsichtlich des Flankenanteils, welcher für jede der Substrukturen (B1, B2) jeweils als Quotient aus der mit einem Flankenwinkel von wenigstens 80° strukturbelegten Fläche und der gesamten strukturbelegten Fläche definiert ist, um wenigstens 30%, bezogen auf den jeweils größeren Wert, voneinander unterscheiden.
- Ermitteln eines Modellparameters auf Basis einer anhand des Kontrollbereichs des CGH (120, 320, 420, 520) durchgeführten interferometrischen Messung; und
- Korrigieren von bei interferometrischer Messung anhand des die Nutzstruktur (A) aufweisenden ersten Bereichs (121, 321, 421) des CGH (120, 320, 420, 520) erhaltenen Messergebnissen auf Basis dieses Modellparameters.
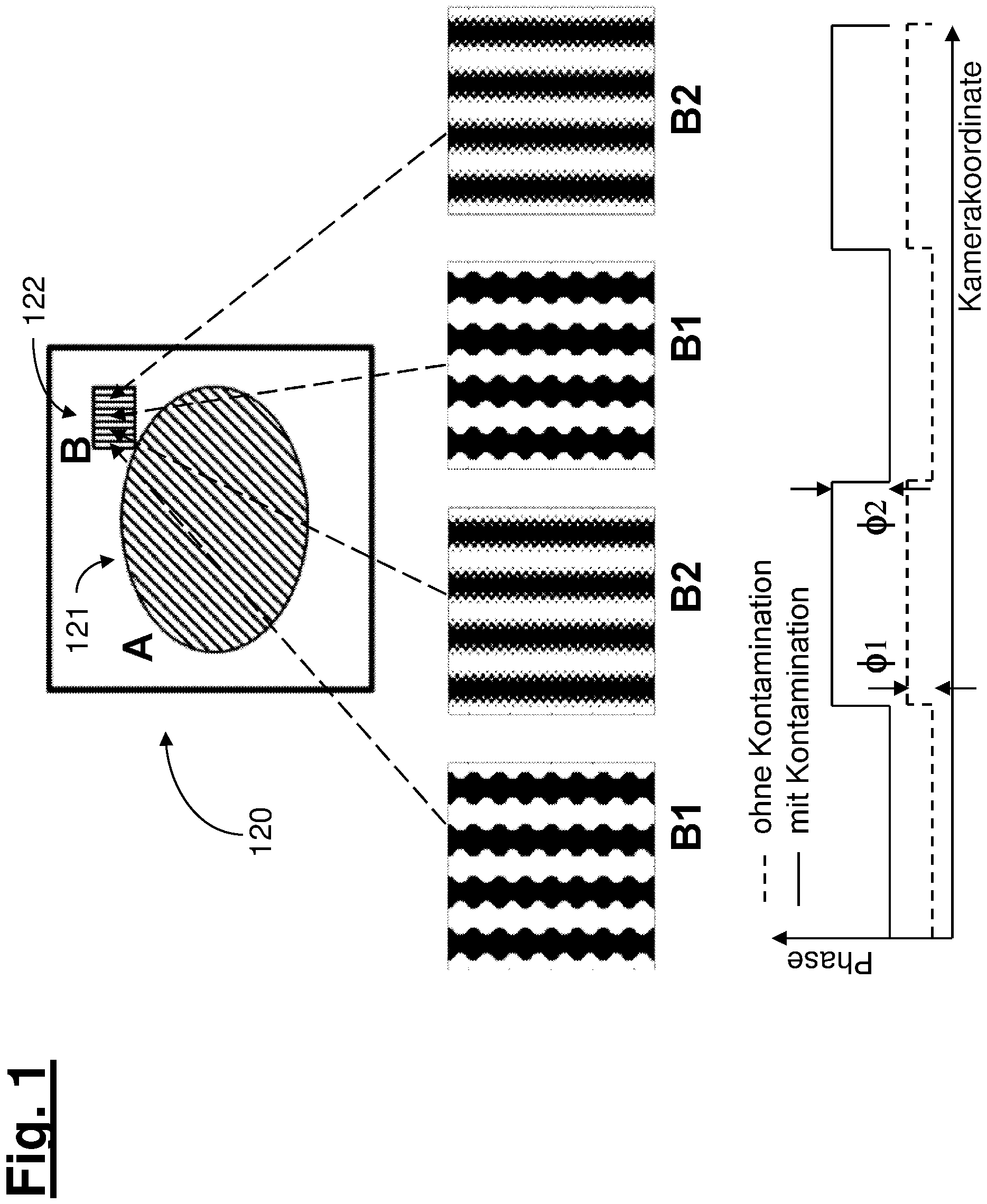
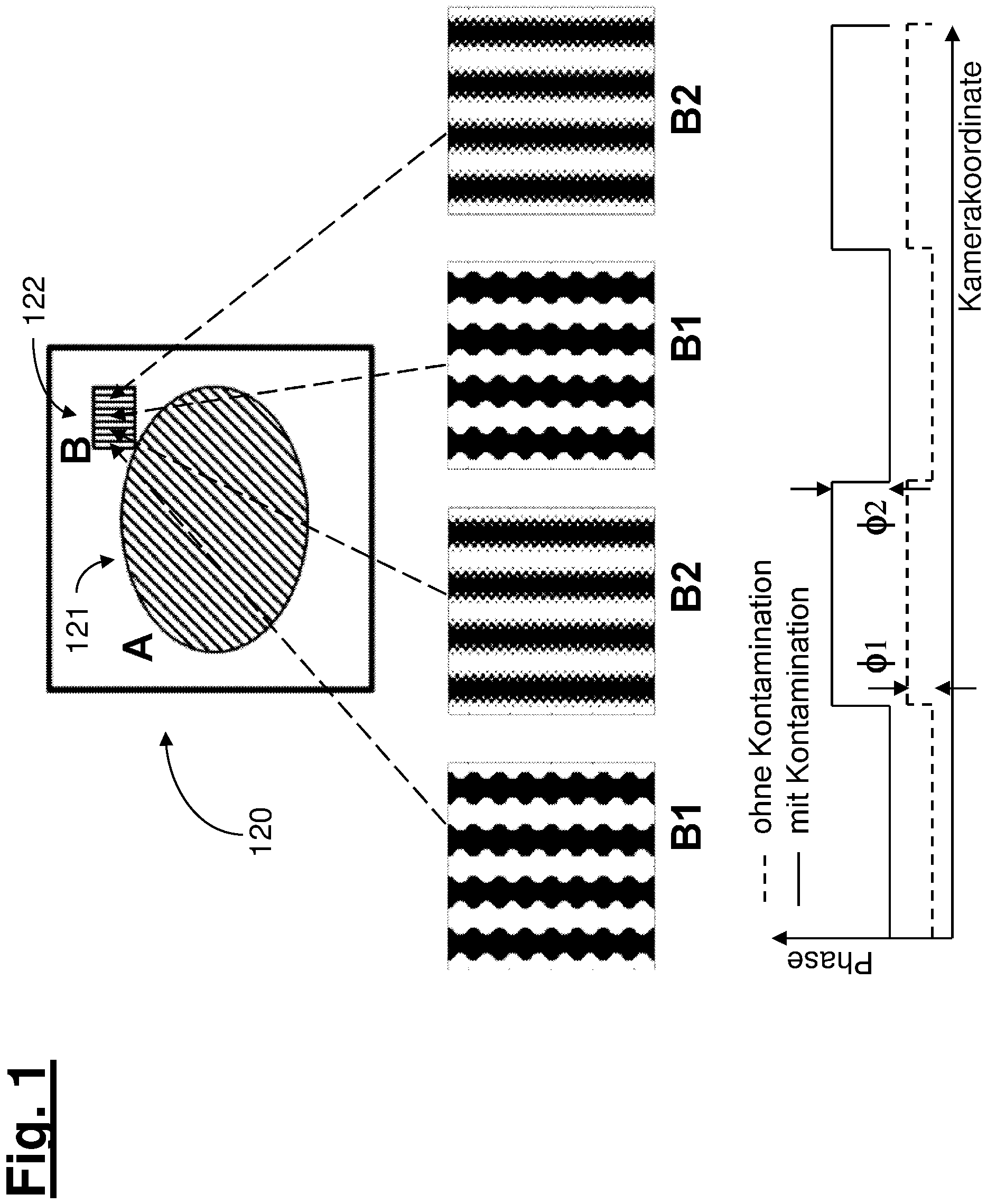
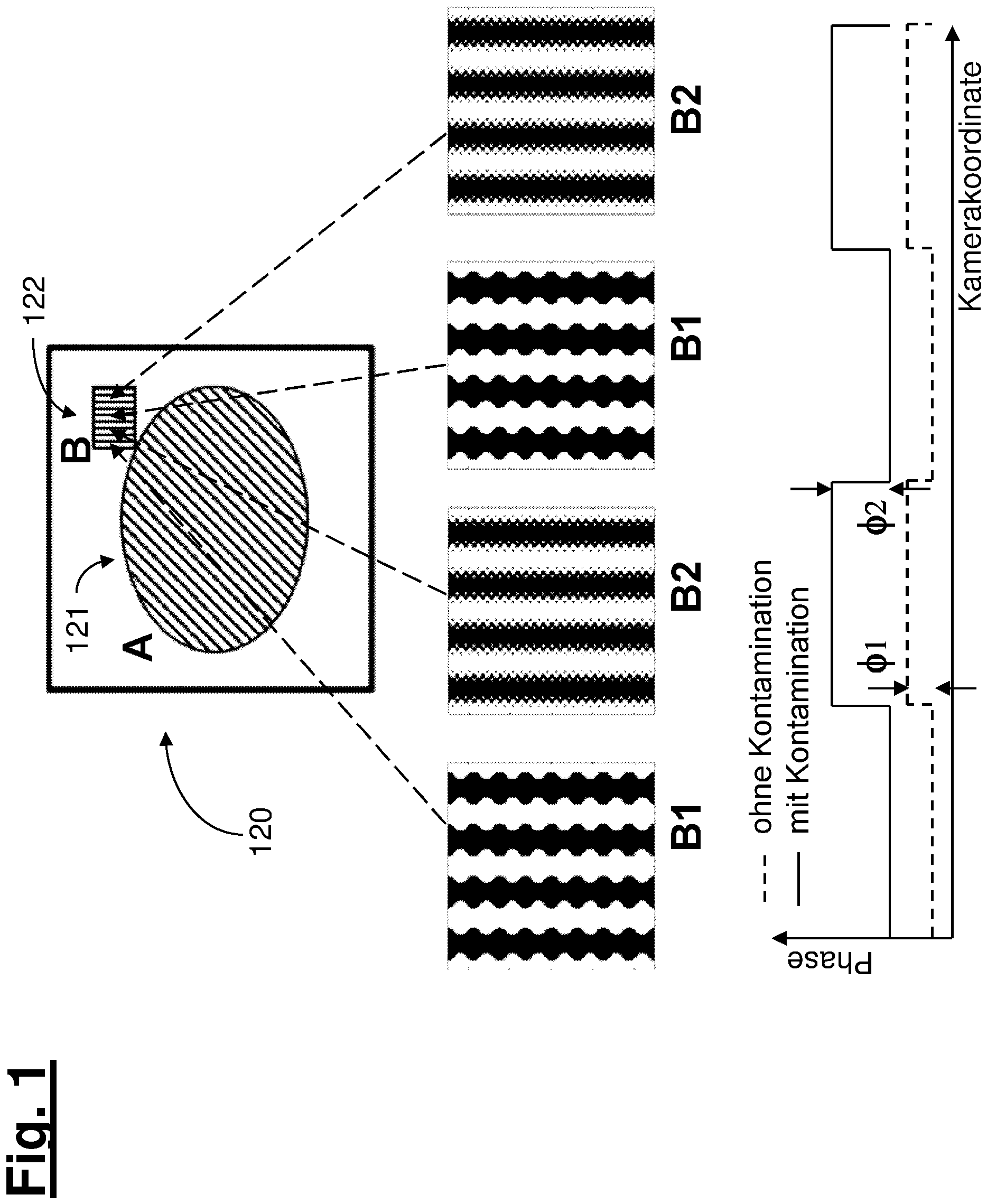
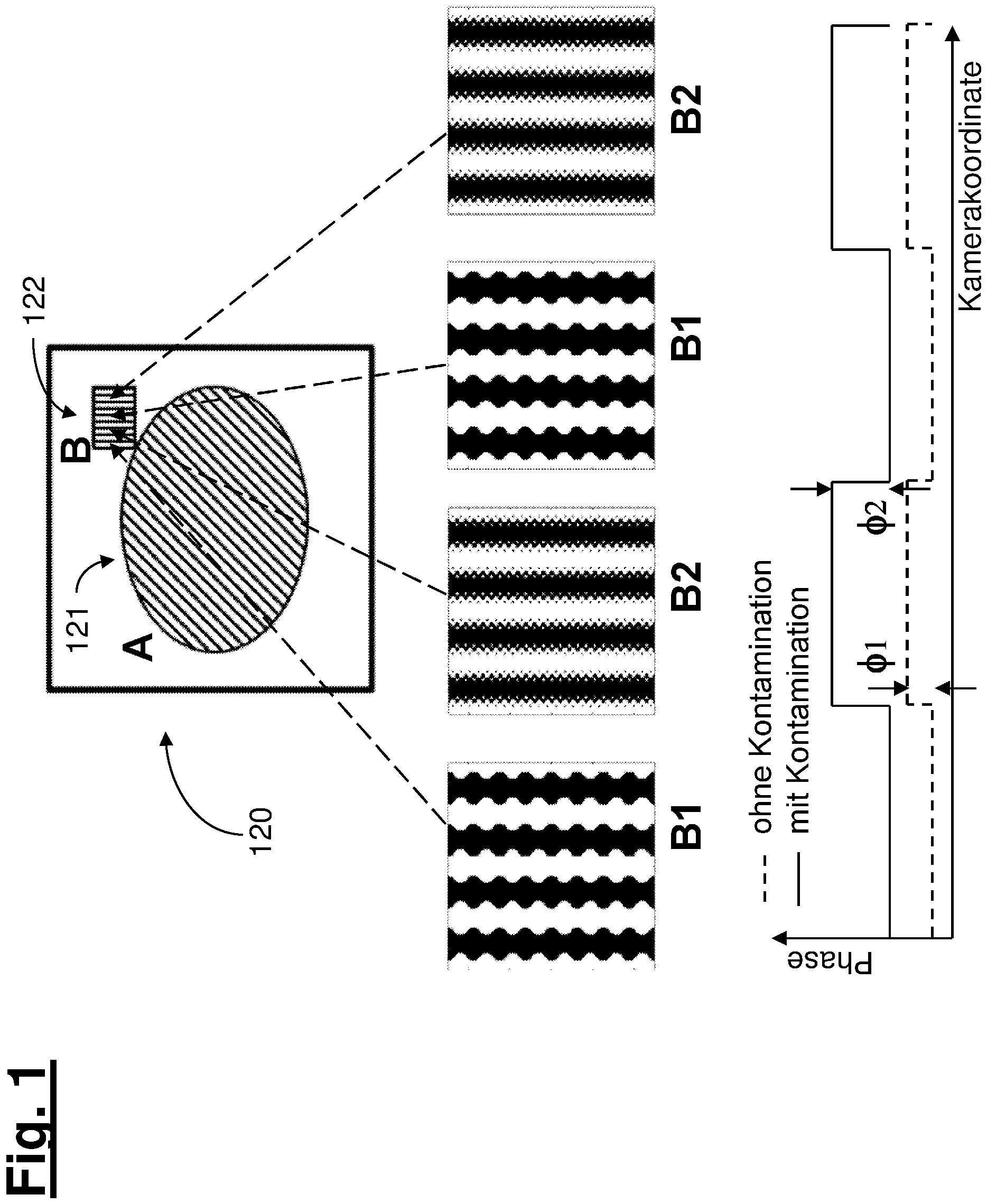
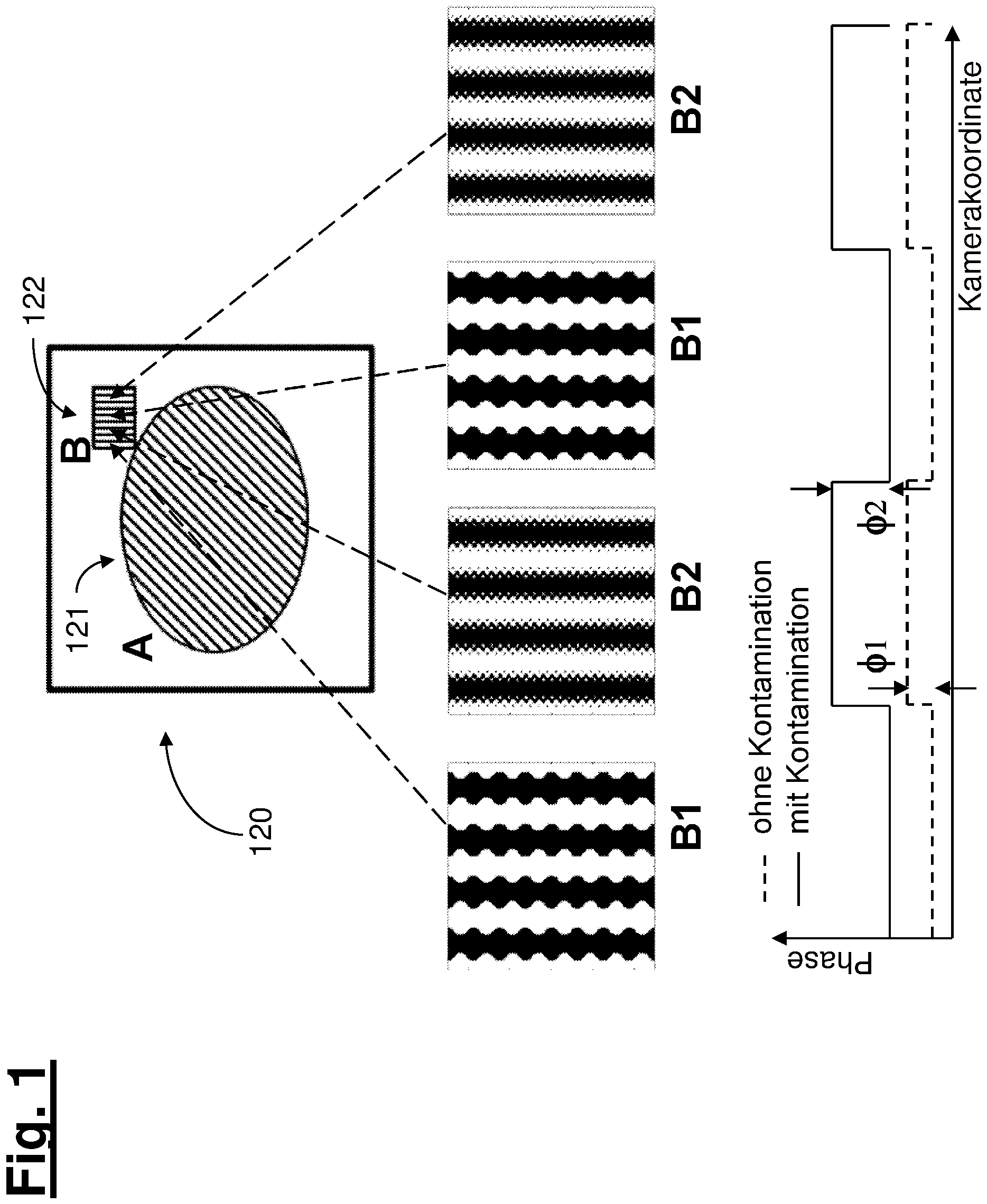
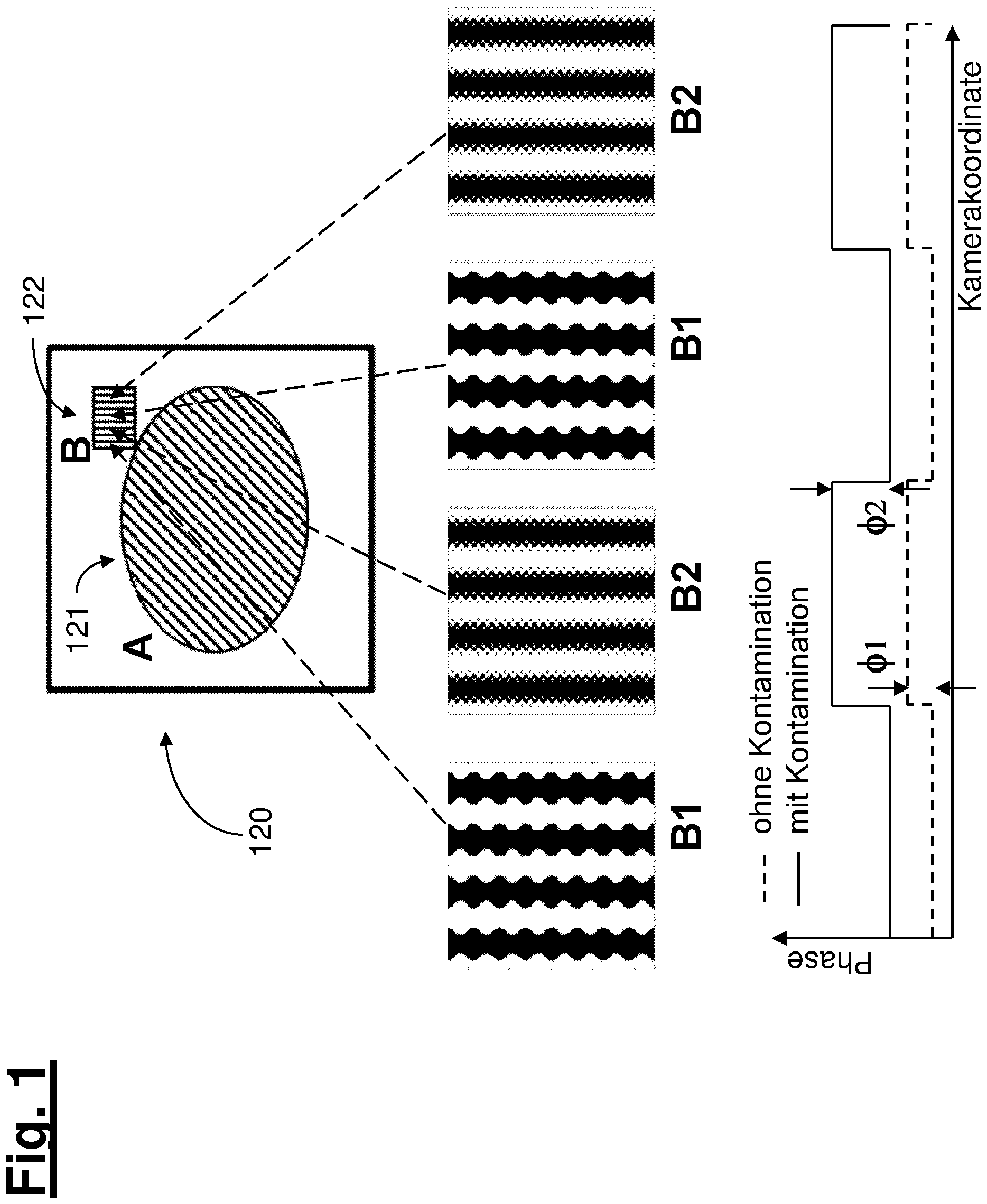
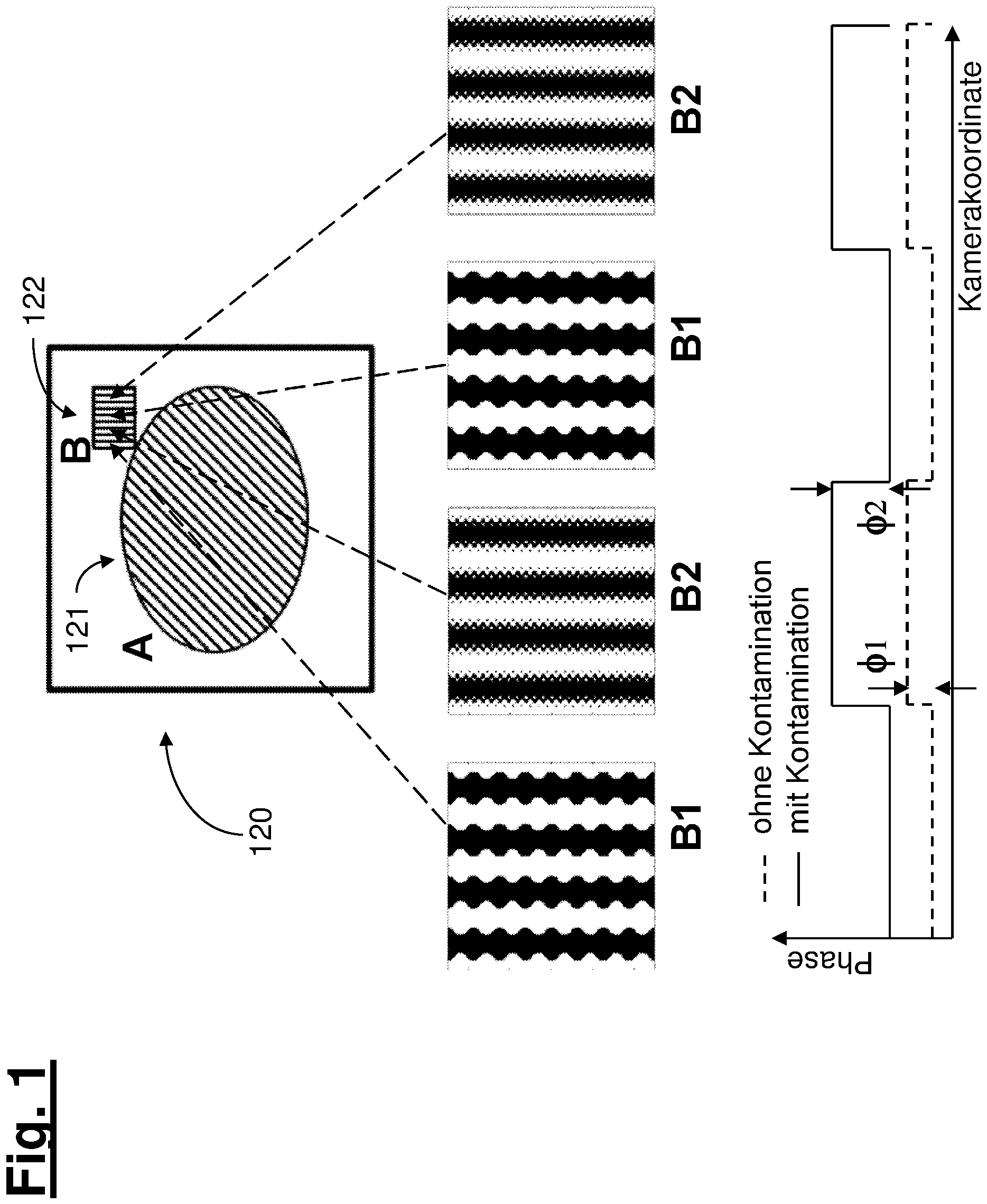
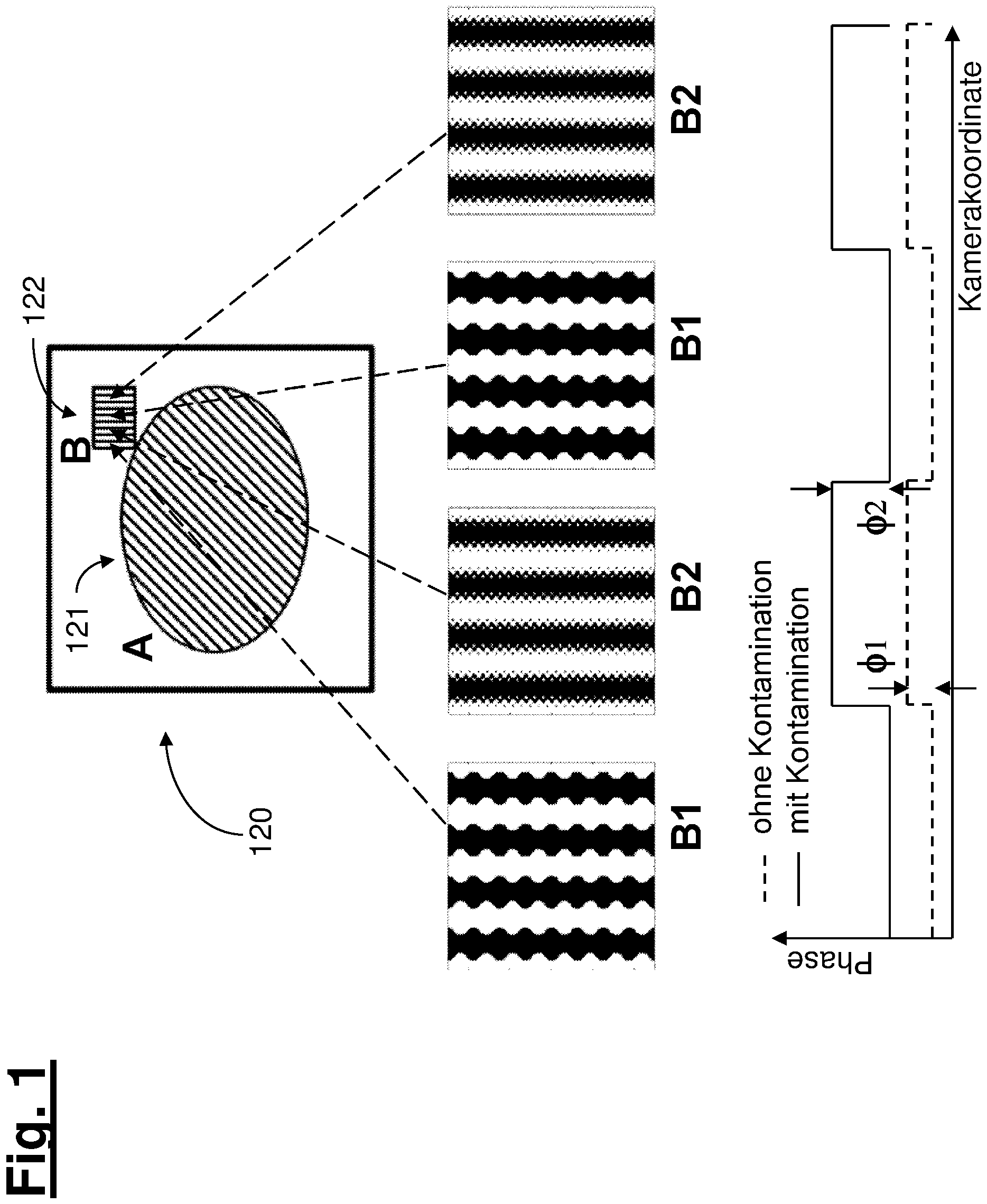