METHOD FOR RECOVERING VALUABLE METALS SELECTIVELY FROM WASTE MIXED BATTERIES
The present invention refers to a method of selective acid from waste mixing cell are disclosed. Portable electronic device, toy, made of a synthetic resin is used by various electronic number in addition to the high demand of demand etc. preferably include the updated by 20%. These cell greatly reuse impossible MPEG 1 (manganese dry battery, alkali manganese dry battery, battery, oxidation cell, lithium battery) (lead-acid, nickel - cadmium cell) on the secondary battery re-charging time can be divided into 2. Wherein one of the 80% of the entire secondary battery 1 is judged whether 55% manganese dry cell is mostly composed of secondary battery which includes 2 which occupies in 45% of the first disclosed. In addition presently used battery at least 70% of cadmium, lead, mercury containing heavy metals such as harmful in the event that the estimation value. Current with a large amount of China, Hong Kong, Taiwan in revenue to obtain an resembled the consumption by back support are disclosed. In such situations various the value metal and the development of the mirror number containing heavy metals from waste battery recycling process, in terms of environmental very important disclosed. Currently being developed in the case of manganese and the recycling of the alkali manganese dry cell by heat treatment at a temperature 700 °C alkaline cell number after zinc (Zn) mercury alone increasing temperature up to 1500 °C and an iron (Fe) and manganese (Mn) is manganese forms a BATRE number tank provided with recovery process, by infrared rays and [...] after leaching by the manganese sulfate, a process similar to zinc sulfate bath so as to number and number REVABAT REVABAT process for recovering and metal zinc (Zn) wet application [lyen the law after extraction process such as a photoresist layer number bath BATENUS commercialization of the in the nanometer range. While nickel cadmium cell in nickel (Ni) is a heavy metals cadmium (Cd) iron (Fe) vaporizing after retrieving the Ni-MH battery comprises sulfuric acid or hydrochloric acid to be supplied as the raw material with magnetic nickel leaching and recovering rare earth components are in the form of precipitation of sodium sulfate to be coated. However, a nickel-nickel (Ni) is mainly commercial recycling, iron (Fe) in a rotary kiln (rotary kiln) provided with nickel recovered in the form of a curved portion, said recycling process and collecting as above are generated by single cell of a user to be coated. In addition, nickel (Ni) nickel cadmium and hydrogen cell in a preform into a simple metal without high pressure liquid coolant in the form of nickel with a source of sale management number lung etc. provided with nickel. Nickel (Ni) and iron (Fe) is a source of Ni ferrite but last product as well as small quantities of impurities is cobalt (Co), manganese (Mn), rare earth and the like since the number actually door number as well sample impurities number Ni ferrite pore comprehensively to the TFTs. The present invention refers to said number provided which secures the door in order to solve the inconvenience such as point, the selection of a value metal from waste mixed cell number [...] method intended for steel. (A) said mixed waste including iron (Fe) is waste Ni provided Mh cell from cell, nickel (Ni) metal containing lanthanum (La) and to obtain a mixture; (b) said metal mixture it buys leaching solution and nickel (Ni) in EAF Eh area increase, and applying an oxidation number obtaining lanthanum (La) precipitating the leaching solution; said leaching solution iron (Fe) and lanthanum (La) comprising the precipitated residue. (C) said acidity (pH) is provided with a solution to the lanthanum (La) in residues to recovering method is achieved by selection of a value metal from mixed cell waste including steel. (A) said step waste mixed cell waste lithium ion battery, additional services of waste lithium 1, waste nickel cadmium battery and waste manganese can be further includes at least one alkaline cell. Said step (a) a cobalt metal mixture (Co), manganese (Mn), lithium (Li), cadmium (Cd) and zinc (Zn) containing more thereof can. (B) improvement in the in the second said it buys leaching solution (H2 SO4 ), Hydrochloric acid (HCl) and nitric acid (HNO3 ) Can be selected from the group consisting. Said step (b) hydrogen peroxide (H2 O2 ), Oxygen (O2 ), Ozone (O3 ), Sodium hypochlorite (NaClO) and potassium permanganate (KMnO4) subjecting the selected at least one number 1 oxidation number; peroxide and double sodium sulfate (Na2 S2 O8 ) And [...] (K2 S2 O8 ) Can be at least either one of the group comprising subjecting the oxidation number number 2. (B) oxidation number after said directing step said number 1 number oxide to 100 parts by mass said number 2 can be characterized. Said nickel (Ni) and said increasing said number 1 oxidation number is Eh value increase in EAF lanthanum (La), iron (Fe) by precipitating the crystalline form of FeOOH can be said. Said nickel (Ni) increasing said number 2 oxidation number increase in EAF is Eh value, said La a lanthanum (La) (SO4 )2 Na, H2 O capable of precipitation. (C) zinc (Zn) in said said residues, cadmium (Cd) and lithium (Li) including at least one of the residues additional metal additionally includes, in residues having acidity number 1 residues additional metal to said solution to said annealing; and said number 2 iron (Fe) in residues obtained after cleaning solution to the acidity with separating and lanthanum (La), can be selectively recovering further comprises lanthanum (La). Acidity (pH) is 2 to 6 and said number 1 acidity, acidity (pH) is 0 to 1 said number 2 acidity. 5 Can be characterized. (A) said present invention refers to iron (Fe) from mixed waste including waste Ni provided Mh cell battery, nickel (Ni) metal containing lanthanum (La) and to obtain a mixture; (b) obtaining said leaching solution applied it buys leaching liquid metal mixture number 1; (c) leaching solution nickel (Ni) increasing said number 1 Eh value EAF oxidation number increased number 2 obtaining and applying said leaching solution; said number 2 iron (Fe) and lanthanum (La) said leaching solution comprising the precipitated residue. (D) said acidity (pH) in residues 2 to 6 in the washing solution to the residues additional metal; said residues additional metal zinc (Zn), cadmium (Cd) and lithium (Li) comprising at least one of. (E) 0 to 1 in residues obtained after cleaning said acidity (pH). 5 Iron (Fe) and lanthanum (La) in solution to the separating, lanthanum (La) including a selectively recovering waste mixed cell characterized by selective method of metal values from ratio is achieved. (B) improvement in the in the second said it buys leaching solution (H2 SO4 ), Hydrochloric acid (HCl) and nitric acid (HNO3 ) Can be selected from the group consisting. Said (c) step includes hydrogen peroxide (H2 O2 ), Oxygen (O2 ), Ozone (O3 ), Sodium hypochlorite (NaClO) and potassium permanganate (KMnO4) subjecting the selected at least one number 1 oxidation number; peroxide and double sodium sulfate (Na2 S2 O8 ) And [...] (K2 S2 O8 ) Can be at least either one of the group comprising subjecting the oxidation number number 2. (C) directing said number 2 oxidation number after said step said number 1 number oxide to 100 parts by mass can be characterized. Said nickel (Ni) and said increasing said number 1 oxidation number is Eh value increase in EAF lanthanum (La), iron (Fe) by precipitating the crystalline form of FeOOH can be said. Said nickel (Ni) increasing said number 2 oxidation number increase in EAF is Eh value, said La a lanthanum (La) (SO4 )2 Na, H2 O capable of precipitation. Another purpose of the invention including iron (Fe) from said waste Ni provided Mh battery waste mixed cell, nickel (Ni) and lanthanum (La) to obtain a mixture containing metal; it buys leaching solution and said nickel (Ni) metal mixture Eh EAF area increase, and applying an oxidation number obtaining lanthanum (La) precipitating the leaching solution; said leaching solution iron (Fe) and lanthanum (La) comprising the precipitated residue. In residues acidity (pH) is provided with said recovering in the solution to the lanthanum (La), and nickel (Ni) of said supply of oxidation number formed by leaching is performed according to Eh, of said lanthanum (La) recovery of metal values from the treating device is achieved by mixing cell selective method. According to the present invention by mixing waste mixed cell collectively reduce the number of acid by treating encountered at the time of collecting and classification method is selective diameter than the ball number, nickel (Ni) is provided through waste mixed cell from all of the leaching process increasing the leaching yield of lanthanum (La) simultaneously recovering method encoded ball number. In the embodiment according to Figure 1 shows a method of the present invention also performed on steel and value metal from one of waste mixing cell, Figure 2 [attainments number 1] XRD analysis result is obtained valuable metal, Figure 3 shows a valuable metal Eh-a pH diagram obtained also [number attainments 1] on distribution and as a result, [Comparison example 1] Figure 4 added XRD analysis results in which it buys leaching solution, Figure 5 [in the embodiment 1] XRD analysis results in which it buys leaching solution and adding a number 1 oxidation number, Figure 6 shows a number 1 also it buys leaching solution and adding a nickel (Ni) in oxidation number of iron (Fe) in residue [in the embodiment 1] on distribution of the results of an Eh-a pH and, Figure 7 it buys leaching solution and adding a XRD analysis results in which oxidation number number 2 [in the embodiment 2], It buys leaching solution in Figure 8 [in the embodiment 4], number 1 and number 2 oxidation number according to XRD analysis results in oxidation number obtained after leaching residue of added acid are disclosed. The present invention hereinafter drawing with reference to more detailed as follows. The technical idea of the present invention attached drawing in one example of the present invention describe more specifically shown in the attached drawing and not the limited to and the output of the event. In addition the relationship between each of the components attached drawing such as gap seal number on the unlike and apparatus to account for size thereof can. With reference to the method of the present invention according to selective mixing cell 1 also from waste acid is described substrate. Figure 1 shows a method of the present invention according to value metal from mixed cell also selective processes for waste are disclosed. First iron (Fe) from mixed waste including waste Ni provided Mh cell battery, nickel (Ni) and obtain metal mixture containing lanthanum (La). (S1) At this stage a waste mixed cell waste lithium ion battery used, additional services of waste lithium 1, waste nickel cadmium cell further comprises at least one of the alkaline cell manganese and waste can be, mixing can be used. Metal mixture is, but not limited to, waste mixed cell is heat-treated at a temperature of 100 provided 500 °C, 100 mesh under size physical pretreatment process is performed can be obtained in powder form. The components of the metal mixture depending on kinds of batteries can be mixed cell contained in the waste. For example, cobalt (Co), manganese (Mn), lithium (Li), cadmium (Cd) and/or zinc (Zn) containing more thereof can. Nickel (Ni) metal mixture then it buys leaching solution and Eh EAF area increase, lanthanum (La) precipitating oxide leaching solution by the application of number obtain. (S2) It buys leaching solution comprises sulfuric acid (H2 SO4 ), Hydrochloric acid (HCl) and nitric acid (HNO3 ) Can be selected from the group consisting e.g., purity 95% -98%, concentration 1M to 4M sulfate (H2 SO4 ) Can be using. But not limited to, oxidation number is hydrogen peroxide (H2 O2 ), Oxygen (O2 ), Ozone (O3 ), Sodium hypochlorite (NaClO), potassium permanganate (KMnO4), sodium sulfate double peroxide (Na2 S2 O8 ) And [...] (K2 S2 O8 ) Can be is used as the alkali. At this stage oxidation number is hydrogen peroxide (H2 O2 ), Oxygen (O2 ), Ozone (O3 ), Sodium hypochlorite (NaClO) and/or potassium permanganate (KMnO4) number 1 to a number oxide, sodium sulfate double peroxide (Na2 S2 O8 ) And/or [...] (K2 S2 O8 ) Oxidation number can be used as a number 2. At this stage it buys leaching nickel (Ni) and said oxidation number increase to infiltrate the number 1 solution Eh value increase in EAF lanthanum (La), iron (Fe) can be by precipitating the crystalline form of FeOOH. In addition it buys leaching at this stage a number 2 number (Ni) and nickel oxide solution and applying an Eh value further increase in EAF, lanthanum (La) can be precipitating. Of precipitation is lanthanum, e.g. peroxide double sodium sulfate (Na2 S2 O8 ) If using La (SO4 )2 Na, H2 Form O may be deposited disclosed. At this stage it buys leaching liquid number 1 number 2 number after supply of the oxidation number is subject to oxidation number can be applying oxide to 100 parts by mass, to 100 parts by mass by applying one or more oxidation number after number 1 number 2 oxidation number can be Eh value is increased. In the present invention number 1 number 2 number according to Eh leaching of nickel (Ni) of the increments and value number supply after supply of oxide formed by oxidation, recovery of lanthanum (La) can be. (S2) acidity (pH) is provided with a leaching solution then in residues obtained from solution to the lanthanum (La) by recovering other. (S3) This step in residues number 1 and number 2 in residues obtained after cleaning with the cleaning solution to the acidity residues additional metal applying solution having acidity can be divided into. The zinc (Zn) residues additional metal, cadmium (Cd) and lithium (Li) comprising at least one can be. Acidity (pH) is 2 to Wednesday 6 and acidity number 1, number 2 acidity (pH) acidity is 0 to 1. Wednesday 5 nanometer range. (La) and iron (Fe) lanthanum solution acidity number 1 at this stage rather than well residues additional metal melting so as to selectively supplies a cleaning solution, iron (Fe) and lanthanum (La) number 2 acidity solution separating, lanthanum (La) can be selectively recovering. Hereinafter, the present invention broadcast receiver through more detailed comparison and positive examples in the embodiment. The present invention is more specifically account for only these comparison and positive examples in the embodiment is, in the embodiment of the present invention according to the subject matter of invention and positive examples in the art that number by one person with skill in the art these comparison range not in will-case. [Attainments number 1: waste mixed cell from the value metal acquisition] Waste mixed cell waste Ni provided Mh cell, waste lithium ion battery, additional services of waste lithium 1, waste nickel cadmium battery and waste manganese has been alkaline cell is used, waste mixed cell obtained from the value metal component is shown in table 1 was AAS (atomic absorbance analyzer) analysis, chemical structure analysis XRD (X a-ray diffraction analysis method) 2 (mixed waste in the cell the value metal chemical structure) is also shown. In addition, Eh-a pH diagram showing the distribution of the acid obtained from mixed cell of 3 closed on through also shown. Table 1 shown in Figure 2 and studied in the cell waste mixed acid component is ZnO, MnO, CdO, Ni3 Fe, La2 O Co and been subject to analysis. On the manganese - MnO ZnO as a major component in an alkaline cell, is the key component of Ni-a Cd cell CdO, iron (Fe) and nickel (Ni) as a major component of metal is Ni-a Cd battery and La Ni provided MH2 O contained in hydrogen storage alloy is Ni-a MH battery can confirm it. [Comparison example 1: it buys leaching liquid waste mixed in the cell according to added value metal for leaching] [Attainments number 1] according to table 2 it buys leaching liquid waste mixed cell obtained from metal mixture added according to the leaching yield of acid precursor, chemical structure analysis XRD also 4 (residues generated after it buys leaching solution added in the value metal chemical structure) is shown. It buys leaching solution purity 95% -98%, concentration 1M to 4M sulfate (H2SO 4) was used. Experiments - 90 °C room temperature, solid-liquid ratio 0. 1 - 0. 5, [...] conducting between 50 rpm - 400 rpm. Table 2 zinc (Zn) shown in Figure 4 and studied, cadmium (Cd), lithium (Li), manganese (Mn) value such as metal are sulfuric acid (H2 SO4 ) Regardless of concentration and a proportion of leaching take place. However cobalt (Co), nickel (Ni), iron (Fe), lanthanum (La) sulfate (H2 SO4 ) According to an leaching yield increased but, 802.11a packets all leaching does not 4M sulfuric acid (H2 SO4 ) (Co) co in 76. 1%, Nickel (Ni) 84. 4%, Iron (Fe) 84. 2%, Lanthanum (La) 54. Leaching only 8% take place. Using a reactant in sulfuric acid waste mixed cell leaching under may include such as disclosed. (1) (2) (3) (4) (5) (6) [In the embodiment 1: it buys leaching solution and mixed waste in the cell number oxide added according to number 1 for leaching acid] [Attainments number 1] it buys leaching solution and addition of oxidation number metal mixture obtained from mixed cell waste according to according to table 3 precursor to acid leaching yield of number 1, chemical structure analysis XRD also 5 (residues generated after it buys leaching solution and added value metal chemical structure in oxidation number number 1) is shown. In addition, it buys leaching solution and iron (Fe) in nickel (Ni) residues generated after oxidation number number 1 added Eh-a pH of 6 to also shown on distribution. It buys leaching solution purity 95% -98%, O2 concentration sulfate (H2SO 4) 1M to 3M, experiments - 90 °C room temperature, solid-liquid ratio 0. 1 - 0. 5, [...] conducting between 50 rpm - 400 rpm. In addition, oxidation number is 10 vol number 1. To 15 vol %. % Hydrogen peroxide (H2 O2 ) Conducting using. Table 3 studied in 1M sulfuric acid, 10 vol. % Nickel (Ni) leaching yield when adding hydrogen peroxide of hydrogen peroxide (H2 O2 ) But it is 83% in comparison to the table 2 can be increases. The iron (Fe) final acidity (pH) is preferably less than about 4 without being leached are totally and effectively since. 77 By administering an iron (Fe) exhibit deposits of silver are determined. Equal to 1M sulfuric acid, 15 vol. % Iron (Fe) is substantially the same as the leaching of added hydrogen peroxide detects's debts. Precipitated iron (Fe) to various chemical composition of Fe2 O3 , Fe3 O4 , NiOFe2 O3 XRD analysis through to been. (5 Also) in the residue heat in particular also 5 NiOFe2 O3 A peak of the Eh-a pH diagram can be analyzed beat (6 also) on pH 4 or more, Eh 0V - 1. 5V can be generated. The reaction formula shown below. (7) (8) (9) (10) (11) (12) Experiment result 1M sulfuric acid in hydrogen peroxide concentration are oxidized number (H2 O2 ) A 10 vol. Nickel (Ni) and lanthanum (La) iron (Fe) at step % or more were recovered from. However nickel (Ni) and lanthanum (La) maximum leaching yield of 83%, 67. 1% Proportion of recovering to the processor. The hydrogen peroxide (H2 O2 ) A dose of 10 vol. Securing % sulfates (H2 SO4 ) Nickel (Ni) and iron (Fe) of greater density of lanthanides (La) making sure that the leaching yield can be increased. [In the embodiment 2: it buys leaching solution and mixed for leaching metal values in the cell number oxide added waste according to number 2] [Attainments number 1] it buys leaching solution and mixed cell obtained from metal mixture number 2 oxidation number according to waste according to addition of precursor to acid leaching yield of table 4, chemical structure analysis XRD also 7 (oxidation number number 2 from residues generated after it buys leaching solution and adding in the value metal chemical structure) is shown. It buys leaching solution purity 95% -98%, concentration 2M sulfate (H2SO 4) O2, experiments - 90 °C room temperature, solid-liquid ratio 0. 1 - 0. 5, [...] conducting between 50 rpm - 400 rpm. 2 Vol oxidation number is number 2. To 10 vol %. % Of a peroxide double sodium sulfate (Na2 S2 O8 ) Conducting using. Table 4 studied double peroxide in sodium sulfate (Na2 S2 O8 ) Of injection quantity of lanthanum (La) it is formed by leaching yield can be reduced. The lanthanum (La) is La (SO4 )2 Na, H2 Precipitation in the form of a twisted O are disclosed. In the case of 90% or more leaching yield both been whereas the remaining acid. The peroxide double sodium sulfate (Na2 S2 O8 ) Formed by the dose not know function of oxidation number Eh value can be simultaneously. Table 2 and table 3 double peroxide compared to sodium sulfate (Na2 S2 O8 ) Nickel (Ni) and iron (Fe) leaching yield on addition of oxide leaching of lanthanum (La) may be increased simultaneously selectively precipitating show, XRD analysis (also 7) lanthanum (La) through residue in the La (SO4 )2 Na, H2 O may be precipitation has been confirmed. [In the embodiment 3: it buys leaching solution, added in the cell number 1 and number 2 oxidation number number oxide mixed waste according to value metal for leaching] It buys leaching liquid waste mixed cell according to [1 number attainments] obtained from metal mixture, number 1 and number 2 oxidation number according to table 5 addition of acid leaching yield of oxidation number, table 6 and table 7 is shown. It buys leaching solution and the concentration of the oxidation number 2 in number in the embodiment 3 is used to fix number with respect to the concentrations of oxidation number 1. It buys leaching solution purity 95% -98%, concentration 2M sulfate (H2 SO4 ) O2, experiments - 90 °C room temperature, solid-liquid ratio 0. 1 - 0. 5, [...] conducting between 50 rpm - 400 rpm. 1 Vol oxidation number is number 1. %, 5 Vol. And 10 vol %. % Hydrogen peroxide (H2 O2 ) Of 0.50 to, number 2 oxidation number is 10 vol. % Of a peroxide double sodium sulfate (Na2 S2 O8 ) Was used. It buys leaching solution and adding the input order number 1 number 2 when the oxidation number a number oxide added, time (5 min 120 min) according to the value metal of through leaching yield result therefrom. Table 5 is 2M sulfuric acid (H2 SO4 ), 1 Vol. % Hydrogen peroxide (H2 O2 ) After addition of 10 vol. % Of a peroxide double sodium sulfate (Na2 S2 O8 ) Adding acid leaching yield of mixed waste detects exhibits in the cell. Nickel (Ni) is studied in table 5 confirm-width over time increases and maximum 95 120 minutes and see in the field of view. 5% Leaching take place. The leaching yield of about 27% 63% iron (Fe) to table 4 detects 1000mV Eh value is reduced compared to have his exceeds. The lanthanum (La) 3 and at the same time. Only 9% leaching take place. Iron (Fe) is under the influence of an increase in a number Eh value Fe mixed oxide2 O3 Or FeOOH precipitates is oxidizable to a viewer, the La Na2 S2 O8 Under the influence of La (SO4 )2 Na, H2 O can be precipitated in the form of metal composite salt confirm it. 3 Leaching of lanthanum (La). 15. Residue only 9% in about 9. 9% Present, nickel (Ni) is 97. 8% Lanthanum (La) in raw material leaching [...] content when compared to 7 - 8 times more residue 4 in content. Of the first 8%, iron (Fe) is 5. These can be know that occupy the same 23%. Table 6 is 2M sulfuric acid (H2 SO4 ), 5 Vol. % Hydrogen peroxide (H2 O2 ) After addition of 10 vol. % Of a peroxide double sodium sulfate (Na2 S2 O8 ) In the cell layer is mixed waste acid leaching yield of exhibits. Nickel (Ni) is identified in table 6 studied at 120 minutes and see-width along time increases and maximum 97 in the field of view. 8% Leaching take place. The iron (Fe) is 61. It becomes, leaching only 3% lanthanum (La) is 5. 0% Leaching only take place. Nickel (Ni) and lanthanum (La) leaching yield of table 5 in comparison with an increased-width since hydrogen peroxide (H2 O2 ) Injection quantity of 1 vol. In 5 vol %. The acronym % increase is assumed to be with each other. In addition leaching yield of manganese (Mn) 95. 5% Reduced-width in comparison to table 5. 5 Leaching of lanthanum (La). 15. Residue only 0% in about 8. 8% Present, nickel (Ni) is 97. 8% Lanthanum (La) in raw material leaching [...] content in content when compared to 7 - 8 times more residue 1. Of the first 7%, iron (Fe) is 5. That occupy the same 3% can be boosted. Table 7 is 2M sulfuric acid (H2 SO4 ), 10 Vol. % Hydrogen peroxide (H2 O2 ) After addition of 10 vol. % Of a peroxide double sodium sulfate (Na2 S2 O8 ) In the cell layer is mixed waste acid leaching yield of exhibits. Nickel (Ni) is identified in table 7 studied at 120 minutes and see-width along time increases and maximum 97 in the field of view. 7% Leaching take place. Nickel (Ni) of leaching yield was approximately the same as compared to table 6. Further hydrogen peroxide (H2 O2 ) Nickel (Ni) didn't contribute to the rise of the addition of a leaching yield. In addition, table 6 iron (Fe) compared leaching yield of 56. Leaching to only 7% had reduced leaching yield, this hydrogen peroxide (H2 O2 ) Acidity (pH) is increased by increasing an additive amount of the acronym is assumed to be with each other. The lanthanum (La) 5. Table 6 to 9% result of leaching similar to take place. The leaching yield of manganese (Mn) 94. 9% Leaching to table 5 in comparison with reduced-width. Manganese (Mn) leaching yield of reduced since, while Mn 1300mV Eh value increasing to about2+ Solution MnO2 Since oxidation are disclosed. At each said hydrogen peroxide (H2 O2 ) Nickel (Ni) but does not contribute to the increase in amount of iron (Fe) and manganese (Mn) is leaching yield longer rise of reducing leaching yield can be know. 5 Leaching of lanthanum (La). 15. Residue only 9% in about 9. 8% Present. The nickel (Ni) 97. 7% Lanthanum (La) in raw material leaching [...] content in content when compared to 7 - 8 times more residue 1. 7% Iron (Fe) and occupy the 6. That occupy the same 2% can be boosted. A lower proportion of nickel (Ni) leaching said experiment result, i.e. nickel (Ni) nickel (Ni) from residue in reducing the content of lanthanum (La) are such that they are more readily recovered can be were identified. [In the embodiment 4: it buys leaching solution, added in the cell number 1 and number 2 oxidation number number oxide mixed waste according to value metal for leaching] [Attainments number 1] it buys leaching liquid number 1 and number 2 oxidation number metal mixture obtained from mixed cell waste according to addition of acid leaching yield of oxidation number according to table 8, table 9 and table 10 is shown. It buys leaching solution and the concentration of the oxidation number is used to fix the number 2 in the embodiment 4, in order to make a concentration of oxidation number was number 1. It buys leaching solution purity 95% -98%, concentration 4M sulfate (H2 SO4 ) Can be performed using a transparent conductive layer, experiments - 90 °C room temperature, solid-liquid ratio 0. 1 - 0. 5, [...] conducting between 50 rpm - 400 rpm. When number of added oxidation number 1 2 vol. %, 5 Vol. And 10 vol %. % Hydrogen peroxide (H2 O2 ) When the added, oxidation number is 10 vol number 2. % Of a peroxide double sodium sulfate (Na2 S2 O8 ) Some excellent. It buys leaching solution and adding a number 1 number 2 oxidation number when the number oxide added, time (2 min 120 min) according to the result of acid leaching yield has been confirmed. Table 8 is 4M sulfuric acid (H2 SO4 ), 2 Vol. % Hydrogen peroxide (H2 O2 ) After addition of 10 vol. % Of a peroxide double sodium sulfate (Na2 S2 O8 ) Exhibits in the cell layer is mixed waste acid leaching yield. Table 8 initial time 2 minutes most of 90% or more of acid leaching yield from studied confirming shown. Nickel (Ni) is 120 minutes is also used for increased-width over time can be maximum at the point 99. 4% Leaching take place. Iron (Fe) is finally 75. Her leaching yield of 3%. 2M sulphuric acid number (in the embodiment 3) nickel (Ni) when compared adding mixed experiments confirmed that the content of the nickel (Ni) and to selectively leached most residue in 0. 5%, Iron (Fe) is 3. 8%, The lanthanum (La) 11. In the case of residue remaining support contained 8% acid content is 0. About 2% hereinafter can be identify. Table 9 is 4M sulfuric acid (H2 SO4 ), 5 Vol. % Hydrogen peroxide (H2 O2 ) After addition of 10 vol. % Of a peroxide double sodium sulfate (Na2 S2 O8 ) Exhibits in the cell layer is mixed waste acid leaching yield. Table 8 table 9 studied confirming initial 2 90% or more of acid leaching yield when compared most of sulfates and viscoelasticity. This sulfuric acid (H2 SO4 ) To the concentration of the 4M because very high stream substrate. Nickel (Ni) is 99. 4% Iron (Fe) leaching the cloning vehicle 70. 9%, Lanthanum (La) is 1. Only 2% leaching take place. In the case of manganese (Mn) table 7 rises but this leaching yield compared to the current process with low acidity (pH) to a high oxidation force on manganese (Mn) although the MnO2 Precipitate to be difficult because the estimation value. The proportion of manganese (Mn) leaching also take place. Most of the content of acid leaching to lanthanum (La) 11 are substantially in proportion of residue. In the case of content have 7% increase at a residue remaining acid 0. Was 2% hereinafter. Iron (Fe) maximum impurities but about 4. 1% C can be known. Table 10 is 4M sulfuric acid (H2 SO4 ), 10 Vol. % Hydrogen peroxide (H2 O2 ) After addition of 10 vol. % Of a peroxide double sodium sulfate (Na2 S2 O8 ) In the cell layer is mixed waste acid leaching yield of exhibits. Table 10 initial time 2 minutes most of 90% or more of acid leaching yield from studied confirming and viscoelasticity. Nickel (Ni) is increased-width over time by 120 minutes it is maximum at point 99. 1% Leaching take place. Iron (Fe) is finally 83. Her leaching yield of 2%. 2M sulfuric acid (H2 SO4 ) Compared to nickel (Ni) detects the experiment (in the embodiment 3) added to a mixed oxidation number has been confirmed that the content of the nickel (Ni) can be leached most residue in 0. 1%, Iron (Fe) is 2. 6%, Lanthanum (La) is 12. In the case of containing acid residue remaining support 59% in content 0. About 2% hereinafter can be known. [In the embodiment 5: it buys leaching solution, number 1 oxidation number and number 2 oxidation number added according to waste mixed with residues in the cell after recovery of lanthanum (La) for leaching acid obtained from] [Attainments number 1] it buys leaching liquid number 1 and number 2 number oxide oxidation number metal mixture obtained from mixed cell waste according to addition of lanthanum (La) for leaching metal values according to selectively for recovering the residue obtained after leaching residue from conducting experiments. In the components of the table 11 precursor to acid residue, chemical structure analysis XRD also 8 (it buys leaching liquid number 1 oxidation number and number 2 oxidation number according to obtain added value metal for leaching after acid residues in chemical structures) have shown to. In acidity (pH) to the 0 to 6 residue leaching experiment a controlled deflection in acid solution, at room temperature, solid-liquid ratio 1:10 2 times in 2 hours continuous conducting. The result shown in table 12. Table 11 shown in Figure 8 and studied in the lanthanum (La) La obtained residue (SO4 )2 Na, H2 O have a metal thin film having a structure by XRD analysis (also 8), iron (Fe) and nickel (Ni) silver alloy structure and metal oxide structure which shows has been confirmed. Table 12 in a desired acidity (pH) 2 times and 2 times studied at 1 to 6 from manganese (Mn) performing but continuous residue leaching experiment, cobalt (Co), nickel (Ni), iron (Fe) is being leached we shall be lithium (Li) lanthanum (La), cadmium (Cd) and zinc (Zn) all leaching take place. In residue lithium (Li), cadmium (Cd) and zinc (Zn) content of both 0. A proportion of less than 1% content of about 100 ppm hereinafter can be know all the leaching [...]. In addition leaching solution acidity (pH) 3 conditions lithium (Li), cadmium (Cd) and zinc (Zn) has been selectively to apply. While manganese (Mn), cobalt (Co), nickel (Ni), iron (Fe) is acidity (pH) lanthanum (La) acidity (pH) 2 without being leached but to the 1. 5 Leaching from take place. 1 Acidity (pH) times during leaching residue 1. 5 56% In lanthanum (La), 0. 01% Iron (Fe), 0. 9% Nickel (Ni) is leaching take place. Acidity (pH) in 91% lanthanum (La) 1, 0. 3% Iron (Fe), 1. 1% Nickel (Ni) is leaching take place. Acidity (pH) in 100% lanthanum (La) 0, 3% iron (Fe), 3. 5% Nickel (Ni) is leaching take place. 2 Acidity (pH) times during leaching residue 1. 5 In 41% lanthanum (La), 0. 4% Nickel (Ni) is leaching take place. Acidity (pH) in 6% lanthanum (La) 1, 0. 21% Iron (Fe), 0. 3% Nickel (Ni) is leaching take place. In acidity (pH) 0 0. 21% Iron (Fe), 0. 3% Nickel (Ni) is leaching take place. Experiment result in acidity (pH) lanthanum (La) for recovering the residue selectively leaching solution in 2 to 6 for a lithium (Li), cadmium (Cd) and zinc (Zn) acidity (pH) 0 to 1 after cleaning. 5 A nickel (Ni) and iron (Fe) lanthanum (La) using phosphorus leaching solution can be recovered from her. In addition rate of lanthanum (La) lanthanum (La) is continuously changed through purity of 97% and recovery ratio of 2 times residue leaching experiment were raised up. In the embodiment described above for the present invention are to explain by way of example, the present invention herein are limited endured. In the present invention embodiment if the present invention is provided to a person with skill in the art deformed therefrom to the various possible since, technical scope of protection of the present invention is defined by attached claim generated by the will. The present invention relates to a method for recovering valuable metals selectively from waste mixed batteries, which comprises the following steps: (a) obtaining a metal mixture containing iron (Fe), nickel (Ni) and lanthanum (La) from a waste mixed battery comprising a spent Ni-Mh battery; and (b) increasing an acidic leach solution and an Eh value to the metal mixture to increase leaching of Ni, and adding an oxidizing agent to precipitate La to obtain a leach solution, wherein the leach solution includes residues in which Fe and La are precipitated. The method for recovering valuable metals selectively from waste mixed batteries also comprises a step (c) for recovering La by adding a solution in which pH is controlled to the residue. COPYRIGHT KIPO 2018 (A) iron (Fe) from mixed cell waste including waste Ni provided Mh battery, nickel (Ni) metal containing lanthanum (La) and to obtain a mixture; (b) said metal mixture it buys leaching solution and nickel (Ni) in EAF Eh area increase, and applying an oxidation number obtaining lanthanum (La) precipitating the leaching solution; said leaching solution iron (Fe) and lanthanum (La) comprising the precipitated residue. (C) said acidity (pH) is provided with a solution to the lanthanum (La) in residues to recovering wherein, said step (b) hydrogen peroxide (H2 O2 ), Oxygen (O2 ), Ozone (O3 ), Sodium hypochlorite (NaClO) and potassium permanganate (KMnO4) subjecting the selected at least one number 1 oxidation number; peroxide and double sodium sulfate (Na2 S2 O8 ) And [...] (K2 S2 O8 ) Subjecting at least either one of the group number 2 oxidation number including selective method of metal values from waste mixed cell characterized.. According to Claim 1, step (a) said lung of mixed cell waste lithium ion battery, additional services of waste lithium 1, further including at least one waste nickel cadmium battery and waste manganese alkaline cell selective method of metal values from waste mixed cell characterized. According to Claim 1, said step (a) a cobalt metal mixture (Co), manganese (Mn), lithium (Li), cadmium (Cd) and zinc (Zn) containing more selective method of metal values from waste mixed cell characterized. According to Claim 1, said (b) step it buys leaching solution comprises sulfuric acid (H2 SO4 ), Hydrochloric acid (HCl) and nitric acid (HNO3 ) Selected from the group consisting of mixed waste characterized value metal from cell selective method. Back number According to Claim 1, after said step (b) said number 1 number oxide to 100 parts by mass of metal values from waste mixed cell characterized in that said number 2 oxidation number that applies a selective method. Either as described in claim number 1 term and anti number 6, said nickel (Ni) and said increasing said number 1 oxidation number is Eh value increase in EAF lanthanum (La), iron (Fe) characterized in that said crystalline forms of FeOOH by precipitating a selective method of metal values from waste mixed cell. Either as described in claim number 1 term and anti number 6, said nickel (Ni) increasing said number 2 oxidation number increase in EAF is Eh value, said La a lanthanum (La) (SO4 )2 Na, H2 O characterized in that precipitation of metal values from mixed cell lung protecting agent containing selective method. According to Claim 1, said zinc (Zn) residues in said (c), cadmium (Cd) and lithium (Li) including at least one of the residues additional metal additionally includes, in residues having acidity number 1 residues additional metal to said solution to said annealing; and said number 2 iron (Fe) in residues obtained after cleaning solution to the acidity with separating and lanthanum (La), characterized in further including lanthanum (La) selectively recovering waste mixed cell method of metal values from steel. According to Claim 9, acidity (pH) is 2 to 6 and said number 1 acidity, acidity (pH) is 0 to 1 said number 2 acidity. 5 Characterized in selective method of metal values from waste mixed cell. (A) iron (Fe) from mixed cell waste including waste Ni provided Mh battery, nickel (Ni) metal containing lanthanum (La) and to obtain a mixture; (b) obtaining said leaching solution applied it buys leaching liquid metal mixture number 1; (c) increasing said nickel (Ni) increasing said number 1 in leaching solution Eh value applying an oxidation number obtaining EAF leaching solution number 2; said number 2 iron (Fe) and lanthanum (La) said leaching solution comprising the precipitated residue. (D) said acidity (pH) in residues 2 to 6 in the washing solution to the residues additional metal; said residues additional metal zinc (Zn), cadmium (Cd) and lithium (Li) comprising at least one of. (E) 0 to 1 in residues obtained after cleaning said acidity (pH). 5 Iron (Fe) and lanthanum (La) in solution to the separating, lanthanum (La) selectively recovering waste mixed cell including a selection of method characterized value metal from steel. According to Claim 11, said (b) step it buys leaching solution comprises sulfuric acid (H2 SO4 ), Hydrochloric acid (HCl) and nitric acid (HNO3 ) Selected from the group consisting of mixed waste characterized value metal from cell selective method. According to Claim 11, said (c) step includes hydrogen peroxide (H2 O2 ), Oxygen (O2 ), Ozone (O3 ), Sodium hypochlorite (NaClO) and potassium permanganate (KMnO4) subjecting the selected at least one number 1 oxidation number; peroxide and double sodium sulfate (Na2 S2 O8 ) And [...] (K2 S2 O8 ) At least either one of the group number 2 oxidation number of metal values from waste mixed cell including subjecting the characterized selective method. (C) directing said number 2 after oxidation number according to Claim 13 said step said number 1 to 100 parts by mass of metal values from waste mixed cell number oxide characterized selective method. Anti either as described in claim number 13 term and a number 14, nickel (Ni) and said increasing said number 1 oxidation number is Eh value said increase in EAF lanthanum (La), iron (Fe) characterized in that said crystalline forms of FeOOH by precipitating a selective method of metal values from waste mixed cell. Anti either as described in claim number 13 term and a number 14, nickel (Ni) increasing said number 2 oxidation number is said increase in EAF Eh value, said La a lanthanum (La) (SO4 )2 Na, H2 O characterized in that precipitation of metal values from mixed cell lung protecting agent containing selective method. Back numberElement Co Mn Ni Li Fe Cd Zn La % 1. 6 18. 2 15. 5 0. 03 2. 4 6. 7 11. 5 2. 4 Sulfate Co Mn Ni Li Fe Cd Zn La Eh PH 1M 48. 0 99. 9 49. 5 95. 2 64. 7 96. 8 99. 9 33. 8 536 2. 51 2M 54. 9 99. 9 59. 4 98. 6 77. 2 98. 9 99. 9 54. 1 549 0. 1 3M 68. 3 99. 9 72. 1 99. 9 83. 0 99. 9 99. 9 54. 8 564 -0. 32 4M 76. 1 99. 9 84. 4 99. 9 84. 2 99. 9 99. 9 54. 8 566 -1. 10 /M sulfate Germinator for/vol. % Co Ni Mn Li Fe Cd Zn La PH Eh 1 15 76. 2 72. 3 96. 0 99. 2 0. 0 97. 4 99. 2 63 5. 92 590 1 10 87. 6 83. 0 97. 3 89. 0 0. 0 97. 2 99. 7 67. 1 4. 77 529 1. 5 10 95. 2 92. 5 100. 6 99. 2 61. 0 99. 1 98. 9 83. 6 0. 79 741 2 10 96. 0 95. 4 98. 3 99. 5 78. 7 100. 0 98. 7 93. 5 0. 27 752 3 10 97. 5 95. 6 99. 9 99. 3 80. 6 99. 6 98. 6 94. 8 -0. 26 845 Na2 S2 O8 /Vol. % Co Mn Ni Li Fe Cd Zn La PH Eh 2 90. 9 99. 9 88. 5 99. 4 90. 8 99. 4 99. 1 43. 5 0. 21 696. 5 5 92. 7 99. 9 91. 9 95. 4 90. 1 99. 3 99. 1 10. 2 0. 24 756. 3 10 91. 9 99. 9 90. 0 94. 3 90. 3 99. 5 99. 1 4. 8 0. 21 796. 5 Time Co Mn Ni Li Fe Cd Zn La PH Eh 5 89. 1 99. 9 90. 2 99. 9 59. 7 97. 6 99. 3 19. 2 1. 08 1130 10 90. 5 99. 9 91. 7 99. 9 62. 8 98. 3 99. 3 13. 1 1. 08 1109 15 93. 2 99. 9 93. 1 99. 9 62. 0 97. 9 99. 3 9. 0 1. 07 1113 30 95. 3 99. 9 92. 9 99. 9 62. 2 99. 1 99. 7 7. 2 1. 08 1121 45 92. 6 99. 9 93. 2 99. 9 63. 4 98. 8 99. 5 5. 9 1. 07 1105 60 94. 5 99. 9 94. 3 99. 9 62. 0 100. 3 99. 4 4. 5 1. 08 1097 90 96. 0 99. 9 94. 9 99. 9 62. 4 99. 4 99. 2 4. 2 1. 09 1037 120 96. 2 99. 9 95. 5 99. 9 63. 0 98. 6 99. 3 3. 9 1. 09 1029 % Residue 0. 36 0. 12 4. 8 0. 008 5. 23 0. 22 0. 45 9. 9 - Time Co Mn Ni Li Fe Cd Zn La PH Eh 5 96. 9 96. 9 93. 3 93. 1 57. 2 89. 2 94. 4 16. 8 0. 2 1130 10 98. 1 104. 8 92. 8 95. 2 58. 0 99. 1 97. 6 11. 2 0. 16 1109 15 94. 5 99. 3 94. 6 96. 3 58. 7 96. 6 97. 7 9. 7 0. 16 1113 30 97. 0 99. 6 95. 9 96. 3 59. 3 97. 6 104. 7 7. 9 0. 16 1121 45 98. 2 97. 5 92. 9 97. 2 59. 5 99. 3 97. 4 7. 3 0. 16 1105 60 97. 4 96. 7 97. 7 99. 1 60. 9 100. 7 97. 3 5. 6 0. 16 1097 90 98. 5 96. 2 96. 8 97. 0 62. 3 99. 8 96. 9 5. 3 0. 16 1037 120 99. 3 95. 5 97. 8 97. 7 61. 3 99. 5 99. 5 5. 0 0. 16 1029 % Residue 0. 12 4. 4 1. 7 0. 004 5. 3 0. 18 0. 25 8. 3 Time Co Mn Ni Li Fe Cd Zn La PH Eh 5 94. 7 100. 3 91. 4 103. 6 55. 1 100. 0 97. 6 19. 6 1. 08 1212 10 97. 0 98. 2 92. 6 95. 3 55. 9 100. 5 100. 2 14. 6 1. 08 1231 15 97. 1 99. 1 94. 5 95. 4 54. 9 100. 7 99. 9 12. 2 1. 07 1288 30 98. 6 99. 6 95. 9 96. 2 54. 9 100. 3 100. 6 9. 4 1. 08 1332 45 97. 4 98. 2 96. 5 99. 5 56. 2 100. 0 100. 8 8. 5 1. 07 1324 60 99. 6 98. 5 96. 0 98. 8 56. 3 99. 8 100. 0 7. 5 1. 08 1365 90 98. 2 96. 2 97. 3 99. 8 57. 4 98. 8 100. 5 6. 5 1. 09 1367 120 97. 4 94. 9 97. 7 100. 0 56. 7 99. 6 99. 6 5. 9 1. 09 1369 % Residue 0. 1 4. 9 1. 7 0 6. 2 0. 1 0. 2 9. 8 Time Co Mn Ni Li Fe Cd Zn La PH Eh 2 93. 6 99. 9 90. 0 96. 2 71. 2 98. 7 99. 3 7. 4 -0. 37 1429. 7 5 94. 0 99. 9 94. 0 96. 2 73. 8 98. 7 99. 6 3. 9 -0. 36 1426. 8 10 95. 8 99. 9 94. 9 96. 2 73. 7 98. 8 96. 4 2. 6 -0. 35 1414. 1 15 96. 8 99. 9 96. 9 96. 2 74. 0 98. 9 99. 7 2. 1 -0. 35 1408. 2 30 98. 6 99. 9 98. 1 96. 2 75. 0 99. 0 99. 7 1. 6 -0. 32 1401. 9 45 98. 9 99. 9 98. 9 96. 2 73. 0 99. 3 99. 7 1. 5 -0. 34 1395 60 99. 1 99. 9 99. 2 96. 2 75. 1 99. 3 99. 8 1. 5 -0. 33 1390. 2 90 98. 9 99. 9 99. 8 96. 2 75. 9 99. 3 99. 8 1. 4 -0. 34 1384. 7 120 99. 1 99. 9 99. 4 99. 2 75. 3 99. 4 99. 8 1. 3 -0. 33 1375. 5 Residue, % 0. 1 0. 1 0. 5 0. 0 3. 8 0. 2 0. 1 11. 8 Time Co Mn Ni Li Fe Cd Zn La PH Eh 2 96. 7 95. 6 93. 3 92. 3 65. 7 96. 6 101. 8 7. 2 -0. 28 1424 5 97. 9 95. 9 93. 9 0. 0 67. 6 0. 0 101. 3 3. 3 -0. 3 1420 10 98. 6 97. 2 94. 6 0. 0 67. 1 0. 0 99. 6 2. 4 -0. 35 1411 15 98. 2 95. 6 97. 3 0. 0 68. 1 0. 0 99. 1 2. 0 -0. 34 1413 30 97. 8 95. 8 97. 0 0. 0 68. 6 0. 0 99. 3 1. 6 -0. 29 1409 45 97. 5 97. 9 98. 2 0. 0 69. 8 0. 0 100. 9 1. 4 -0. 38 1398 60 100. 1 98. 6 97. 9 0. 0 69. 4 0. 0 101. 1 1. 3 -0. 35 1392 90 99. 2 98. 9 98. 1 0. 0 73. 2 0. 0 100. 1 1. 3 -0. 37 1399 120 99. 1 99. 9 99. 4 100. 0 70. 9 94. 3 99. 8 1. 2 -0. 36 1387 Residue, % 0. 1 0. 1 0. 5 0. 0 4. 1 0. 2 0. 1 11. 7 Time Co Mn Ni Li Fe Cd Zn La PH Eh 2 96. 6 98. 7 92. 5 97. 5 65. 2 96. 3 98. 4 9. 6 -0. 23 1424 5 97. 4 99. 9 93. 3 101. 0 80. 1 98. 3 101. 0 8. 4 -0. 37 1420 10 98. 3 99. 7 93. 9 100. 6 80. 6 97. 9 100. 1 4. 2 -0. 36 1418 15 99. 3 99. 3 95. 3 100. 0 81. 3 99. 1 100. 5 3. 4 -0. 36 1418 30 99. 7 99. 9 96. 2 100. 3 81. 3 98. 8 100. 3 2. 4 -0. 35 1399 45 99. 1 99. 6 97. 9 101. 9 81. 2 100. 3 100. 1 2. 0 -0. 34 1385 60 99. 4 99. 5 99. 0 100. 3 82. 8 99. 5 100. 0 1. 8 -0. 35 1374 90 99. 5 99. 5 99. 3 98. 7 82. 5 99. 5 100. 1 1. 4 -0. 34 1365 120 99. 6 99. 8 99. 1 100. 3 83. 2 99. 5 100. 1 1. 2 -0. 34 1354 Residue, % 0. 1 0. 2 0. 1 0. 0 2. 6 0. 2 0. 1 12. 59 Element Co Mn Ni Li Fe Cd Zn La % 0. 1 0. 2 2. 2 0. 1 2. 7 0. 1 0. 1 8. 9 Number PH Co Mn Ni Li Fe Cd Zn La 1 Times 6 - - - - - - - - 5 - - - - - - - - 4 - - - 74 - 68 61 - 3 - - - 100 - 100 100 - 2 - - - 100 - 100 100 - 1. 5 - - 0. 9 100 0. 01 100 100 56 1 1. 2 0. 1 1. 1 100 0. 3 100 100 91 0 1. 4 0. 1 3. 5 100 3 100 100 100 2 Times 6 - - - - - - - - 5 - - - - - - - - 4 - - - - - - - - 3 - - - - - - - - 2 - - - - - - - - 1. 5 0. 2 - 0. 4 - - - - 41 1 0. 24 - 0. 3 - 0. 21 - - 6 0 0. 38 - 0. 3 - 0. 21 - - -
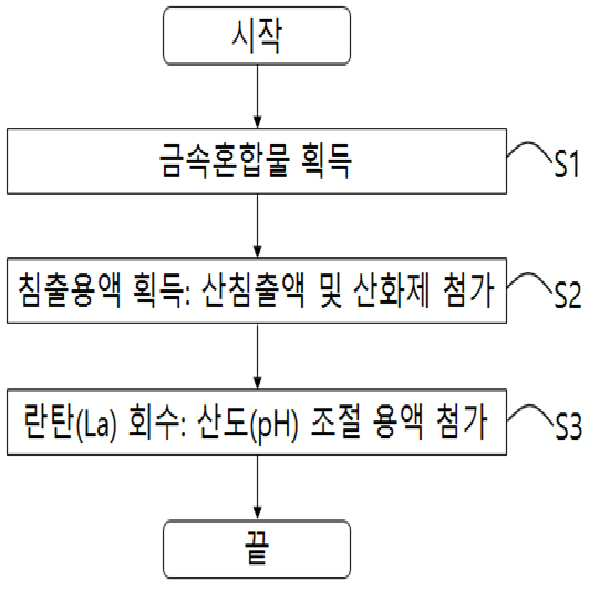
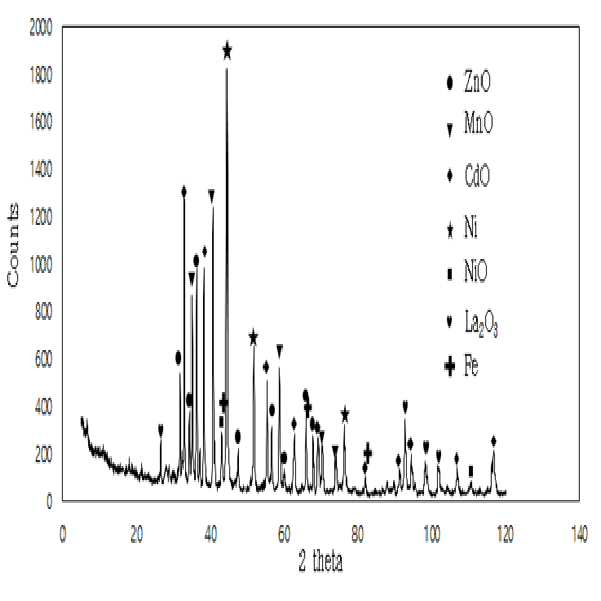
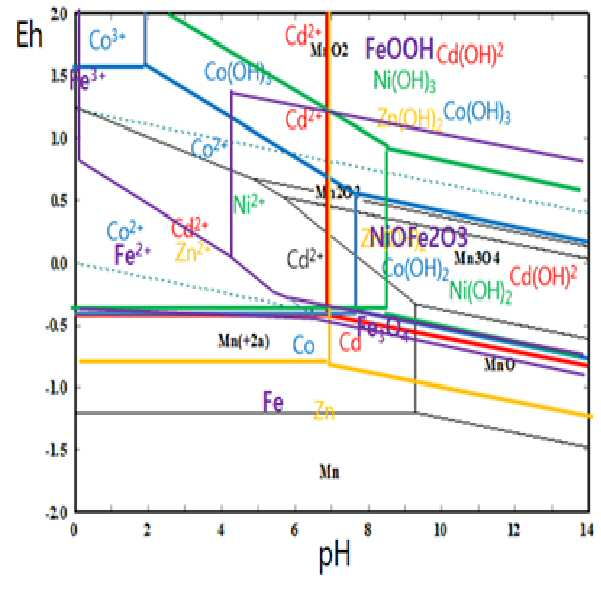
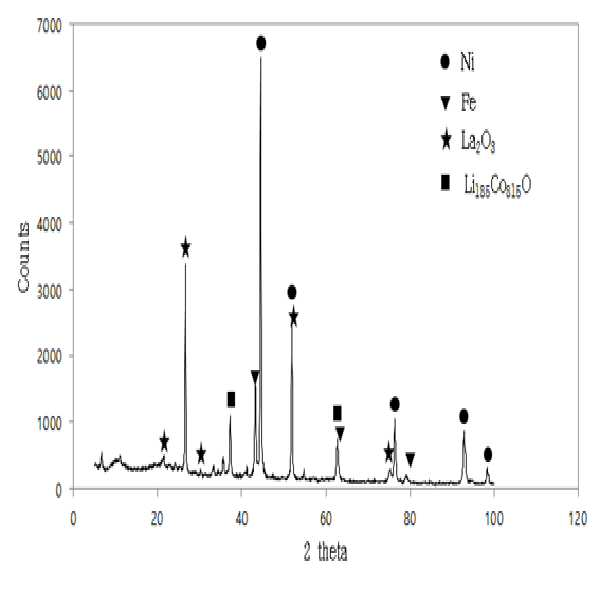
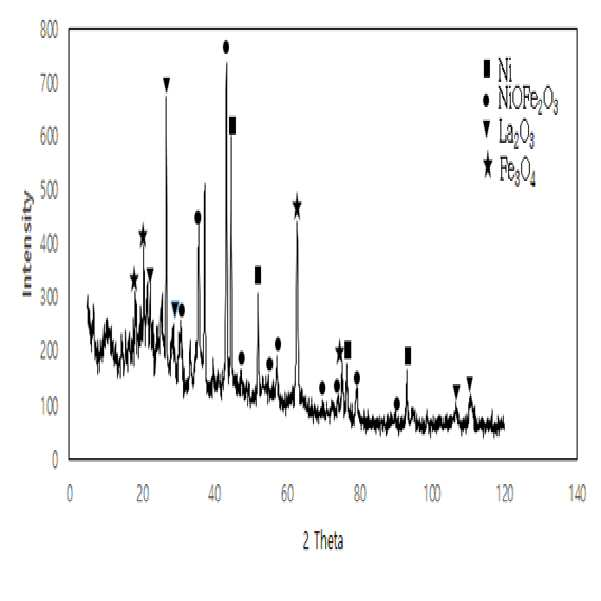
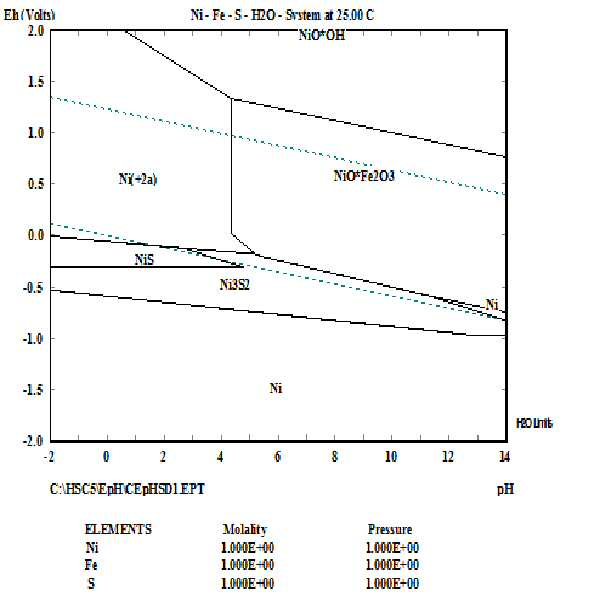
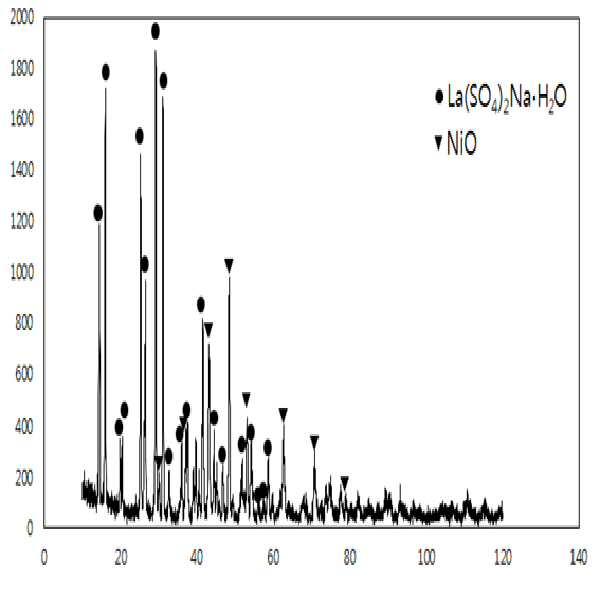
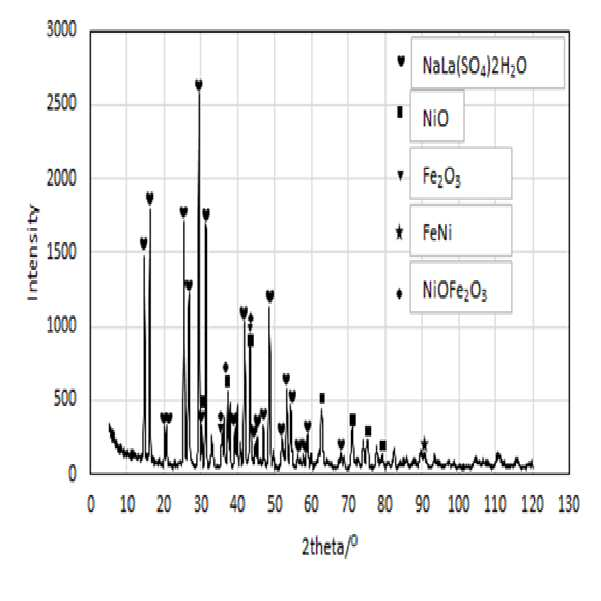