СПОСОБ ПОЛУЧЕНИЯ ОТЛИВОК ИЗ КОМПОЗИЦИОННОГО МАТЕРИАЛА НА МЕТАЛЛИЧЕСКОЙ ОСНОВЕ
Изобретение относится к области металлургии,
конкретно к способам производства литых материалов на металлической основе, армированных дисперсными частицами. Основные этапы технологического процесса получения литых композиционных
материалов включают ("Solidification, structures and properties" of cast metal ceramic particle composites PK.Asthana R., Das S-I nst. Metal Rev - 1986, 31 N 3 - 115-139) Для введения дисперсных частиц в
расплав используют следующие способы ("Cast aluminium - graphite particle composites - a potential engineering material" - Rotatgi PK. , Das S., Dan TK - I nst. Eng - 1987 - 67, N 2 - 277-283) Сложности, возникающие
при получении
литых композиционных материалов, связаны с отсутствием или низкой смачиваемостью упрочняющих частиц матричным расплавом, а также неоднородностью материала из-за большой разницы в
плотности матрицы и
наполнителя. Повышение прочности соединения армирующих частиц с матрицей достигается несколькими путями (Wetcability of Grafite to liqued aluminium and the effect
of alloying elements
on it "- choh Takao, Kemmel Rotand., Oki Takeo - Z Metall Kunde" - 1987 - 78, N4 - 286 - 290) Известен способ получения композиционных материалов, по которому в качестве
наполнителя предлагается
использовать природные полые микросферы диаметром 150 мкм, достаточно хорошо совместимые с различными металлическими материалами, а также порошки графита TiB2,
нитрида и оксида алюминия,
чешуйчатый и рубленый графит, а для обеспечения однородности материала добавлять в матричный расплав 0,05-5,0 мас.% металлического кальция. Основным
недостатком этого способа является
необходимость введения в расплав элемента (кальция), растворяющегося в жидкой основе, но практически не растворяющегося в твердой матрице и образующего с ней
хрупкую эвтектическую составляющую. Это
приводит к снижению механических свойств матрицы и всего композиционного материала. Кроме того, применение в качестве наполнителя полых микросфер указанных
размеров (150 мкм) не способствует повышению
абсолютных значений механических свойств и может приводить только к некоторому улучшению их относительных значений в пересчете на единицу массы. Наиболее близким по технической сущности
к заявляемому решению является способ получения композиционных материалов из расплавленных металлов - Mg, Al, Fe, Ni, Cr, Co, в которые вводят
нерастворимые частицы оксидов (Al2O3
, BeO, CaO, CeO2, TiO2, MgO, ThO2, VO2, ZrO3), карбидов, боридов, нитридов Nb, Ta, Hf,
Ti, Zr с размером 0,01-10 мкм. Частицы вводят в виде
порошка или тонких волокон. Для достижения равномерного распределения частиц в расплаве их вводят в потоке подогретого инертного газа (Ar, He) при
энергичном перемешивании основного металла. Объемная
доля частиц может изменяться от 0,5 до 20%. В расплавленный металл вводят также один из элементов, увеличивающих поверхностную активность на
границе частица - расплав. Введение поверхностно активных
металлов (Mg, Si, Ti, Zr, V, Nb) обеспечивает образование металлофильной оболочки на оксидах, что значительно увеличивает смачиваемость в
системе, и в течение 30 мин расплав не расслаивается. Этот способ имеет следующие недостатки: Целью изобретения
является повышение качества композиционного материала за счет
диспергирования частиц, увеличения равномерности распределения и прочности их соединения с матрицей, а также расширение номенклатуры
композиционных материалов за счет использования в качестве
армирующих веществ как керамических, так и металлических соединений. Цель достигается тем, что в известном способе получения
композиционного материала, включающем введение твердых
дисперсных частиц в жидкий матричный расплав, перемешивание и формирование отливки, дисперсные частицы нагревают в процессе введения в матричный
расплав в потоке ионизированного инертного газа до 0,
5-0,9 температуры их плавления, перемешивание осуществляют непрерывно при изменении объема жидкой фазы от 100 до 0%, а в качестве армирующего
материала используют дисперсные синтетические частицы,
термодинамически устойчивые по отношению к матричному расплаву. Сущность предполагаемого изобретения состоит в том, что для
диспергирования и повышения прочности соединения упрочняющих
частиц с матрицей поверхность добавок активируют путем нагрева до 0,5-0,9 температуры их плавления в потоке ионизированного инертного газа,
образованию сегрегаций и расслоений препятствует непрерывное
перемешивание при изменении объема жидкой фазы от 100 до 0% в процессе введения добавок, литья и затвердевания, а условие
термодинамической устойчивости добавок в матричном расплаве позволяет
использовать данный способ для получения широкой гаммы материалов типа металл - интерметаллид (металл) с гарантированными формой
и размерами дисперсных фаз независимо от скорости охлаждения отливки
при затвердевании. Поиск по источникам научно-технической информации и патентной документации по классам показал,
что не известных технические решения, в которых используются
отличительные признаки предложенного способа получения композиционных материалов. Следовательно, заявленное решение соответствует критерию
изобретения "cущественные отличия", так как представляет
собой новую совокупность признаков, обеспечивающую достижение положительного эффекта, заключающегося в улучшении качества композиционного
материала, повышению его прочности, твердости, структурной
однородности, упрощению технологического процесса его получения. Температурный интервал нагрева частиц определялся
экспериментально из условия необходимой и достаточной степени
активации межфазного взаимодействия, обеспечивающей прочное соединение с металлической основой за счет образования в процессе ионного
травления и дробления частиц в газовом потоке развитой
поверхности. При нагреве ниже 0,5 Тпл. эффективность поверхностной обработки значительно снижается, прочность частиц становится недостаточно
низкой для их дробления. Нагрев выше 0,9 температуры
плавления приводит к слипанию частиц и образованию их крупных конгломератов. Непрерывное перемешивание при изменении объема жидкой
фазы от 100 до 0% является необходимым условием для
обеспечения равномерного распределения армирующего материала в объеме матрицы и улучшения смачиваемости по границе частица - расплав. Отсутствие
перемешивания на любой из стадий существования
жидко-твердого состояния композиционного материала может привести к ослаблению поверхностного контакта матрицы с частицами, образованию расслоений,
сегрегаций и неоднородности по химическому и
структурному составу. Термодинамическая устойчивость частиц в матричном расплаве препятствует их химическому взаимодействию с основным
металлом и образованию новых соединений
неконтролируемых размеров и формы, обеспечивая тем самым, в отличие от традиционной технологии, получения дисперсно-упрочненных сплавов путем сплавления жидких
компонентов, последующей совместной
кристаллизации и термообработки, возможность получения композиционных материалов типа металл - интерметаллид (металл) с заданными значениями количества, размеров и
формы упрочняющих фаз. Пример конкретного осуществления способа. Для опробования предлагаемого способа в качестве основы для получения композиционных материалов
использовали чистые металлы алюминий
и железо, а также сплав на основе алюминия Д16. Армирующими материалами служили порошки карбида кремния размером 5-50 мкм, алюминида титана TiAl3 с
исходными размерами частиц 1-10 мкм, а
также порошок титана размером 10-100 мкм. Опыты по получению композиционных материалов проводились на полупромышленной установке, схема которой приведена на
чертеже. В тигель с матричным расплавом 1 с
помощью плазмотрона 2, снабженного дозатором 3 для обеспечения заданного расхода порошка, в потоке ионизированного газа вводили армирующие частицы,
нагретые до заданной температуры. Контроль
температуры частиц Тч проводили косвенным методом по изменению теплосодержания основного расплава до и после введения порошка, Тч
рассчитывали по формуле Перемешивание смеси в процессе ввода добавок и литья производилось с помощью магнитного индуктора 4. После введения заданного количества добавок стопор
5 убирали, и жидко-твердая смесь через
отверстие в днище тигля заполняла литейную форму. В качестве формы использовали стальную изложницу 6 диаметром 50 мм, перемешивание смеси в которой
осуществлялось с помощью ультразвукового генератора
7. Полученную отливку подвергали горячему прессованию. Оценку качества композиционного материала производили по следующим параметрам: Химическую неоднородность композиционного материала
оценивали по изменению содержания компонентов
армирующих частиц в различных сечениях отливки, перпендикулярных направлению литья, по коэффициенту неоднородности химической Кх:
Структурную неоднородность композиционного
материала оценивали по изменению средних размеров n частиц - упрочнителей с помощью коэффициента Кс : Прочность оценивали по временному сопротивлению при разрыве. Химический состав определяли по
квантометре ARL-72000, структурные характеристики - на
металлографическом световом микроскопе MeF-3A и структурном анализаторе Omnimet-2. Определение прочностных характеристик производили на
разрывной машине УТС-100. Результаты испытаний приведены в
таблице. Из полученных данных следует, что наилучшие характеристики имеют образцы композиционных материалов, полученные в
результате опытов 6, 9, 12, 36, 39, 42, 51, 54, 57, 66, 69, 72,
соответствующих заявляемому способу получения композиционных материалов на металлической основе. Использование: в области металлургии, а именно при производстве отливок из
материалов на металлической основе для повышения качества отливок и расширения их номенклатуры.
Сущность изобретения: дисперсные частицы нагревают в процессе введения в матричный расплав в потоке
ионизированного инертного газа до 0,5 - 0,9 температуры их плавления, перемешивание осуществляют
непрерывно, а в качестве армирующего материала используют дисперсные синтетические частицы,
термодинамически устойчивые по отношению к матричному расплаву. 3 з.п.ф-лы, 1 ил. 1. СПОСОБ ПОЛУЧЕНИЯ ОТЛИВОК
ИЗ КОМПОЗИЦИОННОГО МАТЕРИАЛА НА МЕТАЛЛИЧЕСКОЙ ОСНОВЕ, включающий введение твердых дисперсных частиц, нагретых в потоке инертного
газа, в расплав матрицы, перемешивание, заливку в литейную форму и
последующую кристаллизацию, отличающийся тем, что, с целью повышения качества отливок и расширения их номенклатуры, нагрев
дисперсных частиц ведут в потоке ионизированного инертного газа до 0,5 - 0,9
температуры их плавления, а перемешивание производят дополнительно на стадиях заливки и кристаллизации. 2. Способ по п.1, отличающийся тем, что в качестве дисперсных частиц
используют синтетические интерметаллидные соединения на основе металла матрицы. 3. Способ по
п.1, отличающийся тем, что в качестве металла матрицы используют алюминий, железо
или сплав на основе алюминия, а в качестве дисперсных частиц - карбид кремния, алюминид титана или порошок
титана. 4. Способ по п.1, отличающийся тем, что перемешивание на
стадиях введения дисперсных частиц и заливки расплава ведут бегущим магнитным полем, а на стадии
кристаллизации - ультразвуковыми колебаниями.
- получение
основного расплава;
- равномерное распределение твердых частиц в объеме жидкого металла;
- кристаллизацию композиционного материала.
- инжекционное распыление частиц в расплаве в струе инертного газа;
- механическое смешивание расплава и частиц;
- совместное прессование порошка матричного металла и
упрочняющих
частиц с последующим расплавлением прессовки и механическим перемешиванием расплава;
- распыление частиц в расплав при помощи ультразвука.
- нанесением металлофильных покрытий на поверхность упрочняющих частиц;
- введением в
расплав поверхностно-активных добавок;
- повышением температуры расплава.
- химический состав матричного расплава ограничен требованиями введения
поверхностно активных металлов, что в ряде случаев может приводить к
ухудшению технологических и механических свойств композиционного материала;
- отсутствие перемешивания в процессе
затвердевания способствует, особенно в случае его большой продолжительности,
образованию сегрегаций и расслоений и, как следствие, снижению качества композиционного материала;
- условие
нерастворимости упрочняющих частиц исключает возможность применения данного
способа для получения материалов, армированных дисперсными частицами элементов или их соединений с металлом матрицы,
являющихся традиционными упрочнителями при получении материалов совместной
кристаллизацией основы с легирующими добавками и последующей термомеханической обработкой.
Tч=
1 - где θ
- температура расплава после введения добавок,оС;
Тм - температура матрицы перед введением добавок,оС;
Кт - безразмерный коэффициент,
учитывающий тепловые эффекты при воздушном охлаждении поверхности расплава в процессе легирования и нагреве при обработке потоком ионизированного газа без
введения добавок, К = 0,05-0,06.
- химической и структурной однородности;
- величине армирующих частиц;
- прочности композиционного материала.
Kx= где Ск - содержание компонентов упрочняющих частиц в сечении отливки, мас.%;
n - число анализируемых сечений;
Cmax, Cmin - максимальное и минимальное содержание компонентов упрочняющих частиц в анализируемых сечениях, мас.%.
Kc= где di - средний размер i-й частицы, мкм;
dmax, dmin - максимальный и
минимальный размеры анализируемых частиц, мкм,
n
- число анализируемых частиц.
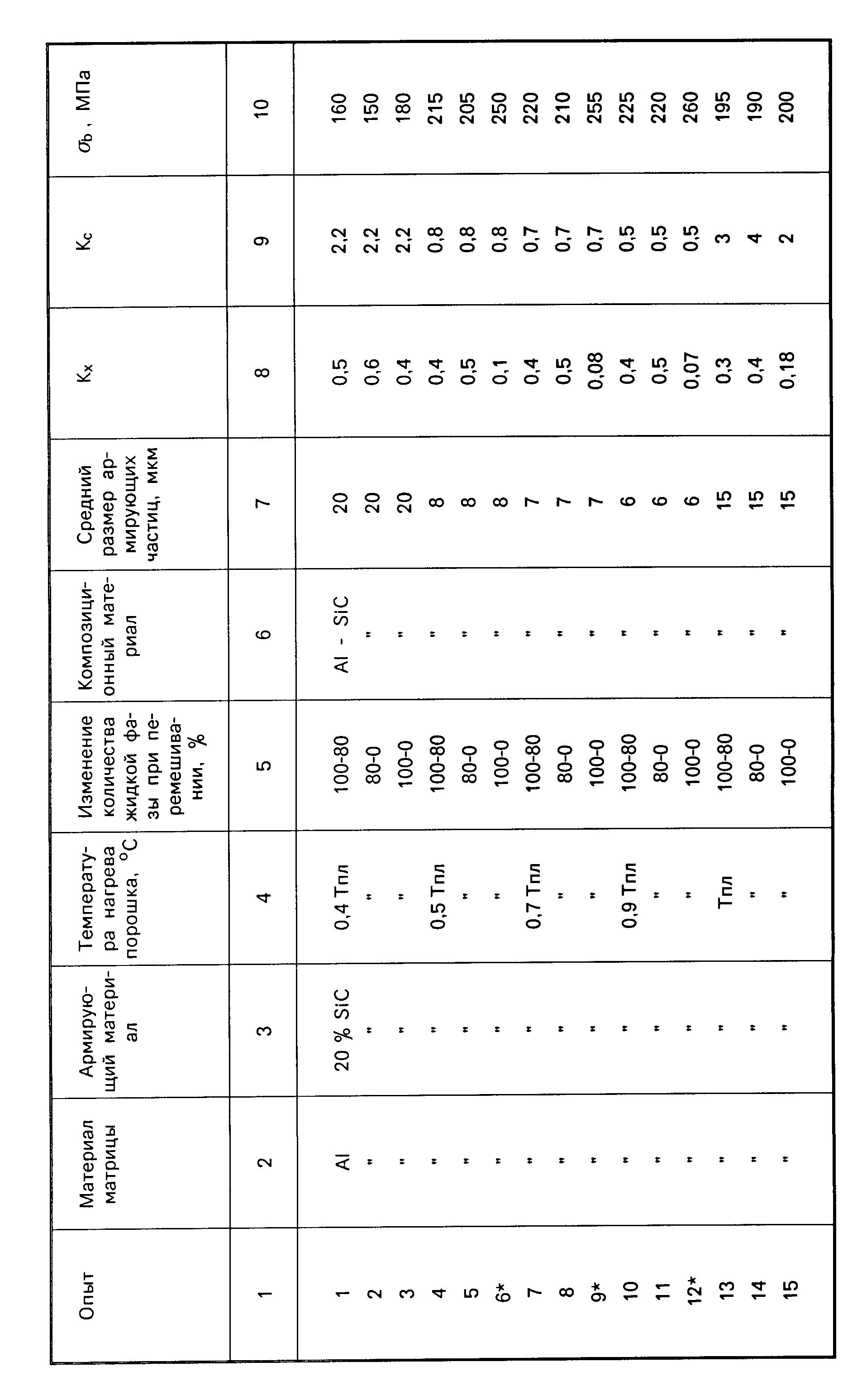
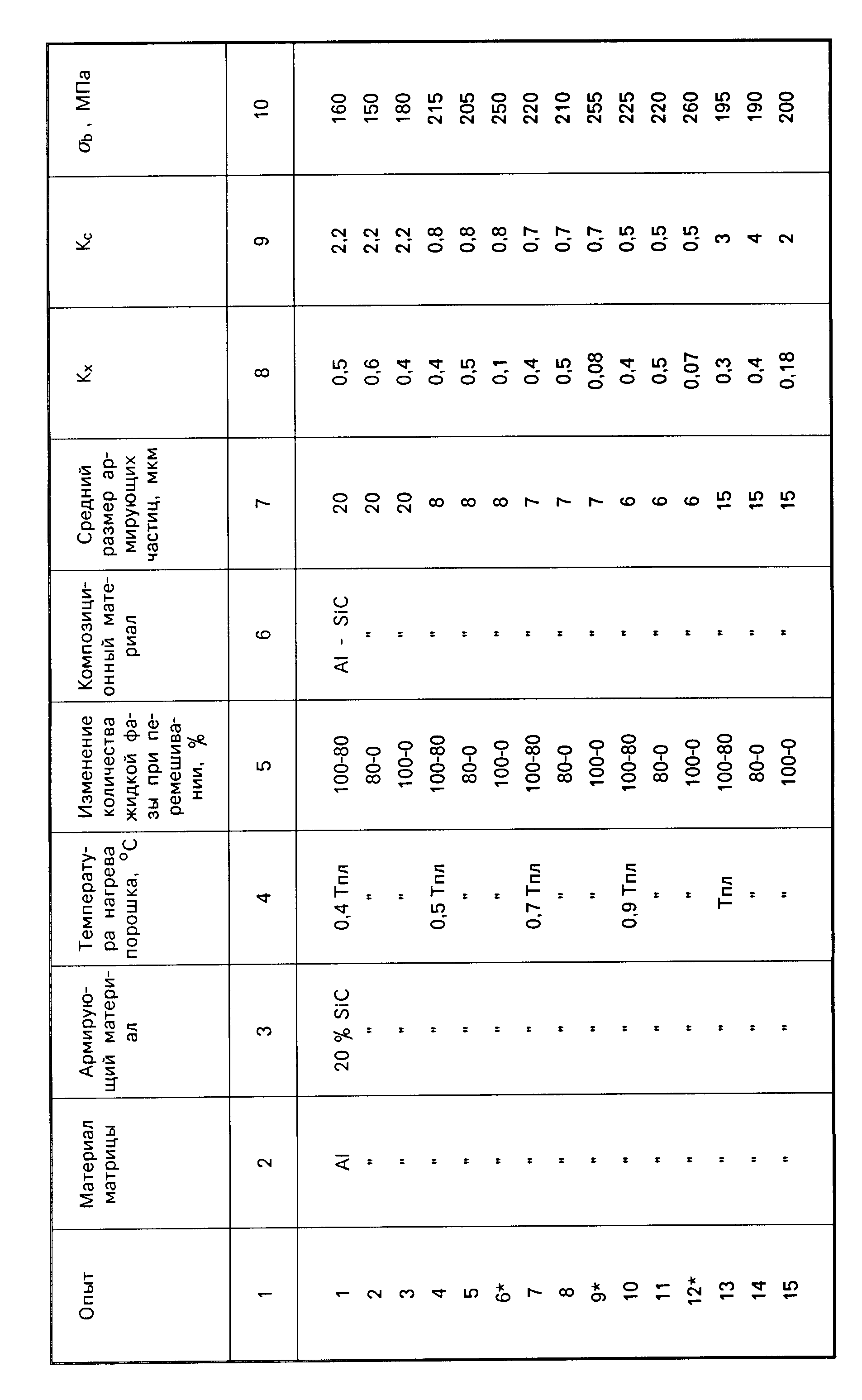
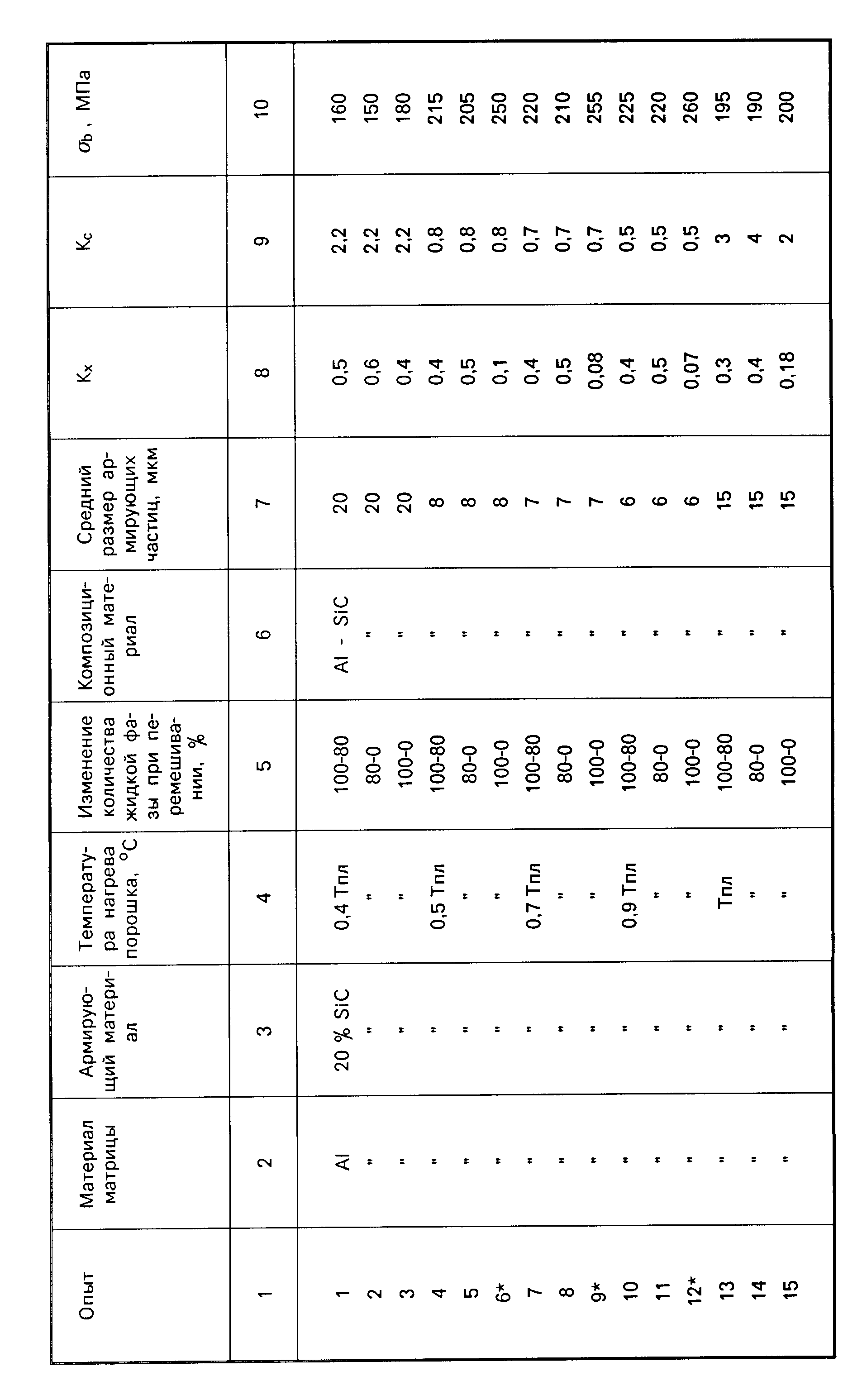
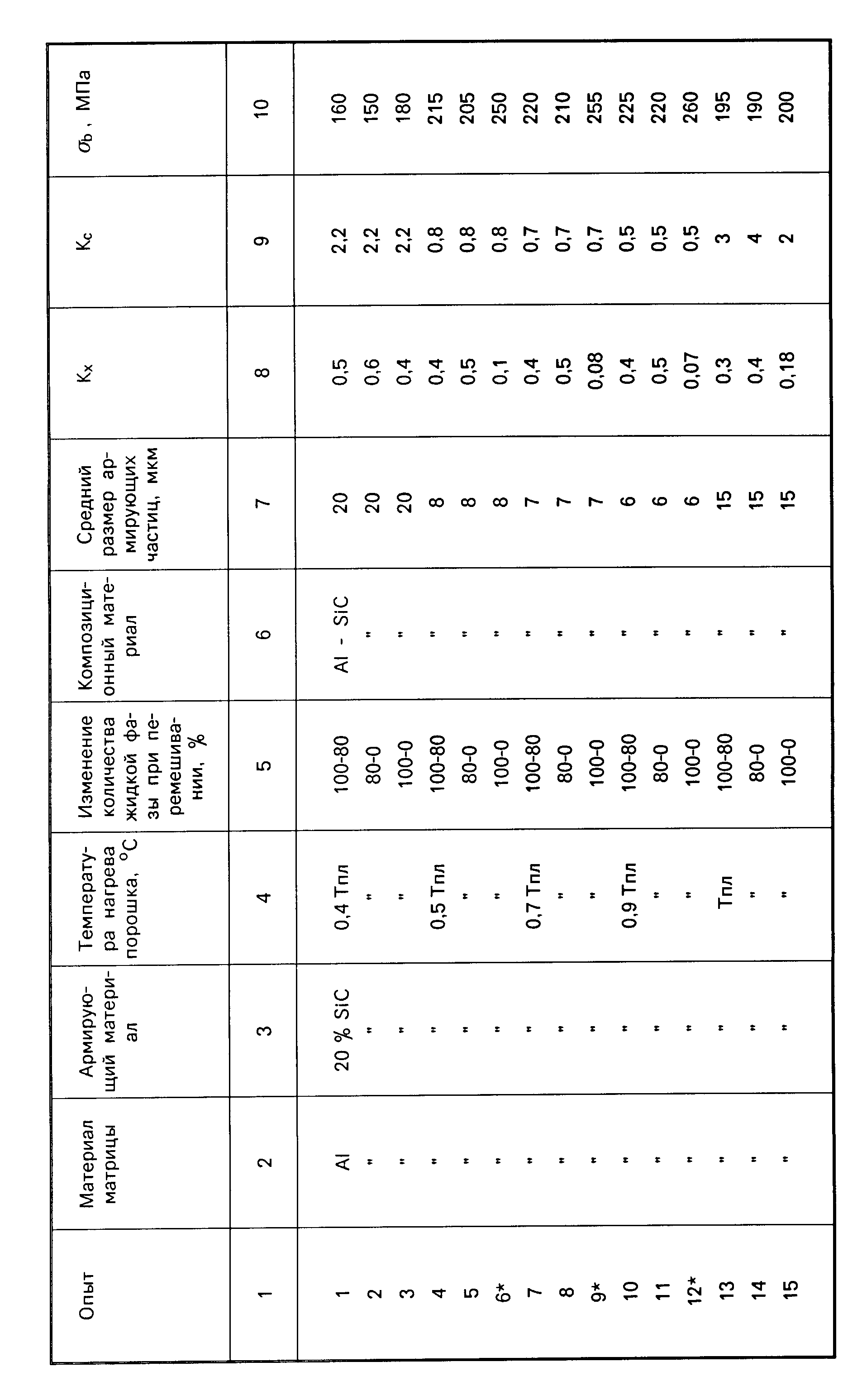
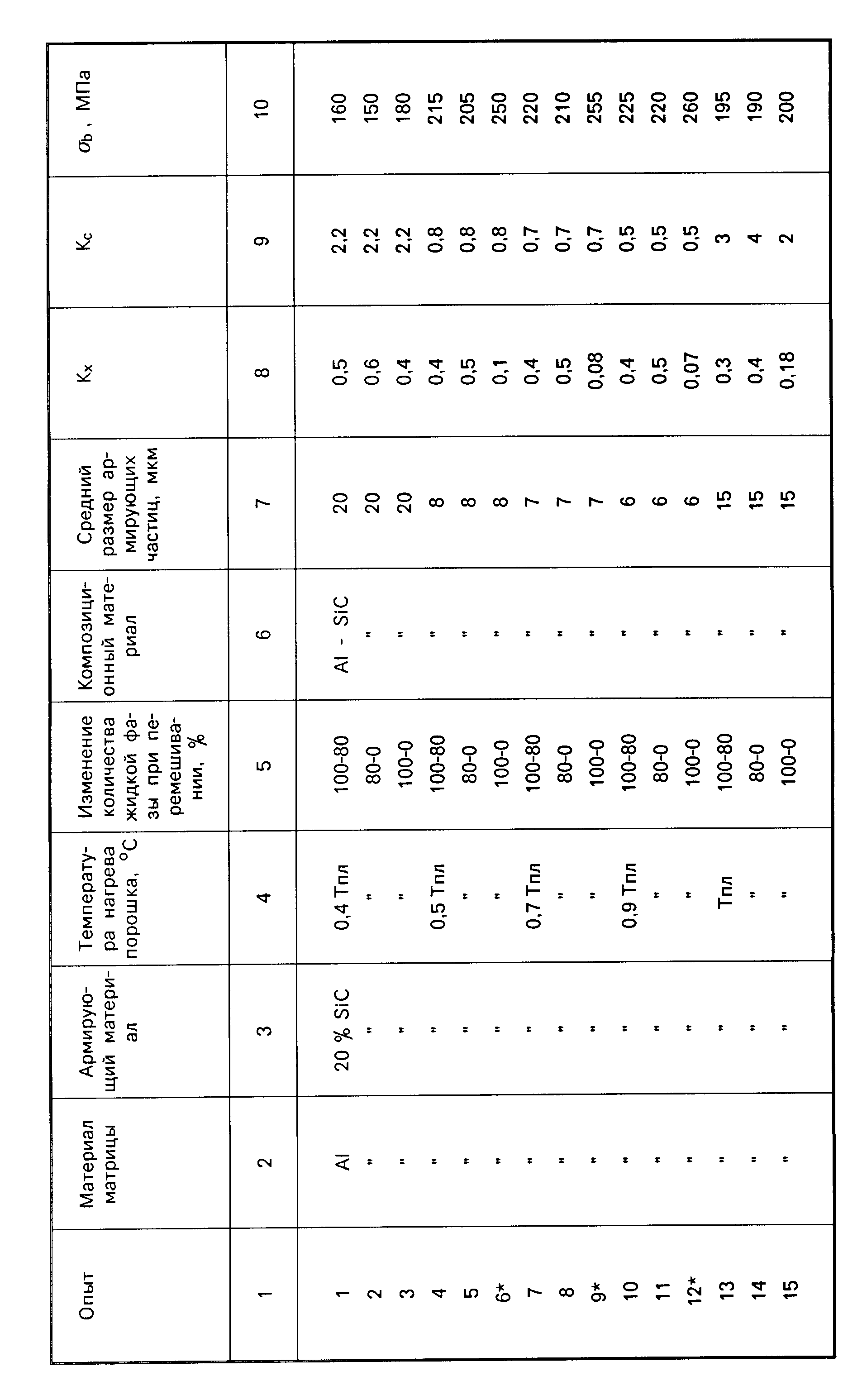