GAS TURBINE ENGINE CASE MOUNT WITH VIBRATION DAMPING
This disclosure relates generally to a gas turbine engine and, more particularly, to mounting components to a case of a gas turbine engine. Various systems and devices for mounting electronics as well as other devices to a case of a gas turbine engine are known in the art. While these systems and devices have various advantages, there is still room in the art for improvement. For example, there is a need in the art to provide vibration damping between a composite case structure and a metal mounting plate as well as accommodate misalignment between mounts on the composite case and mounting holes in the mounting plate. According to an aspect of the present disclosure, an assembly is provided for a gas turbine engine. This gas turbine engine assembly includes a mount, a component and a fastener assembly attaching the component to the mount. The fastener assembly includes a fastener, a bushing and a damper. The fastener extends axially along an axis through an aperture in the component and into the mount. The bushing extends axially along the axis through the aperture and axially engages the mount and the fastener. The damper is configured to damp vibration transmission between the mount and the component. The damper is arranged between the mount and the component and between the component and the bushing. According to another aspect of the present disclosure, another assembly is provided for a gas turbine engine. This gas turbine engine assembly includes an engine case, a mounting boss, a mounting tray, electronics and a fastener assembly. The engine case is configured from and/or otherwise includes fiber-reinforced composite material. The mounting boss is connected to the engine case. The mounting boss includes composite material and a threaded insert. The electronics are attached to the mounting tray. The fastener assembly attaches the mounting tray to the mounting boss. The fastener assembly includes a fastener, a flanged bushing, a first annular isolator and a second annular isolator. The fastener extends axially along an axis through an aperture in the mounting tray and is mated with the threaded insert. The flanged bushing extends axially along the axis through the aperture and axially engages the mounting boss and the fastener. The first annular isolator is configured axially between the mounting boss and the mounting tray. The second annular isolator is configured axially between the mounting tray and the flanged bushing. The mount may be configured from and/or otherwise include non-metal composite material. The mount may be configured as and/or otherwise include a mounting boss. An engine case may be included. The mount may be affixed to the engine case. The mount and the engine case may each be configured from and/or otherwise include composite material. The component may be configured as and/or otherwise include a metal mounting tray. The mount may include a threaded insert. The fastener may be threaded into the threaded insert. The fastener may be configured as and/or otherwise include a bolt. The bushing may be configured from and/or otherwise include metal. The bushing may include an annular flange and a tubular base that projects axially out from the annular flange and extends axially through the aperture. The annular flange may axially engage the fastener. The tubular base may axially engage the mount. The aperture may have an aperture diameter. The tubular base may have a base diameter that is less than the aperture diameter. The tubular base may have an axial base length. The damper may have an axial damper length. The axial damper length may be greater than the axial base length when the damper is in a relaxed state, and the axial damper length may be approximately equal to the axial base length when the damper is in a compressed state. The bushing may not contact the component. The damper may be configured from and/or otherwise include polymer. The damper may be configured as and/or otherwise include an annular isolator disposed axially between and axially engaging the mount and the component. The annular isolator may be affixed to the component. The damper may be configured as and/or otherwise include an annular isolator disposed axially between and axially engaging the component and the bushing. The annular isolator may be affixed to the bushing. The damper may include a second annular isolator disposed axially between and axially engaging the mount and the component. A second fastener assembly may be included for attaching the component to the mount. The second fastener assembly may include a second fastener, a second bushing and a second damper configured to further damp vibration transmission between the mount and the component. The foregoing features and the operation of the invention will become more apparent in light of the following description and the accompanying drawings. The engine sections 18-21 are arranged sequentially along the centerline 12 within an engine housing 22. This housing 22 includes an inner engine case 24 (e.g., a core case) and an outer engine case 26 (e.g., a fan case). The inner engine case 24 may house one or more of the engine sections 19-21; e.g., an engine core. The outer engine case 26 may house at least the fan section 18. Each of the engine sections 18, 19A, 19B, 21A and 21B includes a respective rotor 28-32. Each of these rotors 28-32 includes a plurality of rotor blades arranged circumferentially around and connected to one or more respective rotor disks. An annular array of the rotor blades, for example, may be fainted integral with or mechanically fastened, welded, brazed, adhered and/or otherwise attached to each respective rotor disk. The fan rotor 28 is connected to a gear train 34, for example, through a fan shaft 36. The gear train 34 and the LPC rotor 29 are connected to and driven by the LPT rotor 32 through a low speed shaft 37. The HPC rotor 30 is connected to and driven by the HPT rotor 31 through a high speed shaft 38. The shafts 36-38 are rotatably supported by a plurality of bearings 40. Each of these bearings 40 is connected to the engine housing 22 by at least one stationary structure such as, for example, an annular support strut. During operation, air enters the gas turbine engine 10 through the airflow inlet 14. This air is directed through the fan section 18 and into an annular core gas path 42 and an annular bypass gas path 44. The core gas path 42 extends sequentially through the engine sections 19-21. The air within the core gas path 42 may be referred to as “core air”. The air within the bypass gas path 44 may be referred to as “bypass air”. This air is referred to as “bypass air” since the bypass gas path 44 extends outside of and thereby bypasses the engine core. The core air is compressed by the compressor rotors 29 and 30 and directed into a combustion chamber of a combustor in the combustor section 20. Fuel is injected into the combustion chamber and mixed with the compressed core air to provide a fuel-air mixture. This fuel air mixture is ignited and combustion products thereof flow through and sequentially cause the turbine rotors 31 and 32 to rotate. The rotation of the turbine rotors 31 and 32 respectively drive rotation of the compressor rotors 30 and 29 and, thus, compression of the air received from a core airflow inlet. The rotation of the turbine rotor 32 also drives rotation of the fan rotor 28, which propels the bypass air through and out of the bypass gas path 44. The propulsion of the bypass air may account for a majority of thrust generated by the turbine engine 10, e.g., more than seventy-five percent (75%) of engine thrust. The turbine engine 10 of the present disclosure, however, is not limited to the foregoing exemplary thrust ratio. The component 48 of Referring to The boss base 62 is configured with one or more insert apertures. Each of the insert apertures receives a respective one of the first inserts 64; e.g., a tubular metal (e.g., steel) reinforcement insert. A bore of each of the first inserts 64 receives a respective one of the second inserts 66; e.g., a tubular metal (e.g., steel) threaded insert. Of course, in other embodiments, a single insert may be inserted into each insert aperture where that single insert replaces the respective first and second inserts 64 and 66. Each fastener assembly 52 includes a fastener 68, a flanged bushing 70 and a damper 72. The fastener 68 may be configured as a threaded bolt as shown in Referring to Referring to In the embodiment of Referring to Referring now to Each of the flanged bushings 70 is mated with a respective one of the apertures 98 in the component 48. In particular, the tubular base 76 is positioned to axially project through the respective aperture 98 and axially engage (e.g., contact) a respective one of the mounts 50 and, more particularly, a respective one or set of the inserts 66. Each of the second annular isolators 92 is positioned axially between and thereby axially engages (e.g., contacts) the component 48 and a respective one of the flanged bushings 70. The base diameter 82 (see Each of the fasteners 68 projects axially through a respective one of the flanged bushings 70, dampers 72 and apertures 98, and is mated with (e.g., threaded into) a respective one of the second inserts 66. When the fasteners 68 are first mated with the inserts 66, an axial gap may extend between the distal ends 88 (see With the configuration of In some embodiments, one or more non-electronic devices may also or alternatively be mounted onto the component 48; e.g., the mounting tray 58. The present disclosure therefore is not limited to the mounting of electronic equipment. In some embodiments, at least one additional element may be positioned between the isolator 90, 92 and an adjacent element. An example of such an additional element is an additional isolator and a metal washer. The turbine engine assembly 46 may be included in various turbine engines other than the one described above. The turbine engine assembly 46, for example, may be included in a geared turbine engine where a gear train connects one or more shafts to one or more rotors in a fan section, a compressor section and/or any other engine section. Alternatively, the turbine engine assembly 46 may be included in a turbine engine configured without a gear train. The turbine engine assembly 46 may be included in a geared or non-geared turbine engine configured with a single spool, with two spools (e.g., see While various embodiments of the present invention have been disclosed, it will be apparent to those of ordinary skill in the art that many more embodiments and implementations are possible within the scope of the invention. For example, the present invention as described herein includes several aspects and embodiments that include particular features. Although these features may be described individually, it is within the scope of the present invention that some or all of these features may be combined with any one of the aspects and remain within the scope of the invention. Accordingly, the present invention is not to be restricted except in light of the attached claims and their equivalents. An assembly is provided for a gas turbine engine. This assembly includes a mount, a component and a fastener assembly attaching the component to the mount. The fastener assembly includes a fastener, a bushing and a damper. The fastener extends axially along an axis through an aperture in the component and into the mount. The bushing extends axially along the axis through the aperture and axially engages the mount and the fastener. The damper is configured to damp vibration transmission between the mount and the component. The damper is arranged between the mount and the component and between the component and the bushing. 1. An assembly for a gas turbine engine, comprising:
a mount; a component; and a fastener assembly attaching the component to the mount, the fastener assembly comprising a fastener, a bushing and a damper; the fastener extending axially along an axis through an aperture in the component and into the mount; the bushing extending axially along the axis through the aperture and axially engaging the mount and the fastener; and the damper configured to damp vibration transmission between the mount and the component, and the damper arranged between the mount and the component and between the component and the bushing. 2. The assembly of 3. The assembly of 4. The assembly of 5. The assembly of 6. The assembly of the fastener is threaded into the threaded insert. 7. The assembly of 8. The assembly of 9. The assembly of the bushing includes an annular flange and a tubular base that projects axially out from the annular flange and extends axially through the aperture; the annular flange axially engages the fastener; and the tubular base axially engages the mount. 10. The assembly of the aperture has an aperture diameter; and the tubular base has a base diameter that is less than the aperture diameter. 11. The assembly of the tubular base has an axial base length; the damper has an axial damper length; and the axial damper length is greater than the axial base length when the damper is in a relaxed state, and the axial damper length is approximately equal to the axial base length when the damper is in a compressed state. 12. The assembly of 13. The assembly of 14. The assembly of 15. The assembly of 16. The assembly of 17. The assembly of 18. The assembly of 19. The assembly of 20. An assembly for a gas turbine engine, comprising:
an engine case comprising fiber-reinforced composite material; a mounting boss connected to the engine case, the mounting boss comprising composite material and a threaded insert; a mounting tray; electronics attached to the mounting tray; and a fastener assembly attaching the mounting tray to the mounting boss, the fastener assembly comprising a fastener, a flanged bushing, a first annular isolator and a second annular isolator; the fastener extending axially along an axis through an aperture in the mounting tray and mated with the threaded insert; the flanged bushing extending axially along the axis through the aperture and axially engaging the mounting boss and the fastener; the first annular isolator configured axially between the mounting boss and the mounting tray; and the second annular isolator configured axially between the mounting tray and the flanged bushing.BACKGROUND OF THE INVENTION
1. Technical Field
2. Background Information
SUMMARY OF THE DISCLOSURE
BRIEF DESCRIPTION OF THE DRAWINGS
DETAILED DESCRIPTION OF THE DISCLOSURE
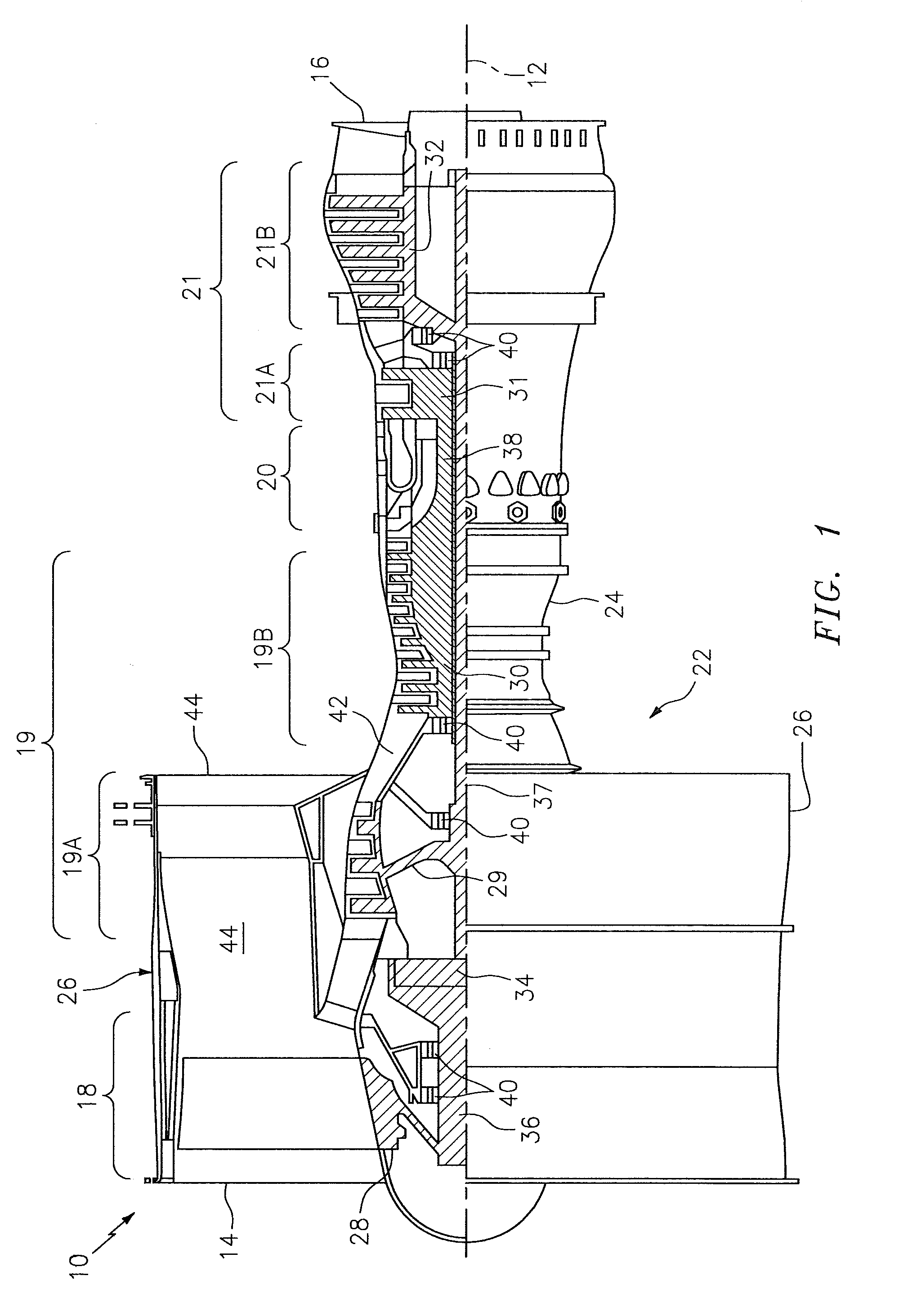
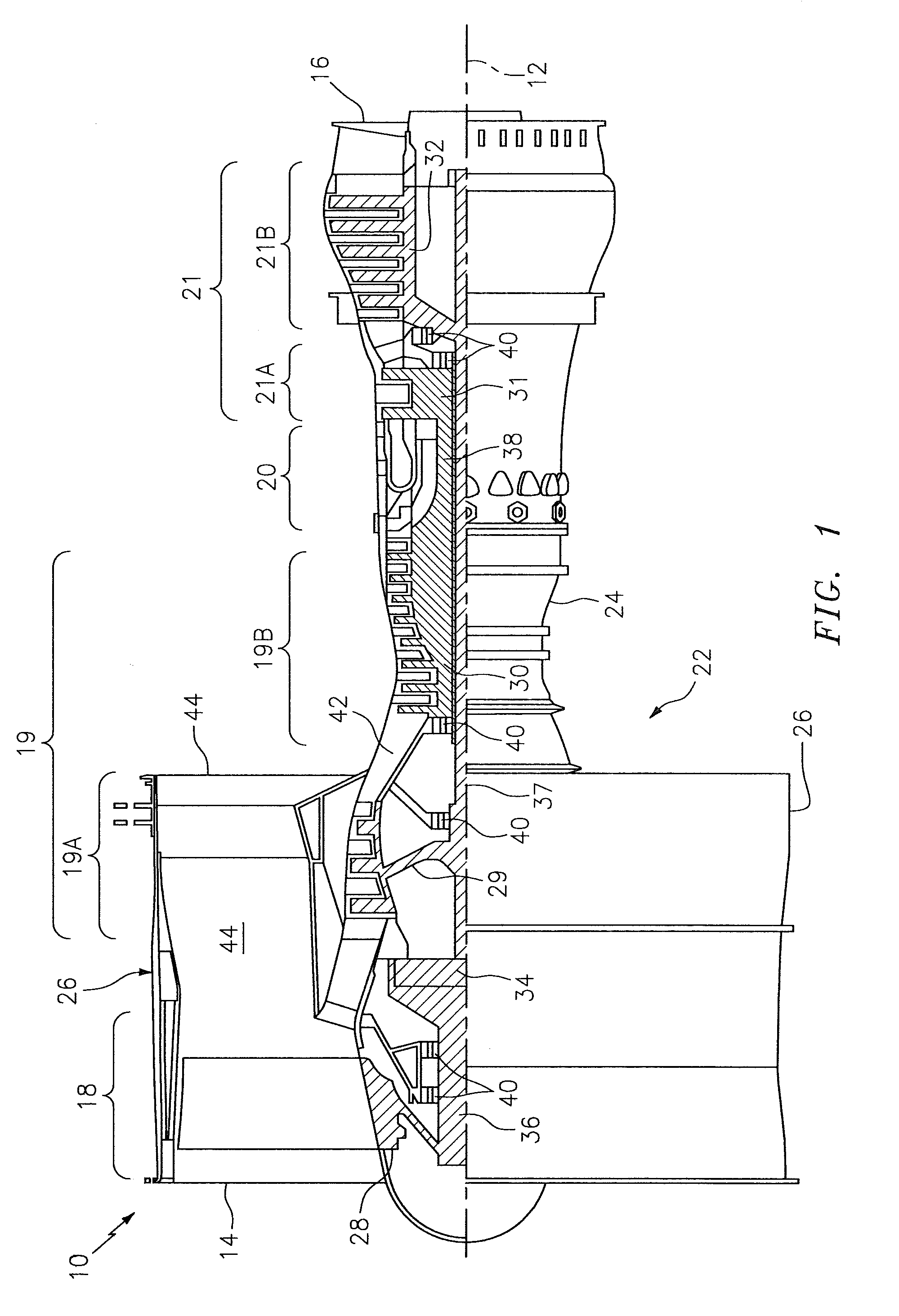
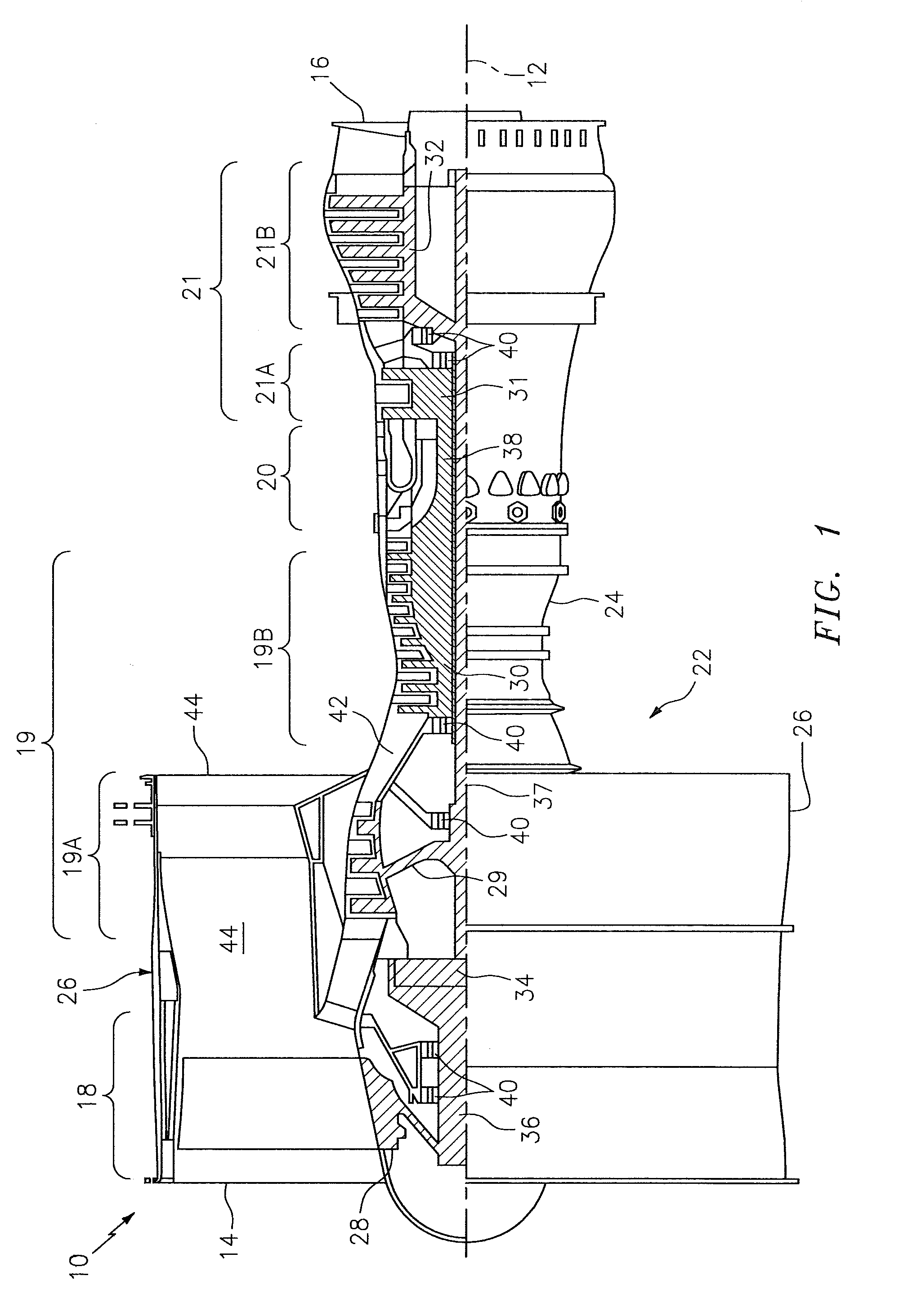
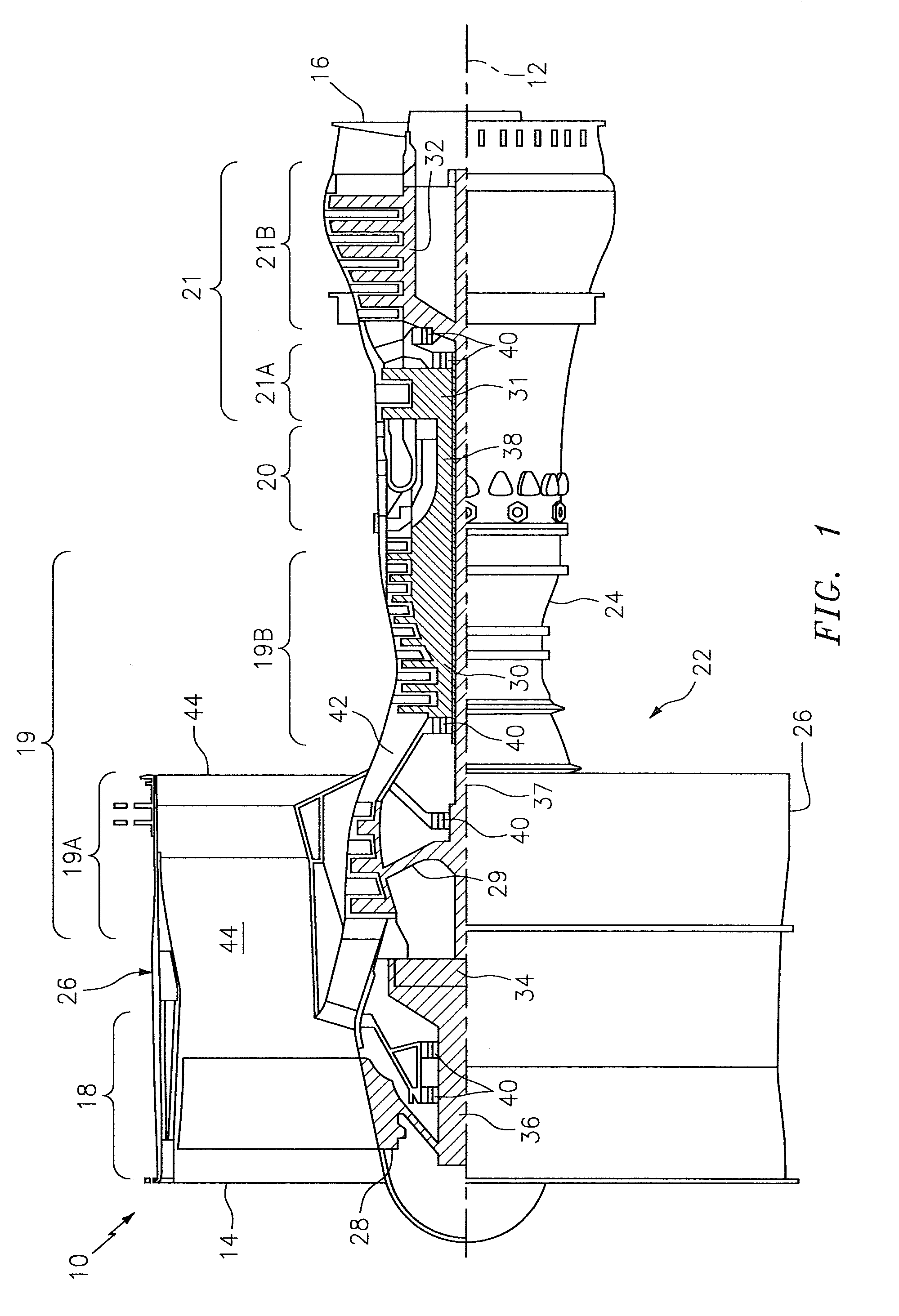
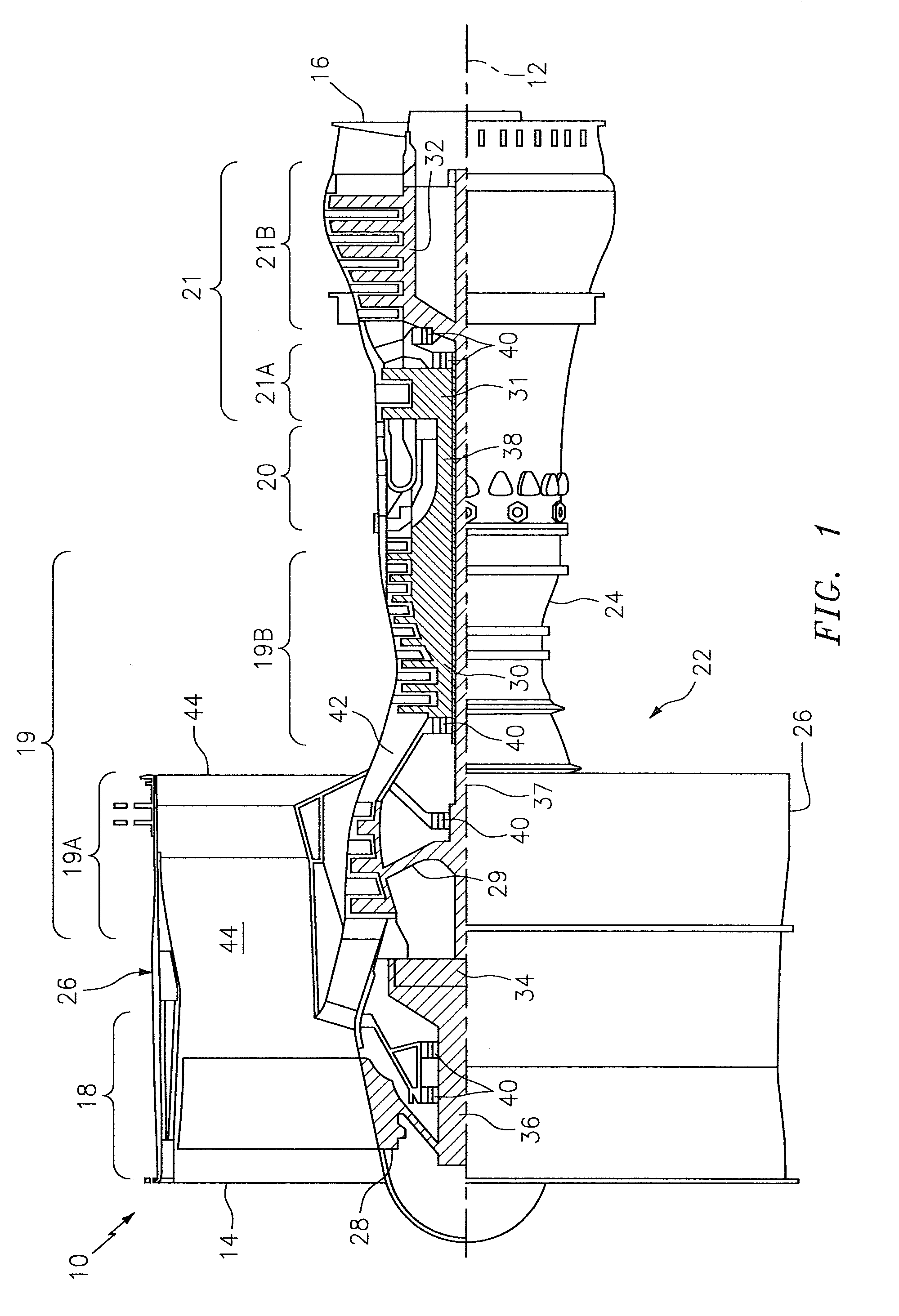
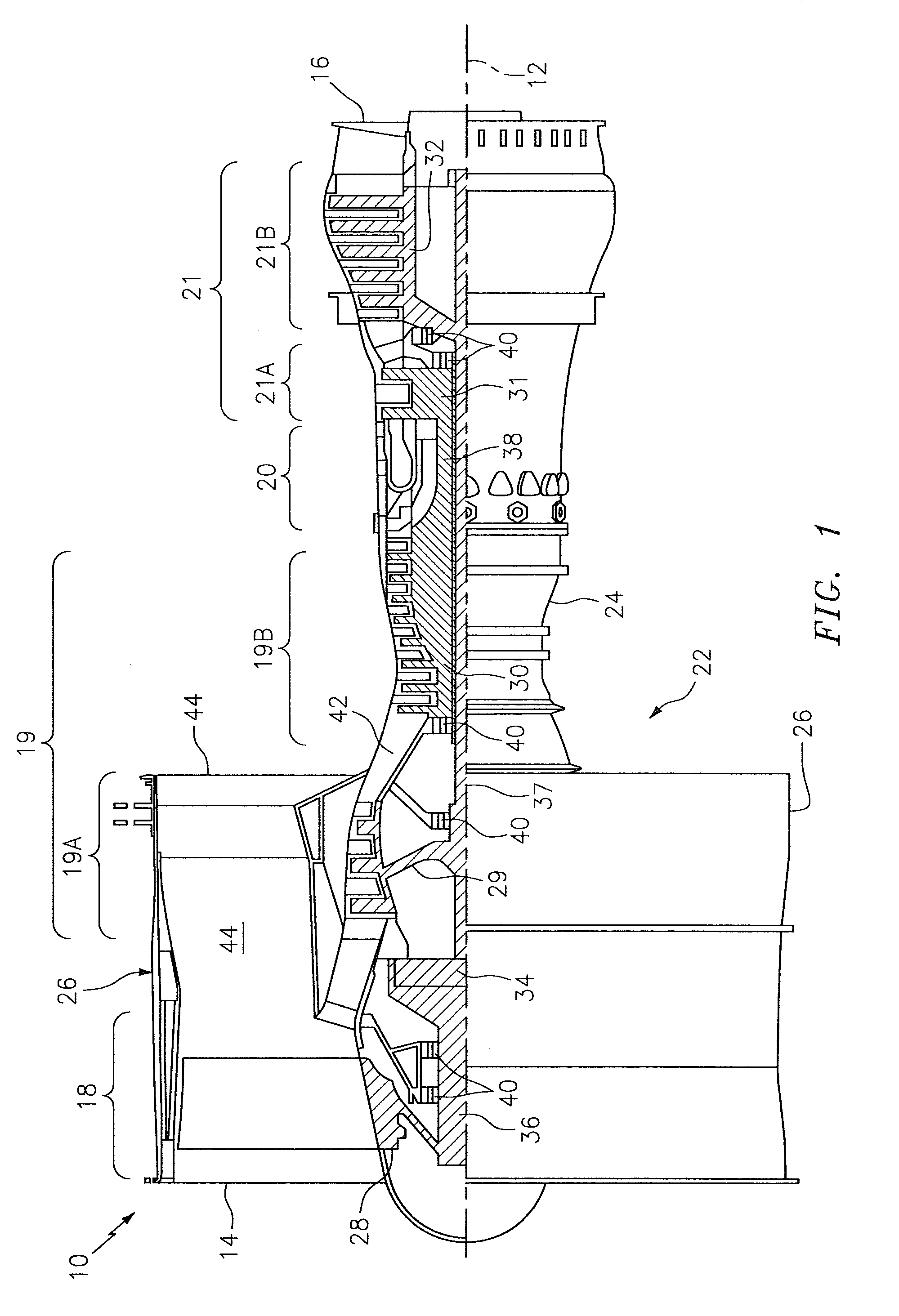
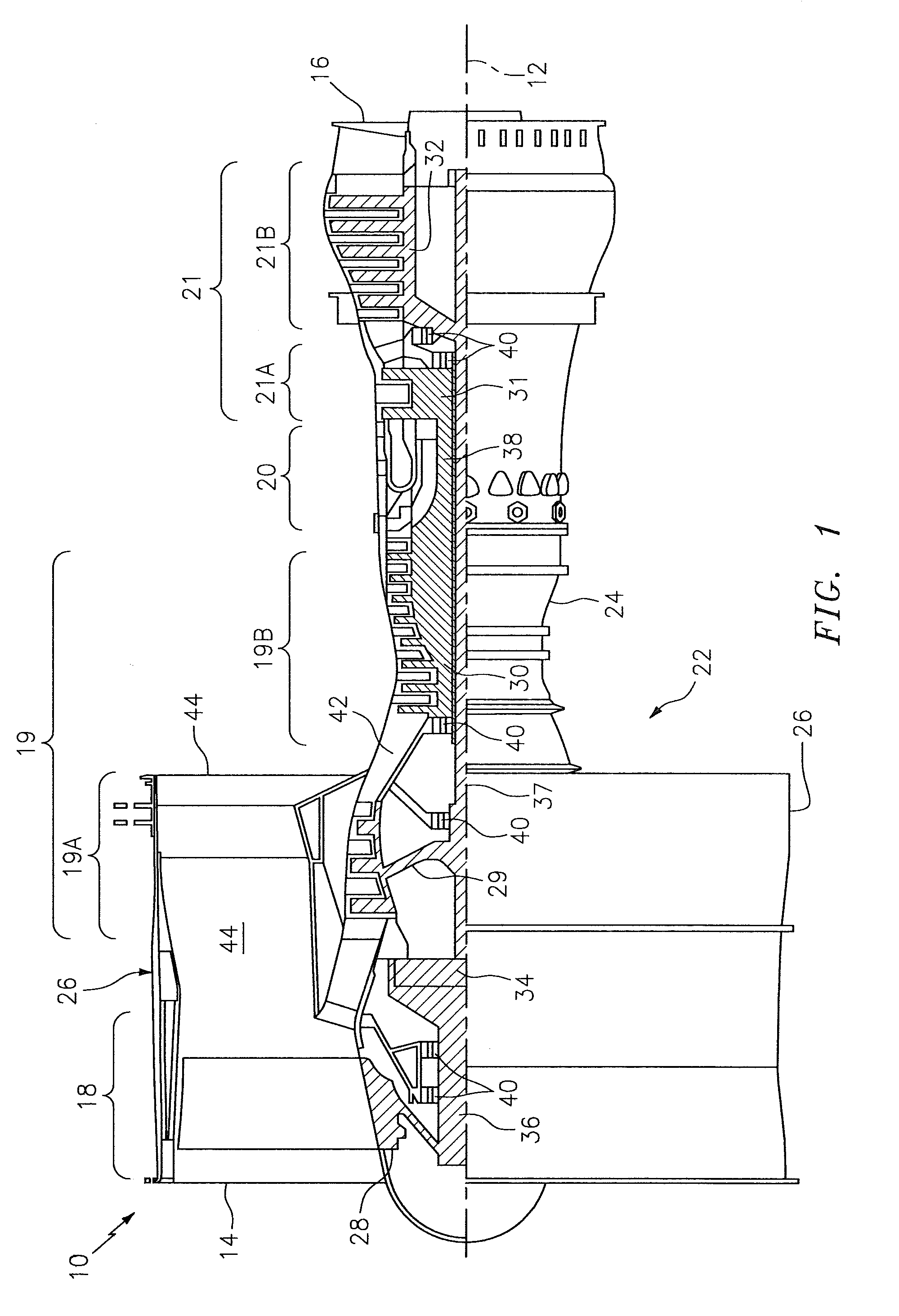