WASHING MACHINE
This application claims the priority benefit of Korean Application No. 10-2019-0075432, filed on Jun. 25, 2019, Korean Application No. 10-2019-0075431, filed on Jun. 25, 2019, and Korean Application No. 10-2018-0073911, filed on Jun. 27, 2018. The disclosures of the prior applications are incorporated by reference in their entirety. The present invention relates to a washing machine and particularly to a washing machine in which a nozzle for spraying circulating water into a drum is disposed at a gasket. Korean Patent Application Publication No. 10-2018-0131894 (hereinafter, referred to as a “related art”) discloses a washing machine having nozzles for spraying circulation water, pumped by a pump, into a drum. In the washing machine, a plurality of nozzles are provided along an inner circumferential surface of a gasket disposed between a casing forming an exterior appearance of the washing machine and a tub containing water, and a plurality of port receiving pipes communicates with the plurality of nozzles, respectively. There is a guide pipe that guides water (circulating water) pumped by the pump. In the guide pipe, a plurality of outlet port protruding from an annular flow path is inserted into the plurality of port receiving pipes. Each of the port receiving pipes protrude from an outer circumferential surface of a gasket approximately toward an outer side of a radial direction, and, in response, each of the outlet ports protrude from the annular flow path to an inner side of the radial direction. As such, in order to fabricate the gasket in a shape in which the port receiving pipes extend radially, a mold needs to move in a direction in which each of the port receiving pipes extends, and thus, a complicated structure is required for the mold. In addition, since the outlet ports are inserted into the port receiving pipes in different directions, it is not possible to assemble two or more nozzle water supply ports to two or more port receiving pipes, and thus, a complicated fabricating process is required. A first object of the present invention is to provide a washing machine which includes a plurality of nozzles provided on a gasket to spray circulating water into a drum, and which has a structure that allows the gasket to be easily molded by an injection technique. A second object of the present invention is to provide a washing machine having two or more nozzles on the left and right sides of the gasket are provided, wherein water supply ports for supplying circulating water to the nozzles are formed integrally with the gasket. A third object of the present invention is to provide a washing machine having the port receiving pipes disposed parallel to each other. A fourth object of the present invention is to provide a washing machine that allows distribution pipes, which supplies circulating water to the nozzles, to be easily assembled to the gasket. Objects of the present invention should not be limited to the aforementioned objects and other unmentioned objects will be clearly understood by those skilled in the art from the following description. In the washing machine of the present invention, a wash water is discharged from a tub accommodating a rotating drum, pumped by a pump, and supplied through a plurality of outlet ports to a plurality of nozzles disposed in a gasket. The gasket includes a gasket body forming a passage connecting an entry hole formed in a casing and an entrance hole of the tub, and a plurality of nozzles is provided on an inner circumferential surface of the gasket. In addition, the gasket further includes a plurality of a plurality of port receiving pipes communicating with the plurality of nozzles, respectively. The plurality of outlet ports protrude from an outer circumferential surface of the gasket body and inserted into the plurality of port receiving pipes, respectively. When the gasket body is bilaterally divided into a first area and a second area, the plurality of port receiving pipes includes a first port receiving pipe and a second port receiving pipe that are disposed in the first area in a top-to-bottom direction and parallel to each other. The gasket may include a third port receiving pipe and a fourth port receiving pipe that are disposed in the second area in the top-to-bottom direction and parallel to each other. The first and second port receiving pipes horizontally may extend in a first direction. The first port receiving pipe may be disposed higher than a middle height of the gasket body, and the second port receiving pipe may be disposed lower than a middle height of the gasket body. The third and fourth port receiving pipes horizontally may extend in a direction opposite to the first direction. The third port receiving pipe may be disposed at a height equal to a height of the first port receiving pipe, and the fourth port receiving pipe may be disposed at a height equal to a height of the second port receiving pipe. The gasket may include a casing coupling part coupled to a circumference of the entry hole, a tub coupling part coupled to a circumference of the entrance hole of the tub, and a basket body extending from the casing coupling part to the tub coupling part. The first to fourth port receiving pipes may protrude from an outer circumferential surface of the gasket body. The gasket body may include a rim part extending from the casing coupling part to the tub coupling part, an inner circumferential part extending from the rim part to the casing coupling part, and an outer circumferential part extending from the inner circumferential part to the tub coupling part. The first to fourth port receiving pipes may protrude from an outer circumferential surface of the outer circumferential part. A length of the second port receiving pipe may be smaller than a length of the first port receiving pipe. The first port receiving pipe may be disposed higher at a first distance than a middle height point of the gasket body, and the second port receiving pipe may be disposed lower at a second distance, smaller than the first distance, than the middle height point of the gasket body. A length of the fourth port receiving pipe may be smaller than a length of the third port receiving pipe. The third port receiving pipe may be disposed higher at a first distance than a middle height point of the gasket body, and the fourth port receiving pipe may be disposed lower at a second distance, smaller than the first distance, than the middle height point of the gasket body. The first and second port receiving pipes and the third and fourth port receiving pipes may be disposed symmetrically. The washing machine may further include: a circulation pipe for guiding wash water discharged from the pump; and a distribution pipe fixed to the gasket to supply the wash water, guided along the circulation pipe, to the plurality of nozzles. The distribution pipe may include an inlet port connected to the circulation pipe, and a first conduit part and a second conduit part that branch wash water supplied through the inlet port. The plurality of outlet ports may include: a first outlet port and a second outlet port that are disposed in the first conduit part and inserted into the first and second port receiving pipes, respectively; and a third outlet port and a fourth outlet port that are disposed in the first conduit part and inserted into the third and fourth port receiving pipes, respectively The washing machine may further include: a first circulation pipe and a second circulation pipe that guide wash water discharged from the pump; a first distribution pipe fixed to the first area and guides wash water supplied through the first circulation pipe; and a second distribution pipe fixed to the second area and guides wash water supplied through the second circulation pipe. The plurality of outlet ports may include: a first outlet port and a second outlet port that are disposed in the first distribution pipe and inserted into the first and second port receiving pipes, respectively; and a third outlet port and a fourth outlet port that are disposed in the second distribution pipe and inserted into the third and fourth port receiving pipes, respectively. The washing machine of the present invention may have one or more effects, as below. First, since two or more port receiving pipes integrally formed with the gasket are disposed to be parallel to each other, it is possible to perform an opening or separating operation even if the two or more nozzles are injected using a movable mold. Second, the two or more port receiving pipes are, when seen from the front, parallelly formed in one of a first area and a second area into which the gasket is divided, and thus, if the distribution pipe is installed to the gasket, the outlet ports provided in the distribution pipe may be moved in the substantially identical direction, and therefore, the outlet ports can be inserted into the port receiving pipes at the same time and the assembling process may be performed more conveniently. In particular, in a structure in which the distribution pipe includes a first conduit part and a second conduit part that are branched from a circulating water connection port, in which the two or more outlet ports are formed in one of the first conduit part and the second conduit part, in which the two or more outlet ports extend in a radial direction and the two or more port receiving pipes extend in the radial direction, it is difficult to insert the outlet ports into the port receiving pipes at the same time because the directions for the outlet orts to be inserted are different. However, the present invention solves this problem as the port receiving pipes (or the outlet ports) are disposed to be parallel to each other. A washing machine according to another aspect of the present invention includes a first nozzle, a second nozzle, a third nozzle, and a fourth nozzle provided on an inner circumferential surface of the gasket body, wherein, when the gasket body is bilaterally divided into a first area and a second area, the first and second nozzles are disposed in the first area sequentially in a top-to-bottom direction and the third and fourth nozzles are disposed in the second area sequentially in the top-to-bottom direction. The first and third nozzles are disposed higher than half a height of the gasket body to thereby spray water downward, and the second and fourth nozzles are disposed lower than half the height of the gasket body to thereby spray water upward. The first and second nozzle may spray water toward the second area. The third and fourth nozzles may spray water toward the first area. Water streams sprayed through the first and second nozzles and water streams sprayed through the third and fourth nozzles may be bilaterally symmetrical. A first spray width angle of a water stream sprayed through the first nozzle may be smaller than a spray width angle of a water stream sprayed through the second nozzle. A difference between the second spray width angle and the first spray width angle may be between 4° and 6°. The first spray width angle may be between 38° and 42°. The spray direction of the first nozzle may form a deviation angle upwardly relative to a line that connects the first nozzle and a center of the gasket. The deviation angle may be between 5° and 9°. The first nozzle may be disposed between a position corresponding to an angle from a lowest point in the gasket body to the second nozzle and a highest point in the gasket body, and disposed higher than a point that equally divides the angle from the lowest point in the gasket body to the second nozzle. A first angle between the first nozzle and the second nozzle may be greater than a second angle between a highest point in the gasket body and the first nozzle. The first angle may be between 63° and 67°. The second nozzle may be disposed at a point corresponding to one third of the height of the gasket body. The first nozzle may be disposed at a point higher than two thirds of the height of the gasket body. The embodiments will be described in detail with reference to the following drawings in which like reference numerals refer to like elements wherein: Advantages and features of the present disclosure and methods to achieve them will become apparent from the descriptions of exemplary embodiments herein below with reference to the accompanying drawings. However, the present disclosure is not limited to exemplary embodiments disclosed herein but may be implemented in various different ways. The exemplary embodiments are provided for making the disclosure of the present disclosure thorough and for fully conveying the scope of the present disclosure to those skilled in the art. It is to be noted that the scope of the present disclosure is defined only by the claims. Like reference numerals denote like elements throughout the descriptions. Hereinafter, the present invention will be described in detail with reference to the accompanying drawings. Referring to A tub containing water may be disposed inside the casing 10. An entrance hole (or a tub entrance hole 31 A door 20 for opening and closing the entry hole 12 The gasket 60 prevents leakage of water contained in the tub 31. The gasket 60 may extend from an annular front part to an annular rear part to thereby form an annular passage that connects the entry hole 12 The gasket 60 may be formed of a flexible or elastic substance. The gasket 60 may be formed of natural rubber or synthetic resin. The gasket 60 may be formed of a substance such as Ethylene Propylene Diene Monomer (EPDM), Thermo Plastic Elastomer (TPE), or the like. Hereinafter, a portion defining the inside of the annular shape of the gasket 60 is referred to as an inner circumferential part (or an inner circumferential surface) of the gasket 60, and a portion opposite thereto is referred to as an outer circumferential part (or an outer circumferential surface) of the gasket 60. A drum 32 receiving laundry may be rotatably provided in the tub 31. In order to allow water contained in the tub to flow into the drum 32, a plurality of through holes 32 The drum 32 is disposed in such a way that an entrance hole to receive laundry is disposed at a front surface of the drum 32, and the drum 32 is rotated about a rotation center line C that is approximately horizontal. In this case, “horizontal” does not refer to the mathematical definition thereof. That is, even in the case where the rotation center line C is inclined at a predetermined angle relative to a horizontal state, the axis is more like in the horizontal state than in a vertical state, and thus, it is considered that the rotation center line is substantially horizontal. A plurality of lifter 34 may be provided on an inner surface of the drum 32. The plurality of liters 34 may be disposed at a predetermined angle relative to the center of the drum 32. When the drum 32 is rotated, laundry repeatedly goes through an operation of being lifted by the lifter 34 and falling. A driving unit 38 for rotating the drum 32 may be further provided. A driving shaft 38 Preferably, the driving unit 38 includes a direct drive wash motor, and the wash motor may include a stator fixed to the rear of the tub 31, and a rotor rotating by a magnetic force acting in relation with the stator. The driving shaft 38 The tub 31 may be supported by a damper 16 installed at the base 15. Vibration of the tub 31 caused by rotation of the drum 32 is attenuated by the damper 16. In some embodiments, although not illustrated, a hanger (e.g., a spring) for hanging the tub 31 to the casing 10 may be further provided. There may be provided at least one water supply horse (not shown) for guiding water introduced from an external water source such as a water tap or the like to the tub 31, and a water supply unit 33 for controlling the water supplied through the at least one water supply horse to flow to at least one water supply pipe 34 A dispenser 35 for supplying additives such as detergent for washing, fabric softener, and the like into the tub 31 or the drum 32 may be provided. The additives are contained in the dispenser 35 separately by types thereof. The dispenser 35 may include a detergent container (not shown) for containing detergent for washing, and a fabric softer container (not shown) for containing a fabric softener. At least one water supply pipe 34 The at least one water supply pipe 34 The gasket 60 may include a direct nozzle 42 for spraying water into the drum 32, and a direct water supply tube 39 for guiding water supplied from the water supply unit 33 to the direct nozzle 42. The direct nozzle 42 may be a whirl nozzle or a spray nozzle, but aspects of the present invention are not necessarily limited thereto. When viewed from the front, the direct nozzle 42 may be disposed vertically above the rotation center line C. Water discharged from the dispenser 35 may be supplied to the tub 31 through a water supply bellows 37. A water supply hole (not shown) connected to the water supply bellows 37 may be formed on a side surface of the tub 31. A drain hole for draining water may be formed in the tub 31, and a drain bellows 17 may be connected to the drain hole. A pump 901 for pumping water discharged from the tub 31 through the drain bellows 17 may be provided. A drain valve 96 for regulating the drain bellows 17 may be further provided. The pump 901 may selectively perform a draining function of pumping water drained through the drain bellows 17 to a drain pipe 19, and a circulation function of pumping water to a circulation tube 18. Hereinafter, circulating water pumped by the pump 90 to be guided along the circulation tube 18 may be referred to as circulating water. Referring to An inlet port 911, a circulation port 912, and a drain port 913 may be formed in the pump housing 91. A first chamber 914 for housing the first impeller 915, and a second chamber 916 for housing the second impeller 917 may be formed in the pump housing 91. The first impeller 915 is rotated by the first pump motor 92, and the second impeller 917 is rotated by the second pump motor 93. The first chamber 914 and the circulation port 912 forms a volute-shaped flow path that is rolled in a direction of rotation of the first impeller 915, and the second chamber 916 and the drain port 913 forms a volute-shaped flow path that is rolled in a direction of rotation of the second impeller 917. Herein, a direction of rotation of each of the impellers 915 and 917 are preset to be controllable. The inlet port 911 is connected to the drain bellows 17, and the first chamber 914 and the second chamber 916 communicate with the inlet port 911. Water discharged from the tub 31 through the drain bellows 17 is supplied to the first chamber 914 and the second chamber 916 through the inlet port 911. The first chamber 914 communicates with the circulation port 912, and the second chamber 916 communicates with the drain port 913. Accordingly, if the first impeller 915 is rotated as the first pump motor 92 operates, water in the first chamber 914 is discharged through the circulation port 912. In addition, if the second pump motor 93 operates, the second impeller 917 is rotated and thereby water in the second camber 916 is discharged through the drain port 913. The circulation port 912 is connected to the circulation pipe 18, and the drain port 913 is connected to the drain pipe 19. An amount of water to be discharged from (or discharge pressure) of the pump 901 is variable. To this end, the pump motors 92 and 93 are speed-variable motors of which speeds or rotation is controllable. Each of the pump motors 92 and 93 is preferably, but not limited to, a Brushless Direct current Motor (BLDC). A driver for controlling speeds of the pump motors 92 and 93 may be further provided, and the driver may be an inverter driver. The inverter driver inverts AC power into DC power, and inputs the DC power to the motors at a target frequency. A controller (not shown) for controlling the pump motors 92 and 93 may be further provided. The controller may include a Proportional-Integral (PI) controller, a Proportional-Integral-Derivative (PID) controller), and the like. The controller may receive an output value (e.g., an output current) of a pump motor, and control an output value of the driver based on the received output value of the pump motor so that the number of times of rotation of the pump motor follows a preset target number of times of rotation. The controller is capable of controlling not just speeds of rotation of the pump motors 92 and 93, but also directions of rotation thereof. In particular, a motor applied in a conventional pump is not capable of controlling a direction of rotation in a driving operation, and thus, it is difficult to control rotation of each impeller in a predetermined direction, as shown in Meanwhile, the controller is capable of controlling not just the pump motors 92 and 93, but also overall operations of the washing machine. It is understood that each component described in the following is controlled by the controller. Referring to The circumference of the entry hole 12 The circumference of the entrance hole of the tub 31 is rolled outward, and the tub coupling part 62 is fitted in a concave area formed by the outward rolled portion. An annular groove 62 While the casing coupling part 61 is fixed to the front panel 12, the tub coupling part 62 is displaceable in accordance with movement of the tub 31. Accordingly, the gasket body 63 needs to be able to transform in accordance with the displacement of the tub coupling part 62. In order to allow the gasket body 63 to transform easily, the gasket 60 may include a folding part 63 More particularly, referring to The gasket 60 may include an outer door contact part 68 that bends outwardly from the front end of the rim part 63 The gasket 60 may further include an inner door contact part 66 that bends inwardly from the front end of the rim part 63 Meanwhile, during rotation, the drum 32 vibrates (which means that the rotation center line C of the drum 32 moves) and, in turn, the center line of the tub 31 (which is approximately identical to the rotation center line C of the drum 32) moves as well. In this case, a moving direction (hereinafter, referred to as an eccentric direction”) has a radial direction component. The folding part 63 If a portion of the folding part 63 A direct nozzle 42 and a steam spray nozzle 47 may be installed at the rim part 63 When viewed from the front, a plurality of port receiving pipes 641, 642, 643, and 644 may be disposed on the on the left side and/or the right side of the outer circumferential portion 632. Specifically, when viewed from the front, the gasket body 63 is divided into a first area and a second area, which respectively correspond to the left and right sides of the gasket body 63. First and second port receiving pipes 641 and 642 are disposed in the first area (e.g., the left area of a reference line L) in a top-to-bottom direction and parallel to each other. Third and fourth port receiving pipes 643 and 644 are disposed in the second area (e.g., the right area of the reference line L) in the top-to-bottom direction and parallel to each other. The port receiving pipes 641, 642, 643, and 644 may protrude outwardly from the outer circumferential portion 632. In the present embodiment, two of the port receiving pipes 641, 642, 643, and 644 are disposed on the left side of the outer circumferential portion 632, and the other two are disposed on the right side of the outer circumferential portion 632. For distinction, such pipes are respectively referred to as a first port receiving pipe 641, a second port receiving pipe 642, a third port receiving pipe 643, and a fourth port receiving pipe 644. Referring to The second port receiving pipe 642 is disposed below the first port receiving pipe 641. The first port receiving pipe 641 and the second port receiving pipe 642 may be disposed in parallel with each other. The first port receiving pipe 641 and the second port receiving pipe 642 may extend in a horizontal direction (or a left-and-right direction. Through holes respectively formed in the first port receiving pipe 641 and the second port receiving pipe 642 may extend horizontally and be parallel to each other. Referring to The second port receiving pipe 642 is disposed lower at a second distance d2 than the middle height point O of the gasket body 63. Here, the second distance d2 is smaller than the first distance d1 (d2<d1). The exterior appearance of the gasket body 63 is approximate a round shape, and thus, if a random point on the outer circumferential portion 632 is closer to the middle height point O in an upward or downward direction, the random point may be relatively distal from a symmetry reference line L. Thus, in the present embodiment, a connection point between the second port receiving pipe 642 and the outer circumferential portion 632 is distal from the symmetry reference line L than a connection point between the first port receiving pipe 641 and the outer circumferential portion 632, and it appears that the second port receiving pipe 642 protrudes rightward further from the symmetric reference line L. Accordingly, it is preferable that a length of the second port receiving pipe 642 is set relatively short so as to secure a space to install a distribution pipe 70 between the gasket body 63 and the cabinet 11. Likewise, a length of the fourth port receiving pipe 644 may be shorter than a length of the third port receiving pipe 643. The fourth port receiving pipe 644 is disposed below the third port receiving pipe 643. The third port receiving pipe 643 and the fourth port receiving pipe 644 may be disposed in parallel with each other. The third port receiving pipe 643 and the fourth port receiving pipe 644 may extend in a horizontal direction (or a left-and-right direction. Through holes respectively formed in the third port receiving pipe 643 and the fourth port receiving pipe 644 may extend horizontally and be parallel to each other. Referring to Meanwhile, the gasket 60 may be fabricated using an injection molding machine 800. Specifically, referring to Molten synthetic resin discharged from an injection machine (not shown) is injected into a cavity that is formed by the fixed mold 850, the first movable mold 810, the second movable mold 820, the third movable mold 830, and the fourth movable mold 840. The fixed mold 850 may be disposed at the center, and the first movable mold 810, the second movable mold 820, the third movable mold 830, and the fourth movable mold 840 may be disposed on a circumference of the fixed mold 850. When the molds are opened up, the first movable mold 810 moves in a forward direction (the upward direction in The direct nozzle port 621 and the steam spray nozzle port 622 disposed in an upper side of the gasket 60 may be molded by the first movable mold 810. Since the direct nozzle port 621 and the steam spray nozzle port 622 extend in the moving direction of the first movable mold 810, mold stripping may be performed smoothly. The residual water port 645 disposed in a lower side of the gasket 60 may be molded by the third movable mold 830. Since the residual water port 645 extends in the moving direction of the third movable mold 830, mold stripping may be performed smoothly. The first port receiving pipe 641 and the second port receiving pipe 642 disposed on the left side of the gasket 60 may be molded by the fourth movable mold 840. The fourth movable mold 840 may move in the left direction, and the first port receiving pipe 641 and the second port receiving pipe 642 may protrude in a direction identical to the moving direction (that is, the left direction) of the fourth movable mold 840. The first port receiving pipe 641 and the second port receiving pipe 642 may be disposed in parallel with each other. In other words, a direction in which the first port receiving pipe 641 protrudes from the outer circumferential surface of the outer circumferential portion 632 may be identical to a direction in which the second port receiving pipe 642 protrudes from the outer circumferential surface of the outer circumferential portion 632. The third port receiving pipe 643 and the fourth port receiving pipe 644 disposed on the right side of the gasket 60 may be molded by the second movable mold 820. The second movable mold 820 may move in the right direction, and the third port receiving pipe 643 and the fourth port receiving pipe 644 may protrude in a direction identical to the moving direction (that is, the right direction) of the second movable mold 820. The third port receiving pipe 643 and the fourth port receiving pipe 644 may be disposed in parallel with each other. In other words, a direction in which the third port receiving pipe 643 protrudes from the outer circumferential surface of the outer circumferential portion 632 may be identical to a direction in which the fourth port receiving pipe 644 protrudes from the outer circumferential surface of the outer circumferential portion 632. Since the first movable mold 810, the second movable mold 820, the third movable mold 830, and the fourth movable mold 840 move in different directions (or the first movable mold 810 and the third movable mold 830 moves in different directions and the second movable mold 820 and the fourth movable mold 840 move in different directions), receiving pipes or ports may be formed on the upper side, the left side, the right side, and the lower side of the gasket 60, respectively. The gasket body 63 may be symmetrical about the symmetry reference line L. The first port receiving pipe 641 and the third port receiving pipe 643 may be disposed at the same height. The second port receiving pipe 642 and the fourth port receiving pipe 644 may be disposed at the same height. The first port receiving pipe 641 and the third port receiving pipe 643 may be in a vertically symmetrical structure which is a structure symmetrical about the symmetry reference line L. Likewise, the second port receiving pipe 642 and the fourth port receiving pipe 644 may be in a vertically symmetrical structure. Meanwhile, referring to [Nozzle] There may be provided a plurality of nozzles 650 As described above, the plurality of port receiving pipes 641, 642, 643, and 644 extends horizontally, and a plurality of outlet ports 761, 762, 763, and 764 described in the following extends horizontally as well to correspond to the plurality of port receiving pipes 641, 642, 643, and 644. Accordingly, circulating water is supplied or guided by each of the outlet ports 761, 762, 763, and 764 in a horizontal direction. The nozzles 650 The upper nozzles 650 When viewed from the front, the first upper nozzle 650 The first upper nozzle 650 In addition, two nozzles positioned below the upper nozzles 650 When viewed from the front, the first lower nozzle 650 When viewed from the front, the second lower nozzle 650 The first lower nozzle 650 Referring to Referring to The first side surface 652 An angle γ formed by the first side surface 652 If a spray width of each water stream sprayed through the nozzles 650 is defined by a spray width angle, the spray width angle may be defined by the first side surface 652 Referring to A difference β2-β1 between the spray width angle β2 for the lower nozzles 650 Meanwhile, a spray direction for each upper nozzle 650 Due to various conditions such as a height, a position, and the spray width angle β1 of each upper nozzle 650 Meanwhile, in the case where an angle from the lowest point in the gasket body 63 to each lower nozzle 650 Meanwhile, each lower nozzle 650 In order to spray circulating water evenly upward and downward in the drum, it is preferable that the upper nozzles 650 Meanwhile, when circulating is sprayed through the lower nozzles 650 Meanwhile, referring to Since the first nozzle 650 In addition, when viewed from the front, a spray direction DR2 of the second nozzle 650 Since the second nozzle 650 Hereinafter, referring to The collision surface 652 Since the nozzle conduit 651 extends horizontally to thereby guide water in a horizontal direction, a water stream travels in a constant direction without influence of the gravity before reaching the nozzle head 652 and is then dispersed by the collision surface 652 If the length direction of the nozzle conduit 651 is not arranged approximately horizontally but arranged toward the center O of the gasket 60, the weight of gravity acts on downward movement of water flowing in the nozzle conduit 651 of each upper nozzle 650 Referring to The gasket 60 may include a protruding part 655 protruding from the inner circumferential surface of the gasket body 63. To correspond to the plurality of nozzles 650 The nozzle conduit 651 may include a flow path reducing portion 651 Meanwhile, at least a portion of the distribution pipe 701 may be disposed between the outer circumferential surface of the gasket 60 and a balancer 81 and 82. The distribution 701 may be installed in an existing space (that is, a space between the outer circumferential surface of the gasket 60 and the balancer 81 and 82), without need for an additional space for the installation. The pair of the upper nozzles 650 The pair of the upper nozzles 650 The pair of the lower nozzles 650 The pair of the lower nozzles 650 Taken an example of the first nozzle 650 The nozzle head 652 interferes with sprayed circulating water and changes a spray direction of the circulating water. The nozzle head 652 sprays the circulating water toward an inner portion of the rear side of the tub 32. The other end 653 of the nozzle head 652 is spaced apart from a discharge side (the other side) of the nozzle conduit 651. Spaced apart from the other end of the nozzle conduit 651, the nozzle head 652 is disposed to hide the nozzle conduit 651. Circulating water hits an inner surface of the nozzle head 652, thereby changing a direction to be discharged. The other end 653 of the nozzle head 652 is disposed to face the rear of the tub 31. Circulating water discharged through a discharge hole 651 The distribution pipe 701 includes the inlet port 71 connected to a circulation pipe 18, a transport conduit 74 guiding water introduced through the inlet port 73, and a plurality of outlet ports 761, 762, 763, and 764 protruding from the transport conduit 74. The distribution pipes 701 may be formed of synthetic resin that is harder or stiffer than the gasket 60. The distribution pipes 701 maintains a predetermined shape in spite of vibration occurring during operation of the washing machine, and the distribution pipes 701 is relatively rigid compared to the gasket 60, which transforms in response to vibration of the tub 31. The same description apply to a first distribution pipe 701 and a second distribution pipe 703 which are described in the following. The distribution pipe 701 branches circulating water discharged from the circulation pipe 18 to thereby form a first sub-flow FL1 (see One end of the first conduit 75 and one end of the second conduit 76 are connected to each other, and the inlet port 73 protrudes in the connected portion. However, the other end of the first conduit 75 and the other end of the second conduit 76 are separated from each other. That is, the transport conduit 74 generally has a “Y” shape to thereby branch circulating water introduced through one entrance hole (that is, the inlet port 73) into two flow paths. The nozzles 650 The outlet ports 761, 762, 763, and 764 are provided in a number corresponding to the number of the nozzles 650 The outlet ports 761, 762, 763, and 764 may include a first upper outlet port 761 supplying circulating water to the first upper nozzle 650 The transport conduit 74 is disposed in a circumference of the outer circumferential part of the gasket 60, and connected to a pump 901 via the circulation pipe 18. The respective outlet ports 761, 762, 763, 764 protrudes inwardly from the transport conduit 74 along a radial direction and are inserted into the gasket 60 to thereby supply circulating water to the corresponding nozzles 650 The distribution pipe 701 may include the inlet port 73 that protrudes from the transport conduit 74 to be connected to the circulation pipe 18. The inlet port 73 may protrude outwardly from the transport conduit 74 along the radial direction. Referring to The first section 751 extends from the inlet port 73. The first section 751 is an arc-shaped section that extends at a predetermined curvature. In the present embodiment, the first section 751 is a curved line having an approximately predetermined curvature, but aspects of the present invention are not limited thereto. In some embodiments, the first section 751 may be in a shape in which two or more curved lines having different curvatures are connected. The second section 752 may continue from the first section 751 and have a shape spreading outwardly from the first section 751. In other words, the second section 752 corresponds to a portion that is bent outwardly (that is, a direction distal from the center O) from the top end of the first section 751 and extends by a distance L2. The length L2 of the second section 752 may be shorter than a length Ll of the first section 751. The third section 753 is a portion that is bent inwardly (that is, a direction proximal to the center O) from the second section 752 and extends by a distance L3. The third section 753 may extend substantially vertically upward from the second section 752. The lower outlet port 762 may be formed in the third section 753 and extend in a horizontal direction (or a direction orthogonal to the second section 752). In the third section 753, a surface 750 The fourth section 754 is bent inwardly (that is, in a direction proximal to the enter O) from the third section 753 and further extends by a distance L4 to thereby reach an end portion of the first conduit 75. The upper outlet port 761 may be formed in the fourth section 754 and preferably at an end portion of the fourth section 754 as shown in the present embodiment. The fourth section 754 may be in the shape of a curved line having a predetermined curvature, and may extend in a direction intersecting with a length direction of the upper outlet port 761. At an end portion of the first conduit 75 (or an end portion of the fourth section 754, a surface 750 Meanwhile, since the fourth section 754 is in the shape bent inwardly from the third section 753, the surface 750 In addition, when viewed from the front, an end portion of the first outlet port 761 is disposed at a location closer by a distance S to the symmetry reference line L than an end portion of the second outlet port 762. Referring to Likewise, in the second conduit 760, a third port connection part 767 may be formed at a portion connected to the third outlet port 763, and a fourth port connection part 768 may be formed at a portion connected to the fourth outlet port 764. When viewed from the front, the respective port connection parts 757, 758, 767, and 768 may be in the shape that is convex further forward compared to a surrounding area. A width P of each of the port connection parts 757, 758, 767, and 768 may be greater than a width W of the surrounding portions. In other words, the conduits 75 ad 76 may extend from the inlet port 73 with a constant width W, protrude forward convexly, and is then reduced in width to thereby extend to the port connection part 757 with the width W. Meanwhile, the width P of the port connection parts 757, 758, 767, and 768 may be greater than a diameter t of the outlet port 761. Referring to If a direction in which the outlet port 761 is inserted into the port receiving pipe 641 is defined as a first direction, the press-fit protrusion 769 may include a vertical surface and a slope surface that is inclined so that a height thereof is gradually reduced from the vertical surface toward the first direction. When the outlet port 761 is inserted into the port receiving pipe 641, press fitting is enabled easily due to the slope surface. After the press fitting is completed, the outlet port 761 is not allowed to be separated from the port receiving pipe 641 easily due to the vertical surface. The distribution pipe 701 is capable of being coupled to the gasket 60 without using a binding member (e.g., a clamp), and thus, a work time for screwing the binding member is not required Meanwhile, while the outlet ports 761, 762, 763, and 764 are inserted into the port receiving pipes 641, 642, 643, and 644, an end portion of each of the outlet ports 761, 762, 763, and 764 is able to reach the nozzle conduit 651. At this point, the inner circumferential surface of each of the outlet ports 761, 762, 763, and 764 and the inner circumferential surface of the conduit 651 forms a substantially continuing surface, thereby reducing resistance of circulating water. The nozzle conduit 651 has an annular shape, protrudes from the inner circumferential surface of the outer circumferential portion 632, and is connected to a corresponding nozzle head 652. There is provided a pump 902 for supplying circulating water to the two distribution pipes 702 and 703. The pump 902 may include two circulation ports 912 More particularly, the pump 902 includes a pump housing 91, an impeller 915 disposed in the pump housing 915, and a pump motor 92 configured to provide a torque to rotate the impeller 915. The pump housing 91 forms a chamber where the impeller 915 is housed. The pump housing 91 includes an inlet port 911 connected to a drain bellows 17 to guide circulating water into the chamber, and a first circulation port 912 and a second circulation port 912 A water current formed upon rotation of the impeller 815 by the pump motor 92 is discharged through the first circulation port 912 The first distribution pipe 912 The two outlet ports 761 and 762 may be inserted into a first port receiving pipe 641 and a second port receiving pipe 642, respectively. The second distribution pipe 703 supplies circulating water to the third nozzle 650 The two outlet ports 763 and 764 may be inserted into the third port receiving pipe 643 and the fourth port receiving pipe 644, respectively. Meanwhile, the pump housing 91 may further include a drain port 913 connected to the drain pipe 19. Like the above-described embodiment, the pump 901 may further include a chamber 916 into which circulating water is introduced through the inlet port 911 and which communicates with the drain port 913, an impeller 917 rotating in the chamber 916, and a second pump motor 93 rotating the impeller 917 (see Although some embodiments have been described above, it should be understood that the present invention is not limited to these embodiments, and that various modifications, changes, alterations and variations can be made by those skilled in the art without departing from the spirit and scope of the invention. Therefore, it should be understood that the above embodiments are provided for illustration only and are not to be construed in any way as limiting the present invention. A washing machine includes a casing, a tub, a drum, a pump for circulating water from the tub, a gasket connecting an entry hole of the casing to an entrance hole of the tub and including nozzles for spraying water to the drum, and outlet ports for supplying water to the nozzles. The nozzles are arranged at an inner surface of the gasket at both lateral sides of the gasket in a vertical direction. The gasket includes port receiving pipes that receive the outlet ports, respectively, that are arranged in the vertical direction at an outer surface of the gasket, and that extend parallel to each other. 1. A washing machine comprising:
a casing that defines an entry hole at a front surface of the casing; a tub disposed in the casing and configured to receive wash water, the tub defining a tub opening at a front surface of the tub; a drum rotatably disposed in the tub; a gasket comprising:
a gasket body that defines a passage connecting the entry hole to the tub opening, wherein the gasket body includes a first area and a second area that correspond to bilateral areas of the gasket body, a plurality of nozzles disposed at an inner circumferential surface of the gasket body and configured to spray wash water into the drum, and a plurality of port receiving pipes that protrude from an outer circumferential surface of the gasket body and that are configured to communicate with the plurality of nozzles, respectively; a plurality of outlet ports inserted into the plurality of port receiving pipes, respectively; and a pump configured to circulate wash water discharged from the tub to the plurality of outlet ports, wherein the plurality of port receiving pipes comprise a first port receiving pipe and a second port receiving pipe that are arranged in a vertical direction at the first area of the gasket body, and wherein the first port receiving pipe and the second port receiving pipe extend parallel to each other. 2. The washing machine of 3. The washing machine of 4. The washing machine of wherein the third port receiving pipe and the fourth port receiving pipe extend parallel to each other. 5. The washing machine of 6. The washing machine of wherein the fourth port receiving pipe is disposed at a position corresponding to a height of the second port receiving pipe with respect to the lowest point of the gasket body. 7. The washing machine of a casing coupling part coupled to a circumference of the entry hole; and a tub coupling part coupled to a circumference of the tub opening, and wherein the gasket body extends from the casing coupling part to the tub coupling part. 8. The washing machine of a rim part that extends from the casing coupling part toward the tub coupling part; an inner circumferential part that extends from the rim part toward the casing coupling part; and an outer circumferential part that extends from the inner circumferential part toward the tub coupling part, and wherein the first port receiving pipe and the second port receiving pipe protrude from an outer circumferential surface of the outer circumferential part of the gasket body. 9. The washing machine of 10. The washing machine of wherein the second port receiving pipe is disposed vertically below the middle height point of the gasket body, and wherein a first distance between the first port receiving pipe and the middle height point of the gasket body is greater than a second distance between the second port receiving pipe and the middle height point of the gasket body. 11. The washing machine of wherein the third port receiving pipe and the fourth port receiving pipe extend parallel to each other, and wherein a length of the fourth port receiving pipe is less than a length of the third port receiving pipe. 12. The washing machine of wherein the fourth port receiving pipe is disposed vertically below the middle height point of the gasket body, and wherein a first distance between the third port receiving pipe and the middle height point of the gasket body is greater than a second distance between the fourth port receiving pipe and the middle height point of the gasket body. 13. The washing machine of wherein the second port receiving pipe and the fourth port receiving pipe are disposed symmetrically at the gasket body. 14. The washing machine of wherein the third port receiving pipe and the fourth port receiving pipe extend parallel to each other, wherein the washing machine further comprises:
a circulation pipe configured to guide wash water discharged from the pump, and a distribution pipe fixed to the gasket and configured to supply, to the plurality of nozzles, wash water guided along the circulation pipe, wherein the distribution pipe comprises:
an inlet port connected to the circulation pipe, and a first conduit part and a second conduit part that extend from the inlet port and that are configured to branch wash water supplied through the inlet port, and wherein the plurality of outlet ports comprise: a first outlet port and a second outlet port that are disposed at the first conduit part and that are inserted into the first port receiving pipe and the second port receiving pipe, respectively, and a third outlet port and a fourth outlet port that are disposed at the second conduit part and that are inserted into the third port receiving pipe and the fourth port receiving pipe, respectively. 15. The washing machine of wherein the third port receiving pipe and the fourth port receiving pipe extend parallel to each other, wherein the washing machine further comprises:
a first circulation pipe and a second circulation pipe that are configured to guide wash water discharged from the pump, a first distribution pipe fixed to the first area of the gasket body and configured to guide wash water supplied through the first circulation pipe, and a second distribution pipe fixed to the second area of the gasket body and configured to guide wash water supplied through the second circulation pipe, and wherein the plurality of outlet ports comprise: a first outlet port and a second outlet port that are disposed at the first distribution pipe and that are inserted into the first port receiving pipe and the second port receiving pipe, respectively, and a third outlet port and a fourth outlet port that are disposed at the second distribution pipe and that are inserted into the third port receiving pipe and the fourth port receiving pipe, respectively. 16. A washing machine comprising:
a casing that defines an entry hole at a front surface of the casing; a tub disposed in the casing and configured to receive wash water, the tub defining a tub opening at a front surface of the tub; a drum rotatably disposed in the tub; a gasket comprising:
a gasket body that defines a passage connecting the entry hole to the tub opening, wherein the gasket body includes a first area and a second area that correspond to bilateral areas of the gasket body, a first nozzle and a second nozzle that are disposed at an inner circumferential surface of the gasket body and that are arranged in a vertical direction at the first area of the gasket body, and a third nozzle and a fourth nozzle that are disposed the inner circumferential surface of the gasket body and that are arranged in the vertical direction at the second area of the gasket body facing the first area of the gasket body; at least one pump configured to circulate wash water discharged from the tub; and at least one distribution pipe configured to receive wash water discharged from the pump and to supply received wash water to the first nozzle, the second nozzle, the third nozzle, and the fourth nozzle, wherein the first nozzle and the third nozzle are disposed vertically above a half point of the gasket body corresponding to a half of a height of the gasket body with respect to a lowest point of the gasket body, the first nozzle and the third nozzle being configured to spray water downward to the drum, and wherein the second nozzle and the fourth nozzle are disposed vertically below the half point of the gasket body and configured to spray water upward to the drum. 17. The washing machine of 18. The washing machine of 19. The washing machine of Wherein the second nozzle is configured to spray a second water stream in a second direction laterally symmetrical with a fourth water stream sprayed through the fourth nozzle. 20. The washing machine of wherein the second nozzle is configured to spray a second water stream having a second spray width angle about the second nozzle, the second spray width angle being greater than the first spray width angle. 21. The washing machine of 22. The washing machine of 23. The washing machine of 24. The washing machine of 25. The washing machine of wherein the first nozzle is disposed at an upper position between the second nozzle and a highest point of the gasket body, the upper position defining a second angle with respect to the highest point of the gasket body about the center of the gasket, wherein the second angle is less than a half of a difference between 180° and the first angle, and wherein the first nozzle is disposed closer to the highest point of the gasket than to the second nozzle. 26. The washing machine of 27. The washing machine of 28. The washing machine of 29. The washing machine of CROSS-REFERENCE TO RELATED APPLICATIONS
BACKGROUND OF THE INVENTION
1. Field of the Invention
2. Description of the Related Art
SUMMARY OF THE INVENTION
BRIEF DESCRIPTION OF THE DRAWINGS
DETAILED DESCRIPTION OF THE PREFERRED EMBODIMENTS
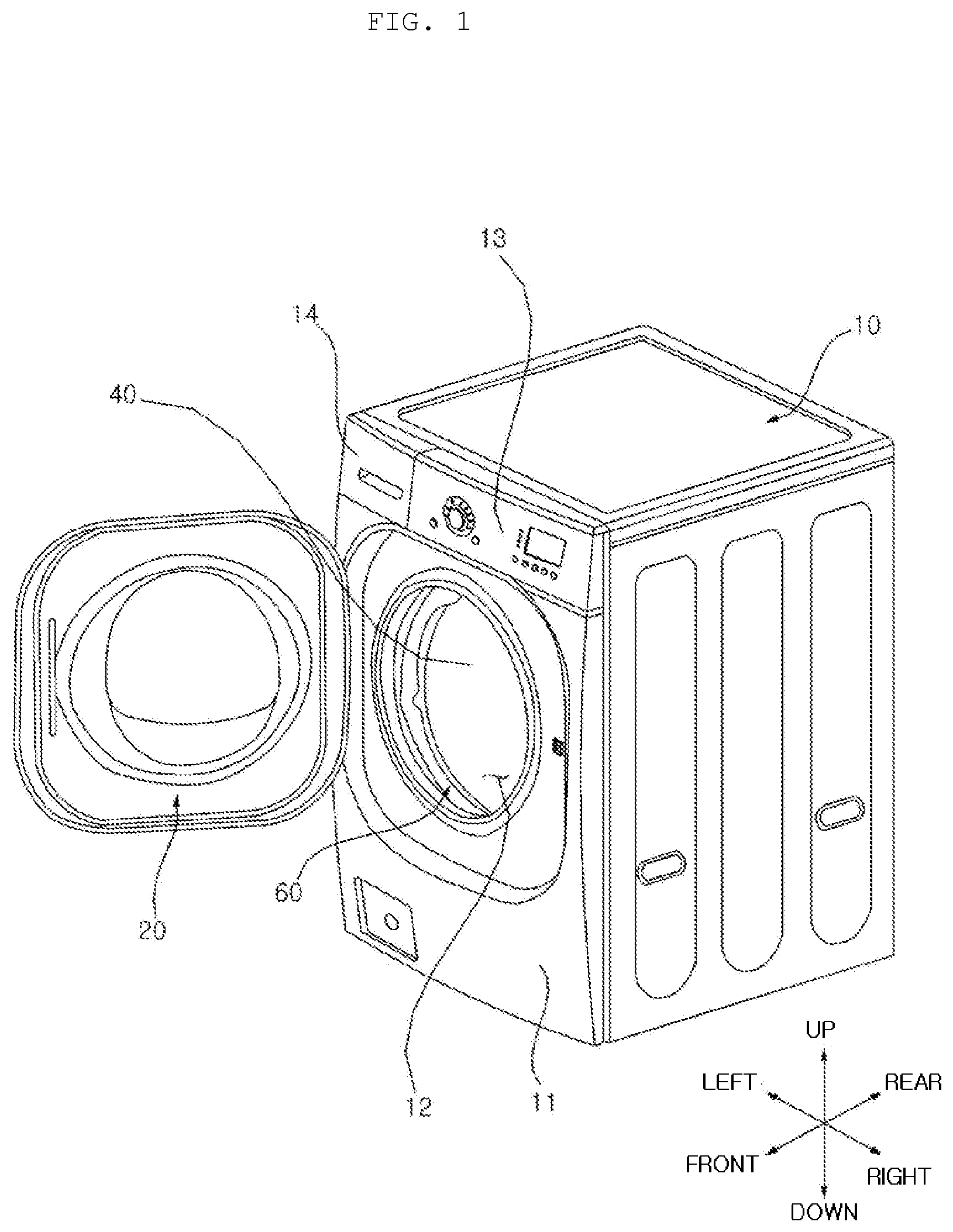
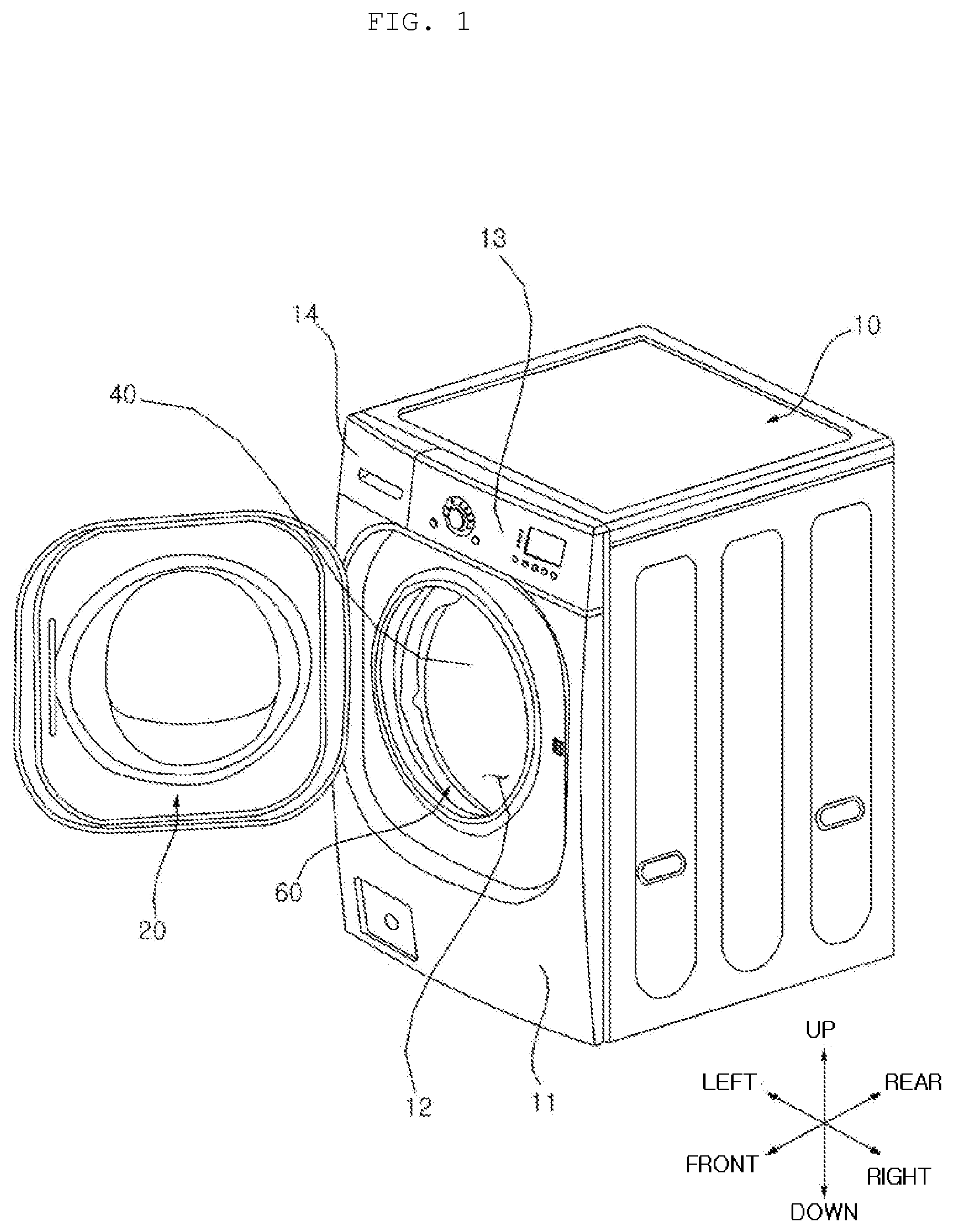
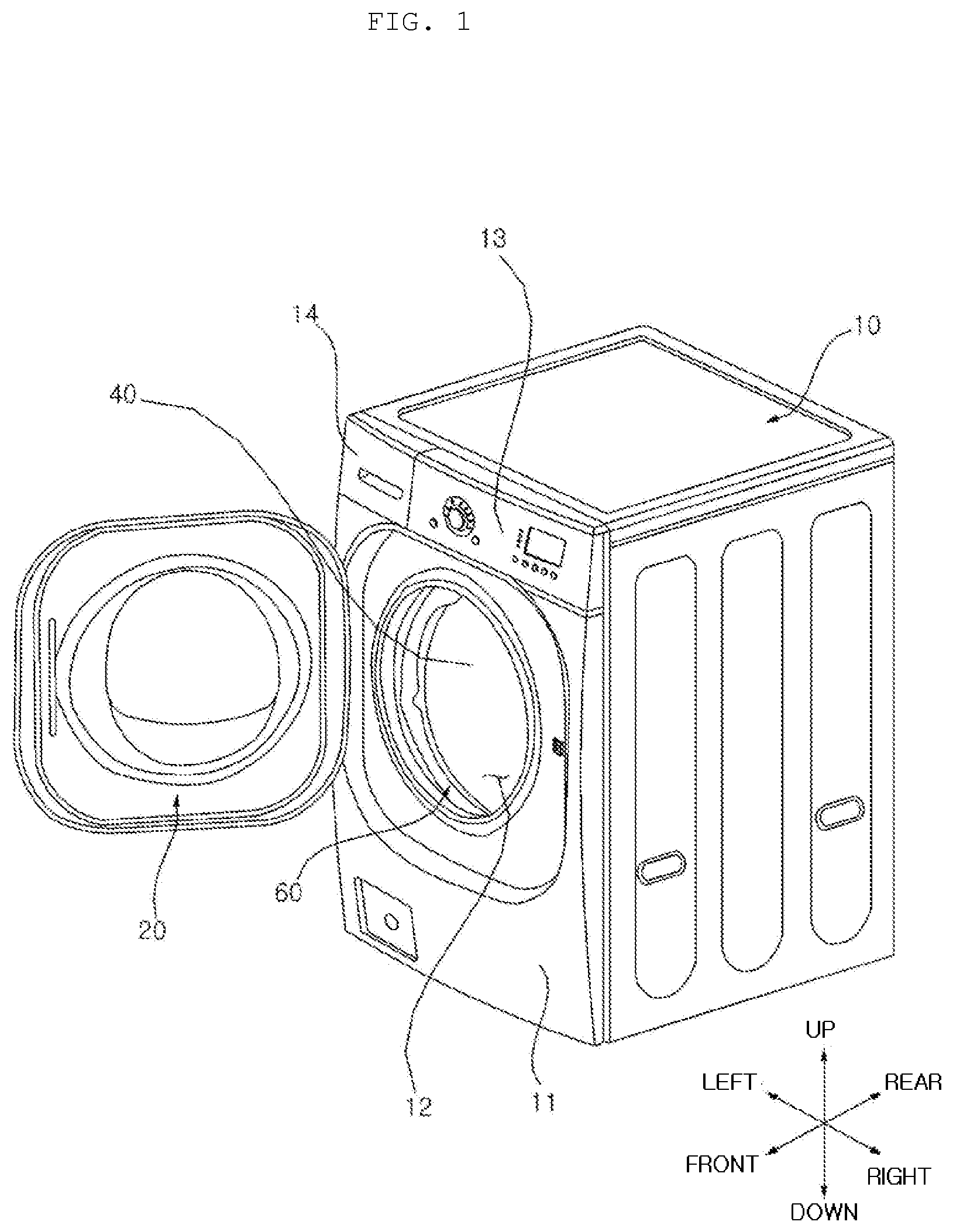
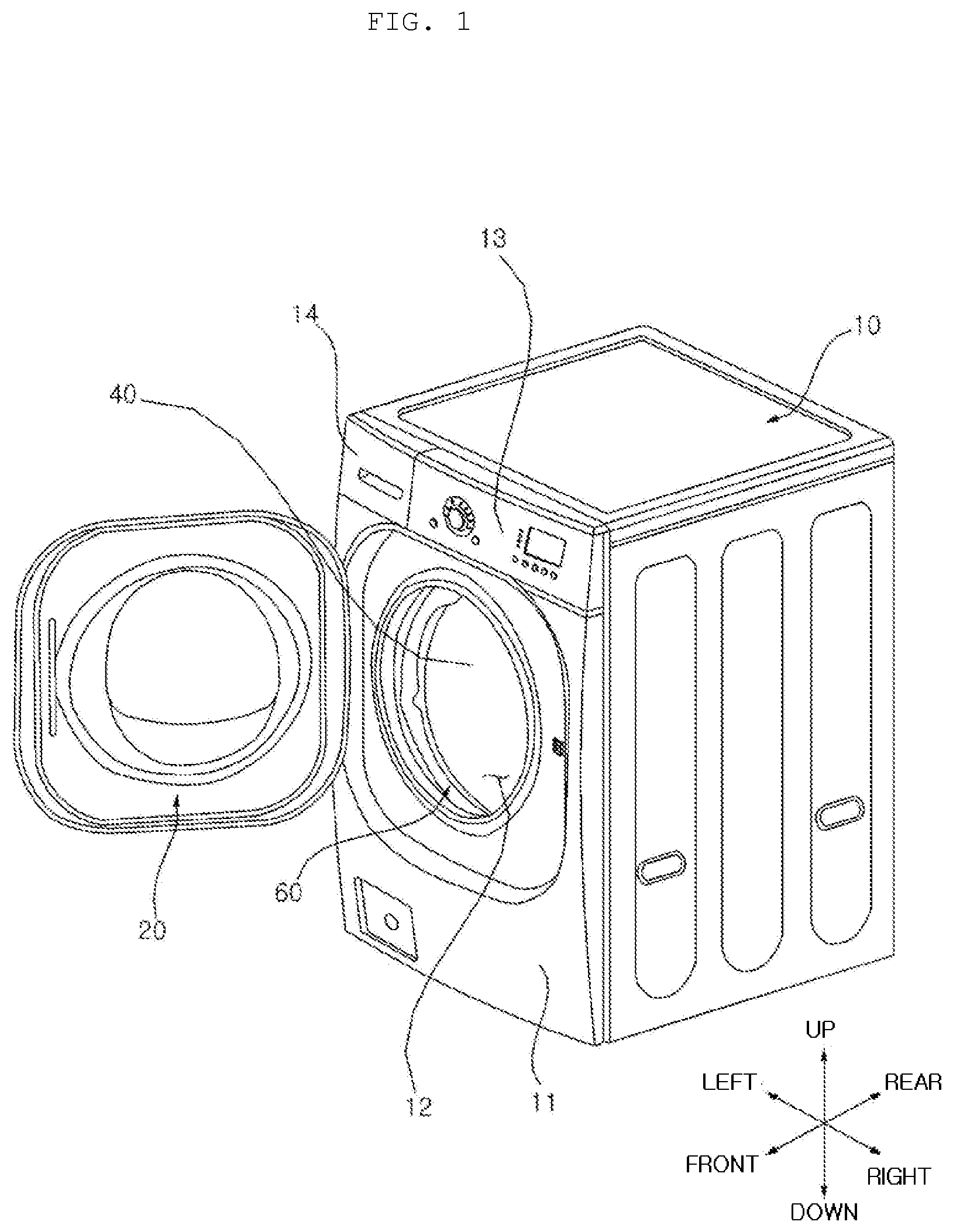
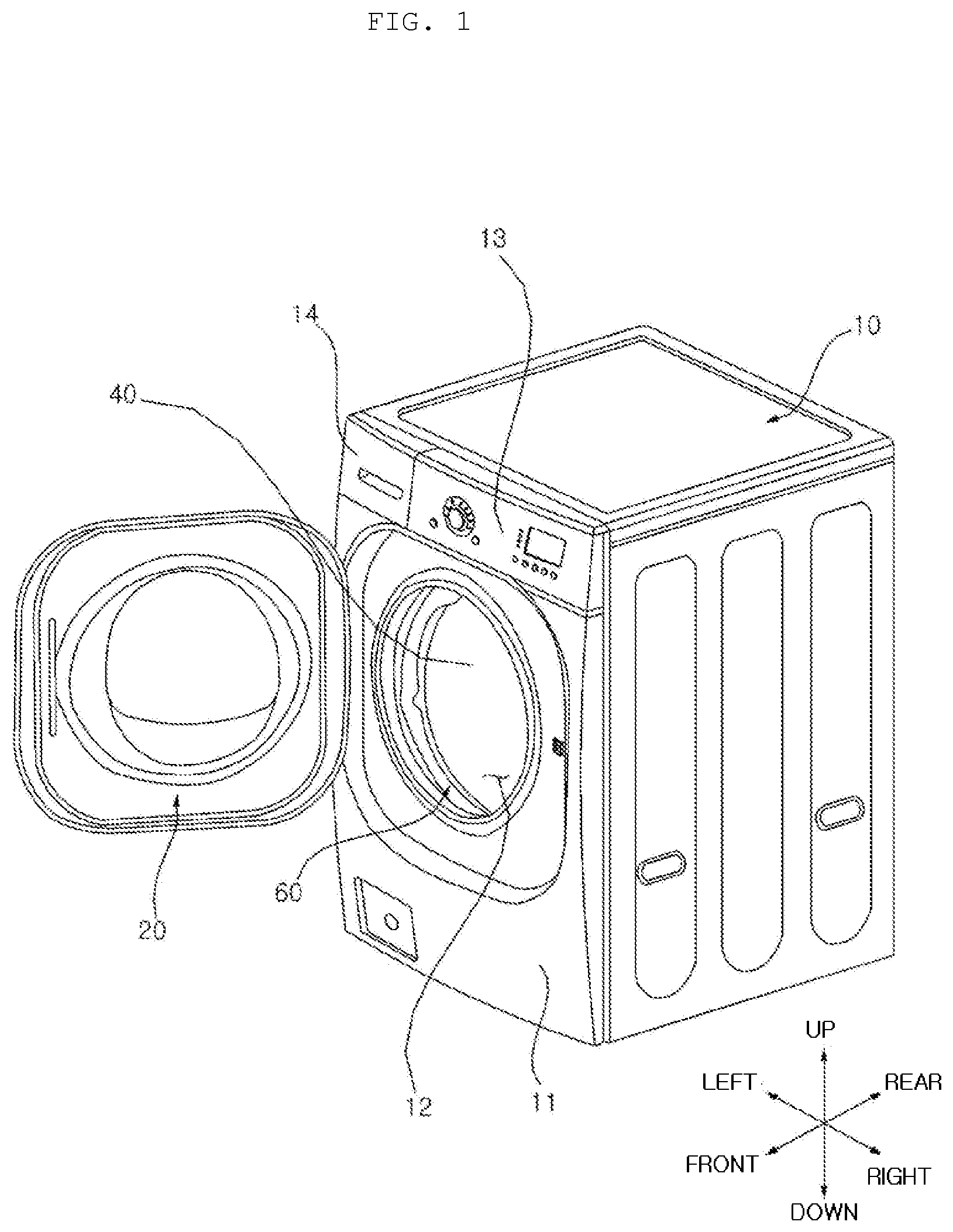
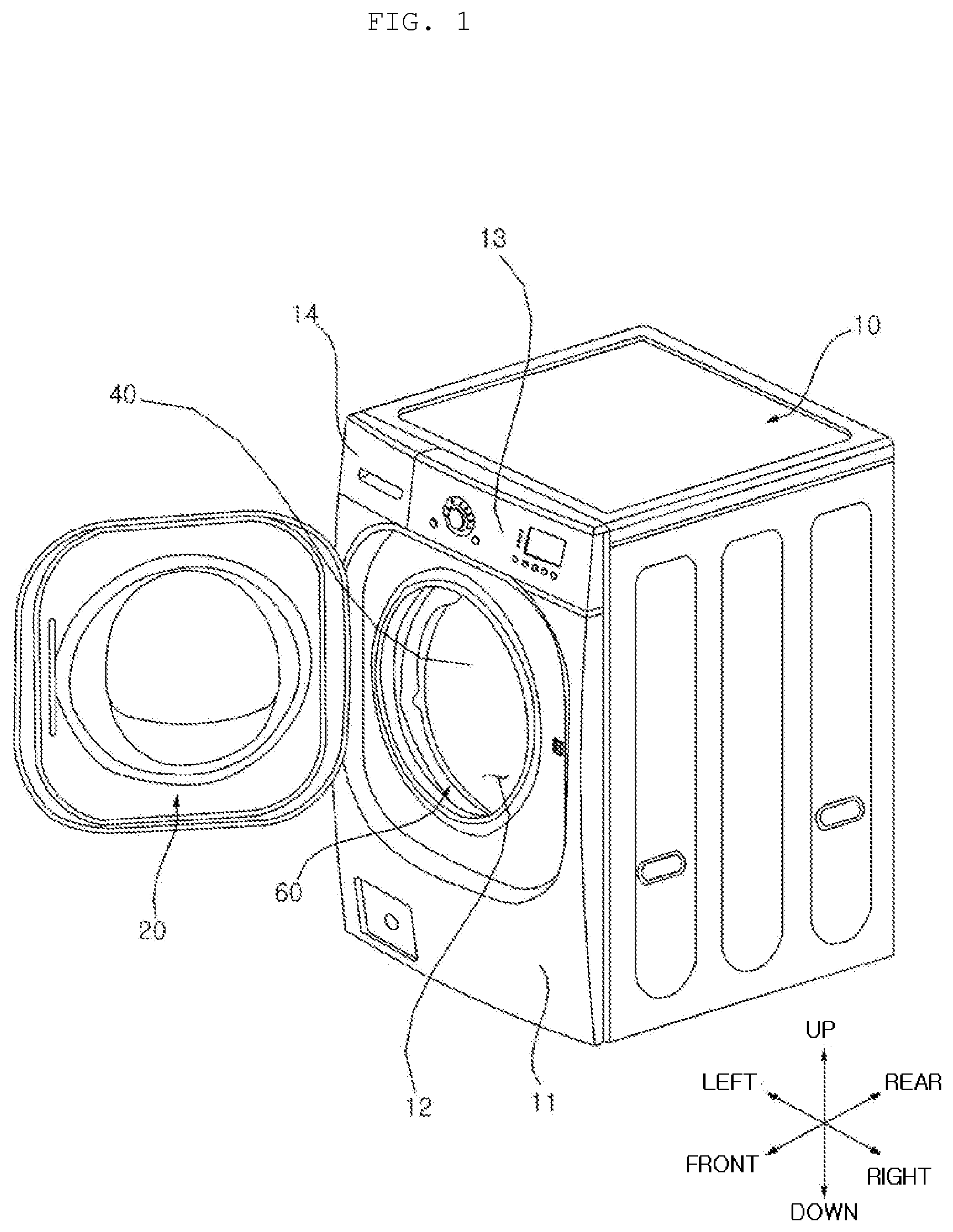
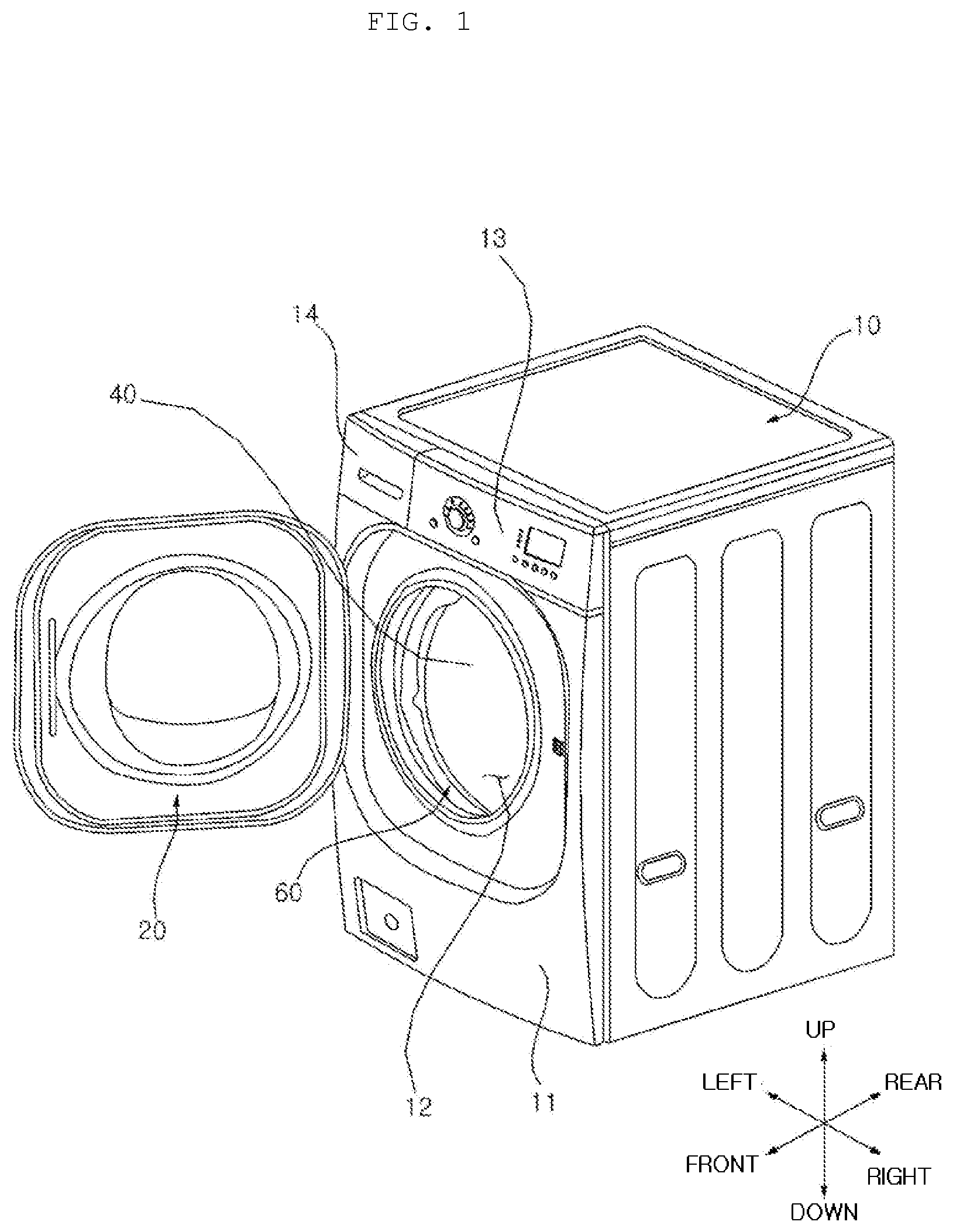
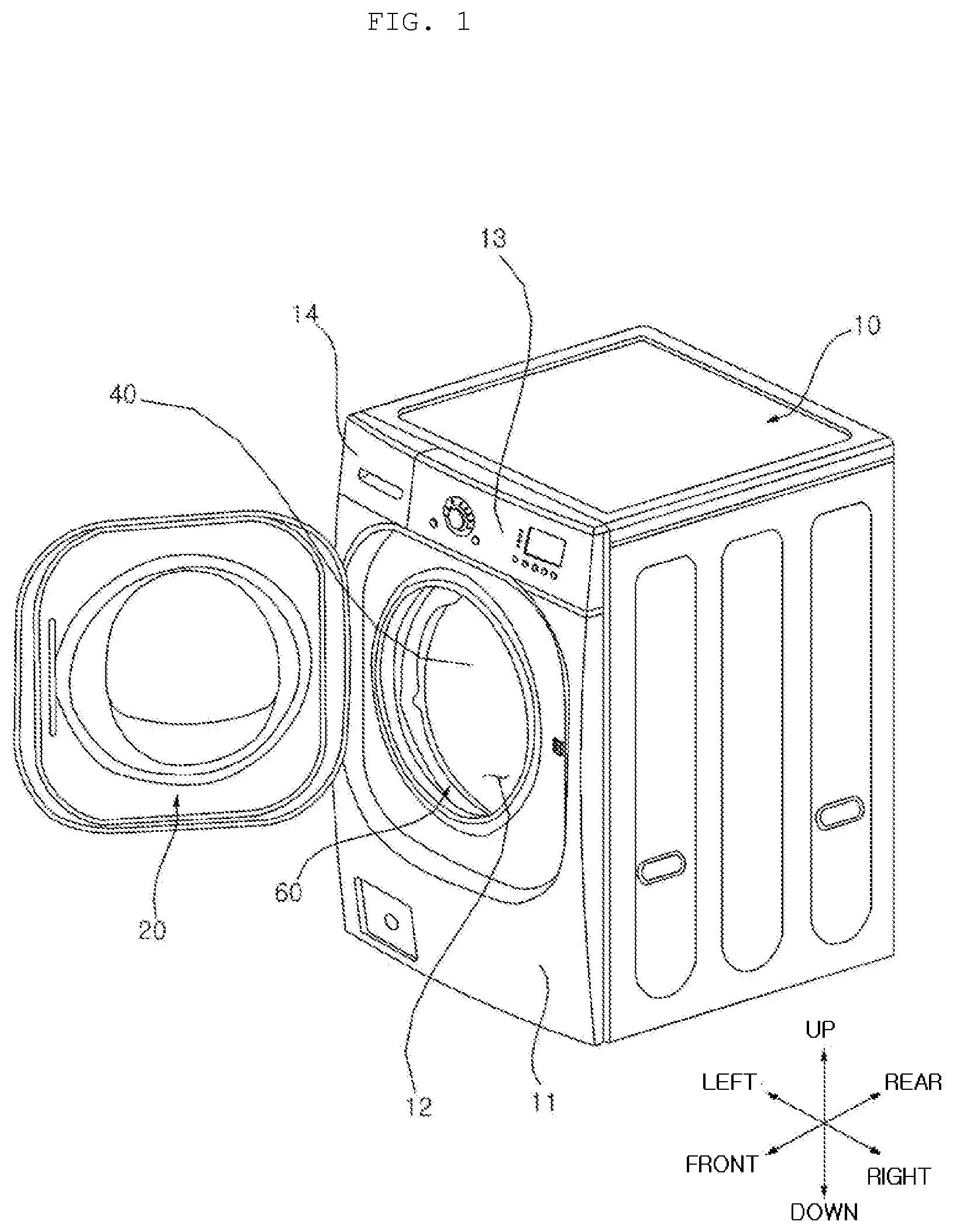
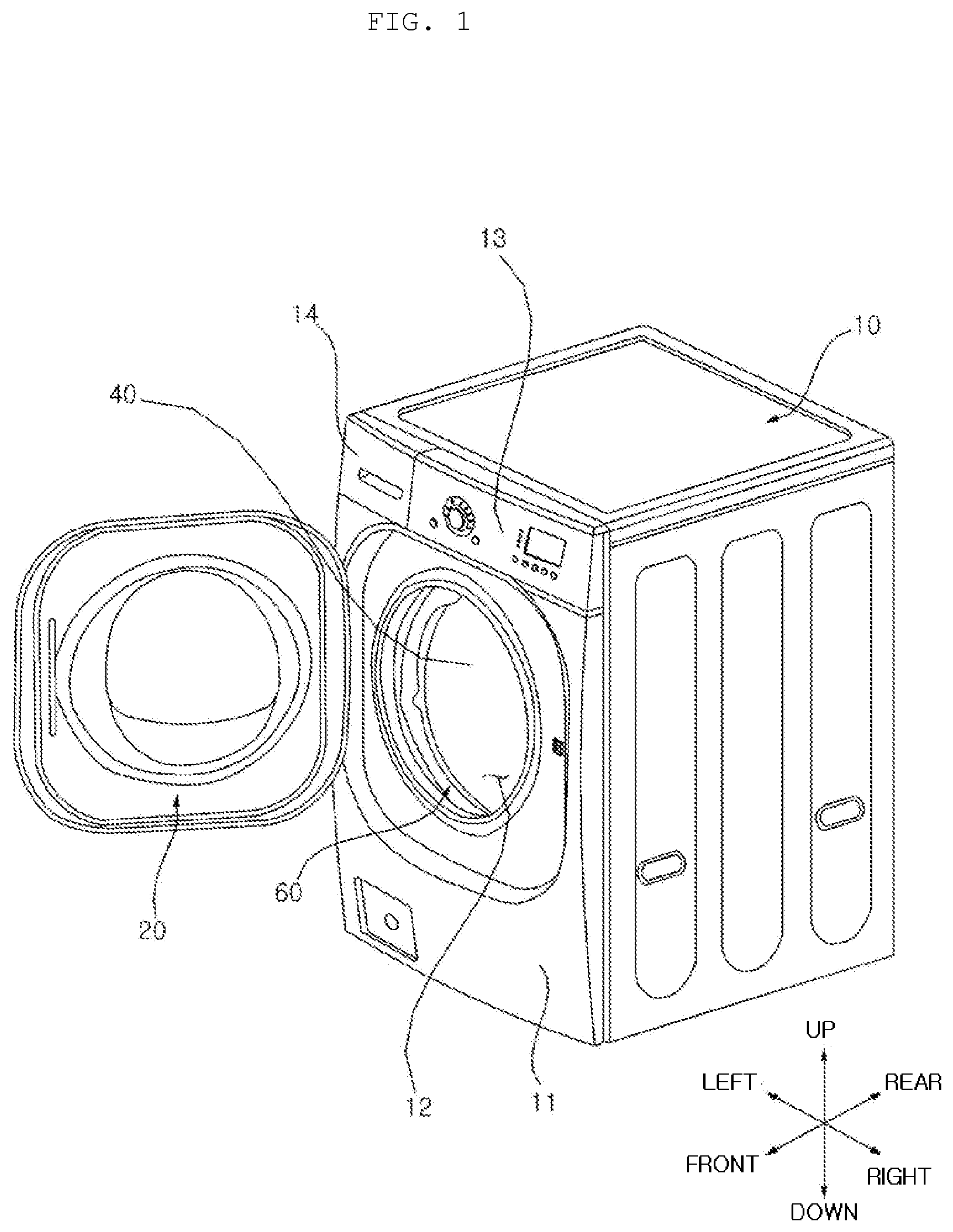
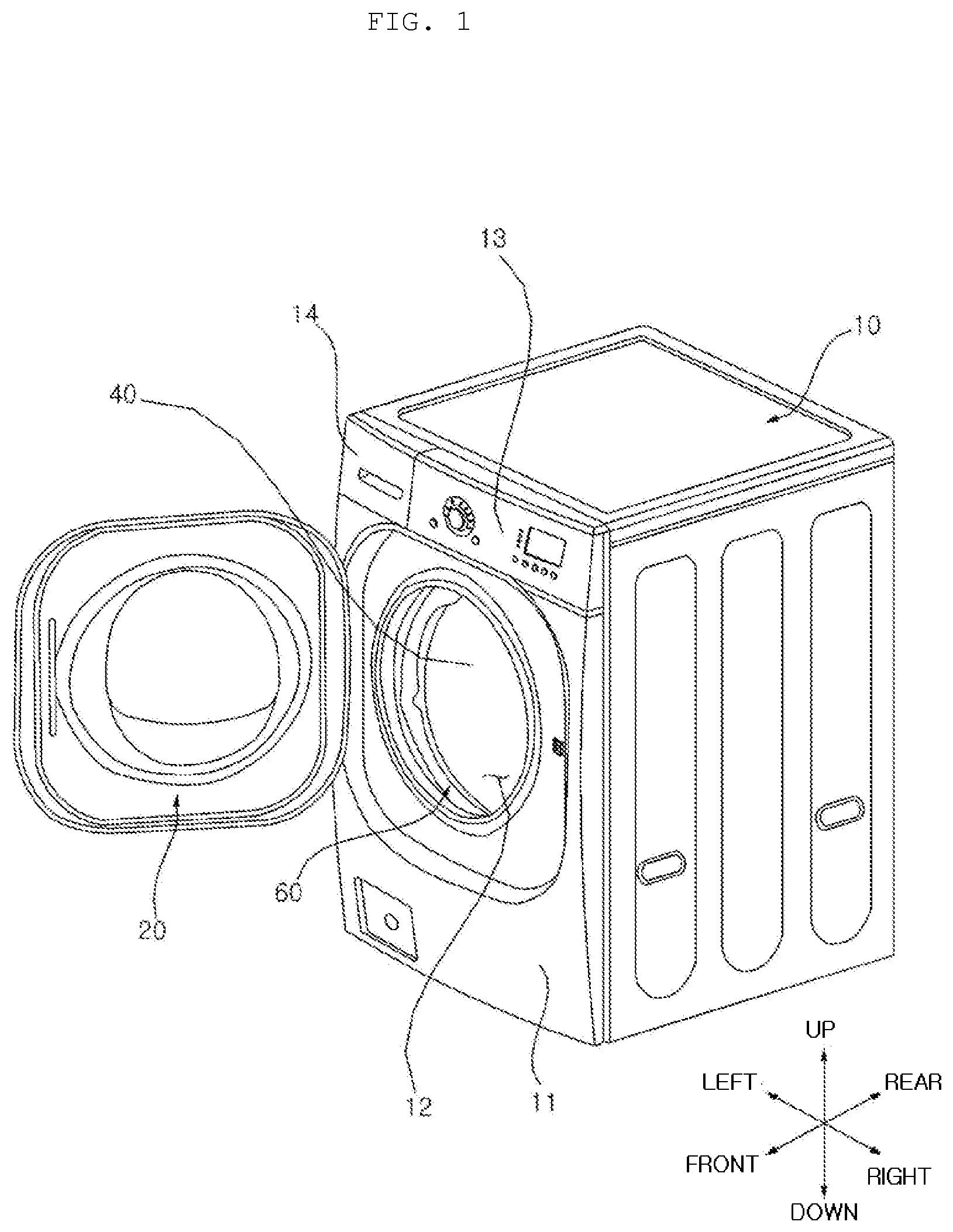
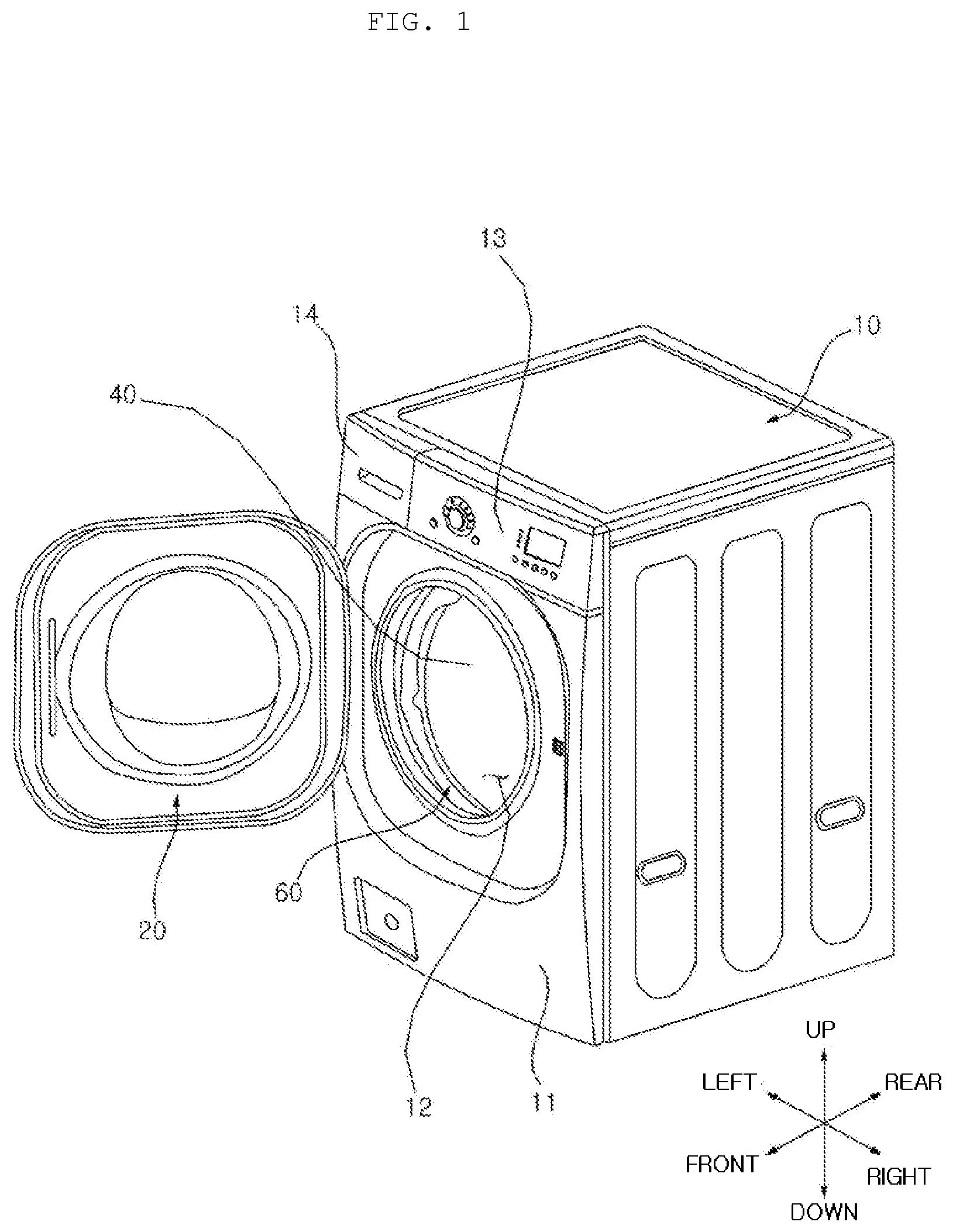
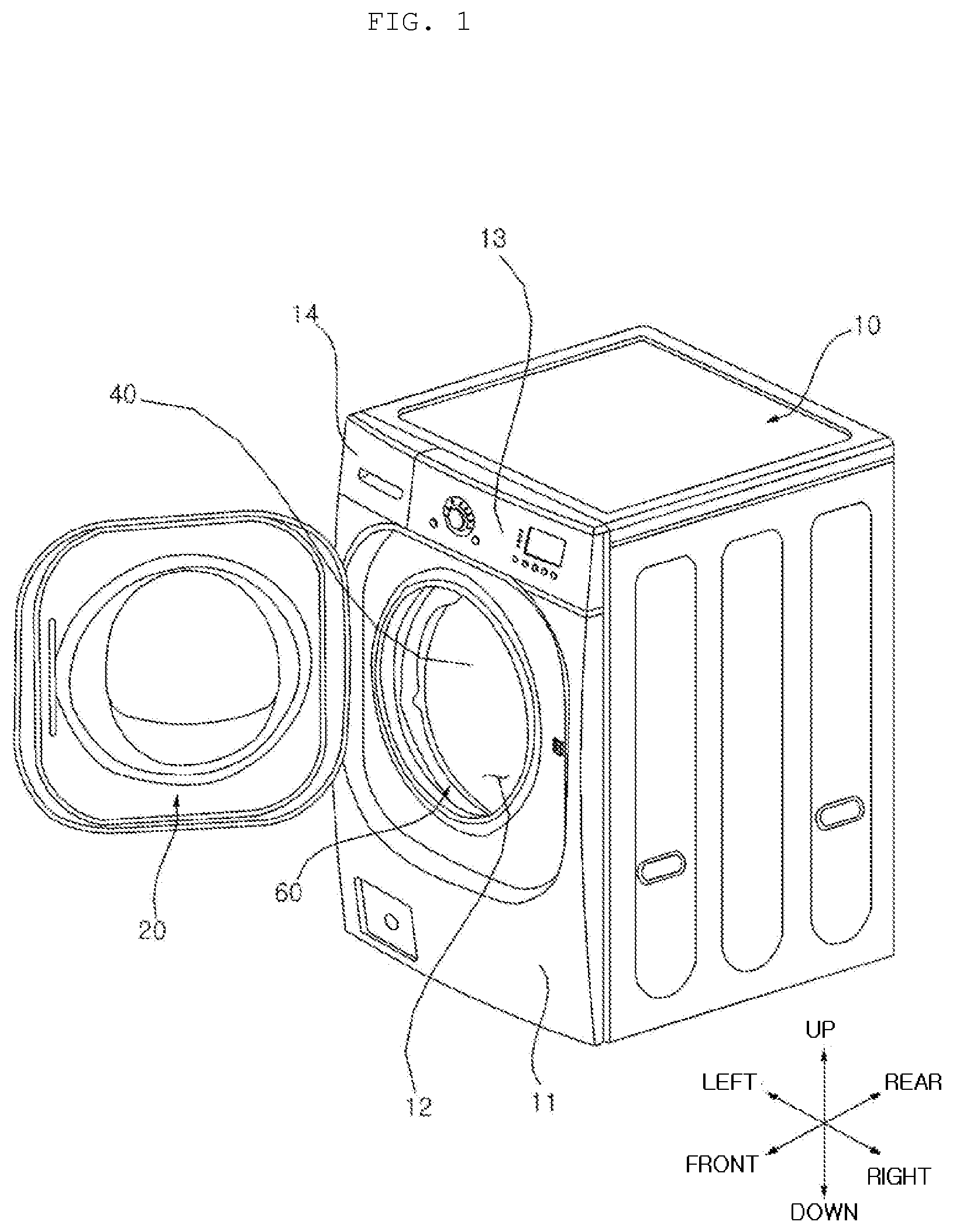
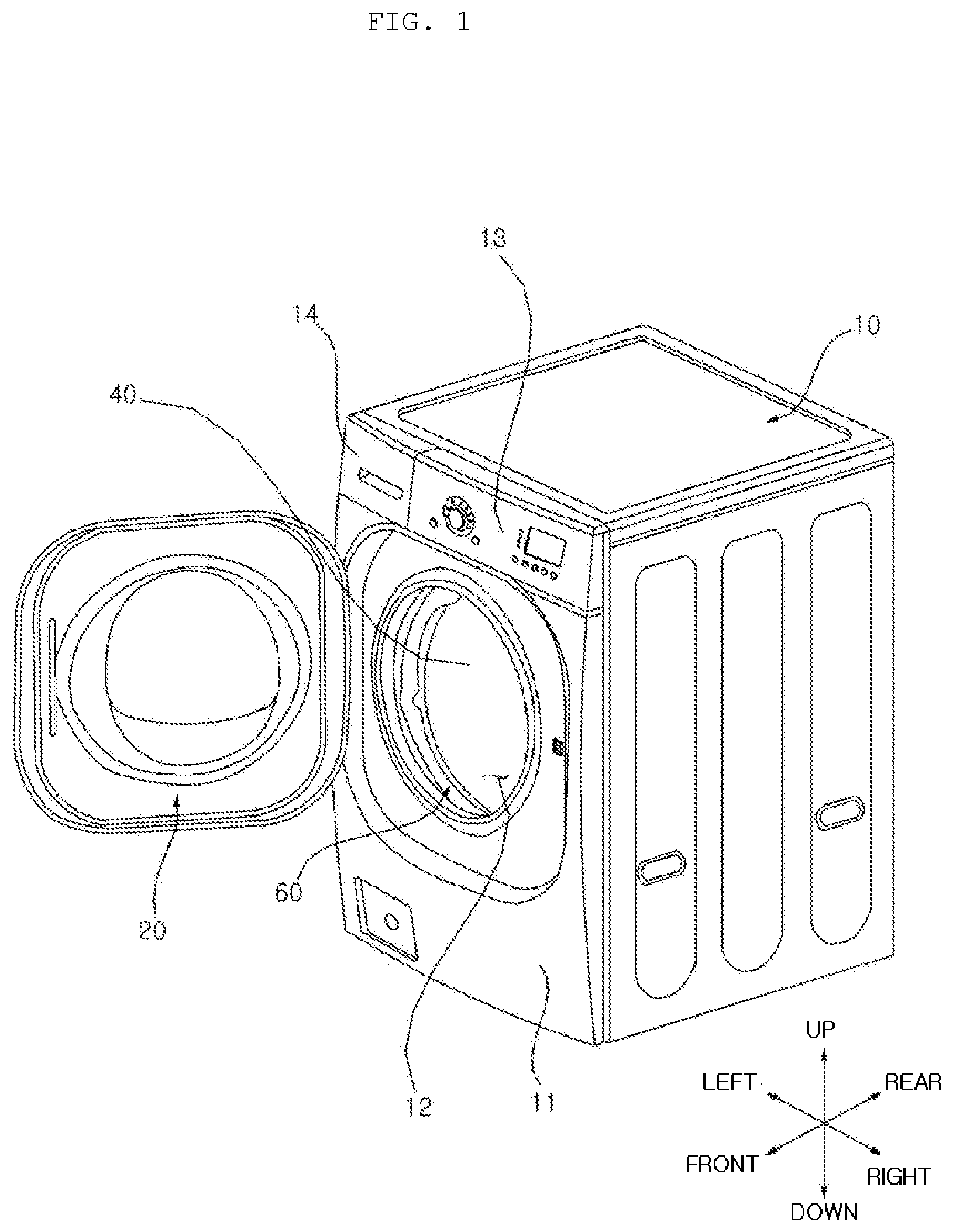
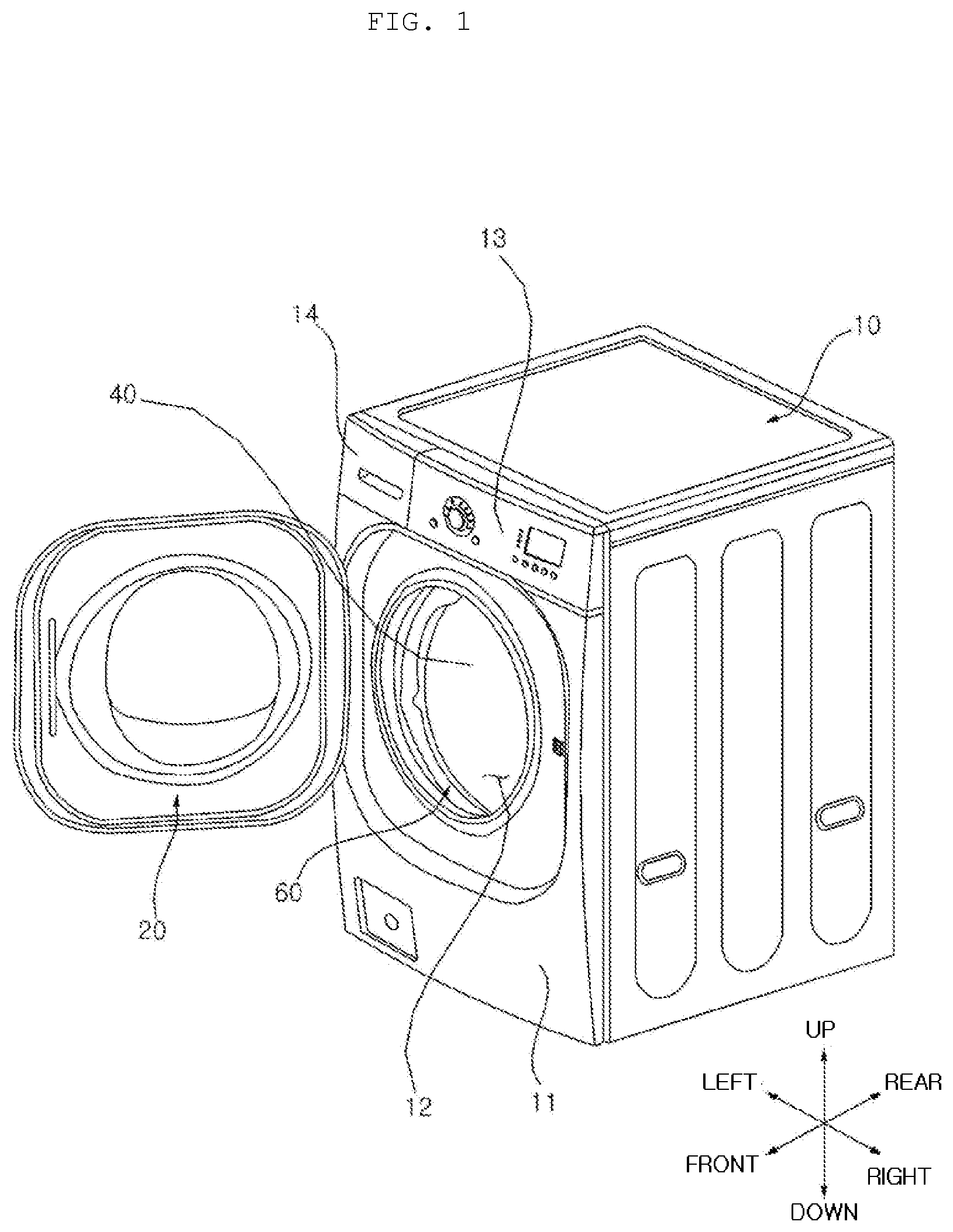
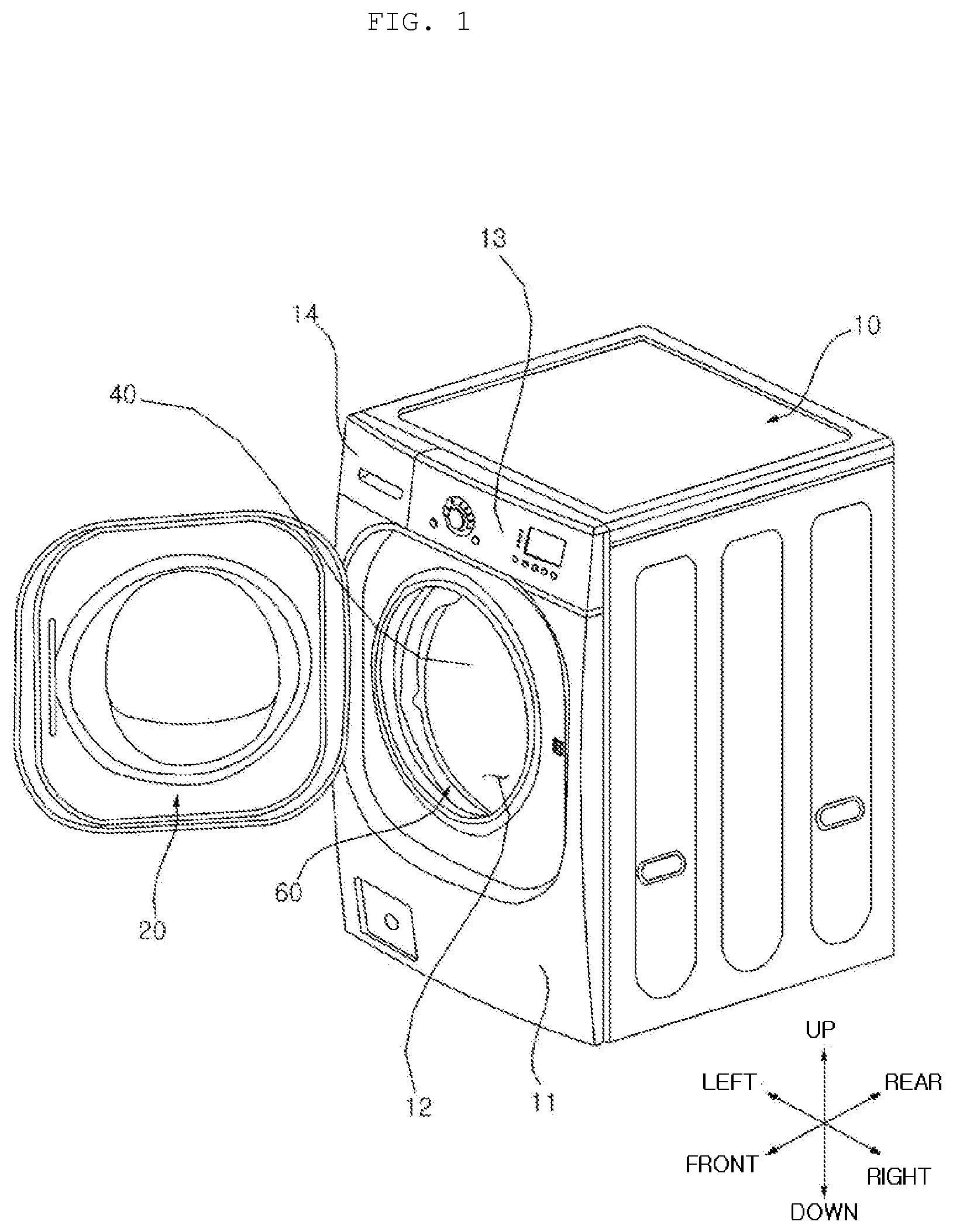

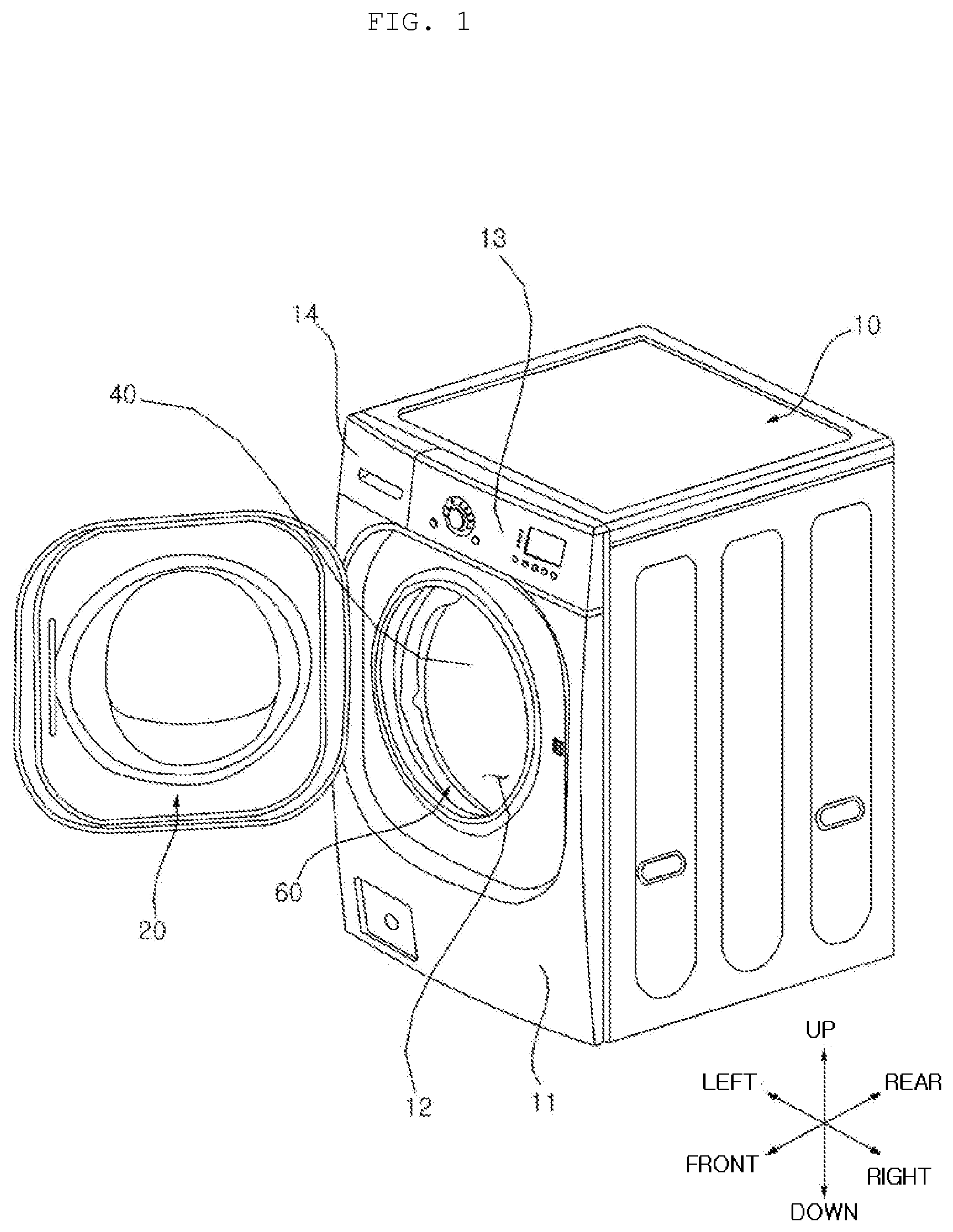