FASTENING MEMBER
The present disclosure relates to fastening members. Reduction in weight of fastening members, such as bolts and screws, as well as fastening structures with these fastening members has conventionally been attempted from various points of view, due to a demand for reduction in weight of components in the industrial field in general. Improvement in reliability and durability of the fastening members needs to be undertaken also, and the reduction in weight and the improvement in reliability and durability are both becoming necessary. With respect to the above described problems, a technique where a material combined of two types of alloys by cladding or the like is applied to bolts is becoming widespread. For example, a bolt having a base material formed of aluminum is described in Patent Literature 1, the base material having a surface covered by nickel. Patent Literature 1: Japanese Laid-open Patent Publication No. 11-210728 However, bolts, which are formed of a material combined of two types of alloys, such as a cladding material including aluminum, often still have problems remaining in their reliability and durability as fastening structures even if these bolts are able to be reduced in weight. That is, as these bolts are repeatedly used, loosening may occur. In view of the above, an object of the present invention is to: realize reduction in weight of fastening members; reduce occurrence of loosening; and improve reliability and durability of fastening structures of the fastening members. To solve the above-described problem, a fastening member according to the present invention includes a screw thread formed therein, wherein a portion including a crest portion of the screw thread is formed of a first alloy material and includes: a thick portion where the portion is maximized in thickness in a circumferential direction; and a thin portion where the portion is minimized in thickness in the circumferential direction, and a portion including a root of the screw thread is formed of a second alloy material having a tensile strength higher than that of the first alloy material. Moreover, according to another fastening member according to the present invention includes: a head portion; and a shaft portion including a screw thread formed therein, wherein the shaft portion includes a main body portion, and an outer peripheral portion provided radially outside the main body portion, the outer peripheral portion in the screw thread is formed of a first alloy material, and forms a portion including at least a crest portion of the screw thread, the main body portion in the screw thread is formed of a second alloy material having a tensile strength higher than that of the first alloy material, and forms a portion including a root of the screw thread, and the outer peripheral portion in the screw thread includes: a thick portion where the outer peripheral portion is maximized in thickness in a circumferential direction of the shaft portion; and a thin portion where the outer peripheral portion is minimized in thickness in the circumferential direction of the shaft portion. In the other fastening member according to the present invention, the thick portion and the thin portion are formed by the outer peripheral portion being eccentric with respect to the main body portion. In the other fastening member according to the present invention, the thick portion and the thin portion are opposite to each other across a central axis of the shaft portion. In the other fastening member according to the present invention, one or more of the screw threads are formed in a screw portion formed in an axial direction intermediate portion of the shaft portion, the screw thread extends one round about an axis of the shaft portion, and the thick portion and the thin portion are formed at least one each in the one round of the screw thread in the screw portion. In the other fastening member according to the present invention, the first alloy material is a 1000 series or 6000 series aluminum-based alloy according to the Japanese Industrial Standards, and the second alloy material is a 2000 series or 7000 series aluminum-based alloy according to the Japanese Industrial Standards. Another fastening member according to the present invention includes: a screw thread formed therein; a main body portion; and an inner peripheral portion provided radially inside the main body portion, wherein the inner peripheral portion in the screw thread is formed of a first alloy material, and forms a portion including at least a crest portion of the screw thread, the main body portion in the screw thread is formed of a second alloy material having a tensile strength higher than that of the first alloy material, and forms a part including a root of the screw thread, and the inner peripheral portion in the screw thread includes: a thick portion where the inner peripheral portion is maximized in thickness in a circumferential direction; and a thin portion where the inner peripheral portion is minimized in thickness in the circumferential direction. According to the present invention, a fastening member having excellent reliability and durability is able to be provided, while reduction in weight of the fastening member is realized. Hereinafter, embodiments of the present invention will be described while reference is made to the drawings. A cladding material of the first alloy material 1 Two types of alloys having the same element as their main component may be used as the first alloy material 1 A 1000 series or 6000 series aluminum-based alloy may be used as the first alloy material 1 A 2000 series or 7000 series aluminum-based alloy may be used as the second alloy material 1 Two types of alloys having different elements as their main components may be used as the first alloy material 1 The main body portion 12 exists at an inner peripheral side of the shaft portion 2, and an outer peripheral part thereof is covered by the outer peripheral portion 14. The outer peripheral portion 14 does not need to completely cover the main body portion 12, and as illustrated in The outer peripheral portion 14 being eccentric with respect to the main body portion 12 means that: a virtual central axis of the outer peripheral portion 14 and likewise a virtual central axis of the main body portion 12 are positionally shifted from each other in a sectional view along the central axis direction of the shaft portion 2, and do not coincide with each other. The screw threads 21 are formed of the main body portion 12, at a root side thereof. That is, the screw threads 21 are formed of the second alloy material 1 The screw threads 21 are formed of the main body portion 12, at a root side thereof. That is, the screw threads 21 are formed of the second alloy material 1 As described above, in the screw portion 22 of the fastening member 1, the outer peripheral portion 14 formed of the first alloy material 1 The maximum thickness portion (the thick portion 23) and the minimum thickness portion (the thin portion 24) that the outer peripheral portion 14 has are each not limited to a single location, and may each be plurally provided in a single screw thread 21. Furthermore, both the maximum thickness portion (the thick portion 23) and the minimum thickness portion (the thin portion 24) that the outer peripheral portion 14 has do not need to be provided in all of the screw threads 21 in the screw portion 22, and may be provided only in a part of the screw threads 21. Moreover, both the maximum thickness portion (the thick portion 23) and the minimum thickness portion (the thin portion 24) that the outer peripheral portion 14 has may be configured to be not present opposite to each other by 180°. Described below are functions and effects of the above described fastening member 1 according to the first embodiment of the present invention. When the fastening member 1 is fastened to a counterpart member, the screw threads 21 of the screw portion 22 are engaged with and fastened to the counterpart member. The thick portion 23 has a larger portion made of the first alloy material 1 Furthermore, because the shaft portion 2 of the fastening member 1 has the outer peripheral portion 14 formed of the first alloy material 1 Furthermore, since the thick portion 23 and the thin portion 24 are formed, with the outer peripheral portion 14 being formed eccentrically with respect to the central axis of the shaft portion 2; the fastening member 1 is able to be manufactured more easily. Furthermore, because the thick portion 23 and the thin portion 24 are positioned in regions opposite to each other about the central axis of the shaft portion 2 (in portions opposite to each other by about 180 degrees), inclined load on the central axis is able to be generated effectively, and firmer fastening is able to be realized. Furthermore, since the 1000 series or 6000 series aluminum-based alloy serving as the first alloy material 1 Described below are specific examples of a configuration of the above described fastening member 1. A first example, a second example, and a conventional example all described below were manufactured as specific configuration examples. The fastening member 1 (bolt) according to this example was manufactured by: forming the screw portion 22 through a rolling process after a header process and a heat treatment process both on a rod-shaped cladding material formed by using A2618 according to the Japanese Industrial Standards in the main body portion 12 of the shaft portion 2 and covering the outer peripheral part of the main body portion 12 with A6063 according to the Japanese Industrial Standards. Its bolts size was M8×50. The fastening member 1 (bolt) according to this example was manufactured similarly to that according to the first example, except that the thickness of the outer peripheral portion of the cladding material was changed. A fastening member (bolt) according to the conventional example was manufactured similarly to that according to the first example, except that only an A2618 material according to the Japanese Industrial Standards was used in formation of the shaft portion 2 and head portion 3. Described hereinafter is a fastening member according to a second embodiment. Any portion serving as a component in common with the fastening member 1 according to the first embodiment will be assigned with the same reference sign, and description thereof will be omitted. As illustrated in The screw threads 21 are formed of the main body portion 12, at the root side thereof. That is, since there are convex portions at the outer periphery of the main body portion, a part of the screw threads 21 at the root side is formed of the second alloy material 1 The screw threads 21 are formed of the main body portion 12, at the root side thereof. That is, the screw threads 21 are formed of the second alloy material 1 As described above, in the screw portion 22 of the fastening member 1, the outer peripheral portion 14 formed of the first alloy material 1 The maximum thickness portion (the thick portion 23) that the outer peripheral portion 14 has is not limited to a single location, and may be plurally provided in a single screw thread 21. Furthermore, both the maximum thickness portion (the thick portion 23) and the minimum thickness portion (the thin portion 24) that the outer peripheral portion 14 has do not need to be provided in all of the screw threads 21 in the screw portion 22, and may be provided only in a part of the screw threads 21. Described hereinafter is a fastening member according to a third embodiment. Any portion in common with the fastening member 1 according to the first embodiment or second embodiment will be assigned with the same reference sign, and description thereof will be omitted. The fastening member 101 is formed of a first alloy material 11 The main body portion 102 is present at an outer peripheral side of the fastening member 101, and the inner peripheral portion, 104 covers the inner surface in the hole formed in the central portion thereof. Both crest portions 201 The inner peripheral portion 104 (the first alloy material 11 Embodiments of the present invention have been described thus far, but the present invention is not limited to these embodiments, and may be implemented in various modes, without departing from the gist of the present invention. For example, the fastening member may be a male screw other than a bolt, such as a machine screw or a tapping screw. The present invention may thus include various embodiments and the like not described herein, and various design changes and the like may be made without departing from the technical ideas determined by the claims. As described above, a fastening member according to the present invention is suitable for: realization of reduction in weight of the fastening member; reduction of occurrence of loosening; and improvement of reliability and durability of a fastening structure of the fastening member. 1, 101 FASTENING MEMBER 1 1 12, 102 MAIN BODY PORTION 14 OUTER PERIPHERAL PORTION 104 INNER PERIPHERAL PORTION 2 SHAFT PORTION 3 HEAD PORTION 21, 201 SCREW THREAD 21 21 22, 202 SCREW PORTION 23, 203 THICK PORTION 24, 204 THIN PORTION A fastening member includes a screw thread formed therein. A portion including a crest portion of the screw thread is formed of a first alloy material and includes: a thick portion where the portion is maximized in thickness in a circumferential direction; and a thin portion where the portion is minimized in thickness in the circumferential direction. A portion including a root of the screw thread is formed of a second alloy material having a tensile strength higher than that of the first alloy material. 1. A fastening member comprising a screw thread formed therein, wherein
a portion including a crest portion of the screw thread is formed of a first alloy material and includes: a thick portion where the portion is maximized in thickness in a circumferential direction; and a thin portion where the portion is minimized in thickness in the circumferential direction, and a portion including a root of the screw thread is formed of a second alloy material having a tensile strength higher than that of the first alloy material. 2. A fastening member comprising:
a head portion; and a shaft portion including a screw thread formed therein, wherein the shaft portion includes a main body portion, and an outer peripheral portion provided radially outside the main body portion, the outer peripheral portion in the screw thread is formed of a first alloy material, and forms a portion including at least a crest portion of the screw thread, the main body portion in the screw thread is formed of a second alloy material having a tensile strength higher than that of the first alloy material, and forms a portion including a root of the screw thread, and the outer peripheral portion in the screw thread includes: a thick portion where the outer peripheral portion is maximized in thickness in a circumferential direction of the shaft portion; and a thin portion where the outer peripheral portion is minimized in thickness in the circumferential direction of the shaft portion. 3. The fastening member according to 4. The fastening member according to 5. The fastening member according to one or more of the screw threads are formed in a screw portion formed in an axial direction intermediate portion of the shaft portion, the screw thread extends one round about an axis of the shaft portion, and the thick portion and the thin portion are formed at least one each in the one round of the screw thread in the screw portion. 6. The fastening member according to 7. A fastening member comprising:
a screw thread formed therein; a main body portion; and an inner peripheral portion provided radially inside the main body portion, wherein the inner peripheral portion in the screw thread is formed of a first alloy material, and forms a portion including at least a crest portion of the screw thread, the main body portion in the screw thread is formed of a second alloy material having a tensile strength higher than that of the first alloy material, and forms a part including a root of the screw thread, and the inner peripheral portion in the screw thread includes: a thick portion where the inner peripheral portion is maximized in thickness in a circumferential direction; and a thin portion where the inner peripheral portion is minimized in thickness in the circumferential direction.BACKGROUND
CITATION LIST
Patent Literature
SUMMARY
Technical Problem
Solution to Problem
Advantageous Effects of Invention
BRIEF DESCRIPTION OF DRAWINGS
DESCRIPTION OF EMBODIMENTS
First Embodiment
FIRST EXAMPLE
SECOND EXAMPLE
CONVENTIONAL EXAMPLE
Second Embodiment
Third Embodiment
INDUSTRIAL APPLICABILITY
REFERENCE SIGNS LIST
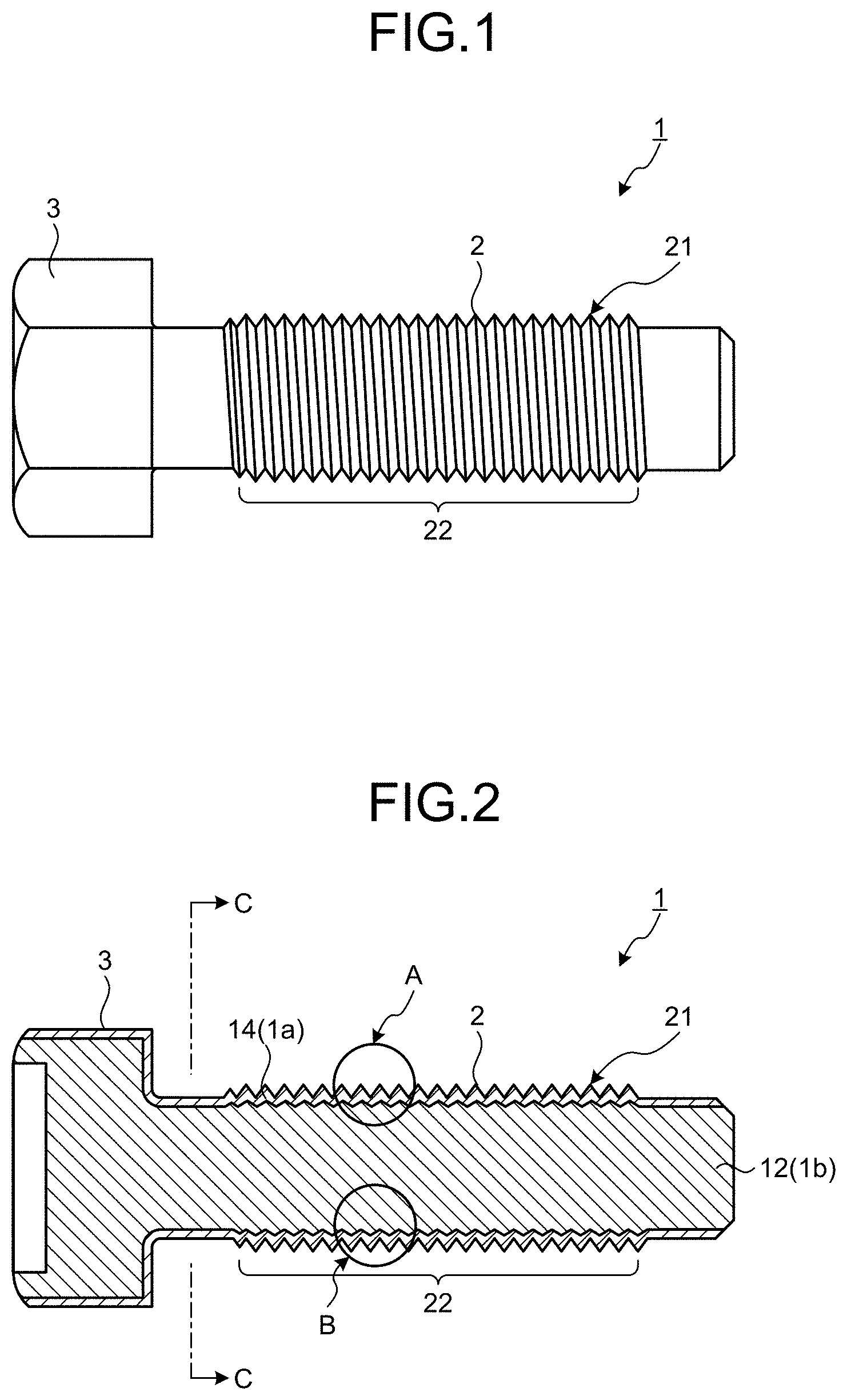
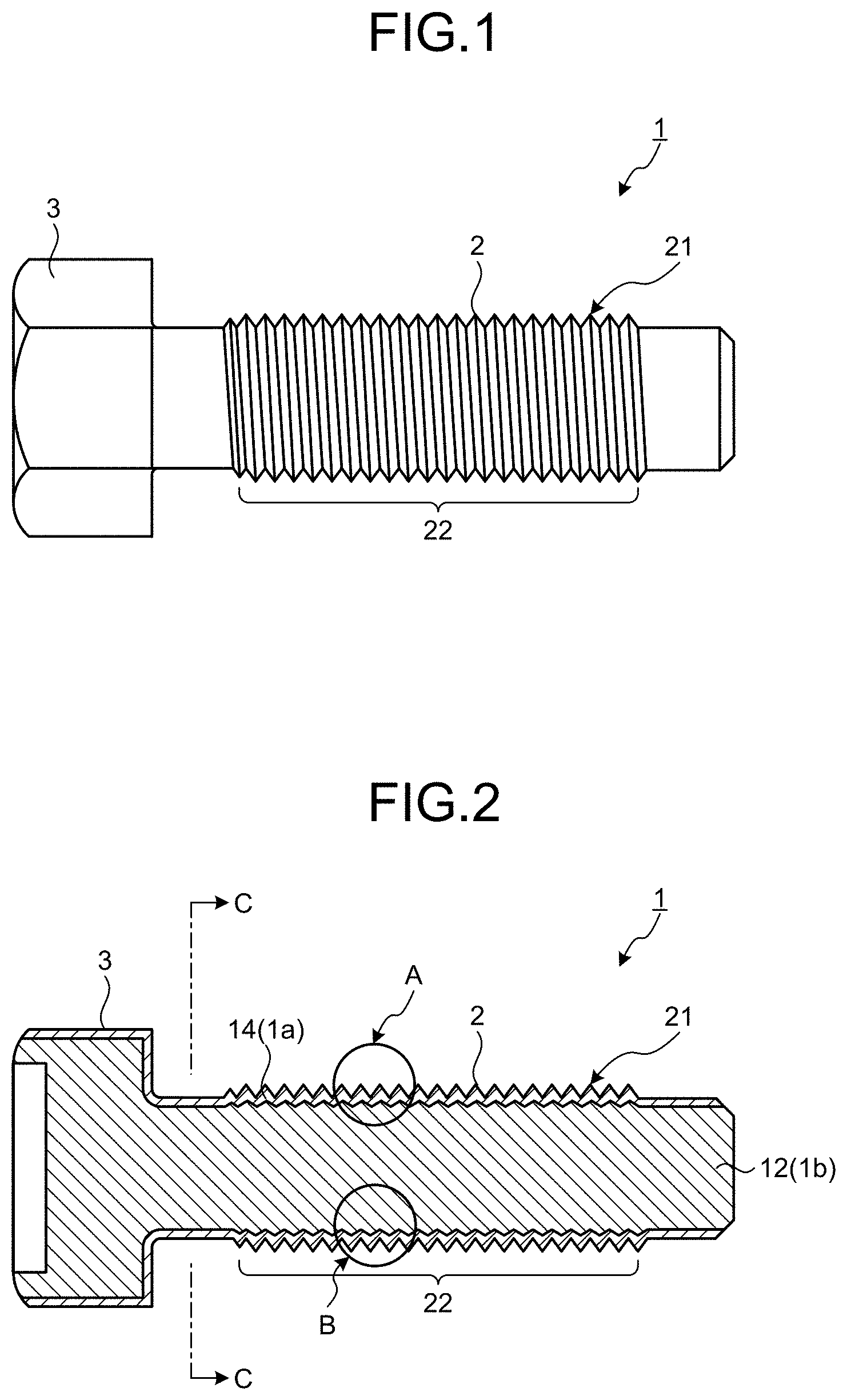
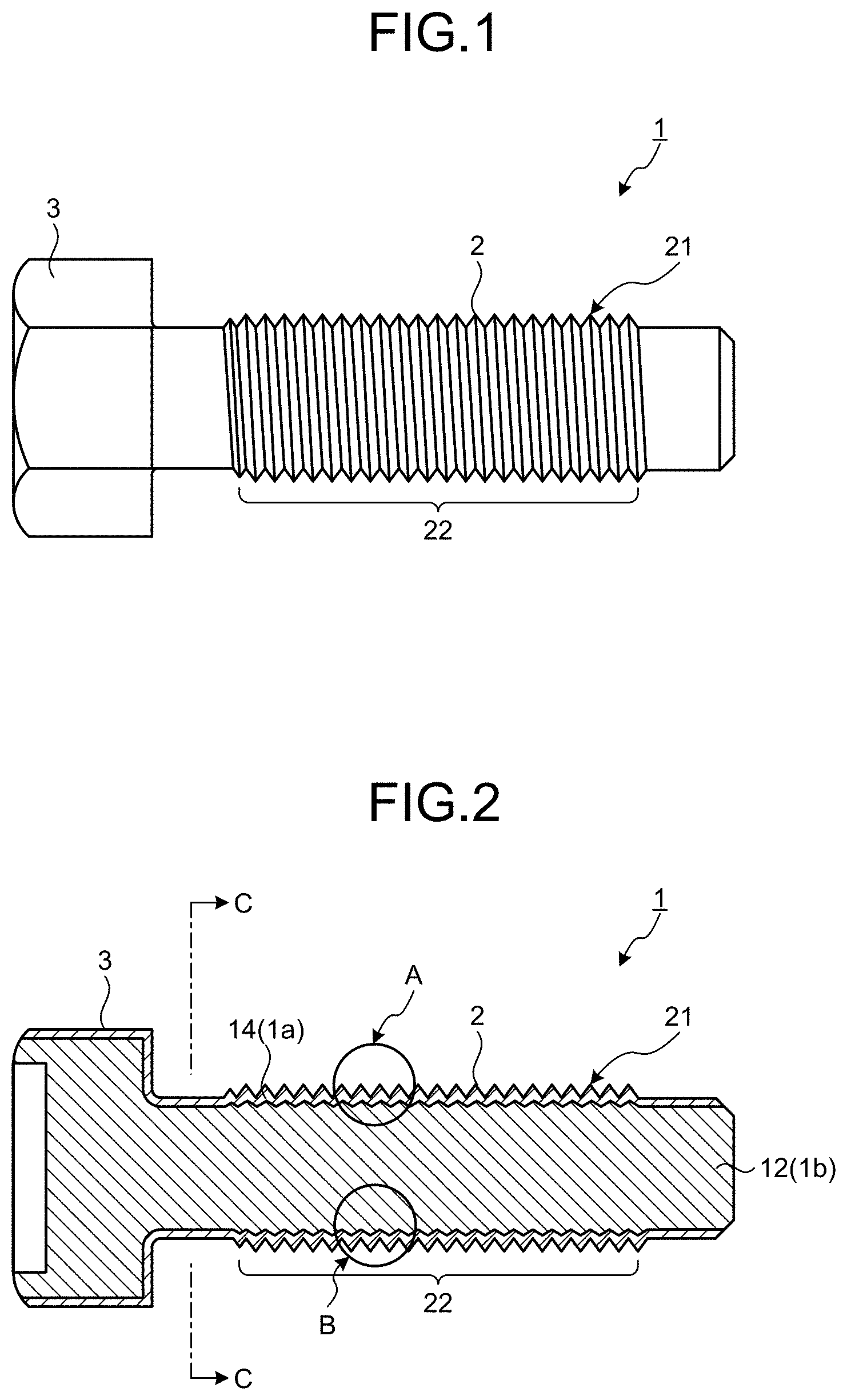
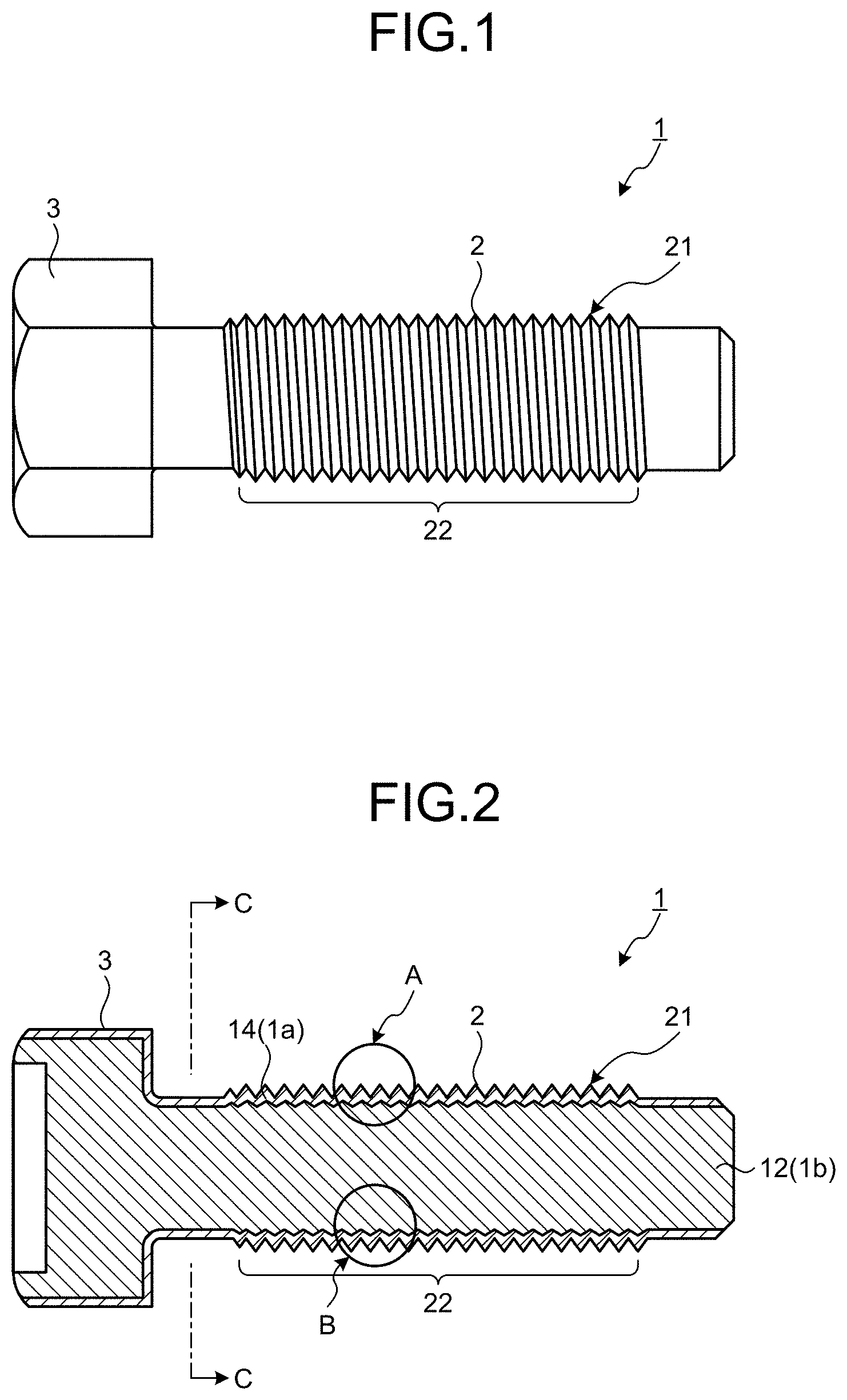
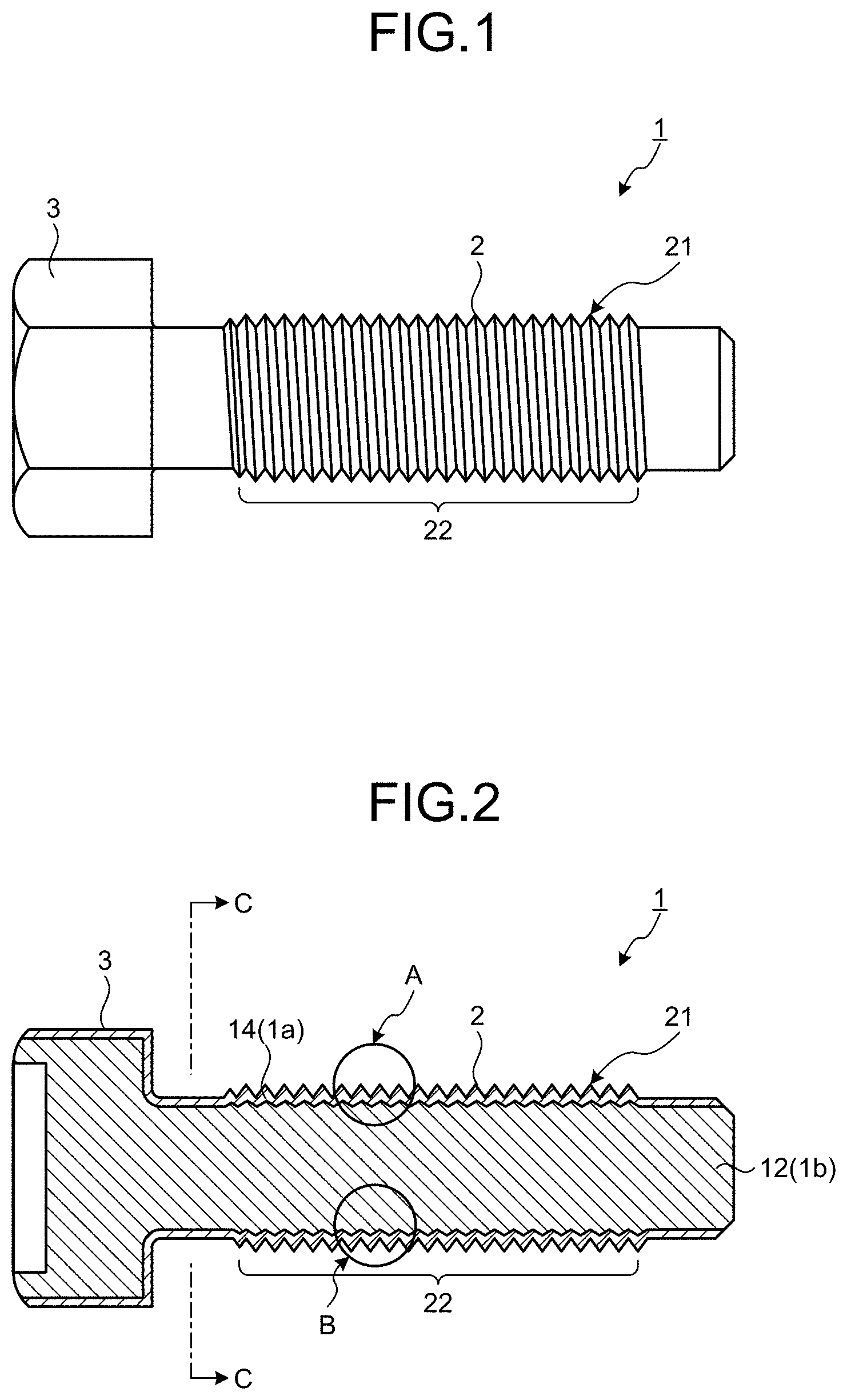
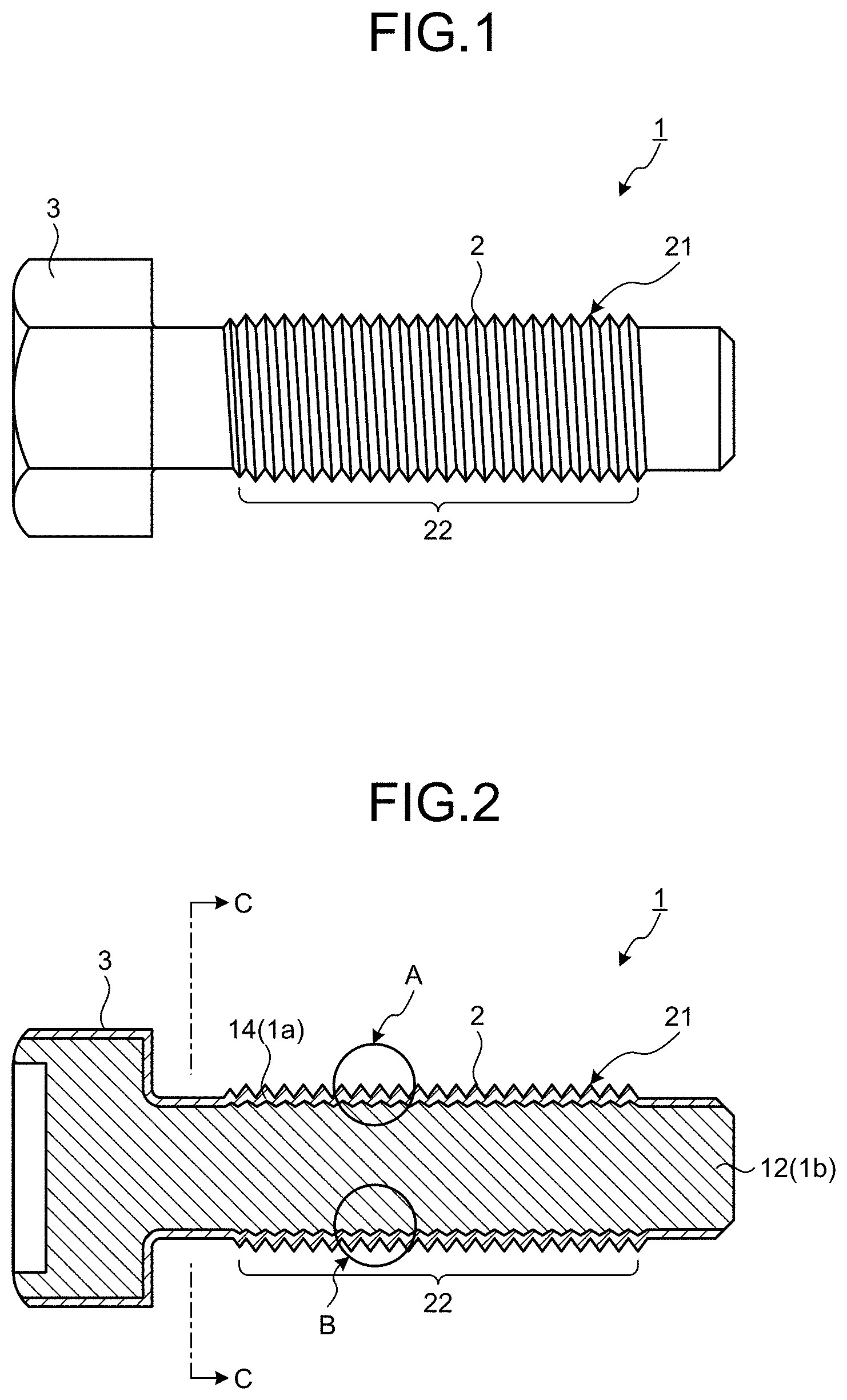