NITRIC OXIDE GENERATION PROCESS CONTROLS
This application claims the benefit of and priority to U.S. Provisional Application No. 63/093,040 filed Oct. 16, 2020, and the contents of which is hereby incorporated herein by reference in its entirety. The present disclosure relates to systems and methods for generating and delivering nitric oxide for use with various ventilation devices, and more particularly to nitric oxide generation process controls. Nitric oxide (NO) has been found to be useful in a number of ways for treatment of disease, particularly cardiac and respiratory ailments. Previous systems for producing NO and delivering the NO gas to a patient have a number of disadvantages. For example, tank-based systems required large tanks of NO gas at a high concentration and are required to purge with NO when treatment is resumed. Synthesizing NO from NO2or N2O4requires the handling of toxic chemicals. Prior electric generation systems involve generating plasma in the main flow of air to be delivered to patients or pumped through a delivery tube. The present disclosure relates to systems and methods for generating and/or delivering nitric oxide. In some aspects, the present disclosure provides a system for generating nitric oxide that comprises a plasma chamber housing two or more electrodes in communication with a resonant high voltage circuit configured to send a signal to the plasma chamber for generating nitric oxide in a product gas from a flow of a reactant gas, and a controller configured to generate a pulse width modulation signal having multiple harmonic frequencies to excite the resonant high voltage circuit. The controller is configured to adjust the duty cycle of the pulse width modulation signal, the controller selecting the duty cycle based on a target voltage before plasma formation and a target current after plasma formation in the plasma chamber. In some embodiments, the voltage before plasma formation and the current after plasma formation are independently controlled by varying harmonic amplitudes in the pulse width modulation signal. In some embodiments, the harmonic amplitudes are varied by alternating between two or more duty cycles of the pulse width modulation signal. In some embodiments, control of the current after plasma formation allows for current modulation within a plasma pulse. In some embodiments, the controller is configured to pulse modulate the plasma to control the NO production rate. In some embodiments, the controller is configured to adjust a concentration of nitric oxide in the product gas. In some embodiments, the controller is configured to facilitate breakdown in an electrode gap in the plasma chamber. In some embodiments, the controller is configured to optimize a ratio between NO and NO2in the product gas. In some embodiments, the controller is configured to compensate for changes to an electrode in the plasma chamber, such as electrode wear. In some embodiments, the controller is configured to compensate for reactant properties in the system, including at least one of humidity, oxygen/nitrogen ratio, temperature and pressure. A system is provided for generating nitric oxide that comprises a plasma chamber housing two or more electrodes in communication with a resonant high voltage circuit configured to send a signal to the plasma chamber for generating nitric oxide in a product gas from a flow of a reactant gas, and a controller in communication with the resonant high voltage circuit for independently controlling a voltage to form a plasma in the plasma chamber and a current in a plasma in the plasma chamber by alternating between two or more duty cycles to independently adjust the amplitudes of the waveform's harmonic frequencies. In some embodiments, the controller is configured to adjust a concentration of nitric oxide in the product gas. In some embodiments, the controller is configured to facilitate breakdown in an electrode gap in the plasma chamber. In some embodiments, the controller is configured to optimize a ratio between NO and NO2in the product gas. In some embodiments, the controller is configured to compensate for changes to an electrode in the plasma chamber, such as electrode wear. In some embodiments, the controller is configured to compensate for reactant properties in the system, including at least one of humidity, oxygen/nitrogen ratio, and pressure. A method for generating nitric oxide is provided that comprising energizing a plasma chamber using a resonant high voltage circuit to generate nitric oxide in a product gas from a flow of a reactant gas, and controlling, using a controller in communication with the resonant high voltage circuit, a voltage that forms a plasma in the plasma chamber and a current that sustains a plasma in the plasma chamber by adjusting a duty cycle of a waveform used to excite the resonant high voltage circuit using multiple harmonic frequencies. In some embodiments, the voltage before plasma formation and the current after plasma formation are independently controlled by varying the harmonic amplitudes in the pulse width modulation signal. The present disclosure is further described in the detailed description which follows, in reference to the noted plurality of drawings by way of non-limiting examples of exemplary embodiments, in which like reference numerals represent similar parts throughout the several views of the drawings, and wherein: While the above-identified drawings set forth presently disclosed embodiments, other embodiments are also contemplated, as noted in the discussion. This disclosure presents illustrative embodiments by way of representation and not limitation. Numerous other modifications and embodiments can be devised by those skilled in the art which fall within the scope and spirit of the principles of the presently disclosed embodiments. The following description provides exemplary embodiments only, and is not intended to limit the scope, applicability, or configuration of the disclosure. Rather, the following description of the exemplary embodiments will provide those skilled in the art with an enabling description for implementing one or more exemplary embodiments. It will be understood that various changes may be made in the function and arrangement of elements without departing from the spirit and scope of the presently disclosed embodiments. Specific details are given in the following description to provide a thorough understanding of the embodiments. However, it will be understood by one of ordinary skill in the art that the embodiments may be practiced without these specific details. For example, systems, processes, and other elements in the presently disclosed embodiments may be shown as components in block diagram form in order not to obscure the embodiments in unnecessary detail. In other instances, well-known processes, structures, and techniques may be shown without unnecessary detail in order to avoid obscuring the embodiments. Also, it is noted that individual embodiments may be described as a process which is depicted as a flowchart, a flow diagram, a data flow diagram, a structure diagram, or a block diagram. Although a flowchart may describe the operations as a sequential process, many of the operations can be performed in parallel or concurrently. In addition, the order of the operations may be re-arranged. A process may be terminated when its operations are completed, but could have additional steps not discussed or included in a figure. Furthermore, not all operations in any particularly described process may occur in all embodiments. A process may correspond to a method, a function, a procedure, a subroutine, a subprogram, etc. When a process corresponds to a function, its termination corresponds to a return of the function to the calling function or the main function. Subject matter will now be described more fully with reference to the accompanying drawings, which form a part hereof, and which show, by way of illustration, specific example aspects and embodiments of the present disclosure. Subject matter may, however, be embodied in a variety of different forms and, therefore, covered or claimed subject matter is intended to be construed as not being limited to any example embodiments set forth herein; example embodiments are provided merely to be illustrative. The following detailed description is, therefore, not intended to be taken in a limiting sense. In general, terminology may be understood at least in part from usage in context. For example, terms, such as “and”, “or”, or “and/or,” as used herein may include a variety of meanings that may depend at least in part upon the context in which such terms are used. Typically, “or” if used to associate a list, such as A, B, or C, is intended to mean A, B, and C, here used in the inclusive sense, as well as A, B, or C, here used in the exclusive sense. In addition, the term “one or more” as used herein, depending at least in part upon context, may be used to describe any feature, structure, or characteristic in a singular sense or may be used to describe combinations of features, structures or characteristics in a plural sense. Similarly, terms, such as “a,” “an,” or “the,” again, may be understood to convey a singular usage or to convey a plural usage, depending at least in part upon context. In addition, the term “based on” may be understood as not necessarily intended to convey an exclusive set of factors and may, instead, allow for existence of additional factors not necessarily expressly described, again, depending at least in part on context. The present disclosure relates to systems and methods of nitric oxide (NO) delivery for use in various applications, for example, inside a hospital room, in an emergency room, in a doctor's office, in a clinic, and outside a hospital setting as a portable or ambulatory device or gas source during patient transport. An NO generation and/or delivery system can take many forms, including but not limited to a device configured to work with an existing medical device that utilizes a product gas, a stand-alone (ambulatory) device, a module that can be integrated with an existing medical device, one or more types of cartridges that can perform various functions of the NO system, a compact NO inhaler, and an electronic NO tank. The NO generation system uses a reactant gas containing a mixture of at least oxygen and nitrogen, including but not limited to ambient air, and an electrical discharge (plasma) to produce a product gas that is enriched with NO. An NO generation device can be used with any device that can utilize NO, including but not limited to a ventilator, an anesthesia device, a defibrillator, a ventricular assist device (VAD), a Continuous Positive Airway Pressure (CPAP) machine, a Bilevel Positive Airway Pressure (BiPAP) machine, a non-invasive positive pressure ventilator (NIPPV), a nasal cannula application, a nebulizer, an extracorporeal membrane oxygenation (ECMO), a bypass system, an automated CPR system, an oxygen delivery system, an oxygen concentrator, an oxygen generation system, and an automated external defibrillator AED, MRI, and a patient monitor. In addition, the destination for nitric oxide produced can be any type of delivery device associated with any medical device, including but not limited to a nasal cannula, a manual ventilation device, a face mask, inhaler, or any other delivery circuit. The NO generation capabilities can be integrated into any of these devices, or the devices can be used with a NO generation device as described herein. The present disclosure includes ideas in the areas of NO generation and NO delivery. It should be noted that NO delivery concepts can be applicable to NO delivered from a multitude of sources, including NO tanks, electrically-generated NO and chemically-derived NO. NO therapy involves delivering known quantities of NO to a patient. Doses for NO therapy can be prescribed in terms of inhaled concentration (e.g. ppm) or a number of moles of NO per unit time (e.g. mg/hr). When prescribed as concentration, the intention is for the inspiratory gas to be a homogeneous mixture of NO and other gases so that the lung is filled with a consistent concentration of NO throughout. Gas containing NO within a NO generator is referred to as “product gas.” Some NO devices generate NO from a reactant gas containing nitrogen and oxygen, while other devices derive NO from solid and/or liquid reagents. NO rapidly oxidizes into NO2in the presence of oxygen and therefore cannot be stored for long periods of time without significant loss. This chemistry fact is an issue whenever NO coexists with oxygen, regardless of how the NO was generated, be it by electrical discharge, RF heating, or chemical derivation. This rapid conversion of NO to NO2in the presence of oxygen presents a challenge since NO must be transported from its place of generation, through a pathway within the NO device to a pneumatic conduit carrying inspiratory gas. NO can be lost to oxidation within the pathway, surface materials within the pathway and scrubbing materials within the pathway. A constant inhaled concentration of NO can be achieved by introducing the correct number of NO molecules to the inspiratory flow. In some embodiments, this is achieved in a constant inspiratory flow by delivering the appropriate concentration of product gas to the inspiratory flow at a constant flow rate. Achieving a constant inhaled concentration in a variable inspiratory flow can be challenging, however. One approach is to deliver product gas at a constant flow rate and vary the concentration of the product gas so that an appropriate number of moles of NO are added to the inspiratory flow at each flow level. It is challenging to maintain the correct concentration of NO at the injector at all times with this approach since there is transit time, diffusion, surface losses and scrubber losses taking place as the product gas is transferred from the location of generation to the injector. Flow restrictive components within the product gas pathway (e.g., scrubbers and filters) introduce a time lag which can limit the level of inspiratory flow variability that a NO generation system can accurately dose. The transit time between the location of generation and the injector further requires the production rate to be predictive, making variable concentration/constant flow solutions unsuitable for inspiratory flows that are not periodic. Another approach to dosing a variable inspiratory flow is to generate constant concentration product gas that is injected at variable flow rates. To achieve constant inspiratory flow concentration, the NO gas is injected at a flow rate that is directly proportional to inspiratory flow. The ratio of injected flow to inspiratory flow is referred to as the “dilution ratio.” NO production rate is defined as the mathematical product of NO concentration in ppm and the gas mass flow rate in (slpm), and can be measured in units of ppm·slpm, or abbreviated as ppm·lpm. Although it is fairly simple to create an electrical discharge in a gas, it is incredibly challenging to generate known quantities of NO using this method. NO production is dependent on a multitude of factors, including but not limited to the level of plasma activity, the flow rate of reactant gas and environmental factors (pressure, temperature, and humidity). Once formed, the rate of loss of NO is dependent on the residence time, pressure, temperature, scrubber, and other factors. The fewer variables present in an NO generation process, the greater the ability to control NO production to accurate levels. For example, the risk of humidity effects on NO generation can be eliminated by using dry reactant gas. The risk of reactant gas flow rate effects on NO generation can be eliminated by operating at a fixed reactant gas flow rate. In some embodiments, NO is delivered into an inspiratory limb gas flow, thereby diluting the inspiratory gas and adding volume/pressure to that flow. When NO-containing gas is added to a ventilator circuit, for example, the additional volume of gas can increase the pressure at the patient, interfere with ventilator operation and dilute medicinal gases in the ventilator circuit (e.g., O2). For this reason, it can be beneficial to dilute an inspiratory gas flow as little as possible. Higher concentrations of NO enable lower levels of dilution but can increase the loss of NO to oxidation, making it more difficult to know the concentration of NO injected. Higher concentrations of NO within the system can also result in higher NO2levels pre-injector. In embodiments where constant concentration is delivered at variable mass flow rates, and where NO is produced on-demand, the production rate of NO is matched to the mass flow rate being injected. This results in the NO production rate bandwidth requirements being close to the flow control bandwidth requirements. Most NO sensing technologies, particularly the small, inexpensive ones suitable for integration into portable devices, have insufficient bandwidth and insufficient response time to support closed-loop regulation of the NO production rate. A high-bandwidth NO generation device must therefore utilize accurate, open-loop process controls to obtain the required bandwidth. In some embodiments, high bandwidth open-loop controls are combined with low-bandwidth closed loop controls to improve overall accuracy. An open-loop process controller accounts for process variables by either controlling them directly (independent variables) or adjusting the operating point of the plant to correct for them (dependent variables). In a NO generation device, process variables include, but are not limited to, plasma parameters (e.g., intensity, duty cycle, etc.), reactant gas flow rate, reactant gas pressure, temperature, and humidity. In some embodiments, the bandwidth requirements of the NO production rate may be reduced by diverting excess NO to a waste path. In some embodiments the bandwidth requirements may be reduced by temporarily storing product gas in a reservoir. In this document, references to flow are inclusive of mass flow. In many embodiments, NO is added to an inspiratory flow. The inspiratory flow can be within the inspiratory limb of a ventilator, within an inhaler, or other device delivering gas to a patient. In some embodiments, NO is delivered though a delivery device and introduced to an inspiratory flow at the patient (e.g., a nasal prong delivering flow directly to the patient's nose). Discharge plasmas can be DC or AC. In some embodiments, the reactant gas flow makes the plasma arc increase beyond the length of the electrode gap. NO production for a given electrode spacing is maximized by stretching the arc with reactant gas flow. In some embodiments, plasma is generated with radio frequency energy (e.g., RF heating, microwave). In some embodiments, NO generation can be modulated by adjusting one or more of the following parameters: RF Frequency, wave guide spacing, antenna location, flow, pressure, temperature, etc. as variables in production. In some embodiments, the plasma generator circuit is a radio frequency (RF) power generator delivering RF power to one or more RF antennas. In some embodiments, the RF power operates around 13.56 MHz with power in the 50-100 W range, however other power ranges can be effective depending on antenna design, production targets and reactant gas conditions. In some embodiments, RF power operates around 2.45 GHz for improved coupling and excitation of N2molecules with peak power up to 100 W. In another embodiment, the system operates at roughly 2.5 GHz and less than 4 W to generate up to 500 ppm·lpm. In some embodiments, the range of possible RF frequencies that can be utilized to generate NO is 30 kHz to 300 GHz. In some embodiments, the NO system pneumatic path includes a pump pushing air through a manifold 36. In some embodiments, the manifold is configured with one or more valves: three-way valves, binary valves, check valves, and/or proportional orifices. The treatment controller 30 controls the flow of the pump, the power in the plasma and the direction of the gas flow post-electrical discharge. By configuring valves, the treatment controller can direct gas to the manual respiration pathway, the ventilator pathway or the gas sensor chamber for direct measurement of NO, NO2and O2levels in the product gas. In some embodiments, respiratory gas (i.e. the treatment flow) can be directed through a ventilator cartridge that measures the flow of the respiratory gas and can merge the respiratory gas with NO product gas. The output from the NO generation system in the form of the product gas 32 enriched with the NO produced in the plasma chamber 22 can either be directed to a respiratory or other (e.g. external applicator) device for delivery to a patient, or can be directed to a plurality of components provided for self-test or calibration of the NO generation system. In some embodiments, the system collects gases to sample in two ways: 1) gases are collected from a patient inspiratory circuit near the patient and pass through a sample line 48, a filter 50, and a water trap 52, or 2) gases are shunted directly from the pneumatic circuit as they exit the plasma chamber 22. In some embodiments, product gases are shunted with a shunt valve 44 to the gas sensors after being scrubbed but before dilution into a patient airstream. In some embodiments (not shown), shunted product gas is diluted to reduce the concentration before delivery to gas sensors. In some embodiments, product gases are collected from an inspiratory air stream near the device and/or within the device post-dilution. Within the gas analysis portion of the device, the product gas passes through one or more sensors to measure one or more of temperature, humidity, concentrations, pressure, and flow rate of various gasses therein. AC Waveform Control In some embodiments, the modulation of current and voltage in a plasma can be achieved by manipulating harmonics of an AC waveform. This is particularly valuable in plasma generation because the electrical load of the plasma changes between before and after electrical breakdown and during plasma generation, which may cause changes in the operating mode of a resonant circuit. In the case of a gliding arc electrode, the load also changes as the arc glides down the electrode with increases in the gap. Compensation from warm-up in a plasma generation system can also be accomplished with these techniques by varying plasma current. In some embodiments, current can be modulated as a function of duty cycle. In some embodiments, short duty cycle events have lower current than long duty cycle events. This can provide a broader range of production for an NO system. In some embodiments, the electrical current within the plasma is ramped as a function of elapsed time. The elapsed time can be relative to the time voltage was set high or from the time of plasma formation (e.g. electrical breakdown between electrodes). This approach enables a broad range of NO production with added resolution, as needed. In some embodiments, current modulation is utilized with a variable gap electrode (gliding arc, gliding torch, etc.). By varying the current as a function of time, plasma current is effectively mapped to specific locations on the electrode with specific electrode gap, owing to the fact that the arc moves along the electrodes in a predictable manner based on the reactant gas velocity through the plasma chamber. In some embodiments, at the time of electrical discharge, the current is kept low to enable low production values and minimize the power within the plasma at the short electrical gap. The arc travels along the electrodes at a velocity dictated by the reactant gas velocity. Design attention to the interplay between electrode geometry, reactant gas velocity and intra pulse current modulation can enable fine production resolution, where needed, while still supporting a wide range of production values. In some embodiments, the plasma power can be minimized when the arc is in the short gap thereby minimizing electrode temperature and wear in the short gap region. Given the interplay between reactant gas velocity, plasma current and electrode geometry, there are multiple combinations that can achieve the same production output for a discharge duration. In some embodiments, a gliding arc electrode has straight edges (linear increase in gap over time for a constant velocity) and intra pulse current is varied as a second order polynomial in time. In some embodiments, a gliding arc electrode has curved edges (non-linear increase in gap over time for a constant velocity), and intra pulse current is varied linearly in time. These two examples could have equivalent NO production and serve only as examples of the way electrode gap and current can be designed and controlled. In some embodiments, straight-edged electrodes are preferred for their manufacturability. Breakdown happens within a few usec of high voltage being applied to the electrodes. Current ramp rate can be influenced by how much gliding occurs (for example, as it relates to flow rate, electrode geometry, etc.). Pulse Parameter Measurement Circuit (PPMC) In some embodiments, a NO generation system includes features within the high voltage circuit to measure current, voltage and/or power within the plasma. This feature can provide insights into the electrical discharge activity and health of a NO generator system. In some embodiments, plasma power is measured and utilized as an indicator for NO production. It will be understood by those skilled in the art that there is a direct correlation between the plasma power and the concentration level produced by the NO generator system. In some embodiments, a NO generator alters plasma activity in response to increases/decreases in plasma power with respect to expected levels. For example, if plasma power is measured to be lower than expected, plasma power can be increased and or prolonged (e.g., a duty cycle increase) to make up for lost NO production. In some embodiments, if electrical break-down is detected to be delayed, the plasma pulse can be prolonged to compensate for lost production from the delay. In some embodiments, plasma voltage, current and/or power measurements are utilized to inform the NO generator system about the condition of electrodes. For example, a system can detect whether or not arcing occurs at all or whether it is delayed. In another embodiment, a mechanical sensor may be used to detect the presence or absence of electrical discharges. An example of a mechanical sensor is a sound measuring device located either in fluid communication with the plasma chamber or outside the plasma chamber that detects changes in sound pressure. The sound measuring device is able to sense that electrical discharges are occurring. In some embodiments, the mechanical sensor is an accelerometer that detects motions associated with the electrical discharge and pressure wave. In another embodiment, an electrical sensor is used to detect the presence or absence of electrical discharges. In some embodiments, the electrical discharges are detected with an antenna that receives an EMF signal generated by the arc. In some embodiments, a temperature sensing device may be used to detect the presence or absence of electrical discharges. The temperature sensing device measures levels within the plasma chamber or outside the plasma chamber that are indicative of heat generated as arcing occurs. Decreases in electrode activity could indicate a worn, contaminated, or defective electrode or electrical creepage along the surfaces of the plasma chamber (internal or external). A worn electrode (larger gap) can be detected by detecting higher voltage required to breakdown at the gap, and/or an increase in time from pulse initiation to electrical breakdown. A NO generation system can respond by applying additional voltage/power/current to compensate and/or alert the user that device service is required or switch the device to a secondary back-up NO generation system. In some embodiments, one or more of the following parameters is determined by the plasma electrical monitoring feature: breakdown voltage, max breakdown voltage, min breakdown voltage, time to breakdown, maximum plasma current, max plasma voltage, minimum plasma voltage, RMS power per cycle, number of pulses in plasma cycle, duration of plasma cycle, and number of missed or misidentified waveforms. It should be noted that maximum and minimum values can be determined for the positive half of the waveform and the negative half of the waveform. This level of information on each and every electrical discharge can provide a profound understanding of the actual NO concentration production occurring and health of a system. In turn, a system can utilize this information to optimize plasma control and/or adjustment parameters to deliver accurate levels of NO. Plasma electrical monitoring also benefits fault detection. For example, a NO generation system can detect one or more of the following: electrical creepage (rather than arcing) between electrodes within the chamber, arcing/creepage outside of the plasma chamber, conditions that could generate/alter EMI emissions, arcing to other components within the device (e.g. the enclosure or low voltage circuitry), an inability to generate NO, and the potential for ozone generation by the electrical circuitry. For example, delays to arc formation can be associated with high voltage applied to the electrodes which has the potential to generate corona and ozone. Exemplary plasma power measurement scheme are depicted in An exemplary plasma power measurement circuit system is depicted in In some embodiments, the PPM controller contains a microprocessor or microcontroller and an analog to digital converter (ADC). In some embodiments, the sensor signals are delivered as analog signals to avoid operating a microprocessor in a high-EMI environment, as found near a plasma chamber. In some embodiments, the PPM controller ADC sampling frequency is at least 5 times the frequency of the fundamental frequency of the AC plasma. In some embodiments, a 1 MHz sample rate is used to measure a 115 kHz AC plasma waveform. Other sampling frequencies can work depending on the level of resolution and accuracy needed for voltage and current data. In the event that a dedicated PPMC processer is utilized, that processor communicates the plasma power to the NO generation controller. In some embodiments, primary side measurements can provide a reasonably accurate proxy for the plasma voltage and current on the secondary side. After plasma formation, transformer primary current is directly proportional to plasma current and may either be measured directly or can be measured indirectly (albeit out of phase) by observing the voltage on the primary-side DC blocking capacitor (Cp, as indicated in Electrode performance is expected to change over time due to a combination of contamination, erosion, oxidation, electrical creepage, changes in gap and other factors. These changes manifest themselves as changes in the NO production calibration curve, break-down timing, plasma voltage, and plasma current. A PPM controller system can be used to detect these changes in performance so that a NO generation system can apply appropriate mitigations to keep the generated NO levels accurate. The PPMC provides one or more of voltage level and high voltage current level. These measurements enable a NO generation system to monitor electrode status, provide feedback for the NO generation algorithm, and enable real time plasma power measurement. A PPMC can also be utilized to detect electrode and/or plasma chamber failure, electrode erosion (larger gap), and other changes to the electrode performance. In some embodiments, when a PPMC does not detect current when electrodes are energized, it can be inferred that the system has failed (e.g., transformer failure, electrode gap too large). In some embodiments, a PPMC can detect electrical creepage along the internal or external walls of the plasma chamber that results in change in the rate of rise in the voltage. In another embodiment, a PPMC can detect electrical creepage in the chamber by detecting an operating frequency that is indicative of a low impendence path (an absence of the operating frequencies associated with an open circuit condition before breakdown). This is also detectible by a marked shift in NO levels in the product gas. In some embodiments, a PPMC detects an elevated breakdown voltage or delayed breakdown which can be indicative of increased electrode gap or a faulty connection in the circuit. In some embodiments, when these measurements reach a threshold, the NO generation system recommends electrode and/or plasma chamber replacement. In some embodiments, a NO generator compensates for the level of electrode wear by altering the timing of the electrical discharges or by adjusting the NO production calibration curve. In some embodiments, the adjustments to the NO production curve are made based on prior characterization work that have been recorded in a table or formula. In some embodiments, a NO generation device prompts NO production calibration to be done either manually or automatically, using a calibrated NO sensor. The calibrated NO sensor can by either internal or external to the NO generation system. In some embodiments, a PPMC is used to sample n plasma cycles every time patient therapy starts. This can be done during device calibration, system self-test, or actual treatment. The system software then calculates the slope (Theta1) and error (R2) over every plasma cycle. In some embodiments, reduced slope (less NO produced for a given power level) and increased in R{circumflex over ( )}2 (greater data variance) are indicative of electrode wear. A PPMC provides feedback for a NO generation algorithm by providing actual breakdown timing. A PPMC enables a NO generation controller to detect the actual breakdown time and thus adjust the electrical discharge end point for each discharge so that the discharge ends only after the target discharge duration (AKA duty cycle). Similarly, the timing of a current ramp can be shifted back in time to account for the delay in break-down, as required. This NO generation feature can provide significant improvements in NO production accuracy over the service life of the device. The change in break-down time and/or measured break-down voltage can also be an indication as to the level of wear of the electrode and prompt electrode replacement and/or recalibration if it exceeds acceptable limits. The mathematical product of the PPMC outputs of secondary circuit voltage and current is the plasma power. In some embodiments, a NO generator drives an electrode pair to a specific power level for a specific duration, using the PPMC output to calculate a real time plasma power level during discrete electrical discharges. In some embodiments, NO production calibration for a given reactant gas flow rate is stored within the device in terms of power level and discharge duration. Copious amounts of data can be collected by a NO generator for additional analysis of system performance and dose accuracy improvements. In some embodiments, a NO generator measures one or more of the following parameters for one or more electrical discharges: maximum breakdown voltage, minimum breakdown voltage, voltage at the breakdown, time to breakdown, maximum plasma current (positive half of the waveform), maximum plasma current index, minimum plasma current (negative half of the waveform), minimum plasma current index, maximum plasma voltage (positive half of the waveform), maximum plasma voltage index, minimum plasma voltage (negative half of the waveform), minimum plasma voltage index, RMS power per cycle (sum((V*I){circumflex over ( )}2)/N), number of pulses in plasma cycle, duration of plasma cycle in msec, and number of missed or misidentified waveforms. A PPMC affects the characteristics of the high voltage circuit being measured (e.g., natural frequency). By integrating the PPMC into the actual hardware of a NO generation system so that it is present all of the time, the characterization of the system (e.g., NO production calibration) is inclusive of any effects from the PPMC, thereby rendering their effects on production moot. NO Production Control It is possible to detect electrical discharge. In some embodiments, a NO generation system detects a breakdown event. This can be done by detecting a change in voltage (dV/dt), current (dI/dt), and/or frequency (dω/dt). Voltage across the electrode gap increases until electrical breakdown. The drop-in voltage associated with breakdown can be detected as an indication of electrical discharge. Likewise, breakdown can also cause a sudden spike in current. In some embodiments, electrical breakdown occurs within a few microseconds of the application of high voltage (pulse initiation). Dithering Plus Controlled Duration In some embodiments, a NO generation system operating with fixed pulse modulation frequency and using a dithering method alternates the pulse width of finite length electrical discharges to produce an average NO production rate that is between the finite rates. In some embodiments, the system alternates between the two discrete electrical discharge lengths in a ratio of 50/50. In some embodiments, the ratio of different discharge lengths is a non-equal (i.e., non-50/50) ratio for additional NO production resolution. In some embodiments, one of the pulse widths and production rates is zero. In some embodiments, dithering is combined with plasma current modulation to provide finer resolution control of the production rate. Finite Duration Production The time to achieve electrical breakdown within the electrode gap can vary with one or more of the following parameters: voltage rate of rise, reactant gas humidity, electrode temperature, electrode type, electrode wear, plasma chamber pressure, and the presence or absence of free ions. This variation in breakdown time can affect the amount of NO generated during a discharge event. For example, if a NO generation system applies high voltage to the electrode for a set duration of time, increases or decreases in electrical breakdown time will inversely affect the pulse duration after breakdown occurs, decreasing or increasing NO production, respectively. In some embodiments, a NO generation system detects the breakdown event and maintains the plasma for a set amount of time after the breakdown event. This approach can be used with a either a fixed electrode gap design or a variable electrode gap design, such as a gliding arc electrode. In a gliding arc electrode, the electrode gap increases with time as the arc travels along the electrode edges. Thus, variation in the duration of electrical discharge can have even more significant effects on NO production than in a fixed-gap design because the highest magnitude of NO production occurs towards the end of the discharge event where the electrode gap is largest. Flow Control Flow Control An iNO delivery system can include one or more gas flow controllers to deliver nitric oxide therapy. At a minimum, reactant gas and injector flow are controlled. In some embodiments this is accomplished with a single flow controller (reactant gas flow is equal to injector flow). Some embodiments incorporate several flow and pressure controllers, such as those described for the recirculating architecture. Exemplary embodiments of a recirculation, closed loop pneumatic architecture are shown in Linear Flow Control In some embodiments, one or more valves acts as a linear flow controller. In some embodiments, referred to as linear architectures, a flow controller supplies reactant gas flow, which also becomes product gas flow and injected gas flow. In some embodiments, including the recirculating architecture, plasma chamber flow and injected product gas flow are independently controlled. In some embodiments, a bypass architecture is utilized which is similar to a linear architecture with the flow divided between the plasma chamber and a bypass around the plasma chamber. This approach enables injected flow to differ from plasma chamber flow as well as rapid dilution of product gas after formation to reduce NO concentration and NO2formation. A flow controller can include one or more pumps, valves, inlet and/or outlet pressure sensors, and a flow sensor. In some embodiments, the valve is a proportional valve. The flow sensor is used for closed loop control of the proportional valve while the pressure sensors are used for feed-forward control. A proportional valve or pump can be driven by a variable voltage or current source including the use of pulse width modulation to vary the applied voltage. Feed-Forward In some embodiments, feed-forward control is used to improve the step response of the valve. In some embodiments, the feed-forward control uses the equation for the flow through an orifice plate. After simplifying all parameters that are a function of the orifice geometry into a single constant, K, the equation becomes: where,
In some embodiments, a proportional valve's orifice can be treated like a linear resistor. A calibration curve can model a valve “conductance,” in units of flow divided by pressure, as a function of control signal. Flow Divider Control In some embodiments, including the recirculating architecture, as well as any other constant concentration/constant reactant gas flow architecture, a fixed product gas flow rate is divided between the injector, the recirculation path and optionally, a NO sensor path without disturbing the reactant gas flow rate or pressure. This reduces the range of process variables that affect NO production rate and would otherwise need to be compensated dynamically. In some embodiments, a proportional flow divider therefore can be designed to maintain a constant product gas pressure downstream of the scrubber. Mechanical Control In some embodiments, the flow divider is implemented with a 3-port proportional valve that is sized such that the total pressure drop into an inlet port is constant as flow transitions from one outlet port to the other. Open-Loop Control In some embodiments, two or more adjustable valves are electronically controlled to divide the flow such that their total pressure drop is constant for a given input flow. In some embodiments, two matched valves are calibrated to determine their percent open as a function of drive voltage/current. A flow sensor and controller regulate the flow through one of the valves. In some embodiments, the controller servos the desired open fraction, and a feed-forward lookup computes the drive voltage/current. The other valve is then driven to the inverse open fraction, also using feed-forward, such that the sum of the two valves is equal to 100%. In some embodiments, dissimilar valves are calibrated for flow restriction with respect to drive voltage/current. The controller servos the desired operating point of the injector valves to regulate the injector flow. The controller drives the other valves to the inverse flow restriction to maintain a constant flow restriction through the pair (injector and return path). Valve calibration linearizes the valve response by mapping a control signal to percent open. This allows the flow controller to drive the two valves opposite each other such that the two valves add up to 100% open, providing a constant pressure drop. In some embodiments, the control signal is a PWM duty cycle. In some embodiments, calibration is accomplished by driving one valve to 100% open and sweeping the other over its drive range (voltage or current). In some embodiments, the sweep is run with both increasing and decreasing drive signal to compensate for any hysteresis in the valve. For each operating point (duty cycle), the mean percent open is used to minimize the error due to hysteresis in either direction. where Xiis the injector flow and Xtis the total flow through both valves. Closed-Loop Pressure Control In some embodiments, a closed loop pressure control on the inlet of the injector valve (outlet of the scrubber) can be used. In this context, “closed loop” is intended to mean the inlet pressure is measured and a negative feedback controller (e.g. PID) is used to regulate it. By using closed loop control, which compensates such imperfections as hysteresis, stiction, and model error, these embodiments may achieve tighter control of the pressure drop across the flow divider than is possible with open loop control. A closed-loop control can also compensate for variations in ventilator circuit pressure at the outlet of the injector. In some embodiments, two proportional valves form the flow divider: one to control injector flow and another to control recirculation flow (or waste flow in architectures that do not recirculate excess product gas). In these embodiments, the recirculation valve acts as a backpressure regulator, i.e. it regulates the upstream pressure by bleeding off excess flow. In some embodiments, the injector valve acts as a simple linear flow controller, as described above, fed by a constant pressure source. In some embodiments, a plurality of valves can be used to provide finer control of the injector flow or inlet pressure to the flow divider. In some embodiments, a plurality of valves can control a plurality of output flows. In some embodiments, a total of three valves can be used to control inlet pressure, an injector flow, and a sample gas flow to a nitric oxide sensor, respectively. In some embodiments, the recirculation (or waste) valve is controlled using a PID controller with a pressure sensor as its feedback source. In some embodiments, it can be necessary to provide extra dead volume in the product gas path (in addition to the dead volume in the pneumatic and scrubber design). This acts as an accumulator to supply the injector valve gas without significant pressure variation during the brief delay required for the pressure controller to actuate. The flow restriction of the scrubber and/or pump should generally isolate the plasma from this transient. Recirculation The recirculating architecture is one in which the system operates at a fixed flow through the plasma chamber and a fixed product gas concentration. To regulate the injected dose, only a portion of the product gas is directed to the patient, and the remaining flow can be purged or, as in the case of the recirculating architecture, recirculated back to the input. In all cases, injector flow control is achieved using a proportional flow divider, consisting of two variable orifices, instead of a single proportional valve with a single variable orifice. Where the single orifice changes flow by changing the flow restriction, with the effect of increased back-pressure under a constant flow condition, the two orifices of the flow divider are electrically controlled or mechanically linked such that the total flow restriction through the combination of orifices is approximately constant. This results not only in constant flow but also in constant pressure within the eNO plant (i.e., plasma chamber, scrubber), regardless of injector flow. The recirculating architecture mitigates several constraints that can otherwise limit the effective performance of eNO dose delivery. For example, the product gas flow slew rate is limited by the compressibility of the gas and the dead volume/flow restriction of the scrubber, which limits the ability of linear architectures to track fast-changing ventilator flows. non-recirculating architectures may also result in variable residence time in the scrubber and other dead volumes, which can result in hard-to-compensate NO loss rates. By eliminating variable flow through the plasma chamber, recirculation removes a process variable that must otherwise be compensated for. Variable flow through the plasma chamber is also generally incompatible with gliding arc electrodes. Recirculating architecture systems are designed to minimize the quantity of NO post-scrubber because of the tendency of NO to react with oxygen to form NO2and the desire to accurately know the concentration of NO at the injector. In some embodiments, reactant gas is drawn from the inlet through the plasma chamber by the air pump at a constant flow rate. The pump can be located after the plasma chamber to avoid pressurizing the plasma chamber. As the pump is drawing a vacuum, the chamber operates at atmospheric pressure, minus the pressure drop of the inlet filter. Because the NO production rate is sensitive to flow, especially if gliding arc electrodes are used, in some embodiments a pulse damper is used to smooth the pulsatile input flow of the air pump. This consists of a flow restriction and/or a dead volume between the flow restriction and the pump inlet. In some embodiments, the flow restriction consists of a fixed orifice (e.g. 0.030″ diameter), the size of which depends on the target flow rate, the amount of dead volume present, and the frequencies being damped. In some embodiments, the electrical discharge frequency is set to match or be a multiple of the pump pulse frequency (e.g. ½ the frequency, or every other pump pulse). Electrical discharges are generated at the same point in the pump pulsatility cycle for each electrical discharge, eliminating NO production variation resulting from electrical breakdown and arcing at varying pressure levels within the plasma chamber. In one example, the pump flows at a constant 3 lpm, generating pulsations at a frequency of 75 Hz. The plasma discharges are programmed to be generated at the same frequency, in phase with the pump pulsations. In another embodiment, the discharges are triggered when the plasma chamber pressure reaches a certain level (e.g. lowest pressure level, zero crossing point, highest pressure) within the pump pressure cycle, as sensed by the plasma chamber pressure sensor. In another embodiment, an encoder on the pump is used to trigger electrical discharges at the same point in the pump cycle every time. After the pump, the product gas is passed through a soda lime or other scrubber to remove NO2. NO naturally decays to NO2in the presence of oxygen, so the pneumatic path between the scrubber and the injector is minimized. In some embodiments, one or more particulate filters are located before and/or after the scrubber component to capture particles from the electrodes, scrubber material, pump and other sources. After the scrubber, a proportional flow divider, consisting of a flow controller FC1 and a flow controller FC2, is used to direct a controlled flow to the injector while maintaining a constant product gas pressure at the scrubber outlet. In some embodiments, the pump cannot be controlled as fast as the injector flow, so changes in injector flow that change pressure drop across the scrubber would adversely affect reactant and product gas flow. Maintaining a constant pressure at the injector ensures the pump can operate at a constant or nearly constant speed. The flow divider can be implemented using a single 3-way valve, a pair of proportional valves controlled opposite each other to maintain a constant pressure drop, or a pair of valves operating as a flow controller (injector valve) and a backpressure regulator (recirculation valve). A small, constant sample flow is also drawn off the post-scrubber product gas flow to be sensed by the electrochemical NO sensor, which in some embodiments is cross-sensitive to changes in flow. Maintaining a constant flow improves its stability and repeatability. As both the target flow and input pressure are constant, this flow controller may have low bandwidth and appears primarily as a steady-state flow offset to the flow divider control. In some embodiments, the sample gas flow is 200 ml/min. Sample flow rates from 10 to 1000 ml/min can be utilized, however. Gas which is not directed to the injector, including the gas that flows through the NO sensor, is recirculated back to the plasma chamber inlet and mixed with the room air to form the reactant gas stream, thus forming a closed system. The flow of room air into the system can be equal to the injector flow leaving the system. Dose Control Algorithm In some embodiments, a dose control algorithm for the recirculating architecture operates much like the dose control algorithm for other architectures. Mainly, the injector concentration cannot be varied fast enough to support dose delivery methods other than constant concentration with fixed dilution fraction and the production rate must be regulated using open-loop process control due to the slow response of available NO sensing technologies. The addition of a recirculating path complicates the control system: the product gas exiting the plasma chamber is partially composed of recirculated product gas. Errors in the calculated or measured recirculated mass flow of nitric oxide (ppm*slpm) therefore result in errors in the expected product gas mass flow. Because this new product gas flow is also recirculated, such errors have a tendency to accumulate with every iteration through the loop. The required production rate of the plasma can be determined by the required mass flow of nitric oxide (ppm*slpm) in the product gas stream minus the recirculated mass flow of nitric oxide. To a first order approximation, then, the production rate should be equal to the injection rate because the product gas flow minus the recirculated flow is equal to the injector flow. If the product gas flow is constant, the product gas concentration is constant, and the size of the recirculation path is sufficiently small and/or low pressure drop, then the propagation delay of the recirculation flow rate is negligible, and this approximation holds. There can be an issue with errors accumulating in the system. For example, the issue with the above approximation is that the amount of NO being recirculated may not be equal to the amount of product gas less the measured injection flow. NO is lost in the loop due to one or more mechanisms, including oxidation to NO2. In some examples, NO is lost to direct interaction with scrubber materials as well. Additionally, errors in the injector flow rate cause an excess or deficient amount of replacement NO to be generated. Because of the recirculation loop, these errors in the inferred NO concentration can accumulate with each lap through the recirculation loop. Errors in measured reactant/product gas flow or production rate do result in errors in output product gas concentration, but for a given bolus of gas, they appear once and decrease in magnitude with each cycle around the recirculation loop. The upper bound for error caused by these sources is therefore equal to the original error. NO loss errors, on the other hand, occur each time a particular bolus of gas transits the loop and therefore accumulate beyond the original error. Sources of NO loss or gain can include, but are not limited to, injector flow rate errors, NO lost/absorbed within the scrubber, NO converted to NO2by oxidation (and subsequently removed by the scrubber), NO wash-in/wash-out from permeable materials in the pneumatic pathway, leaks, over-estimation of NO loss (resulting in apparent NO gain), and recirculated NO destroyed by the plasma. To mitigate the accumulation of errors, a nitric oxide sensor can be employed to provide negative feedback. Because only NO loss results in accumulating error, the feedback loop can be designed to compensate NO loss specifically. Because NO loss is expected to be a steady state or slowly changing process, the performance requirements of this control loop are compatible with the slow response of electrochemical nitric oxide sensors. Fast transients, i.e. tracking of the breath cycle, still utilize open-loop process control. In some embodiments, the NO sensor measures up to 2000 ppm NO. In some embodiments, the NO sensor measures up to 5000 ppm NO. In general, the NO sensor could be rated for between 100 and 10,000 ppm of NO, depending on the clinical application and NO production required. As shown in In some embodiments, a sufficiently high bandwidth NO sensor replaces the control system described above. A measured concentration C_om is compared against the target concentration C_ot and a process controller (e.g. PID) is used to set either the target production rate Z_nt or the plasma operating point directly. The closed loop controller also compensates errors in production rate. However, because the NO sensor and associated feedback loop are slow compared to the breath cycle, the controller cannot be expected to correct gain errors or nonlinearities in the production rate. Rather, it will adjust the average operating point of the plasma to result in the correct time-averaged concentration. In a pulsed delivery environment such as a ventilator system, this can result in the plasma alternating between operating points that have positive and negative errors such that the mean error is zero. These errors will result in an intra-breath concentration ripple/error in the product gas, and injection flows sourced from this product gas will therefore contain varying concentrations of nitric oxide. Because the injector flow rate is pulsed, the volume-averaged concentration of the injector may differ from the time-averaged concentration of the product gas. It is for this reason that the system incorporates a production rate model in addition to the NO sensor to determine the plasma operating point. In some embodiments, product gas which is not delivered through the injector is diverted to an exhaust port, NO absorption medium, or other waste path instead of being recirculated. In these embodiments, the plasma may be operated at a constant production rate and flow that is independent of the injector flow. In such embodiments, closed loop control using a NO sensor may not have intra-breath variations in the product gas concentration and may require only the NO sensor feedback loop, without additional models, for accurate regulation of the injector concentration. In some embodiments, feed-forward control is used. The response of the closed loop control is limited by the response time of the NO sensor and the propagation delay of the loop. Although this provides acceptable performance for steady-state operation, it results in a slower response to step changes in operating point. In particular, the control responds poorly to two scenarios: step change in NO loss, and step change in concentration. System performance can be improved by including a predictive (feed-forward) model for NO loss. In some embodiments, a predictive model for NO loss may be sufficiently accurate to eliminate the need for a NO sensor. This is most feasible when there is a high turnover rate of product gas within the recirculation loop, i.e. there are few loop iterations in which errors in the predictive model can accumulate. In some embodiments, the dominant form of NO loss, other than errors in the injector flow rate, can be a constant function of concentration and residence time. If the system is operating at constant flow and constant product gas concentration, it should therefore have a constant NO loss offset to correct for these losses. Changes in this transfer function, for example due to scrubber aging or environmental factors, are expected to be significantly slower than the bandwidth of the injector concentration closed loop controller. It is therefore expected that the control system can be able to compensate for them. However, in some embodiments, NO loss within a soda lime NO scrubber can also depend on other factors, such as the amount of NO2absorbed. If so, the NO loss rate can vary with NO2production rate which, in turn, varies within the breath cycle. The closed loop control responds too slowly to compensate this kind of dynamic loss. A feed-forward model that predicts NO2production and associated NO loss can therefore be used. By un-burdening the negative feedback control system, an accurate feed-forward model also improves the startup/settling time of the control system. This can be useful given the relatively low bandwidth of the control system. A feed-forward compensator can take into account one or more of the following factors (in no particular order): operating environment (temperature, pressure, humidity, etc.), scrubber age, manufacturing variation (e.g., per-unit calibration), production byproducts (e.g. NO2), residence time of the product gas, system operating temperature, concentration of the product gas, flow rate, and oxygen content of the product gas. There is a long propagation delay between when the NO production rate is changed and when the gas reaches the NO sensor and the sensor responds to the change. In some embodiments this delay can be between 5 and 30 seconds. In some embodiments, an extremely slow/overdamped loop response is required to mitigate the overshoot due to integrator windup during this delay period. In some embodiments, the integrator wind-up can be minimized by adding a feed-forward term to prime the loop. Because flow in the system is constant, the feed-forward can be integrated as a simple propagation delay based on the dead volumes of the system. An exemplary embodiment of a recirculation/closed loop pneumatic architecture with a feed-forward pneumatic volume is shown in The propagation delay for a given product gas bolus can be computed in software by assuming that the variable-flow recirculating volume is negligible. The remaining volume in the system is divided into a number of equal-sized volumes (i.e., discretized). A buffer stores concentration history for each of these volumes; the oldest sample therefore represents the concentration that is being recirculated into the plasma chamber. The concentration is computed from the recirculating flow and NO production rate. An integrator accumulates the mass flow of gas through the loop by adding (mass flow rate*time step) at each computation interval; the concentration history is populated according to the volume that flowed during the computation interval. A recirculating architecture can also provide low-dose rates. Low production rates, using dithering or other means, may result in long intervals between plasma pulses. In linear architectures, this produces regions in the product gas volume that with low NO concentration and others with high NO concentration; diffusion or mixing techniques must be relied upon to minimize error in the delivered concentration. In contrast, a recirculating architecture injects only a fraction of the product gas flow during low dose conditions. As a result, the majority of the NO molecules exiting the plasma chamber are recirculated rather than newly produced, so any variation in the concentration due to large pulse spacings represents only a small fraction of the total NO concentration. Priming of the Recirculation Loop In some embodiments, high concentration NO can be made for one lap around the recirculation loop and plasma can be turned off prior to directing any gas to the patient. The timing of turning the plasma off is important so there is not a spike or drop in concentration within the recirculation loop. In some embodiments, a recirculation loop can be primed before injecting to the patient to reduce the time to achieve accurate dosing from a cold start. Purging of the Recirculation Loop NO and NO2gases should not be left in proximity with flow control and sensing elements for extended periods of time. Residual NO within the system can turn into NO2over time. Hence, it is important to clean the flow pathways within a NO generation device after use. NO and NO2can be embedded in the actual materials of the NO generator, requiring sufficient time for these materials to off-gas before device storage. In some embodiments, the recirculation loop is scrubbed of NO/NO2gas after use. In some embodiments, product gas is circulated within the recirculation loop for sufficient time for all the NO to oxidize into NO2, all the NO/NO2adsorbed by the loop materials (e.g., tubing) to be released, and all NO2to be adsorbed by the scrubber. In some embodiments, loop scrubbing is completed when the NO2sensor indicates that there is no remaining NO2. In some embodiments, gas is circulated for a set amount of time that has been characterized to provide sufficient time to scrub all remaining NO and NO2. In some embodiments, non-NO/NO2containing gas (purge gas) is flowed through the recirculation loop and a valve is opened to release NO/NO2containing gas from the recirculation loop into the atmosphere directly or through a Nox scrubber to purge the loop. In some embodiments, a volume of purge gas flowed through the recirculation loop and out the purge valve is greater than the volume of the recirculation loop. Ventilator Systems In some embodiments, a ventilator provides assisted or complete ventilation of a patient with compromised lung function. It can supply either normal or oxygen-enriched air. When inhaled nitric oxide (iNO) therapy is combined with a ventilator, it can be supplied to the patient in a constant inhaled concentration dose. Mechanical ventilators use a number of different ventilation modes, such as (but not limited to) constant positive airway pressure, pressure-control ventilation, volume-controlled ventilation, assist-control ventilation, and pressure support ventilation. Ventilator flow and pressure waveforms can vary dramatically depending on ventilation method, breath rate, spontaneous breathing by the patient, and other variables. Many modes involve rapid slew of air flow from a small bias flow (2-10 LPM) to large inspiratory flows (up to 150 LPM) and back. A period of no flow (0 slpm) may also occur. An exemplary ventilator waveform 300 with zero bias flow is shown in Product Gas NO Sensor Calibration In some embodiments, calibration gas is passed by the product gas NO sensor (e.g., through the recirculation loop) to calibrate the product gas NO sensor. In some embodiments, the output of the NO device is utilized to calibrate the product gas concentration NO sensor within the NO generator. This is accomplished by generating a flow of NO and passing it to either the NO gas sensor used for inspiratory gas monitoring or an external NO sensor. In some embodiments, the NO product gas is diluted prior to passing it to the gas sensor, however this can introduce some error into the calibration. The NO concentration measured by the gas sensor is used to identify a known concentration of gas within the recirculation loop which can be used to update the calibration settings of the product gas NO sensor. In some embodiments, a correction factor is applied to the measured gas to account for additional gas aging that may be associated with traveling to the reference sensor that would not occur when traveling to the product gas NO sensor. When inspiratory gas sensors are used, this calibration is typically performed soon after sensor calibration so that their state of calibration is known. Electrode Replacement In some embodiments, the product gas NO sensor can be utilized for NO production calibration. NO production calibration can be done periodically throughout the service life of a system, or after one or more components have been replaced (e.g., electrodes). In some embodiments, the NO generator supplies a known flow rate of reactant gas to the plasma chamber and sweeps through a range of electrical discharge duty cycles while measuring the NO concentration within the product gas with the product gas NO sensor. In some embodiments involving a recirculation loop, the system directs all product gas flow out of the system (no recirculation) during this calibration step. In some embodiments, the system keeps the recirculation loop closed and compensates the calibration measurements for the buildup of NO within the reactant gas through the course of the calibration sequence. In some embodiments, the NO generation system requires the product gas NO sensor to be calibrated prior to being used to calibrate NO production. In some embodiments, an external NO measurement device is utilized to measure product gas concentration from a NO generation/delivery device. Product gas is routed to the external device either from a scrubber connection, a ventilation cartridge, a ventilation cartridge connection, a bag connection or other external pneumatic connection. In this embodiment, the device sweeps through a range of NO production levels, holding each level long enough for the system and external measurement device to stabilize before moving to the next production level (e.g., 30 seconds in some applications). In some embodiments, the external NO measurement device utilizes one or more of the following methodologies to measure NO: Infrared spectroscopy, chemiluminescence, gas detector tube, photoionization and electrochemical. In some embodiments, the external device also measures NO2so that a product gas NO/NO2ratio can be determined as well. In some embodiments, the NO generator purges the product gas NO sensor with either ambient air or another zero-gas to zero the product gas NO sensor within the device to achieve a zero value from the sensor. In some embodiments, plasma is turned off and the product gas pump is utilized to pull fresh air through the system. In some embodiments, with redundant NO generation channels, a NO generation system can zero the NO sensor in one channel while producing NO for a patient within a redundant NO generation channel. In some embodiments, purge gas that does not contain NO is passed through the recirculation loop to zero the product gas sensor (e.g., nitrogen, oxygen, air). In some embodiments, a NO generator/delivery device can automatically rezero the NO product gas sensor after detecting a change in ambient conditions. This is because some NO/NO2measurement approaches are sensitive to one or more of temperature, humidity and pressure. In some embodiments, the NO/NO2measurement capability includes compensation for one or more of temperature, humidity and pressure variation. Product Gas NO Sensor Redundancy Some embodiments include more than one product gas NO sensor for redundancy. In NO generators with redundant generation channels, this can result in 4 total product gas NO sensors for single redundancy per channel and 6 product gas NO sensors for double redundancy per channel. In some embodiments, one or more central NO product gas sensors can be in fluid communication with the one or more NO generation channels, thereby reducing the total number of NO sensors required. The central bank of sensors can only measure the NO from one channel at a time, however. In some embodiments, if one channel is treating a ventilator and the other channel is treating a manual resuscitator, the central sensor bank is applied to the ventilator as priority since it is the longer term and more complex treatment. Dose Delivery and Dose Accuracy Requirements In some embodiments, to ensure the correct concentration of NO is inhaled by the patient, a constant concentration of NO can be maintained within the inspiratory gas flow (e.g., ventilator flow) throughout the entire breath cycle. In ventilator applications, FDA guidance recommends a ±20% tolerance on delivered NO concentration. In some embodiments, target performance is a nominal accuracy of ≤10% based on market research and clinicians' experience with existing iNO therapies. Because a spontaneously breathing patient can inspire any portion of air from the ventilator tubing, including air that passed by the injector during bias flow, it is necessary for the NO concentration accuracy to be maintained throughout the entirety of the breath cycle. FDA guidance indicates that the tidal volume of any breath, regardless of phasing with the ventilator resulting from variation in inspiratory limb length, shall have a NO concentration within 20% of target concentration except for 10% of the volume which may be between zero and 150% of the target concentration. Manual Resuscitation In some embodiments, ventilation is performed manually using a bag valve mask. The bag can be filled with air/oxygen from an external source and the patient inspiration can be generated by a caregiver squeezing the bag. NO therapy can be provided in these cases by supplying a roughly constant supply of NO-enriched air or NO-enriched oxygen from which the bag is inflated. Excess gas may be vented to the room or to a vacuum system. In these cases, the response time demands on the iNO system are comparatively low because the flow is not changing rapidly. Pulsed NO Delivery In some embodiments, the system can deliver NO-enriched air or oxygen in pulses via a cannula. Instead of supplying a constant concentration supply of dosed air from which the patient inspires, the system supplies a known molar mass of nitric oxide to the patient with each breath. The dose is calculated in mg/hr or equivalent units, instead of concentration (ppm). In a pulsed delivery scheme, the pulse is timed to ensure that the entirety of the NO supplied is inspired by the patient. NO Injection Methodology The goal of any NO injection method is to regulate the dose of NO that is inspired by the patient. In some embodiments, this can be achieved by providing sufficient gas at constant concentration to the patient. Dilution The dilution ratio or dilution fraction is defined as the ratio of NO-enriched flow to ventilator flow. It can be viewed as either the amount the NO dilutes the ventilator flow or the amount the ventilator flow dilutes the NO. In some embodiments, the dilution ratio is defined as the ratio of NO product gas flow to combined inspiratory flow (NO product gas+ventilator gas), however all ratios presented herein use the prior definition. The term dilution factor is defined to be the ratio of vent flow to injector flow (i.e. the inverse of the dilution ratio): The NO concentration after dilution/mixing is equal to: It follows that for a given diluted (ventilator) concentration and injector concentration, injector flow must be directly proportional to the ventilator flow, resulting in a constant dilution factor. Conversely, a variable dilution factor requires a variable injector concentration to maintain a constant diluted (ventilator) concentration. In other words, the mass flow of nitric oxide must be proportional to the total (post-dilution) ventilator flow to maintain constant concentration. In some embodiments, the dilution fraction is fixed. For example, an embodiment where the dilution fraction is fixed at 10:1 for all treatments. In some embodiments, the dilution fraction is variable. In one embodiment, the dilution fraction is held constant for a particular patient treatment (combination of flow and NO dose). The actual dilution fraction selected is a function of one or more of patient dose, patient flow rate, and NO production requirements. In some embodiments, the dilution fraction is determined as a function of the dose only. Low doses can have a high dilution fraction (100:1 for example), which has the advantage of adding less volume to a patient breathing circuit. As patient doses and flow rates increase, commensurate increases in injected NO mass flow rate are required. This is addressed by increasing product gas NO concentration and/or increasing injected flow rate, effectively decreasing the dilution fraction. In some embodiments, a variable dilution fraction enables a NO system to minimize the added volume to a patient circuit, thereby minimizing the risk of affecting concomitant and/or adjunct treatments. Oxygen Dilution The NO-enriched air that is injected into the ventilator circuit dilutes the gas that is normally being supplied to the patient. When atmospheric levels of oxygen are administered to a patient, dilution with NO in a balance of air does not present an oxygen dilution issue. Treatment with supplemental oxygen (e.g., O2concentration >21%) will incur dilution of oxygen in proportion to the amount of NO added. For example, a treatment of 80 ppm NO from an 800 ppm NO tank will dilute the inspired oxygen 10%, turning a 100% oxygen treatment into a 90% oxygen treatment. Units of Measure Because concentration is an incomplete measure of NO delivery, for example as it is also dependent on flow, it is often useful to consider NO in terms of its mass flow, moles per minute or equivalent units. For working with quantities of NO being produced, injected, and diluted, units of ppm*slpm are particularly convenient. Because slpm is compensated for temperature and pressure, ppm*slpm is directly proportional to moles per minute and therefore represent a true mass flow. Injection Modes for Constant Inspiratory Limb Concentration As described above, maintaining a constant ventilator concentration requires maintaining a constant ratio of NO mass flow to total (post-dilution) ventilator flow. Because ventilator flows can change quickly, this requires fast dynamic performance from the system. For example, if FDA's “volumetric duration” term is interpreted to mean tidal volume, then a tidal volume of 500 ml and a peak inspiratory flow of 120 slpm, this suggests a response time of 25 ms is required to meet the 10% volumetric duration guidance from the FDA. While in some embodiments the constant concentration method described below is used, other methods can also be used. A key constraint of any injection mode used in an eNO system is that storage time is limited due to the presence of oxygen in the product gas. NO converts to NO2in the presence of oxygen at a rate that increases with concentration, pressure, and temperature; NO produced on-demand from air, therefore, has a very short half-life; on the order of seconds. This precludes injection modes which store NO for any length of time. Constant Product Gas Concentration In some embodiments, a method of control is used to maintain a constant injector concentration and vary the injector flow. Mass flow controllers can be implemented with millisecond response time, supporting rapid response to changes in ventilator flow. If a constant injector concentration can be maintained, meeting the FDA guidance for 20% accuracy with 10% “volumetric duration” allowance is quite feasible. The constant concentration level of NO from a NO generator can vary with the clinical application. For example, low dose patient treatments require a lower constant concentration within the NO generator and high dose patient treatments will require higher concentrations within the NO generator. In general, the concentration of NO within the NO generator can vary from 1 to 10,000 ppm, depending on the patient dose, inspiratory limb gas flow rate, and dilution ratio. Constant Product Gas Flow Rate In some embodiments, a system which operates with fixed injected NO flow (variable dilution factor) varies its nitric oxide concentration to track the inspiratory flow. In some embodiments, there is a propagation delay between NO production and NO injection, influenced by pneumatic components, scrubbers, and tubing. This propagation delay makes it impossible to dose a breath in real time and meeting the “volumetric duration” requirement. It is therefore necessary for such a system to use a highly accurate predictive model such that NO is generated in advance of the breath. Such a system is likely to perform poorly when used with spontaneously breathing patients, but could function adequately during easily-predicted periodic inspirations (e.g. ventilator treatment). The propensity for intentionally varying concentrations in the NO product gas to diffuse, and the complexity of anticipating and tracking such diffusion, further makes this architecture impractical. The flow rate of such a system must also be low to prevent excessive dilution of the ventilator circuit during bias flows. This necessitates extremely high injector concentrations to achieve high mass flow at low flow rate, which adds still more difficulties. Variable Flow and Variable Concentration In some embodiments, a hybrid approach with variable flow and variable concentration can be used. This adds further complexity to any predictive model or tracking algorithm: such a model must also account for the fact that propagation times are not constant but rather vary with varying injector flow. Variable Inspiratory Limb Concentration In some embodiments, it can be possible to circumvent the requirement for constant inspiratory limb concentration by accurately dosing a subset of the gas within the inspiratory limb that is actually inspired. This is accomplished by utilizing a known dead volume between the injector and patient as well as the inspiratory limb gas flow rate profile. In a ventilator application, for example, the dead volume would be comprised of the tubing, humidifier, and other accessories. When the flow is repeatable, and the dead volume is known, propagation time from the injector to the patient can also be known. In such cases, the subset of flow that is actually inspired can be accurately identified and dosed. It follows that maintaining constant concentration within the inspiratory limb at all times is not necessary and the system can be designed to operate with a lower peak injection rate. This approach to NO generation and delivery can help reduce power consumption, increase scrubber longevity, and decrease electrode wear owing to the fact that less NO is generated overall. Constant NO Delivery When NO is delivered at a constant concentration and flow rate into a dynamic inspiratory flow, concentration in the inhaled gas concentration (i.e., combined flow concentration) will vary. With this NO delivery method, periods of low inspiratory flow, i.e. bias flow between breaths, result in higher NO concentrations than periods of high inspiratory flow rate. The location of the zone of high concentration NO with respect to the patient at a point in time this a function of the volume of tubing between injection point and patient and the integral of flow since the time of injection to. This zone of high concentration can be leveraged to improve overall device efficiency if the system is designed so that the zone of high concentration NO is the volume of gas that is inspired by the patient. In some embodiments, NO is generated and delivered during periods of low velocity during a dynamic inspiratory flow and the tubing volumes are such that it is the high concentration volume that is inspired. In some embodiments, an NO generation system accurately doses a sufficient volume during low velocity flow and ensures that it is the same volume that will be inspired by the patient, thereby effectively pre-loading a lung's worth of air at the correct concentration within the inspiratory limb while running at much lower production rates than would be needed to dose the inspiratory flow. This approach can allow for continuous production while conserving power, allowing the system to be sized for a lower peak production rate, and ensuring that all generated NO is inhaled and little to no NO is released to the surroundings. Generating less overall NO results in energy savings as well as decreased wear on consumable components of a NO generator, such as scrubbers, filters, desiccant and electrodes. In some embodiments, this approach is integrated into a CPAP device. Bias Flow Dosing The volume of the inspiratory limb between the NO device and patient is comprised of tubing (diameter, length), humidifier, adaptors, nebulizer ports, sampling ports, and any other source of volume in the inspiratory limb. In one particular embodiment, the volume of inspiratory limb between the NO device and the patient is greater than the patient tidal volume and the bias flow is sufficiently high to refresh the volume between NO device and patient between breaths. In this case, the inspired volume is comprised entirely of bias flow. The NO device is only required to inject NO at a constant concentration and flow rate that doses the bias flow. This greatly simplifies the NO delivery controls and reduces the overall amount of NO produced since rapid gas flow rates associated with inspiratory events will be under-dosed. In other words, NO injection at a constant flow rate and concentration will result in low NO concentration regions within the inspiratory flow associated with the high flow rates of inhalation. The subset of inspiratory gas comprised of bias flow will be dosed at a constant level and the highest NO concentration within the ventilator circuit. This zone of high concentration can be leveraged to improve overall device efficiency if the system can be designed so that the zone of high concentration NO is the volume of gas that is inspired by the patient. It follows that if a sufficient volume of bias flow is accurately dosed AND that volume is located between the NO device and the patient, arriving at the patient at the time of inspiration, the system effectively pre-loads a lung's worth of dosed inspiratory gas at the correct concentration while running at much lower production rate than would be needed to dose the peak inspiratory flow. This approach functions best when the bias flow is sufficiently high to flow the amount of the tidal volume between inspiratory breaths. In mathematical terms: Variable Production In one form of variable production, a NO device operates at low dose levels (for example, <80 ppm) to improve blood oxygenation and periodically dose the patient at high levels of NO (for example >160 ppm) to prevent or treat infection within the patient's inspiratory tract and inspiratory tubing to the patient. In some embodiments, methemoglobin levels are monitored by a NO device for patient safety. In the event that methemoglobin levels are elevated, a NO generation and/or delivery system can alarm, lower the dose, skip the high dose phase, and/or pause treatment. eNO Production Rate Control Some embodiments of an electric nitric oxide system generate NO on demand and must manage the NO production rate. This must be controlled to regulate injector concentration. In some embodiments, excess NO can be purged to a Nox trap, to the room, or to some form of waste disposal system. The injector delivers the required quantity of NO to accurately dose the inspiratory flow and the remaining NO is discarded. In such embodiments, the NO generator can run at a fixed operating point or one of several fixed operating points. In some embodiments, the operating points are calibrated to result in an accurate NO production rate. For some embodiments, all NO generated is delivered to the patient (minus losses in the system); in such embodiments it is necessary for the NO production rate to match the NO injection mass flow rate—on average if not instantaneously. In process controllers, sensor feedback can be used to implement a closed-loop control. The selection of such a sensor can be matched to the bandwidth of the system. In the case of NO delivery systems, in some embodiments it is impractical to integrate a NO sensor of sufficient bandwidth to measure the instantaneous concentration within a breath waveform. It is therefore necessary to control nitric oxide production using open loop control. Nitric oxide production rate is a function of many input variables. Some of these can be controlled variables (e.g., plasma intensity, reactant gas flow rate) and some may be uncontrolled (e.g. temperature, humidity). The bulk of dynamic range of production comes from modulating the plasma. Some additional control may be achieved by modulating flow. The remaining factors have small effects—they are errors sources that must be considered and/or compensated but do not need to be controlled in order to have sufficient control of NO production. These include but are not limited to:
The plasma intensity may be modulated using a combination of current modulation, voltage modulation, gap length modulation, and/or pulse modulation. In some embodiments, a NO generator actively controls the gas pressure within the plasma chamber to enable more or less NO production. In some embodiments, a NO generator dries the reactant gas to eliminate the effects of humidity on NO production. In some embodiments, a NO generator humidifies reactant gas to a known level to eliminate variation in NO production due to humidity variation. In some embodiments, a NO generator actively controls the temperature of the reactant gas and/or electrodes and/or plasma chamber to modulate NO and/or NO2production. In some embodiments, a NO generator actively measures the electrode gap before, during and/or after treatment to compensate in variation in electrode gap over time. In one embodiment, a NO generator includes an oxygen sensor within the gas inlet or recirculation loop to actively measure and compensate of oxygen concentration variation in the reactant gas. In some embodiments, a NO generator actively controls the N2to O2ratio to vary NO production. This can be done by blending reactant gas from independent sources of N2and O2, or utilizing a molecular sieve material, such as zeolite, to vary the N2to O2ratio. In some embodiments, a NO generator makes adjustments to the flow rate and/or plasma parameters (duty cycle, current) based on input from an orientation sensor Flow Modulation Schemes In some embodiments, flow modulation schemes can be defined by the architecture of the system. In linear architectures where the reactant gas flow is fed directly to the injector, flow is not an independent variable; rather it tracks the ventilator flow (scaled by the reciprocal of the dilution factor), so plasma modulation is the primary control mechanism. Dilution factor may be adjusted for different uses cases (e.g., high reactant gas flow for high dose cases, low reactant gas flow for low dose cases). An example of this control system is shown in In some embodiments, aside from gross adjustment for use cases, flow is treated as a dependent rather than an independent variable (i.e. it is not used to directly control production rate). Plasma Modulation Schemes In some embodiments, production rate is predominantly controlled by modulating the plasma. Any method or combination of methods described in the “plasma control” section of this document can be used. In some embodiments, a fixed-frequency pulse modulation scheme is used with the addition of dithering (to provide low production rate turn-down and improved resolution) and intra-pulse current modulation (to improve gliding arc electrode life and resolution). In some embodiments, gap length modulation inherently results from the use of gliding arc electrodes. In some embodiments, the current in intra-pulse current modulation is a function of the elapsed time from the start of the pulse; it is, in effect, a dependent variable. The control system therefore modulates the pulse width (duty cycle) as a single independent variable. Gap length in a gliding arc is likewise a function of air velocity and plasma on-time. Compensation for uncontrolled factors (dependent variables) that affect the production rate may be performed by applying a correction factor to a state variable in the control system such as the plasma duty cycle or the target production rate. Determining this correction factor requires thorough characterization of the NO plant under a wide range of environmental and other operating conditions. An exemplary overview of an embodiment of a production control scheme is shown in Plasma Duty Lookup In some embodiments, a plasma duty lookup table is utilized. Since the other process variables, with the exception of dithering, are effectively dependent variables, the main control variable is plasma modulation. In some embodiments, plasma parameters are covariate with a PWM duty cycle. Production rate, in units of mass flow (for example, ppm*slpm), is characterized as a function of reactant gas flow rate through the plasma chamber (labeled as plasma flow) and plasma duty cycle, as in In some embodiments, multiple tables are generated for discrete current modulation levels. For example, when the target production rate is below what can be achieved at nominal current, the unit switches to a low current modulation scheme and its associated production curve. Plasma Chamber Plasma Electrical Characteristics A plasma is defined as a gas of ions and free electrons. Air is nominally an insulator; however, when sufficient voltage is applied across an air gap, an avalanche breakdown occurs, and the air becomes a plasma. The voltage at which breakdown occurs is nominally a function of air gap distance and reactant gas pressure but is also affected by many other variables including electrode geometry, time, and the presence of free electrons. After the breakdown occurs, the presence of ions and electrons in the plasma make it conductive; the air effectively transitions from an insulator to a conductor. Plasmas can also exhibit a negative impedance characteristic: as current increases, the number of ions and free electrons increases, and resistance drops. Thus, more current results in lower voltage drop, i.e. the effective resistance of the plasma is negative. High Voltage Generator Circuit In some embodiments of a NO generation device, a high voltage assembly uses a resonant transformer to efficiently produce the required breakdown voltage for plasma formation and to efficiently supply AC power to the plasma after it forms. The presently disclosed embodiment can improve on the resonant topology by tuning the circuit and controlling the harmonic content of the excitation voltage waveform to enable a single resonant transformer to provide the following: rapid initiation of high-voltage breakdown by operating at resonance with a high Q factor, controlled discharge current after plasma formation and during short circuit conditions, rapid adjustment of the discharge current, and automatic reignition of the plasma if the arc becomes extinguished. A high resonant frequency, in the range of 10-1000 kHz, minimizes the size of the transformer and other reactive components. It also provides good temporal resolution when accounting for the power fluctuation inherent in the AC waveform. Other operating frequency ranges can also be used, such as, for example, 50-400 kHz. The resonant circuit may be constructed as shown in The resonant circuit is excited by a MOSFET half bridge or full bridge which is digitally controlled by a microcontroller. It will be apparent to an individual skilled in the art that other semiconductor devices or topologies may be utilized to achieve comparable results, and that discrete, analog, ASIC, or programmable logic may also be used to generate the control signals. Because the LC circuit filters out harmonics of the square wave excitation, a fundamental harmonic analysis can be a reasonable approximation of resonant circuit operation, resulting in the simulation model of the resonant circuit shown in Input voltage to the resonant circuit may be supplied from either a battery or an external power supply. In some embodiments, the input voltage is conditioned to a fixed voltage by a pre-regulator to produce repeatable resonant circuit operation when the input voltage is variable, such as when a battery discharges or when the power source is switched between battery and external supply. The pre-regulator could be any form of linear or switching power supply, including but not limited to boost, buck, or buck-boost topologies. In some embodiments, a large bulk energy storage capacitance is employed at the output of the pre-regulator and the pre-regulator's control loop is tuned to limit the peak input current and input current ripple, as seen by the battery or power supply, that would otherwise result if the plasma is pulse modulated. This prevents the high instantaneous power of the plasma from tripping overload protection circuitry and reduces the. An example of a system power flow diagram is shown in Resonant Modes of Operation Continuing to refer to the circuit in There is also a parallel resonance formed by the transformer's magnetizing inductance (Lmp), the secondary capacitance (Cs), and the primary capacitance (Cp). This is hereafter referred to as the “parallel resonance.” In some embodiments, this resonance may be used instead of the secondary resonance to generate high voltage on the secondary and ignite the plasma. In some embodiments, the capacitance on the transformer secondary (Cs) consists entirely of “parasitic” elements such as the transformer's inter-winding capacitance, the capacitance of the electrodes, and stray capacitance in the high voltage wiring. In some embodiments, one or more discrete capacitors are also added to the circuit. In some embodiments, the transformer turns count and construction is designed to minimize this parasitic capacitance in order to produce higher resonant frequencies and faster voltage rise times with smaller power electronic circuitry. The nature of the circuit to have different resonant frequencies depending on whether or not a plasma is present can be visualized by performing an AC analysis of the simulation model from Secondary Resonance To initiate a plasma discharge, the resonant circuit is excited at the frequency of the secondary resonance. When damping is small, each successive cycle of excitation builds energy in the resonant circuit, producing higher and higher output voltages across the transformer secondary capacitance (Cs) until a plasma forms between the electrodes or until a critical voltage/current is reached such that the losses due to damping are equal the energy being added. Damping results from a plurality of parasitic and/or intentional elements in the system, including but not limited to series resistance, parallel resistance/leakage, capacitor dielectric losses, transformer hysteresis, eddy current losses, skin and proximity effects, and magnetic core losses. In some embodiments, a controlled amount of damping is utilized to limit the peak voltage the system can produce. This adds a degree of inherent safety and/or fault tolerance to the design. In some embodiments the transformer is designed to saturate when a maximum voltage is reached. Because the resonant circuit current is limited by the impedance of the series LC tank at the excitation frequency, the short-circuit load presented by a saturated transformer can be non-destructive. To compute the resonant frequency, the secondary capacitance (Cs) may be reflected across the transformer and scaled by the turns ratio N2/N1. It therefore appears in series with the primary capacitance, producing a resonant frequency wsof: where the resonant capacitance Cris, and the effective (transformed) secondary capacitance Cs(eff)is, The DC blocking capacitor (Cp) in series with the primary forms a capacitive voltage divider with the secondary resonance (Cs(eff)), reducing the secondary voltage. It also produces an effective resonant capacitance Cr, that is necessarily lower than Cs, raising the resonant frequency. A large value of Cp can be used to maximize the voltage on the secondary and minimize the effect on the resonant frequency. In some embodiments, Cs=20.7 pF, Lleak=1.2 μH, Cp=4.2 μF. Cr is therefore 1.58 μF and ωsis 116 kHz, as shown in the impedance plots of Primary Resonance When the circuit operates in the “primary resonance” mode of operation, the impedance of the plasma is transformed by the high turns ratio of the transformer, producing a small load impedance on the primary. The current flow in the plasma is determined by the excitation voltage and the impedance of the resulting series RCL circuit consisting of the series inductance (Lleak+Lleak2), the DC blocking capacitance (Cp), and the transformed impedance of the plasma (Rarc). Other parasitic elements in the system may also limit the current if care is not taken to minimize them. These elements may include but are not limited to series resistance, parallel resistance, capacitor dielectric losses, transformer hysteresis, eddy current losses, skin and proximity effects, and magnetic core losses. The frequency of primary resonance is necessarily lower than the frequency of secondary resonance: because capacitors in series have an effective capacitance that is smaller than either individual capacitor, shorting out the secondary capacitance necessarily increases the effective resonant capacitance and therefore lowers the resonant frequency. To a first-order approximation, the resonant capacitance is then equal to the primary capacitance and the resonant frequency is therefore, If the circuit is in the primary resonance mode of operation and it is operated at its resonant frequency, the reactive impedance jωL−j/(ωC) is zero and the plasma current is determined only by the excitation voltage, the plasma impedance, and the parasitic loss elements of the system. In some embodiments, the resulting current can be excessively high. In some embodiments, the circuit is operated at a frequency other than resonance, such that the reactive impedance of the series inductance and capacitance is non-zero and limits the current in the plasma and under short-circuit fault conditions. In some embodiments, the circuit is designed to produce a controlled plasma current by operating such that the reactive impedance is significantly larger than the plasma impedance and therefore the plasma current exhibits low sensitivity to variability in the plasma impedance. Resonant Circuit Tuning In some embodiments, resonant circuit tuning provides fast breakdown, a stable plasma current, and efficient operation. As is described forthwith, tuning the circuit to operate in both the primary resonance and secondary resonance modes of operation with a single excitation frequency produces suboptimal results. To initiate plasma formation, it is generally desirable to excite the circuit with a frequency as close as possible to its natural secondary resonance. This produces the maximum voltage in the minimum amount of time. The breakdown of the air within the electrode gap when a high voltage develops causes the circuit to be self-limiting in the secondary resonance mode of operation. After plasma formation, in some embodiments, the circuit is excited with a frequency other than natural primary resonance such that the reactive impedance Zr=jωL−j/(ωC) limits the current in the circuit when driving a low-impedance plasma and/or in short-circuit fault conditions. In some embodiments, the circuit is designed to produce a controlled plasma current by operating such that the reactive impedance is significantly larger than the plasma impedance and therefore the plasma current exhibits low sensitivity to variability in the plasma impedance. Plasma impedance may exhibit variability due to various factors, especially the changing arc length that occurs in a gliding arc electrode. This produces a plasma current that is a stable function of excitation voltage: Resonant frequency and excitation frequency may drift as components age and experience changing operating temperature or other environmental conditions. Another benefit of operating the circuit at a frequency other than its natural resonant frequency is that it results in lower sensitivity to changes in operating frequency or resonant frequency: the slope ΔZ/Δf is highest at resonance, so circuits operating at frequencies other than resonance are less sensitive to errors in operating frequency and component value drift. Tuning the Series Resonance for a Single Operating Frequency For a given series inductance, smaller values of Cpproduce values of ωsand ωpthat are higher and closer together such that significant plasma current can be developed if the primary resonance is excited at ωs. However, the primary voltage developed across Cpalso rises and the proportion of the input voltage applied across the secondary decreases; therefore to achieve the same breakdown voltage, a greater input voltage is required and a significantly higher voltage is developed on the primary capacitor. The resonant peak also becomes very narrow, resulting in high sensitivity to errors in resonant frequency. Tuning a Parallel Resonance for a Single Operating Frequency Tuning of the magnetizing inductance in the parallel resonance is a more viable means of ‘stacking’ the resonances than reducing primary capacitance. Reducing the magnetizing inductance of the transformer (e.g., by gapping the transformer core) raises the parallel resonance and can be used to bring it close to the primary resonance. Increasing the value of the primary-side capacitance can further reduce the magnitude of the change in resonant frequency when the secondary capacitance becomes shorted. However, low values of magnetizing inductance and large values of primary-side capacitance result in very large circulating currents in the parallel resonant tank. Multi-Harmonic Tuning To mitigate the challenges of bringing ws close to wp by tuning the primary capacitance and/or magnetizing inductance, the circuit can be designed for two different excitation frequencies. This can allow the plasma ignition and sustained current to be controlled independently by controlling the amplitudes of the different excitation frequencies. In some embodiments, the secondary resonance is used to ignite the plasma while the primary resonance is used to sustain the plasma current. In some embodiments, a high voltage generator can be designed to excite the circuit at ws/2 with a waveform that has a significant second harmonic component at ws. The primary resonance can then be tuned to be near, but not exactly at, ws/2. In some embodiments, the transformer's magnetizing inductance is maximized to reduce magnetizing currents and their associated damping/losses. In some embodiments, the circuit of The DC blocking capacitor, Cp, can utilize a low-loss dielectric to prevent significant losses and heating. The DC blocking capacitor, Cp, can utilize a dielectric that is extremely stable over time, temperature, and applied voltage to prevent drift in the resonant frequencies. Non-limiting examples include polypropylene film and COG ceramic capacitors for providing the necessary performance characteristics. In some embodiments, the circuit is tuned such that the primary resonance is below the excitation frequency. Compared to a circuit where the primary resonance is above the excitation frequency, this produces a higher secondary voltage due to the larger ratio of Cp/Cs. It can also result in a larger difference in the impedance of the primary resonance between the first and second harmonics, reducing the sensitivity of each mode of operation to the harmonics that excite the other mode of operation. In particular, when a circuit operating in the primary resonance mode of operation has a finite impedance at the second harmonic frequency, the presence of a second harmonic excitation component can limit the ability of a controller to reduce the plasma current by modulation of the first harmonic component alone. In other embodiments, it is more practical to have the circuit tuned such that the primary resonance is below the operating frequency. For example, the circuit of In some embodiments, the parallel resonance is used instead of the secondary resonance to ignite the plasma. In these embodiments the fundamental excitation frequency produces ignition while the higher-order harmonic or harmonics produce(s) controlled plasma current. Resonant Circuit Excitation As described above, the circuit can be tuned such that the primary and secondary resonances can be excited with different frequencies. Because the MOSFET excitation circuit, such as the embodiments shown in In some embodiments, the excitation voltage for the primary and secondary resonances can be controlled independently by adjusting the amplitudes of the associated harmonic components of the excitation waveform. This adjustment may be accomplished by adjusting the pulse width of a rectangular excitation waveform. It is therefore possible, for example, to modulate plasma current without significantly affecting breakdown time and vice versa. Resonant Circuit Excitation Wave Shaping/Harmonic Content A square wave (50% duty cycle) contains only odd-ordered harmonics (1, 3, 5, 7, etc), while waveforms with other duty cycles also contain even-ordered harmonics (2, 4, 6, etc). The amplitude for a given harmonic in a generic rectangular waveform is: where n is the harmonic number, A is the peak-to-peak amplitude, and d is the duty cycle. By operating the MOSFET excitation circuit with a 33.3% or 66.7% duty cycle, the amplitude of the 2nd harmonic is maximized (0.276*Vin) while the amplitude of the fundamental is 0.33*Vin. In some embodiments, a NO generator operates nominally at this operating point without current modulation. Resonant Frequency Determination In some embodiments, the circuit generates a harmonic component that is as close as possible to the secondary resonant frequency of the circuit to produce rapid plasma formation. Because the circuit is tuned to operate at a frequency slightly different from the primary resonance and is therefore tolerant of errors in the primary resonance excitation frequency, the fundamental excitation frequency is controlled to produce a harmonic at the secondary resonant frequency. In some embodiments, the NO generator is capable of self-determining its secondary resonant frequency by sweeping excitation frequency with a low excitation amplitude that does not produce a plasma discharge and observing the response of the circuit. In some embodiments, it measures the current in the transformer primary winding. At resonance, the reactive impedance of the circuit is zero, and the current is therefore at a maximum. It will be apparent to an individual skilled in the art that other electrical quantities in the circuit may alternately be used to detect the resonant peak, including but not limited to secondary voltage, voltage across Cp, etc. Current Modulation In some embodiments, harmonic amplitudes are modulated by changing the excitation duty cycle on a pulse-by-pulse basis. This allows the plasma current to be modulated with a time resolution as small as one period of the excitation frequency (e.g., 1 microsecond for a 1 MHz excitation frequency). The pulse width is alternated between two or more discrete duty cycles with an operating frequency equal to the higher harmonic frequency. For example, the PWM waveform shown in The harmonic amplitudes of a waveform consisting of two discrete duty cycles can be determined as follows. The Fourier expansion of a PWM waveform is: where an is the amplitude of harmonic n, d is the duty cycle, A is the peak-peak amplitude, and bnis zero because the signal has no imaginary component. a0is the DC offset of the signal and is rejected by the blocking capacitor. When 180° phase shift is added for duty cycle d2, the first and second harmonic components x1(t) and x2(t) become: Normalizing for A and using the trigonometric identity cos(A+B)=cos(A) cos(B)−sin(A)sin(B), this simplifies to: If the two waveforms (d1 at 0° and d2 at 180°) are added, the resulting harmonic amplitudes a1 and a2 are: In some embodiments, d1and d2are modulated to maintain a constant excitation voltage a2at the secondary resonant frequency while varying the excitation voltage a1at the primary resonant frequency. This provides consistent plasma formation time but variable current after plasma formation, allowing for modulated production rates with repeatable breakdown time. For alternating duty cycles d1and d2, In some embodiments, a2 is elevated at the start of a plasma pulse to initiate faster breakdown but is reduced later in the pulse (after the plasma has formed) to allow higher values of a1 (since maximizing a2 necessarily limits a1 and vice-versa). This can be seen in the exemplary intra-pulse current modulation waveform of In some embodiments the circuit is operated using the parallel resonance and the primary resonance. In these embodiments, a1 is associated with breakdown time and a2 is associated with plasma current. It must be noted that the fundamental harmonic approximation used to analyze the circuit produces inaccurate results when analyzing current modulation. This is because the resonant circuit does have finite impedance at frequencies other than its resonant frequencies. The fundamental component (a1) therefore does contribute some energy to producing plasma formation, while the second harmonic component (a2) does contribute some current after the plasma has formed. This is particularly important when using current modulation to reduce plasma current—the value of a2, combined with the tuning of the resonant circuit, results in a minimum current that can be produced. This can be seen in the exemplary intra-pulse current modulation waveform of Current modulation by shaping of the excitation waveform can result in significantly faster response times than can be achieved by varying the input voltage. The rate of change of the input voltage is limited by the capacitance of the power supply or input voltage pre-regulator, while wave shape can be adjusted at the resonant excitation frequency. By using wave shaping, the plasma current be modulated within each pulse of a pulse-modulated plasma. This is hereafter referred to as “intra-pulse current modulation.” For example, current can be modulated synchronously with the location of the plasma within a gliding arc electrode to produce a current that is tailored to a particular gap length. Input Voltage Pre-Regulator In some embodiments, the input voltage pre-regulator serves two purposes. The first is to provide a consistent excitation voltage, independent of input voltage. The second purpose of the pre-regulator is to smooth the input power to the NO generator. After plasma formation, the plasma current is approximately I≈V/Z, where V is the excitation voltage and Z is the resonant circuit impedance, including the plasma impedance. The NO production control circuit can be supplied by a regulated DC power supply or by a battery, resulting in a wide input voltage range, so it is therefore necessary to pre-regulate the voltage to ensure consistent plasma current. The NO production control circuit can be supplied by power sources with current limits, such as a battery or DC power supply. The instantaneous plasma power is high but the duty cycle is limited, so the NO production control circuit can trigger current limits even when the average power limit of the supply is not exceeded. A pre-regulator that provides tight voltage regulation will draw input power equal to its output power (plus losses) and thus will not prevent false-tripping of any input current limits. In some embodiments, the pre-regulator therefore utilizes a feedback loop which controls the average input current of the converter. The set point for this loop may be determined by an outer voltage loop. The converter employs a large output capacitance, capable of absorbing and supplying up to 50% of the pulse energy without significant voltage ripple, and the voltage loop bandwidth is tuned to be below the plasma pulse frequency. The result is that the pre-regulator acts as a ripple smoother. A control system block diagram 504 is shown in Plasma Intensity Control Control of the plasma intensity is the primary means of controlling the nitric oxide production rate; in some architectures it is the only means. Plasma intensity can be controlled by excitation voltage modulation, resonant circuit excitation wave shaping, and/or pulse modulation. Excitation Voltage Modulation In some embodiments, plasma intensity can be modulated by varying the excitation voltage of the resonant circuit. This is accomplished by one or more of: (1) modulation of the DC input voltage to the half bridge and (2) resonant circuit excitation wave shaping. Pulse Modulation In some embodiments, the plasma is pulse modulated by enabling/disabling the half bridge resonant excitation at a modulation frequency that is below the operating frequency of the resonant circuit (see In some embodiments, pulse modulation is the primary means of controlling the plasma. It provides a large dynamic range and high repeatability. In some embodiments, such as when a digital controller is used, the plasma pulse width is adjustable over finite increments. For example, in some embodiments, the plasma pulse width can have 10 μs resolution. In some embodiments, aliasing between pulse modulation frequency and the resonant excitation frequency can introduce some randomness into the quantity of NO produced for a given duration discharge. For example, if the resonant frequency is 50.02 kHz and a pulse is initiated every 5 ms, a 20 Hz alias appears. Each modulation pulse will start at a different point within the AC excitation waveform and the resulting impact on breakdown time and plasma duration will have a 20 Hz frequency. This effect is most pronounced when the modulation pulse width is short. In some embodiments, the magnitude of these variations may be decreased by increasing the AC excitation frequency, thereby discretizing the duration of the electrical discharge into smaller AC period-long increments. In some embodiments, the variation is eliminated by synchronizing the AC excitation frequency and the pulse modulation frequency. These improvements in pulse energy repeatability manifest as improvements in NO production consistency. In some embodiments, synchronization is achieved by resynchronizing the AC frequency generator at the beginning of each modulation pulse. In other embodiments, synchronization is achieved by delaying the start of the modulation pulse until a particular point in the AC waveform. Pulse Grouping In some embodiments, production rate can be adjusted by grouping pulses. For example, the plasma can be pulse modulated at a fairly high frequency (≥1 kHz) for a finite number or “group” of pulses. This grouping is then repeated at a fixed or variable interval. The high pulse frequency, by preventing the ionized air from fully exiting the electrode gap, can shorten plasma formation times and therefore reduce ozone production (ozone rapidly combines with nitric oxide to form nitrogen dioxide). However, this approach is subject to the same minimum on time constraints as for simple pulse modulation. Thus, pulse grouping produces elevated temporal quantization of the product gas concentration, requiring a level of gas mixing downstream of the plasma chamber in some applications. Dithering In some embodiments, the plasma pulse width is adjustable over finite increments. The NO production control circuit also has a minimum pulse width that results in both plasma formation and a repeatable discharge duration, producing a minimum acceptable on-time and, therefore, a minimum production rate for a given pulse frequency. To improve the effective resolution and turn-down of the NO generator, some embodiments employ a dithering algorithm to produce average production rates that are between two discrete values. For example, to achieve a production rate that is 10% of the way between two steps, the system will operate 9 out of 10 steps at the lower duty cycle and one step at the higher duty cycle. In some embodiments, one of the duty cycles is 0%. In some embodiments, the smallest non-zero duty cycle is determined by a minimum pulse width that produces a repeatable plasma duration after formation. In some embodiments, one of the duty cycles is 100%. In some embodiments, the dithering algorithm is implemented by using a “demand” integrator and a “production” integrator. For computation interval, the desired production rate is added to the demand integrator while the expected production rate for the actual (quantized) duty cycle that just occurred is added to the production integrator. The controller determines an ideal duty cycle to set the desired production rate that is between two realizable (quantized) duty cycles. If the demand integrator is larger than the production integrator, the system will round up to the nearest duty cycle; otherwise it will round down. The resolution limit to this dithering algorithm is a function of tolerance to error-in-time, as well as the extent to which diffusion will equalize the concentrations of nitric oxide within the stream of product gas. Low Production Current Modulation In some embodiments, a low production current modulation scheme can be used to overcome the temporal quantization issues of dithering at very low production rates. The system operates with one of two resonant excitation wave shapes: nominal and low-current. NO production rate is nominally controlled by plasma pulse width modulation. When production demand is sufficiently low, the excitation wave shape is switched to low current. In some embodiments this current modulation is combined with a dithering algorithm. Operating at reduced current has the effect of reducing the error-in-time of dithering at low production rates. Inter-Pulse Current Modulation In some embodiments, an inter-pulse current modulation scheme can be used such that the resonant excitation wave shape is modulated synchronously with the pulse modulation frequency and is determined as a function of modulation duty cycle, i.e. each duty cycle is associated with a specific wave shape. In some embodiments, where the modulation frequency is variable, the wave shape is a function of the modulation frequency. Unlike the low-production current modulation, this produces a continuous transfer function with a single independent variable (duty cycle or frequency) for the control system to adjust. The shape of the current vs. duty cycle curve can be adjusted/fine-tuned to produce the optimum resolution (ulpm per step, or % per step) that maximizes the dynamic range of the NO generator. Example inter-pulse current modulation curves are shown in In some embodiments, dithering of inter-pulse current is inherently coupled to dithering of pulse duty cycle because the excitation wave shape is a function of duty cycle. In some embodiments, pulse current is adjusted independently of modulation pulse width to produce finer resolution of production rate control. For example, 10 finite currents can be used to produce 10, linearly varying, discrete production rates between the production rates associated with discrete pulse widths of 80 μs and 90 μs to produce a 10× improvement in production rate resolution. In some embodiments, the excitation wave shape is continuously variable. In some embodiments, a finite number of discrete wave shapes is used. In some embodiments, a dithering algorithm is used to explicitly modulate between two or more discrete excitation wave shapes that produce different plasma currents to improve the production rate resolution further. Intra-Pulse Current Modulation In some embodiments, the resonant circuit excitation wave shape is adjusted dynamically throughout each plasma pulse to produce intra-pulse current modulation. Current is therefore a function of time since the start of the pulse. This is particularly applicable to gliding arc electrodes, where the use of a low current limits erosion/heating in the small gap at the base of the electrode while higher currents provide plasma stability and increased production in the larger gaps. This also increases the dynamic range of the system by ensuring that short pulse widths, which are associated with low production rates, have low plasma intensity and therefore high resolution (small change in production per change in time) while long pulse widths, which are associated with high production rates, end with high plasma intensity and therefore maximize production within a finite time window. In some embodiments, the second harmonic excitation voltage (a2) is held constant while the first harmonic excitation voltage (a1) is varied. In some embodiments, the second harmonic excitation voltage (a2) is also varied, either to produce a lower overall current and/or to produce a faster breakdown/plasma formation time. In some embodiments, when a dithering algorithm is applied in conjunction with intra-pulse current modulation, the plasma current ramp profile remains a fixed function of the time since the start of the modulation pulse. A combination of short pulse widths and low current at the start of the ramp profile can be used to achieve very low levels of NO production (e.g. <1 ppm·lpm). In some embodiments, different plasma current ramp profiles can be used to produce finer production rate resolution between two discrete modulation duty cycles or modulation pulse frequencies. In some embodiments, a dithering algorithm selects between two or more discrete plasma current ramp profiles to produce finer production rate resolution. In some embodiments, a discrete number of ramp profiles is used. In some embodiments, the ramp profile is continuously variable. In some embodiments, the circuit detects plasma formation and adjusts its excitation frequency and/or modulation duty cycle (i.e. the duration of the subject discharge) and/or excitation wave shape and/or plasma current ramp profile after plasma formation. In some embodiments, plasma formation can be detected by measuring and recognizing a high dv/dt in the secondary voltage, a high di/dt in the secondary current, or a change in resonant circuit operating frequency from the second harmonic to the fundamental, as shown in Nozzles One or more nozzles can be used to direct reactant gas through an orifice or nozzle towards one or more electrodes. In some embodiments, the nozzle 510 is a circular hole, which can help with machineability, however can generate a non-uniform flow velocity pattern as shown in In some embodiments, the nozzle 512 is shaped like a slit, as shown in Product Gas Flow Control Product Gas Humidity Measurement A humidity sensor within the recirculation loop can be utilized to determine the status of the soda lime of a scavenger in the system. Soda lime requires water to absorb NO2and convert it. Soda lime typically is comprised of 15-20% water content when new. As the soda lime dries out, there is less water content to capture NO2, resulting in a decreased capability to remove NO2from the product gas stream. In some embodiments, a NO system uses one or more of the ambient humidity, ambient pressure, ambient temperature, and recirculation loop humidity, recirculation loop temperature, recirculation loop pressure to determine status of scrubber water content. In some embodiments, a product gas humidity measurement is also used for compensation of the product gas NO measurement with respect to humidity. Environmental Compensation for NO Dose Control In some embodiments, humidity or other environmental factors can be used as input into the control algorithm. In some embodiments, the system compensates the influence of environmental factors such as ambient temperature, reactant gas humidity, reactant gas temperature, electrode temperature, and reactant gas pressure. The system can measure each of these parameters directly using dedicated sensors or may infer indirectly using other sensors and known physical properties of the system. In some embodiments, a system model consisting of regression equations and/or lookup tables determines a correction factor for the target production rate as a function of environmental factors. In some embodiments, a system model consisting of regression equations and/or lookup tables determines the NO production rate as a function of the environmental factors and a plasma operating point that consists of at least one of plasma duty cycle, frequency, dithering, and/or current. A target production rate and measured environmental conditions are then used to determine the corresponding plasma operating point. NO Delivery Constraints A NO delivery system injecting a fixed concentration product gas into a dynamic ventilator flow must meet certain flow response time requirements in order to produce a stable dose concentration. In some embodiments, the concentration may be permitted to deviate from the target concentration by 20%. In some embodiments, up to 10% of the volumetric duration of the breath may be permitted to be up to 150% or 0% of the target concentration. In some cases, this necessitates that an injector flow controller track the ventilator flow with a latency of at most 25 milliseconds. For example, 10% of the tidal volume will pass the injector in 25 ms for an adult patient with a peak inspiratory flow of 120 LPM and a tidal volume of 500 ml. In some embodiments, a nitrogen dioxide scrubber has a flow restriction and dead volume that has the effect of low-pass filtering a reactant gas flow. In some embodiments, the time constant of this filtering is significantly longer than 25 milliseconds. This limits the ability of some linear architectures to meet flow response time requirements. In some embodiments this is mitigated by locating an injector flow controller downstream of the scrubber. In some embodiments this is mitigated by using a constant pressure drop flow divider to allow the scrubber to operate at a constant flow, independent of variations in injector flow. By having scrubber flow already established at the time of the inspiratory event, some architectures are able to respond more quickly with proportional NO flow. NO Loss The amount of NO produced in a plasma chamber is often not the amount of NO available at an injector. This can be caused by various factors, including but not limited to NO oxidation between the plasma chamber and injector, wash-in and wash-out effects of the pneumatic circuit (i.e. absorption of NO into the walls of the pneumatic pathway), and reactions with a scrubber material. In some embodiments, a NO generation system compensates for anticipated loss of NO by producing additional NO within the plasma chamber. This compensation can be a function of one or more of the product gas NO concentration, product gas temperature, product gas pressure, product gas flow rate, volume between plasma chamber and injector, scrubber interaction with NO, oxygen concentration in the reactant gas, oxygen concentration in the product gas, and NO2concentration. Increases in NO concentration relate to increased oxidation and absorption of NO into the pneumatic circuit materials. Increases in product gas pressure result in increased interaction between NO and O2in the product gas, resulting in increased NO loss. Increases in product gas flow rate produce increases in pressure due to the flow restriction of the system but also decrease transit time. Increases in the volume of the pneumatic circuit between plasma chamber and injector relate to increased transit time and greater NO loss due to oxidation. Increases in O2concentration within the product gas result in greater NO to O2interaction and NO oxidation. In some embodiments, it is assumed that equal amounts of NO and NO2are absorbed by a scrubber. Computational feed forward algorithm can be based on one or more of the following parameters: production byproducts, environmental factors, NO oxidation models. etc. In a recirculating architecture, a product gas concentration, flow rate, and pressure may be constant. In some embodiments a feed-forward may subtract a predicted NO2production rate from a predicted NO production rate to compensate NO absorption by a scrubber. In some embodiments, a gas-phase oxidation model can be used to predict additional NO loss due to oxidation. In some embodiments, the estimated product gas NO level may be further compensated by assuming that NO2resulting from oxidation will cause a scrubber to absorb more NO. In some embodiments, the NO absorption rate of a scrubber is characterized as a function of input NO concentration, input NO2concentration, temperature, and humidity. A feed-forward compensator uses this characterization to predict NO absorption based on the measured or modeled operating point of the system. NO Production with High Efficiency Large electrode gaps produce NO with high electrical efficiency (ppm·lpm/watt) but require high breakdown voltage to initiate the electrical discharge. In some embodiments, a smaller break down gap is utilized to facilitate electrical break-down in combination with a high reactant gas velocity to elongate the arc, as shown in The arc stretching effect creates plasma arc lengths that are longer than the actual electrode gap. Hence, an electrode assembly with smaller gap electrode can be made more electrically efficient by “arc bending” through the use of higher reactant gas flow velocity, thereby effectively increasing the arc length of the plasma. Flow velocity affects the bend rate but not the flow rate. For example, a 1 mm gap and an air velocity of 7 m/s can generate more than 500 ppm·lpm with a flow rate of 0.15 l/mn, and the velocity can be controlled with a lower nozzle diameter. There are two ways that an arc can extinguish: 1) active shut off of the arc or 2) passive shut off as the arc elongates to a length that cannot be supported. Passive shut-off introduces variability into the NO production levels since every arc will terminate after a different duration. Active shut off, as can be done by applying an appropriate duty cycle to the high voltage, provides precise arc travel and elongation between discharge events for tighter control of NO production. Nozzle size contributes to NO production efficiency as well, as shown in In some embodiments, reactant gas velocity within the electrode gap is kept at a low enough flow rate that the arc does not glide or elongate, thereby improving the precision of production control. In one nozzle and plasma chamber embodiment, low reactant gas flow rates (e.g., 0.15 lpm) result in low reactant gas velocity (e.g., <1 m/s) resulting in a “straight” plasma arc. Electrode Design Electrode Materials Electrodes are typically constructed entirely or in part with an electrically-conductive material. In some embodiments, electrodes are constructed from ruthenium, a metal with high melting temperature. Ruthenium can be used as an electrode material in its pure form but can also be alloyed with other materials to improve properties such as oxidation resistance, machineability, and cost. In some embodiments, ruthenium is alloyed with one or more of titanium, platinum, and palladium. In some embodiments, some or all of the electrode is coated with ruthenium or an alloy containing ruthenium. Other materials within the platinum metal group, namely ruthenium, rhodium, palladium, osmium, iridium, and platinum, can serve as electrode materials. In some embodiments, platinum group metals are alloyed with iron or other metals to make the resulting material magnetic. This property facilitates removal of sputtered electrode materials from a gas stream using a permanent or electro-magnet. Parallel Electrodes A parallel electrode design involves two or more electrodes that overlap with a gap in between them. When AC voltage is applied, arcing occurs in more than one location due to the concentration of the electric field and propensity to break down. In some embodiments, parallel electrodes have non-uniform profile on their sides, as shown in In some embodiments, a manufacturable parallel electrode design can be provided. In some embodiments, a parallel design does not have a nozzle to focus reactant gas. In some embodiments, parallel electrodes are simply embedded in the wall of a tube. In some embodiments, nozzles are used to improve the stability and quantity of reactant gas flow across both arcing locations. As a parallel electrode wears, the end of the electrode erodes, changing the shape of the electrode. In some embodiments, the end of the parallel electrode is formed during manufacturing to resemble the shape of a worn electrode. In some embodiments, a parallel electrode design 620 with more than two electrodes can be used, as shown in Parallel electrodes can present more than one discrete arcing location. It follows that high power efficiencies can be achieved by focusing reactant gas flow at the arcing locations, thereby improving gas/plasma interaction. In some embodiments, the number of reactant gas flow nozzles is equal to the number of arcing locations. In some embodiments, reactant gas flow through the nozzles is controlled in either a binary or analog sense based on the amount of arcing occurring at a corresponding electrode gap. In some embodiments, lower NO concentration product gas is achieved by flowing reactant gas through a nozzle that is not directed at an active electrode pair, thereby decreasing the amount of reactant gas converted to NO for a given reactant gas flow rate. In some embodiments, a slit nozzle is used to direct a wide fan of reactant gas across the arcing locations of a parallel electrode. Over time, an end edge of the parallel electrode can erode and become more rounded. In some embodiments, electrodes are rotated about their long axis to present a new, sharper edge to the gap. In some embodiments, a parallel electrode can be indexed to 2 or more rotational locations, enabling greater longevity and production consistency from a single electrode pair. As electrodes wear, NO production characteristics can differ from what they were when the electrode was new. An electrode and/or chamber can be replaced to prolong the service life of the rest of the NO generation system. As electrodes wear, in some embodiments, the entire electrode/plasma chamber assembly is removed and replaced. In some embodiments, electrodes are mounted to a frame. When electrodes are replaced, only the electrodes and frame are replaced, rather than the some or all of the plasma chamber. This reduces expense of replacement. Multiple Parallel Electrodes In some embodiments, an array of parallel electrodes provides multiple electrode gaps. In some embodiments, all of the electrode gaps have the same distance so that there is no propensity to arc in one location over another. As shown in an exemplary embodiment in In some embodiments, each triple electrode set is independently controlled. In one approach a first triple electrode is utilized for a certain period of time and/or cycles and/or power before switching to another triple electrode. In some embodiments, electrodes are utilized until they reach a particular temperature prior to switching to another electrode pair. This can prevent electrodes from getting too hot which can affect wear rates, particulate generation and nearby mate. In Another embodiment of a parallel electrode array is depicted in A parallel electrode array can be used to produce consistent levels of NO production when all electrodes in the array are energized at once and when electrodes are energized in discrete pairs. Energizing all electrodes at once results in electrical break-down in only one electrode gap at a time. As electrodes wear and the gap between them increases, electrical breakdown will tend to occur at the pair of electrodes with the shortest gap, thereby distributing the use/wear amongst electrode gaps and prolonging the lifetime of the overall electrode assembly. Modular Gliding Arc Edge Design Gliding Arc Cartridge Design In some embodiments, a gliding arc electrode insert enables replacement of electrodes. Offset Gliding Arc Design In some embodiments, a gliding arc electrode 800, as shown in 3D in Gliding Arc Array In some embodiments, the longevity of a NO generation system is prolonged by utilizing multiple pairs of gliding arc electrodes. In some embodiments, the gap is the same for each of the electrode pairs in an array of electrodes so that each pair is functionally equivalent with the others. In some embodiments, the gap varies between electrode pairs so that specific electrode pairs are energized for specific levels (or ranges) of NO production. In some embodiments, one or more nozzles are directed towards the electrode gap(s) and a combination of one or more of the nozzles is selected to achieve a particular NO production level or range. Electrode Wear Detection As electrodes wear, the gap between them can change. For example, sharp features can become rounded and the distance between electrodes can increase. Increases in electrode gap can affect the break-down voltage, break down timing and level of NO production. In some embodiments, the break-down time is used as an indicator of electrode gap/wear. In some embodiments, the phase angle between the AC voltage and the AC current at the gap are an indicator of electrode gap length. Because plasma impedance is mostly resistive and longer gaps are associated with higher resistance, the change in gap length may be observable as a change in the ratio of active power in the plasma to reactive power in the AC resonant circuit, which manifests as a phase shift. In some embodiments, the cumulative electrode use is used as a predictor of electrode gap. Cumulative use can be a function of one or more of cumulative run time, median moles of NO produced, cumulative number of discharges, and cumulative moles of NO produced. Larger gaps require larger voltage to break down. In some embodiments, a NO generation system uses the high voltage magnitude of one or more discharges to determine the electrode gap. In some embodiments, a NO generation system uses one or more of the following parameters in addition to breakdown voltage to infer electrode gap: thermionic emissions, reactant gas humidity, reactant gas temperature, electrode temperature, plasma chamber temperature, and initial electrode gap. In some embodiments, a NO generation system can generate an alarm and/or prompt electrode replacement based on the measured/indicated electrode gap. In some embodiments, a NO generation system can compensate for changes to electrode gap in order to maintain accurate NO production. For example, longer gaps indicate longer arcs that create more NO. In response to longer gaps, as can occur with electrode erosion, some embodiments of a NO generation system can do one or more of decrease the electrode current, decrease the discharge duration, change the discharge current/time relationship, and/or decrease the frequency of discharges. Electrode Wear Compensation The factory production calibration for an electrode pair may not be accurate throughout the expected life (wear) of the electrodes. In other words, the amount of NO generated by a particular frequency and/or duty cycle of electrical discharges can shift as a function of electrode wear and erosion. In some embodiments, a NO generation system includes an adaptive calibration scheme whereby a series of production calibration curves (production to Duty Cycle) are established and utilized during the life of the electrode to ensure accurate generation/delivery as the electrode wears. In some embodiments, a single mathematical function is utilized to calculate the correct plasma parameters (e.g. frequency, duty cycle, etc.) as a function of one or more of an electrode's design (e.g. material, geometry, initial gap, etc.), and service life (e.g. cumulative NO produced (e.g. moles), cumulative run time, historical duty cycle applied (e.g. average, range, weighted average), voltage range applied (e.g. average, range, weighted average), power levels applied and other parameters pertaining to the electrodes use). In some embodiments, the compensation algorithm consists of several calibration curves, the first curve representing the actual calibration of the electrode at time=0 (factory). In one embodiment, subsequent curves are based on actual calibration of worn electrodes to account to non-linear wear as electrodes “break-in.” In some embodiments, assume that the form of the initial calibration curve is similar over time and multiply the calibration curve with a scaling factor. For example, if after a given amount of production or a given amount of time at a given setpoint (moles or ppm*lpm*time) the average production has shifted by 10%, then a subsequent calibration curve may be generated by inducing an equivalent shift (in this case 10%) on the t=0 curve. The same process may be followed to generate as many subsequent calibration curves as observed production checkpoints for a population of electrodes as they wear. In one embodiment, once the series of production calibration curves is established, the system selects a calibration curve to use based on the amount of total NO delivered (in moles) historically produced by the electrode. In some embodiments, the system interpolates between two or more discrete curves for finer resolution adjustments to NO production as a function of electrode wear. It should be noted that the term “electrode wear” applies to changes in the electrode gap as well as the rounding or sharp features over time. The generation and adaptive selection of calibration curves (or interpolation thereof) may also be based on detected power or current draw over time (as the electrode wears), or any other parameter that may be strongly correlated to production as the electrode wears, rather than or in addition electrode history. Since electrode wear patterns may be dependent on the usage profile (NO setpoint, flow rate, time), leading to increased wear patterns at specific portions of the electrode, it may be possible to interpolate between calibration curves based on the usage history. For example, a gliding arc electrode typically set to a 20 ppm NO target or less uses a particular range of the electrode surface associated with duty cycles required to generate low production levels. It follows that wear of the electrode would be in the region of the electrode where the arcing has occurred and not along the entire length of the electrode. In some embodiments, adaptive calibration is only applied to a first portion of the electrode (closest gap) whereas calibration for portions associated with longer duty cycles continue to refer to the factory curve (Time zero). These approaches to characterizing electrodes before use and adapting to real time measurements of electrode performance present ways of maintaining required production accuracy of an electrode system, thereby prolonging the service life. Discharge Monitoring In some embodiments, a sensor monitors the travel of a gliding arc. In some embodiments, the sensor is comprised of one or more of an optical sensor, a thermal sensor, or a camera. In some embodiments, the phase angle of voltage and current is used to infer a gap and infer where along the arc is along the length of the electrode. For further illustration, when an AC arc is located at the small gap of a variable gap electrode, more reactive power (or imaginary power) is generated than active, NO-generating power. Contrastingly, in large gap, more active power is produced. Imaginary power is power within capacitors and inductors within the high-voltage circuitry. The shorter the length of the arc, the closer the resistance is to zero. In this case, the majority of the apparent power would be circulating within the circuit (capacitors and inductors), and the phase angle approaches 90 degrees. If all the power was to be in arc discharge, the phase angle would be 0 degrees. It follows that as an arc moves from the short gap to the large gap, the amount of power within the arc increases and the phase angle decreases. In some embodiments, a NO generation system can determine the electrode gap and adjust the electrical discharge characteristics to produce a specific quantity of NO. As an electrode wears, the gap can become larger, producing physically longer arcs that produce greater amounts of NO. A NO generation system can compensate for an increase in electrode gap by decreasing the duty cycle and/or decreasing the current in the arc, for example. In the event that an arc does not travel as far as expected, a NO generation system can prolong an electrical discharge to achieve a target amount of NO production. Electrode Cooling Electrode erosion can increase with electrode temperature. Each arcing event adds thermal energy to an electrode. This thermal energy can build up, increasing the electrode temperature and accelerating electrode wear. Electrode temperature can be reduced using various methods, including the use of a spooled wire electrode and a hollow electrode. Electrode Replacement Electrode replacement can be done on an as-needed basis, prophylactically, as part of planned maintenance or other frequencies. A sample work-flow for replacing the electrodes is as follows: a. Power down device. (Allows cool-down) b. Remove side-plate, breaking electrical and pneumatic connections c. Remove plasma chamber d. Exchange electrodes (may include plasma chamber) e. Re-assemble unit (2×) In some embodiments, a NO generation system is recalibrated after the electrodes have been replaced. This can be a manual operation involving calibration gases and/or known NO measurement devices. It can also be an automatic method, relying on calibrated gas sensors within the NO generation system. In general, it is desirable for electrode replacement to not require any tools for removal and installation. All pneumatic connections should be accomplished in one step. In some embodiments, the mechanical connection is completed as a protective cover is installed, the protective covering serving as protection against one or more of high voltage, user contact, particulate and fluids. Spooled Wire Electrode In the embodiment depicted in Electrode wire travel can occur concomitant with plasma arcing. Electrode wires can be provided on separate spools as shown or be wrapped around a common spool. In some embodiments, the electrode wire travel rate is related to one or more of NO production, environmental conditions, and operating temperature. For example, in some embodiments, wire travel rate increases when operating temperatures are higher to compensate for accelerated electrode wear. In some embodiments, wire travel rate is slow when a NO generator is producing low levels of NO and increases for high NO production levels to maximize the use of the electrode material. In some embodiments, the electrode wire is advanced between patient treatments. In some embodiments, the electrode wire is advanced at the beginning or end of use of the plasma chamber. Convection from Reactant Gas Electrodes can be cooled by the reactant gas flowing through the plasma chamber. In some embodiments, reactant gas is actively cooled prior to entering the plasma chamber. In some embodiments, reactant gas is insulated from and routed away from heat sources within a NO generation device prior to injection into the plasma chamber. In some embodiments, reactant gas loses pressure as it enters the plasma chamber to decrease temperature. In some embodiments, a plasma chamber includes a plurality of nozzles for flowing gas over electrodes for cooling, rather than plasma generation. In some embodiments, electrodes have ridges, cooling fins, and/or other features to increase convective cooling. External Electrode Cooling In some embodiments, a flow of gas external to the plasma chamber cools the electrodes. Hollow Electrodes In some embodiments, coolant gas or liquid passes through hollow electrodes to reduce temperature, as shown in In some embodiments, the electrodes are coated on the inside with ceramic, polymer, or another electrically insulating material to prevent electrical shorting through conductive cooling fluids. The cross-section of the tubular electrodes can be round, square, hexagonal, teardrop shape, or some other shape. A sharp edge, such as found on a teardrop shape can increase electrical field in the gap when the sharp edge is oriented towards the gap. In some embodiments, a slit nozzle is used that is parallel to the orientation of the plasma. This approach focuses the reactant gas more than a single circular nozzle in the electrode gap to increase NO production. In some embodiments, the direction of reactant gas flow can be reversed to double the life of electrodes. This can be accomplished pneumatically by routing gas the opposite direction through the chamber. In some embodiments, the nozzle and chamber are separable such that the plasma chamber can be removed and inserted in the reverse direction. This approach can apply to solid and/or hollow electrodes. Coolant for the electrodes can be a gas (air, nitrogen, etc.), or a liquid (water, ethylene glycol, mineral oil, etc.). When liquids are utilized for cooling, non-electrically conductive liquids can be used to prevent shorting of the high voltage circuit through the cooling system. Alternatively, independent cooling systems can be used for each electrode. In some embodiments of liquid cooling, a closed loop coolant path is used. In some embodiments, liquid passes through the electrodes and returns to a reservoir to lose heat. In some embodiments, a heat exchanger with cooing fins is used to dissipate heat from the electrode coolant. In some embodiments, a heat exchanger is located within a NO generator such that box cooling air is used to cool the coolant. In some embodiments, a thermo-electric device is used to actively cool electrode gas or liquid coolant. Thermal Coupling of Electrode to Chamber Another means to reduce electrode temperature is to ensure thermal coupling between the electrodes and the plasma chamber. In some embodiments, a thermal paste is used between the electrode and plasma chamber to improve thermal conductivity. In some embodiments, a plasma chamber is made from a thermally conductive and non-electrically conductive material. Scrubber Cage Capture In some embodiments, cage capture technology is used to selectively remove NO2from product gas. Cage capture involves the use of custom nanomaterials to selectively attract specific types of molecules chemically and/or physically. This approach effectively attracts and retains pollutants within the structure of the cage capture material. It can allow for increases in absorption capacity and environmental robustness (e.g., immunity to environmental humidity). In some embodiments, NO2in a gas stream is sequestered into a molecular cage within the cage capture material and stored in the form of N2O4. In some embodiments, the cage capture reaction is reversible, enabling cage capture materials to be reused multiple times. In one embodiment, soaking the scrubber in water dissolves the N2O4, forming nitric acid in the process. In some embodiments, the NO2scrubber of a NO device can be removed and soaked in water to remove the NO2from the scrubber material. The nitric acid formed is then neutralized with an alkaline material prior to disposal into a sewer. In one embodiment, the pH of the nitric acid is neutralized with an alkaline material (e.g., sodium hydroxide or soda lime) to a value of 5.5 to 8.5 before disposal. The benefit of this approach is that a scrubber using cage capture technology can be reused over many cycles, reducing the amount of material that goes to the landfill or incinerator. In some embodiments, the cage capture material is a metal-organic framework (e.g., Manchester Framework Material MFM-520). Scrubber Design In some embodiments, a replaceable NO2scrubber cartridge 960 can interface with the NO generator 962 with a triple lumen connection that engages with a twist (e.g. bayonet fitting or threads), as shown in In some embodiments, gas flow within a scrubber cartridge may be parallel to the long axis of the scrubber with gas flowing through filters and media in a sequential fashion. In some embodiments, filtration and/or scrubbing is accomplished as gas flows radially from an inner location within the scrubber housing to an outer location (or vice-versa). Scrubber Cartridge Retention In some embodiments, the NO generator includes an interlock to prevent insertion and/or removal of a scrubber cartridge. In some embodiments, the interlock is activated during NO treatment to prevent a user from removing a scrubber cartridge and interrupting therapy. Reactant Gas Scrubbing In some embodiments, reactant gas is scrubbed to remove VOCs and other contaminants that may be present in the environment prior to passing through the plasma chamber. VOC removal from reactant gas can be important in two ways: (1) it controls the inputs to the plasma chamber to limit the types of chemical reactions occurring within the plasma chamber, and (2) it mitigates against VOC cross-sensitivity in sensors within the pneumatic path, such as the NO sensor. In some embodiments, the reactant gas scrubber contains one or more of activated charcoal, molecular sieve material, or cage capture material. The reactant gas scrubber can be a stand-alone scrubber, or combined with an inlet filter, product gas scrubber, electrode and/or other disposable and semi-disposable components of a NO generation system. Extrusions that Scrub In some embodiments, a tube or conduit for the flow of product gas includes a material for scrubbing NO2. In some embodiments, a material that sequesters NO2is coated along a surface of an extrusion. In some embodiments, the ID of a tube is coated. Coatings can be made from one or more NO2scrubber material alone. In one embodiment, a third material is used to bind the NO2scrubber material to the substrate tubing material. In some embodiments, a NO2scrubbing material is mixed with a matrix material that adheres to the substrate tubing material. In some embodiments, the tube is comprised of a co-extrusion where the inner extrusion is comprised at least in part of an NO2-scrubber material. In some embodiments, the entire tube is comprised of a material that has been compounded with a NO2-scrubber material. In some embodiments, a polymer such as polyurethane or PEBAX compounded with, for example, soda lime. In some embodiments, a tube 990, as shown in The level of scrubbing of a coated tube is a function of one or more of available tube surface area, tube length, coating chemistry, available scrubber material surface area, gas velocity, gas flow state (laminar vs. turbulent), density of the coating, age of coating, and environmental factors (pressure, temperature, humidity). Gas Sampling In some embodiments, sample gases are chilled prior to or within a water trap to promote water condensation and improve water removal from a gas sample. In some embodiments, this eliminates the need for Nafion tubing to reduce the humidity of the gas sample. In some embodiments, cooling is achieved by one or more of a thermoelectric cooler, ice, and a pressure drop. In some embodiments, a gas sample passes through Nafion tubing where a heating element increases the temperature and lowers the relative humidity outside the Nafion tubing thereby removing water content from the gas sample. In some embodiments, the humidity of the gas sample is measured and the temperature of the heating element is modulated to maintain gas sample humidity within a target range. In some embodiments, the target gas sample range is 30 to 70% relative humidity. In some embodiments, a thermoelectric cooler is used to cool a water trap while simultaneously warming the environment around Nafion tubing to dry sample gas. In some embodiments, sample gases are passed through and/or near desiccant that removes excess humidity. In some embodiments, sample gases pass through Nafion tubing that is located in a bed of desiccant. In some embodiments, desiccant is in the form of beads. In some embodiments, desiccant is selected to maintain a particular humidity range so that it absorbs humidity from excessively humid sample gas and provides humidity to excessively dry sample gas. In some embodiments, desiccant is packaged with a water trap so that it is replaced periodically by the user without adding a use step. NO sensors can drift over time. In a scenario where a NO sensor drifts up, a NO controller can generate a high NO alarm based on false information. This is a concern because, a typical NO delivery system will stop therapy in the presence of a high inhaled NO alarm. In some embodiments, a NO generation system can check the validity of a high NO alarm by assessing NO production levels to determine whether or not NO production has increased. NO production can be assessed by measurement of one or more of product gas NO concentration, plasma activity (current, voltage, power, light emissions), diluted product gas NO concentration, product gas flow rate, reactant gas flow rate, and other parameters related to NO production. By confirming that NO production has not changed, there is no mechanism for inhaled NO concentration to increase and a NO generation and delivery system can infer that the inhaled NO concentration sensor has drifted up. This enables a NO generation and delivery system in the presence of a high inhaled NO reading to decrease the severity of the alarm condition and continue treatment. Compensation for Inhaled Gas Mixture The gas mixture within the inspiratory limb of a device varies from treatment to treatment. Some patients receive supplemental oxygen while others receive supplemental Helium. Oxygen Compensation Inhaled oxygen levels can range from atmospheric (21%) to pure oxygen (100%). The density of air is 1.225 kg/m3 while the density of oxygen is 1.429 kg/m3. Worst case, a system calibrated at atmospheric levels of oxygen to operate without inspiratory gas mixture compensation will experience a 16% measurement error in inspiratory mass flow measurements when 100% oxygen is utilized. Compensation for mass flow measurement errors can be made for various oxygen fractions within the inspiratory limb. In some embodiments, a controller determines the oxygen level and/or nitrogen level within the breathing circuit based on an oxygen sensor measurement and/or user input and adjusts the calibration of the inspiratory flow sensor, accordingly. In some embodiments, the NO generation system measures the nitrogen content within the inspiratory gas and infers that the balance of the gas is oxygen as an input to the mass flow measurement compensation. In some embodiments, the calibration of the inspiratory flow sensor is compensated by looking up an appropriate calibration for the inspiratory flow sensor according to the indicated oxygen level. In some embodiments, the compensation value is based on prior characterization of the sensor with various levels of oxygen. In some embodiments, the compensation is simply calculated based on the ratio of the gas density of the indicated gas mixture vs. the gas mixture the system was calibrated with. In another embodiment, the NO device uses the measured NO concentration in the inspired gas as feedback to the NO generation/delivery system to drive inhaled NO concentrations to the target value. Helium Treatment In some embodiments, the patient inspiratory flow includes helium mixed with air, oxygen and potentially other gases (AKA Heliox treatment). The density of the inspired gas changes, which can affect the calibration of the mass flow sensor in the system by up to a factor of 2. In some embodiments, the system enables the user to enter the amount of helium in the inspired gas and the device treatment controller compensates for the amount of helium in the mass flow sensor calibration. In some embodiments, a NO generation system includes a helium sensor to measure the fraction of helium in the inspired gas. This measurement is then used as an input to the controller to shift the calibration of the inspired gas mass flow sensor, accordingly. In another embodiment, a sensor measuring inhaled NO concentrations is used as feedback to drive inhaled NO concentrations to the target value. Similar approaches can be utilized for other supplemental inspiratory gases and combinations thereof that can be sensed. Pulsed NO Delivery Constant Duration NO Pulsing Pulsed NO delivery can allow for savings in energy and delivering NO to specific parts of the lung. In some embodiments, a NO generator and/or delivery system always generates NO pulses of the same duration. In one embodiment, all pulses last 0.5 seconds. In some embodiments, a NO generator and/or delivery system does one or more of the following to accurately dose a patient while delivering constant duration pulses: alter pulse flow rate, alter pulse concentration, alter pulse onset timing with respect to breath initiation, and dose a subset of breaths (breath skipping). In some embodiments, a NO generation and/or delivery system delivers pulses to a patient based on a dithering algorithm that tracks NO demand vs. NO delivered over time such that a new pulse is delivered to the patient whenever the NO demand exceeds NO delivered. Patient Indication Compensation In some embodiments, a NO delivery device alters the NO pulse strategy according to the patient diagnosis, as indicated by an external user (care provider), or patient, or based on input to the NO generator. As an example, Interstitial Lung Disease (ILD) is a clinical condition where the lung tissue of a patient scars up, loses its elasticity and has reduced compliance. Patients have to labor with their respiratory muscles to expand their lungs to bring in enough air and often cannot bring in sufficient air. Thickening of the gas exchange membrane in the air sacs (alveoli) with scar tissue and reduced ventilation in heavily scarred areas of the lung lead to low oxygen levels systemically. ILD patients typically have a breathing waveform that can be identified by its rapid transitions from inhalation to exhalation, faster than normal respiratory rates, and lack of a pause after exhalation. These patients can benefit from receiving NO throughout the breath, so that blood vessels in healthier regions of the lung can be dilated leading to reduced blood flow in the sickest part of the lung. It follows, that a NO delivery device should dose the early part of inspiration in these patients, and not the final portion of the breath that travels to the anatomic the sickest lung and the dead space. This same approach for pulsed dosing is applicable to patients with a left ventricular assist device and pulmonary hypertension even if the entire lung is healthy and able to take up oxygen. Another patient indication is Chronic Obstructive Pulmonary Disease. These patients tend to have one or more diseased regions of the lung with the remaining lung more or less healthy. Medical research has shown that these patients tend to recruit the healthy parts of the lung before the unhealthy parts of the lung during inhalation. NO dosing of the unhealthy parts of the lung can result in increased blood flow to the unhealthy parts and actually decrease patient oxygenation overall. Thus, it is beneficial in these patients as in ILD to dose only an initial portion of the patient inspiration. The fraction of the inspiration that can be dosed to benefit the patient will vary from patient to patient. Patient oxygenation is an indication of patient well-being. This parameter can be measured by an SpO2 sensor built into the NO delivery device or measured by an external device and communicated to the NO delivery device. In some embodiments, a NO delivery device that measures or receives SpO2 information from an external device can determine an optimal fraction of inspiration to dose using a closed-loop control scheme (this could also apply to ILD). In some embodiments, the fraction of the breath that should be dosed is entered into the device by an external user. Gas Sensor Calibration Sensors within a NO generation and/or delivery system require calibration from time to time with the gas sensors being no exception. State of the art calibration involves a 15 minute process whereby the user connects various calibration gases to the gas sensor bank of a gas analyzer so that the system can obtain high and low readings for a calibration of each type of gas sensor. Oxygen sensors can be calibrated using atmospheric air (20.8% oxygen) and another value. In some embodiments, a gas containing no oxygen (e.g. NO in a balance of N2) is used to provide a zero value for the oxygen sensor. In some embodiments, oxygen from the hospital supply is utilized to obtain a high calibration reading (e.g. 100% O2). In some embodiments, NO and NO2gas sensors are calibrated using a calibration kit. A calibration gas kit (CGK) provides automated calibration of a 3P-001 device with known gas concentrations. In one embodiment, the GCK includes calibration gas cylinders, flow regulators, tubing, one or more smart chips and unique connectors that resemble the components that already interface with the NO device (e.g. a water trap, a scrubber cartridge, or a gas conditioning cartridge). In some embodiments, power to the CGK is provided by and controlled by the NO generation/delivery device. The t90 (i.e. the rise time of a gas sensor from 10% to 90% of full scale) of an electrochemical sensor can be very slow with some approaching 400 seconds. Some gas sensor manufacturers recommend that calibration gas flows past the sensor for the lessor of either 10 minutes or when the sensor signal has not changed for 30 seconds for each sensor prior to taking a calibration reading. In the gas calibration kit shown, the two cylinders on the left are utilized to calibrate gas sensors that measure inspired concentrations of NO and NO2. A zero value for NO and NO2can either be obtained from the Oxygen calibration step or from ambient air. In some embodiments, a calibration gas cylinder includes NO and NO2in a balance of N2, in which case only one inhaled gas calibration cylinder is required in the kit. Example concentrations for the NO and NO2calibration gases are 100 ppm and 5 ppm, respectively. The kit also includes a gas cylinder for calibration of an internal, high concentration NO sensor furthest to the right. In some embodiments, the high calibration gas concentration is 2500 ppm. Other embodiments calibrate the internal high NO sensor with gas ranging from 1000 ppm to 3000 ppm. In the embodiment depicted, the gas calibration kit interfaces with a NO device through existing interfaces. Sample inspiratory gas normally flows through a water trap into the system. Hence, a water-trap shaped-connector enables the GCK to introduce calibration gases to the inspired gas measurement sensors. The GCK provides calibration gas under pressure. In some embodiments, the GCK pushes calibration gases through the inhaled gas sensor path. In other embodiments, the gas sampling pump within the NO device pulls calibration gas into the NO device from the GCK. Typically, the flow rate during calibration is identical to the flow rate during operation (e.g. in the range of 100 to 300 ml/min). The high concentration NO calibration gas enters the NO system using a connector that resembles a NO2scrubber. In the embodiment depicted, power is provided to the GCK through electrical connections established with the pneumatic connections. This power can be used to open gas valves, power a microprocessor, read from memory devices, and other uses. In some embodiments, the GCK includes a battery or receives power from a wall outlet or other external source. In some embodiments, data are exchanged between the NO device and the GCK. For example, the GCK can provide the NO device with the actual concentration of the calibration gases, their expiration date, lot number, and a count of calibrations performed. The NO device can reject calibration gases that are expired or have been used a sufficient number of times that the calibration gas concentration may have been altered. In some embodiments, the mechanical interfaces include a smart chip connection, similar to what is used by the system to communicate with disposable components. The NO delivery device reads the smart chip and identifies the component inserted to be part of a GCK and can automatically enter a calibration mode and/or calibration sequence. The smart chip can include information including but not limited to: cal gas concentration, Cal gas lot number, Cal gas expiration date, CGK serial number, and number of calibrations remaining. Ambient pressure changes resulting from altitude and/or weather shall be accommodated by the NO generation device (e.g. gas sample pump, recirculation flow controller). User Safety In some embodiments, a NO generation or delivery device measures the ambient air to check that NO and NO2levels are safe for the clinicians. In some embodiments, the NO device utilizes the same sensors that are used to analyze inhaled gas. In some embodiments, a dedicated sensor is used for safety monitoring. In some embodiments, the NO generation device generates an alarm (e.g. audible, visible) when NO2levels exceed a threshold (e.g. 2 ppm). Publications cited throughout this document are hereby incorporated by reference in their entirety. While one or more embodiments of the present disclosure have been described, it is understood that these embodiments are illustrative only, and not restrictive, and that many modifications may become apparent to those of ordinary skill in the art, including that various embodiments of the inventive methodologies, the illustrative systems and platforms, and the illustrative devices described herein can be utilized in any combination with each other. Further still, the various steps may be carried out in any desired order (and any desired steps may be added and/or any desired steps may be eliminated). The present disclosure describes systems and methods for controlling the electrical generation of nitric oxide. In some aspects, a system for generating nitric oxide comprises a plasma chamber housing two or more electrodes in communication with a resonant high voltage circuit configured to send a signal to the plasma chamber for generating nitric oxide in a product gas from a flow of a reactant gas, and a controller configured to generate a pulse width modulation signal having multiple harmonic frequencies to excite the resonant high voltage circuit. The controller is configured to adjust the duty cycle of the pulse width modulation signal, the controller selecting the duty cycle based on a target voltage before plasma formation and a target current after plasma formation in the plasma chamber. 1. A system for generating nitric oxide, comprising:
a plasma chamber housing two or more electrodes in communication with a resonant high voltage circuit configured to send a signal to the plasma chamber for generating nitric oxide in a product gas from a flow of a reactant gas; and a controller configured to generate a pulse width modulation signal having multiple harmonic frequencies to excite the resonant high voltage circuit, wherein the controller is configured to adjust the duty cycle of the pulse width modulation signal, the controller selecting the duty cycle based on a target voltage before plasma formation and a target current after plasma formation in the plasma chamber. 2. The system of 3. The system of 4. The system of 5. The system of 6. The system of 7. The system of 8. The system of 9. The system of 10. The system of 11. The system of 12. A system for generating nitric oxide, comprising:
a plasma chamber housing two or more electrodes in communication with a resonant high voltage circuit configured to send a signal to the plasma chamber for generating nitric oxide in a product gas from a flow of a reactant gas; and a controller in communication with the resonant high voltage circuit for independently controlling a voltage to form a plasma in the plasma chamber and a current in a plasma in the plasma chamber by alternating between two or more duty cycles to independently adjust the amplitudes of the waveform's harmonic frequencies. 13. The system of 14. The system of 15. The system of 16. The system of 17. The system of 18. The system of 19. A method for generating nitric oxide, comprising:
energizing a plasma chamber using a resonant high voltage circuit to generate nitric oxide in a product gas from a flow of a reactant gas; and controlling, using a controller in communication with the resonant high voltage circuit, a voltage that forms a plasma in the plasma chamber and a current that sustains a plasma in the plasma chamber by adjusting a duty cycle of a waveform used to excite the resonant high voltage circuit using multiple harmonic frequencies. 20. The method of RELATED APPLICATIONS
FIELD
BACKGROUND
SUMMARY
BRIEF DESCRIPTION OF THE DRAWINGS
DETAILED DESCRIPTION
Bias Flow*(breath period−inspiratory time)>tidal volume
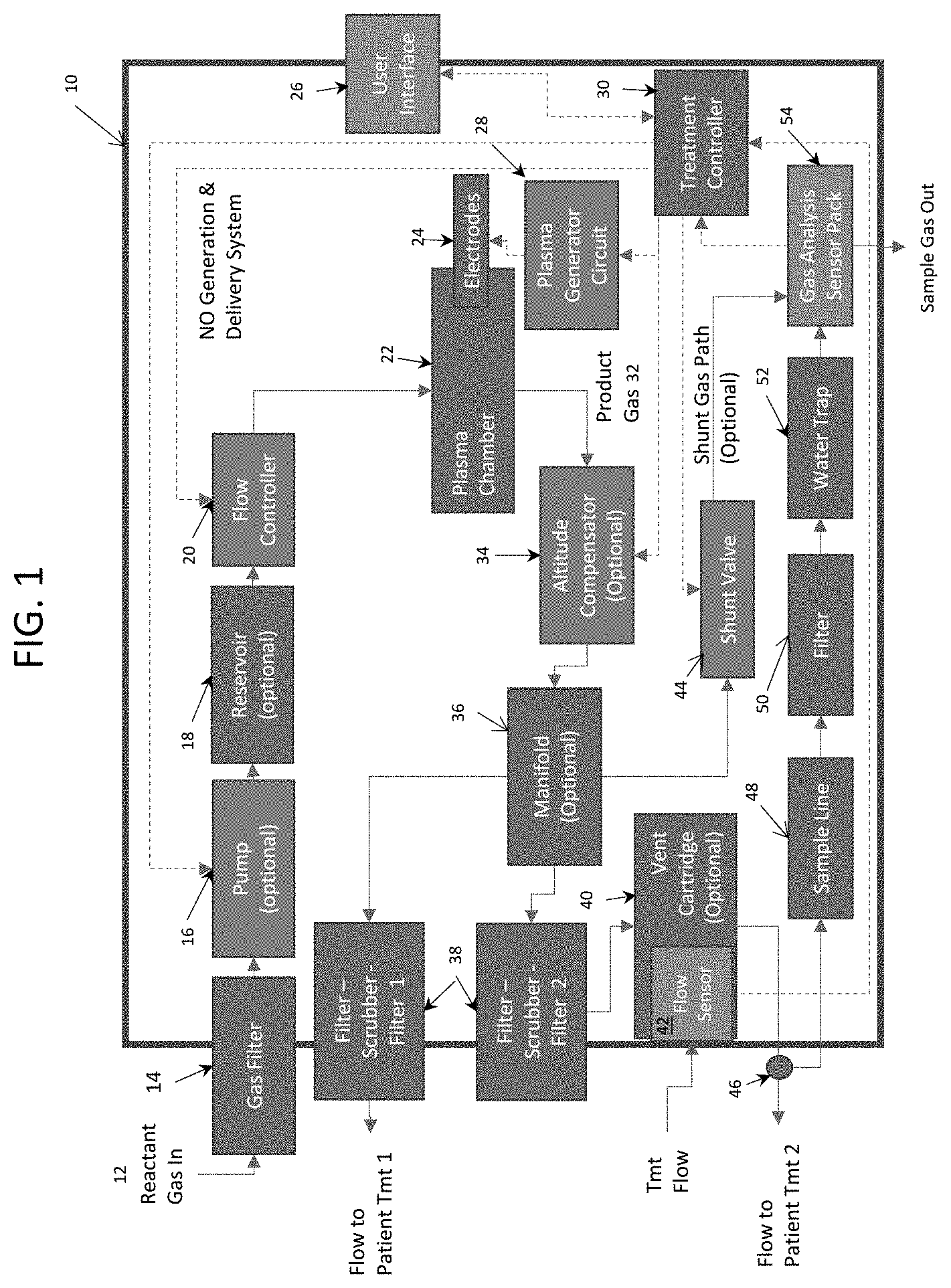
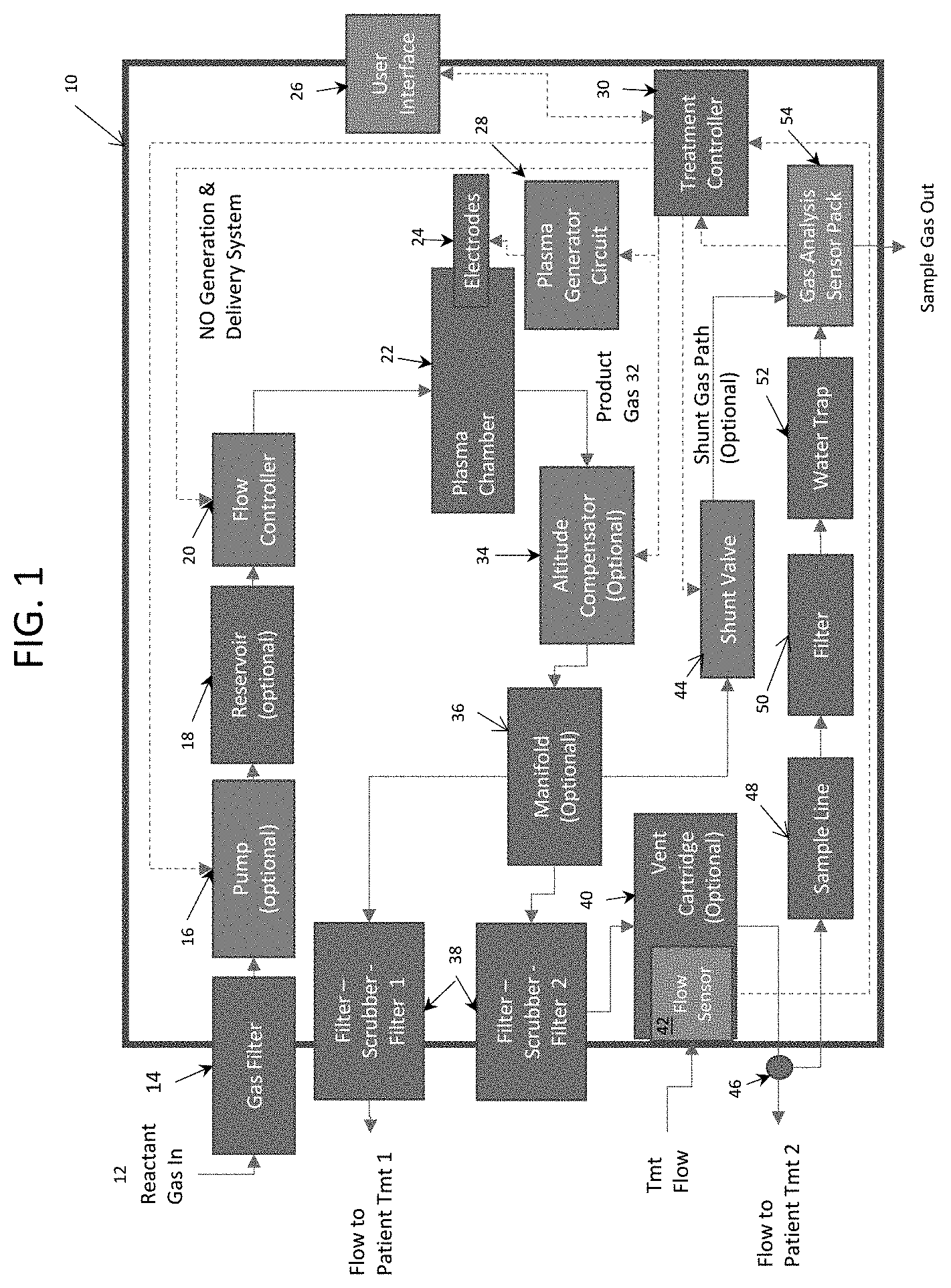
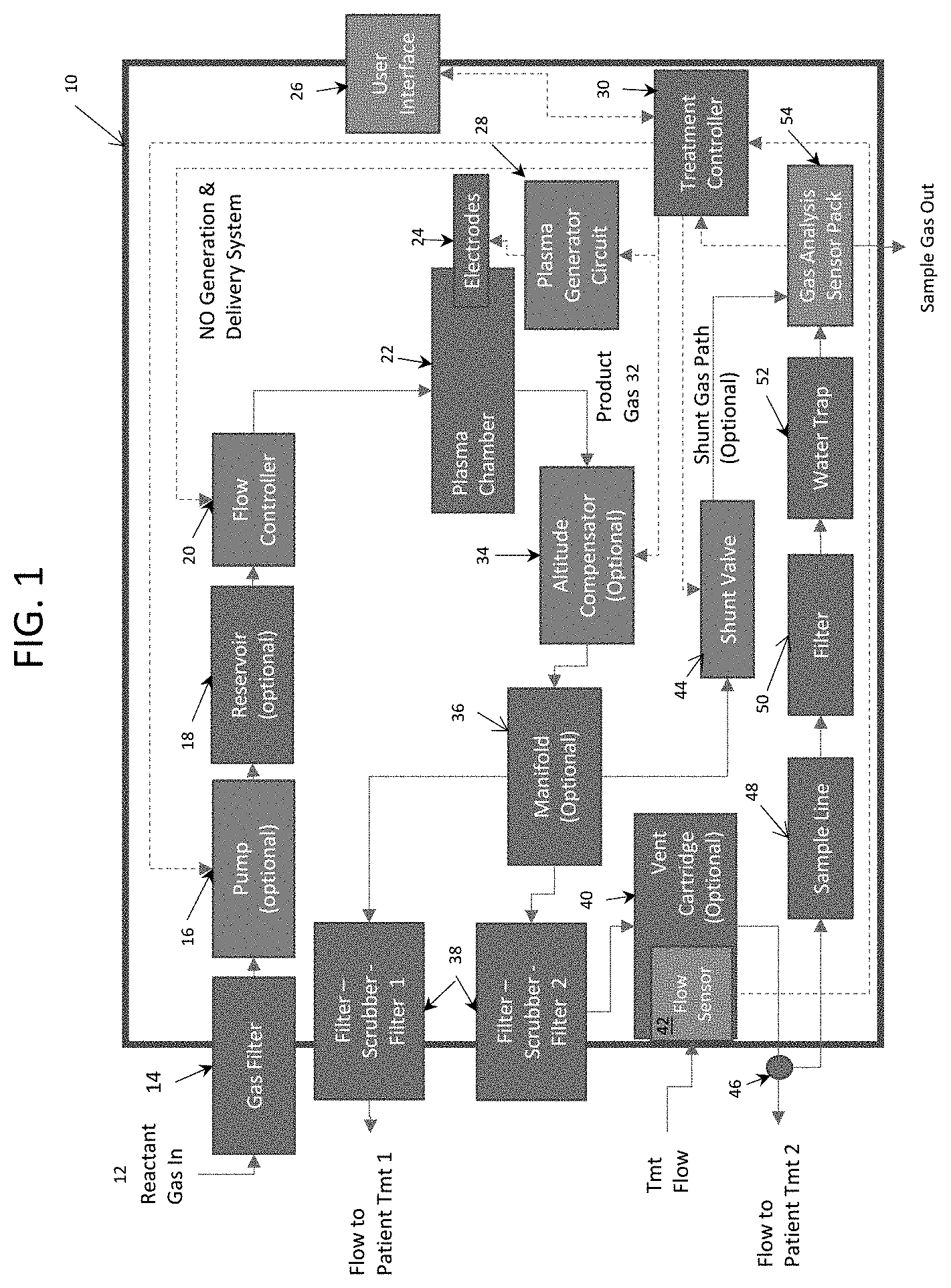
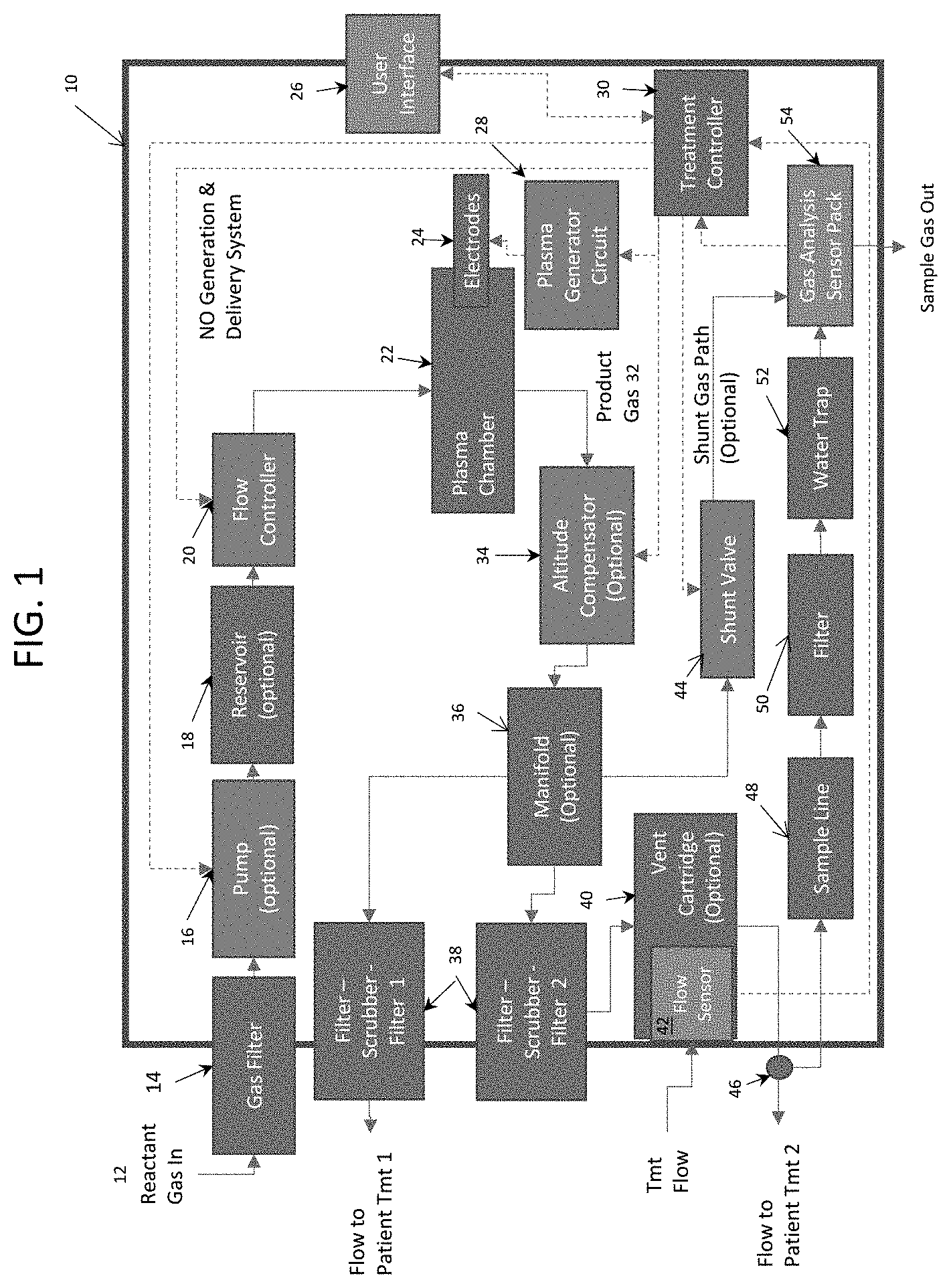

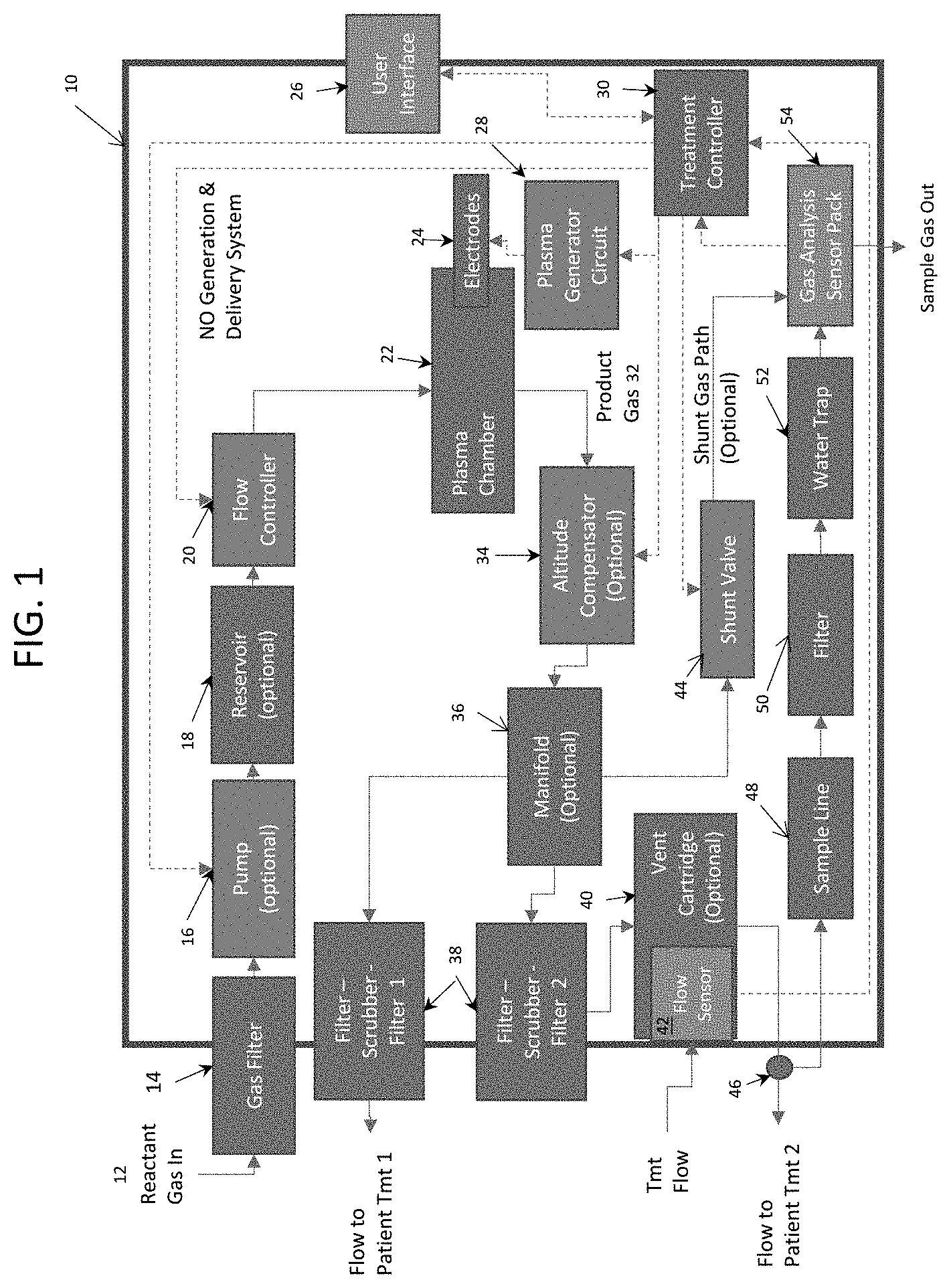
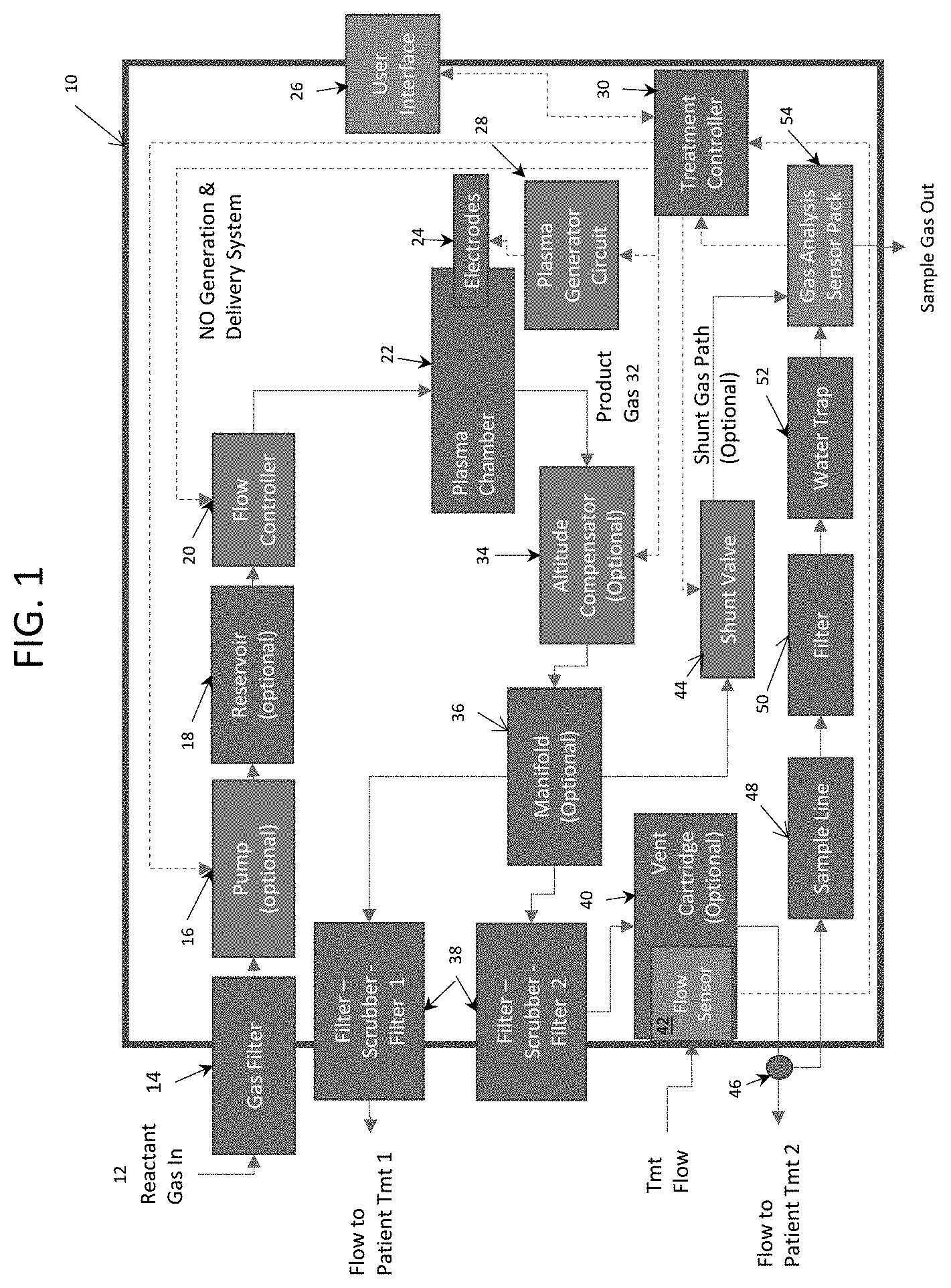
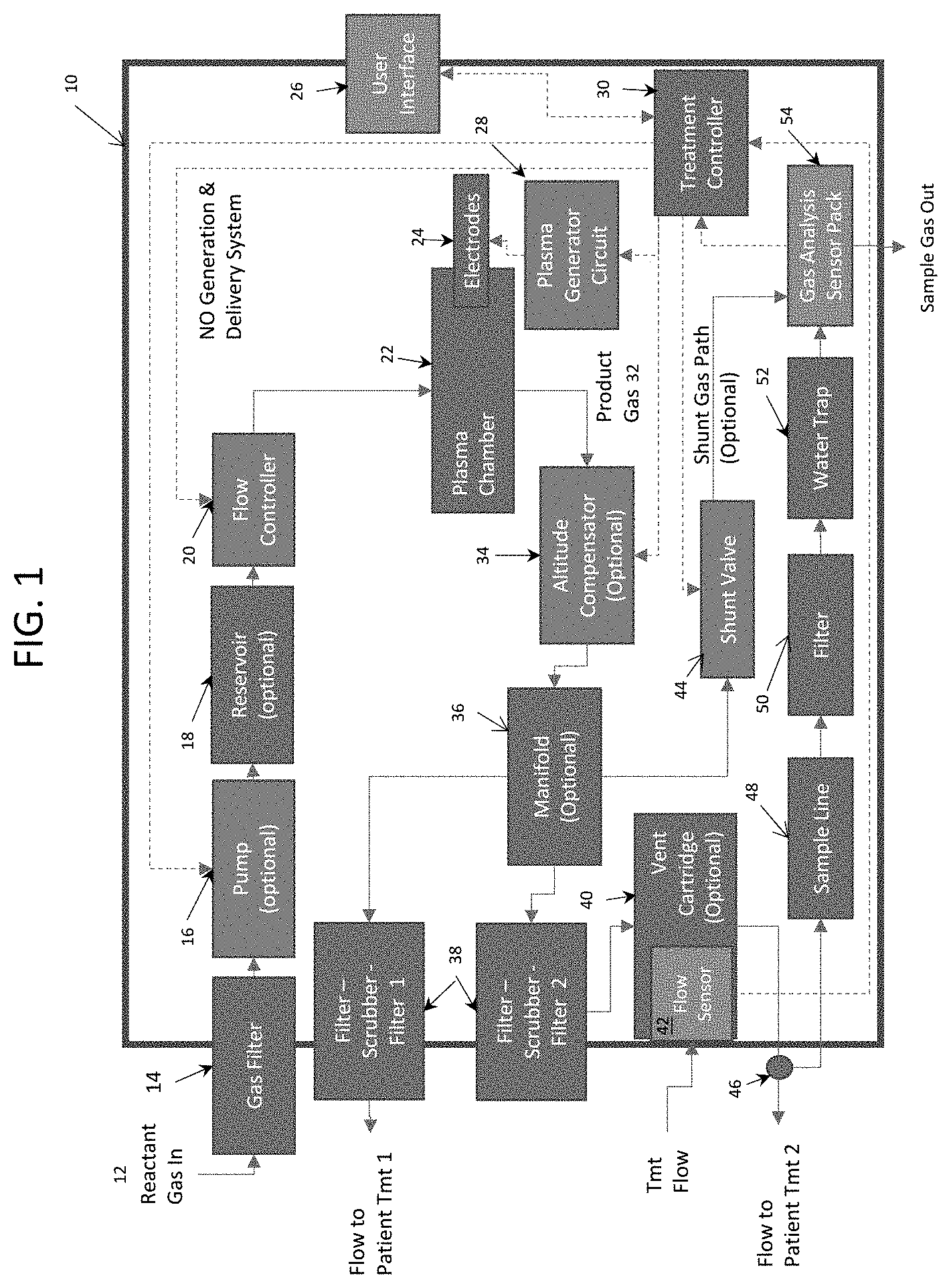
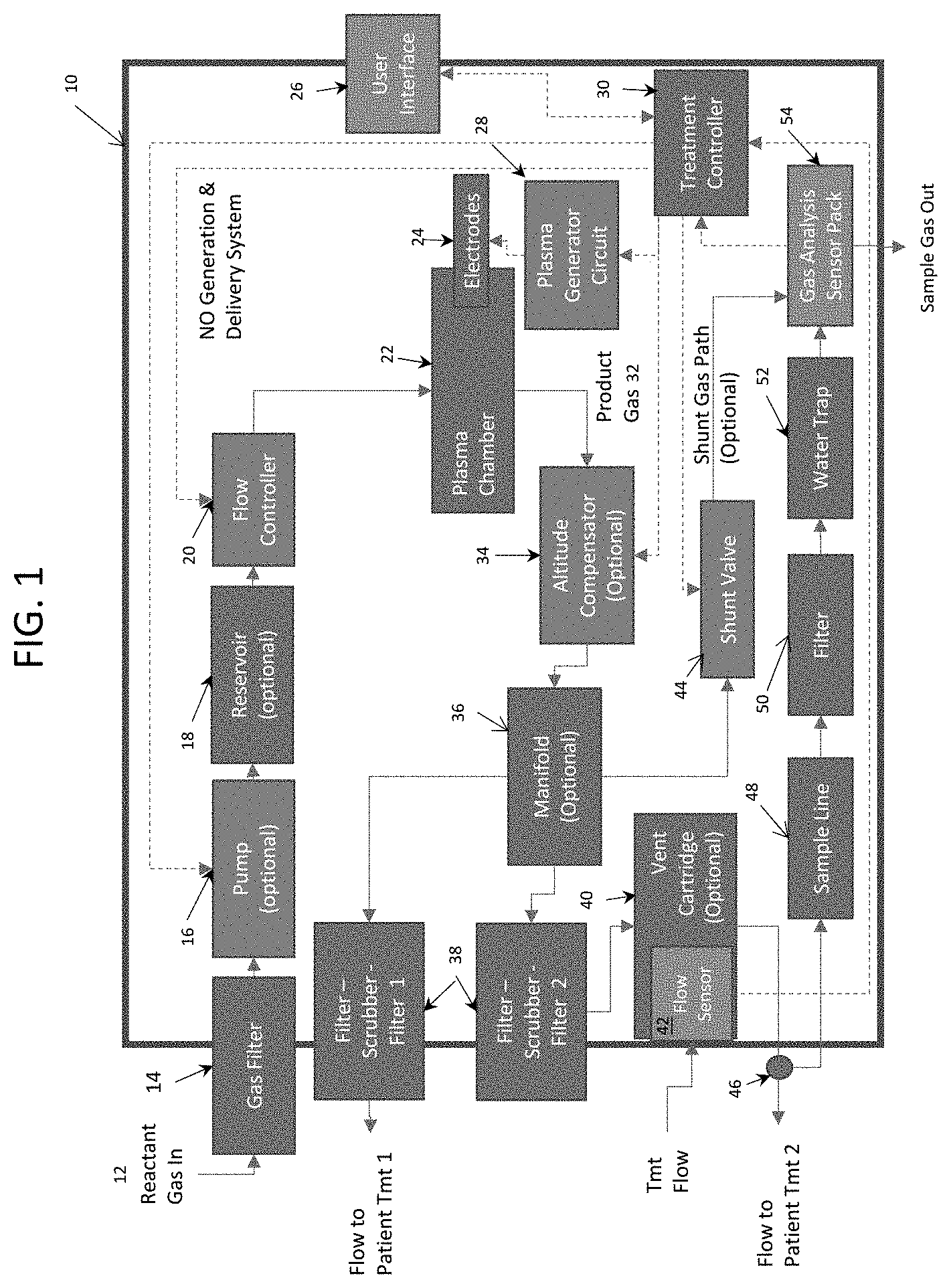
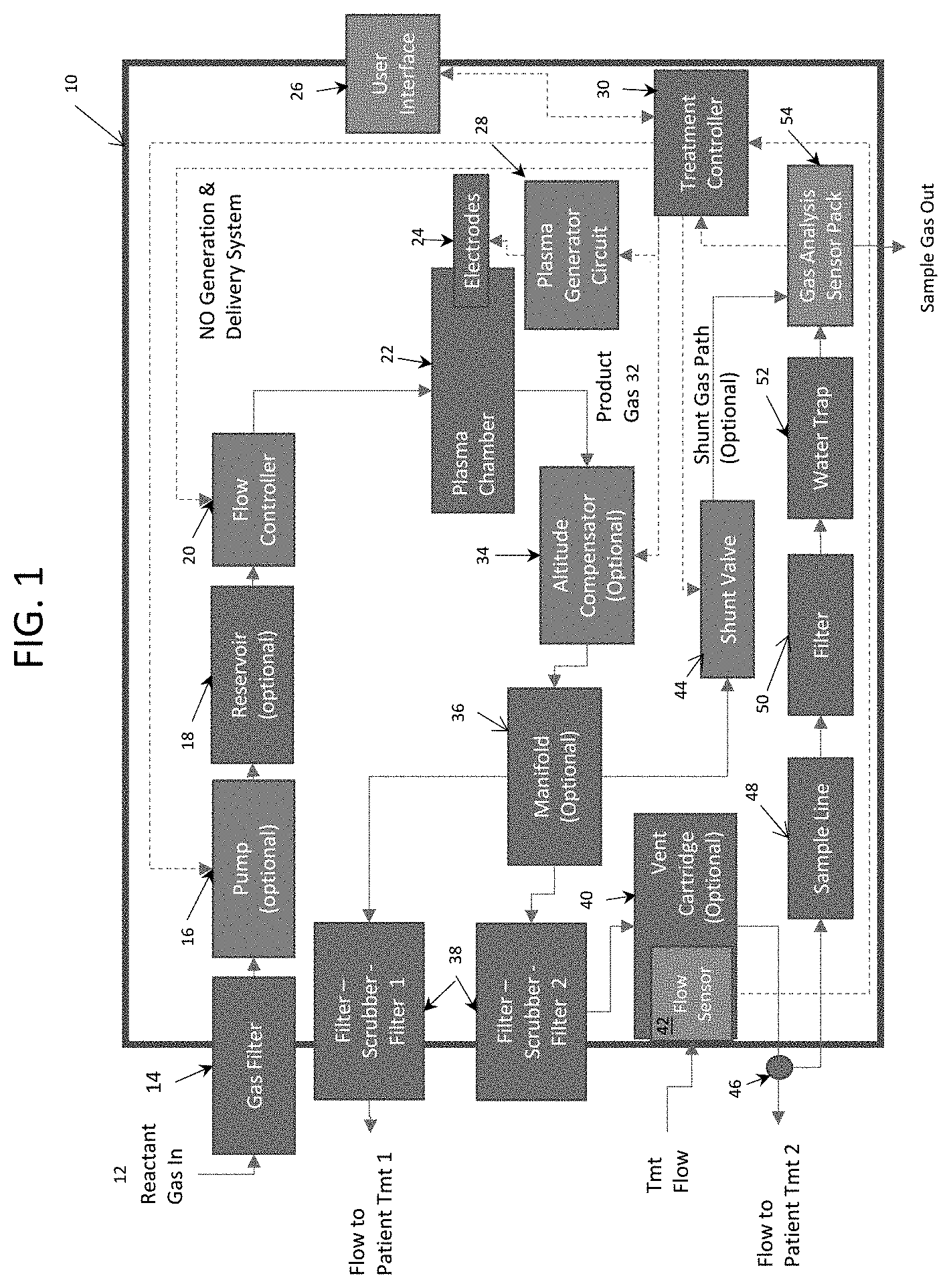
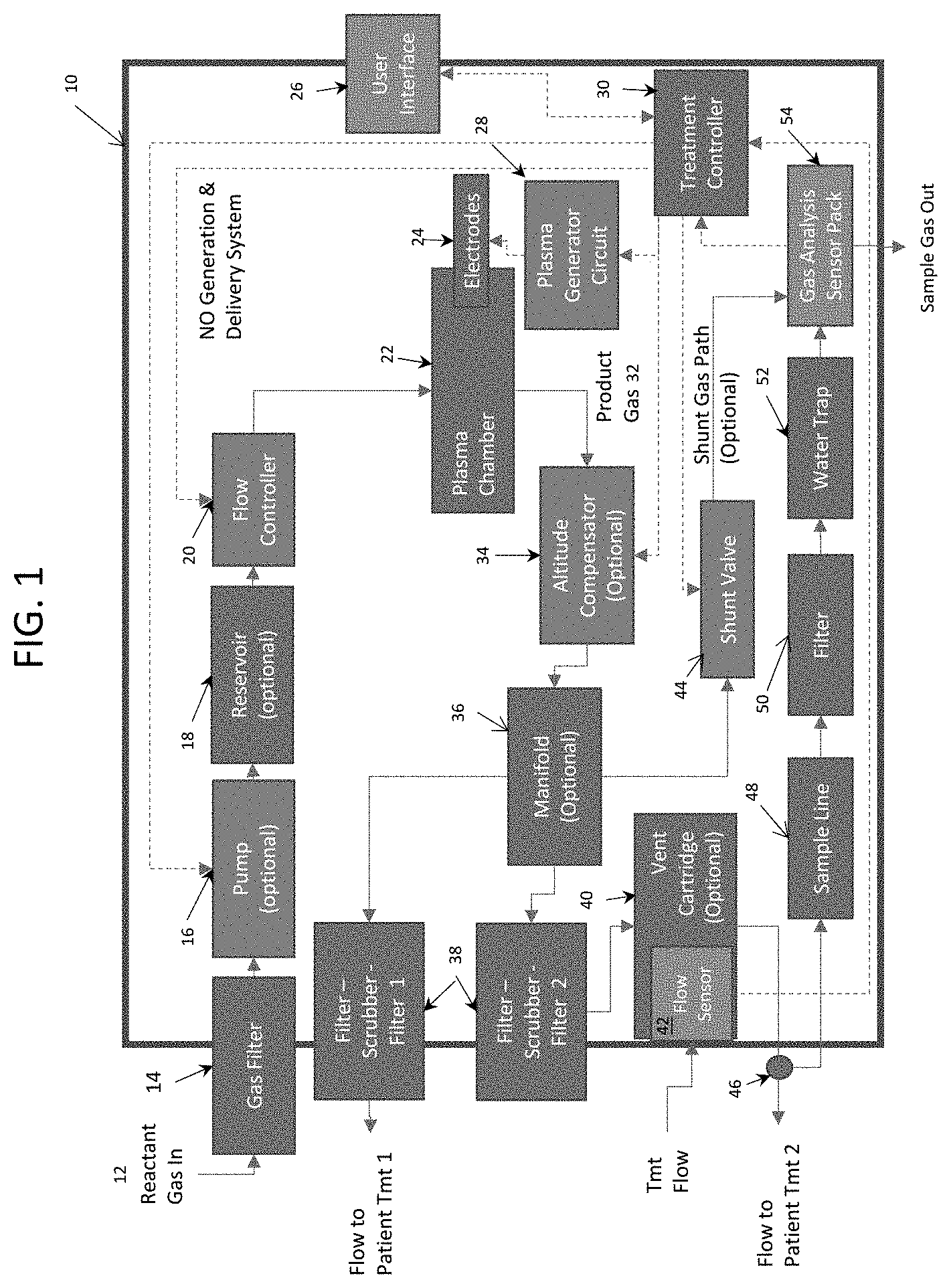
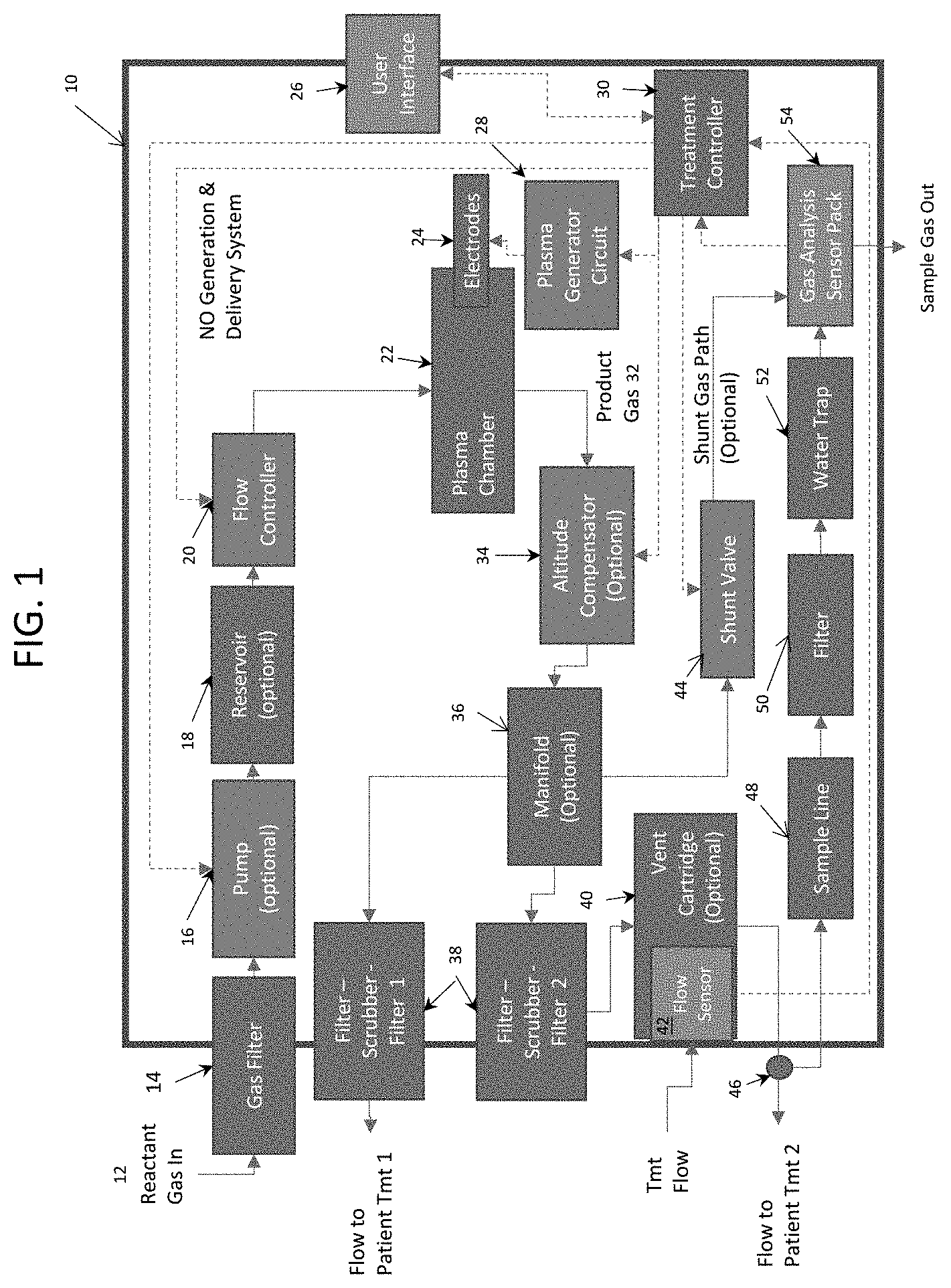
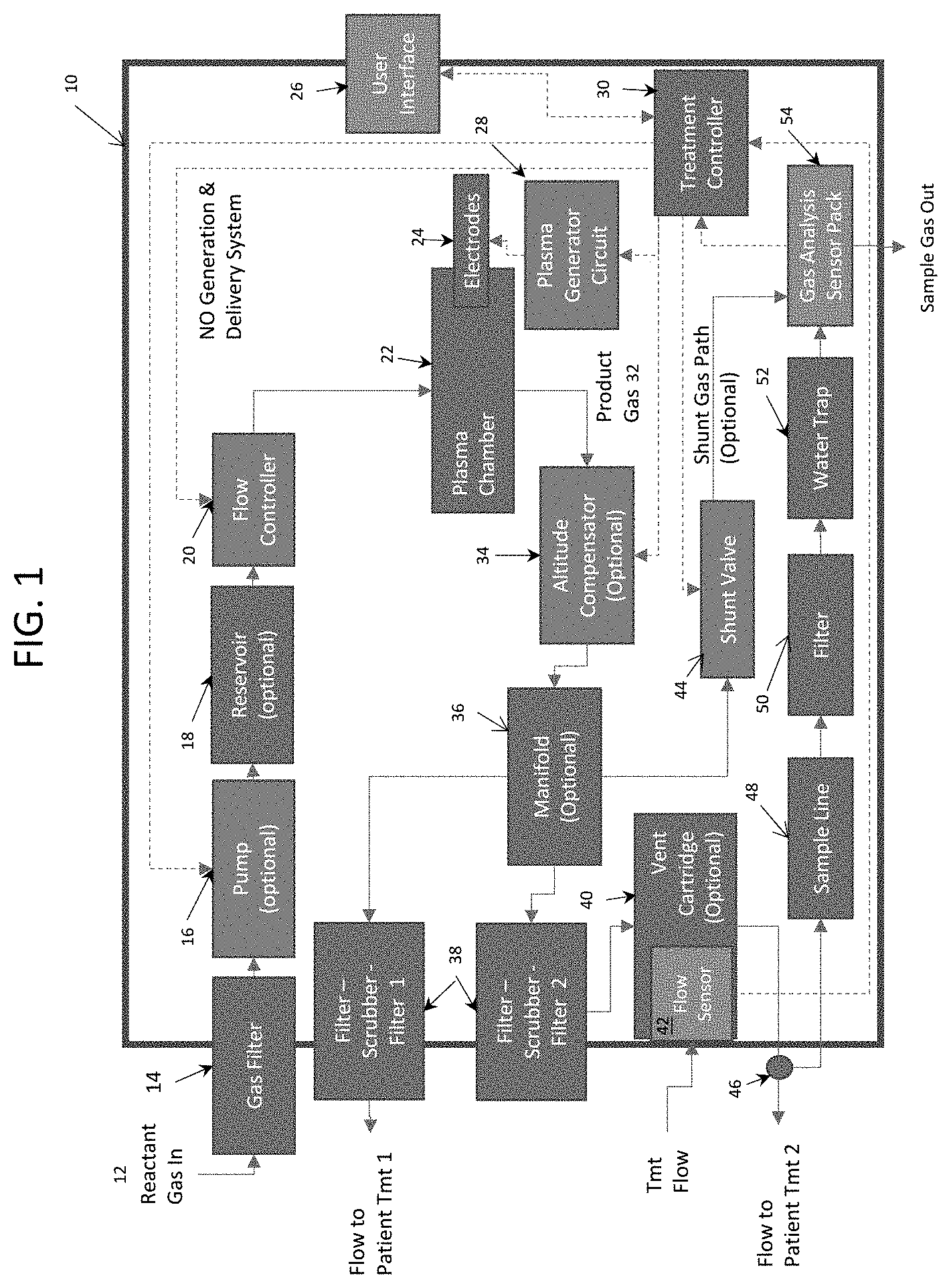
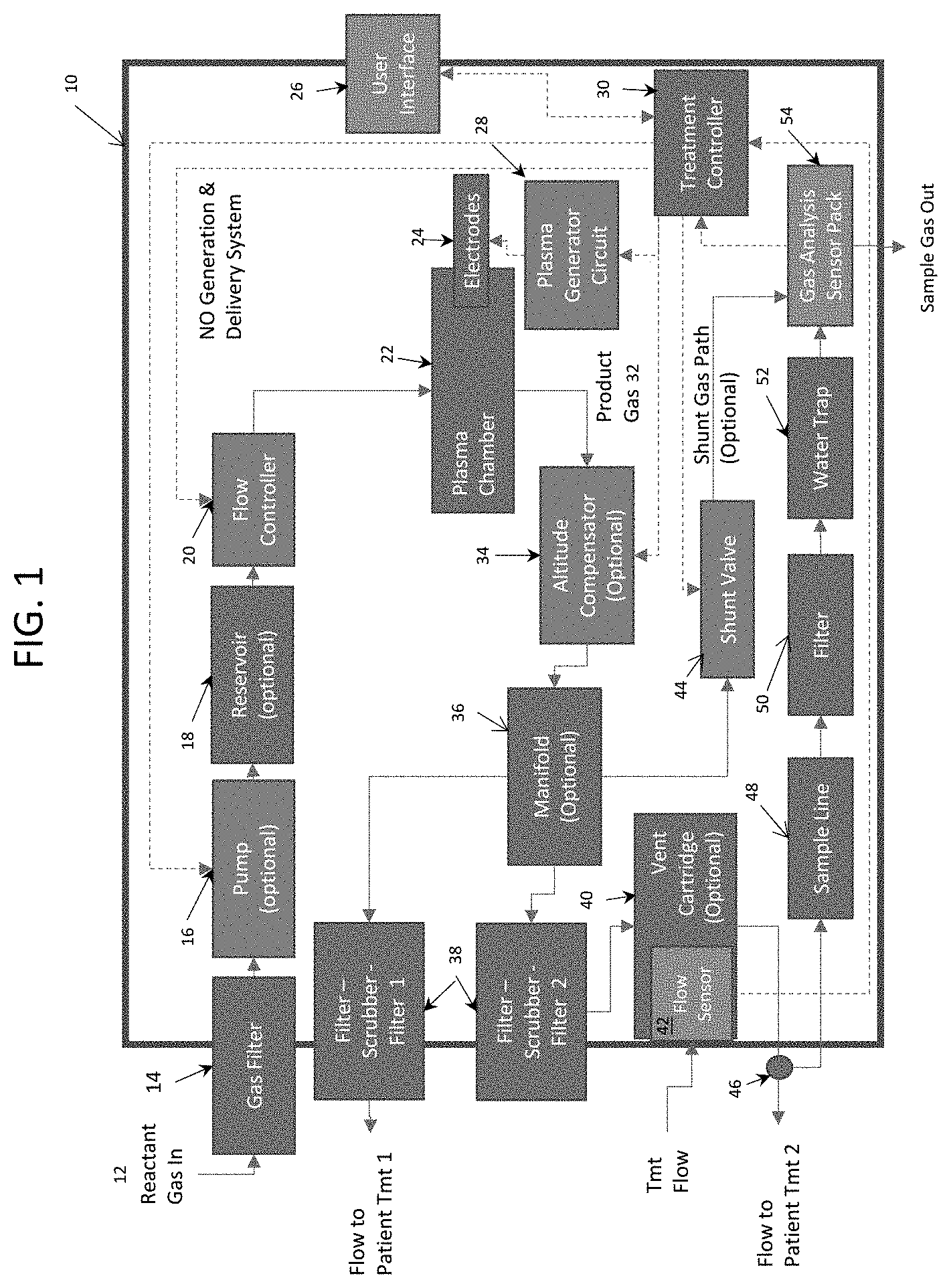
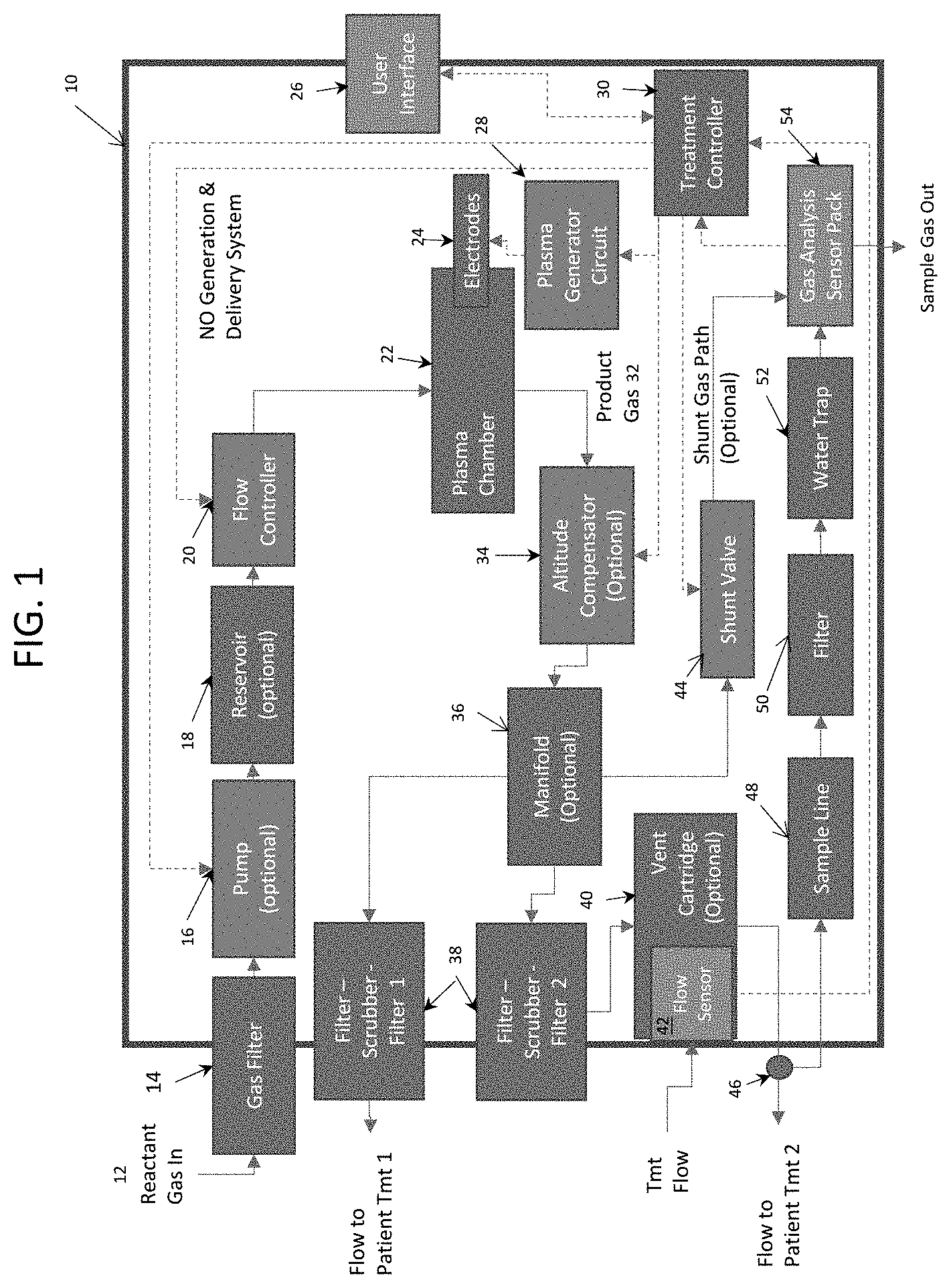
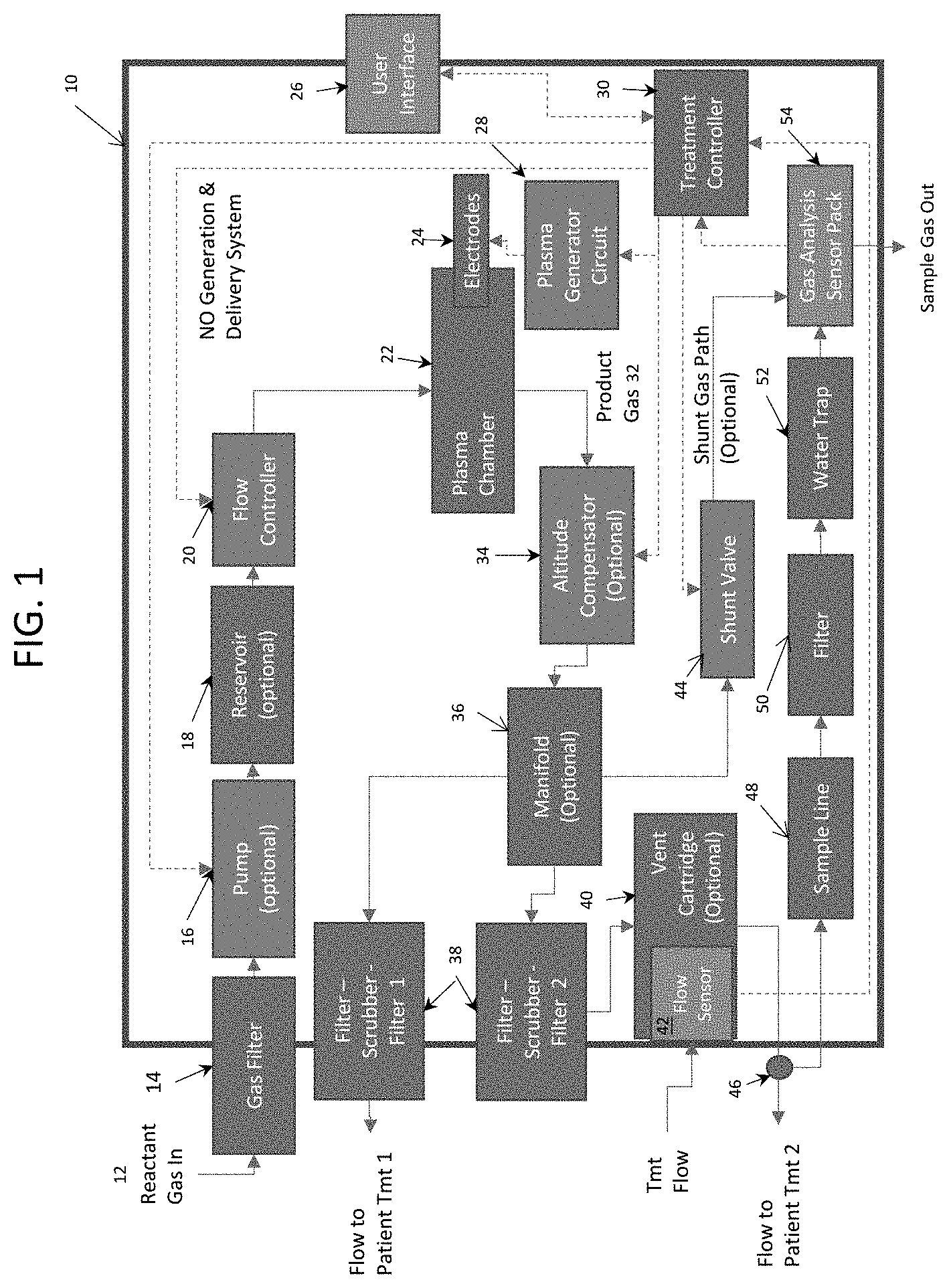
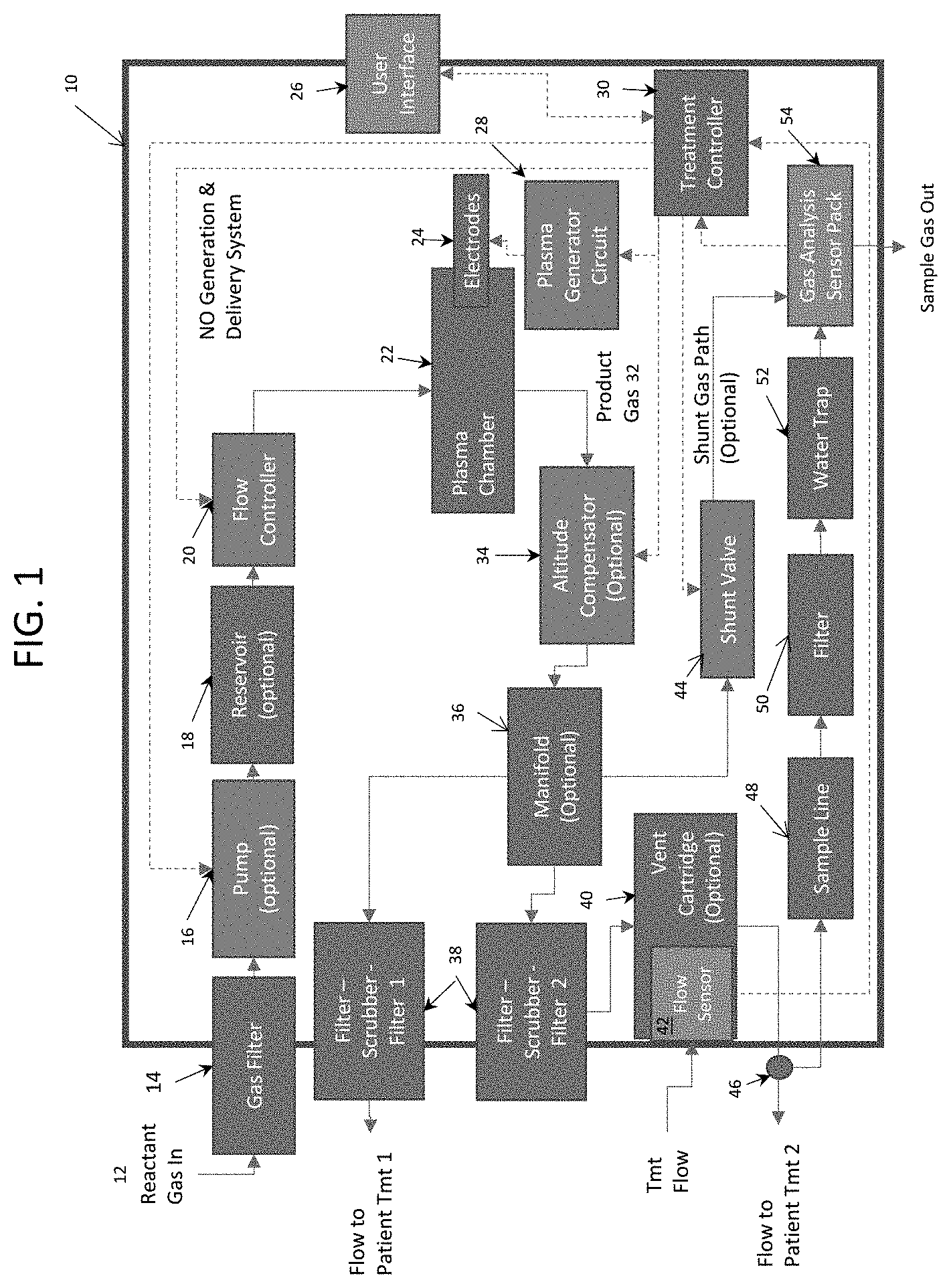
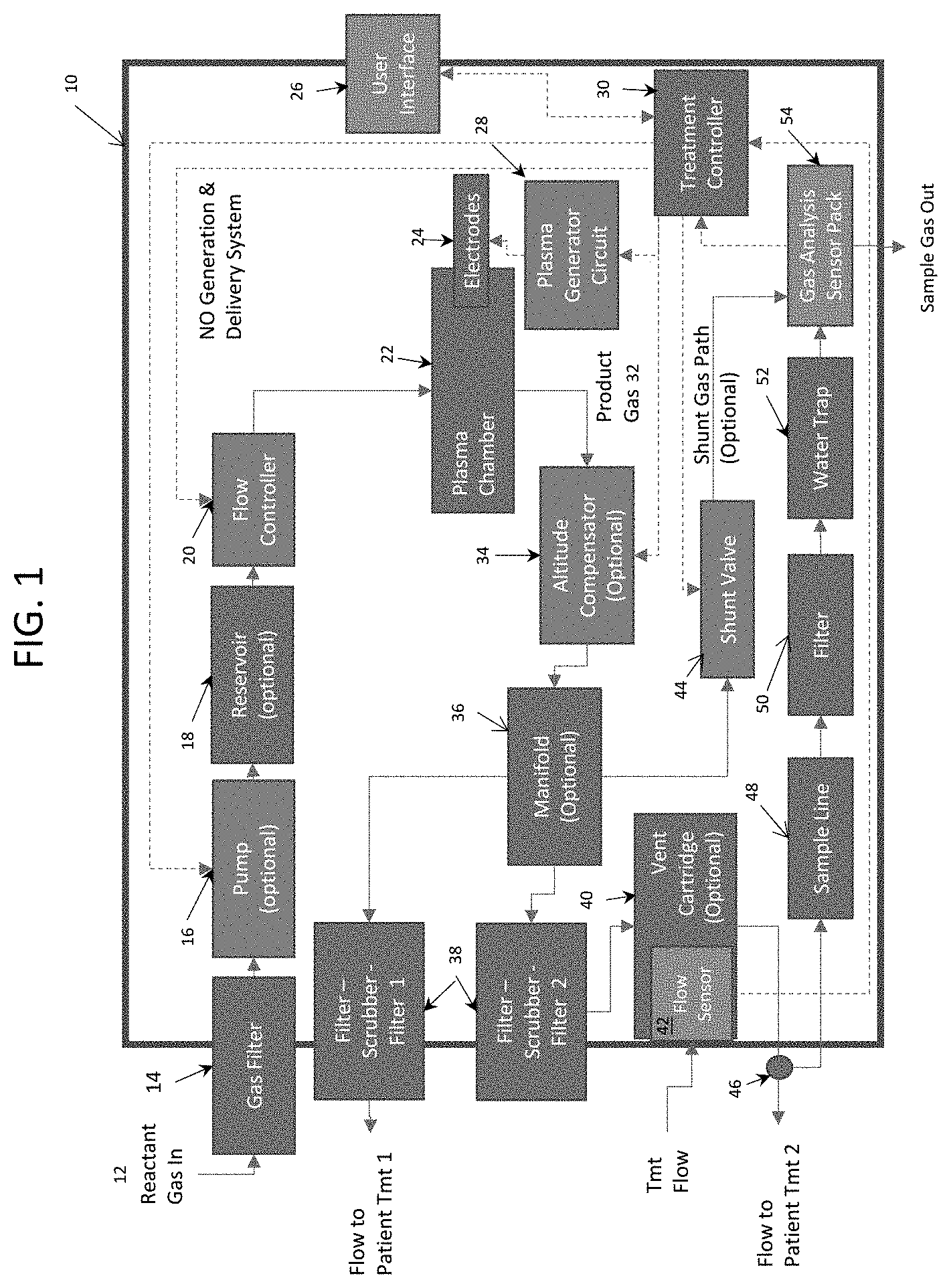
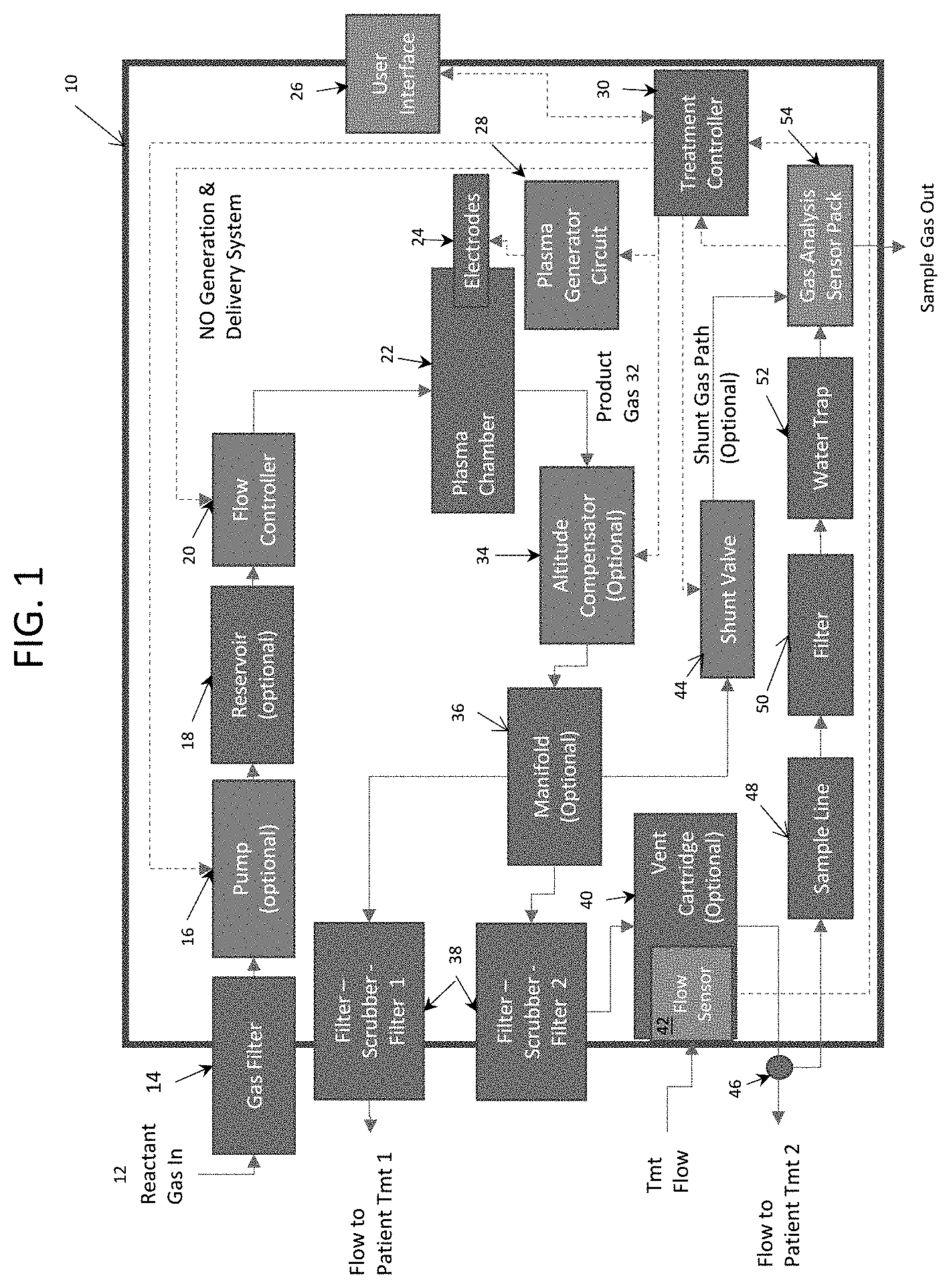
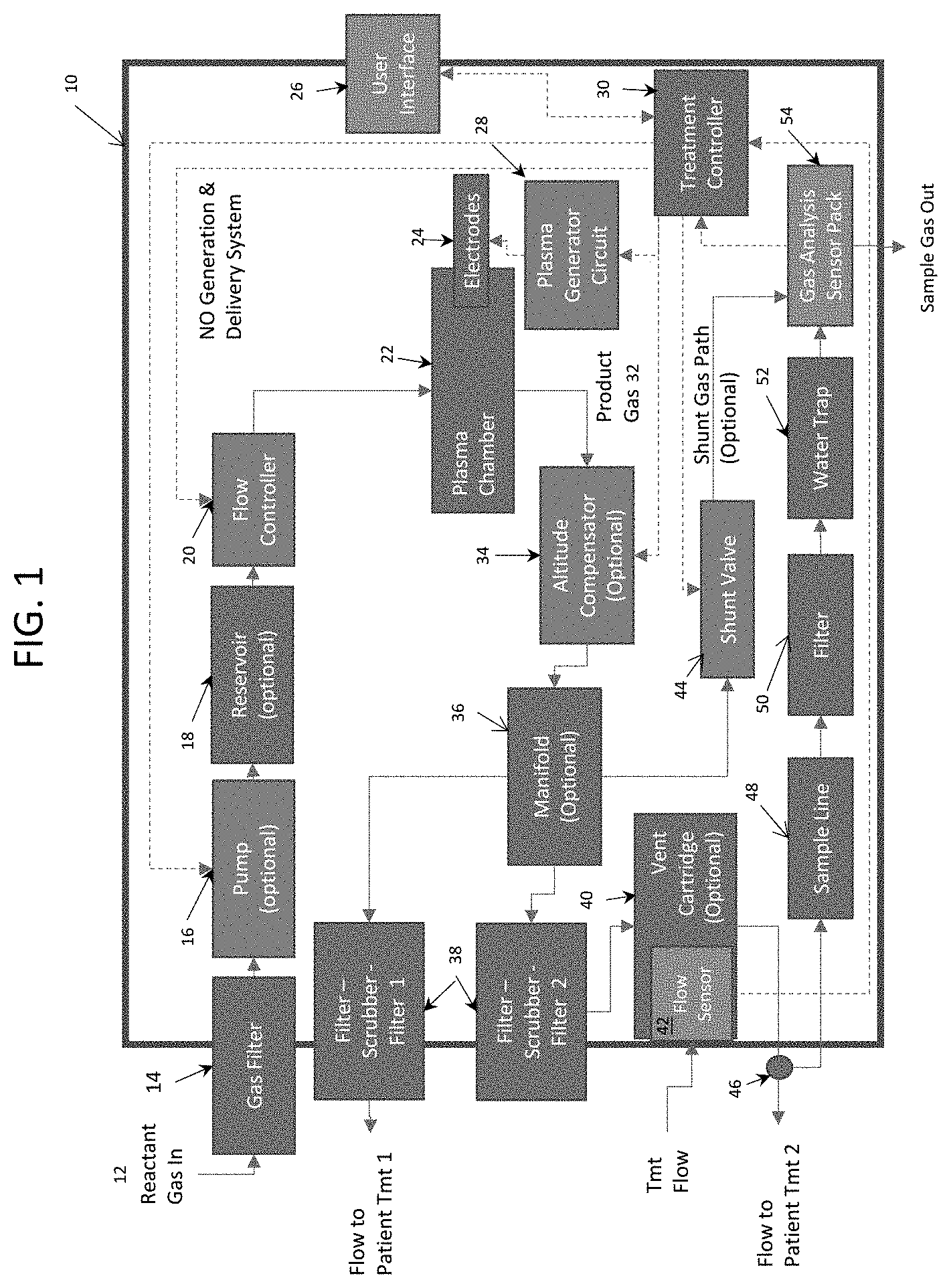
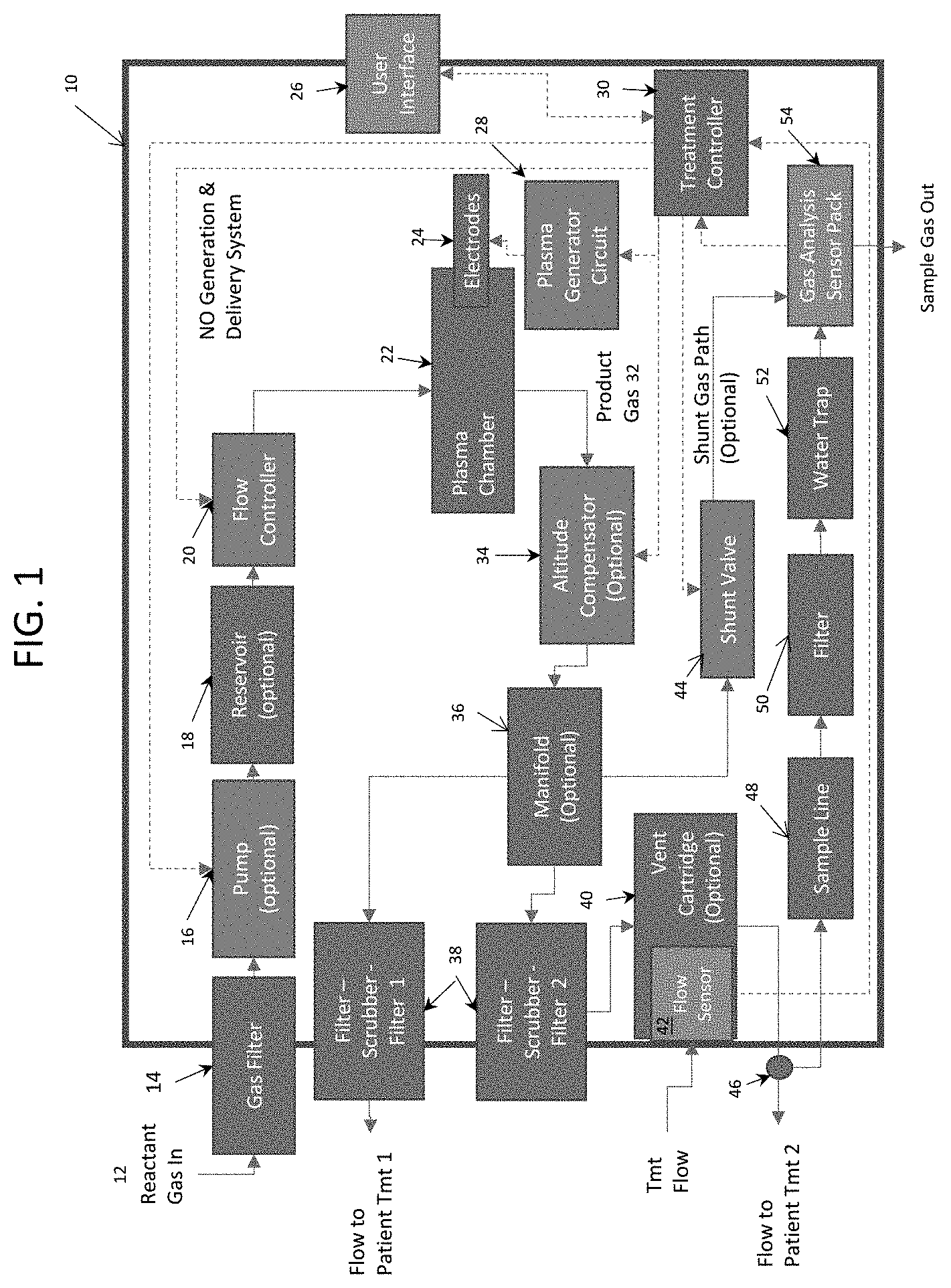
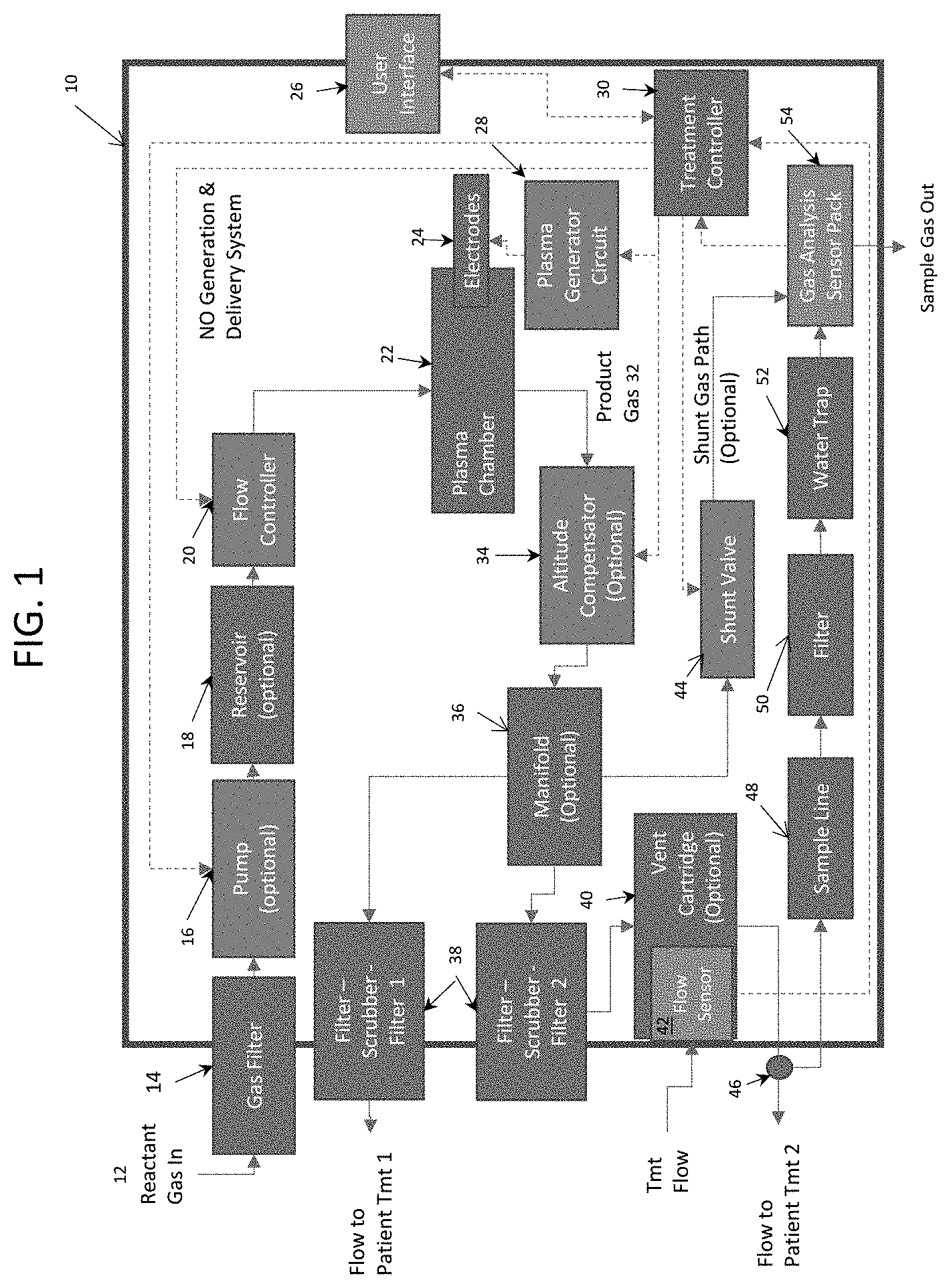
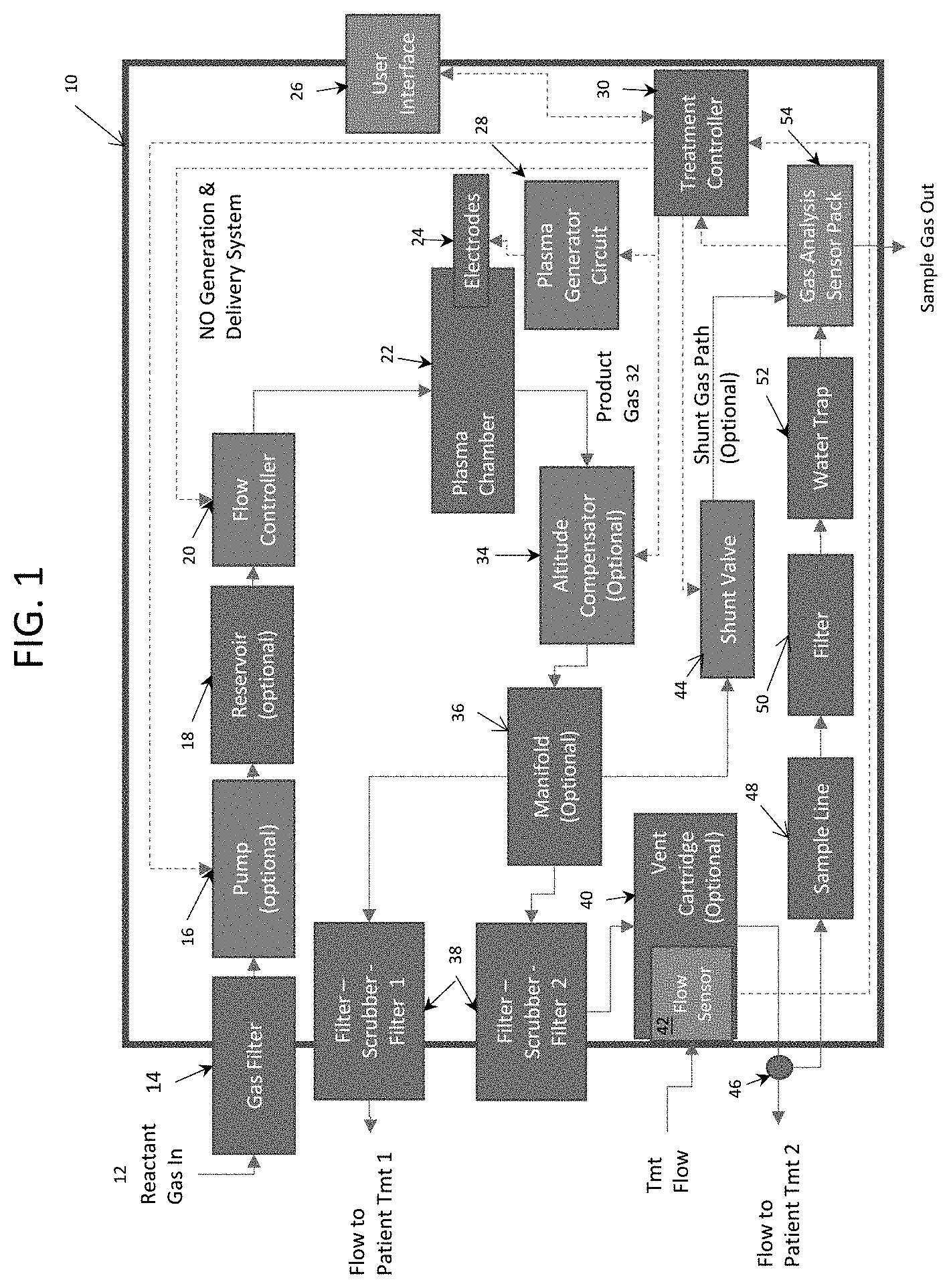
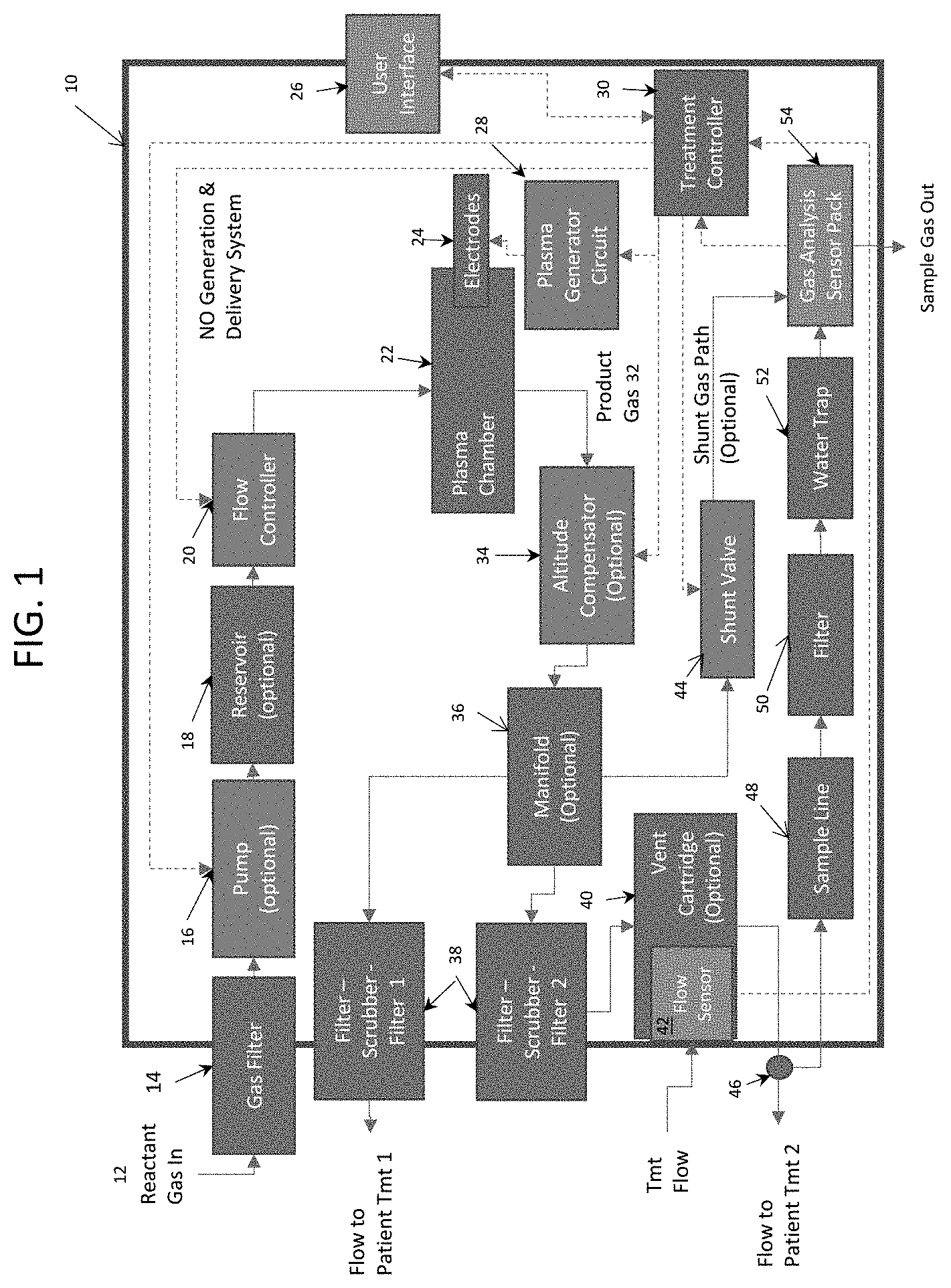
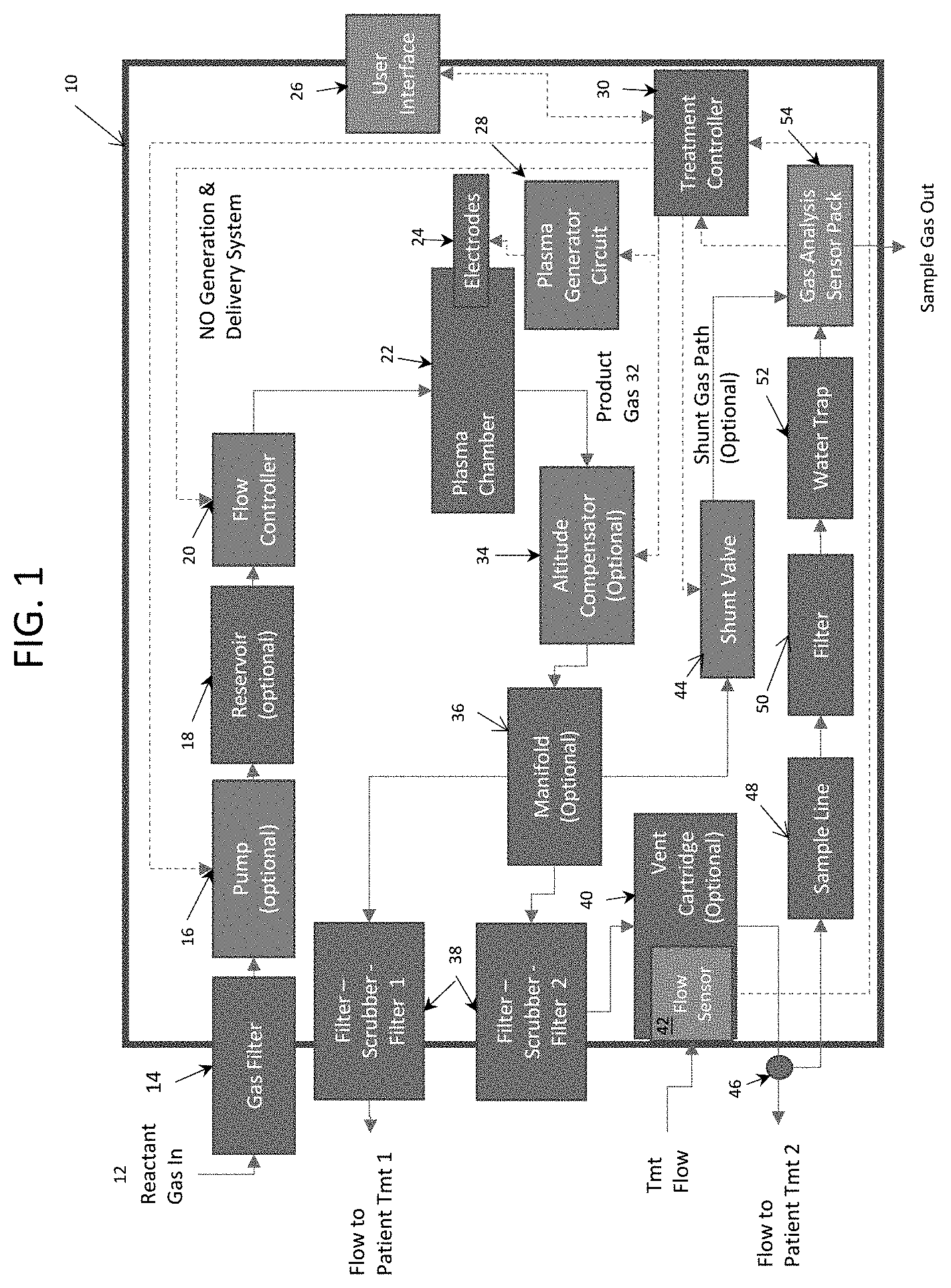
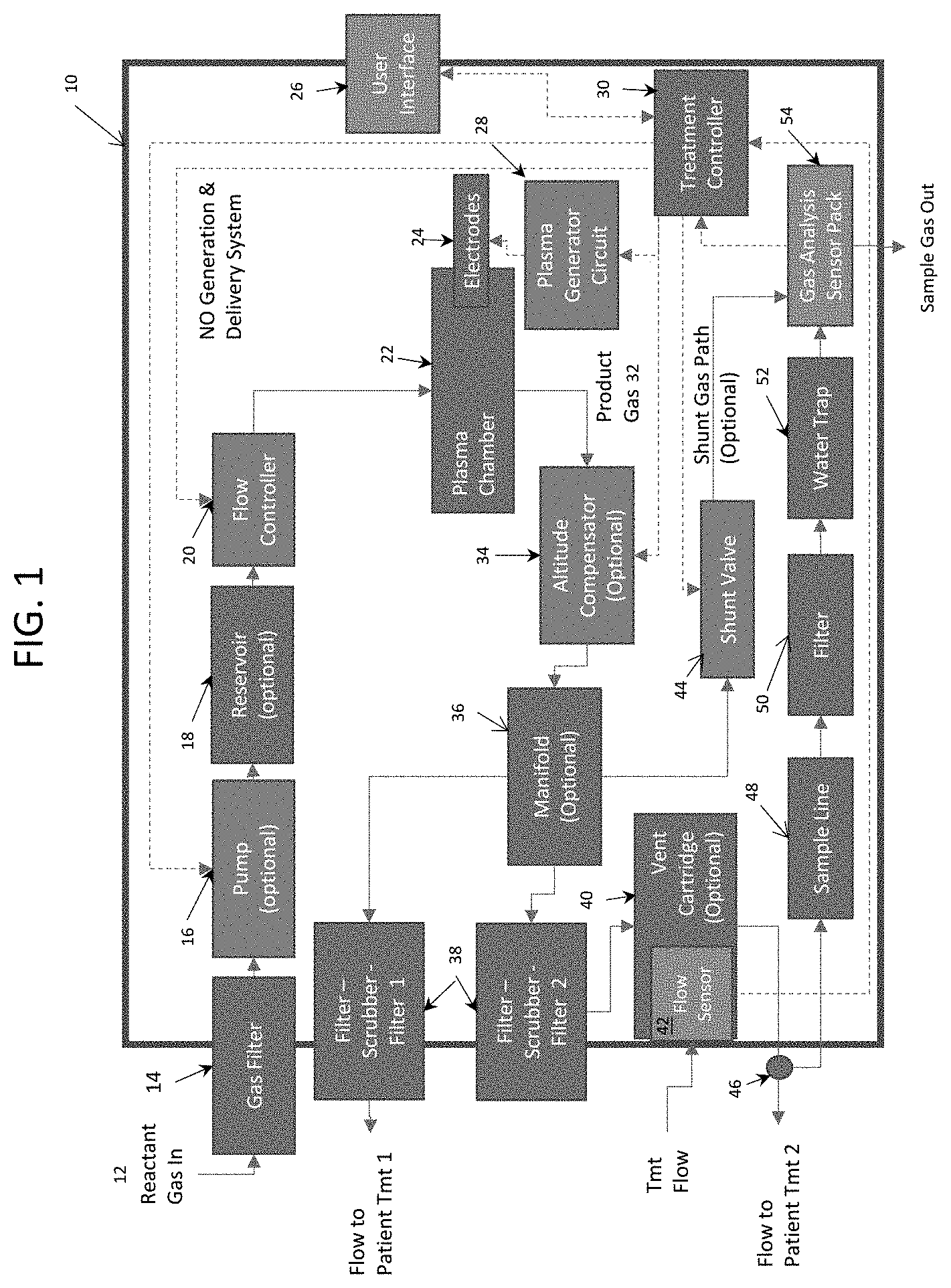
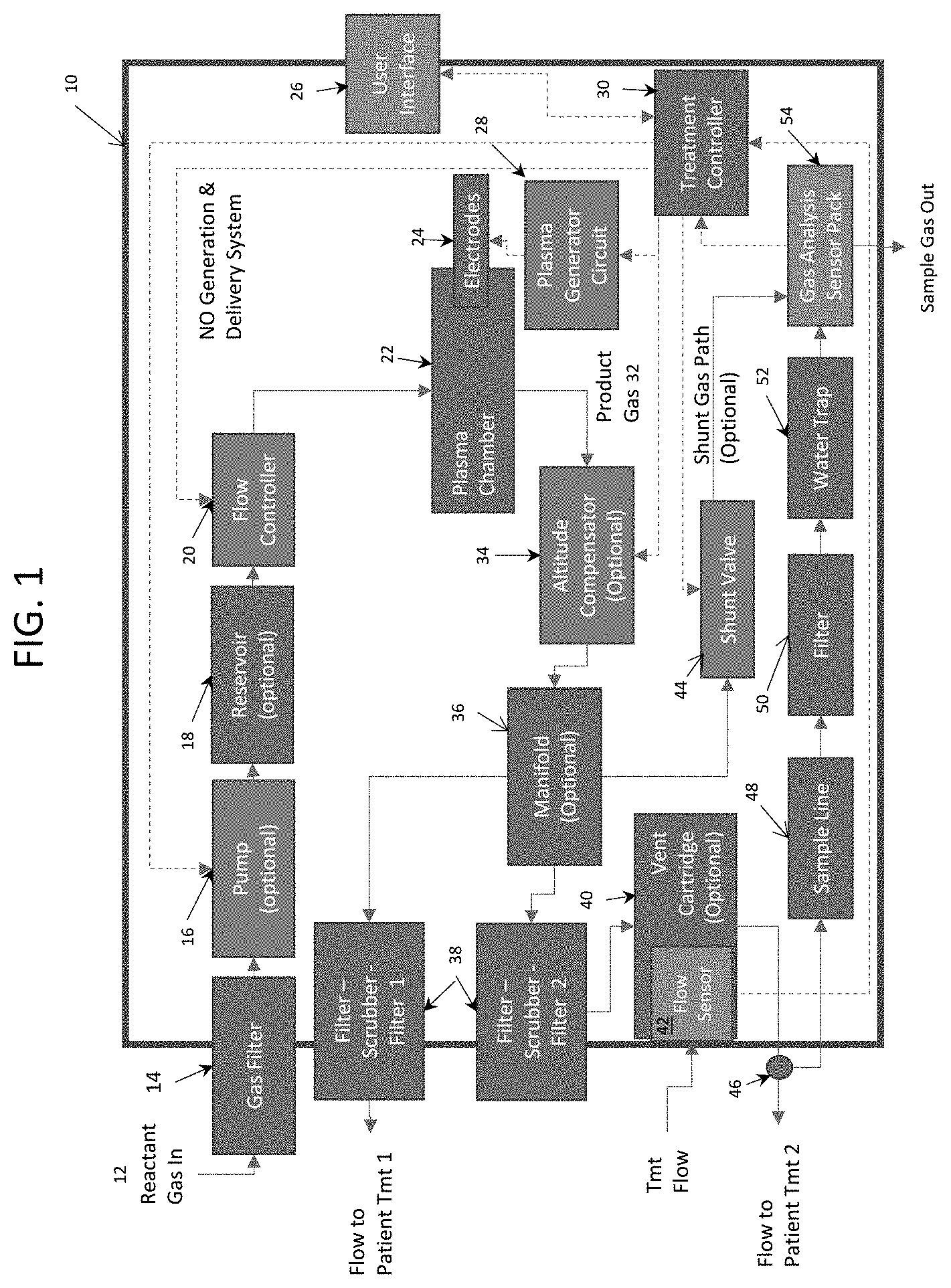
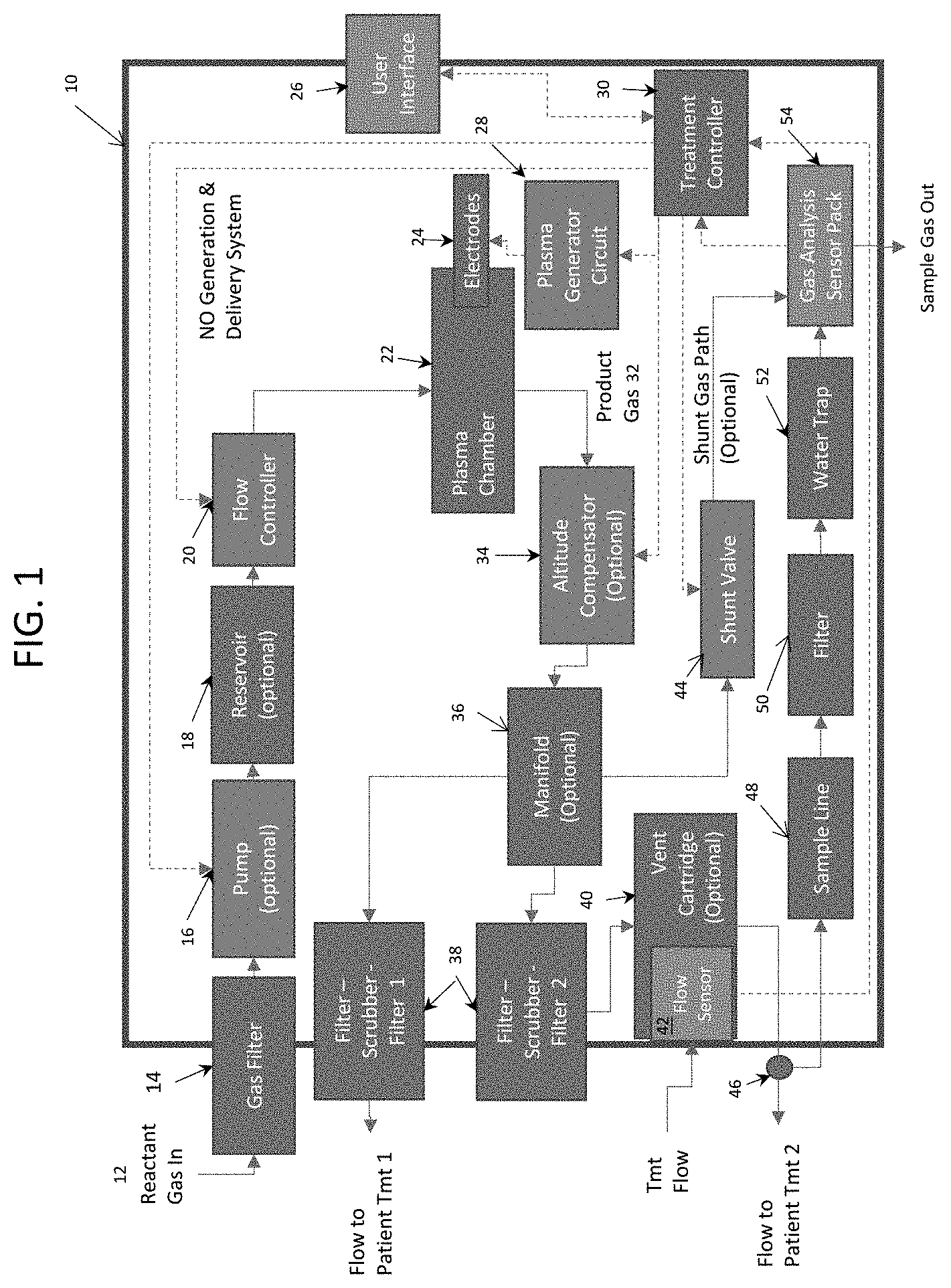
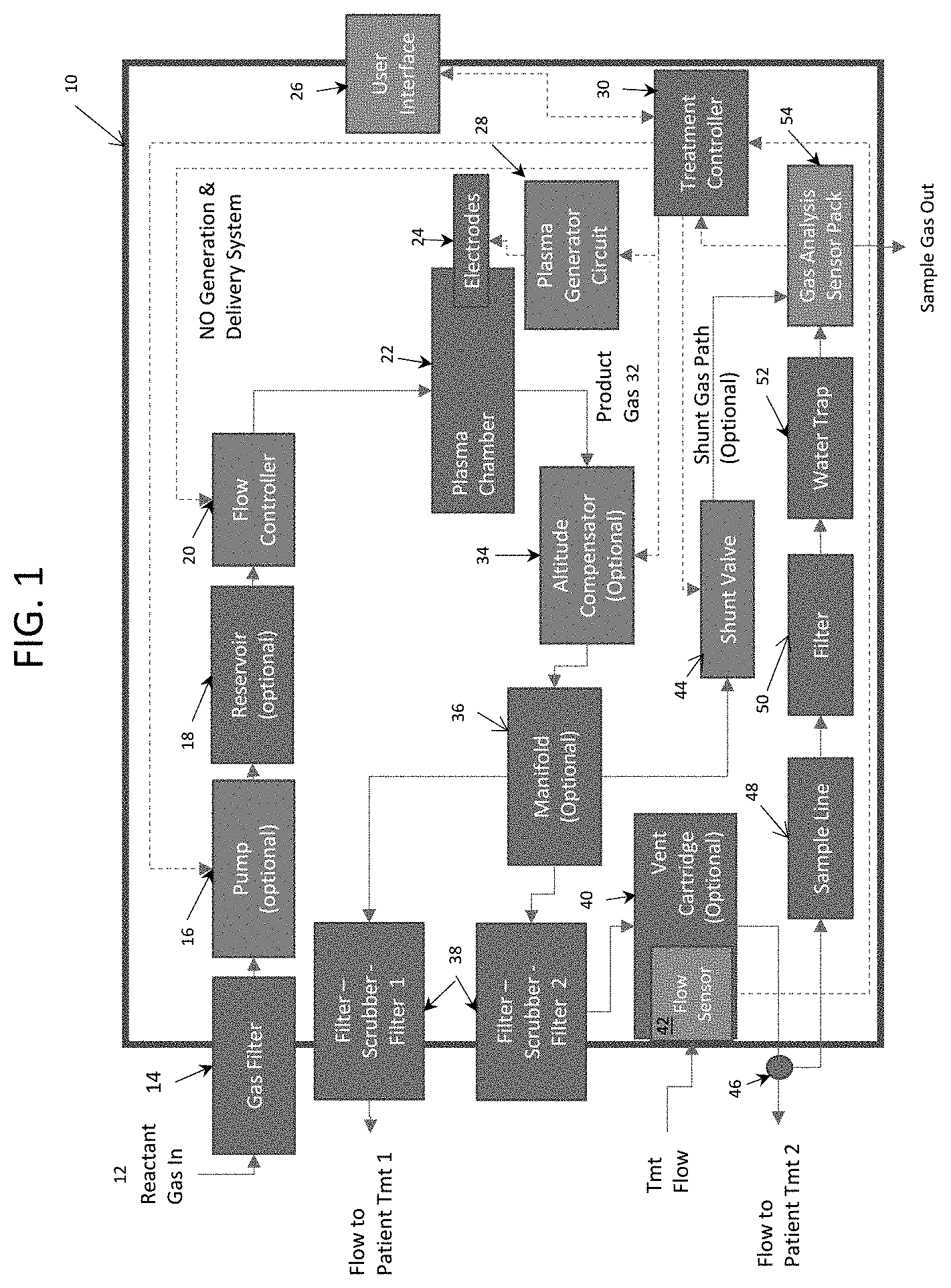
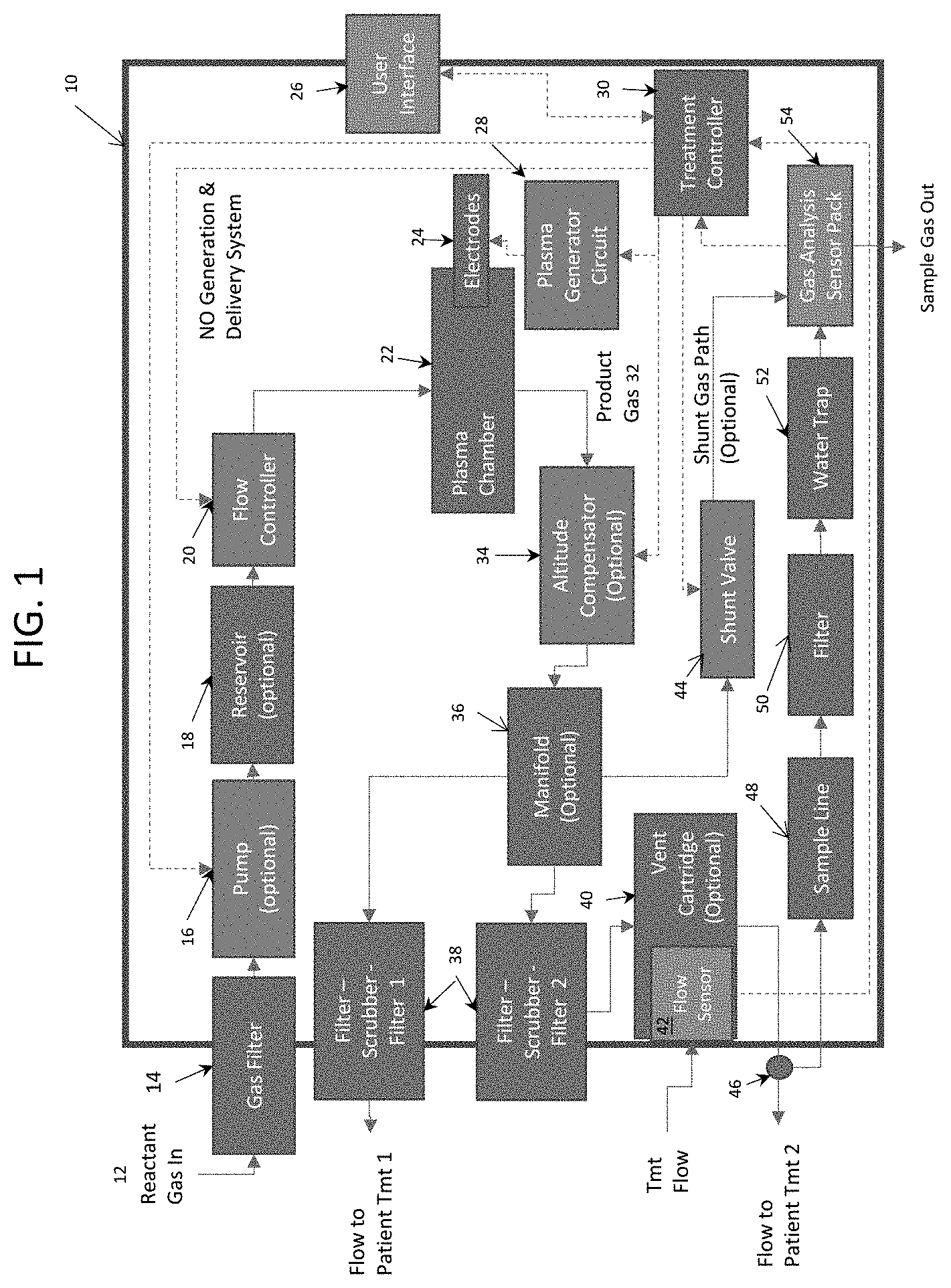
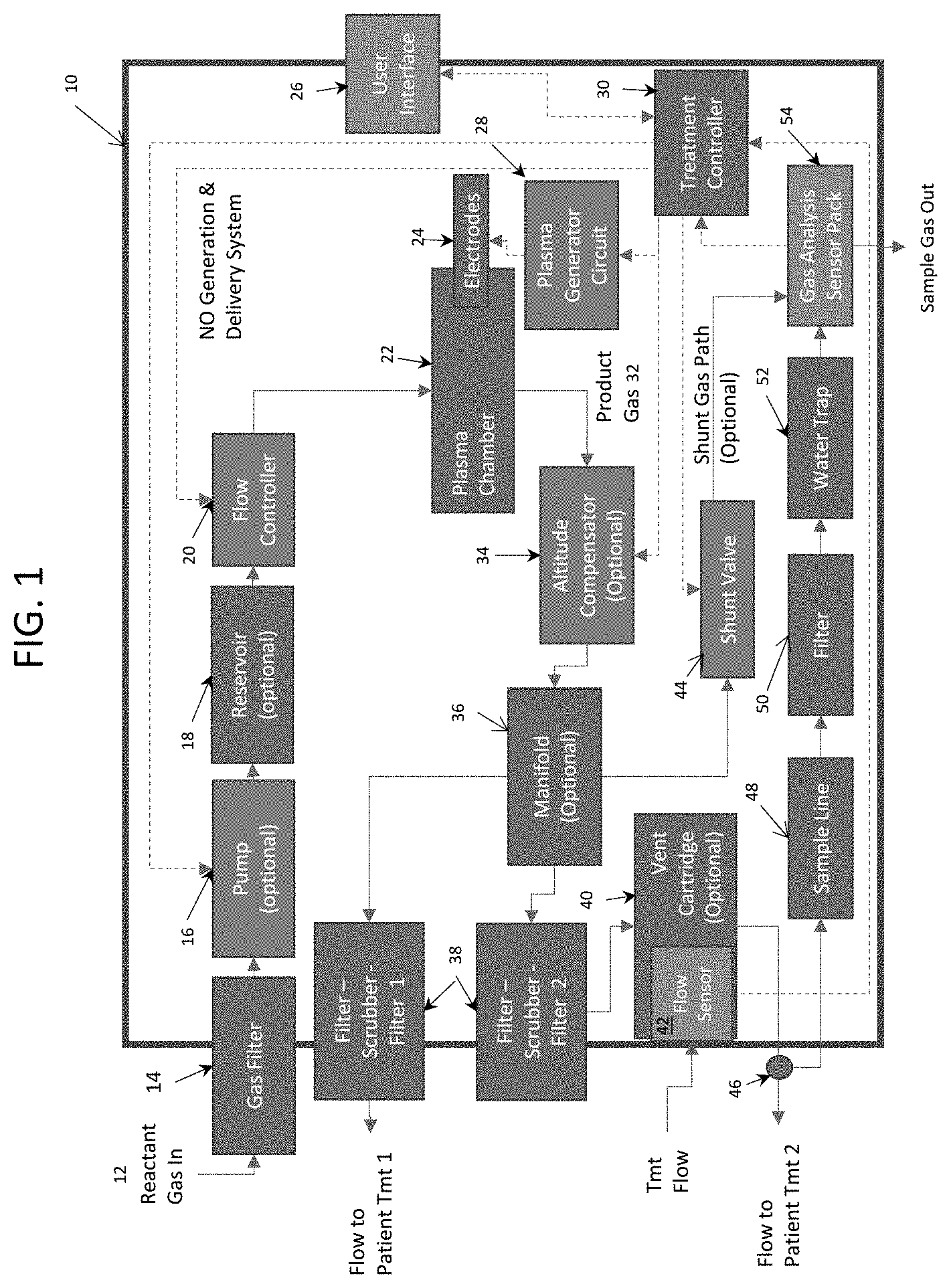
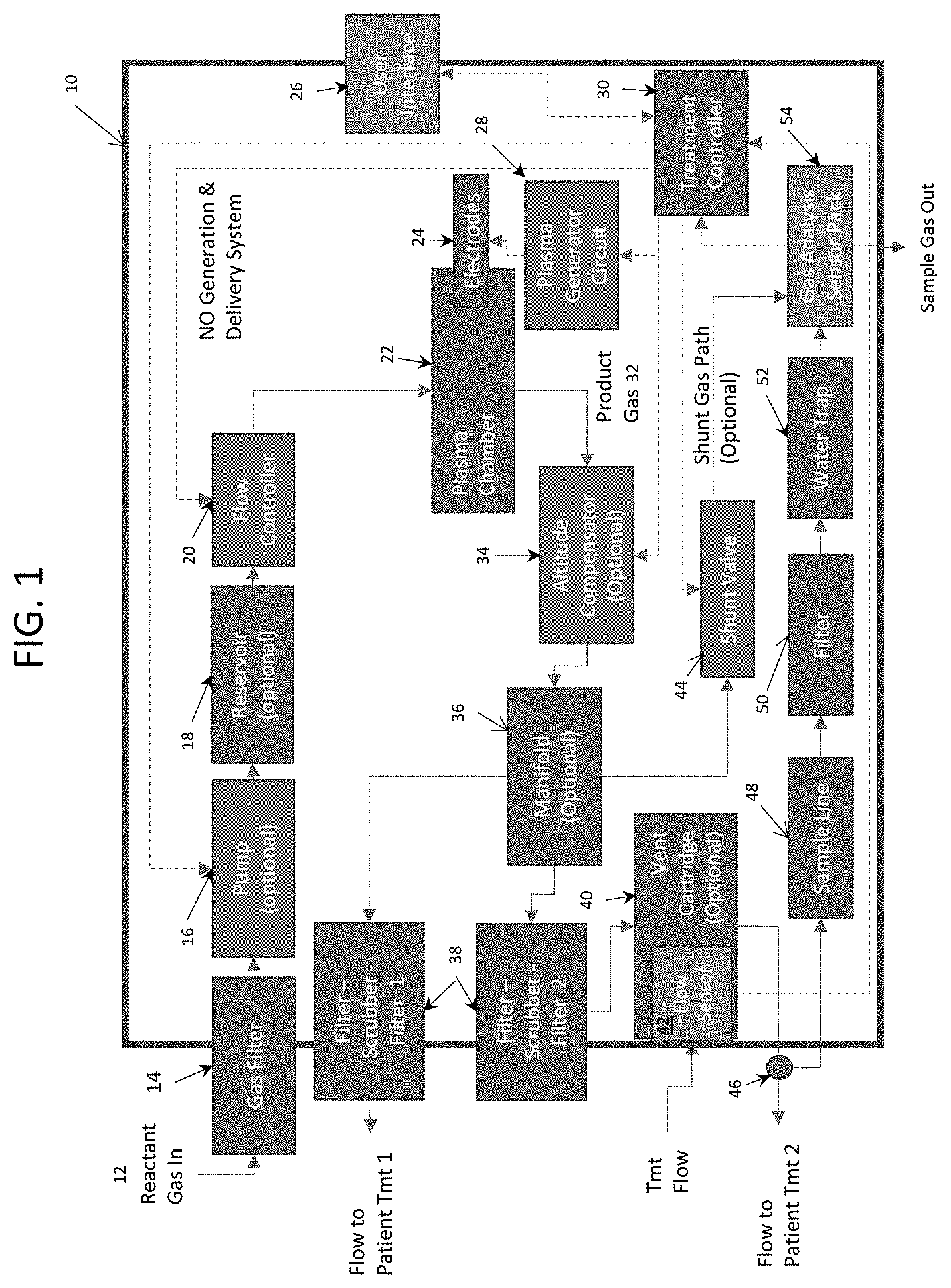
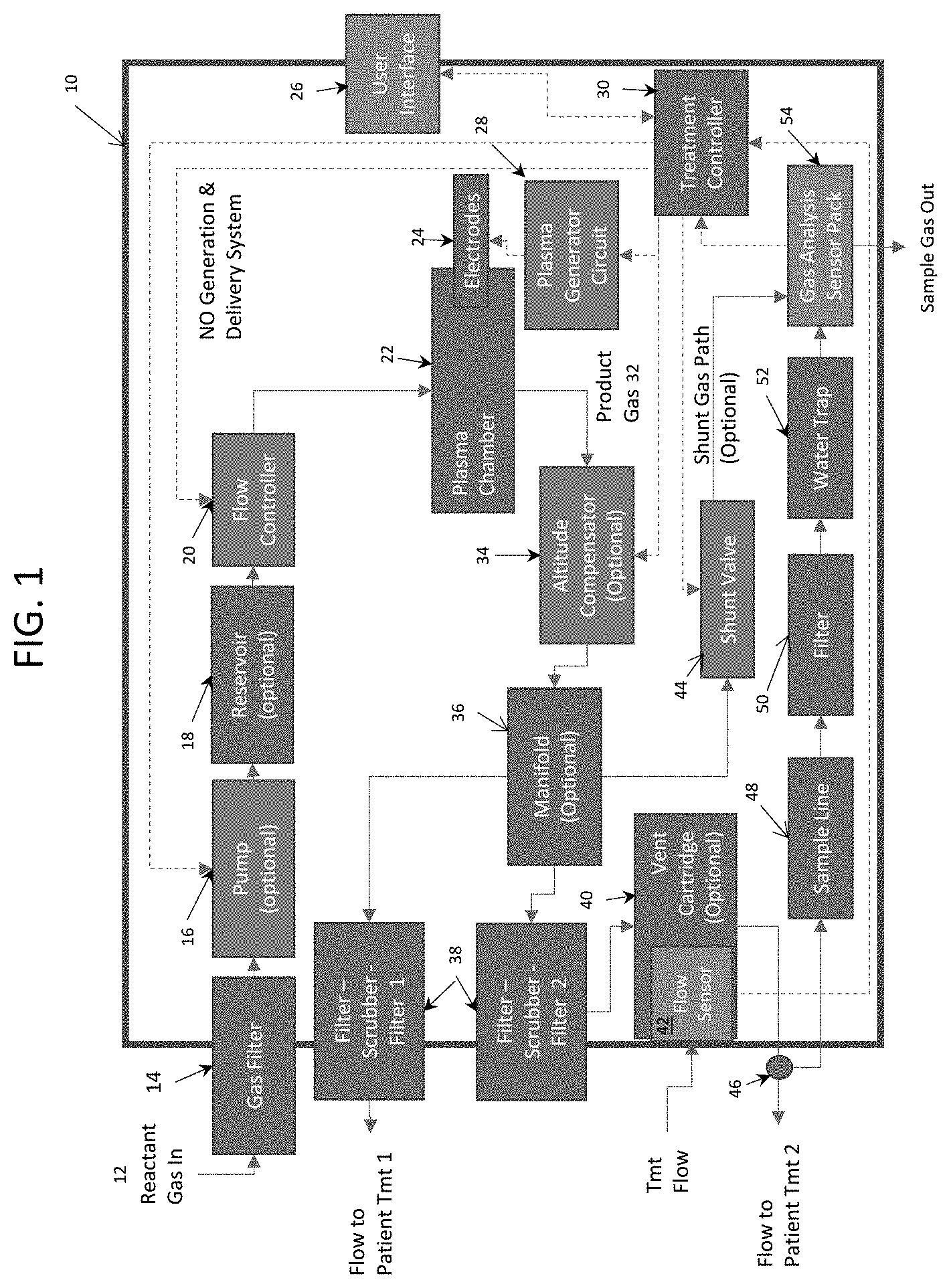
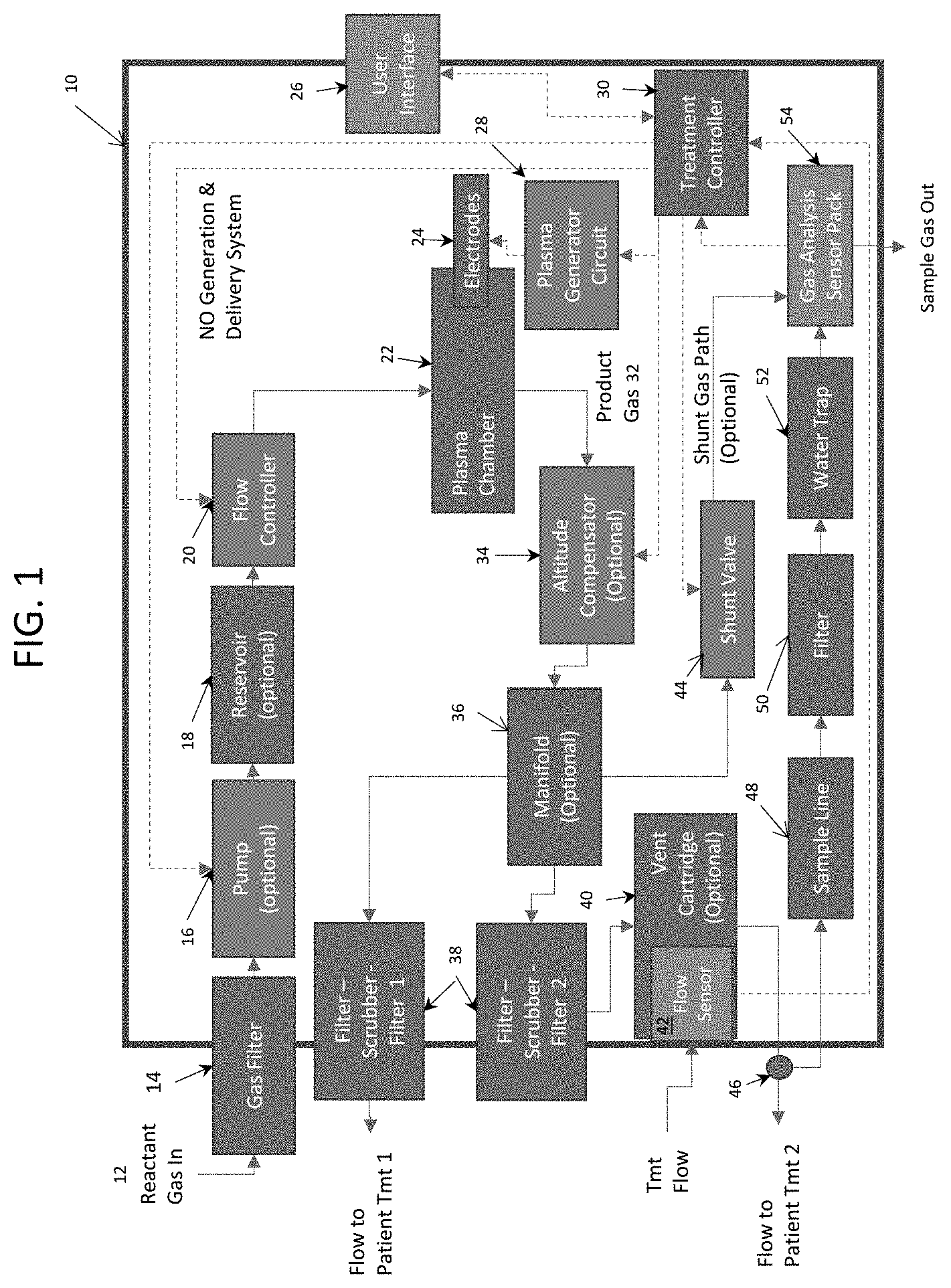

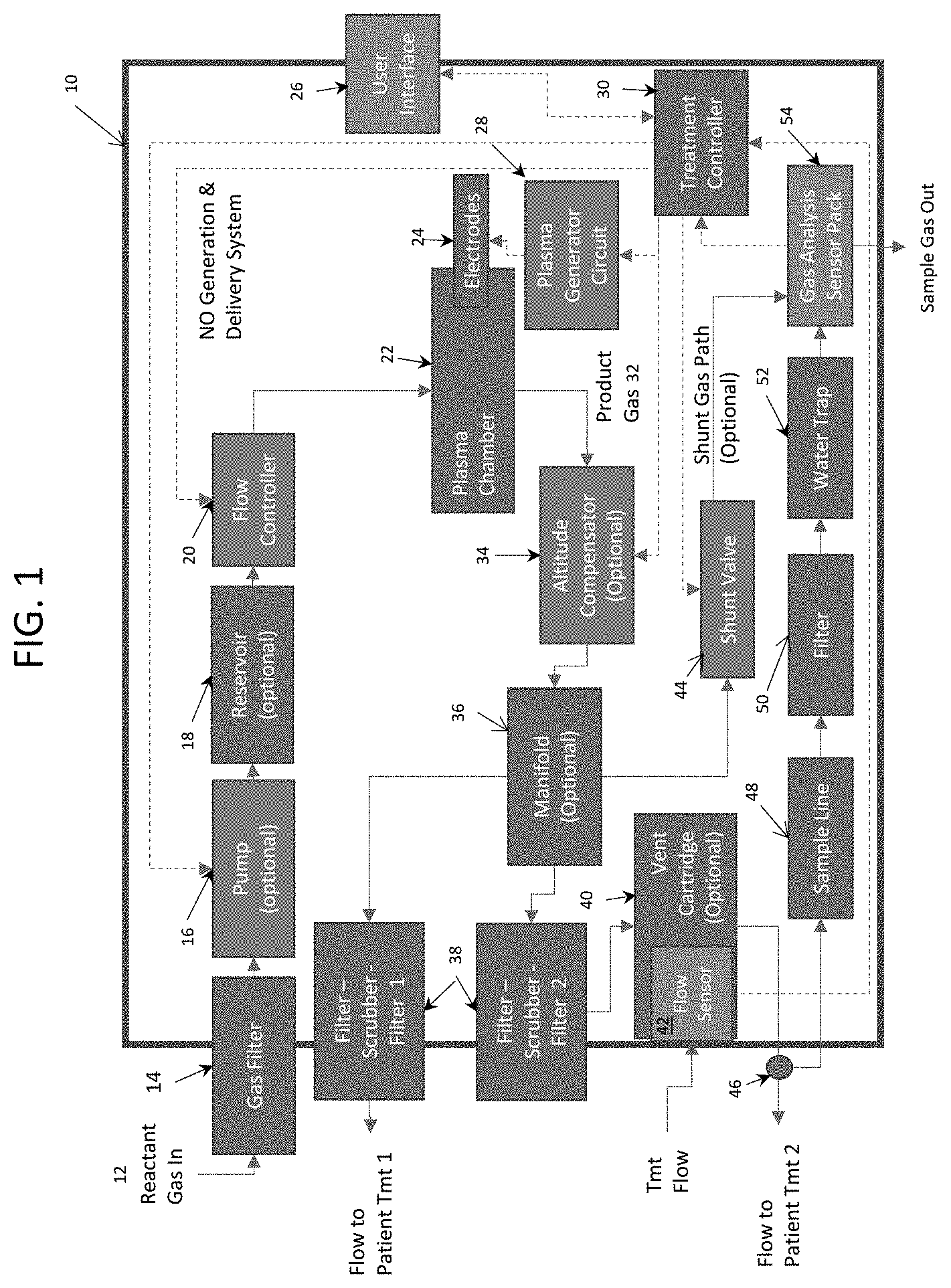
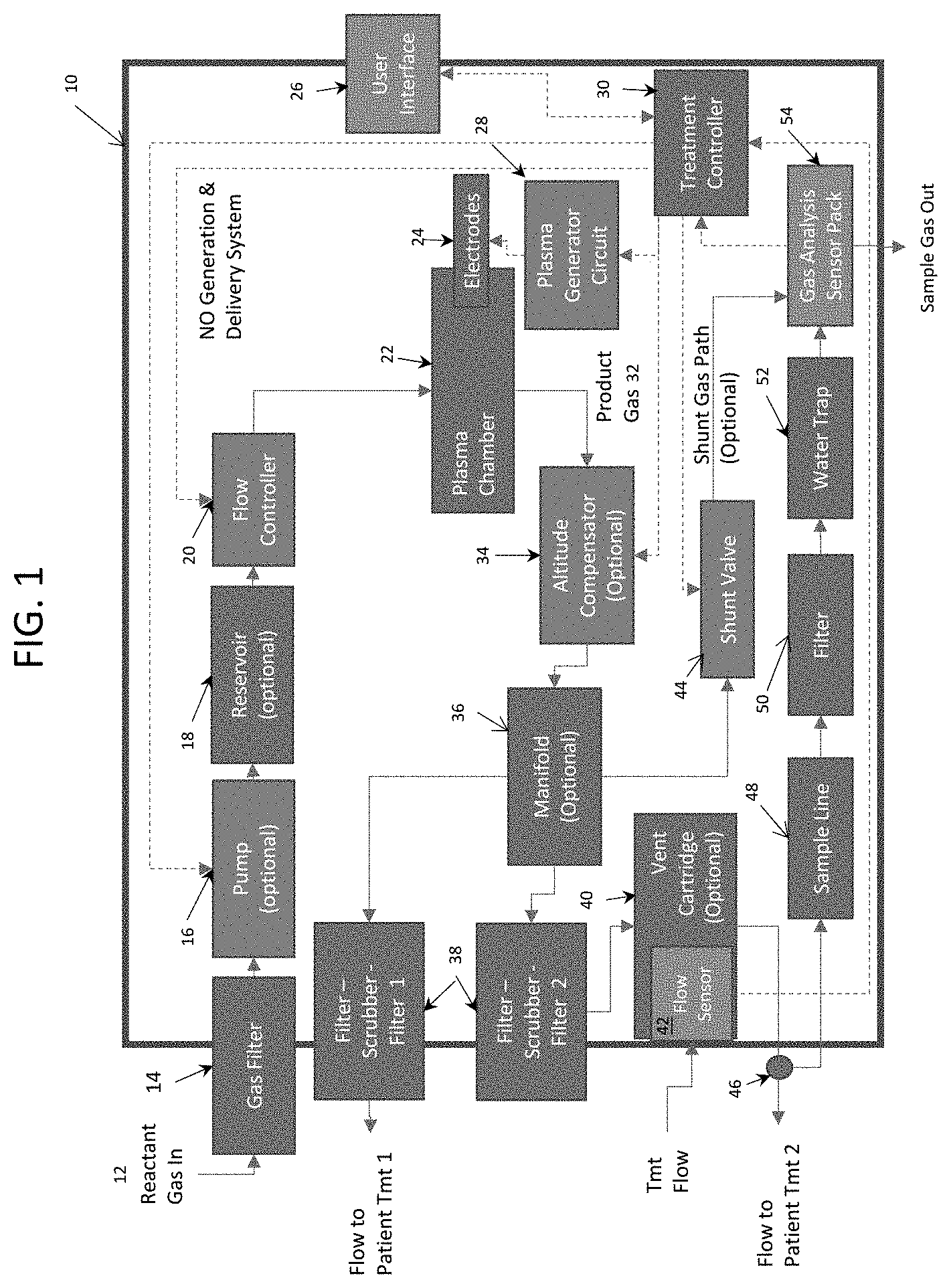
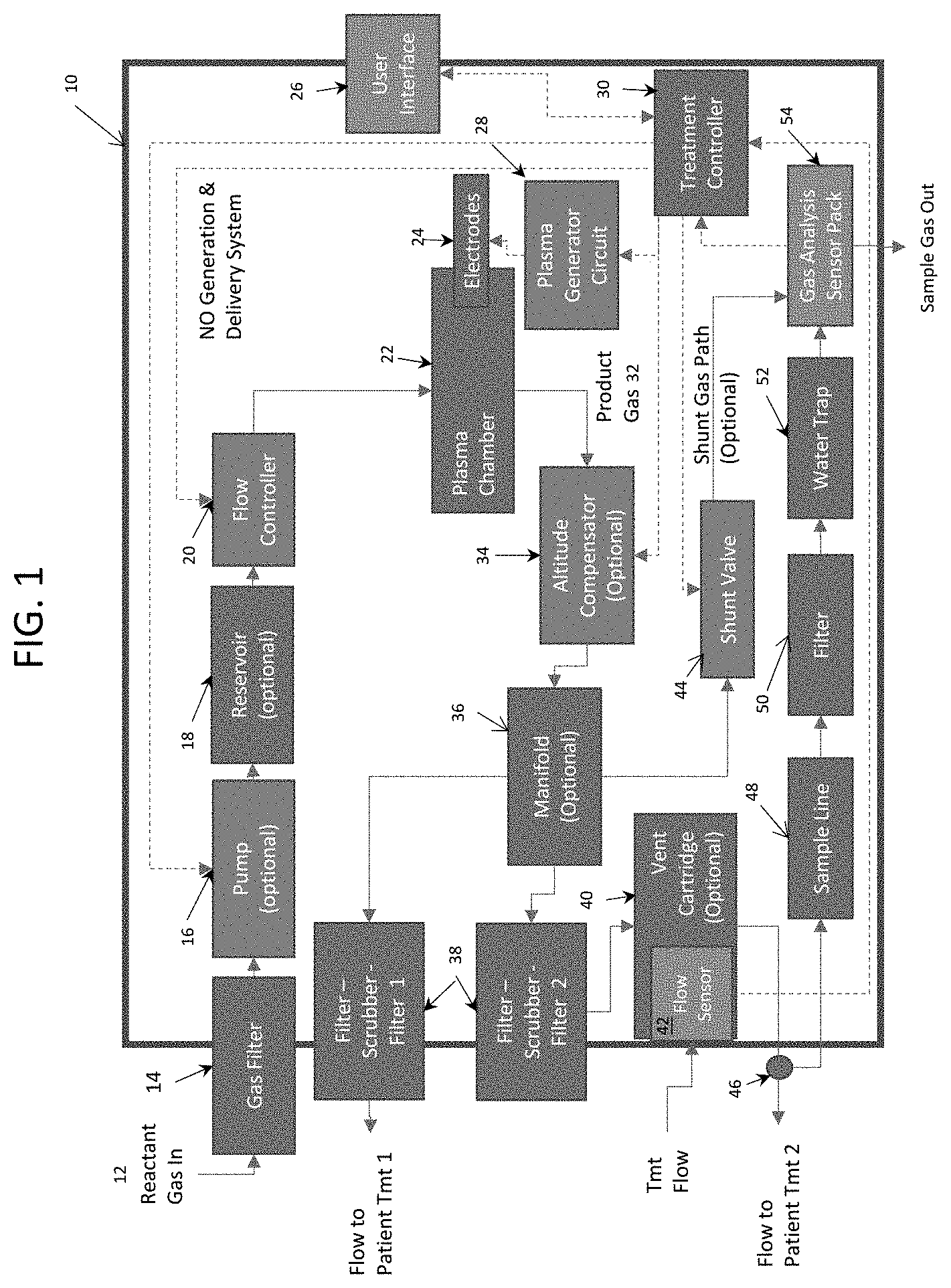
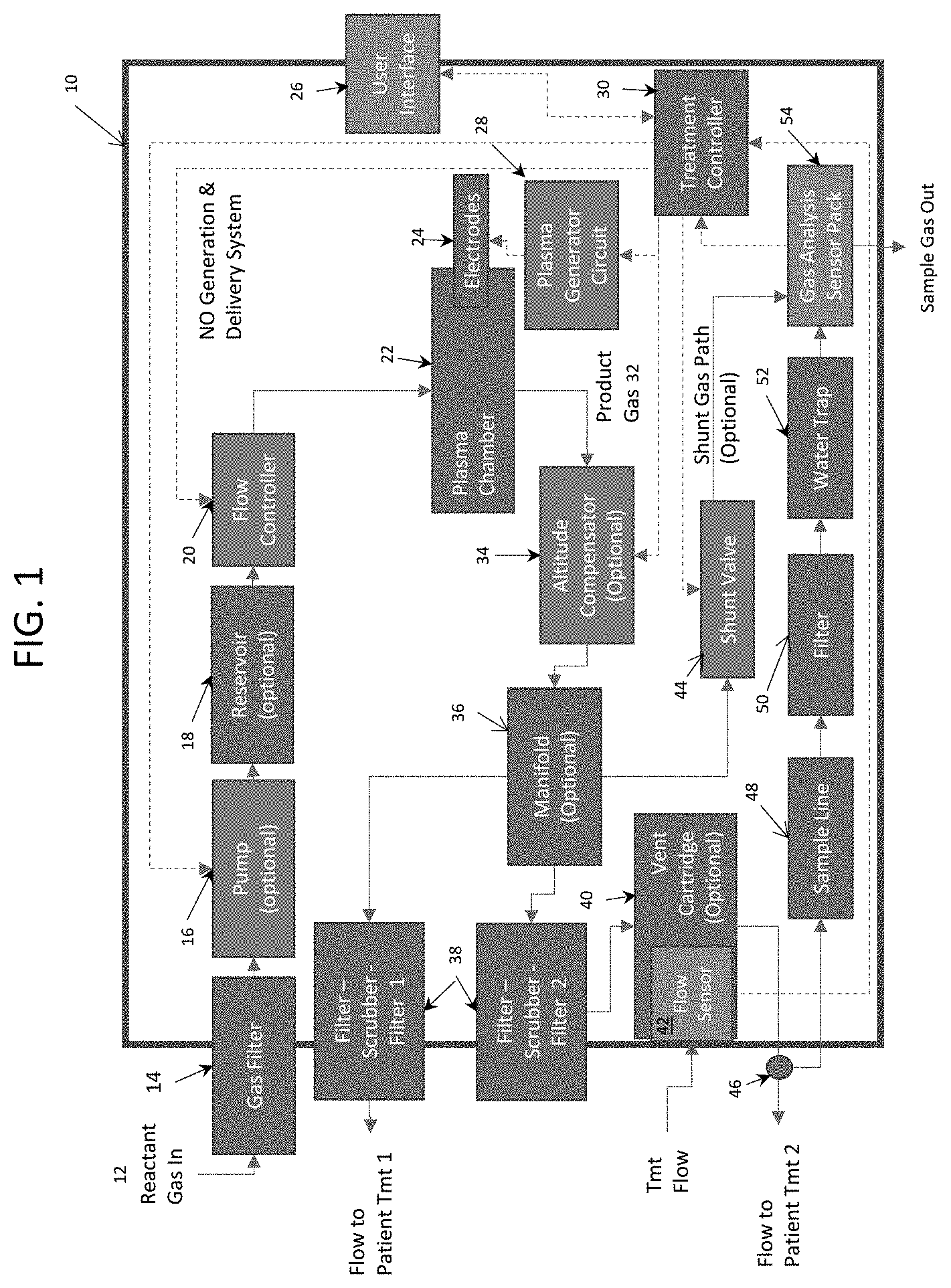

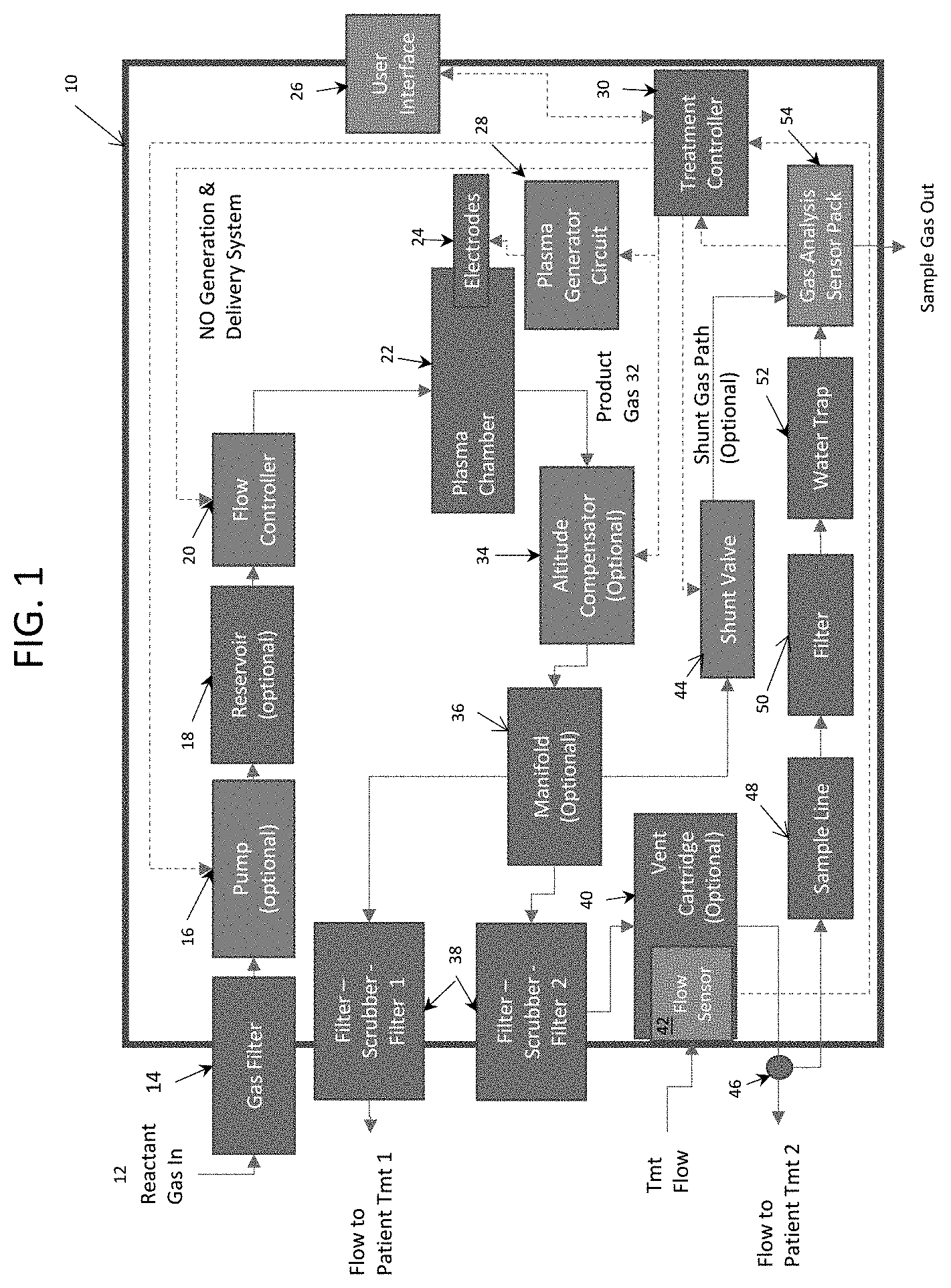
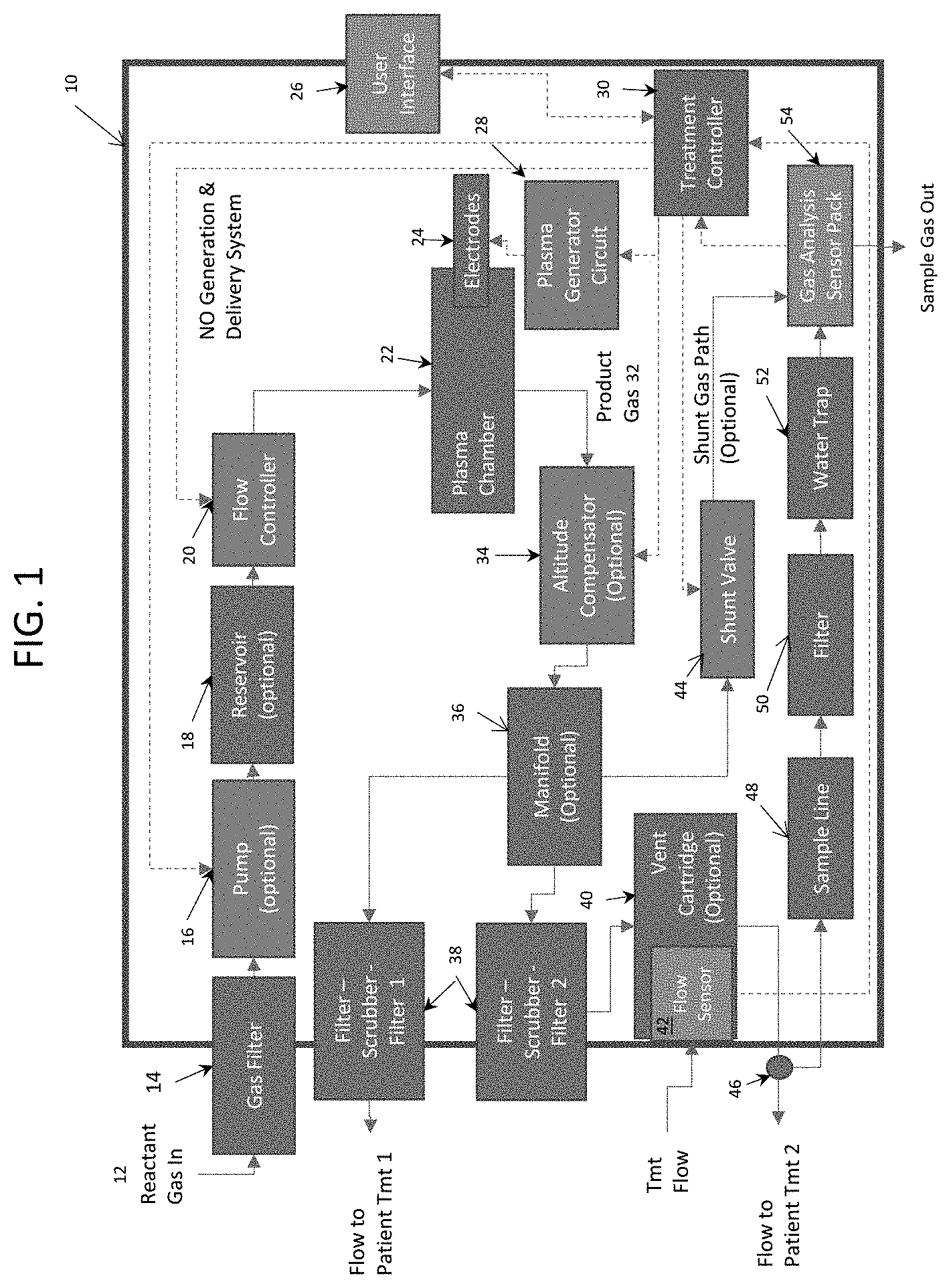
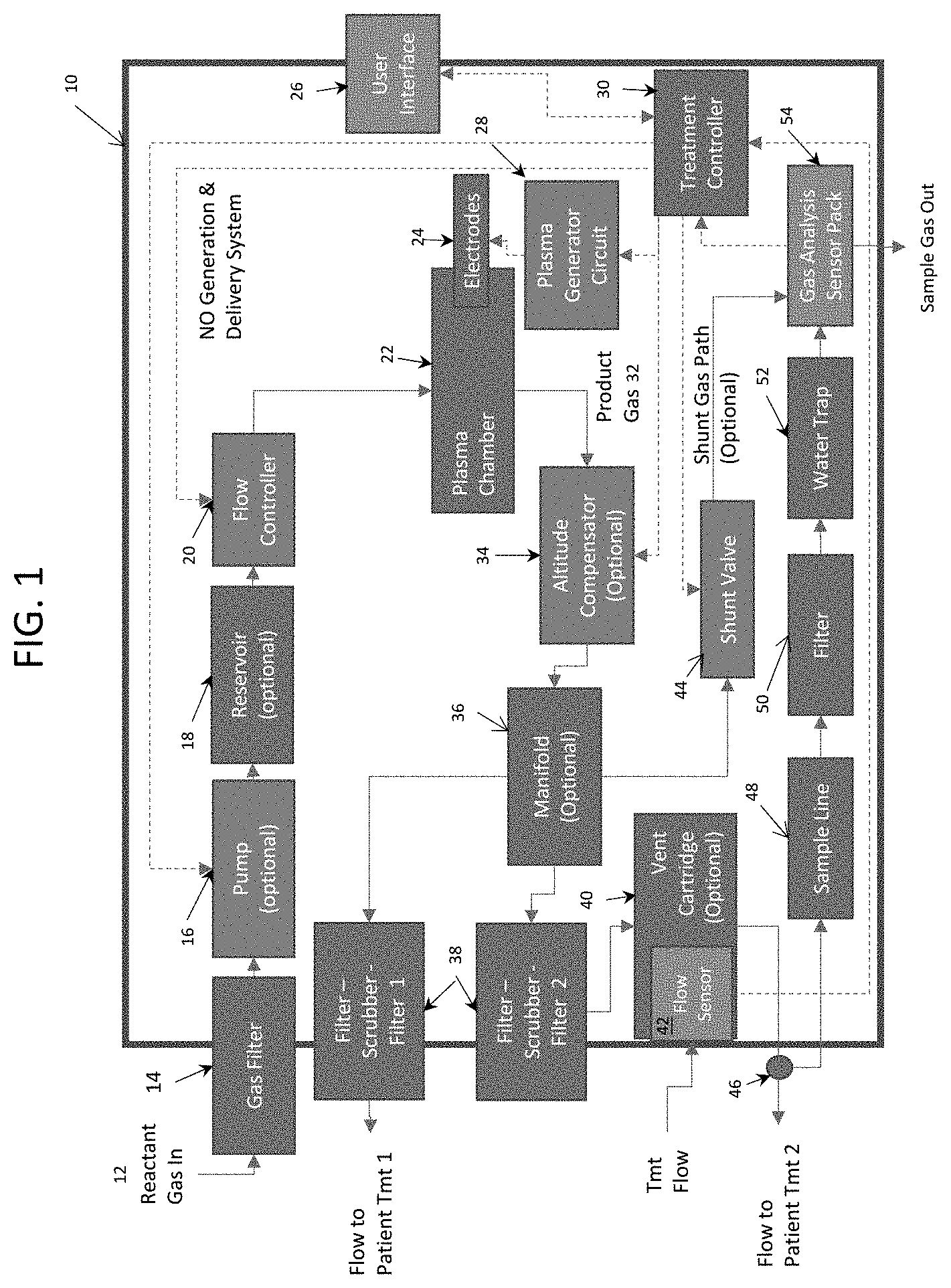
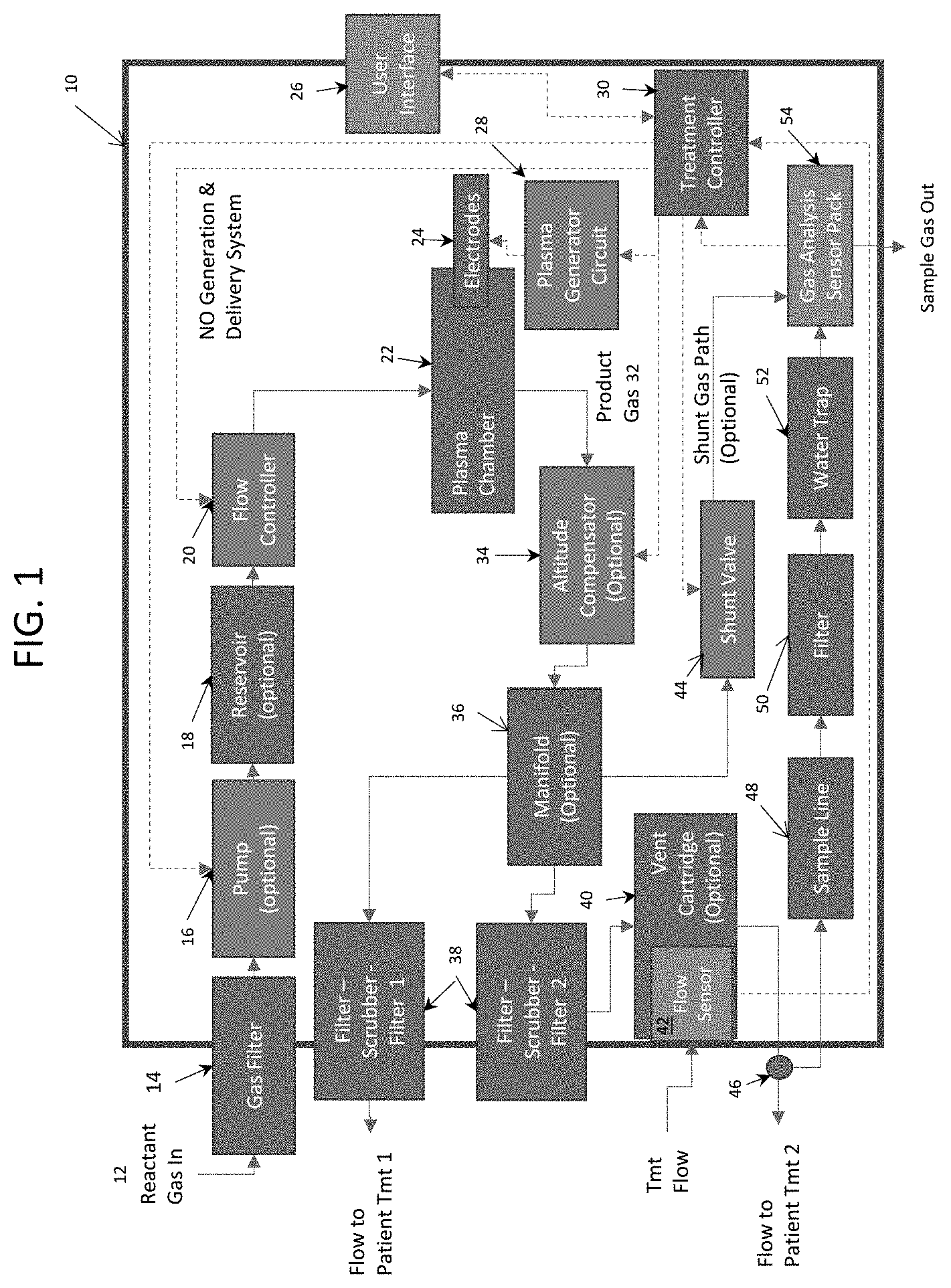
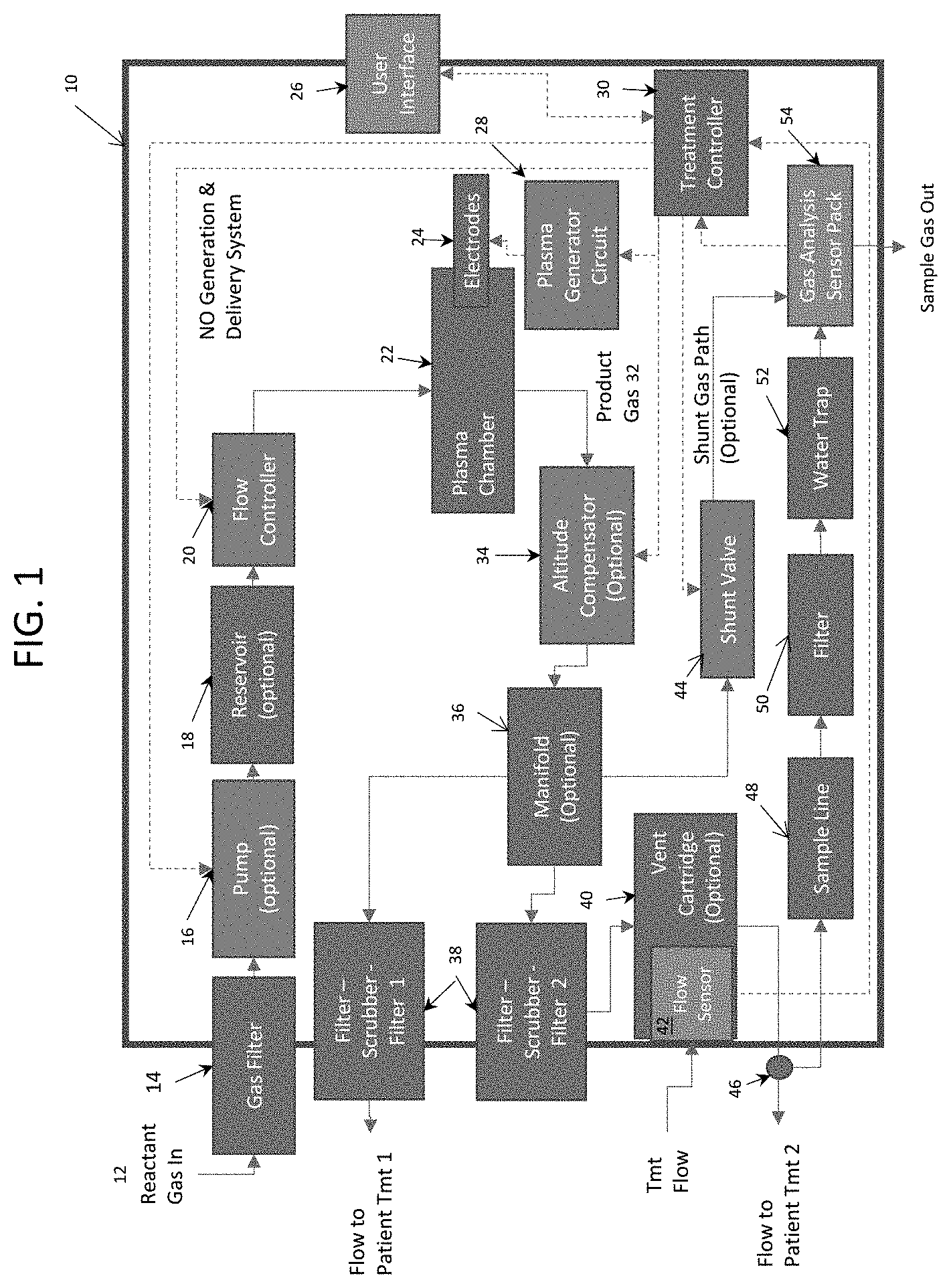
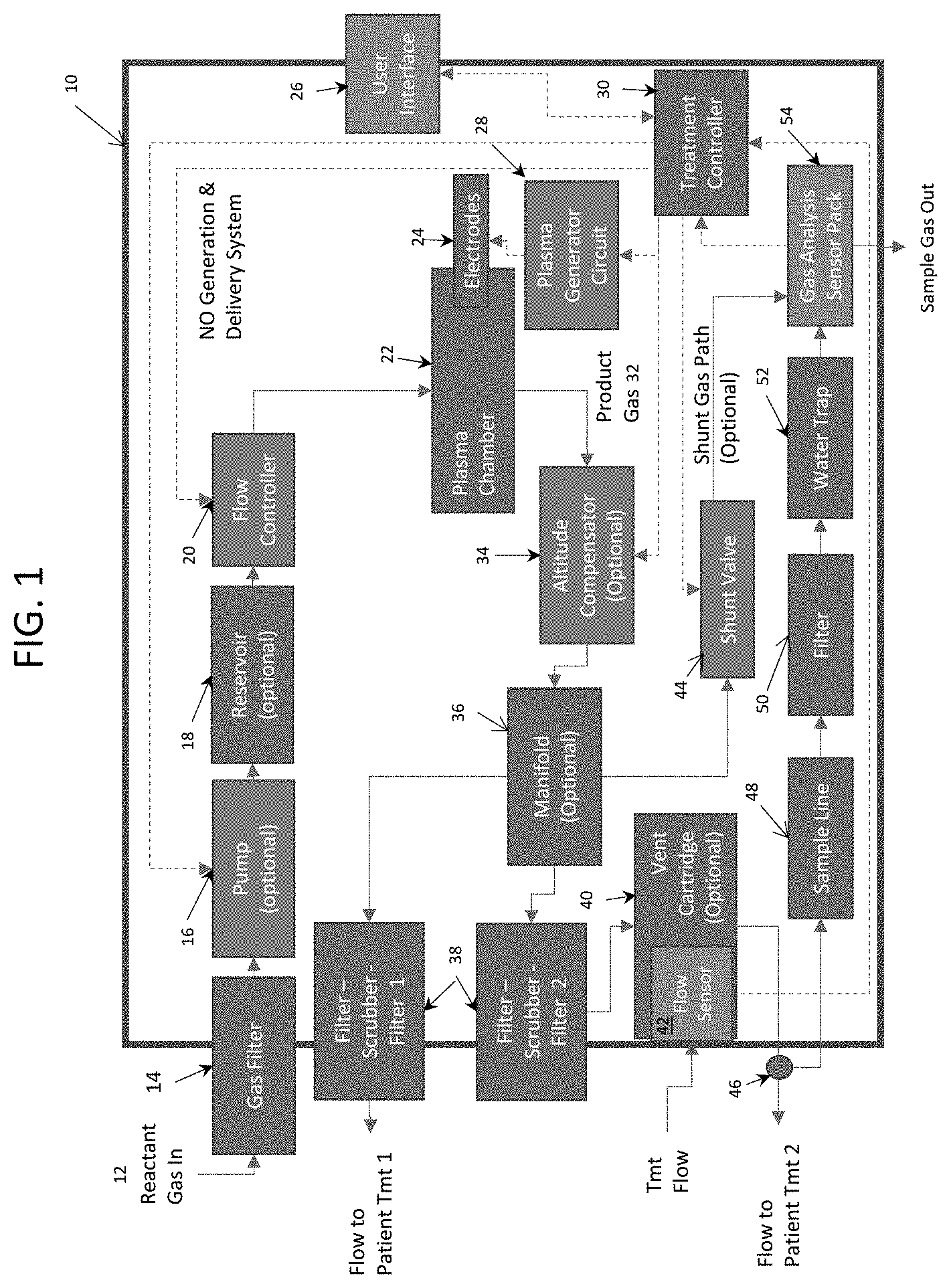
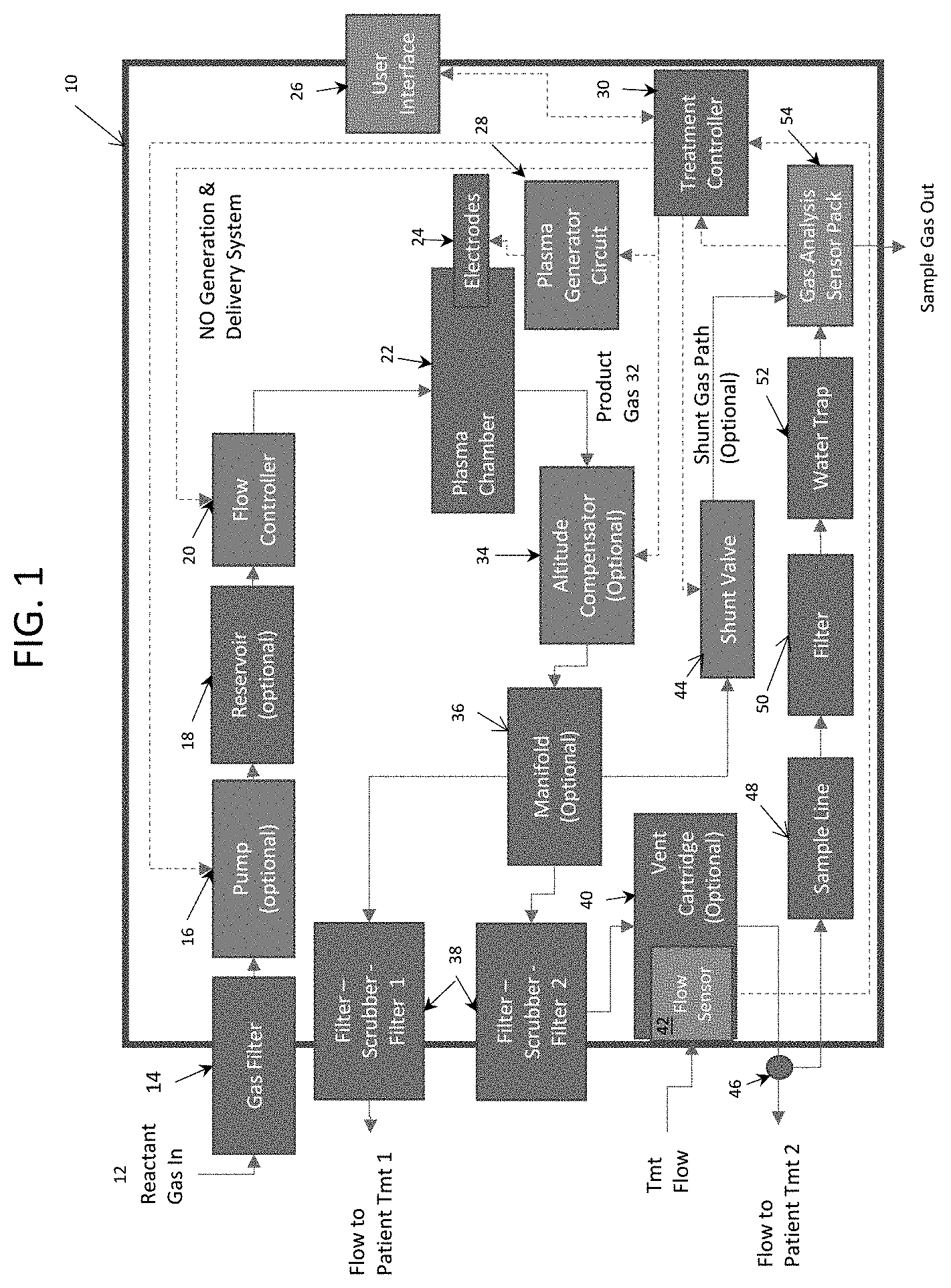
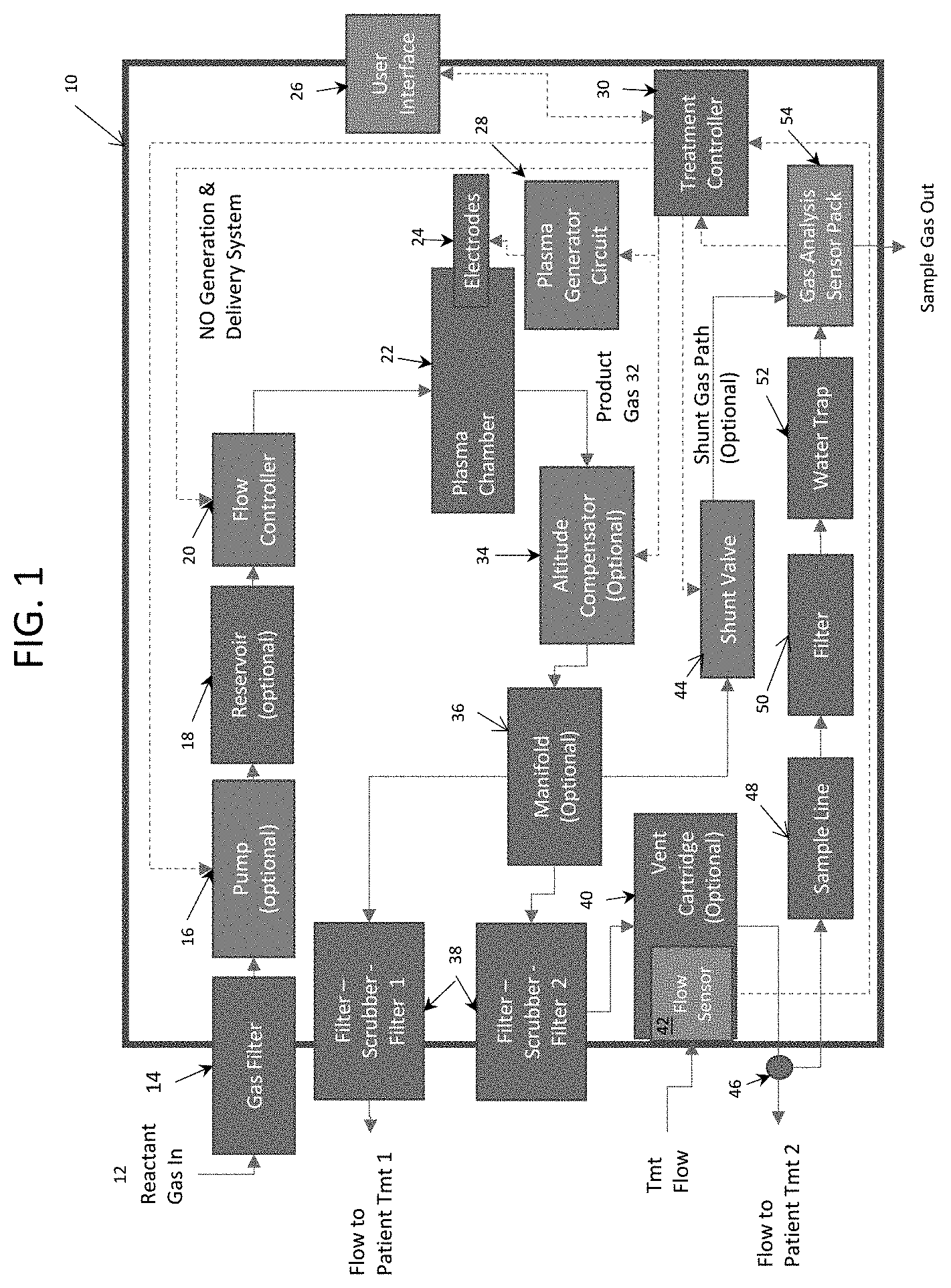
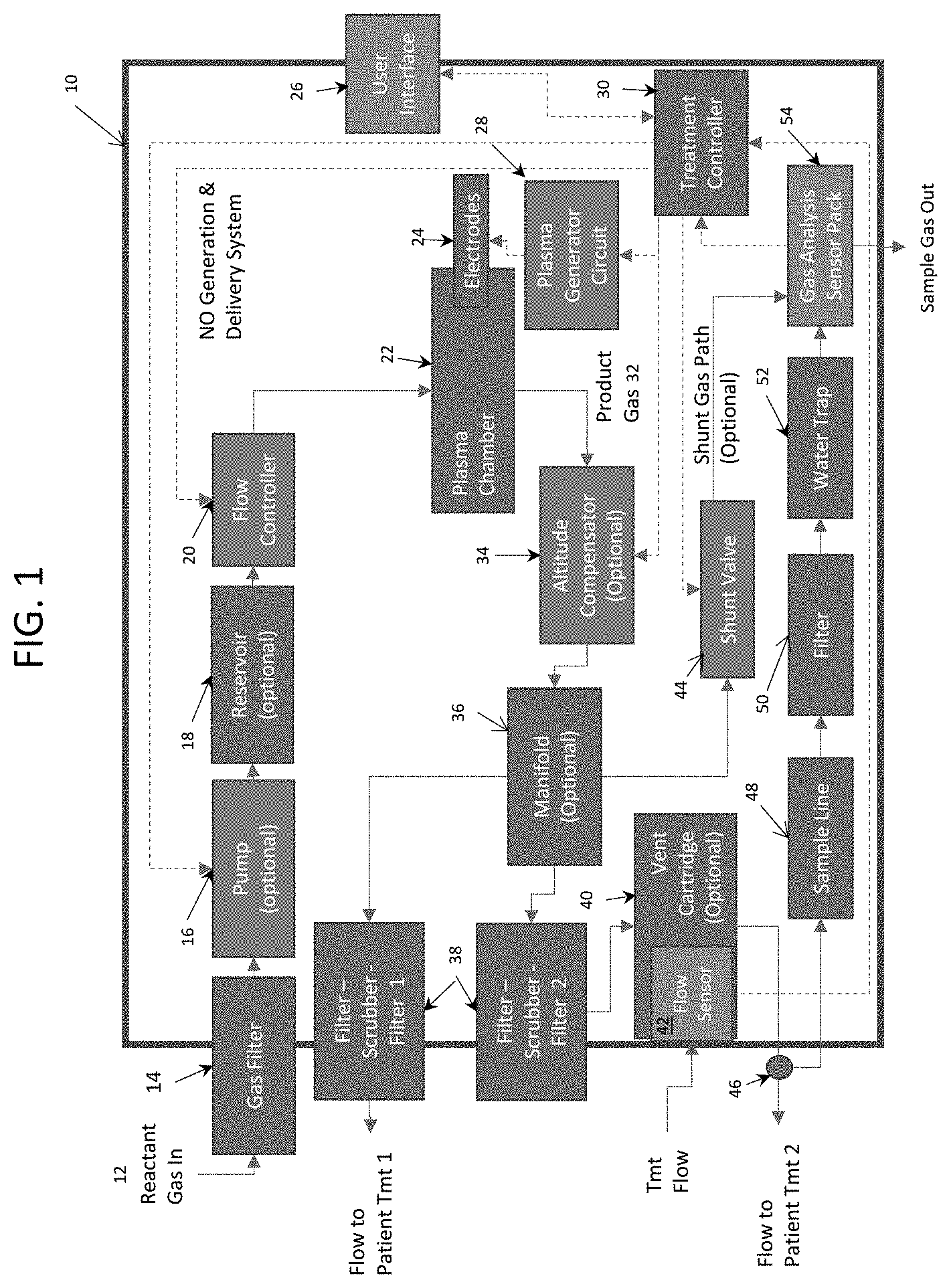
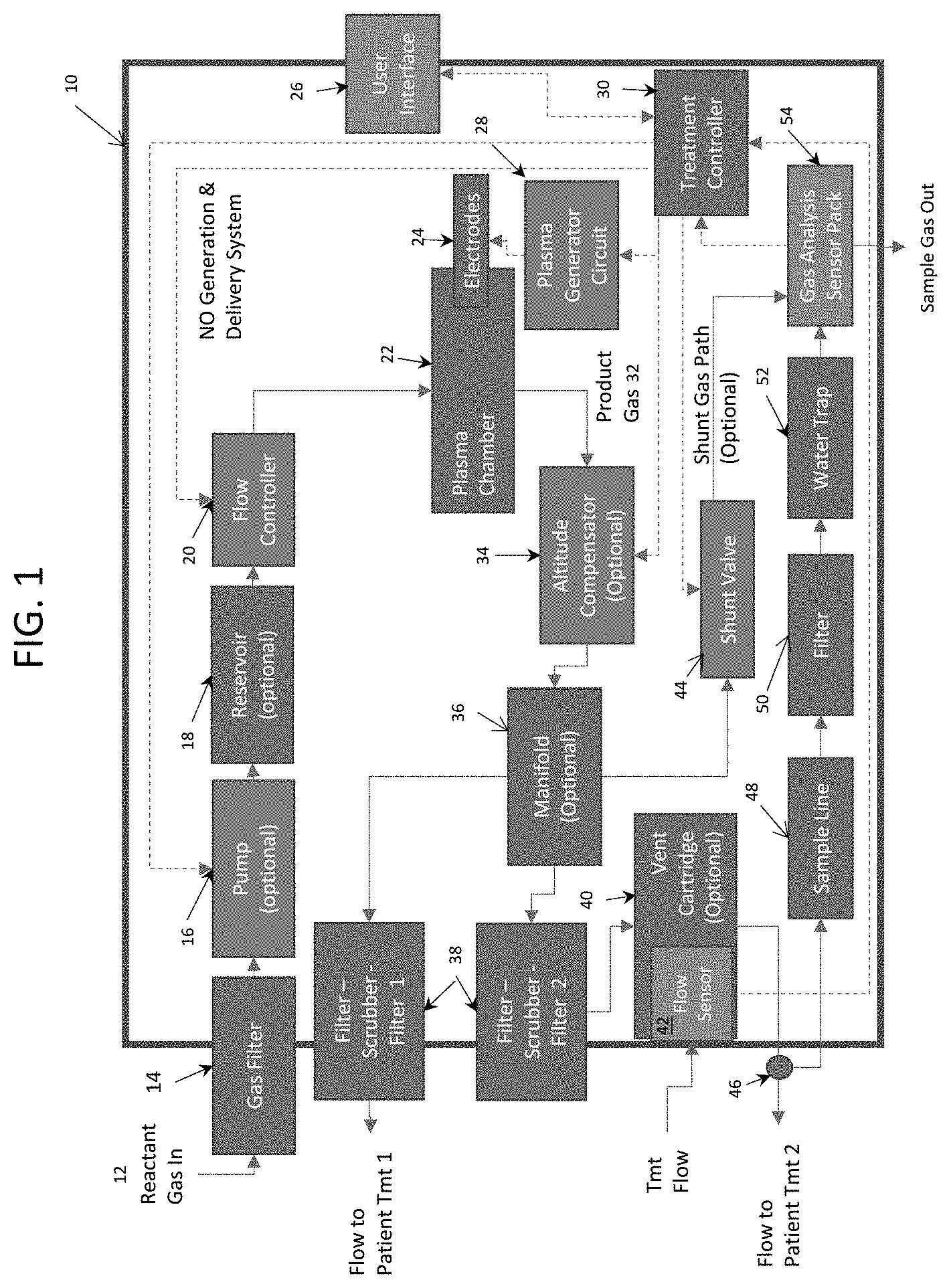
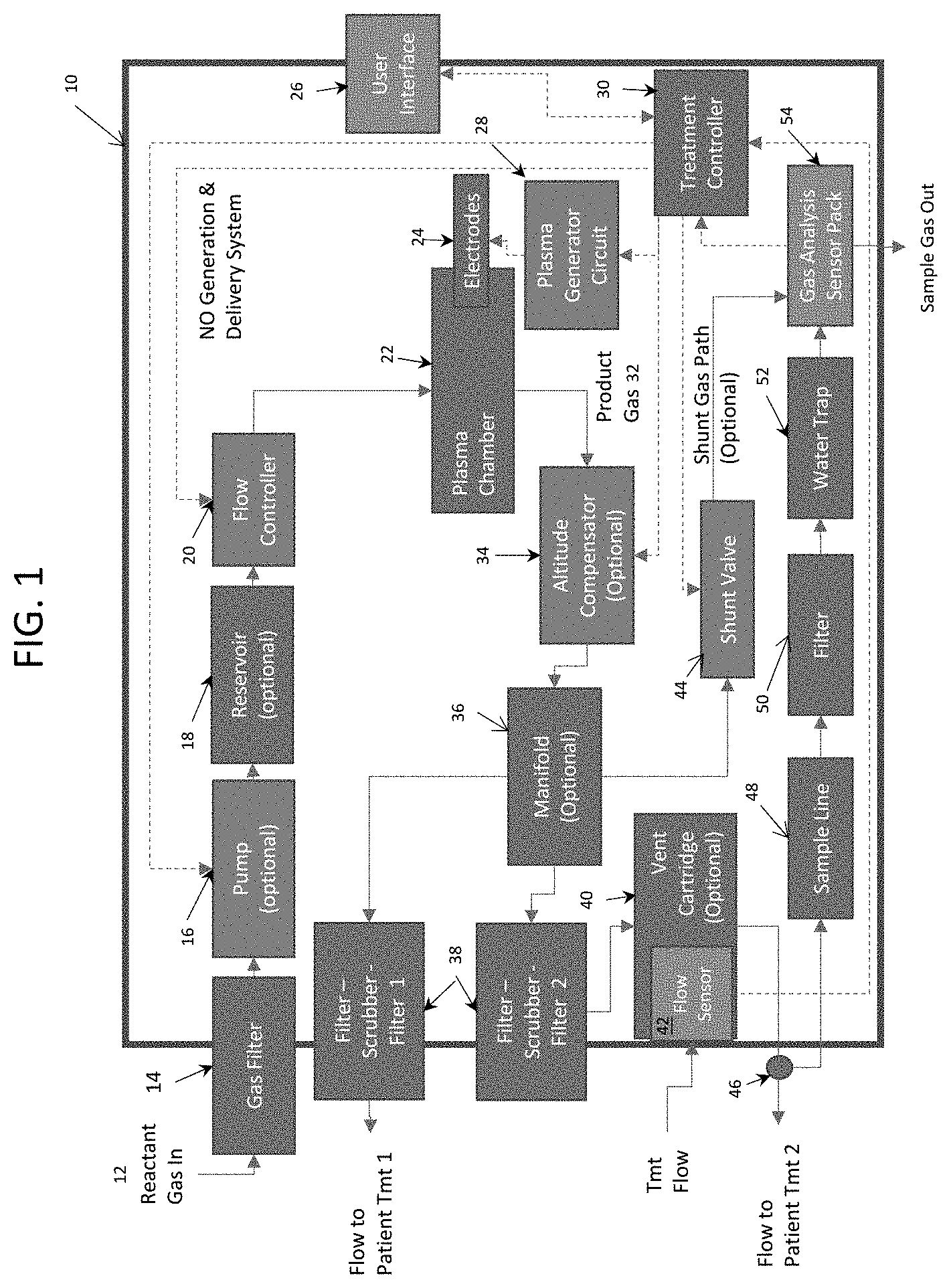
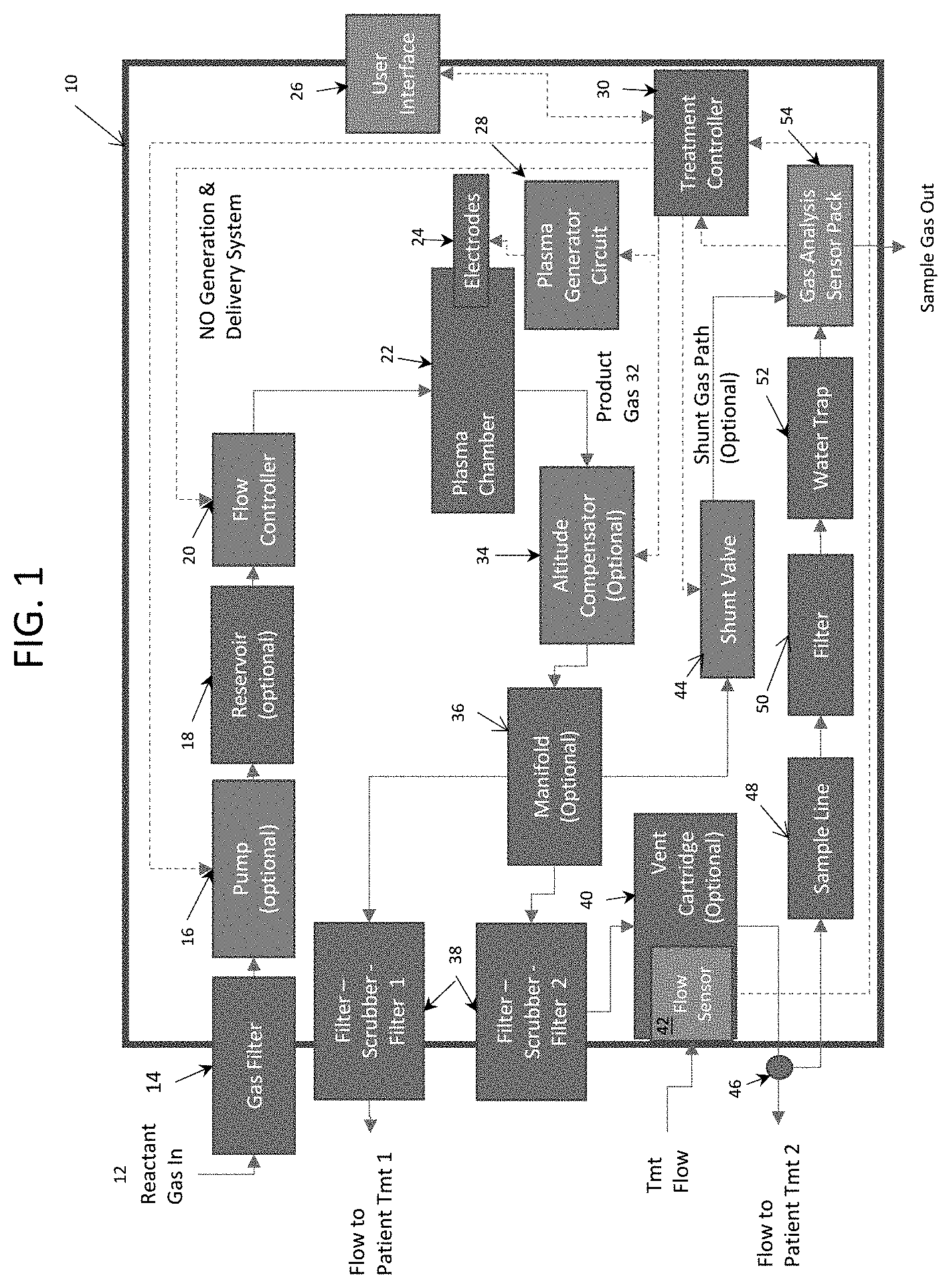
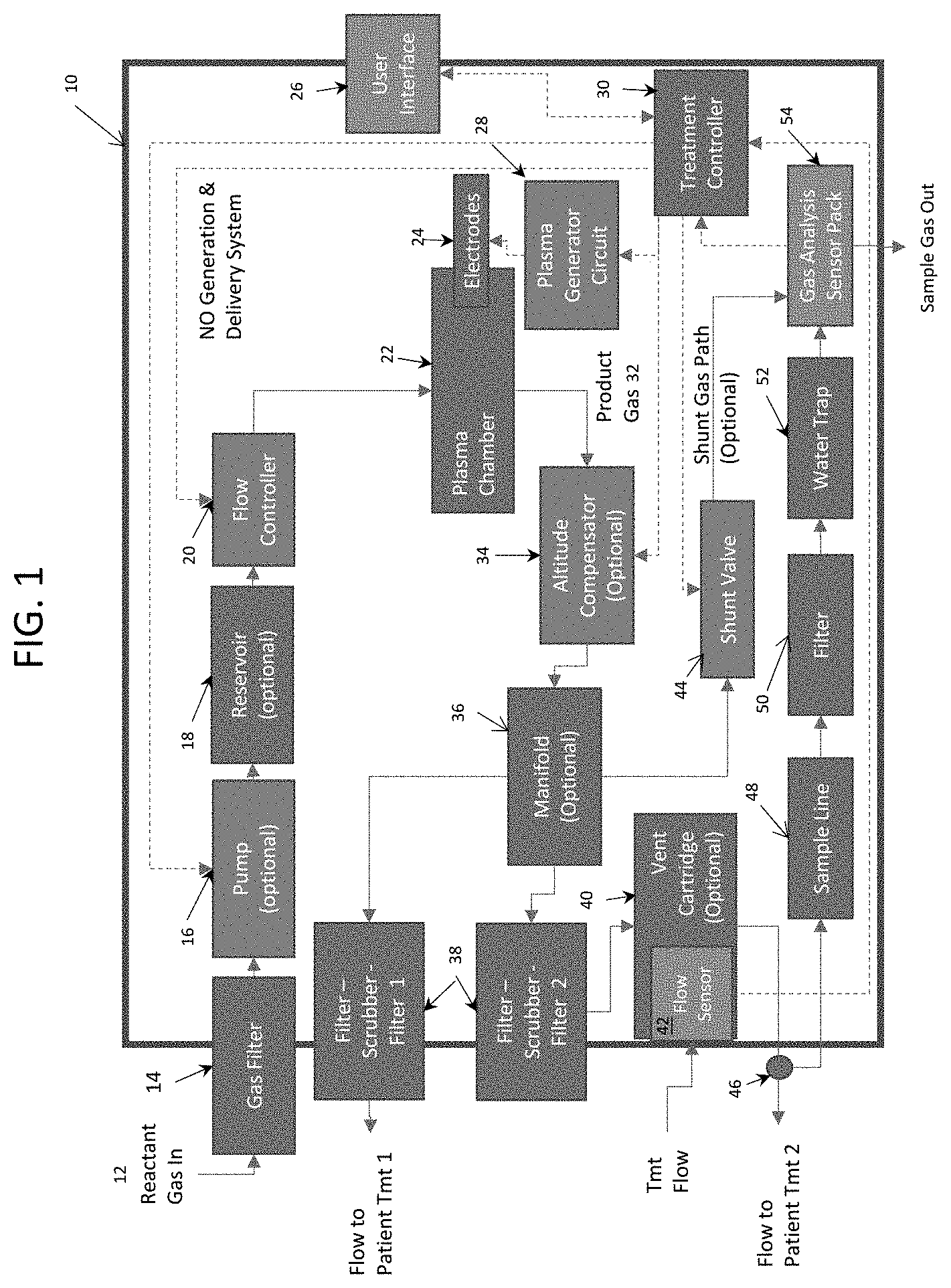
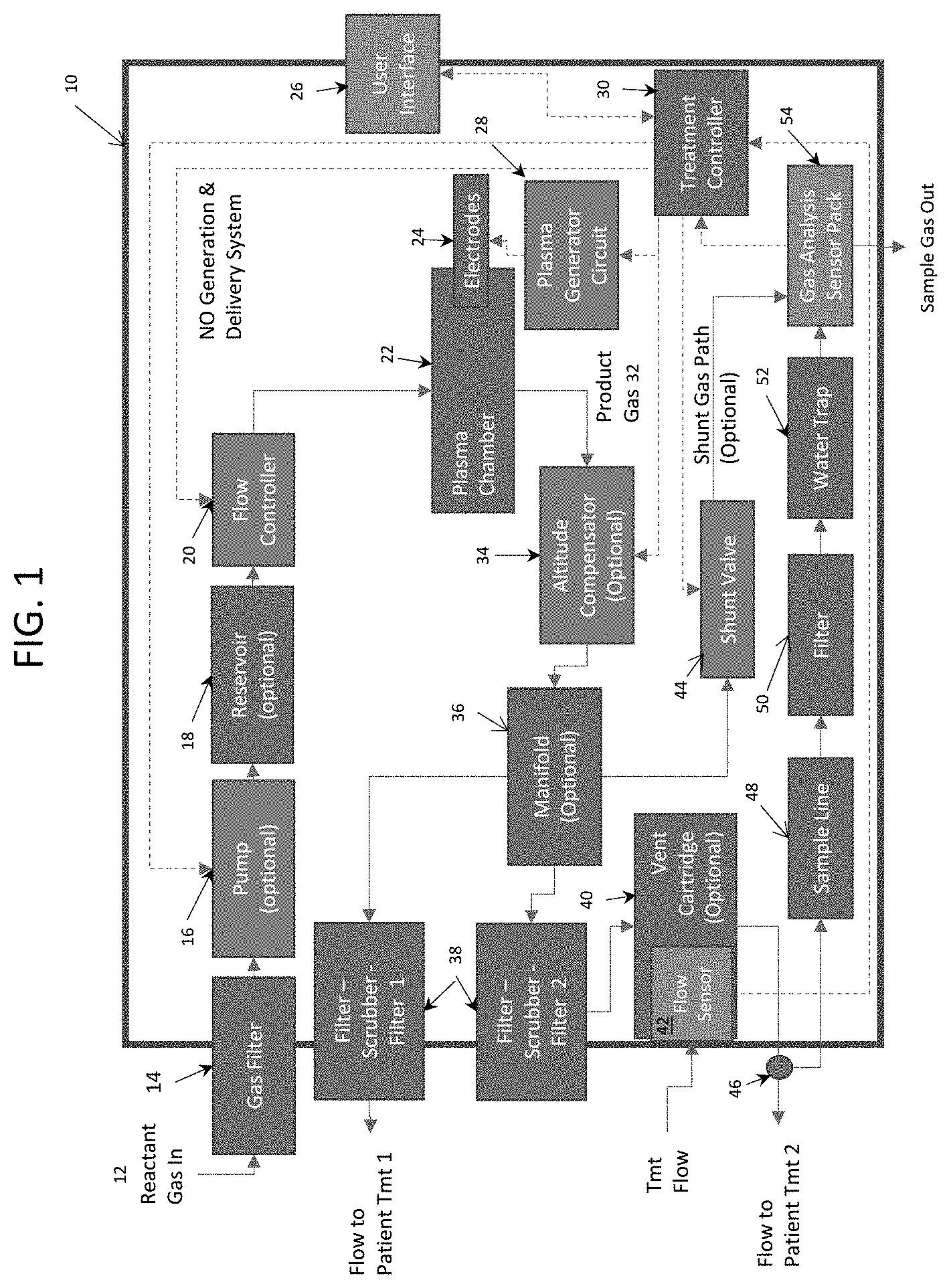
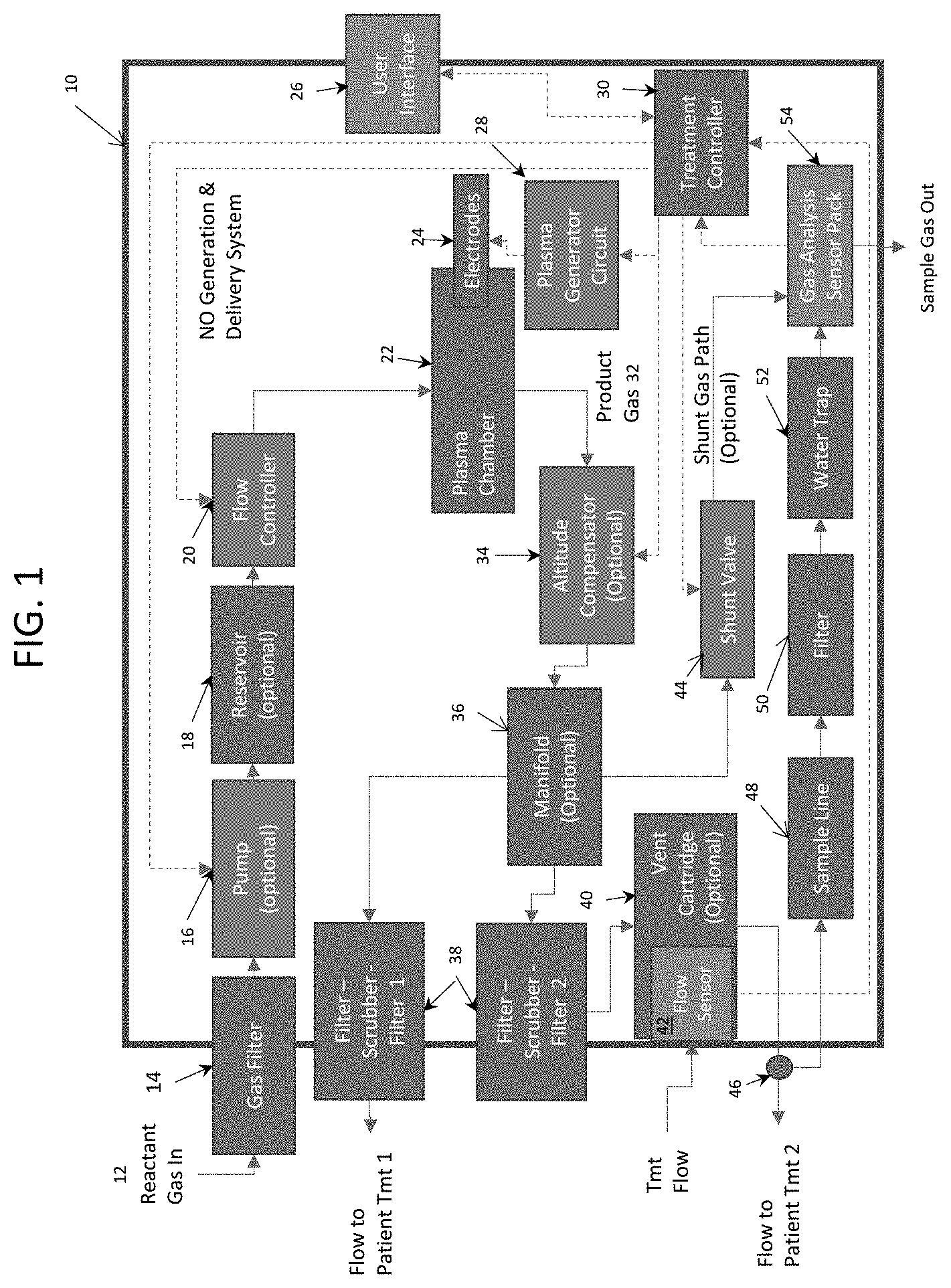
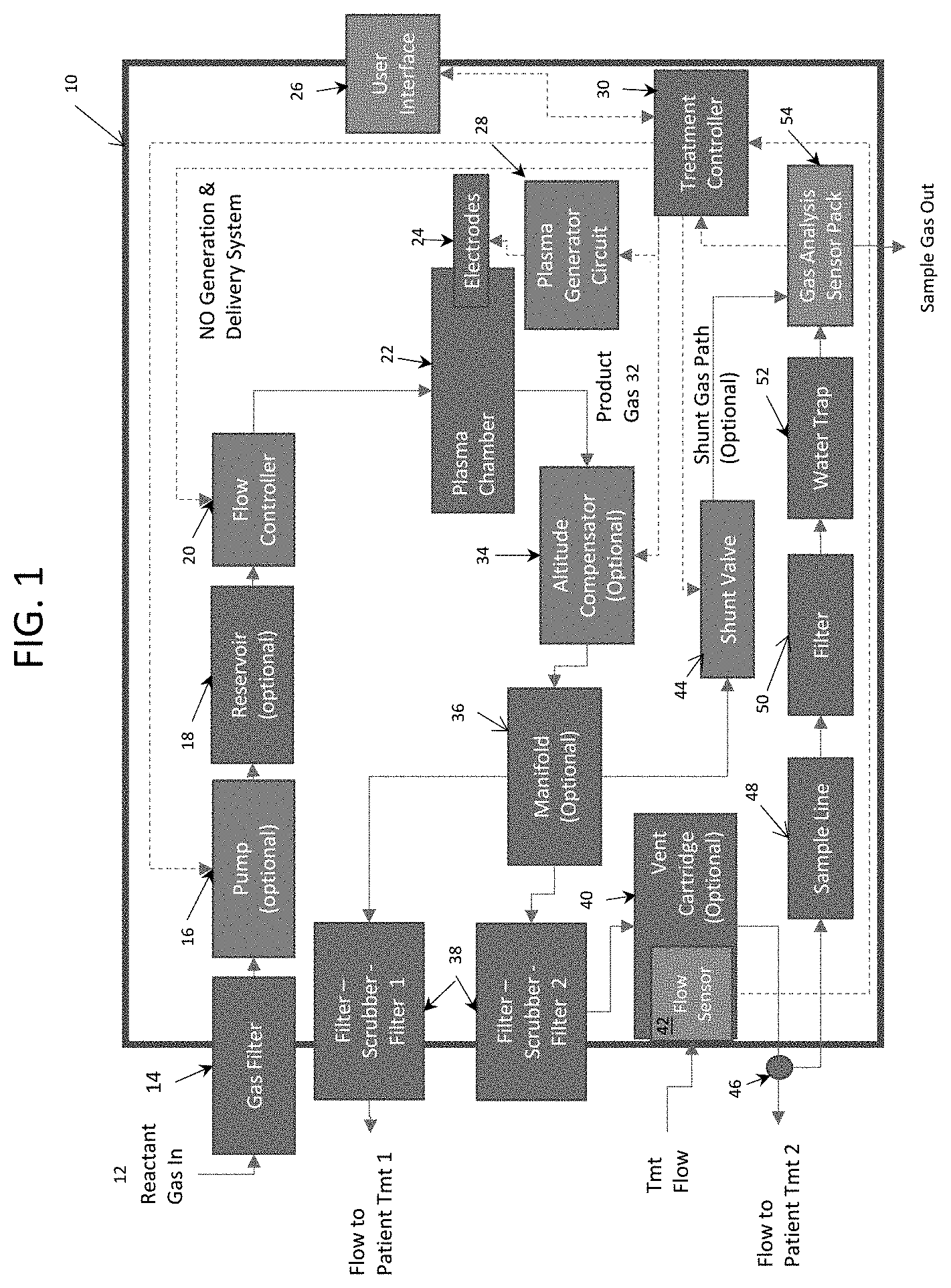
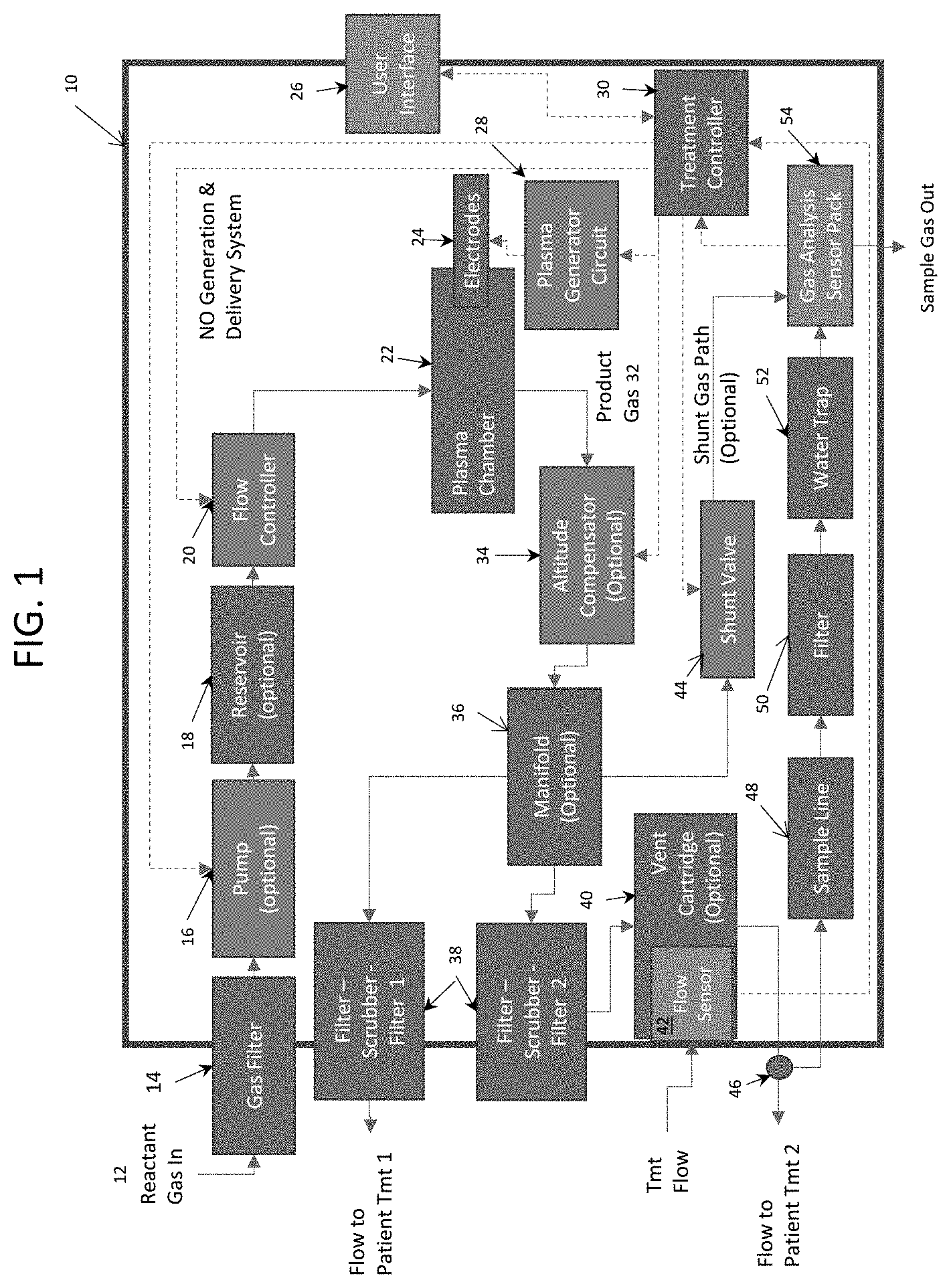
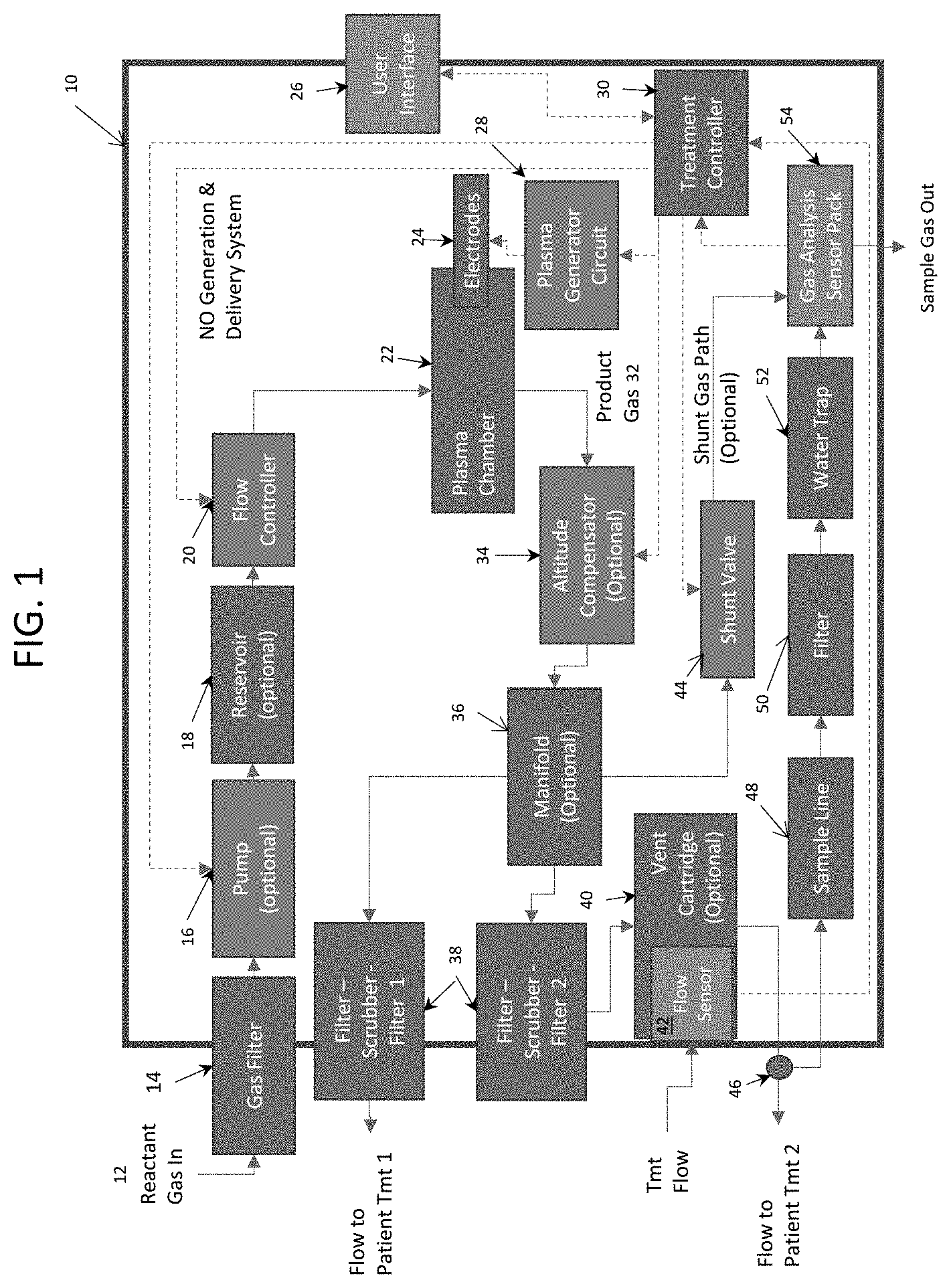
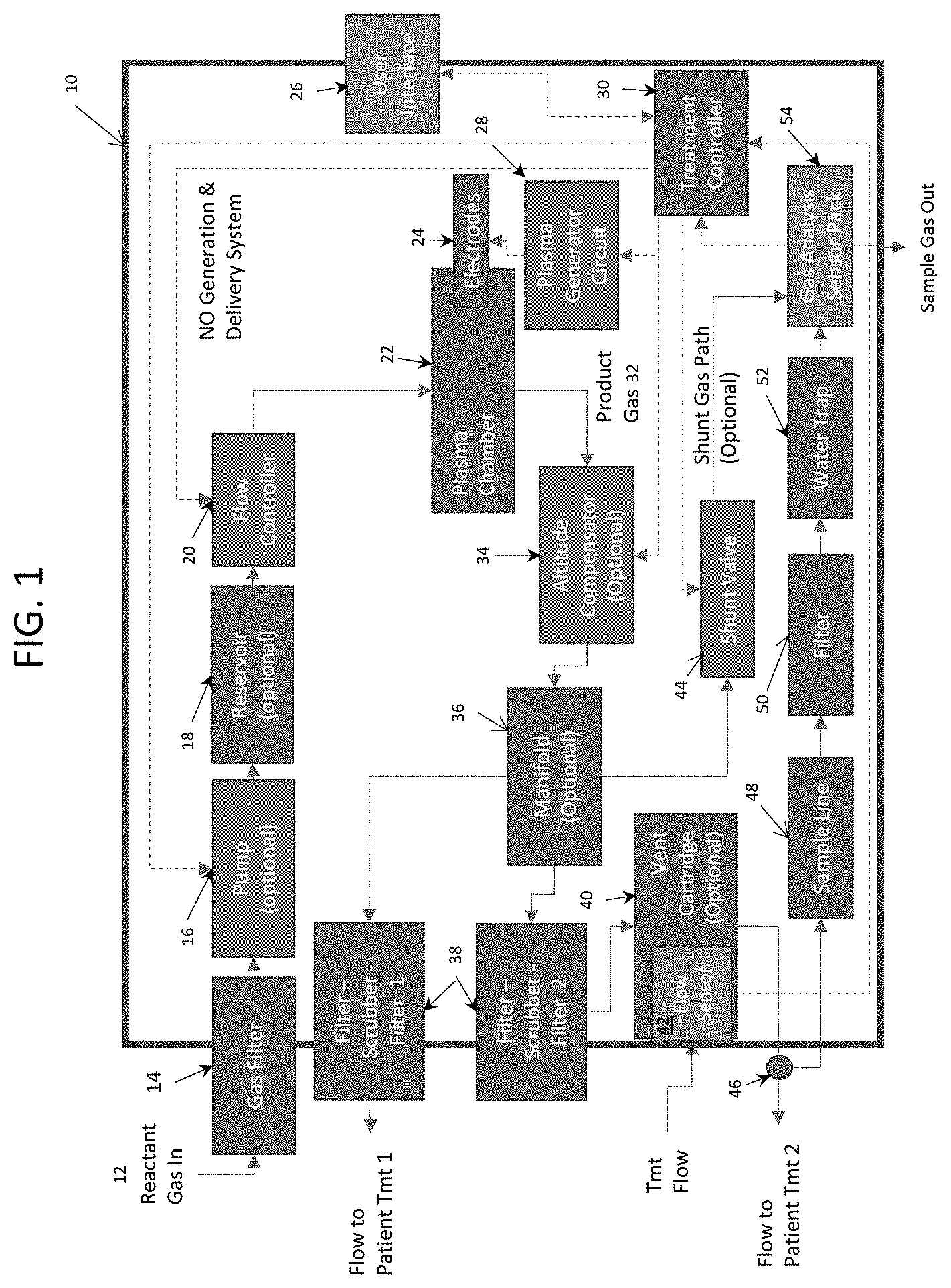
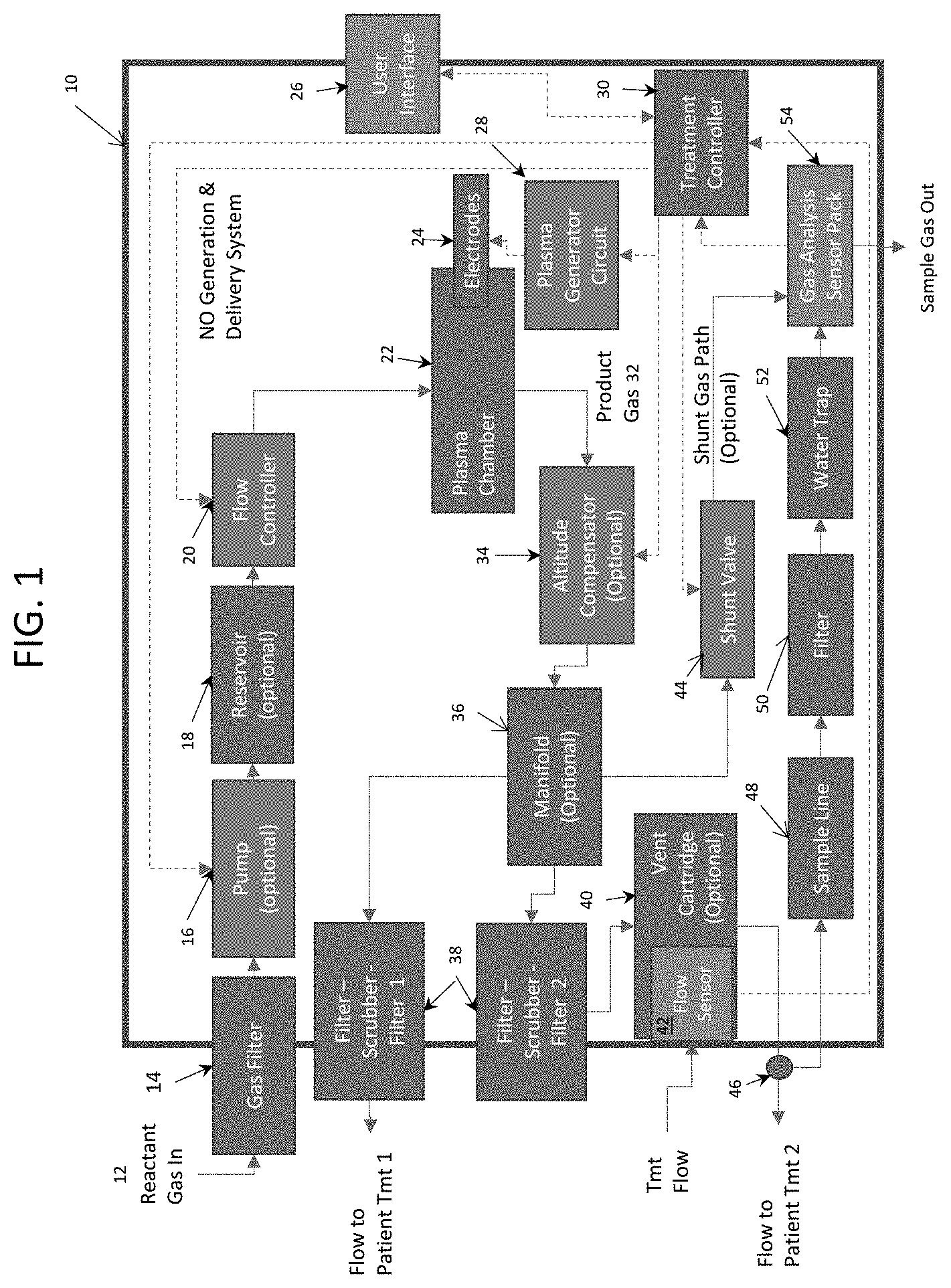
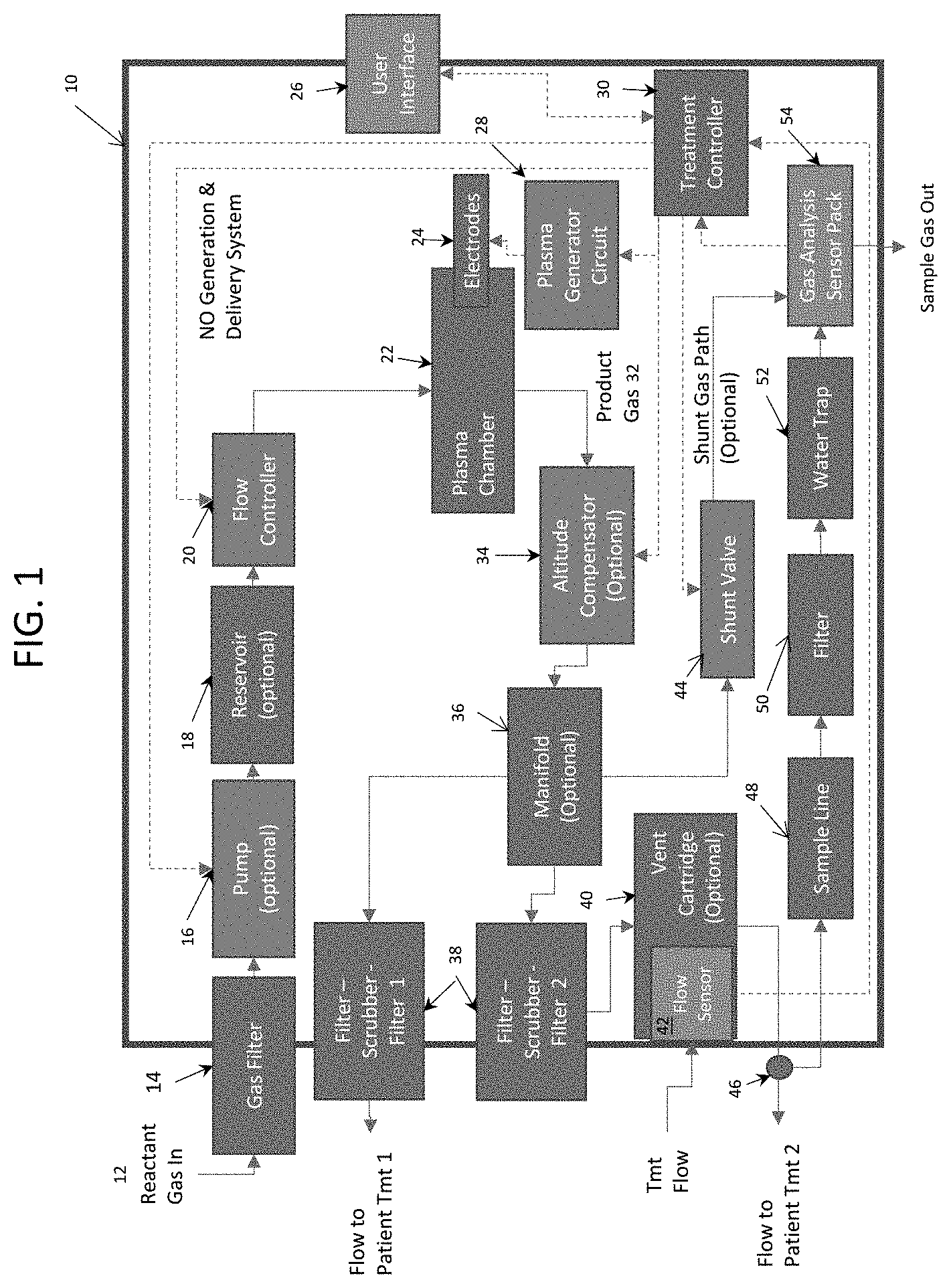
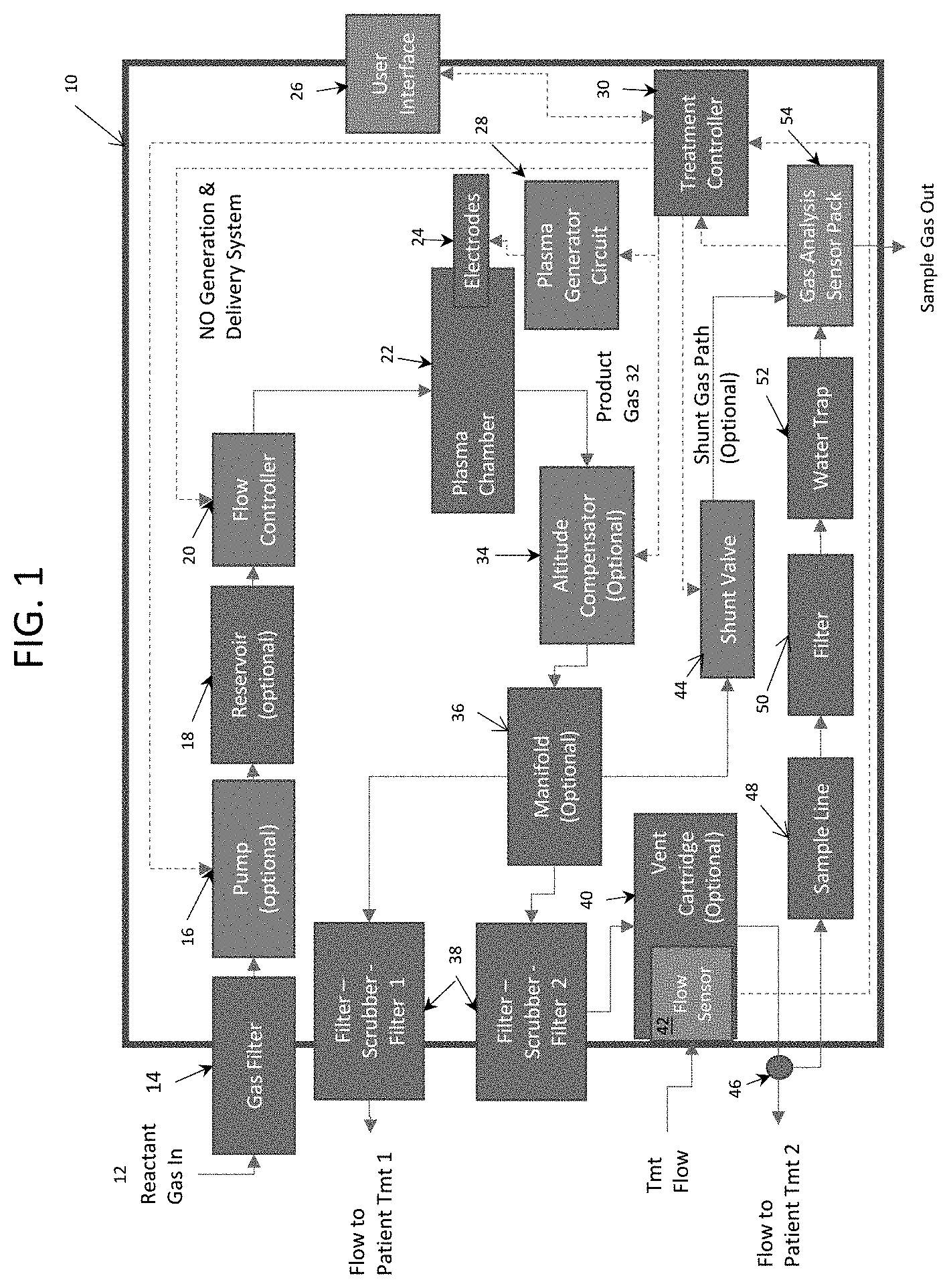
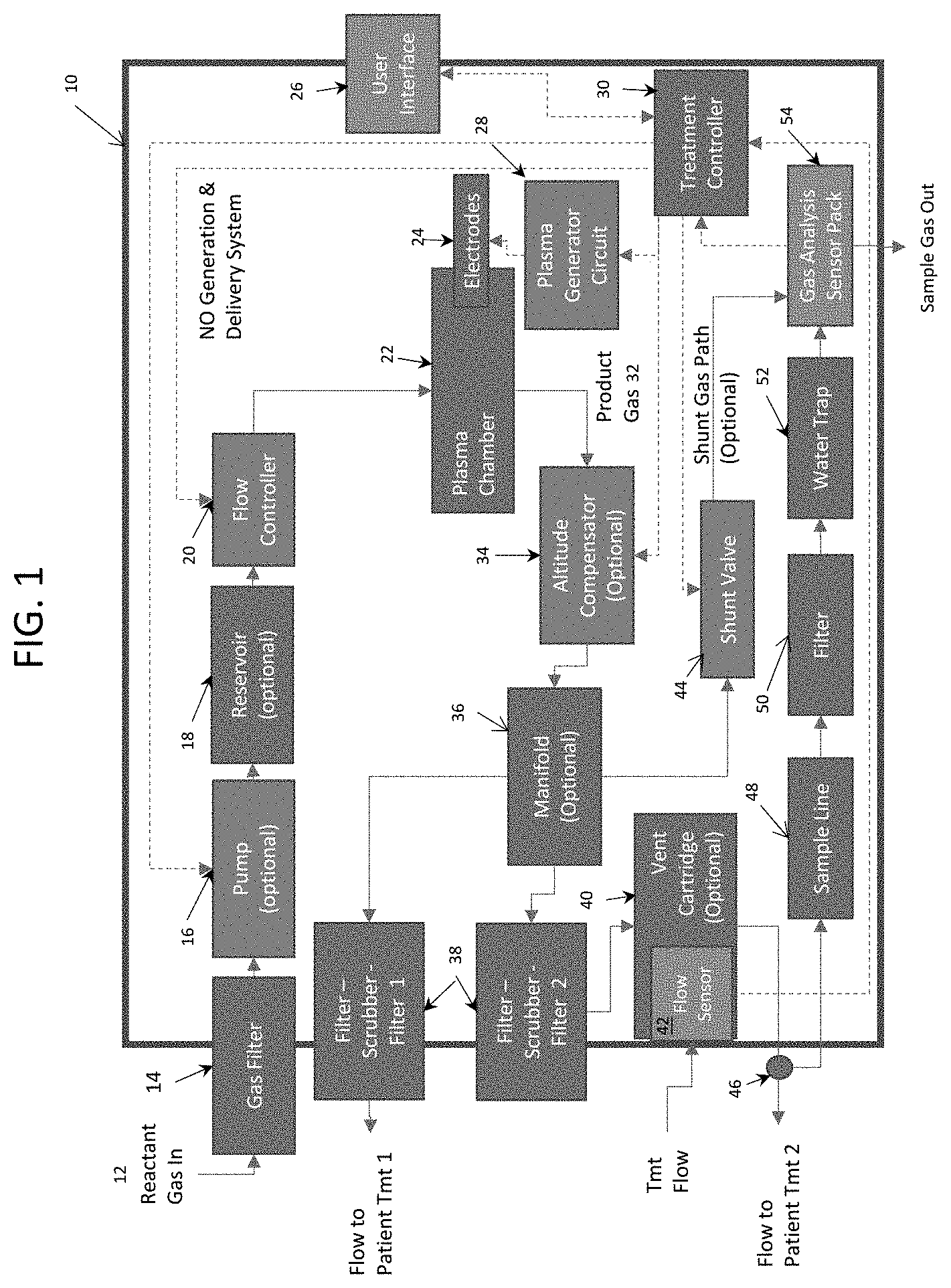
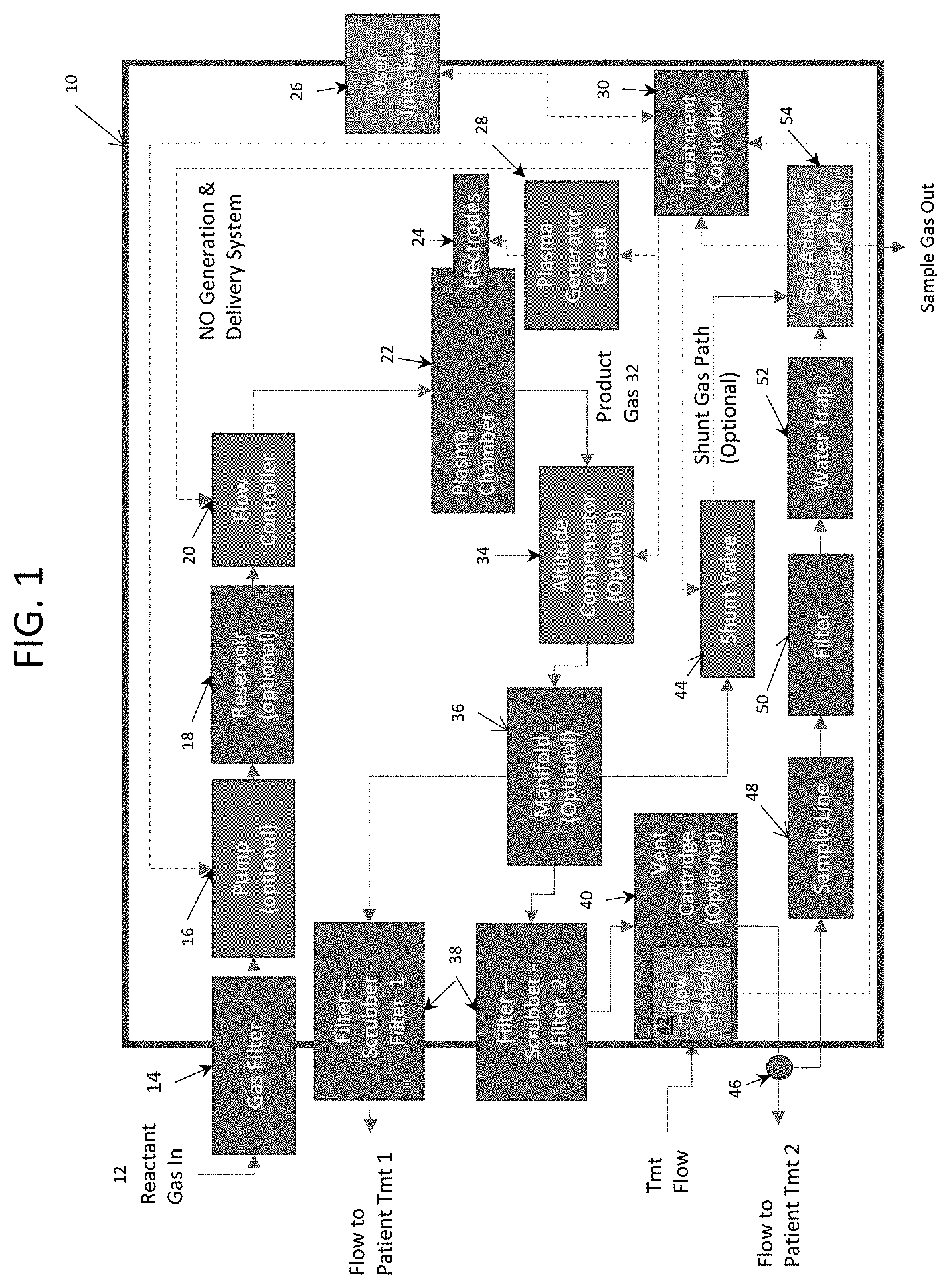
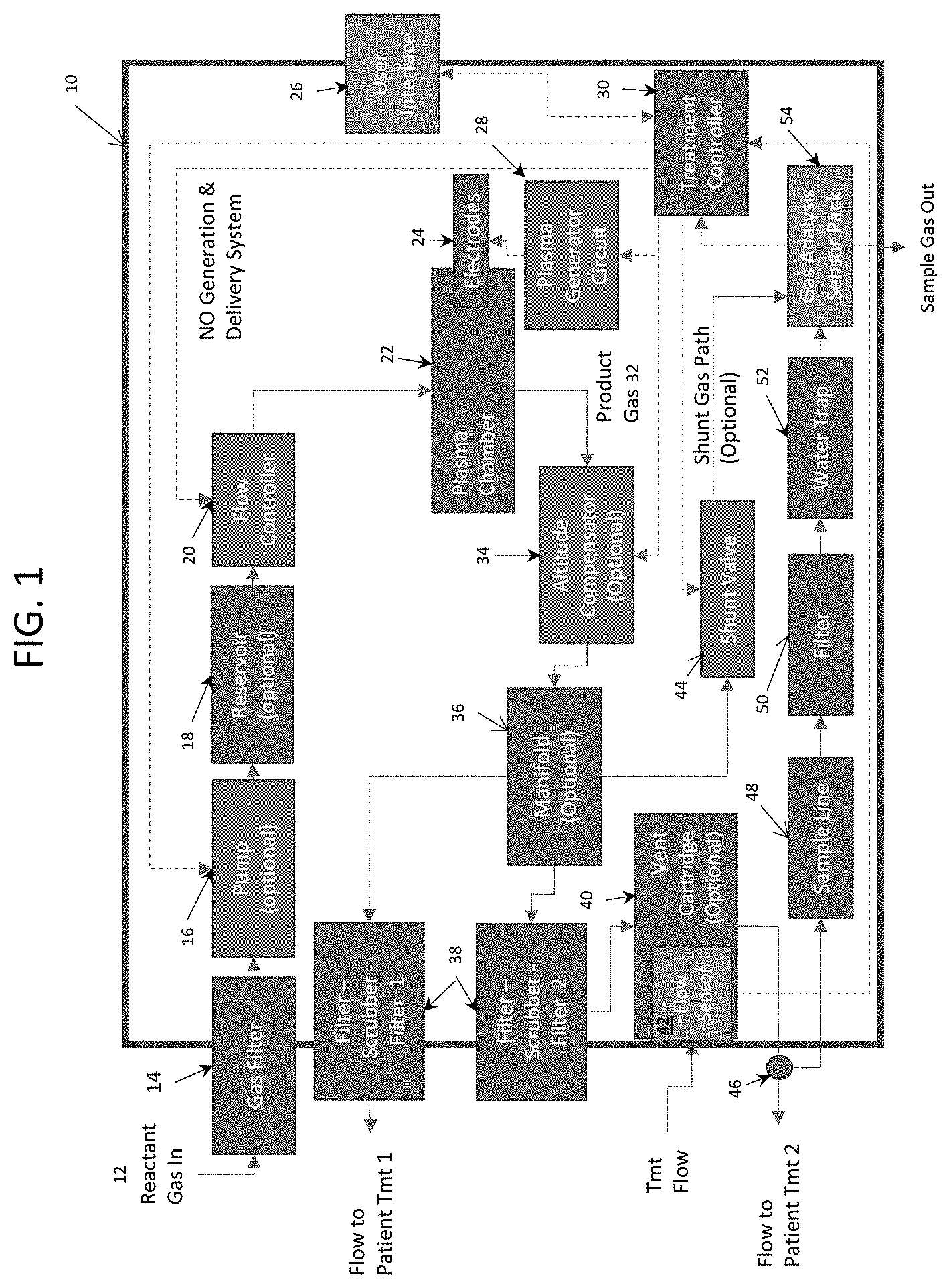
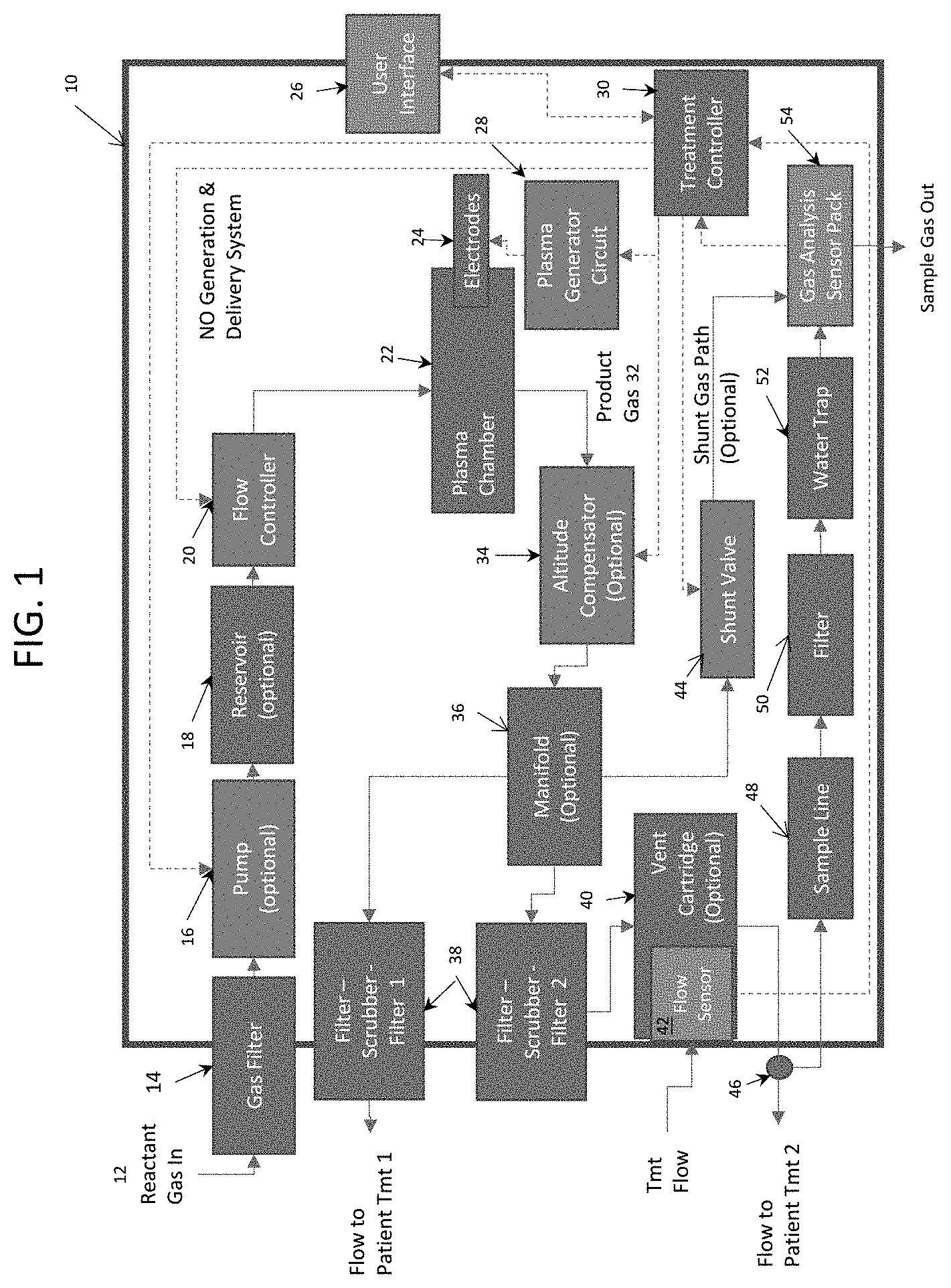
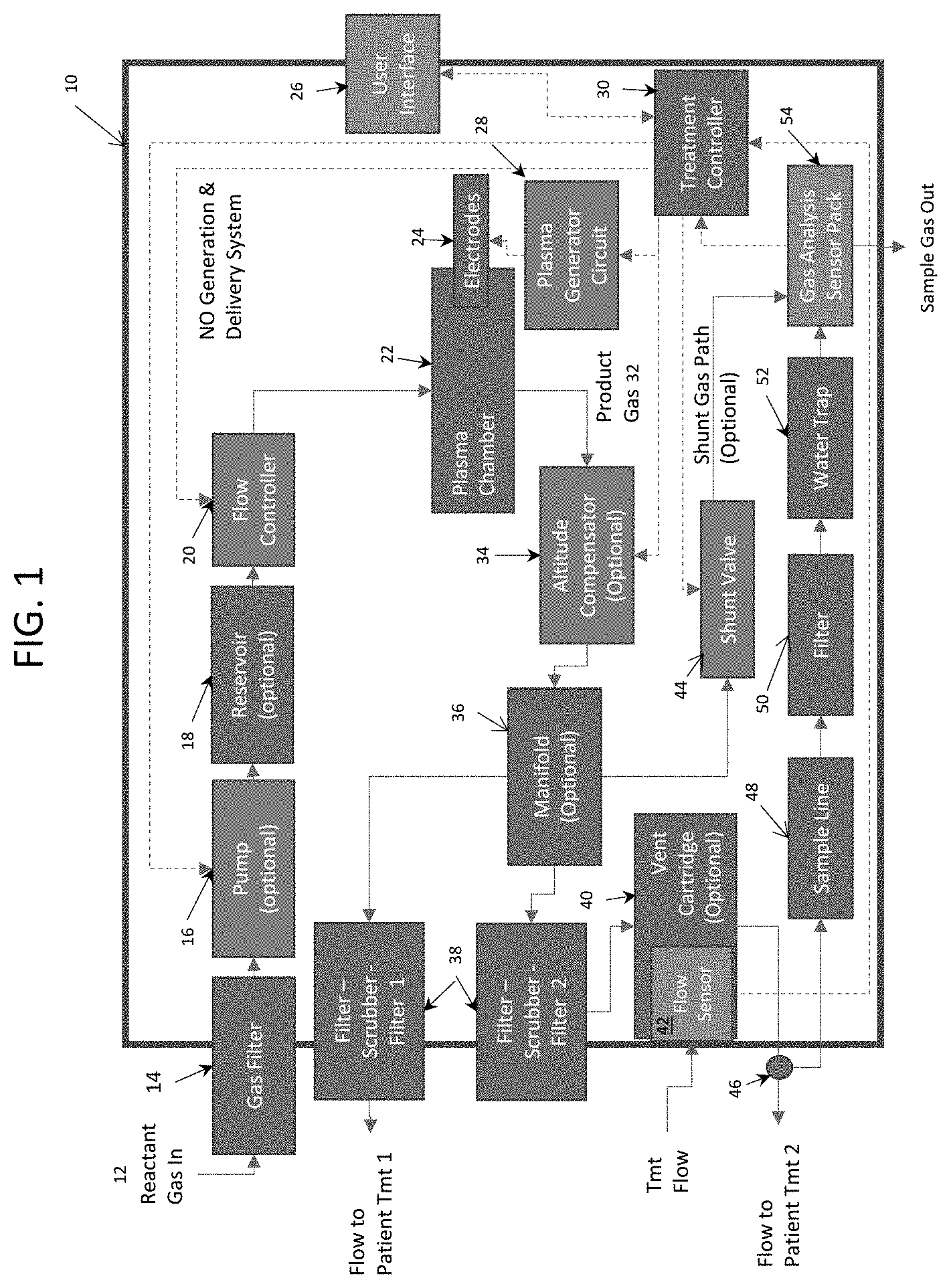

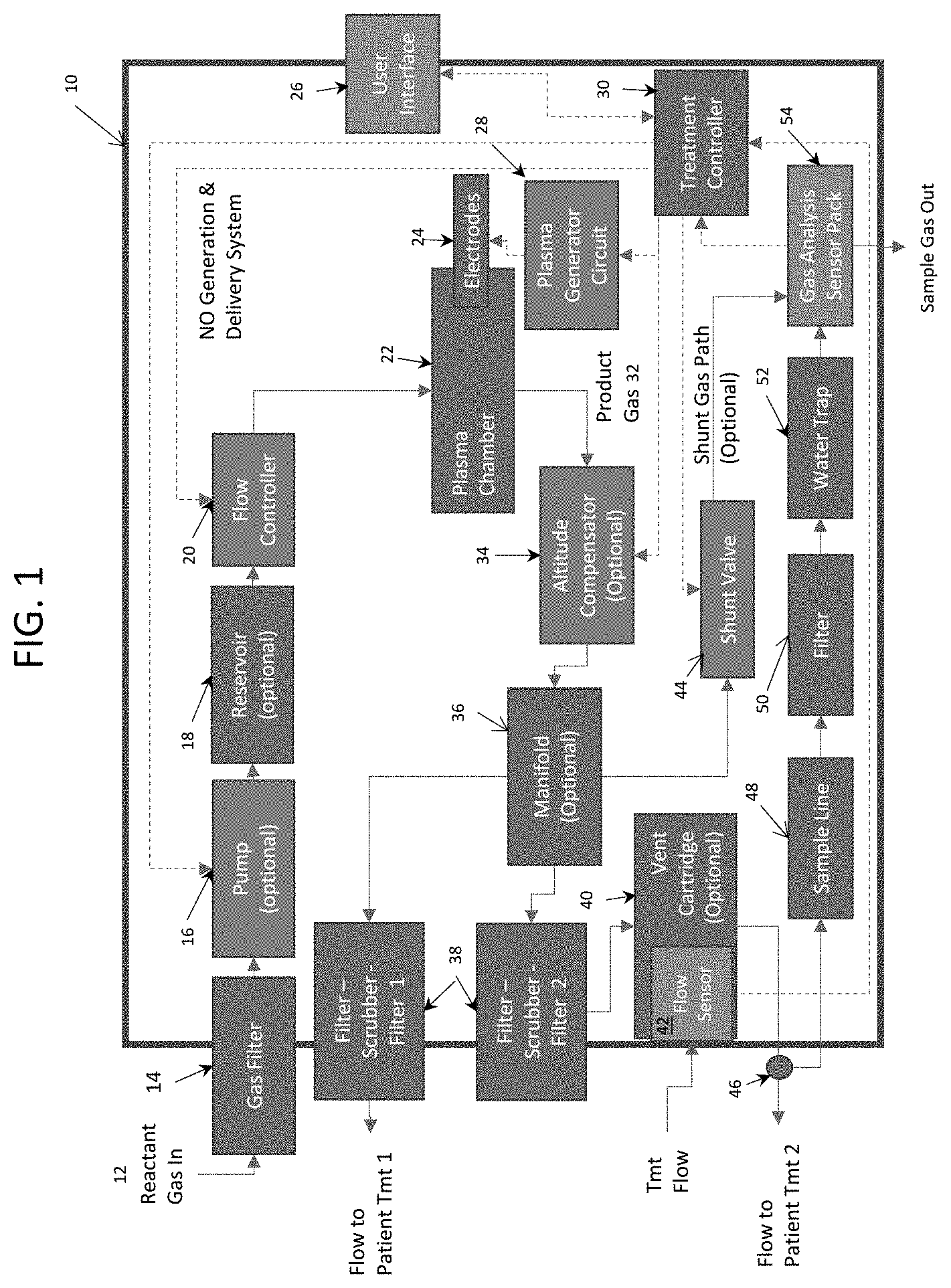

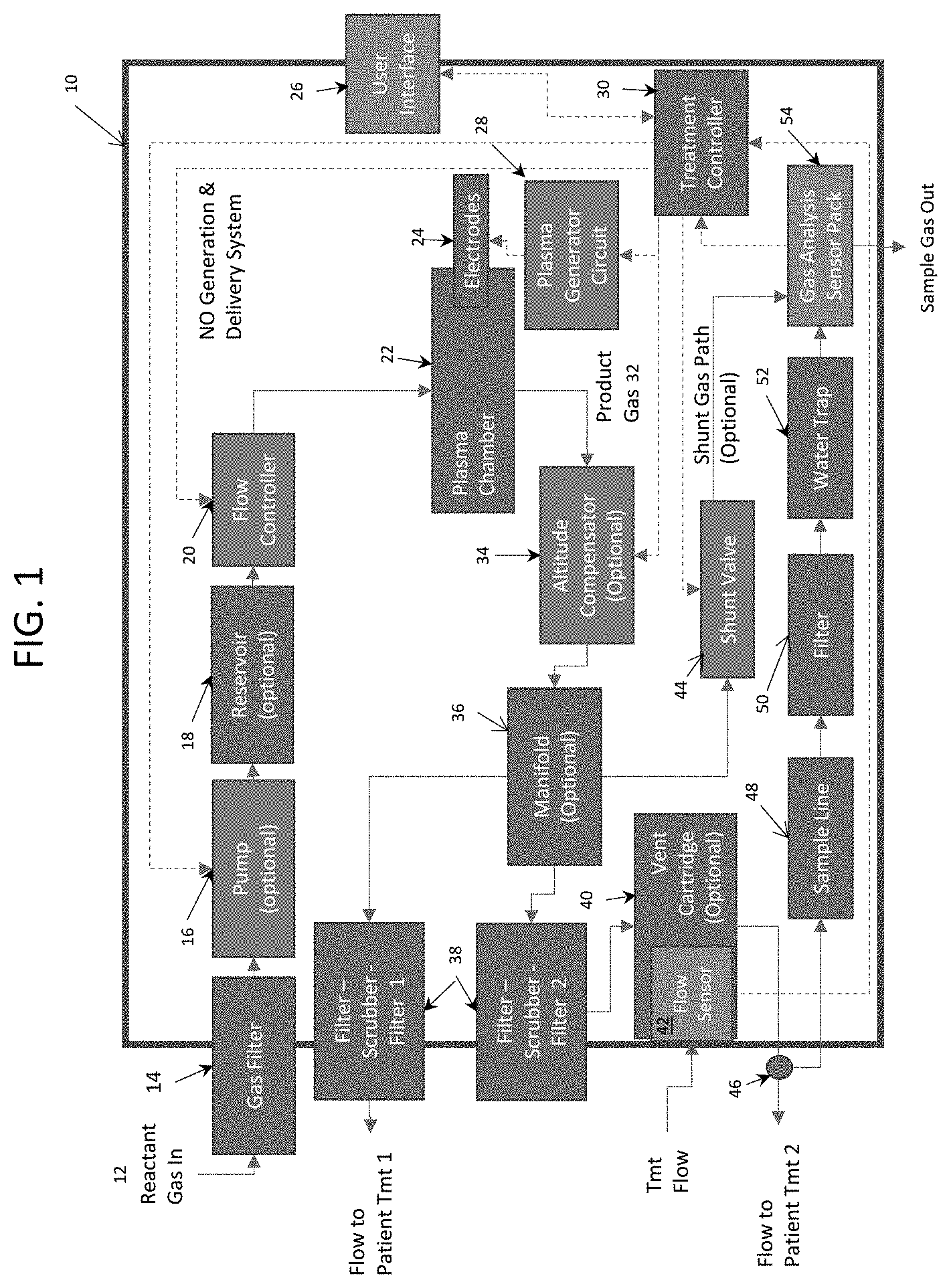
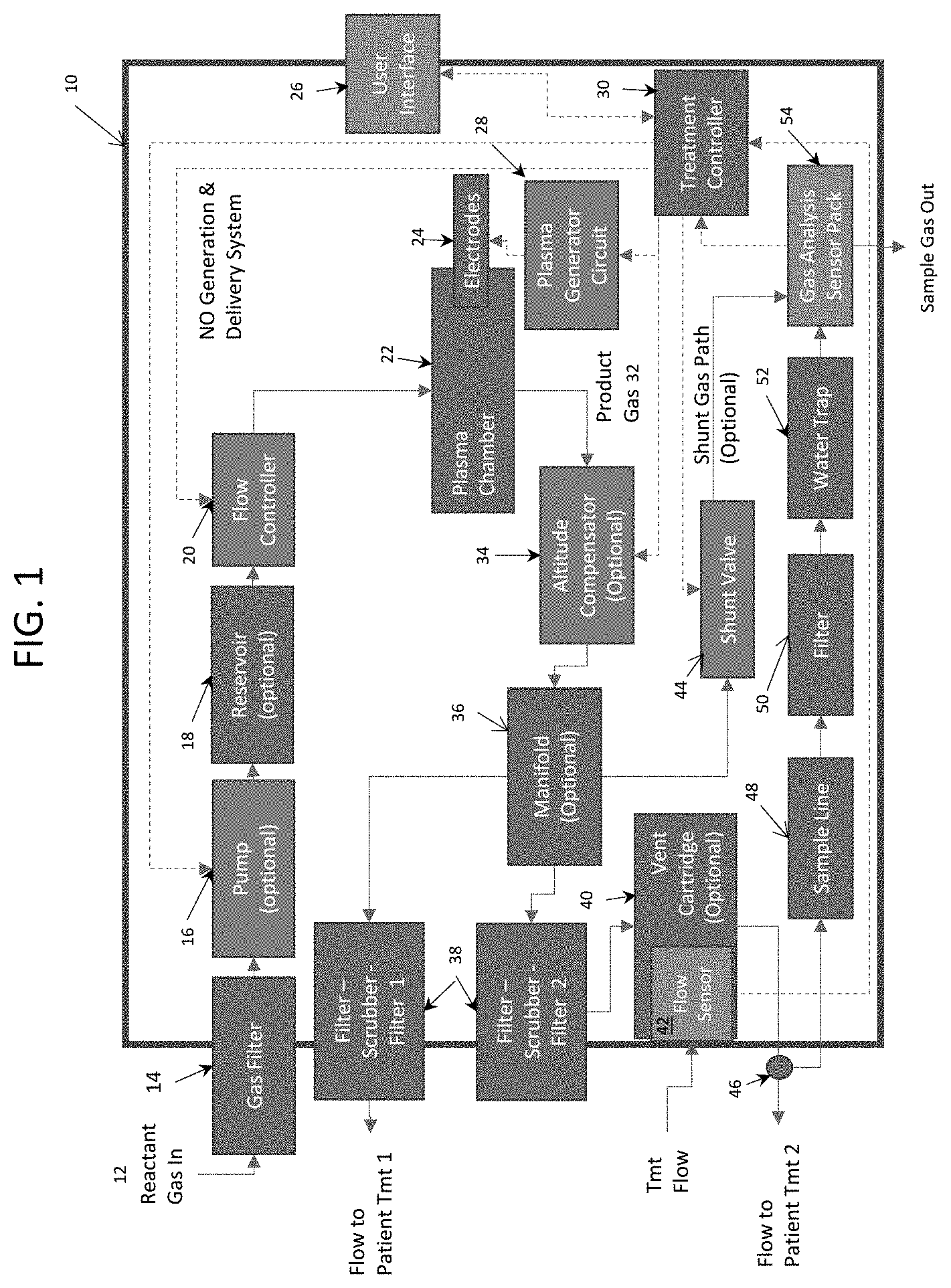
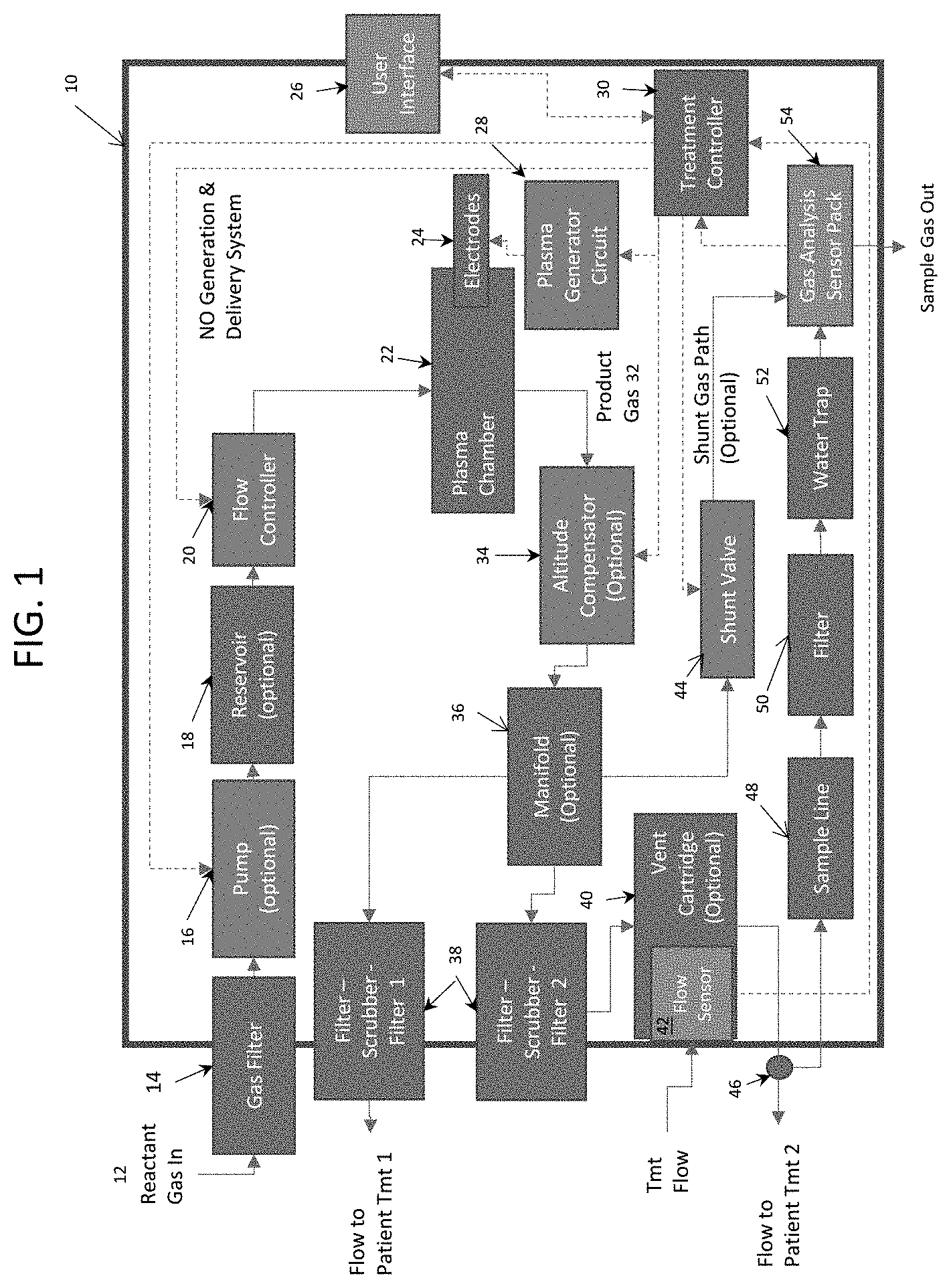
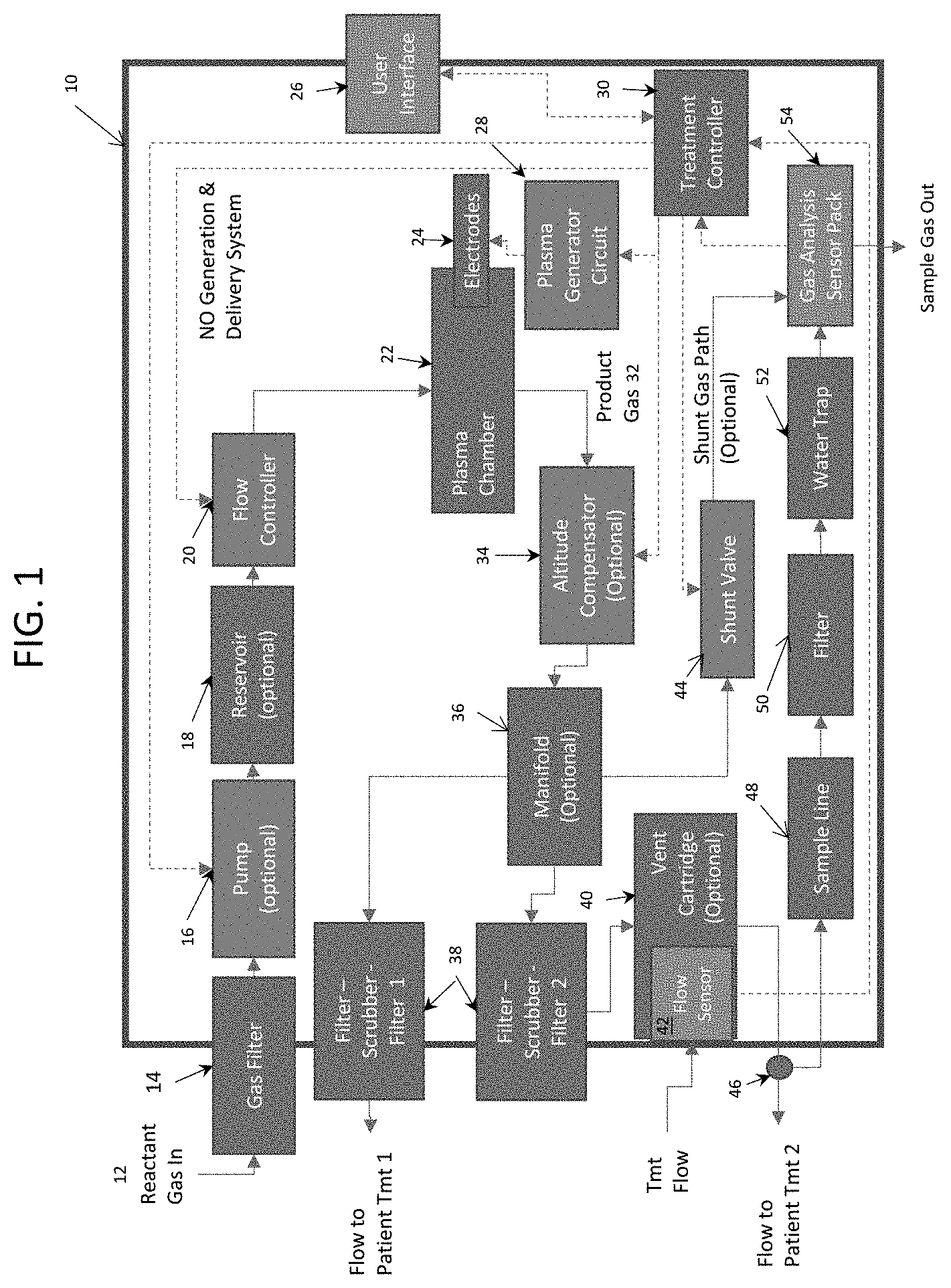
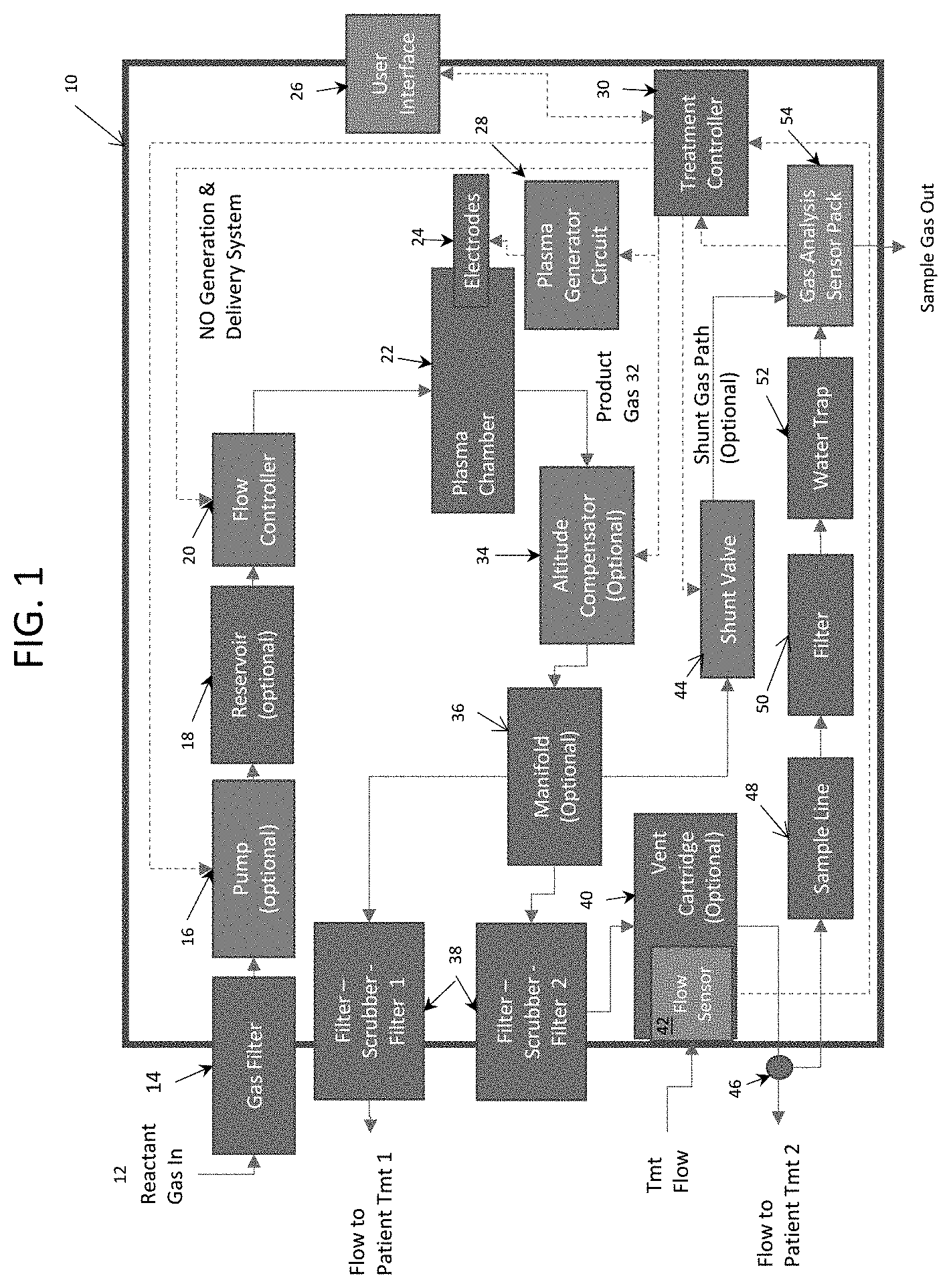
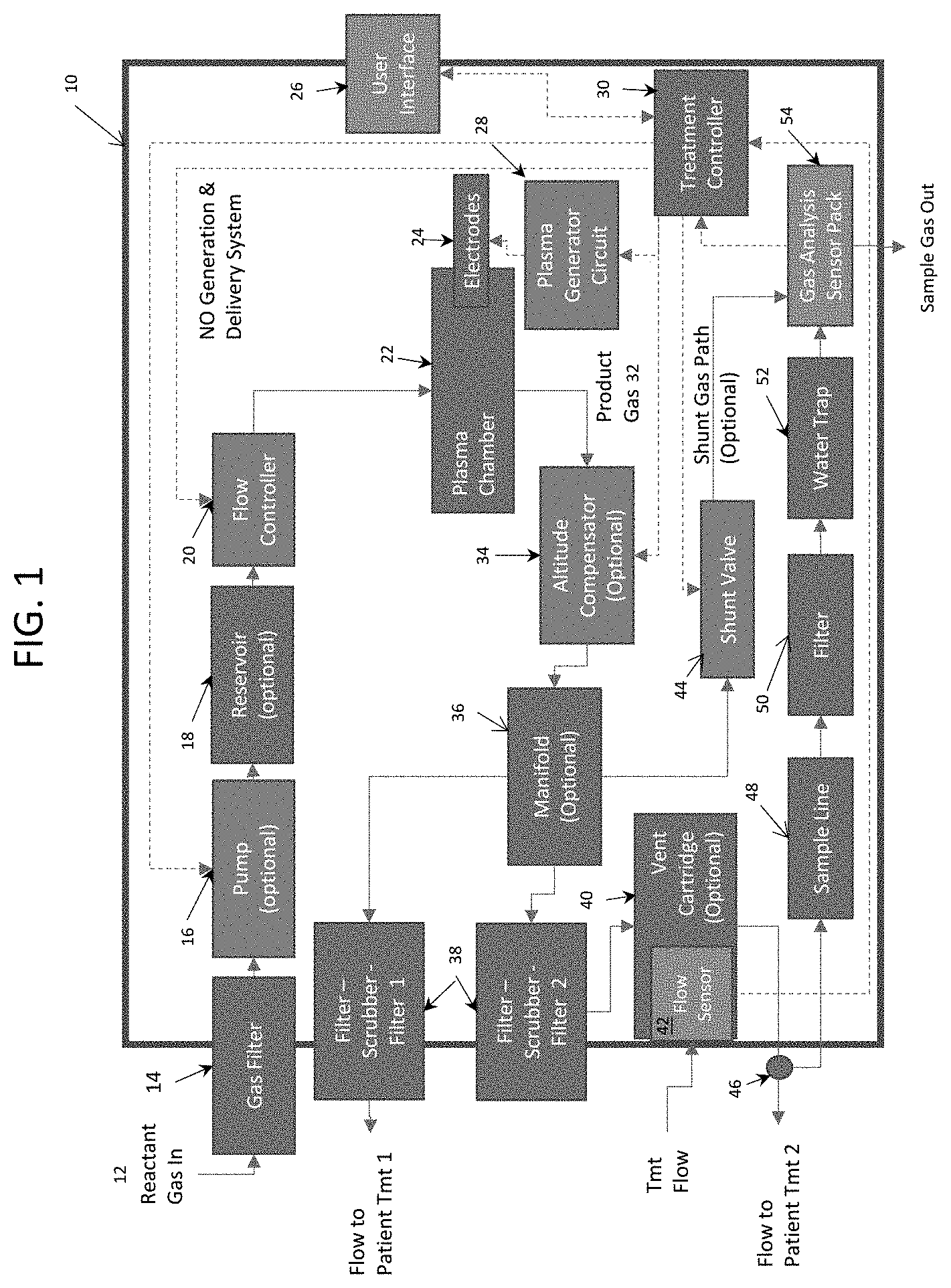
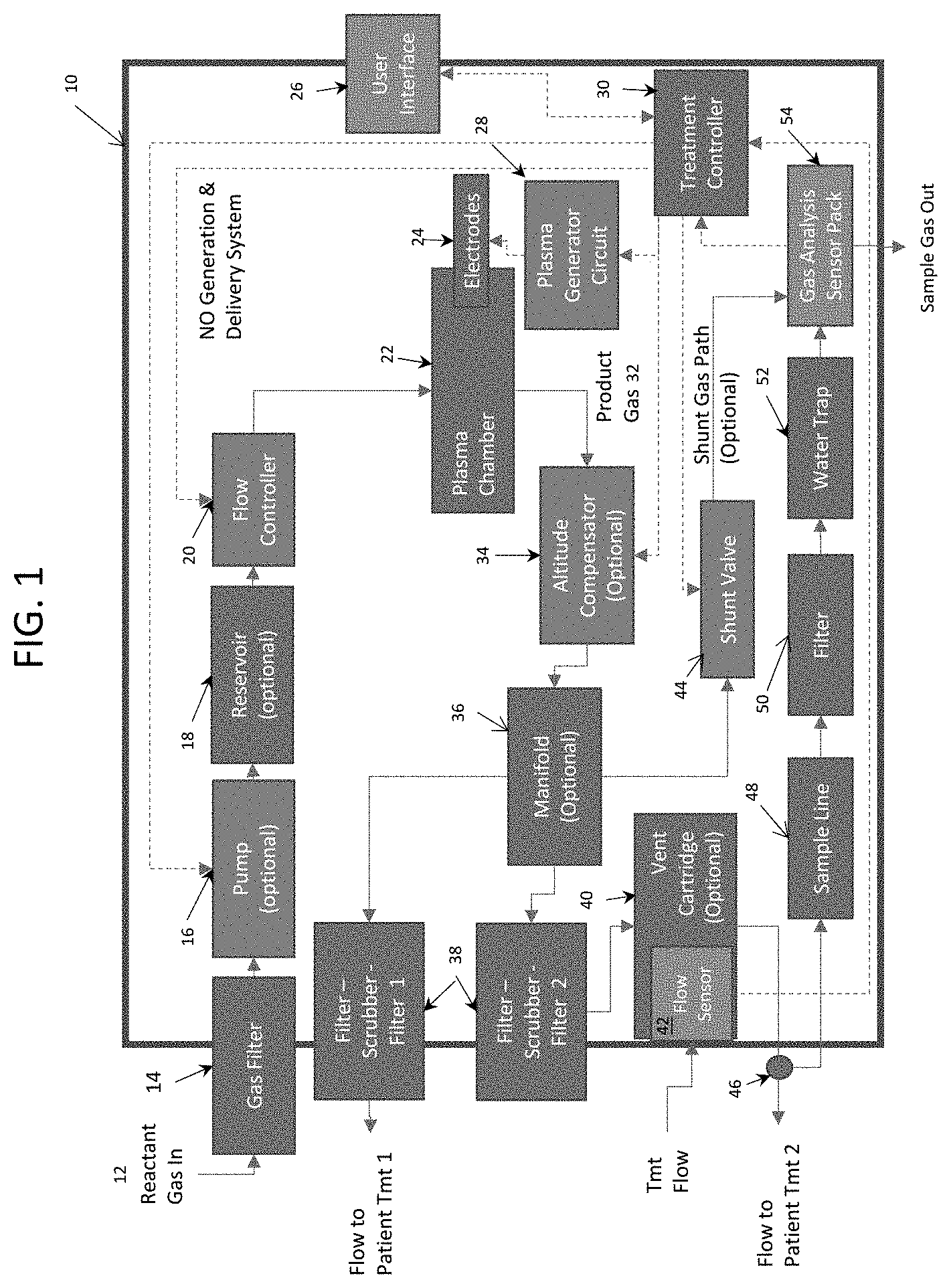
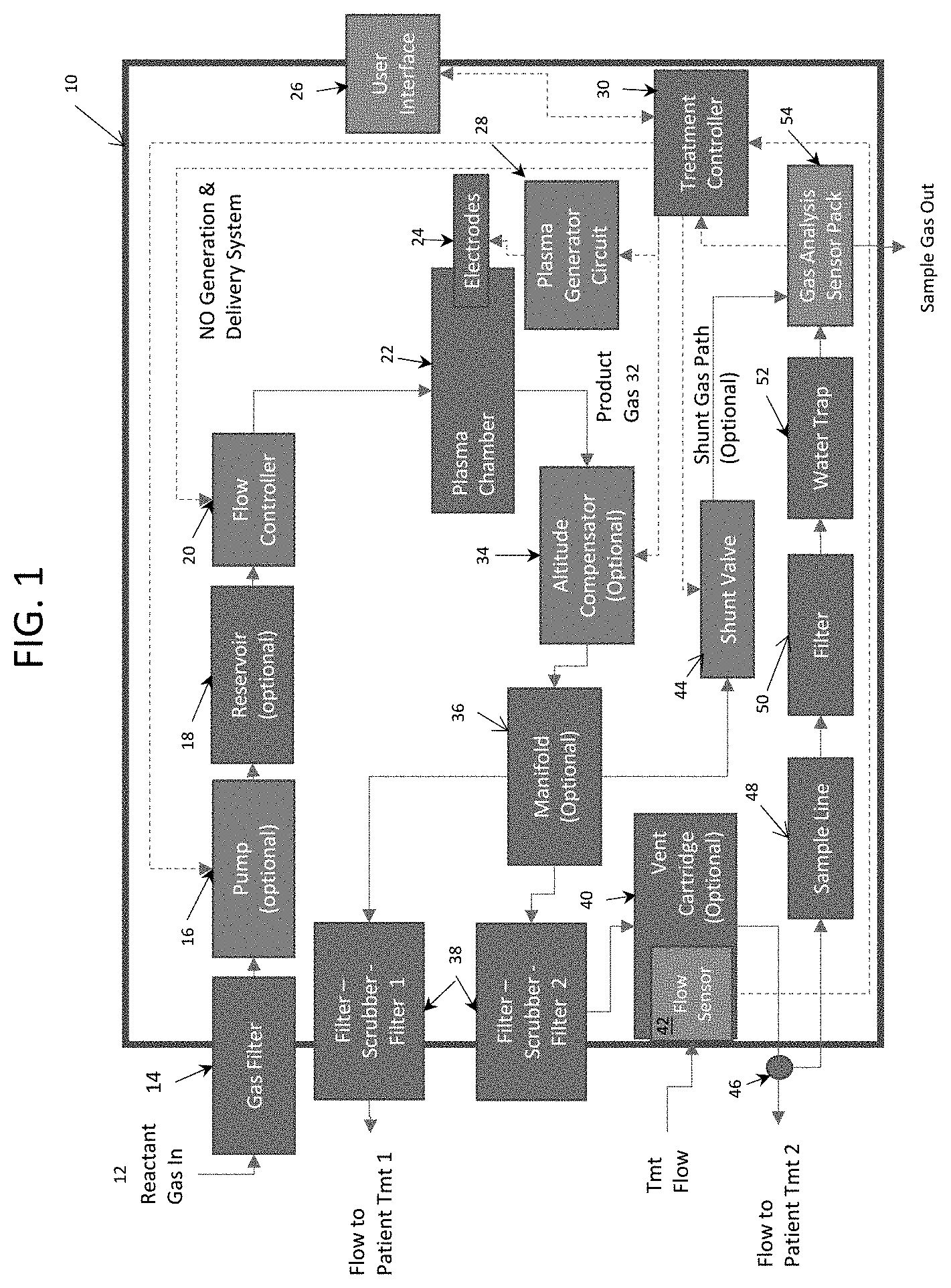