EXTRACTION AND SEPARATION METHOD
本発明は、原料流体から特定成分を抽出して分離する抽出分離方法に関する。
従来、原料流体から特定成分を抽出して分離するための抽出分離方法が知られている。例えば、下記特許文献1にこのような抽出分離方法の一例が開示されている。
下記特許文献1では、多数の流路が内部に設けられた流路構造体を備えた装置が原料流体(被抽出流体)からの特定成分(抽出対象物)の抽出分離に用いられている。流路構造体内の各流路には、原料流体と抽剤とが互いに接触した状態で流され、その流通過程で原料流体から抽剤へ前記特定成分が抽出される。流路構造体の外面には、分離ヘッダが取り付けられている。流路構造体内に設けられた上流側の流路の出口と下流側の流路の入口とが分離ヘッダの内部空間に連通している。上流側の流路を通って流れた原料流体と抽剤の混合流体は、その流路の出口から分離ヘッダの内部空間へ排出される。分離ヘッダの内部空間に排出された混合流体は、その内部空間において比重差により原料流体と抽剤とに分離する。分離した原料流体は、下流側の流路に導入されて前記特定成分のさらなる抽出が行われる。
上記特許文献1に開示された抽出分離方法では、分離ヘッダの内部空間に排出された混合流体を原料流体と抽剤とに完全に分離している。このため、分離ヘッダ内での混合流体の滞留時間が増大し、その結果、抽出分離にかかる処理時間が増大する。また、分離ヘッダが、混合流体が完全に原料流体と抽剤とに分離するまで混合流体を滞留させておくことが可能な大容量の内部空間を有している必要がある。このため、分離ヘッダが大型化し、それに伴って分離装置全体が大型化する。
本発明の目的は、抽出装置を小型化しつつ、原料流体からの特定成分の抽出分離にかかる処理時間を短縮することである。
本発明の一局面に従う抽出分離方法は、原料流体から特定成分を抽出して分離する方法であって、順次接続された複数段の抽出部を備えた抽出装置を用いて、原料流体から前記特定成分を抽出して分離する抽出分離工程を備え、前記抽出分離工程は、各段の前記抽出部において原料流体とその原料流体に対して比重差を有する抽剤とを互いに接触させた状態で流通させながら原料流体から抽剤へ前記特定成分を抽出する抽出工程と、前記抽出部から排出される流体の少なくとも一部を次段の前記抽出部へ原料流体と抽剤が混ざった状態で導入する導入工程と、最終段の前記抽出部から排出された流体を前記特定成分が抽出された後の原料流体と前記特定成分を抽出した抽剤とに分離する最終分離工程とを有する。
以下、本発明の実施形態について図面を参照して説明する。
(第1実施形態)
図1には、抽出分離装置1の全体構成が概略的に示されている。抽出分離装置1は、原料流体から特定成分の5段の抽出処理を行い、その抽出処理後の流体を原料流体と抽剤とに分離する分離処理を行うように構成されている。抽出分離装置1は、原料流体よりも比重の小さい抽剤を用いて抽出を行うように構成されている。この抽出分離装置1は、原料供給ポンプ2aと、抽剤供給ポンプ2bと、順次接続された第1~第5抽出部4~8を有する抽出装置3と、セトラー9と、第1~第5流入量調節弁10~14と、第1~第4排出量調節弁15~18と、最終排出量調節弁19と、液面計20とを備える。
原料供給ポンプ2aは、特定成分を含有した原料流体を抽出装置3の第1抽出部4へ供給(送出)するポンプである。
抽剤供給ポンプ2bは、原料流体から特定成分を抽出するための抽剤を抽出装置3の第1~第5抽出部4~8へ供給(送出)するポンプである。
抽出装置3は、原料流体から抽剤への特定成分の抽出を第1~第5抽出部4~8により順次行うものである。すなわち、抽出装置3は、5段の抽出処理を行うように構成されている。なお、第1抽出部4は、本発明における「最初の段の抽出部」の一例である。また、第5抽出部8は、本発明における「最終段の抽出部」の一例である。
第1抽出部4は、1段目の抽出処理を行うものである。図1では、第1~第5抽出部4~8が模式的に表されているが、第1抽出部4は、具体的には、例えば図2に示すような構造を有する。第1抽出部4は、積層体24と、原料供給ヘッダ25と、抽剤供給ヘッダ26と、排出ヘッダ27とを有する。
積層体24は、厚み方向に互いに積層された多数のプレート30によって形成されている。積層体46を形成する多数のプレート30には、抽出プレート31(図3参照)が複数含まれている。各抽出プレート31には、原料流体と抽剤を流通させるマイクロチャネル(微細流路)である多数の抽出流路33が設けられている。各抽出流路33は、例えば、図3に示すような構造を有する。具体的に、各抽出流路33は、原料導入路34と、抽剤導入路35と、合流部36と、合流流体流路37とからなる。原料導入路34は、原料流体が導入されて流れる部分である。抽剤導入路35は、抽剤が導入されて流れる部分である。合流部36は、原料導入路34と抽剤導入路35の下流側の端部に繋がり、原料導入路34を流れた原料流体と抽剤導入路35を流れた抽剤が合流する部分である。合流流体流路37は、合流部36の下流側に繋がり、合流した後の原料流体と抽剤が互いに接触した状態で流れる部分である。
各原料導入路34及び各抽剤導入路35は、抽出プレート31の厚み方向における一方の板面に溝を形成し、その板面に形成された溝の開口をその板面に積層されて接合された他のプレート30で封止することによって形成されている。また、各合流流体流路37は、原料導入路34及び抽剤導入路35が形成された抽出プレート31の一方の板面の反対側の板面に溝を形成し、その板面に形成された溝の開口をその板面に積層されて接合された他のプレート30で封止することによって形成されている。また、各合流部36は、抽出プレート31を厚み方向に貫通する貫通穴からなる。各抽出プレート31に設けられた複数の抽出流路33は、抽出プレート31の積層方向と直交する方向に配列されている。積層体24は、多数の抽出流路33を内部に有する多流路構造体となっている。
原料供給ヘッダ25(図2参照)は、各抽出流路33の各原料導入路34(図3参照)へ原料流体を分配して供給するためのヘッダである。原料供給ヘッダ25は、その内部空間が積層体24に設けられた全ての抽出流路33の原料導入路34の入口34aと連通するように積層体24に取り付けられている。原料供給ヘッダ25には、原料供給ポンプ2a(図1参照)の吐出口に繋がる原料供給配管21が接続されている。
抽剤供給ヘッダ26(図2参照)は、各抽出流路33の各抽剤導入路35(図3参照)へ抽剤を供給するためのヘッダである。抽剤供給ヘッダ26は、その内部空間が積層体24に設けられた全ての抽出流路33の抽剤導入路35の入口35aと連通するように積層体24に取り付けられている。抽剤供給ヘッダ26には、抽剤供給ポンプ2b(図1参照)の吐出口に繋がる抽剤供給配管22の第1分岐管22aが接続されている。
排出ヘッダ27(図2参照)は、各抽出流路33の各合流流体流路37の出口37a(図3参照)から原料流体と抽剤との混合流体が排出されるヘッダである。排出ヘッダ27は、その内部空間が積層体24に設けられた全ての抽出流路33の合流流体流路37の出口37aと連通するように積層体24に取り付けられている。排出ヘッダ27の下部には、第1接続配管23a(図1参照)が接続されている。排出ヘッダ27の上部には、第1排出配管28aが接続されている。
第2~第5抽出部5~8は、2~5段目の抽出処理をそれぞれ行うものである。第2~第5抽出部5~8は、第1抽出部4と同様の構成をそれぞれ有する。具体的に、第2抽出部5は、積層体40、原料供給ヘッダ41、抽剤供給ヘッダ42及び排出ヘッダ43を有する。第3抽出部6は、積層体46、原料供給ヘッダ47、抽剤供給ヘッダ48及び排出ヘッダ49を有する。第4抽出部7は、積層体52、原料供給ヘッダ53、抽剤供給ヘッダ54及び排出ヘッダ55を有する。第5抽出部8は、積層体58、原料供給ヘッダ59、抽剤供給ヘッダ60及び排出ヘッダ61を有する。第2~第5抽出部5~8の積層体40,46,52,58は、第1抽出部8の積層体24に対応する構造を有する。第2~第5抽出部5~8の原料供給ヘッダ41,47,53,59は、第1抽出部8の原料供給ヘッダ25に対応する構造を有する。第2~第5抽出部5~8の抽剤供給ヘッダ42,48,54,60は、第1抽出部4の抽剤供給ヘッダ26に対応する構造を有する。第2~第5抽出部5~8の排出ヘッダ43,49,55,61は、第1抽出部8の排出ヘッダ27に対応する構造を有する。なお、排出ヘッダ27,43,49,55,61は、本発明の排出部の一例である。
第2抽出部5の原料供給ヘッダ41は、第1接続配管23aを介して第1抽出部4の排出ヘッダ27と繋がっている。すなわち、第2抽出部5の各抽出流路33の原料導入路34の入口34aは、第2抽出部5の原料供給ヘッダ41の内部空間及び第1接続配管23a内の流路を通じて第1抽出部4の排出ヘッダ27の内部空間と連通している。第2抽出部5の抽剤供給ヘッダ42には、抽剤供給ポンプ2bの吐出口に繋がる抽剤供給配管22の第2分岐管22bが接続されている。第2抽出部5の排出ヘッダ43の下部には、第2接続配管23bが接続されている。排出ヘッダ43の上部には、第2排出配管28bが接続されている。
第3抽出部6の原料供給ヘッダ47は、第2接続配管23bを介して第2抽出部5の排出ヘッダ43と繋がっている。すなわち、第3抽出部6の各抽出流路33の原料導入路34の入口34aは、第3抽出部6の原料供給ヘッダ47の内部空間及び第2接続配管23b内の流路を通じて第2抽出部5の排出ヘッダ43の内部空間と連通している。第3抽出部6の抽剤供給ヘッダ48には、抽剤供給ポンプ2bの吐出口に繋がる抽剤供給配管22の第3分岐管22cが接続されている。第3抽出部6の排出ヘッダ49の下部には、第3接続配管23cが接続されている。排出ヘッダ49の上部には、第3排出配管28cが接続されている。
第4抽出部7の原料供給ヘッダ53は、第3接続配管23cを介して第3抽出部6の排出ヘッダ49と繋がっている。すなわち、第4抽出部7の各抽出流路33の原料導入路34の入口34aは、第4抽出部7の原料供給ヘッダ53の内部空間及び第3接続配管23c内の流路を通じて第3抽出部6の排出ヘッダ49の内部空間と連通している。第4抽出部7の抽剤供給ヘッダ54には、抽剤供給ポンプ2bの吐出口に繋がる抽剤供給配管22の第4分岐管22dが接続されている。第4抽出部7の排出ヘッダ55の下部には、第4接続配管23dが接続されている。排出ヘッダ55の上部には、第4排出配管28dが接続されている。
第5抽出部8の原料供給ヘッダ59は、第4接続配管23dを介して第4抽出部7の排出ヘッダ55と繋がっている。すなわち、第5抽出部8の各抽出流路33の原料導入路34の入口34aは、第5抽出部8の原料供給ヘッダ59の内部空間及び第4接続配管23d内の流路を通じて第4抽出部7の排出ヘッダ55の内部空間と連通している。第5抽出部8の抽剤供給ヘッダ60には、抽剤供給ポンプ2bの吐出口に繋がる抽剤供給配管22の第5分岐管22eが接続されている。第5抽出部8の排出ヘッダ61には、第5接続配管23eが接続されている。
第1流入量調節弁10は、第1分岐管22aに設けられている。第2流入量調節弁11は、第2分岐管22bに設けられている。第3流入量調節弁12は、第3分岐管22cに設けられている。第4流入量調節弁13は、第4分岐管22dに設けられている。第5流入量調節弁14は、第5分岐管22eに設けられている。第1~第5流入量調節弁10~14は、それらが設けられた第1~第5分岐管22a~22eを通じて第1~第5抽出部4~8の抽剤供給ヘッダ26,42,48,54,60内に導入される抽剤の流量を調節するものである。
第1排出量調節弁15は、第1排出配管28aに設けられている。第2排出量調節弁16は、第2排出配管28bに設けられている。第3排出量調節弁17は、第3排出配管28cに設けられている。第4排出量調節弁18は、第4排出配管28dに設けられている。第1~第4排出量調節弁15~18は、それらが設けられた第1~第4排出配管28a~28dを通じて第1~第4抽出部4~7の排出ヘッダ27,43,49,55の上部から排出される抽剤の流量を調節するものである。
セトラー9は、第5接続配管23eを介して第5抽出部8の排出ヘッダ61と接続されている。セトラー9は、第5抽出部8の排出ヘッダ61の内部空間から第5接続配管23eへ排出された流体がその第5接続配管23eを通じて導入される内部空間を有する。セトラー9は、その内部空間に導入された流体を滞留させることにより、その流体を、特定成分を抽出した抽剤と特定成分が抽出された後の原料流体とに比重差によって分離するものである。セトラー9の下部には、下側排出配管38が接続されている。セトラー9の上部には、上側排出配管39が接続されている。セトラー9の内部空間では、分離した原料流体が下側に溜まるとともにその原料流体の上側に分離した抽剤が溜まるようになっている。セトラー9の内部空間で分離した原料流体は、下側排出配管38を通じて排出される。セトラー9の内部空間で分離した抽剤は、上側排出配管39を通じて排出される。
上側排出配管39には、最終排出量調節弁19が設けられている。最終排出量調節弁19は、セトラー9の内部空間から上側排出配管39を通じて排出される抽剤の流量を調節するものである。また、セトラー9には、液面計20が設けられている。液面計20は、セトラー9の内部空間で分離した原料流体と抽剤との間の界面の高さ位置を検出するものである。液面計20によって検出された界面の高さ位置のデータは、最終排出量調節弁19に入力される。最終排出量調節弁19は、入力された界面の高さ位置のデータに基づいて、その界面の高さ位置がセトラー9に対する第5接続配管23eの接続部の高さ位置よりも上側に維持されるようにセトラー9からの抽剤の排出流量を制御する。
次に、本発明の第1実施形態による抽出分離方法について説明する。
この第1実施形態による抽出分離方法では、上述した構成を有する抽出分離装置1を用いて原料流体から特定成分を抽出して分離する抽出分離工程を行う。以下、その抽出分離工程について具体的に説明する。
まず、原料流体が原料供給ポンプ2aから原料供給配管21を通じて第1抽出部4の原料供給ヘッダ25へ供給されるとともに、抽剤が抽剤供給ポンプ2bから抽剤供給配管22の第1分岐管22aを通じて第1抽出部4の抽剤供給ヘッダ26へ供給される。原料流体としては、例えば希土類金属等の特定成分を含有する水溶液が用いられる。抽剤としては、原料流体の水溶液中の特定成分を選択的に抽出可能な有機溶剤が用いられる。原料供給ヘッダ25の内部空間に導入された原料流体は、積層体24内の各抽出流路33の原料導入路34に分配されて導入される。抽剤供給ヘッダ26の内部空間に導入された抽剤は、積層体24内の各抽出流路33の抽剤導入路35に分配されて導入される。
各原料導入路34に導入された原料流体と各抽剤導入路35に導入された抽剤は、対応する合流部36で合流して対応する合流流体流路37へ流れる。各合流流体流路37では、原料流体と抽剤とが互いに接触した状態で流れ、その流通過程で原料流体から抽剤へ特定成分が抽出される。
各合流流体流路37を流れた原料流体と抽剤は、それらの合流流体流路37の出口37aから排出ヘッダ27の内部空間へ排出される。排出ヘッダ27の内部空間に排出された原料流体と抽剤は、互いに混合された状態となるが、その内部空間で所定の時間だけ滞留することにより、比重の大きい原料流体は下側へ偏るとともに比重の小さい抽剤が上側に偏る。そして、排出ヘッダ27の内部空間の上部から第1排出配管28aを通じて抽剤が排出されるとともに、排出ヘッダ27の内部空間の下部に位置する流体が第1接続配管23aへ排出される。すなわち、排出ヘッダ27の内部空間に排出された流体が比重差により粗く分離されて、その分離後の一方の流体である抽剤が第1排出配管28aへ排出されるとともに分離後の他方の流体が第1接続配管23aへ排出される。
ここで、第1排出量調節弁15によって排出ヘッダ27からの抽剤の排出流量が調節されることにより、排出ヘッダ27の内部空間で流体が滞留する時間の長さが、その排出ヘッダ27の内部空間において流体が原料流体と抽剤とに完全に分離するのに必要な滞留時間よりも短く設定されている。これにより、排出ヘッダ27の内部空間から第1接続配管23aへ排出される流体は、原料流体と抽剤が混ざった状態の混合流体となる。この第1接続配管23a排出される流体は、その流体中の抽剤の比率がその流体中の原料流体の比率よりも低い流体となる。詳しくは、上記排出ヘッダ27の内部空間で流体が滞留する時間の長さは、原料流体に体積分率で最大10%の抽剤が混ざった状態の混合流体が排出ヘッダ27の内部空間から第1接続配管23aへ排出されるような長さに設定されている。そして、第1抽出部4の排出ヘッダ27から第1接続配管23aへ排出された混合流体は、第2抽出部5の原料供給ヘッダ41へ導入される。なお、排出ヘッダ27で分離されて第1接続配管23aへ排出される混合流体は、本発明の第1流体の一例である。また、排出ヘッダ27で分離されて第1排出配管28aへ排出される抽剤は、本発明の第2流体の一例である。
また、この第1実施形態では、抽剤供給ヘッダ26に供給されて各抽出流路33へ流れる抽剤の流量を第1流入量調節弁10によって調節するとともに、排出ヘッダ27から第1排出配管28aを通じて排出される抽剤の流量を第1排出量調節弁15によって調節する。この調節により、第1抽出部4において原料流体と抽剤を互いに接触した状態にしておく時間の長さを、原料流体に抽剤が接触してからその原料流体から抽剤への特定成分の抽出が平衡状態に達するまでにかかる時間よりも短く設定する。すなわち、合流部36で原料流体と抽剤とが合流してから排出ヘッダ27から第1排出配管28aへ抽剤が排出されるとともに排出ヘッダ27から第1接続配管23aへ流体が排出されるまでにかかる時間の長さを、原料流体に抽剤が接触してから前記抽出が並行状態に達するまでにかかる時間よりも短く設定する。
具体的には、原料流体と抽剤とが接触した状態で滞留する時間(滞留時間)とその原料流体から抽剤への特定成分の抽出率との間には、図4に示すような相関関係がある。この図4から判るように、原料流体から抽剤への特定成分の抽出が平衡状態に達するまでにかかる時間は150秒以上であり、その平衡状態に達したときの特定成分の抽出率は65%である。本実施形態では、第1抽出部4において原料流体と抽剤を互いに接触した状態にしておく時間の長さを15秒に設定している。この15秒では、原料流体からの特定成分の抽出率は、40%までしか得られず、抽出が平衡状態に達したときの抽出率(65%)よりも低い。しかしながら、原料流体と抽剤が接触した直後は抽出率の上昇が早いため、短時間で平衡状態の抽出率に対してある程度のレベルの抽出率にまで達することができる。このため、第1抽出部4において原料流体と抽剤を互いに接触した状態にしておく時間の長さを15秒に設定することは、処理時間の短縮のために有効である。
第2抽出部5の原料供給ヘッダ41へ流れた流体は、その原料供給ヘッダ41の内部空間から第2抽出部5の積層体24内の各抽出流路33の原料導入路34に分配されて導入される。一方、第2抽出部5の抽剤供給ヘッダ42には、抽剤供給ポンプ2bから抽剤供給配管22の第2分岐管22bを通じて抽剤が供給される。抽剤供給ヘッダ42に供給された抽剤は、抽剤供給ヘッダ42の内部空間から第2抽出部5の積層体24内の各抽出流路33の抽剤導入路35に分配されて導入される。その後、第2抽出部5では、各原料導入路34に導入された流体と各抽剤導入路35に導入された抽剤とが、第1抽出部4での工程と同様、対応する合流部36で合流して合流流体流路37を流れて原料流体から抽剤への特定成分の抽出が行われる。その後、原料流体及び抽剤が第2抽出部5の合流流体流路37から排出ヘッダ43の内部空間に排出される。排出ヘッダ43では、第1抽出部4の排出ヘッダ27での工程と同様に、当該排出ヘッダ43内の上部から抽剤が第2排出配管28bを通じて排出されるとともに、当該排出ヘッダ43内の下部から原料流体に抽剤が混ざった状態の流体が第2接続配管23bへ排出される。第2接続配管23bへ排出された流体は、第3抽出部6の原料供給ヘッダ47へ流れる。また、第2抽出部5では、第2流入量調節弁11による抽剤供給ヘッダ42への抽剤の供給流量の調節及び第2排出量調節弁16による排出ヘッダ43からの抽剤の排出流量の調節についても、第1抽出部5での工程と同様に行われる。
以上のような工程と同様の工程が第3抽出部6及び第4抽出部7においても順次行われる。そして、第5抽出部8では、抽剤の導入、第4抽出部7からの排出された流体の導入、及び、各抽出流路33における原料流体から抽剤への特定成分の抽出が、第2~第4抽出部5~7の場合と同様に行われる。一方、第5抽出部8では、各抽出流路33の合流流体流路37から排出ヘッダ61の内部空間に排出された流体は、全て第5接続配管23eを通じてセトラー9の内部空間に導入される。
セトラー9では、その内部空間に導入された流体が滞留され、それによって当該流体が特定成分を抽出した抽剤と特定成分が抽出された後の原料流体とに比重差により完全に分離する。分離した原料流体は、セトラー9の内部空間において下側に溜まる。分離した抽剤は、原料流体よりも比重が小さいため、セトラー9の内部空間において原料流体の上側に溜まる。そして、セトラー9の内部空間から下側排出配管38を通じて、特定成分が抽出された後の原料流体が排出されるとともに、セトラー9の内部空間から上側排出配管39を通じて、特定成分を抽出した抽剤が排出される。このとき、最終排出量調節弁19は、液面計20によって検出されたセトラー9内での原料流体と抽剤との間の界面の高さ位置のデータに基づいて、その界面の高さ位置がセトラー9に対する第5接続配管23eの接続部の高さ位置よりも上側の位置に維持されるようにセトラー9からの排出流量を制御する。
以上のようにして、本発明の第1実施形態による抽出分離方法が行われる。
この第1実施形態では、第1~第4抽出部4~7において抽出流路33から対応する排出ヘッダ27,43,49,55,61の内部空間に排出された流体の一部を原料流体と抽剤が混ざった状態で次段の抽出部5~8の抽出流路33へ導入する。このため、各段の抽出部毎に滞留部を設けてその滞留部で対応する抽出流路から排出された流体を完全に原料流体と抽剤とに分離するまで滞留させるような場合に比べて、抽出分離にかかる処理時間を短縮することができる。
仮に各段の抽出部毎に滞留部を設けてそれらの滞留部で各段の抽出部の抽出流路から排出された流体を完全に原料流体と抽剤とに分離するまで滞留させる場合には、各滞留部においてそれぞれ流体を長時間滞留させる必要があり、その結果、各滞留部を大型化せざるを得ない。これに対し、第1実施形態では、第1~第4抽出部4~7の排出ヘッダ27,43,49,55から次段の抽出部5~8の抽出流路33へ原料流体と抽剤が混ざった状態の混合流体を導入するから、第1~第4抽出部4~7の排出ヘッダ27,43,49,55の内部空間での流体の滞留時間を短縮できる。このため、排出ヘッダ27,43,49,55を小型化できる。また、第5抽出部8の排出ヘッダ61では流体の分離を行う必要はなく、その後のセトラー9において流体を原料流体と抽剤とに分離するため、第5抽出部8の排出ヘッダ61の内部空間での流体の滞留時間も短時間とすることができる。その結果、第5抽出部8の排出ヘッダ61も小型化できる。以上のことから、この第1実施形態では、抽出装置3(抽出分離装置1)の小型化が可能になる。
また、第1実施形態では、第5抽出部8の抽出流路33から対応する排出ヘッダ61に排出された流体をセトラー9の内部空間に導入して滞留させることにより、その流体を、特定成分が抽出された後の原料流体と特定成分を抽出した抽剤とに比重差によって分離する。このため、上記のように各段の排出ヘッダ27,43,49,55での流体の滞留時間を短縮して処理時間を短縮したとしても、抽出処理後の流体を特定成分が抽出された後の原料流体と特定成分を抽出した抽剤とに完全に分離することができる。
また、第1実施形態では、第1~第4抽出部4~7の排出ヘッダ27,43,49,55で分離した、抽剤の比率が原料流体の比率よりも低い混合流体を、次段の抽出部の抽出流路33へ供給する。このため、後段の抽出部へ向かうに従って原料流体からの特定成分の抽出を促進しつつ、後段の抽出部へ向かうに従って処理すべき流体の流量が増大していくのを抑制できる。
また、第1実施形態では、抽出分離装置1として、第1~第5抽出部4~8が互いに積層された多数のプレート30からなる積層体24をそれぞれ有し、その各抽出部4~8の積層体24の各抽出プレート31に複数の抽出流路33を構成する複数のマイクロチャネルが配列されたものを用いる。そして、第1~第5抽出部4~8それぞれの各抽出流路33の合流流体流路37において、原料流体と抽剤を互いに接触した状態で流通させながら原料流体から抽剤へ特定成分を抽出する。このため、多数の抽出流路33の合流流体流路37内で原料流体から抽剤への特定成分の抽出を行うことができる。しかも、各合流流体流路37はマイクロチャネルであることから、各合流流体流路37内での単位体積当りでの原料流体と抽剤との接触面積を増やすことができる。その結果、抽出分離の処理効率を高めることができる。
また、第1実施形態では、第1~第5抽出部4~8のそれぞれにおいて原料流体と抽剤を互いに接触した状態にしておく時間の長さを、原料流体に抽剤が接触してからその原料流体から抽剤への特定成分の抽出が平衡状態に達するまでにかかる時間よりも短く設定している。このため、単位時間あたりの抽出率が高く且つ効率の良い抽出処理を行える。
(第2実施形態)
この第2実施形態による抽出分離装置1は、上記第1実施形態の抽出分離装置1と同様の構成を有する前半抽出分離装置1aに加えて、後半抽出分離装置1bを備えている。後半抽出分離装置1bは、前半抽出分離装置1aの後段側に接続されて、前半抽出分離装置1aで行われる抽出分離と同様の抽出分離を前半抽出分離装置1aから排出された抽出分離処理後の原料流体に再度行うものである。
前半抽出分離装置1aは、第1原料供給ポンプ2a、第1抽剤供給ポンプ2b、第1抽出装置3、第1セトラー9、第1~第5流入量調節弁10~14、第1~第4排出量調節弁15~18、前半最終排出量調節弁19、第1液面計20を備える。前半抽出分離装置1aを構成する各要素についての構成は、上記第1実施形態による抽出分離装置1において同じ符号が付された各要素の構成と同様である。
また、後半抽出分離装置1bの構成は、前半抽出分離装置1aの構成と同様である。すなわち、後半抽出分離装置1bは、上記第1実施形態の抽出分離装置1と同様の構成を有する。具体的に、後半抽出分離装置1bは、第2原料供給ポンプ62a、第2抽剤供給ポンプ62b、第6~第10抽出部64~68を有する第2抽出装置63、第2セトラー69、第6~第10流入量調節弁70~74、第6~第9排出量調節弁75~78、後半最終排出量調節弁79、第2液面計80を備える。
第2抽出装置63の構成は、第1抽出装置3の構成と同様である。第6~第10抽出部64~68は、第1~第10抽出部4~8と同様に構成されているとともに接続配管により同様に接続されている。また、前半抽出分離装置1aの第1セトラー9は、下側排出配管38を介して後半抽出分離装置1bの第6抽出部64の原料供給ヘッダ64aに接続されている。
また、下側排出配管38には、第2原料供給ポンプ62aが設けられている。第1セトラー9の内部空間で分離して下側排出配管38に排出された原料流体は、第2原料供給ポンプ62aによって第6抽出部64の原料供給ヘッダ64aへ送られるようになっている。第2抽剤供給ポンプ62bの構成は、第1抽剤供給ポンプ2bの構成と同様である。第6~第10抽出部64~68に対する第2抽剤供給ポンプ62bの接続構成は、第1~第5抽出部4~8に対する第1抽剤供給ポンプ2bの接続構成と同様である。第2抽剤供給ポンプ62bは、第6~第10抽出部64~68へ第1抽剤供給ポンプ2bの場合と同様に抽剤をそれぞれ供給する。第6~第10抽出部64~68の図略の各抽出流路では、第1~第5抽出部4~8の各抽出流路33(図3参照)の場合と同様に、原料流体から抽剤への特定成分の抽出が行われる。
また、後半抽出分離装置1bにおいて、第6~第10流入量調節弁70~74は、前半抽出分離装置1aにおける第1~第5流入量調節弁10~14と同様の形態で設けられている。第6~第10流入量調節弁70~74は、第1~第5流入量調節弁10~14に対応する機能を有するものである。また、後半抽出分離装置1bにおいて、第6~第9排出量調節弁75~78は、前半抽出分離装置1aにおける第1~第4排出量調節弁15~18と同様の形態で設けられている。第6~第9排出量調節弁75~78は、第1~第4排出量調節弁15~18に対応する機能を有するものである。また、後半抽出分離装置1bにおいて、後半最終排出量調節弁79は、前半抽出分離装置1aにおける前半最終排出量調節弁19と同様の形態で設けられている。後半最終排出量調節弁79は、前半最終排出量調節弁19に対応する機能を有するものである。また、後半抽出分離装置1bにおいて、第2液面計80は、前半抽出分離装置1aにおける第1液面計20と同様の形態で設けられている。第2液面計80は、第1液面計20に対応する機能を有するものである。
この第2実施形態による抽出分離方法では、前半抽出分離装置1aの第1抽出装置3の第1~第5抽出部4~8において、上記第1実施形態による抽出分離方法の場合と同様のプロセスで原料流体から抽剤へ特定成分を抽出する。その後、前半抽出分離装置1aの第1セトラー9において、上記第1実施形態のセトラー9の場合と同様に、抽出処理後の流体を特定成分が抽出された後の原料流体と特定成分を抽出した抽剤とに分離する。
前半抽出分離装置1aの第1セトラー9の内部空間で分離した原料流体は、下側排出配管38へ排出される。下側排出配管38に排出された原料流体は、その下側排出配管38を通じて第2原料供給ポンプ62aにより後半抽出分離装置1bの第6抽出部64の原料供給ヘッダ64aへ供給され、第6抽出部64の図略の各抽出流路へ導入される。また、第2抽剤供給ポンプ62bによって送出された抽剤が、第6抽出部64の図略の各抽出流路へ導入される。第6抽出部64の図略の各抽出流路の合流流体流路において、原料流体と抽剤が互いに接触した状態で流れながら原料流体から抽剤へ特定成分が抽出される。第6抽出部64から次段の第7抽出部65へは、第6抽出部64での抽出処理後の原料流体に抽剤が混ざった状態の流体が供給される。第7抽出部65では、第6抽出部64から供給された流体に対して特定成分の抽出処理が行われる。以降、第8~第10抽出部66~68において同様の抽出処理が順次行われる。最後に、第2セトラー69において、第10抽出部68から排出された抽出処理後の流体を、特定成分が抽出された後の原料流体と特定成分を抽出した抽剤とに分離する。第6~第10抽出部66~68において行われる抽出処理の工程は、第1~第5抽出部4~8において行われる抽出処理の工程と同様である。第2セトラー69で行われる分離処理の工程は、第1セトラー9で行われる分離処理の工程と同様である。
以上のようにして、本発明の第2実施形態による抽出分離方法が行われる。
この第2実施形態では、後半抽出分離装置1bの第2抽出装置63と第2セトラー69により、前半抽出分離装置1aの第1抽出装置3と第1セトラー9で抽出分離した後の原料流体からさらに特定成分を抽出分離することができる。このため、原料流体からの特定成分の抽出分離をより促進することができる。
この第2実施形態の抽出分離方法によって得られる上記以外の効果は、上記第1実施形態の抽出分離方法によって得られる効果と同様である。
(実施例)
まず、初期濃度で100ppmの特定成分を含有する原料流体から特定成分を抽出する場合を想定する。そして、上記第1実施形態の抽出分離方法において、第1~第5抽出部4~8のそれぞれで原料流体と抽剤とが合流してから対応する排出ヘッダ27,43,49,55,61から流体が排出されるまでの時間、すなわち第1~第5抽出部4~8のそれぞれにおいて原料流体と抽剤とが互いに接触している時間を15秒ずつに設定する。この場合、図4に示す滞留時間と抽出率との相関関係から、各抽出部4~8においてそれぞれ40%の抽出率が得られることが判る。その結果、第1抽出部4の排出ヘッダ27から排出される原料流体中の特定成分の濃度は60ppmになる。第2抽出部5の排出ヘッダ43から排出される原料流体中の特定成分の濃度は36ppmになる。第3抽出部6の排出ヘッダ49から排出される原料流体中の特定成分の濃度は21.6ppmになる。第4抽出部7の排出ヘッダ55から排出される原料流体中の特定成分の濃度は12.96ppmになる。第5抽出部8の排出ヘッダ61から排出される原料流体中の特定成分の濃度は7.77ppmになる。また、第1~第5抽出部4~8で原料流体と抽剤とが互いに接触した状態にある時間の合計は75秒になる。
一方、各段の抽出部毎にセトラーを設けた抽出分離装置を用いて、各段の抽出部で抽出処理を行う毎にセトラーで分離処理を行う抽出分離方法を本発明の比較例として想定する。図6には、この比較例による抽出分離方法に用いる抽出分離装置の一部の構成が示されている。図6では、1段目の抽出部104とそれに付設された1段目のセトラー106、及び、2段目の抽出部105とそれに付設された2段目のセトラー107が示されているが、この比較例による抽出分離方法では、2段目のセトラー107の後に2段目の抽出部105及び2段目のセトラー107と同様の構成を有する図略の3組の抽出部及びセトラーが順番に接続された抽出分離装置を用いるものとする。すなわち、この比較例で用いる抽出分離装置は、5段の抽出部と5段のセトラーを備えていて、その抽出部とセトラーとが交互に接続された構成を有する。この比較例における各抽出部の構成は、上記第1実施形態の抽出部4~8の構成と同様である。また、この比較例における各セトラーの構成は、上記第1実施形態のセトラー9と同様である。
そして、この比較例による抽出分離方法において、各段の抽出部で原料流体と抽剤とが合流してからその段のセトラーから分離した原料流体が排出されるまでの時間、すなわち各段の抽出部とセトラーにおいて原料流体と抽剤とが互いに接触した状態にある時間を150秒ずつに設定する。この場合、図4に示す滞留時間と抽出率との相関関係から、各段での抽出分離処理によりそれぞれ65%の抽出率が得られることが判る。従って、初期濃度で100ppmの特定成分を含有する原料流体を1段目の抽出部に供給すると、1段目のセトラーでの分離後の原料流体中の特定成分の濃度は35ppmになる。この場合、2段目のセトラーでの分離後の原料流体中の特定成分の濃度は12.25ppmになり、3段目のセトラーでの分離後の原料流体中の特定成分の濃度は約4.28ppmになる。また、この場合、4段目のセトラーでの分離後の原料流体中の特定成分の濃度は約1.50ppmになり、5段目のセトラーでの分離後の原料流体中の特定成分の濃度は約0.52ppmになる。また、1~5段目の抽出部及びセトラーで原料流体と抽剤とが互いに接触した状態にある時間の合計は750秒になる。
上記第1実施形態の抽出分離方法による処理後の最終の原料流体中の特定成分の濃度(7.77ppm)は、比較例の抽出分離方法による処理後の最終の原料流体中の特定成分の濃度(約0.52ppm)よりも高くなるが、10ppm以下という比較的低い濃度に低減することができる。このため、有用な抽出分離効果が得られることが判る。第1実施形態の抽出分離方法において原料流体と抽剤を互いに接触した状態にしておく時間(75秒)は、比較例の抽出分離方法における対応する時間(750秒)の1/10の時間になる。このことから、処理時間の著しい低減効果が得られることが判る。
また、第1実施形態の抽出分離方法よりも原料流体からの特定成分の抽出分離を促進したい場合には、上記第2実施形態の抽出分離方法を用いればよい。
上記第2実施形態の抽出分離方法において、初期濃度で100ppmの特定成分を含有する原料流体を前半抽出分離装置1aの第1抽出部4に供給したとすると、第1セトラー9で分離した原料流体中の特定成分の濃度は、上記第1実施形態の場合と同じ7.77ppmとなる。そして、後半抽出分離装置1bの第6~第10抽出部64~68のそれぞれにおいて原料流体と抽剤とが互いに接触している時間を第1~第5抽出部4~8の場合と同じ15秒ずつに設定した場合、第6抽出部64の排出ヘッダから排出される原料流体中の特定成分の濃度は約4.7ppmになる。この場合、第7抽出部65の排出ヘッダから排出される原料流体中の特定成分の濃度は約2.8ppmになり、第8抽出部66の排出ヘッダから排出される原料流体中の特定成分の濃度は約1.68ppmになり、第9抽出部67の排出ヘッダから排出される原料流体中の特定成分の濃度は約1.01ppmになる。また、この場合、最後の第10抽出部68の排出ヘッダから排出された後、第2セトラー69で分離した原料流体中の特定成分の濃度は約0.60ppmになる。また、この第2実施形態の抽出分離方法において、第1~第10抽出部4~8,64~68で原料流体と抽剤とが互いに接触した状態にある時間の合計は150秒になる。
この第2実施形態の抽出分離方法による処理後の最終の原料流体中の特定成分の濃度は、上記比較例の抽出分離方法による処理後の最終の原料流体中の特定成分の濃度にほぼ等しくなる。このため、当該第2実施形態の抽出分離方法では上記比較例の抽出分離方法とほぼ同等の抽出分離効果が得られることが判る。そして、第2実施形態の抽出分離方法において原料流体と抽剤を互いに接触した状態にしておく時間(150秒)は、比較例の抽出分離方法における対応する時間(750秒)の1/5の時間である。すなわち、この第2実施形態の抽出分離方法でも、処理時間の低減効果を十分に得られることが判る。
なお、今回開示された実施形態は、すべての点で例示であって制限的なものではないと考えられるべきである。本発明の範囲は、上記した実施形態の説明ではなく請求の範囲によって示され、請求の範囲と均等の意味及び範囲内でのすべての変更を含む。
例えば、上記実施形態では、抽出装置、第1抽出装置及び第2抽出装置が5段の抽出部をそれぞれ備えているが、本発明は、必ずしもこのような構成に限定されない。具体的には、抽出装置は2段以上の抽出部を備えていればよい。なお、この場合には、セトラーは抽出装置が備える2段以上の抽出部のうちの最終段の抽出部の後に設けてその最終段の抽出部から排出される流体を原料流体と抽剤とに分離するようにすればよい。
また、セトラーは省略してもよく、セトラー以外の分離手段によって最終分離工程を行ってもよい。
また、各抽出部の構成は、必ずしも上述した構成に限定されるものではない。具体的には、各抽出部に設けられた各ヘッダの配置や構造、積層体内の抽出流路の形状、配置及び本数等について、上述した構成や図面に表された構成以外の構成を採用してもよい。
例えば、図7に示す変形例のように、排出部27aを、排出ヘッダ27bとその排出ヘッダ27bに接続された簡易分液槽27cとによって構成してもよい。簡易分液槽27cは、本発明の分液槽の一例である。なお、図7では、第1抽出部4について例示しているが、他の段の抽出部の排出部も同様に構成すればよい。この構成では、排出ヘッダ27bが対応する抽出流路の出口に接続され、その抽出流路から排出ヘッダ27bに排出された流体を簡易分液槽27cの内部空間に導入してその内部空間で比重差により抽剤と混合流体とに分離する。
この構成によれば、簡易分液槽27cの内部空間で比重差による分離を行うことができるため、排出ヘッダ27bとして比重差による分離を行う機能を持たない一般的な排出ヘッダを用いることができる。そして、排出ヘッダ27bは比重差による分離を行う機能を持たなくてもよいことから、その排出ヘッダ27bとして容量が小さい最小サイズの排出ヘッダを用いることができる。このため、簡易分液槽27cを設けたとしても、抽出装置3全体のサイズを比較的コンパクトに保つことができる。
また、図8に示す別の変形例のように、第1排出配管28aを第2抽出部5の抽剤供給ヘッダ42に接続し、第2排出配管28bを第3抽出部6の抽剤供給ヘッダ48に接続し、第3排出配管28cを第4抽出部7の抽剤供給ヘッダ54に接続し、第4排出配管28dを第5抽出部8の抽剤供給ヘッダ60に接続してもよい。これにより、第1~第4抽出部4~7の排出ヘッダ27,43,49,55で分離された抽剤が次段の抽出部の抽出流路に供給され、その抽出流路での原料流体からの特定成分の抽出に当該抽剤を再利用できる。このため、抽剤の使用量を削減できる。
また、図9に示すさらに別の変形例のように、第2排出配管28bを第1抽出部4の抽剤供給ヘッダ26に接続し、第3排出配管28cを第2抽出部5の抽剤供給ヘッダ42に接続し、第4排出配管28dを第3抽出部6の抽剤供給ヘッダ48に接続し、セトラー9の上部に接続された上側排出配管39を第4抽出部7の抽剤供給ヘッダ54に接続してもよい。この変形例では、上側排出配管39に、セトラー9から上側排出配管39へ排出される抽剤を第4抽出部7の抽剤供給ヘッダ54へ送るポンプ2cが設けられる。また、第4排出配管28dに、第4抽出部7の排出ヘッダ55から排出された抽剤を第3抽出部6の抽剤供給ヘッダ48へ送るポンプ2dが設けられる。また、第3排出配管28cに、第3抽出部6の排出ヘッダ49から排出された抽剤を第2抽出部5の抽剤供給ヘッダ42へ送るポンプ2eが設けられる。また、第2排出配管28bに、第2抽出部5の排出ヘッダ43から排出された抽剤を第1抽出部4の抽剤供給ヘッダ26へ送るポンプ2fが設けられる。また、この変形例では、第5抽出部8の抽剤供給ヘッダ60に抽剤供給配管22が接続されている。この抽剤供給配管22を通じて、抽剤供給ヘッダ6へフレッシュな抽剤が供給されるようになっている。すなわち、抽出対象としての特定成分を含有しない抽剤が抽剤供給ヘッダ6へ供給される。
この変形例の構成では、第2~第4抽出部5~7の排出ヘッダ43,49,55で分離された抽剤が1つ前の段の抽出部の抽出流路に供給されるとともに、セトラー9で分離された抽剤が第4抽出部7の抽出流路に供給される。このため、第2~第4抽出部5~7の排出ヘッダ43,49,55及びセトラー9で分離された抽剤を前段の抽出部の抽出流路での原料流体からの特定成分の抽出に再利用できる。その結果、抽剤の使用量を削減できる。
また、原料流体は、必ずしも、希土類金属等の特定成分を含有した水溶液に限定されるものではない。また、抽剤は、必ずしも有機溶剤に限定されるものではない。
また、原料流体から抽出分離される特定成分は、その原料流体から除去したい除去成分、例えば不純物や汚染物質等であってもよい。すなわち、本発明の抽出分離方法は、原料流体中から有用な特定成分を採取する目的、及び、原料流体中から不要な特定成分を除去する目的のいずれにも用いることができる。
また、原料流体は、抽剤よりも比重が小さい流体であってもよい。この場合には、上述した抽出分離装置の構成を上下逆にすることによって、前段の抽出部で抽出処理した後の原料流体を次段の抽出部へ供給することができる。
また、各段の抽出部の排出部において、必ずしも比重差による分離(各段分離工程)を行わなくてもよい。例えば、各段の排出部に排出された流体を滞留させずにその流体から所定量の混合流体を抜き出して次段の抽出部へ供給してもよい。また、各段の排出部に排出された流体を原料流体と抽剤とが混ざった状態で次段の抽出部へ全量供給してもよい。
[実施の形態の概要]
前記実施形態による抽出分離方法は、原料流体から特定成分を抽出して分離する方法であって、順次接続された複数段の抽出部を備えた抽出装置を用いて、原料流体から前記特定成分を抽出して分離する抽出分離工程を備え、前記抽出分離工程は、各段の前記抽出部において原料流体とその原料流体に対して比重差を有する抽剤とを互いに接触させた状態で流通させながら原料流体から抽剤へ前記特定成分を抽出する抽出工程と、前記抽出部から排出される流体の少なくとも一部を次段の前記抽出部へ原料流体と抽剤が混ざった状態で導入する導入工程と、最終段の前記抽出部から排出された流体を前記特定成分が抽出された後の原料流体と前記特定成分を抽出した抽剤とに分離する最終分離工程とを有する。
この抽出分離方法では、抽出部から排出される流体の少なくとも一部を原料流体と抽剤が混ざった状態で次段の抽出部へ導入する。このため、各段の抽出部毎に滞留部を設けてその滞留部で流体を完全に原料流体と抽剤に分離するまで滞留させるような場合に比べて抽出分離にかかる処理時間を短縮することができる。また、流体を完全に原料流体と抽剤に分離するのに必要な大きな滞留部が不要となることから、抽出装置の小型化が可能になる。また、この抽出分離方法では、最終段の抽出部から排出された流体を、特定成分が抽出された後の原料流体と特定成分を抽出した抽剤とに分離する。このため、各段の抽出部での流体の滞留時間を短縮して処理時間を短縮したとしても、抽出処理後の流体を特定成分が抽出された後の原料流体と特定成分を抽出した抽剤とに完全に分離することができる。
上記抽出分離方法において、前記抽出分離工程では、前記抽出装置として、前記各段の抽出部がその抽出部に導入された流体を流通させる抽出流路を有し、且つ、少なくとも前記最終段の抽出部以外の前記各抽出部がその抽出部の前記抽出流路の出口に接続された排出部を有する抽出装置を用い、前記導入工程は、前記最終段の抽出部以外の前記各抽出部において前記抽出流路から前記排出部に排出された流体を比重差により第1流体と第2流体とに分離し且つその第1流体には原料流体と抽剤が含まれるように分離する各段分離工程と、その各段分離工程において前記排出部で分離された前記第1流体を次段の前記抽出部の前記抽出流路へ導入する分離流体導入工程とを含むことが好ましい。
この構成では、各段分離工程において分離した第1流体と第2流体のうちの第1流体を、分離流体導入工程で次段の抽出部の抽出流路へ導入する。このため、後段の抽出部へ向かうに従って処理すべき流体の流量が増大していくのを抑制できる。
この場合において、前記各段分離工程において分離される前記第1流体中の抽剤の比率は、その第1流体中の原料流体の比率よりも低いことが好ましい。
この構成によれば、各段分離工程において第1流体中の抽剤の比率がその第1流体中の原料流体の比率よりも低くなるように分離された第1流体を次段の抽出部へ導入できる。このため、後段の抽出部へ向かうに従って原料流体の量を維持しつつその原料流体中の特定成分の抽出を促進することができる。
上記導入工程が各段分離工程を含む構成において、前記排出部は、前記抽出流路の出口に接続された排出ヘッダであり、前記各段分離工程では、前記抽出流路から前記排出ヘッダの内部空間に排出された流体をその内部空間で比重差により前記第1流体と前記第2流体とに分離してもよい。
この構成によれば、排出ヘッダの内部空間で抽出流路から排出された流体を第1流体と第2流体に分離できる。このため、各段の抽出部が排出ヘッダ以外に分液槽を備える構成に比べて抽出装置の構成を簡略化できる。
また、上記導入工程が各段分離工程を含む構成において、前記排出部は、前記抽出流路の出口に接続された排出ヘッダと、その排出ヘッダに接続された分液槽とを有し、前記各段分離工程では、前記抽出流路から前記排出ヘッダへ排出された流体を前記分液槽の内部空間に導入してその分液槽の内部空間で比重差により前記第1流体と前記第2流体とに分離してもよい。
この構成によれば、分液槽の内部空間で比重差による分離を行うことができる。このため、比重差による分離を行う機能を持たない一般的な排出ヘッダを用いることができる。また、この構成では、排出ヘッダは比重差による分離を行う機能を持たなくてもよい。このため、容量が小さいコンパクトな排出ヘッダを用いることができる。このため、分液槽を設けたとしても、抽出装置全体のサイズをコンパクトに保つことができる。
上記導入工程が各段分離工程を含む構成において、前記各段分離工程では、前記各抽出部において前記排出部に排出された流体のうちの所定量の抽剤を前記第2流体として分離し、前記抽出分離工程は、前記各段分離工程において前記排出部で分離された前記第2流体を次段の前記抽出部の前記抽出流路へ供給する抽剤供給工程を有していてもよい。また、上記導入工程が各段分離工程を含む構成において、前記各段分離工程では、前記各抽出部において前記排出部に排出された流体のうちの所定量の抽剤を前記第2流体として分離し、前記抽出分離工程は、前記各段分離工程において前記排出部で分離された前記第2流体を前段の前記抽出部の前記抽出流路へ供給する抽剤供給工程を有していてもよい。
これらの構成によれば、各段分離工程において分離した第2流体としての抽剤を原料流体からの特定成分の抽出に再利用できる。このため、抽剤の使用量を削減できる。
上記各段の抽出部がその抽出部に導入された流体を流通させる抽出流路を有する抽出装置を用いる構成において、前記抽出分離工程では、前記抽出装置として、前記各段の抽出部が互いに積層された複数の層を含み、各層においてそれぞれ前記抽出流路を構成する複数のマイクロチャネルが配列された抽出装置を用い、前記抽出工程では、前記各段の抽出部が有する前記各マイクロチャネルにおいて原料流体から抽剤へ前記特定成分を抽出することが好ましい。
この構成によれば、各段の抽出部において多数のマイクロチャネル内で原料流体から抽剤への特定成分の抽出を行うことができる。このため、抽出分離の処理効率を高めることができる。
上記抽出分離方法において、前記抽出工程では、前記各段の抽出部において原料流体と抽剤を互いに接触した状態にしておく時間の長さを、原料流体に抽剤が接触してからその原料流体から抽剤への前記特定成分の抽出が平衡状態に達するまでにかかる時間よりも短く設定することが好ましい。
この構成によれば、単位時間あたりの抽出率が高く且つ効率の良い抽出処理を行える。
上記抽出分離方法において、前記抽出分離工程で用いる前記抽出装置には、前記最終段の抽出部と接続されたセトラーが付設され、前記最終分離工程では、前記最終段の抽出部から排出された流体を前記セトラーの内部空間に導入してその内部空間で滞留させることにより、当該流体を、前記特定成分が抽出された後の原料流体と前記特定成分を抽出した抽剤とに分離することが好ましい。
この構成によれば、最終分離工程において、抽出処理後の流体をセトラー内での滞留により特定成分が抽出された後の原料流体と特定成分を抽出した抽剤とに完全に分離することができる。
以上説明したように、前記実施形態によれば、抽出装置を小型化しつつ、原料流体からの特定成分の抽出分離にかかる処理時間を短縮することができる。 An extraction and separation method is a method for extracting and separating a specific component from a raw material fluid and is provided with a separation and extraction step wherein the specific component is extracted and separated from the raw material fluid using an extraction device provided with plural stages of extraction units connected sequentially. The extraction and separation step has: an extraction step for extracting the specific component into an extraction solvent having a difference in specific gravity with respect to that raw material fluid from the raw material fluid while causing the raw material fluid and the extraction solvent to flow in a state of contact with each other in the extraction units for each stage; introduction step for introducing at least part of the fluid discharged from an extraction unit to the next stage extraction unit in a state wherein the raw material fluid and the extraction solvent are mixed; and a final separation step for separating the raw material fluid, after the specific component has been extracted in the fluid discharged from the extraction unit in a final stage, and the extraction solvent that has extracted the specific component.
原料流体から特定成分を抽出して分離する方法であって、
請求項1に記載の抽出分離方法において、
請求項2に記載の抽出分離方法において、
請求項2又は3に記載の抽出分離方法において、
請求項2又は3に記載の抽出分離方法において、
請求項2又は3に記載の抽出分離方法において、
請求項2又は3に記載の抽出分離方法において、
請求項2又は3に記載の抽出分離方法において、
請求項1~3のいずれか1項に記載の抽出分離方法において、
請求項1~3のいずれか1項に記載の抽出分離方法において、
本発明の第1実施形態による抽出分離方法は、抽出分離装置1を用いて原料流体から特定成分を抽出して分離する方法である。まず、図1~図4を参照して、この第1実施形態による抽出分離方法に用いる抽出分離装置1について説明する。
次に、本発明の第2実施形態による抽出分離方法について説明する。この第2実施形態による抽出分離方法では、図5に示すような抽出分離装置1を用いて原料流体からの特定成分の抽出分離を行う。
次に、上記各実施形態の抽出分離方法によって原料流体からの特定成分の抽出分離を行った場合に得られる効果を調べるために行ったシミュレーションの結果について説明する。
前記実施形態をまとめると、以下の通りである。
順次接続された複数段の抽出部を備えた抽出装置を用いて、原料流体から前記特定成分を抽出して分離する抽出分離工程を備え、
前記抽出分離工程は、
各段の前記抽出部において原料流体とその原料流体に対して比重差を有する抽剤とを互いに接触させた状態で流通させながら原料流体から抽剤へ前記特定成分を抽出する抽出工程と、
前記抽出部から排出される流体の少なくとも一部を次段の前記抽出部へ原料流体と抽剤が混ざった状態で導入する導入工程と、
最終段の前記抽出部から排出された流体を前記特定成分が抽出された後の原料流体と前記特定成分を抽出した抽剤とに分離する最終分離工程とを有する、抽出分離方法。
前記抽出分離工程では、前記抽出装置として、前記各段の抽出部がその抽出部に導入された流体を流通させる抽出流路を有し、且つ、少なくとも前記最終段の抽出部以外の前記各抽出部が前記抽出流路の出口に接続された排出部を有する抽出装置を用い、
前記導入工程は、前記最終段の抽出部以外の前記各抽出部において前記抽出流路から前記排出部に排出された流体を比重差により第1流体と第2流体とに分離し且つその第1流体には原料流体と抽剤が含まれるように分離する各段分離工程と、その各段分離工程において前記排出部で分離された前記第1流体を次段の前記抽出部の前記抽出流路へ導入する分離流体導入工程とを含む、抽出分離方法。
前記各段分離工程において分離される前記第1流体中の抽剤の比率は、その第1流体中の原料流体の比率よりも低い、抽出分離方法。
前記排出部は、前記抽出流路の出口に接続された排出ヘッダであり、
前記各段分離工程では、前記抽出流路から前記排出ヘッダの内部空間に排出された流体をその内部空間で比重差により前記第1流体と前記第2流体とに分離する、抽出分離方法。
前記排出部は、前記抽出流路の出口に接続された排出ヘッダと、その排出ヘッダに接続された分液槽とを有し、
前記各段分離工程では、前記抽出流路から前記排出ヘッダへ排出された流体を前記分液槽の内部空間に導入してその分液槽の内部空間で比重差により前記第1流体と前記第2流体とに分離する、抽出分離方法。
前記各段分離工程では、前記各抽出部において前記排出部に排出された流体のうちの所定量の抽剤を前記第2流体として分離し、
前記抽出分離工程は、前記各段分離工程において前記排出部で分離された前記第2流体を次段の前記抽出部の前記抽出流路へ供給する抽剤供給工程を有する、抽出分離方法。
前記各段分離工程では、前記各抽出部において前記排出部に排出された流体のうちの所定量の抽剤を前記第2流体として分離し、
前記抽出分離工程は、前記各段分離工程において前記排出部で分離された前記第2流体を前段の前記抽出部の前記抽出流路へ供給する抽剤供給工程を有する、抽出分離方法。
前記抽出分離工程では、前記抽出装置として、前記各段の抽出部が互いに積層された複数の層を含み、各層においてそれぞれ前記抽出流路を構成する複数のマイクロチャネルが配列された抽出装置を用い、
前記抽出工程では、前記各段の抽出部が有する前記各マイクロチャネルにおいて原料流体から抽剤へ前記特定成分を抽出する、抽出分離方法。
前記抽出工程では、前記各段の抽出部において原料流体と抽剤を互いに接触した状態にしておく時間の長さを、原料流体に抽剤が接触してからその原料流体から抽剤への前記特定成分の抽出が平衡状態に達するまでにかかる時間よりも短く設定する、抽出分離方法。
前記抽出分離工程で用いる前記抽出装置には、前記最終段の抽出部と接続されたセトラーが付設され、
前記最終分離工程では、前記最終段の抽出部から排出された流体を前記セトラーの内部空間に導入してその内部空間で滞留させることにより、当該流体を、前記特定成分が抽出された後の原料流体と前記特定成分を抽出した抽剤とに分離する、抽出分離方法。
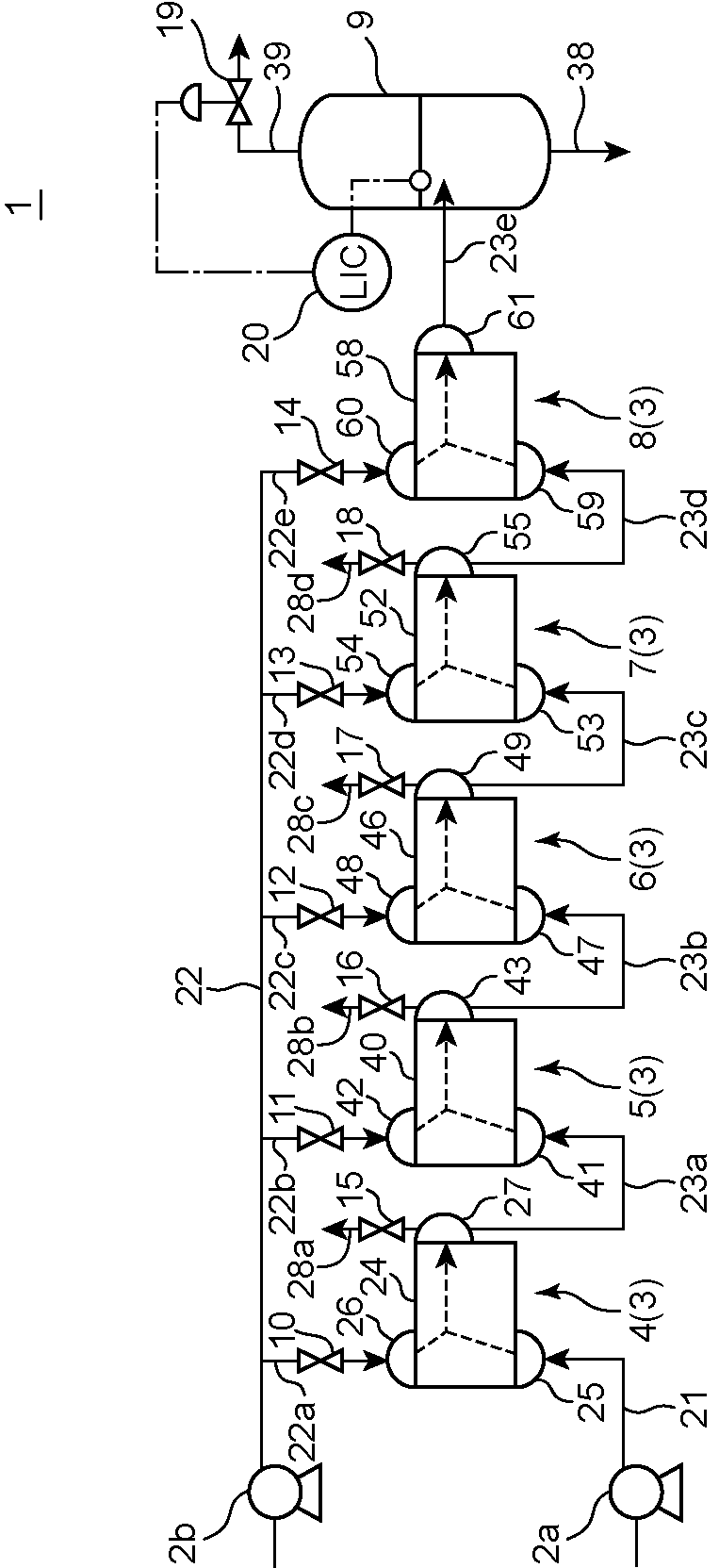
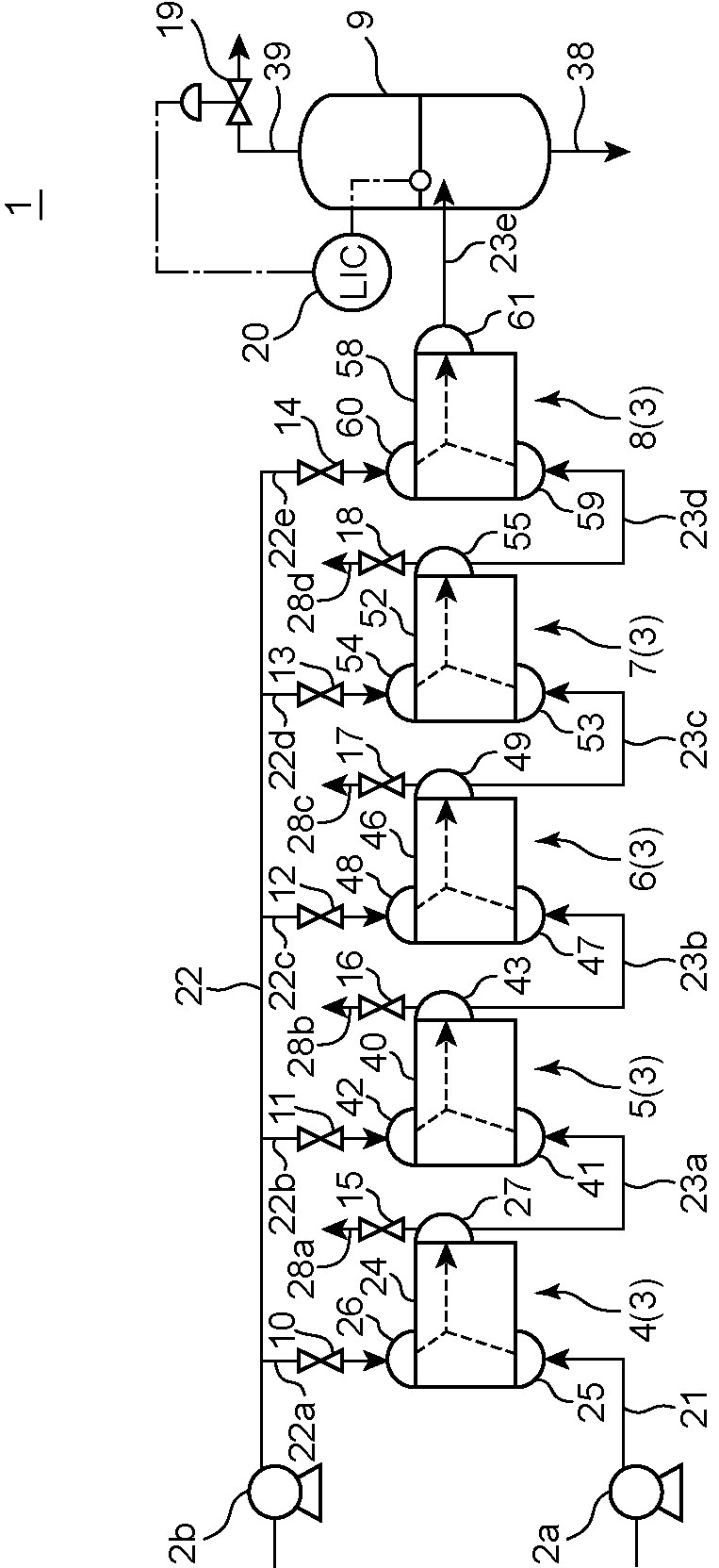
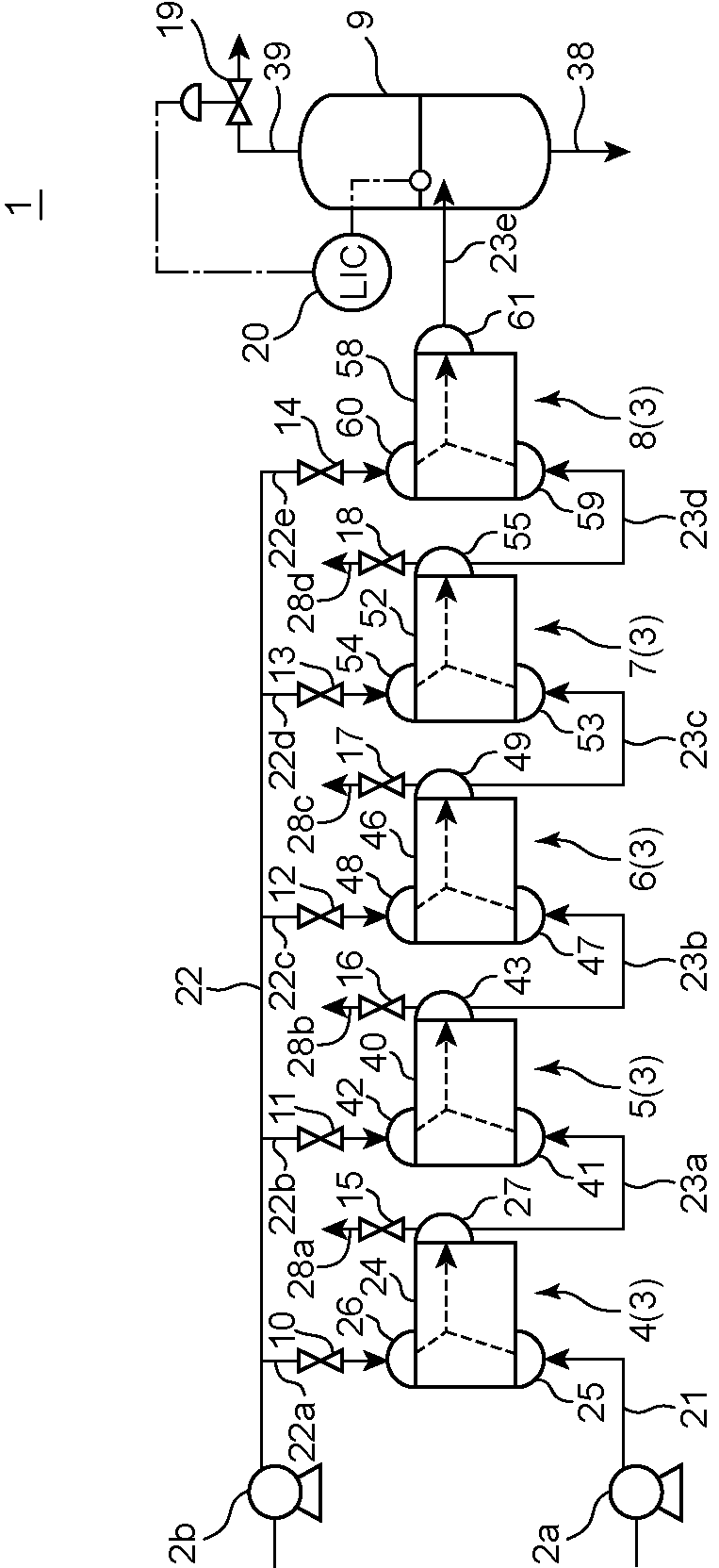

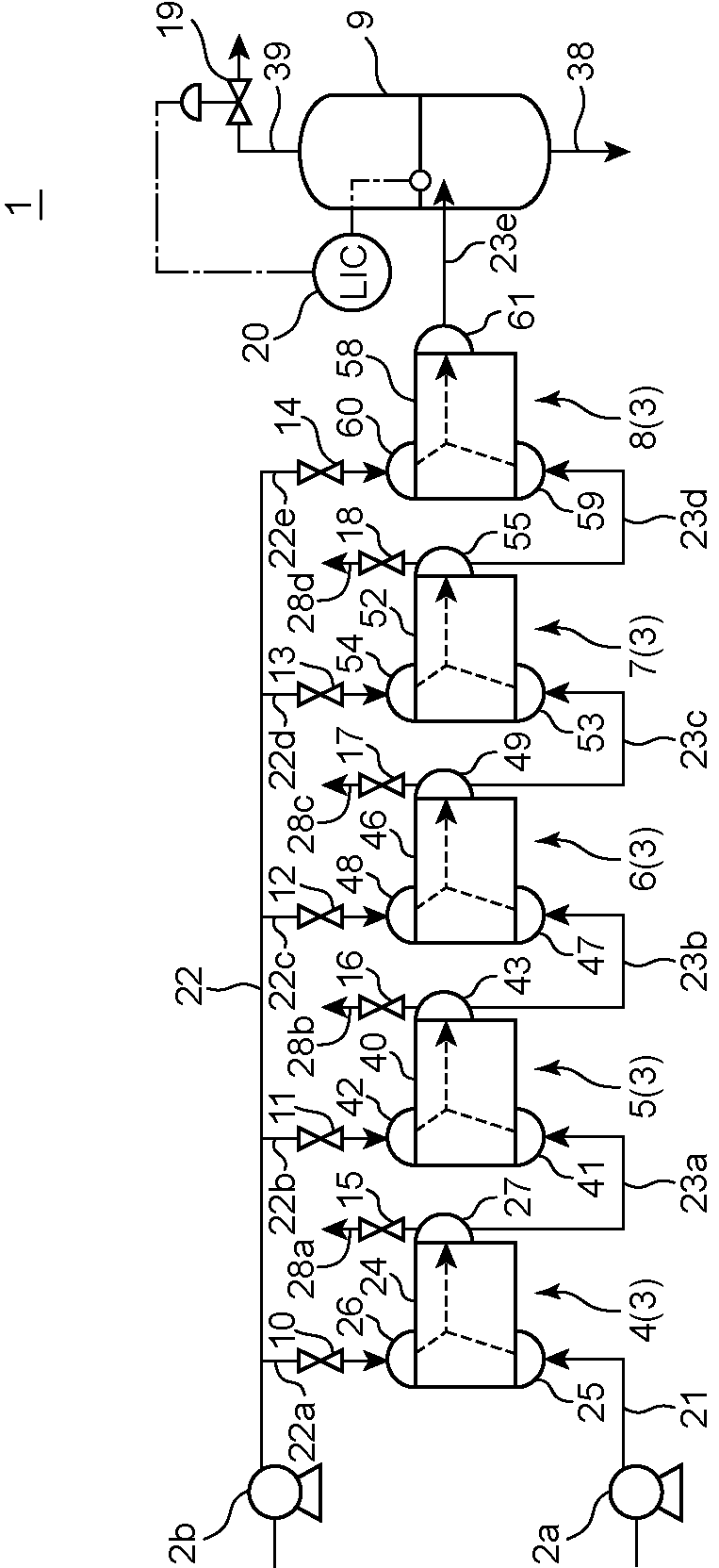


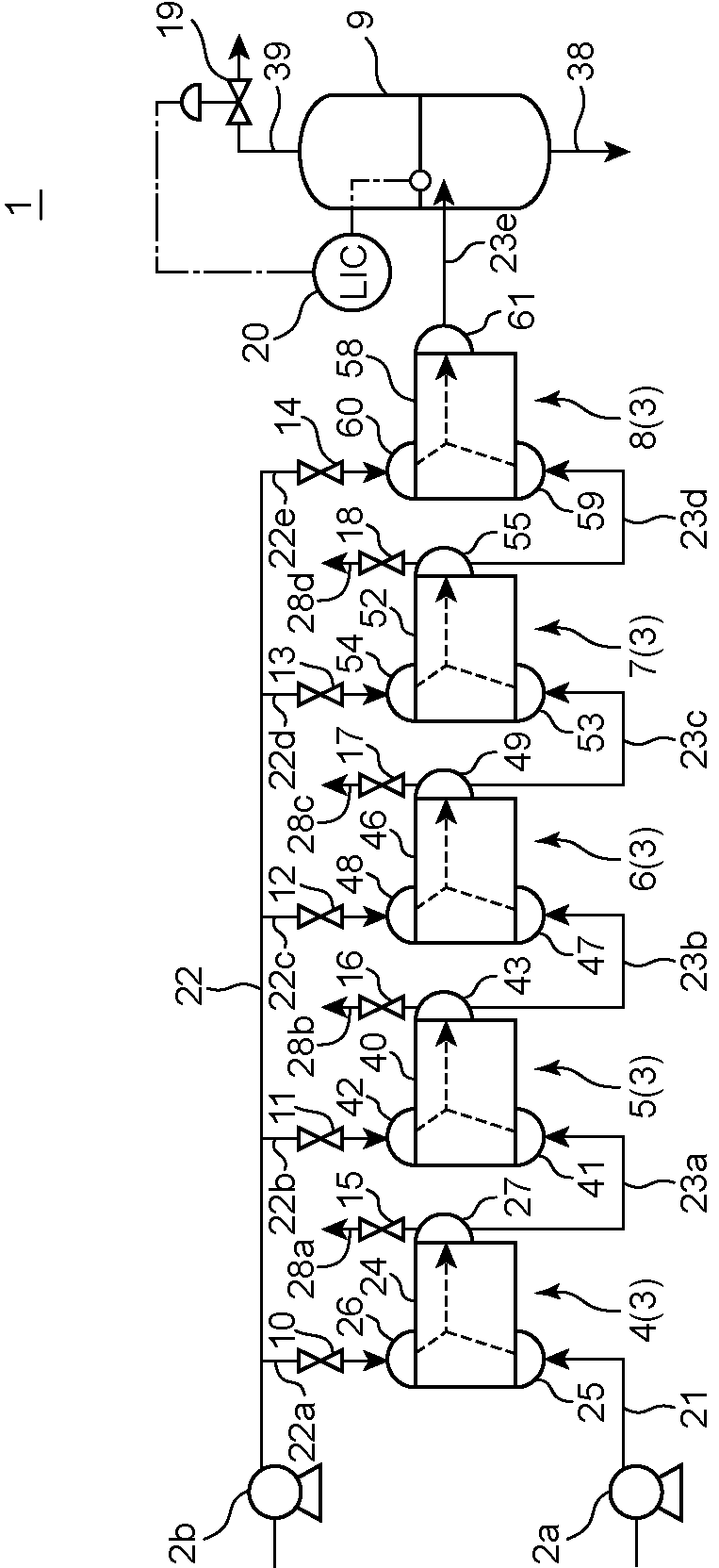
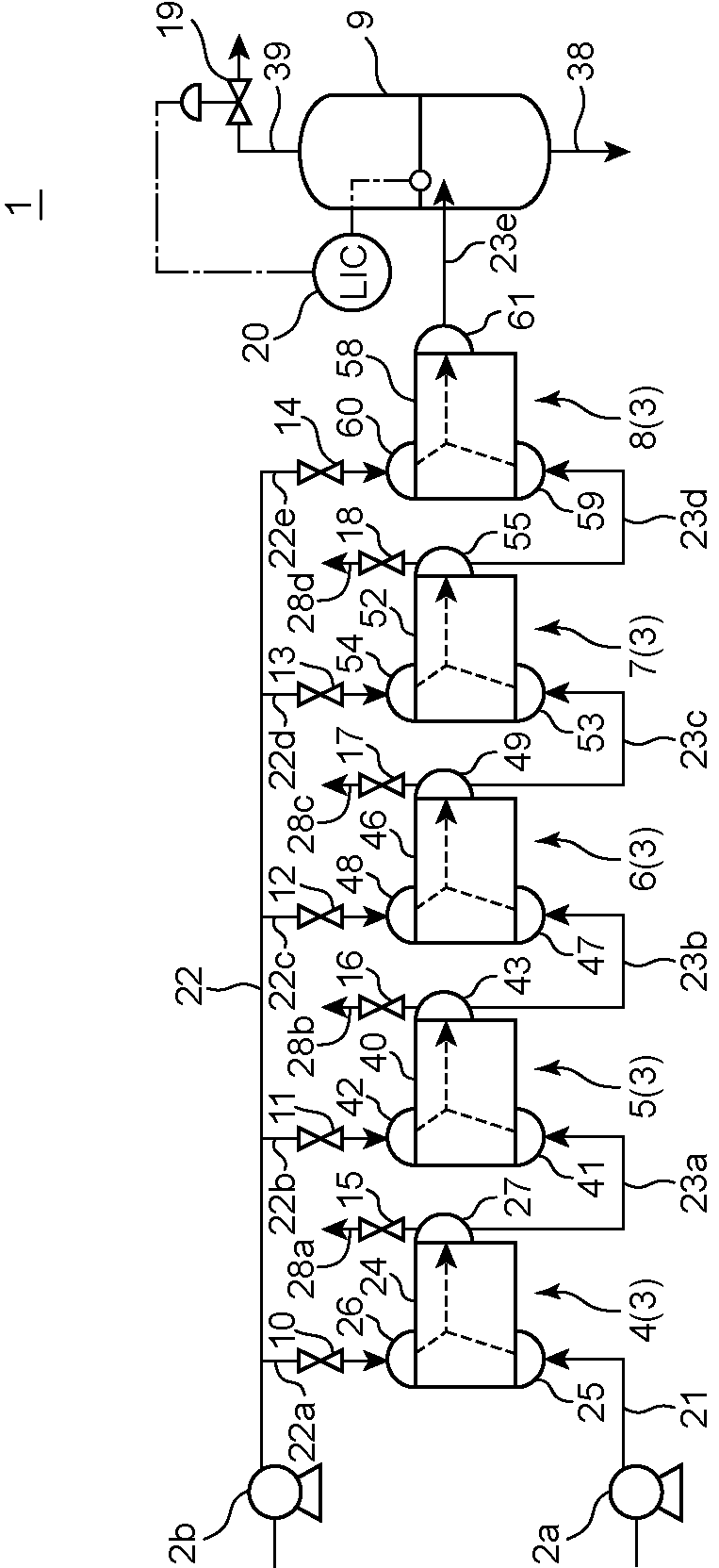