EFFICIENT NEAR NET SHAPE PRECISION FORMING METHOD OF HOLLOW VALVE BLANK FOR ENGINE
本发明涉及金属塑性成形技术领域,特别是涉及一种高效近净的发动机空心气门毛坯精密成形方法。 气门是发动机配气机构的一个关键零件,气门的开启和关闭使可燃气体进入气缸并排出燃烧后的废气。空心气门实现了轻量化,且由于其空心部位封闭了一定体积的金属钠的作用有效地提高了导热性能。发动机工作过程中气门盘部与气门座之间频繁撞击,并受到高温高压燃气的冲蚀,尤其是对气门颈部施加了很大负载,因此气门不仅要具有较高的机械性能,且要求其内部金属流线方向与外形一致、金相组织细密,具有一定的疲劳强度。 国内常用的空心气门生产方法有实心气门钻孔法,该方法只能获得杆部空心而盘部仍为实心的空心气门,且生产效率低,材料利用率低,尤其是对于不同形状尺寸的回转体组形成的空心气门造成材料浪费。 发明内容 本发明的目的在于克服现有技术的缺点与不足,提供一种高效近净的发动机空心气门毛坯精密成形方法,通过楔横轧模具和模锻成形模具依次对受热后的金属管料进行轧制及锻造,由此使得金属管料成形为空心气门,不需要通过打孔实现气门的挖空,从而避免材料浪费,并有效提高生产效率和材料利用率。 本发明是通过以下技术方案实现的:一种高效近净的发动机空心气门毛坯精密成形方法,其包括以下步骤: 步骤1:制造楔横轧模具和模锻成形模具; 步骤2:将气阀金属管料加热至轧制温度; 步骤3:通过所述楔横轧模具对加热至轧制温度的气阀金属管料进行轧制,实现气阀金属管料产生外径变化并沿其轴向伸长形成一左右对称的空心气门坯料;所述空心气门坯料左右对称的对称线与其轴线垂直,且所述空心气门坯料的中部为杆部,其两端为盘部,且其杆部与盘部之间的连接段为其颈部; 步骤4:沿所述空心气门坯料的对称线分割所述空心气门坯料,形成结构相同的第一空心气门预制坯和第二空心气门预制坯;每个空心气门预制坯由连续且依次连接的杆部、颈部和盘部组成; 步骤5:通过所述模锻成形模具对所述第一空心气门预制坯或第二空心气门预制坯进行锻造,完成第一空心气门预制坯的盘部或第二空心气门预制坯的盘部成形为空心气门盘部,
实现空心气门的制成。 本发明中,所述模锻成形模具包括分离设置的模具主体和冲击下压部件。所述模具主体中设有上下设置并连续连通且轴线共线的冲击内腔、空心气门盘部成形内腔、空心气门颈部成形内腔及空心气门杆部放置内腔;所述空心气门盘部成形内腔由上下设置且连续的盘外圆成形腔、盘锥面成形腔及盘部凹面成形腔组成,所述盘外圆成形腔用于形成空心气门盘部的盘外圆,所述盘锥面成形腔用于形成空心气门盘部的盘锥面,所述盘部凹面成形腔用于形成空心气门盘部的弧形凹面;所述空心气门颈部成形内腔的轮廓与所述空心气门坯料的颈部的外轮廓一致;所述空心气门杆部放置内腔的轮廓与所述空心气门坯料的杆部的外轮廓一致。所述冲击下压部件的顶端端面为一用于承载外部冲压力的冲压承载平面,其底端端面的中部设有一可伸入空心气门预制坯的内腔中并将冲压力作用于空心气门预制坯盘部的锻造件;所述锻造件的外围面由上下设置、轴线共线且连续的圆台侧面、弧形凹面及圆柱面组合形成。 本发明中,所述步骤3中,所述空心气门坯料的颈部的外围面由连续的圆台侧面与弧形凹面相互连接形成。 每个空心气门预制坯的颈部的弧形凹面的半径R1与所述模锻成形模具中盘部凹面成形腔腔面的半径R0之间的关系满足R1=1.05×R0;制成的空心气门的盘部的弧形凹面的半径R2与所述模锻成形模具中盘部凹面成形腔腔面的半径R0之间的关系满足R2=R0。 所述楔横轧模具包括楔入部分、展宽部分和精整部分。作为本发明的进一步改进,所述楔横轧模具的成形角为35°~38°,其楔入部分的展宽角为4°~6°,其展宽部分的展宽角为3°~5°。 作为本发明的进一步改进,所述步骤3中,所述楔横轧模具在脱空情况下对所述加热至轧制温度的气阀金属管料进行轧制。 本发明中,所述步骤5中,利用所述第一空心气门预制坯或第二空心气门预制坯的轧制余热实现锻造,或者,在锻造前,对所述第一空心气门预制坯或第二空心气门预制坯进行加热。 本发明中,所述步骤1中,根据需要制得的空心气门的规格制造与其相应的楔横轧模具和模锻成形模具。 本发明中,所述步骤2中,通过加热炉实现气阀金属管料的加热;且所述气阀金属管料为钢管料;所述步骤3中,通过将所述楔横轧模具安装于楔横轧机,及通过推料装置将所述加热至轧制温度的气阀金属管料推送至所述楔横轧机中,实现所述楔横轧模具对所述加热至轧制温度的气阀金属管料的轧制。 作为本发明的进一步改进,所述轧制温度为1000℃~1200℃。 通过上述技术方案,本发明高效近净的发动机空心气门毛坯精密成形方法使用了楔横轧
技术生产汽车发动机气门毛坯,其与传统的电热镦粗工艺相比具有以下优点: (1)通过楔横轧模具实现楔横轧精密制坯,使气阀金属管料在楔横轧模具的轧制作用下发生形变而中部凹陷、两端伸长,中部形成空心气门的杆部,两端形成待加工的盘部,盘部与杆部之间的连接段形成空心气门的颈部(外围面由弧形凹面和圆台侧面组成),由此实现气阀金属管料在楔横轧轧制阶段达到制造要求,使获得的空心气门坯料的形状与尺寸之间的一致性好,并避免了通过后续粗加工的方式获得杆部回转面,有效提高了生产效率和材料利用率; (2)通过轧制完成后,利用与所述制得的空心气门盘部结构匹配的模锻成形模具对获得的空心气门预制坯进行盘部加工,将空心气门预制坯直接置于模锻成形模具的腔体中实现锻造,从而实现制成的空心气门的杆部、颈部及盘部整体流线分布合理,组织细密,满足性能要求; (3)通过利用气阀金属管料作为坯料实现轧制和锻造,不需要通过打孔的方式实现气门的挖空,有效避免材料浪费,具有废品率低、节材率高、成形精度高、生产率高等优点。 为了更好地理解和实施,下面结合附图详细说明本发明。 图1是本发明的方法步骤的流程简图; 图2是本发明的楔横轧模具的简图; 图3是图2中A’-A向的结构示意图; 图4是本发明的模锻成形模具的结构示意图; 图5是本发明的气阀金属管料的结构示意图; 图6是本发明的楔横轧模具对气阀金属管料的轧制过程的示意图,其中,(a)是楔横轧模具楔入段时气阀金属管料的结构示意图,(b)是楔横轧模具楔入平整段时气阀金属管料的结构示意图,(c)是楔横轧模具展宽段时气阀金属管料的结构示意图,(d)是楔横轧模具精整段时由气阀金属管料形成的空心气门坯料的结构示意图; 图7是本发明中轧制形成的空心气门坯料的结构示意图; 图8是本发明中对空心气门坯料分割后形成的其中一空心气门预制坯的结构示意图; 图9是本发明制成的空心气门的结构示意图。 请同时参阅图1~9,本发明高效近净的发动机空心气门毛坯精密成形方法包括以下步骤: 步骤1:制造楔横轧模具1和模锻成形模具2; 在本实施例中,楔横轧模具1和模锻成形模具2的制造方法与现有技术模具的制造方法
相同,故在此不再赘述。具体地,所述步骤1中,根据需要制得的空心气门的规格制造与其相应的楔横轧模具1和模锻成形模具2;也即,先设计好所述制得的空心气门的图纸,再根据设计好的空心气门的图纸制造相应的楔横轧模具1和模锻成形模具2。 具体地,所述楔横轧模具1包括楔入部分11、展宽部分12和精整部分13。作为本发明的进一步改进,所述楔横轧模具1的成形角为35°~38°,其楔入部分11的展宽角β1为4°~6°,其展宽部分12的展宽角β2为3°~5°。 具体地,所述模锻成形模具2包括分离设置的模具主体21和冲击下压部件22。 所述模具主体21中设有上下设置并连续连通且轴线共线的冲击内腔211、空心气门盘部成形内腔212、空心气门颈部成形内腔213及空心气门杆部放置内腔214;所述空心气门盘部成形内腔212由上下设置且连续的盘外圆成形腔212a、盘锥面成形腔212b及盘部凹面成形腔212c组成,所述盘外圆成形腔212a用于形成空心气门盘部的盘外圆,所述盘锥面成形腔212b用于形成空心气门盘部的盘锥面,所述盘部凹面成形腔212c用于形成空心气门盘部的弧形凹面。 所述冲击下压部件22的顶端端面为一用于承载外部冲压力的冲压承载平面221,其底端端面的中部设有一可伸入空心气门预制坯的内腔中并将冲压力作用于空心气门预制坯盘部的锻造件222;所述锻造件222的外围面由上下设置、轴线共线且连续的圆台侧面222a、弧形凹面222b及圆柱面222c组合形成。 步骤2:将气阀金属管料3加热至轧制温度;优选地,所述轧制温度为1000℃~1200℃。 具体地,在所述步骤2中,通过加热炉实现气阀金属管料3的加热;在本实施例中,所述气阀金属管料3为钢管料。 步骤3:通过所述楔横轧模具1对加热至轧制温度的气阀金属管料3进行轧制,实现气阀金属管料3产生外径变化并沿其轴向伸长形成一左右对称的空心气门坯料4;所述空心气门坯料4左右对称的对称线与其轴线垂直,且所述空心气门坯料4的中部为杆部41,其两端为盘部(44和45),且其杆部41与盘部(44和45)之间的连接段为其颈部(42和43)。 具体地,所述步骤3中,通过将所述楔横轧模具1安装于楔横轧机,及通过推料装置将所述加热至轧制温度的气阀金属管料3推送至所述楔横轧机中,实现所述楔横轧模具1对所述加热至轧制温度的气阀金属管料3的轧制。 所述步骤3中,所述空心气门坯料4的颈部的外围面由连续的圆台侧面与弧形凹面相互连接形成。作为一种更优的技术方案,所述步骤3中,所述楔横轧模具1在脱空情况下对所述加热至轧制温度的气阀金属管料3进行轧制。 进一步,所述空心气门颈部成形内腔213的轮廓与所述空心气门坯料4的颈部的外轮廓
一致;所述空心气门杆部放置内腔214的轮廓与所述空心气门坯料4的杆部的外轮廓一致。 步骤4:沿所述空心气门坯料4的对称线分割所述空心气门坯料4,形成结构相同的第一空心气门预制坯和第二空心气门预制坯;每个空心气门预制坯5由连续且依次连接的杆部51、颈部52和盘部53组成。 步骤5:通过所述模锻成形模具2对所述第一空心气门预制坯或第二空心气门预制坯进行锻造,完成第一空心气门预制坯的盘部或第二空心气门预制坯的盘部成形为空心气门盘部,实现空心气门6的制成。 进一步,在步骤5中,利用所述第一空心气门预制坯或第二空心气门预制坯的轧制余热实现锻造,或者,在锻造前,对所述第一空心气门预制坯或第二空心气门预制坯进行加热。 具体地,在步骤5中,通过将其中一空心气门预制坯置于模锻成形模具2的空心气门盘部成形内腔212、空心气门颈部成形内腔213及空心气门杆部放置内腔214中,然后利用冲击下压部件22对空心气门预制坯盘部端面进行冲击下压,逐渐使空心气门预制坯盘部受压而填满空心气门盘部成形内腔212,由此制成的空心气门盘部内腔轮廓与冲击下压部件22的锻造件222外轮廓一致,且其盘部外轮廓与空心气门盘部成形内腔212轮廓一致。 为了保证制得的空心气门整体流线分布更加合理、组织更加细密及进一步满足制造要求,优选地,每个空心气门预制坯5的颈部的弧形凹面的半径R1与所述模锻成形模具2中盘部凹面成形腔212c腔面的半径R0之间的关系满足R1=1.05×R0;制成的空心气门6的盘部的弧形凹面的半径R2与所述模锻成形模具2中盘部凹面成形腔212c腔面的半径R0之间的关系满足R2=R0。每个空心气门预制坯5的颈部外围的圆台面与其轴线之间的夹角θ1、所述制成的空心气门6的颈部外围的圆台面与其轴线之间的夹角θ2、及所述模锻成形模具2中空心气门颈部成形内腔213的圆台面与其轴线之间的夹角θ0之间的关系满足θ1=θ2=θ0。 以下结合一例子对本发明的技术进一步说明: 例如:某型号空心气门采用本发明的方法对称加工毛坯,加工后在毛坯特定位置形成球形凹台(也即毛坯此处位置的外围面形成弧形凹面)、锥形台(也即毛坯此处位置的外围面形成圆台侧面)和圆柱体(也即毛坯此处位置的外围面形成圆柱面)。 (1)轧制获取空心气门预制坯 例如,选择规格为Φ12×6mm的钢管按尺寸下料,坯料长度为100mm。用高频加热炉将坯料加热到1150℃,由推料装置送入楔横轧机上楔横轧模具轧制。轧制成形的楔横轧预制坯,锥形台锥角为4°,最大外圆直径9.5mm,球形台外径7mm。将轧件从中间切断即可得到两件空心气门预制坯。 (2)锻造实现空心气门预制坯的盘部紧密成形
将通过楔横轧模具轧制完成的其中一个空心气门预制坯再次加热,加热完成后将其放入所述模锻成形模具中,进行盘部锻造成形。 该类空心气门采用本发明提供的楔横轧—模锻精密成形工艺所用的坯料的体积比按杆部最大外圆直径进行楔横轧预制坯节材20%,并省掉了粗车杆部椎体的工序。模锻成形模具利用圆台侧面定位,定位可靠。 相对于现有技术,本发明高效近净的发动机空心气门毛坯精密成形方法通过楔横轧模具实现楔横轧精密制坯,使气阀金属管料在楔横轧模具的轧制作用下发生形变而中部凹陷、两端伸长,中部形成空心气门的杆部,两端形成待加工的盘部,盘部与杆部之间的连接段形成空心气门的颈部(外围面由弧形凹面和圆台侧面组成),由此实现气阀金属管料在楔横轧轧制阶段达到制造要求,使获得的空心气门坯料的形状与尺寸之间的一致性好,并避免了通过后续粗加工的方式获得杆部回转面,有效提高了生产效率和材料利用率;通过轧制完成后,利用与所述制得的空心气门盘部结构匹配的模锻成形模具对获得的空心气门预制坯进行盘部加工,将空心气门预制坯直接置于模锻成形模具的腔体中实现锻造,从而实现制成的空心气门的杆部、颈部及盘部整体流线分布合理,组织细密,满足性能要求;通过利用气阀金属管料作为坯料实现轧制和锻造,不需要通过打孔的方式实现气门的挖空,有效避免材料浪费,具有废品率低、节材率高、成形精度高、生产率高等优点。 本发明并不局限于上述实施方式,如果对本发明的各种改动或变形不脱离本发明的精神和范围,倘若这些改动和变形属于本发明的权利要求和等同技术范围之内,则本发明也意图包含这些改动和变形。
Disclosed is an efficient near net shape precision forming method of a hollow valve blank for an engine. Cross wedge rolling precision blank forming is realized via a cross wedge rolling die (1), a valve metal pipe material (3) deforms under the rolling action of the cross wedge rolling die (1) to be recessed in the middle and elongated at two ends, a rod portion (41) of a hollow valve is formed in the middle, plate portions (44 and 45) to be processed are formed at two ends, connecting segments between the plate portions (44 and 45) and the rod portion (41) form necks (42 and 43) with arc-shaped concave faces and cone frustum side face structures, and thus the consistency of the shape and size of the obtained hollow valve blank is good; and a die forging forming die (2) matching the structure of the prepared hollow valve plate portion is utilized to process the plate portions of the obtained hollow valve blank preform, and the hollow valve blank preform is directly put in a cavity of the die forging forming die to be forged, so that the rod portion, the necks and the plate portions of the prepared hollow valve are rational in overall streamline distribution, and the texture is fine, thereby meeting the performance requirements, avoiding material waste, and increasing the production efficiency and material utilization. 一种高效近净的发动机空心气门毛坯精密成形方法,其特征在于:包括以下步骤: 步骤1:制造楔横轧模具和模锻成形模具; 步骤2:将气阀金属管料加热至轧制温度; 步骤3:通过所述楔横轧模具对加热至轧制温度的气阀金属管料进行轧制,实现气阀金属管料产生外径变化并沿其轴向伸长形成一左右对称的空心气门坯料;所述空心气门坯料左右对称的对称线与其轴线垂直,且所述空心气门坯料的中部为杆部,其两端为盘部,且其杆部与盘部之间的连接段为其颈部; 步骤4:沿所述空心气门坯料的对称线分割所述空心气门坯料,形成结构相同的第一空心气门预制坯和第二空心气门预制坯;每个空心气门预制坯由连续且依次连接的杆部、颈部和盘部组成; 步骤5:通过所述模锻成形模具对所述第一空心气门预制坯或第二空心气门预制坯进行锻造,完成第一空心气门预制坯的盘部或第二空心气门预制坯的盘部成形为空心气门盘部,实现空心气门的制成。 根据权利要求1所述的高效近净的发动机空心气门毛坯精密成形方法,其特征在于:所述模锻成形模具包括分离设置的模具主体和冲击下压部件; 所述模具主体中设有上下设置并连续连通且轴线共线的冲击内腔、空心气门盘部成形内腔、空心气门颈部成形内腔及空心气门杆部放置内腔;所述空心气门盘部成形内腔由上下设置且连续的盘外圆成形腔、盘锥面成形腔及盘部凹面成形腔组成,所述盘外圆成形腔用于形成空心气门盘部的盘外圆,所述盘锥面成形腔用于形成空心气门盘部的盘锥面,所述盘部凹面成形腔用于形成空心气门盘部的弧形凹面;所述空心气门颈部成形内腔的轮廓与所述空心气门坯料的颈部的外轮廓一致;所述空心气门杆部放置内腔的轮廓与所述空心气门坯料的杆部的外轮廓一致; 所述冲击下压部件的顶端端面为一用于承载外部冲压力的冲压承载平面,其底端端面的中部设有一可伸入空心气门预制坯的内腔中并将冲压力作用于空心气门预制坯盘部的锻造件;所述锻造件的外围面由上下设置、轴线共线且连续的圆台侧面、弧形凹面及圆柱面组合形成。 根据权利要求2所述的高效近净的发动机空心气门毛坯精密成形方法,其特征在于:所述步骤3中,所述空心气门坯料的颈部的外围面由连续的圆台侧面与弧形凹面相互连接形成。
根据权利要求3所述的高效近净的发动机空心气门毛坯精密成形方法,其特征在于:每个空心气门预制坯的颈部的弧形凹面的半径R1与所述模锻成形模具中盘部凹面成形腔腔面的半径R0之间的关系满足R1=1.05×R0;制成的空心气门的盘部的弧形凹面的半径R2与所述模锻成形模具中盘部凹面成形腔腔面的半径R0之间的关系满足R2=R0。 根据权利要求1所述的高效近净的发动机空心气门毛坯精密成形方法,其特征在于:所述楔横轧模具包括楔入部分、展宽部分和精整部分;所述楔横轧模具的成形角为35°~38°,其楔入部分的展宽角为4°~6°,其展宽部分的展宽角为3°~5°。 根据权利要求1所述的高效近净的发动机空心气门毛坯精密成形方法,其特征在于:所述步骤3中,所述楔横轧模具在脱空情况下对所述加热至轧制温度的气阀金属管料进行轧制。 根据权利要求1所述的高效近净的发动机空心气门毛坯精密成形方法,其特征在于:所述步骤5中,利用所述第一空心气门预制坯或第二空心气门预制坯的轧制余热实现锻造,或者,在锻造前,对所述第一空心气门预制坯或第二空心气门预制坯进行加热。 根据权利要求1所述的高效近净的发动机空心气门毛坯精密成形方法,其特征在于:所述步骤1中,根据需要制得的空心气门的规格制造与其相应的楔横轧模具和模锻成形模具。 根据权利要求1所述的高效近净的发动机空心气门毛坯精密成形方法,其特征在于:所述步骤2中,通过加热炉实现气阀金属管料的加热;且所述气阀金属管料为钢管料;所述步骤3中,通过将所述楔横轧模具安装于楔横轧机,及通过推料装置将所述加热至轧制温度的气阀金属管料推送至所述楔横轧机中,实现所述楔横轧模具对所述加热至轧制温度的气阀金属管料的轧制。 根据权利要求1所述的高效近净的发动机空心气门毛坯精密成形方法,其特征在于:所述轧制温度为1000℃~1200℃。
技术领域
背景技术
附图说明
具体实施方式


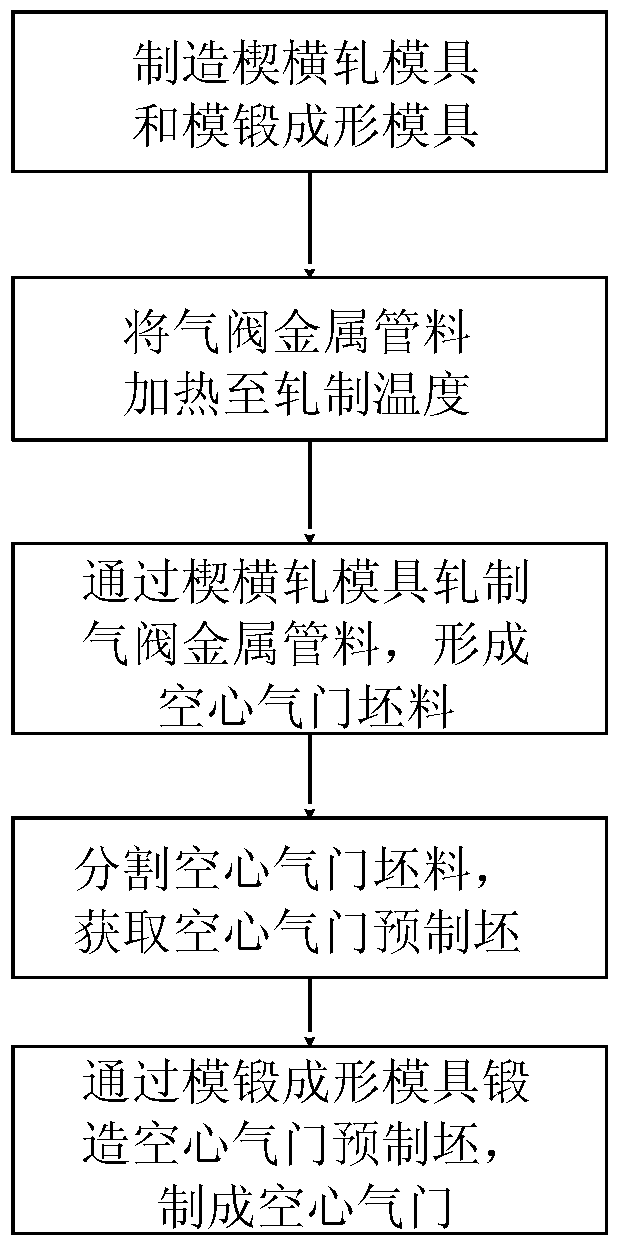





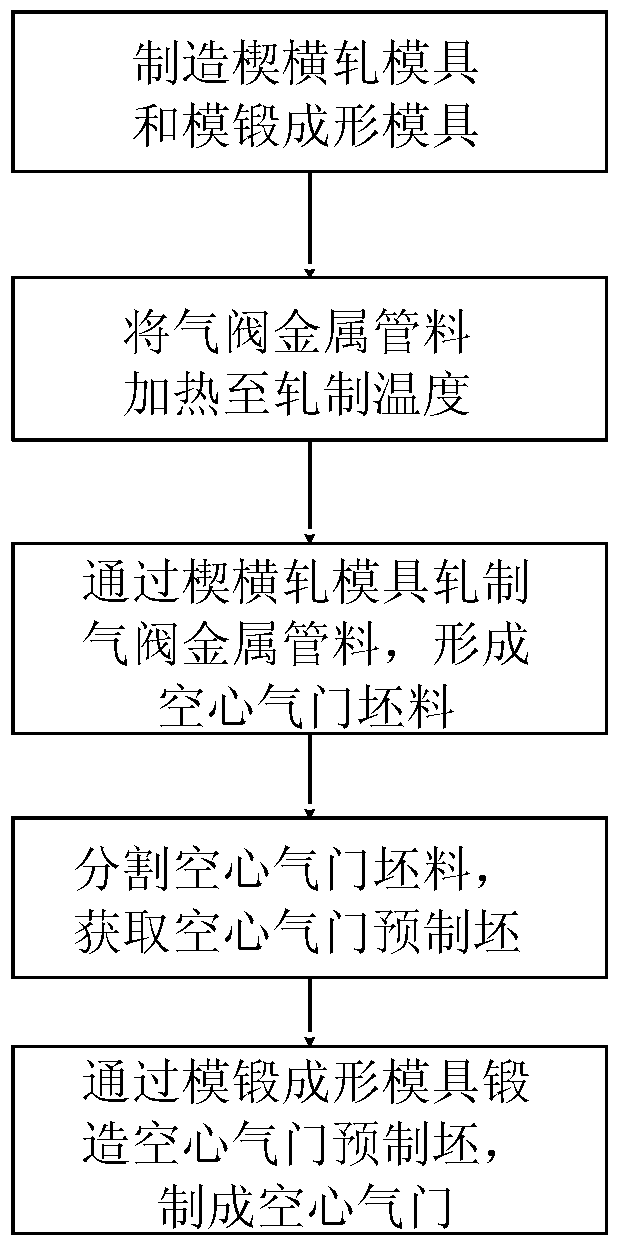