MACHINE TOOL
本発明は、工作機械に関する。
工作機械は、主軸の先端から突出した棒材を位置決め部材に突き当て、加工に際して棒材の位置決めが行われる。一方、棒材は、加工が終わった部分が突切り工具を用いた突切り加工によって切り離される。突切り加工後は、突切り状態の判定が行われている(例えば、特許文献1参照)。特許文献1に記載の工作機械は、棒材に接触する検出子を検出手段とし、検出手段を移動させることによって突切り状態の判定が行われている。なお、検出手段を主軸の軸心方向に交差する方向に移動させて進行させて突切り状態の判定を行うことも一般的に公知となっている。
位置決め部材による棒材の位置決めは、突切り状態の判定に続いて行われるため、検出手段を突切り状態の判定を行うことができる位置に配置し、例えば、検出手段を主軸の軸心方向に交差する方向に移動させて進行させ、突切り状態の判定を行い、棒材に対して適切に突切り加工が行われたことが検出されると、続いて、予め設定された位置に位置決め部材を配置し、その位置決め部材に、棒材の先端面を突き当てることにより棒材の位置決めが行われる。
つまり、突切り加工が終了した後は、検出手段の突切り状態の判定を行うことができる所定位置への移動と、位置決め部材の棒材の突き当てが可能な所定位置への移動を行う必要がある。検出手段と位置決め部材をそれぞれ移動させる時間により加工に必要な時間が長時間化する問題点があり、加工全体のサイクルタイムを短縮することが望まれている。
本発明は上記事情に鑑みなされたものであり、突切り状態の検出動作及び棒材の位置決め動作に要する時間を短縮することができる工作機械を提供することを目的とする。
本発明は、主軸から突出する棒材が突き当てられ、前記棒材を位置決めする位置決め部材と、前記主軸の軸心方向に交差する方向への進行によって前記棒材の突切り状態を検出する検出手段と、を備え、前記位置決め部材は、前記検出手段の進行を許容する通路を有するとともに、前記検出手段の進行する方向と同方向に移動して、前記棒材と突き当てた突き当て姿勢と前記棒材との突き当てを解除した解除姿勢とが切り替えられ、前記検出手段は、前記解除姿勢で、前記通路を介して前記進行を行う工作機械である。
本発明に係る工作機械によれば、突切り状態の検出動作及び棒材の位置決め動作に要する時間を短縮することができる。
本発明に係る工作機械の一例である自動旋盤1は、図1に示すように、制御部70の制御にしたがって、主軸50から突出するように主軸50に把持された棒材90に対して、主軸50の軸心C方向(Z方向)の前方で、くし歯型の刃物台10(工具台の一例)に固定されたバイト11(工具の一例)等によって加工を行う。刃物台10にはZ方向に直交するY方向のY軸を中心として旋回可能な旋回刃物台が一体的に固定され、旋回刃物台によって棒材90をいわゆるB軸加工することができる。棒材90は刃物台10に対して主軸50の軸心Cを挟んで対向する別のくし歯型の刃物台10′に固定されたバイトで加工することもできる。なお、当該刃物台10′は主軸50の軸線方向(Z方向)に移動自在に支持されている。また、棒材90は、公知のバーフィーダ等によって、主軸50に対して後方から供給される。
刃物台10は、軸心Cに対して互いに直交する水平方向のX方向と鉛直方向のY方向とにそれぞれ移動する。刃物台10には、棒材90の加工が終わった部分を突切って切り離す突切り加工を行う突切りバイト15(突切り工具の一例)を含む複数の加工用のバイト11がY方向に並んで装着されている。
刃物台10は、各バイト11が棒材90に接触しないようにX方向に退避し、Y方向に移動することにより、加工に用いられるバイト11が選択され、X方向の棒材90側に移動することにより、選択されたバイト11による棒材90の加工を行うことができる。
刃物台10には、図2,3に示すように、突切りバイト15の下方に位置決めブロック20(位置決め部材の一例)が一体的に固定されている。位置決めブロック20は刃物台10の移動によって、X方向及びY方向に移動する。
位置決めブロック20には、主軸50側に棒材90の先端面91が突き当てられる突き当て面23が形成されている。位置決めブロック20は、刃物台10の移動によって、棒材90(先端面91)の突き当てが可能となる突き当て位置(突き当て姿勢)からX方向に沿って、棒材90に接触しない退避位置(解除姿勢)まで移動することができる。
位置決めブロック20には、図2に示すように、X方向(主軸50の軸心C方向に交差する方向)に延びた溝21(通路の一例)が形成されている。この溝21は、図3に示すように、突き当て面23に凹状の部分として形成されている。溝21には、溝21に沿って真っ直ぐに延びた棒状の剛体の検出子30(検出手段の一例)が配置されている。検出子30には、ガイド32に沿って進退する屈曲可能のワイヤ33を介してエアシリンダ31が接続されている。
検出子30は、エアシリンダ31によって、溝21に沿ってX方向に移動することができる。エアシリンダ31の動作によりワイヤ33がガイド32に対して繰り出された状態では、ワイヤ33に押された検出子30がX方向に前進し、図2の二点鎖線で示すように、位置決めブロック20の内側端面22から突出する。一方、エアシリンダ31の動作によりワイヤ33がガイド32に対して引き込まれた状態では、ワイヤ33に引っ張られた検出子30がX方向に後退し、図2の破線で示すように、位置決めブロック20の内側端面22よりも引っ込む。
検出子30が棒材90に当たることによって、検出子30の移動が規制される。制御部70は、検出子30の突出した長さに応じて、突切り加工による棒材90の突切りの成否(突切り状態の一例)を検出することができる。検出子30、エアシリンダ31、ガイド32、ワイヤ33及び制御部70等によって、突切り検出装置が構成されている。
以上のように構成された自動旋盤1は、図4に示す処理の流れにしたがって動作する。棒材90に対して、バイト11による通常の加工が行われ(S1)、この加工が終了した後は、突切りバイト15による突切り加工が行われる(S2)。突切りバイト15の折損等がなく、突切り加工が正常に行われた場合は、図5に示すように、突切り加工により切り離された部分は例えば下方に落下しているため図示されていない。
図6に示すように、突切り加工後、刃物台10はX方向に移動して退避し(図4のS3)、図7に示すように、Y方向において溝21の中心を軸心Cに合わせ、検出子30の位置が軸心Cと同じ位置になるように、Y方向に移動する(図4のS3)。このとき位置決めブロック20は退避位置にある。この後、制御部70の制御により、検出子30をX方向に前進して進行させることによって、制御部70は突切り状態を検出する(図4のS4)。制御部70が、突切り加工が正常に行われなかったことを検出したとき(図4のS4においてNO)は、突切りバイト15の折損等が考えられるため、自動旋盤1による加工は終了する。
制御部70が、突切り加工が正常に行われたことを検出したとき(図4のS4においてYES)は、自動旋盤1は、棒材90の、Z方向における位置決めを行う。図10に示すように、制御部70はエアシリンダ31を、ワイヤ33を引き込むように動作させて、検出子30を位置決めブロック20の内側に、溝21に沿って引き込むとともに、刃物台10をX方向に前進させて位置決めブロック20を軸心C上に配置する(図4のS5)。
続いて、制御部70は主軸50が棒材90を保持しているチャックを開いて主軸50に対し棒材90をZ方向に移動可能とし(図4のS6)、棒材90をZ方向に前進させ、図11に示すように、先端面91が位置決めブロック20の突き当て面23に突き当て、棒材90の位置決めを行う(図4のS6)。
棒材90の位置決めが行われた状態で、制御部70は、主軸50を加工長さ分後退させ、棒材90をチャックするように制御する。その後、制御部70は、位置決めブロック20が棒材90から離れるように、刃物台10をX方向に後退させ、次の加工に用いる特定のバイト11を選択するように、刃物台10をY方向に移動させ(図4のS7)、ステップ1(S1)に戻って、棒材90に対する次の加工を行うように主軸50及び刃物台10を制御し、以下、上記動作を繰り返す。
このように構成された実施形態の自動旋盤1によれば、検出子30を、溝21を介して進行させることによって、突切り状態の検出を行うことができ、検出子30の検出動作での移動方向(X方向)と、位置決めブロック20の位置決め動作での移動方向(X方向)とが同じであるため、突切り状態の検出後に、刃物台10をY方向に移動させることなく、X方向に移動させるだけで、棒材90の位置決めを行うことができる。したがって、刃物台10をY方向に移動させてから、位置決めブロック20を軸心Cに向けてX方向に前進させる場合に比べて、突切り状態の検出動作及び位置決め動作に要する時間を短縮することができる。
本実施形態の自動旋盤1は、位置決めブロック20が刃物台10に固定されたものであるため、位置決めブロック20を刃物台10とは別に独立して移動させる移動手段を備える必要がない。ただし、本発明に係る工作機械は、位置決め部材が工具台に固定されたものに限定されず、工具台とは別体で、工具台とは独立して移動するものであってもよい。
本実施形態の自動旋盤1は、検出子30の通過する通路が、位置決めブロック20の突き当て面23に凹状に形成されたものであるため、突き当て面23を凹状に切削等することで簡単に通路を形成することができる。ただし、本発明に係る工作機械は、検出子の通過する通路が位置決め部材の突き当て面に形成されたものに限定されず、位置決め部材の内部に形成された柱状の空間である孔であってもよい。
なお、突き当て面23に形成された凹状の部分としては、溝21(底面及び両側面を有し(底面が両側面と区別されずに滑らかに連なっているものを含む)、上方が開放した凹状の空間部分)という形態に限定されず、例えば、一方の側面が存在しない凹状の部分である切欠きや、底面が存在しない凹状の部分であるスリットなどであってもよい。
本実施形態の自動旋盤1は、凹状の部分の一例としての溝21が、棒材90の先端面91が位置決めブロック20の突き当て面23に接した状態で、先端面91における中心である軸心Cに対応して形成されているため、仮に、突切り加工において、棒材90の先端面91の中心に先端面91からZ方向に突出した円柱状のボスが残存した場合にも、位置決めの際に、その突出したボスは、突き当て面23より凹んだ溝21に進入するため、先端面91を突き当て面23に突き当てることができ、ボスが突き当て面23に当たることによる棒材90の位置決めの精度が低下するのを防止することができる。
ただし、本発明に係る工作機械は、凹状の部分が、棒材の先端面が位置決め部材の突き当て面に接した状態で、棒材の先端面における中心に対応して形成されているものに限定されず、凹状の部分が、棒材の先端面における中心からずれた位置に形成されていてもよい。
上記実施形態は、剛体の検出子30を溝21を介してX方向に進行させて突切り状態の検出を行うように構成された例を説明したが、突切り検出装置を、レーザ光の照射と照射したレーザ光の反射の受光等によって突切り状態を検出するように構成することもできる。この場合、照射されるレーザ光や反射されるレーザ光を溝21を介して進行させることができる。
本出願は、2016年8月31日に日本国特許庁に出願された特願2016-170350に基づいて優先権を主張し、その全ての開示は完全に本明細書で参照により組み込まれる。
The purpose of the invention is to reduce the time required, in a machine tool, for the overall operation including a detection operation of a cutoff state and a positioning operation. This automatic lathe (1) (machine tool) comprises: a positioning block (20) against which a rod member (90) projecting from a main spindle (50) abuts, and that positions the rod member (90); and a detector (30) that detects a cutoff state of the rod member (90) by advancing in a direction intersecting with the direction of the axial center C of the main spindle (50). The positioning block (20) includes a groove (21) (an example of a passage) allowing the detector (30) to advance, moves in the same direction as the direction in which the detector (30) advances, and is switched between an abutting posture in abutment against the rod member (90) and a release posture in which the abutment against the rod member (90) is released. The detector (30) advances through the passage in the release posture.
主軸から突出する棒材が突き当てられ、前記棒材を位置決めする位置決め部材と、
前記位置決め部材は、前記棒材の突切り加工を行う突切り工具が装着された工具台に固定されている請求項1に記載の工作機械。
前記通路は、前記棒材の先端面が突き当てられる突き当て面に形成された凹状の部分である請求項1又は2に記載の工作機械。
前記凹状の部分は、前記先端面が前記突き当て面に接した状態で、前記先端面における中心に対応して形成されている請求項3に記載の工作機械。
関連出願の相互参照
前記主軸の軸心方向に交差する方向への進行によって前記棒材の突切り状態を検出する検出手段と、を備え、
前記位置決め部材は、前記検出手段の進行を許容する通路を有するとともに、前記検出手段の進行する方向と同方向に移動して、前記棒材と突き当てた突き当て姿勢と前記棒材との突き当てを解除した解除姿勢とが切り替えられ、
前記検出手段は、前記位置決め部材が前記解除姿勢のとき、前記通路を介して前記進行を行う工作機械。
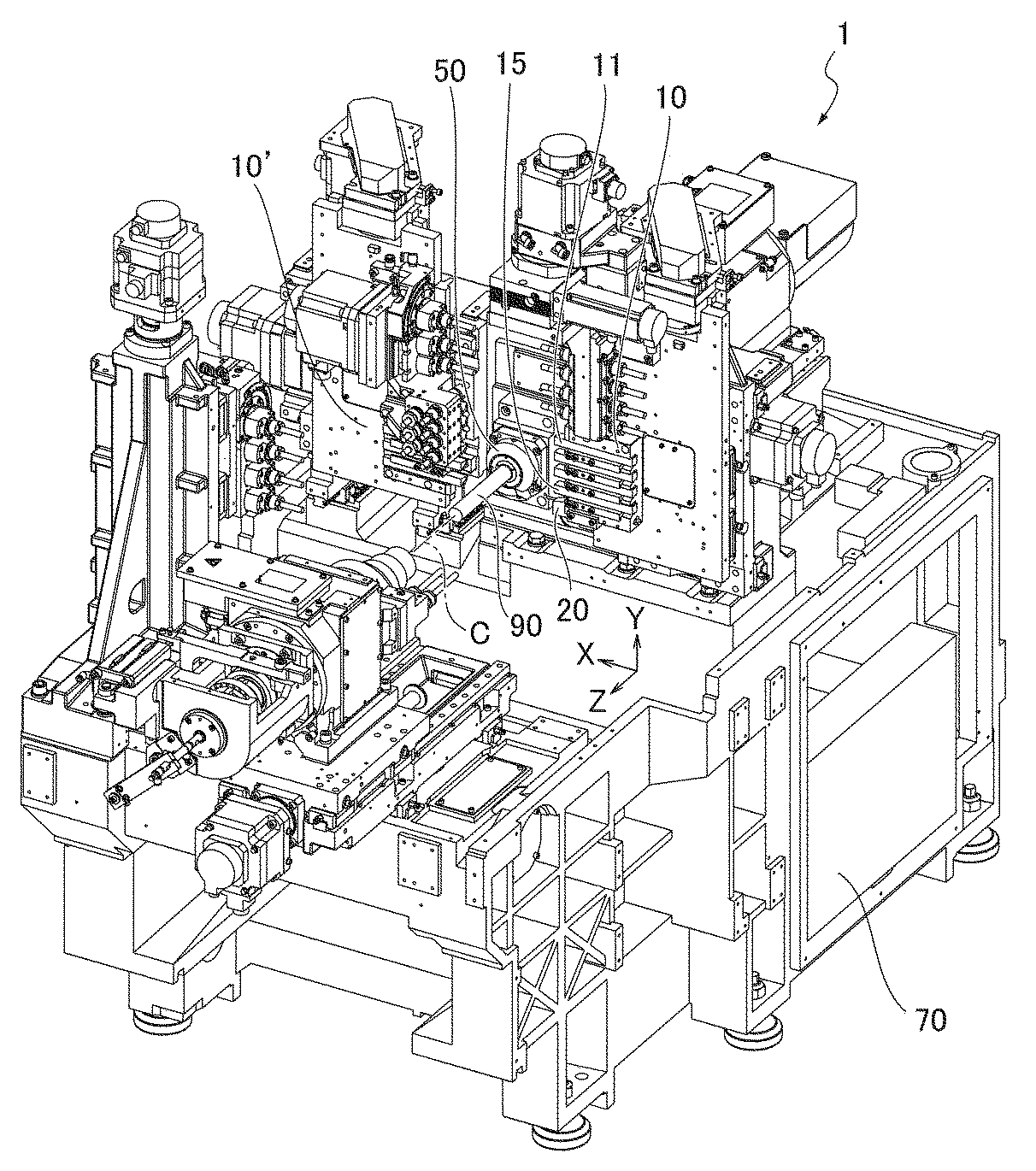
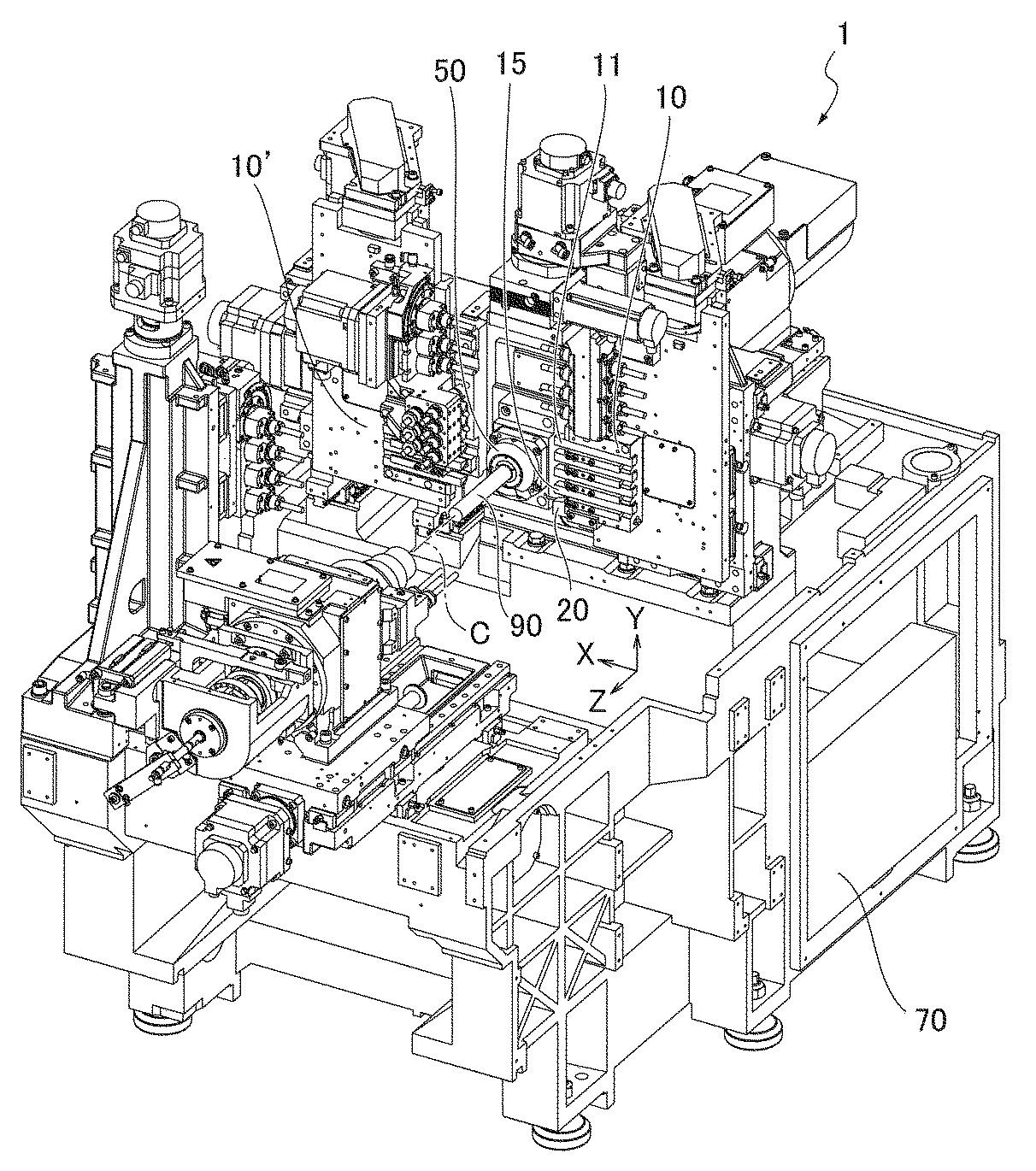
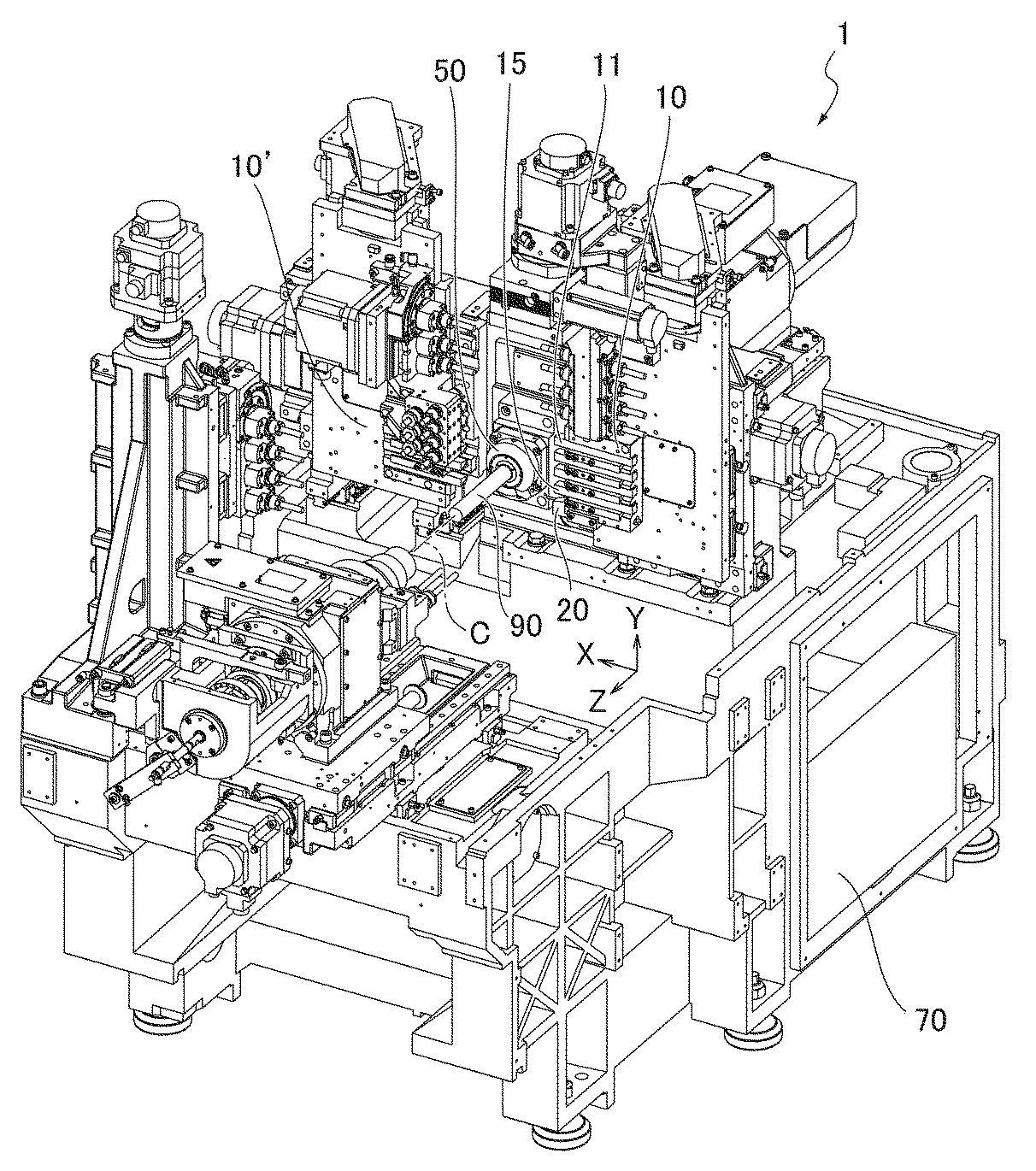
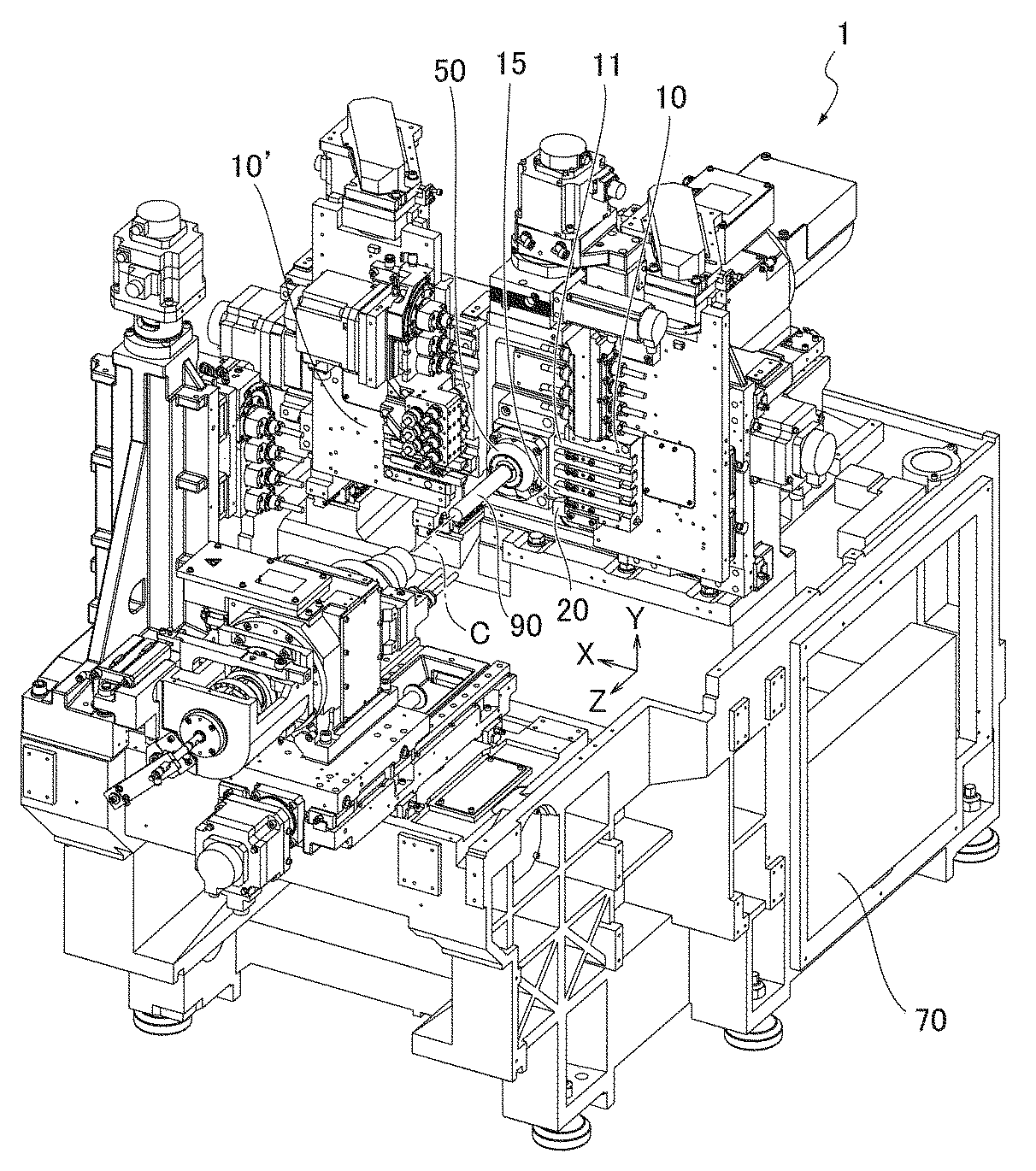
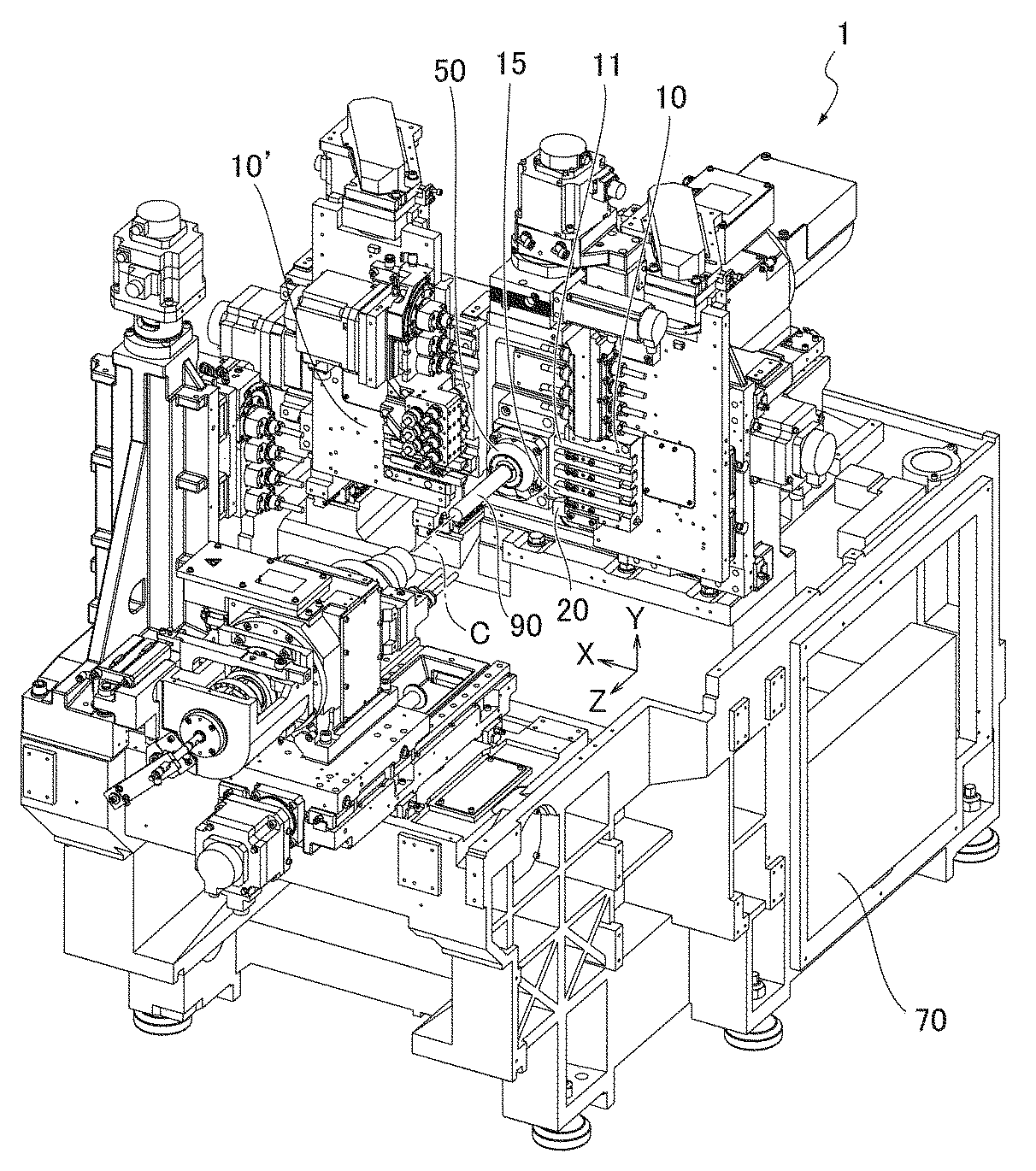
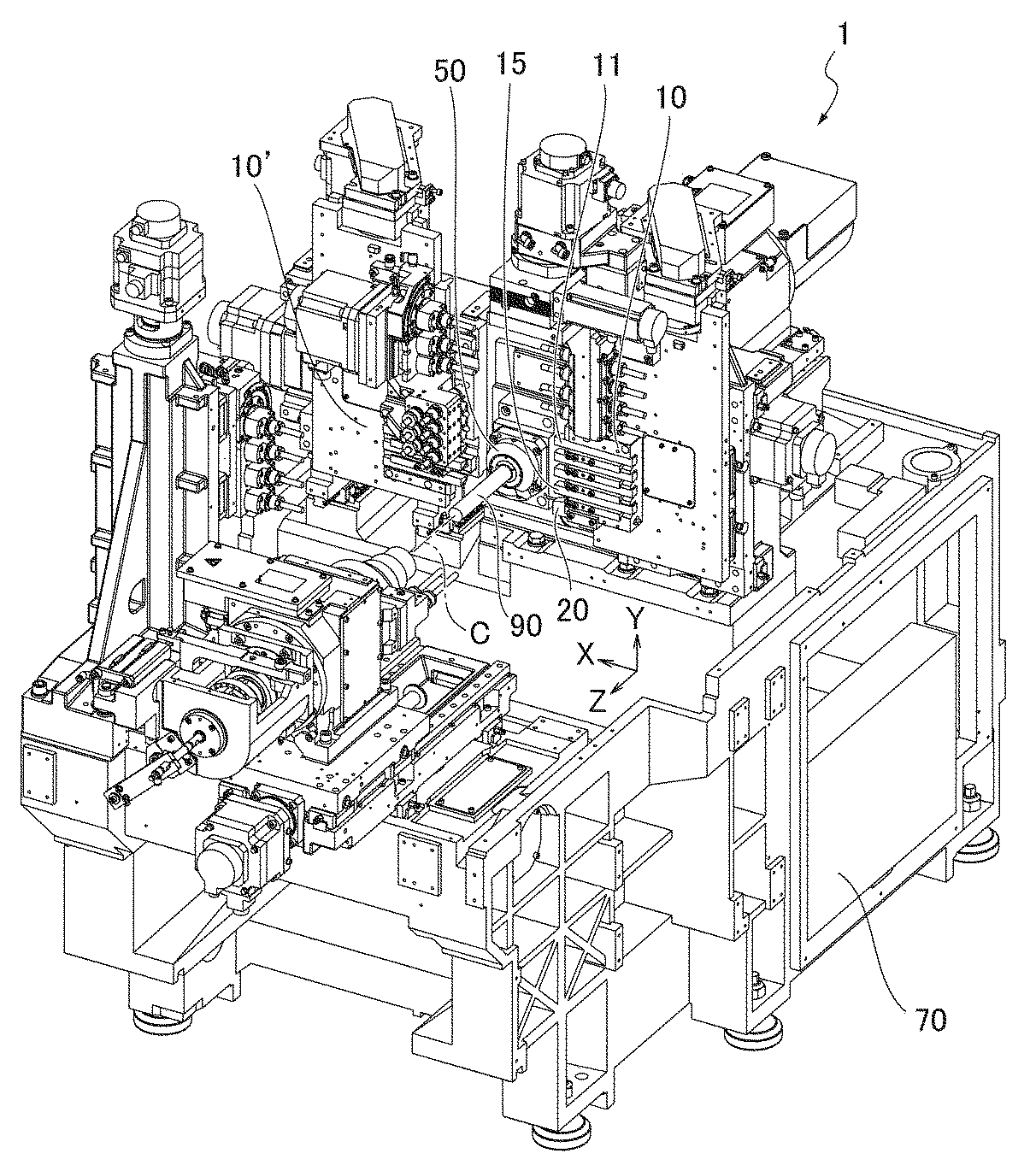
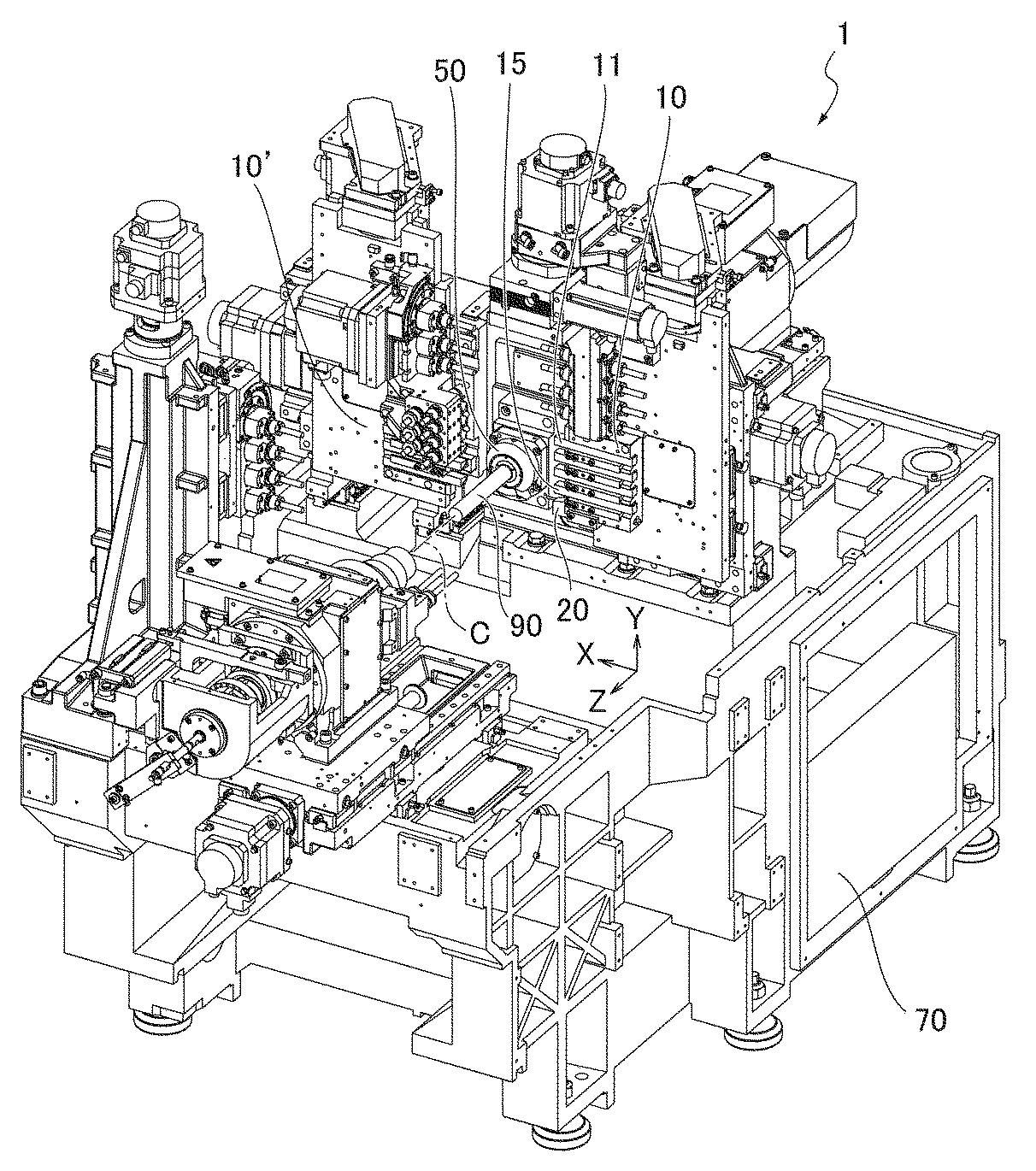
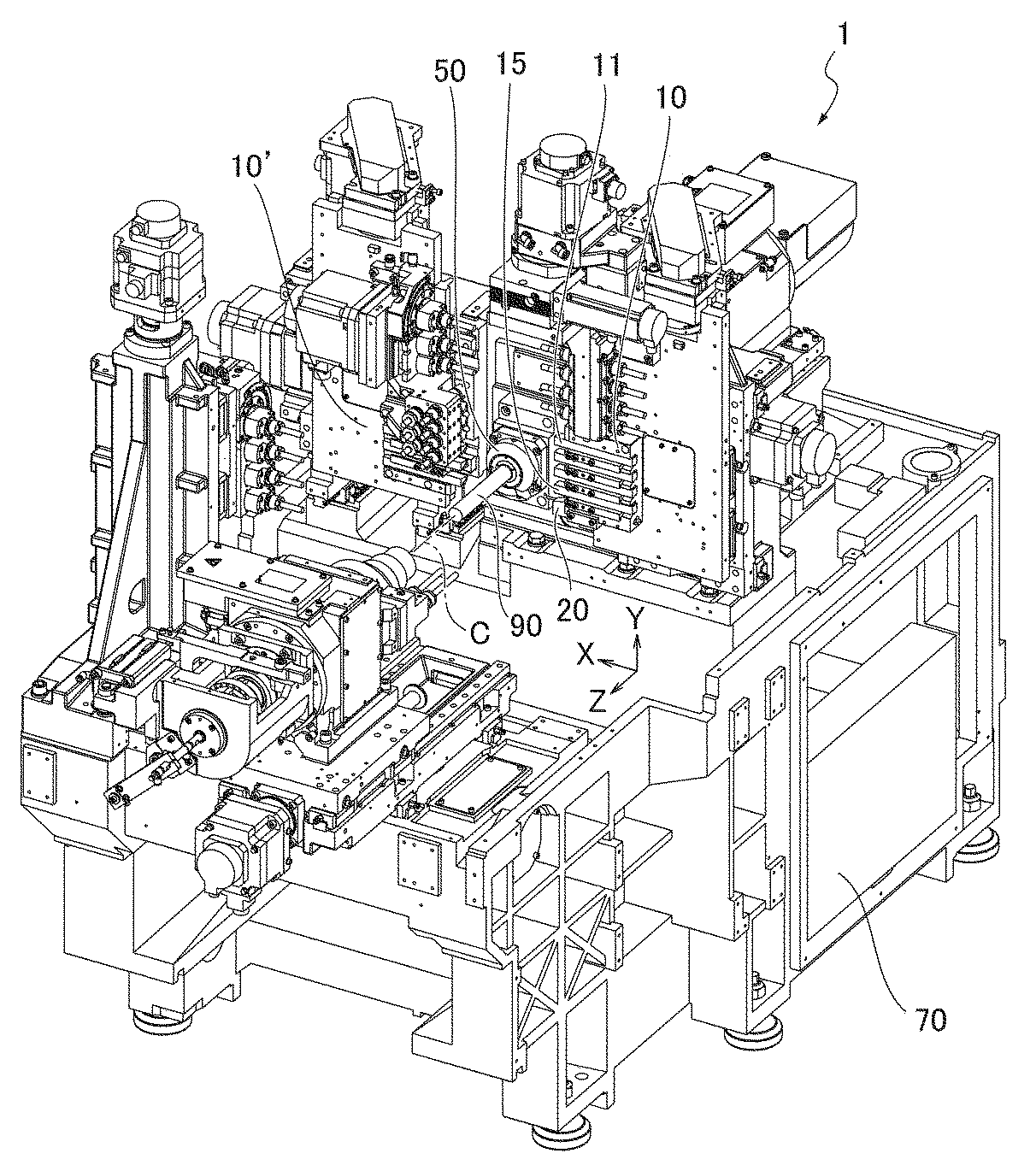
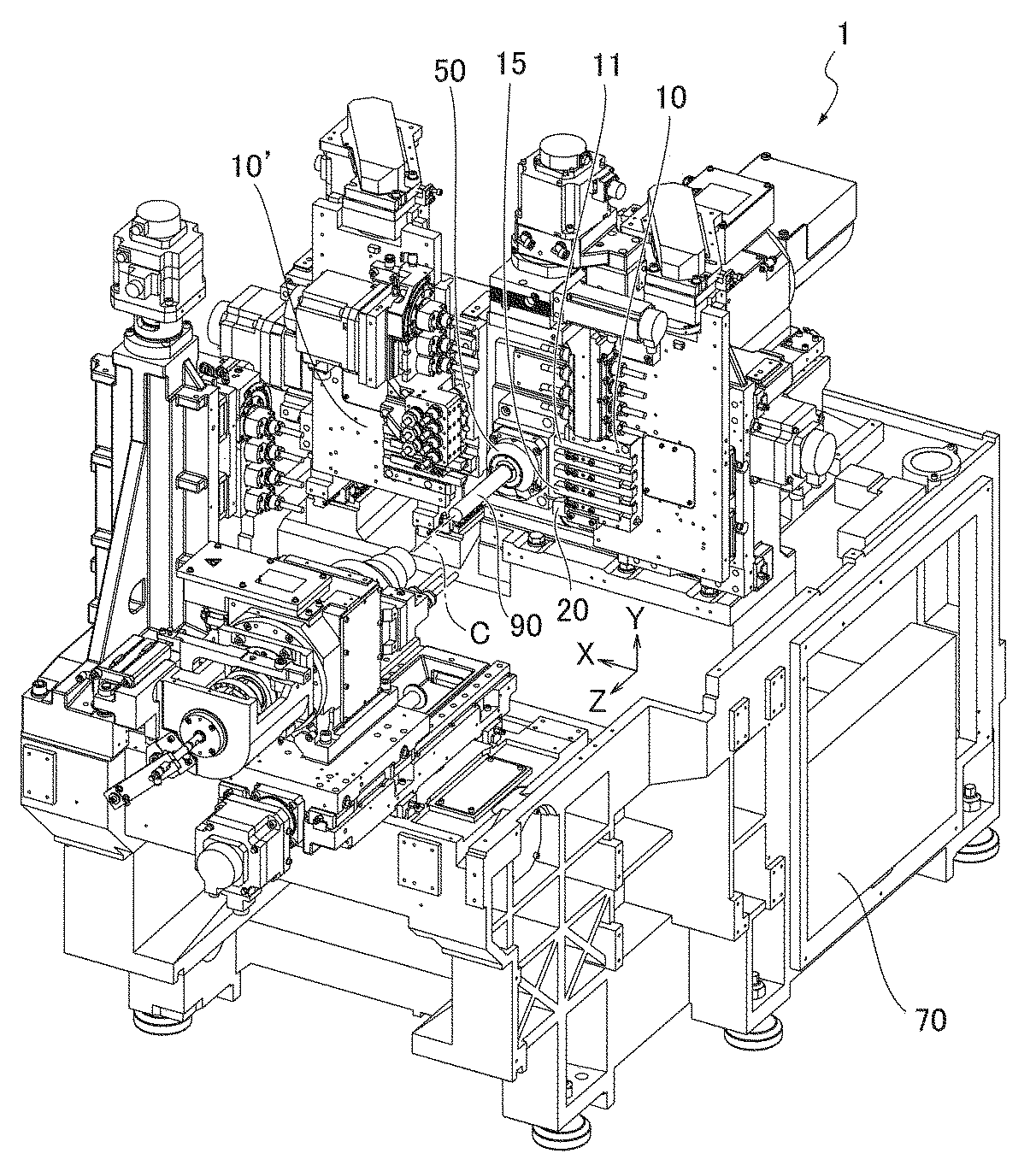
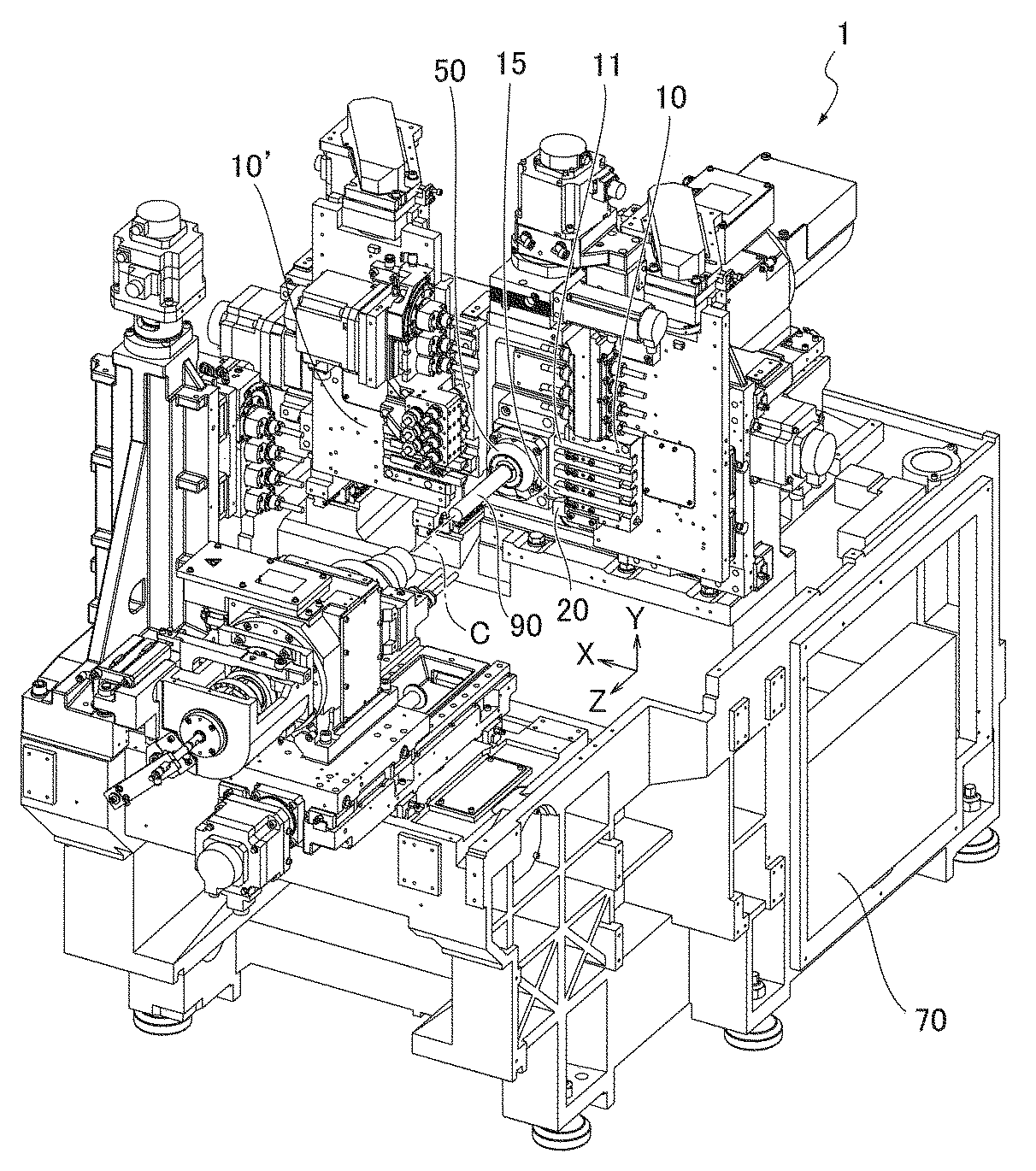
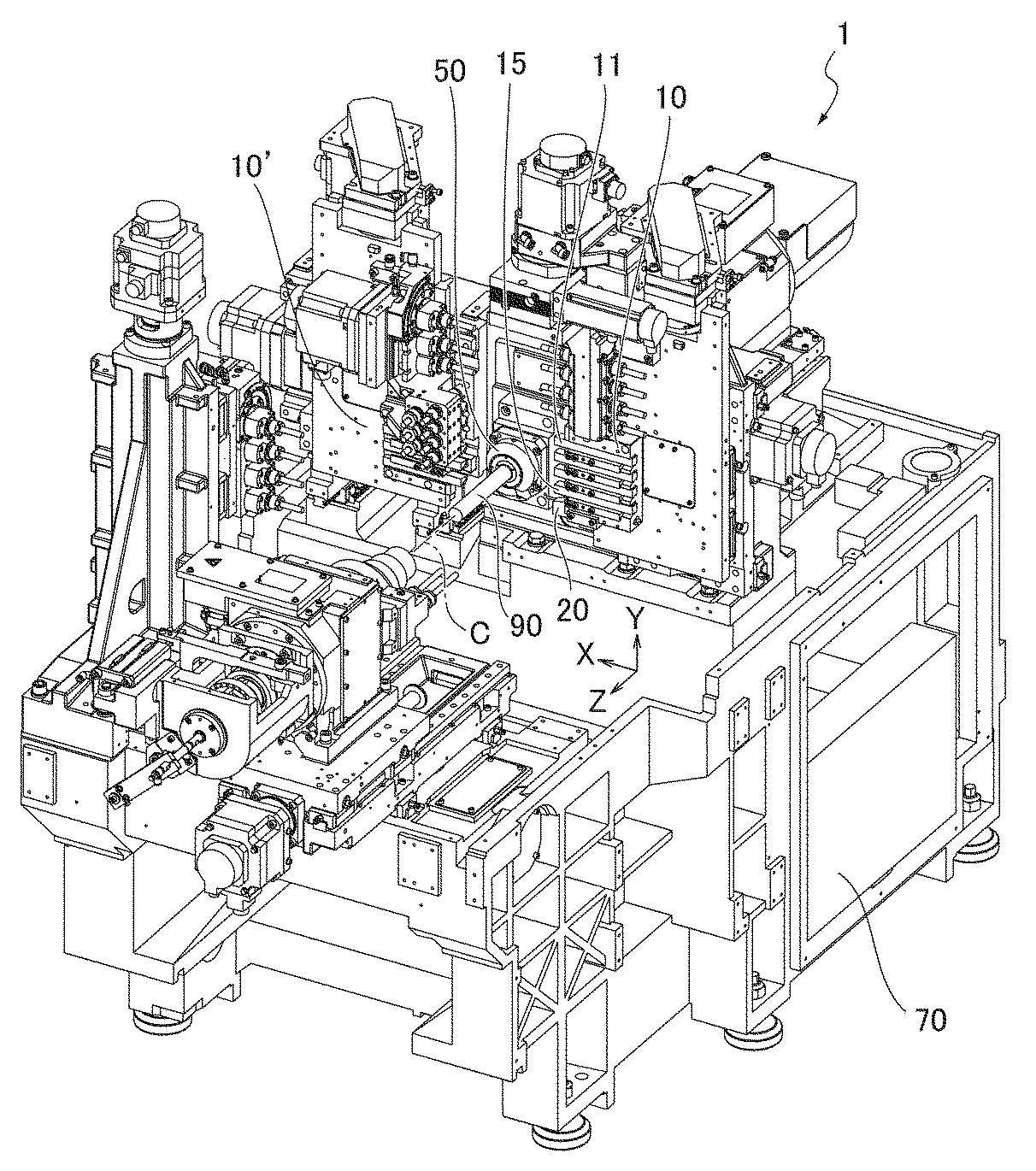