Drive control method for a military equipment, in particular a weapon or a sensor.
[0001] The invention relates to a drive control method for, in particular an electric drive of a military equipment, in particular a weapon or a gun, wherein a control structure for regulating the drive is used. [0002] The present invention concerns in particular a method for electric drive control of a weapon, in particular a gun. The apparatus is oriented in azimuth and in elevation by means of the drive. This may be provided two partial drives, wherein a part or both drive part drives according to the method or are regulated before-preserving. This method can for example. Regulating the drive of a anti-aircraft gun, in particular a naval gun are used. The gun can have for example a 35 mm caliber. The control of the engine speed is a challenge, since the drive train consisting of an electric motor, an elastic shaft and a load comprises a structural tendency to oscillate. As a distance or in a drive train of a genus control path is hereinafter correct device, namely the unit consisting of a motor, a transmission and for example a ring gear with a corresponding rotation angle encoder understood. The motor acts on the transmission and this acts on a ring gear on a corresponding shaft for example. It is a torque to the motor and in so doing will set the position and the speed of the corresponding shaft via the encoder values measured and determined. [0003] Control structures are also used for machine tools such inter alia. The control engine speed in drives, for example machine tools, represents a challenge, since the drive train consisting of electric motor, shaft and load has a structural tendency to oscillate. It is desirable, to achieve a constant engine speed under varying load as possible. [0004] The use of frequency suppressing, passive filters is disadvantageous, because the bandwidth of the control path is thereby restricted. [0005] Further is known, the control structure to extend around an inner control loop with a state regulator, with the active damping of resonance of the controlled system can be obtained. This allows a higher engine speed and better control quality control structure against external disturbances sensitivity. Nevertheless the control response with respect to the setpoint tracking is the interference suppression and strongly coupled, so that a balance between these complex by adjusting in realizing the desired value according to guide and the interference suppression values and must be completed, so that vibrations do not result. [0006] From DE 1 0301,765 a1 is a control structure for active damping of low frequency oscillations in stamps must known controlled machine tools. The control structure has a speed controller with a proportional part and an integral part on. A to a interfering, low-frequency vibration phase shifted and DC component-free, low frequency correction signal is asserted at a addition site before or after the integral part. The correction signal is formed in an active damping element. In the damping element is for generating the correction signal at a low frequency vibration interfering with the addition site a difference between the target rotational speed from a position of a position regulator and a superimposed setpoint derived speed formed. The correction signal to the undesired damping vibrations or even eliminating. The correction signal has the frequency of the undesired vibration, is about 180° out of phase but not this. [0007] From DE 10,150,710 a1 detect the position of at least one function is a method for a rotating machine element known carrier. [0008] The state of the art is not yet optimum configuration. The above rule structures are in the art with condition control for speed control of machine tools used on the motor side. This is sufficient for machine tools, since the absolute angular position of the workpiece during processing of a rotating workpiece with respect to the axis of rotation is not of interest, since the tool during machining passes through a plurality of rotations. An electrically driven shaft of a gun in the control however is the knowledge of the angular position of the driven shaft of central importance. [0009] Of the invention based on the has, a control system for a drive of a military device indicate, with a particularly effective suppression of vibrations and resonant oscillations is possible. [0010] Of this invention by a method having the features of Patent preserving task is now claim 1 dissolved. [0011] It is a load side and/or a load side speed control position control carried out. It is the load on the controlled system controlled, wherein it is subordinated, in which other parts are for example the motor state. For the load position and the load speed values are predetermined. The invention extends the control structure is a load side and a speed control - angular position. The signals are integrated into the control system for the motor speed of the drive motor and the position of the drive motor. These two signals are provided by the motor controller can be read out and with corresponding signal transmitters and are determined. The position and the speed of the load side by a model of the control system software are determined. The method is implemented by a software in the engine control device. The invention extends the control structure software side. It is any additional hardware to the signal transmitters except for measuring the motor position and motor speed required. [0012] It is a cascading control structure used. Am first inner control loop can have a state regulator. A second inner or medium speed control for the load side and a third outer-loop control loop is the load side is used for position control. This control is the control for two motors connected upstream of the gun. By means of the two motors is about a respective axis alignment, for example in azimuth or the elevation axis executable. The two motors are in particularly preferred configuration with respect to one another. The rule structure is used for control of two clamped-together motors. [0013] In particularly preferred configuration is a naval gun regulated the drive. The position of the naval gun against the ship movement is regulated this horizon. In this system the static friction of the drive are overcome. The invention regulates quickly method however, the state of the static friction is that the system does not, whereby the quality of the stabilization is greatly increased. This jerk in vibrations and are largely, in particular completely eliminated. [0014] To the method has the advantage, that an active damping takes place by means of a regulating path, whereby vibrations are eliminated. A further drive control on the load side is instead on the motor side. There is an angular position control for rotational axes in military applications. [0015] By means of a state regulator is an active damping of resonance and thus improve the control quality of the load position and the load speed and an effective suppression of external disturbances. By the active damping is the problem of resonance of the regulating path not only treating symptoms of dissolved and therefore makes en route control problems are occurring. A setpoint tracking and a better sensitivity to disturbance can be individually adjusted. The useful frequency range is extended. For the weapon and their control is thus an increased precision. [0016]Amain field of application of the method is a gun with azimuth and elevation axes - electrically driven, in particular a naval gun with the need for horizon position control under the ship movement. Further fields of application of the invention are sensors, trackers, laser or the like. Such military equipment in azimuth and/or elevational are also by means of the respective drives or by means of the corresponding drive can be aligned. [0017] In a preferred embodiment of the process is a friction compensation used, wherein certain parameters are determined in advance by means of a static model, wherein the necessary friction compensation values are calculated by means of the model as a pilot control. Friction in a drive train is a complex, highly non-linear phenomenon, is influenced by various factors. Static friction and sliding friction friction can be distinguished. In particular the static friction is preferably taken into account in the control, position and speed control error in sequence to - a drive speed behavior during a zero crossing to avoid. It can be used for this purpose a static model, with predetermined parameters, the necessary friction compensation values calculated as the pilot control. This concept can be sufficient, although no variable factors such as temperature, aging, and compensates for manufacturing tolerances into account. [0018] In a preferred embodiment is an adaptive interference compensation used, wherein during the duration of the process disturbance compensation values based on a dynamic model and on the basis of measured values are determined from the control system. This comprises a friction compensation, in which the friction compensation values based on a dynamic model and on the basis of measured values from the control system in operation, i.e. are determined on-line. This has the advantage, that an adaptive friction compensation in the form of an adaptive, general interference compensation throughout the life of the drive train always correct compensation values independently of varying ambient factors such as the temperature provides. By means of this adaptive interference compensation is taken into account not only the friction, but it can also be automatically further disturbance into account. The adaptive interference compensation is on-line, i.e. during execution of the process on the basis of the measured values from the control system on the basis of the dynamic model and made. [0019] The aforementioned disadvantages are avoided and corresponding advantages are achieved therefore. [0020] There is now a plurality of opportunities, developing and education to the method. Therefor may be referred claims 1 to claim first with the downstream. In the following three preferred embodiments of the invention with reference to the drawing in detail below and associated description. In the drawing shows: Fig. 1 a first control structure with a condition control, Fig. 2 a second control structure with an additional friction compensation, and Fig. 3 a third control structure with an adaptive interference compensation. [0021] With reference to the Fig. 1 io 3 must now a method for regulating an electric drive of a military equipment, particularly a gun or a sensor are explained. By means of the electric drive device in azimuth and/or elevational can be aligned. The drive has two electric motors (not shown) on particular tensioned one against, in azimuth and/or around the device aligning two mutually braced electric motors, the aligning device in elevation. The device is in particular as gun, preferably formed as marine gun. In the Fig. 1 io 3 are now different cone structures 1, 2, 3 represented. The rule used for structures or are used for regulating the driving of the drive. [0022] Hereinafter must first the similarities between control structures 1, 2, 3 are explained, then allowed on the differences with respect to the Fig. 1 3 2 rule structures and control structure into 1 are enlarged. 4 Serves as control path wherein apparatus wherein the unit from the engine or gun, the transmission and in particular the ring gear a rotational axis, wherein the axis of rotation with a rotation angle encoder is provided. The motor acts on the transmission and the gear mechanism acts on the ring gear. In Fig. 4 the control path is 1 io 3 represented by a dotted box. Input signals of the control structures 1, 2, 3 are a desired value for the load position and a desired value for a 5 6 for the load speed. The desired value for the load position is a position controller 7 5 supplied. The output of the position regulator 6 7 and the desired value for the load speed is a downstream speed regulator 8 supplied. The output of the speed regulator 9 8 now provides a motor control signal, the control section 4 is supplied. [0023] The aforementioned disadvantages are now avoided in, speed control and/or a load side that a load side position control are carried out. A control circuit 10 is used for carrying out the speed control and a load-side load-side control circuit 11 is used for position control. The control system 12 for a load of 4 will speed input of the speed regulator 8 returned, wherein the difference between the desired value for the load speed and load speed 12 is formed 6. [0024]Aload position 13 is further from the control system 4 for input of the position regulator 7 returned, wherein a difference between the desired value for the load position and the load position 13 5 is formed. The control loop for regulating the load position here forms an outer control loop 11 11. The control loop 10 forms an inner control loop 10, a cascading control structure whereby each 1.2, 3 is formed. [0025] In the Fig. 1 design forms the control loop represented an average loop 10. It is a further inner control loop 14 with a state regulator 15 present. Starting from this the state regulator 15 16 4 of the control path of the control system 4 via the state regulator and conditions supplied 15 for output of the speed regulator 8 recycled through difference formation in the motor control signal converted. By the additional state regulator 15 may be achieved better control quality active damping of resonance and thus the load position and the load speed and an effective suppression of external disturbances are achieved. [0026] Fig. 2 represented in 2 mm and a friction compensation control structure has 17 on. Friction in the drive train is a complex, highly non-linear phenomenon, is influenced by various factors. The static friction and sliding friction and friction differs in rule can lead to errors. This configuration is therefore a static model used with predetermined parameters, the necessary friction compensation values calculated as the pilot control. The pilot control is achieved at the output of the speed regulator 8th a disadvantage of this configuration is, that the friction compensation variable factors such as temperature, aging, and not capable of compensating for manufacturing tolerances into account. [0027] On the preferred control structure in the Fig. 3 3 may therefore now be elaborated. Fig. 3 is a further control loop 18 in the represented, wherein the control circuit comprises an adaptive interference compensation 18 19. There either friction compensation values and generally the values of the disturbance acting on the drive train-line based on a dynamic model and on the basis of measured values from the control system 4 determined. This thus provides an adaptive interference compensation always throughout the life of the drive train 14 correct compensation values as a function of variable ambient factors, such as the temperature. [0028] The aforementioned disadvantages are therefore avoided, corresponding advantages are achieved. [0029] 1 Control structure 2 Control structure 3 Control structure 4 Control system 5 Desired value for load position The invention concerns a method for controlling an electric drive of a military equipment, in particular a weapon or a sensor, wherein the apparatus is oriented in azimuth and in elevation by means of the drive, wherein a control structure (1) is used for regulating the drive. A particularly effective in suppressing vibrations and resonant oscillations is possible, that a load side and/or a load side be made speed control position control. Desired value for load speed Position controller Speed regulator Motor control signal Control loop (load side speed control) Control circuit Load speed Load position Control circuit State regulator Conditions of the controlled system Friction compensation Control loop (interference compensation) an adaptive interference compensation Method for regulating an electric drive of a military equipment, in particular a weapon or a sensor, wherein the device is oriented in azimuth and elevation by means of the drive, wherein a control structure (1.2, 3) is used for regulating the drive, characterized in that a load side and/or a load side speed control position control are performed. A method according to claim 1, characterized in that by means of a state regulator (15) a resonance of the controlled system (4) is damped. A method according to claim 1 or 2, characterized in that a cascaded control structure (1.2, 3) is used, wherein a outer-loop (11) for the load side and inner loop position control (10) is used for the load-side speed control. A method according to claim 3, characterized in that a further inner control loop (14) the state regulator (15) has. A method according to any of claims 1 to 4, characterized in that the control structure (1.2, 3) for control of two clamped-together motors is used. A method according to any of claims 1 to 5, characterized in that the drive of a naval gun is regulated, wherein the horizon position of the naval gun against a ship is controlled movement. A method according to any of claims 1 to 6, characterized in that an adaptive interference compensation (19) is used, wherein during the duration of the process disturbance compensation values (19) on the basis of a dynamic model and on the basis of measured values from the control stage (4) are determined. A method according to any of claims 1 to 6, characterized in that a friction compensation (17) is used, wherein by means of a static model certain parameters are determined in advance, wherein the necessary friction compensation values are calculated by means of the model as a pilot control.Description
List of reference symbols

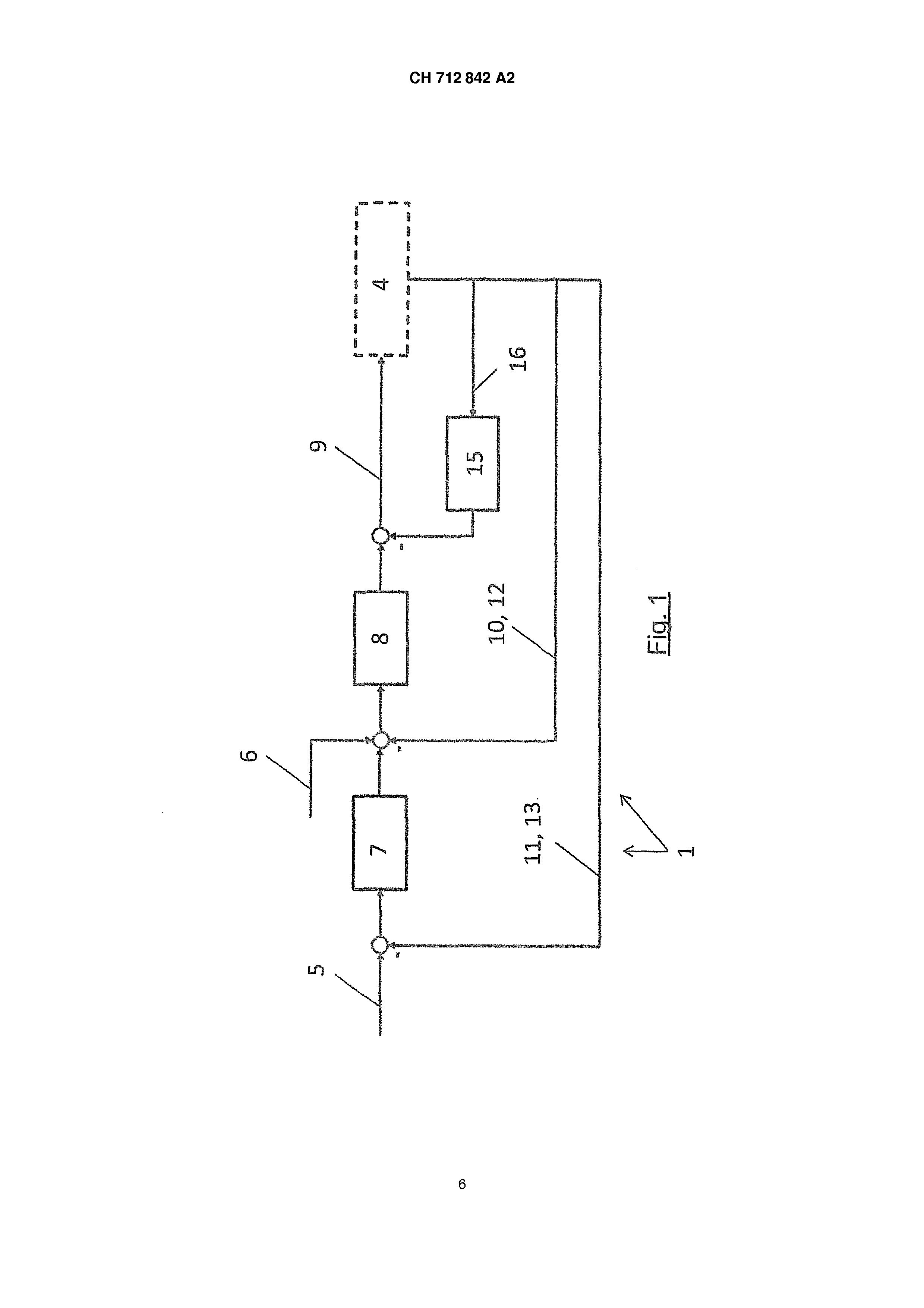
