Rotary Machine
ROTARY MACHINE A rotary fluid machine has an inner rotor 21 and an outer shell 22, arranged so that sealing points on the inside of the shell interact in a sealing arrangement with the outer surface of the rotor, such that in use the relative motion of the rotor to the shell causes fluid to be moved through the machine by means of ducts 27, 30, and ports 28, 29 in the rotor. Preferably the outer surface of the rotor and the inner surface of the shell are in the form of an epitrochoid. In a preferred arrangement the rotor rotates on a first axis and the shell rotates on a second axis offset from the first. Fluid enters the machine by a duct 26 in one side of the rotor shaft and exits via a duct 31 in the other side of the rotor shaft. The machine may be used as a four stroke internal combustion engine or as a fluid compressor.
BACKGROUND OF THE INVENTION
Many different kinds of rotary engines and compressors are known. It has long been the goal to replace reciprocating compressors and engines with rotary machines, however certainly in the case of engines, in practice only one, the Wankel engine, has come close to being successful and widely used today.
The Wankel engine suffers from a number of problems, one of which is wear issues with the internal rotor seals, and another is that the Wankel engine design in common use is not a true rotary machine, in that there are still reciprocating parts which generally requires there to be two counterbalanced rotors. Furthermore, the location of the tip seals on the inner rotor means that these cannot be replaced without stripping the entire engine down.
It is possible to use a Wankel design and to spin both the inner rotor and the outer casing axially, thus having no reciprocating components (as in the very first Wankel engine), however because the sealing tips are on the inner rotor therefore the sliding surface containing the inlet and exhaust ports must be in the shell or casing, thus making it is difficultto make the sealing arrangements necessary to get the gases to and from the rotating casing.
Cooley proposed an engine (US 724994) very similar to the invention here, using two axially spinning rotors. In his design the inlet and outlet routes were via sliding seals between the shell and the casing which made this design very problematic.
It is the aim of this invention to overcome some of the problems that most previously known rotary machines suffer from: that is the difficulty of seal replacement, the balancing and mechanical problems of reciprocating components, and their overall complexity.
SUMMARY OF THE INVENTION
This invention concerns a rotary machine designed to be used as a compressor or an engine. More specifically, it concerns a machine where the sliding seals form part of the outer casing or shell, and the surface which the seals slide against forms part of the central rotor, allowing the gases to be transferred via the ports on the rotor. There are some principal advantages to this arrangement: the seals can be accessed from outside the machine enabling easy replacement and opening up the possibility of using cheaper materials, and the gases can be transferred in and out through the rotor shaft with simple rotary seals at the shaft ends, which enables both the rotor and shell to spin axially so making a true rotary machine.
Thus according to the invention there is a rotary machine comprising an inner rotor and an outer shell, said shell having sealing points on its inner surface which interact in a sealing arrangement with the outer surface of said rotor, said rotor having a fluid inlet means and a fluid outlet means terminating at ports in the rotor, so that in use the movement of the rotor relative to the shell causes the movement of fluid through the machine.
The outer surface of the inner rotor is preferably substantially in the form of an epitrochoid, however other suitable shapes may be used for the outer surface of the rotor, providing of course that in use the sealing points of the shell maintain contact or very close proximity to the surface of the rotor. Preferably the inside surface of the shell is also substantially epitrochoidal in shape.
The ports are preferably positioned on the outer surface of the rotor.
The outer shell may be made to rotate axially, on an axis offset from the axis of the inner rotor, thus making a true rotary machine with no reciprocating parts.
The said inlet and outlet means may conveniently be formed as cylindrica! ducts in the shaft of the inner rotor connected to the ports. In such an arrangement the gases will preferably enter at one side of the rotor and exit at the other, although other arrangements are possible.
The rotor surface may typically have two lobes and the shell have three sealing points, but other arrangements are possible for instance a rotor with three lobes and a shell with four sealing points. Many other combinations are possible generally using a rotor with one less lobe than there are sealing points on the shell.
The rotor and shell are preferably mounted in a frame, structure or casing to locate the axes of the shell and rotor accurately in relation to each other.
The shell preferably includes an internal gear wheel, which meshes with an outer gear wheel attached to the rotor so as to keep these two pads moving in correct relationship with each other and therefore minimising internal wear of the sealing points and surfaces.
The sealing points may be comprised movable strips. Said strips may be conveniently accessed from the outside of the shell, enabling their easy replacement.
With a design using a two lobed rotor, there may be provided one inlet and one outlet port at suitable locations on the rotor to enable the machine to operate as a four stroke internal combustion engine. Alternatively a similar two lobed design may be used as a pump or compressor by providing two inlet ports and two outlet ports at -suitable locations on the rotor.
When the machine is being used as an engine, spark plugs may be provided around the periphery of the shell. One skilled in the art will see that the inlet means may be provided with a means to add fuel to and regulate the air flow into the engine, e.g. an injection system or carburettor which may conveniently be attached to the frame holding the rotor and shell, and the outlet means may be connected to an exhaust system.
BRIEF DESCRIPTION OF THE DRAWINGS
Figure 1 shows a cross section of an engine perpendicular to the axes of rotation Figure 2 shows the engine as in Figure 1, after an anticlockwise rotation of the rotor of 90 degrees Figure 3 shows a cross section of an engine in line with the axes of rotation Figure 4 shows a modification of the sealing points Figure 5 shows a compressor with four ports Figure 6 shows an engine comprising a rotor with four lobes and a shell with five.
sealing points * 5
DETAILED DESCRIPTION
Theinventionwillnow-bedescribed,-by-way-ofexample-only-, with-referenceto the accompanying drawings.
Referring first to figure 1, this shows the internal workings of a four stroke internal combustion engine 19 according to the invention. In this engine an inner rotor 1 rotates around an axis 2 within an outer shell 3 which rotates around an axis 4 offset from axis 2, the direction of rotation being by the arrows 2r and 3r. The rotor in this embodiment has two lobes 40 and the shell has three sealing points 5. The sealing points are comprised moveable sealing strips 6 with spring arrangements 7 and retaining plates 8. Both the shell 3 and the rotor 1 rotate in the same direction at different speeds in the ratio 2:3 respectively. Due to the epitrochoidal geometry of the rotor surface and the relative speeds of the rotor and shell, the sealing points maintain a sliding gas tight seal with the rotor surface. The rotor shaft 9 is cylindrical and the duct 10 in the centre comprises part of the inlet and outlet means. The inlet means includes the duct in the shaft nearest the observer extending to a duct 11 through the rotor terminating at the inlet port 12 in the external surface of the rotor.
The outlet means consists of a duct in the shaft (which is furthest from the observer extending to a duct 13 through the rotor terminating at the outlet port 14. In use the rotation of the rotor and the shell create varying volume cavities A, B. C between the rotor and shell, which in conjunction with the position of the inlet and outlet ports cause gas to be drawn in, compressed, combusted and expanded and then expelled as in a standard four stroke engine. In this diagram the cavity A between the rotor and the shell is in the process of expelling gas through the outlet port 14, the direction of flow shown by the arrow, and cavity B is drawing in gas through the inlet port 12, again the gas flow is shown by the arrow. Cavity C is at the fully compressed pdsition for firing. The outer shell may include one or more combustion chambers 15 to hold the bulk of the compressed gas. Spark plugs 16 ignite the compressed gases at the point of maximum compression.
Figure 2 shows the rotor and shell as in Figure 1 after the rotor has passed through 90 degrees of anticlockwise rotation, with a corresponding 60 degrees of rotation of the shell. Cavity A has decreased in volume, B has reached maximum volume and C is just starting to expand. Thus it can be seen that the rotation causes gas flow compatible with a four stroke engine cycle.
Note the location of the two meshing gear wheels on the shell 50 and the rotor 51. These gears ensure that the rotor moves in the correct relationship to the shell, preventing contact between the rotor surface and the shell surface (except at the sealing points) and reducing the stress and wear to the shell and sealing points Figure 3 shows a cross section of an engine in line with the axes of rotation. A housing 20 locates the rotor 21 and the shell 22 in position by means of bearings 23.
The rotor is equipped with side seals around its periphery 24 which seal against the inside of the shell 22 (the said sealing points of the shell are notshown in this diagram). The shaft 25 of the rotor has a concentric duct 26 which is sealed against the housing with the rotary seal 34 and said duct 26 extends to a further duct 27 through the rotor terminating at the port 28, this arrangement comprising the inlet means. Likewise a second port 29 is connected to duct 30 in the rotor and duct 31 in the shaft 36, which is sealed against the housing with the seal 35, this forming the outlet means. A high voltage electrical current is supplied to an electrode 32 which is in close proximity to the spark plug 33 at the point when the engine is at the position of maximum compression, thus initiating combustion.
Figure 4 shows a variation of the sealing points of the embodiment in Figure 1, in * which the sealing points 60 are contiguous with the shell 61 and achieve the gas tight sealing by being maintained in very close proximity to the rotor 62.
Figure 5 shows a compressor which has two inlet ports 70 and two outlet ports * 71. This uses the same principal of variable size cavities as the engine in Figure 1, but omits the combustion I expansion cycle and instead performs two compression cycles for every 360 degree rotation of the rotor.
Figure 6 shows an engine 100 comprising a shell 101 with five sealing points 102, and a rotor 103 with four lobes 104. In this arrangement it is necessary to have two pairs of ports 110, 111. It may be seen that this arrangement creates a well-balanced rotor both mechanically and in terms of thermal expansion due to the symmetrical arrangement of the rotor.
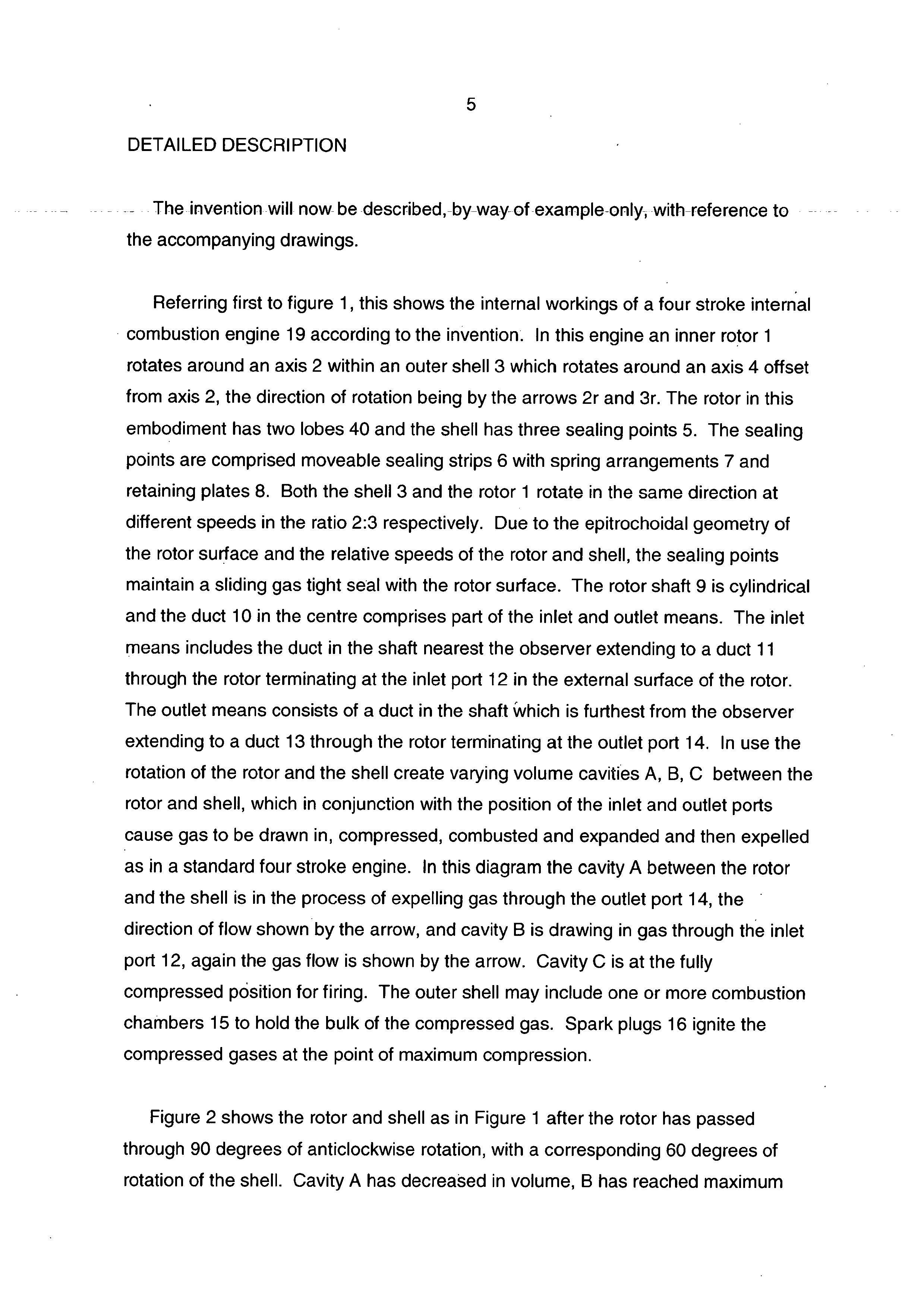
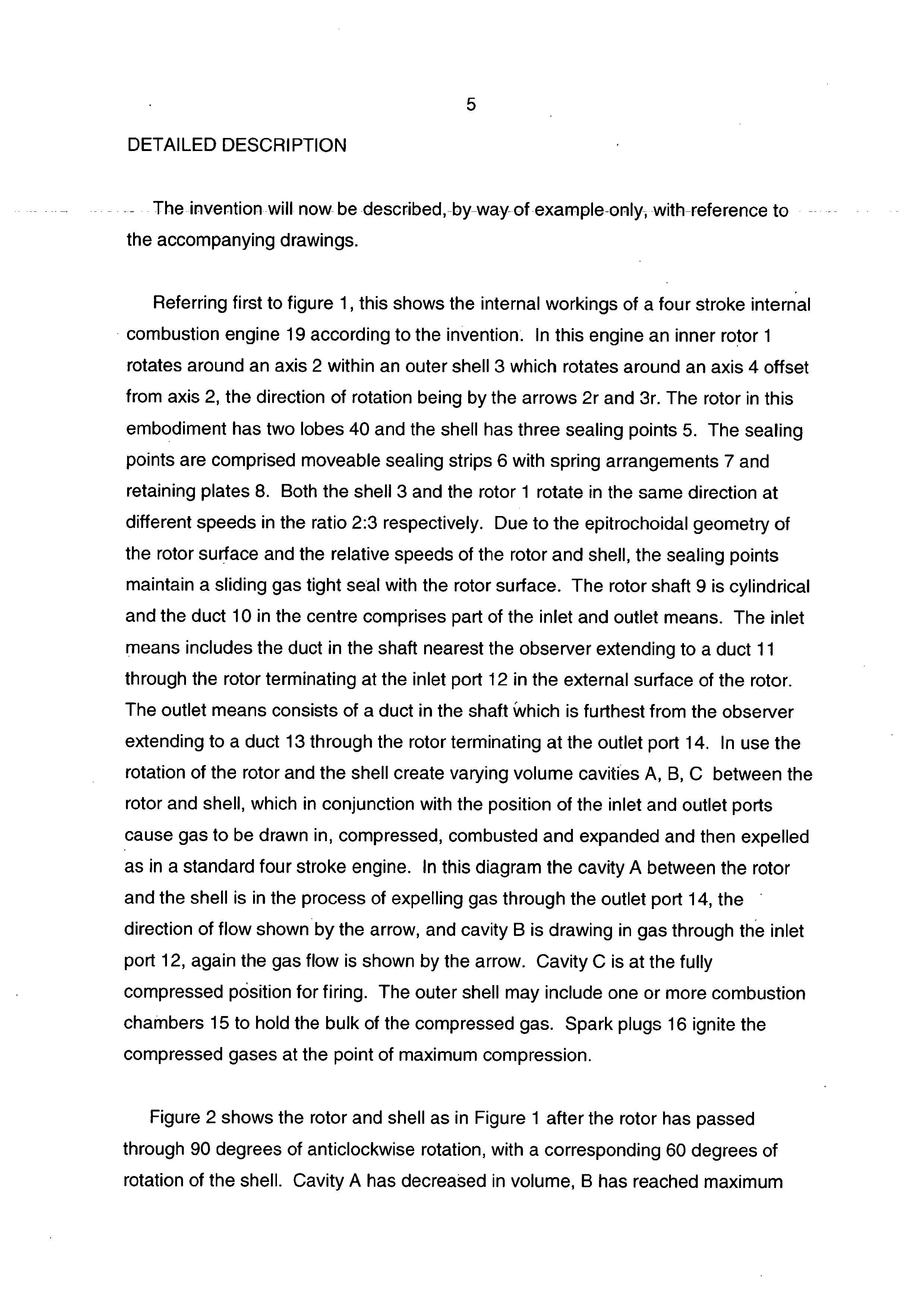
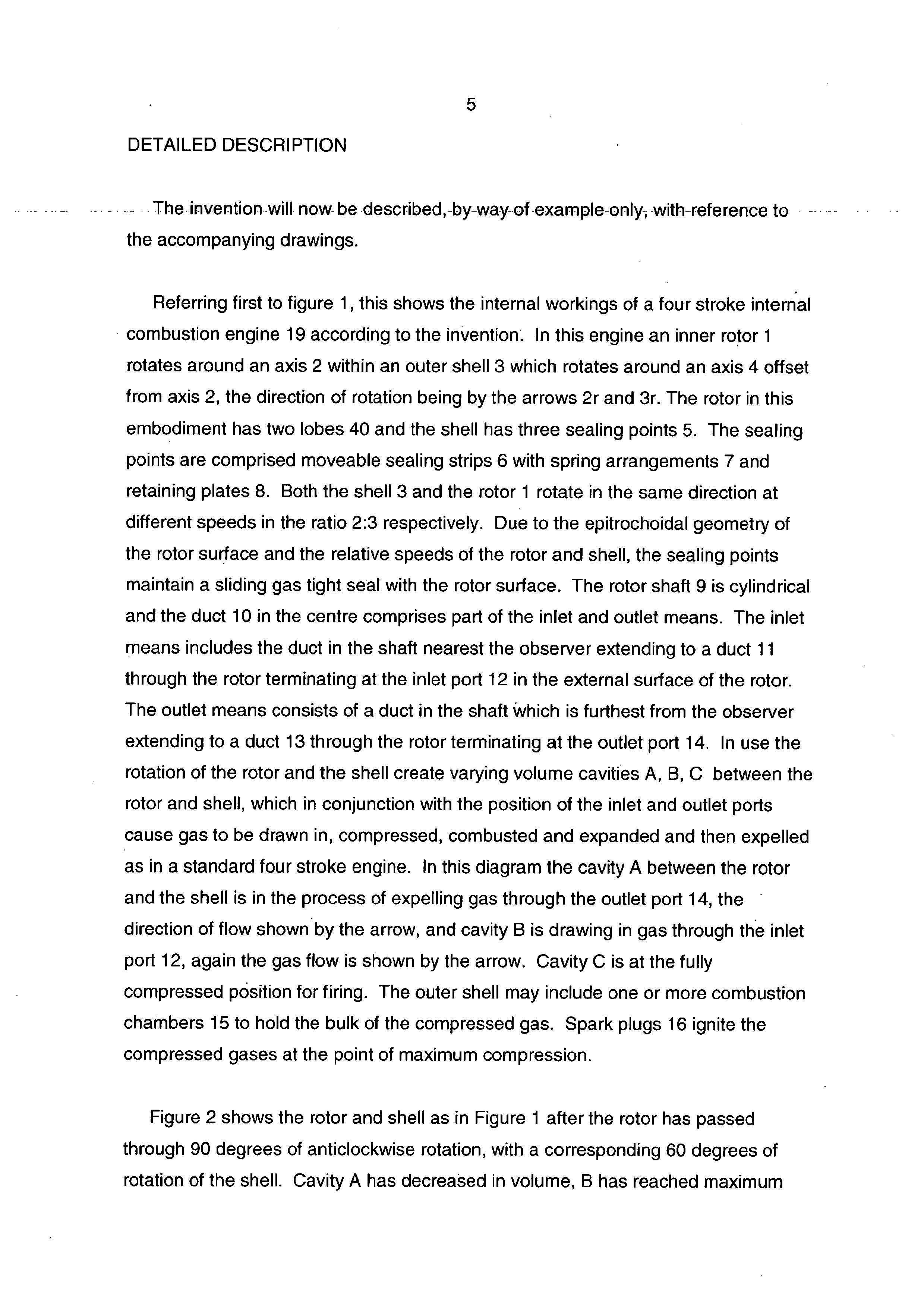
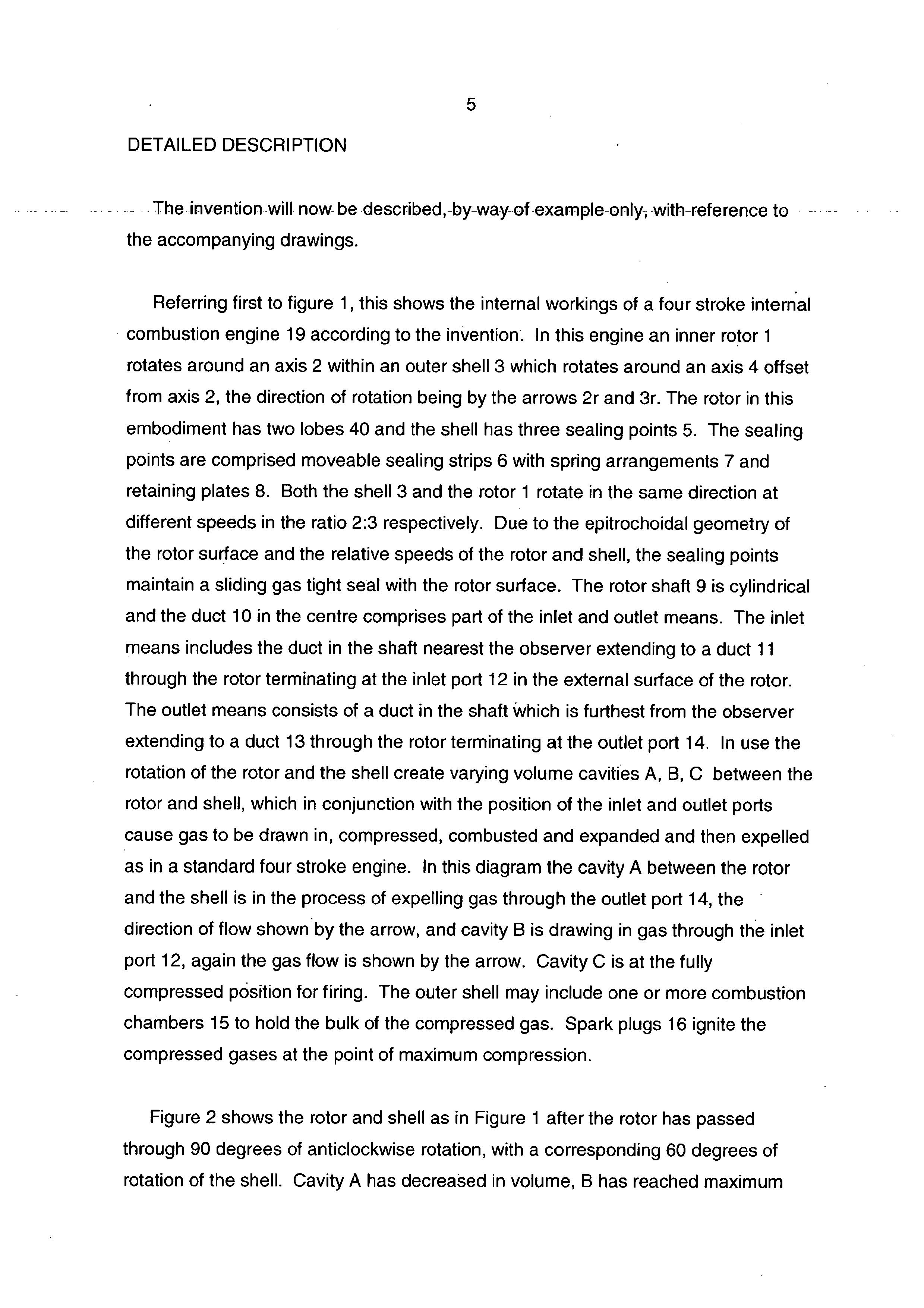