SECONDARY ELECTRODE PRESSING AND SLITTING APPARATUS
The present invention refers to secondary battery electrode is formed by compressing a longitudinal direction of a plurality of secondary battery electrode strip (strip) (percentage) slitting (slitting) divided into a secondary battery electrode pressed slitting device are disclosed. (Recharging) rechargeable secondary battery as an electric cell, electrolyte of ion (separator) moves between the anode electrode and the negative electrode layer by an insulation region consists of by repeated charging and discharging. A positive and a negative secondary battery such as electrode is commonly, current collector and metal material, a plurality of electrodes spaced from each other on a current collector electrode active material layer stacked with each other. A plurality of electrodes extending parallel to the length of current collector qualitative layer active material. A pair of electrodes spaced from each other between the exposed portions of the directional unit as active material layer current collector is age of vehicle from the outside. Current collector for example, copper (Cu) or aluminum (Al) sheet (sheet) or foil (foil) made implementation being. Said qualitative layer electrode formed and dried to secondary battery electrode active material on a current collector. The higher the degree of integration of an electrode active material on an inside a matrix shape with a capacity of the secondary battery, said secondary battery electrode and compressing the pressing (pressing) operation to 10sup16. In addition, appropriate width said secondary battery electrode divided into a plurality of secondary battery electrode strip (strip) (percentage) a slitting (slitting) work is required substrate. To form a pressing device pressing to form a slitting device is provided on said pressing operation and said slitting operation in slitting are separated individually satisfactorily. The, mount about the pin is spatial number to said device. In addition, device pressing roll (roll) and unloading (unloading) form wound secondary battery electrode, is transferred through a second same slitting device loading (loading), productivity is also the door number flow tides. On the other hand, slitting (slitting) retrieve secondary battery electrode strip holding the small diameter roller being fitted detachably to less than branch. Recovery roller secondary battery electrode strip sandwiched branch when an allowable peak load winding, the rollers roll (roll) recovering branch out form wound secondary battery electrode strip recovery and, secondary battery electrode wound main should not recovering roller mounted on new branch. This branch is not replacing the automated, movable branch and a decrease in productivity due to some unexpected delays, worker industrial disaster risk rising substrate. The present invention refers to, roll-to-roll (roll-a to a-roll) terminates at a secondary battery electrode can seamlessly manner maintains secondary battery electrode and compressing the pressing work, a plurality of secondary battery electrode (strip) and dividing the slitting work performed sequentially strip electrode for secondary battery, recovery roller supporting branch around secondary battery electrode strip with the replacement work automatic secondary battery electrode pressed a slitting device number [...] substrate. The present invention refers to, roll (roll) form a tangled wound secondary battery electrode and the supply roller, said feed roller supplied in reducing its thickness in order to radiate secondary battery electrode pressing unit pressing (pressing unit), which passes a secondary battery electrode pass through said pressing, advancing parallel to the plurality of secondary battery electrode strip (strip) cut dividing the slitting unit (slitting unit), said slitting unit through a plurality of secondary battery electrode strip all odd in th secondary battery electrode strip branch number 1 ([...]) recovering by winding the recovery device, and a plurality of secondary battery electrode strip formed in said slitting pass through all the odd th secondary battery electrode strip with recovering by winding the branch number 2 recovery, recovery and said number 2 recovery unit comprises said number 1, said secondary battery electrode strip for their development has been stopped automatically replacing said secondary battery electrode strip is wound branch, said slitting unit is disposed between said number 1 recovery recovery device and said number 2, secondary battery electrode pressed a slitting device number [...] substrate. Recovery and said number 2 recovery unit comprises said number 1, mounted as rotating roller can be removably fixed to said branch, said branch pipe to said secondary battery electrode strip is wound position number 1, number 2 and the winding branch said secondary battery electrode strip wound with a non-alternating between the float branch ([...]) move a pair of sheet support roller, said roller through said secondary battery electrode strip being wound branch advance as, said number 1 direction and the opposite direction in a position that is branch pipe support roller approaches which reciprocates reciprocating roller, and said secondary battery electrode strip width with cutting knife for cutting (cutting knife), said branch pipe with such a branch pipe supporting roller in said roller and said number 2 position reciprocating said number 1 into both ends said number 1 position of sheet, said cutting knife is said reciprocating roller and said number 1 position of sheet preserve said number 2 position of sheet support roller can be cut in a direction facing the secondary battery electrode strip width. Recovery and said number 2 recovery unit comprises said number 1, said pair of sheet support roller supports, [...] (turret) rotating in one direction, and reciprocating said rollers towards the branch position instead of a guiding roller as said number 2 strip secondary battery electrode, said further guide roller supported in a pair of [...][...], said pair of sheet support roller [...] 180° intervals and said rotation with respect to the center at a distance such as, a pair of said rotation with respect to the center 180° intervals in said [...][...] at a distance such as can be. Recovery and said number 2 recovery unit comprises said number 1, said number 1 position of sheet being wound onto the secondary battery electrode strip winding density can be further touch roller (touch roller). Said plurality among all differ from the secondary battery electrode strip is odd, all odd said th secondary battery electrode strip is wound around the apart from one another in said number 1 to branch recovery in its longitudinal direction, the plurality differ from the secondary battery electrode among all the odd said strip, said strip is said number 2 in its longitudinal direction to branch recovery all the odd th secondary battery electrode spaced from each other can be wound disclosed. Said slitting unit, said secondary battery electrode extending in the lateral direction of said secondary battery electrode carries a support roller, being introduced into the outer peripheral surface of said support roller groove (groove) number 1 (knife) installed on a knife knife, said secondary battery electrode the shear force (shear force) corresponding to said number 1 to be cut by a knife and knife can be disposed with number 2. Said slitting unit during said pressing unit disposed in said number 1 and said number 2 recovery recovery unit located closer to located higher than, said secondary battery electrode is closer to said pressing unit disposed in said number 1 and said number 2 during recovery recovery unit can be advanced toward said slitting unit on. The proceeds to said slitting unit through said secondary battery electrode in top down while said strip can be divided into a plurality of secondary battery electrode. Of the present invention secondary battery electrode is pressed slitting device, said secondary battery electrode pass through the pressing surface provided at upper side and if underneath capturing surface inspection unit, and surface inspection unit through said secondary battery electrode and the second picked Image (image) is repeated when the centralization of the defect is performed a label (label) fitted on the number 2 (marking) unit and a further defect marking unit number 1 defect marking, said number 1 defect marking unit is disposed between said slitting unit recovery said number 1, said number 2 defect marking unit can be disposed between said slitting unit recovery said number 2. Said secondary battery the electrode collector, one side of said at least one current collector at the sides of said current collector having a plurality of electrodes stacked apart in the lateral direction of the active material layer, said plurality of electrode active material layer in said active material layer between a pair of electrodes adjacent current collector of fat part is formed on a side surface exposed, is pressed slitting device of the present invention secondary battery electrode, said secondary battery electrode is pressed slitting device, said corrugations forming said non-directional unit number billion to a further heat treatment unit and the evaporation number 1 number 2 thermal treatment of units, said number 1 heat treatment unit is disposed between said slitting unit recovery said number 1, said number 2 heat treatment unit is said slitting unit recovery can be disposed between said number 2. Of the present invention secondary battery electrode is pressed slitting device, said secondary battery electrode number 1 and number 2 surface of impurities industry further cleaning unit (cleaning unit) number, said number 1 cleaning said slitting unit disposed between said number 1 recovery, said number 2 cleaning said slitting unit recovery can be disposed between said number 2. Instead of a plurality along said secondary battery electrode while said pressing unit, said pressing unit comprises a plurality of, which passes through the nip while said secondary battery electrode be pressurized (nip) up and down to form a disposed at the upper roller and a lower roller with, instead of a secondary battery electrode along said upper roller and a lower roller formed between the pressing unit located upstream of endless interval is, arranged downstream of the pressing unit relatively than upper roller and a lower roller formed between the nips and greater than or equal interval, a plurality of pressing said pressing unit arranged downstream of the upper roller and a lower roller most unit formed between the nips interval is, target set smaller than the thickness of secondary battery electrode thereof can. Pressed secondary battery electrode of the present invention includes a slitting device, a plurality of pressing said thickness measuring unit for measuring the thickness of a secondary battery electrode pass through further, thickness measurement unit measuring said thickness of said secondary battery electrode set compares target thickness of secondary battery electrode, according to at least one of said plurality of pressing unit pressing unit result formed between upper roller and a lower roller endless interval can be adjusted. Of the present invention secondary battery electrode is pressed slitting device, feed roller to change recovered roller pressing unit slitting unit on a propagation path of secondary battery electrode sequentially by pressing operation and slitting work table, productivity are combined each other. In particular, number 1 and number 2 recovery unit has a branch pipe is recovered and wound secondary battery electrode so as to automatically replace further enhanced productivity and work, reduces the risk of unfavorable industrial disaster. In addition, the present invention refers to pressing device installed in the installation space on the slitting device independently than if device is reduced, and reducing costs for gripping and fixing are disclosed. On the other hand, secondary battery electrode and thereafter pressing the first slitting (slitting) (pressing) the number of terminals installed secondary battery electrode strip require a pressing unit. The present invention refers to compared the number of pressing unit so that, instead of a secondary battery electrode and for design are hereinafter, are formed in the lower part for gripping and fixing. Figure 1 shows a secondary battery electrode shown one example of a dB also are disclosed. Figure 2 shows a device according to an embodiment of the present invention secondary battery electrode of pressed slitting also are disclosed. Figure 3 shows a III of Figure 2 shown portion after expanding the also are disclosed. Figure 4 shows a IV portion after expanding of Figure 2 is also shown are disclosed. Figure 5 shows a cross-section according to a 2 V a-V also shown cut also are disclosed. Figure 6 shows a number 1 and number 2 through a plurality of secondary battery electrode strip divided path separation roller is shown in the perspective view of Figure 2. Figure 10 shows a number 2 to 7 also shown in elevational view of Figure 2 sequentially operation of recovery are disclosed. Hereinafter, with reference to the attached drawing pressed slitting device according to an embodiment of the present invention secondary battery electrode detail of the SFC substrate. The specification of the present invention preferred embodiment used in terms (terminology) are properly as terms used in the order, such as the user or operator by means of which said depending on intended or the present invention can be flawless. Thus, the terms for definition throughout the content based on the specification will been commanded. Figure 1 shows a perspective view and a one example of secondary battery electrode also shown, Figure 2 according to an embodiment of the present invention secondary battery electrode of degrees and pressed slitting device, Figure 3 shows a III portion after expanding and shown in the drawing, shown in Figure 4 of Figure 2 IV portion after expanding and drawing, Figure 5 a V-a V cut cross-sectional drawing shown and also 2 according, Figure 6 of Figure 2 number 1 and number 2 through a plurality of secondary battery electrode strip separation roller of Figure 2 shown divided path sensors mounted thereon are disclosed. The reference also 1, secondary battery electrode (1) a positive electrode (anode) and a cathode (cathode) a frame shape, commonly current collector (2) on, said current collector (2) stacked at upper side and if underneath, MgO electrode active material a plurality of electrode active material layer (5) with each other. Said plurality of electrode active material layer (5) is current collector (2) width direction, i.e. a direction parallel to the Y axis rods are disposed, said plurality of electrode active material layer (5) adjacent pair of electrodes in the active material layer (5) between the free electrode active material onto the current collector (2) mounting portion exposed side or at least one of directional unit (4) is formed. Said directional unit (4) as well as current collector (2) on both sides in the lateral direction of end (3) also electrode active material layer (5) undergoes no laminate current collector (2) side or at least one of a mounting portion can be partially exposed. On the other hand, 1 also shown in maintenance work, the secondary battery electrode current collector (2) laterally provided at upper side and lower side one stacked electrode active material layer (5) may be with, pressed slitting device of the present invention secondary battery electrode current collector electrodes (2) both lateral sides of the electrode active material layer (5) is folded in a secondary battery electrode as well as, current collector (2) only one side of the electrode active material layer (5) is folded in a secondary battery electrode can be compressing. 1 Also shown in secondary battery electrode (1) may be the anode cathode may be disclosed. Current collector for the anode has at least one side provided at upper side and lower side for positive electrode active material is applied, the cathode is on the upper side and lower side at least one side of a collector for a negative active material for a negative applied. For positive current collector (2) for a cathode current collector (2) is generally, metal foil (foil) having a thickness of 3 to 500 micro m implementation being. For positive current collector (2) includes a secondary battery without chemical change has a particularly high conductivity and if not one number, e.g. stainless steel, aluminum, nickel, titanium, plastic carbon, or aluminum or stainless steel surface of carbon, nickel, titanium, surface treatment like the like can be used. For a negative current collector (2) includes a secondary battery without chemical change have specially if the number one has the conductive, e.g. copper, stainless steel, aluminum, nickel, titanium, plastic carbon, carbon surface of either of copper of stainless steel, nickel, titanium, surface treated with a like, cadmium alloy is used as the aluminum - can be. For positive current collector (2) or for a negative current collector (2) comprises a foil (foil) form which are not limited to, film (film), sheet (sheet), net (net), porous, foam, permits various forms such as a nonwoven fabric. For positive electrode active material layer (5) electrode active material for the positive electrode material, e.g., LiCoO2 , LiMn2 O4 , LiNiO2 , LiMnO2 Such as containing a lithium-based oxide-based, resin acids as a binder (binder) (resin) having a predetermined wavelength. For a negative active material layer (5) cathode material for electrode active material, e.g., carbon (C) based material, silicon (Si), tin (Sn), tin oxide (tin oxide), tin alloy composite (composite tin alloys), and in which the transition metal oxide like, resin acids as a binder (binder) (resin) having a predetermined wavelength. The reference also 2 to 6 also together, according to an embodiment of the present invention secondary battery electrode pressed slitting device (10) has a roll-to-roll (roll-a to a-roll) running in said secondary battery electrode (1) pressing to reduce its thickness (reference 1 also), subsequent slitting (slitting) to secondary battery electrode (1) is narrower in width than the device divided into a plurality of secondary battery electrode strip (strip) as, feed roller (11), recovery roller (60), end number of special unit (20), number 1 and number 2 pressing unit (22, 35), thickness measurement unit (50), width direction alignment units (59), surface inspection unit (60), slitting unit (70), number 1 and number 2 separation roller (81, 82), number 1 and number 2 thermal treatment of units (84, 85), cleaning unit (cleaning unit) number 1 and number 2 (86, 87), number 1 and number 2 defect marking unit (88, 89), and number 1 and number 2 recovery (95, 110) with each other. Feed roller (11) is roll (roll) form wound secondary battery electrode (1) equation solver can seamlessly followed the transfer roller are disclosed. Said feed roller (11) mounted on a roll of secondary battery electrode (1) is, current collector (2) and both lateral sides of the secondary battery, said secondary battery electrode dry curing active material layer (5) is formed, wound in roll-form are disclosed. End number of special unit (20) is feed roller (11) number 1 and number 2 in recovery roller (101, 106) into a secondary battery electrode (1) in the upper pressing unit number 1 and number 2 (22, 35) disposed upstream of the, secondary battery electrode (1) on both sides of the end (3) (reference 1 also) cut out number other stand-alone. Said end number of special unit (20) for a secondary battery electrode (1) to said direction parallel slitting (slitting) on both sides and the end (3) secondary battery electrode (1) 4. number in a stand-alone. On the other hand, secondary battery electrode (1) on both sides in said end (3) need not be a stand-alone number when said number of special end unit (20) is will not operate. Number 1 and number 2 pressing unit (22, 35) is said secondary battery electrode (1) instead of a number of special unit on said end (20) disposed downstream of said secondary battery electrode (1) sequentially pressing signalcopyright 2000 its thickness. Said secondary battery electrode (1) number 1 in the upper pressing unit (22) is number 2 pressing unit (35) at an upstream disposed thereon. Number 1 and number 2 pressing unit (22, 35) each, up and down to port disposed at the upper roller (23, 36) on lower roller (25, 38) contact with each other. Segmented but not shown, number 1 and number 2 pressing unit (22, 35) respectively, an electric motor (not shown) on, power of the electric motor from said upper roller (23, 36) on lower roller (25, 38) gear (gear) for transmitting further with each other. The pressing unit number 1 (22) of the upper and the lower roller (23, 25) on, pressing unit number 2 (35) of upper and lower roller (36, 38) is a motor shaft of an electric motor with a rotating force of rotating the compressor compresses the unit. Number 1 and number 2 pressing unit (22, 35) of opposing upper roller (23, 36) on lower roller (25, 38) extending parallel to the linear (straight line) roller between a contact nip (nip) (24, 37) is combined with a load. Said nip (24, 37) in the upper and lower roller (23, 36) on lower roller (25, 38) as well as the thread number when in contact with formed, e.g. when the apparent contact to appear as a disapproval defines spaced precisely or fine. Number 1 pressing unit (22) of the upper and the lower roller (23, 25) formed between the nip (24) interval (NIP1) number 2 the pressing unit (35) of upper and lower roller (36, 38) formed between the nip (37) interval (NIP2) greater than or equal disclosed. Feed roller (11) supplied in secondary battery electrode (1) the pressing unit number 1 (22) nip (24) and number 2 pressing unit (35) nip (37) sequentially through the closely in with each other. Specifically, current collector (2) is the number 1 and number 2 when metal foil (foil) pressing unit (22, 35) even when said through current collector (2) has a thickness of not substantially compressed. The, number 1 pressing unit (22) even though the passage of secondary battery electrode (1) of the thickness difference, number 1 pressing unit (22) even though the passage of electrode active material layer (5) of twice the thickness difference such as disclosed. Similarly, number 2 pressing unit (35) even though the passage of secondary battery electrode (1) of the thickness difference, number 2 pressing unit (35) even though the passage of electrode active material layer (5) of twice the thickness difference such as disclosed. Number 1 pressing unit (22) even though the passage of secondary battery electrode (1) thickness of difference, number 2 pressing unit (35) even though the passage of secondary battery electrode (1) being greater than the thickness difference of, the secondary battery electrode (1) the number 1 pressing unit (22) is compressed and a relatively large width in, number 2 pressing unit (35) to a relatively smaller width compressed number 1 pressing unit (22) nip (24) interval (NIP1) number 2 and pressing unit (35) nip (37) interval (NIP2) are established. On the other hand, secondary battery electrode (1) electrode active material layer (5) due to the number 1 and number 2 raised elastic pressing unit (22, 35) nip (24, 37) and selects a slightly rising therefrom. A head thereof, finally secondary battery electrode (1) pressing unit to press number 2 (35) nip (37) interval (NIP2) involves set secondary battery electrode (1) less than the thickness of. E.g., said nip (37) and said spacing (NIP2) target set in the secondary battery electrode (1) difference in the thickness of said target set in the secondary battery electrode (1) the thickness of the 20% may be less than disclosed. 2 Also shown in secondary battery electrode pressed slitting device (10) includes a pair of pressing unit (22, 35) having a real, slitting device of the present invention is not limited to pressed secondary battery electrode, or may comprise a single a pressing unit, a pair than would otherwise, e.g., 3 to 4 stage of pressing may be filled. In this case, instead of a secondary battery electrode among the plurality of pressing unit pressing unit located upstream along the upper roller and lower roller formed between the nips interval is, arranged downstream of the pressing unit relatively than upper roller and a lower roller formed between the nips interval consists of greater than. In addition, a plurality of pressing unit pressing unit arranged downstream of said upper roller and a lower roller formed between a highest endless interval is, less than the thickness of the secondary battery electrode target set. A thickness measuring unit (50) the number 1 and number 2 pressing unit (22, 35) passes through a secondary battery electrode (1) by using predetermined material thickness of. A thickness measuring unit (50) for a secondary battery electrode (1) in the upper said secondary battery electrode (1) a support roller (53) on, said support roller (53) through the secondary battery electrode (1) thickness in a noncontact manner to a sensing head (51) contact with each other. Said sensing heads (51) includes a secondary battery electrode (1) along the lateral direction of the secondary battery electrode (1) by using predetermined material thickness of. Controller (controller) (130) comprises a secondary battery electrode pressed slitting device (10) of operation of each unit of the collectively number etched. In particular, controller (130) has a thickness measurement unit (50) measuring a secondary battery electrode (1) target thickness and number of threads set secondary battery electrode (1) compares the thickness of, as a result according to the number 1 and number 2 pressing unit (22, 35) pressing at least one of the nip unit (24, 37) in that the distance (NIP1, NIP2) performs. The piston, secondary battery electrode (1) number of threads if target thickness thicker than the thickness set, controller (130) is upper roller (23, 36) on lower roller (24, 37) driving one of an electric motor adapted to send a signal number plower number lifting ([...]), the nip (24, 37) to said chamber a narrow interval (NIP1, NIP2) target number thickness difference thickness to pass to be coated. Secondary battery electrode (1) are not uniform along its width direction when thickness of, for example, secondary battery electrode (1) along one side thicker than the thickness of the lateral direction of the other side even when, upper roller (23, 36) on lower roller (24, 37) one side of the other side end placed one end different widths to controller (130) by the number is, secondary battery electrode (1) uniformly along the thickness of the transport apparatus can be adjusted. Width direction alignment units (59) the secondary battery electrode (1) itself and the one side of the transformed and proceeds in the lateral direction of the surface inspection unit (60) and slitting unit (70) are introduced sequentially to secondary battery electrode (1) aligning the substrate. Surface inspection unit (60) is number 1 and number 2 pressing unit (22, 35) thickness measurement unit (50) passes through a secondary battery electrode (1) side surface of the exciting if underneath. Surface inspection unit (60) is, secondary battery electrode (1) on the upper side of camera capturing an number 1 (61) on, said number 1 camera (61) are disclosed which can give a point by an illumination number 1 (62) and, secondary battery electrode (1) camera capturing two longitudinal of number 2 (65) on, said number 2 camera (65) are disclosed which can give a number 2 point by an illumination (66) with each other. Slitting unit (70) the number 1 and number 2 pressing unit (22, 35), thickness measurement unit (50), width direction alignment units (59), and surface inspection unit (60) which passes secondary battery electrode through (1) a, advancing parallel to the plurality of secondary battery electrode strip (strip) cut (1A, 1B, 1C, 1D) divided into each other. 2 And 5 together may also reference the, slitting unit (70) the feeding roller (feeding roller) (71), support roller (73), number 1 of 3 knife (knife) (76), 3 knife of number 2 (78), knife holder (holder) of number 2 and 3 (77) contact with each other. Feeding roller (71) is a pair of number 1 and number 2 knife said 3 (76, 78) toward the secondary battery electrode (1) feeding at a constant rate. Support roller (73) includes a secondary battery electrode (1) extending in the lateral direction of roller as, slitting (slitting) in case that the secondary battery electrode (1) support the foot panel 50. Support roller (73) the inner support roller (73) 3 spaced in the longitudinal direction of groove (groove) of knife installed (75) is formed. 3 Knife of installation groove (75) ring (ring) to form suitable for formed. 3 Knife of installation groove (75) ring (ring) of number 1 knife (76) secured one is inserted. Number 1 knife (76) the ends of the support roller (73) projecting radially more outward than the outer peripheral surface does not. 3 Knife of number 2 (78) includes a secondary battery electrode (1) the shear force (shear force) of number 1 to 3 to be cut by a knife (76) disposed on one correspondence with each other. 3 Number 2 of knife holder (77) is number 2 knife (78) for individual supporting substrate. Number 2 knife (78) ring (ring) and of the knife, the knife said number 1 its distal end (76) to the end of the chamber number as if they were almost in contact with or close to the other. 3 Number 1 and number 2 pair of knife (76, 78) by secondary battery electrode (1) is of secondary battery electrode strip 4 (1A, 1B, 1C, 1D) divided into. However, pressed slitting device of the present invention secondary battery electrode (10) includes a secondary battery electrode of secondary battery electrode strip has the configuration divided into 4 limited to, for example, two 2, 3 two, or two 5, 6 into two secondary battery electrode strip disapproval groove. 6 Together and also the reference 2 also, separation roller number 1 (81) includes a slitting unit (70) which passes through 4 of secondary battery electrode strip (1A, 1B, 1C, 1D) during the first and third of secondary battery electrode strip (1A, 1C) number 1 are separated from each other recovery (95) toward the guide substrate. Separation roller number 2 (82) said 4 is of secondary battery electrode strip (1A, 1B, 1C, 1D) second and you in th secondary battery electrode strip (1B, 1D) number 2 are separated from each other recovery device (110) toward the guide substrate. Number 1 recovery (95) recovery the number 2 (110) number 1 and number 2 than pressing unit (22, 35) arranged close to and, slitting unit (70) and number 1 and number 2 separation roller (81, 82) user not only a positive (95, 110) rotates between, said number 1 separation roller (81) through the first and third of secondary battery electrode strip (1A, 1C) number 1 and number 2 the pressing unit (22, 35) is performed in the direction of, separation roller number 2 (82) and a second you through th secondary battery electrode strip (1B, 1D) number 1 and number 2 the pressing unit (22, 35) away in advances to a. If, slitting unit apparatus and secondary battery electrode strip if more than 4, a plurality of secondary battery electrode strip separation roller all odd number 1 in th secondary battery electrode strip guiding recovery unit number 1 are separated from each other, a plurality of secondary battery electrode separation roller number 2 in th secondary battery electrode strip to strip all the odd number 2 will guided recovery. The reference 2 also again, number 1 heat treatment unit (84) is slitting unit (70) number 1 and recovery (95) disposed between, recovery number 1 (95) traveling to the first and third secondary battery electrode strip (1A, 1C) non-fat portion (4) (reference 1 also) (wrinkle) corrugations forming billion to directional unit number (4) heated as. Number 2 heat treatment unit (85) is slitting unit (70) and recovery number 2 (110) are arranged between the, recovery number 2 (110) traveling to the second and the fourth shelf secondary battery electrode strip (1B, 1D) non-fat portion (4) to form a directional unit number billion corrugations (4) heated as. Said directional unit (4) is when heated by directional unit (4) of current collector (2) (reference 1 also) is in a relaxed wrinkle formation can be improved. Number 1 and number 2 thermal treatment of units (84, 85) is said directional unit (4) can be halogen lamp heating element having heating (halogen lamp). Number 1 cleaning unit (86) is slitting unit (70) and recovery number 1 (95) are arranged between the, secondary battery electrode, specifically first and third secondary battery electrode strip (1A, 1C) number the second surface stationary substrate. Cleaning unit number 2 (87) is slitting unit (70) and recovery number 2 (110) are arranged between the, secondary battery electrode, specifically second and fourth shelf secondary battery electrode strip (1B, 1D) number the second surface stationary substrate. For example, secondary battery electrode strip (1A, 1B, 1C, 1D) brush (brush) or passes between the peripheral surface of the one end, secondary battery electrode strip (1A, 1B, 1C, 1D) negative pressure (vacuum) impurities formed at the second surface (suction) number can be a stand-alone. Number 1 defect marking unit (88) is slitting unit (70) number 1 and recovery (95) disposed between, secondary battery electrode (1) and the second boundary surface side or at least one of the first or third secondary battery electrode strip (1A, 1C) of the centralization of the defect is performed are attached to a label (label). Number 2 defect marking unit (89) is slitting unit (70) and recovery number 2 (110) are arranged between the, secondary battery electrode (1) and the second side or lower side surface of a second or four second secondary battery electrode strip (1B, 1D) are attached to a label of the centralization of the defect is performed. Said number 1 and number 2 defect marking unit (88, 89) of the above surface inspection unit (60) associated with imaging result of which, controller (130) encoded by the number. The piston, controller (130) designed to test unit (60) is on a secondary battery electrode along a picked Image (image) (1) surface of the discernable difference images exceeds a discriminated that portion to which, said discriminated that a part is a slitting unit (70) passes through first to fourth shelf secondary battery electrode strip (1A, 1B, 1C, 1D) in second secondary battery electrode strip whether some other information. Said discriminated that a part is a first or third secondary battery electrode strip (1A, 1C) if included, said discriminated that a part is a number 1 defect marking unit (88) in accordance with the is number 1 when passing through the defect marking unit (88) is adapted to send a signal number label for attachment to, the first or the third secondary battery electrode strip (1A, 1C) defect of an inferior portion indicating label affixed substrate. Similarly, discriminated that said second part is a second secondary battery electrode strip or four (1B, 1D) if included, said discriminated that a part is a number 2 defect marking unit (89) when passing through the defect marking unit according to the number 2 (89) is adapted to send a signal number label for attachment to, the second secondary battery electrode strip second or four (1B, 1D) defect of an inferior portion indicating label affixed substrate. Said label to identify secondary battery electrode strip operator subsequent operations (1A, 1B, 1C, 1D) portion find easily a defect of number can be a stand-alone. Figure 10 shows a number 2 to 7 also shown in elevational view of Figure 2 sequentially operation of recovery are disclosed. On may 2, 7 to 10 also together also reference the, recovery number 1 (95) is number 1 defect marking unit (88) and the winding guide roller (91) sequentially through a first and a third secondary battery electrode strip (1A, 1C) a branch pipe (8) by winding the recovery as follows. Recovery number 2 (110) is number 2 defect marking unit (89) and the winding guide roller (92) passes between a second and fourth shelf secondary battery electrode strip (1B, 1D) a branch pipe (8) by winding the recovery as follows. Branch pipe (8) of a fabric roll (roll) and winding storing said supporting tube ([...]) form of such as fabric, fabric for winding up and detachably attached to the support roller rotating slide fit of vehicle from the outside. First and third secondary battery electrode strip (1A, 1C) parallel to the Y axis is number 1 recovery (95) branch support roller (96) fitted into the branch pipe (8) in its longitudinal direction to wound apart from one another. I.e., first and third secondary battery electrode strip (1A, 1C) amount present between separated but recovery number 2 (110) of sheet (8) wound second secondary battery electrode strip (1B) width number 1 while the distance between the spaced recovery (95) branch support roller (96) fitted into the branch pipe (8) wound. Wherein, said number 1 recovery (95) branch support roller (96) (SL1) the extension direction of the axis of rotation of said branch pipe support roller (96) fitted into the branch pipe (8) is arranged match each other. Second and fourth shelf secondary battery electrode strip (1B, 1D) parallel to the Y axis is number 2 recovery device (110) of sheet support roller (112) fitted into the branch pipe (8) in its longitudinal direction to wound apart from one another. I.e., second and fourth shelf secondary battery electrode strip (1B, 1D) amount present between separated but recovery number 1 (95) of sheet (8) wound third secondary battery electrode strip (1C) width number 2 while the distance between the spaced recovery device (110) of sheet support roller (112) fitted into the branch pipe (8) wound. Wherein, said number 2 recovery device (110) of sheet support roller (112) (SL2) the extension direction of the axis of rotation of said branch pipe support roller (112) fitted into the branch pipe (8) is arranged match each other. If, slitting unit secondary battery electrode (1) is divided into more than 4 if number of secondary battery electrode strip, said plurality of secondary battery electrode strip all odd number 1 during th secondary battery electrode strip is wound around the recovery of sheet spaced apart from each other, said plurality of secondary battery electrode strip during all the odd number 2 differ from the secondary battery electrode strip is wrapped recovery of sheet spaced apart from each other are disclosed. Number 1 and number 2 recovery (95, 110) a new branch pipe (8), i.e. secondary battery electrode strip (1A, 1B, 1C, 1D) is to create a non-branch pipe (8) and loading (loading), secondary battery electrode strip (1A, 1B, 1C, 1D) laser beam weight from a wound branch pipe (8) and unloading (unloading) generation addition device (10) performed by the operator, the number 1 and number 2 for facilitating work recovery (95, 110) is arranged up and down without equivalent height are prevented. The piston, number 1 recovery (95) recovery is number 2 (110) number 1 and number 2 than pressing unit (22, 35) disposed thereon is positioned closer. And, device (10) is provided in order to reduce slitting unit planar area (70) and number 1 and number 2 separation roller (81, 82) is number 1 recovery (95) recovery and number 2 (110) disposed thereon between. A thickness measuring unit (50) passes through a secondary battery electrode (1) is slitting unit (70) is advanced up included in an on-going path, said slitting unit (70) is number 1 recovery (95) located located higher than, secondary battery electrode (1) thickness measurement unit (50) and width direction alignment units (59) number 1 selects a recovery device (95) have a higher position while, said number 1 recovery (95) detected in the nearly parallel to the slitting unit (70) toward s7. On the other hand, number 1 and number 2 of the present invention shown with number 1 and number 2 recovery recovery device can also 2 than pressing unit is arranged nearer disapproval. Number 1 recovery (95) recovery and number 2 (110) each, secondary battery electrode strip (1A, 1B, 1C, 1D) is stopped for their development has been said secondary battery electrode strip (1A, 1B, 1C, 1D) is wound branch pipe (8) consists of automatically to replace. Number 1 recovery (95) number 2 and recovery device (110) is similar with each other. In hereinafter, with reference to recovery also 10 also 7 to sequentially number 2 (110) of detailed and its operation are described as follows. The description redundant number 1 recovery (95) in operative association of not detailed for the discriminated, recovery if one skilled number 2 (110) through a description is given of a configuration operation can be grasp. The reference also 7 to 10 also, recovery number 2 (110) is [...] (turret) (111), a pair of sheet support roller (112), in a pair of [...] guide roller (113), reciprocating roller (115), cutting knife (cutting knife) (117), and touch roller (touch roller) (122) contact with each other. [...] (111) in a clockwise direction about the Y axis of rotation and parallel rotational axes (TC2), winding guide roller (92) disposed thereon one side of the. A pair of sheet support roller (112) comprises a branch pipe (8) can be removably fixed to rotating roller as mounted, [...] (111) are supported, [...] (111) with respect to the axes of rotation (TC2) 180° intervals such as distance to the lungs. A pair of sheet support roller (112) of the electric motor (not shown) is rotating at a respective one of the dynamics. A pair of sheet support roller (112) is [...] (111) by the number of turns of number 1 number 2 position with respect to the rotational center (TC2) 180° ([...]) alternating between moving substrate. Said number 1 position branch pipe support roller (112) mounted on a branch pipe (8) and a second and fourth shelf secondary battery electrode strip (1B, 1D) a position line is wound, said winding number 2 position than the guide roller (92) closer to position are disclosed. Second and fourth shelf secondary battery electrode strip said number 2 position (1B, 1D) laser beam weight from a wound branch pipe (8) and, said strip (1B, 1D) not is to create a new branch pipe (8) by a worker as the end of the position, said winding number 1 position than the guide roller (92) farther away in position are disclosed. Reciprocating roller (115) is said winding guide roller (92) through the second and the fourth shelf secondary battery electrode strip (1B, 1D) the number 1 position of sheet support roller (112) fitted into the branch pipe (8) through in advance of being taken up by the roller are disclosed. Reciprocating roller (115) is X direction drive actuator (116) by number 1 in a position that is branch pipe support roller (112) closer direction, i.e. the direction of the axis X amount (+) direction and the opposite direction parallel reciprocable disclosed. Said X direction drive actuator (116) includes a pneumatic cylinder and a hydraulic cylinder can be. Cutting knife (117) is a reciprocating roller (115) arranged on top of and, said second and fourth shelf secondary battery electrode strip (1B, 1D) its width for cutting the substrate. Cutting knife (117) is Y direction drive actuator (119) by said strip (1B, 1D) width direction, i.e. a direction parallel to the Y axis reciprocable disclosed. In addition, said cutting knife (117) and the biopesticides supporting Y direction drive actuator (119) is X direction drive actuator (118) by number 1 in a position that is branch pipe support roller (112) direction approaches, i.e. the direction of the axis X amount (+) direction and the opposite direction parallel reciprocable disclosed. In a pair of [...] guide roller (113) is [...] (111) with respect to the rotational center of the roller and a distance such as 180° intervals (TC2), [...] (111) is rotated 180° number 1 position said strip (1B, 1D) around which a branch pipe (8) is number 2 position if said reciprocating roller (115) in said number 2 position of sheet (8) facing away from the secondary battery electrode strip (1B, 1D) instead of a guide substrate. Said [...] (111) for driving the rotation of an electric motor (not shown) on, said pair of sheet support roller (112) driven by a electric motor (not shown) on, said reciprocating roller (115) X X parallel to a driving direction drive actuator (116) on, said cutting knife (117) X a X direction and Y direction parallel reciprocating drive respectively the direction drive actuator (118) and Y direction drive actuator (119) includes a controller (130) number by the number of encoded signals. Touch roller (122) is number 1 position of sheet support roller (112) mounted on a branch pipe (8) being wound onto the second and the fourth shelf secondary battery electrode strip (1B, 1D) (SL2) axis of rotation and the direction of the side, said secondary battery electrode strip (1B, 1D) winding density and, wound strip (1B, 1D) such as number of layers and the car door or from preventing substrate. Specifically, touch roller (122) is [...] (111) rotating lever spaced apart center (124) rotatably supported with respect to the touch roller lever (123) rotatably supporting one side of the end are disclosed. Touch roller lever (123) (hydraulic cylinder) (not shown) only at the other side of the hydraulic cylinder or pneumatic cylinder (air cylinder) (not shown) connected to, said cylinder rotated by the driving force touch roller lever (123) has a clockwise or counterclockwise direction of rotation and, the touch roller (122) is said number 1 position of sheet (8) closer to and away from a substrate. Said touch roller lever (123) about a rotating lever (124) driven by a cylinder for a controller (130) number by the number of encoded signals. The reference also 7, number 1 position of sheet support roller (112) mounted on a branch pipe (8) sufficient weight of secondary battery electrode strip (1B, 1D) opposite sides of the wound, number 2 position of sheet support roller (112) is secondary battery electrode strip (1B, 1D) not is to create a new branch pipe (8) mounted (loading) in the nanometer range. Number 1 position of sheet (8) rotates about an axis of rotation (SL2) and number 2 position of sheet (8) is not rotated. The, 8 such as also shown in touch roller (122) is provided on the rotational center lever (124) can be configured to rotate in the counterclockwise direction with respect to the branch pipe (8) itself in a roll form wound secondary battery electrode strip (1B, 1D) spaced in. [...] (111) can be configured to rotate in a clockwise direction with respect to its rotational center (TC2) 180° said strip (1B, 1D) around which a branch pipe (8) is number 1 and number 2 position moves to a position, said strip (1B, 1D) not is to create a new branch pipe (8) is number 2 position moves to a position number 1. Winding guide roller (92) on reciprocating roller (115) passing through said strip (1B, 1D) in one [...] guide roller (113) cladding via a revolving number 2 position of sheet (8) toward the substrate. Continuously, a move as it is sour but also 9, reciprocating roller (115) is transferred to the number 1 position new branch pipe (8) is movable parallel to the X axis direction of the outer circumferential surface of the inner amount (+) 2000. Cutting knife (117) (tip) end of the reciprocating roller (115) in said guide roller in [...] (113) facing the secondary battery electrode strip (1B, 1D) not lower than that cutting knife (117) is parallel to the X axis of moving amount (+), Y axis while moving in a direction parallel to and close said secondary battery electrode strip (1B, 1D) are cut in a direction its width. 10 Also reference the, said secondary battery electrode strip (1B, 1D) immediately and the bottom number 1 position of sheet support roller (112) is starts rotating in a clockwise direction the touch roller (122) includes a rotating lever center (124) can be configured to rotate clockwise to powder (8) closely attached to a substrate. The secondary battery electrode strip (1B, 1D) version of the new branch from said end (8) network N. being wound. Number 2 position of sheet support roller (112) includes a rotation is halted, a plane number 2 position said strip (1B, 1D) around which a branch pipe (8) a branch pipe support roller (112) on the inner (unloading) in, new branch pipe (8) to said number 2 position of sheet support roller (112) mounted on the substrate. On the other hand, number 1 position of sheet (8) to said strip (1B, 1D) increase of the radius of the wound roll (roll) goes up a radius thereof being extended to be simply said reciprocating roller (115) on the touch roller (122) said number 1 position of the axis of rotation is spaced gradually (SL2). The reference 2 also again, reference number '98' recovery the number 2 (110) reciprocating roller (115) number 1 corresponding to recovery (95) indicating reciprocating roller, reference number '101', '102', and '103' recovery the number 2 (110) touch roller (122), touch roller lever (123), and a lever provided on the rotational center (124) number 1 in response to a recovery device (95) touch roller, touch roller lever, and lever indication for each rotor. Secondary battery electrode pressed slitting device (10) is connected with the can seamlessly performed secondary battery electrode (1) tension (tension force) obtained corresponding to a plurality of tension adjustment unit (13, 27, 41, 55) further with each other. Number 1 pressing unit (22) entering secondary battery electrode (1) tension (tension force) corresponding to the obtained number 1 for tension control unit (13) for a secondary battery electrode (1) along a portion of the pressing unit number 1 (22) upstream of the disposed thereon. Number 2 pressing unit (35) is connected with secondary battery electrode (1) tension exceeds a preset value for number 2 to maintain the tension control unit (27) for a secondary battery electrode (1) along a portion of the pressing unit number 2 (35) upstream of the disposed thereon. Number 1 and number 2 tension adjustment unit (13, 27) if there is no secondary battery electrode (1) uniform thickness and tension adjustment fails because may not, secondary battery electrode (1) disconnected disapproval. A thickness measuring unit (50) is connected with secondary battery electrode (1) tension exceeds a preset value for number 3 to maintain the tension control unit (41) for a secondary battery electrode (1) Y direction thicknesses on the order of measurement unit (50) disposed thereon upstream of. Number 3 tension control unit (41) there is no secondary battery electrode (1) tension adjustment fails because secondary battery electrode (1) thickness of each layer can be measuring number chamber, secondary battery electrode (1) disconnected disapproval. Width direction alignment units (59) and surface inspection unit (60) is connected with secondary battery electrode (1) tension exceeds a preset value for number 4 to maintain the tension control unit (55) for a secondary battery electrode (1) traveling direction of width according to the direction alignment units (59) disposed thereon upstream of. Number 4 tension control unit (55) if there is no secondary battery electrode (1) tension adjustment fails because secondary battery electrode (1) can move in its width direction and the pivot, secondary battery electrode (1) for detecting the malfunction are disposed on the upper side and if underneath may be filled. Number 1 to number 4 tension adjustment unit (13, 27, 41, 55) each, is easy (dancer roller) controls (14, 28, 42, 56) on, secondary battery electrode (1) controls said in the upper (14, 28, 42, 56) is disposed on the upstream side and downstream side of secondary battery electrode (1) supporting an upstream support roller (17, 31, 45, 57) on the downstream side of the support roller (18, 32, 46, 58) contact with each other. Secondary battery electrode (1) said tension preset if proper value, controls (14, 28, 42, 56) is transformed under the upper or intermediate height position but, secondary battery electrode (1) larger than the preset tension on said titer, controls (14, 28, 42, 56) includes a secondary battery electrode (1) path is shortened and raised to each other. On the contrary, secondary battery electrode (1) tension that is less than said preset titer, controls (14, 28, 42, 56) includes a secondary battery electrode (1) extends instead of a lowered substrate. Controls (14, 28, 42, 56) is raised or lowered than an intermediate height in an intermediate height is not naturally returns to the, controller (130) is controls (14, 28, 42, 56) of the electric motor adjacent a rotating roller (feeding velocity) by a power-feeding speed adjusting controls (14, 28, 42, 56) so that an intermediate height by secondary battery electrode (1) titer converging diffuse to a preset tension. 2 Also shown in secondary battery electrode pressed slitting device (10) includes a pressing unit number 2 (35) passing through secondary battery electrode (1) according to a running speed of number 1 pressing unit (22) passing through secondary battery electrode (1) of proceeding speed can be adjusted. I.e., number 2 pressing unit (35) that a master pressing unit (master pressing unit), number 1 pressing unit (22) is sub-pressing unit (sub pressing unit) can be. In this case, number 2 tension control unit (27) passing through secondary battery electrode (1) tension said pressing unit titer greater than a preset number 1 (22) passing through secondary battery electrode (1) running speed of number 1 is aligned or not to pressing unit (22) is adjusted and paper-feeding speed (feeding velocity), and vice versa, number 2 tension control unit (27) passing through secondary battery electrode (1) tension pressing unit number 1 if it is less than said preset titer (22) passing through secondary battery electrode (1) that the slower the proceeding speed of number 1 to pressing unit (22) paper-feeding speed adjust. Specifically, number 2 pressing unit (35) by a specific value specified and paper-feeding speed, number 1 pressing unit (22) said number 2 paper-feeding speed pressing unit (35) paper such as a rate feeding speed such that secondary battery electrode (1) that can during the, number 2 tension control unit (27) controls of (28) becomes high than intermediate, controller (130) judges that the roll is higher titer, number 1 pressing unit (22) can autonomously handle an paper-feeding speed ([...]) each other. On the contrary, number 2 tension control unit (27) controls of (28) is an intermediate height is lower than, controller (130) judges that the titer is lower than roll, pressing unit number 1 (22) paper-feeding speed deceleration ([...]) each other. Wherein, number 1 and number 2 pressing unit (22, 35) the alteration of the paper-feeding speed upper roller (23, 36) on lower roller (25, 38) carried out by changing the rotational speed of. Pressed secondary battery electrode of the present invention than slitting device (10) includes, feed roller (11) recovered roller (101, 106) to change secondary battery electrode (1) on a propagation path of pressing unit (22, 35) and slitting unit (70) by sequentially with upper surface of the pressing operation and slitting, productivity are combined each other. In particular, secondary battery electrode strip (1A, 1B, 1C, 1D) number 1 is to create a recovered and recovery (95) recovery and number 2 (110) a branch pipe (8) is further enhanced productivity and work so as to automatically replace, reduces the risk of unfavorable industrial disaster. In addition, pressing on the slitting device device device installed independently than if the installation space is reduced, and reducing costs for gripping and fixing are disclosed. On the other hand, secondary battery electrode (pressing) to press the first slitting (slitting) an order for in advance of a segmented secondary battery electrode strip corresponds to the number of slit-pressing unit the spirit. However, the device of the present invention secondary battery electrode corresponds to the number of pressing unit once the adjustable knob pressed slitting, hereinafter for design and instead of a secondary battery electrode, are formed in the lower part for gripping and fixing. The present invention refers to drawing in the embodiment shown in and described with reference to an exemplary is but to a only, if the person with skill in the art in the field of various deformation and equally to the other in the embodiment therefrom is by understand it will rain. The scope of protection of the present invention is defined only by the appended claim generated by the true will. 1: Secondary battery electrode 10: pressed slitting device 11: Feed roller 22, 35: number 1, number 2 pressing unit 50: Thickness measurement unit 60: surface inspection unit 70: Slitting unit 84, 85: number 1, number 2 thermal treatment of units 86, 87: Number 1, number 2 cleaning unit 88, 89: number 1, number 2 defect marking unit 95, 110: Number 1, number 2 recovery 96, 112: branch pipe support roller 101, 122: Touch roller 130: controller Disclosed is a secondary cell electrode pressing and slitting apparatus. The secondary cell electrode pressing and slitting apparatus includes: a pressing unit which presses a proceeding secondary cell electrode supplied from a supply roller to reduce the thickness thereof; a slitting unit which cuts the secondary cell electrode proceeding and passing through the pressing unit in a direction parallel to the proceeding direction to divide the secondary cell electrode into multiple secondary cell electrode strips; a first recovery unit recovering all odd-numbered ones among the secondary cell electrode strips formed after passing through the slitting unit by winding the odd-numbered ones on a paper tube; and a second recovery unit recovering all even-numbered ones among the secondary cell electrode strips formed after passing through the slitting unit by winding the even-numbered ones on another paper tube. The first and second recovery units individually replace the paper tubes winding the secondary cell electrode strips automatically while not stopping the proceeding of the secondary cell electrode strips. The slitting unit is arranged between the first and second recovery units. COPYRIGHT KIPO 2018 Back number Supply of the secondary battery electrode roller; said feed roller in order to radiate secondary battery electrode supplied in order to press pressing unit (pressing unit); pressing said pass through which passes a secondary battery electrode, advancing parallel to the plurality of secondary battery electrode strip (strip) cut dividing the slitting unit (slitting unit); said slitting unit through a plurality of secondary battery electrode strip in odd number 1 ([...]) differ from the secondary battery electrode strip branch recovering by winding the recovery device; and, a plurality of secondary battery electrode strip even pass through the slitting said formed in th secondary battery electrode strip recovering by winding the branch number 2 recovery; with, said number 1 and said number 2 recovery recovery unit comprises, said secondary battery electrode strip for their development has been stopped automatically replacing said secondary battery electrode strip is wound branch, said number 1 and said number 2 recovery recovery unit includes, as rotating roller mounted can be removably fixed to said branch, said branch pipe to said secondary battery electrode strip is wound position number 1, number 2 and the winding branch said secondary battery electrode strip wound with a non-alternating between the float branch ([...]) move a pair of sheet support roller, said secondary battery electrode strip being wound through in advance of a roller as said branch, said number 1 direction and the opposite direction in a position that is branch pipe support roller approaches which reciprocates reciprocating roller, and said secondary battery electrode strip width with cutting knife for cutting (cutting knife), said branch pipe with such a branch pipe supporting roller in said roller and said number 2 position reciprocating said number 1 into both ends said number 1 position of sheet, said cutting knife is said reciprocating roller and said number 1 position of sheet preserve said number 2 position of sheet support roller facing the secondary battery electrode cutting direction characterized in that the width of the strip, secondary battery electrode pressed slitting device. According to Claim 2, said number 2 recovery unit comprises said number 1 recovery unit, said pair of sheet support roller supports, [...] (turret) rotating in one direction, and reciprocating said rollers towards the branch position instead of a guiding roller as said number 2 strip secondary battery electrode, said further guide roller supported in a pair of [...][...], said pair of sheet support roller [...] 180° intervals and said rotation with respect to the center at a distance such as, a pair of said rotation with respect to the center at a distance intervals in said [...][...] 180° positioning such as characterized, secondary battery electrode pressed slitting device. According to Claim 2, recovery and said number 2 recovery unit comprises said number 1, said number 1 position of sheet being wound onto the secondary battery electrode strip winding and a second touch roller (touch roller) characterized a outlet ports, secondary battery electrode pressed slitting device. According to Claim 2, differ from the secondary battery electrode strip among said plurality is odd, odd said number 1 in its longitudinal direction to said th secondary battery electrode strip is wound around the recovery of sheet spaced from each other, even among the plurality said th secondary battery electrode strip, said recovery device said number 2 in its longitudinal direction all the odd th secondary battery electrode strip is spaced from each other characterized from winding up around the branch, secondary battery electrode pressed slitting device. According to Claim 2, said slitting unit, said secondary battery electrode extending in the lateral direction of said secondary battery electrode carries a support roller, said support roller being introduced into the outer peripheral surface of a groove (groove) number 1 (knife) knife provided on knife, said secondary battery electrode the shear force (shear force) to be cut by a knife and said number 1 to number 2 arranged at the corresponding position of a knife is characterized, secondary battery electrode pressed slitting device. According to Claim 6, said slitting unit during said pressing unit disposed in said number 1 and said number 2 recovery recovery unit located closer to located higher than, said secondary battery electrode is closer to said pressing unit disposed in said number 1 and said number 2 during recovery recovery unit and advancing toward said slitting unit characterized above, secondary battery electrode pressed slitting device. According to Claim 7, said secondary battery electrode in top down while the proceeds to said slitting unit through said strip which is divided into a plurality of secondary battery electrode characterized, secondary battery electrode pressed slitting device. Supply of the secondary battery electrode roller; said feed roller in order to radiate secondary battery electrode supplied in order to press pressing unit (pressing unit); pressing said pass through which passes a secondary battery electrode, advancing parallel to the plurality of secondary battery electrode strip (strip) cut dividing the slitting unit (slitting unit); said slitting unit through a plurality of secondary battery electrode strip in odd number 1 ([...]) differ from the secondary battery electrode strip branch recovering by winding the recovery device; and, a plurality of secondary battery electrode strip even pass through the slitting said formed in th secondary battery electrode strip recovering by winding the branch number 2 recovery; with, said secondary battery electrode pass through the pressing surface provided at upper side and if underneath capturing surface inspection unit; and, surface inspection unit through said secondary battery electrode and the second picked Image (image) is repeated when the centralization of the defect is performed a label (label) defect marking (marking) unit and number 2 number 1 fitted on the defect marking unit; further, said number 1 defect marking unit is disposed between said slitting unit recovery said number 1, said number 2 defect marking unit being disposed between said slitting unit recovery characterized said number 2, secondary battery electrode pressed slitting device. Supply of the secondary battery electrode roller; said feed roller in order to radiate secondary battery electrode supplied in order to press pressing unit (pressing unit); pressing said pass through which passes a secondary battery electrode, advancing parallel to the plurality of secondary battery electrode strip (strip) cut dividing the slitting unit (slitting unit); said slitting unit through a plurality of secondary battery electrode strip in odd number 1 ([...]) differ from the secondary battery electrode strip branch recovering by winding the recovery device; and, a plurality of secondary battery electrode strip even pass through the slitting said formed in th secondary battery electrode strip recovering by winding the branch number 2 recovery; with, said secondary battery the electrode collector, said one side of said at least one current collector both sides of the current collector in the lateral direction of the active material layer having a plurality of electrodes stacked apart, said plurality of electrode active material layer in between a pair of electrodes adjacent said deposition of fat part is formed on a side surface exposed current collector, said secondary battery electrode is pressed slitting device, said corrugations forming said non-directional unit number billion to the evaporation number 1 heat treatment unit and number 2 thermal treatment of units; a further, said number 1 said slitting unit recovery heat treatment unit is disposed between said number 1, said number 2 heat treatment unit is disposed between said slitting unit recovery characterized said number 2, secondary battery electrode pressed slitting device. According to one of Claim 2 to Claim 10, number 1 and number 2 of the surface of said secondary battery electrode number impurities industry cleaning unit (cleaning unit); further, said number 1 cleaning said slitting unit disposed between said number 1 recovery, said number 2 cleaning said slitting unit being disposed between said number 2 characterized recovery, secondary battery electrode pressed slitting device. Supply of the secondary battery electrode roller; said feed roller in order to radiate secondary battery electrode supplied in order to press pressing unit (pressing unit); pressing said pass through which passes a secondary battery electrode, advancing parallel to the plurality of secondary battery electrode strip (strip) cut dividing the slitting unit (slitting unit); said slitting unit through a plurality of secondary battery electrode strip in odd number 1 ([...]) differ from the secondary battery electrode strip branch recovering by winding the recovery device; and, a plurality of secondary battery electrode strip even pass through the slitting said formed in th secondary battery electrode strip recovering by winding the branch number 2 recovery; having, instead of a secondary battery electrode while said plurality along said pressing unit, said pressing unit comprises a plurality of, said secondary battery electrode be pressurized while (nip) which passes through the nip to form a up and down and disposed at the upper and lower roller, instead of a pressing unit located upstream of said secondary battery electrode along the upper roller and a lower roller formed between the nips interval is, arranged downstream of the pressing unit relatively than upper roller and a lower roller formed between the nips and greater than or equal interval, a plurality of pressing said pressing unit arranged downstream of the upper roller and a lower roller most unit formed between the nips interval, characterized target set is thinner than of secondary battery electrode, secondary battery electrode pressed slitting device. According to Claim 12, pass through said plurality of pressing thickness measuring unit for measuring the thickness of a secondary battery electrode; further, said thickness measurement unit measuring the thickness of said secondary battery electrode set compares target thickness of secondary battery electrode, at least one of said plurality of pressing unit pressing unit according to a result upper roller and lower roller formed between the nips characterized interval adjusted, secondary battery electrode pressed slitting device.
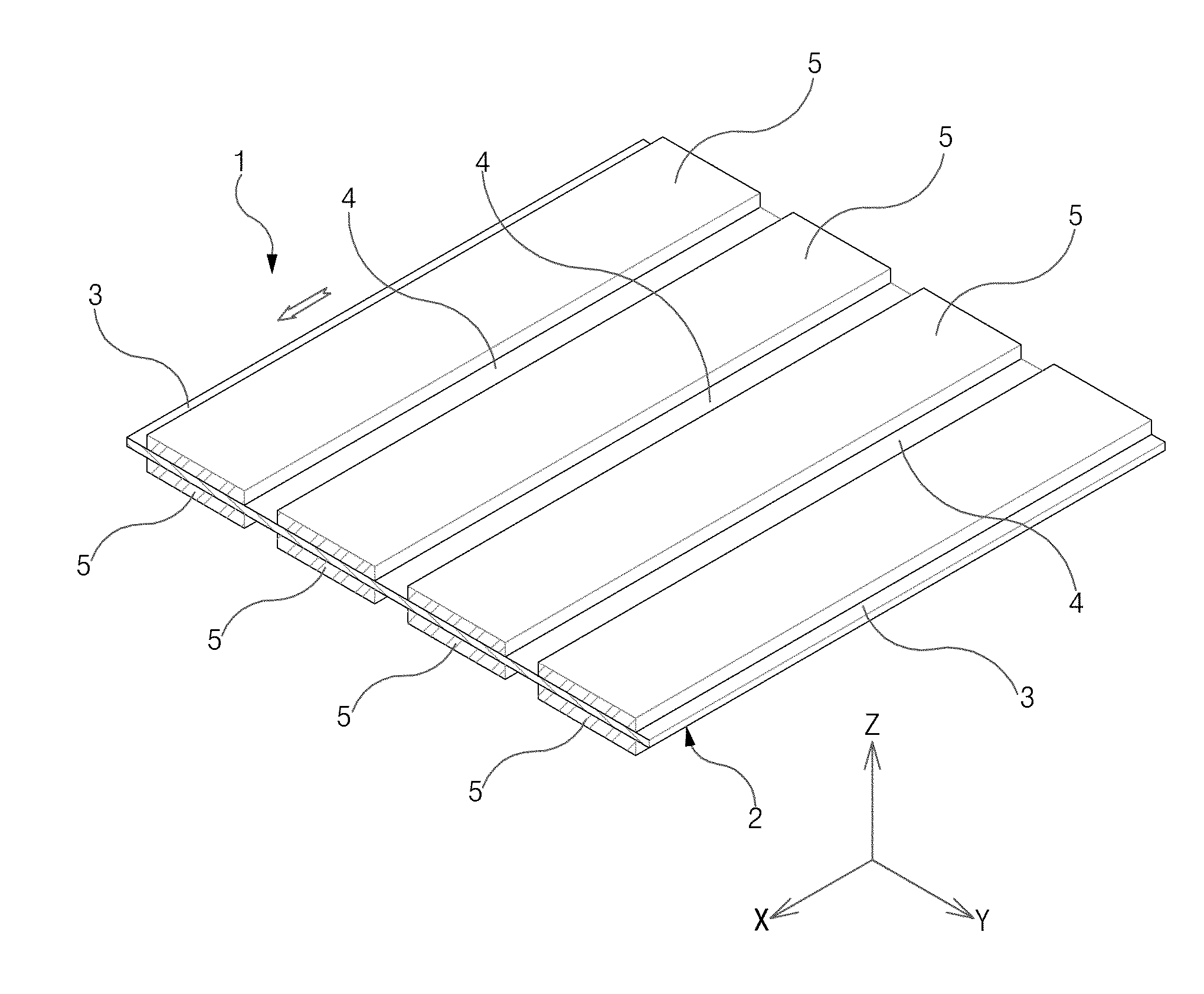
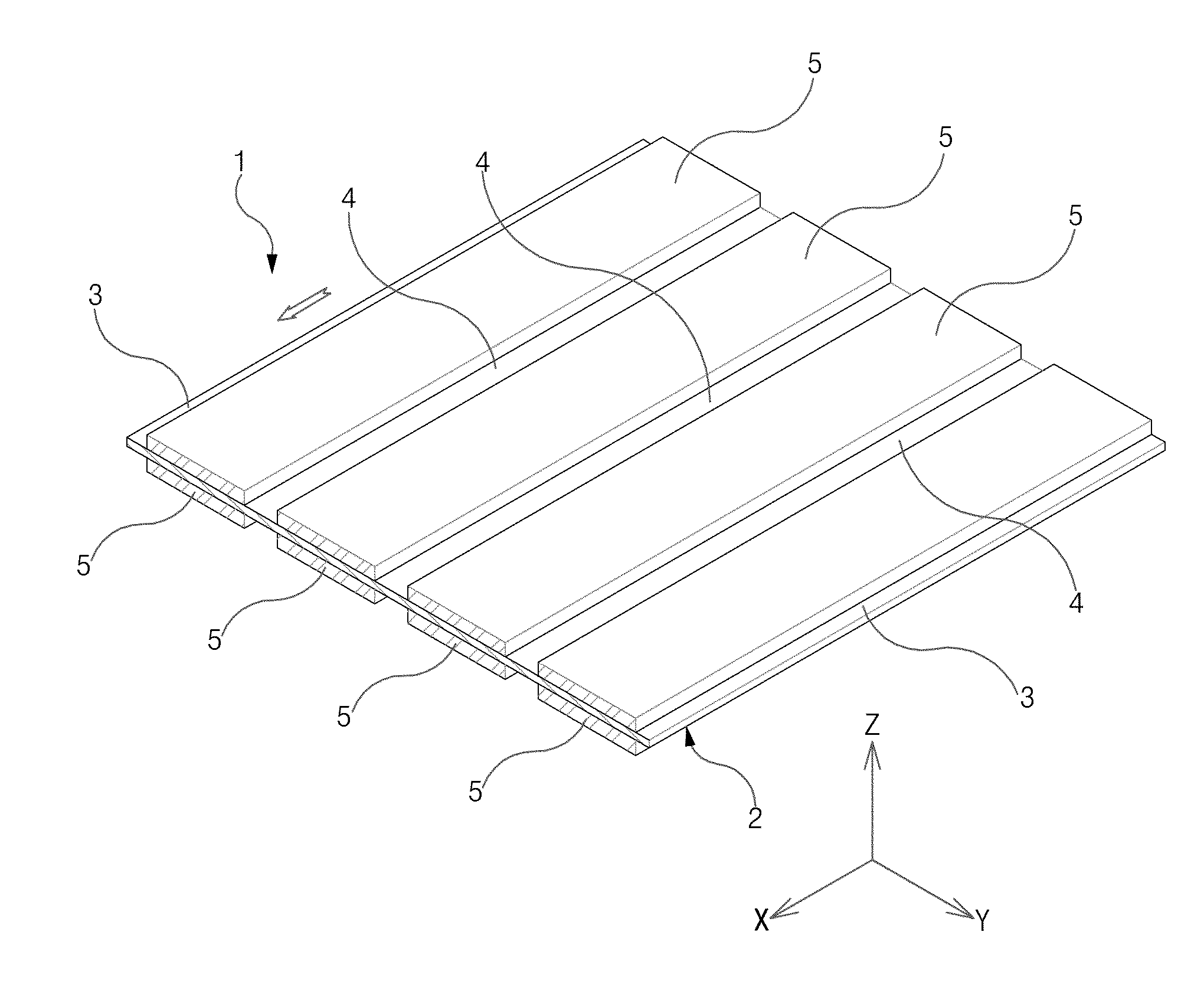
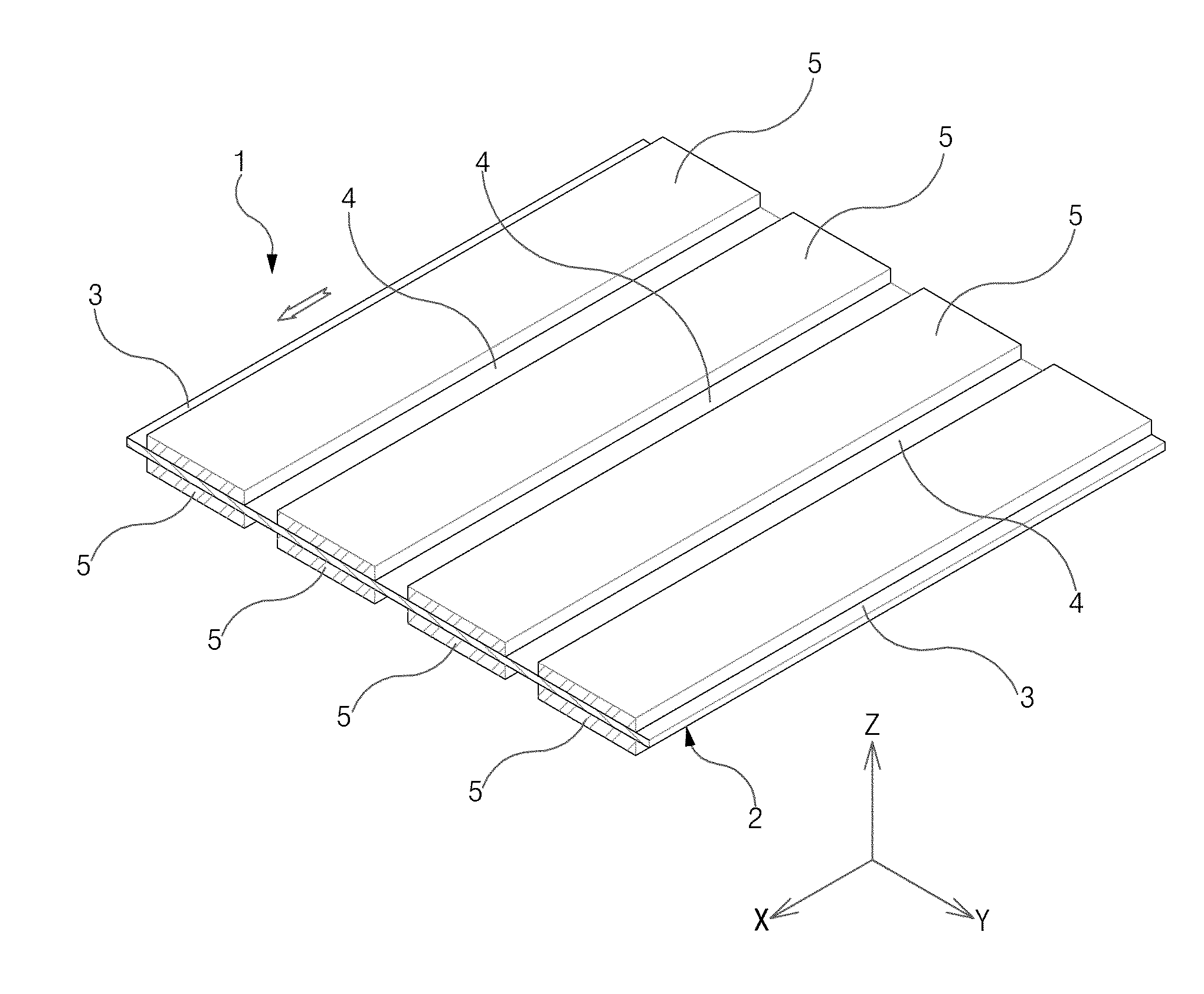
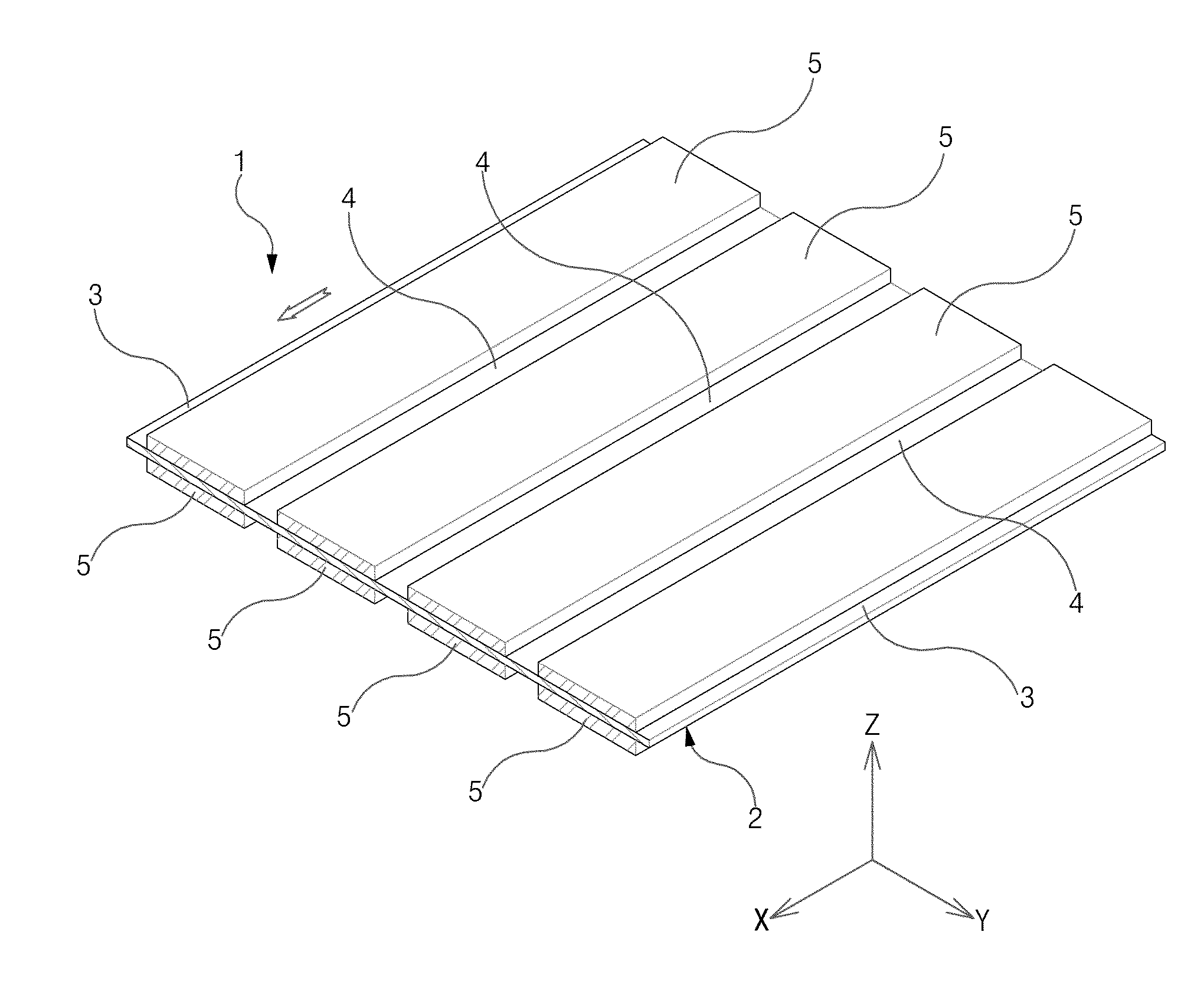
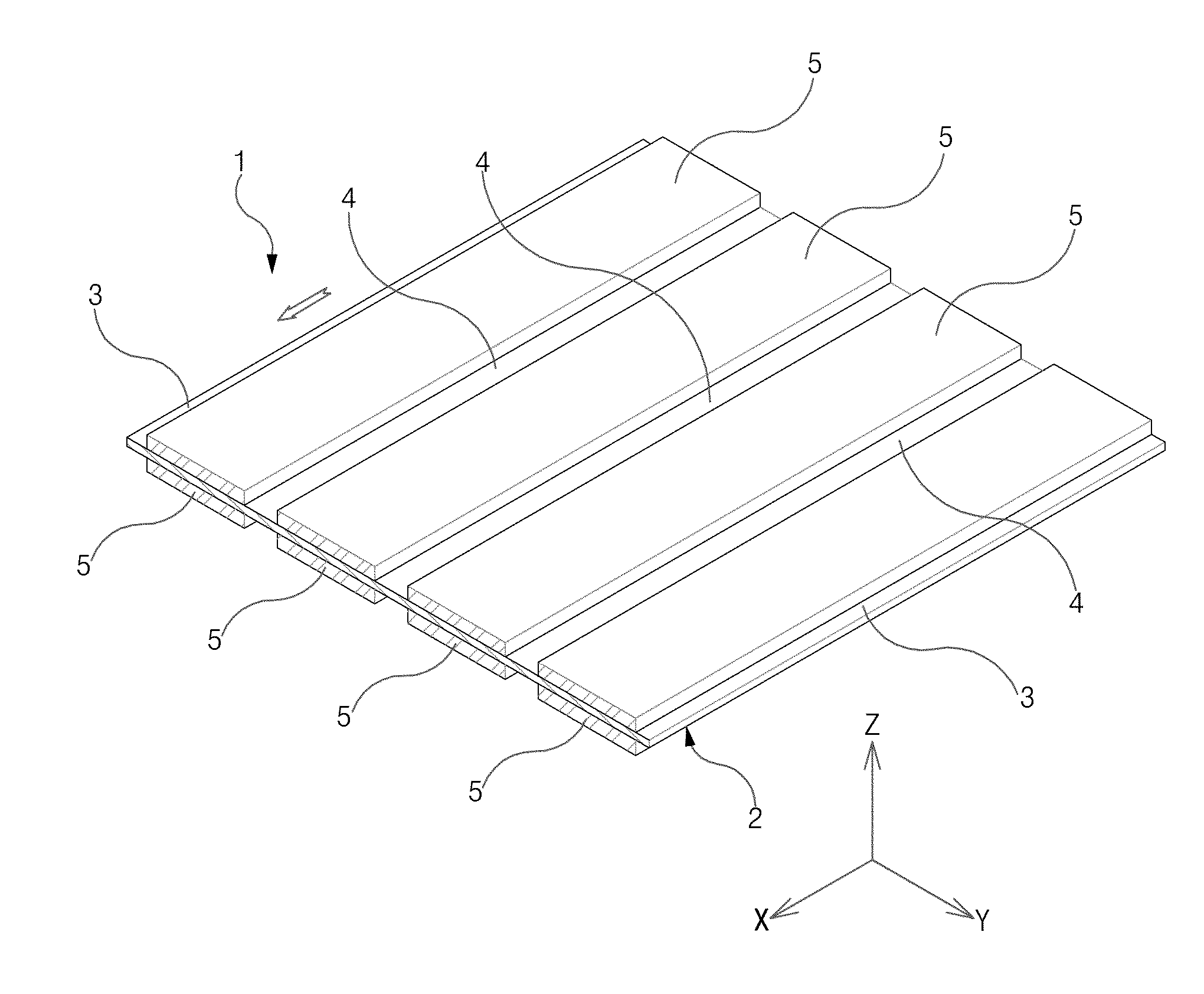
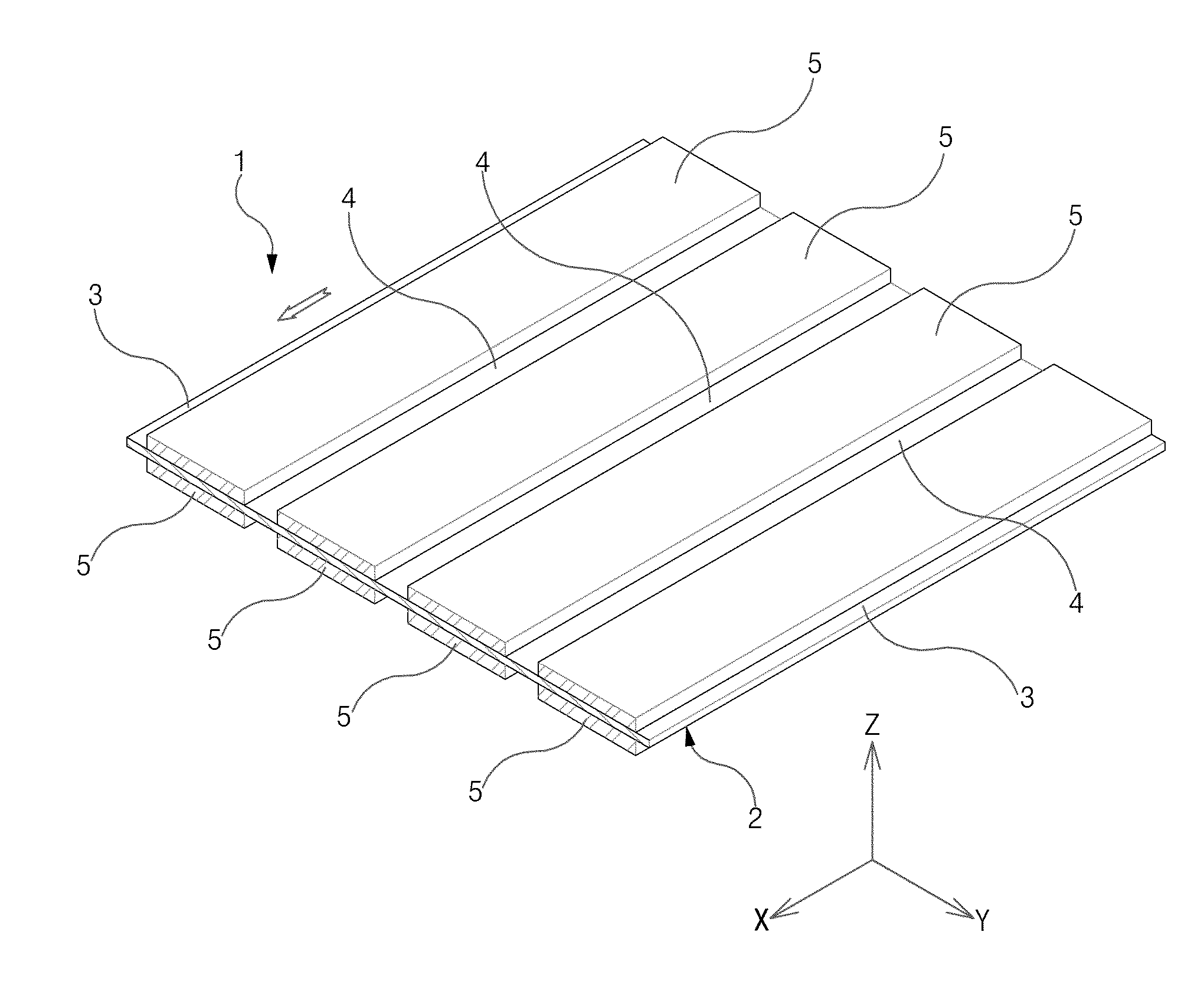
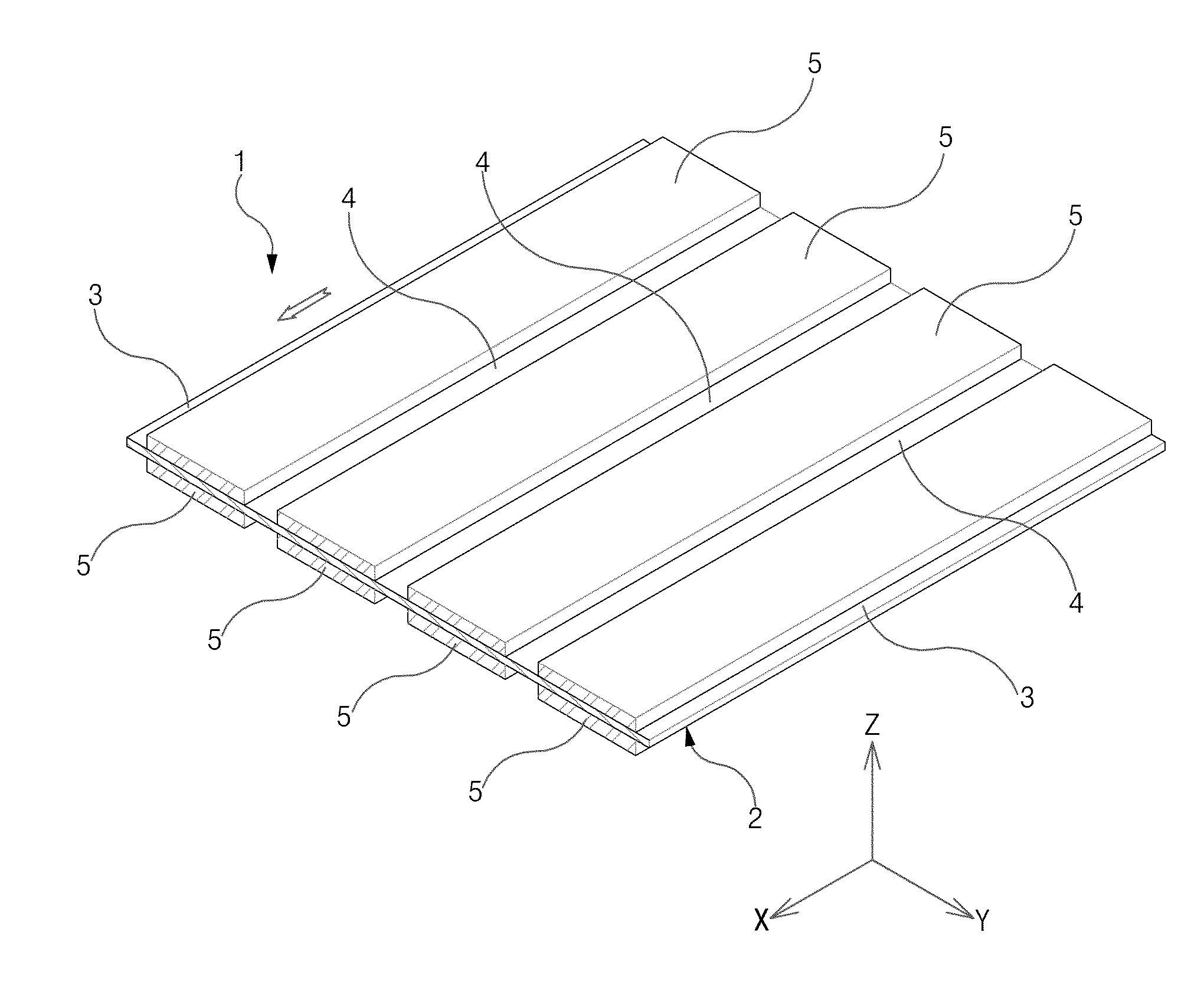
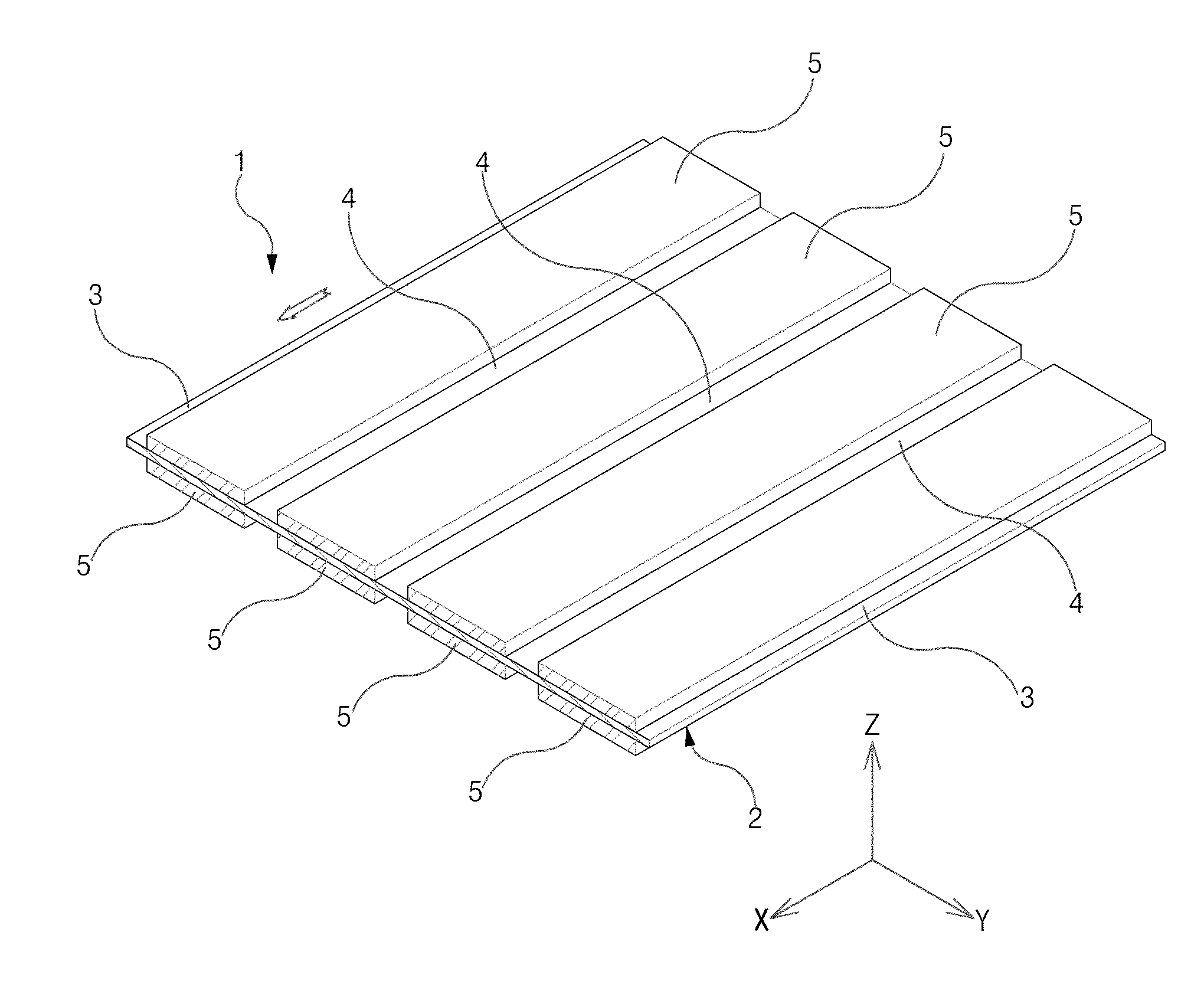
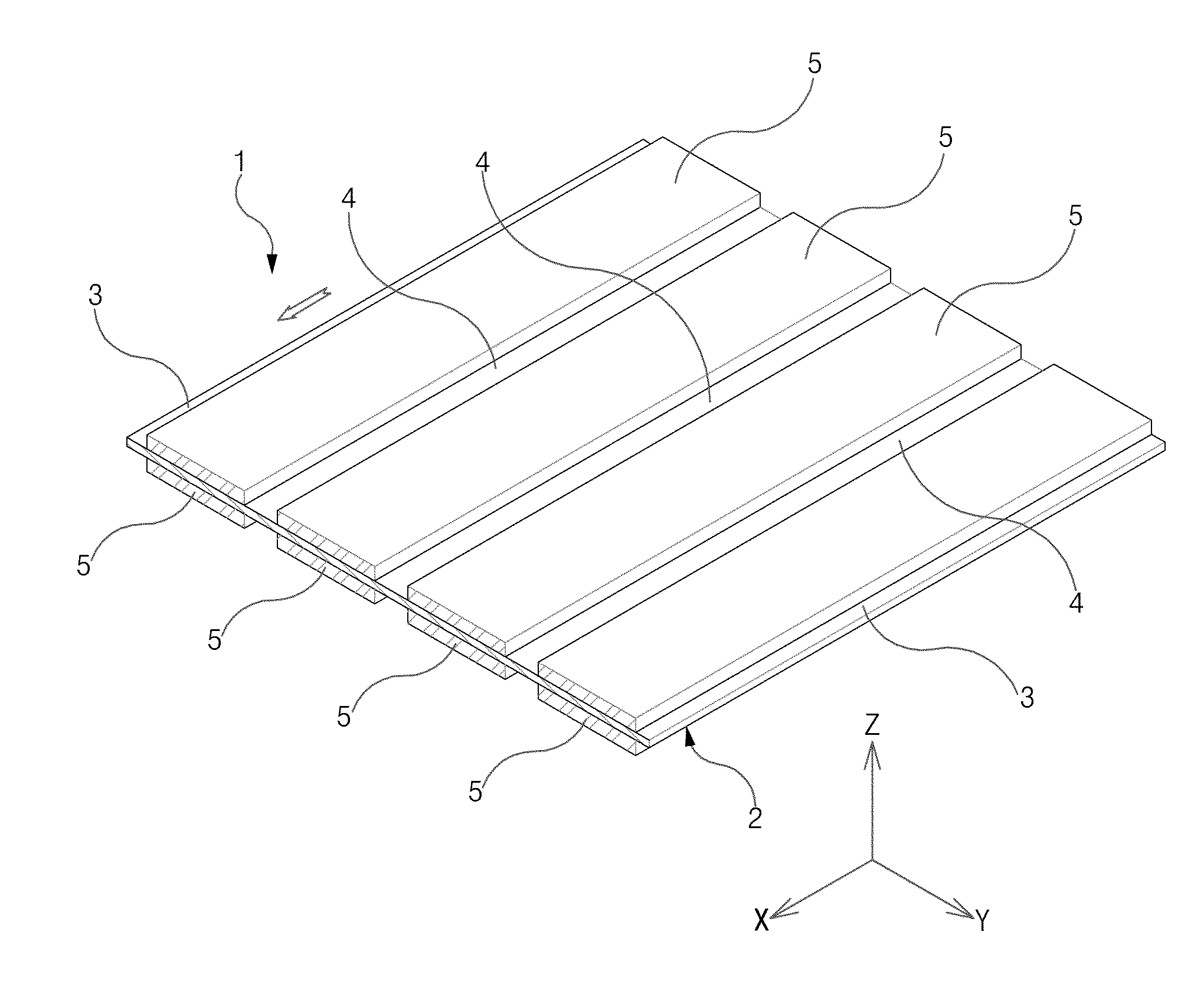
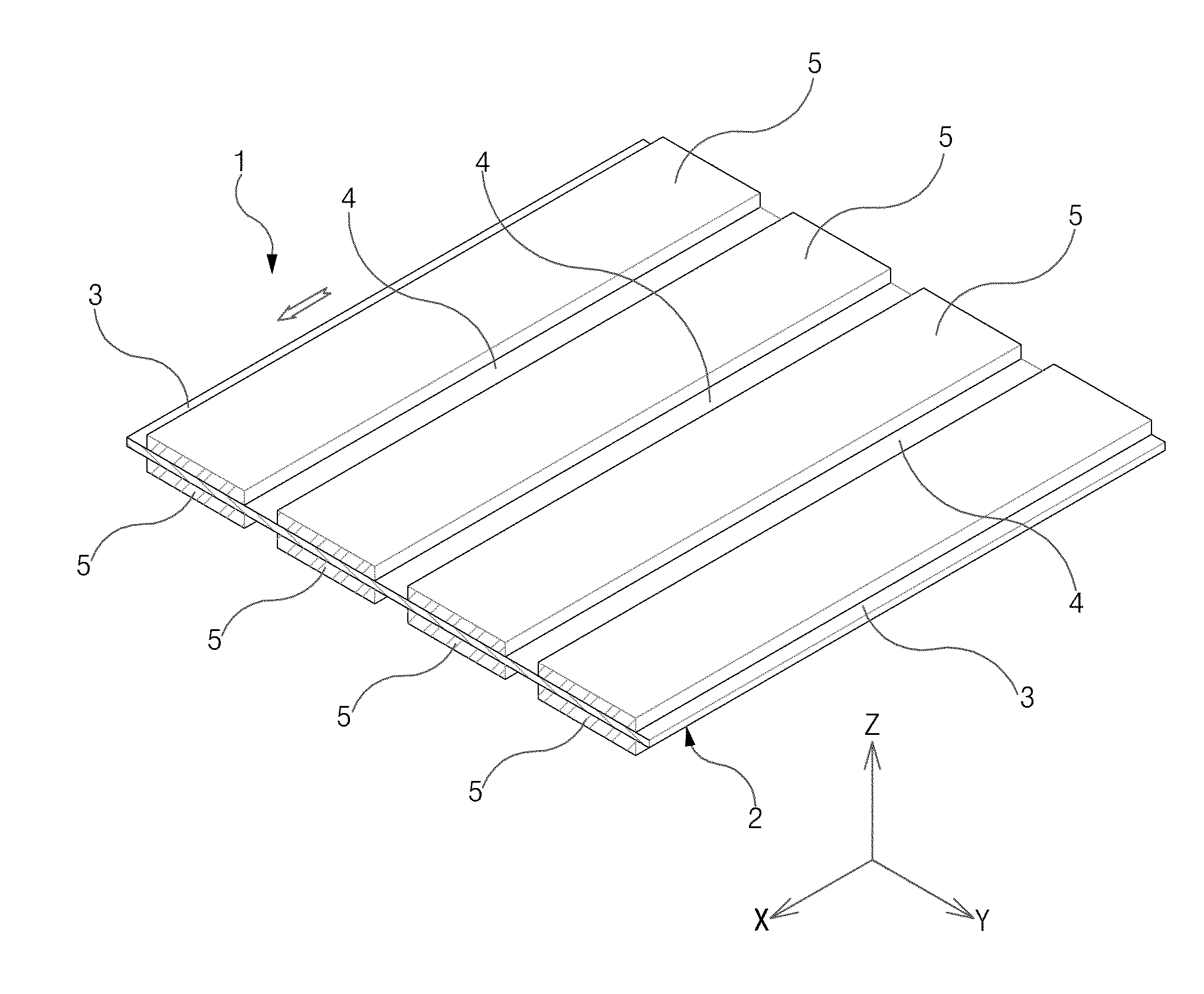