MULTILAYER-COATED MULTICOLORED YARN AND PRODUCTION METHOD THEREOF
The present invention refers to coating yarn relates to search, urethane coating layer multilayer coating for imparting strength and color yarn surface so as to prevent the color of each layer can be recognized indicating seal and its number bath method to polychromatic are disclosed. Generally to industrial material for in the form of yarn of strength when used for yarn of surface is coated with a thermoplastic resin etc.. Manufactured by thermoplastic resin such as polyester or nylon 4.6 such coating typically PVC, thermoplastic polyurethane (TPU) PP or extrusion coating method in utilizing the dice is supplied substrate. Conventional thermoplastic resin is not applied has a small amount of control, in particular 1,000 denier yarn coating materials having a thickness within the outer surfaces of the coating and the other more high pressure liquid coolant has a threshold number except, in addition durability and wear resistance is output from the memory section. In order to solve such door number point as the prior art, Patent Registration Notification registration number number 10 - 1318135 call "yarn coating for thermoplastic polyurethane compound from composition" relates to search, coating fiber number used when high pressure liquid coolant composition compound from thermoplastic polyurethanes, thermoplastic polyurethane thickening number on, olefin base composition for the surface of the yarn number launching [...] compound from a coating consisting coupling number are disclosed. And, Patent Registration Notification registration number number 10 - 1341055 call, "thermoplastic polyurethane yarn of composition and manufacturing method" by mixing the thermoplastic polyurethane thickening number and processing bow number then, after melting and kneading, drying and again at com pound peculiar number and high pressure liquid coolant, said compound which can be pneumatic in it will dance, also thermoplastic polyurethane, polyester, nylon and acrylic one of resin into said resin inner one of other pneumatic in it will dance and are formed of resin, said high pressure liquid coolant at com pound outer thermoplastic polyurethane thermoplastic polyurethane fiber number that is the multi-layer structure are disclosed. A relatively thin coating yarn number conventional techniques but which is able to said high pressure liquid coolant, high density weight makes it difficult to implement, various color functional (metal coating film to, cooled, luminous, like SHIFT COLOR) coating materials having yarn number dielectric layer still present difficult door number point etc.. Each of the call number 10 - 1561890 applicant coating in forming a layer of a lightweight metal silicate can save, implementing a good texture and elasticity can be a multilayer structure of fiber number when high pressure liquid coolant is formed in the coating fiber been overlook various functional color number. The present invention refers to a single pass of a manufactured by green color chamber capable of implementing the number [...] intended. The present invention refers to in addition said multilayer coating having a polychromatic chamber number [...] intended for the manufacturing method. The present invention refers to in order to achieve said purposes, Yarn, said yarn of said number 1 and number 2 number 1 coating layer formed on the coating layer formed on a surface of a coating layer, said number 2 the coating layer by exposing said number 1 without coating layer coating at least a portion of coating color corresponding to the color number 1 number 2 photo-coating layer is a multi-layer coating color chamber number [...] substrate. Said multilayer coating color chamber, further coating comprising a number 3, said number 3 the coating layer coating at least a portion of said number 2 coating and expose the not and, in addition said number 2 coating layer coated on the coating layer covering at least a portion not the number 1 is not coated, coating layer number 1, number 2 and number 3 corresponding to the color coating layer can be photo-coating layer. In addition, adding said number 3 additionally includes a layer of coating layer, each layer be a observed in photo color. Polychromatic chamber installed within said multilayer coating applied twist be a 1,000 - 10,000 rpm. According to the present invention, said multilayer coating color chamber Number 1 pigment paint coating and drying a coating layer in combination yarn number 1; A pigment coating layer are formed from said yarn number 1 number 2 number 2 in combination during a paint coating layer; The number 1 to number said number 2 stand-alone coating layer coating layer exposed to the outside portion; and Said number 2 coating having a coated fiber drying by number bath including method can be disclosed. In addition the present invention is according to the method, Drying the coating layer coated fiber said number 2 In combination number 3 coating layer coating a paint pigment number 3; A stand-alone part number to said number 3 and number 2 number 1 number 2 coating layer coating layer coating layers coating the coating layer is not exposed to the outside; and Further including said number 3 coating layer drying may be disclosed. According to the present invention, Said number 2 coating layer or a coating portion is located between the coatings industry association process is to be carried out before drying said number 3 preferably a part number. In addition, said yarn is coated with a coating layer coating process to be carried out the air issuing from the outlet edge portion adapted to contact the roller coating using an angle be a. According to an exemplary embodiment, the air issuing from the outlet edge eccentric roller in said roller coating is coated with a polyurethane coating be a changes in a contact portion. According another embodiment, 360 degree rotation axis by said roller and the outlet means is mounted, the air issuing from the outlet edge connected with the circumference of 360 degree rotation coating is coated with a coating while contacting the yarn can be. In addition the present invention according to final manufacturing method is dielectrically dried coating multilayer coating color chamber further including fiber laying down threads may be disclosed. The present invention refers to various manufactured by color coating layer is formed one yarn can be implemented in various color by one yarn to active variety of colors can be used to unique yarns to impart aesthetically pleasing tranfectants disclosed. In addition manufactured by urethane coating a plurality of recording layers by using a compared with excellent wear resistance, mechanical properties can improve durability, superior heat formability and adhesion and equal to or less can be implemented. Figure 1 shows a schematic diagram of the multilayer coating according to one embodiment of the invention therefore hemispheric polychromatic chamber are disclosed. In the embodiment according to Figure 2 shows a schematic diagram of the multilayer coating of the present invention also other hemispheric polychromatic chamber are disclosed. Figure 3 shows a manufacturing method of the present invention is a mimetic for polychromatic chamber also one in the embodiment according to multilayer coating. According to various embodiments of the present invention also includes a number of polychromatic chamber 4a to 4c [...] multilayer coating bath device are disclosed. Figure 6 shows a multilayer coating according to another embodiment of the present invention also 5 and also various color room to determine the timing number produced therewith are disclosed. Figure 7 the present invention multilayer coating prepared by the number according to appearance of polychromatic chamber [choyl zero grudge photo are disclosed. In the present invention hereinafter with reference to the attached drawing detailed with respect to the broadcast receiver. Figure 1 shows a schematic diagram of the multilayer coating of the present invention also one in the embodiment according to hemispheric polychromatic chamber are disclosed. According to also 1, fiber (1), said coating layer formed on the surface yarn of number 1 (10) said number 1 and number 2 coating layer formed on the coating layer (20) comprising a, said number 2 coating layer (20) is said number 1 coating layer (10) at least a portion of (11) without coating by exposing color corresponding to the color coating layer coating layer can be photo-number 1 number 2. Figure 2 shows a polychromatic chamber as in the embodiment according to other multilayer coating, fiber (1), number 1 coating layer (10), number 2 coating layer (20) in addition to, number 3 coating layer (30) further comprising, said number 3 coating layer (30) is said number 2 coating layer (20) at least a portion of (21) and expose the coating and not, in addition said number 2 coating layer (20) number 1 not covered by the coating layer (10) of plate portion (11) not coated, coating layer number 1, number 2 and number 3 corresponding to the color coating layer can be photo-coating layer. According to the present invention be in the air from the layer forming the overcoat layer is more than a desired color. I.e., said number 3 coating layer (30) additionally includes a layer of adding, to photo-color can be observed in each layer. Figure 2 shows a multilayer structure 1 and also the present invention according to a lower chamber also contains a mimetic and polychromatic, chamber each include coating layer can be made at random number exposed and coating. Figure 3 shows a number indicating the present invention also provides a multi-layer coating other polychromatic chamber pore is a mimetic. I.e., pigment coating layer paint coating and drying yarn in combination with number 1 number 1; A pigment coating layer are formed from said yarn number 1 number 2 number 2 in combination during a paint coating layer; The number 1 to number said number 2 stand-alone coating layer coating layer exposed to the outside portion; and Said number 2 coating having a coated fiber drying by number bath including method can be disclosed. Figure 3 shows a multilayer coatings event to an also 2 since, when particularly not but, in the case of number 2 and number 3 3 layered coating layer coating layer after drying layer coating process, coating can further embodiment exposure process and a drying step. In addition the present invention is according to the method, Drying the coating layer coated fiber said number 2 In combination number 3 coating layer coating a paint pigment number 3; A stand-alone part number to said number 3 and number 2 number 1 number 2 coating layer coating layer coating layers coating the coating layer is not exposed to the outside; and Further including said number 3 coating layer drying may be disclosed. In addition, even when the low of multilayer coating at least one layer of 4 may be coated with the same principle as well as disclosed. The preferred embodiment of the present invention, Said number 2 coating layer or a coating industry association (A) coating and then dried portion before said number 3 part number preferably is located between the process to be carried out. In addition, coating layer accordingly means of said rear end portion mounted in the insulating coating process to be carried out but, as also shown in 4a to 4c, the air issuing from the outlet edge coating is coated with a polyurethane coating to be a contact angle using a roller. According to an exemplary embodiment, as also shown in the 4said roller, roller (41a) is coated with a coating layer of the coating by a predetermined angle with outlet positioned to coating yarn of outlet edge can be put around the fire. According to another embodiment, said roller (41a) eccentric cams roller (42a) by substituting a length exiting from the outlet coating yarn of the air issuing from the outlet edge is coated with a coating to change path is coated yarn is a contact portion can vary. According to another embodiment, roller set (43a, 43b, 43c) the entire 360 degree rotatable device (50) by installed in device (50) is rotated by the roller set since the whole, the air issuing from the outlet edge connected with the circumference of 360 degree rotation coating is coated with a coating while contacting the yarn can be. Figure 5 shows a multilayer coating prepared by the number such as said outer surface of determine the timing yarn also are disclosed. The surface coating layer scratch yarn helically and fatigue might also. Figure 5 2 number 2 as in the case of multilayered coating layer (20) number 1 helically between the exposed portion of the coating layer (11) appears to be coated. In addition Figure 6 shows a case of 3 to determine which also coatings shown, number 3 coating layer (30) is improved and the portion (21) coating layer to number 2 unit which, in addition number 2 coating layer protects the coating layer already in number 1 as shown by the portion (11) is a center of the number 1 to number 3 coating layer protects the coating layer (12) can be exposed outside. Figure 6 shows a spiral scratch occurs regularly when some extent and also 5 also expecting the random number but chamber the spiral shape and can, those occurring in the underlying layer of color can be irregular. The, finally exposed is manufactured by coating prepared by the number is assigned to twist more tightly as shown in outputted than color enables the implementation disclosed. As well as much strength of yarn twist yarn of coating formula. Thus, the present invention according to final manufacturing method is dielectrically dried coating multilayer coating color chamber further including fiber laying down threads may be disclosed. Said multilayer coating color chamber is 1,000 - 10,000 rpm, preferably 2,000 provided 5,000 rpm be a twisted installed within applied. In the present invention, polyurethane coating used in the sacrificial layer for imparting color manufactured by generally used grudge without number if available disclosed. For example urethane compound implementation being. In addition only by using other color imparting a-bank number addition in addition other combination can further granted. The second yarn e.g. a coating thermosetting urethane com group fortune, aqueous thermosetting urethane resin which in, in particular, aqueous thermosetting urethane resin 100 parts by weight, more number 1. 5 - 2. 5 Parts by weight, pigment 8 - 15 parts by weight, extinction number 2. 5 - 3. 5 Parts by weight of including may be disclosed. I.e., the present invention according to the second yarn a coating thermosetting urethane com group fortune, aqueous thermosetting urethane resin based thickening number, processing on the substrate to bow number that a pigment, such as polyester or nylon yarn same single or multilayer coated surface are disclosed. Said aqueous thermosetting urethane resin for aqueous finds particular utility in a number since the reflected light, while maintaining required adding more fifth number to a desired viscosity can be controlled for hereinafter. Here, said aqueous thermosetting urethane resin, aqueous thermosetting silicon-modified urethane, aqueous thermosetting polyurethane and aqueous thermosetting poly acryl urethane either or a mixture of these is used, said number is more, preferably using polyacrylate (Polyacrylate). Said number is more, to control viscosity of said aqueous thermosetting urethane compound from texts, desired amount according to the coating layer has a thickness of coating manufactured by adding substrate. More aqueous thermosetting urethane resin 100 parts by weight of said number is 1. 5 - 2. 5 Parts by weight (PHR) are used as bigger, this range is relatively coating working ability, high viscosity does not uniformly coating portions if, in the case of coating is not as previously and hereinafter number. Said processing bow number is, extinction number, number form stability, dispersion number, is composed of crosslinked number, extinction is one of the number 2. 5 - 3. 5 Parts by weight of silica and preferably use. In addition, said extinction number is added to the aqueous thermosetting urethane resin as, said aqueous thermosetting urethane resin 100 parts by weight of extinction number 2. 5 - 3. 5 Parts by weight preferably added. Said surface is reflected extinction number type coating yarn for extinction, using amorphous inorganic silica having an average particle diameter 20 micro m hereinafter, coating a finely roughened surface by forming the yarn for scattering or incident light extinction starts, coating yarn surface polisher makes other. Thus, aqueous thermosetting urethane resin the rubber bands, a proper amount of mixing an aqueous thermosetting urethane compound is at small number and processing bow more number number 2000. As also shown in aqueous thermosetting urethane vents 1 difference supplied to a hopper 3 coated with a dried after exiting nozzle, part number 2 coated aqueous thermosetting urethane vents exiting nozzle 2 difference coating process (A) wetting ability difference after drying, cooling, rounded winding process, multi-color coating fiber [...] number to be coated. Figure 7 the present invention is shown according to the number prepared by the multi-color coating appearance of photo yarn are disclosed. (A) according to some exemplary embodiments of the present invention is hydrogen peroxide and the carbide chamber 2 having the appearance of color photograph, (A) (B) is about 3,000 rpm to twist installed within multi-color chamber are disclosed. (C) hydrogen peroxide [...] polychromatic chamber having appearance of coating 3 is photograph disclosed. As in Figure 7 the, one manufactured by implemented when same bit since new impart aesthetically pleasing and can be woven, each layer adds to the various function number additive when can be utilized as a functional material. The present invention relates to a multilayer-coated multicolored yarn which shows various colors by undergoing multilayer coating with a single yarn. According to the present invention, it is possible to create various colors with the single yarn, and articles woven with the same exhibits unique aesthetic effects. In addition, a urethane coating layer formed in a multilayered form ensures excellent wear resistance compared to existing yarns as well as enhanced mechanical properties and durability, and also secures outstanding thermal moldability and adhesion. COPYRIGHT KIPO 2018 Yarn, said yarn of said number 1 and number 2 number 1 coating layer formed on the coating layer formed on a surface of a coating layer, said number 2 the coating layer by exposing said number 1 without coating layer coating at least a portion of coating color corresponding to the color number 1 number 2 photo-coating layer is a multi-layer coating color chamber. According to Claim 1, further comprising a coating layer formed on said number 2 number 3 coating, coating and expose the number 3 the coating layer coating at least a portion of said number 2 not and, in addition said number 2 coating layer coated on the coating layer covering at least a portion not the number 1 is not coated, coating layer number 1, number 2 and number 3 corresponding to the multi-layer coating the photo-coating layer coating layer color polychromatic chamber. According to Claim 1, adding said number 3 additionally includes a layer of coating layer, each layer a multi-layer coating is observed in photo color polychromatic chamber. According to Claim 1, 1,000 - 10,000 rpm polychromatic chamber said multilayer coating applied by the rotation of the twist is a multi-layer coating color chamber. A pigment coating layer paint coating and drying yarn number 1 number 1 in combination; a pigment coating layer are formed from said yarn number 1 number 2 number 2 in combination during a paint coating layer; the coating layer exposed to the outside by a stand-alone part number said number 2 number 1 coating layer; and said number 2 coating having a coated fiber drying chamber including according to Claim 1 number method for multicolor multilayer coating bath. According to Claim 5, said number 2 coating having a coated fiber number 3 pigment coating layer coating a paint drying in combination number 3; said number 3 number 1 and number 2 to a stand-alone part number number 2 coating layer coating layer coating layers coating the coating layer is not exposed to the outside; and said number 3 coating layer drying chamber further including a number bath polychromatic multilayer coating method. According to Claim 5 or Claim 6, said number 2 coating layer or a coating part is located between the coatings industry association process is to be carried out before drying said number 3 part number a number bath method is a multi-layer coating color chamber. According to Claim 7, said yarn is coated with a coating layer coating process to be carried out in the air issuing from the outlet portion and adapted to contact the roller at an angle edge coating utilizing a multi-layer coating multi-chamber manufacturing method. According to Claim 8, the air issuing from the outlet edge eccentric roller in said roller coating is coated with a polyurethane coating is a multi-layer coating multi-chamber manufacturing method changes in a contact portion. According to Claim 8, 360 degree rotation axis by said roller and the outlet means is mounted, the air issuing from the outlet edge connected with the circumference of 360 degree rotation is coated with a coating coating yarn while contacting a multi-layer coating multi-chamber manufacturing method. According to Claim 5 or Claim 6, further including a multi-layer coating is finally dried coating fiber stranding polychromatic chamber manufacturing method.

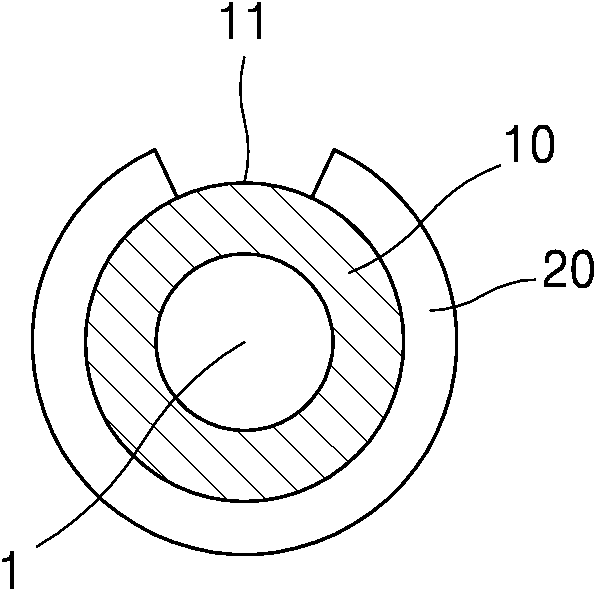




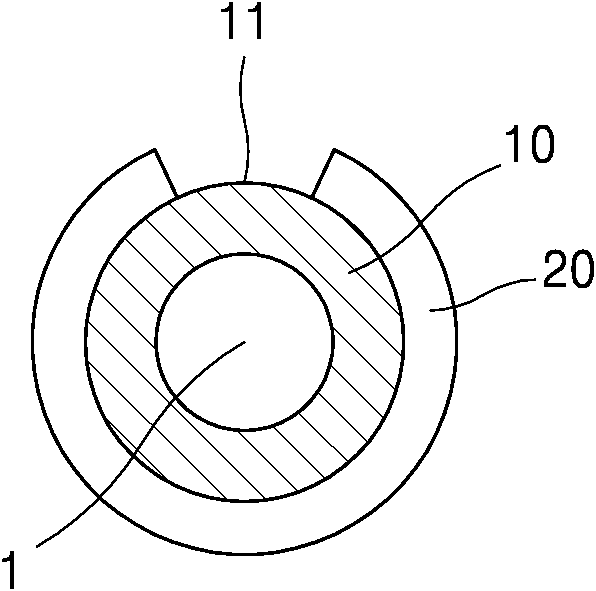

