Articles spray coated with non-melting polymer
[0001] This application claims the benefit of U.S. Provisional Application No. 60/340,155, filed Dec. 14, 2001. [0002] Cross reference is made to Application No. 60/340,420, entitled “High Velocity Oxygen Fuel (HVOF) Method for Spray Coating Non-Melting Polymers” having been concurrently filed provisionally with the present application and is herein incorporated by reference. [0003] The present invention relates to coating surfaces using non-melting polymers. More particularly, the present invention relates to an article that is spray coated with at least one non-melting polymer preferably using a high velocity oxygen fuel (HVOF). [0004] The following disclosures may be relevant to various aspects of the present invention and may be briefly summarized as follows: [0005] High Velocity Oxygen Fuel (HVOF) processes have historically been used to spray coat metallic and ceramic materials. The spray coat process has used materials that are at least partially meltable or heat softenable such that they could be spray coated. For example, U.S. Pat. No. 5,285,967 to Weidman discloses a high velocity, oxygen fuel (HVOF) thermal spray gun for spraying a melted powder composition of, for example, thermoplastic compounds, thermoplastic/metallic composites, or thermoplastic/ceramic composites onto a substrate to form a coating thereon. The gun includes an HVOF flame generator for providing an HVOF gas stream to a fluid cooled nozzle. A portion of the gas stream is diverted for preheating the powder, with the preheated powder being injected into the main gas stream at a downstream location within the nozzle. Forced air and vacuum sources are provided in a shroud circumscribing the nozzle for cooling the melted powder in flight before deposition onto the substrate. [0006] Another example is U.S. Pat. No. 4,999,225 to Rotolico which discloses a method for producing a dense and tenacious coating with a thermal spray gun including a nozzle member and a gas cap. This patent discloses powder particles having heat softenable, meltable component and a heat-stable, non-fusible component sprayed with a thermal process. [0007] Non-melting polymers, such as polyimides, have been applied with successful results in semi-conductor applications that require resistance to corrosive plasma gas and high material purity. However, the method of application of these polymers has been limited to hot molding or directly forming parts with these polymer coatings in the semiconductor methods. There are instances where these methods are not practical. For example, for large and/or geometrically complex surfaces. [0008] Thus, it is desirable to have an article that is spray coated with non-meltable polymers to provide the resistance and high material purity of the non-meltable polymer. Such coatings are also believed to extend the life of the substrate. [0009] Briefly stated, and in accordance with one aspect of the present invention, there is provided an article being spray coated with at least one non-melting polymer. [0010] Pursuant to another aspect of the present invention, there is provided an article that is spray coated using a process comprising a high velocity oxygen fuel (HVOF) and spraying an HVOF stream containing at least one non-melting polymer from an elongated nozzle downstream from and in flow communication with said HVOF, said elongated nozzle comprising a cooling fluid, circulating externally around said barrel having a central bore with an inlet opening and an outlet opening, said at least one non-melting polymer being fed into said HVOF stream at a point within said elongated nozzle downstream from said inlet opening to coat said article with the at least one non-melting polymer. [0011] The invention will be more fully understood from the following detailed description, taken in connection with the accompanying drawings, in which: [0012] [0013] [0014] [0015] [0016] [0017] [0018] [0019] [0020] [0021] [0022] [0023] [0024] [0025] [0026] [0027] [0028] [0029] [0030] [0031] [0032] [0033] [0034] [0035] [0036] [0037] [0038] [0039] [0040] [0041] While the present invention will be described in connection with a preferred embodiment thereof, it will be understood that it is not intended to limit the invention to that embodiment. On the contrary, it is intended to cover all alternatives, modifications, and equivalents as may be included within the spirit and scope of the invention as defined by the appended claims. [0042] A limitation of the prior art, as mentioned above, is the cost prohibitive element of bulk polyimide materials that contain the desired wear and friction and high temperature properties desired for a variety of applications. It is believed that this cost is reduced by using composites of polyimide and metal, where smaller amounts of the higher cost polyimide is used as the functional surface in combination with lower cost metals such as steel or aluminum for the bulk of the composite. A process for making these composites is the high velocity oxygen fuel process. Applications that require high material purity in addition to the resistance to wear and friction and the ability to be used in high temperature applications requires the application of non-meltable polymer as a coating to a substrate. [0043] “Polyimides” for purpose of this application have linear macromolecules which include aromatic or heterocyclic rings that are tightly packed together and have the following characteristics of polyimides; high temperature resistance (−240 up to 370 C.); high toughness and hardness; high thermostability; very good dimensional stability (coefficient of thermal expansion around 50 μm/m/° K); very good wear performance; high radiation resistance; high flame retardation; and low outgassing in vacuum (less 10−10g/cm2/S). [0044] High performance parts made from polyimide resin include rotary seal rings, thrust washers and discs, bearings, printer platen bars and wire guides, wear strips, valve seats, check valve balls, thermal and electrical insulators. These are some of the variety of applications for polyimide parts. All of these parts exhibit a combination of properties which gives them advantages over metals, other plastics and ceramics. In comparison to metals, polyimide parts exhibit better sealing characteristics, lower weight, a lower coefficient of friction and improved resistance to corrosion. In comparison to other plastic materials, polyimide has a wider continuous-use temperature range, no melting or softening point and high creep resistance. Polyimide is compatible with oxygen, most fuels, solvents, lubricants and hydraulic fluids. In comparison to ceramics, polyimide parts seal better and are less brittle while still exhibiting dimensional and thermal stability. [0045] Polyimide parts can replace parts made from conventional materials in many applications and can also enhance their performance. The low wear and self-lubricating characteristics make it possible to replace assembled parts by a directly formed piece. Examples are tape guides in VCRs and bearings in printers. The low coefficient of friction and the improved seal characteristics make it attractive and reasonable to use polyimide piston rings instead of steel ones. [0046] As previously mentioned, a downside of replacement of common materials by polyimide parts is the higher costs of the polyimide bulk material. An alternative solution is to use composite components consisting of low cost metal substrates with high performance polymer surfaces that combine the superior properties of the polymer and limit the use of the bulk material in order to reduce costs. [0047] Thermal spraying is a versatile and sometimes cost effective solution for a variety of engineering and maintenance tasks. These include the production of corrosion and wear resistant coatings and repair of worn machinery parts. The expression “thermal spraying” defines a group of processes that use chemical or electrical energy to deposit metallic and non-metallic material droplets onto substrates to form a coating. The combination of high temperatures producing particles either molten or at least softened and the high velocities cause the droplets to deform into thin “splats” on impact at the surface. As more and more particles impact, the droplets are rapidly built up and cooled into a lamellar structure which forms the coating. The deposits usually contain porosity, unmelted or incompletely melted particles and inclusions such as oxides, depending on the level of heating of the different particles. There are several different methods of thermal spraying which are differentiated by characteristics such as the energy source (combustion or electrical), the feed stock (particles or solid) and the surrounding environment. Typically three categories comprise the thermal spray processes: combustion spray, wire-arc and plasma as shown in [0048] One of the processes in the combustion category is known as the High Velocity Oxy Fuel (HVOF) process, which was used working the present invention. The HVOF process is one of the newest and fastest growing of the thermal spray processes. The HVOF process can be used for a diverse range of applications such as jet aircraft, land based gas turbines, chemical reactors, metalworking forges, mills and rolls, textiles, bridges, pumps, compressors, medical prostheses and even household items like frying pans. The coatings provide protection against wear, corrosion, and thermal degradation and can also be used for refurbishment and maintenance. [0049] Reference is now made to the drawings for a detailed description of the present invention. [0050] In the present invention, an embodiment of a process for spray coating non-melting polymers such as polyimides using high velocity oxygen fuel is disclosed in [0051] An embodiment of the present invention shown in [0052] The chief differences between various HVOF systems are water vs. air cooling, axial or radial powder injection, fuel flows and composition, combustion chamber pressure and configuration, powder injection location and nozzle design and length. The cooling aspect has been found to be one of the essential elements. Most systems are water cooled in order to prevent melting and degradation of the nozzle and deposition of molten/softened powder on the nozzle walls. Also the high gas flow rates and the criticality of combustion fuel mixtures require precise gas flow control systems. Thus, the control of these parameters is essential for obtaining consistent deposit quality. The key HVOF components are: oxygen-fuel gas mixtures; powder injection; water or air cooling; nozzle cooling flow and control; and combustion gas injectors. [0053] The Jet-Kote II® system manufactured by Stellite is another thermal spray process. In this design the fuel/oxygen mixture is combusted in the “handle” of the gun. The combusting gases are then turned through 90 degrees, split into four jets and the powder is injected into the center of this region. After a short pass through the nozzle the particle gas stream exits and expands to the atmosphere. [0054] Typical gas velocities for HVOF spraying are 1370-2930 m/s (4500-9600 ft/s), with particle velocities of 480-1020 m/s (1570-3350 ft/s) and jet temperatures range from 1650 to 2760 C. (3000-5000 F.). In comparison to other thermal spray processes, the HVOF process has both advantages and disadvantages. The advantages include lower capital costs, portability for easy use in the field, the usually high density and adherent coatings and reduced phase changes during spraying. The disadvantages include high noise levels (up to 130 dB(A), high operating costs due to high gas flows, and high heat inputs into the substrate and coating which may result in decomposition, residual stresses and cracking. However, the high operating costs are minimized when viewed in light of the process of the present invention leading to a less expensive end product. [0055] Many thermoplastic polymers can be thermally sprayed which include urethanes, ethylenevinylalcohols (EVA's), polytetraflourethylene (PTFE), polymethylmetacrylate (PMMA), Polyetheretherketone (PEEK), nylon, polyethylene (PE) and others. The consolidation process of the polymers depends on sufficient in flight heating and acceleration in order to achieve full densities and cohesive strengths. It has also been found that the thermal spray process might decompose the meltable polymer, thus, lowering the molecular weight during spraying. For this reason, sprayed meltable polymers might have different properties compared to conventionally consolidated meltable polymers. The non-meltable polymer of the present invention is believed to avoid this decomposition problem of the meltable polymer. [0056] Another embodiment of the present invention is for the article being spray coated with at least one non-melting polymer to be post-cured. The post-curing being the spray coating of at least one non-meltable polymer being sintered onto the article. Being sintered comprises heating at least one non-melting polymer spray coated onto said article, wherein the heating does not to exceed a maximum temperature of 450° C. in an enclosure having an atmosphere devoid of oxygen. [0057] Referring again to [0058] The following examples are embodiments of the present invention with the following developed spray system parameters:
[0059] The non-meltable polymer coating is of considerable value as a coating in a corrosive environment such as inside a semiconductor etch chamber reactor 230 as shown in [0060] The non-meltable polymer coatings protect the metal and ceramic parts in the corrosive environment and have high purity as mentioned above. Examples of such non-meltable polymer coatings for such protection include: polyphenylenes, polyether sulfones, polyphenylene sulfides, polyimidothioethers, polyoxamides, polyimines, polysulfonamides, polyimides, polysulfonimides, polyimidines, polypyrazoles, polyisoxazoles, polybenzoxazoles, polybenzimidazoles, polythiazoles, polybenzothiazoles, polyoxadiazoles, polytriazoles, polytriazolines, polytetrazoles, polyquinolines, polyanthrazolines, polypyrazines, polyquinoxalines, polyquinoxalones, polyquinazolones, polytriazines, polytetrazines, polythiazones, polypyrrones, polyphenanthrolines, polycarbosilanes, and polysiloxanes. [0061] The tests run and the results obtained using the thermal spray coating method for non-meltable polymer are described in the following Examples section. [0062] The following experiment was run: Initially, the powder compositions were characterized through their characteristic values and morphology examined by optical microscopy. After that, parameters to obtain coatings without significant degradation of the polymer were developed. A sample preparation procedure for the actual spray cycles followed. The coatings were characterized through their microstructure and porosity using standard metallographic techniques. Tests to determine the coating cohesion, adhesion and wear performance included Tape Test, Pencil Test, Scratch Test and Wear Test with a Pin-on-Disc (POD) Wear Tester. These tests and the data attained will be discussed later in the text. [0063] Two polyimide powders were used, an unfilled base resin (Vespel® SP-1 manufactured by DuPont) and a graphite filled resin (Vespel® SP-21 manufactured by DuPont). Table 1 discloses characteristic values for the unfilled resin (Vespel® SP-1) and the filled resin (Vespel® SP-21).
[0064] The quality of a coating on a substrate is dependent mainly on the temperature and the velocity of the particles prior to the impact with the substrate. These two parameters are influenced by several variables of the HVOF process. The fuel to oxygen ratio flow determines the temperature of the flame. The velocity of the particles is influenced by a higher amount of combusted gas due to flow rates and pressures of the oxygen and fuel. Thus, velocity will be increased by a higher pressure in the nozzle. [0065] The samples that were prepared for the different types of tests were 1×3 coupons (0.12″ (3.1 mm) thick) and wear discs with a diameter of 2.4″ (60 mm). Prior to spraying they were grit blasted to enhance the bonding between substrate and coating. The substrate materials were 1040 steel and aluminum and the coating materials were the unfilled and the 15% graphite filled polyimide. Samples with all substrates and all coatings were sintered according to the following method: The parts were placed in an oven at a temperature below 140° C. The oven was purged with nitrogen at a flow rate of 4 scfm until the oxygen level reached less than 0.2%. The temperature was ramped up from 140 to 400° C. at a maximum rate of 90K per hour. The ramping was stopped when the temperature was in the range of 395 to 400° C. The temperature of 395 to 400° C. was held for approximately three hours +/−10 minutes. The oven was turned off and the parts were removed when the temperature reached 50° C. Thus, eight different substrate/coating/post-deposition treatment combinations were studied. Each of the combinations was tested with different test methods and the effects of different substrates, filler and sintering on the properties of the coating for evaluation of the coating.
[0066] Tape Test: [0067] A Tape Test was used to measure adhesion of the coatings. The average thickness of the samples was over 125 μm (0.005″), thus, test method A in accordance with ASTM D3359-95 (from “Standard Test Methods for Measuring Adhesion by Tape Test”, Publication of the American Society for Testing and Materials, Philadelphia, April 1995) was used. An X-cut is made in the film to the substrate, pressure-sensitive tape is applied over the cut and then removed, and the adhesion is assessed qualitatively on the following 0 to 5 scale:
[0068] The test was made using 3M Scotch 600 tape, 25.4 mm (1 inch) in width. The results of the Tape Test are shown in Table 3.
[0069] The trend seen from this table is that the sintering process enhanced the adhesion of the coating to the substrate and also enhanced the cohesion within the coating. Influences of the substrate material or the filler were not apparent in this test. [0070] Pencil Test: [0071] A Pencil Test allows a relative comparison of samples and does not give an absolute value of coating hardness. The Pencil Test should be performed as follows according to ASTM D3363-92a, (from “Standard Test Methods for Film Hardness by Pencil Test”, Publication of the American Society for Testing and Materials, January 1993): A coated panel is placed on a firm horizontal surface. The pencil is held firmly against the film at a 45 degree angle (point away from the operator) and pushed away from the operator in a 6.5 mm (¼ inch) stroke. The process is started with the hardest pencil and continued down the scale of hardness to wither one of tow end points: one, the pencil that will not cut into or gouge the film (pencil hardness), or two, the pencil, that will not scratch the film (scratch hardness). In this case the pencil hardness was tested. The pencils that are used for this test meet the following scale of hardness:
[0072] The results of the pencil tests of the present invention are summarized in Table 4 using the above scale of hardness.
[0073] In table 4, in the case of the unfilled material, the substrate and the sinter process appear to have virtually no effect on the hardness (e.g. for steel the hardness slightly decreased and for aluminum the hardness stayed at F). In the case of the filled material the test showed that the sintering process enhanced the coating hardness, which was improved approximately by ½ point on the hardness scale. On the steel substrate, is the filled material showed a higher pencil hardness than the unfilled one. The pencil hardness was higher for the filled material on the steel substrate than on the aluminum substrate, in both the unsintered and sintered case. [0074] The Pencil Test results can be strongly operator dependent, despite the fact that coatings with different characteristics showed different pencil hardness. Thus, it is important to test the samples under the same conditions, particularly with regard to pencil sharpness, force and angle. [0075] Scratch Test: [0076] The Scratch Test can be performed on an apparatus that uses a simple device which applies a fixed load on a sharpened needle which is dragged over a surface of a coating. The resulting scratch depth is measured using a stylus-tracing profilometer and compared to scratches with the same load in different coatings. Scratch Testing is an easy method of investigating the cohesion of a coating. In order to reduce errors in the profilometer reading the surfaces of the samples were polished with dry abrasive paper. In order to provide a sufficient thickness for the test the polishing had to be done carefully to ensure that the coating was at least 190 μm thick after polishing. It was also important to ensure that the surface was smooth enough to enable a proper profilometer reading. The range of the load for the scratch test was from 500 g to 2000 g in steps of 250 g. [0077] The results of the scratch tests in the present invention are shown in the graphs shown in FIGS. 5-13. Each graph is representative of the properties of the sample tested (e.g. [0078] [0079] The results for the scratch test of the combination Aluminum, unfilled, sintered were not available. [0080] [0081] For both substrates and for unfilled and filled material the diagrams is show clearly the influence of sintering. The sintered material showed a lower scratch depth independent from substrate and filler. The sinter process obviously made the coating more dense and enhanced its cohesion by increasing the amount of bonds resulting in a higher scratch resistance. [0082] Wear Test: [0083] In a POD (pin-on-disc) wear tester, the wear disc with the coating is fastened with a screw to a rotating disc, which is turned by the motor of the wear tester. The pin with the steel ball applies the test load onto the wear disc and can be moved to both sides in order to change the wear track radius. According to this wear track radius the rotations per minute of the rotating disc had to be changed in order to achieve the same sliding speed. The pin also contained the sensors to measure the forces during wear testing and was connected to the control computer. [0084] Wear testing was carried out using a pin-on-disc tribometer according to ASTM G 99-90 standards. The counterbody was a 10 mm diameter 52100 steel ball in all cases. The sliding speed was kept constant at 0.65 m/s. Two tracks were tested on each disc at radii of 17 and 21 mm. In order to keep the sliding speed constant, the RPM of the disc was varied accordingly. The duration of the test was 10000 cycles and the interfacial medium between the coating and the steel ball was air. For each of the eight conditions two discs were available, of which one was tested on two tracks at a load of 10N and the second one at a load of 20N. The discs were first polished with dry abrasive paper in order to reduce the noise in the profilometer reading. Another problem that occurred was the “wavy” profile of the wear discs due to the different passes during spraying. The following parameters were recorded during the sliding wear tests: a) the wear track cross-sectional area was measured as an average of four measurements using the profilometer and the integrals under the resulting profiles were calculated by a computer; and b) the coefficient of friction was recorded from the tribometer using a data acquisition system. (The coefficient of friction was averaged over a useful period of rotations (6000-8000 cycles on average), i.e. run-in-effects up to the first 2000 rotations were not considered. Also sudden steps in the friction curves were averaged over a useful period of rotations.) [0085] For comparison purposes, wear testing was also performed on samples made of conventionally produced polyimide parts. The polyimide used was Vespel® SP-1 manufactured by DuPont for the unfilled sample, and Vespel® SP-21 manufactured by DuPont for the 15% graphite filled samples. As expected, these samples performed better than the coated samples as shown in FIGS. 14-29. However, because they are made completely of polyimide, they are significantly more expensive than the coated samples made of an inexpensive metal substrate and thin polyimide coating. The coated samples exhibit desirable characteristics of the polyimide, at a much lower total cost. [0086] One of the discs with the configuration Al, filled, unsintered, which was supposed to be tested with a 20 N load, had a very thin coating. Because of that the coating wore through during the test and no values for wear track area and width could be determined. Since the coating wore away after about 8000 cycles, the values for the coefficient of friction could still be used. All of the following results were the average of the results for the 17 and 21 mm radius tracks. [0087] [0088] [0089] [0090] [0091] [0092] [0093] [0094] The experiments demonstrated, that Polyimides can be sprayed by HVOF and adherent coatings can be produced. Wear testing showed the beneficial effects of the sintering process. A wide range of tests was performed to characterize the coatings' adhesion, cohesion, hardness and sliding wear performance. [0095] The Tape Test showed that sintering enhanced adhesion and cohesion whereas substrate and filler had no influence. Concerning coating hardness the Pencil Test gave information about the hardness increasing effect of sintering and the fact, that coatings on steel exhibit a higher hardness than on aluminum. Scratch testing showed the cohesion enhancing effect of sintering resulting in a lower scratch depth independent from substrate and filler. The potential wear mechanism was described through a model for the effects of different factors such as filler and substrate. The graphite filler should have a lubricating and bond reducing effect resulting in lower coefficients of friction and higher wear rates. Due to the higher thermal conductivity coatings on aluminum substrates should exhibit less cohesion and thus less resistance during wear. Sintering should increase coating cohesion and equalize differences between filled and unfilled materials and coatings on steel and aluminum substrates. [0096] Concerning wear track area some points of the model could be confirmed. The filled material showed higher wear rates due to less cohesion because of the filler. Coatings on aluminum exhibited higher wear rates than the ones on steel. Sintering equalized the difference in wear performance between filled and unfilled material on steel but-not on aluminum. Also the difference between coatings on steel and aluminum, as assumed in the model, were not equalized. [0097] Regarding coefficient of friction, the experiments showed that the filled material exhibited a lower coefficient of friction than the unfilled one. In addition to the wear rates the results for the COF could support the assumption that coatings on aluminum exhibit less wear resistance and thus lower COF's than the ones on steel due to reduced cohesion. Again an equalizing effect of sintering between coatings on steel and aluminum substrates could not be noticed. It is therefore, apparent that there has been provided in accordance with the present invention, a method of spray coating non-meltable polymers using HVOF that fully satisfies the aims and advantages hereinbefore set forth. While this invention has been described in conjunction with a specific embodiment thereof, it is evident that many alternatives, modifications, and variations will be apparent to those skilled in the art. Accordingly, it is intended to embrace all such alternatives, modifications and variations that fall within the spirit and broad scope of the appended claims. An article spray coated with non-melting polymers using a high velocity oxygen fuel spray gun to coat a substrate with the non-melting polymers. 1. An article being spray coated with at least one non-melting polymer. 2. An article of 3. An article according to 4. The article according to 5. An article according to 6. An article according to 7. An article according to 8. An article according to 9. An article according to 10. An article according to 11. An article according to 12. An article according to 13. An article according to 14. An article according to 15. An article according to 16. An article according to 17. An article according to 18. An article according to 19. An article according to 20. An article according to 21. An article according to 22. A article according to 23. An article according to 24. An article according to 25. An article according to 26. An article according to 27. An article according to 28. An article according to 29. An article according to CROSS REFERENCE
FIELD OF THE INVENTION
BACKGROUND OF THE INVENTION
SUMMARY OF THE INVENTION
BRIEF DESCRIPTION OF THE DRAWINGS
DETAILED DESCRIPTION OF THE INVENTION
Example 1 Example 2 HVOF Spray Gun Stellite Jet Kote IIA Stellite Jet Kote IIA Fuel Hydrogen Hydrogen Nozzle {fraction (5/16)}″ D × 2″ L {fraction (5/16)}″ D × 3″ L (8 mm × 51 mm) (8 mm × 76 mm) Gas Injector #40 #40 Fuel Flow 800 scfh @ 120 psi 600 scfh @ 120 psi (22.7 scmh @ 0.8 MPA) (17 scmh @ 0.8 MPA) Oxygen Flow 1400 scfh @ 120 psi 1400 schf @ 120 psi (39.6 scmh @ 0.8 MPA) (39.6 scmh @ 0.8 MPA) Powder Vespel ® SP-1 Polyimide Vespel ® SP-21 Polyimide Powder Feeder Plasmadyne Plasmadyne Powder Carrier Nitrogen Argon Gas Powder Carrier 40 scfh @ 100 psi >50 scfh @ 160 psi Gas Flow (1.1 scmh @ 0.7 MPA) (>1.4 scmh @ 1.1 MPA) Powder Feed Rate 9 rpm 8 rpm Spray Distance 4″-6″ (102-152 mm) 6″ (152 mm) Part Speed dx/dt = 100% (45 ft/min) dx/dt = 50% (13.7 m/min) Spray Time Preheat: 1 Cycle Preheat: 1 Cycle Coating: 2 Cycles Coating: 2 Cycles Step Size ½″ (13 mm) ½″ (13 mm) Cooling none none Substrate Aluminum Aluminum Substrate 0.125″ (3 mm) 0.160″ (4 mm) Thickness Surface Prepara- Grit Blasted (#60 Al2O3) Grit Blasted (#60 Al2O3) tion Coating 0.011″ (0.3 mm) 0.010″ (0.3 mm) Thickness Example 3 HVOF Spray Gun Stellite Jet Kote IIA Fuel Hydrogen Nozzle {fraction (5/16)}″ D × 3″ L (8 mm × 76 mm) Gas Injector #40 Fuel Flow 600 scfh @ 120 psi (17 scmh @ 0.8 MPA) Oxygen Flow 1400 scfh @ 150 psi (39.6 scmh @ 1 MPA) Powder Vespel ® SP-1 Polyimide (filled resin, ˜30-40 μm) Powder Feeder Plasmadyne Powder Carrier Nitrogen Gas Powder Carrier >50 scfh @ 100 psi Gas Flow (>1.4 scmh @ 0.7 MPA) Powder Feed Rate 9 rpm Spray Distance 4″-6″ (102-152 mm) Part Speed dx/dt = 100% (45 ft/min) (13.7 m/min) Spray Time Preheat: 1 Cycle Coating: 2 Cycles Step Size ½″ (13 mm) Cooling none Substrate 1018 Steel Substrate 0.117″ (3 mm) Thickness Surface Grit Blasted (#12 Al2O3) Preparation Ultrasonic Degrease in Alcohol Coating 0.004″-0.010″ (0.1-0.3 mm) Thickness EXAMPLES
Characteristic values for test resins Characteristics Unfilled Resin Filled Resin Specific Gravity 1.34-1.43 1.42-1.51 Thermal conductivity 0.29-0.39 0.46-0.87 [W/m K] Coefficient of Linear 50-54 41-49 Expansion [μm/mK] Melting Point None None Filler None 15% graphite Particle Size 20-30 μm 20-30 μm Substrate/Coating/Post-Deposition Treatment Substrate Material Coating Material Sinter State Steel Unfilled (SP-1) unsintered Steel Unfilled (SP-1) sintered Steel Filled (SP-21) unsintered Steel Filled (SP-21) sintered Aluminum Unfilled (SP-1) unsintered Aluminum Unfilled (SP-1) sintered Aluminum Filled (SP-21) unsintered Aluminum Filled (SP-21) sintered 5A No peeling or removal; 4A Trace peeling or removal along incisions or their intersection; 3A Jagged removal along incisions up to 1.6 mm ({fraction (1/16)} inch) on either side; 2A Jagged removal along incisions up to 3.2 mm (⅛ inch) on either side; 1A Removal from most of the area of the X under the tape; and 0A Removal beyond the area of the X. Results of Tape Test Sample Tape Test Steel, unfilled, unsintered 4A Steel, unfilled, sintered 5A Steel, filled, unsintered 4A-5A Steel, filled, sintered 5A Aluminum, unfilled, unsintered 5A Aluminum, filled, sintered 5A Aluminum, filled, unsintered 4A-5A Aluminum, filled, sintered 5A 6B-5B-4B-3B-2B-B-HB-F-H-2H-3H-4H-5H-6H softer harder Results of Pencil Test Sample Tape Test Steel, unfilled, unsintered F Steel, unfilled, sintered HB Steel, filled, unsintered H Steel, filled, sintered H-2H Aluminum, unfilled, unsintered F Aluminum, unfilled, sintered F Aluminum, filled, unsintered F Aluminum, filled, sintered H-F
















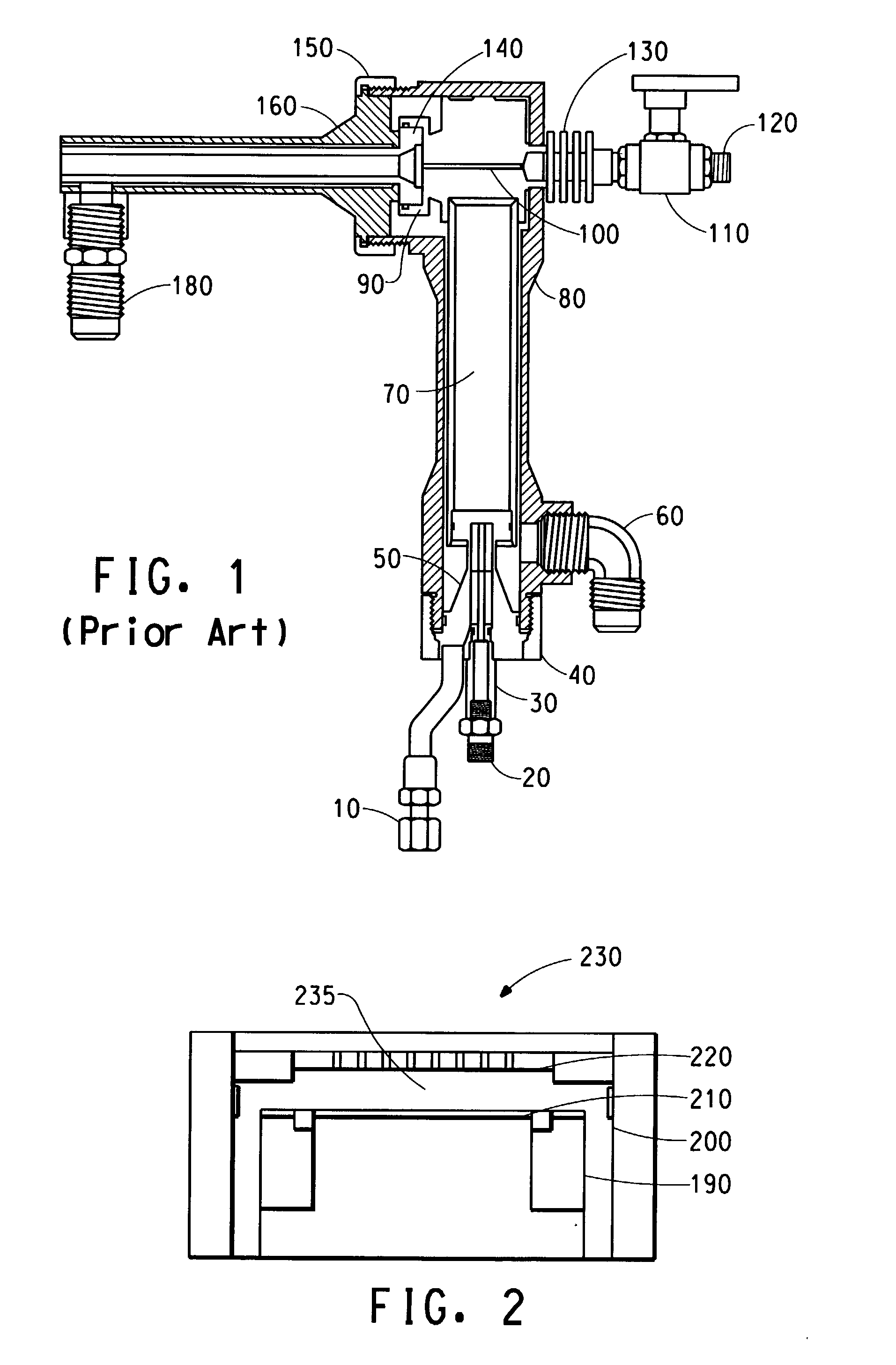



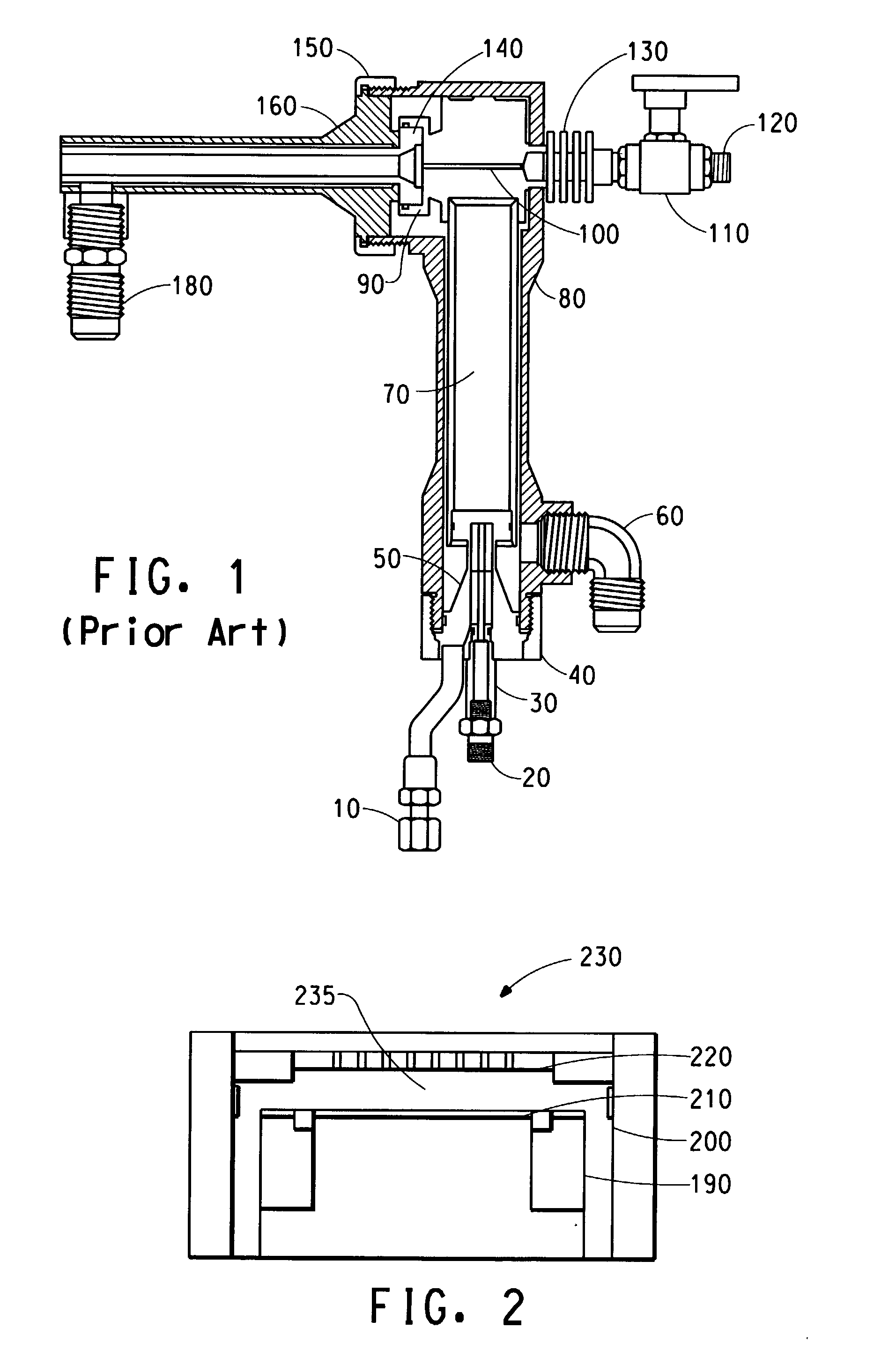






