POWDER BED RE-COATER APPARATUS AND METHODS OF USE THEREOF
The present disclosure generally relates to methods and systems adapted to perform additive manufacturing (“AM”) processes, for example by direct melt laser manufacturing (“DMLM”). The process utilizes an energy source that emits an energy beam to fuse successive layers of powder material to form a desired object. More particularly, the disclosure relates to methods and systems that utilize a recoater blades to distribute and smooth out the powder. Additive manufacturing (AM) techniques may include electron beam freeform fabrication, laser metal deposition (LMD), laser wire metal deposition (LMD-w), gas metal arc-welding, laser engineered net shaping (LENS), laser sintering (SLS), direct metal laser sintering (DMLS), electron beam melting (EBM), powder-fed directed-energy deposition (DED), and three dimensional printing (3DP), as examples. AM processes generally involve the buildup of one or more materials to make a net or near net shape (NNS) object in contrast to subtractive manufacturing methods. Though “additive manufacturing” is an industry standard term (ASTM F2792), AM encompasses various manufacturing and prototyping techniques known under a variety of names, including freeform fabrication, 3D printing, rapid prototyping/tooling, etc. AM techniques are capable of fabricating complex components from a wide variety of materials. Generally, a freestanding object can be fabricated from a computer aided design (CAD) model. As an example, a particular type of AM process uses an energy beam, for example, an electron beam or electromagnetic radiation such as a laser beam, to sinter or melt a powder material and/or wire-stock, creating a solid three-dimensional object in which a material is bonded together. Selective laser sintering, direct laser sintering, selective laser melting, and direct laser melting are common industry terms used to refer to producing three-dimensional (3D) objects by using a laser beam to sinter or melt a fine powder. For example, U.S. Pat. No. 4,863,538 and U.S. Pat. No. 5,460,758 describe conventional laser sintering techniques. More specifically, sintering entails fusing (agglomerating) particles of a powder at a temperature below the melting point of the powder material, whereas melting entails fully melting particles of a powder to form a solid homogeneous mass. The physical processes associated with laser sintering or laser melting include heat transfer to a powder material and then either sintering or melting the powder material. Electron beam melting (EBM) utilizes a focused electron beam to melt powder. These processes involve melting layers of powder successively to build an object in a metal powder. The abovementioned AM processes is controlled by a computer executing a control program. For example, the apparatus 110 includes a processor (e.g., a microprocessor) executing firmware, an operating system, or other software that provides an interface between the apparatus 110 and an operator. The computer receives, as input, a three dimensional model of the object to be formed. For example, the three dimensional model is generated using a computer aided design (CAD) program. The computer analyzes the model and proposes a tool path for each object within the model. The operator may define or adjust various parameters of the scan pattern such as power, speed, and spacing, but generally does not program the tool path directly. One having ordinary skill in the art would fully appreciate the abovementioned control program may be applicable to any of the abovementioned AM processes. The above additive manufacturing techniques may be used to form a component from any material conducive to an AM process. For example polymers, ceramics and various plastics may be formed. Further, metallic objects can be formed from materials such as stainless steel, aluminum, titanium, Inconel 625, Inconel 718, Inconel 188, cobalt chrome, among other metal materials or any alloy, for example. The above alloys may further include materials with trade names, Haynes 188®, Haynes 625®, Super Alloy Inconel 625™, Chronin® 625, Altemp® 625, Nickelvac® 625, Nicrofer® 6020, Inconel 188, and any other material having material properties attractive for the formation of components using the abovementioned techniques. A problem that arises when making additive manufactured components is that, over the course of the build, a recoater blade mounted on the recoater arm may encounter surface features of the object being formed. Since the recoater blade is generally rigid so that it can smooth out the powder into a substantially even layer, if it encounters a surface feature the recoater blade may become damaged, or it may damage the surface feature. If the recoater blade is damaged, the AM process may need to be stopped so that the blade can be replaced, which results in significant downtime. Further, if the surface feature of the object is damaged, the object maybe have to be discarded and rebuilt. Sometimes, neither the blade nor the surface feature becomes damaged, but the surface feature stops the recoater from moving further (i.e. it becomes “jammed”). Thus, damage to a recoater blade and/or contact between the build surface and recoater blade can result in a significant loss in production efficiency. Therefore there is a need for a recoating system and apparatus that is less prone to contact between the blade and surface features of the component being built during an AM process. As shown in During an AM process, a large percentage of problems are related to the abovementioned issues and/or other issues arising at the interface of the powder bed and the re-coater blade. As larger parts are manufactured using AM processes, even more issues arise as the formation of larger parts results in larger dimensional variations which may further exacerbate any problems associated with the supply of powder and the re-coater blade and powder bed interface. Thus, a need exists to further improve powder distribution and the interface of the powder bed and the re-coater blade. Further, compatibility issues with powders and powder size distribution can cause problems in prior re-coater blade and/or powder distribution systems. For example, the need to keep powder size consistent in a traditional apparatus results in an increase expense in sourcing powder. Further, there is a desire to use finer powder to increase resolution of the AM build, which previously may have not been usable with traditional powder recoating systems. The present disclosure is related to an apparatus that reduces the aforementioned undesirable situations. An embodiment of the present invention is related to an apparatus for making an object from powder comprising an energy directing device, a powder dispenser, and a set of recoater blades positioned to provide a layer of powder over a work surface by moving over the work surface, the thickness of the layer of powder determined by a powder distribution member and/or the height a set of blades above the work surface, wherein the recoater blades are mounted to allow movement of the blade height with respect to the work surface while providing the layer of powder over the work surface. In one aspect the apparatus provides powder during the additive manufacturing of a component, wherein the apparatus provides powder to at least a portion of component to be solidified, wherein the clearance between at least one of the first sweep strip and the second sweep strip and the component is less than 1 mm. In one aspect the apparatus may include at least a first sweep strip and the second sweep strip extending along a first direction. The first sweep strip may include a top portion connected to the apparatus and a bottom portion further from the apparatus than the top portion. The second sweep strip may also include a top portion connected to the apparatus and a bottom portion further from the apparatus than the top portion. The sweep strips may be adjusted so that the bottom portion of one of the first and second sweep strips extends further below the apparatus than the other of the first and second sweep strips. In one aspect of the disclosure, the apparatus may be configured to travel and supply a layer of powder along at least a first direction. When the first sweep strip is the forward sweep strip in the first direction and the second sweep strip is the aft sweep strip with relation to the first direction, the bottom portion of the first sweep strip may be adjusted to extend further below the apparatus than the second sweep strip. Conversely, when the second sweep strip is the forward sweep strip and the first sweep strip is the aft sweep strip with relation to the direction of travel, the bottom portion of the second sweep strip may be set to extend further below the apparatus than the first sweep strip. In one aspect of the disclosure an apparatus is described for supplying a powder used in an AM process. The apparatus comprises a powder reservoir, a first sweep strip, and a second sweep strip which may be located proximate to a powder bed and/or build component during an AM manufacturing process. The apparatus may further include a powder distribution system having an inlet for receiving powder form the reservoir and an outlet for supplying powder received from the inlet, wherein the outlet is located between the first sweep strip and the second sweep strip to better shield the powder from the operating environment of the apparatus (e.g. a gas flow within the apparatus provided during an AM manufacturing operation). The powder distribution system may further include a housing portion in fluid communication with the inlet and a roller rotatable around an axis within the housing, the axis extending in a first direction, wherein the roller is configured to convey powder from the inlet into the housing portion. In the abovementioned aspects of the disclosure, the roller may be textured and/or may include a plurality of metering protrusions extending along the first direction. The textured portion and/or metering protrusions may be configured to convey powder to the outlet via a communication path in fluid communication with the outlet and the housing portion. In another aspect of the disclosure, the roller may be textured and/or may include a plurality of metering protrusions extending along the first direction. The textured portion and/or metering protrusions may be configured to convey powder to a powder distribution member having a plurality of openings for supplying powder to the outlet of the apparatus. In another aspect of the disclosure, the rollers may be textured and/or may include a plurality of metering protrusions extending along the first direction. The textured portion and/or metering protrusions may be configured to convey powder to a fluidizing chamber, the fluidizing chamber may include a fluidizing gas inlet, a fluidizing gas outlet, and a fluidizing powder device having a plurality of openings and an overflow portion for supplying powder to the abovementioned outlet. When powder is supplied to the fluidizing chamber by the abovementioned roller, and fluidizing gas is supplied from the fluidizing gas inlet though the plurality of openings, powder may overflow from the overflow portion to the outlet between the first and second sweep strips. In each of the abovementioned aspects, the apparatus may further include a first height detector for detecting a height of the apparatus from the powder bed at a first location and a second height detector for detecting a height of the apparatus from a powder bed at a second location different from the first location. Based on at least the output of the first height detector and the second height detector, the flow of powder through the outlet is controlled using at least one of the abovementioned roller, powder distribution member, and/or the fluidizing chamber. The accompanying drawings, which are incorporated into and constitute a part of this specification, illustrate one or more example aspects of the present disclosure and, together with the detailed description, serve to explain their principles and implementations. The detailed description set forth below in connection with the appended drawings is intended as a description of various configurations and is not intended to represent the only configurations in which the concepts described herein may be practiced. In one aspect of the invention, as shown in U.S. patent application Ser. No. 15/406,467, titled “Additive Manufacturing Using a Mobile Build Volume,” with attorney docket number 037216.00059, and filed Jan. 13, 2017; U.S. patent application Ser. No. 15/406,454, titled “Additive Manufacturing Using a Mobile Scan Area,” with attorney docket number 037216.00060, and filed Jan. 13, 2017; U.S. patent application Ser. No. 15/406,444, titled “Additive Manufacturing Using a Dynamically Grown Build Envelope,” with attorney docket number 037216.00061, and filed Jan. 13, 2017; U.S. patent application Ser. No. 15/406,461, titled “Additive Manufacturing Using a Selective Recoater,” with attorney docket number 037216.00062, and filed Jan. 13, 2017; U.S. patent application Ser. No. 15/609,965, titled “Apparatus and Method for Continuous Additive Manufacturing,” with attorney docket number 037216.00102, and filed May 31, 2017; U.S. patent application Ser. No. 15/406,471, titled “Large Scale Additive Machine,” with attorney docket number 037216.00071, and filed Jan. 13, 2017; U.S. patent application Ser. No. 15/406,454, titled “Additive Manufacturing Using a Mobile Scan Area,” with attorney docket number 037216.00060, and filed Jan. 13, 2017; U.S. patent application Ser. No. 15/610,214, titled “Method for Real-Time Simultaneous and Calibrated Additive and Subtractive Manufacturing,” with attorney docket number 037216.00109, and filed May 31, 2017; U.S. patent application Ser. No. 15/609,747, titled “Apparatus and Method for Real-Time Simultaneous Additive and Subtractive Manufacturing with Mechanism to Recover Unused Raw Material,” with attorney docket number 037216.00110, and filed May 31, 2017. The disclosures of the above applications are incorporated herein in their entirety to the extent that they disclose additional aspects of powder bed additive manufacturing methods and systems that can be used in conjunction with those disclosed herein. The recoater apparatus 300 shown in As mentioned above, the recoater apparatus 300 shown in The recoater apparatus may further include an aft sweep strip 306 and a forward sweep strip 307. The sweep strips 306 and 307 may be positioned such that the powder supply exit 318 is located between the sweep strips 306 and 307. Thus, the sweep strips 306 and 307 may function as a shield to block gas flow from interfering with the powder distribution process. The sweep strips may be adjustable along the z-axis either through height (i.e. z-axis) adjustment of the recoater apparatus 300, or the sweep strips may be individually adjustable along the z-axis through an individual adjustment mechanism on each of the forward and aft sweep strips. Further, the height of each of the forward sweep strip 307 and aft sweep strip 306 may be adjustable through tilting of the recoater apparatus in combination with the abovementioned height adjustment of the recoater apparatus 300. As discussed below, the sweep strips may be adjusted using any one of or combination of the aforementioned methods such that the sweep strips do not contact or minimally contact the powder bed while effectively blocking gas flow which may interfere with the powder distribution process. Further, the sweep strip height may be controlled to sweep powder across the powder bed. Each of the sweep strips may be comprised of a soft pliable material (e.g. a foam, silicone, rubber), a rigid or semi rigid material. The sweep strips 307 and/or 306 may also be configured to remove a quantity of powder from a build region. For example, while a build process progresses by solidifying powder, a portion of the build may begin to increase in height at a faster rate than another portion of the build. In other words, with reference to The recoater apparatus 300 may further include several sensors to assure that powder is precisely metered and distributed along the surface of the powder bed and/or the build component in the powder bed. As an example, the recoater apparatus 300 may include a photo-emitter-receiver pair to sense the consistency and uniformity of powder flow through the passage 322, the powder supply exit 318, and/or within the cylindrical housing portion. It is noted that the abovementioned sensor locations may be used in any combination to determine the amount of powder being supplied to the powder bed. Further, it is noted that a plurality of sensors may be located in each location, for example a plurality of sensors may be located along the y-axis direction to assure detect the amount of powder being supplied along the width of the powder bed along the length of the recoater apparatus 300. The sensors may also include an aft z-height sensor array 316 and a forward z-height sensor array 317 to precisely monitor the height of the recoater apparatus 300 with respect to the powder bed and/or to determine a height difference between the forward z-height sensor 317 and the aft z-height sensor 316 with respect to the powder bed, which may be used to determine the thickness of the layer of powder provided by the recoater apparatus to the powder bed 302. The forward z-height sensor array 317 and the aft z-height sensor array 316 may be capacitive proximity sensors. The forward z-height sensor array 317 and the aft z-height sensor array 316 may also include or be combined with any well-known sensors in the art usable to determine a height in a non-contact manner. The abovementioned forward z-height sensor array 317 and the aft z-height sensor array 316 may be used to adjust the height of the recoater apparatus 300 and/or may be used to adjust the quantity or distribution of powder to be supplied to the powder bed 302 through the powder supply exit 318. As discussed above, outputs from the forward z-height sensor array 317, aft z-height sensor array 316, photo-emitter-receiver pair in the passage 322, the photo-emitter-receiver pair in the powder supply exit 318, and/or within the cylindrical housing portion may be processed by a controller to continuously adjust the output to the motor connected to the rotatable textured roller 310. Thus, by controlling the rotation of the textured roller 310 the powder 319 can be precisely distributed along the powder bed 302 and/or build component as the recoater travels in direction 301 across the powder bed 302. Based on the output of any of the mentioned sensors, the forward sweep strip 307 and the aft sweep strip 306 may be adjusted such that the a bottom portion of the forward sweep strip 307 that is further from the apparatus than a top portion of the forward sweep strip 307 is offset with relation to the bottom portion of the aft sweep strip 306 (i.e. lower in the z-direction). In other words, because a layer of powder is supplied from the opening to the powder bed and/or component being built in the powder bed, it may be preferable to adjust the aft sweep strip 306 in the z-direction to compensate for the thickness of the layer of powder provided. If the recoater apparatus reverses direction (i.e. causing the aft sweep strip to become the forward sweep strip), it may be necessary to adjust the sweep strip height in a similar manner (i.e. the forward sweep strip lower in the z-direction that the aft sweep strip). Using any of the abovementioned techniques, it may be further preferable to adjust the sweep strip heights such that a clearance in the z-direction between the powder bed and/or build component and the sweep strips is less than 1 mm. As shown in The rotatable metering roller 410 may be connected to motor (e.g. a stepper motor). Accordingly, powder 419 may be in contact with the roller 310 through passage 422. Thus, when the roller 410 is rotated via the motor, powder is conveyed along the surface of the roller 410 to the powder distribution member 432. As shown in As mentioned above, the recoater apparatus 400 shown in The recoater apparatus may further include an aft sweep strip 406 and a forward sweep strip 407. The sweep strips 406 and 407 may be positioned such that the powder distributed by the distribution member 432 to the powder bed proximal to location 404 is between the sweep strips 406 and 407. Thus, the sweep strips 406 and 407 may function as a shield to block any gas flow from interfering with the powder distribution process. Optionally, the sweep strips may be adjustable along the z-axis either through height (i.e. z-axis) adjustment of the recoater apparatus 400, or the sweep strips may be individually adjustable along the z-axis through an individual adjustment mechanism on each of the forward and aft sweep strips. Further, the height of each of the forward sweep strip 407 and aft sweep strip 406 may be adjustable through tilting of the recoater apparatus 400 in combination with the abovementioned height adjustment of the recoater apparatus 400. As discussed below, the sweep strips may be adjusted using any one of or combination of the aforementioned methods such that the sweep strips do not contact or minimally contact the powder bed while effectively blocking gas flow which may interfere with the powder distribution process. Further, the sweep strip height may be controlled to sweep powder across the powder bed. The sweep strips 407 and/or 406 may also be configured to remove a quantity of powder from a build region. For example, while a build process progresses by solidifying powder, a portion of the build may begin to increase in height at a faster rate than another portion of the build. In other words, with reference to The recoater apparatus 400 may further include several sensors to assure that powder is precisely metered and distributed along the surface of the powder bed and/or the build component in the powder bed. As an example, the recoater apparatus may include a photo-emitter-receiver pair (not shown) to sense the consistency and uniformity of powder flow through the passage 422, the powder supply exit proximal to location 404, and/or within the cylindrical housing portion 421. It is noted that the abovementioned sensor locations may be used individually or in any combination to determine the amount of powder being supplied to the powder bed. Further, it is noted that a plurality of sensors may be located in each location, for example a plurality of sensors may be located along the y-axis direction to assure detect the amount of powder being supplied along the width of the powder bed along the length of the recoater apparatus 400. The sensors may also include an aft z-height sensor array 416 and a forward z-height sensor array 417 to precisely monitor the height of the recoater apparatus 400 with respect to the powder bed and/or to determine a height difference and/or clearance between the sweep strips 407 and 406 and powder bed at the forward z-height sensor 417 at location 403 and the aft z-height sensor 416 at location 402, which may be used to determine the amount of powder to be provided by the recoater apparatus to the powder bed 402 through control of the metering wheel 410 and the distribution member 432. The forward z-height sensor array 417 and the aft z-height sensor array 416 may be capacitive proximity sensors. The forward z-height sensor array 417 and the aft z-height sensor array 416 may also include or be combined with any well-known sensors in the art usable to determine a height in a non-contact manner. The abovementioned forward z-height sensor array 417 and the aft z-height sensor array 416 may be used to adjust the height of the recoater apparatus 400 and/or may be used to adjust the quantity or distribution of powder to be supplied to the powder bed 402 through the powder supply exit 418. As discussed above, outputs from the forward z-height sensor array 417, aft z-height sensor array 416, photo-emitter-receiver pair in the passage 422, the photo-emitter-receiver pair in the powder supply exit 404, and/or within the cylindrical housing portion 421 may be processed by a controller to continuously adjust the output to the motor connected to the rotatable metering roller 410 and/or the ultrasonic transducers on the powder distribution member 432. Thus, by controlling the rotation of the metering roller 410 and/or powder distribution member 432, the powder 419 can be precisely distributed along the powder bed 403 at location 404 and/or at the build component as the recoater travels in direction 401 across the powder bed. As shown in The rotatable metering roller 510 may be connected to motor (e.g. a stepper motor). Accordingly, powder 519 may be in contact with the roller 510 through passage 522. Thus, when the roller 510 is rotated via the motor, powder is conveyed along the surface of the roller 510 to the powder distribution member 538. As shown in As mentioned above, the recoater apparatus 500 shown in The recoater apparatus may further include an aft sweep strip 506 and a forward sweep strip 507. The sweep strips 506 and 507 may be positioned such that the powder distributed by the distribution member 505 to the powder bed proximal to location 540 is between the sweep strips 506 and 507. Thus, the sweep strips 506 and 507 may function as a shield to block gas flow from interfering with the powder distribution process. Optionally, the sweep strips may be adjustable along the z-axis either through height (i.e. z-axis) adjustment of the recoater apparatus 500, or the sweep strips may be individually adjustable along the z-axis through an individual adjustment mechanism on each of the forward and aft sweep strips. Further, the height of each of the forward sweep strip 507 and aft sweep strip 506 may be adjustable through tilting of the recoater apparatus 500 in combination with the abovementioned height adjustment of the recoater apparatus 500. As discussed below, the sweep strips may be adjusted using any one of or combination of the aforementioned methods such that the sweep strips do not contact or minimally contact the powder bed while effectively blocking gas flow which may interfere with the powder distribution process. Further, the sweep strip height may be controlled to sweep powder across the powder bed. The recoater apparatus 500 may further include several sensors to assure that powder is precisely metered and distributed along the surface of the powder bed and/or the build component in the powder bed. As an example, the recoater apparatus may include a photo-emitter-receiver pair (not shown) to sense the consistency and uniformity of powder flow through the passage 522, the powder supply exit proximal to location 548, within the fluidizing portion 550, and/or within the cylindrical housing portion 521. It is noted that the abovementioned sensor locations may be used individually or in any combination to determine the amount of powder being supplied to the powder bed. Sensors may also be located at the fluidizing gas inlet and outlet to so that the supply of fluidizing gas may monitored and controlled. Further, it is noted that a plurality of sensors may be located in each of the above-mentioned locations, for example a plurality of sensors may be located along the y-axis direction to assure detect the amount of powder being supplied along the width of the powder bed along the length of the recoater apparatus 500. The sensors may also include an aft z-height sensor array 516 and a forward z-height sensor array 517 to precisely monitor the height of the recoater apparatus 500 with respect to the powder bed and/or to determine a height difference and/or clearance between the sweep strips 507 and 506 and powder bed at the forward z-height sensor 517 at location 503 and the aft z-height sensor 516 at location 502, which may be used to determine the amount of powder to be provided by the recoater apparatus to the powder bed 502 through control of the metering wheel 510 and the distribution member 432. The forward z-height sensor array 517 and the aft z-height sensor array 516 may be capacitive proximity sensors. The forward z-height sensor array 517 and the aft z-height sensor array 516 may also include or be combined with any well-known sensors in the art usable to determine a height in a non-contact manner. The abovementioned forward z-height sensor array 517 and the aft z-height sensor array 516 may be used to adjust the height of the recoater apparatus 500 and/or may be used to adjust the quantity or distribution of powder to be supplied to the powder bed 502 through the powder supply exit 548. Based on the output of the abovementioned sensors, the forward sweep strip 507 and the aft sweep strip 506 may be adjusted such that the a bottom portion of the forward sweep strip 507 that is further from the apparatus than a top portion of the forward sweep strip 507 is offset with relation to the bottom portion of the aft sweep strip 506 (i.e. lower in the z-direction). In other words, because a layer of powder is supplied from the opening to the powder bed and/or component being built in the powder bed, it may be preferable to adjust the aft sweep strip 506 in the z-direction to compensate for the thickness of the layer of powder provided. If the recoater apparatus reverses direction (i.e. causing the aft sweep strip to become the forward sweep strip), it may be necessary to adjust the sweep strip height in a similar manner (i.e. the forward sweep strip lower in the z-direction that the aft sweep strip). Using any of the abovementioned techniques, it may be further preferable to adjust the sweep strip heights such that a clearance in the z-direction between the powder bed and/or build component and the sweep strips is less than 1 mm. The sweep strips 503 and/or 506 may also be configured to remove a quantity of powder from a build region. For example, while a build process progresses by solidifying powder, a portion of the build may begin to increase in height at a faster rate than another portion of the build. In other words, with reference to As discussed above, outputs from the forward z-height sensor array 517, aft z-height sensor array 516, photo-emitter-receiver pair in the passage 522, the photo-emitter-receiver pair in the powder supply exit 504, the fluidizing portion 550, the fluidizing gas inlet 543, the fluidizing gas outlet 539, and/or within the cylindrical housing portion 521 may be processed by a controller to continuously adjust the output to the motor connected to the rotatable metering roller 510, the supply of fluid to the fluidizing gas inlet 543 and/or the fluidizing gas outlet 539, and/or the ultrasonic transducers 536. Thus, by controlling abovementioned variables in powder distribution member 505, the powder 519 can be precisely distributed along the powder bed 502 at location in a vicinity of portion 540 and/or at the build component as the recoater 500 travels across the powder bed 502. This written description uses examples to disclose the invention, including the preferred embodiments, and also to enable any person skilled in the art to practice the invention, including making and using any devices or systems and performing any incorporated methods. The patentable scope of the invention is defined by the claims, and may include other examples that occur to those skilled in the art. Such other examples are intended to be within the scope of the claims if they have structural elements that do not differ from the literal language of the claims, or if they include equivalent structural elements with insubstantial differences from the literal language of the claims. Aspects from the various embodiments described, as well as other known equivalents for each such aspect, can be mixed and matched by one of ordinary skill in the art to construct additional embodiments and techniques in accordance with principles of this application. The present disclosure relates to systems, methods, and apparatuses for supplying powder to a powder bed during an additive manufacturing process. A recoater apparatus includes a powder reservoir and a powder distribution system for conveying powder from the powder reservoir to the powder bed. The recoater apparatus further includes at least two sweep strips, wherein at least one exit of the powder distribution system is located between the two sweep strips so as to shield the exit of the powder distribution system. 1. An apparatus for supplying a powder comprising:
a powder reservoir; a first sweep strip; a second sweep strip; and a powder distribution system comprising;
an inlet for receiving powder from the reservoir; an outlet for supplying powder received from the inlet, the outlet being located between the first sweep strip and the second sweep strip. 2. The apparatus for supplying a powder of a housing portion in fluid communication with the inlet; a roller rotatable around an axis within the housing, the axis extending in a first direction, wherein the roller is configured to convey powder from the inlet. 3. The apparatus for supplying a powder of 4. The apparatus for supplying a powder of 5. The apparatus for supplying a powder of 6. The apparatus for supplying a powder of a first height detector for detecting a height of the apparatus from a powder bed at a first location, wherein the quantity of powder supplied at the outlet is controlled based on an output from the first height detector. 7. The apparatus for supplying a powder of a second height detector for detecting a height of the apparatus from a powder bed at a second location different from the first location, wherein the quantity of powder supplied at the outlet is controlled based on an output from the first height detector and the second height detector. 8. The apparatus for supplying a powder of a powder distribution member having a plurality of openings for supplying powder to the outlet, wherein powder is supplied to the distribution member by the metering roller. 9. The apparatus for supplying a powder of 10. The apparatus for supplying a powder of 11. The apparatus for supplying a powder of a fluidizing gas inlet; a fluidizing gas outlet; a fluidizing powder device having a plurality of openings and an overflow portion for supplying powder to the outlet, wherein the fluidizing gas is supplied from the fluidizing gas inlet through the plurality of openings, wherein the fluidized powder overflows from the overflow portion to the outlet. 12. The apparatus for supplying a powder of 13. The apparatus of 14. The apparatus of 15. The apparatus of a top portion connected to the apparatus and a bottom portion further from the apparatus than the top portion, wherein the second sweep strip further comprises: top portion connected to the apparatus and a bottom portion further from the apparatus than the top portion, wherein the bottom portion of one of the first and second sweep strips extends further below the apparatus than the other of the first and second sweep strips. 16. The apparatus of 17. The apparatus of 18. A method for supplying a powder comprising:
storing powder in a powder reservoir, conveying the powder from the powder reservoir to a powder outlet located between a first sweep strip and a second sweep strip via a powder distribution system. 19. The method of supplying a powder of conveying the powder from the powder reservoir to at least one of a powder bed and a fused powder region; setting the sweep strip height of at least one of the sweep strips such that the clearance between the at least one of the powder bed and fused powder region is less than 1 mm. 20. The method of supplying a powder of conveying the powder from the powder reservoir to supply a layer of powder to the at least one of a powder bed and fused powder region along a first direction; setting the sweep strip height such that the forward most sweep strip along the first direction is offset with respect to the rearward most sweep strip along the first direction, wherein the rearward most sweep strip is offset higher than the forward most sweep strip to compensate for the height of the powder layer provided to the at least one of a powder bed and fused powder region. 21. The method for supplying a powder of controlling the quantity of powder supplied at the outlet based on a distance between at least one of the first sweep strip and second sweep strip and the at least one of a powder bed and fused region, wherein the distance is determined based on the output from a first height detector. 22. The method for supplying a powder of INTRODUCTION
BACKGROUND
BRIEF DESCRIPTION OF THE INVENTION
BRIEF DESCRIPTION OF THE DRAWINGS
DETAILED DESCRIPTION OF THE INVENTION


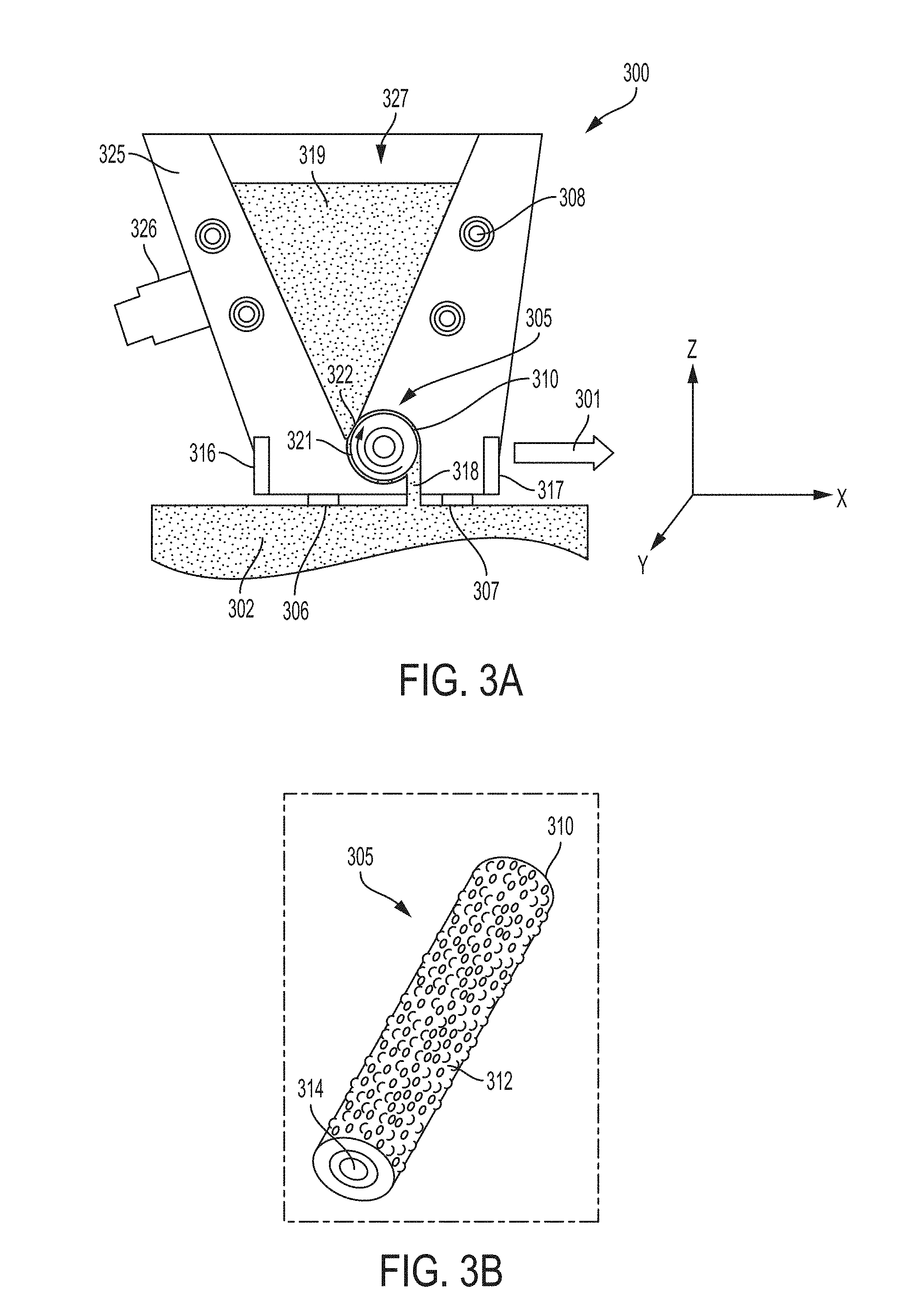
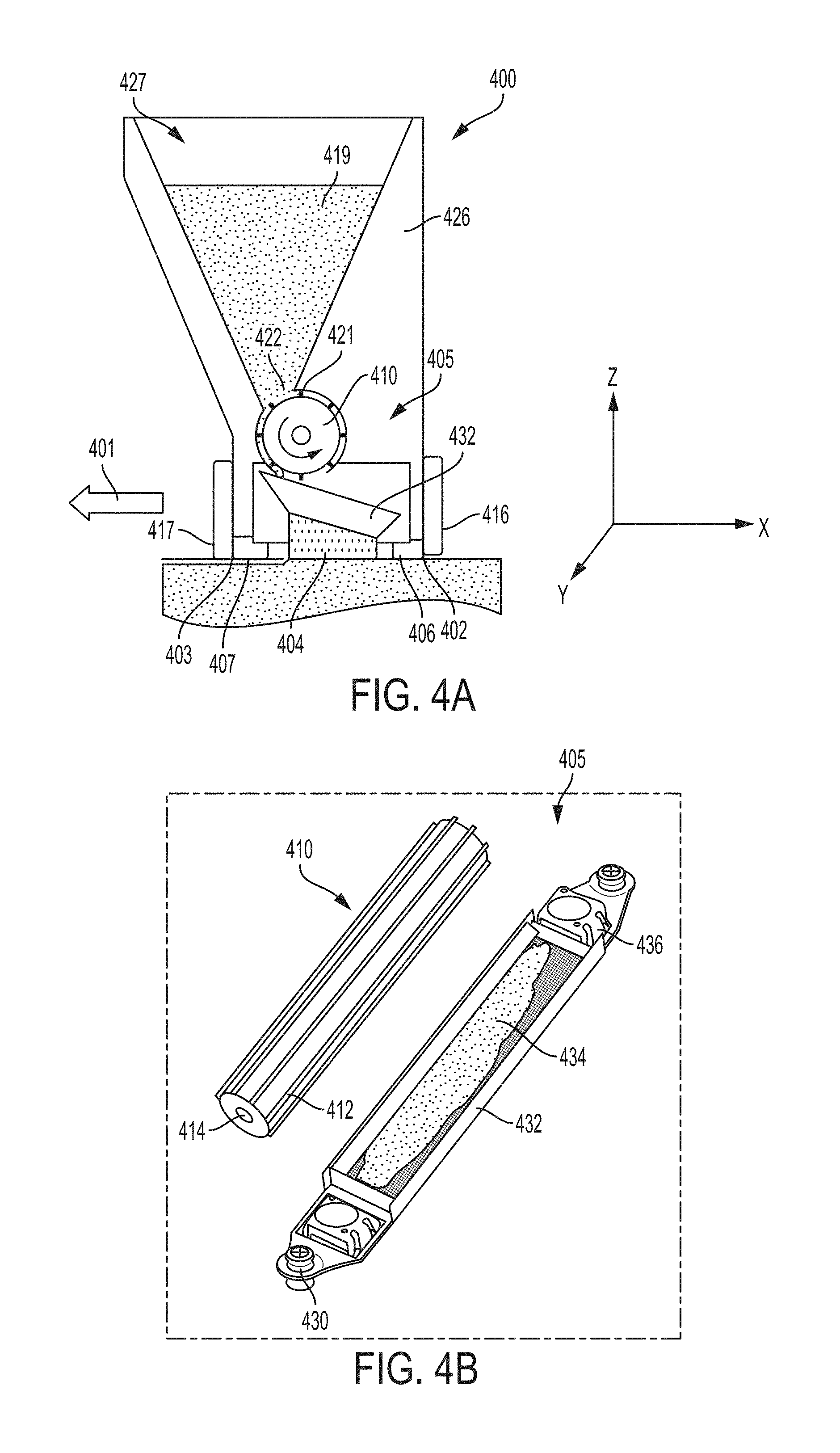
