PRODUCTION LINE FOR MACHINING METAL SHEETS
Die Erfindung betrifft eine Produktionslinie zum Bearbeiten von Blechtafeln gemäß dem Oberbegriff des Anspruches 1. Durch die Durch die Der Erfindung liegt die Aufgabe zugrunde, eine Produktionslinie zum Bearbeiten von Blechtafeln zu schaffen, wobei in einer Massenproduktion von Blechtafeln mit einer Produktionsgeschwindigkeit von mehreren tausend Blechtafeln pro Stunde deren störungsfreier Einzeltransport durch die Produktionslinie hindurch sichergestellt ist. Die Aufgabe wird erfindungsgemäß durch die Merkmale des Anspruches 1 gelöst. Die abhängigen Ansprüche betreffen vorteilhafte Ausgestaltungen und/oder Weiterbildungen der gefundenen Lösung. Die mit der Erfindung erzielbaren Vorteile bestehen insbesondere darin, dass in einer Massenproduktion von Blechtafeln mit einer Produktionsgeschwindigkeit von mehreren tausend Blechtafeln pro Stunde deren störungsfreier Einzeltransport durch die Produktionslinie hindurch z. B. mit einer Überwachung des Synchronpunktes und/oder ohne ein unbeabsichtigtes Auflaufen und/oder Verkanten oder Verhaken von aufeinanderfolgend transportierten Blechtafeln sichergestellt ist. Ein Ausführungsbeispiel der Erfindung ist in den Zeichnungen dargestellt und wird im Folgenden näher beschrieben, wodurch noch weitere Vorteile der gefundenen Lösung aufgezeigt werden. Es zeigen:
Im industriellen Blechdruck werden Blechtafeln 08 ( In der Praxis hat sich gezeigt, dass mit einer hohen Geschwindigkeit durch die Produktionslinie 01 transportierte Blechtafeln 08 bei ihrem Transport zu Störungen neigen, und zwar insbesondere aufgrund von Reibungseffekten in ihrer jeweiligen Transportebene und/oder zufolge von Verschmutzungen auf ihrem jeweiligen Transportweg. Störende Reibungseffekte treten auch z. B. bei übermäßigem Verschleiß oder bei Alterung eines für den Transport der Blechtafeln 08 verwendeten Riementransportsystems auf. Jeder dieser unerwünschten Einflüsse kann dazu führen, dass z. B. mehrere nacheinander durch die Produktionslinie 01 transportierte Blechtafeln 08 unbeabsichtigt aufeinander auflaufen und/oder sich verkanten oder verhaken. Blechtafeln 08 können in ihrer jeweiligen Transportebene auch aus ihrem linearen Transportweg herausgedreht werden und dadurch z. B. eine Kollision mit anderen Blechtafeln 08 und/oder einem Bauteil von einer der Maschineneinheiten dieser Produktionslinie 01 verursachen. Und selbst wenn sich keine Kollision ereignet, so kann sich trotz konstanter Produktionsgeschwindigkeit in der Produktionslinie 01 zumindest ein freier Abstand zwischen aufeinanderfolgend transportierten Blechtafeln 08, d. h. der Abstand zwischen der Hinterkante einer ersten Blechtafel 08 und der Vorderkante einer nächsten nachfolgenden zweiten Blechtafel 08 verändern, so dass sich ein sogenannter Synchronpunkt verschiebt, was bedeutet, dass sich insbesondere die Vorderkantenlage einer Blechtafel 08 relativ zu in verschiedenen Maschineneinheiten der Produktionslinie 01 angeordneten Einrichtungen verschiebt. Durch eine derartige Verschiebung des Synchronpunktes können beim Transport der betreffenden Blechtafel 08 durch die Produktionslinie 01 z. B. in Verbindung mit der Blechdruckmaschine 03 und/oder Blechlackiermaschine 06 vorgesehene Beschleunigungs- und/oder Verzögerungsvorgänge außer Tritt geraten, wodurch insbesondere ein Zusammenspiel von im Produktionsprozess miteinander verketteter Maschineneinheiten wie z. B. der Blechdruckmaschine 03 oder einer Blechlackiermaschine 06, des mindestens einen Transportmoduls 04, der Beladestation 02, des Durchlauftrockners 17 und der Entladestation 07 gestört wird. Solche Ereignisse führen zu einer unerwünschten Produktionsbeeinträchtigung und/oder zu Beschädigungen bis hin zu einem Produktionsausfall durch einen störungsbedingten Maschinenstillstand. Zumindest das jeweilige Transportmodul 04 und/oder die Beladestation 02 und/oder die Entladestation 07 weisen jeweils als eine ihrer Baueinheiten mindestens eine eigene Transportvorrichtung 09 ( Der jeweilige Transportriemen 11 der Transportvorrichtung 09 ist vorzugsweise an Umlenkrollen umlaufend mit seinem jeweiligen Lasttrum längs zur Transportebene derart angeordnet, dass jede auf dem jeweiligen Lasttrum der Transportriemen 11 aufliegende und auf den betreffenden Transportriemen 11 z. B. auch gehaltene Blechtafel 08 relativ zur betreffenden ortsfest angeordneten Platte 12 entlang einer linearen Transportstrecke transportierbar ist, wobei sich diese Transportstrecke z. B. zumindest über die Länge L12 der Transportvorrichtung 09 erstreckt. Die zum Halten einer auf dem betreffenden Transportriemen 11 aufliegenden Blechtafel 08 erforderliche Haltekraft erfolgt z. B. durch einen Sog, wobei der erforderliche Sog z. B. durch einen unterhalb der Platte 12 der Transportvorrichtung 09 angeordneten Saugkasten in Verbindung mit einer daran angeschlossenen Saugpumpe erzeugt wird. Die Saugpumpe ist vorzugsweise bedarfsweise angeschaltet und/oder abgeschaltet oder zumindest anschaltbar und/oder abschaltbar. Alternativ oder zusätzlich können zum Halten einer auf dem betreffenden Transportriemen 11 aufliegenden Blechtafel 08 auch magnetische Haltemittel vorgesehen sein, die vorzugsweise ebenfalls schaltbar sind. Die betreffende Transportvorrichtung 09 kann auch mehrere, z. B. zwei jeweils parallel zueinander angeordnete Transportriemen 11 aufweisen. In der Produktionslinie 01 sind vorzugsweise mindestens zwei dieser Transportvorrichtungen 09 jeweils separat voneinander, d. h. als jeweils eigenständige Baueinheiten in verschiedenen Maschineneinheiten angeordnet, wobei jeweils eine dieser Transportvorrichtungen 09 insbesondere in der Beladestation 02 oder in der Entladestation 07 angeordnet ist. Die Transportriemen 11 der betreffenden Transportvorrichtungen 09 sind jeweils von einem elektrischen Antrieb 16 derart angetrieben, dass in unterschiedlichen Transportvorrichtungen 09 angeordnete Transportriemen 11 in ihrer jeweiligen Umlaufgeschwindigkeit vorzugsweise jeweils zueinander synchronisiert sind, so dass von diesen Transportriemen 11 transportierte Blechtafeln 08 jeweils mit von zulässigen geringfügigen Toleranzen abgesehen betragsgleicher Lineargeschwindigkeit transportiert werden, wobei diese Blechtafeln 08 auf diesen Transportriemen 11 jeweils z. B. durch Sog und/oder magnetisch gehalten sind. Dabei erfolgt der Transport der auf den Transportriemen 11 aufliegenden Blechtafeln 08 in deren Transportebene, d. h. insbesondere mit Bezug auf die Platte 12 der Transportvorrichtung 09 jeweils weitestgehend auf einem Luftkissen schwebend und ist damit nahezu reibungsfrei, zumindest aber äußerst reibungsarm und praktisch schlupffrei, denn die jeweiligen Blechtafeln 08 stehen nur mit den vergleichsweise schmalen Transportriemen 11 in einem Berührungskontakt. Der jeweilige elektrische Antrieb 16 der betreffenden Transportvorrichtungen 09 ist z. B. jeweils als ein Elektromotor ausgebildet und vorzugsweise jeweils mit einer den einzelnen Maschineneinheiten übergeordneten Maschinensteuerung 34 der Produktionslinie 01 zumindest datentechnisch verbunden, so z. B. mit einem Leitstand dieser Produktionslinie 01. In unterschiedlichen Transportvorrichtungen 09 angeordnete Transportriemen 11 sind von ihrem jeweiligen elektrischen Antrieb 16 vorzugsweise derart angetrieben, dass sie z. B. kontinuierlich, insbesondere in einem Gleichlauf umlaufen. Alternativ können diese Transportriemen 11 auch getaktet angetrieben sein. Es kann auch vorgesehen sein, dass die Transportriemen 11 einer z. B. in der Beladestation 02 angeordneten Transportvorrichtung 09 vorzugsweise von der Maschinensteuerung 34 getaktet und/oder eine auf ihren Transportriemen 11 aufliegende Blechtafel 08 in ihrer Lineargeschwindigkeit zeitweise abbremsend angetrieben sind, wohingegen die Transportriemen 11 einer z. B. in der Entladestation 07 angeordneten Transportvorrichtung 09 vorzugsweise von der Maschinensteuerung 34 getaktet und/oder eine auf ihren Transportriemen 11 aufliegende Blechtafel 08 in ihrer Lineargeschwindigkeit zeitweise beschleunigend angetrieben sind. Der Synchronlauf der in unterschiedlichen Transportvorrichtungen 09 angeordneten Transportriemen 11 und damit vor allem der Synchronlauf der von diesen Transportriemen 11 gehaltenen Blechtafeln 08 ist insbesondere bei einem Hochlauf oder bei einem Runterfahren der Maschineneinheiten dieser Produktionslinie 01 von Vorteil. Für einen störungsfreien Transport der Blechtafeln 08 durch die Produktionslinie 01 muss der Synchronlauf der in unterschiedlichen Transportvorrichtungen 09 angeordneten Transportriemen 11 und damit auch der Blechtafeln 08 aber insbesondere auch an den Übergängen zwischen den am Produktionsprozess beteiligten Maschineneinheiten dieser Produktionslinie 01 sichergestellt sein. Die Platte 12 der betreffenden Transportvorrichtung 09 weist an beiden Seiten ihres jeweiligen Mittenbereichs M jeweils einen riemenfreien Randbereich R1; R2 auf, wobei diese Randbereiche R1; R2 eine sich quer zur Transportrichtung T der Blechtafeln 08 erstreckende vorzugsweise gleich große Breite aufweisen und bezüglich einer Längserstreckung der betreffenden Transportvorrichtung 09 vorzugsweise symmetrisch angeordnet sind. Zumindest in den riemenfreien Randbereichen R1; R2, z. B. aber auch zusätzlich im Mittenbereich M der betreffenden Transportvorrichtung 09 sind jeweils mindestens ein Düsenfeld 13 mit jeweils mehreren Düsen 14 ausgebildet. Die dort angeordneten Düsen 14 sind derart betrieben, dass aus ihnen zur Ausbildung des Luftkissens jeweils Blasluft gegen die Unterseite einer auf dem mindestens einen Transportriemen 11 der betreffenden Transportvorrichtung 09 aufliegenden und auf dem oder den betreffenden Transportriemen 11 gehaltenen Blechtafel 08 geblasen wird. In einer vorteilhaften Ausführung sind zumindest einige der Düsen 14 der Düsenfelder 13 z. B. jeweils als Venturidüsen ausgebildet. In den jeweiligen Düsenfeldern 13 sind z. B. eine erste Teilmenge einzelner Düsen 14 und/oder eine zweite Teilmenge einzelner Düsen 14 jeweils derart angeordnet, dass die erste Teilmenge von Düsen 14 die Blasluft jeweils in Transportrichtung T der Blechtafeln 08 unter einem spitzen Winkel schräg nach außen gerichtet, d. h. jeweils in Richtung des nächstgelegenen sich längs zur Transportrichtung T der Blechtafeln 08 erstreckenden Randes der betreffenden Transportvorrichtung 09 und/oder die zweite Teilmenge von Düsen 14 die Blasluft jeweils senkrecht nach oben ausblasen. Zusammenfassend ergibt sich eine Produktionslinie 01 zum Bearbeiten von Blechtafeln 08, wobei diese Produktionslinie 01 mehrere verschiedene Maschineneinheiten aufweist, wobei mindestens eine dieser Maschineneinheiten als ein Durchlauftrockner 17 ausgebildet ist. Der Durchlauftrockner 17 ist derart ausgebildet, dass zu trocknende Blechtafeln 08 diesen Durchlauftrockner 17 vertikal aufgerichtet und i. d. R. beabstandet voneinander durchlaufen, wobei dem Durchlauftrockner 17 eine in einer Transportebene einer Transportvorrichtung 09 flach liegende Blechtafeln 08 vertikal aufrichtende Beladestation 02 vorgeordnet und eine durch den Durchlauftrockner 17 vertikal aufgerichtet transportierte Blechtafeln 08 in einer Transportebene einer Transportvorrichtung 09 flach ablegende Entladestation 07 nachgeordnet ist. Der Abstand zwischen benachbart durch den Durchlauftrockner 17 vertikal aufgerichtet transportierte Blechtafeln 08 beträgt nur wenige Zentimeter, z. B. zwischen 1 cm und 5 cm, insbesondere weniger als 3 cm. Auf jeweils mindestens einer Oberfläche der im Durchlauftrockner 17 zu trocknenden Blechtafeln 08, d. h. einseitig oder beidseitig, wurde zuvor in mindestens einer als Blechdruckmaschine 03 und/oder in mindestens einer als eine Blechlackiermaschine 06 ausgebildeten Maschineneinheit jeweils mindestens ein Druckfluid aufgetragen. Die bedruckten und/oder lackierten Blechtafeln 08 werden dem Durchlauftrockner 17 nacheinander insbesondere einzeln zugeführt, wobei diese Blechtafeln 08 aus ihrer in dieser Produktionslinie 01 ansonsten in ihrer Transportebene flach liegenden Position in der Beladestation 02 vor ihrem Zuführen zum Durchlauftrockner 17 vertikal aufgerichtet werden. Als vertikale Aufrichtung gilt hier z. B. eine Aufrichtung der einzelnen zuvor in der Transportebene der jeweiligen Transportvorrichtung 09 flach liegenden Blechtafeln 08 mit einer Toleranz von weniger als ±30°, vorzugsweise von weniger als ±15° jeweils zur Lotrechten, wobei diese Lotrechte vorzugsweise auf die Transportebene der jeweiligen Transportvorrichtung 09 bezogen ist. Nach ihrem vertikal aufgerichteten Transport durch den Durchlauftrockner 17 werden die Blechtafeln 08 in der Entladestation 07 nacheinander insbesondere einzeln wieder in der Transportebene einer Transportvorrichtung 09 flach abgelegt. In der Produktionslinie 01 ist in Transportrichtung T zu bearbeitender Blechtafeln 08 zwischen dem Durchlauftrockner 17 und der Entladestation 07 des Weiteren insbesondere eine Kühlzone 18 ( In der bevorzugten Ausführung sind mindestens zwei Maschineneinheiten dieser Produktionslinie 01 jeweils in einem eigenen Gestell 19; 21 ausgebildet. Dabei weisen mindestens zwei dieser Maschineneinheiten jeweils mindestens eine Transportvorrichtung 09 zum Transportieren mindestens einer jeweils insbesondere einzeln in der jeweiligen Transportebene flach aufliegenden Blechtafel 08 auf, wobei jede dieser separat voneinander angeordneten Transportvorrichtungen 09 für den Transport der betreffenden Blechtafel 08 jeweils mindestens einen Transportriemen 11 aufweist. Dabei sind die Transportriemen 11 der betreffenden Transportvorrichtungen 09 jeweils vorzugsweise von einem elektrischen Antrieb 16 insbesondere derart angetrieben, dass in unterschiedlichen Transportvorrichtungen 09 angeordnete Transportriemen 11 in ihrer jeweiligen Umlaufgeschwindigkeit jeweils zueinander synchronisiert sind, so dass von diesen Transportriemen 11 transportierte Blechtafeln 08 jeweils mit zumindest nahezu betragsgleicher, d. h. von geringfügigen zulässigen Toleranzen abgesehen gleicher Lineargeschwindigkeit transportiert werden. In der Transportebene der auf den Transportriemen 11 flach aufliegenden Blechtafeln 08 ist unterhalb dieser Blechtafeln 08 vorzugsweise ein Luftkissen ausgebildet und diese Blechtafeln 08 sind in ihrer Transportebene durch das Luftkissen schwebend angeordnet. In der Produktionslinie 01 sind die in Transportrichtung der bearbeiteten oder zu bearbeitenden Blechtafeln 08 hintereinander angeordneten Maschineneinheiten der Beladestation 02, des Durchlauftrockners 17, der Kühlzone 18 und der Entladestation 07 stets miteinander verkettet, und zwar nicht nur durch eine funktionale, d. h. steuerungstechnische Verkettung der betreffenden Transportvorrichtungen 09, sondern auch physisch, d. h. mechanisch durch mindestens ein für den Transport der Blechtafeln 08 vorgesehenes Zugmittel 29 z. B. in Form mindestens einer durch vorzugsweise alle diese Maschineneinheiten hindurchlaufenden Kette. Dabei greift das mindestens eine die betreffenden Maschineneinheiten durchlaufende Zugmittel 29 sowohl an den schwenkbaren Drahtrahmen 22 der Beladestation 02 als auch an den schwenkbaren Drahtrahmen 22 der Entladestation 07 an, so dass eine Kopplung des betreffenden Drahtrahmens 22 mit dem Zugmittel 29 erfolgt, wobei das Zugmittel 29 z. B. mindestens ein Koppelelement 37 aufweist ( Insbesondere bei einer hohen Produktionsgeschwindigkeit von mehreren tausend Blechtafeln 08 pro Stunde, z. B. von mindestens 6.000 Blechtafeln 08 pro Stunde, und/oder bei einem großen Format der in der Produktionslinie 01 zu bearbeitenden Blechtafeln 08 von z. B. mehr als 700 mm x 1.000 mm und/oder bei einer geringen Blechdicke der Blechtafeln 08 von z. B. weniger als 0,3 mm wirken auf die betreffenden Blechtafeln 08 in dem Moment, in dem sie durch den jeweiligen Drahtrahmen 22 der Transportvorrichtung der Beladestation 02 angehoben werden, erhöhte Beschleunigungskräfte. Diese Beschleunigungskräfte führen dazu, dass sich unter den vorgenannten Umständen labil ausgebildete Ecken der Blechtafeln 08, die nicht auf dem jeweiligen Drahtrahmen 22 aufliegen, im Bereich der Hinterkante der von den Drahtrahmen 22 angehobenen Blechtafeln 08 infolge der Massenträgheitsmomente der Schwerkraft folgend nach unten verbiegen und somit in den Bereich des Transportweges insbesondere einer nachfolgenden Blechtafel 08 gelangen. Da die Ecken der angehobenen Blechtafel 08 in diesem Bereich nicht durch den jeweiligen Drahtrahmen 22 der Transportvorrichtung der Beladestation 02 unterstützt sind, können diese deshalb durchhängen. Dies kann zu einer Kollision mit der Vorderkante derjenigen Blechtafel 08 führen, die der vom jeweiligen Drahtrahmen 22 gerade anzuhebenden Blechtafel 08 unmittelbar nachfolgt, was zur Folge hat, dass sich in der Produktionslinie 01 eine Produktionsunterbrechung und/oder ein Ausschuss von Blechtafeln 08 ergeben können. Zur Vermeidung dieser potentiellen Betriebsstörung wird eine Produktionslinie 01 zum Bearbeiten von Blechtafeln 08 vorgeschlagen, die eine Blechdruckmaschine 03 und/oder eine Lackiermaschine 06 aufweist, wobei in Transportrichtung T der Blechtafeln 08 nach der Blechdruckmaschine 03 und/oder der Lackiermaschine 06 eine Beladestation 02 und unmittelbar nach der Beladestation 02 ein Durchlauftrockner 17 zum Trocknen der bedruckten und/oder lackierten Blechtafeln 08 angeordnet sind. Dabei weist die Beladestation 02 mehrere jeweils um eine sich quer zur Transportrichtung T der transportierten Blechtafeln 08 erstreckende Rotationsachse 23 rotierende Drahtrahmen 22 auf, wobei diese Drahtrahmen 22 nacheinander die jeweils liegend der Beladestation 02 zugeführten Blechtafeln 08 jeweils insbesondere einzeln aus ihrer Transportebene hebend angeordnet sind, wobei jeder dieser Drahtrahmen 22 derart ausgebildet ist, dass er die Transportebene der Blechtafeln 08 in einem Bereich, in dem diese Blechtafeln 08 jeweils insbesondere einzeln der Beladestation 02 zugeführt werden, kreisförmig von unten nach oben durchfährt und mit dieser Schwenkbewegung eine der flach liegenden durch den Durchlauftrockner 17 zu transportierenden Blechtafeln 08 aufrichtet. Die Beladestation 02 weist zudem z. B. in in der Transportebene der Blechtafeln 08 längs zu deren Transportrichtung T ausgebildeten Randbereichen R1; R2 jeweils mindestens ein Düsenfeld 13 mit jeweils mehreren Düsen 14 auf, wobei dort angeordnete Düsen 14 derart betrieben sind, dass aus ihnen Blasluft jeweils vorzugsweise senkrecht nach oben gegen die Unterseite einer Blechtafel 08 geblasen wird. Zumindest eine Teilmenge von den die Blasluft jeweils vorzugsweise senkrecht nach oben ausblasenden Düsen 14 sind getaktet betrieben, wobei diese getaktet betriebenen Düsen 14 Blasluft ausstoßend eingeschaltet sind, während die betreffende Blechtafel 08 vom Drahtrahmen 22 übernommen und angehoben wird, und wobei diese Düsen 14 ausgeschaltet sind, bevor deren Blasluft die Vorderkante 46 derjenigen Blechtafel 08 erfasst, die der vom Drahtrahmen 22 gerade übernommenen und angehobenen Blechtafel 08 unmittelbar nachfolgt. In einer bevorzugten Ausführung sind die Blasluft jeweils vorzugsweise senkrecht nach oben ausblasenden Düsen 14 mit einem in seiner Stärke einstellbarem Blasdruck betrieben. Dabei ist die Stärke des Blasdrucks der die Blasluft jeweils vorzugsweise senkrecht nach oben ausblasenden Düsen 14 z. B. in Abhängigkeit von einer Produktionsgeschwindigkeit der in dieser Produktionslinie 01 zu bearbeitenden Blechtafeln 08 und/oder in Abhängigkeit von einem Format der in der Produktionslinie 01 zu bearbeitenden Blechtafeln 08 und/oder in Abhängigkeit von einer Blechdicke der in der Produktionslinie 01 zu bearbeitenden Blechtafeln 08 eingestellt oder zumindest einstellbar. Zur Einstellung der Stärke des Blasdrucks der die Blasluft jeweils vorzugsweise senkrecht nach oben ausblasenden Düsen 14 sind vorzugsweise ein ausgangsseitig mit diesen Düsen 14 und eingangsseitig mit einer Druckluftquelle 41 verbundenes Drosselventil 38, dessen Durchflussquerschnitt z. B. ferngesteuert, insbesondere an einer z. B. als ein Leitstand dieser Produktionslinie 01 ausgebildeten Maschinensteuerung 34 einstellbar ist, und ein Manometer 39 vorgesehen. Die Blasluft jeweils vorzugsweise senkrecht nach oben ausblasenden Düsen 14 sind insbesondere nur dann Blasluft ausstoßend eingeschaltet, wenn Blechtafeln 08 mit einer Produktionsgeschwindigkeit größer einer voreingestellten Mindestgeschwindigkeit durch die Produktionslinie 01 transportiert werden. Die Blasluft jeweils vorzugsweise senkrecht nach oben ausblasenden Düsen 14 sind z. B. bis zum Erreichen eines voreingestellten Mindestwertes für die Produktionsgeschwindigkeit der in dieser Produktionslinie 01 zu bearbeitenden Blechtafeln 08 und/oder für Blechtafeln 08 mit einem kleineren Format als ein voreingestelltes Mindestformat für die in der Produktionslinie 01 zu bearbeitenden Blechtafeln 08 und/oder für Blechtafeln 08 mit einer größeren Blechdicke als eine voreingestellte Mindestblechdicke für die in der Produktionslinie 01 zu bearbeitenden Blechtafeln 08 ausgeschaltet. Dadurch kann sichergestellt werden, dass die vorstehend beschriebene Betriebsart der Produktionslinie 01 nur dann aktiv ist, wenn sich labil ausgebildete Ecken der Blechtafeln 08 tatsächlich verbiegen. So können eine Betriebsstörung in der Produktionslinie 01 und/oder eine Betriebsunterbrechung und/oder eine Produktion von Ausschuss an Blechtafeln 08 vermieden werden. Zudem ist die beschriebene Lösung sowohl an einer neuen Produktionslinie 01 als auch zur Nachrüstung in einer bereits bei einem Kunden im Einsatz befindlichen Produktionslinie 01 verwendbar. Wie bereits erwähnt, kann sich selbst bei konstanter Produktionsgeschwindigkeit in der Produktionslinie 01 infolge von Störeinflüssen wie z. B. einem sich ändernden Traktionsverhalten zwischen der jeweiligen zu transportierenden Blechtafel 08 und dem mindestens einen die betreffende Blechtafel 08 tragenden Transportriemen 11 der freie Abstand zwischen aufeinanderfolgend transportierten Blechtafeln 08, d. h. der Abstand zwischen der Hinterkante einer ersten Blechtafel 08 und der Vorderkante 46 einer der ersten Blechtafel 08 unmittelbar nachfolgenden zweiten Blechtafel 08 verändern, so dass sich der Synchronpunkt verschiebt, was bedeutet, dass sich insbesondere auch die Vorderkantenlage einer der Beladestation 02 aktuell zugeführten Blechtafel 08 relativ zu einem dieser Blechtafel 08 zugewandten Ende desjenigen Drahtrahmens 22 der Transportvorrichtung dieser Beladestation 02 verschiebt, der zur Übernahme der aktuell zugeführten Blechtafel 08 vorgesehen ist und sich gerade aufgrund seiner Schwenkbewegung in denjenigen Bereich bewegt, in welchem er die aktuell der Beladestation 02 zugeführte Blechtafel 08 übernehmen soll. Denn alle der Beladestation 02 zugeführten Blechtafeln 08 müssen nacheinander jeweils insbesondere einzeln von einem der mehreren jeweils um die Rotationsachse 23 rotierenden Drahtrahmen 22 zuverlässig übernommen und infolge der Schwenkbewegung des jeweiligen Drahtrahmens 22 rechtzeitig angehoben werden, bevor eine der aktuell angehobenen Blechtafel 08 unmittelbar nachfolgende Blechtafel 08 in den Wirkbereich eines weiteren Drahtrahmens 22 einläuft. Ansonsten kommt es zu Störungen im Transport der Blechtafeln 08 und in der Folge zu Produktionsunterbrechungen in der Produktionslinie 01. Zur Vermeidung dieser Störungsursache wird - wie aus der In einer bevorzugten Ausführung ist ein mit der Steuereinheit 44 signaltechnisch verbundener, die Schwenkbewegung der Drahtrahmen 22 um die Rotationsachse 23 antreibender z. B. als ein elektrischer Motor ausgebildeter Antrieb 47 vorgesehen, wobei die Steuereinheit 44 im Fall einer außerhalb zulässiger Toleranzgrenzen liegenden Abweichung des Istwertes vom Sollwert zumindest diesen Antrieb 47 derart steuernd ausgebildet ist, dass derjenige Drahtrahmen 22, der für die Übernahme einer nächsten der Beladestation 02 zugeführten Blechtafel 08 vorgesehen ist, zu einem solchen Zeitpunkt in die Transportebene dieser nächsten Blechtafel 08 schwenkt, so dass für diese nächste Blechtafel 08 der Istwert der Zeitdifferenz ΔT wieder innerhalb der zulässigen Toleranzgrenzen liegt. Die zulässigen Toleranzgrenzen liegen z. B. im einstelligen Prozentbereich vom Sollwert oder auch darunter. In einer besonders bevorzugten Ausführung ist der den Drahtrahmen 22 um die Rotationsachse 23 schwenkende Antrieb 47 mit dem das Zugmittel 29 antreibenden Antrieb 32 identisch, wobei das Zugmittel 29 zumindest die Beladestation 02 und den ihr nachgeordneten Durchlauftrockner 17 durchlaufend angeordnet ist. Diese letztere Ausführung ist dann sehr vorteilhaft, wenn das Zugmittel 29 an dem betreffenden schwenkbaren Drahtrahmen 22 der Beladestation 02 angreifend und eine vorzugsweise mechanische Kopplung des betreffenden Drahtrahmens 22 mit dem betreffenden Zugmittel 29 herstellend ausgebildet ist. Die Steuereinheit 44 kann derart ausgebildet sein, dass sie mehrere Istwerte für eine Zeitdifferenz ΔT zwischen dem ersten Zeitpunkt und dem zweiten Zeitpunkt ermittelt und einen nicht plausiblen Istwert aussortiert, bevor sie die Istwerte mit dem für die Zeitdifferenz ΔT vorgegebenen Sollwert vergleicht. Die Steuereinheit 44 kann ferner vorzugsweise derart ausgebildet sein, dass sie auch auf dem Antrieb 47 vorgelagerte Komponenten der Produktionslinie wie z. B. die Beladestation 02 oder die Lackiermaschine 06 oder auf eine auf mehrere Maschineneinheiten der Produktionslinie wirkende virtuelle Antriebsachse wirkt. Die beschriebene Lösung erleichtert die Einstellung des optimalen Synchronpunkts für den Zulauf von Blechtafeln 08 zur Belademaschine 02 bei veränderten Produktionsbedingungen. Sie hilft auch, eine Kollision von Blechtafeln 08 mit den Drahtrahmen 22 zu vermeiden, wodurch wiederum Produktionsunterbrechungen und Ausschuss von Blechtafeln 08 vermieden wird. Außerdem besteht für diese Lösung eine Möglichkeit zur Nachrüstung an Altanlagen. Wie bereits erläutert, befindet sich eine hinsichtlich des Produktionsprozesses leider sehr störanfällige Stelle in der Produktionslinie 01 an der dem Durchlauftrockner 17 vorgeordneten Belademaschine 02. Denn jede der durch die Produktionslinie 01 transportierten Blechtafeln 08 muss an der Belademaschine 02 durch einen der Drahtrahmen 22 rechtzeitig übernommen und angehoben werden, bevor eine nächste Blechtafel 08 in den Schwenkbereich der Drahtrahmen 22 einläuft. Gelingt dies nicht, stößt mindestens eine der einer gerade aufgenommenen Blechtafel 08 nachfolgenden Blechtafeln 08 an das der Vorderkante dieser Blechtafeln 08 zugewandte Ende desjenigen Drahtrahmens 22, der die unmittelbar vorausgegangene Blechtafel 08 aufgenommen hat. Bedauerlicherweise kann eine solche Kollision und damit eine Störung im Produktionsprozess dieser Produktionslinie 01 sogar dann auftreten, wenn der Synchronpunkt zur vorgelagerten Blechdruckmaschine 03 oder Blechlackiermaschine 06 optimal eingestellt ist. Gleichzeitig wirken im Schwenkbereich des jeweiligen Drahtrahmens 22 der Belademaschine 02 die vergleichsweise höchsten Kräfte auf den betreffenden Drahtrahmen 22, wobei jeder dieser Drahtrahmen 22 aufgrund seiner filigranen Konstruktion jeweils flexibel ausgebildet ist. Zufolge dieser flexiblen Ausbildung der Drahtrahmen 22 kann es vorkommen, dass einer dieser eigentlich um die Rotationsachse 23 rotierende Drahtrahmen 22 in einer Position verharrt, die sich in der Transportebene der Blechtafeln 08 zu einem Zeitpunkt befindet, zu dem der betreffende Drahtrahmen 22 gerade eine der Belademaschine 02 zugeführte Blechtafel 08 übernommen hat. Wie bereits erwähnt, kann es dann zu einer Kollision von Blechtafeln 08 und damit zu einer Störung im Produktionsprozess dieser Produktionslinie 01 kommen. Eine Ursache für das verzögerte Anheben einer gerade durch einen der Drahtrahmen 22 aufgenommenen Blechtafel 08 kann darin bestehen, dass einzelne Drahtrahmen 22 leicht verbogen sind. Auch ein geringfügiges Spiel von Drahtrahmen 22 in dem z. B. jeweils als eine Aufnahmebohrung ausgebildeten Koppelelement 37 am durch die Belademaschine 02 und den ihr nachgeordneten Durchlauftrockner 17 hindurchlaufenden als eine Transportkette ausgebildeten Zugmittel 29 in Folge von Verschleiß oder Fertigungsungenauigkeiten kann zu einem verzögerten Anheben von einzelnen Drahtrahmen 22 führen. Ebenso können geringe Unregelmäßigkeiten in der Führung oder in der Umlenkung des Zugmittels 29 dazu führen, dass das Anheben der Drahtrahmen 22 ungleichmäßig und ruckelnd erfolgt und einzelne Blechtafeln 08 dadurch verspätet angehoben werden. Die angeführten Ursachen für eine Betriebsstörung treten insbesondere dann deutlich zutage, wenn obendrein plötzliche Lastwechsel und Belastungen auf die Drahtrahmen 22 einwirken, wie dies durch das zusätzliche Gewicht der aufgenommenen Blechtafeln 08 zusammen mit den rückwirkenden Beschleunigungskräften an der Belademaschine 02 der Fall ist. Bei einer hohen Produktionsgeschwindigkeit von mehreren tausend Blechtafeln 08 pro Stunde, z. B. von mindestens 6.000 Blechtafeln 08 pro Stunde erhöhen sich naturgemäß ebenso wie bei schweren Blechtafeln 08 mit einer Masse von z. B. mehr als 2 Kilogramm die kurzzeitig auf die Drahtrahmen 22 wirkenden Kräfte zum Zeitpunkt der Aufnahme dieser Blechtafeln 08, was zu einer elastischen Verformung der flexiblen Drahtrahmen 22 und nachfolgend zu einer mechanischen Schwingung der Drahtrahmen 22 führt. Im schlimmsten Fall können diese Schwingungen die jeweils frisch bedruckte und/oder lackierte Oberfläche dieser Blechtafeln 08 beschädigen. Gleichzeitig verkürzen sich bei höheren Geschwindigkeiten die zur Verfügung stehende Zeiten für den Beladevorgang, was die Problematik von Verformungen der flexiblen Drahtrahmen 22 und/oder auftretende Schwingungen noch weiter verstärkt. Zur Verbesserung der Funktionssicherheit in der Belademaschine 02 und um dadurch einen weniger störanfälligen Betrieb der Produktionslinie 01 sicher zu stellen, wird vorgeschlagen, in der Belademaschine 02 für deren Drahtrahmen 22 eine Hebeeinrichtung vorzusehen. Diese Hebeeinrichtung hat den Vorteil, dass sie die flexiblen Drahtrahmen 22 beim Anheben einer übernommenen Blechtafel 08 jeweils abstützt und einen Teil der an dem betreffenden Drahtrahmen 22 angreifenden Beschleunigungskräfte übernimmt und damit eine elastische Verformung der Drahtrahmen 22 und ihr mechanisches Schwingen zumindest weitgehend verhindert. Eine solche Hebeeinrichtung trägt dazu bei, dass das Gewicht der Drahtrahmen 22 weiter reduziert werden kann, wodurch letztlich eine Energieeinsparung beim Durchlauftrockner 17 erzielt werden kann. Die ein Anheben einer von einem Drahtrahmen 22 übernommenen Blechtafel 08 unterstützende Hebeeinrichtung ist - wie aus der Eine zweite Ausführung der Hebeeinrichtung ist ebenfalls in der Bei einer dritten Ausführung der Hebeeinrichtung ist - wie in der Gemäß einer in den Ein wesentlicher Vorteil der genannten Hebeeinrichtung besteht darin, dass die flexiblen Drahtrahmen 22 nicht alleine die Kraft zur Anhebung der Blechtafeln 08 aufbringen müssen. Um den Transport der Blechtafeln 08 insbesondere durch den Durchlauftrockner 17 noch effizienter zu gestalten, wird vorgeschlagen, in der beschriebenen Produktionslinie 01 zum Bearbeiten von Blechtafeln 08 die Beladestation 02 derart auszubilden, dass ihr nacheinander zugeführte Blechtafeln 08 jeweils insbesondere einzeln in einem von mehreren in der Beladestation 02 lose bereit gestellten Drahtrahmen 22 angeordnet werden, und ein endlos umlaufendes zumindest den Durchlauftrockner 17 durchlaufendes Zugmittel 29 mit mindestens einem Koppelelement 37 vorzusehen, wobei das betreffende z. B. als eine Einhängelasche ausgebildete Koppelelement 37 an dem betreffenden eine der Blechtafeln 08 aufgenommenen Drahtrahmen 22 angreifend und eine Kopplung des betreffenden Drahtrahmens 22 mit dem Zugmittel 29 herstellend ausgebildet ist, wobei in dieser vorgeschlagenen effizienteren Ausgestaltung der Produktionslinie 01 im Betriebszustand des Durchlaufs der Drahtrahmen 22 durch den Durchlauftrockner 17 der betreffende die Blechtafel 08 aufgenommene Drahtrahmen 22 am Untertrum des Zugmittels 29 hängend gekoppelt und an seinem unteren Ende an einer Auflage 62 abstützend angeordnet ist, wobei der derart hängend und abstützend angeordnete Drahtrahmen 22 in einer Schrägstellung mit einem Winkel W im Bereich zwischen 10° und 45° gegenüber der Senkrechten angeordnet ist. Dabei kann die Schrägstellung des hängend und abstützend angeordneten Drahtrahmens 22 in seinem Betriebszustand des Durchlaufs durch den Durchlauftrockner 17 entlang der Transportstrecke durch diesen Durchlauftrockner 17 variierend ausgebildet sein und an unterschiedlichen Positionen dieser Transportstrecke voneinander verschiedene Winkel W annehmen. Der am Untertrum des Zugmittels 29 hängend zu koppelnde Drahtrahmen 22 weist z. B. einen Aufnahmebolzen zum Einklinken in die Einhängelaschen des Zugmittels 29 auf. Die jeweils das untere Ende des eine Blechtafel 08 aufgenommenen Drahtrahmens 22 abstützende Auflage 62 ist z. B. als eine fest installierte Schiene oder als ein mit dem Zugmittel 29 vorzugsweise synchron umlaufendes Tragsystem z. B. in Form eines Riemens ausgebildet. Die Schrägstellung des hängend und abstützend angeordneten Drahtrahmens 22 stellt die Stabilität der derart transportierten Blechtafeln 08 sicher, und zwar insofern, als dass diese Blechtafeln 08 bei der jeweiligen Schrägstellung weder einsinken noch ausbauchen. Die hier vorgeschlagene besonders effiziente Ausbildung der Produktionslinie 01 ist beispielhaft in der Diese Ausgestaltung der Produktionslinie 01 hat den Vorteil, dass im Unterschied zu um eine Rotationsachse 23 rotierend ausgebildeten Drahtrahmen 22 die am Untertrum des Zugmittels 29 hängend gekoppelten Drahtrahmen 22 sehr filigran ausgebildet sein können, so dass nur eine sehr geringe Masse bewegt werden muss, was beim Betrieb der Produktionslinie 01 zu einer Energieeinsparung führt. Außerdem müssen die der Beladestation 02 zugeführten Blechtafeln 08 bei einem Transport mittels eines am Untertrum des Zugmittels 29 hängend gekoppelten Drahtrahmens 22 im Unterschied zum Transport mittels eines um eine Rotationsachse 23 rotierend ausgebildeten Drahtrahmens 22 in ihrer Transportgeschwindigkeit vor ihrer Übernahme durch den betreffenden Drahtrahmen 22 nicht vollständig abgebremst werden, so dass die Produktionslinie 01 mit einem höheren Durchsatz an Blechtafeln 08 betrieben werden kann. Außerdem verringern am Untertrum des Zugmittels 29 hängend gekoppelte Drahtrahmen 22 die Gefahr, dass eine von ihnen transportierte Blechtafel 08 an der bedruckten und/oder lackierten Oberfläche z. B. durch Vibrationen in einer Kontaktzone zwischen betreffender Blechtafel 08 und Drahtrahmen 22 Schaden nimmt. Wie bereits beschrieben, ist die Beladestation 02 zum Beladen des Durchlauftrockners 17 mit den bedruckten und/oder lackierten Blechtafeln 08 in Transportrichtung T der Blechtafeln 08 unmittelbar vor dem Durchlauftrockner 17 angeordnet. Des Weiteren ist unmittelbar nach dem Durchlauftrockner 17 vorzugsweise eine Entladestation 07 zum Entladen der durch den Durchlauftrockner 17 transportierten Blechtafeln 08 angeordnet, wobei die Entladestation 07 derart ausgebildet ist, dass sie den betreffenden die Blechtafel 08 transportierenden Drahtrahmen 22 vom Untertrum des Zugmittels 29 aushängt. Ferner ist in einer bevorzugten Weiterbildung eine vom Zugmittel 29 unabhängige Transporteinrichtung 63 vorgesehen, wobei diese Transporteinrichtung 63 an der Entladestation 07 vom Untertrum des Zugmittels 29 ausgehängte und damit gelöste Drahtrahmen 22 einzeln oder gestapelt oder geschuppt zurück zur Beladestation 02 transportierend ausgebildet ist. In der Das Drahtrahmen 22 hängend transportierende Zugmittel 29 ist z. B. durch zwei spiegelbildlich ausgeführte Ketten ausgebildet, wobei diese Ketten über mehrere jeweils Zahnräder aufweisende Wellen 31 synchron angetrieben sind, wobei zwei dieser Wellen 31 jeweils an den Enden der von diesen Ketten überspannten Transportstrecke durch die Produktionslinie 01 angeordnet sind. In einer besonders effizienten Ausgestaltung der Produktionslinie 01 sind - wie beispielhaft in der Production line (01) for processing metal sheets (08), comprising a sheet printing machine (03) and/or a coating machine (06), and comprising a continuous dryer (17) for drying the metal sheets (08) printed by the sheet printing machine (03) and/or coated by the coating machine (06), wherein a loading station (02) is arranged immediately upstream of the continuous dryer (17) in the transport direction (T) of the metal sheets (08), wherein the loading station (02) comprises a plurality of wire frames (22), each rotating about an axis of rotation (23) which extends transversely to the transport direction (T) of the transported metal sheets (08), wherein the wire frames (22) are arranged to lift metal sheets (08), which are transported horizontally one after the other, out of their transport plane, wherein each of these wire frames (22) is designed in such a way that it travels in a circle, from the bottom upward, through the transport plane of the metal sheets (08) in a region in which these metal sheets (08) are being fed to the loading station (02), and by this pivoting movement sets upright one of the laid-flat metal sheets (08) that is to be transported through the continuous dryer (17), wherein a lifting device is provided in the loading machine (02) for the wire frames (22) thereof, wherein the lifting device is arranged to aid the lifting of a metal sheet (08) that is being transferred by a wire frame (22), characterized in that the lifting device comprises a plurality of timed compressed air nozzles (49), wherein these compressed air nozzles (49) are arranged in the loading machine (02) below the transport plane of a metal sheet (08) that is being fed to the loading machine (02) and are operated in such a way that they blow vertically upward with a pressure surge against the underside of the metal sheet (08) that is to be lifted by said wire frame (22) at the moment at which said metal sheet (08) is being transferred by said wire frame (22), and/or in that the lifting device comprises electromagnets (51) arranged above or below the transport plane of a metal sheet (08) that is being fed to the loading machine (02), and/or in that the lifting device comprises at least one rotating cam (54) above the transport plane of a metal sheet (08) that is being fed to the loading machine (02), wherein said cam (54) is designed to mechanically lift said wire frame (22), and/or in that the lifting device is designed as a stroke-motion device, wherein the stroke-motion device is arranged below the transport plane of a metal sheet (08) that is being fed to the loading machine (02), wherein this stroke-motion device is designed either in the form of a cyclically moving lever (57), which rotates about an axis of rotation (61), or in the form of a ram (58), which is moved at an angle relative to the underside of the metal sheet (08) that is to be lifted by said wire frame (22). Production line (01) according to claim 1, characterized in that, in the case of the lifting device comprising the electromagnets (51), said wire frame (22) which lifts the metal sheet (08) that is being fed to the loading machine (02) has at least one spacer (52) at its end remote from the axis of rotation (23), wherein the electromagnets (51) above or below the transport plane of the metal sheet (08) that is being fed to the loading machine (02) are arranged in the region of the at least one spacer (52). Production line (01) according to claim 1 or 2, characterized in that, in the case of the lifting device comprising the electromagnets (51), the electromagnets (51) are switched in a timed fashion by a control unit (53). Production line (01) according to claim 1 or 2 or 3, characterized in that, in the case of the lifting device comprising the electromagnets (51), the control unit (53) which switches the electromagnets (51) is designed to be integrated in a machine controller (34) of the production line (01). Production line (01) according to claim 1 or 2 or 3 or 4, characterized in that, in the case of the lifting device comprising the at least one cam (54), said cam (54) is designed to pivot away cyclically while a metal sheet (08) is being fed to the loading machine (02). Production line (01) according to claim 1 or 2 or 3 or 4 or 5, characterized in that, in the case of the lifting device designed as a stroke-motion device, the lever (57) or the ram (58) in each case has a roller (56) at its free end. Production line (01) according to claim 1 or 2 or 3 or 4 or 5 or 6, characterized in that, in the case of the lifting device designed as a stroke-motion device, said wire frame (22) that lifts a metal sheet (08) has at least one longitudinal bar (59) or longitudinal beam (59), wherein the stroke-motion device acts in a form-fitting manner in a central region of said longitudinal bar (59) or longitudinal beam (59) to lift said wire frame (22). Production line (01) according to claim 1 or 2 or 3 or 4 or 5 or 6 or 7, characterized in that, in the case of the lifting device designed as a stroke-motion device arranged below the transport plane, a cyclic traversing of the lever (57) or ram (58) transversely to the transport direction (T) of the metal sheets (08) is provided.Bezugszeichenliste
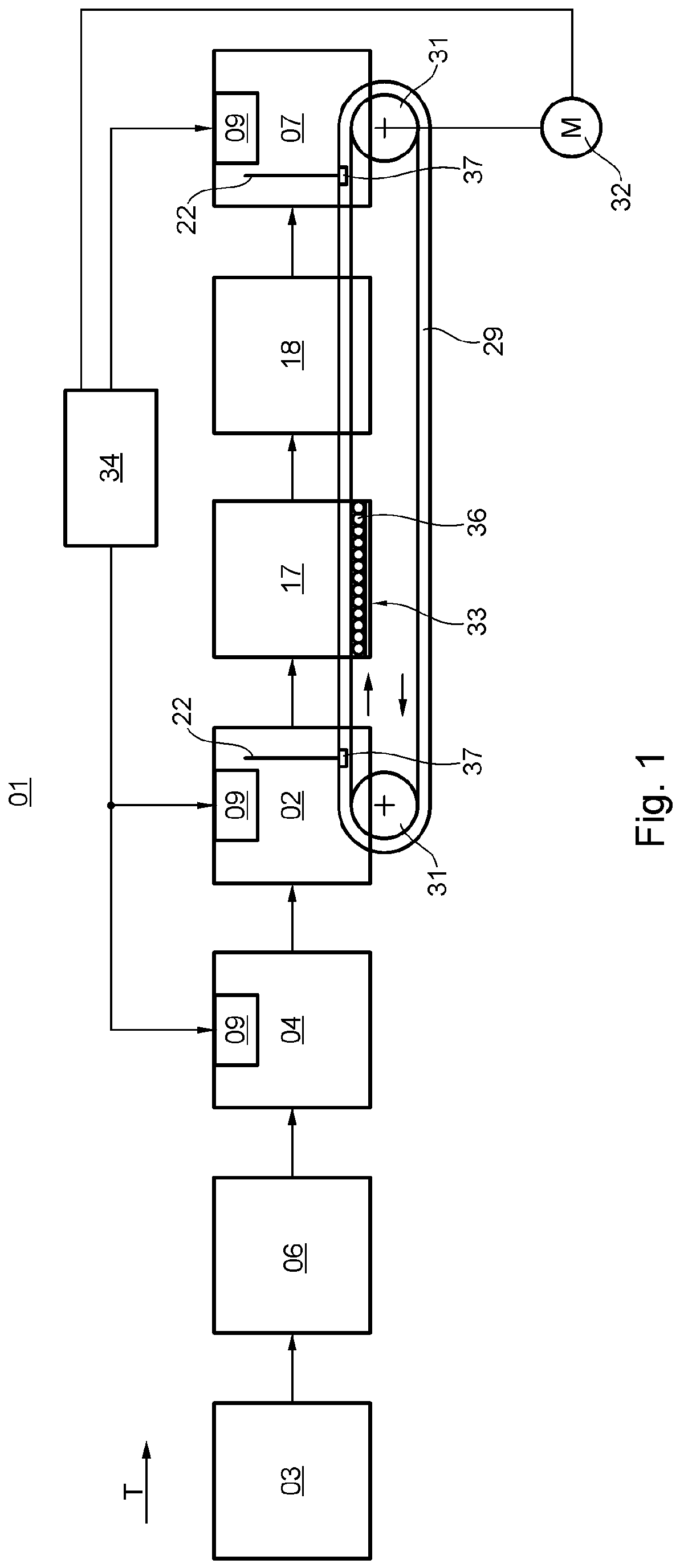
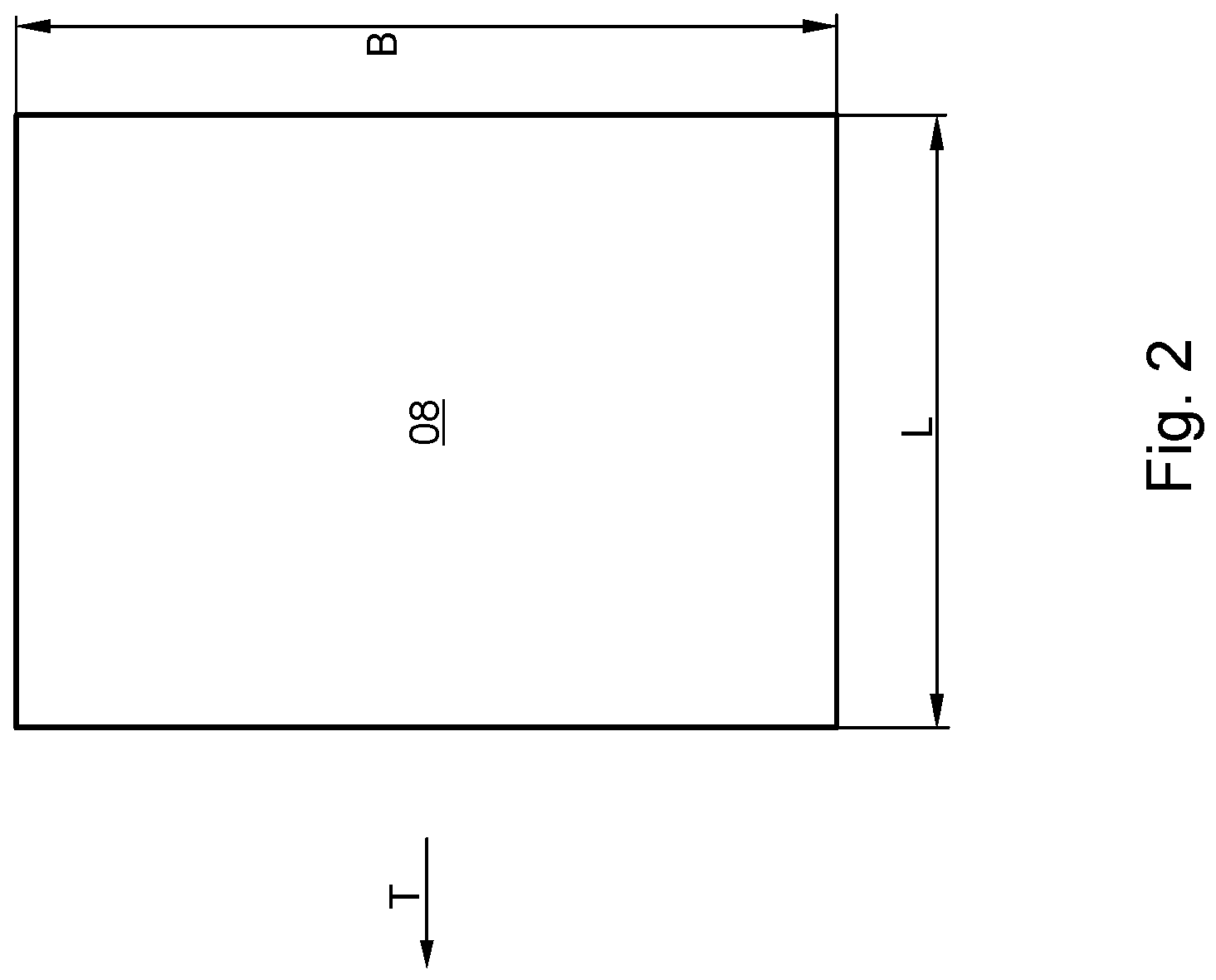
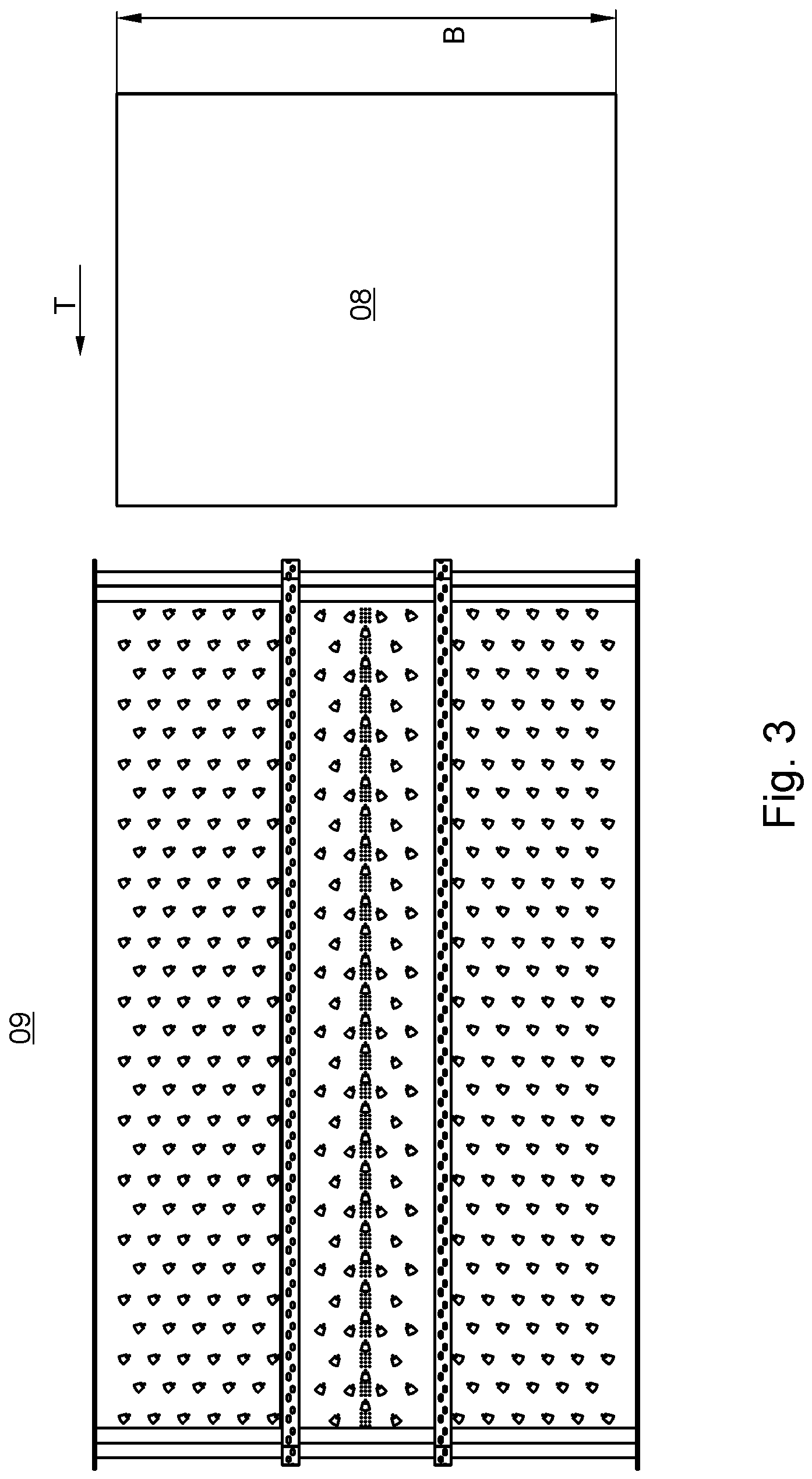
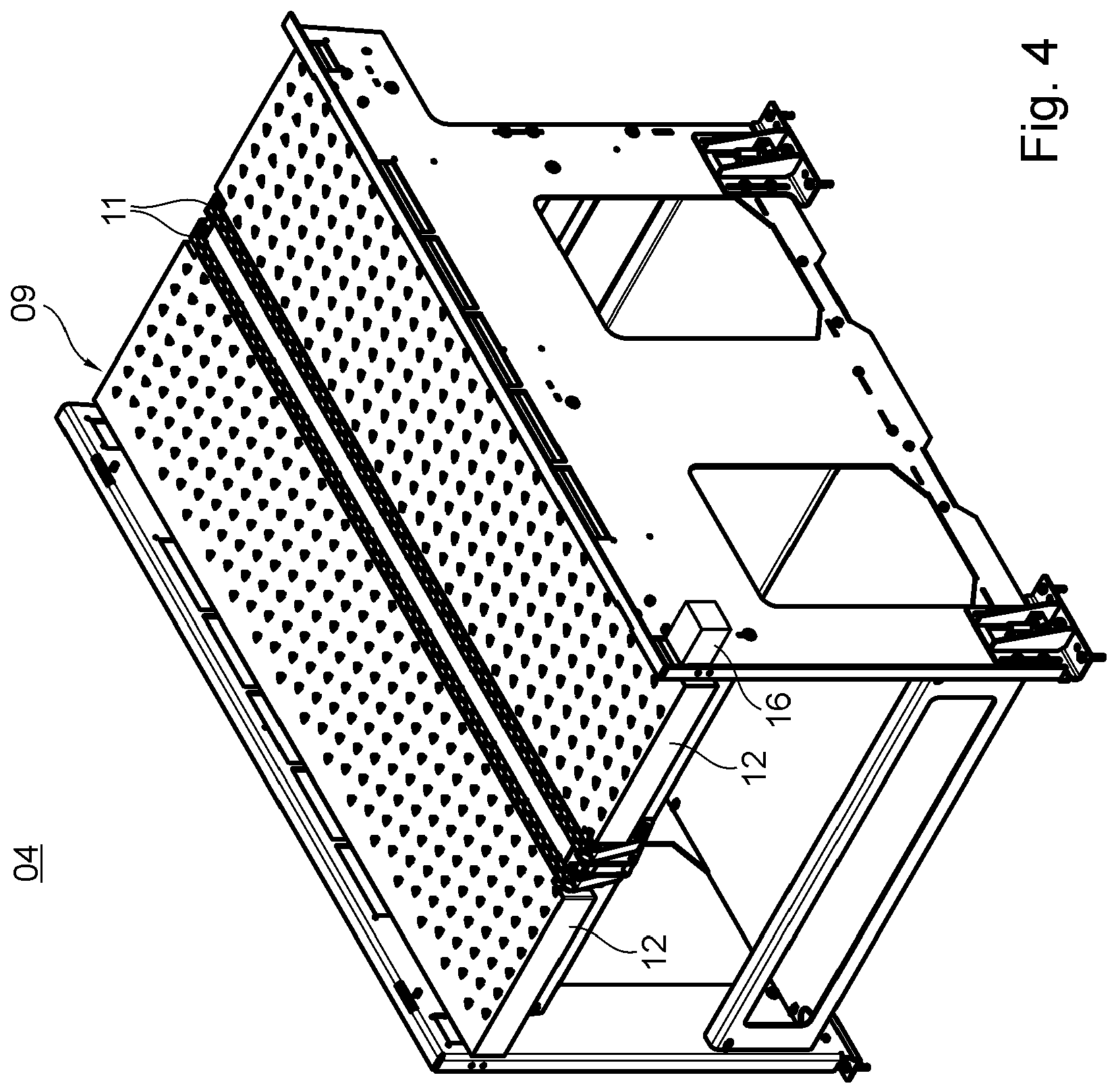
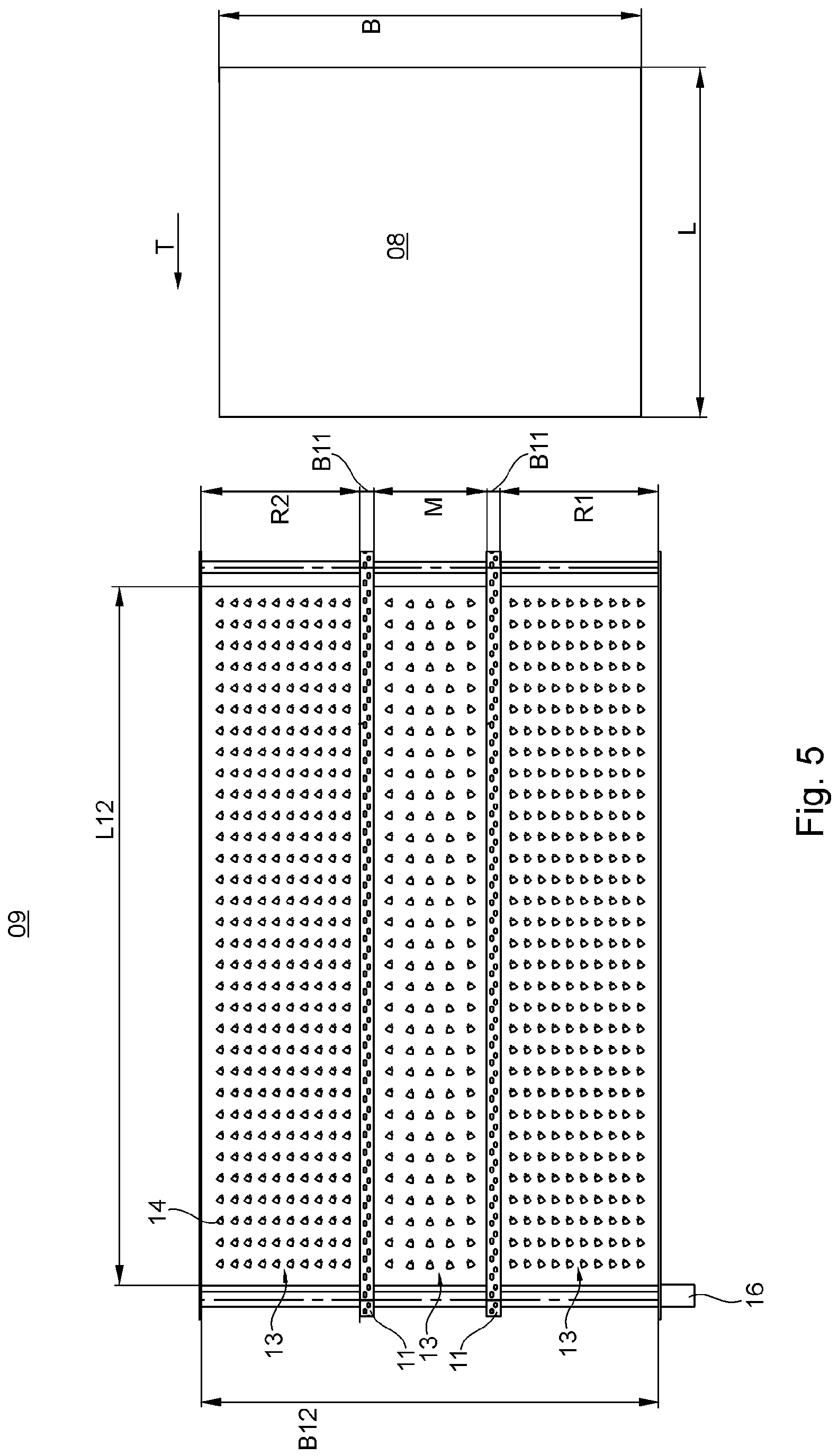
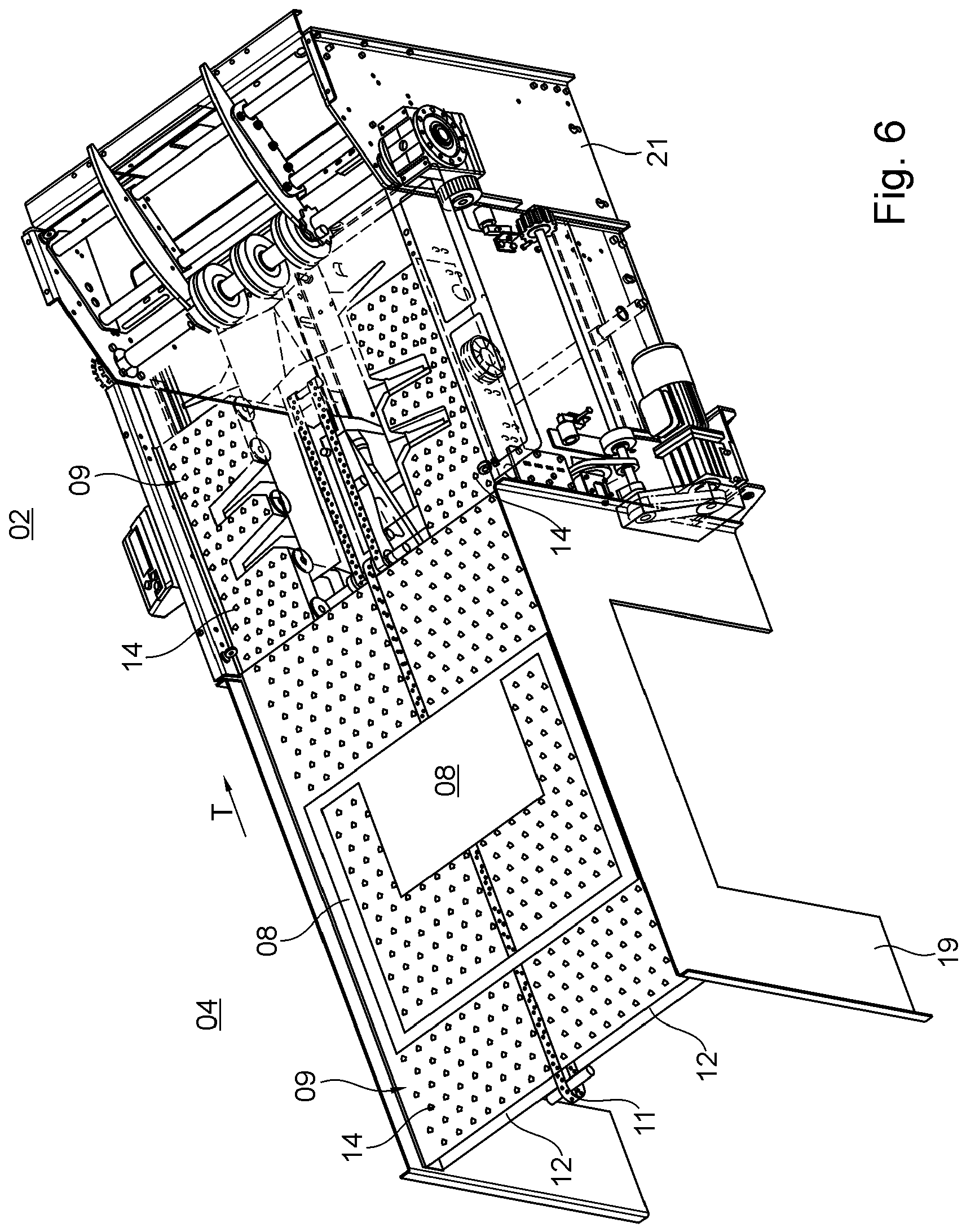
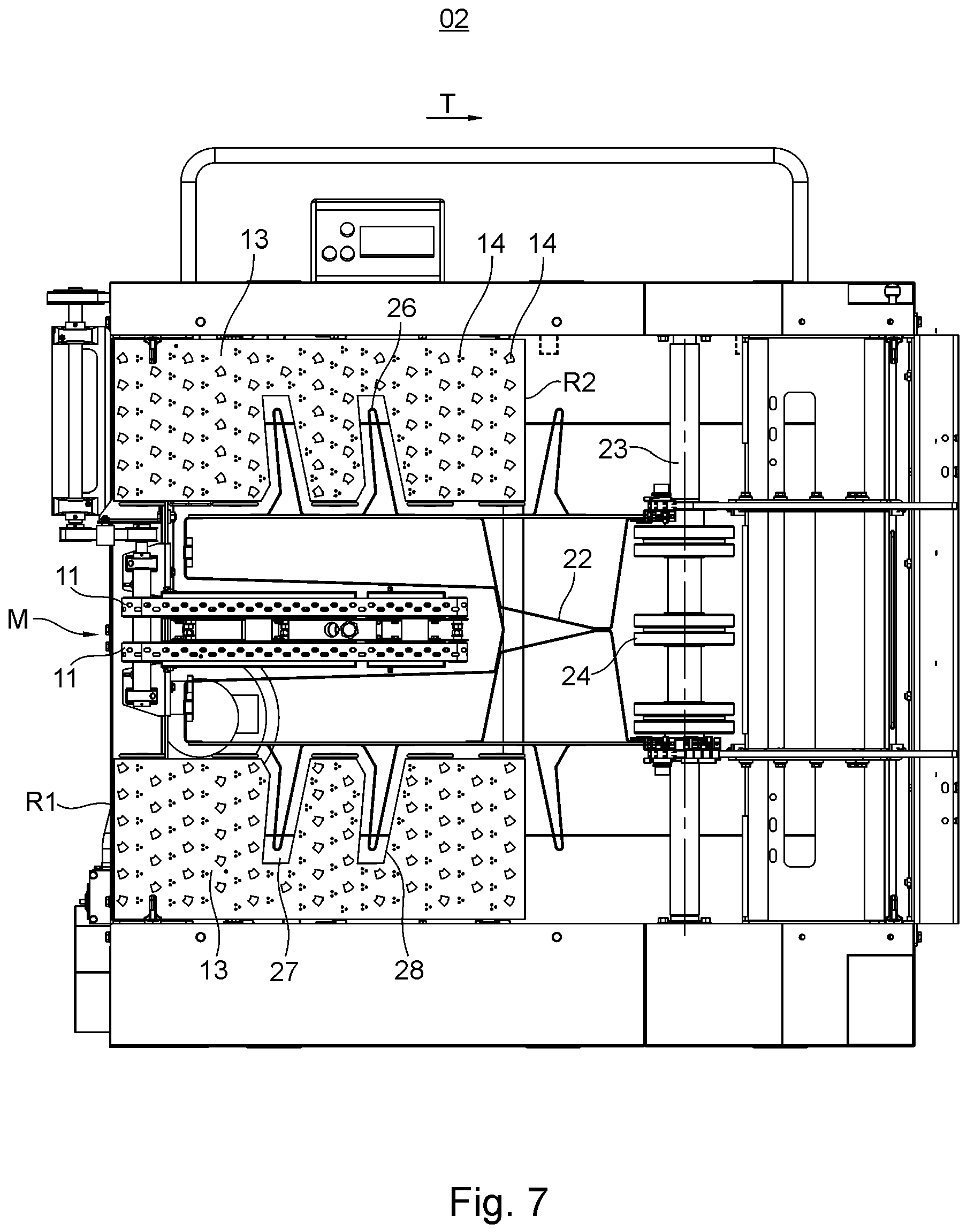
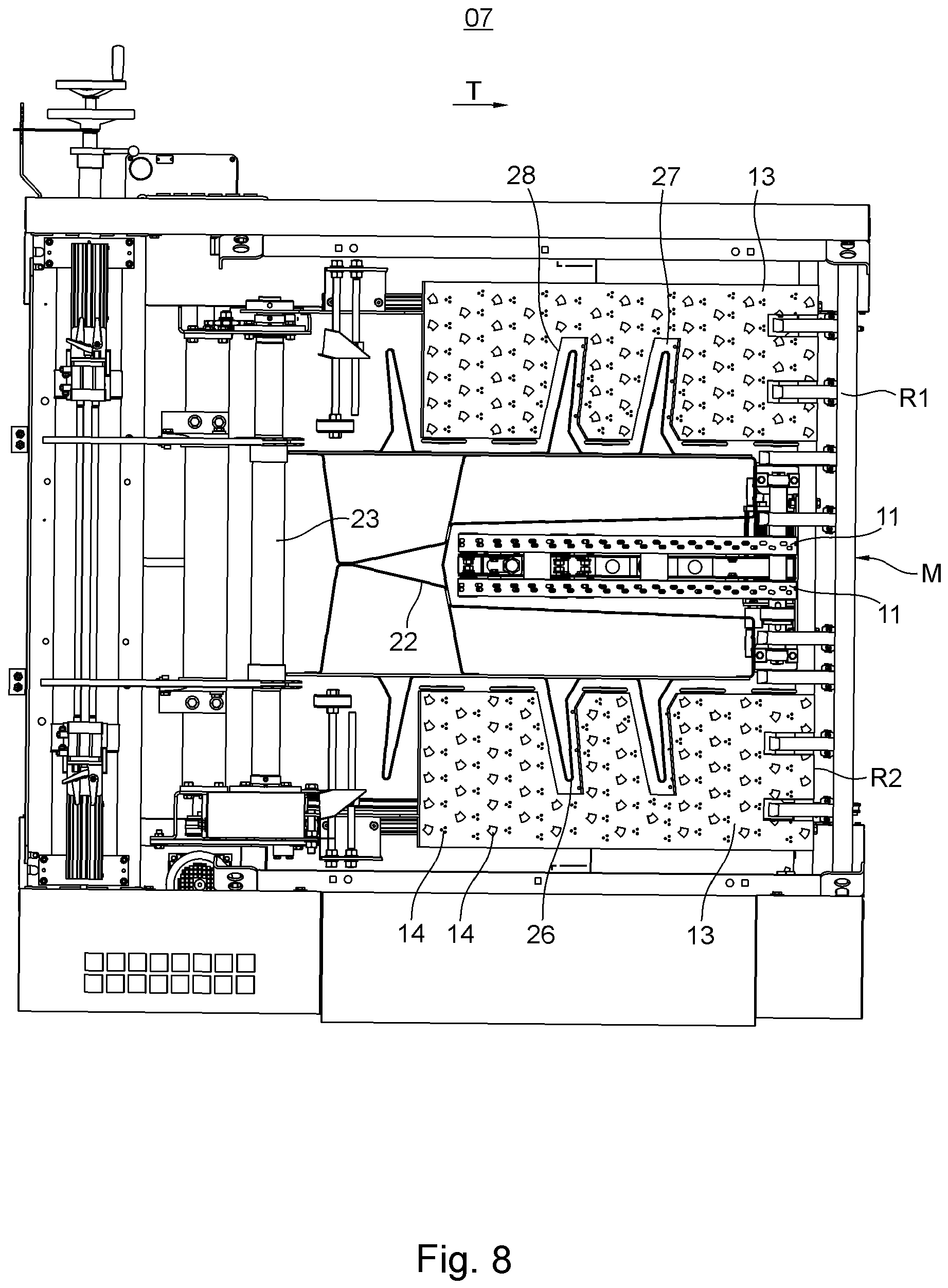
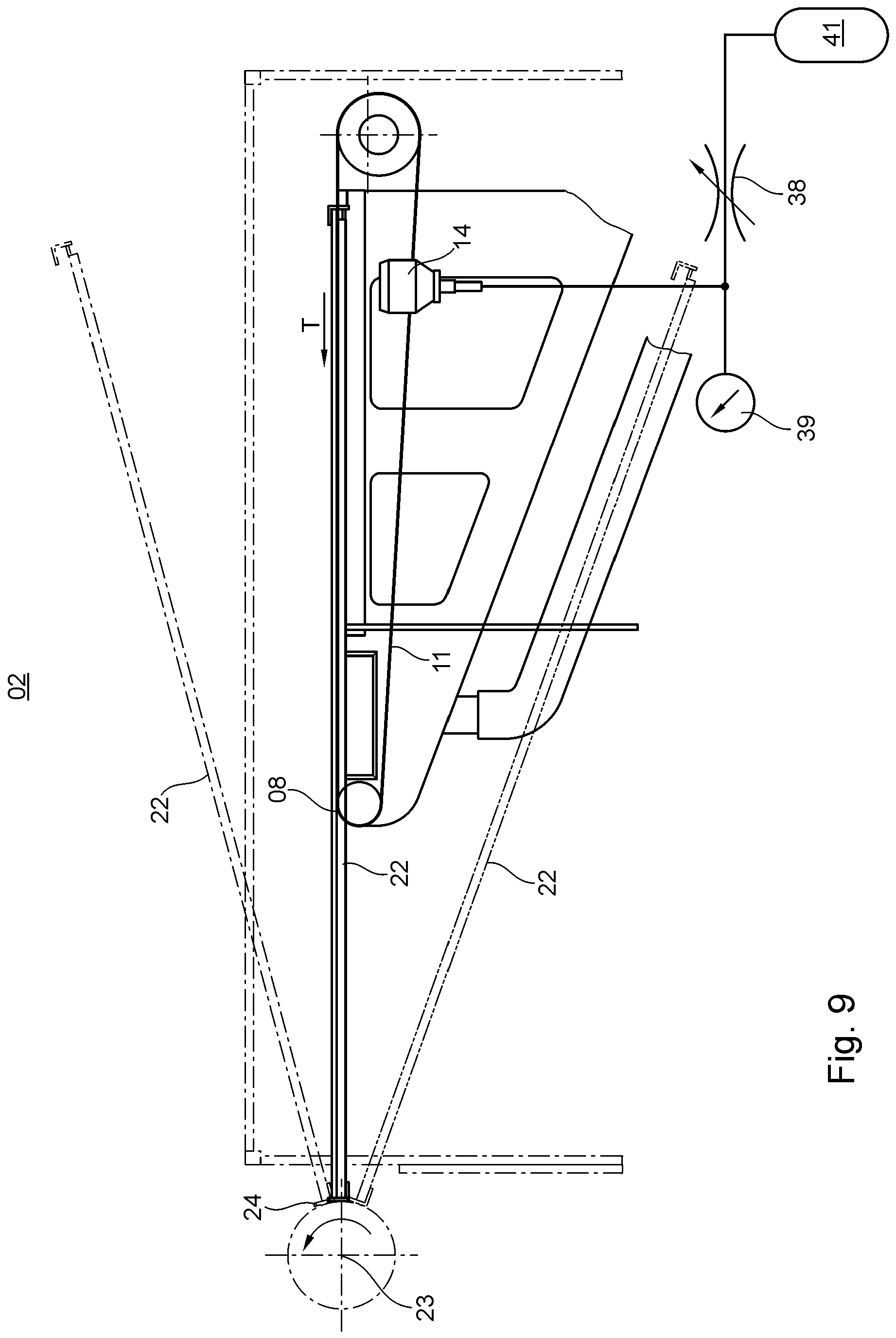
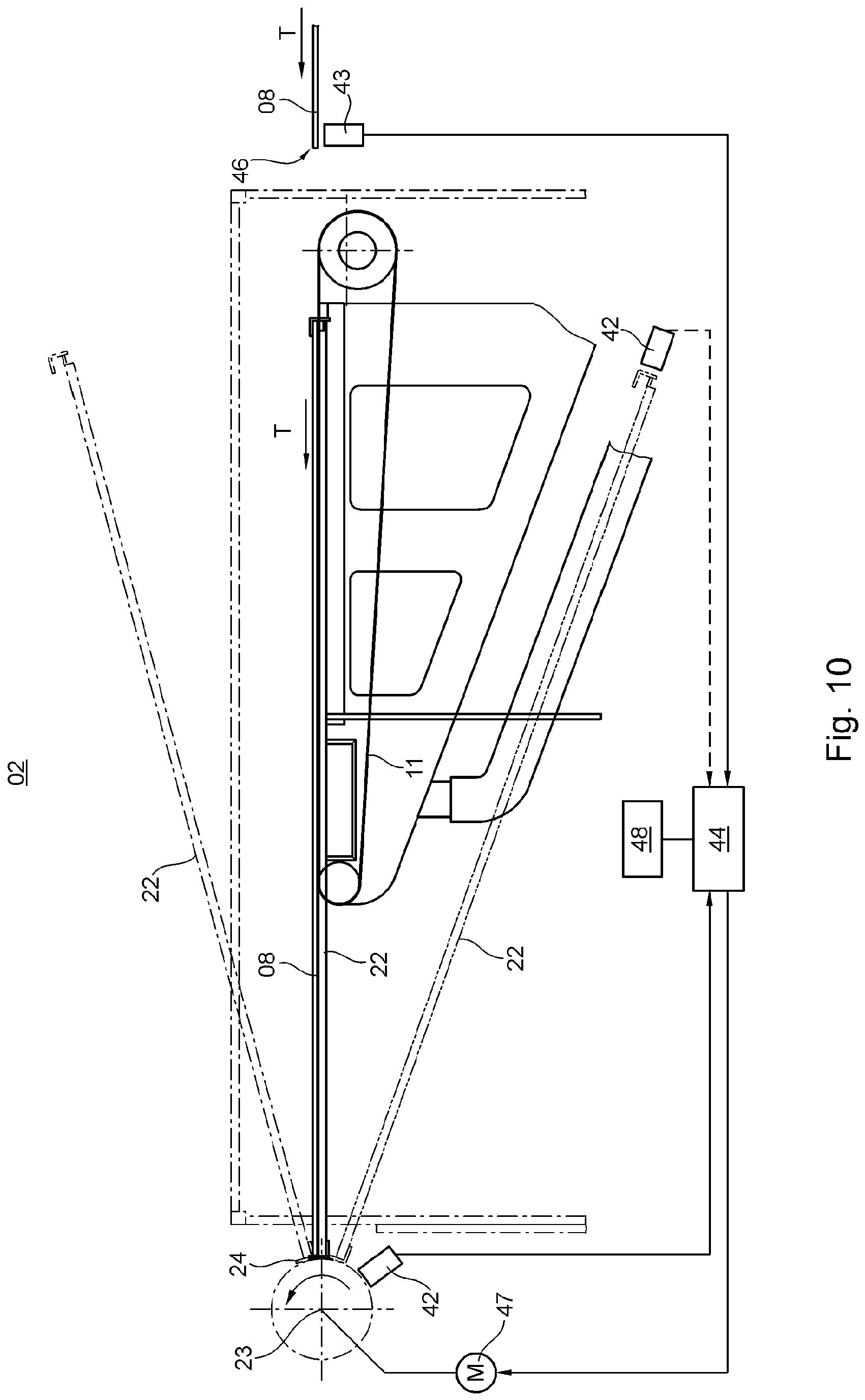
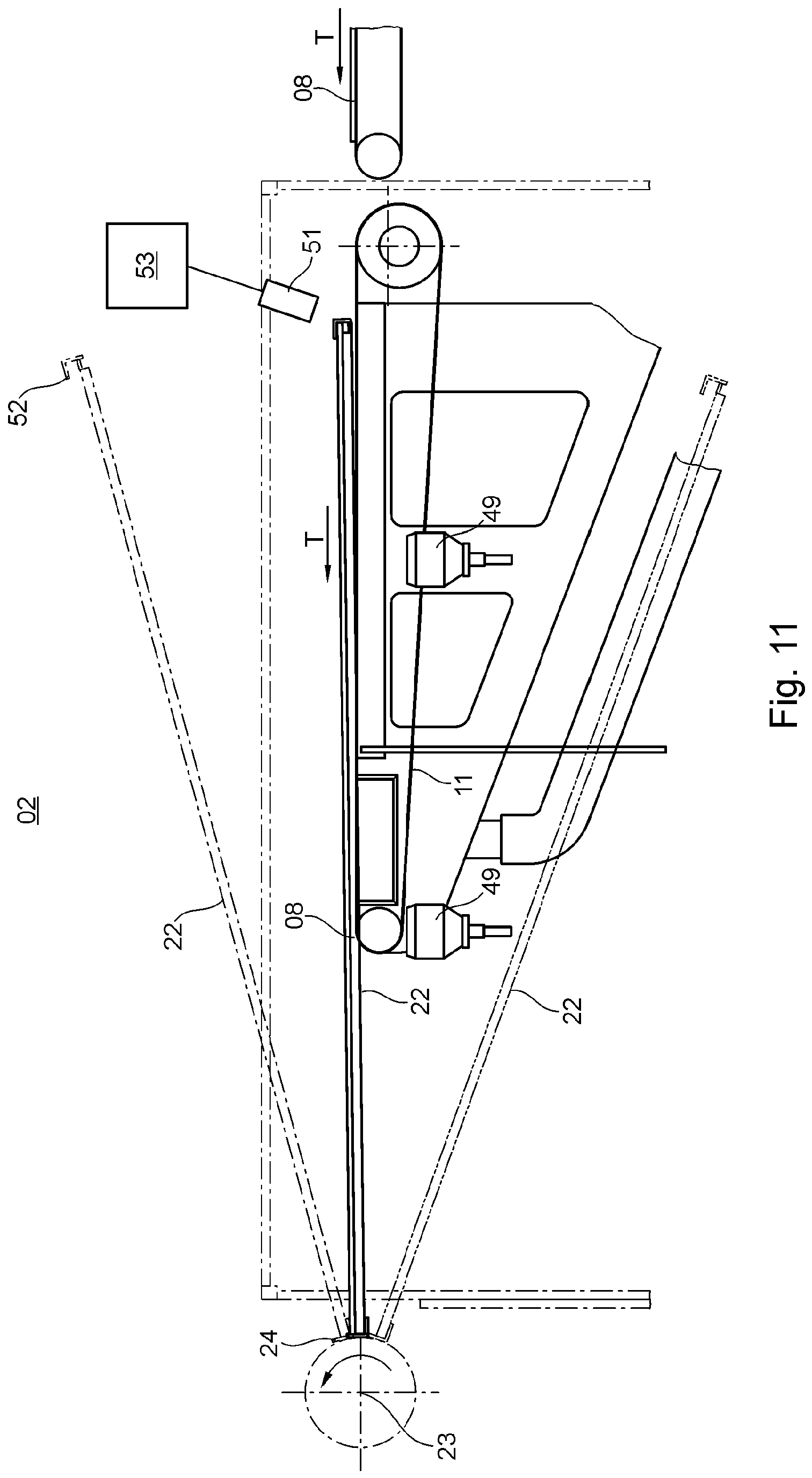
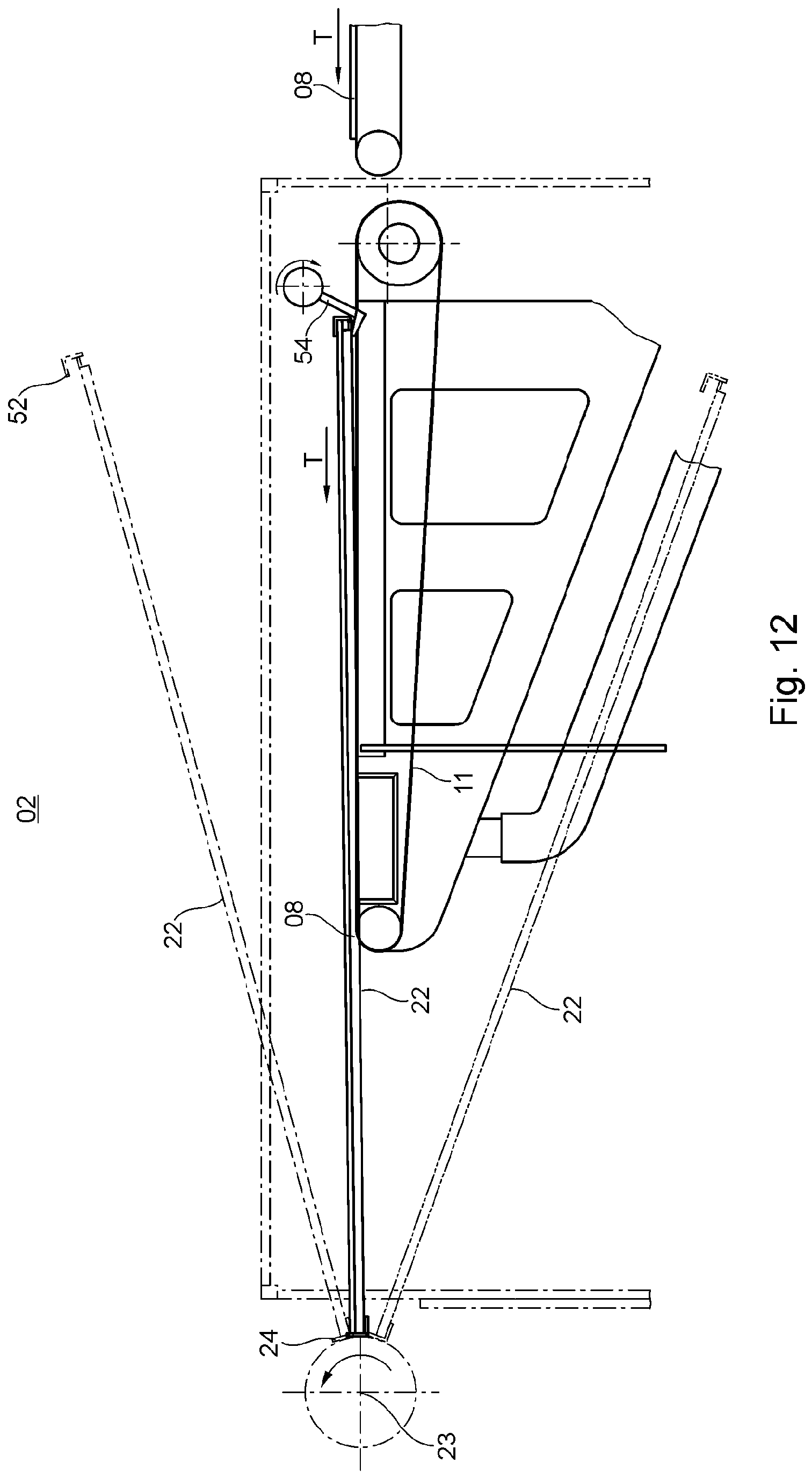
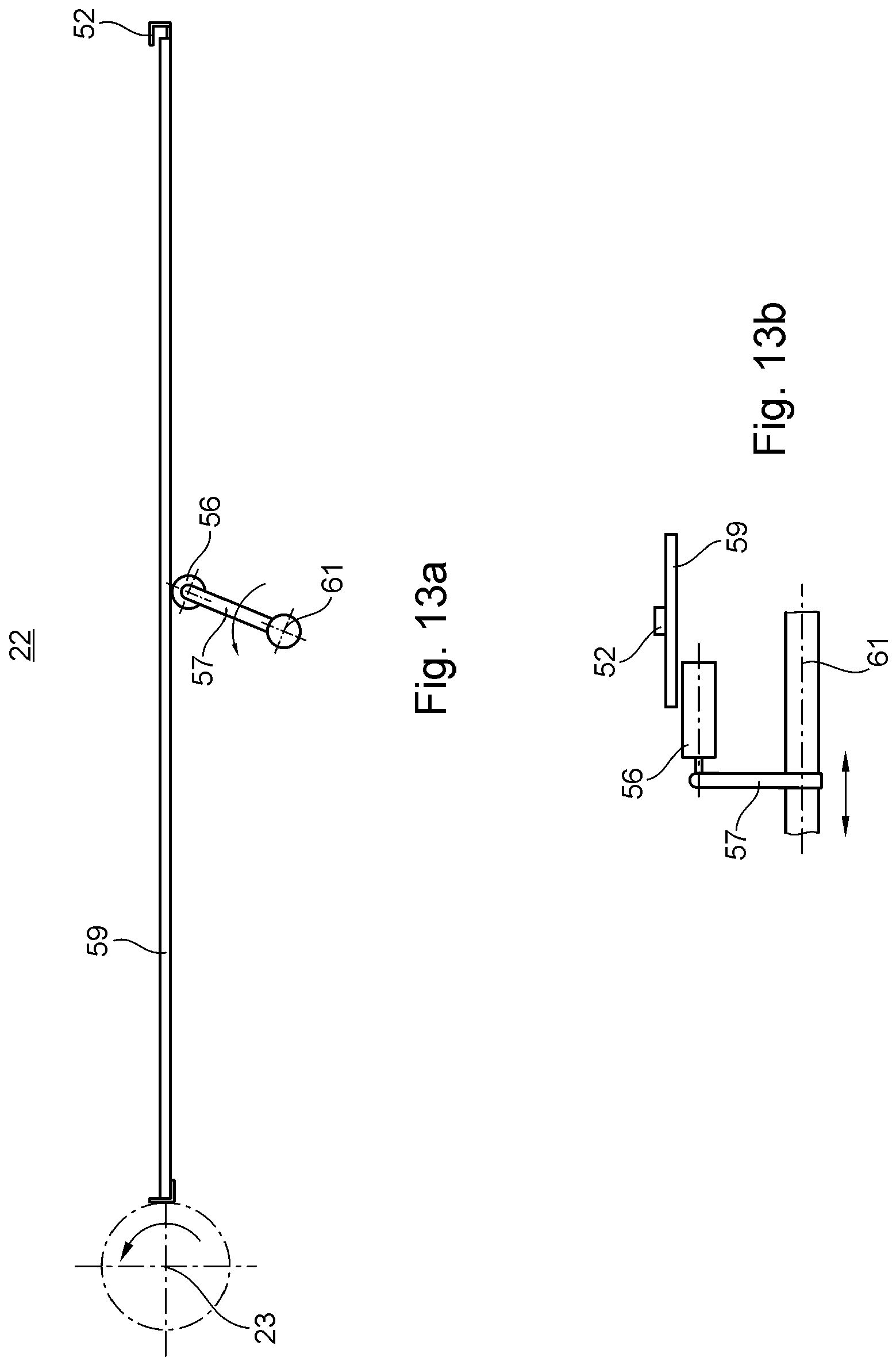
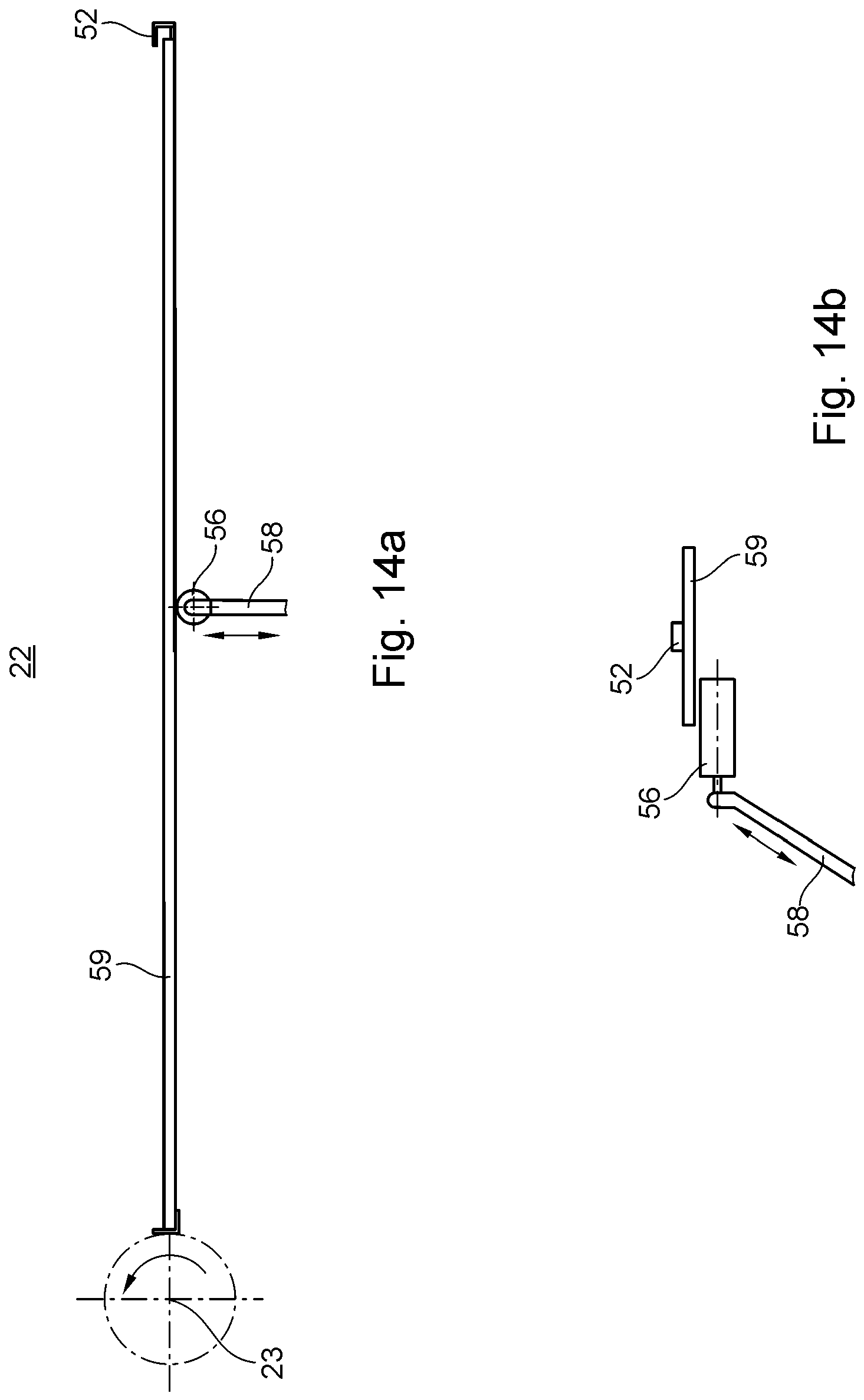
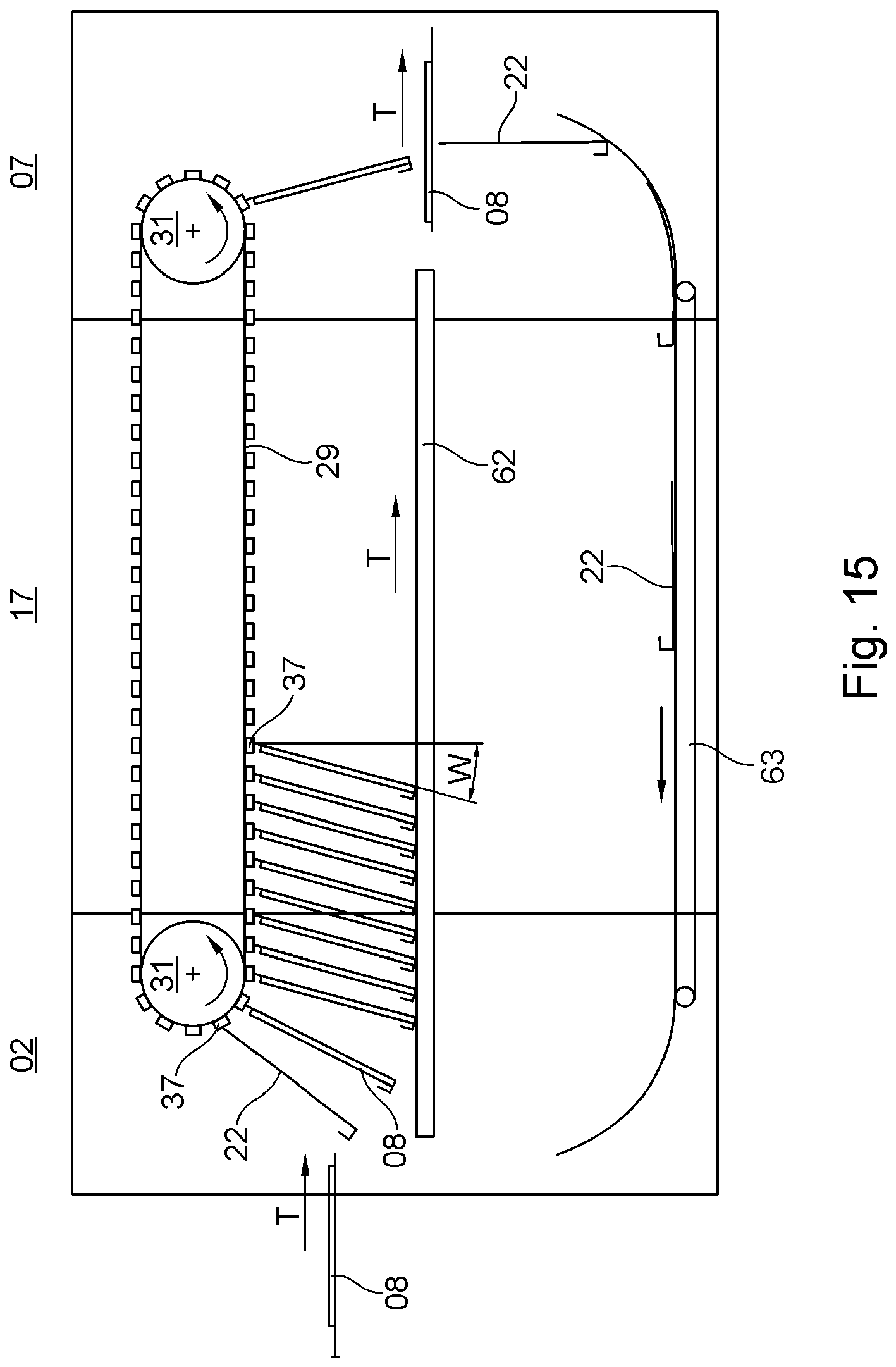
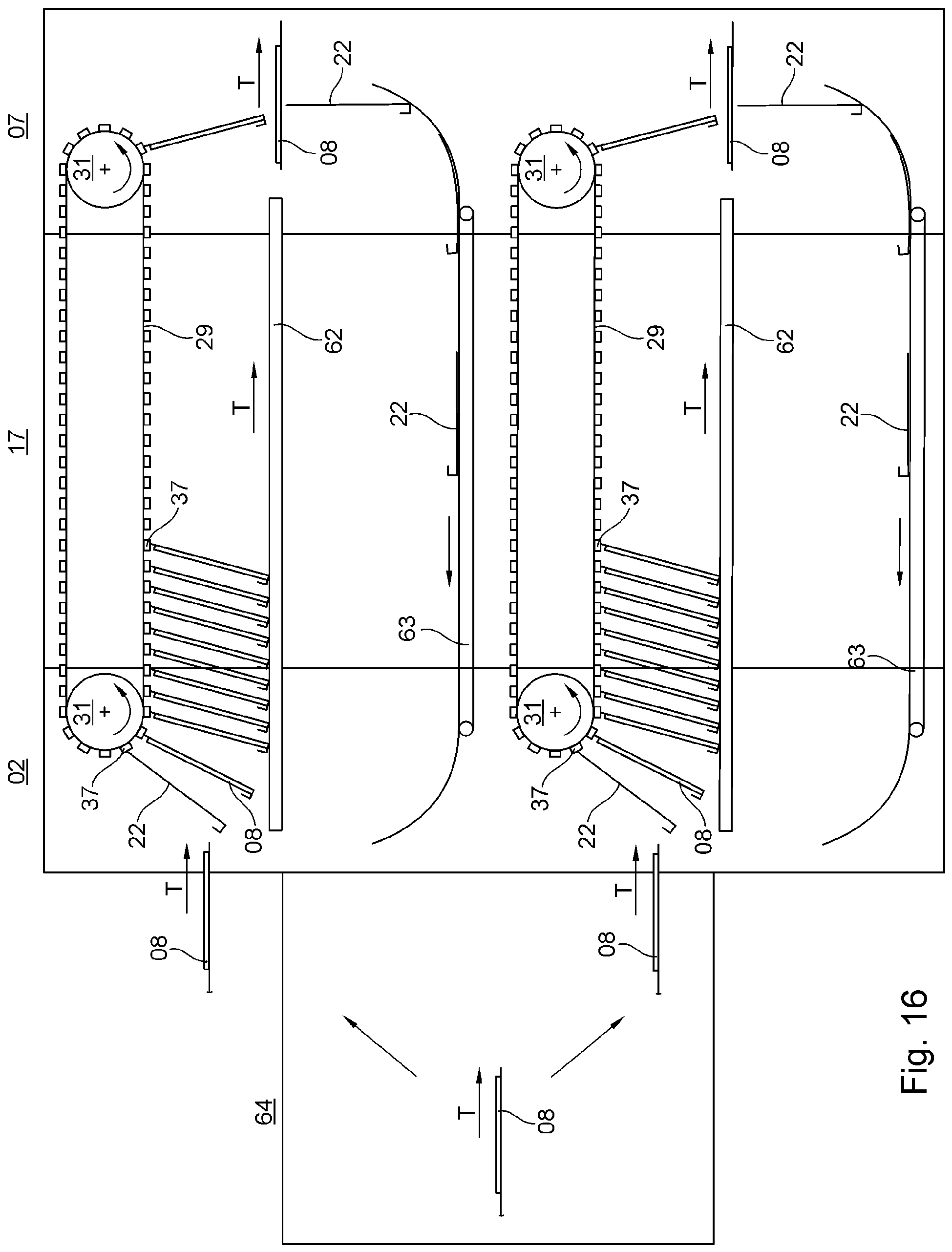
CPC - классификация
BB4B41B41FB41F2B41F21B41F21/B41F21/1B41F21/12B41F23B41F23/B41F23/0B41F23/04B41F23/044B41F23/0443B6B65B65HB65H2B65H23B65H230B65H2301B65H2301/B65H2301/3B65H2301/33B65H2301/332B65H2301/3321B65H2301/33214B65H2301/3322B65H2301/33222B65H2301/5B65H2301/51B65H2301/517B65H24B65H240B65H2405B65H2405/B65H2405/3B65H2405/35B65H2405/352B65H27B65H270B65H2701B65H2701/B65H2701/1B65H2701/17B65H2701/173B65H28B65H280B65H2801B65H2801/B65H2801/3B65H2801/31B65H5B65H5/B65H5/1B65H5/18B65H7B65H7/B65H7/0B65H7/06IPC - классификация
BB4B41B41FB41F2B41F21B41F21/B41F21/1B41F21/12B41F23B41F23/B41F23/0B41F23/04B6B65B65HB65H5B65H5/B65H5/1B65H5/18B65H7B65H7/B65H7/0B65H7/06Цитирование НПИ
DE-A1-102020 111 752DE-U1- 9 421 974
EP-A1- 3 896 018
US-A- 3 880 272