PROCEDURE FOR MANUFACTURING A LAYER COMPOSITE MATERIAL
The invention refers to a procedure for manufacturing a layer composite material, whereby a layer from sinterable solid particles is applied on an band-shaped metal base and sintered by heat supply in a feed direction sequentially with liquid phase.
In order to have to lead a layer composite material, which consists for example of a steel girder and a composite layer on copper basis and finds for sliding bearing use to be able to manufacture by sintering the composite layer applied in powder form on the steel girder without the band-shaped steel girder with the applied sinter powder by a complex sintering furnace and a cooling device downstream, is it admits (GB 2,383,051 A) to melt and ago cool following this melt open range from the side of the steel girder rapidly the sinter powder down of the composite layer up-strewn on the steel girder by laser beams over the width of the band-shaped steel girder within a locally limited length range, around the surface of the steel girder outgoing, outward progressive solidification of the composite layer with a fine-grained, dendritischen To reach structure. Although with the help of this procedure for manufacturing a layer composite material the length hiefür of the necessary plants can be substantially shortened compared with conventional plants for sintering layer composite materials, the expenditure remains substantial because of the necessary use of laser mechanisms over the width of the band-shaped steel girder.
The invention is thus the basis the task in such a way to out-arrange a procedure for manufacturing a layer composite material of the initially described kind that the advantages in a feed direction of a progressing, on a short • "; : … “.oo 0o • • • • 0 o • length range limited sintering with liquid phase to be useful can, without having to warm up the appropriate layer of the composite layer by laser mechanisms to the Sintertemperatur.
The invention solves the task posed thereby that the metal base in feed direction is warmed up sequentially with a temperature distribution, which drops from a highest temperature above the fusing temperature of the solid particles within the range the particle layer taking up layer against a nuclear layer of the metal base to lower temperatures, and that the particle layer is sintered at least in a layer resting against the metal base by a heat transmission of the warmed up metal base.
Since according to these measures the warmed up metal base exhibits from a highest temperature within the range the particle layer taking up layer outgoing temperature gradient toward a nuclear layer, a solidification of the liquid phase outward outgoing from the surface of the metal base progressive and can be guaranteed despite the heating up of the solid particles of the composite layer on the Sintertemperatur necessary for sintering with Flüssigphase by a heat transmission from the metal base. Those the metal base from its layer near the surface withdrawed heat of fusion leads with an appropriate vote hiefür of determining conditions due to the temperature gradient to a cooling of the layers near the surface of the metal base and thus to a solidification of the liquid phase with increasing feed motion progressively from the inside outward. Hiefür a sufficient temperature gradient, which is to amount to for the Sicherstellung of the effect desired in many applications at least 5 K/mm, is substantial.
Because of the penetration depth of an electromagnetic alternating field into an band-shaped metal base, considerably dependent on the frequency, the temperature distribution desired for the heating up of the metal base can be achieved in favourable way by an inductive heating up, particularly by an appropriate arrangement of the turns of the energizing wind within the range that each other gegenü • • • • • • • O • 0 • • • o • oo • °°oo •; oo berliegenden surfaces of the band-shaped metal base or by a one-sided turn arrangement different field densities to be easily adjusted can. Thus the metal base in feed direction can be warmed up sequentially with the temperature distribution wished in each case, in order to be able to transfer the heat of fusion necessary for sintering the solid particles with liquid phase from the metal base to the applied particle layer. The particle layer can be manufactured with conventional sinter powders. In addition, it is possible to use substantially roughmore granular materials or granulates without endangering sintering desired by a heat transmission from the metal base.
The heat energy necessary for sintering the solid particles over the entire layer thickness needs to be applied however not completely over the heating up of the metal base. The particle layer applied on the metal base can be warmed up during the sinter procedure additionally inductively, so that a layer of the solid particles resting against the metal base is only sintered by a heat transmission from the warmed up metal base with liquid phase. With the melting of a sublayer of the solid particles eddy currents can be induced in this melted sublayer, which provide for an appropriate auxiliary warmth, in order to accelerate the sinter procedure outward. The solidification of the sinter material introduced over the cooled down metal base is not affected thereby so that also thicker composite layers at a comparatively small expenditure can be sintered, which however for example regarding layer composite materials for sliding bearings of subordinated importance is. Beyond that the solid particles before sintering can be preheated, in order to find with a smaller heat energy within the range of the metal base the sufficiency.
On the basis the design the procedure according to invention is more near described. Fig show. 1 a device for manufacturing a layer composite material in a procedure according to invention in a schematic profile, o o ° o °°t, ° “: ° t, oo°'° o.°:
Ill III Fig. 2 one the Fig. 1 appropriate representation of a structural variant of a device for manufacturing a layer composite material, Fig. 3 the temporal temperature gradient with the inductive heating up of the metal base in a layer and in a nuclear layer and a Fig. 4 the temperature gradient between a layer and a nuclear layer of the metal base with a warming up process after the Fig. 3.
In accordance with after the remark example the Fig. 1 is intended within a protection hood 1 for the maintenance of an inert gas atmosphere a mechanism 2 for inductive warming up of an band-shaped metal base 3, which is promoted by driving rollers 4 by the protection hood 1 and warmed up when going through the turns 5 at least one induction pick-up coil, before solid particles, for example a sinter powder, for which composite layer which can be applied with the help of a Aufstreueinrichtung 6 on the metal base 3 one applies.
In the Fig. the temporal warming up process for a steel metal base 3 with a thickness of 5 mm is on the one hand in a Oberfiächenund on the other hand represented 3 in a nuclear layer. From the process 7 of the surface temperature drawn in full line that with a suitable field frequency of for example 200kHz the surface temperature of the metal base 3 rises after the exceeding of the Curie point only again gradually, but the necessary, above the fusing temperature of the solid particles lying maximum temperature from e.g. 1100 to 1200°C results within can be achieved one time interval from 4 to 5 seconds easily during an appropriate power supply. Due to the penetration depth of the magnetic alternating field dependent on the exciter frequency follows in accordance with the nuclear temperature strichliert drawn curve 8 of the surface temperature 7 of the metal base 3 with a temporal delay, so that within the metal base 3 a temperature distribution with a temperature gradient of a highest in each case temperature in a layer results to according to lower temperatures in a nuclear layer.
The temperature difference between the temperature gradient 7 within the surface range and the temperature gradient 8 within the nuclear range is in the Fig. 4 in a size • "". "" ““F”: ” “': ” ren • 1 • • • O • • 1 • yardstick as curve 9 represented. It is shown that after the exceeding of the Curie point the temperature difference between surface and core decreases that this temperature difference does not drop however with given conditions within the range of the final temperature desired under 50 °C. This means that after warming up the metal base 3 surface temperature a sufficient temperature gradient exceeding on the fusing temperature of the solid particles is present toward the nuclear layer of the metal base 3, so that despite the transmission of the heat of fusion of the metal base on the particle layer and associated sintering of the composite layer with liquid phase the solidification of the melted solid particles proceeds from the surface of the metal base 3 and progresses outward. The cooling of the melted solid particles introduced over the arising temperature gradients can be supported by a cooling of the metal base 1 side cleared away from that the composite layer ago, like this by one in the Fig. 1 dash-dotted suggested cooling equipment 10 is illustrated.
Since the metal base 3 in a feed direction 11 is progressively inductively warmed up, whereby the warming up range on a short by which inductive warming up mechanism 2 certain length range is limited, to provide and which is likewise sintered up-strewn particle layer in a limited length section of the warmed up metal base 3 with liquid phase, in order immediately after it over the metal base 3 to be cooled down ago, results for the sinter device a comparatively short overall length, so that it, not only volumes becomes quite possible but also as plates available metal bases 3 for the production of layer composite materials with a composite layer.
After the execution form the Fig, to 2 that essentially corresponds the Fig. 1. To the difference to the execution form after the Fig. 1 is however an auxiliary coil with turns 12 assigned to the mechanism 2, which are subordinate the Aufstreueinrichtung 6 in feed direction 11 and are in such a way laid out that over the metal base 3 to the particle layer will not transfer the entire fusion energy for the particle layer must. Such additional induction turns 6: i.; “!!! i 12 permit naturally also a following Aufstreuen of solid particles, how this is suggested by the dash-dotted drawn Aufstreueinrichtung 13.
i the invention is naturally not limited to the represented remark examples, because both regarding the coil arrangement and the Aufstreuung of the solid particles influence on the sinter procedure and the training of the composite layer can be taken. Since both regarding the pretreatment of the too besinternden metal base 3 and concerning the subsequent treatment of the layer composite material by the procedure according to invention no restrictions are forced, with the usual Vorund subsequent treatments one does not deal more in greater detail.
Patent lawyers Dipl. - engineer Gerhard of pretty Dipl. - engineer Helmut of pretty Spittelwiese 7, A-4020 Linz O0 • 0000 00 0 OD • •. o. : ::.:.
• “• Ö • O0 • 0 • 0 • 00 A • patent claims” (32 97O) II 1st procedure for manufacturing a layer composite material, whereby a layer from sinterable solid particles is applied on an band-shaped metal base and sintered by heat supply in a feed direction sequentially with liquid phase, thereby characterized that the metal base in feed direction is warmed up sequentially with a temperature distribution, which drops from a highest temperature above the fusing temperature of the solid particles within the range the particle layer taking up layer against a nuclear layer of the metal base to lower temperatures, and that the particle layer is sintered at least in a layer resting against the metal base by a heat transmission of the warmed up metal base.
2. Procedure according to requirement 1, by characterized that the metal base is warmed up to a temperature distribution with a temperature gradient by at least 5K/mm.
3. Procedure according to requirement 1 or 2, by characterized that the band-shaped metal base is inductively warmed up.
4. Procedure after one of the requirements 1 to 3, by characterized that the particle layer is additionally inductively warmed up during the sinter procedure.
Procedure after one of the requirements 1 to 4, by characterized that the solid particles before the sinter procedure are preheated.
Linz, to 28. May 2004 Miba sliding bearing GmbH through: A method is described for producing a stratified composite material, with a layer of sinterable solids particles being applied to a strip-like metal carrier and being sintered with liquid phase by the supply of heat continuously in the forward feed direction. In order to provide simplified production conditions it is proposed that the metal carrier is heated continuously in the forward feed direction with a temperature profile which decreases towards lower temperatures from a maximum temperature above the melting temperature of the solids particles in the region of a surface layer receiving the particle layer towards a core layer of the metal carrier, and that the particle layer is sintered at least in a layer resting on the metal carrier by a heat transmission from the heated metal carrier. Patent lawyers Dipl. - engineer Gerhard of pretty Dipl. - engineer Helmut of pretty Spittelwiese 7, A-4020 Linz O0 • 0000 00 0 OD • •. o. : ::.:.
• “• Ö • O0 • 0 • 0 • 00 A • patent claims” (32 97O) II 1. Procedure for manufacturing a layer composite material, whereby a layer from sinterable solid particles is applied on an band-shaped metal base and sintered by heat supply in a feed direction sequentially with liquid phase, thereby characterized that the metal base in feed direction is warmed up sequentially with a temperature distribution, which drops from a highest temperature above the fusing temperature of the solid particles within the range the particle layer taking up layer against a nuclear layer of the metal base to lower temperatures, and that the particle layer is sintered at least in a layer resting against the metal base by a heat transmission of the warmed up metal base. 2. Procedure according to requirement 1, by characterized that the metal base is warmed up to a temperature distribution with a temperature gradient by at least 5K/mm. 3. Procedure according to requirement 1 or 2, by characterized that the band-shaped metal base is inductively warmed up. 4. Procedure after one of the requirements 1 to 3, by characterized that the particle layer is additionally inductively warmed up during the sinter procedure.
Procedure after one of the requirements 1 to 4, by characterized that the solid particles before the sinter procedure are preheated.
Linz, to 28. May 2004 Miba sliding bearing GmbH through:
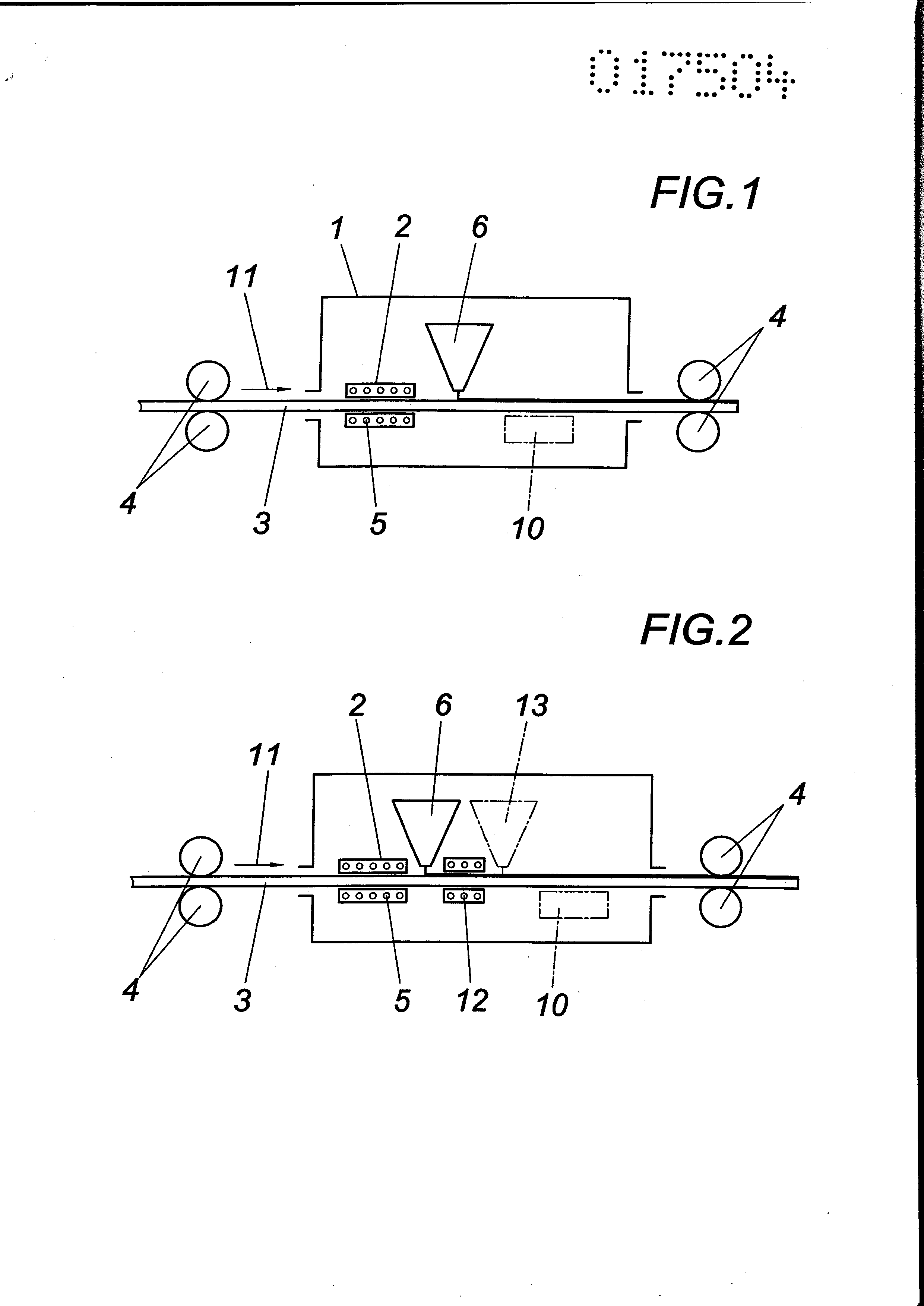
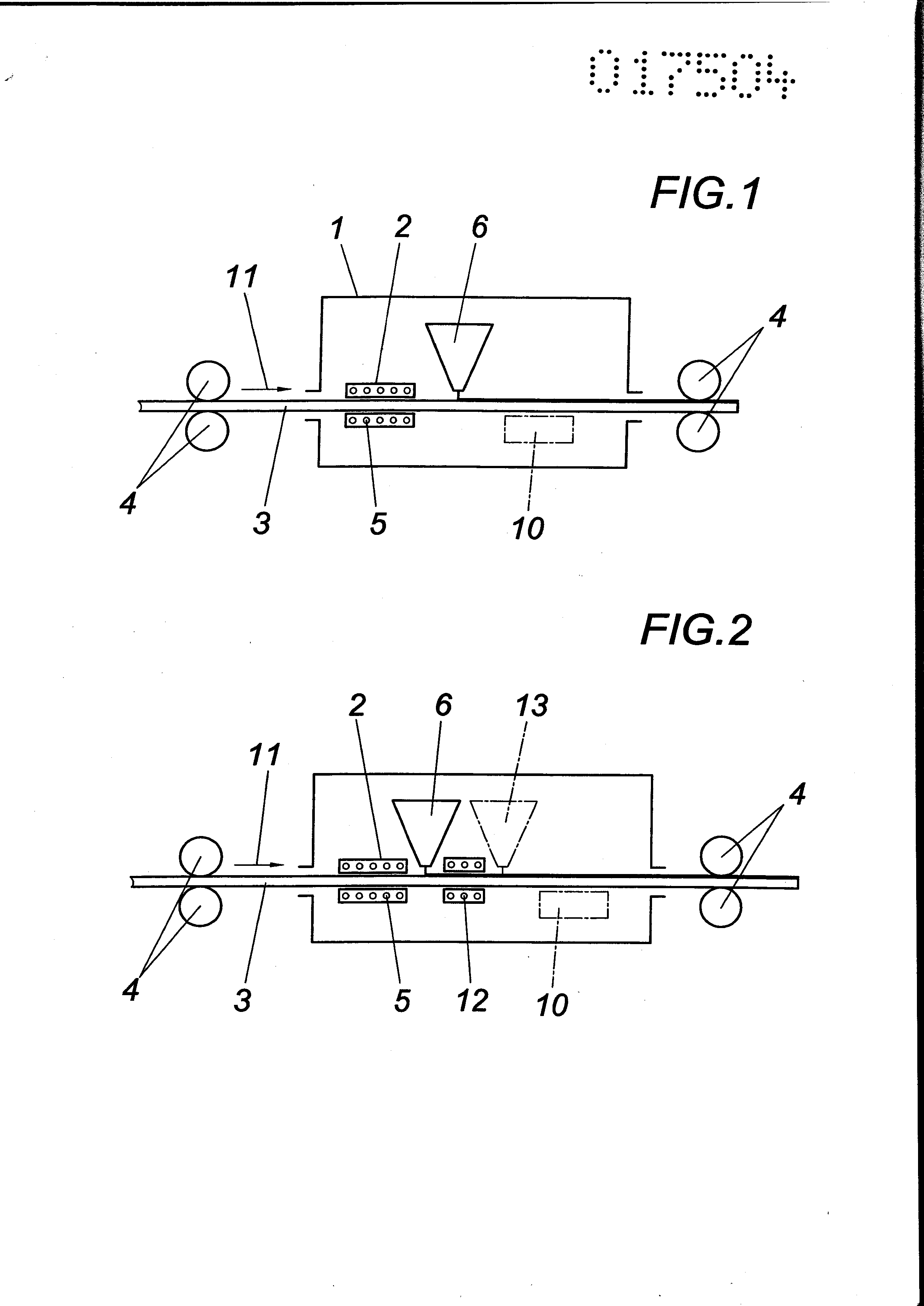
CPC - классификация
BB0B05B05CB05C1B05C19B05C19/B05C19/0B05C19/04B05C9B05C9/B05C9/1B05C9/14B05DB05D1B05D1/B05D1/3B05D1/30B05D2B05D22B05D225B05D2252B05D2252/B05D2252/0B05D2252/02B05D24B05D240B05D2401B05D2401/B05D2401/3B05D2401/32B05D3B05D3/B05D3/0B05D3/02B05D3/024B05D3/0245B05D3/028B05D3/0281B05D3/04B05D3/048B05D3/0486B05D7B05D7/B05D7/1B05D7/14B05D7/5B05D7/52IPC - классификация
BB0B05B05CB05C1B05C19B05C19/B05C19/0B05C19/04B05C9B05C9/B05C9/1B05C9/14B05DB05D1B05D1/B05D1/1B05D1/12B05D1/3B05D1/30B05D3B05D3/B05D3/0B05D3/02B05D3/04B05D7B05D7/B05D7/0B05D7/00B05D7/1B05D7/14Цитирование НПИ
EP 709491 A1 19960501JP 2003183707 A 20030703
WO 9429490 A1 19941222
WO 9936210 A1 19990722