AUTOMATIC TURNOVER DEVICE
This application claims the priority and benefit of the Chinese Patent Application No. 201410069989.1, entitled “Automatic Turnover Device”, filed on Feb. 28, 2014, the disclosure of which is incorporated herein by reference in its entirety as part of the present application. The invention relates to the field of industrial control and automation, and more particularly to an automatic turnover device used for opening and closing a turnover piece such as a lid and a door. Products such as household appliances and automobiles generally comprise a turnover piece, for example, a lid and a door. Some turnover pieces are manually opened and closed. However, with the development of technology, people have more and more high requirements on automation of those products, and it is desired that the turnover piece like the lid or door can be automatically opened and closed. In order to implement the automatic opening and closing function of the turnover piece, many manufacturers develop a turnover piece with the automatic opening and closing function. However, the product with such turnover piece still suffers from some problems and cannot fully meet the demands of consumers. For example, most of the existing turnover pieces are directly driven by a motor, and a high-power motor is required in case of a large weight of the turnover piece. The high-power motor not only generates a noise during working, but also is high in power consumption, large in size, inconvenient to assemble, and thus can increases the cost of a whole system. In addition, since a turnover torque of the turnover piece is not linearly changed, the turnover piece cannot be turned over smoothly at a constant speed and is poor in comfort level. Besides, if the motor directly drives the turnover piece with a larger weight, the motor has larger load, such that the motor works at an overload for a long time and is extremely easy to damage and a maintenance cost is increased, a user complains about the quality of the product, and the market competitiveness and the brand image of an enterprise are affected. Furthermore, the existing turnover piece is not automatically stopped in abnormal cases (for example, power failure motor fault or part failure), and is closed downwards under the action of gravity. A human body may be smashed due to a huge impact force in closing, and a safety accident occurs. Besides, since the existing turnover piece is not stopped or ascends oppositely even encountering a counteraction force in the closing process, and rather continues to descend. As result, the human body may be clamped and lead to the safety accident. Therefore, there is a need for a turnover mechanism which is capable of smoothly turning over and is convenient and flexible to operate. In the meantime, such turnover mechanism should be driven by a small-power drive mechanism (for example, a motor, a hydraulic motor or a pneumatic motor). Besides, such turnover mechanism should also have a safety function and a fault warning function. The present invention aims at the above problems in prior art, and an object of the present invention is to provide an automatic turnover device used for opening and closing a turnover piece. With the automatic turnover device of the present invention, the turnover piece can be turned over smoothly, the power and noise of the drive mechanism can be reduced and thus the production cost can be reduced. In addition, with the automatic turnover mechanism according to the present invention, it is ensured that an alarm is given out when the turnover mechanism has a fault, thereby facilitating use and maintenance. Furthermore, with the automatic turnover mechanism according to the present invention, it is ensured that the turnover piece can be safely turned over without causing any safety problem. According to one aspect of the present invention, there is provided an automatic turnover device used for opening and closing a turnover piece, the automatic turnover piece comprises: a base mounted on a device body having the turnover piece; at least one drive mechanism mounted on the base and connected to the turnover piece, and enabling the turnover piece to automatically move between a closed position and an open position; and at least one elastic element configured and mounted to store the predetermined energy when the turnover piece is in the closed position, and to at least partially release the stored predetermined energy during the process that the at least one drive mechanism is driving the turnover piece from the closed position to the open position, thereby at least partially balancing the weight of the turnover piece during the driving process. In one embodiment of the present invention, the automatic turnover device further comprises: at least one rotary shaft, one end of the at least one first rotary shaft of the at least one rotary shaft being connected to an output shaft of the at least one drive mechanism respectively by a coupler and the other end being connected to the turnover piece; and at least one supporting member, rotatably supporting the at least one rotary shaft on the base respectively. In one embodiment of the present invention, one end of at least one second rotary shaft of the at least one rotary shaft is a free end, and the other end is connected to the turnover piece. In one embodiment of the present invention, the automatic turnover device further comprises at least one connecting member connected to the other end of the at least one rotary shaft respectively and used for mounting the turnover device. In one embodiment of the present invention, the number of the at least one supporting member is twice that of the at least one rotary shaft, and each rotary shaft of the at least one rotary shaft is supported by two supporting members. In one embodiment of the present invention, the at least one supporting member is a bearing. In one embodiment of the present invention, the at least one drive mechanism comprises a motor. In one embodiment of the present invention, the automatic turnover device further comprises at least one elastic element mounting portion, respectively fixed to at least one of the at least one first rotary shaft, wherein, one end of the at least one elastic element is connected to the elastic element mounting portion, and the other end of the at least one elastic element is connected to the base respectively. In one embodiment of the present invention, the automatic turnover device further comprises at least one elastic element mounting portion, respectively fixed to at least one of the at least one first rotary shaft and/or the at least one second rotary shaft, wherein, one end of the at least one elastic element is connected to the elastic element mounting portion, and the other end of the at least one elastic element is connected to the base respectively. In one embodiment of the present invention, one or two sides of each elastic element mounting portion of the at least one elastic element mounting portion are provided with at least one elastic element. In one embodiment of the present invention, the elastic element mounting portion is a fixing sleeve fixedly connected to at least one of the at least one second rotary shaft and/or at least one first rotary shaft, wherein both sides or one side of the fixing sleeve in the axial direction are or is provided with a concave portion for containing one end of the elastic element. In one embodiment of the present invention, the elastic element mounting portion is a radial through hole penetrating through the rotary shaft, one end of the elastic element is mounted in the through hole and the other end is mounted to the base. In one embodiment of the present invention, one supporting member for supporting the rotary shaft is arranged on each of both sides of each of the at least one elastic element mounting portion. In one embodiment of the present invention, the at least one elastic element is at least one selected from a group consisting of a torsional spring, a coil spring and a compression spiral spring or any combination thereof. In one embodiment of the present invention, the automatic turnover device further comprises an elastic element mounting base, mounted on the device body having the turnover piece or serving as a part of the device body, wherein, one end of the at least one elastic element is fixed to the mounting base and the other end abuts against the underside of at least a part of the turnover piece. In one embodiment of the present invention, at least one elastic element is at least one selected from a group consisting of a plate spring, a compression spiral spring and a leaf spring or any combination thereof. In one embodiment of the present invention, the at least one drive mechanism comprises a speed reduction motor, and a static torque Mstatic torqueof the speed reduction motor, a maximal load torque Mmaximal turnover piece torqueof the turnover piece and the maximal torque Mmaximal elastic element torqueof the at least one elastic element are set to meet: Mmaximal turnover piece torque>Mstatic torque>Mmaximal turnover piece torque−Mmaximal elastic element torque, such that the turnover piece is capable of stopping in any position in a predetermined interval between the closed position and the open position. In one embodiment of the present invention the automatic turnover device further comprises a cover, the cover and the base together constitute a housing for defining an airtight space, the at least one drive mechanism is contained in the airtight space, wherein the other end of the at least one rotary shaft extends out of the housing respectively. In one embodiment of the present invention, the automatic turnover device further comprises a control system in communication connection with the drive mechanism, wherein the control system monitors a current of the at least one drive mechanism in an opening process of the turnover piece, and gives out a fault warning when the current of the at least one drive mechanism is higher than a first predetermined threshold value. In one embodiment of the present invention, the control system further monitors a current of the at least one drive mechanism in a closing process of the turnover piece, and gives out a fault warning when the current of the at least one drive mechanism is lower than a second predetermined threshold value. In one embodiment of the present invention, the control system further monitors a current of the at least one drive mechanism in a closing process of the turnover piece, gives out a safety warning when the current of the at least one drive mechanism is higher than a third predetermined threshold value and drives the turnover piece toward the open position by the at least one drive mechanism. In one embodiment of the present invention, the control system is in communication connection with an external main control system by a connector disposed outside the base. In one embodiment of the present invention, the automatic turnover device further comprises a control system, wherein the control system is connected to a motor of the at least one drive mechanism and comprises: a controller, being in communication connection with an external main control system and connected to the motor so as to control the motor according to a signal from the external main control system, and comprising at least two AD converters; and a signal acquiring circuit, comprising: a first resistor, one end of the first resistor being connected to one of at least two AD converters and the other end being connected to a power source input end of the motor and used for acquiring a voltage or current signal of the motor; a second resistor, one end of the second resistor being connected to the other of the at least two AD converters, and the other end being connected to a ground terminal of the motor; and a milliohm resistor, one end of the milliohm resistor being connected to the other end of the first resistor and the other end of the milliohm resistor being connected to the ground terminal of the motor, wherein the controller performs differential treatment on the two signals acquired by the two AD converters to eliminate the interference in the collected motor signals. In one embodiment of the present invention, the ground terminal of the motor and the ground terminal of the controller are connected to separate grounds. In one embodiment of the present invention, the signal acquiring circuit further comprises capacitors, connected in parallel with each other, and connected between the other end of the first resistor and the ground of the motor in parallel with the milliohm resistor. In one embodiment of the present invention, the one end of the first resistor is also connected to one end of a filter circuit, the other end of the filter circuit is connected to the terminal of the controller, the one end of the second resistor is connected to one end of another filter circuit, and the other end of the another filter circuit is connected to the ground of the controller. According to another aspect of the present invention, there is provided a control system for controlling motor operation, the control system comprises: a controller, being in communication connection with an external main control system and connected to the motor so as to control the motor according to a signal from an external main control system, and comprising at least two AD converters; and a signal acquiring circuit, comprising: a first resistor, one end of the first resistor being connected to one of at least two AD converters and the other end being connected to a power source input end of the motor and used for acquiring a voltage or current signal of the motor; a second resistor, one end of the second resistor being connected to the other of the at least two AD converters, and the other end being connected to a ground terminal of the motor; and a milliohm resistor, one end of the milliohm resistor being connected to the other end of the first resistor and the other end of the milliohm resistor being connected to the ground terminal of the motor, wherein the controller performs differential treatment on the two signals acquired by the two AD converters to eliminate the interference in the collected motor signals. In one embodiment of the present invention, the ground terminal of the motor and the ground terminal of the controller are connected to separate grounds. In one embodiment of the present invention, the signal acquiring circuit further comprises capacitors, connected in parallel with each other, and connected between the other end of the first resistor and the ground of the motor in parallel with the milliohm resistor. In one embodiment of the present invention, the one end of the first resistor is connected to one end of a filter circuit, the other end of the filter circuit is connected to the ground of the controller, the one end of the second resistor is connected to one end of another filter circuit, and the other end of the another filter circuit is connected to the ground of the controller. According to the automatic turnover device of the present invention, since the elastic element (for example, the torsional spring or plate spring) is installed, the elastic element stores the predetermined energy when the turnover piece is in the closed position, and at least partially releases the stored predetermined energy in the open process of the turnover piece, thereby reducing the torque when the motor drives the turnover piece to open, and causing the turnover piece to be smoothly opened. Therefore, the motor with smaller power can be adopted, and the production cost is reduced. Besides, a motor with smaller powder can be adopted, the noise is small, and thus the comfort level of the operation environment is further improved. In addition, when the turnover piece encounters a counteraction force when closed, the control system can send an instruction to rotate the motor backwards and a clamping preventing function is realized; when any torsional spring is failed, the control system can give out the instruction instantly, such that the turnover piece is turned over upwards to be opened, stops movement when arriving at a final position, and causes the device main body to give out an alarm, thereby greatly improving the use safety performance of the device and greatly improving the market competitiveness and the brand image of an enterprise. Other features, advantages and effects of the present invention become more clear and explicit by means of the description on the exemplary embodiments given in the following accompanying drawings. The exemplary embodiments of the present invention are described exemplarily in detail in combination with the accompanying drawings, wherein in the accompanying drawings: The exemplary embodiments of the present invention will be described with reference to the accompanying drawings. It should be noted that the exemplary embodiments illustrated in the accompanying drawings and described in detail herein are merely intended to make those skilled in the art better understand the present invention rather than limit the present invention to the described and illustrated specific structural form. The protection scope of the present invention is defined by the accompanying claims and equivalents thereof. As shown in The cover 12 covers the base so as to define an airtight space in the housing 1. A motor, rotary shafts and torsional springs of the automatic turnover device 100 (described later) are contained in the airtight space. Since constituting components of the automatic turnover device 100 are contained in the airtight space, foreign matters such as dust and water are prevented from entering the housing 1, and a working noise of the motor, etc., can be reduced. In order to improve the airtightness of the housing 1 consisting of the base 11 and the cover 12, a sealing member (not shown) can be arranged between the base 11 and the cover 12. The sealing member can be in any form, for example, a sealing ring or sealing adhesive. When the base 11 and the cover 12 are assembled together to form the housing 1 defining the airtight space, openings or holes for mounting the bearings 6 described later are defined in two ends of the base 11 and the cover 12. The rotary shaft 3 of the automatic turnover device 100 extends through the bearings 6 in the openings or holes to connect the connecting member 5. As shown in In addition, the rotary shaft 3 can be connected to the connecting member 5 in any proper manner. For example, the rotary shaft 3 can be connected to the connecting member 5 by means of key connection, spline connection, etc. With reference to In the present exemplary embodiment, the drive mechanism 2 comprises a motor and a speed reduction gearbox (not shown). The speed reduction gearbox is used for reducing a high rotating speed output from the motor to a low rotating speed suitable for driving the rotary shaft 3. The speed reduction gearbox can comprise a first speed reduction gear and a second speed reduction gear, wherein the first speed reduction gear is connected to an output shaft of the motor and meshed with the second speed reduction gear, the second speed reduction gear is connected to the output shaft of the drive mechanism, the tooth number of the first speed reduction gear is less than that of the second speed reduction gear, so as to reduce the high rotating speed output from the motor. The tooth number of the first speed reduction gear and the tooth number of the speed reduction gear can be determined according to an expected turnover and opening speed of the turnover piece. Of course, the drive mechanism 2 can only comprise a motor, that is, use the motor to directly drive the rotary shaft 3. The power and number of the motor can be properly selected according to a load torque (for example the weight of the turnover piece) of the turnover piece, a friction, a preset torque of a torsional described later (one preferable example of the elastic element), etc. Although the exemplary embodiment describes that the drive mechanism 2 uses the motor as a drive source, the present invention is not limited thereto. Other drive sources can be selected according to specific application conditions. For example, a hydraulic motor, a pneumatic motor, etc., can be adopted as the drive source. As shown in The rotary shaft 3 is supported on the base 11 using two bearings 6. Preferably, one bearing is mounted in the opening or hole defined by the base 11 and cover 12. The rotary shaft 3 extends out of the housing 1 via the bearing mounted in the opening or hole so as to be connected with the connecting member 5 for mounting the turnover piece. Continuing to refer to It needs to be noted that Continuing to describe with reference to In The example of the elastic element mounting portion is not only limited to the fixing sleeve 7. For example, a fixing way in How to mount the torsional spring 8 is described as follows. When the turnover piece mounted on the connecting member 5 is located in the closed position, the torsional spring 8 is forced to store predetermined energy (for example, elastic potential energy (torque force and torque)), when the drive mechanism 2 (for example the motor) drives the turnover piece from the closed position to the open position, the predetermined energy stored by the torsional spring 8 is released, thus balancing the weight of the turnover piece mounted to the connector during the driving process. That is to say, in the open process, the turnover piece is driven to the open position from the closed position by means of the combination of the drive torque of the drive mechanism 2 and the torque of the torsional spring. Hence, since the torque of the torsional spring assists the drive mechanism to drive the turnover piece during the drive process, compared with a case without using the torsional spring 8, the drive mechanism 2 with smaller power can be adopted. For example, the motor with smaller power can be adopted. Since the power of the motor is smaller, the noise generated during operation of the motor is further reduced, and a comfort level of an operation environment is improved. In addition, the cost of the whole system is reduced since the motor with smaller power is adopted. On another aspect, since the torsional spring is mounted to store predetermined energy when the turnover piece is in the closed position, the turnover piece can be turned over (i.e., opening and closing) more smoothly using a buffering action of the torsional spring. The predetermined energy stored by the torsional spring 8 when the turnover piece is located in the closed position can be set in such a way: when the turnover piece is located in the closed position, the predetermined energy stored by the torsional spring 8 is not enough to open the turnover piece separately. That is to say, the predetermined energy stored by the torsional spring 8 cannot open the turnover piece in a case that the drive mechanism does not drive the turnover piece. Preferably, in the process that the drive mechanism drives the turnover piece to move toward the open position, the torsional spring 8 at least partially releases the stored predetermined energy, therefore, in the process that the turnover piece moves to the open position, a weight action thereof can be at least partially balanced by the predetermined energy of the torsional spring 8, and the drive power required by the motor of the drive mechanism is thud reduced. In addition, when the turnover piece arrives at the open position, preferably, the torsional spring 8 still remains at least one part of the pre-stored energy (elastic potential energy). In this way, even the turnover piece is located in the open position, the torsional spring 8 can also keep certain tension using the remaining torque force thereof. In above description, the torsional spring is configured and mounted to store the predetermined energy when the turnover piece is in the closed position, and to at least partially release the stored predetermined energy when the at least one drive mechanism is driving the turnover piece from the closed position to the open position, thus at least partially balancing the weight of the turnover piece during the driving process. Under the teaching of the present invention, those skilled in the art can properly select various design parameters of the torsional spring according to specific working load (the weight, friction force and the like of the turnover piece), a turnover angle of the turnover piece and required predetermined stored energy (for example, elastic potential energy), thereby meeting the above requirements of the present invention. For example, those skilled in the art can calculate rigidity of the torsional spring according to the following formula: wherein, E is elastic modulus, d is steel wire diameter, D is the mean diameter of the torsional spring, and n is the number of active coils or turns. A working torque of the torsional spring is calculated according to the above formula (1): T1=T′*φ (N·mm), wherein, φ is a working angle (°) of the torsional spring. Thus it can be seen that the torque of the torsional spring is in direct proportion to the working angle thereof. The torque of the turnover piece is calculated according to the weight and gravity center of the turnover piece, and the remaining torque when the turnover piece is located in the open position is considered to determine the pre-stored torque (elastic potential energy) required when the turnover piece is located in the closed position. In addition, in a case that the drive mechanism comprises a static motor, a static torque Mstatic torqueof the static motor of the at least one drive mechanism, a maximal load torque Mmaximal turnover piece torqueof the turnover piece and the maximal torque Mmaximal elastic element torqueof the at least one elastic element (for example the torsional spring) are set to meet: Mmaximal turnover piece torque>Mstatic torque>Mmaximal turnover piece torque−Mmaximal elastic element torque, such that the turnover piece is capable of stopping in any position in a predetermined interval between the closed position and the open position. If the turnover piece is C degrees (for example 0 degree generally) when in the closed position and P degrees when in a fully open position (relative to the closed position), then a range of the predetermined interval is for example, from (C+X degrees) to (P−Y) degrees. In some examples, X can be 1-20 degrees, and preferably 5-15 degrees, Y can be 1-20 degrees and preferably 5-15 degrees. Of course, X and Y can be other values according to the elastic characteristic of the selected elastic element (for example, the torsional spring), thereby defining different predetermined intervals. When the turnover piece is located in a horizontal position, a load torque of the turnover piece is the maximal, while the elastic element (for example the torsional spring) has the maximal torque in the closed position, and stores the maximal torque, that is, store the predetermined energy. For the cases that the elastic element adopts other forms (for example, a coil spring and a compression spiral spring), the predetermined energy that the elastic element needs to store when the turnover piece is in the closed position can be determined in a similar way. The above described the example that the torsional spring 8 and the fixing sleeve 7 are adopted as the elastic element and the elastic element mounting portion. However, the elastic element and the elastic element mounting portion can also adopt other forms. For example, if the required torque is smaller, a coil spring can be adopted except for the torsional spring. In a case that the coil spring is adopted, the inner end of the coil spring is directly fixed to the rotary shaft 3 and the other end is fixed to the base 11. In such a case, a part of the rotary shaft 3 serves as the elastic element mounting portion. Similarly, when the turnover piece is located in the closed position, the coil spring is forced to store the predetermined energy and releases the stored predetermined energy in a process that the drive mechanism 2 drives the turnover piece toward the open position from the closed position, thus at least partially balancing an opening resistance or weight action of the turnover piece. The predetermined energy that the coil spring needs to store can be determined by referring to the manner of determining the predetermined energy stored by the torsional spring. In addition, the compression spiral spring can be selected. In a case of selecting the compression spiral spring, one end of the compression spring is fixed to the fixing sleeve 7, and the other end is fixed to the base 11. Similarly, the compression spring is mounted to store the predetermined energy when the turnover piece is in the closed position, and to release the stored predetermined energy when the drive mechanism 2 is driving the turnover piece from the closed position to the open position, thus at least partially balancing the weight of the turnover piece during the driving process. Therefore, the compression spiral spring and the coil spring can achieve the same action and effect as those of the torsional spring. As the elastic element mounting portion, except for the fixing sleeve 7, other forms of elastic element mounting portion can also be adopted. For example, one end of a U-shaped platelike member having a shape consistent with the shape of the rotary shaft 3 can be fixed to the rotary shaft by welding or other manners, and the other end is provided with a hole. One end of the elastic element such as the torsional spring can be fixed to the hole, and the other end is fixed to the base 11. The torsional spring 8 can sleeve the rotary shaft 3. Those skilled in the art can adopt other types of elastic elements and corresponding fixing manners according to specific application. The operation process of the automatic turnover mechanism 100 is described by taking the exemplary embodiments as shown in As shown in When the control system 9 receives a starting signal from the external main control system, the drive mechanism 2 is started. At this point, the turnover piece is located in the closed position, and the torsional spring 8 stores predetermined energy. When the opening instruction is received, the drive mechanism 2 drives the rotary shaft 3 to rotate by the coupler 4, under the action of the bearing 6, the rotary shaft 3 stably rotates, and the rotary shaft 3 drives the connecting member 5 and the turnover piece to turn over. Since the fixing sleeve 7 is fixed to the rotary shaft 3, the fixing sleeve 7 and the rotary shaft 3 rotate together. Along with the rotation of the fixing sleeve 7, the predetermined energy stored by the torsional spring 8 is gradually released, thus balancing the weight of the turnover piece. Since the energy pre-stored by the torsional spring assists the drive mechanism to open the turnover piece, the torque to drive the rotary shaft by the drive mechanism 2 is smaller, therefore, the drive mechanism with small power can be adopted and the noise of the drive mechanism is thus reduced. In addition, since the motor of the drive mechanism can work under smaller load, the stability is ensured, the reliability of the product is thus improved and the turnover piece is smoothly turned over. In the exemplary embodiment as shown in Another exemplary embodiment is described with reference to The automatic turnover mechanism 101 as illustrated in As shown in Two bearings 6 are mounted on two sides of the fixing sleeves 7 and the torsional springs 8 respectively, and the bearings 6 can support the rotary shaft 3 in the base 11 rotatably. In the exemplary embodiment as shown in In a case of disposing two torsional springs 8, the specific design parameters of the torsional springs 8 are determined according to the weight (working load) and gravity center of the turnover piece, the turnover angle of the turnover piece, etc. The two torsional springs are unnecessary to have the same design parameters as long as their combinations can store the predetermined energy when the turnover piece is in the closed position, and at least partially release the stored predetermined energy when the at least one drive mechanism is driving the turnover piece from the closed position to the open position, thus at least partially balancing the weight of the turnover piece during the driving process. In addition, any combination of the torsional spring, the coil spring and the compression spiral spring can be adopted without fully adopting torsional springs. A working process of the automatic turnover mechanism as illustrated in FIG. 3 and A further exemplary embodiment of the automatic turnover piece of the present invention is described with reference to The automatic turnover mechanism 102 as illustrated in As shown in In the embodiment as illustrated in An operation manner of the automatic turnover mechanism 102 is same as that of the automatic turnover mechanism 100. The automatic turnover device 103 of the present invention is described with reference to The automatic turnover mechanism 103 as illustrated in As shown in In the embodiment as illustrated in Similarly, in the embodiment as shown in As shown in In the embodiment as illustrated in The predetermined energy can be set as follows: in the process that the cover plate 43 moves to the open position from the closed position, the plate spring 42 at least partially releases the stored predetermined energy. But preferably, when the cover plate 43 is located in the open position, the plate spring 42 is not recovered to its free state completely. Thus, it can be ensured that the plate spring 42 firmly abuts against the cover plate 43 with proper tension. The torque of the turnover piece can be calculated according to the weight and gravity center of the turnover piece, and the parameters of the plate spring 42 are determined according to a turnover angle of the turnover piece, the predetermined energy that the plate spring 42 needs to store when the turnover piece is in the closed position, and the remaining energy of the plate spring 42 when the turnover piece is located in the fully open position. As abovementioned, the automatic turnover piece 100 further comprises a control system 9. The control system 9 is communicatively connected with an external main control system (for example, a main control system of a device having a turnover piece) and the drive mechanism 2. The control system 9 receives a signal (for example, a starting signal, a reset signal or other signals) from the external main control system, analyzes and processes the external input signal, and then sends a control instruction to control the operation of the motor of the drive mechanism. For example, the motor rotates forwards to close the turnover piece, the motor rotates backwards to open the turnover piece. In addition, the control system monitors a current of the motor. A protection control signal is sent if the current is abnormal to correspondingly control the motor. An operation process of the control system 9 is described in detail with reference to the automatic turnover device 100 as illustrated in As illustrated in In addition, in the closing process of the turnover piece, the control system 9 also detects the current of the motor. If the current of the motor is lower than a second predetermined threshold value, it is indicated that the torsional spring 8 does not buffer the closing action of the turnover piece, and thus the predetermined energy cannot be stored using the weight of the turnover piece, therefore it is judged that the torsional spring 9 has a fault (failed or falling off). In such case, the control system gives out a warning. In addition, in the closing process of the turnover piece, if the current of the motor is larger than a third predetermined threshold value, it is indicated that the turnover piece clamps or collides other objects (for example the hand of a child) in the closing process. In such case, the control system 9 controls the drive mechanism 2 to rotate backwards, thus enabling the turnover piece to rotate to an opening direction to avoid clamping or damaging the objects. When the control system 9 receives a reset signal, the control system 9 controls the drive mechanism 2, closes the turnover piece, and enables the torsional spring 8 to store energy in the closing process. The singlechip U2 receives a control instruction from the external main control system by pins 3, 4, 5 and controls the motor of the drive mechanism 2 by means of two pins key5 and key6, that is, control the motor to rotate forwards and backwards. The reference number 131 in The other end of the resistor R4 is connected to one end of the resistor R2 at AD1, and the AD1 is connected to a power source input end of the motor and is used for sampling a voltage or current signal of the motor. The other end of the resistor R2 is connected to a ground GND2, and the other end AD2 of the resistor R3 is connected to the GND2. Two capacitors EC3 and C3 are connected in parallel between the AD1 and AD2. In addition, a filter circuit consisting of a resistor R6 and a capacitor EC6 are connected between the pin 1 of the U2 and the resistor R4 and between the pin 2 of the U2 and the resistor R3. The filter circuit is used for filtering signals of the input pins 1, 2 to make the signals more smooth. As abovementioned, the AD1 is connected to a power source input end of the motor so as to sample the voltage or current of the motor. When the motor operates, a signal sampled from the AD1 is input to the pin 1 of the U2 as one input signal of the AD converter of U2 via the resistor R4. Meanwhile, the AD2 signal (zero voltage theoretically) connected to the ground GND2 is input to the pin 2 of the U2 via the resistor R3. The U2 performs differential treatment on the two input signals by means of software so as to eliminate the interference in the acquired motor signals. In the traditional motor signal acquiring solution, usually, the motor signals are directly input to one channel of AD converter of the singlechip by a differential amplifier. The solution has the defects that the amplifier occupies the space of a circuit board and the cost is higher. While in the present invention, the multiple channels of AD of the singlechip are used, and two signals (one signal is the motor signal and the other signal is a reference signal, i.e., a ground signal) are input via two channels. Thus, the interference to the motor signal can be eliminated by performing differential treatment via software programming of the singlechip. In addition, the inventor also found in the experiment that if the ground terminals of the signal acquiring circuit and the singlechip U2 are connected to the same ground, as the signal acquiring circuit and the motor share the same ground, the inducted high electromotive force produced during the process the motor frequently turns on and off can interfere with the singlechip and even cause system damage. Therefore, in the present invention, the ground terminal of the signal acquiring circuit and the ground terminal of the motor are connected to the GND2, and the ground terminal of the singlechip is connected to a different ground GND3. Hence, since the ground terminal of the motor and the ground terminal of the singlechip are connected to different grounds, the influence on the singlechip caused by frequently turning on and off the motor is avoided and a sampling precision and stability of the motor signal are further improved. In addition, It should be noted that the specific type and resistance values and capacitance values of the resistors and capacitors as shown in Other circuit structures are not related to the theme of the present invention and belong to a common technology in the art that is not repeated here. Although the present invention has been described with reference to the exemplary embodiments as illustrated in the accompanying drawings, the present invention is not limited to the described specific embodiments. In the spirit and scope of the present invention, those skilled in the art can perform various modifications and changes on the exemplary embodiments. The scope of the present invention is defined by accompanying claims and equivalents thereof. An automatic turnover device for opening and closing a turnover piece is disclosed. The automatic turnover device comprises a base (11) mounted on the device body having a turnover piece; at least one drive mechanism (2) mounted on the base (11) and connected to the turnover piece, and enabling the turnover piece to automatically move between a closed position and an open position; and at least one elastic element configured and mounted to store the predetermined energy when the turnover piece is in the closed position, and to at least partially release the stored predetermined energy during the process the at least one drive mechanism is driving the turnover piece from the closed position to the open position, thereby at least partially balancing the weight of the turnover piece during the driving process 1. An automatic turnover device for opening and closing a turnover piece, comprising:
a base mounted on a device body having the turnover piece; at least one drive mechanism mounted on the base and connected to the turnover piece, and enabling the turnover piece to automatically move between a closed position and an open position; and at least one elastic element configured and mounted to store predetermined energy when the turnover piece is in the closed position, and to partially release the stored predetermined energy during the process that the at least one drive mechanism is driving the turnover piece from the closed position to the open position, thereby at least partially balancing the weight of the turnover piece during the driving process. 2. The automatic turnover device according to at least one rotary shaft, one end of the at least one first rotary shaft of the at least one rotary shaft being connected to an output shaft of the at least one drive mechanism respectively by a coupler and the other end being connected to the turnover piece; and at least one supporting member, rotatably supporting the at least one rotary shaft on the base respectively. 3. The automatic turnover device according to 4. The automatic turnover device according to 5. The automatic turnover device according to 6-7. (canceled) 8. The automatic turnover device according to 9. The automatic turnover device according to 10. The automatic turnover device according to 11. The automatic turnover device according to 12. The automatic turnover device according to 13. The automatic turnover device according to 14. (canceled) 15. The automatic turnover device according to 16. (canceled) 17. The automatic turnover device according to 18. The automatic turnover device according to 19. The automatic turnover device according to 20. The automatic turnover device according to 21. The automatic turnover device according to 22. (canceled) 23. The automatic turnover device according to a controller, being in communication connection with an external main control system and connected to the motor so as to control the motor according to a signal from the external main control system, and comprising at least two AD converters; and a signal acquiring circuit, comprising:
a first resistor, one end of the first resistor being connected to one of the at least two AD converters and the other end being connected to a power source input end of the motor and used for acquiring a voltage or current signal of the motor; a second resistor, one end of the second resistor being connected to the other of the at least two AD converters, and the other end being connected to a ground terminal of the motor; and a milliohm resistor, one end of the milliohm resistor being connected to the other end of the first resistor and the other end of the milliohm resistor being connected to the ground terminal of the motor, wherein the controller performs differential treatment on the two signals acquired by the two AD converters to eliminate the interference in the acquired motor signals. 24-25. (canceled) 26. The automatic turnover device according to 27-30. (canceled) 31. The automatic turnover device according to CROSS REFERENCE OF RELATED APPLICATION
TECHNICAL FIELD
BACKGROUND OF THE ART
SUMMARY OF THE INVENTION
BRIEF DESCRIPTION OF THE DRAWINGS
DETAILED DESCRIPTION
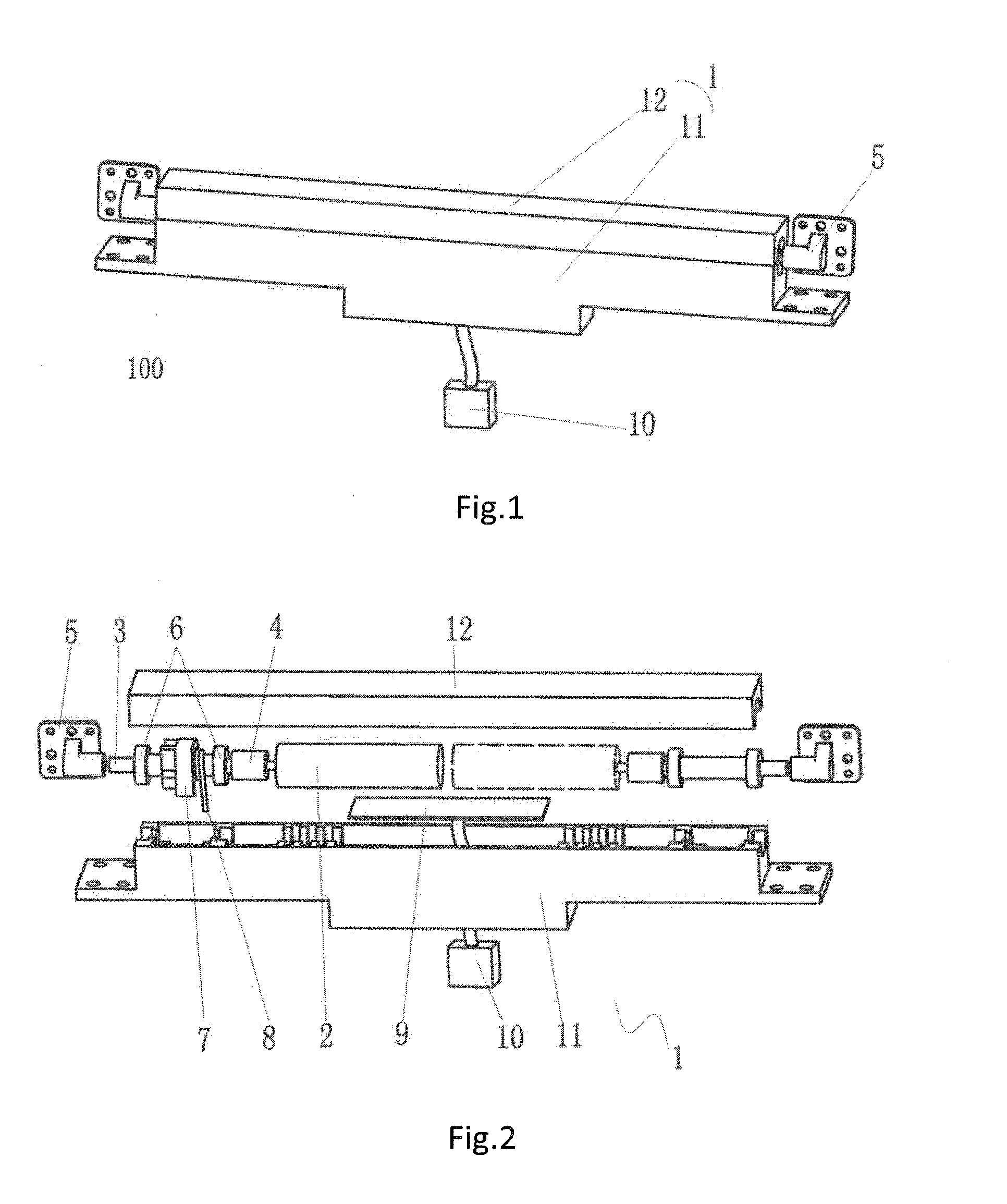
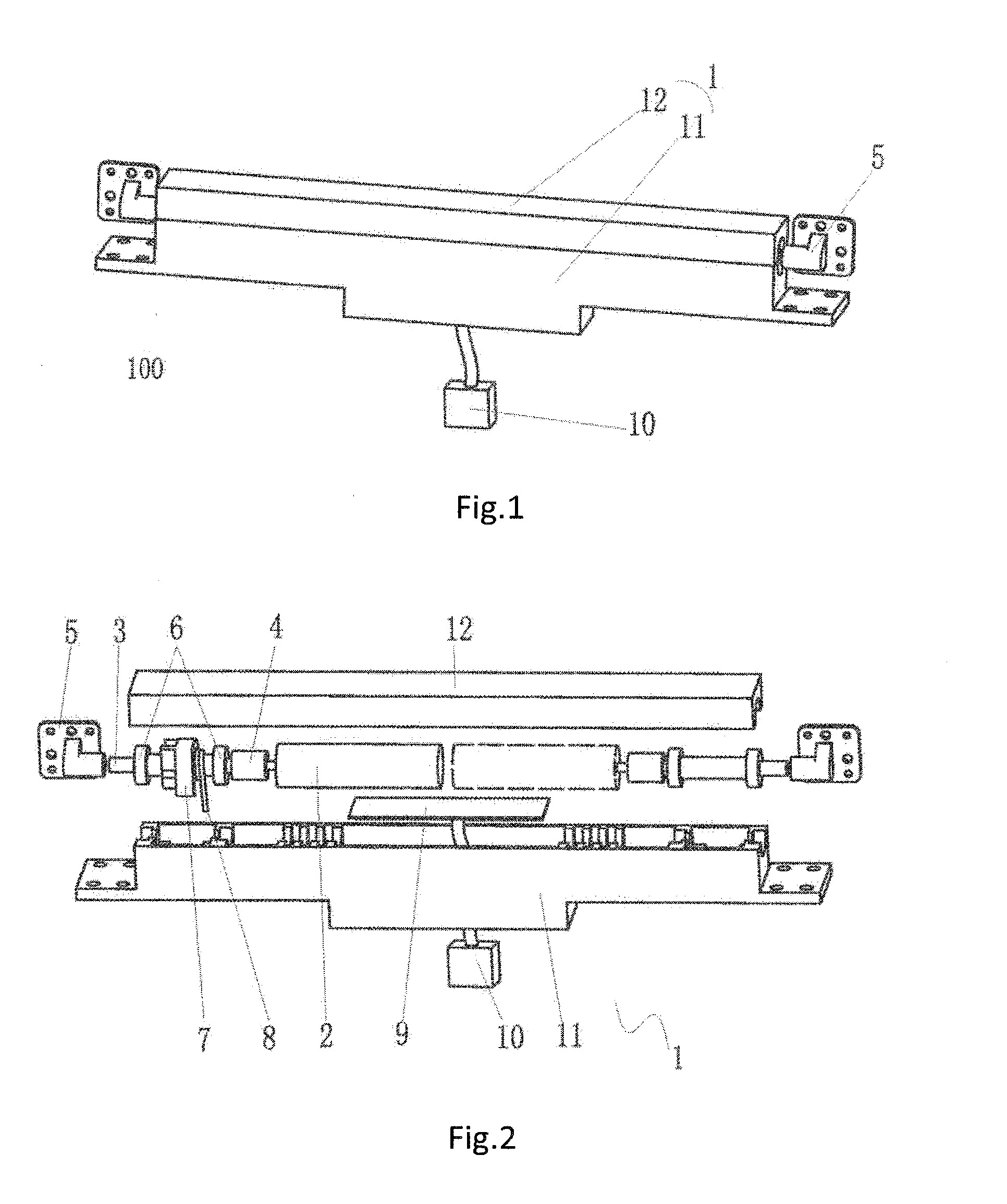
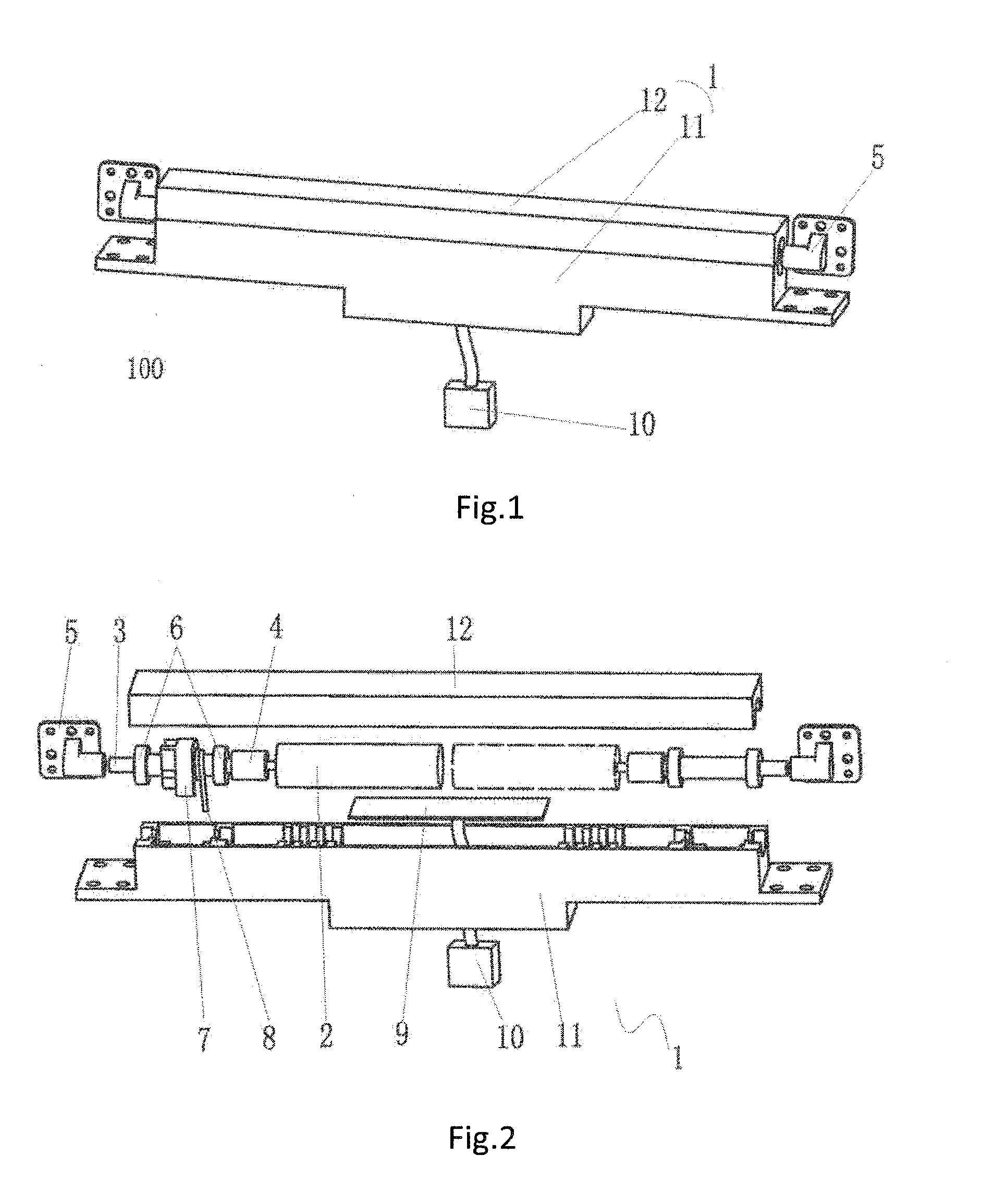
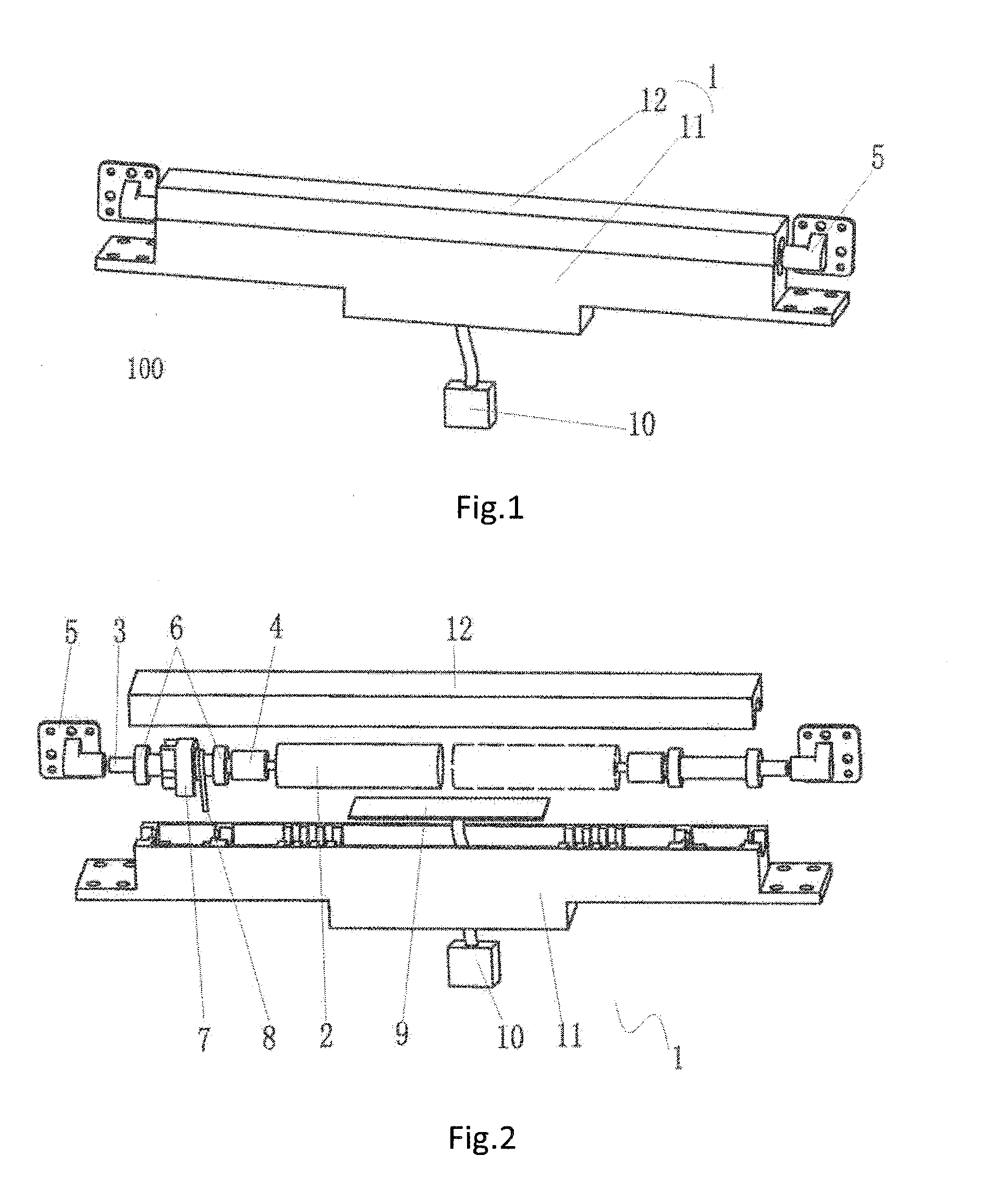
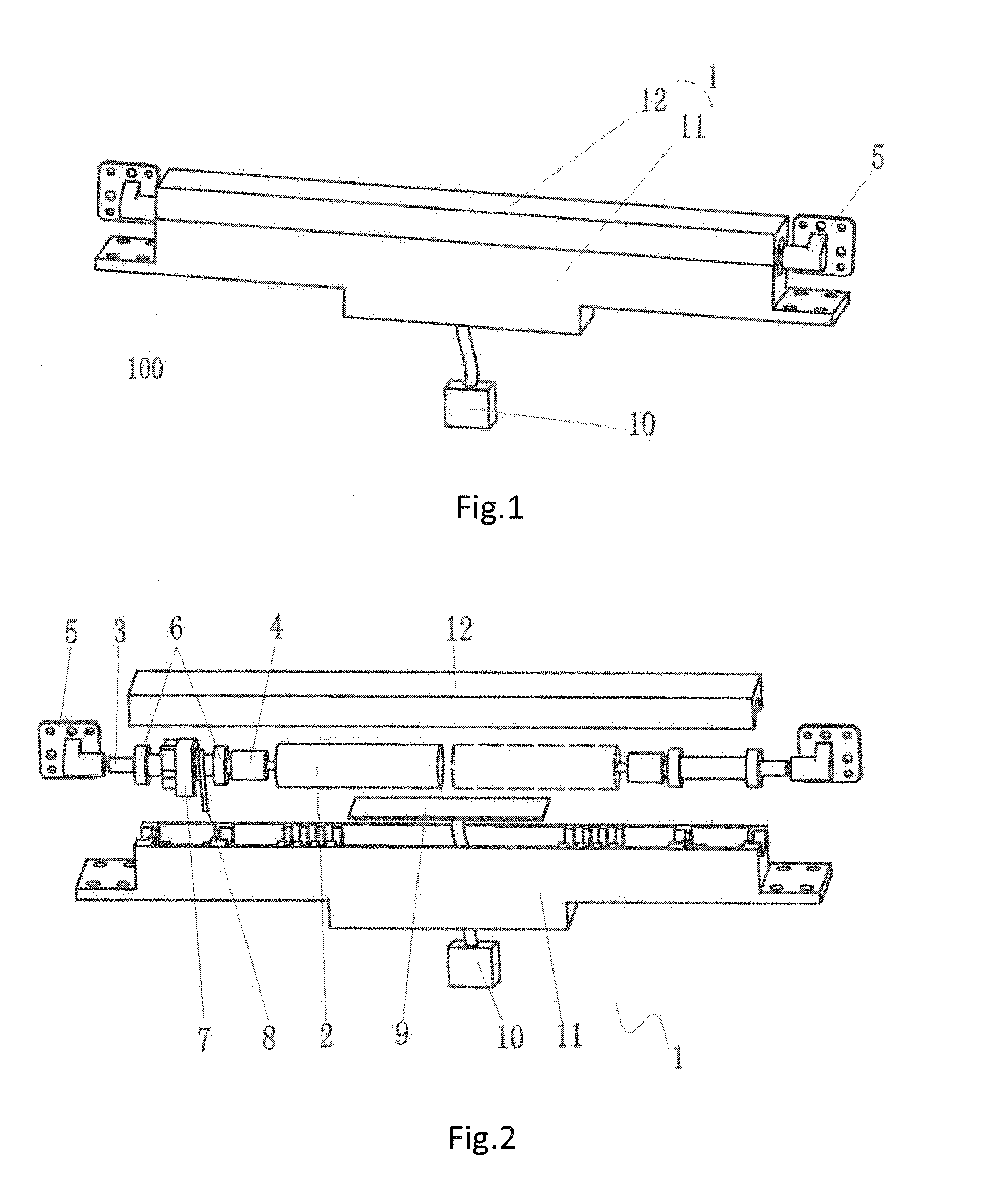
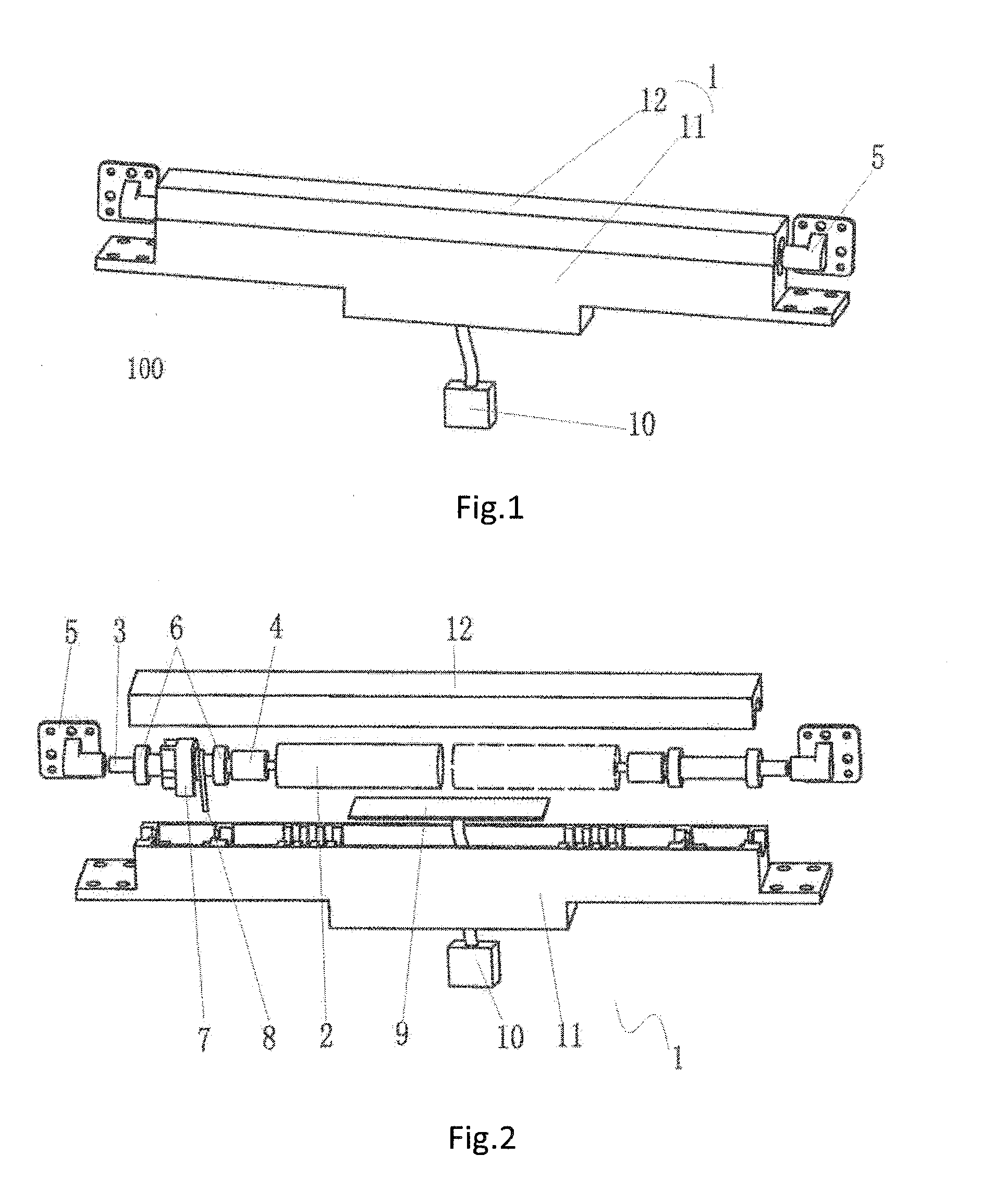
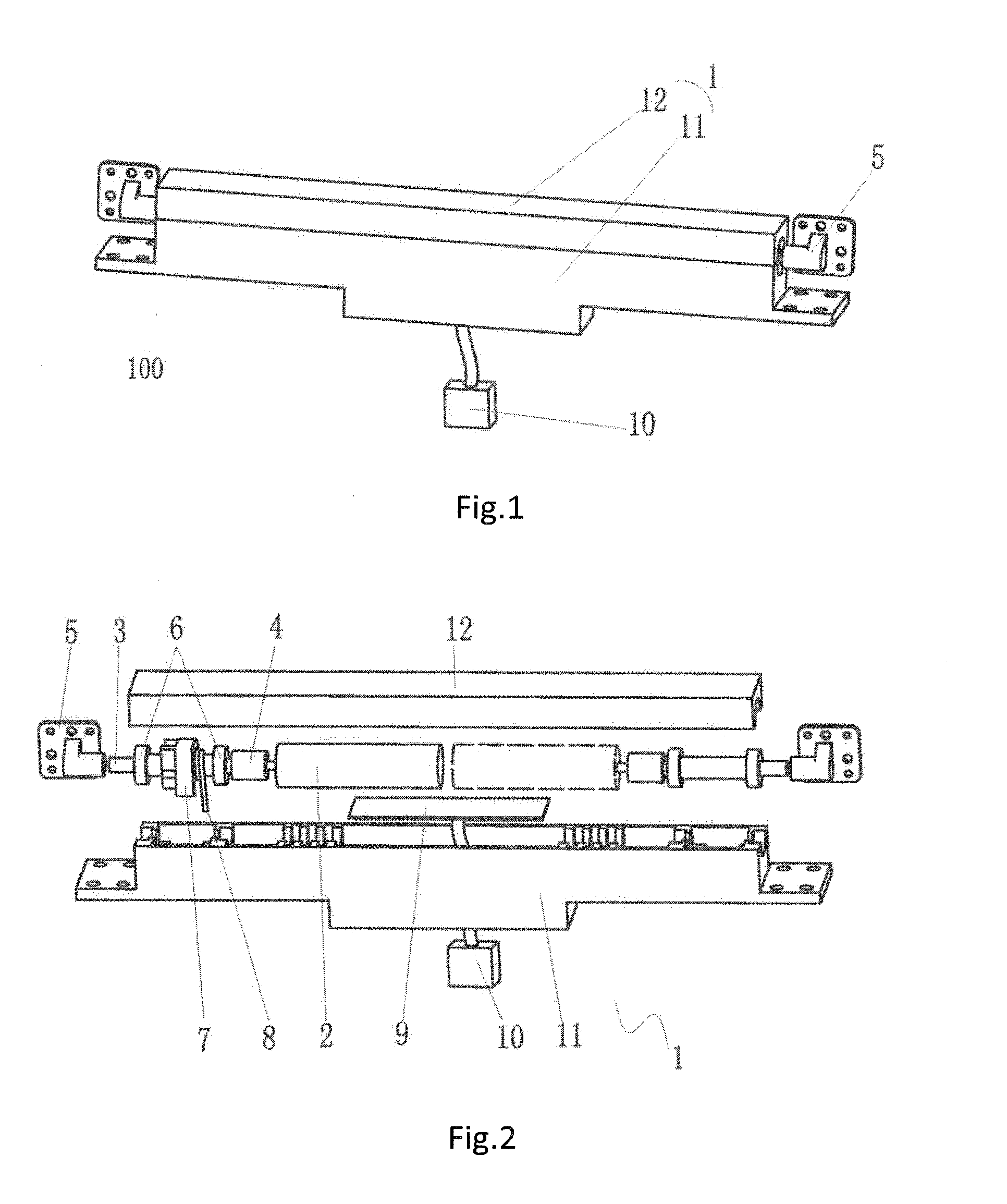
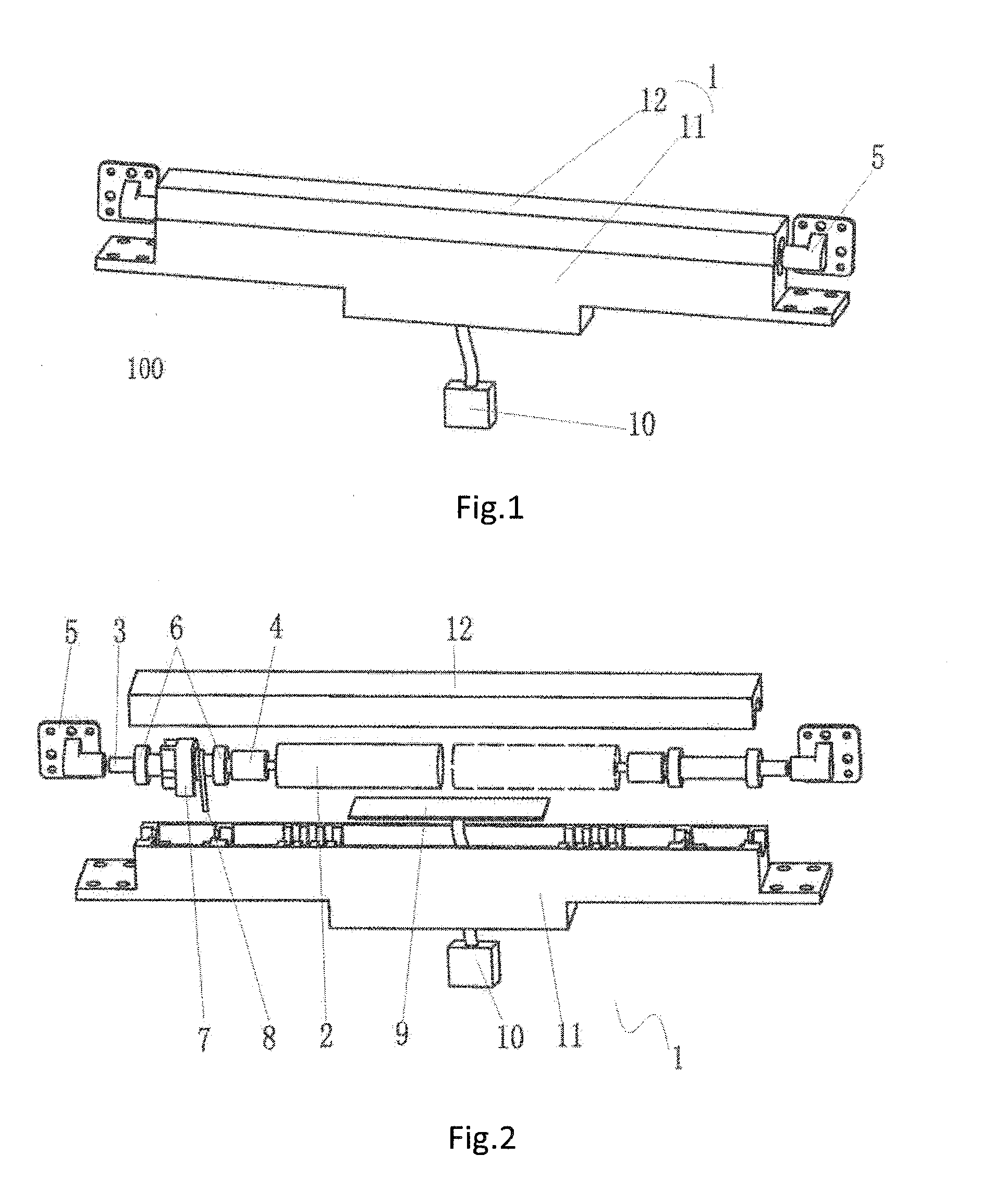
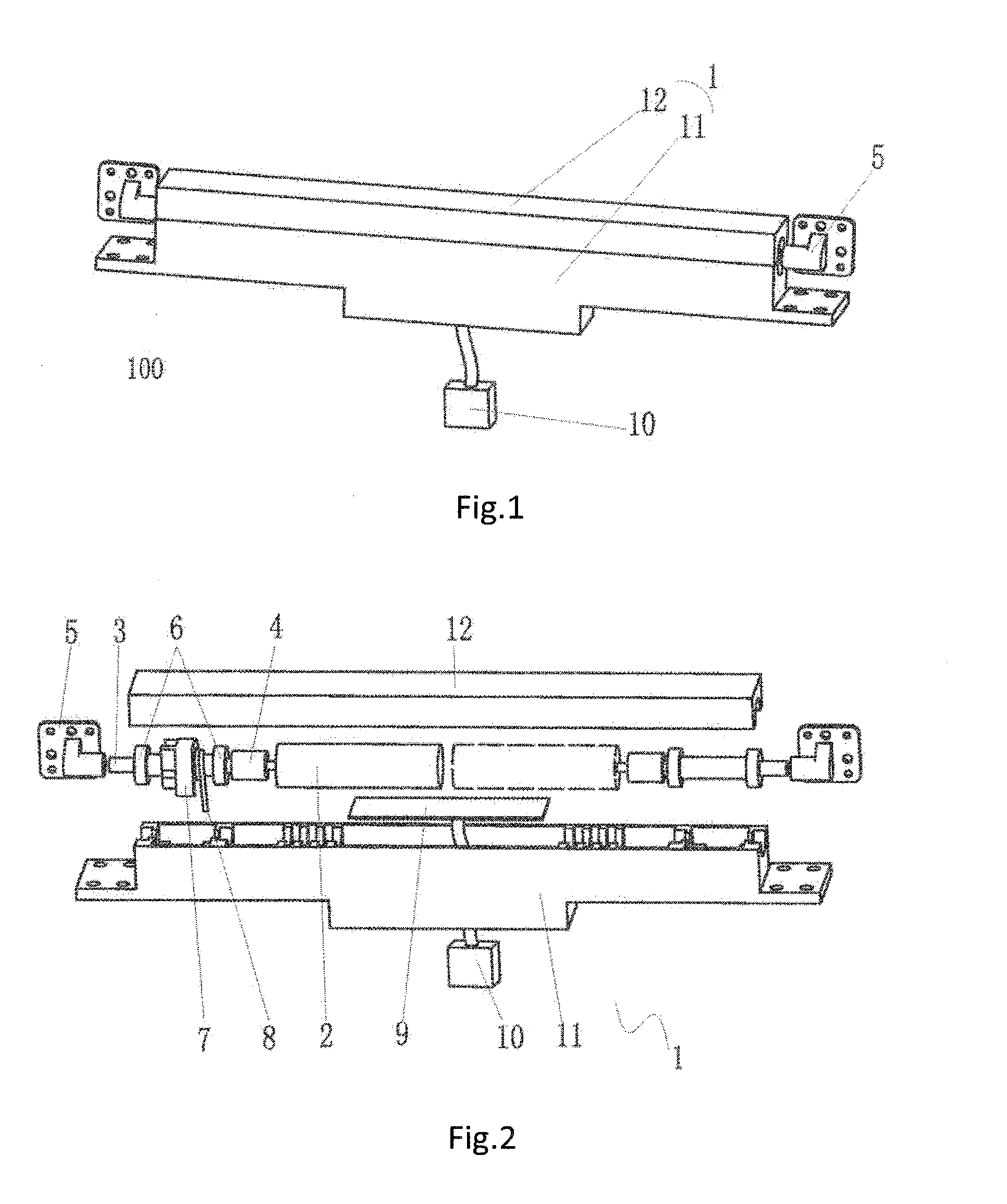