HIGH-STRENGTH COLD ROLLED STEEL SHEET HAVING EXCELLENT SHEAR PROCESSABILITY, AND MANUFACTURING METHOD THEREFOR
The present disclosure relates to a high-strength cold rolled steel sheet having high shear processability, and a method for manufacturing the high-strength cold rolled steel sheet. Parts, such as the friction plates of automatic transmissions of automobiles, are required to have an ability of suppressing the propagation of cracks in under frictional heat conditions and to have high strength and hardness in addition to having crack resistance in a shearing process. In the related art, as disclosed in Patent Document 1, a technique, in which low carbon steel or steel having various alloying elements is annealed by a recovery annealing method after a cold rolling process, has been applied to high-strength cold rolled steel sheets used for friction plates or guaranteeing hardness. In addition, a method of performing a spheroidizing heat treatment on high carbon steel has generally been used, and Patent Document 2 has proposed a technique in which cold rolling is performed twice, in a process of cold rolling, annealing, and cold rolling. However, it is difficult to manufacture high-strength steel sheets using the recovery annealing method, and techniques using the spheroidizing heat treatment method and performing cold rolling twice incur high manufacturing costs. In addition, although alloying elements such as carbon (C), silicon (Si), manganese (Mn), molybdenum (Mo), or chromium (Cr), mainly used to manufacture high-strength steel sheets through cold rolling, are effective in improving the strength of steel sheets through solid-solution strengthening, the excessive addition of such elements causes segregation of the elements and formation of non-uniform microstructures. In particular, ferrite transformation is markedly delayed because of an increase in the hardenability of steel during cooling, low-temperature phases (martensite and austenite) are formed, and grain boundaries become non-uniform. Thus, cracks increase during a shearing process, and if frictional heat is generated during operations, cracks may easily propagate and form defects. In addition, if alloying elements such as titanium (Ti), niobium (Nb), or vanadium (V) used for additional strength improvements are improperly added, coarse carbides, nitrides, and precipitates are formed along grain boundaries, thereby increasing formation of cracks and facilitating propagation of cracks during a shearing process. Furthermore, if frictional heat is generated on a sheared portion during an operation, the propagation of cracks may more easily occur. (Patent Document 1) Application No: KR 1998-0059809 (Patent Document 2) Application No: DE 2005-031462 Aspects of the present disclosure may provide a high-strength cold rolled steel sheet having high shear processability and capable of suppressing the formation of cracks in a shearing process and under frictional heat conditions, and a method for manufacturing the high-strength cold rolled steel sheet. Aspects of the present disclosure are not limited to the above-mentioned aspects. The above-mentioned aspects and other aspects of the present disclosure will be clearly understood by those skilled in the art through the following description. According to an aspect of the present disclosure, there may be provided a high-strength cold rolled steel sheet having high shear processability, the high-strength cold rolled steel sheet including, by wt %, carbon (C): 0.05% to 0.10%, silicon (Si): 0.01% to 0.5%, manganese (Mn): 1.2% to 2.0%, aluminum (Al): 0.01% to 0.1%, chromium (Cr): 0.005% to 0.3%, boron (B): 0.0003% to 0.0010%, molybdenum (Mo): 0.005% to 0.2%, phosphorus (P): 0.001% to 0.05%, sulfur (S): 0.001% to 0.01%, nitrogen (N): 0.001% to 0.01%, niobium (Nb): 0.005% to 0.08%, titanium (Ti): 0.005% to 0.13%, vanadium (V): 0.005% to 0.2%, and a balance of iron (Fe) and inevitable impurities, wherein the high-strength cold rolled steel sheet may satisfy Formulas 1 and 2 below, and may include at least one of carbides, nitrides, and carbonitrides. According to another aspect of the present disclosure, a method for manufacturing a high-strength cold rolled steel sheet having high shear processability may include: reheating a steel slab to a temperature of 1200° C. to 1350° C., the steel slab including, by wt %, carbon (C): 0.05% to 0.10%, silicon (Si): 0.01% to 0.5%, manganese (Mn): 1.2% to 2.0%, aluminum (Al): 0.01% to 0.1%, chromium (Cr): 0.005% to 0.3%, boron (B): 0.0003% to 0.0010%, molybdenum (Mo): 0.005% to 0.2%, phosphorus (P): 0.001% to 0.05%, sulfur (S): 0.001% to 0.01%, nitrogen (N): 0.001% to 0.01%, niobium (Nb): 0.005% to 0.08%, titanium (Ti): 0.005% to 0.13%, vanadium (V): 0.005% to 0.2%, and a balance of iron (Fe) and inevitable impurities, the steel slab satisfying Formulas 1 and 2 below; hot rolling the heated steel slab within a temperature range of 850° C. to 1150° C. to form a hot rolled steel sheet; after the hot rolling, cooling the hot rolled steel sheet to a temperature of 550° C. to 750° C. and coiling the cooled hot rolled steel sheet; and after the coiling, pickling the hot rolled steel sheet and cold rolling the hot rolled steel sheet at a reduction ratio of 60% to 70%. (In Formulas 1 and 2, each element symbol refers to the weight percent (wt %) of the corresponding element.) The above-described aspects of the present disclosure do not include all aspects or features of the present disclosure. Other aspects or features, and effects of the present disclosure will be clearly understood from the following descriptions of exemplary embodiments. The present disclosure provides a high-strength cold rolled steel sheet having high shear processability and capable of suppressing the formation of cracks in a shearing process and under frictional heat conditions in addition to having high strength and high hardness, and a method of manufacturing the high-strength cold rolled steel sheet. Embodiments of the present disclosure will now be described in detail. The disclosure may, however, be exemplified in many different forms and should not be construed as being limited to the specific embodiments set forth herein. Rather, these embodiments are provided so that this disclosure will be thorough and complete, and will fully convey the scope of the present disclosure to those skilled in the art. Hereinafter, a high-strength cold rolled steel sheet having high shear processability of the present disclosure will be described in detail. In the following description, the content of each alloying element is given in wt %, unless otherwise specified. The high-strength cold rolled steel sheet having high shear processability of the present disclosure includes, by wt %, carbon (C): 0.05% to 0.10%, silicon (Si): 0.01% to 0.5%, manganese (Mn): 1.2% to 2.0%, aluminum (Al): 0.01% to 0.1%, chromium (Cr): 0.005% to 0.3%, boron (B): 0.0003% to 0.0010%, molybdenum (Mo): 0.005% to 0.2%, phosphorus (P): 0.001% to 0.05%, sulfur (S): 0.001% to 0.01%, nitrogen (N): 0.001% to 0.01%, niobium (Nb): 0.005% to 0.08%, titanium (Ti): 0.005% to 0.13%, vanadium (V): 0.005% to 0.2%, and a balance of iron (Fe) and inevitable impurities, wherein the high-strength cold rolled steel sheet satisfies Formulas 1 and 2 below and includes at least one of carbides, nitrides, and carbonitrides. Carbon (C): 0.05% to 0.10% Carbon (C) is the most economical and effective element in strengthening steel, and as the content of carbon (C) increases, tensile strength increases by the effect of precipitation strengthening or an increase in the fraction of bainite. However, if the content of carbon (C) is less than 0.05%, reactions with titanium (Ti), niobium (Nb), and vanadium (V) for forming precipitates are reduced, and thus, the effect of precipitation strengthening is low. Conversely, if the content of carbon (C) is greater than 0.10 wt %, coarse carbides are easily formed along grain boundaries, and shear processability is poor because fine cracks are formed along coarse carbide interfaces during a shearing process. Therefore, it may be preferable that the content of carbon (C) be within the range of 0.05 wt % to 0.10 wt %. Silicon (Si): 0.01% to 0.5% Silicon (Si) has a deoxidizing effect on molten steel and a solid-solution strengthening effect, and improves formability by delaying the formation of coarse carbides. However, if the content of silicon (Si) is less than 0.01%, the effect of delaying the formation of carbides is low, and thus it may be difficult to improve formability. Conversely, if the content of silicon (Si) is greater than 0.5%, the surface quality of the steel sheet may be markedly worsened because red scale may be formed on the surface of the steel sheet during a hot rolling process, and the ductility and weldability of the steel sheet may also be worsened. Therefore, it may be preferable that the content of silicon (Si) be within the range of 0.01% to 0.5%. Manganese (Mn): 1.2% to 2.0% Like silicon (Si), manganese (Mn) is an effective element having a solid-solution strengthening effect on steel and facilitating the formation of bainite in a weld heat affected zone after a welding process by increasing the hardenability of the steel. However, if the content of manganese (Mn) is less than 1.2%, these effects may not be sufficiently obtained by the addition of manganese (Mn). Conversely, if the content of manganese (Mn) is greater than 2.0%, hardenability markedly increases to result in a delay in ferrite transformation and a decrease in the effect of precipitation strengthening. In addition, when a slab is manufactured through a continuous casting process, segregation markedly occurs in a thickness wise center portion, and thus a non-uniform microstructure is formed in a thickness direction during cooling after a hot rolling process, thereby markedly increasing cracks in a shearing process. Therefore, it may be preferable that the content of manganese (Mn) be within the range of 1.2% to 2.0%. Molybdenum (Mo): 0.005% to 0.2% Molybdenum (Mo) has a solid-solution strengthening effect and increases hardenability, thereby increasing the strength of steel. However, if the content of molybdenum (Mo) is less than 0.005%, these effects may not be obtained. If the content of molybdenum (Mo) is greater than 0.2%, hardenability excessively increases, thereby delaying ferrite transformation and decreasing precipitation strengthening. In addition, it has a negative effect on economical aspects and weldability. Therefore, it may be preferable that the content of molybdenum (Mo) be within the range of 0.01% to 0.2%. Chromium (Cr): 0.005% to 0.3% Chromium (Cr) has a solid-solution strengthening effect and increases hardenability, thereby increasing the strength of steel. However, if the content of chromium (Cr) is less than 0.005%, these effects may not be obtained. Conversely, if the content of chromium (Cr) is greater than 0.3%, ferrite transformation is excessively delayed, and thus martensite is formed to result in poor elongation. In addition, the effect of precipitation strengthening is reduced. Furthermore, like in the case of manganese (Mn), segregation markedly increases in a thickness wise center portion, and a non-uniform microstructure is formed in a thickness direction to result in poor sheer processability. Therefore, it may be preferable that the content of chromium (Cr) be within the range of 0.005% to 0.3%. Boron (B): 0.0003% to 0.0010% If even a small amount of boron (B) is added to steel, the hardenability of the steel improves. If the content of boron (B) is greater than 0.0003%, boron (B) may segregate along austenite grain boundaries at high temperatures, thereby stabilizing grain boundaries and improving impact resistance. However, if the content of boron (B) is less than 0.0003%, these effects may not be sufficiently obtained. Conversely, if the content of boron (B) is greater than 0.0010%, elongated grains increase because recrystallization is delayed during a hot rolling process, and a non-uniform microstructure is formed because ferrite transformation is delayed during cooling. In addition, it may be difficult to obtain an intended degree of strength as the effect of precipitation strengthening may decrease, and since a non-uniform microstructure of an initial hot rolled steel sheet may be a cause of local stress concentration in a cold rolling process, it is not favored in the present disclosure. Therefore, it may be preferable that the content of boron (B) be within the range of 0.0003% to 0.0010%. Phosphorus (P): 0.001% to 0.05% Like silicon (Si), phosphorus (P) has a solid-solution strengthening effect and an effect of facilitating ferrite transformation. However, if the content of phosphorus (P) is less than 0.001%, it is not economically favorable, because of high manufacturing costs, and sufficient strength may also not be obtained. Conversely, if the content of phosphorus (P) is greater than 0.05%, embrittlement may occur because of grain boundary segregation, fine cracks may easily be formed during a shearing process, and ductility and impact resistance may be worsened. Therefore, it may be preferable that the content of phosphorus (P) be within the range of 0.001% to 0.05%. Sulfur (S): 0.001% to 0.01% Sulfur (S) is an impurity existing in steel. If the content of sulfur (S) is greater than 0.01%, sulfur (S) may combine with an element such as manganese (Mn) and form a non-metallic inclusion, thereby facilitating the formation of fine cracks during a cutting process of steel and markedly decreasing stretch flangeability and impact resistance. Conversely, if the content of sulfur (S) is lower than 0.001%, performing a steel making process may require an excessive amount of time, and thus the productivity of the steel making process may be lowered. Therefore, it may be preferable that the content of sulfur (S) be within the range of 0.001% to 0.01%. Aluminum (Al): 0.01% to 0.1% In general, aluminum (Al) is added for deoxidation. If the content of aluminum (Al) is less than 0.01%, this effect is insufficient. Conversely, if the content of aluminum (Al) is greater than 0.1%, aluminum (Al) may combine with nitrogen (N) and form AlN, thereby increasing the possibility of cracks in slab corners during a continuous casting process and the possibility of inclusion defects in edge portions of a hot rolled steel sheet. In addition, surface defects may be formed during a cold rolling process after a hot rolling process, thereby resulting in poor surface quality. Therefore, it may be preferable that the content of aluminum (Al) be within the range of 0.01% to 0.1%. Nitrogen (N): 0.001% to 0.01% Together with carbon (C), nitrogen (N) is a typical element having a solid-solution strengthening effect and forms coarse precipitates together with elements such as titanium (Ti) or aluminum (Al). In general, although nitrogen (N) has a solid-solution strengthening effect greater than that of carbon (C), as the content of nitrogen (N) increases in steel, the toughness of the steel decreases. In addition, it takes an excessive amount of time to make steel having nitrogen (N) in an amount of less than 0.001%, and thus the productivity of a steel making process decreases. Therefore, according to the present disclosure, it may be preferable that the content of nitrogen (N) be within the range of 0.001% to 0.01%. Titanium (Ti): 0.005% to 0.13% Together with niobium (Nb) and vanadium (V), titanium (Ti) is a typical element having a precipitation strengthening effect and has a strong affinity for nitrogen (N), forming coarse TiN in steel. TiN has an effect of suppressing the growth of grains during a heating process for hot rolling. In addition, titanium (Ti) remaining after reaction with nitrogen (N) dissolves in steel and combines with carbon (C), thereby forming a TiC precipitate and thus improving the strength of the steel. However, if the content of titanium (Ti) is less than 0.005%, these effects may not be obtained, and if the content of titanium (Ti) is greater than 0.13%, coarse TiN is formed to worsen shear processability during a shearing process. Therefore, according to the present disclosure, it may be preferable that the content of titanium (Ti) be within the range of 0.005% to 0.13%. Niobium (Nb): 0.005% to 0.08% Together with titanium (Ti) and vanadium (V), niobium (Nb) is a typical element having a precipitation strengthening effect. During a hot rolling process, niobium (Nb) precipitates and delays recrystallization, thereby having a grain refinement effect and thus improving the strength and impact toughness of steel. However, if the content of niobium (Nb) is less than 0.005%, these effects may not be sufficiently obtained. Conversely, if the content of niobium (Nb) is greater than 0.08%, recrystallization is excessively delayed during a hot rolling process, and thus shear processability deteriorates due to the formation of elongated grains and coarse complex precipitates. Therefore, according to the present disclosure, it may be preferable that the content of titanium (Ti) be within the range of 0.005% to 0.08%. Vanadium (V): 0.005% to 0.2% Together with niobium (Nb) and titanium (Ti), vanadium (V) is a typical element having a precipitation strengthening effect. Vanadium (V) forms precipitates after a coiling process, thereby effectively improving the strength of steel. However, if the content of vanadium (V) is less than 0.005%, this effect may not be sufficiently obtained, and if the content of vanadium (V) is greater than 0.2%, coarse complex precipitates are formed, thereby worsening shear processability and having an economically negative effect. Therefore, according to the present disclosure, it may be preferable that the content of vanadium (V) be within the range of 0.005% to 0.2%. The other component of the high-strength cold rolled steel sheet of the present disclosure is iron (Fe). However, impurities of raw materials or manufacturing environments may be inevitably included in the high-strength cold rolled steel sheet, and such impurities may not be removed from the high-strength cold rolled steel sheet. Such impurities are well-known to those of ordinary skill in manufacturing industries, and thus specific descriptions of the impurities will not be given in the present disclosure. In the present disclosure, the composition of the high-strength cold rolled steel sheet may satisfy Formulas 1 and 2 below. Then, the microstructure of the high-strength cold rolled steel sheet may be uniform after a hot rolling process, and the formation of cracks may be suppressed during a shearing process after a cold rolling process. (In Formulas 1 and 2, each element symbol refers to the weight percent (wt %) of the corresponding element.) Formula 1 relates the hardenability and segregates of steel. Formula 1 is proposed by considering a solid-solution strengthening effect on steel and a non-uniform microstructure of steel. If Formula 1 is less than 2.0, the solid-solution strengthening effect on steel is insufficient, and thus sufficiently high strength is not obtained. Conversely, if Formula 1 is greater than 2.5, the microstructure of steel is non-uniform in a thickness direction of the steel, and ferrite transformation is delayed, thereby decreasing the effect of precipitation strengthening. Therefore, it may be preferable that Formula 1 be within the range of 2.0 to 2.5. Formula 2 regulates elements relating to precipitates in steel. That is, since the formation of precipitates relates to the relationship between the contents of Ti, Nb, and V, and the contents of C and N, Formula 2 is proposed to adjust the contents of Ti, Nb, and V according to the contents of C and N. If Formula 2 is less than 0.2, precipitation strengthening is markedly lowered, and thus, intended levels of strength and hardness may not be obtained. Conversely, if Formula 2 is greater than 0.5, fine precipitates are formed in large amounts, thereby markedly increasing yield strength and thus worsening cold rollability. In addition, precipitates may be unevenly formed in the thickness direction of the steel sheet, increasing the formation of cracks in a shearing process after a cold rolling process. Therefore, it may be preferable that Formula 2 be within the range of 0.2 to 0.5. If the high-strength cold rolled steel sheet is controlled to satisfy the above-described alloying composition, the high-strength cold rolled steel sheet may have high shear processability and be capable of suppressing the formation of cracks in a shearing process and under frictional heat conditions in addition to having high strength and high hardness. The cold rolled steel sheet of the present disclosure is obtained by performing a cold rolling process on a hot rolled steel sheet having a microstructure of ferrite and fine pearlite, and thus the cold rolled steel sheet has a microstructure (full hard microstructure) markedly deformed in the rolling direction. In this case, each phase in the microstructure of the cold rolled steel sheet may not be identified, but before the cold rolling process, the hot rolled steel sheet may include ferrite in an area fraction of 90% or greater, fine pearlite in an area fraction of less than 5%, and bainite as an inevitable remainder. According to the present disclosure, the high-strength cold rolled steel sheet having high shear processability includes at least one of carbides, nitrides, and carbonitrides. For example, the high-strength cold rolled steel sheet may include at least one of TiN, TiC, NbC, NbN, (Ti,Nb) (C,N), (Ti,Mo,Nb) (C,N), (Fe,Mn)3C, and (Fe,Mn,Mo)C. In this case, preferably, the average size of the carbides, nitrides, and carbonitrides may be within the range of 10 nm to 50 nm. If the average size is less than 10 nm, the yield strength of the hot rolled steel sheet may be excessively high, thereby easily causing local work hardening deviations during a cold rolling process, and easily causing cracks during a shearing process and a heat treatment process of the cold rolled steel sheet. Conversely, if the average size is greater than 50 nm, it is difficult to obtain intended tensile strength and hardness. In addition, the cold rolled steel sheet may have a tensile strength of 1200 MPa or greater and a hardness (micro-Vickers) of 340 Hv or greater. If the cold rolled steel sheet has tensile strength and hardness in these ranges, the cold rolled steel sheet may be suitably used for applications such as fiction plates of automatic transmissions of automobiles. In addition, when a shearing process is performed on the cold rolled steel sheet, the maximum length of cracks may preferably be 1 mm or less. The maximum length of cracks is measured by punching the cold rolled steel sheet using a circular die having a diameter of 10 mm with a clearance of 6%, heat treating the cold rolled steel sheet at 200° C. for 1 hour, and measuring the maximum length of cracks in a cross-section. If the maximum length of cracks is greater than 1 mm, cracks may be formed in large amounts and may easily propagate during a shearing process, and the propagation of cracks may be facilitated if temperature increases due to frictional heat. Hereinafter, a method for manufacturing a high-strength cold rolled steel sheet having high shear processability will be described in detail according to another aspect of the present disclosure. Another aspect of the present disclosure provides a method for manufacturing an high-strength cold rolled steel sheet having high shear processability, the method including: heating a steel slab having the above-described alloying composition to a temperature of 1200° C. to 1350° c.; hot rolling the heated steel slab within a temperature range of 850° C. to 1150° C. to form a hot rolled steel sheet; cooling the hot rolled steel sheet to a temperature of 550° C. to 750° C. and coiling the hot rolled steel sheet; and pickling the coiled hot rolled steel sheet and cold rolling the pickled hot rolled steel sheet at a reduction ratio of 60% to 70%. Heating A steel slab having the above-described alloying composition is heated to a temperature of 1200° C. to 1350° C. If the heating temperature is lower than 1200° C., sufficient amounts of precipitates may not redissolved. In this case, after a hot rolling process, the formation of precipitates decreases, and coarse TiN remains. Conversely, if the heating temperature is higher than 1350° C., strength decreases because of abnormal growth of austenite grains. Thus, it may be preferable that the reheating temperature be adjusted to be within the range of 1200° C. to 1350° C. In this case, the steel slab may be manufactured through a continuous casting process directly connected to a hot rolling process. Since the temperature of the steel slab is adjusted to be within the range of 1200° C. to 1350° C. so as to re-dissolve TiN, TiC, NbC, NbN, (Ti,Nb) (C,N), and (Ti,Mo,Nb) (C,N) precipitates, this manufacturing method may be used for the case in which a continuous casting process is directly connected to a hot rolling process as described above. Hot Rolling The heated steel slab is hot rolled within the temperature range of 850° C. to 1150° C. If the hot rolling starts at a temperature higher than 1150° C., a hot rolled steel sheet having coarse grains and poor surface quality may be manufactured because the hot rolling temperature is too high. In addition, if the hot rolling finishes at a temperature lower than 850° C., since recrystallization is excessively delayed, elongated grains are developed, and yield strength increases, thereby worsening cold rollability and shear processability. Cooling and Coiling After the hot rolling, the hot rolled steel sheet is cooled to a temperature of 550° C. to 750° C. and is then coiled. If the hot rolled steel sheet is cooled to a temperature less than 550° C. and is then coiled, the material quality of the steel sheet may be degraded due to the formation of bainite and martensite. Conversely, if the hot rolled steel sheet is cooled to a temperature greater than 750° C. and is then coiled, coarse ferrite is formed, and coarse carbides and nitrides may easily be formed, thereby worsening the material quality of the steel sheet. The average rate of the cooling may be within the range of 10° C./sec to 70° C./sec. If the average cooling rate is less than 10° C./sec, a non-uniform microstructure may be formed because of the formation of coarse ferrite. Conversely, if the average cooling rate is greater than 70° C./sec, bainite may easily be formed, and the microstructure of the steel sheet may become non-uniform in the thickness direction, thereby worsening the shear processability of the steel sheet. Cold Rolling After the coiling, the hot rolled steel sheet is cold rolled at a reduction ratio of 60% to 70% to manufacture a cold rolled steel sheet. If the reduction ratio of the cold rolling process is less than 60%, the effect of work hardening may not be sufficiently obtained, and thus it is difficult to guarantee the strength and hardness of the cold rolled steel sheet. Conversely, if the reduction ratio of the cold rolling process is greater than 70%, the quality of the cold rolled steel sheet may decrease at edge portions, and the shear processability of the cold rolled steel sheet may deteriorate. The cold rolled steel sheet manufactured by the above-described method may have high strength and high hardness, and may not be easily cracked in a shearing process and under frictional heat conditions. In addition, the cold rolled steel sheet manufactured by the above-described method may include at least one of carbides, nitrides, and carbonitrides, and the average size of the carbides, nitrides, and carbonitrides may be within the range of 10 nm to 50 nm. In addition, the cold rolled steel sheet may have a tensile strength of 1200 MPa or greater and a hardness of 340 Hv or greater, and the maximum length of cracks formed in the cold rolled steel sheet during a shearing process may be 1 mm or less. Hereinafter, the present disclosure will be described more specifically through examples. However, the following examples should be considered in a descriptive sense only and not for purposes of limitation. The scope of the present invention is defined by the appended claims, and modifications and variations may be reasonably made therefrom. Steel slabs having the compositions shown in Table 1 below were heated to 1250° C., and cold rolled steel sheets were manufactured using the heated steel slabs under the conditions shown in Table 2 below. At that time, the rate of cooling after a hot rolling process was adjusted to be within the range of 20° C./sec to 30° C./sec. Furthermore, as shown in Table 2 below, values of Formulas 1 and 2 were calculated for comparative examples and inventive examples, and FDT and CT refer to a finish rolling termination temperature in the hot rolling process and a coiling temperature, respectively. In addition, Table 3 below shows mechanical properties and results of microstructure observation of inventive examples and comparative examples. In Table 3 below, TS and Hv refer to the tensile strength and micro-Vickers hardness of each cold rolled steel sheet, respectively, and a maximum length of cracks refers to a value measured by punching each cold rolled steel sheet using a circular die having a diameter of 10 mm with a clearance of 6%, heat treating the cold rolled steel sheet at 200° C. for 1 hour, and measuring the length of the maximum crack in a cross-section. The length of cracks was measured from results of observation using an optical microscope at a magnification of 100 times. The size of carbides, nitrides, and carbonitrides was analyzed using hot rolled steel sheets before cold rolling. Carbides, nitrides, and carbonitrides having an average size of 10 nm to 50 nm do not vary in size and fraction after cold rolling, and it is difficult to accurately measure the sizes and fractions of carbides, nitrides, and carbonitrides from microstructures markedly deformed after cold rolling. Thus, the size thereof was analyzed using the hot rolled steel sheets. The average size of carbides, nitrides, and carbonitrides was determined from results of measurements obtained using a transmission electron microscope. Results of measurement at a magnification of 50,000 times were used to measure carbides and nitrides having an average size of 100 nm or greater, and results of measurement at a magnification of 100,000 times were used to measure precipitates having an average size of 100 nm or less. A tensile test was performed using specimens taken by JIS5 from rolled steel sheets in a 0-degree direction with respect to the rolling direction of the rolled steel sheets. Comparative Examples 1 and 2 did not satisfy both Formulas 1 and 2, and Comparative Example 1 had a carbon (C) content outside of the range proposed in the present disclosure. In both the comparative examples, sufficient solid-solution strengthening did not occur, and Formula 2 exceeded the upper limit because of a relative low content of carbon (C) and relatively excessive contents of titanium (Ti), niobium (Nb), and vanadium (V). Therefore, although the size of carbides, nitrides, and precipitates in steel was small, strength was insufficient. In addition, since Comparative Example 2 was prepared at a cold rolling reduction ratio greater than the range proposed in the present disclosure, somewhat excessive cracks were formed in a sheared surface after punching, and the quality of the sheared surface was poor. Comparative Examples 3 and 5 did not satisfy Formula 1. In Comparative Example 3, the value of Formula 1 was greater than the range proposed in the present disclosure, and thus, segregation increased in a center portion of steel, resulting in poor quality in a sheared portion. In addition, Comparative Example 5 had very good quality on a sheared surface because contents of elements such as manganese (Mn), chromium (Cr), and boron (B) were low, and thus, the occurrence of segregation was low. However, solid-solution strengthening was not sufficient, and thus intended strength and hardness were not obtained. Comparative Examples 4 and 6 did not satisfy Formula 2. In Comparative Example 4, surplus carbon (C) remained and formed coarse precipitates and carbides, and thus intended strength and hardness were not obtained because of insufficient precipitation strengthening. In Comparative Example 6, the value of Formula 2 was greater than the range proposed in the present disclosure, and thus fine precipitates were formed in large amounts, thereby guaranteeing high strength but resulting in excessive cracking in a sheared portion. Comparative Examples 7, 8, 9, and 10 were steel sheets manufactured to have a tensile strength of 1350 MPa or greater and a hardness of 355 Hv or greater after a cold rolling process. Although Comparative Example 7 did not satisfy Formula 1, Comparative Example 7 had intended physical properties owing to a high cold rolling reduction ratio. However, Comparative Example 7 had somewhat excessive cracks in a sheared portion because of the high cold rolling reduction ratio. Comparative Examples 8 and 9 satisfied both Formulas 1 and 2, but the cold rolling reduction ratios thereof were improper, thereby failing to obtain intended physical properties or resulting in poor quality in sheared portions. Comparative Example 10 did not satisfy both Formulas 1 and 2 and had poor quality in a sheared portion. However, inventive examples satisfying the composition, manufacturing conditions, and Formulas 1 and 2 proposed in the present disclosure had intended material characteristics and good quality in sheared portions. While exemplary embodiments have been shown and described above, the scope of the present disclosure is not limited thereto, and it will be apparent to those skilled in the art that modifications and variations could be made without departing from the scope of the present invention as defined by the appended claims. Provided is a high-strength cold rolled steel sheet having high shear processability, including, by wt %, C: 0.05% to 0.10%, Si: 0.01% to 0.5%, Mn: 1.2% to 2.0%, Al: 0.01% to 0.1%, Cr: 0.005% to 0.3%, B: 0.0003% to 0.0010%, Mo: 0.005% to 0.2%, P: 0.001% to 0.05%, S: 0.001% to 0.01%, N: 0.001% to 0.01%, Nb: 0.005% to 0.08%, Ti: 0.005% to 0.13%, V: 0.005% to 0.2%, and a balance of Fe and inevitable impurities. The high-strength cold rolled steel sheet satisfies Formulas 1 and 2 below, and the high-strength cold rolled steel sheet includes at least one of carbides, nitrides, and carbonitrides. Formula 1: 2.0≤[Mn]+2.5[Mo]+1.5[Cr]+300[B]≤2.5, Formula 2: 0.2≤([Nb]/93+[Ti]/48+[V]/51)/([C]/12+[N]/14)≤0.5 (in Formulas 1 and 2, each element symbol refers to a weight percent (wt %) of a corresponding element). 1. A high-strength cold rolled steel sheet having high shear processability, the high-strength cold rolled steel sheet comprising, by wt %, carbon (C): 0.05% to 0.10%, silicon (Si): 0.01% to 0.5%, manganese (Mn): 1.2% to 2.0%, aluminum (Al): 0.01% to 0.1%, chromium (Cr): 0.005% to 0.3%, boron (B): 0.0003% to 0.0010%, molybdenum (Mo): 0.005% to 0.2%, phosphorus (P): 0.001% to 0.05%, sulfur (S): 0.001% to 0.01%, nitrogen (N): 0.001% to 0.01%, niobium (Nb): 0.005% to 0.08%, titanium (Ti): 0.005% to 0.13%, vanadium (V): 0.005% to 0.2%, and a balance of iron (Fe) and inevitable impurities,
wherein the high-strength cold rolled steel sheet satisfies Formulas 1 and 2 below, and the high-strength cold rolled steel sheet comprises at least one of carbides, nitrides, and carbonitrides,
where each element symbol in Formulas 1 and 2 refers to a weight percent (wt %) of a corresponding element. 2. The high-strength cold rolled steel sheet of 3. The high-strength cold rolled steel sheet of 4. The high-strength cold rolled steel sheet of 5. The high-strength cold rolled steel sheet of 6. A method for manufacturing a high-strength cold rolled steel sheet having high shear processability, the method comprising:
reheating a steel slab to a temperature of 1200° C. to 1350° C., the steel slab comprising, by wt %, carbon (C): 0.05% to 0.10%, silicon (Si): 0.01% to 0.5%, manganese (Mn): 1.2% to 2.0%, aluminum (Al): 0.01% to 0.1%, chromium (Cr): 0.005% to 0.3%, boron (B): 0.0003% to 0.0010%, molybdenum (Mo): 0.005% to 0.2%, phosphorus (P): 0.001% to 0.05%, sulfur (S): 0.001% to 0.01%, nitrogen (N): 0.001% to 0.01%, niobium (Nb): 0.005% to 0.08%, titanium (Ti): 0.005% to 0.13%, vanadium (V): 0.005% to 0.2%, and a balance of iron (Fe) and inevitable impurities, the steel slab satisfying Formulas 1 and 2 below; hot rolling the heated steel slab within a temperature range of 850° C. to 1150° C. to form a hot rolled steel sheet; after the hot rolling, cooling the hot rolled steel sheet to a temperature of 550° C. to 750° C. and coiling the cooled hot rolled steel sheet; and after the coiling, pickling the hot rolled steel sheet and cold rolling the hot rolled steel sheet at a reduction ratio of 60% to 70%,
where each element symbol in Formulas 1 and 2 refers to a weight percent (wt %) of a corresponding element. 7. The method of 8. The method of 9. The method of 10. The method of TECHNICAL FIELD
BACKGROUND ART
RELATED ART DOCUMENTS
DISCLOSURE
Technical Problem
Technical Solution
2.0≤[Mn]+2.5[Mo]+1.5[Cr]+300[B]≤2.5 Formula 1:
0.2≤([Nb]/93+[Ti]/48+[V]/51)/([C]/12+[N]/14)≤0.5 Formula 2:Advantageous Effects
DESCRIPTION OF DRAWINGS
BEST MODE
2.0≤[Mn]+2.5[Mo]+1.5[Cr]+300[B]≤2.5 Formula 1:
0.2≤([Nb]/93+[Ti]/48+[V]/51)/([C]/12+[N]/14)≤0.5 Formula 2:MODE FOR INVENTION
Examples C Si Mn Cr Al P S N Mo Ti Nb V B *CE 1 0.04 0.2 1.6 0.01 0.03 0.01 0.004 0.004 0.005 0.1 0.04 0.005 0.0003 CE 2 0.05 0.1 1.4 0.1 0.03 0.008 0.003 0.004 0.007 0.06 0.03 0.1 0.0003 CE 3 0.06 0.1 1.9 0.2 0.035 0.01 0.003 0.005 0.05 0.08 0.03 0.005 0.001 CE 4 0.07 0.2 1.8 0.01 0.05 0.01 0.005 0.004 0.1 0.035 0.03 0.005 0.0003 CE 5 0.08 0.3 1.4 0.01 0.025 0.009 0.003 0.004 0.1 0.08 0.005 0.05 0.0003 CE 6 0.07 0.2 1.7 0.1 0.03 0.01 0.003 0.003 0.05 0.12 0.055 0.006 0.0003 CE 7 0.085 0.1 1.8 0.01 0.05 0.01 0.004 0.004 0.009 0.09 0.04 0.005 0.0003 CE 8 0.09 0.05 1.9 0.1 0.025 0.007 0.003 0.004 0.007 0.11 0.035 0.05 0.0003 CE 9 0.12 0.2 2 0.01 0.5 0.01 0.003 0.004 0.006 0.12 0.03 0.1 0.0003 CE 10 0.08 0.5 2.2 0.01 0.1 0.01 0.003 0.004 0.05 0.15 0.03 0.02 0.0012 **IE 1 0.055 0.1 1.7 0.01 0.03 0.01 0.003 0.005 0.1 0.06 0.02 0.005 0.0003 IE 2 0.06 0.15 1.8 0.01 0.028 0.006 0.004 0.004 0.05 0.11 0.02 0.005 0.0003 IE 3 0.07 0.1 1.9 0.01 0.03 0.008 0.003 0.004 0.15 0.05 0.06 0.005 0.0003 IE 4 0.07 0.2 1.9 0.01 0.035 0.01 0.002 0.003 0.15 0.055 0.045 0.005 0.0003 IE 5 0.07 0.1 1.7 0.1 0.03 0.009 0.003 0.004 0.05 0.08 0.03 0.05 0.0003 IE 6 0.07 0.4 1.9 0.01 0.037 0.01 0.003 0.004 0.14 0.12 0.03 0.005 0.0003 IE 7 0.07 0.15 1.95 0.15 0.03 0.01 0.004 0.003 0.05 0.1 0.02 0.005 0.0003 IE 8 0.075 0.2 1.8 0.01 0.03 0.007 0.003 0.004 0.1 0.09 0.02 0.06 0.0003 *CE: Comparative Example, **IE: Inventive Example *CE 1 1.72 0.72 887 605 66 CE 2 1.66 0.80 889 614 73 CE 3 2.63 0.39 908 613 62 CE 4 2.16 0.19 892 615 65 CE 5 1.76 0.39 894 604 63 CE 6 2.07 0.53 895 612 62 CE 7 1.93 0.33 901 614 72 CE 8 2.16 0.47 898 608 56 CE 9 2.12 0.47 905 599 74 CE 10 2.70 0.55 911 617 65 **IE 1 2.06 0.32 899 612 67 IE 2 2.03 0.49 905 610 66 IE 3 2.38 0.29 909 623 62 IE 4 2.38 0.29 912 601 65 IE 5 2.07 0.49 915 625 65 IE 6 2.36 0.48 915 624 64 IE 7 2.39 0.40 918 626 68 IE 8 2.16 0.50 913 627 63 *CE: Comparative Example, **IE: Inventive Example *CE 1 1237 334 ≥1200 ≥340 4 0.06 ⊚ CE 2 1260 341 7 4 Δ CE 3 1238 334 12 2 Δ CE 4 1098 297 35 0.03 ⊚ CE 5 1236 334 13 0.08 ⊚ CE 6 1315 356 8 6 X CE 7 1372 362 ≥1350 ≥355 15 3 Δ CE 8 1291 349 13 0.05 ◯ CE 9 1434 384 22 8 X CE 10 1460 390 8 10 X **IE 1 1271 344 ≥1200 ≥340 15 0.06 ⊚ IE 2 1330 353 16 0.2 ◯ IE 3 1263 342 18 0.4 ◯ IE 4 1281 346 19 0.05 ⊚ IE 5 1287 348 18 0.04 ⊚ IE 6 1384 368 ≥1350 ≥355 21 0.8 ◯ IE 7 1374 370 22 0.6 ◯ IE 8 1359 367 15 0.3 ◯ *CE: Comparative Example, **IE: Inventive Example
2.0≤[Mn]+2.5[Mo]+1.5[Cr]+300[B]≤2.5 Formula 1:
0.2≤([Nb]/93+[Ti]/48+[V]/51)/([C]/12+[N]/14)≤0.5 Formula 2:
2.0≤[Mn]+2.5[Mo]+1.5[Cr]+300[B]≤2.5 Formula 1:
0.2≤([Nb]/93+[Ti]/48+[V]/51)/([C]/12+[N]/14)≤0.5 Formula 2:
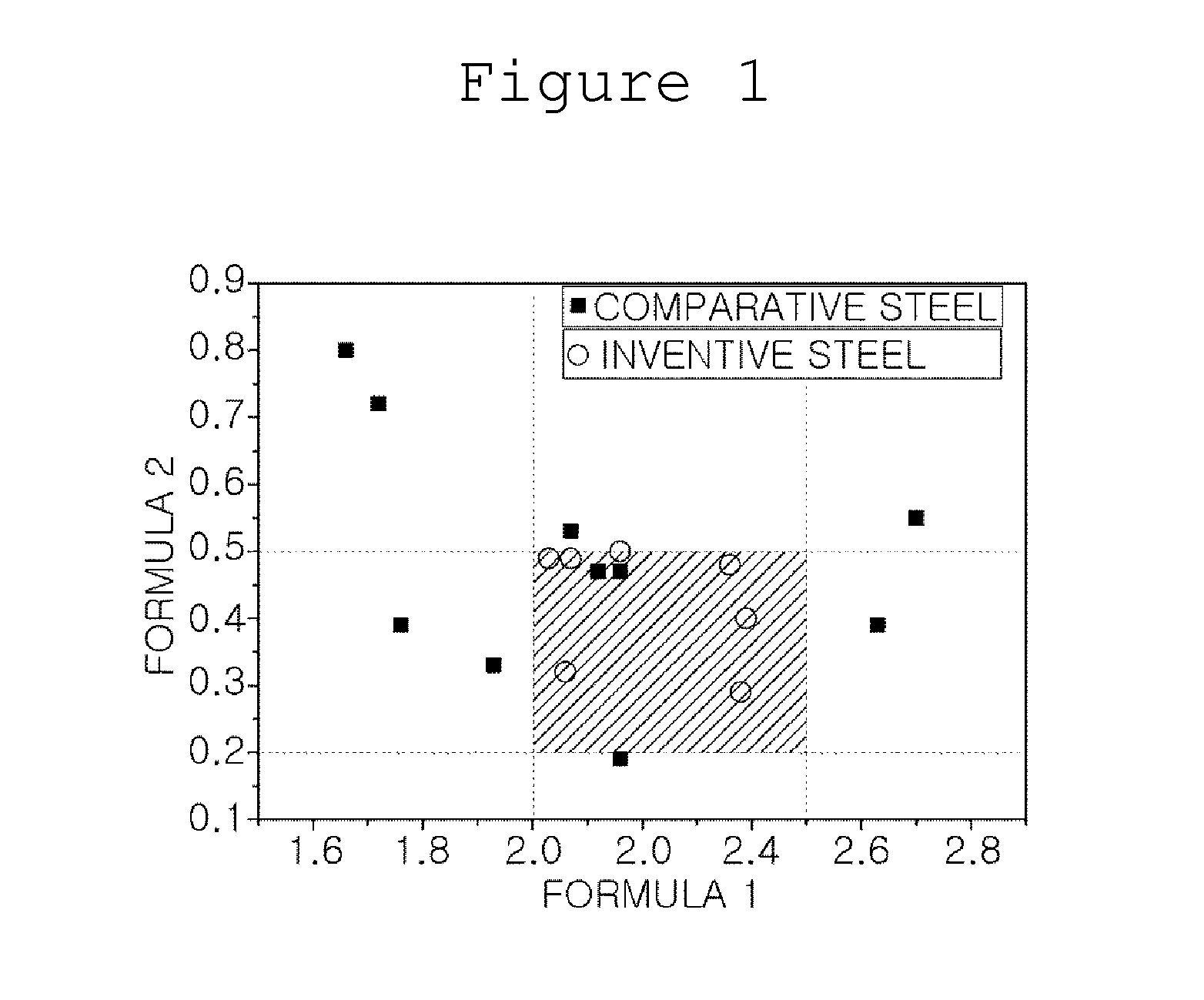