Immobilization of Molecular Catalysts on Solid Powders via Vapor Deposition of Encapsulating Nano-Layers for Use as Heterogeneous Chemical Catalysts
This application claims the benefit of U.S. Provisional Application Ser. No. 63/379,297, filed on Oct. 13, 2022, which is incorporated herein by reference in its entirety as if fully set forth below. The various embodiments of the present disclosure relate generally to immobilization of molecular catalysts on solid powders via vapor deposition of encapsulating nano-layers for use as heterogeneous chemical catalysts. Molecular transition metal catalysts in homogeneous solutions tend to exhibit high catalytic activity and reaction selectivity, but also exhibit poor stability and short lifetimes. One major pathway to molecular catalyst deactivation is the formation of off-cycle intermediates via intermolecular catalyst interactions. While catalyst dimers or trimers are sometimes necessary for catalytic activity most catalyst “multi”-mers result in catalytic dead ends. Multimer formation is often promoted by water in the reaction solution, as shown in The immobilization of molecular catalysts onto solid supports is an approach designed towards preventing intermolecular catalyst interactions and extending molecular catalysts lifetimes. The isolation of molecular catalysts on solid supports inhibits bimolecular catalyst interactions and thus takes advantage of the inherent catalyst activity. This approach of creating a molecular/heterogeneous catalyst has the added benefits of increased solvent compatibility, increased ease of catalyst separation from reaction mixtures, possible incorporation into flow reactors, and potential for catalyst recycling. This approach, however, can have its own set of drawbacks including increased cost of catalyst synthesis, possible decreases in catalyst selectivity, and difficulty in preventing catalyst leaching from the solid support. The increased cost of both the materials and catalyst preparation can be overcome by achieving previously unattainable reactivity through extending catalyst lifetimes and recyclability. Extensive research has been reported on immobilized catalysts in the field of surface organometallic chemistry (SOMC). This approach generates individual catalyst molecules on solid oxide supports through direct binding of transition metals to the oxide supports. This binding occurs after a thorough preparation of the oxide surface to create sites capable of strong binding to individual metal atoms. The metal atoms that bind the oxide support can be introduced to the support through solution phase chemistry. Many of these SOMC catalysts are composed of early transition metals due to their oxophilicity, but recent reports have extended SOMC to the late transition metals. An impressive array of catalytic transformations has been achieved with this class of SOMC catalyst. Similar to polymer-supported catalysts, SOMC catalysts utilize the support as a ligand for the catalysts, therefore, there is no direct analogous homogeneous catalysts for comparison. Iterative design of SOMC catalysts, hence, cannot directly benefit from homogeneous catalyst studies. Ligand-first binding of molecular catalysts to a support is an alternative approach to catalyst immobilization on solid metal oxides that could benefit from previous understandings of homogeneous catalysis. The ligand-first class of molecular/heterogeneous catalysts on oxide supports is inspired by the design of dye sensitized solar cells and electrocatalysis. In this approach catalytic activity and selectivity of homogeneous catalyst can often be translated to the molecular/heterogeneous system. Furthermore, the lifetimes of homogeneous catalysts that rapidly deactivate in solution through bimolecular routes such as dimerization, may have their lifetimes greatly enhanced by isolation on a solid support as illustrated in The present disclosure is directed to overcoming limitations in the art. An exemplary embodiment of the present disclosure provides a heterogeneous chemical catalyst comprising a substrate, a molecule attached to the substrate via a binding site, wherein the molecule comprises a catalytic active site, and a coating layer coating at least a portion of the binding site. In any of the embodiments disclosed herein, the coating layer can adhere the molecule to the substrate. In any of the embodiments disclosed herein, the coating layer can be a vapor deposited coating layer. In any of the embodiments disclosed herein, the binding site can comprise a linking group, wherein the linking group couples the substrate to the molecule. In any of the embodiments disclosed herein, the coating layer can coat the entirety of the linking group. In any of the embodiments disclosed herein, the linking group can be selected from the group consisting of —COOH, —PO3H2, —SO3H, —OPO3H, —OSO3H, C(O)NHOH, silatranes, silanes, siloxanes, disulfides, and thiols. In any of the embodiments disclosed herein, the coating layer can have a thickness of between about 0.1 nm and about 10 nm. In any of the embodiments disclosed herein, the coating layer can coat the binding site, such that the catalytic active site is exposed. In any of the embodiments disclosed herein, the substrate can comprise one or more compounds selected from the group consisting of silicon oxide, titanium oxide, aluminum oxide, zirconium oxide, nickel oxide, zinc oxide, niobium oxide, chromium oxide, hafnium oxide, lanthanum oxide, yttrium oxide, cerium oxide, tantalum oxide, magnesium oxide, strontium oxide, calcium oxide, indium oxide, tin doped indium oxide, tin oxide, fluorine doped tin oxide, copper oxide, cobalt oxide, iron oxide, and mixtures thereof. In any of the embodiments disclosed herein, the molecule can comprise one or more transition metal coordination complexes. In any of the embodiments disclosed herein, the coating layer can comprise one or more compounds selected from the group consisting of metal oxides, metal oxyhydroxides, metal hydroxides, metal nitrides, metal carbides and their compounds, including aluminum oxide, titanium oxide, hafnium oxide, zirconium oxide, zinc oxide, silicon oxide, magnesium oxide, calcium oxide, strontium oxide, barium oxide, vanadium oxide, chromium oxide, manganese oxide, iron oxide, cobalt oxide, nickel oxide, copper oxide, niobium oxide, molybdenum oxide, ruthenium oxide, indium oxide, tin oxide, bismuth oxide, lead oxide, Lanthanum oxide, tantalum oxide, tungsten oxide, cerium oxide, neodymium oxide, europium oxide, ytterbium oxide, dysprosium oxide, and their solid solutions and multicomponent compounds. In any of the embodiments disclosed herein, the heterogeneous chemical catalyst can be suspended in a polar protic, polar, or protic solvent. Another embodiment of the present disclosure provides a method of preparing a heterogeneous chemical catalyst. This method comprises providing a substrate, attaching a molecule to the substrate via a binding site, wherein the molecule comprises a catalytic active site, and coating, with a coating layer, at least a portion of the binding site to form the heterogeneous chemical catalyst. In any of the embodiments disclosed herein, coating the at least a portion of the binding site can comprise one or more cycles of a vapor deposition process that undergoes self-limiting sequential reactions. In any of the embodiments disclosed herein, the method can further comprise suspending the heterogeneous chemical catalyst in a polar protic, polar, or protic solvent to undergo a chemical reaction. In any of the embodiments disclosed herein, the chemical reaction can be a coupling reaction. In any of the embodiments disclosed herein, coating the at least a portion of the binding site can leave the catalytic active site exposed. These and other aspects of the present disclosure are described in the Detailed Description below and the accompanying drawings. Other aspects and features of embodiments will become apparent to those of ordinary skill in the art upon reviewing the following description of specific, exemplary embodiments in concert with the drawings. While features of the present disclosure may be discussed relative to certain embodiments and figures, all embodiments of the present disclosure can include one or more of the features discussed herein. Further, while one or more embodiments may be discussed as having certain advantageous features, one or more of such features may also be used with the various embodiments discussed herein. In similar fashion, while exemplary embodiments may be discussed below as device, system, or method embodiments, it is to be understood that such exemplary embodiments can be implemented in various devices, systems, and methods of the present disclosure. The following detailed description of specific embodiments of the disclosure will be better understood when read in conjunction with the appended drawings. For the purpose of illustrating the disclosure, specific embodiments are shown in the drawings. It should be understood, however, that the disclosure is not limited to the precise arrangements and instrumentalities of the embodiments shown in the drawings. To facilitate an understanding of the principles and features of the present disclosure, various illustrative embodiments are explained below. The components, steps, and materials described hereinafter as making up various elements of the embodiments disclosed herein are intended to be illustrative and not restrictive. Many suitable components, steps, and materials that would perform the same or similar functions as the components, steps, and materials described herein are intended to be embraced within the scope of the disclosure. Such other components, steps, and materials not described herein can include, but are not limited to, similar components or steps that are developed after development of the embodiments disclosed herein. Herein are described potentially universal methods for reliably attaching and isolating molecular catalysts ligand-first to solid metal oxide supports for solution-based chemical catalysis. This paradigm can use atomic layer deposition (ALD) to physically encapsulate pre-bound molecular catalysts to solids including metal oxide powders. ALD can allow for precise control of oxide layer growth and has been used to isolate single-site heterogeneous catalysts (Liu et al., “Stabilizing Single-Atom and Small-Domain Platinum via Combining Organometallic Chemisorption and Atomic Layer Deposition,” This approach builds upon the inventors prior work that used ALD to attach active molecular photosensitizers to nanostructured electrodes for photoelectrochemical devices (Vannucci et al., “Crossing the Divide Between Homogeneous and Heterogeneous Catalysis in Water Oxidation,” An exemplary embodiment of the present disclosure provides a heterogeneous chemical catalyst comprising a substrate, a molecule attached to the substrate via a binding site, wherein the molecule comprises a catalytic active site, and a coating layer coating at least a portion of the binding site. In some embodiments, the substrate comprises one or more metal oxides. For example, in some embodiments, the substrate comprises one or more compounds selected from the group consisting of silicon oxide, titanium oxide, aluminum oxide, zirconium oxide, nickel oxide, zinc oxide, niobium oxide, chromium oxide, hafnium oxide, lanthanum oxide, yttrium oxide, cerium oxide, tantalum oxide, magnesium oxide, strontium oxide, calcium oxide, indium oxide, tin doped indium oxide, tin oxide, fluorine doped tin oxide, copper oxide, cobalt oxide, iron oxide, and mixtures thereof. In some embodiments, the molecule comprises one or more transition metal coordination complexes. For example, in some embodiments the molecule comprises nickel coordination complexes, palladium coordination complexes, or ruthenium coordination complexes. In some embodiments, the binding site comprises a linking group, wherein the linking group couples the substrate to the molecule. For example, in some embodiments, the linking group is selected from the group consisting of —COOH, —PO3H2, —SO3H, —OPO3H, —OSO3H, C(O)NHOH, silatranes, silanes, siloxanes, disulfides, and thiols. In some embodiments, the coating layer adheres the molecule to the substrate. In some embodiments, the coating layer coats the entirety of the linking group. In some embodiments, the coating layer coats the binding site, such that the catalytic active site is exposed. The catalytic active site is the portion of the molecule attached to the substrate that interacts with reactants in solution to promote a particular chemical reaction. In some embodiments, the chemical reaction is a Suzuki-Miyaura coupling reaction. In some embodiments, the chemical reaction is a hydrodeoxygenation. In some embodiments, the chemical reaction is a hydrogenation. As disclosed herein, the term “exposed” means that the catalytic active site is capable of interacting with reactants in liquid solution. In some embodiments, at least 10% to 99% of the catalytic active site is exposed. For example, in some embodiments at least 10% to 25%, at least 10% to 50%, at least 10% to 75%, at least 10% to 99%, at least 20% to 25%, at least 20% to 50%, at least 20% to 75%, at least 20% to 99%, at least 30% to 50%, at least 30% to 75%, at least 30% to 99%, at least 40% to 50%, at least 40% to 75%, at least 40% to 99%, at least 50% to 55%, at least 50% to 60%, at least 50% to 65%, at least 50% to 70%, at least 50% to 75%, at least 50% to 80%, at least 50% to 85%, at least 60% to 65%, at least 60% to 70%, at least 60% to 75%, at least 60% to 80%, at least 60% to 85%, at least 60% to 90%, at least 70% to 75%, at least 70% to 80%, at least 70% to 85%, at least 70% to 90%, at least 80% to 85%, at least 80% to 90%, or at least 85% to 90%. In some embodiments, the coating layer is a vapor deposited coating layer. In some embodiments, the coating layer has a thickness of between about 0.1 nm and about 10 nm. For example, in some embodiments the coating layer has a thickness of between about 0.1 nm and about 1 nm, about 0.1 nm and about 2 nm, about 0.1 nm and about 3 nm, about 0.1 nm and about 4 nm, about 0.1 nm and about 5 nm, about 0.1 nm and about 6 nm, about 0.1 nm and about 7 nm, about 0.1 nm and about 8 nm, about 0.1 nm and about 9 nm, about 0.5 nm and about 1 nm, about 0.5 nm and about 2 nm, about 0.5 nm and about 3 nm, about 0.5 nm and about 4 nm, about 0.5 nm and about 5 nm, about 0.5 nm and about 6 nm, about 0.5 nm and about 7 nm, about 0.5 nm and about 8 nm, about 0.5 nm and about 9 nm, about 0.5 nm and about 10 nm, about 1 nm and about 2 nm, about 1 nm and about 3 nm, about 1 nm and about 4 nm, about 1 nm and about 5 nm, about 1 nm and about 6 nm, about 1 nm and about 7 nm, about 1 nm and about 8 nm, about 1 nm and about 9 nm, about 1 nm and about 10 nm, about 1.5 nm and about 2 nm, about 1.5 nm and about 3 nm, about 1.5 nm and about 4 nm, about 1.5 nm and about 5 nm, about 1.5 nm and about 6 nm, about 1.5 nm and about 7 nm, about 1.5 nm and about 8 nm, about 1.5 nm and about 9 nm, about 1.5 nm and about 10 nm, about 2 nm and about 3 nm, about 2 nm and about 4 nm, about 2 nm and about 5 nm, about 2 nm and about 6 nm, about 2 nm and about 7 nm, about 2 nm and about 8 nm, about 2 nm and about 9 nm, about 2 nm and about 10 nm, about 2.5 nm and about 3 nm, about 2.5 nm and about 4 nm, about 2.5 nm and about 5 nm, about 2.5 nm and about 6 nm, about 2.5 nm and about 7 nm, about 2.5 nm and about 8 nm, about 2.5 nm and about 9 nm, about 2.5 nm and about 10 nm, about 3 nm and about 4 nm, about 3 nm and about 5 nm, about 3 nm and about 6 nm, about 3 nm and about 7 nm, about 3 nm and about 8 nm, about 3 nm and about 9 nm, about 3 nm and about 10 nm, about 3.5 nm and about 4 nm, about 3.5 nm and about 5 nm, about 3.5 nm and about 6 nm, about 3.5 nm and about 7 nm, about 3.5 nm and about 8 nm, about 3.5 nm and about 9 nm, about 3.5 nm and about 10 nm, about 4 nm and about 5 nm, about 4 nm and about 6 nm, about 4 nm and about 7 nm, about 4 nm and about 8 nm, about 4 nm and about 9 nm, about 4 nm and about 10 nm, about 5 nm and about 6 nm, about 5 nm and about 7 nm, about 5 nm and about 8 nm, about 5 nm and about 9 nm, about 5 nm and about 10 nm, about 6 nm and about 7 nm, about 6 nm and about 8 nm, about 6 nm and about 9 nm, about 6 nm and about 10 nm, about 7 nm and about 8 nm, about 7 nm and about 9 nm, or about 7 nm and about 10 nm. In some embodiments, the coating layer comprises one or more compounds selected from the group consisting of metal oxides, metal oxyhydroxides, metal hydroxides, metal nitrides, metal carbides and their compounds, including aluminum oxide, titanium oxide, hafnium oxide, zirconium oxide, zinc oxide, silicon oxide, magnesium oxide, calcium oxide, strontium oxide, barium oxide, vanadium oxide, chromium oxide, manganese oxide, iron oxide, cobalt oxide, nickel oxide, copper oxide, niobium oxide, molybdenum oxide, ruthenium oxide, indium oxide, tin oxide, bismuth oxide, lead oxide, Lanthanum oxide, tantalum oxide, tungsten oxide, cerium oxide, neodymium oxide, europium oxide, ytterbium oxide, dysprosium oxide, and their solid solutions and multicomponent compounds. In some embodiments, the heterogeneous chemical catalyst is suspended in a polar protic, polar, or protic solvent. For example, in some embodiments the solvent is water, ethanol, methanol, isopropanol, 1,4-dioxane, acetonitrile, dichloromethane, tetrahydrofuran, acetic acid, dimethylformamide, ethyl acetate, or mixtures thereof. In some embodiments, the heterogeneous chemical catalyst is suspended in a non-polar solvent. For example, in some embodiments the solvent is pentane, hexane, heptane, octane, decane, undecane, dodecane, or mixtures thereof. Another embodiment of the present disclosure provides a method of preparing a heterogeneous chemical catalyst. This method comprises providing a substrate, attaching a molecule to the substrate via a binding site, wherein the molecule comprises a catalytic active site, and coating, with a coating layer, at least a portion of the binding site to form the heterogeneous chemical catalyst. In carrying out the method of preparing a heterogeneous chemical catalyst, the resulting catalyst can have the various characteristics described above. In some embodiments of the method, the coating at least a portion of the binding site comprises one or more cycles of a vapor deposition process that undergoes self-limiting sequential reactions. For example, in some embodiments the coating comprises 1 to 5 cycles, 1 to 10 cycles, 1 to 15 cycles, 1 to 20 cycles, 5 to 10 cycles, 5 to 15 cycles, 5 to 20 cycles, 10 to 15 cycles, 10 to 20 cycles, or 15 to 20 cycles of a vapor deposition process that undergoes self-limiting sequential reactions. In some embodiments, the vapor deposition process is atomic layer deposition. In some embodiments, the method further comprises suspending the heterogeneous chemical catalyst in a polar protic, polar, or protic solvent to undergo a chemical reaction. For example, in some embodiments, the solvent is water, ethanol, methanol, isopropanol, acetonitrile, dichloromethane, tetrahydrofuran, acetic acid, dimethylformamide, ethyl acetate, or mixtures thereof. In some embodiments, the heterogeneous chemical catalyst is suspended in a non-polar solvent. For example, in some embodiments the solvent is pentane, hexane, heptane, octane, decane, undecane, dodecane, or mixtures thereof. In some embodiments, the chemical reaction is a coupling reaction. In some embodiments, the chemical reaction is a Suzuki-Miyaura coupling reaction. In some embodiments, the chemical reaction is a hydrodeoxygenation. In some embodiments, the chemical reaction is a hydrogenation. It is to be understood that the embodiments and claims disclosed herein are not limited in their application to the details of construction and arrangement of the components set forth in the description and illustrated in the drawings. Rather, the description and the drawings provide examples of the embodiments envisioned. The embodiments and claims disclosed herein are further capable of other embodiments and of being practiced and carried out in various ways. Also, it is to be understood that the phraseology and terminology employed herein are for the purposes of description and should not be regarded as limiting the claims. Accordingly, those skilled in the art will appreciate that the conception upon which the application and claims are based may be readily utilized as a basis for the design of other structures, methods, and systems for carrying out the several purposes of the embodiments and claims presented in this application. It is important, therefore, that the claims be regarded as including such equivalent constructions. Furthermore, the purpose of the foregoing Abstract is to enable the United States Patent and Trademark Office and the public generally, and especially including the practitioners in the art who are not familiar with patent and legal terms or phraseology, to determine quickly from a cursory inspection the nature and essence of the technical disclosure of the application. The Abstract is neither intended to define the claims of the application, nor is it intended to be limiting to the scope of the claims in any way. The following Examples are presented to illustrate various aspects of the present application, but are not intended to limit the scope of the claimed application. Materials: Compound 1 was synthesized according to previously reported procedures (Key et al., “A Molecular/Heterogeneous Nickel Catalyst for Suzuki-Miyaura Coupling,” Instrumentation: A Bruker Advance III HD 300 was used for NMR spectroscopy. 1H data were collected at 300 MHz and 13C at 75 MHz. Bruker TopSpin software was used to process the NMR data. Inductively coupled plasma-mass spectrometry (ICP-MS) was collected on a Finnigan ELEMENT XR with a double focusing magnetic field with a quartz torch and injector (Thermo Fisher Scientific) and a 0.2 mL/min micromist U-series nebulizer (GE). Gas chromatography-mass spectrometry analyses were performed with a Shimadzu QP-20105 containing a RXI-5MS (Restek) column (30 m, 0.25 mm id). Mass spectrometer electron ionization was at 70 eV and the spectrometer was scanned from 1000 to 50 m/z at low resolution. Powder X-ray diffraction (XRD) was carried out with a Rigaku Miniflex-II with a D/teX Ultra silicon strip detector. Cu Kα radiation (l−1.5406 Å) was operated at 15 kV and 30 mA. Samples were loaded on a zero-background holder and scanned from 20-80° 2θ range at a scan rate of 3° 2θ/min. Fourier transform infrared-attenuated total reflection (FTIR-ATR) was performed on a Nicolet iS Fourier transform infrared spectrometer with an iD7 attenuated total reflectance attachment (diamond crystal). Before each sample set, a background scan of ambient atmosphere was collected and then subtracted from the experimental signal to calculate the final spectra reported. EPR spectra were collected on a Bruker EMXplus instrument equipped with a Bruker X-band microwave bridgehead. Spectra were recorded in a quartz EPR tube at room temperature at a power of 1.589 mW with a modulation amplitude of 2.0 G using the Xenon v1.1b.66 software. Nitrogen physisorption measurements were performed on samples pretreated for by placing the samples under 10 μmHg vacuum at room temperature, then ramping the temperature to 90° C. at 10° C./minute and holding for 6 hours. Nitrogen physisorption measurements were collected at 77 K and surface area characterized by BET. General Cross-Coupling Reaction Set Up: In a 50 mL round-bottom flask, 0.68 mmol aryl halide and 0.82 mmol of boronic acid were added to a 20 mL solution comprise of 1:1 ethanol: water. 1.7 mmol of K3PO4and 0.1 g of 1|SiO2|TiO2were added to the flask (unless otherwise stated in the manuscript). The solution was heated to 105° C. for 24 hours. The reaction was then allowed to cool to room temperature and the products were extracted with 3 rinses with pentane and purified by preparative scale TLC (90:10 pentane:ethyl acetate mobile phase). For catalyst recycling, the solid catalyst was gravity filtered from the reaction solution and rinsed three times with pentane and three times with ethanol and dried under a stream of N2 (99.999%, Airgas) before being used in a new reaction. We recently reported on the design and catalytic testing of a molecular/heterogeneous nickel catalyst (Key et al., “A Molecular/Heterogeneous Nickel Catalyst for Suzuki-Miyaura Coupling,” Synthesis of 1|SiO2|TiO2 The molecular catalyst [(2,2′:6′,2″-terpyridine-4′-benzoic acid)Ni(II)]Cl2(1) was synthesized following a previously reported procedure (Key et al., “A Molecular/Heterogeneous Nickel Catalyst for Suzuki-Miyaura Coupling,” Catalyst 1|SiO2was then immobilized using TiO2ALD (10 cycles of TiCl4+H2O as described in the experimental section). The ALD procedure was designed to coat 1|SiO2with a ˜1.0 nm thick layer of TiO2to create the hybrid catalyst 1|SiO2|TiO2as depicted in To investigate the stability of the nickel center of the catalyst, electron paramagnetic resonance (EPR) spectroscopy was utilized as shown on the right-hand side of To illustrate the advantage of this hybrid ALD catalyst approach, and to determine the optimized ALD layer thickness, a series of catalytic Suzuki cross-coupling reactions were performed. The results in Next, a roughly 1 nm layer of TiO2was applied to the 1|SiO2structure via 10 ALD cycles to yield catalyst 1|SiO2|TiO2. As can be seen in These results suggest that the 10 ALD cycle TiO2layer now sufficiently coats the SiO2surface, fully immobilizing the molecular catalyst by stabilizing the ligand COOH binding to the oxide surface. This stabilized ligand binding prevents catalyst desorption and protects the catalyst from bimolecular degradations. Furthermore, BET analysis of 1|SiO2and 1|SiO2|TiO2indicated that the ALD layer does not lead to an appreciable difference in surface area of the solid support (216±0.8 m2/g and 223±0.8 m2/g respectively, Lastly, a 2.0 nm layer of TiO2was applied to the catalyst via 20 ALD cycles. This “thick” coating results in almost no yield of the desired product, as shown in With the optimized ALD layer thickness determined, control reactions were performed to help further identify the active catalyst species. Results from these control reactions are summarized in Table 1. Reaction 1 in Table 1 shows the designed hybrid catalyst 1|SiO2|TiO2leads to an efficient product yield of 90%. For rxn. 3 in Table 1, the solid 1|SiO2|TiO2catalyst was filtered from reaction mixture and additional substrate was added to the filtrate solution and a second reaction was performed. No new product formation or substrate consumption was observed after the second reaction showing that the active catalyst is not present in the reaction filtrate post reaction. To confirm the necessity of the 1|SiO2|TiO2structure, numerous other active catalysts were also considered. As indicated by reactions 4 and 5, the untreated metal oxides powders are not catalytically active for this cross-coupling transformation. SiO2ALD coated with TiO2without molecular nickel catalyst present was also not active (reaction 6). A mixture of homogenous molecular catalyst and fresh oxide particles, reactions 7 and 8, did not result in appreciable product formation, indicating that the ligand-first surface-attachment of the molecular catalyst is necessary in the hybrid design. Decomposition of the molecular nickel catalyst to nickel salts (NiCl2) or metallic nickel during the reaction could have also been possible. Testing of NiCl2or metallic Rainey Ni both in solution and in the presence of oxide support (reactions 9-12) resulted in poor product yields (<5%), indicating that these possible decomposition products are not responsible for the observed catalytic activity of 1|SiO2|TiO2. We further examined the possibility that reduced nickel nanoparticles act as the catalytically active species. We synthesized 0.5 weight % nickel nanoparticle catalyst on the SiO2support using charge enhanced dry impregnation (CEDI) (Zhu et al., “Charge-Enhanced Dry Impregnation: A Simple Way to Improve the Preparation of Supported Metal Catalysts,” A further summary of the reactivity and stability of 1|SiO2|TiO2in comparison to 1 and 1|SiO2can be found in Table 2. The data in Table 2 supports the conclusion that the hybrid catalyst containing an ALD overcoating (1|SiO2|TiO2) exhibits increased Suzuki cross-coupling reactivity due to the construction of the catalyst leading to extended lifetimes for the molecular component of the catalyst. IR spectroscopy focusing on the carboxylic frequencies indicates prolonged binding of the ligand to the oxide surface only when the ALD overcoat is applied. In addition, ICPMS analysis of the catalyst and the reaction solution shows retention of the majority of the nickel on the solid catalyst with 1|SiO2|TiO2. STEM-EDS analysis supports the ICPMS data, and elemental mapping ( This hybrid catalyst exhibits desirable green chemistry principles (Bryan et al., “Key Green Chemistry Research Areas from a Pharmaceutical Manufacturers' Perspective Revisited,” To ensure this catalyst is generally amenable to Suzuki cross-coupling reactivity and not just applicable to a single reaction, a modest substrate scope for this catalyst was examined. List of1H &13C NMR peaks of products: Multiplicity was indicated as follows: s (singlet), d (doublet), t (triplet), q (quartet), m (multiplet). NMR spectra are provided in 1H NMR (DMSO, 300 MHz) δ 2.62 (s, 3H), 7.46 (d, J=9.0 Hz, 2H), 7.55-7.57 (m, 1H), 7.63 (t, J=7.3 Hz, 2H), 7.71-7.74 (d, J=9.0 Hz, 2H), 7.80-7.82 (m, 2H).13C NMR (CDCl3, 300 MHz) δ (ppm): 21.13, 127.00, 128.74, 129.51, 131.23, 137.05, 138.39, 141.19. 1H NMR (CD2Cl2, 300 MHz) δ 3.84 (s, 3H), 6.96-6.99 (m, 2H), 7.09-7.15 (m, 2H), 7.48-7.55 (m, 4H).13C NMR (CD2Cl2, 300 MHz) δ (ppm): 55.28, 114.18, 115.27, 115.55, 127.91, 128.20, 132.55, 136.95, 159.25, 163.69. 1H NMR (CDCl3, 300 MHz) δ 1.37 (s, 9H), 2.40 (s, 3H), 7.24-7.26 (d, J=7.9 Hz, 2H), 7.45-7.55 (m, 6H).13C NMR (CDCl3, 300 MHz) δ (ppm): 21.11, 31.39, 34.51, 125.67, 126.60, 126.87, 129.43, 131.21, 136.71, 137.24, 138.26. 1H NMR (CD2Cl2, 300 MHz) δ 2.36 (s, 3H), 3.82 (s, 3H), 6.94-6.96 (d, J=8.8 Hz, 2H), 7.20-7.23 (d, J=8.0 Hz, 2H), 7.43-7.46 (d, J=8.13, 2H), 7.49-7.52 (d, J=8.8 Hz, 2H).13C NMR (CD2Cl2, 300 MHz) δ (ppm): 20.72, 55.26, 114.10, 126.35, 127.75, 129.39, 133.47, 136.46, 137.74, 159.05. 1H NMR (DMSO, 300 MHz) δ 3.85 (s, 3H), 6.99-7.02 (d, J=8.6 Hz, 2H), 7.56-7.59 (d, J=8.6 Hz, 2H), 7.65-7.71 (m, 4H).13C NMR (CDCl3, 300 MHz) δ (ppm): 55.33, 114.09, 114.36, 125.62, 126.82, 127.53, 128.28, 160.30. This study demonstrates a new paradigm in the design of hybrid catalysts in which ALD is used to improve the attachment and stability of molecular catalysts on solid metal oxide supports. Generating hybrid catalysts with increased catalyst lifetimes makes the catalysts amenable for the use of green solvents and easily separable from reaction solutions. At an optimal ALD layer thickness, the molecular catalyst remains highly active while still being resistant to surface detachment and subsequent deactivation. Through a series of control experiments and spectroscopic characterizations, we provide strong evidence for the active species to be the unperturbed molecular catalyst attached to the metal oxide surface and encased with an optimal ALD deposited TiO2layer. Interestingly, the exemplary molecular catalyst studied here is not catalytically active by itself in homogeneous solution for the target carbon-carbon cross-coupling reaction due to extremely short catalyst lifetimes. Thus, a combination of ligand-first surface attachment with molecular design and ALD application could lead to new approaches in catalyst discovery. Noteworthy here for green chemistry principles is that this hybrid catalyst was able to perform cross-coupling catalysis using a non-noble metal (nickel) and earth abundant oxides and is active in a near-neutral pH, primarily aqueous solution. Moreover, since the optimal ALD coating requires only about 10 reaction cycles, this process is technologically and economically viable for large-scale manufacturing. An exemplary embodiment of the present disclosure provides a heterogeneous chemical catalyst comprising a substrate, a molecule attached to the substrate via a binding site, wherein the molecule comprises a catalytic active site, and a coating layer coating at least a portion of the binding site. Another embodiment of the present disclosure provides a method of preparing a heterogeneous chemical catalyst. This method comprises providing a substrate, attaching a molecule to the substrate via a binding site, wherein the molecule comprises a catalytic active site, and coating, with a coating layer, at least a portion of the binding site to form the heterogeneous chemical catalyst. 1. A heterogeneous chemical catalyst comprising:
a substrate; a molecule attached to the substrate via a binding site, wherein the molecule comprises a catalytic active site; a coating layer coating at least a portion of the binding site. 2. The heterogeneous chemical catalyst of 3. The heterogeneous chemical catalyst of 4. The heterogeneous chemical catalyst of 5. The heterogeneous chemical catalyst of 6. The heterogeneous chemical catalyst of 7. The heterogeneous chemical catalyst of 8. The heterogeneous chemical catalyst of 9. The heterogeneous chemical catalyst of 10. The heterogeneous chemical catalyst of 11. The heterogeneous chemical catalyst of 12. The heterogeneous chemical catalyst of 13. A method of preparing a heterogeneous chemical catalyst comprising:
providing a substrate; attaching a molecule to the substrate via a binding site, the molecule comprising a catalytic active site; coating, with a coating layer, at least a portion of the binding site to form the heterogeneous chemical catalyst. 14. The method of 15. The method of 16. The method of 17. The method of 18. The method of 19. The method of 20. The method of CROSS-REFERENCE TO RELATED APPLICATIONS
FIELD OF THE DISCLOSURE
BACKGROUND
BRIEF SUMMARY
BRIEF DESCRIPTION OF THE DRAWINGS
DETAILED DESCRIPTION
EXAMPLES
Example 1
Materials and Methods
Example 2
Results and Discussion
Catalytic Performance
1 1|SiO2|TiO2 90% 2 1|TiO2 32% 3 Reaction Filtrate 0% 4 Only SiO2 0% 5 Only TiO2 0% 6 1 nm TiO2on SiO2 0% 7 1 mol % 1 + SiO2in situ 0% 8 1 mol % 1 + TiO2in situ 4% 9 1 mol % NiCl2in solution 0% 10 1 mol % Rainey Ni in solution 1% 11 1 mol % NiCl2+ SiO2in situ 0% 12 1 mol % Raney Ni + SiO2in situ 0% 13 Ni nanoparticles|SiO2(CEDI) 1% 14 1|SiO2|TiO2+ Hg drop 82% Conditions: 0.82 mmol phenylboronic acid, 0.68 mmol iodotoluene, 1.7 mmol K3PO4in 20 ml 1:1 ethanol/water. 105° C. 24 hr. 0.9 mol % 1|SiO2|TiO2, 1.1 mol % CEDI. aDetermined by GC-MS analysis. Summary of the Characterization Data Comparing Homogeneous Catalyst (1), Hybrid Catalyst without ALD (1|SiO2), and Hybrid Catalyst with ALD Overcoating (1|SiO2|TiO2). IR ICPMS (Ni ICPMS (Ni) EDS elements XRD (Ni (COOH cm−1) wt %) catalyst solution detected* particles?) Catalyst % Yield Pre Post Pre Post Post Pre Post Pre Post 1 0 1729 N/A N/A N/A N/A N/A N/A N/A N/A 1|SiO2 5 1639 N.S. 0.35 0.06 170 μg Ni N.S. No No 1|SiO2|TiO2 90 1640 1640 0.35 0.31 35 μg Ni, Ti Ni, Ti, K, P No No N/A: data not collected/not applicable. N.S.: no signal. Pre and Post refer to pre-reaction and post-reaction, reaction details in FIG. 20. *EDS detected Si and O in every measurement. CONCLUSIONS











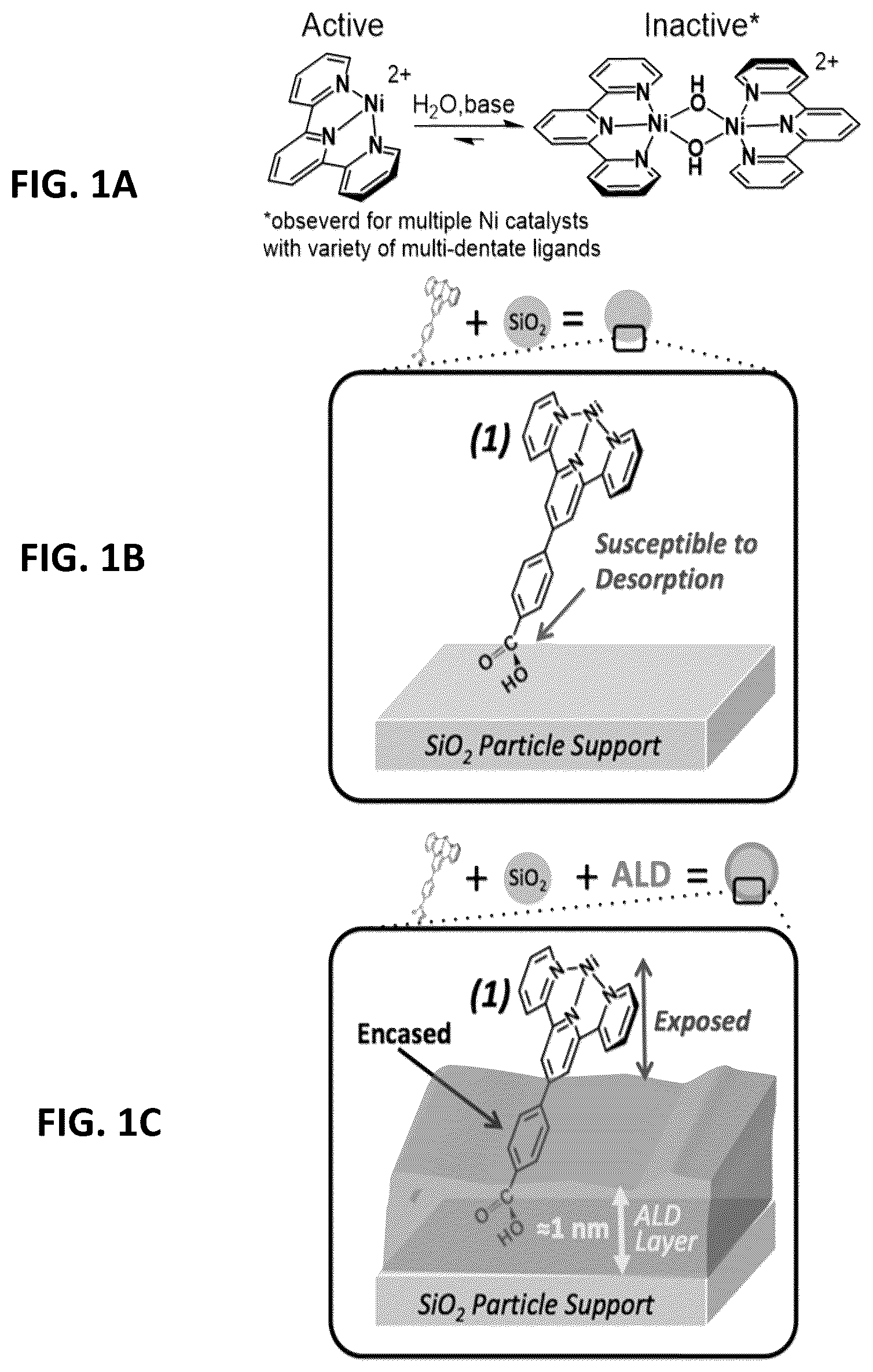
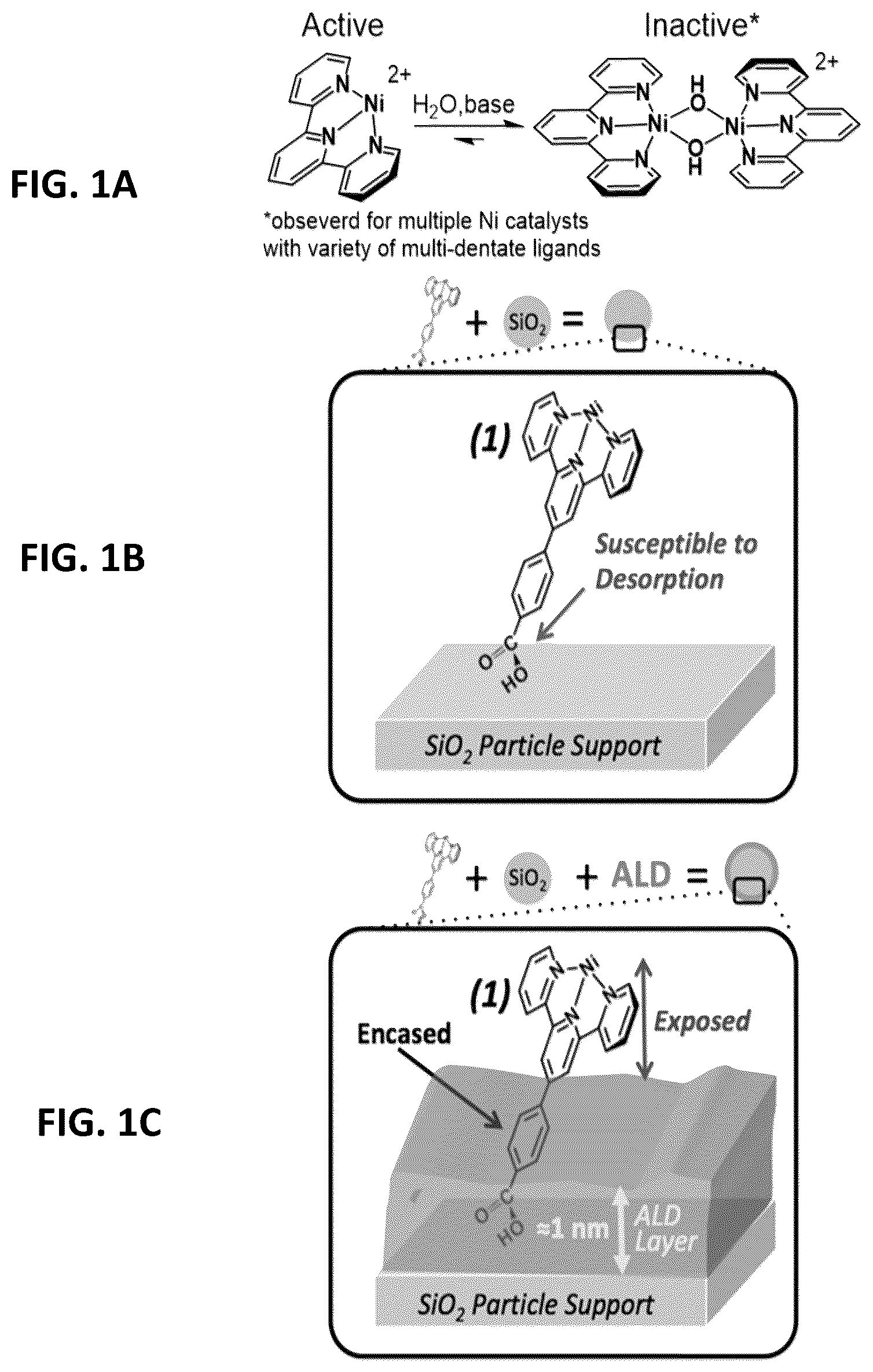





