SEAL MATERIAL FOR ANALYTICAL INSTRUMENT, AND FLOW CELL, DETECTION INSTRUMENT, AND ANALYTICAL INSTRUMENT USING SAID SEAL MATERIAL
本発明は、分析機器用シール材、及び、それを用いたフローセル、検出機器、分析機器に関する。
ガスケットやパッキンといったシール材は、機器や配管などの接続部に、流体の漏れ防止用として用いられ、金属製、ゴム製、樹脂製等の様々な材質のものが存在する。高圧がかかる接続部では、より強い力でシールする必要があるため、剛性の低い材質では、シール材がすぐに変形・破損してしまい、漏れの原因となってしまう。また、その様なシール材は交換頻度が高い(耐久性が低い)ため、設備や装置のダウンタイムが長くなってしまう。そのため、金属製のシール材や厚みのある樹脂製の剛性の高いシール材が用いられている。しかしながら、小型の精密機器などの接続部の用いられる場合には、シール材を厚くすることには限界があり、薄く、小さく、且つ、剛性の高い(耐久性の高い)シール材が必要とされている。
また、配管などを流れる流体が、金属や樹脂などを腐食したり、溶解させたりするものである場合には、使用できる材質が耐薬性の高い材質等に制限される。特に、シール材が、高精度の分析機器等に用いられる場合には、シール材の成分などが、配管内等を流れる流体に混ざってしまい、正確な分析が行えないという問題がある。
具体的な例としては、液体クロマトグラフィーや超臨界流体クロマトグラフィー等の分析機器に用いられるフローセルが挙げられる。液体クロマトグラフィー又は超臨界流体クロマトグラフィーは、液体又は超臨界流体に、被分析物を溶解させ、カラムで被分析成分を分離し、それぞれの成分について、定量的、定性的な分析を行う装置である。前記定量的な分析を行う機器として、UV吸光度検出器や示差屈折率検出器等が挙げられる。UV吸光度検出器や示差屈折率検出器等は、フローセルを内蔵しており、被分析成分が溶解した流体を流しながら、フローセルにUV光などを照射し、UV吸光量や屈折率の差を検知するものである。非常に細い配管に流体を流しながら測定を行うため、送液ポンプによって高い送液圧力が負荷される。また、超臨界流体クロマトグラフィーにおいては、二酸化炭素等を超臨界流体とするために高い圧力が必要である。そのため、フローセルの接続部にも高い圧力が負荷され、接続部には高いシール力(例えば、圧縮力)が必要となる。
特許文献1は、液体クロマトグラフィーの検出機器に用いられるフローセルに、金属製のシール材を用いる発明を提案している。また、特許文献2は樹脂製のシール材と樹脂製のシール材の間に金属層を設ける発明を提案している。
しかしながら、特許文献1で開示されている金属製のシール材では、材質の腐食や金属成分の混入のおそれがあり、特許文献2で開示されている樹脂製のシール材と金属層の組み合わせでは、金属成分の混入や、高シール力(りょく)下で樹脂製シールが変形・破損してしまい、流体の漏れのおそれがあった。また、特許文献3に開示されているガスケットは、金属不織布にゴムが充填されているため、従来のゴムのシール材よりも剛性が高くなるが、金属分がむき出しであるため金属成分の混入のおそれがある。さらに剛性の低いゴムを用いていることにより、ゴムが変形・破損し、流体の漏れのおそれがあった。特許文献3のシール材は、制動作用を発揮する必要もあるため、ゴムを使用する必要があり、シール材の剛性を高くするには、限界があった。
また、これらシール材を用いたフローセル、検出機器及び分析機器は、分析精度が低くなるおそれがあり、さらにシール材が破損しやすいため、交換頻度が高く、装置などのダウンタイムが長くなるおそれがあった。
本発明は、上述した事情に鑑みてなされたものであり、その目的は、高シール力下における使用時に、変形・破損しない高い剛性、流体に対する優れた耐腐食性や低い溶解性を有するシール材を提供することである。また、本発明のシール材を用いることにより、流体の漏れがなく、シール材成分の混入を防ぎ、交換頻度の少ないフローセル、検出機器及び分析機器を提供することができる。
上記課題について、本発明者らが鋭意検討を行ったところ、樹脂に、繊維シートを包埋させることで、高シール力が負荷される環境下においても変形し過ぎず、破損し難い高い剛性、流体に対する優れた耐腐食性、低い溶解性を有するシール材が得られることを発見し、本発明を完成させるに至った。
本発明によれば、高シール力下における使用時に、変形し過ぎず容易に破損し難い高い剛性、流体に対する優れた耐腐食性や低い溶解性を有するシール材を提供することが可能である。
1.シール材の構成
ここで、「略平行」とは、完全に平行であることを意味するだけでなく、実質的に平行である、すなわち、例えば繊維シート表面と前記シール面とに、10度の傾きを有する場合を含むことも意味する。また、この場合に、繊維シート表面及び前記樹脂部のシール面表面に存在する凹凸の有無や、該凹凸の傾きは無視でき、繊維シート表面が延在する平面方向と、前記シール面が延在する平面方向とが、略平行であればよい。
さらに、繊維シートが反りを含む場合には、平面度が本発明にかかるシール材の厚さの1/2以下であり、且つ、繊維シートの平面形体の幾何学的に正しい平面が前記略平行である場合も略平行であるとする。なお、平面度は、JIS B0621-1984「幾何偏差の定義及び表示」に準拠する。
前記シール材の形状、大きさ、厚みは、特に限定されず、被シール部材の形状や用途に合わせて選択することができ、少なくとも一部に、シール面として、略平行な2つの平面(任意の一方の平面を第1のシール面とし、他方を第2のシール面とする)を含んでいればよい。例えば、円板状、楕円板状、多角形状等の板状部材とすることができる。前記板状部材は、その平面部に流体を通すための貫通孔やボルトなどの留め具を通すための貫通孔を有することができる。また、被シール部材の接触部の形状に合わせた、溝などの凹凸を有することもできる。
また、本発明において、「略平行な2つの平面を含む」とは、シール材を使用する前、又は、シール材使用時に、シール面を形成する2つの平面(第1のシール面と第2のシール面)が略平行であることをいうものとする。従って、前記第1及び第2のシール面と、繊維シートとは、使用中に略平行な関係であればよい。
シール材に含まれる繊維シートの、数量、形状、大きさ、厚みは、繊維シートが、シール材のシール面に飛び出さない限りにおいて特に限定されず、シール材の形状や用途に合わせて選択することができ、少なくとも1層の繊維シートが、前記シール材のシール面である2つの略平行な樹脂面(任意の一方の平面を第1のシール面とし、他方を第2のシール面とする)と略平行に包埋されていればよい。
また、上述した通り、繊維シートの大きさは、数量、形状、大きさ、厚みは、繊維シートが、シール材のシール面に飛び出さない限りにおいて特に限定されないが、シール材を使用する際に、樹脂部からはみ出した部分が欠損し、樹脂部の強度を下げてしまう場合や、特に内径側側面にはみ出した場合には、流体の流路を遮る場合や、流体に繊維シートの一部が混入される場合などがあるため、完全に内包されることが好ましい。しかしながら、製造工程上の都合により、樹脂部の外周部から繊維シートの一部(ごくわずかな部分)が露出することもあり得るので、本発明において包埋とは完全に包埋の意味に限定されず、樹脂部の外周部から繊維シートの一部が露出する場合も包含する。
なお、シール材に含まれる繊維シートの数は、1つ以上含まれれば良く、2つ以上の繊維シートを結着した態様としても良い。また、複数の繊維シートをシール材の厚み方向に配置してもよいが、シール材中の繊維シートの配置の正確性を考慮すると、繊維シートは1つ又は2つ以上の繊維シートを結着した態様とすることが好ましい。
図1に、本発明にかかるシール材の例を示し、本願発明の構造をより詳しく説明する。図1に示したシール材は、本発明のシール材の1例に過ぎず、これに限定されるものではない。
図1には中心部に、例えば、流体が通過するため又は丸形の部品をはめ込むための、貫通孔を有する、ドーナツ形状(外径DO、内径DI、厚さTs)のシール材1(樹脂部10と外形は共通)を示している。繊維シート20は、シール材1(樹脂部10)に内包されている。樹脂部10は、任意に選択した第1のシール面11と第2のシール面12を有している。繊維シート20は第1の繊維シート表面21と第2の繊維シート表面22を有しており、第1のシール面11、第2のシール面12、第1の繊維シート表面21及び第2の繊維シート表面22は、互いに略平行となっている。
前述したように、シール材1の大きさ、即ち、外径DO及び内径DIの大きさは特に限定されず、被シール部材をシールすることが可能であり、例えば、流体が流れるのに十分な大きさ又は丸形の部品をはめ込むことができる大きさであればよい。例えば、分析機器内のフローセルに用いられているシール材としては、外径DO2mm~20mm、内径DI0.3mm~10mmとすることができる。
シール材1の厚さTsは、特に限定されないが、シール部に付加されるシール力とシール材1の樹脂のヤング率等を参考にして、十分な潰ししろを有するように選択することができる。例えば、分析機器内のフローセルに用いられているシール材としては、厚さ0.05mm~2mmとすることができる。
ここで「潰ししろ」とは、図2に示したように、シール材1にシール力を負荷した際に、シール材が弾性変形及び/又は塑性変形し、被シール材のシール面の形状に追従及び密着するために必要とされる圧縮方向(本例の場合、シール材1の二つのシール面における法線方向)の変形量を意味する。
また、図2に示したように、シール材1の樹脂部10が、シール力により圧縮される際、繊維シート20の表面21と表面22には、せん断力f1及びf2が発生する。詳細は不明であるが、本発明の効果は、繊維シート20を構成する各繊維の表面が、せん断力f1及びf2に対する面抵抗を発揮することによるものであると推察できる。すなわち、繊維シート20は、シール力により樹脂が必要以上に変形することを抑制する効果を有するもの推察される。
また、繊維シート20の第1の表面21と、樹脂部10の第1のシール面11との距離(樹脂の肉厚)T1と、繊維シートの第2の表面12と、樹脂部(樹脂の肉厚)の第2のシール面22との距離(厚さ)T2とは、同一でも、異なっていてもよく、特に限定されない。
また、繊維シートの厚みTfと、繊維シート20の第1の表面21と、樹脂部10の第1のシール面11との距離(樹脂の肉厚)T1、繊維シートの第2の表面12と、樹脂部(樹脂の肉厚)の第2のシール面22との距離(厚さ)T2との比率は特に限定されないが、Tf/T1、Tf/T2は、独立して0.5~5が好ましく、1~3がより好ましい。
ここで、前述したように、シール材1の樹脂部10が、シール力により圧縮される際、繊維シート20の表面21と表面22には、せん断力f1及びf2が発生する。その際、T1とT2に差異があった場合、T1及びT2の樹脂の変形量にも差異が生まれ、その結果f1とf2に差異が発生する。かかる場合、繊維シート20の一方の表面(21又は22)から他方の表面(22又は21)にかけて、応力勾配が存在することになる。その結果、繊維シートの一方の表面には平面方向に沿った引張力(f1又はf2の大きい方の力)が働くが、他方の表面に働く力(f1又はf2の小さい力)は相対的に弱いため、繊維シートの該平面は平面方向に沿った圧縮方向の力を受けることとなる。一般に繊維は引張方向の力には強く、圧縮方向の力には弱いため、該圧縮方向の力がかかる繊維シートの表面は、変形や破損の原因となりやすく、繊維シートが変形したり、破損したりする場合がある。それにともない、シール材1が変形したり、破損したりする恐れがある。そのため、T1とT2は、略同一であることが好ましい。ここで『略同一』とは、完全に同一でない場合を含み、T1とT2の差が、T1又はT2の10%以下であればよい。
図1のシール材1における、繊維シートの長さLfは、シール材1(シール面)の長さLsよりも短く、繊維シート20は、樹脂部10に完全に内包されているが、これに限定されない。即ち、Lfが、Lsよりも長い場合も含まれ、図1におけるシール材1の外径部又は内径部に、繊維シート20の一部が、樹脂部からはみ出していてもよい。しかしながらシール材を使用する際に、樹脂部からはみ出した部分が欠損し、樹脂部10の強度を下げてしまう場合や、特に内径側側面にはみ出した場合には、流体の流路を遮る場合や、流体に繊維シートの一部が混入される場合などがあるため、完全に内包されることが好ましい(Ls>Lfとなる場合が好ましい)。
また、Lf/Lsは、0.1~0.9である場合が好ましく、0.3~0.7がより好ましく、0.4~0.6がさらに好ましい。Lf/Lsが、かかる範囲にある場合に、シール材は、十分な剛性を有しやすく、且つ、変形しろを保持しやすい。変形しろとは、図1の繊維シート20と樹脂部の内径側面部13までの樹脂の厚さ(Li)と、繊維シート20と樹脂部の外径側面部14までの樹脂の厚さ(Lo)を意味し、LiとLoが、十分にないと、樹脂部が適度に変形できず、シール性が担保できない恐れがある。
さらに、LfとLsの位置関係は、特に限定されないが、圧縮力が働くシール面の長さ(Ls)に対して、繊維シートがシール材の内径側又は外径側に偏らず、均等に配置されることが好ましい。図1の場合には、シール面又は繊維シート表面の平面方向に平行な方向において、Lsの中点と、Lfの中点が一致していることが好ましい。即ち、Li=Loとなる場合が好ましい。
以上のように、本願発明のシール材は、繊維シートによって樹脂部の変形を妨げる作用とシール性を担保するための潰ししろの存在が重要である。すなわち、繊維シートを構成する繊維の表面積の総和と、シール材に含まれる樹脂の体積との、比が重要である。前記シール材に含まれる前記繊維シートを構成する繊維の表面積の総和と、前記樹脂の体積との比は、特に限定されないが、例えば、30cm2/cm3~500cm2/cm3とすることができ、40cm2/cm3~500cm2/cm3が好ましく、50cm2/cm3~300cm2/cm3がより好ましい。かかる範囲にある場合、前記シール材の樹脂部が、被シール部材のシール部の形状に追従し得る潰ししろを有するとともに、繊維シートが樹脂部の変形を妨げる抵抗となるため、変形し過ぎることがない。従って、高いシール力が負荷された場合でも、樹脂が変形し過ぎず又は破損しないため、流体の漏れなどが発生しない。
ここで、樹脂の体積の測定方法は、特に限定されず、公知の方法を用いることができる。例えば、シール材の外形から算出されるシール材の体積と、内部に含まれる繊維シートの外形から算出される繊維シートの体積との差とすることができる。
ここで、繊維の表面積の総和は、繊維シートを構成する全ての繊維の表面積の総和である。繊維の表面積の総和の求め方は、特に限定されず、公知の方法を用いることができる。例えば、繊維の表面積の総和は、以下のように算出できる。なお、下記では繊維シートを構成する繊維が単一の材質の場合について詳述する。
第2に、繊維シートに含まれる繊維1本当たりの平均体積(Vf)を求める。前記平均体積は、無作為に抜き出した20本の繊維について、走査型電子顕微鏡などの観察装置を用い、それら繊維の両端面の直径(D1及びD2)、繊維の長さ(L3)を測定し、下式により計算される繊維1本の体積を選択した20本に対して算出し、それらの数平均を平均体積とする。
第3に、繊維シートに含まれる繊維1本当たりの平均質量(Mf)を求める。前記質量は、Vfと、繊維材質の密度(Df)とから、下式より算出される。繊維材質の密度とは、繊維を構成する材質の密度を用い、例えば、SUS316L(JIS G3214等に規定されている)の場合には、7.98g/cm3を用いる。
第4に、繊維シートに含まれる繊維総数(Nf)を求める。前記総数は、繊維シートの質量(Ms)と、Mfとから、下式により算出される。繊維シートの質量(Ms)は、天秤など、公知の方法で測定することができる。
最後に、繊維の総表面積を下式により算出する。
なお、繊維シートが複数の材質の繊維(以降、各材質とする)を混在して含む場合には、上記と同様に下記(A)~(E)に従って算出することができる。複数の材質の繊維とは、材質の違いのみならず、材質が同一でも、大きさや密度が異なる繊維を含む。
本発明にかかる繊維シートの密度は、特に限定されないが、例えば、0.5g/cm3~5.5g/cm3とすることができ、1.0g/cm3~5.0g/cm3が好ましく、1.5g/cm3~4.0g/cm3がさらに好ましい。
1-1.樹脂
また、樹脂には、繊維シートの他に、さらに充填剤や可塑剤等の添加物を含むことができる。
樹脂の材質は、シール材に負荷されるシール力や使用される液体等の温度によって選択することができる。例えば、ガラス転移温度を40℃以上とすることができ、80℃以上が好ましく、100℃以上がより好ましい。ガラス転移温度の上限値は、高い方が好ましく、特に限定されないが、例えば、300℃以下とすることができる。樹脂のガラス転移温度がかかる範囲にある場合に、分析機器に用いられたシール材は、適度な硬さを有しており、変形し過ぎたり、破損したりせず、液体の漏れを発生させない。また、ガラス転移温度を高くすることで、高温において使用される場合に、適度な硬さを有することができる。
ここで、ガラス転移温度の測定は、公知の測定方法を用いることができ、例えば、JIS K7121-1987「プラスチックの転移温度測定方法」に準拠した方法により測定することができる。
また、樹脂の材質は、使用される温度におけるヤング率によって選択することもできる。樹脂のヤング率としては、使用される温度において、例えば、50MPa以上とすることができ、100MPa以上が好ましく、150MPa以上がより好ましい。上限値としては、3500MPa以下とすることができる。樹脂のヤング率がかかる範囲にあることで、シール力が負荷された際に、十分な変形が可能であるため、シール面の形状を追従することができ、且つ、変形し過ぎたり、破損したりせず、液体の漏れを発生させない。
ヤング率の測定方法は、公知の方法を用いることができる。例えば、JIS K7161-1994「プラスチック-引張特性の試験方法」に準拠する方法を用いて測定することができる。
シール材の樹脂部に、充填剤や可塑剤等の添加剤を含む場合には、それらの添加剤等を含んだ樹脂のガラス転移温度やヤング率とする。従って、樹脂単体で、ガラス転移温度やヤング率が低い場合でも、充填剤や添加剤等を添加することで、ガラス転移温度やヤング率を調整することが可能である。
熱可塑性樹脂としては、例えば、アクリロニトリルブタジエンスチレン(ABS)樹脂;ポリスチレン、シンジオタクティックポリスチレンなどのスチレン系樹脂;ナイロンなどのポリアミド系樹脂;ポリエチレンテレフタレート(PET)、ポリブチレンテレフタレート(PBT)などのポリエステル系樹脂;超高分子量ポリエチレン;変性ポリフェニレンエーテル;アクリル系樹脂;ポリカーボネート(PC);ポリイミド(PI);ポリベンゾイミダゾール(PBI);液晶ポリマー;ポリフェニレンサルファイド(PPS);ポリエーテルエーテルケトン(PEEK);テトラフルオロエチレン(PTFE)やパーフルオロアルキルビニルエーテル共重合体(PFA)等のフッ素樹脂等;の熱可塑性樹脂が挙げられる。これらは1種単独で使用してもよく、2種以上を併用してもよい。なお、液晶ポリマーとしては、サーモトロピック液晶ポリマーが好ましく、具体的にはポリカーボネート系液晶ポリマー、ポリウレタン系液晶ポリマー、ポリアミド系液晶ポリマー、ポリエステル系液晶ポリマーなどが挙げられる。
熱硬化性樹脂としては、例えば、エポキシ樹脂、不飽和ポリエステル樹脂、ポリビニルエステル樹脂、フェノール樹脂、ポリウレタン樹脂、アクリル系樹脂、メラニン樹脂、メラミン樹脂、尿素樹脂、ベンゾグアナミン樹脂、ロジン変性マレイン酸樹脂、ロジン変性フマル酸樹脂等を用いることができる。これらは1種単独で使用してもよく、2種以上を併用してもよい。
エネルギー線硬化樹脂としては、例えば、エポキシ樹脂、アクリル系樹脂、シリコーン系樹脂、ポリエステル系樹脂などが挙げられる。これらは1種単独で使用してもよく、2種以上を併用してもよい。
ゴムやエラストマーとしては、例えば、ニトリルゴム、水素化ニトリルゴム、フッ素ゴム、シリコーンゴム、エチレンプロピレンゴム、クロロプレンゴム、アクリルゴム、ブチルゴム、ウレタンゴム、天然ゴム、クロロスルフォン化ポリエチレンゴム、エピクロルヒドリンゴム、オレフィン系エラストマー、スチレン系エラストマー、塩ビ系エラストマー、ウレタン系エラストマー、エステル系エラストマー、アミド系エラストマー等が挙げられる。これらは1種単独で使用してもよく、2種以上を併用してもよい。
これらの樹脂のうち、製造の容易さから熱可塑性樹脂が好ましく、シール材としてのシール面への追従性が高く、さらに、流体に対する優れた耐腐食性や低い溶解性を有する樹脂であるフッ素樹脂及びPEEKがより好ましく、UV光による光分解反応が起こらないテトラフルオロエチレン(PTFE)やパーフルオロアルキルビニルエーテル共重合体(PFA)がさらに好ましい。
前記樹脂には、本発明の効果を阻害しない限りにおいて、添加剤を添加することができる。添加剤としては、例えば、粘着性付与剤、充填材(無機充填剤、有機充填剤)、可塑剤、繊維、柔軟性コントロール剤、老化防止剤、シランカップリング剤、生成する硬化物の引張特性を調整する物性調整剤、光硬化性樹脂、タレ防止剤、溶剤、難燃性付与剤、滑剤、顔料、スペーサ形状保持剤、フロー性改良剤、架橋剤、重合開始剤その他必要に応じて各種添加剤が添加することができる。
1-2.繊維シート
繊維シートの形状は、特に限定されず、シール材の形状、大きさ、厚み等により選択することができる。一般には、例えば、円板状、楕円板状、多角形状等の板状部材とすることができる。前記繊維シートは、その平面部に流体を通すための貫通孔やボルトなどの留め具を通すための貫通孔を有することができる。
本発明にかかる繊維シートの厚みは、特に限定されず、シール材の形状により選択することができる。繊維シートは、厚みが薄すぎると繊維シートの強度や弾性率など力学的性質が低くなる恐れがある。従って、本発明にかかる繊維シートの厚みは、例えば、20μm~500μmが好ましく、30μm~200μmがより好ましい。
1-2-1.繊維
繊維シートを構成する繊維は、繊維同士を結着することができる。繊維シートが有機繊維を含む場合には、融着により結着することができる。繊維シートが金属繊維や、無機繊維を含む場合には、繊維同士の結合力を上げるために、繊維シートを加熱して焼結させることができる。焼結方法は、公知の方法を用いることができ、繊維の材質により異なるが、例えば、ステンレス鋼繊維(例えば、SUS304やSUS316L等のステンレス鋼)を単独で用いる場合には、水素ガス雰囲気の還元焼結炉を用い、熱処理温度1120℃、速度15cm/minの焼結条件とすることができる。
また、繊維シートに有機繊維が含まれると、ファブリル化や加熱による軟化等により繊維間の接着や絡み合いに寄与して、繊維シートを強固に形成できる。無機繊維が含まれると繊維シートの剛性や強度を高くすることができる。
本発明の繊維シートに用いられる繊維の繊維径は、特に限定されないが、例えば、1μm~50μm、好ましくは2μm~30μm、より好ましくは3μm~20μm、特に好ましくは4μm~8μmとすることができる。
本発明の繊維シートに用いられる繊維の繊維長は、製造に支障をきたさない限りにおいて、特に限定されず、例えば、0.1mm~5mm、好ましくは0.5mm~3mm、より好ましくは1mm~2mmとすることができる。
繊維シートの空隙率は、特に限定されないが、例えば、30%~90%とすることができ、40%~85%がより好ましく、50%~80%がさらに好ましい。かかる範囲にある場合に、剛性の高い繊維シートを形成でき、剛性が高く、破損しにくいシール材を得ることが可能となる。また、繊維シート内部に渡って行き渡った樹脂が、繊維シートを構成する繊維表面と密着し、高いシール効果を発生させやすい。
前記空隙率は、繊維シートの体積に対して繊維が存在しない空間の割合で、繊維シートの体積と質量及び繊維素材の密度から算出される。
1-2-2.繊維シートの製造方法
以下に、本発明における好適例である湿式抄造法による繊維シート形成工程を説明する。
セルロース系繊維等は、予め叩解しておくことが好ましい。叩解は、シングルディスクリファイナー(SDR)、ダブルディスクリファイナー(DDR)、ビーター等の叩解機により適宜行なうことができる。
湿式抄紙に用いる湿式抄紙機としては特に限定されず、一般の抄紙技術に適用されている抄紙機、具体的には長網抄紙機、円網抄紙機、傾斜式抄紙機、ツインワイヤー抄紙機等を使用できる。
抄造工程に於ける脱水及び乾燥工程のプレス圧力、乾燥工程のロール表面温度等を調節することで、所望の空隙率を得ることができる。
繊維シートに有機繊維を含む場合には、乾燥工程のロール温度を調節することで、繊維同士の結着を高めることができる。
また、金属繊維や無機繊維を含む場合等は、さらに焼結工程を設けることで、強固な繊維シートを形成することができる。焼結条件や装置構成は公知の方法・装置・条件を用いることができ、特に限定されないが、例えば、ステンレス鋼繊維のみ含まれる繊維シートを形成する場合には、真空焼結装置を用いて、真空度13.3mPaの真空焼結炉内で、焼結温度1120℃、保持時間30分の焼結条件で、焼結することができる。
さらに、本工程では、繊維シートの作製上の効率のため、又は、繊維シートに特別な機能を付与するために、その他の添加剤を添加することができる。例えば、繊維同士の結合力が弱い場合には、アクリル樹脂等をバインダーとして追加することができる。
2.シール材の性質
サイクル試験は、ポンプに接続されたステンレス鋼製の配管(外径3mm)に対し、シール材を用いて接続し、配管内に水を流して行うことができる。ポンプを駆動させ、水を流すことで、配管内に背圧をかけ、10分間放置する。10分後、ポンプを停止させ、背圧を除いて10分間放置する。以降、背圧の負荷と背圧の除荷を繰り返す。所定の回数繰り返し、水漏れの有無、サイクルテスト後のシール材の変形の度合い観察を行い、圧力サイクル試験評価とすることができる。下記のような条件で行うことができる。溝漏れの有無及びシール材の変形の度合いは、肉眼による観察によって行うことができる。
3.シール材の製造方法
また、熱硬化性樹脂を用いる場合には、熱可塑性樹脂の場合と同様に、加熱した金型に繊維シートを設置し、プレス機によって加圧しながら、加熱により溶融した熱硬化性樹脂(必要に応じて硬化触媒を添加する)を流し込む。さらに硬化温度まで加熱し、冷却することで作製することができる。
なお、作製したシール材の残留応力(残留歪)を取り除くため、残留応力(残留歪)除去処理を行うことができる。残留応力(残留歪)除去する方法としては、特に限定されないが、例えば、ショットピーニングによる方法やアニール処理(加熱処理)等を行うことができる。分析機器に用いられるシール材のアニール処理としては、被分析物への混入がないこと、さらにサイズの小さなシール材の場合にも均一の処理できるアニール処理が好ましい。
アニール処理は、公知の方法、条件で行うことができる。一般に、結晶性樹脂の場合には、樹脂のガラス転移温度以上、例えばガラス転移温度よりも高く、使用が想定される温度よりも10℃~30℃高い温度に加熱し、30分~24時間維持することでアニール処理できる。非晶性樹脂の場合には、例えば、ガラス転移温度より20℃~30℃低い温度、もしくは荷重たわみ温度より5℃~10℃低い温度に加熱し、30分~24時間維持することでアニール処理できる。例えば、パーフルオロアルキルビニルエーテル共重合体の場合には、220℃、16時間の条件でアニール処理することができる。
4.シール材の用途
(実施例1~3)
<シール材の作製>
比較例1として、繊維シートを含まない(樹脂のみ)以外は、実施例1~3と同様にして、シール材を作製した。作製したシール材を表1に示した。
<評価方法>
前記抵抗管の温度が変化すると、抵抗管中を流れる流体の粘度が変化、また抵抗管内径も変化することで、一定の圧力を加えることができなくなる。このため本評価では、抵抗管を恒温槽(島津製作所製:CTO-20AC)に入れて20℃に温調することで、フローセルに加わる圧力を一定になるようにした。
移動相として水を使用し、10MPaから110MPaの任意の圧力がフローセルに加わるように送液量を変化させた。
測定は、圧力を、プランジャーポンプの背圧が、30MPa、70MPa、100MPaとし、10分ごとに、背圧をかけた状態と、大気圧の状態を繰り返し、1サイクルとした。評価は、100サイクル行い、水漏れ評価及び変形性評価を行った。結果を表1に示した。
<評価>
・変形性評価(水漏れ発生時点におけるフローの有無)
<評価結果>
1 シール材 [Problem] To provide: a seal material which shows high rigidity capable of withstanding deformation/breakage when subjected to a high sealing force and which exhibits excellent corrosion resistance and low dissolvability with respect to a fluid; a flow cell that is free from fluid leakage, is capable of preventing entry of a seal material component, and requires replacement less frequently; a detection instrument; and an analytical instrument. This seal material is for an analytical instrument, and comprises a resin and at least one layer of a fiber sheet embedded in the resin, wherein the at least one layer of the fiber sheet is embedded, between a first seal surface being one resin surface of the seal material and a second seal surface being the other resin surface that is substantially parallel to the first resin surface, in such a manner as to be disposed substantially parallel to the two seal surfaces. The flow cell, the detection instrument, and the analytical instrument use said seal material.
樹脂と、前記樹脂に包埋された、少なくとも1層の繊維シートとを含むシール材であって、
前記繊維シートが不織布である、請求項1に記載の分析機器用シール材。
前記繊維シートを構成する繊維の表面積の総和と、前記樹脂の体積との、関係が30cm2/cm3~500cm2/cm3である、請求項1又は2に記載の分析機器用シール材。
前記樹脂のガラス転移温度が40℃以上である、請求項1~3いずれか一項に記載の分析機器用シール材。
前記樹脂が、熱可塑性樹脂を含む、請求項1~4いずれか一項に記載の分析機器用シール材。
前記熱可塑性樹脂が、フッ素樹脂を含む、請求項5記載の分析機器用シール材。
前記フッ素樹脂が、テトラフルオロエチレン又はパーフルオロアルキルビニルエーテル共重合体を含む、請求項6記載の分析機器用シール材。
前記シール面と略平行である繊維シートが、金属繊維、無機繊維、有機繊維のうち少なくとも1種を含む、請求項1~7のいずれか一項に記載の分析機器用シール材。
請求項1~8の分析機器用シール材を、少なくとも1つ含む、フローセル。
請求項9のフローセルを含む、検出機器。
請求項1~8の分析機器用シール材を、少なくとも1つ含む、分析機器。
前記分析機器が、液体クロマトグラフ又は超臨界流体クロマトグラフである、請求項11記載の分析機器。
特許文献3には、高温・高面圧下で用いられる、内燃機関の燃料インジェクタ用のガスケットが開示されており、金属の不織布の空隙をゴムで充填してなるガスケットが提案されている。
即ち
本発明(1)は、
樹脂と、前記樹脂に包埋された、少なくとも1層の繊維シートとを含むシール材であって、
前記少なくとも1層の繊維シートは、前記シール材の一方の樹脂面である第1のシール面と、お互いに略平行な他方の樹脂面である第2のシール面との間に、前記2つのシール面と略平行に包埋されている、分析機器用シール材である。
本発明(2)は、
前記繊維シートが不織布である、前記発明(1)の分析機器用シール材である。
本発明(3)は、
前記繊維シートを構成する繊維の表面積の総和と、前記樹脂の体積との、関係が40cm2/cm3~500cm2/cm3である、前記発明(1)又は(2)の分析機器用シール材である。
本発明(4)は、
前記樹脂のガラス転移温度が40℃以上である、前記発明(1)~(3)のいずれかの分析機器用シール材である。
本発明(5)は、
前記樹脂が、熱可塑性樹脂を含む、前記発明(1)~(4)のいずれかの分析機器用シール材である。
本発明(6)は、
前記熱可塑性樹脂が、フッ素樹脂を含む、前記発明(5)の分析機器用シール材である。
本発明(7)は、
前記熱可塑性樹脂が、テトラフルオロエチレン又はパーフルオロアルキルビニルエーテル共重合体を含む、本発明(6)の分析機器用シール材である。
本発明(8)は、
前記シール面と略平行である繊維シートが、金属繊維、無機繊維、有機繊維のうち少なくとも1種を含む、前記発明(1)~(7)の分析機器用シール材である。
本発明(9)は、
前記発明(1)~(8)の分析機器用シール材を、少なくとも1つ含む、フローセルである。
本発明(10)は、
前記発明(9)のフローセルを含む、検出機器である。
本発明(11)は、
前記発明(1)~(8)の分析機器用シール材を、少なくとも1つを含む、分析機器である。
本発明(12)は、
前記分析機器が、液体クロマトグラフ又は超臨界流体クロマトグラフである、前記発明(11)の分析機器である。
本発明にかかるシール材は、樹脂と、前記樹脂に包埋された繊維シートを含む。前記シール材は、少なくとも1層の繊維シートが、前記シール材のシール面である2つの略平行な樹脂面(任意の一方の平面を第1のシール面とし、他方を第2のシール面とする)と略平行に包埋されていることを特徴とする。
第1に繊維シートに含まれる繊維1本当たりの、平均表面積(Sf)を求める。前記平均表面積(Sf)は、無作為に抜き出した20本の繊維について、走査型電子顕微鏡などの観察装置を用い、それら繊維の両端面の表面積(S1及びS2)、繊維の二つの端面の周囲長(L1及びL2)、繊維の長さ(L3)を測定し、下式により計算される繊維1本の表面積を選択した20本に対して算出し、それらの数平均を平均表面積とする。
繊維1本の表面積(Sf)={S1+S2+(L1+L2)/2×L3}
繊維1本の体積(Vf)={(D1+D2)/2/2}2×π×L3
繊維1本当たりの平均質量(Mf)=Vf×Df
繊維総数(Nf)=Ms÷Mf
繊維の総表面積=Nf×Sf
(A) 各材質の夫々についてSf、Vf、Mfを求める。
(B) Msに各材質の配合比を乗じ、繊維シートに含まれる各材質の総質量とする。
(C) 前記各材質の総質量を、各材質のMfで除することで、各材質のNfを求める。
(D) 各材質のNfと各材質のSfを乗じて、各材質の総表面積を算出する。
(E) 全ての各材質の総表面積の合計を繊維の表面積の総和とすることができる。
なお、各材質の配合比は、組成分析等公知の方法で実施すればよい。
本発明にかかる樹脂の材質は、特に限定されず、本願にかかる分析機器に流れる流体の種類(耐溶解性等)、温度、シール材に負荷されるシール力等の用途に応じて選択することができる。樹脂としては、例えば、熱可塑性樹脂、熱硬化性樹脂、エネルギー線硬化樹脂、ゴムやエラストマー等を挙げることができる。
本発明にかかる繊維シートは、繊維が集合したシートである限りにおいて、特に限定されず、例えば、織布(綾織、2重織り、3重織り、畳織り等)、不織布(抄造された紙状を含む)が挙げられる。繊維シートのシート平面方向の力学特性が等方性を有する繊維シートが好適である。即ち、前記繊維シートは、その平面方向に異方性がなく、いかなる平面方向においても等方的に強い力学特性を有する。例えば、単純な90度に直行した繊維による平織りした織布の場合には、繊維が織り込まれている方向(繊維が延存している方向)における力学特性は優れているが、直交する繊維と繊維の間の方向(例えば、一方の繊維の延存する方向を0度とした場合の45度方向)の力学特性は低くなる。また、本発明にかかるシール材がシールされる際には、繊維シートに高いシール力が負荷され、繊維シートには繊維シート表面に平行な方向にせん断力が等方的に負荷される(図2)。このとき、繊維の延存する方向には変形しにくいが、前記45度方向には容易に変形してしまう場合があり、シール材が辺変形したり、破損したり、漏れが発生したりするおそれがある。一方、不織布のようなシート表面の平面方向に等方的な力学特性を有する繊維シートの場合には、その平面方向において、異方性がないため、等方的にせん断力が負荷され、どの方向にも変形しづらいという特徴を有している。従って、本発明にかかる繊維シートとしては、不織布を好適に用いることができる。
本発明にかかる繊維シートを形成する繊維は、特に限定されず、公知のものを使用することができ、金属繊維、無機繊維、有機繊維のうち少なくとも1種を含むことができる。前記繊維としては、例えば、ステンレス鋼繊維、ニッケル繊維、銅繊維、アルミニウム繊維、銀繊維、金繊維、チタン繊維等の金属繊維;ポリパラフェニレンベンズオキサゾール、ポリエチレンテレフタレ-ト(PET)樹脂、ポリビニルアルコ-ル(PVA)、ポリエチレン、ポリプロピレン等のポリオレフィン樹脂、ポリ塩化ビニル樹脂、アラミド樹脂、アクリル樹脂、ポリイミド樹脂、ポリパラフェニレンベンズオキサゾール(PBO)繊維、セルロース、ビニロン、ナイロン、レ-ヨン、アラミド、フェノ-ル系繊維、フッ素繊維、パルプ(繊維)、ケナフ、麻、竹繊維等の有機繊維;ガラス繊維、炭素繊維、シリカ繊維、ロックウ-ル、スラグウ-ル、アルミナ繊維、セラミック繊維等の無機繊維;等を挙げることができる。これらのうち一つ又は複数を組み合せて用いることができる。本発明にかかる繊維は、シール材に用いられる樹脂のヤング率よりも高いヤング率を有する繊維が好ましく、金属繊維、無機繊維がより好ましい。繊維のヤング率が高いほど繊維シートの剛性を高くすることが可能であり、前記樹脂に包埋した際、樹脂の剛性を効果的に向上させることが可能となる。従って、剛性が高く、破損し難いシール材を得ることが可能となる。
融着や焼結を行うことで、繊維シートの剛性を向上することができる。
空隙率(%)=(1-繊維シートの質量/(繊維シートの体積×繊維の密度))×100
なお、空隙率は、使用する繊維の太さ、量や、繊維が交絡した材料の密度や、圧縮成形における圧力によって調整することができる。
また、繊維シートが樹脂中に包埋されている場合には、繊維シートの外寸、繊維シートを構成する繊維の繊維径、繊維長から算出してもよい。繊維径は投影面積の円相当径とすることができる。
本発明にかかる繊維シートの製造方法は、公知の方法を用いることができる。例えば、好適例である不織布を製造する方法としては、カーディング方式、エアレイド方式等の乾式法、紙のように漉いて形成する湿式抄造法、スパンボンド法、メルトブロー法等のフリース形成法;サーマルボンド法、ケミカルボンド法、ニードルパンチ法、スパンレース法(水流絡合法)、ステッチボンド法、スチームジェット法等のフリース結合法が挙げられる。このうち、湿式抄造法による製造方法が、繊維シートを薄くすることが可能であり、さらに均一性の点で優れているため好適である。
本発明にかかる繊維シートの製造方法は、例えば公知の抄紙方法により製造することができ、例えば、一つ又は複数の繊維、必要に応じて他の成分を水に分散させて原料スラリーを調製し、得られた原料スラリーを湿式抄紙して繊維シートを得ることができる。
2-1.圧力サイクル試験
上述したように、本発明にかかるシール材は、分析機器の接続部に用いられる。一般にシール材には、流体が流れ始める際(突入時)に強い負荷がかかり、定常状態に落ち着くと安定する。従って、シール材の特性として、圧力の負荷をOn/Offする(突入を繰り返す)サイクル試験における耐久性が要求される。
・周囲温度 :25±2℃
・負荷背圧(ポンプ吐出圧):30MPa、70MPa又は100MPa
・サイクル数:100サイクル
本発明にかかるシール材の製造方法は、特に限定されず、公知の方法を用いることができる。例えば、樹脂として熱可塑性樹脂を用いる場合には、加熱した金型に繊維シートを設置し、プレス機によって加圧しながら、加熱により溶融した熱可塑性樹脂を流し込み、冷却することで作製する方法や、加熱しつつ圧力を調整しながらプレスし、冷却したのち、はみ出した部分を取り除くことでも作製することができる。
本発明にかかるシール材は、シール材としての用途であれば、特に限定されないが、より高いシール力が負荷される用途に好適に用いられる。そのような用途として、高い流体圧力が必要な液体クロマトグラフや超臨界流体クロマトグラフのような分析機器用シール材が挙げられる。特に、液体クロマトグラフや超臨界流体クロマトグラフのような分析機器に用いられる。また、液体クロマトグラフや超臨界流体クロマトグラフのような分析機器にはUV検出器や示差屈折率検出器のレンズ部のシール材や、ミキサ(ミキシングの機能とシール機能)や、配管部の流体が流れ、高圧が付加される部分に用いることができる。これらの装置・機器においては、細い配管内を一定の流量で流体を流すため、高い流体圧力が必要である。また超臨界流体クロマトグラフィーは、例えば、二酸化炭素等を超臨界流体に転移させるため高い圧力が必要となる。従って、前述したUV吸光度検出器や示差屈折率検出器等に内蔵されるフローセルの配管部やレンズ等の接続部にも高い圧力がかかるため、接続部等には強いシール力が必要となり、そのシール力に耐えうるシール材として本願発明のシール材は好適である。
<繊維シートの作製>
繊維長2.0mm、繊維径が4μm、8μm及び22μmのステンレス鋼繊維(SUS316L)とシートハンドリングに必要なPET繊維を適量、それぞれ水中で離解・分散し、それぞれのスラリーを調製した。得られたスラリーを湿式抄紙法によって脱水プレス、加熱乾燥し金属繊維シートを得た。得られた該シートを表面温度が160℃の加熱ロールを用い線圧300kg/cm、速度5m/minの条件で加熱圧着した。次に上記の圧着した金属繊維シートを加圧することなく水素ガス雰囲気の連続焼結炉(メッシュベルト付ろう付炉)を用い、熱処理温度1120℃、速度15cm/minで焼結処理を行い坪量50g/m2、密度1.69g/cm3のステンレス繊維同士が焼結した、繊維径の異なる3種類の金属繊維焼結シートを得た。得られた繊維シートの空隙率を表1に示した。また、得られた繊維シートを下記の形状に裁断した。
・繊維シートの形状:ドーナツ形状
・外径 :5.0mm
・内径 :2.3mm
・繊維シートの厚み:0.1mm
・Lf(図1) :2.7mm
400℃に加熱したプレス機に、パーフルオロアルキルビニルエーテル共重合体(PFA)からなるシート間に実施例1の繊維シートを挟み、圧力を調整しつつ加圧した後、冷却した。その後、余分な樹脂部を打ち抜きにより取り除くことで以下寸法の本発明のシール材を得た。4μm、8μm及び22μmの繊維を含んだ繊維シートを用い、内径を1mmとして作製したシール材をそれぞれ、実施例1~3のシール材とした。作製したシール材を表1に示した。
・シール材の形状:ドーナツ形状
・外径(DO) :6.0mm
・内径(DI) :1mm
・シール材の厚み:0.2mm
・シール材の形状:ドーナツ形状
・外径(DO) :6.0mm
・内径(DI) :1mm
・シール材の厚み:0.2mm
・Ls(図1) :なし
・T1(図1) :なし
・T2(図1) :なし
・Li(図1) :なし
・Lo(図1) :なし
・Lf/Ls :なし
・圧力サイクル試験
送液流量と背圧をモニタできるプランジャーポンプ(島津製作所製:LC-30AD)の送液側に、各実施例と比較例のシール材を用いたフローセルを締結し、その後段に、内径0.1mmのSUS316L製抵抗管を接続した。この抵抗管に一定流量の液体(移動相)を通液することで、フローセルに一定の圧力を加えることができる。
・水漏れ評価
◎:背圧100MPaにおいて水漏れなし
〇:背圧70MPaにおいて水漏れなし、背圧100MPaにおいて水漏れあり
△:背圧30MPaにおいて水漏れなし、背圧70MPaにおいて水漏れ有り
×:背圧30MPaにおいて、水漏れ有り
◎:背圧100MPaにおいて、シール材がドーナツ状の形状を維持している
〇:背圧70MPaにおいて水漏れなし、背圧100MPaにおいて、シール材がドーナツ状の形状を維持している
△:背圧30MPaにおいて水漏れなし、背圧70MPaにおいて、シール材がドーナツ状の形状を維持している
×:背圧30MPaにおいて、ドーナツ状の形状が崩れている
表1の結果から、高圧力のサイクル試験後において、本発明のシール材が、耐変形性が高く、水漏れも発生しない優れたシール材であることが理解でき、本発明の効果が明らかであることが理解できる。
2 配管部材(接合部)
10 樹脂部
11 第1のシール面
12 第2のシール面
13 内径側側面
14 外径側側面
20 繊維シート
21 第1の繊維シート表面
22 第2の繊維シート表面
前記少なくとも1層の繊維シートは、前記シール材の一方の樹脂面である第1のシール面と、お互いに略平行な他方の樹脂面である第2のシール面との間に、前記2つのシール面と略平行に包埋されている、分析機器用シール材。

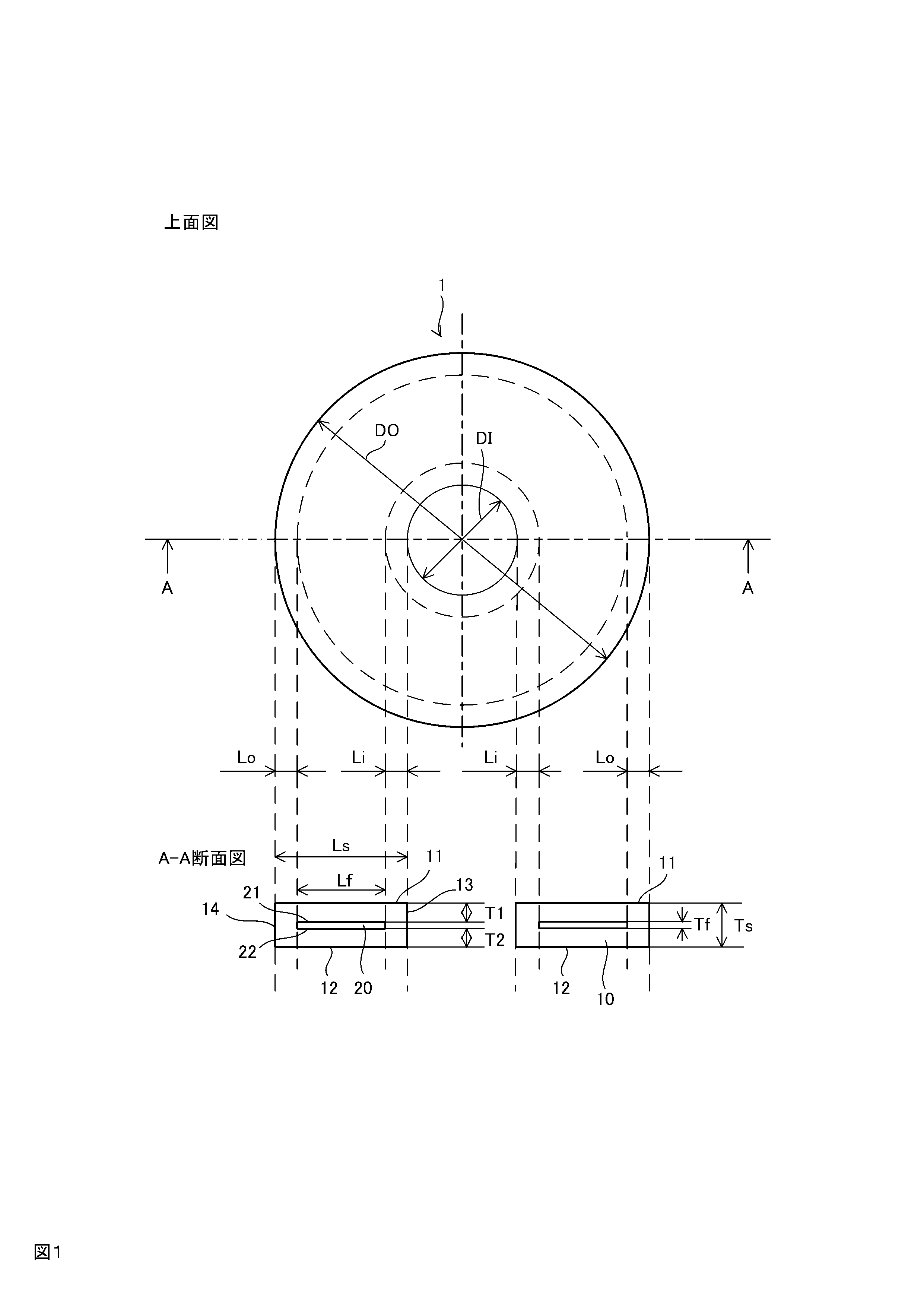