METHOD FOR MANUFACTURING A THERMOPLASTIC MOULDING POWDER
Die vorliegende Erfindung betrifft ein Verfahren zur Herstellung eines thermoplastischen Formmassenpulvers. Aus dem Stand der Technik ist es bekannt, Feedstockmassen bereitzustellen, aus denen in einem oder mehreren weiteren Bearbeitungsschritten Formkörper gewonnen werden. Unter einem thermoplastischen Formmassenpulver ist im Rahmen der Erfindung insbesondere eine pulverförmige Feedstockmasse zu verstehen, aus der in einem oder mehreren weiteren Schritten ein Formkörper z.B. durch Sintern gewonnen wird. Pulverförmige Feedstockmassen sind gemäß dem Stand der Technik beispielsweise dadurch zugänglich, dass durch thermoplastische Formgebung hergestellte Granulate in einem Zerkleinerungsprozess, wie beispielsweise durch einen Mahlprozess entweder nass oder trocken zerkleinert werden. Die auf diese Weise herstellten Pulver besitzen eine zerklüftete Geometrie sowie eine sehr unterschiedliche Teilchengröße, überwiegend im Bereich von 0,01 mm bis 1,0 mm. Aufgrund der zerklüfteten Teilchengeometrie haben diese Pulver bzw. Feedstockmassen eine verhältnismäßig geringe Schüttdichte und besitzen im Teilchenbereich unterhalb von 0,1 mm ein schlechtes Fließvermögen. Diese beiden durch einen Mahlprozess bedingten Eigenschaften des Pulvers sind für bestimmte Anwendungstechnologien störend, insbesondere dann, wenn eine hohe Packungsdichte einer Pulverschüttung angestrebt wird oder wenn das Pulver z.B. mit einem Rakel in einer dünnen Schicht sehr gleichmäßig aufgetragen werden soll. Als Beispiele für diese Anwendungstechnologien sind das sogenannte Pulverschäumen von keramischen oder metallischen Formmassen zu nennen, wie dies z.B. in der In beiden Fällen wird zunächst ein sinterfähiger Grünkörper erzeugt, der nachträglich entbindert wird, d.h. bei dem teilweise oder vollständig der Binder entfernt wird, und anschließend ein Sinterverfahren durchgeführt wird, um den gewünschten Formkörper zu erhalten. Beim SLS-Verfahren ist eine hohe Gründichte, d.h. eine hohe Dichte der die Formmasse bildenden Formmassenteilchen, im Grünkörper von Vorteil, damit bei dem anschließenden Sinterverfahren eine möglichst hohe Dichte des Formkörpers erhalten wird. Dabei ist es von Vorteil, wenn sphärische Formmassenteilchen zum Einsatz kommen. Die sphärische Form der Formmassenteilchen ist auch vorteilhaft, um eine gute Fließfähigkeit der Formmassenteilchen beim Rakeln der einzelnen zu lasernden Schichten zu erhalten. Für die beiden Fertigungstechniken sind pulverförmige Formmassenteilchen vorteilhaft, die sphärisch sind, die Teilchengrößen unterhalb von 0,2 mm aufweisen und die zudem in hohen Schüttdichten vorliegen. Weiterhin offenbart die Zudem ist aus der Der vorliegenden Erfindung liegt somit die Aufgabe zugrunde, pulverförmige Formmassen bereitzustellen, die eine oder mehrere und vorzugsweise alle der genannten Eigenschaften aufweisen, d.h. deren Teilchen eine sphärische Geometrie aufweisen, die frei fließen und die in einer hohen Schüttdichte vorliegen. Diese Aufgabe wird durch ein Verfahren mit den Merkmalen des Anspruchs 1 gelöst. Danach ist vorgesehen, dass das thermoplastische Formmassenpulver bestehend aus oder umfassend sphärische Formmassenteilchen aus einer Suspension aus keramischen und/oder metallischen und/oder glasartigen Substratteilchen in einem Lösungsmittel durch Sprühtrocknung erhalten wird. In dem Lösungsmittel- ist ein Binder gelöst, der wenigstens ein Polymer aufweist, das in dem Lösungsmittel löslich ist. Des Weiteren weist der Binder einen in dem Lösungsmittel löslichen Weichmacher auf. Optional weist der Binder weitere in dem Lösungsmittel lösliche Additive auf, die vorzugsweise molekular in diesem gelöst sind. Bei diesen Additiven kann es sich beispielsweise um einen oder mehrere der Stoffe Gleitmittel, Additive, die mit dem Polymer ein zumindest binäres System bilden. Vorzugsweise handelt es sich bei dem Additiv um eine Substanz, die das rheologische Verhalten des Polymers beeinflusst. Das Polymer ist erfindungsgemäß Polyamid. Beim Sprühtrocknen der Suspension geht das Lösungsmittel vollständig in die Gasphase über und die keramischen und/oder metallischen und/oder glasartigen Substratteilchen bilden dabei Agglomerate in Form der sphärischen Formmassenteilchen. Durch das Verdüsen und das gleichzeitige Verdunsten des Lösungsmittels der Suspension entstehen aus den Tröpfchen, die die keramischen und/oder metallischen und/oder glasartigen Teilchen enthalten, feste weitgehend sphärische Formmassenteilchen, deren keramische und/oder metallische und/oder glasartigen Teilchen durch den Binder zusammengehalten werden. An dieser Stelle wird darauf hingewiesen, dass der Begriff "sphärisch" auch "weitgehend sphärisch" mit umfasst. Vorzugsweise ist darunter ein kugelförmiger oder der Kugelform angenäherter Körper zu verstehen. Des Weiteren wird darauf hingewiesen, dass die Begriffe "ein" und "eine" nicht zwingend bedeuten, dass genau eines der fraglichen Elemente vorhanden ist, wenngleich auch dies eine mögliche Ausgestaltung der Erfindung ist. Von dem Begriff "ein" oder "eine" ist auch eine Mehrzahl der fraglichen Elemente umfasst. Das Verdunsten kann durch die Zufuhr eines erwärmten Gasstroms, wie beispielsweise Luft oder Stickstoff oder eines sonstigen Gases gefördert werden. Durch das Verfahren der Sprühtrocknung werden sphärische Formmassenteilchen geschaffen. Das Verfahren der Sprühtrocknung kennzeichnet sich dadurch aus, dass die zu gewinnenden Stoffe entweder in einer Flüssigkeit gelöst oder dispergiert vorliegen. Beim Sprühtrocknen wird ein vorzugsweise warmer Luftstrom eines Gases, wie Luft oder Stickstoff zugeführt. Durch das Verdüsen und durch das gleichzeitige Verdunsten der Flüssigkeit durch die Zufuhr des genannten Gasstroms entstehen aus den Tröpfchen feste, sphärische Formmassenteilchen, worunter auch weitgehend sphärische Formmassenteilchen zu verstehen sind. Ein wesentlicher Bestandteil des erfindungsgemäßen Verfahrens ist somit das Sprühtrocknen, durch das sphärische Formmassenteilchen, d.h. sphärische Formmassenpulver generiert werden, d.h. Pulver, die aus den sphärischen Formmassenteilchen bestehen oder diese enthalten. In einer Ausgestaltung der Erfindung ist der Binder, wie das oder die alkohollöslichen Polyamide, molekular in der Suspension gelöst. Der Binder hält die keramischen und/oder metallischen und/oder glasartigen Substratteilchen bei und nach dem Sprühtrocknen zusammen, so dass diese die Formmassenteilchen bilden können. Diese sind ausreichend stabil, um weiteren Verarbeitungsschritten unterzogen werden zu können. Bei dem Lösungsmittel handelt es sich erfindungsgemäß um einen oder mehrere Alkohole oder um ein oder mehrere alkoholische Medien. Bevorzugt ist es, wenn es sich bei dem Weichmacher um einen Ester einer aromatischen Hydroxybenzoesäure und vorzugsweise um einen p-Hydroxybenzoesäure-Fettalkoholester handelt, wobei die Länge der Kohlenstoffkette vorzugsweise im Bereich C12 - C26, besonders vorzugsweise im Bereich C18 - C22 liegt. Die metallischen Substratteilchen, die in der Suspension vorliegen, weisen vorzugsweise eine mittlere Größe im Bereich von 5 µm bis 25 µm, vorzugsweise im Bereich von 10 µm bis 20 µm und besonders bevorzugt 15 µm auf. Die keramischen Substratteilchen, die in der Suspension vorliegen, weisen vorzugsweise eine mittlere Größe im Bereich von 0,1 µm bis 5 µm auf. Im Falle glasartiger Substratteilchen, die in der Suspension vorliegen, weisen diese vorzugsweise eine mittlere Größe im Bereich von 1,0 µm bis 50 µm auf. Die Formmassenteilchen, die das thermoplastische Formmassenpulver bilden und die eine Mehrzahl von keramischen und/oder metallischen und/oder glasartigen Substratteilchen und den Binder enthalten, weisen vorzugsweise eine Größe im Bereich von > 0,05 mm und/oder < 0,2 mm, vorzugsweise 0,05 mm bis 0,15 mm und besonders bevorzugt 0,10 mm auf. Bei der genannten Größe kann es um die größte Abmessung der keramischen und/oder metallischen und/oder glasartigen Substratteilchen bzw. der Formmassenteilchen und/oder um deren Durchmesser handeln. Vorzugsweise ist vorgesehen, dass die Formmassenteilchen jeweils eine maximale Abmessung Amax haben und für mindestens 80 % der Formmassenteilchen gilt: 0,005 mm ≤ Amax ≤ 0,3 mm, insbesondere 0,008 mm ≤ Amax ≤ 0,2 mm, und insbesondere 0,01 mm ≤ Amax ≤ 0,1 mm. Erfindungsgemäß ist vorgesehen, dass die Formmassenteilchen jeweils eine minimale Abmessung Amin und eine maximale Abmessung Amax haben und für mindestens 80 % der Formmassenteilchen gilt: 0,6 ≤ Amin/Amax ≤ 1, insbesondere 0,7 ≤ Amin/Amax ≤ 1, und insbesondere 0,8 ≤ Amin/Amax ≤ 1. Denkbar ist es weiterhin, dass die Substratteilchen jeweils eine maximale Abmessung Bmax haben und für mindestens 80 % der Substratteilchen (3) gilt: 1 µm ≤ Bmax ≤ 50 µm, insbesondere 5 µm ≤ Bmax ≤ 40 µm, und insbesondere 10 µm ≤ Bmax ≤ 30 µm. Die Substratteilchen bestehen vorzugsweise aus Glas, Keramik, Edelmetall, Hartmetall, Buntmetall, Eisen, Titan oder Stahl, aus einer oder mehreren von deren Legierungen, Superlegierungen oder Verbindungen oder weisen eines oder mehrere dieser Stoffe bzw. Metalle, Legierungen oder Verbindungen auf. Wie oben ausgeführt, kann es sich bei den Substratteilchen auch um solche handeln, die aus Keramik und/oder Glas bestehen oder Keramik und/oder Glas aufweisen. In einer bevorzugten Ausgestaltung der Erfindung werden zunächst die keramischen und/oder metallischen Substratteilchen in ein Lösungsmittel, wie beispielsweise in eine alkoholische Lösung, umfassend den Binder eingebracht und sodann wird diese Suspension in einer Sprühanlage unter teilweiser oder vollständiger Verdampfung des Lösungsmittels verdüst. Dabei bilden die keramischen und/oder metallischen und/oder glasartigen Substratteilchen sphärische Agglomerate in Form der Formmassenteilchen. Vorzugsweise ist vorgesehen, dass das Einbringen der keramischen und/oder metallischen und/oder glasartigen Substratteilchen in das Lösungsmittel bei erhöhter Temperatur, vorzugsweise bei einer Temperatur im Bereich von 60 °C bis 80 °C und besonders bevorzugt bei 70 °C erfolgt. Erfindungsgemäß ist vorgesehen, dass das Sprühverfahren bei einer Temperatur durchgeführt wird, die 10°C - 30°C, vorzugsweise 20°C unter der Kristallisationstemperatur des additivierten Polymers liegt. Nach dem Eintragen des keramischen und/oder metallischen und/oder glasartigen Pulvers bzw. der Substratteilchen in die Lösung wird diese Suspension vorzugsweise direkt in einer bevorzugt Ex-geschützten Sprühanlage verdüst, wobei die Temperatur so gewählt ist, dass das Lösungsmittel vollständig oder teilweise verdampft. In einer denkbaren Ausführungsform wird das Sprühverfahren so durchgeführt, dass die Suspension in eine Flüssigkeit gesprüht wird, in der der Binder unlöslich ist, wobei es sich bei der Flüssigkeit vorzugsweise um Wasser handelt. Dies bringt den Vorteil mit sich, dass die durch das Sprühverfahren gebildeten Formmassenteilchen und damit auch der Binder gekühlt werden und dadurch eine verbesserte mechanische Stabilität erhalten. Der im Rahmen der vorliegenden Erfindung eingesetzte Binder weist vorzugsweise eine Schmelzeviskosität von 10° Pa·s bis 106 Pa·s, insbesondere von 100 Pa·s bis 105 Pa·s, und insbesondere von 10° Pa·s bis 104 Pa·s bei einer Temperatur auf, die mindestens 10°C über einer Temperatur Ts liegt, wobei die Temperatur Ts eine Glasübergangstemperatur oder eine Kristallitschmelztemperatur des Binders ist und ein Geschwindigkeitsgefälle insbesondere ausgewählt ist aus der Gruppe 1,00 s-1, 2,50 s-1, 5,00 s-1, 10,0 s-1, 25,0 s-1, 50,0 s-1 und 100 s-1. Die Bestimmung der Schmelzeviskosität erfolgt vorzugsweise nach DIN EN ISO 3219 (Stand: Oktober 1994). Die angegebenen Werte der Schmelzeviskosität gelten insbesondere für ein Geschwindigkeitsgefälle von 1,00 s-1, Die Temperatur TS ist bei einer amorphen Struktur des Binders die Glasübergangstemperatur und bei einem teilkristallinen Binder die Kristallitschmelztemperatur, insbesondere die maximale Kristallitschmelztemperatur. Besonders vorteilhaft ist es, wenn die Formmassenteilchen des Formmassenpulvers eine Größe im Bereich von > 0,05 mm, vorzugsweise < 0,2 mm, vorzugsweise 0,05 mm bis 0,15 mm und besonders bevorzugt 0,10 mm aufweisen. Vorzugsweise ist vorgesehen, dass die Formmassenteilchen jeweils eine maximale Abmessung Amax haben und für mindestens 80 % der Formmassenteilchen gilt: 0,005 mm ≤ Amax ≤ 0,3 mm, insbesondere 0,008 mm ≤ Amax ≤ 0,2 mm, und insbesondere 0,01 mm ≤ Amax ≤ 0,1 mm. Erfindungsgemäß ist vorgesehen, dass die Formmassenteilchen jeweils eine minimale Abmessung Amin und eine maximale Abmessung Amax haben und für mindestens 80 % der Formmassenteilchen gilt: 0,6 ≤ Amin/Amax ≤ 1, insbesondere 0,7 ≤ Amin/Amax ≤ 1, und insbesondere 0,8 ≤ Amin/Amax ≤ 1. Die Verwendung des thermoplastischen Formmassenpulvers als Ausgangsmaterial für ein pulverbasiertes, additives Fertigungsverfahren ist vorgesehen. Weitere Einzelheiten und Vorteile der Erfindung werden anhand eines in der Zeichnung dargestellten Ausführungsbeispiels näher erläutert. Es zeigen: Führt man die in Es weist einen Durchmesser von < 0,2 mm auf und lässt sich bei einer Temperatur bei bzw. ab 150 °C ohne Druckanwendung in eine Schmelze, vorzugsweise in eine niedrigviskose Schmelze bringen, die dann z.B. in einem 3D-Druckverfahren zu einem Formteil verarbeitet werden kann. Die Formmassenteilchen gemäß Besonders vorteilhaft ist die Verwendung der erfindungsgemäßen Formmassenteilchen bei einem pulverbasierten, additiven Fertigungsverfahren, wie beispielsweise bei einem 3D-SLS-Verfahren (SLS = selektives Lasersintern) . Aus Während man beim Sprühtrocknen der wässrigen Suspension Agglomerate gemäß Höhere Grün- bzw. Schüttdichten sind beim Lasersintern von wesentlicher Bedeutung für die später am gesinterten Formteil vorhandene Sinterdichte. Method of manufacturing thermoplastic molding compound powder that consists of or comprises spherical molding compound particles from a suspension of glass-like and/or ceramic and/or metallic substrate particles in a solvent, in which a binder is dissolved that comprises a thermoplastic polymer soluble in the solvent, wherein the binder furthermore comprises a plasticizer soluble in the solvent, wherein the method comprises the step of spray drying the suspension, wherein the spray drying is performed at a temperature that is 10°C - 30°C below the glass transition temperature or crystallization temperature of the additive thermoplastic polymer such that the solvent completely transitions into the gas phase, wherein the solvent is one or more alcohols or one or more alcoholic media, and the thermoplastic polymer is a polyamide, wherein the molding compound particles each have a minimum dimension Amin and a maximum dimension Amax and 0.6 ≤ Amin/Amax ≤ 1, in particular 0.7 ≤ Amin/Amax ≤ 1, and in particular 0.8 ≤ Amin/Amax ≤ 1 applies to at least 80% of the molding compound particles. Method in accordance with claim 1, characterized in that the plasticizer is an ester of an aromatic hydroxybenzoic acid and is preferably a p-hydroxybenzoic acid fatty alcohol ester, wherein the length of the carbon chain of the fatty alcohol is preferably in the range C12 - C26, particularly preferably in the range C18 - C22. Method in accordance with one of the preceding claims, characterized in that the substrate particles each have a maximum dimension Bmax and 1 µm ≤ Bmax ≤ 50 µm, in particular 5 µm ≤ Bmax ≤ 40 µm, and in particular 10 µm ≤ Bmax ≤ 30 µm applies to at least 80% of the substrate particles. Method in accordance with one of the preceding claims, characterized in that the molding compound particles each have a maximum dimension Amax and 0.005 mm ≤ Amax ≤ 0.3 mm, in particular 0.008 mm ≤ Amax ≤ 0.2 mm, and in particular 0.01 mm ≤ Amax ≤ 0.1 mm applies to at least 80% of the molding compound particles. Method in accordance with one of the preceding claims, characterized in that the substrate particles consist of one or more of the substances: precious metal, hard metal, glass, ceramics, non-ferrous metal, iron, titanium, alloys and/or compounds thereof, superalloys and steel, or comprise one or more of these substances or metals, alloys or compounds. Method in accordance with one of the preceding claims, characterized in that the ceramic and/or metallic and/or glass-like substrate particles are first introduced into the solvent comprising the binder, and the spray drying of the suspension then is carried out. Method in accordance with claim 6, characterized in that the introduction of the ceramic and/or metallic and/or glass-like substrate particles takes place at elevated temperature, preferably at a temperature in the range from 60°C to 80°C, and particularly preferably at 70°. Method in accordance with one of the preceding claims, characterized in that the method is carried out such that the suspension is sprayed into a liquid in which the binder is insoluble, wherein the liquid preferably is water.
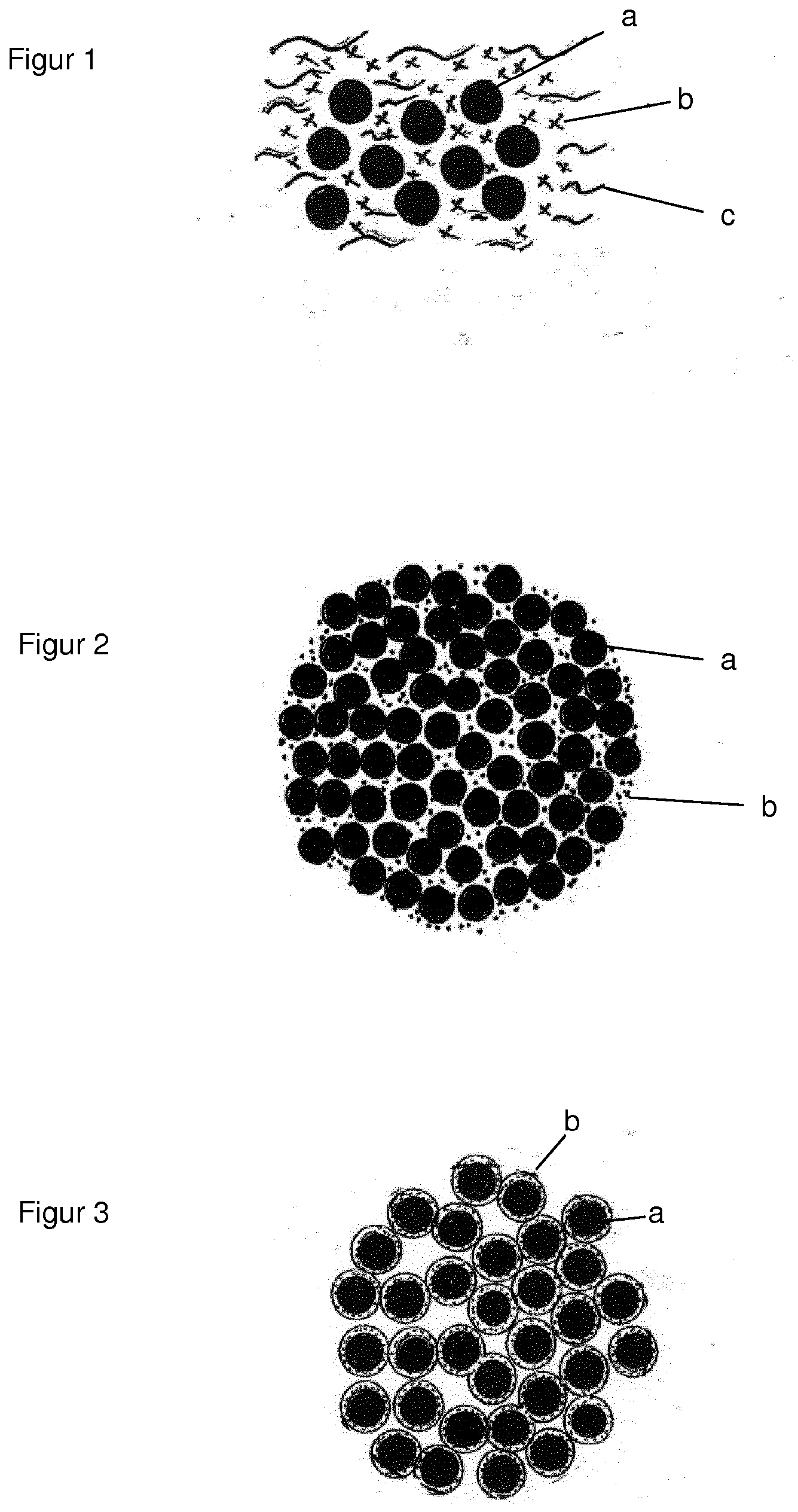
CPC - классификация
BB2B22B22FB22F1B22F1/B22F1/0B22F1/06B22F1/065B22F1/1B22F1/10B22F1/103B22F10B22F10/B22F10/2B22F10/28B22F10/3B22F10/34B22F2B22F29B22F299B22F2998B22F2998/B22F2998/1B22F2998/10B22F9B22F9/B22F9/0B22F9/02B22F9/026B29B29CB29C6B29C64B29C64/B29C64/1B29C64/15B29C64/153B29KB29K2B29K21B29K210B29K2105B29K2105/B29K2105/0B29K2105/00B29K2105/003B29K2105/0038B29K2105/2B29K2105/25B29K2105/251B29K29B29K290B29K2905B29K2905/B29K2905/0B29K2905/00B29K2909B29K2909/B29K2909/0B29K2909/02B29K2909/08B3B33B33YB33Y1B33Y10B33Y10/B33Y10/0B33Y10/00B33Y7B33Y70B33Y70/B33Y70/1B33Y70/10CC0C04C04BC04B2C04B22C04B223C04B2235C04B2235/C04B2235/5C04B2235/52C04B2235/528C04B2235/54C04B2235/542C04B2235/5427C04B2235/6C04B2235/60C04B2235/602C04B2235/6026C04B3C04B35C04B35/C04B35/6C04B35/62C04B35/622C04B35/626C04B35/6265C04B35/62655C04B35/6269C04B35/62695C04B35/63C04B35/634C04B35/6340C04B35/63408C04B35/6342C04B35/63424C04B35/6343C04B35/63432C04B35/6344C04B35/63444C04B35/6345C04B35/63456C04B35/6346C04B35/63468C08C08JC08J2C08J23C08J230C08J2300C08J2300/C08J2300/2C08J2300/22C08J232C08J2323C08J2323/C08J2323/0C08J2323/00C08J2325C08J2325/C08J2325/0C08J2325/06C08J233C08J2333C08J2333/C08J2333/0C08J2333/08C08J2339C08J2339/C08J2339/0C08J2339/06C08J237C08J2375C08J2375/C08J2375/0C08J2375/04C08J3C08J3/C08J3/0C08J3/09C08J3/095C08J3/1C08J3/12C08J3/122C08J5C08J5/C08J5/1C08J5/12C08KC08K3C08K3/C08K3/0C08K3/00C08K3/08C08K3/4C08K3/40C08K5C08K5/C08K5/0C08K5/00C08K5/001C08K5/0016C08K5/1C08K5/10C08K5/101C08K5/105YY0Y02Y02PY02P1Y02P10Y02P10/Y02P10/2Y02P10/25IPC - классификация
BB2B22B22FB22F1B22F1/B22F1/0B22F1/00B22F1/06B22F1/065B22F1/1B22F1/10B22F1/103B22F9B22F9/B22F9/0B22F9/02B3B33B33YB33Y7B33Y70B33Y70/B33Y70/0B33Y70/00CC0C04C04BC04B3C04B35C04B35/C04B35/6C04B35/62C04B35/622C04B35/626C04B35/63C04B35/634C08C08KC08K3C08K3/C08K3/0C08K3/08C08K3/4C08K3/40C08K5C08K5/C08K5/0C08K5/00C08K5/1C08K5/10C08K5/101Цитирование НПИ
Anonymous: "Glasübergangstemperatur | Kunststoffrohrverband e.V. - Fachverband der Kunststoffrohr-Industrie", , 12 June 2020 (2020-06-12), XP055704352, Retrieved from the Internet: URL:https://www.krv.de/artikel/glasueberga ngstemperatur [retrieved on 2020-06-12]CN-A- 106 316 388
DE-A1- 2 065 705
EP-A1- 2 033 724
KR-A- 20160 071 014
WO-A1-2015/175726
WO-A1-96/05038