SINTERING PASTE AND METHOD FOR PRODUCING A SINTERING PASTE
The present invention relates to a sintering paste for forming a copper-containing interconnection layer between two solid substrates, a method for producing a sintering paste and a use of the sintering paste. Die-attach bonding is a key process to realize high-temperature operation of power semiconductor devices. High Pb solders have been a preferred and well established choice over the past decades. However strict regulations concerning hazardous substances restrict the usage of high Pb solders and the few exceptions that exist today are also foreseen to be banned in the near future. With the increase in the usage of wide-bandgap (WBG) semiconductor devices, it is imperative to find sustainable and reliable alternatives both on the economical and the technical fronts. Interconnect materials and technologies need to be able to fulfill the challenging requirements of the WBG semiconductor devices and at the same time need to be economical for enabling mass production. Currently, there are two established methods to produce high-temperature bonds while benefiting from the comparatively low-temperature bonding temperature: Transient liquid phase (TLP) bonding and particle sintering. Although various studies reported successful production of an in-situ phase with a higher re-melting point, thermo-mechanical fracture behavior of TLP bonded joint appeared to have a major drawback. That is due to microstructure of the TLP bonded joint as it is made of brittle intermetallic compounds (IMCs). However, for the case of particle sintering, there are promising reports that suggest Ag-sintered joint as a candidate for high-temperature WBG applications. During sintering, it is possible to realize a connection, which consists of one metal throughout. Beside the high thermal conductivity of the material, the advantage is that the interconnect is established at relative low temperature (250 °C) but is stable at higher temperature (over 300 °C). However, sintered Ag particles have its own drawbacks: High cost and low-electromigration resistance. Copper is approximately 100 times cheaper than silver and also more abundant and easily available. It has a lower co-efficient of thermal expansion than silver and has nearly the same electrical and thermal conductivities. However, the higher melting point of copper means that the sintering temperatures are also slightly higher than in case of silver. Furthermore, the susceptibility to oxidize quickly under atmosphere is a major drawback when using copper as this is detrimental to the mechanical and thermal integrity of the joint. From According to The problem to be solved by the present invention is to provide an alternative sintering paste, an alternative method for producing the sintering paste and a use of this sintering paste. The sintering paste and the method shall enable sintering with short sintering times, with low sintering temperature and/or with low sintering pressure. Sintering of the sintering paste shall result in a homogenous bonding interface. The sintering paste shall further ensure high ductility without requiring a reducing inert gas atmosphere during sintering. The problem is solved by the subject-matter of claims 1, 10 and 15 of the present invention. Embodiments of the invention are subject-matter of claims 2 to 9 and claims 11 to 14. According to the invention a sintering paste for forming a copper-containing interconnection layer between two solid substrates is provided. The sintering paste is obtained by the following steps:
In the mixture according to step b), the complexing agent complexes the copper formate to form a complex. This complex may be formed by interaction of the copper cation of the copper formate with the amine groups and/or the hydroxy groups of the complexing agent, wherein the amine groups and/or the hydroxy groups of the complexing agent act as ligands. The alkanolamine may be an unbranched alkanolamine having a carbon chain length of at most six carbon atoms, in particular of at most five carbon atoms, in particular of at most four carbon atoms, in particular methanolamine, ethanolamine or amino-2-propanol, or 2-amino-2-methylpro-pan-1-ol. The diamine may be ethylenediamine, 1,2-diaminopropane or 1,3-diaminopropane. If the complexing agent has a total of two ligands, such as amino-2-propanol, 2-amino-2-methylpropan-1-ol, ethylenediamine, 1,2-diaminopropane or 1,3-diaminopropane, the complexing agent may be capable of binding the copper atom of the copper formate through two sites, namely the amine group(s) and/or the hydroxy group, so that a chelating effect may be achieved. A complexing agent that binds through two sites is classified as bidentate and the corresponding complexes tend to be relatively stable compared to complexes derived from monodentate complexing agents, in particular monoamines and alcohols, that bind through one site. The relatively high stability, called chelate effect, also affects physicochemical parameters, e.g. the boiling temperature and the decomposition temperature of the formed complex. The inventors of the present invention found that the complex formed by the complexing agent and the copper formate results in the The inventors further found that the size of the copper nanoparticles formed The inventors of the present invention further found that the copper nanoparticles formed do not oxidize during the waiting according to step e). The inventors found that the binder in the composition provides a reducing effect on the copper nanoparticles formed, thus preventing oxidation of the formed copper nanoparticles. Thus, a further agent in the sintering paste according to the invention or a protecting atmosphere for preventing oxidation of the formed copper nanoparticles does not have to be provided. Furthermore, the copper nanoparticles formed do not agglomerate during the waiting according to step e). The inventors of the present invention found that the copper nanoparticles formed are dispersed uniformly between the copper-containing microparticles of elementary metal, in particular if the copper-containing microparticles are provided as flakes, in particular flakes having an arithmetic average particle diameter of at most 5 µm. Thus, a further agent for preventing agglomeration of the formed copper nanoparticles does not have to be provided in the sintering paste according to the invention. The copper-containing microparticles, in particular the flakes, stack in a uniform stacking pattern, in particular by horizontally stacking over each other. Thus, a relatively large surface contact between these copper-containing microparticles is provided. The relatively large surface contact between the copper-containing microparticles allows sintering within a relatively short sintering time, at a relatively low sintering pressure and/or at a relatively low sintering temperature. The inventors of the present invention found that the relatively short sintering time, the relatively low sintering pressure and the relatively low sintering temperature can be further decreased if nanoconnections are provided between the stacked copper-containing microparticles, in particular between the flakes. In the sintering paste according to the invention these nanoconnections may be provided by the copper nanoparticles formed The elementary metal of the copper-containing microparticles may be copper or a copper alloy. In particular, the copper alloy may be bronze or brass. The copper alloy microparticles show good thermal conductivity in the composition according to step c), which can be further increased if the composition according step c) comprises elemental copper microparticles. The copper-containing microparticles may be provided as flakes. In particular, the flakes may have an arithmetic average particle diameter of at most 25 µm, in particular an arithmetic average particle diameter of at most 20 µm, in particular an arithmetic average particle diameter of at most 15 µm, in particular an arithmetic average particle diameter of at most 10 µm, in particular an arithmetic average particle diameter of at most 5 µm, in particular an arithmetic average particle diameter of at most 4 µm, in particular an arithmetic average particle diameter of at most 3 µm. The flakes may be obtained by grinding in a ball mill and have a lamellar or irregular shape. The inventors of the present invention found that the lamellar or irregular shape of the flakes, in particular of the flakes with an arithmetic average particle diameter of at most 5 µm, in particular an arithmetic average particle diameter of at most 4 µm, in particular an arithmetic average particle diameter of at most 3 µm, show better contact surfaces compared to spherical microparticles. The lamellar or irregular shape also results in a larger surface area of the flakes, which leads to improved densification and coarsening. This promotes the formation of sinter necks and material transport. The commercially available copper-containing microparticles, in particular the flakes, may comprise stearic acid, in particular stearic acid coated on the surface of these microparticles. Stearic acid on the surface of these microparticles prevents an agglomeration and cold welding of the copper-containing microparticles. However, due to the boiling point of 361 °C, this stearic acid on the surface of the microparticles does not evaporate during the sintering, thus resulting in a reduced sintering of the copper-containing microparticles. The inventors found that commercially available copper-containing microparticles, in particular the flakes, may be chosen such that they comprise a relatively low total weight of stearic acid in relation to the total weight of the microparticles. The total weight of stearic acid in relation to the total weight of these copper-containing microparticles may be at most 1 wt.%, in particular at most 0.5 wt.%, in particular at most 0.25 wt.%, in particular at most 0.1 wt.% and at least 0.001 wt.%, in particular at least 0.01 wt.%. The inventors of the present invention further found that such a relatively low total weight of stearic acid in relation to the total weight of these copper-containing microparticles is sufficient for preventing agglomeration and cold welding of the copper-containing microparticles without reducing sintering of these microparticles in a relevant extent. The commercially available copper-containing microparticles, in particular the flakes, may comprise oxygen. The inventors found that commercially available copper-containing microparticles, in particular the flakes, may be chosen such that the total weight of oxygen in relation to the total weight of these copper-containing microparticles is in a range of 1 wt.% to 7 wt.%, in particular in a range of 2 wt.% to 6 wt.%, in particular in a range of 3 wt.% to 5 wt.%, in particular in a range of 3.1 wt.% to 4.9 wt.%. The inventors of the present invention further found that generally a relatively low total weight of oxygen in relation to the total weight of said copper-containing microparticles reduces the oxidation of copper to copper oxide. By reducing the oxidation of copper to copper oxide, the formation of a copper oxide layer acting as a barrier of atom diffusion may be reduced. In the sintering paste according to the invention, the oxidation of copper to copper oxide is further reduced during the heating according to step d) and during the waiting according to step e). The inventors found that the binder in the composition provides a reducing effect on the copper-containing microparticles, thus preventing oxidation of the copper-containing microparticles if they are chosen such that the total weight of oxygen in relation to the total weight of these microparticles is in the above given range. In the sintering paste according to the invention, also a relatively high total weight of oxygen in relation to the total weight of said copper-containing microparticles results in a reduced oxidation of copper to copper oxide. Copper flakes and copper-alloy based flakes can be purchased as metal powders Cubrotec, Rogal® Bronze GS and Rogal® Brass GS, which are offered by the company Schlenk Metallic Pigments GmbH, Germany. The copper-containing microparticles may have superficial recesses. The superficial recesses of the copper-containing microparticles may be formed by means of etching with an acid. In particular, the acid may be hydrochloric acid or formic acid. Etching refers to the wet chemical activation of the surface of the copper-containing microparticles or copper-containing flakes resulting in surface modification to a rough surface texture. Etching of copper-containing microparticles through selective etching results in high energy free surfaces. The increased surface area leads to a higher specific surface energy A maximal superficial extension of any of the superficial recesses of the microparticles may be 1 µm, in particular 900 nm, in particular 800 nm, in particular 700 nm, in particular 600 nm, in particular 500 nm, in particular 400 nm, in particular 300 nm, in particular 200 nm, in particular 100 nm. A minimal superficial extension of any of the superficial recesses of the microparticles may be 1 nm, in particular 5 nm, in particular 10 nm. The recesses ensure a relatively large surface area of the microparticles. A relatively large surface area of the microparticles results in a relatively low total surface energy. A relatively low total surface energy of the microparticles enables a relatively high rate of sinter neck formation between the microparticles during sintering. The copper formate may be an anhydrous copper formate, in particular Cu(HCOO)2, or a hydrate of copper formate, in particular a copper formate tetrahydrate (Cu(HCOO)2*4H2O). The copper formate is considered to be anhydrous not only if it contains no water, but also if it contains only traces of water, in particular a water content of at most 5 wt.%, in particular at most 1 wt.%, in particular at most 0.5 wt.%, in particular at most 0.1 wt.%, in particular at most 0.05 wt.%, in particular at most 0.01 wt.%, in particular at most 0.005 wt.%, in particular at most 0.001 wt.%. Anhydrous copper formate can be obtained by drying it, e. g. at a temperature in the range from 85 °C to 110 °C, in particular at a temperature of 100 °C. The diol forming the binder may be a diol having an arithmetic average molar mass of at least 60 g/mol and at most 100 g/mol, in particular ethylene glycol, diethylene glycol, propylene glycol or butylene glycol. The triol forming the binder may be a triol having an arithmetic average molar mass of at least 75 g/mol and at most 100 g/mol, in particular glycerol. During the decomposition of the diol or the triol, a reducing atmosphere is created which prevents the oxidation of the copper to copper oxide without the requirement of providing an additional protective gas atmosphere to be applied from the outside. Therefore, the diol or the triol in the sintering paste according to the invention enables the The total weight of the microparticles may be at most 65 wt.%, in particular at most 60 wt.%, in particular at most 55 wt.%, in particular at most 50 wt.%, in particular at most 45 wt.%, in particular at most 40 wt.%, in particular at most 35 wt.%, of the total weight of the composition as specified in step c). The total weight of the binder may be at most 40 wt.%, in particular at most 35 wt.%, in particular at most 30 wt.%, in particular at most 25 wt.%, in particular at most 20 wt.%, of the total weight of the composition as specified in step c). The remaining part of the composition as specified in step c) may be formed by the copper formate and the complexing agent. The stoichiometric ratio between the copper formate and the complexing agent in the composition as specified in step c) may depend on the number of ligands of the complexing agent. If the complexing agent has a total of two ligands, in particular one hydroxy group and one amine group, e.g. amino-2-propanol or 2-amino-2-methyl-propan-1-ol, the complexing agent and copper formate may be present in a stochiometric ratio of 1:1, in particular in a stochiometric ratio of 2:1, in the composition as specified in step c). However, if the complexing agent has only one ligand, in particular one hydroxy group or one amine group, e.g. hexylamine, the complexing agent and the copper formate may be present in a stoichiometric ratio of 2:1. The total content of solids in the sintering paste according to the invention may be at most 70 wt.%, in particular at most 65 wt.%, in particular at most 60 wt.%. The inventors found that despite the relatively low total content of solids and the resulting relative low viscosity compared to silver sintering pastes having a total content of solids of about 90 wt.%, the sintering paste according to the invention, in particular a sintering paste having a total content of solids of at most 65 wt.%, results in relatively high shear strength value, in particular an arithmetic average shear strength value in the range from 100 MPa to 40 MPa of the sintered joints after sintering of the sintering paste according to the invention. The low viscosity of the sintering paste according to the invention enables its easy processability and a good and its even spreadability on a surface. The inventors further found that a composition as specified in step c) comprising or consisting of in particular brass flake microparticles having superficial recesses formed by means of etching, copper formate, amino-2-propanol as complexing agent complexing the copper formate and ethylene glycol as binder, results in a relatively high shear strength value of 100 MPa of the sintered joints after sintering, in particular if the total content of solids is at most 65 wt.%. The invention also concerns a method for producing the sintering paste according to the invention comprising the steps of
The method may further comprise a step f) of cooling of the sintering paste obtained in step e) to a further temperature in the range from 15 °C to 40 °C, in particular 20 °C to 30 °C. Cooling may be performed by active cooling but usually is passive cooling, i. e. by letting the sintering paste cool down to the further temperature which usually is ambient temperature. Before providing the copper formate according to step a), the copper formate, in particular copper formate tetrahydrate, may be heated to a copper formate drying temperature in the range from 85 °C to 110 °C, in particular in the range from 90 °C to 105 °C, in particular in the range from 95 °C to 100 °C. The copper formate drying temperature may be maintained for at least 10 minutes, in particular at least 20 minutes, in particular at least 30 minutes, and at most 3 hours, in particular at most 2 hours, in particular at most 1 hour. Subsequently, the copper formate may be crushed, in particular manually. The steps of copper formate heating to the copper formate drying temperature, maintaining the copper formate drying temperature and crushing the copper formate may be performed in an atmosphere containing oxygen and may be repeated at least two times, in particular at least three times, in particular at least four times, and at most six times, in particular at most five times. The atmosphere containing oxygen may be provided by means of a gas mixture containing oxygen and nitrogen, such as air. Drying of the copper formate, in particular the copper formate tetrahydrate, results in the evaporation of the water complexed in the copper formate, in particular the water complexed in the copper formate tetrahydrate. By evaporation of the water complexed in the copper formate, in particular by evaporation of the water complexed in the copper formate tetrahydrate, anhydrous copper formate can be provided. The inventors found that providing anhydrous copper formate in the method for producing the sintering paste according to the invention results in relatively weak bubble formation during sintering of this sintering paste. Mixing of the copper formate, in particular the anhydrous copper formate, and the binder in the form of the diol, in particular the ethylene glycol, or the triol results in a mixture in which the copper formate, in particular the anhydrous copper formate, is not dissolved. Only mixing the copper formate and the binder with the complexing agent complexing the copper formate, wherein the complexing agent is in particular the alkanolamine, in particular amino-2-propanol, results in a solution, in particular a solution with the binder as solvent and the complexed copper formate as solute. In this solution a complex, in particular a bidentate complex, of the copper formate and the complexing agent is formed. The following equation exemplarily shows the formation of the bidentate complex of copper formate and amino-2-propanol: The inventors of the present invention found that the copper formate complexed by the complexing agent, in particular the bidentate complex, is soluble in the binder. The mixture obtained in step b) comprises complexed copper formate solved in the binder. The mixing according to step b) may be performed as follows: Firstly, the copper formate and the binder may be mixed. Secondly, the mixture of the copper formate and the binder may be mixed with the complexing agent. By doing so, a relatively good solubility of the copper formate complexed by the complexing agent, in particular the bidentate complex, in the binder is enabled. The inventors of the present invention found that by firstly mixing the copper formate and the complexing agent before mixing the copper formate with the binder, the copper formate complexed by the complexing agent, in particular the bidentate complex, forms agglomerates of copper formate complexes. These agglomerates are relatively hard to solubilize in the binder. In the method according to the invention steps a) to f), in particular at least steps a) to e), in particular at least steps b) to e), in particular at least steps c) to e), in particular at least steps d) and e), may be performed in a reducing atmosphere. The reducing atmosphere may be provided by means of a mixture of evaporated formic acid and nitrogen gas or by means of a gas mixture of hydrogen and an inert gas. The gas mixture of hydrogen and the inert gas may be a gas mixture of nitrogen and hydrogen or a gas mixture of argon and hydrogen. The heating according to step d), the maintaining according to step d) and/or the waiting according to step e) may be performed at atmospheric pressure or at a pressure reduced vis-à-vis atmospheric pressure. The pressure reduced vis-à-vis atmospheric pressure may be a pressure in the range of 0.01 bar to atmospheric pressure, in particular in the range of 0.02 bar to 0.9 bar, in particular in the range of 0.03 bar to 0.7 bar, in particular in the range of 0.03 bar to 0.5 bar, in particular in the range of 0.03 bar to 0.3 bar, in particular in the range of 0.03 bar to 0.1 bar. The inventors of the present invention found that performing the heating according to step d), the maintaining according to step d) and/or the waiting according to step e) at the pressure reduced vis-à-vis atmospheric pressure enables the evaporation of the alkanolamine having a carbon chain length of at most six carbon atoms, in particular of at most five carbon atoms, at the temperature in the range from 120 °C to 180 °C. Heating the composition obtained in step c) to the temperature and maintaining the temperature according to steps d) and e) results in the decomposition of the complexed copper formate, the evaporation of the complexing agent, and the According to the above reaction equation, the copper formate complexed with amino-2-propanol decomposes during heating. The copper atom having the oxidation state +2 in the copper formate is reduced to a copper atom having the oxidation state 0. The formate in the copper formate is oxidized to hydrogen and carbon dioxide which are both evaporated due to their gaseous state. Furthermore, the bond between the amine group of the amino-2-propanol and the copper atom and the bond between the hydroxy group of the amino-2-propanol and the copper atom are broken resulting in the evaporation of the amino-2-propanol during heating. The inventors of the present invention found that the size of the formed copper nanoparticles is dependent on the chain length of the complexing agent and the boiling point of the complexing agent. The inventors of the present invention further found that complexation of copper formate by a long-chain complexing agent, in particular a long-chain alkanolamine, which has a higher boiling point compared to a short-chain complexing agent, in particular a short-chain alkanolamine, results in the formation of smaller nanoparticles. The copper nanoparticles formed according to the method according to the invention have an arithmetic average particle diameter of at least 100 nm, in particular at least 200 nm, in particular at least 300 nm, in particular at least 400 nm, and at most 1000 nm, in particular at most 900 nm, in particular at most 800 nm, in particular at most 700 nm. The The inventors of the present invention further found that the complex, in particular the bidentate complex, of copper formate and the complexing agent results in a relatively low thermal decomposition temperature of the complexed copper formate compared to non-complexed copper formate. Therefore, The inventors of the present invention found that during steps d) and e) according to the invention, the sintering paste according to the invention remains viscous. Viscosity may be at most 300 000 mPas, in particular at most 250 000 mPas. This is particularly surprising since at least 75 wt.%, in particular at least 80 wt.%, in particular at least 85 wt.%, in particular at least 90 wt.%, in particular at least 95 wt.%, in particular at least 99 wt.%, of the complexing agent is evaporated in step e). The inventors further found that the relatively low content of solids, in particular a content of solids of at most 65 wt.%, and the binder, in particular the diol, in particular the diol having an arithmetic average molar mass of at least 60 g/mol and at most 100 g/mol, in particular ethylene glycol, ensure the relatively low viscosity of the sintering paste according to the invention during steps d) and e). The relatively low viscosity of the sintering paste according to the invention ensures a paste-like consistency and a relatively good printability of the sintering paste according to the invention. The viscosity of the sintering paste according to the invention may be measured using a standard viscosimeter, in particular a standard classical rotational viscosimeter, in particular the Thermo Scientific™ HAAKE™ Viscotester™ C. These rotational viscometers measure the resistance of the sintering paste according to the invention against a preset speed. The resulting torque or resistance is a measure for the viscosity of the sintering paste. The higher the torque, the higher the viscosity. The sintering paste produced by the method according to the invention allows a relatively easy storage after production due to its paste-like consistency. In addition, storage of the sintering paste can take place over a relatively long period of time. Since the After the method according to the invention, in particular after step e), or, optionally, after step f), the sintering paste produced by the method according to the invention may be applied in a method for forming a copper-containing interconnection layer between two solid substrates comprising the steps of
Applying the sintering paste according to the invention to the first substrate may be performed by stencil printing, by screen printing or by cartridge dispensing. After applying the sintering paste according to the invention to the first substrate and before applying the bonding pressure to press the first substrate and the second substrate against one another, the sintering paste according to the invention may be heated to a pre-drying temperature in the range from 100 °C to 160 °C, in particular in the range from 105 °C to 155 °C, in particular in the range from 110 °C to 150 °C, in particular in the range from 115 °C to 145 °C, in particular in the range from 120 °C to 140 °C, in particular in the range from 125 °C to 135 °C. The pre-drying temperature may be maintained for at least 30 seconds, in particular at least 1 minute, in particular at least 2 minutes, in particular at least 3 minutes and for at most 6 minutes, in particular at most 5 minutes, in particular at most 4 minutes. Heating the sintering paste according to the invention to the pre-drying temperature and maintaining the pre-drying temperature may be performed in a reducing atmosphere or in an atmosphere containing oxygen. Heating the sintering paste according to the invention to the pre-drying temperature and maintaining the pre-drying temperature may be performed after step h) and before step i). The inventors of the present invention found that Cooling according to step m) may be performed by active cooling but usually is passive cooling, i. e. by letting the sintering paste cool down to the fourth temperature which usually is ambient temperature. At least steps k) and I), in particular at least steps k) to m), in particular at least steps j) to m), in particular at least steps i) to m), in particular at least steps h) to m), in particular steps g) to m), of the method for forming the copper-containing interconnection layer between two solid substrates may be performed in a reducing atmosphere. The reducing atmosphere may be provided by means of a mixture of evaporated formic acid and nitrogen gas or by means of a gas mixture of hydrogen and an inert gas. The gas mixture of hydrogen and the inert gas may be a gas mixture of nitrogen and hydrogen or a gas mixture of argon and hydrogen. The inventors of the present invention found that sintering in a reducing atmosphere, in particular sintering by means of a mixture of evaporated formic acid and nitrogen gas, results in relatively high shear strength values of the resulting copper bond. The inventors of the present invention found that at least steps k) and I), in particular at least steps k) to m), in particular at least steps j) to m), in particular at least steps i) to m), in particular at least steps h) to m), in particular steps g) to m), of the method for forming the copper-containing interconnection layer between two solid substrates may be performed in an atmosphere containing oxygen. The atmosphere containing oxygen in the method according to the invention may be provided by means of a gas mixture containing oxygen and nitrogen. The gas mixture containing oxygen and nitrogen may be air. The inventors of the present invention found that the sintering paste produced by the method according to the invention provides a relatively good conductivity of the copper bond after sintering due to relatively low oxide impurities. The oxide impurities are so low that it is not necessary to apply a reducing atmosphere during sintering. Sintering of the sintering paste produced by the method according to the invention ensures relatively high shear strength values of the resulting bonds. Despite the relatively low content of solids, the shear strength values are similar to the shear strength values achievable with commercial silver sintering pastes with a content of solids of about 90 wt.%. Due to the relatively low content of solids and since silver is relatively expensive compared to copper, material costs can be saved by using the sintering paste according to the invention. In addition, the sintering paste according to the invention enables a relatively energy-efficient production of a copper bond, since the The inventors of the present invention further found that the By forming nanoparticles The first substrate may be made of or consist of a metal or a metal oxide and the second substrate may be made of or consist of the metal, a further metal, the metal oxide, a further metal oxide or a surface mount device component. The metal or the further metal may be gold, silver, nickel, copper, pre-treated copper or tin. The metal oxide or the further metal oxide may be aluminum oxide. The surface mount device component may be a capacitor, a chip resistor, a crystal oscillator, a diode, a fuse, an inductor, an integrated circuit, an LED, a network resistor, a transformer or a transistor. The inventors of the present invention found that the binder can also reduce oxides on the first and/or the second substrate. Therefore, the sintering paste produced by the method according to the invention enables sintering on copper, silver and/or nickel substrates even if these substrates are covered by an oxide layer. The pre-treated copper may be pre-treated for example by coating a copper substrate with an organic surface protection (OSP) layer, wherein the OSP layer protects the copper against oxidation and is dissolved during the soldering process. Alternatively, other methods, e.g. sol-gel application or CVD, can be used to coat the copper substrate with a protective layer in order to protect the copper against oxidation. The invention further concerns the use of the sintering paste according to the invention for forming a copper-containing interconnection layer between two solid substrates, in particular in microelectronics packaging, in electric vehicle technologies, in hybrid electric vehicle technologies, in high power electronics packaging, and/or in thick film technology. The invention further concerns the use of the sintering paste according to the invention for die-attach bonding. The invention further concerns the use of the sintering paste according to the invention for forming a conductive path on a solid substrate. The microelectronics packaging may be WBG semiconductor packaging. The high power electronics packaging may be high power light emitting diode packaging. The inventors of the present invention found that the use of the sintering paste according to the invention for forming a copper-containing interconnection layer between two solid substrates or for forming a conductive path on a solid substrate enables a relatively low thermal load of the solid substrate(s) and any electronic component, in particular the surface mount device component as specified above, on the substrate(s) when forming the interconnection layer or conductive path. This is due to the relatively low sintering temperature required to sinter the sintering paste according to the invention. If the sintering paste according to the invention is used for forming a conductive path on a solid substrate, the solid substrate may be any substrate defined above as first or second substrate as far as it is not an electrically conductive first or second substrate. All features indicated in the specification are to be understood as features applicable to all embodiments of the invention. This means, for example, that a feature indicated for the sintering paste according to the invention can also be applied to the method for producing the sintering paste according to the invention, the method for forming a copper-containing interconnection layer between two solid substrates, and/or the use according to the invention, and vice versa. Furthermore, as far as not specified the term "average" always means "arithmetic average". As far as not specified the term "diameter" always means "Volume Equivalent Spherical Diameter" (=VESD). The particle size for determining that diameter can be determined by static light scattering, laser diffraction, microscopy, in particular optical microscopy, followed by image analysis, sedimentation analysis and by use of a disc centrifuge. The abbreviation "wt.%" means "percent by weight". The invention will be explained in more detail with reference to the following embodiments. The following compositions were tested: Table 1 shows different sintering pastes and their respective compositions. As can be seen in Table 1, the sintering pastes from compositions No. 1 to No. 7 do not contain copper formate and do not contain a complexing agent. The sintering pastes from compositions No. 8 to No. 13 refer to sintering pastes of identical composition, each prepared and tested in trials independent from each other. The same applies to the sintering pastes from compositions No. 14 to No. 20. In each of the sintering pastes from compositions No. 8 to No. 13, the total weight of the copper flakes in relation to the total weight of the composition is 64 wt.%, the total weight of the ethylene glycol in relation to the total weight of the composition is 12 wt.%, the total weight of the copper formate in relation to the total weight of the composition is 12 wt.% and the total weight of the amino-2-propanol in relation to the total weight of the composition is 12 wt.%. The total content of solids in each of the sintering pastes from compositions No. 8 to No. 13 is 68 wt.%. In each of the sintering pastes from compositions No. 14 to No. 20, the total weight of the etched brass flakes in relation to the total weight of the composition is 60 wt.%, the total weight of the ethylene glycol in relation to the total weight of the composition is 13 wt.%, the total weight of the copper formate in relation to the total weight of the composition is 13 wt.% and the total weight of the amino-2-propanol in relation to the total weight of the composition is 13 wt.%. The total content of solids in each of the sintering pastes from compositions No. 14 to No. 20 is 64 wt.%. In the following, the formulation of a sintering paste according to the invention is exemplarily shown. The formulation of the paste comprises the following steps: Equal amounts of mass of the dried and crushed copper formate and ethylene glycol are mixed resulting in a suspension of copper formate in ethylene glycol. In order to dissolve copper formate, amino-2-propanol is added in a molar ratio of 1:2 compared to copper formate (which refers to 1:1 wt.%). The copper formate is complexed by the amino-2-propanol. Since amino-2-propanol has both a hydroxy group (-OH group) and an amine group (-NH2 group), the Cu center of the copper formate is bound by amino-2-propanol through two sites. Therefore, amino-2-propanol serves as a bidentate ligand. The bidentate complexation of the copper formate by the amino-2-propanol results in a complexed copper formate which is able to be dissolved in the ethylene glycol resulting in a mixture of the components. Subsequently, copper flakes or etched brass flakes are added to the mixture in a mass ratio of 50:50. The resulting mixture is then heated to 160 °C in a reflow oven under nitrogen atmosphere and allowed to stay for 30 minutes. During the heating process, copper nanoparticles are formed by thermal decomposition of the copper formate amino-2-propanol complex. The binder ethylene glycol evaporates, but a sufficient quantity remains in order to ensure a paste like consistency, in particular at least 5 wt.%. Due to the remaining ethylene glycol, the obtained sintering paste confers a good printability and is easily cleanable from surfaces compared to traditional solder pastes. The sintering pastes from example 1 are each stencil printed on a copper substrate (30 mm × 30 mm × 1.5 mm) using a PBT-Uniprint-PMGo3v semi-automatic stencil printer equipped with a motorized double blade squeegee and a stencil thickness of 75 µm. The sintering pastes from example 2 are sintered by a two-step sintering process. First, pre-drying of the stencil printed paste in a formic acid enriched nitrogen (N2) atmosphere, in a nitrogen gas atmosphere or in air is performed depending on the respective sintering paste. The pre-drying is performed for 5 minutes to 15 minutes at 120 °C to 140 °C. Here, exemplarily two sintering paste types are compared. In the first sintering paste type, which is not a sintering paste according to the invention, After pre-drying of the sintering paste, Si or Si3N4 chips with a footprint of 2.5 mm2 and 120 µm thickness with gold end metallization are applied on the stencil printed pre-dried sintering paste using a Fineplacer® Sigma bonder with a specifically designed bonding chamber with a precision of ± 1 N of force. After chip placement, sintering for 5 minutes to 30 minutes at a sintering temperature of 250 °C to 275 °C under the application of 10 MPa to 20 MPa bonding pressure in a specifically designed open bond chamber under a nitrogen flow of 3 L/min is performed, depending on the respective sintering paste. The specifically designed open bond chamber contains residual oxygen. However, oxidation of the copper is prevented by provision of a reducing atmosphere. The sintering pastes from compositions No. 1 to No. 5 are sintered at 275 °C in order to obtain a copper bond. Sintering temperature is reached at a heating rate of 5 K/s. An initial contact force of 5 N is applied followed by a ramp up to final bonding force at the rate of 5 N/s. A 75 µm thick polyimide foil is used between the tool tip and the samples to ensure uniform pressure distribution and to avoid any damage to the chip surfaces by direct contact with the metal tool tip. After sintering, the sintering bond strength of the sintered copper bonding is measured by a shear test. The shear test is performed according to MIL-STD-883E test method standard for microcircuits using a XYZTec Condor Sigma Lite shear tester with a shear height of 25 µm and a shear speed of 200 µm/s. The results are given in the following table: In Table 2, the sintering bond strength of the sintered copper bonding is given as mean of arithmetic average shear strength values ± SD (n = 25). As can be seen in Table 2, the sintering bond strength of the sintered copper bonding from compositions No. 1 to No. 7 show arithmetic average shear strength values in the range of 24 MPa to 60 MPa. The sintering bond strength of the sintered copper bonding from compositions No. 8 to No. 13 and No. 14 to No. 20 show arithmetic average shear strength values in the range of 42 MPa to 92 MPa and in the range of 60 MPa to 101 MPa, respectively. Furthermore, the arithmetic average shear strength values of the sintered copper bonding from compositions No. 8 to No. 13 is highest for composition No. 12 and composition No. 13 showing arithmetic average shear strength values of 80 MPa and 92 MPa, respectively. In composition No. 12 and in composition No. 13, the The inventors found that 2-amino-2-methylpropan-1-ol as complexing agent also results in a copper bond with acceptable arithmetic average shear strength values, in particular if the Furthermore, the surface structure of the sintered copper bonding from compositions No. 4, No. 14 and No. 20 are analyzed by acoustic microscopy analysis using a Nordson Sonoscan D9600 scanning acoustic microscope with a 100 MHz transducer. In composition No. 4, no On the left side of On the right side of In a further example, the surface structure of a first sintering paste type and a second sintering paste type after pre-drying are analyzed by optical microscopy. As indicated above, in the first sintering paste type, The exemplary first sintering paste of the first sintering paste type consists of 60 wt.% copper flakes, 13 wt.% Cu(II) formate, 13.5 wt.% ethylene glycol and 13.5 wt.% amino-2-propanol and was pre-dried at 140 °C for 15 minutes in a formic acid enriched nitrogen atmosphere. The first sintering paste has a total content of solids of 73 wt.%. For the second sintering paste type, a second sintering paste consisting of 50 wt.% copper flakes, 16.5 wt.% Cu(II) formate, 16.75 wt.% ethylene glycol and 16.75 wt.% amino-2-propanol was pre-dried at 140 °C for 15 minutes in a formic acid enriched nitrogen atmosphere. Prior to the pre-drying, Optical microscopy imaging of the pre-dried sintering pastes is performed using a Keyence Digital microscope (top view). Side view imaging of the pre-dried sintering pastes is performed using the Fineplacer® PICO. The results are given in As can be seen in As can be seen in Furthermore, by application of a bonding force of 1000 N to the Si microchip placed on the pre-dried first or second sintering paste, the inventors found that the rough surface texture of the printed and pre-dried first sintering paste results in a non-uniform force distribution with a relatively high force variation of the bonding force applied to the microchip. A relatively high force variation of the applied bonding force on the microchip might result in the breaking of the microchip during placement and/or sintering of the microchip even if the microchip is placed by application of a relatively small placement force. In contrast to the first sintering paste, the uniform surface structure of the printed and pre-dried second sintering paste results in a uniform force distribution of the applied bonding force on the microchip, thus allowing the placement of a microchip onto the second sintering paste without breaking of the microchip. In addition, the sintered interconnect is analyzed by electron microscopy. For that, the first sintering paste, the second sintering paste and a control sintering paste are stencil printed on a copper substrate as indicated in example 3. The control sintering paste contains 65 wt.% copper flakes and 35 wt.% ethylene glycol, but no copper formate and no amino-2-propanol. After stencil printing, pre-drying of the stencil printed control sintering paste, the stencil printed first sintering paste and the stencil printed second sintering paste is performed at 140 °C for 5 minutes in a formic acid enriched nitrogen atmosphere followed by sintering at 250 °C for 5 minutes at a bonding pressure of 20 MPa in an open bond chamber under constant flow of formic acid enriched nitrogen. After sintering, cross sections of the control sintering paste interconnect, the first sintering paste interconnect and the second sintering paste interconnect are prepared using a JEOL SM-09010 Ar-lon beam miller. The cross sections of the control sintering paste interconnect, the first sintering paste interconnect and the second sintering paste interconnect are analyzed using a Zeiss EVO MA 1 scanning electron microscope (SEM). The results are given in As can be seen in In another example, after Si chip placement and sintering, the interconnect between the Si chip and the substrate was analyzed by acoustic microscopy analysis using a Nordson Sonoscan D9600 scanning acoustic microscope with a 100 MHz transducer. The results are given in As can be seen in The invention concerns a sintering paste for forming a copper-containing interconnection layer between two solid substrates, wherein the sintering paste is obtained by A sintering paste for forming a copper-containing interconnection layer between two solid substrates, wherein the sintering paste is obtained by the following steps:
a) Providing copper-containing microparticles of elementary metal, a binder, a copper formate and a complexing agent complexing the copper formate, wherein the complexing agent is an alkanolamine or a diamine, wherein the binder is a diol or a triol, b) mixing the copper formate, the binder and the complexing agent for obtaining a mixture, c) mixing the mixture obtained in step b) and the copper-containing microparticles for obtaining a composition, d) heating the composition obtained in step c) to a temperature in the range from 120 °C to 180 °C and maintaining the temperature, e) waiting until at least 75 wt.% of the complexing agent is evaporated and copper nanoparticles are formed for obtaining the sintering paste. Sintering paste according to claim 1, wherein the elementary metal forming the microparticles is copper or a copper alloy, in particular bronze or brass. Sintering paste according to claims 1 or 2, wherein the microparticles are provided as flakes, in particular flakes having an arithmetic average particle diameter of at most 5 µm. Sintering paste according to any of the preceding claims, wherein the microparticles have superficial recesses, in particular recesses formed by means of etching with an acid. Sintering paste according to claim 4, wherein a maximal superficial extension of any of the recesses is 1 µm. Sintering paste according to any of the preceding claims, wherein the copper formate is Cu(HCOO)2, in particular anhydrous Cu(HCOO)2. Sintering paste according to any of the preceding claims, wherein the alkanolamine forming the complexing agent is an unbranched alkanolamine having a carbon chain length of at most six carbon atoms, in particular methanolamine, ethanolamine or amino-2-propanol, or 2-amino-2-methylpropan-1-ol, or wherein the diamine forming the complexing agent is ethylenediamine, 1,2-diaminopropane or 1,3-diaminopropane. Sintering paste according to any of the preceding claims, wherein the diol forming the binder is a diol having an arithmetic average molar mass of at least 60 g/mol and most 100 g/mol, in particular ethylene glycol, diethylene glycol, propylene glycol or butylene glycol, and wherein the triol forming the binder is a triol having an arithmetic average molar mass of at least 75 g/mol and at most 100 g/mol, in particular glycerol. Sintering paste according to any of the preceding claims, wherein the total weight of the microparticles is at most 50 wt.%, in particular at most 35 wt.%, of the total weight of the composition as specified in step c), wherein the total weight of the binder is at most 40 wt.%, in particular at most 25 wt.%, of the total weight of the composition as specified in step c), wherein the remaining part of the composition as specified in step c) is formed by the copper formate and the complexing agent. A method for producing the sintering paste according to any of the preceding claims comprising the steps of
a) providing the copper-containing microparticles of elementary metal as specified in any of claims 1 to 5, the copper formate of claim 1 or the copper formate as specified in claim 6, the complexing agent as specified in claim 1 or 7 and the binder as specified in claim 1 or 8, b) mixing the copper formate, the binder and the complexing agent for obtaining a mixture, c) mixing the mixture obtained in step b) and the copper-containing microparticles for obtaining a composition, d) heating the composition obtained in step c) to a temperature in the range from 120 °C to 180 °C and maintaining the temperature, e) waiting until at least 75 wt.% of the complexing agent is evaporated and copper nanoparticles are formed for obtaining the sintering paste. Method according to claim 10, wherein the temperature is a temperature in the range from 130 °C to 170 °C, in particular a temperature in the range from 140 °C to 160 °C, and/or wherein the temperature is maintained for at least 5 minutes, in particular at least 10 minutes, and for at most 30 minutes, in particular at most 25 minutes. Method according to claim 10 or 11, wherein the method further comprises a step f) of cooling of the sintering paste obtained in step e) to a further temperature in the range from 15 °C to 40 °C. Method according to any of claims 10 to 12, wherein at least steps d) and e) and optionally step f) are performed in a reducing atmosphere. Method according to claim 13, wherein the reducing atmosphere is provided by means of a mixture of evaporated formic-acid and nitrogen gas or by means of a gas mixture of hydrogen and an inert gas, in particular a gas mixture of nitrogen and hydrogen or a gas mixture of argon and hydrogen. Use of the sintering paste according to any of claims 1 to 9 for forming a copper-containing interconnection layer between two solid substrates, for die-attach bonding or for forming a conductive path on a solid substrate.Example 1: Compositions
1 Copper flakes Octanol - 75 25 - 75 2 Copper flakes Butanol - 75 25 - 75 3 Copper flakes Ethylene glycol - 63 37 - 63 4 Etched brass flakes Ethylene glycol - 57 43 - 57 5 Etched brass flakes Polyehtylene glycol 600 - 63 37 - 63 6 Etched brass flakes alpha-terpineol + Polyethylene glycol 600 - 65 35 - 65 7 Copper flakes alpha-terpineol + Polyethylene glycol 600 - 78 22 - 78 8-13 Copper flakes Ethylene glycol Copper formate + Amino-2-propanol 64 12 12:12 68 14-20 Etched brass flakes Ethylene glycol Copper formate + Amino-2-propanol 60 13 13:13 64 Example 2: Sintering paste production
Copper formate tetrahydrate is dried in air at 100 °C for 30 minutes and crushed manually. This procedure is repeated two times. By drying the copper formate, the water complexed with the copper formate molecules are removed and crushed anhydrous copper formate crystals can be obtained.Example 3: Sinter process and sintering bond strength
1 Copper flakes Octanol - 24 ± 15 - formic acid enriched N2 (< 100 ppm O2, < 5 wt.% formic acid) 10 120 formic acid enriched N2 in open bond chamber (< 100 ppm O2, < 5 wt.% formic acid) 5 250 20 2 Copper flakes Butanol - 28 ± 22 - formic acid enriched N2 (< 100 ppm O2, < 5 wt.% formic acid) 10 120 formic acid enriched N2 in open bond chamber (< 100 ppm O2, < 5 wt.% formic acid) 5 250 20 3 Copper flakes Ethylene glycol - 27 ± 15 - N2 5 120 N2 in open bond chamber (> 100 ppm O2) 5 275 10 4 Etched brass flakes Ethylene glycol - 55 ± 6 - N2 5 120 N2 in open bond chamber (> 100 ppm O2) 5 275 10 5 Etched brass flakes Po-lyehty-lene glycol 600 - 57 ± 2 - air 5 120 N2 in open bond chamber (> 100 ppm O2) 30 275 10 6 Etched brass flakaes alpha-terpineol + PEG600 - 60 ± 6 - air 5 120 N2 in open bond chamber (> 100 ppm O2) 5 275 10 7 Copper flakes alpha-terpineol + PEG600 - 50 ± 7 - air 5 120 N2 in open bond chamber (> 100 ppm O2) 5 275 20 8 Copper flakes Ethylene glycol Copper formate + Amino-2-propanol 42 ± 19 During the pre-drying step formic acid enriched N2 (< 100 ppm O2, < 5 wt.% formic acid) 15 140 formic acid enriched N2 in open bond chamber (< 100 ppm O2, < 5 wt.% formic acid) 5 250 20 9 Copper flakes Ethylene glycol Copper formate + Amino-2-propanol 49 ± 27 During the pre-drying step formic acid enriched N2 (< 100 ppm O2, < 5 wt.% formic acid) 15 140 formic acid enriched N2 in open bond chamber (< 100 ppm O2, < 5 wt.% formic acid) 5 250 20 10 Copper flakes Ethylene glycol Copper formate + Amino-2-propanol 59 ± 27 During the pre-drying step formic acid enriched N2 (< 100 ppm O2, < 5 wt.% formic acid) 15 140 formic acid enriched N2 in open bond chamber (< 100 ppm O2, < 5 wt.% formic acid) 5 250 20 11 Copper flakes Ethylene glycol Copper formate + Amino-2-propanol 73 (only one measurement. No std.dev. Available) During the pre-drying step formic acid enriched N2 (< 100ppm O2, < 5 wt.% formic acid) 15 140 formic acid enriched N2 in open bond chamber (< 100 ppm O2, < 5 wt.% formic acid) 5 250 20 12 Copper flakes Ethylene glycol Copper formate + Amino-2-propanol 80 ± 6 Prior to the pre-drying step formic acid enriched N2 (< 100 ppm O2, < 5 wt.% formic acid) 15 140 formic acid enriched N2 in open bond chamber (< 100 ppm 02, < 5 wt.% formic acid) 5 250 20 13 Copper flakes Ethylene glycol Copper formate + Amino-2-propanol 92 ± 15 Prior to the pre-drying step formic acid enriched N2 (< 100 ppm O2, < 5 wt.% formic acid) 15 140 formic acid enriched N2 in open bond chamber (< 100 ppm 02, < 5 wt.% formic acid) 5 250 20 14 Etched brass flakes Ethylene glycol Copper formate + Amino-2-propanol 82 ± 28 During the pre-drying step formic acid enriched N2 (< 100 ppm O2, < 5 wt.% formic acid) 15 140 formic acid enriched N2 in open bond chamber (< 100 ppm 02, < 5 wt.% formic acid) 5 250 20 15 Etched brass flakes Ethylene glycol Copper formate + Amino-2-propanol 66 ± 9 During the pre-drying step formic acid enriched N2 (< 100 ppm O2, < 5 wt.% formic acid) 15 140 formic acid enriched N2 in open bond chamber (< 100 ppm 02, < 5 wt.% formic acid) 5 250 20 16 Etched brass flakes Ethylene glycol Copper formate + Amino-2-propanol 60 ± 9 During the pre-drying step formic acid enriched N2 (< 100 ppm O2, < 5 wt.% formic acid) 15 140 formic acid enriched N2 in open bond chamber (< 100 ppm 02, < 5 wt.% formic acid) 5 250 20 17 Etched brass flakes Ethylene glycol Copper formate + Amino-2-propanol 65 ± 33 During the pre-drying step formic acid enriched N2 (< 100 ppm O2, < 5 wt.% formic acid) 15 140 formic acid enriched N2 in open bond chamber (< 100 ppm 02, < 5 wt.% formic acid) 5 250 20 18 Etched brass flakes Ethylene glycol Copper formate + Amino-2-propanol 101 ± 25 During the pre-drying step formic acid enriched N2 (< 100 ppm O2, < 5 wt.% formic acid) 15 140 formic acid enriched N2 in open bond chamber (< 100 ppm 02, < 5 wt.% formic acid) 5 250 20 19 Etched brass flakes Ethylene glycol Copper formate + Amino-2-propanol 84 ± 28 During the pre-drying step formic acid enriched N2 (< 100 ppm O2, < 5 wt.% formic acid) 15 140 formic acid enriched N2 in open bond chamber (< 100 ppm 02, < 5 wt.% formic acid) 5 250 20 20 Etched brass flakes Ethylene glycol Copper formate + Amino-2-propanol 95 ± 12 Prior to the pre-drying step formic acid enriched N2 (< 100 ppm 02, < 5 wt.% formic acid) 15 140 formic acid enriched N2 in open bond chamber (< 100 ppm 02, < 5 wt.% formic acid) 5 250 20 Example 4: Surface structure
Example 5: Interconnect analysis
a) providing copper-containing microparticles of elementary metal, a binder, a copper formate and a complexing agent complexing the copper formate, wherein the complexing agent is an alkanolamine or a diamine, wherein the binder is a diol or a triol,
b) mixing the copper formate, the binder and the complexing agent for obtaining a mixture,
c) mixing the mixture obtained in step b) and the copper-containing microparticles for obtaining a composition,
d) heating the composition obtained in step c) to a temperature in the range from 120 °C to 180 °C and maintaining the temperature,
e) waiting until at least 75 wt.% of the complexing agent is evaporated and copper nanoparticles are formed for obtaining the sintering paste.

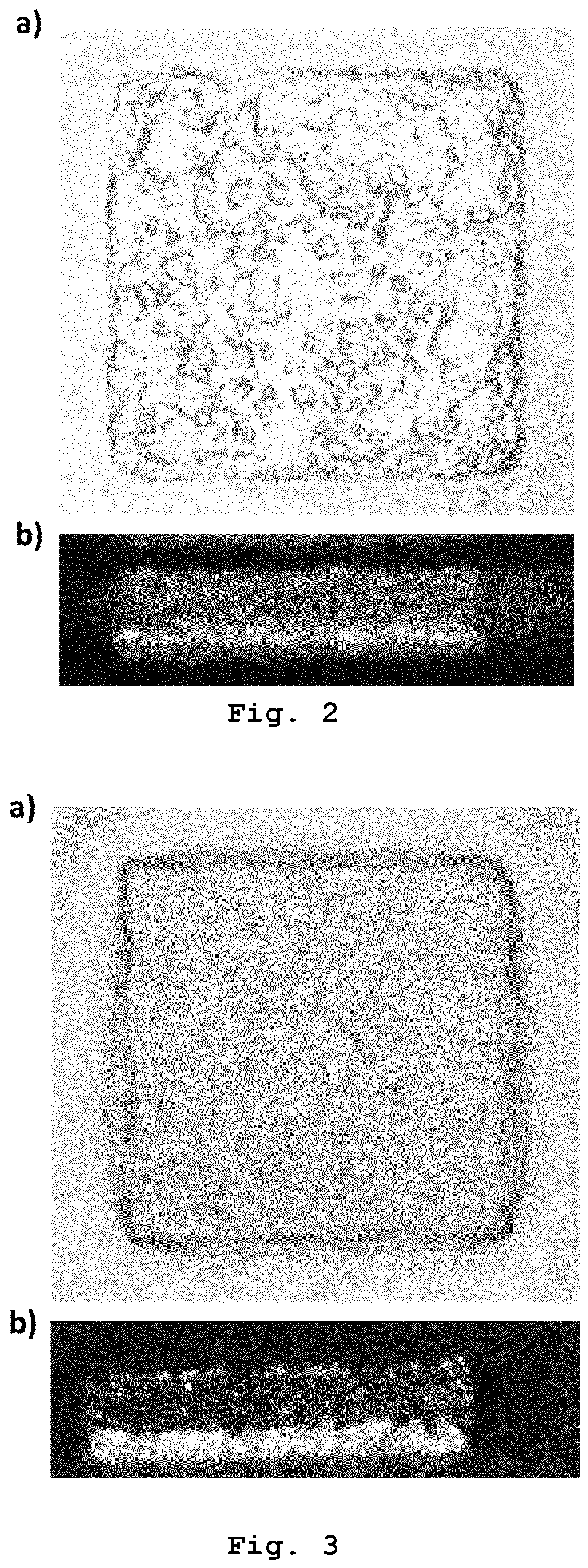
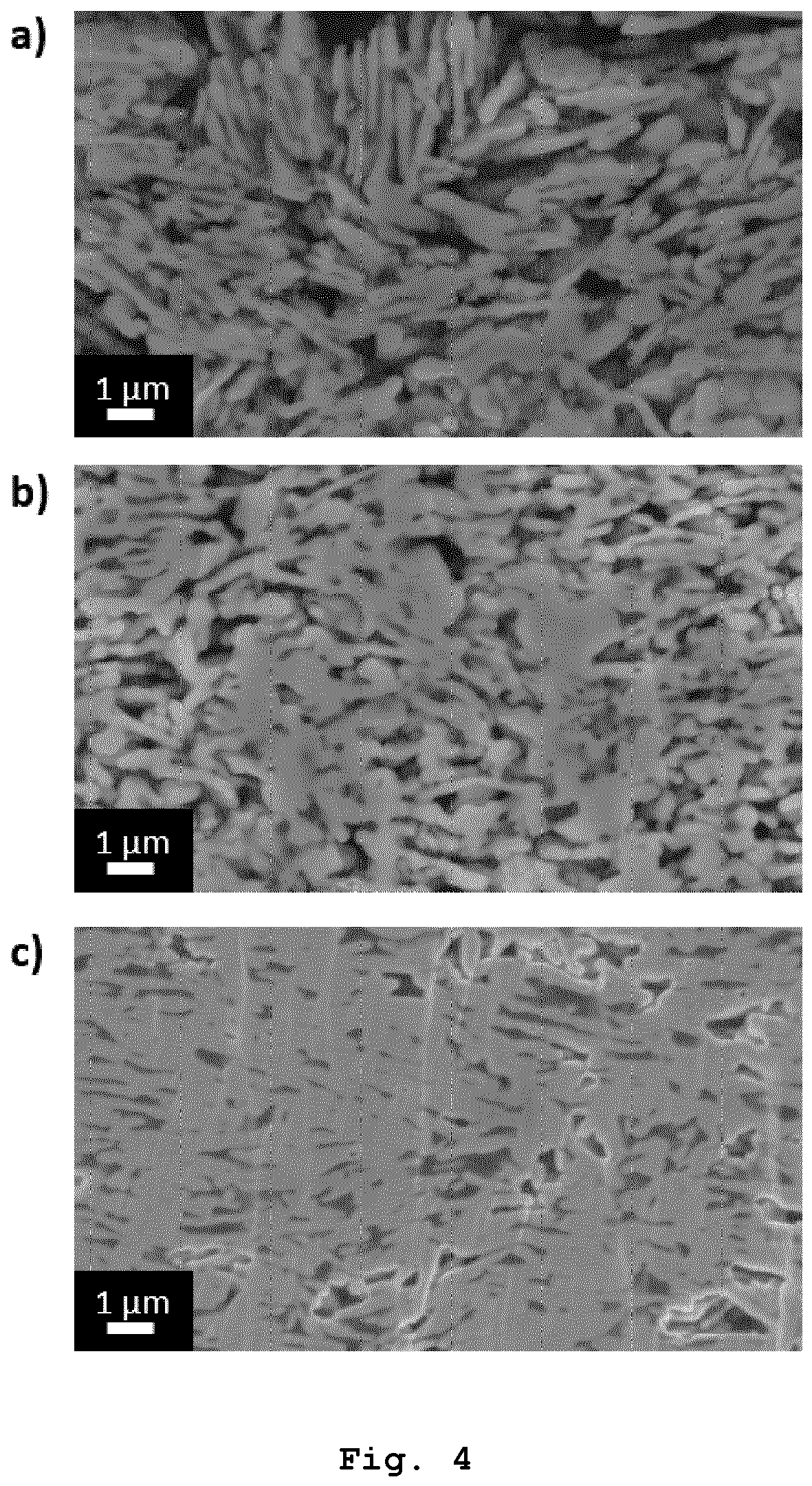
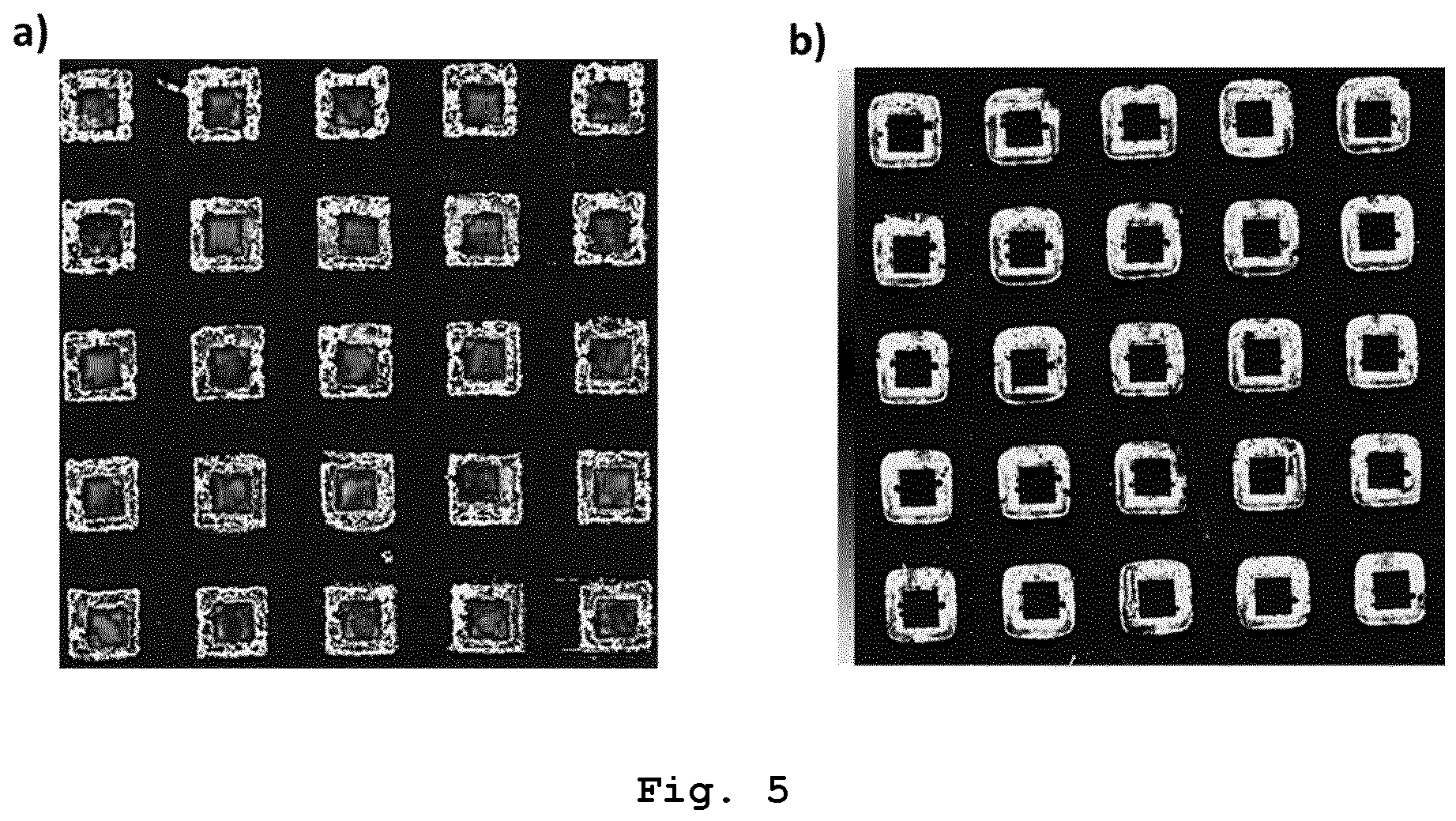