METHOD FOR PRODUCING CHARCOAL
The invention relates to a process for the production of charcoal, as well as to charcoal obtainable by this process. Charcoal is produced by heating wood through pyrolytic decomposition and essentially in the absence of air. In known processes according to the prior art, the wood is first heated and dried and subsequently subjected to pyrolytic decomposition at higher temperatures so that gaseous and liquid components of the wood are gasified and charcoal remains as a residue at the end of the pyrolysis process. The carbon content in the finished charcoal varies depending on the quality of the biomass used. For charcoal of a particularly high quality and with a high carbon content, slowly growing tropical woods currently have to be used in some cases. A high carbon content can only be achieved by charring pure wood, whereby a carbon content of up to 80% by weight is achievable in the finished charcoal with energy-intensive charring methods. If bark or periderm is also present during the charring, the carbon content in the finished charcoal drops significantly. Furthermore, charcoal produced according to known processes has pieces of different sizes with a diameter ranging from fractions of a millimetre to several centimetres. Such a size distribution is unsuitable for numerous areas of application. Quite a few areas of application require small particles with a homogeneous size distribution. Methods with multi-stage gasification processes for generating thermal energy from biomass are disclosed, for example, in EP 2 479 244 A2 and US 2010/095592 A1. In those documents, biomass is converted into combustible gas in a three-stage gasification process which comprises a pyrolysis unit, an oxidation unit and a reduction unit. In doing so, coke or, respectively, ash can be removed from the process as a by-product. However, the coke removed in this way has significant disadvantages in terms of absence of pollutants, particle size and also carbon content. It is therefore the object of the present invention to provide a process for the production of charcoal with a very high carbon content and a very low pollutant content, in which low-quality biomass can be used. In addition, the finished charcoal should have a homogeneous size distribution in the sub mm range. This object is achieved by a process for the production of charcoal comprising the steps of: a) feeding biomass, in particular wood chips, into a pyrolysis unit, in which the wood chips are pyrolyzed into a full stream comprising solid, liquid and gaseous material,
In doing so, in step c), a stable fluidized fixed bed is formed from the coke of the partially oxidized full stream. This means that the coke bed “floats” in the reduction unit on the pyrolysis gas stream, since the weight forces of the fixed bed are almost in equilibrium with the forces of the rising pyrolysis gas stream. As a result, there are only minor pressure losses in the coke bed and an efficient conversion of pollutants, also due to the long retention time of the pyrolysis gas. Using such a process, charcoal can be produced with the mean particle size d50ranging from 30 to 300 μm, preferably from 40 to 250 μm and particularly preferably from 50 to 100 μm. It has surprisingly been found that, by means of this process, wood chips, which constitute the lowest-quality waste in the timber production industry, can be processed into high-quality charcoal with a homogeneous particle size. In a preferred embodiment variant, the gaseous components are separated in the hot gas filter with the aid of porous ceramics at a temperature of 250 to 600° C. By using the hot gas filter, the pollutants formed during the thermochemical process, such as, for example, polycyclic aromatic hydrocarbons (PAH), are prevented from condensing on the charcoal. Due to the absence of pollutants, the pure charcoal produced in this way thus complies with various certificates and regulations. In a further embodiment variant, the charcoal can have a mass percentage of water ranging from 20 to 50%, preferably from 25 to 40% and particularly preferably from 28 to 35%. Furthermore, the charcoal can have an inner surface area of 200 to 400 m2/g. The charcoal produced in this way can be processed further in various processes. In one aspect of the invention, a process for the production of barbecue charcoal briquettes is therefore provided, which is characterized in that charcoal is provided according to a process according to claim 1, comprising the following steps of
In this case, the time required for pre-compression can be compensated for by more power, i.e., by increasing the speed of the rollers. In addition, the drying temperature can be minimized with a higher fan power. The binders can be from the group of preferably recycled vegetable oils or, respectively, fats, starches such as, e.g., rye or corn, sugar solutions such as beet or sugar cane molasses and cellulose compounds and can have a mass percentage of 0.5 to 20%, preferably of 1 to 15% and particularly preferably of 2 to 10%, based on the dry matter of the charcoal briquettes. The additives can be selected from the group of calcium compounds, aluminas, gum arabic and clay minerals and can have a mass percentage of 0 to 10%, preferably of 0.5 to 8% and particularly preferably of 1 to 5%, based on the dry matter of the charcoal briquettes. In principle, additives are optionally added in order to improve specific properties of the barbecue charcoal, such as, for example, ignition behaviour and strength. In one aspect, the invention relates to a process for the production of activated charcoal, characterized in that charcoal is provided according to a process according to claim 1, comprising the following steps of
The charcoal according to the invention offers the advantage over fossil coal, which usually is used for activation, that it has an inner surface area of approx. 200-400 m2/g even before activation. In contrast, fossil coal has no significant inner surface area. After activation, the charcoal preferably has an inner surface area of approx. 1000 m2/g. The second essential parameter of activated coal is the pore size, with a distinction being made between micro-, meso- and macropores. The activated charcoal according to the invention can be adjusted specifically to its application in its pore structure. For example, activated charcoals can be produced with a preferably micro- or preferably meso- or preferably macrostructure. During finishing, the activated charcoal is preferably brought into other forms such as granules or pellets, wherein it can also be used, for example, as powdered activated charcoal. In a further aspect, the invention relates to a process for the production of industrial charcoal, in particular an aggregate for concrete or a secondary raw material for the metal-working industry, characterized in that charcoal is provided according to a process according to claim 1, comprising the following steps of
During finishing, compacts and agglomerates such as, for example, briquettes, pellets and granules can be produced from the charcoal. During finishing, the charcoal can be impregnated with preferably mineral substances such as, for example, potassium, sodium and calcium salts. In the filling plant, packages can be selected from the group of kraft papers, cardboards, cloth bags and plastic packages. One aspect of the invention relates to a process for the production of an insulating material, wherein charcoal is produced according to a previously mentioned process and is mixed with a raw material for insulating materials. Subsequently, this mixture is processed into the insulating material. Typical raw materials for insulating materials are plastics such as polystyrene, polyurethane, formica, or other materials known from the insulation industry such as wood wool, for example. Those materials are processed as known (e.g., foamed), with the charcoal being added before the final processing. Such a procedure leads to lighter insulating materials and possibly also to improved mechanical stability and may involve enhanced fire protection properties. Further advantages and details of the invention are explained below by way of the figures and the descriptions of the figures. The fluidized bed technology describes a new method in the thermochemical gasification of biomass. The fluidized bed reactor describes a unique reactor design and the operation thereof. The process is depicted in Comparable gasification concepts display clear disadvantages in terms of the possibility of scaling them. Furthermore, fluidized bed gasification, for example, is associated with problems with regard to the tar concentrations in the product gas, and fixed bed systems are associated with problems due to the compression of the fuel and the exchange between solid and gaseous phases. The concept of the floating fixed bed reactor consists in constructing a structured bed of fuel that floats on the inlet gas stream of the pyrolysis and oxidation. Without uncontrolled particle movement in the reduction zone and only a relative movement of the fuel particles within the fluidized bed, comparatively long gas residence times can be achieved, which leads to low tar concentrations in the product gas. Such low tar concentrations and the unique operating control of a fluidized bed reactor lead to a very high-quality and “pure” charcoal which is discharged from the process as a by-product. Meanwhile, the technology has demonstrated that it avoids the problems of comparable gasification technologies via more than 100,000 operating hours in commercial plants. As illustrated in Furthermore, the present invention relates to a processing and a refinement of the unique charcoal, which arises in the fluidized bed gasification process. Special features of the charcoal resulting from the above-described process are as follows:
Such charcoal with the composition as indicated above and a carbon content of up to 95% by weight of the dry matter can otherwise be produced only in a pure pyrolysis process. This is mainly due to the fact that, in a subsequent gasification process, the charcoal must continue to lose energy, which is converted into gas. However, the efficiency of the fluidized bed gasification process enables the production of the charcoal of very high quality. A processing according to the invention of said charcoal is a process for the production of high-quality barbecue charcoal briquettes. The processing takes place according to the process illustrated in As shown in Further processing of the charcoal according to the invention is enabled by a process for the production of high-quality activated charcoal and finished activated charcoal. This process provides an ecological option for producing activated carbon, which is produced largely (around 80% of the activated carbon produced worldwide) from fossil coal. The remaining portion of activated carbon is mostly made of coconut shells. Charcoal is processed into activated carbon, if at all, only as a charcoal made from hardwood, the hardwood usually being tropical woods. In addition to the ecological aspect, the charcoal according to the invention has an inner surface area of approx. 200-400 m2/g even before activation, while fossil coal displays no activity whatsoever. The processing into activated charcoal takes place according to the process illustrated in The charcoal according to the invention activated in this way then has an inner surface area of approx. 1000 m2/g, with highly activated laboratory activated charcoal with an inner surface area of up to 2000 m2/g being producible. The inner surface area of the activated charcoal is measured and evaluated using the BET (Brunauer-Emmert-Teller) method. The second essential parameter for the classification of activated carbon is the pore size, with a distinction being made between micro-, meso- and macropores. The activated charcoal according to the invention can be adjusted specifically to its application in its pore structure. For example, activated charcoals can be produced with a preferably micro- or preferably meso- or preferably macrostructure. The pore volume is measured using a process of nitrogen adsorption at approx. 71 K, wherein the evaluation of the process can be performed based on the BJH (Barrett, Joyner and Halenda) method. Further processing of the charcoal according to the invention results from a process for the production of an aggregate for the construction industry. The processing takes place according to the process illustrated in On the one hand, the use of charcoal as an aggregate in concrete enables lighter concrete components due to the lower density of charcoal, and, on the other hand, the charcoal within the concrete provides an insulation based on the decreasing thermal conductivity, which entails major advantages also in terms of fire protection. For the use of charcoal as an aggregate and in the metal-working industry, the manufacture and processing thereof is extremely relevant, since charcoal, unlike activated charcoal, should be highly unreactive. Therefore, most of the coal used in this field is fossil. Hence, the charcoal according to the invention offers an ecological alternative to the fossil coal used. A process for the production of charcoal comprising the steps of: a) feeding biomass, in particular wood chips, into a pyrolysis unit, in which the wood chips are pyrolyzed into a full stream comprising solid, liquid and gaseous material, b) feeding the full stream and a gasifying agent into an oxidation unit, wherein the full stream is oxidized at least partially and transported pneumatically, c) feeding the partially oxidized full stream from the oxidation unit into a reduction unit arranged essentially vertically, the material outlet of the oxidation unit being connected to the reduction unit, with the cross-section of the reduction unit increasing as the distance from the material outlet of the oxidation unit increases, the flow rate of the full stream in the reduction unit being adapted to the material of the full stream and to the shape of the flow cross-section of the reduction unit in such a way that a stable fixed bed kept in suspension is formed in the reduction unit, d) removing the raw charcoal from the reduction unit via an overflow, e) separating gaseous components in a hot gas filter and collecting the charcoal, and f) quenching the collected charcoal with water. 1. A process for the production of charcoal comprising the steps of:
a) feeding biomass, in particular wood chips, into a pyrolysis unit, in which the wood chips are pyrolyzed into a full stream comprising solid, liquid and gaseous material, b) feeding the full stream and a gasifying agent into an oxidation unit, wherein the full stream is oxidized at least partially and transported pneumatically, c) feeding the partially oxidized full stream from the oxidation unit into a reduction unit arranged essentially vertically, the material outlet of the oxidation unit being connected to the reduction unit, with the cross-section of the reduction unit increasing as the distance from the material outlet of the oxidation unit increases, the flow rate of the full stream in the reduction unit being adapted to the material of the full stream and to the shape of the flow cross-section of the reduction unit in such a way that a stable fixed bed kept in suspension is formed in the reduction unit, d) removing the raw charcoal from the reduction unit via an overflow, e) separating gaseous components in a hot gas filter and collecting the charcoal, and f) quenching the collected charcoal with water, the charcoal having
a dry matter content of carbon ranging from 68 to 95%, a dry matter content of ash ranging from 4 to 18%, a mass percentage of water ranging from 5 to 50%. 2. A process for the production of charcoal according to 3. A process for the production of charcoal according to 4. A process for the production of barbecue charcoal briquettes, comprising obtaining charcoal produced according to a process according to charging the charcoal into the briquetting line, with a homogenization of the charcoal occurring in the charging system, mixing the homogenized charcoal with binders and preferably additives in the mixing apparatus, pre-compressing the charcoal/binder/additive mixture by means of rollers for 1 to 30 minutes, in the pre-compressor, briquetting the pre-compressed charcoal/binder/additive mixture in the hydraulic roller briquetting plant, the mixture being guided over at least two rollers with shaping cavities at a contact pressure of 1 to 12 bar, drying the charcoal briquettes at a drying temperature of 50 to 140° C., in a convection dryer, packaging the dry charcoal briquettes in a filling plant. 5. A process according to 6. A process according to 7. A process for the production of activated charcoal, comprising obtaining charcoal produced according to a process according to charging the charcoal into the activation unit, with a homogenization of the charcoal being performed in the charging system, activating the homogenized charcoal in the activation unit with an activating agent, at a temperature of 600 to 1100° C., for 5 to 180 minutes, wherein the conversion of the activating agent per 1 g of charcoal is chosen to be 0.1 to 2 g, finishing the activated charcoal, packaging the finished activated charcoal in the filling plant. 8. A process for the production of industrial charcoal, in particular an aggregate for concrete or a secondary raw material for the metal-working industry, comprising obtaining charcoal produced according to a process according to charging the charcoal into the processing unit, dividing the charcoal in the classifying unit, wherein, depending on the particle size, it is divided into a coarse, a middle and a fine fraction, the coarse fraction having a particle size of 0.4 to 10 mm, the middle fraction having a particle size of 100 to 400 μm, the fine fraction having a particle size of 0 to 100 μm, processing the divided charcoal depending on the fraction to form a compact or a finer material in the compacting or, respectively, grinding unit, wherein, after the grinding process, the finer charcoal is again fed into the classifying unit and divided, finishing the compacted industrial charcoal, packaging the finished industrial charcoal in the filling plant. 9. A process according to 10. A process according to 11. A process according to 12. A process for the production of an insulating material, comprising obtaining charcoal produced according to a process according to 13. A process for the production of charcoal according to 14. A process for the production of charcoal according to a dry matter content of carbon ranging from 75 to 93%, or from 80 to 92%, a dry matter content of ash ranging from 5 to 13%, or from 6 to 10%, and a mass percentage of water ranging from 10 to 40%, or from 15 to 35%. 15. A process according to pre-compressing the charcoal/binder/additive mixture by means of rollers for 2 to 20 minutes, or for 3 to 10 minutes, in the pre-compressor, briquetting the pre-compressed charcoal/binder/additive mixture in the hydraulic roller briquetting plant, the mixture being guided over at least two rollers with shaping cavities at a contact pressure of 1.5 to 9 bar, or a contact pressure of 2 to 7 bar, drying the charcoal briquettes at a drying temperature of 65 to 110° C., or 75 to 105° C., in a convection dryer. 16. A process according to 17. A process according to 18. A process according to 19. A process according to 20. A process according to BACKGROUND OF THE INVENTION
BRIEF DESCRIPTION OF THE INVENTION
b) feeding the full stream and a gasifying agent into an oxidation unit, wherein the full stream is oxidized at least partially and transported pneumatically,
c) feeding the partially oxidized full stream from the oxidation unit into a reduction unit arranged essentially vertically, the material outlet of the oxidation unit being connected to the reduction unit, with the cross-section of the reduction unit increasing as the distance from the material outlet of the oxidation unit increases, the flow rate of the full stream in the reduction unit being adapted to the material of the full stream and to the shape of the flow cross-section of the reduction unit in such a way that a stable fixed bed kept in suspension is formed in the reduction unit,
d) removing the raw charcoal from the reduction unit via an overflow, and
e) separating gaseous components in a hot gas filter and collecting the charcoal,
f) quenching the collected charcoal with water, the charcoal having
DETAILED DESCRIPTION OF THE INVENTION
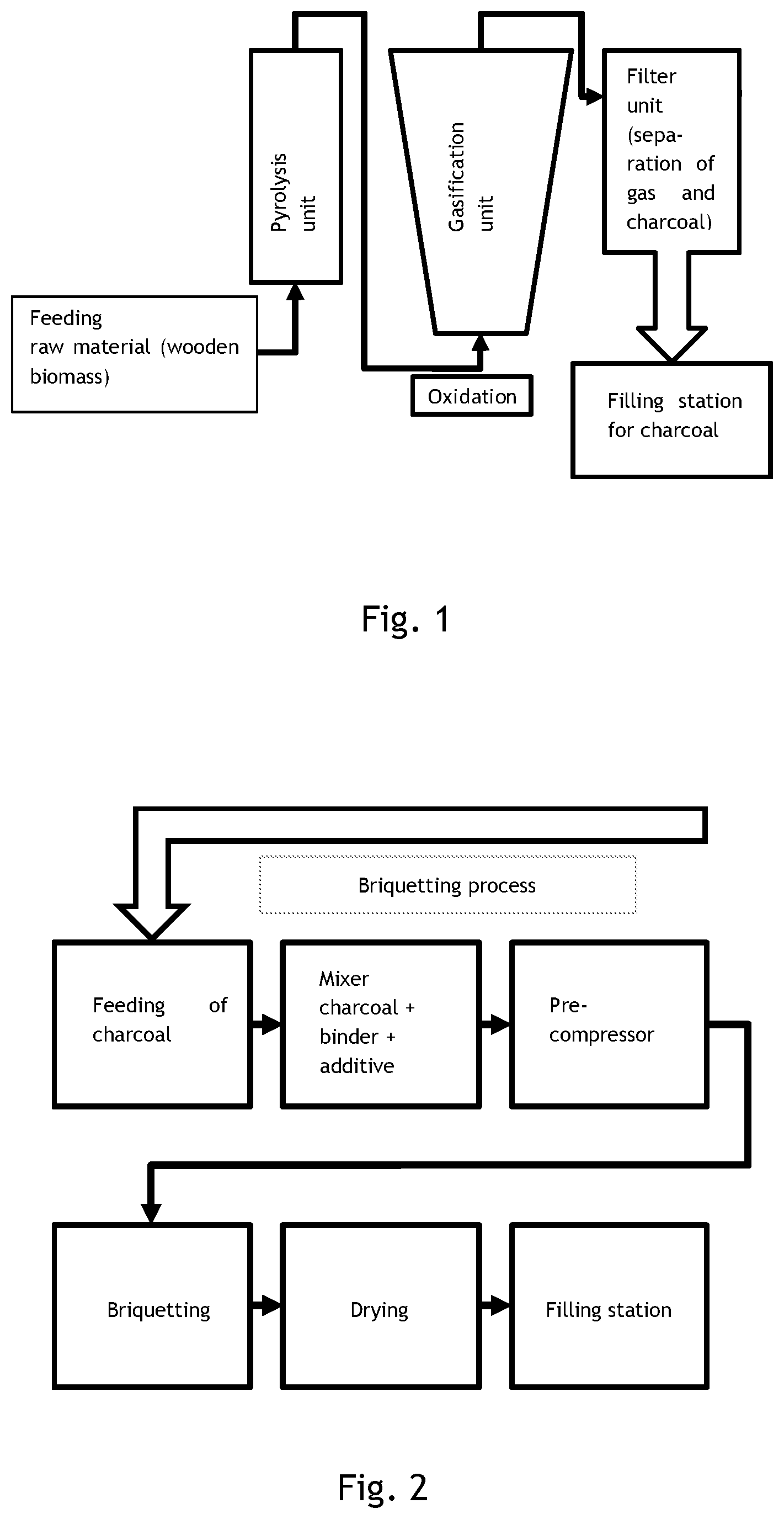
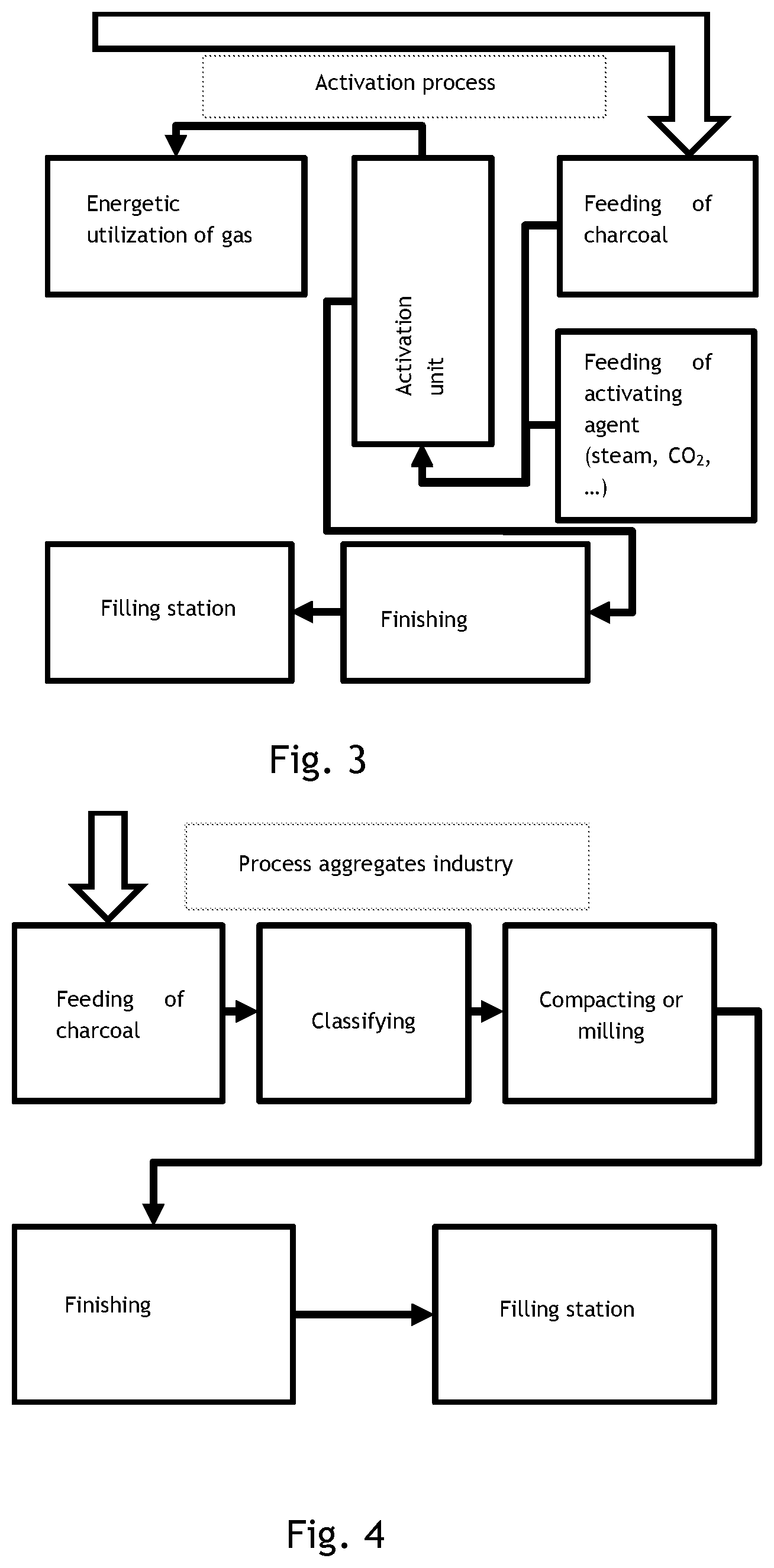