METHOD FOR PRODUCING GLASS SUBSTRATE, AND PLATE-LIKE GLASS
本発明は、ガラス基板の製造方法及びガラス基板の製造方法に供される板状のガラスに関する。
従来、例えば、LSI(Large-Scale Integration)の実装技術として、非特許文献1に記載されているように、シリコン貫通電極(TSV:Through Silicon Via)を用いた実装技術が知られている。貫通電極を有するシリコン基板は、例えば、インターポーザとして広く用いられている。インターポーザは、配線のデザインルールがそれぞれ異なる、IC(Integrated Circuit)及びプリント基板のように、端子間距離が異なる基板同士を中継する基板である。
TSV技術は、シリコン基板が高価であることに加え、シリコンが半導体であることに起因してシリコン基板に貫通孔を形成する前に絶縁処理を行う必要があるので、コストが高いという問題を有する。そこで、例えば、インターポーザの製造コストを低減するために、安価なガラスにガラス貫通電極(TGV:Through Glass Via)を形成したガラス基板が注目されている。
TGV技術においては、ガラス基板に貫通孔を形成する必要がある。ガラス基板に貫通孔を形成する技術としては、例えば、特許文献1に記載されているように、パルス発振YAGレーザーの照射によって貫通穴を形成する技術が知られている。また、特許文献2には、感光性ガラス基板に微細な穴を形成する方法が記載されている。特許文献2に記載の方法では、感光性ガラス基板上の所定の位置にフォトマスクを配置し、紫外線を照射し、潜像が形成される。次に、感光性ガラス基板を加熱処理して潜像を結晶化させる。次に、潜像が形成された部分の中央に潜像より小さい加工先穴をレーザー光により形成する。次に、フッ酸によりエッチングする。これにより、結晶化された部分が選択的にエッチングされて穴が形成される。特許文献3には、板ガラスの両面から相対向した同一軸心上の上下一対のコアドリルにより板ガラスに穿孔する方法が記載されている。
貫通孔が形成されたガラス基板は、機械的強度が低く加工の際に取り扱いにくいという問題を有する。
そこで、本発明は、貫通孔を形成しつつ、高い機械的強度を有するガラス基板を製造する方法を提供することを目的とする。
本発明は、
また、本発明は、
本発明によれば、貫通孔が形成された板状のガラスの一方の主面に樹脂層が形成されるので、製造されたガラス基板が高い機械的強度を有する。このため、本発明に係る方法によって製造されたガラス基板は、加工の際に取扱いやすい。
以下、本発明の実施形態について図面を参照しながら説明する。なお、以下の説明は、本発明の一例に関するものであり、本発明はこれらによって限定されるものではない。
<第1実施形態>
工程(I)のために準備される板状のガラス10の、波長λ1の光の透過率は、1%以下である。板状のガラス10の、波長λ1の光の透過率は小さいほど好ましい。また、板状のガラス10は、工程(III)において板状のガラス10の他方の主面に入射された光Uによって樹脂層20が感光しないように樹脂層20を光Uから保護する。すなわち、波長λ1の光に対し感光性を有する樹脂組成物を用いて板状のガラス10の一方の主面に樹脂層20を形成したうえで、板状のガラス10の他方の主面側から波長λ1を含む光Uを照射したときに、板状のガラス10は、板状のガラス10の他方の主面に入射された光Uによって樹脂層20が感光しないように樹脂層20を前記光Uから保護可能である。板状のガラス10は、このような特性を有する限り特に限定されない。板状のガラス10としては、ホウケイ酸ガラス、アルミノシリケートガラス、ソーダライムガラス、チタン含有シリケートガラス、又は無アルカリガラスを好ましく用いることができる。また、コーティングなどの表面処理によってこのような特性が板状のガラス10に付与されていてもよい。
板状のガラス10がホウケイ酸ガラスである場合、コーニング社の♯7059又はパイレックス(登録商標)を用いることができる。
板状のガラス10がアルミノシリケートガラスである場合、以下のような組成を有するガラス組成物を用いてもよい。
また、以下のような組成を有するガラス組成物を用いてもよい。
さらに、以下のような組成を有するガラス組成物を用いてもよい。
また以下のガラス組成物を用いることができる。
さらに、以下のガラス組成物を用いてもよい。
板状のガラス10がソーダライムガラスである場合、例えば板ガラスに広く用いられるガラス組成物を用いることができる。
また、板状のガラス10がチタン含有シリケートガラスである場合、例えば、TiO2を5モル%以上含有することによって、板状のガラス10の、波長250nm~535nmの範囲内の所定の波長λ2の光の吸収係数を1cm-1以上にすることができ、TiO2を10モル%以上含有することによって、板状のガラス10の、波長λ2の光の吸収係数を4cm-1以上にすることができる。さらに、必要に応じて、板状のガラス10は、Bi、W、Mo、Ce、Co、Fe、Mn、Cr、及びVから選ばれる金属の酸化物を少なくとも1種含んでいてもよい。これらの金属の酸化物は、着色成分として機能し、板状のガラス10の吸収係数を高めることができる。
板状のガラス10がチタン含有シリケートガラスである場合、例えば、以下のガラス組成物を用いることができる。
また上記のチタン含有シリケートガラスにおいて、
さらに上記チタン含有シリケートガラスにおいて、
無アルカリガラスとしては、例えば以下のガラス組成物を用いることができる。
板状のガラス10の厚みは特に限定されない。製造されるガラス基板がインターポーザとして使用される場合、板状のガラス10の厚みは、例えば、0.05~1mmである。
工程(I)において、板状のガラス10に貫通孔11を形成する方法は、特に限定されない。例えば、特許文献1~3に記載の方法などの公知の方法を使用できる。また、工程(I)において、板状のガラス10に貫通孔11を形成する方法としては、製造コストを抑制しつつ、貫通孔11を形成する際に貫通孔11の周辺で板状のガラス10に生じる変形を抑制して形状のそろった貫通孔11を形成する観点から、以下で述べる方法が好ましく用いられる。具体的に、工程(I)は、工程(I-a)と、工程(I-b)とを備える。これらの工程については、特開2008-156200号に記載の方法を適用することができる。
工程(I-a)は、板状のガラス10にレーザーを照射することによって、板状のガラス10のレーザーが照射された部分に変質部を形成する工程である。ここで、レーザーは、波長250nm~535nmの範囲内の所定の波長λ2を有する。工程(I-b)は、板状のガラス10の変質部が形成されていない部分に対するエッチングレートよりも変質部に対するエッチングレートが大きいエッチング液を用いて少なくとも変質部をエッチングすることによって、板状のガラス10に貫通孔11を形成する工程である。
工程(I-a)では、例えば、波長λ2のパルスレーザーをレンズで集光して板状のガラス10に照射する。パルスレーザーのパルス幅は、特に限定されないが、レーザー照射装置のコストを抑制しつつ、レーザーLの尖頭値を所定値以上にして加工性を確保する観点から、例えば、1ns(ナノ秒)~200nsであり、好ましくは1ns~100nsであり、より好ましくは5ns~50nsである。
パルスレーザーは、例えば、Nd:YAGレーザーの高調波、Nd:YVO4レーザーの高調波、又はNd:YLFレーザーの高調波である。この場合、高調波は、例えば、第2高調波、第3高調波、又は第4高調波である。第2高調波の波長は、532nm~535nm近傍であり、第3高調波の波長は、355nm~357nm近傍であり、第4高調波の波長は、266nm~268nmの近傍である。このようなパルスレーザーを用いることによって、板状のガラス10に安価に変質部を形成することができる。
板状のガラス10に微小な貫通孔11を形成できるように、パルスレーザーの照射スポットを所定値以下にする観点から、パルスレーザーの波長λ2は、例えば、535nm以下であり、好ましくは360nm以下であり、より好ましくは350nm~360nmである。また、波長λ1<波長λ2の関係が満たされていることが望ましい。
パルスレーザーが有するエネルギーは、特に限定されないが、板状のガラス10の材質又は板状のガラス10に形成すべき変質部の寸法などに応じたエネルギーであることが好ましい。パルスレーザーが有するエネルギーは、例えば、5μJ/パルス~100μJ/パルスである。パルスレーザーのエネルギーを増加させることによって、それに比例するように変質部の長さを長くすることができる。パルスレーザーのビーム品質M2は、例えば、2以下である。この場合、板状のガラス10に微小な貫通孔11を形成しやすい。
板状のガラス10の、波長λ2の光の吸収係数は、例えば、50cm-1以下であり、好ましくは0.1cm-1~20cm-1である。この場合、パルスレーザーのエネルギーが板状のガラス10の表面近傍で吸収されることを軽減して、板状のガラス10の内部に変質部が形成されやすくなる。なお、波長λ2における板状のガラス10の吸収係数が0.1cm-1未満であっても、板状のガラス10の内部に変質部を形成することはできる。波長λ2の光の吸収係数が50cm-1以下であるガラスは、公知のガラスから選択することができる。
吸収係数は、厚さd(例えば約0.1cm)のサンプルの透過率及び反射率を測定することによって算出できる。まず、厚さd(cm)のサンプルについて、透過率T(%)と、入射角12°における反射率R(%)とを測定する。透過率T及び反射率Rは、例えば、島津製作所社製の分光光度計UV-3100型を用いて測定できる。そして、測定値から以下の式を用いてガラスの吸収係数αを算出できる。
上記の方法によれば、板状のガラス10が感光性ガラスである必要がない。このため、多くの種類のガラスについて変質部を形成できる。すなわち、上記の方法では、板状のガラス10が金又は銀を実質的に含まないガラスである場合にも適用できる。
板状のガラス10にレーザーを照射したときに、板状のガラス10の上面及び下面に割れが発生することを抑制する観点から、板状のガラス10のヤング率は、70GPa以上であることが好ましい。
レンズの焦点距離F(mm)は、例えば50mm~500mmであり、好ましくは100mm~200mmである。
また、パルスレーザーのビーム径D(mm)は、例えば1mm~40mmであり、好ましくは3mm~20mmである。ここで、ビーム径Dは、レンズに入射する際のパルスレーザーのビーム径であり、ビームの中心の強度に対して強度が[1/e2]倍となる範囲の直径を意味する。
焦点距離Fをビーム径Dで除した値、すなわち[F/D]の値は、7以上であり、好ましくは7以上40以下であり、より好ましくは10以上20以下である。この値は、ガラスに照射されるレーザーの集光性に関係する値である。F/Dが7以上であると、ビームウェスト近傍でレーザーパワーが強くなりすぎることを防止でき、板状のガラス10の内部にクラックが発生することを防止できる。
パルスレーザーを板状のガラス10に照射する前に板状のガラス10に対して前処理を行うこと、例えば、パルスレーザーの吸収を促進するような膜を形成することは不要である。ただし、場合によっては、そのような処理を行ってもよい。
板状のガラス10のパルスレーザーが照射された部分に変質部が形成される。変質部は、通常、光学顕微鏡を用いた観察によって他の部分と見分けることができる。変質部は、レーザー照射によって光化学的な反応が起き、E'センターや非架橋酸素などの欠陥が生じた部位やレーザー照射の急熱・急冷によって発生した、高温度域における疎なガラス構造を保持した部位等である。変質部は、板状のガラス10の変質部以外の部分よりも所定のエッチング液に対して、エッチングされやすい。
工程(I-a)では、例えば、板状のガラス10の内部にフォーカスされるようにレーザーを板状のガラス10に照射する。変質部は、工程(I-b)において板状のガラス10に貫通孔11を容易に形成できるように形成されている。このため、例えば、板状のガラス10の厚さ方向の中央付近にフォーカスされるようにレーザーが板状のガラス10に照射される。また、変質部を板状のガラス10に形成できる限り、板状のガラス10の外部にフォーカスされるようにレーザーが照射されてもよい。例えば、板状のガラス10のレーザーが入射する側の面から所定の距離(たとえば1.0mm)だけ離れた位置にフォーカスされるようにレーザーが照射されてもよく、板状のガラス10の、レーザーが入射する側の面と反対側の面から所定の距離(たとえば1.0mm)だけ離れた位置にフォーカスされるようにレーザーが照射されてもよい。換言すると、板状のガラス10に変質部を形成できる限り、レーザーは、(i)板状のガラス10の、レーザーが入射する側の面から、レーザーが進行する方向とは逆の方向に1.0mm以内にある位置(板状のガラス10の、レーザーが入射する側の面を含む)、(ii)板状のガラス10の、レーザーが入射する側の面と反対側の面から、板状のガラス10を透過したレーザーが進行する方向に1.0mm以内にある位置(板状のガラス10の、レーザーが入射する側の面と反対側の面を含む)、又は(iii)板状のガラス10の内部にフォーカスされてもよい。
板状のガラス10に形成される変質部の大きさは、レンズに入射する際のレーザーのビーム径D、レンズの焦点距離F、板状のガラス10の吸収係数、パルスレーザーのパワーなどによって変化する。これらのパラメータを調整することによって、例えば、直径が10μm以下で板状のガラス10の厚み方向における長さが100μm以上である円柱状の変質部を形成することができる。
工程(I-a)において選択される条件の一例を表1に示す。
次に、工程(I-b)について説明する。工程(I-b)において、板状のガラス10の変質部が形成されていない部分に対するエッチングレートよりも変質部に対するエッチングレートが大きいエッチング液が用いられる。このようなエッチング液としては、例えば、フッ酸(フッ化水素(HF)の水溶液)を用いることができる。また、エッチング液として、硫酸(H2SO4)若しくはその水溶液、硝酸(HNO3)若しくはその水溶液、又は塩酸(塩化水素(HCl)の水溶液)を用いてもよい。また、エッチング液として、これらの酸の混合物を用いてもよい。エッチング液としてフッ酸を用いた場合、板状のガラス10に形成された変質部のエッチングが進みやすく、短時間で貫通孔11を形成できる。エッチング液として硫酸を用いた場合、板状のガラス10に形成された変質部以外のガラスがエッチングされにくく、テーパー角の小さいストレートな貫通孔11を形成できる。
エッチング時間及びエッチング液の温度は、板状のガラス10に形成された変質部の形状や寸法に応じて適宜選択される。エッチング時のエッチング液の温度を高くすることによってエッチング速度を高めることができる。また、エッチング条件によって貫通孔11の直径を制御できる。
工程(I-a)において、例えば、板状のガラス10の上面側及び下面側に露出するように変質部が形成されていると、板状のガラス10の上面側及び下面側からエッチングを行うことによって貫通孔11を形成できる。また、工程(I-a)において、板状のガラス10の上面側又は下面側に露出しないように変質部が形成されている場合、工程(I-b)を行う前に、変質部が露出するように板状のガラス10を研磨してもよい。
工程(I-a)における変質部の形成条件及び工程(I-b)におけるエッチング条件を変化させることによって、貫通孔11の形状を、円柱状、円錐台状、又は鼓形状(砂時計形状)等の形状に形成することができる。
次に、工程(II)について説明する。まず、波長120nm~300nmの範囲内の所定の波長λ1の光に対し感光性を有する樹脂組成物を準備する。このような樹脂組成物としては、例えば、波長λ1の光が照射されることによって、所定のアルカリ溶液に対する溶解性が増大する樹脂組成物を用いることができる。すなわち、この樹脂組成物は、感光前は所定のアルカリ溶液に対して不溶である。例えば、化学増幅型であるポジ型のフォトレジストとして使用されている樹脂組成物を、工程(II)において用いることができる。化学増幅型であるポジ型のフォトレジストは、例えば、アルカリ可溶基が酸不安定保護基によって保護されているアルカリ可溶樹脂と、光酸発生剤とを含む。例えば、このような樹脂組成物をスピンコーティング等のコーティング方法を用いて板状のガラス10の一方の主面の全体に塗布することによって、図1の(e)に示すように、樹脂層20を形成できる。この場合、樹脂組成物が板状のガラス10に塗布されることによって貫通孔11を覆うように樹脂層20が形成される。
また、樹脂層20は、波長λ1の光に対し感光性を有する樹脂組成物を含むドライフィルムを板状のガラス10の一方の主面に貼り付けることによって形成されてもよい。このようなドライフィルムは、例えば、加熱プレスによって、板状のガラス10の一方の主面に貼り付けることができる。
次に、工程(III)について説明する。工程(III)では、図1の(f)に示すように、板状のガラス10の他方の主面(樹脂層20が形成されている板状のガラス10の一方の主面の反対側の主面)側から、波長λ1を含む光Uが板状のガラス10及び樹脂層20に照射される。このとき、板状のガラス10及び樹脂層20に照射される光Uは、波長λ1以外の波長を有していてもよい。この場合、板状のガラス10及び樹脂層20に照射される光のスペクトルが波長λ1付近においてピークを有していることが好ましい。上記の通り、板状のガラス10において、波長λ1の光の透過率は1%以下であるので、波長λ1の光は、板状のガラス10をほとんど透過しない。また、板状のガラス10は、工程(III)において板状のガラス10の他方の主面に入射された光Uによって樹脂層20が感光しないように樹脂層20を光Uから保護する。このため、樹脂層20のうち板状のガラス10と接している部分は、光Uによって感光しない。一方、光Uは、貫通孔11を通って樹脂層20の貫通孔11を覆う部分(貫通孔11に面している部分)を感光させる。これにより、光Uは紫外線領域に属するので、例えば、光酸発生剤が光分解して酸を発生し、この酸を触媒に酸不安定保護基が脱保護反応を起こす。これにより、樹脂の極性が変化することによって、樹脂層20の感光した部分がアルカリ不溶からアルカリ可溶に変化する。このため、樹脂層20の貫通孔11を覆う部分の所定のアルカリ溶液に対する溶解性が増大するが、樹脂層20のそれ以外の部分は所定のアルカリ溶液に対して不溶のままである。
光Uの光源は、照射される光の波長が120nm~300nmの範囲内の所定の波長λ1を含む限り、特に限定されない。光Uの光源としては、例えば、エキシマレーザー、エキシマランプ、又は低圧水銀ランプを用いることができる。エキシマレーザーは、例えば、193nm(ArF)、248nm(KrF)等の波長の光を照射する。エキシマランプは、例えば、126nm(Ar2)、146nm(Kr2)、172nm(Xe2)、又は222nm(KrCl)の波長の光を照射する。低圧水銀ランプは、例えば、185nm又は254nmの波長の光を照射する。また、前述のNd:YAGレーザー等の高調波を用いることもできる。場合によっては、照射される光の波長を120nm~300nmの範囲内に制限するフィルタも併せて用いることもできる。光Uの照射時間は、樹脂層20の貫通孔11を覆う部分を十分に感光させることができる限り特に限定されない。光Uの照射時間は、例えば、数秒~数分である。
次に、工程(IV)について説明する。工程(IV)では、樹脂層20の、工程(III)において感光した部分が除去される。例えば、樹脂層20が所定のアルカリ溶液に浸される。これにより、樹脂層20の貫通孔11を覆う部分が除去され、図1の(g)に示すように、樹脂貫通孔21が形成される。このようにして、ガラス基板1aが製造される。
所定のアルカリ溶液としては、例えば、ポジ型のフォトレジストの現像液を用いることができる。例えば、TMAH(テトラメチルアンモニウムハイドロオキサイド)を含む溶液を所定のアルカリ溶液として用いることができる。なお、樹脂層20の貫通孔11を覆う部分以外の部分は、光Uによって感光していないので、所定のアルカリ溶液に対して不溶であり除去されない。
樹脂層20の、工程(III)において感光した部分は貫通孔11の真上に位置するので、工程(IV)が行われることによって、樹脂貫通孔21が貫通孔11に正確にアライメントされて形成される。すなわち、樹脂貫通孔21は、貫通孔11から樹脂層20の厚み方向に延びるように形成される。このように、貫通孔11が形成された板状のガラス10は、樹脂層20の所定の位置に樹脂貫通孔21を形成するためのマスクとして機能する。
第1実施形態に係るガラス基板の製造方法は、工程(V)をさらに備えていてもよい。工程(V)は、貫通孔11の内部及び樹脂貫通孔21の内部に貫通電極30を形成する工程である。貫通孔11の内部及び樹脂貫通孔21の内部に貫通電極30を形成できる限り、貫通電極30を形成する方法は特に限定されない。例えば、Cu(銅)などの金属を用いためっきによって、貫通孔11の内部に貫通電極30を形成する。板状のガラス10に直接めっきを施すことは難しい。このため、例えば、図1の(c)に示すように、貫通電極30をなす導電材料を付着させるためのシード層12を少なくとも貫通孔11の内周面に予め形成したうえで、めっきによって貫通電極30を形成する。貫通孔11の内周面を含む板状のガラス10の表面を、例えばPd(パラジウム)を含む触媒と接触させることによってシード層12を形成することができる。これにより、板状のガラス10に無電解めっきを施すことができる。さらに、第1実施形態に係るガラス基板の製造方法において、図1(d)に示すように、板状のガラス10の、樹脂層20が形成されるべき一方の主面に形成されたシード層12は、研磨によって除去される。これにより、複数の貫通電極30の間での電気の導通が防止される。図1に示すように、シード層12の形成及び除去は、例えば、工程(I)が行われた後、かつ、工程(II)が行われる前の期間に行われる。
板状のガラス10をめっきする金属は、特に限定されないが、導電性を高め、製造コストを低減する観点から、Cu(銅)であることが好ましい。Cu(銅)によってめっきする場合を例に以下の説明を行う。最初に、貫通孔11の内周面に形成されたシード層12に無電解めっきによりCu(銅)が析出してめっき層が形成される。このめっき層の表面にさらにCu(銅)が析出してめっき層が成長することによって、図1の(h)に示す通り、貫通孔11の内部及び樹脂貫通孔21の内部に貫通電極30が形成される。なお、板状のガラス10の他方の主面にシード層12が形成されている場合、板状のガラス10の他方の主面にもCu(銅)が析出してめっき層が形成される。無電解めっきによって、所定の厚みを有するめっき層が、板状のガラス10の他方の主面に形成されると、板状のガラス10の他方の主面側で導電性が確保される。この場合、電解めっきによってより効率的にめっきを行ってもよい。すなわち、無電解めっきと電解めっきとを組み合わせて板状のガラス10に対してめっきを施してもよい。
板状のガラス10の他方の主面にめっき層が形成される場合、このめっき層は研磨によって除去されてもよい。このとき、めっき層とともにシード層12も除去される。このようにして、図1の(i)に示すようなガラス基板1axが製造される。また、このめっき層を利用して、板状のガラス10の他方の主面にフォトリソグラフィによって所定の回路パターンが形成されてもよい。
<第2実施形態>
第2実施形態に係るガラス基板の製造方法において、工程(I)、工程(III)、及び工程(IV)は、第1実施形態と同様に行われる。また、シード層12も第1実施形態と同様に形成される。
第2実施形態に係るガラス基板の製造方法では、図2の(b)に示すように、工程(II)において、板状のガラス10の一方の主面の、貫通孔11から所定の距離離れた位置に光学素子25を形成する。このとき、樹脂層20を形成する樹脂組成物としては、ポジ型の紫外線感光性樹脂組成物を用いることができる。この樹脂組成物は、波長120nm~300の範囲内の所定の波長λ1の光に対し感光性を有する。光学素子25は、例えば、所定の曲面を有するレンズである。光学素子25は、適切な形状を有する型による成形、例えば、熱インプリント等の成形法を用いて、樹脂層20の特定の位置に形成される。このとき、光学素子25を形成する位置を位置決めするためのガイドとして貫通孔11を利用することができる。これにより、光学素子25が形成される位置を光学素子25が形成されるべき位置に高い精度で合わせることができる。光学素子25が形成されるべき位置は、例えば、製造されたガラス基板を、受光素子又は発光素子などの光デバイスを備えた別の基板に重ね合せるときに、別の基板に設けられた光デバイスと光学素子25との位置関係が所定の関係になるように定められている。例えば、製造されたガラス基板が光デバイスを備えた別の基板に重ね合せられたときに、光デバイスから発光される光又は光デバイスで受光される光の光路上に光学素子25が位置するように、光学素子25の位置が定められている。
図2の(c)に示すように、板状のガラス10の他方の主面側から光Uを照射して樹脂層20の貫通孔11を覆う部分を感光させる。その後、図2の(d)に示すように、樹脂層20の感光した部分に所定のアルカリ溶液を接触させて、樹脂層20の感光した部分を除去して樹脂層20を貫通する樹脂貫通孔21を形成する。
第2実施形態に係るガラス基板の製造方法は、第1実施形態と同様に、工程(V)を備えていてもよい。工程(V)は、貫通孔11の内部及び樹脂貫通孔21の内部に貫通電極30を形成する工程である。上記の通り、板状のガラス10の表面には、貫通電極30をなすCu(銅)等の導電材料を付着させるためのシード層12が形成されている。このため、図3の(e)に示すように、めっきによって貫通孔11の内部及び樹脂貫通孔21の内部に貫通電極30を形成することができる。
板状のガラス10の樹脂層20と反対側の主面にもシード層12が形成されているので、この主面にもめっき層が形成される。第2実施形態に係るガラス基板の製造方法の一例では、このめっき層は、図3の(f)に示すように、例えば研磨によって除去される。このとき、めっき層とともにシード層12も除去される。この場合、図3の(g)に示すように、板状のガラス10の樹脂層20と反対側の主面に貫通電極30と電気的に接続された導電部40aを形成することもできる。導電部40aは、例えば、板状のガラス10の樹脂層20と反対側の主面の導電部40aを形成すべき部分以外の部分をマスキングしつつ、導電部40aをなすCu(銅)等の導電材料をスパッタリング又は蒸着させることによって形成できる。このようにして、図3の(g)に示すような、貫通電極30及び導電部40aを備えたガラス基板1bが製造される。
また、第2実施形態に係るガラス基板の製造方法の別の一例では、図3の(h)に示すように、板状のガラス10の樹脂層20と反対側の主面に形成されためっき層にフォトリソグラフィを施してめっき層のうち必要な部分を残すことによって導電部40aを形成できる。このとき、めっき層の不要な部分とともにシード層12も除去される。このようにして、図3の(h)に示すような、貫通電極30及び導電部40aを備えたガラス基板1cが製造される。
ガラス基板1b又はガラス基板1cの使用例について説明する。ガラス基板1b又はガラス基板1cは、例えば、図4に示すように、光デバイス基板2と重ね合わせられて使用される。光デバイス基板2は、基板60と、導電部70と、光デバイス80とを備えている。光デバイス80は、LED(light-emitting diode)若しくはVCSEL(vertical cavity surface emitting laser)などの発光素子又はAPD(avalanche photodiode)などの受光素子である。導電部70は、基板60上に形成された回路パターンであり、光デバイス80に電気的に接続されている。ガラス基板1b又はガラス基板1cは、半田バンプ50によって光デバイス基板2に接合される。具体的には、導電部40aに対して光デバイス基板2を近づけて半田バンプ50によって導電部40aと導電部70とを接合する。
上記の通り、光学素子25は貫通孔11に対して高い精度で位置決めされているので、光学素子25と光デバイス80との位置決めも精度よく行うことができる。例えば、貫通電極30をガイドにしてガラス基板1b又はガラス基板1cと光デバイス基板2との位置決めを行うことができる。ガラス基板1b又はガラス基板1cは、光学素子25が所定の位置に配置されるように光デバイス基板2に対して重ね合わせられている。例えば、光デバイス80から発光された光又は光デバイス80で受光されるべき光の光路上に光学素子25が位置している。貫通孔11又は貫通電極30をガイドにして光学素子25及び光デバイス80を位置決めすることができるので、光学素子25の光軸と光デバイス80の光軸とを合わせることができる。なお、光学素子25、樹脂層20、及び板状のガラス10は、光デバイス80から発光される光又は光デバイス80で受光されるべき光を透過させることができる。
貫通電極30と電気的に接続された導電部40bが、必要に応じて、ガラス基板1bの樹脂層20又はガラス基板1cの樹脂層20の上に形成される。これにより、導電部40b、貫通電極30、導電部40a、及び導電部70によって、光デバイス基板2の外部から、例えば電力又は変調信号を光デバイス80に対して入力できる。また、光学素子25と、光デバイス80とが別々の基板に設けられているので、不良品が発生した場合に、ガラス基板1b又はガラス基板1c、さらに光デバイス基板2のいずれに不具合があるのか容易に探索することができる。
光デバイス80を制御するためのコントローラ(図示省略)が、ガラス基板1b又はガラス基板1cの樹脂層20側に設けられてもよい。この場合、コントローラは、導電部40b、貫通電極30、導電部40a、及び導電部70によって光デバイス80に電気的に接続されている。この場合、光デバイス80を制御するためのコントローラを光デバイス80が設けられている基板とは別の基板に実装させることができる。このように、回路又は素子を基板の主面に垂直な方向に配置することができ、モジュールの集積度を高めることができる。
<第3実施形態>
第3実施形態に係るガラス基板の製造方法は、第1実施形態と同様に、工程(I)、工程(II)、工程(III)、及び工程(IV)を備え、さらに工程(V)を備えている。工程(V)は、貫通孔11の内部及び樹脂貫通孔21の内部に貫通電極30を形成する工程である。例えば、工程(V)において、貫通電極30をなす導電材料を付着させるためのシード層12を少なくとも貫通孔11の内周面に形成したうえで、めっきによって貫通電極30を形成する。ここでは、図5の(a)に示すように、板状のガラス10の樹脂層20側の面を除いて、全体的にシード層12が形成されている。この場合、めっきが施されると、図5の(b)に示すように、貫通電極30が形成されるのに加え、板状のガラス10の樹脂層20と反対側の主面にめっき層が形成される。一方、樹脂層20の表面にはシード層12が形成されていないので、めっき層は形成されない。
板状のガラス10の、樹脂層20と反対側の主面に形成されためっき層は、例えば、図5の(c)に示すように研磨によって除去される。このとき、めっき層とともにシード層12も除去される。この場合、その後、導電部40aが貫通電極30に電気的に接続されるように形成される。導電部40aは、例えば、板状のガラス10の樹脂層20と反対側の主面の、導電部40aを形成すべき部分以外の部分をマスキングしつつ、導電部40aをなすCu(銅)等の導電材料を板状のガラス10の樹脂層20と反対側の主面にスパッタリング又は蒸着させることによって形成できる。
板状のガラス10の樹脂層20と反対側の主面に形成されためっき層を除去せずに、導電部40aを形成するためにこのめっき層を利用してもよい。例えば、図5の(e)に示すように、板状のガラス10の樹脂層20と反対側の主面に形成されためっき層にフォトリソグラフィを施してめっき層のうち必要な部分を残すことによって導電部40aを形成できる。このとき、めっき層の不要な部分とともにシード層12も除去される。
第3実施形態に係るガラス基板の製造方法は、工程(VI)をさらに備えている。工程(VI)は、工程(V)の後に、樹脂層20を除去して、貫通電極30のうち樹脂貫通孔21の内部で樹脂層20に囲まれた部分を露出させる工程である。樹脂層20を除去する方法は、特に制限されない。例えば、樹脂層20に波長120nm~300の範囲内の所定の波長λ1を含む光Uを照射して樹脂層20の全体を感光させ、その後所定のアルカリ溶液を樹脂層20に接触させることによって樹脂層20を除去する。例えば、板状のガラス10の樹脂層20と反対側の主面に形成されためっき層にフォトリソグラフィを施して導電部40aを形成する場合、このフォトリソグラフィに使用される現像液を用いて、めっき層に形成されたレジスト層の現像と同時に樹脂層20を除去してもよい。このようにして、図5の(d)及び(e)に示すように、ガラス基板1d又はガラス基板1eを製造できる。ガラス基板1d及びガラス基板1eは、それぞれ、貫通電極30及び導電部40aを備え、板状のガラス10の導電部40aと反対側の主面で貫通電極30の一部が突出している。
貫通電極30の、板状のガラス10の導電部40aと反対側の主面で露出している部分は、ガラス基板1d又はガラス基板1eの電気的な足がかりとなるピラー35として機能する。このように、第3実施形態に係るガラス基板の製造方法によれば、電気的な接続のための足がかりとなるピラー35を容易に形成できる。図6に示すように、複数のガラス基板1eを積層したときに、ピラー35を用いて素子同士の電気的な接続が実現される。このため、回路パターン又は配線を高集積化することができる。
A method for producing a glass substrate according to the present invention comprises the steps of: (I) forming through-holes (11) in a plate-like glass (10); (II) forming a resin layer (20) on one main surface of the plate-like glass (10) using a resin composition that has photosensitivity to light having a certain wavelength λ1; (III) irradiating the plate-like glass (10) with light U having the wavelength λ1 from the other main surface thereof to photosensitize portions of the resin layer (20) which respectively cover the through-holes (11); and (IV) removing regions which are photosensitized in step (III) to form resin through-holes (21). The plate-like glass (10) protects the resin layer (20) from the light U in such a manner that the resin layer (20) cannot be photosensitized with the light U emitted from the other main surface of the plate-like glass (10) in step (III).
(I)板状のガラスに貫通孔を形成する工程と、
前記工程(I)は、
前記レーザーは、波長250nm~535nmの範囲内の所定の波長λ2を有する、請求項2に記載のガラス基板の製造方法。
前記工程(II)において、前記板状のガラスの前記一方の主面の、前記貫通孔から所定の距離離れた位置に光学素子を形成する、請求項1に記載のガラス基板の製造方法。
(V)前記貫通孔の内部及び前記樹脂貫通孔の内部に貫通電極を形成する工程をさらに備えた、請求項1に記載のガラス基板の製造方法。
前記工程(V)において、前記貫通電極をなす導電材料を付着させるためのシード層を少なくとも前記貫通孔の内周面に形成したうえで、めっきによって前記貫通電極を形成する、請求項5に記載のガラス基板の製造方法。
(VI)前記工程(V)の後に、前記樹脂層を除去して、前記貫通電極のうち前記樹脂貫通孔の内部で前記樹脂層に囲まれた部分を露出させる工程をさらに備えた、請求項5に記載のガラス基板の製造方法。
(VI)前記工程(V)の後に、前記樹脂層を除去して、前記貫通電極のうち前記樹脂貫通孔の内部で前記樹脂層に囲まれた部分を露出させる工程をさらに備えた、請求項6に記載のガラス基板の製造方法。
請求項3に記載のガラス基板の製造方法に供される板状のガラスであって、
(I)板状のガラスに貫通孔を形成する工程と、
(II)波長120nm~300nmの範囲内の所定の波長λ1の光に対し感光性を有する樹脂組成物を用いて前記貫通孔を覆うように前記板状のガラスの一方の主面に樹脂層を形成する工程と、
(III)前記板状のガラスの他方の主面側から前記波長λ1を含む光Uを照射して前記樹脂層の前記貫通孔を覆う部分を感光させる工程と、
(IV)前記樹脂層の、工程(III)において感光した部分を除去して前記樹脂層を貫通する樹脂貫通孔を形成する工程と、を備え、
前記板状のガラスは、前記波長λ1の光の透過率が1%以下であり、かつ、前記工程(III)において前記板状のガラスの前記他方の主面に入射された前記光Uによって前記樹脂層が感光しないように前記樹脂層を前記光Uから保護する、
ガラス基板の製造方法を提供する。
前記工程(I)は、(I-a)前記板状のガラスにレーザーを照射することによって、前記板状のガラスのレーザーが照射された部分に変質部を形成する工程と、(I-b)前記板状のガラスの前記変質部が形成されていない部分に対するエッチングレートよりも前記変質部に対するエッチングレートが大きいエッチング液を用いて少なくとも前記変質部をエッチングすることによって、前記板状のガラスに前記貫通孔を形成する工程と、を備え、前記レーザーは、波長250nm~535nmの範囲内の特定の波長λ2を有する、上記のガラス基板の製造方法に供される板状のガラスであって、
前記波長λ1の光の透過率が1%以下であり、かつ、前記波長λ2の光の吸収係数が50cm-1以下であり、
前記樹脂組成物を用いて当該板状のガラスの一方の主面に樹脂層を形成したうえで、当該板状のガラスの他方の主面側から前記波長λ1を含む前記光Uを照射したときに、当該板状のガラスの前記他方の主面に入射された前記光Uによって前記樹脂層が感光しないように前記樹脂層を前記光Uから保護可能である、板状のガラスを提供する。
第1実施形態に係るガラス基板の製造方法は、工程(I)、工程(II)、工程(III)、及び工程(IV)を備えている。工程(I)のために、図1の(a)に示すように、板状のガラス10を準備する。工程(I)は、図1の(b)に示すように、板状のガラス10に貫通孔11を形成する工程である。工程(II)は、図1の(e)に示すように、波長120nm~300nmの範囲内の所定の波長λ1の光に対し感光性を有する樹脂組成物を用いて貫通孔11を覆うように板状のガラス10の一方の主面に樹脂層20を形成する工程である。工程(III)は、図1の(f)に示すように、板状のガラス10の他方の主面側から波長λ1を含む光Uを照射して樹脂層20の貫通孔11を覆う部分を感光させる工程である。工程(IV)は、図1の(g)に示すように、樹脂層20の、工程(III)において感光した部分を除去して樹脂層20を貫通する樹脂貫通孔21を形成する工程である。
質量%で表して、
SiO2 58~66%、
Al2O3 13~19%、
Li2O 3~4.5%、
Na2O 6~13%、
K2O 0~5%、
R2O 10~18%(ただし、R2O=Li2O+Na2O+K2O)、
MgO 0~3.5%、
CaO 1~7%、
SrO 0~2%、
BaO 0~2%、
RO 2~10%(ただし、RO=MgO+CaO+SrO+BaO)、
TiO2 0~2%、
CeO2 0~2%、
Fe2O3 0~2%、
MnO 0~1%(ただし、TiO2+CeO2+Fe2O3+MnO=0.01~3%)、SO3 0.05~0.5%の組成を有するガラス組成物。
質量%で示して、
SiO2 60~70%、
Al2O3 5~20%、
Li2O+Na2O+K2O 5~25%、
Li2O 0~1%、
Na2O 3~18%、
K2O 0~9%、
MgO+CaO+SrO+BaO 5~20%、
MgO 0~10%、
CaO 1~15%、
SrO 0~4.5%、
BaO 0~1%、
TiO2 0~1%、
ZrO2 0~1%、
からなる組成を有するガラス組成物。
質量%で示して、
SiO2 59~68%、
Al2O3 9.5~15%、
Li2O 0~1%、
Na2O 3~18%、
K2O 0~3.5%、
MgO 0~15%、
CaO 1~15%、
SrO 0~4.5%、
BaO 0~1%、
TiO2 0~2%、
ZrO2 1~10%、
を含むガラス組成物。
質量%で表して、
SiO2 50~70%、
Al2O3 14~28%、
Na2O 1~5%、
MgO 1~13%、及び
ZnO 0~14%、
を含むガラス組成物。
質量%で表して、
SiO2 56~70%、
Al2O3 7~17%、
Li2O 4~8%、
MgO 1~11%、
ZnO 4~12%、
Li2O+MgO+ZnO 14~23%、
B2O3 0~9%、および
CaO+BaO 0~3%
TiO2 0~2%、
からなるガラス組成物。
モル%で表示して、
50≦(SiO2+B2O3)≦79モル%、
5≦(Al2O3+TiO2)≦25モル%、
5≦(Li2O+Na2O+K2O+Rb2O+Cs2O+MgO+CaO+SrO+BaO)≦25モル%、
ただし、5≦TiO2≦25モル%である、ガラス組成物。
(Al2O3+TiO2)/(Li2O+Na2O+K2O+Rb2O+Cs2O+MgO+CaO+SrO+BaO)≦0.9、
であることが好ましい。
70≦(SiO2+B2O3)≦79モル%、
10≦TiO2≦15モル%、
10≦Na2O≦15モル%、
であることが好ましい。
モル%で表示して、
45≦(SiO2+B2O3)≦80モル%、
7≦Al2O3≦15モル%、
0≦TiO2≦5モル%、
2≦(MgO+CaO+SrO+BaO)≦20モル%
を含み、実質的にアルカリ金属酸化物を含まないガラス組成物。
α=ln((100-R)/T)/d
次に、第2実施形態に係るガラス基板の製造方法について説明する。第2実施形態に係るガラス基板の製造方法は、特に説明する場合を除き、第1実施形態に係るガラス基板の製造方法と同様に行われる。第1実施形態に係る説明は、技術的に矛盾しない限り、第2実施形態にもあてはまる。
次に、第3実施形態に係るガラス基板の製造方法について説明する。第3実施形態に係るガラス基板の製造方法は、特に説明する場合を除き、第1実施形態に係るガラス基板の製造方法と同様に行われる。第1実施形態に係る説明は、技術的に矛盾しない限り、第3実施形態にもあてはまる。
(II)波長120nm~300nmの範囲内の所定の波長λ1の光に対し感光性を有する樹脂組成物を用いて前記貫通孔を覆うように前記板状のガラスの一方の主面に樹脂層を形成する工程と、
(III)前記板状のガラスの他方の主面側から前記波長λ1を含む光Uを照射して前記樹脂層の前記貫通孔を覆う部分を感光させる工程と、
(IV)前記樹脂層の、工程(III)において感光した部分を除去して前記樹脂層を貫通する樹脂貫通孔を形成する工程と、を備え、
前記板状のガラスは、前記波長λ1の光の透過率が1%以下であり、かつ、前記工程(III)において前記板状のガラスの前記他方の主面に入射された前記光Uによって前記樹脂層が感光しないように前記樹脂層を前記光Uから保護する、
ガラス基板の製造方法。
(I-a)前記板状のガラスにレーザーを照射することによって、前記板状のガラスのレーザーが照射された部分に変質部を形成する工程と、
(I-b)前記板状のガラスの前記変質部が形成されていない部分に対するエッチングレートよりも前記変質部に対するエッチングレートが大きいエッチング液を用いて少なくとも前記変質部をエッチングすることによって、前記板状のガラスに前記貫通孔を形成する工程と、を備えた、
請求項1に記載のガラス基板の製造方法。
前記波長λ1の光の透過率が1%以下であり、かつ、前記波長λ2の光の吸収係数が50cm-1以下であり、
前記樹脂組成物を用いて当該板状のガラスの一方の主面に樹脂層を形成したうえで、当該板状のガラスの他方の主面側から前記波長λ1を含む前記光Uを照射したときに、当該板状のガラスの前記他方の主面に入射された前記光Uによって前記樹脂層が感光しないように前記樹脂層を前記光Uから保護可能である、板状のガラス。
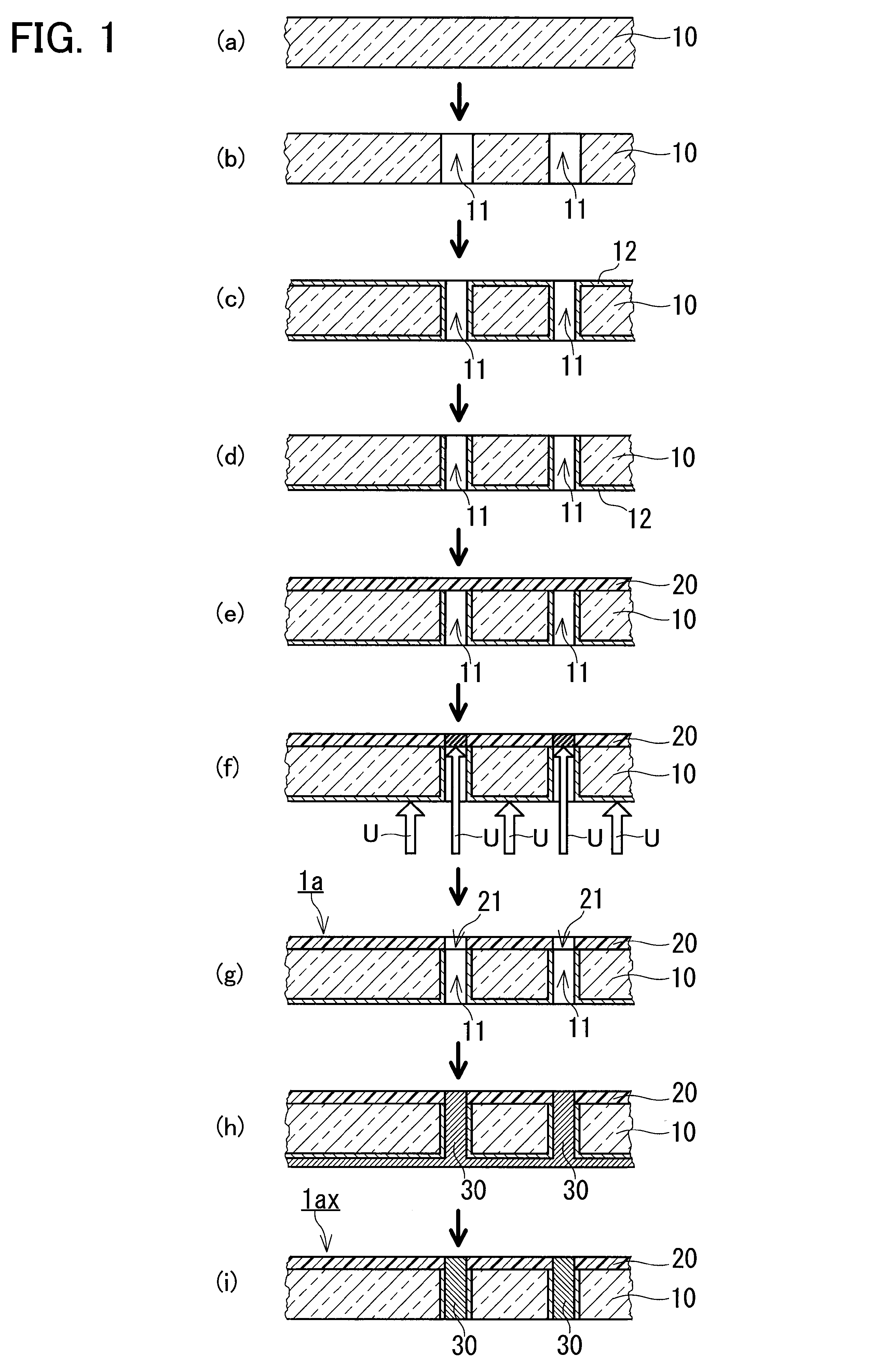
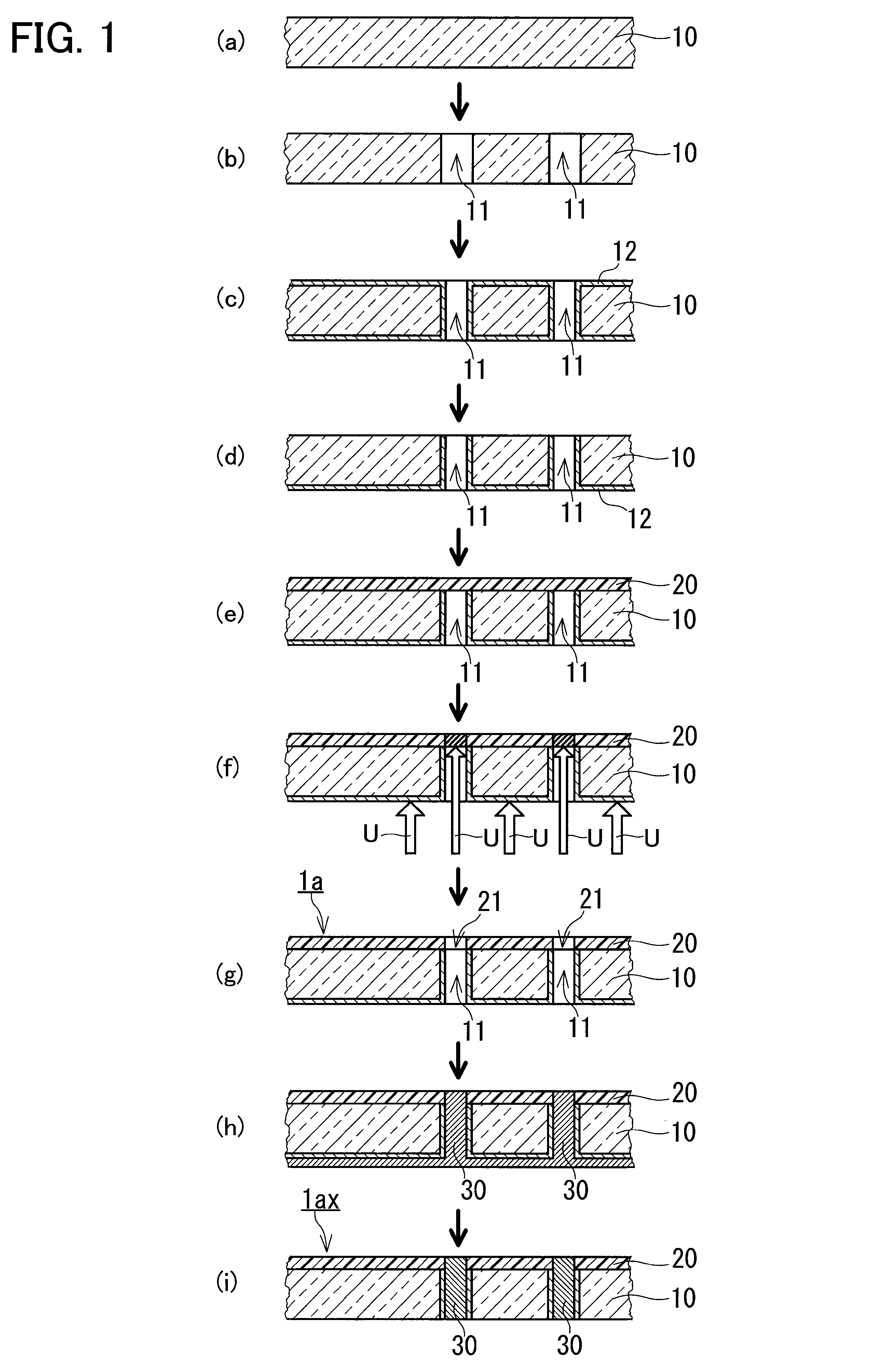
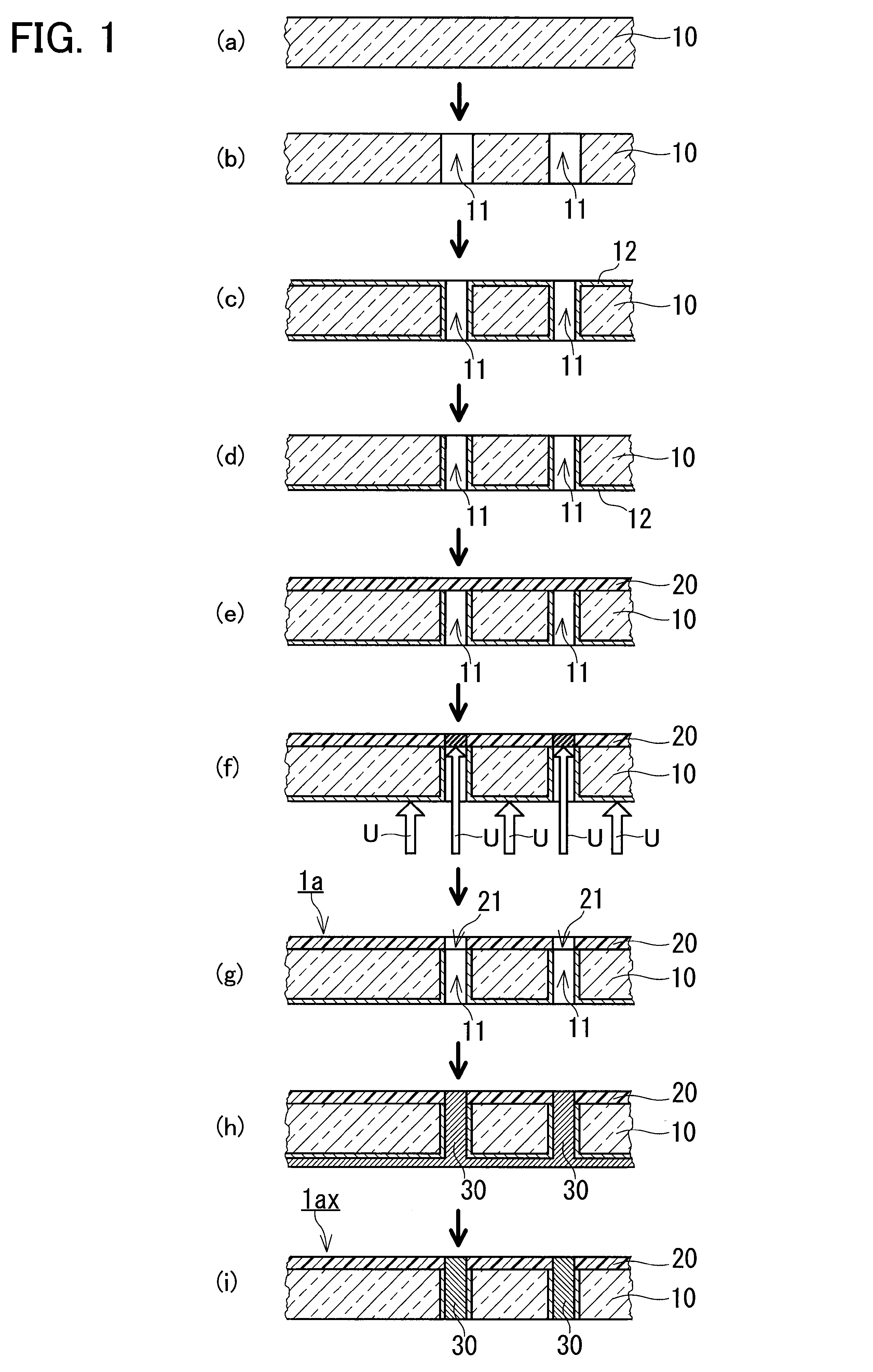
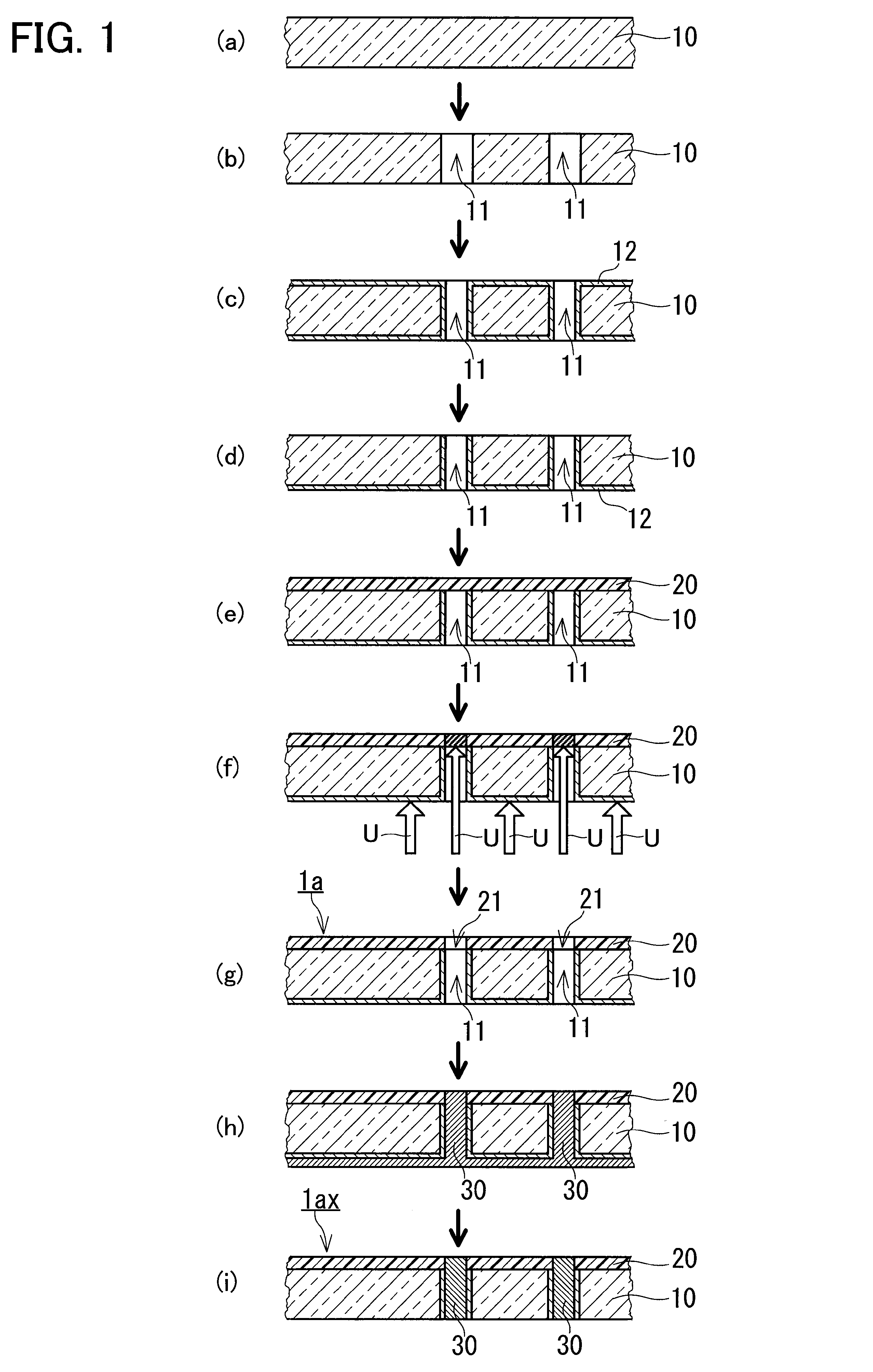
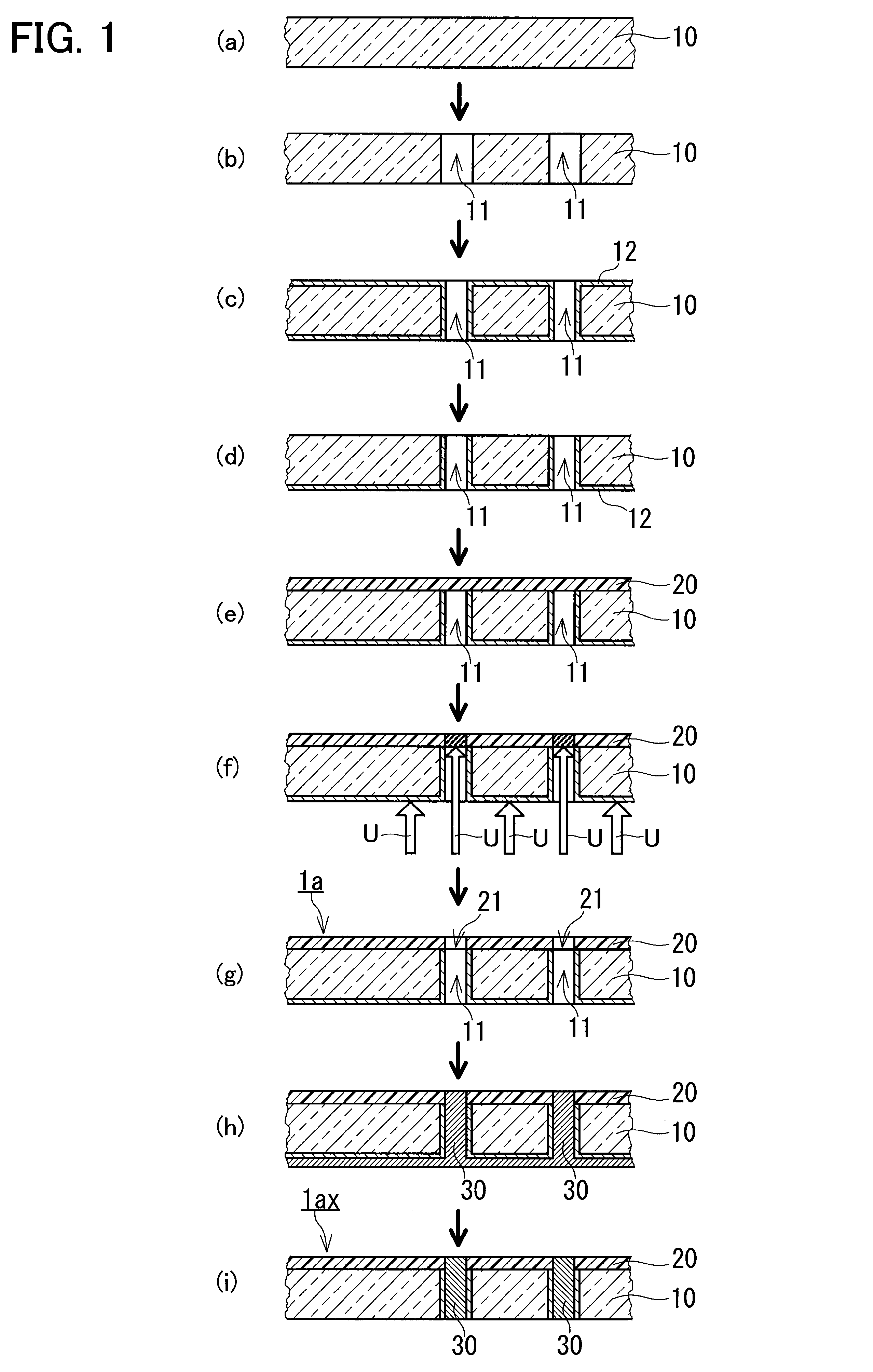
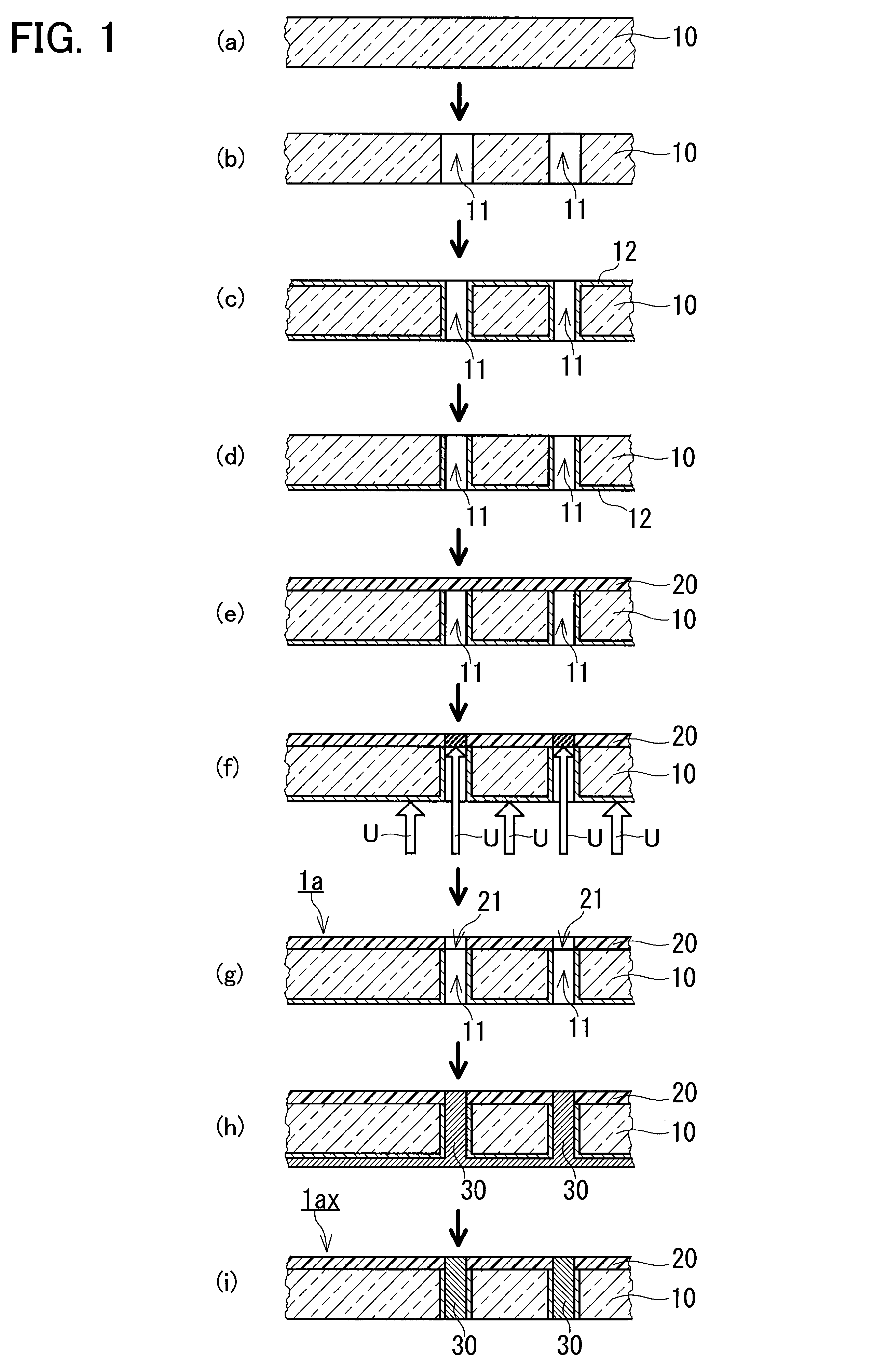